玻璃钢生产流程工艺
玻璃钢化工艺流程及参数

玻璃钢化工艺流程及参数玻璃钢又称玻璃纤维增强塑料,是一种结合了玻璃纤维与树脂的复合材料,具有轻质、高强度、耐腐蚀、耐磨损等特点,在化工、建筑、船舶等领域得到广泛应用。
以下是玻璃钢化工艺流程及参数的详细介绍。
1. 原材料准备玻璃纤维布、树脂、光固剂、促进剂、填料等原材料要事先准备好,并按照一定比例混合均匀。
2. 模具制备制作玻璃钢制品需要用到模具,模具可以根据制品形状进行定制,制作好的模具要进行表面处理,以确保制品表面光滑。
3. 喷涂分布层在模具表面喷涂分布层,分布层可以增强制品表面的平整度和硬度。
4. 手工铺设玻璃纤维布将预先剪好的玻璃纤维布铺设在分布层上,并用刀具整齐地剪裁,以确保玻璃纤维布各处厚度相等。
5. 依次涂层在玻璃纤维布上依次涂上树脂、促进剂、填料等涂层,将涂层均匀涂抹在玻璃纤维布上。
6. 加热固化制品进入加热固化阶段,加热温度和时间视制品尺寸和所用材料而定。
在固化过程中,制品表面会产生气泡,需要用针头将气泡挑破,以保证制品表面光滑。
7. 脱模制品固化后,需要将制品从模具中取出,脱模前需要将模具表面涂上脱模剂以便取出制品。
以上是玻璃钢化工艺流程的具体步骤,下面介绍一些常用的工艺参数:1. 树脂用量:一般为玻璃纤维布重量的30%-40%。
2. 固化温度:一般为55℃-70℃,固化时间一般为6小时左右。
3. 玻璃纤维布厚度:由于玻璃纤维布厚度不同,制品的强度也会有所不同,一般建议选择0.5mm-1mm厚度的玻璃纤维布。
4. 填料用量:填料用量可以根据制品的具体要求进行适当调整,一般为树脂用量的10%-20%。
总的来说,玻璃钢化工艺需要严格控制制品的生产参数,以保证制品的质量和性能。
玻璃钢罐生产工艺流程

玻璃钢罐生产工艺流程下载温馨提示:该文档是我店铺精心编制而成,希望大家下载以后,能够帮助大家解决实际的问题。
文档下载后可定制随意修改,请根据实际需要进行相应的调整和使用,谢谢!并且,本店铺为大家提供各种各样类型的实用资料,如教育随笔、日记赏析、句子摘抄、古诗大全、经典美文、话题作文、工作总结、词语解析、文案摘录、其他资料等等,如想了解不同资料格式和写法,敬请关注!Download tips: This document is carefully compiled by the editor. I hope that after you download them, they can help yousolve practical problems. The document can be customized and modified after downloading, please adjust and use it according to actual needs, thank you!In addition, our shop provides you with various types of practical materials, such as educational essays, diary appreciation, sentence excerpts, ancient poems, classic articles, topic composition, work summary, word parsing, copy excerpts,other materials and so on, want to know different data formats and writing methods, please pay attention!玻璃钢罐是一种常见的储存容器,在工业生产和民用领域都有着广泛的应用。
玻璃钢如何生产工艺
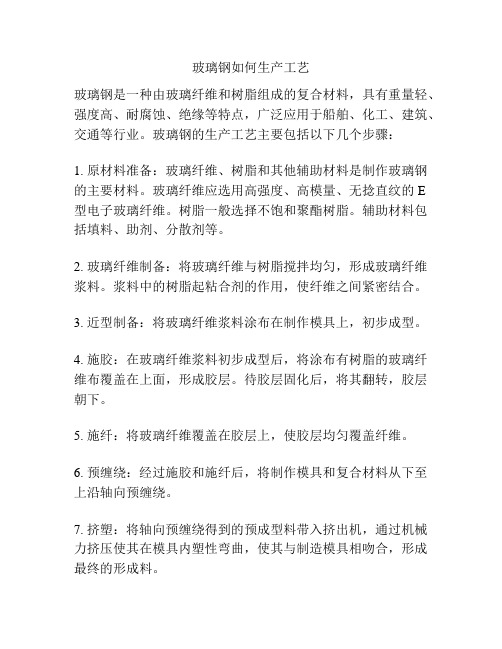
玻璃钢如何生产工艺
玻璃钢是一种由玻璃纤维和树脂组成的复合材料,具有重量轻、强度高、耐腐蚀、绝缘等特点,广泛应用于船舶、化工、建筑、交通等行业。
玻璃钢的生产工艺主要包括以下几个步骤:
1. 原材料准备:玻璃纤维、树脂和其他辅助材料是制作玻璃钢的主要材料。
玻璃纤维应选用高强度、高模量、无捻直纹的E
型电子玻璃纤维。
树脂一般选择不饱和聚酯树脂。
辅助材料包括填料、助剂、分散剂等。
2. 玻璃纤维制备:将玻璃纤维与树脂搅拌均匀,形成玻璃纤维浆料。
浆料中的树脂起粘合剂的作用,使纤维之间紧密结合。
3. 近型制备:将玻璃纤维浆料涂布在制作模具上,初步成型。
4. 施胶:在玻璃纤维浆料初步成型后,将涂布有树脂的玻璃纤维布覆盖在上面,形成胶层。
待胶层固化后,将其翻转,胶层朝下。
5. 施纤:将玻璃纤维覆盖在胶层上,使胶层均匀覆盖纤维。
6. 预缠绕:经过施胶和施纤后,将制作模具和复合材料从下至上沿轴向预缠绕。
7. 挤塑:将轴向预缠绕得到的预成型料带入挤出机,通过机械力挤压使其在模具内塑性弯曲,使其与制造模具相吻合,形成最终的形成料。
8. 固化硬化:经过挤塑后,将模具中的形成料放置一段时间,使树脂硬化,并将成品从模具中取出。
硬化可以通过自身反应、热固化或辐射固化等方式进行。
9. 后续加工:对成品进行切割、打磨、涂漆等后续加工,使其达到所需形状、尺寸和质量要求。
以上就是玻璃钢的主要生产工艺流程。
在实际生产中,还需要根据具体的产品要求进行相应的工艺调整和控制,以确保生产出符合要求的玻璃钢制品。
玻璃钢工艺流程图

河北省枣强玻璃钢集团有限公司
生产工艺流程图
1、手糊产品生产工艺流程
树脂
促进剂
树脂胶液(加固化剂 )
加热固化 脱模 切割修整
检验 产成品
纤维纱
2、模压产品生产工艺流程 树脂 短切毡 纤维纱 辅料
片材制作 →入模 →模压成型→脱模→整理→检验→入库
3、拉挤产品生产工艺流程
上层毡 无碱纱 下层毡
胶液配制
↓
→ 浸渍
→
预 成型
→加固温化 →牵引
→切割
→钻孔
↓
检验 包装
.
可编辑文档
4、缠绕产品生产工艺流程
树脂胶液
付 纤维、表面毡
制衬 缠绕纱 准备 缠绕 固化 修整
检验 交
.
玻璃钢工艺流程
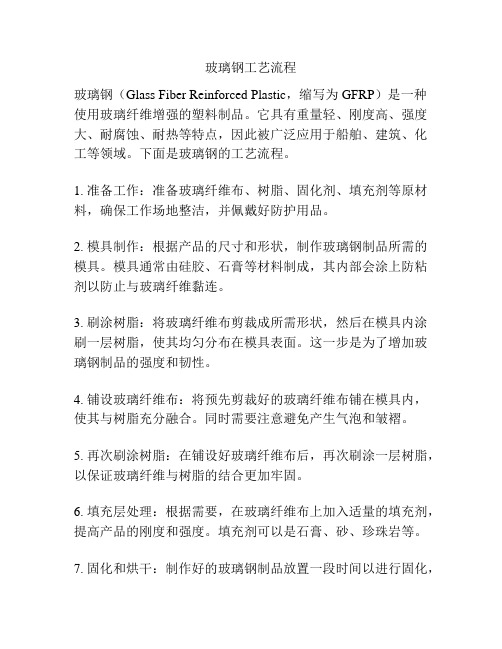
玻璃钢工艺流程玻璃钢(Glass Fiber Reinforced Plastic,缩写为GFRP)是一种使用玻璃纤维增强的塑料制品。
它具有重量轻、刚度高、强度大、耐腐蚀、耐热等特点,因此被广泛应用于船舶、建筑、化工等领域。
下面是玻璃钢的工艺流程。
1. 准备工作:准备玻璃纤维布、树脂、固化剂、填充剂等原材料,确保工作场地整洁,并佩戴好防护用品。
2. 模具制作:根据产品的尺寸和形状,制作玻璃钢制品所需的模具。
模具通常由硅胶、石膏等材料制成,其内部会涂上防粘剂以防止与玻璃纤维黏连。
3. 刷涂树脂:将玻璃纤维布剪裁成所需形状,然后在模具内涂刷一层树脂,使其均匀分布在模具表面。
这一步是为了增加玻璃钢制品的强度和韧性。
4. 铺设玻璃纤维布:将预先剪裁好的玻璃纤维布铺在模具内,使其与树脂充分融合。
同时需要注意避免产生气泡和皱褶。
5. 再次刷涂树脂:在铺设好玻璃纤维布后,再次刷涂一层树脂,以保证玻璃纤维与树脂的结合更加牢固。
6. 填充层处理:根据需要,在玻璃纤维布上加入适量的填充剂,提高产品的刚度和强度。
填充剂可以是石膏、砂、珍珠岩等。
7. 固化和烘干:制作好的玻璃钢制品放置一段时间以进行固化,通常需要使用加热设备加速固化过程。
固化后,可以取出产品。
8. 精加工和装配:将制作好的玻璃钢制品进行必要的精加工,例如修剪边缘、打磨表面等,以得到符合要求的尺寸和外观。
然后进行必要的装配,如添加螺栓、焊接等。
9. 检测和质量控制:对制作好的玻璃钢制品进行检测,包括强度、尺寸、外观等方面的测试。
确保产品符合设计要求和质量标准。
10. 包装与出厂:经过检测合格的玻璃钢制品进行包装,并按照订单安排出货。
这就是玻璃钢的工艺流程。
根据不同的产品需求,可能会有所调整和变化。
玻璃钢槽的工艺流程

玻璃钢槽的工艺流程
玻璃钢槽的工艺流程如下:
1. 设计和确定产品尺寸:根据槽的用途和要求,设计并确定槽的尺寸和结构。
2. 制作模具:根据槽的尺寸和结构,制作相应的模具,用于后续的制作工作。
3. 准备材料:选择适用于制作玻璃钢槽的材料,通常是玻璃纤维布和环氧树脂。
4. 清洁模具:确保模具表面干净,无杂质和灰尘。
5. 喷涂模具胶:在模具表面均匀喷涂一层模具胶,以便后续将玻璃纤维布与树脂粘结在一起。
6. 摆放玻璃纤维布:将预先裁剪好的玻璃纤维布铺在模具上,确保完全覆盖槽的表面,并使其平整。
7. 涂布树脂:将环氧树脂均匀涂布在玻璃纤维布上,保证将其湿透,并确保纤维布与树脂充分浸润。
8. 反复喷涂和涂布:反复喷涂模具胶和涂布树脂,以增加槽的厚度和坚固度,通常需要多层反复处理。
9. 压实和固化:用压缩机或手动工具将槽表面压实,以确保纤维布和树脂之间没有空隙和气泡。
树脂固化期间,根据树脂类型和工艺要求,可能需要进行温度和湿度控制。
10. 拆模和修整:待树脂固化后,拆卸模具,并检查槽的表面和边缘是否平整。
如有不完美的地方,可以进行修整,如打磨、修补等。
11. 检验和测试:对制作好的玻璃钢槽进行质量检验和性能测试,确保其符合设计要求和使用要求。
12. 包装和出厂:对通过检验和测试的玻璃钢槽进行包装,如加固、包装材料等,然后进行出厂备货或发运。
玻璃钢制作工艺流程

玻璃钢制作工艺流程玻璃钢是一种由玻璃纤维和树脂组成的复合材料,具有优良的耐腐蚀性、高强度和良好的绝缘性能。
它被广泛应用于船舶、化工设备、建筑等领域。
下面将介绍玻璃钢制作的工艺流程。
1. 原材料准备玻璃钢的制作需要玻璃纤维、树脂和固化剂等原材料。
首先,需要准备好足够的玻璃纤维布或者玻璃纱,并按照设计要求进行裁剪。
同时,选择适当的树脂和固化剂,根据比例混合好。
2. 模具制作根据产品的形状和尺寸,制作相应的模具。
模具可以是金属模具或者木模具,根据需要进行选择。
模具应具有一定的强度和耐磨性,以确保制作出的产品质量。
3. 表面处理在模具表面涂抹一层脱模剂,以防止玻璃钢与模具粘连。
脱模剂可以是油脂、硅油或者蜡等材料。
然后,将裁剪好的玻璃纤维布或者玻璃纱覆盖在模具表面,使其均匀分布。
4. 树脂涂布将混合好的树脂倒在玻璃纤维布或者玻璃纱上,使用刮板或者刷子将其均匀涂布。
确保树脂能够渗透到纤维布或者纱中,并保持适当的厚度。
树脂的涂布厚度应根据产品的使用要求进行控制。
5. 固化经过树脂涂布后,将模具放置在恒温箱或者室温下进行固化。
固化时间根据树脂类型和环境温度而定,一般需要数小时到数十小时。
在固化过程中,树脂会发生化学反应,形成坚固的结构。
6. 脱模固化完成后,将模具从恒温箱或者室温中取出,进行脱模。
脱模时需要小心操作,以避免损坏制作好的玻璃钢产品。
通过适当的方法,可以将模具与玻璃钢分离。
7. 后处理脱模后的玻璃钢产品可能存在一些不平整或者毛刺等问题,需要进行后处理。
可以使用砂纸、砂轮等工具对产品进行修整,使其表面光滑平整。
同时,可以根据需要进行涂漆或者其他表面处理,以增加产品的美观性和耐久性。
8. 检验和质量控制制作完成的玻璃钢产品需要进行检验和质量控制。
通过检验可以判断产品是否符合设计要求,并对产品的强度、密封性等性能进行评估。
如果发现质量问题,需要进行相应的修复或者调整。
以上就是玻璃钢制作的工艺流程。
通过合理的操作和严格的质量控制,可以制作出高质量的玻璃钢产品。
玻璃钢生产工艺与流程

玻璃钢生产工艺与流程玻璃钢是一种由玻璃纤维和树脂制成的复合材料,其具有优良的物理和化学性能,广泛应用于船舶、建筑、化工等领域。
玻璃钢制品的生产工艺和流程包括纺丝、制备预制件、成型和浸渍固化等环节。
首先是纺丝工艺。
玻璃钢生产的第一步是将无限长度的玻璃纤维分为足够长的纤维束,这个过程称为纺丝。
纺丝的目的是解开纤维的缠结,使其形成平行输送状态,便于后续工序的进行。
纺丝一般采用切割机和梳理机进行,通过机械力和空气吹扫等方式使纤维束得以复原。
接下来是制备预制件。
预制件主要由树脂和填料混合而成。
树脂是起到胶结作用的重要组成部分,常用的有不饱和聚酯树脂和环氧树脂。
填料一般选用硅砂、矿粉、纤维状和薄片状等物料,用于增加产品的强度和硬度。
制备预制件的过程包括树脂和填料的混合、搅拌、施加压力等步骤,以获得均匀的混合物。
再来是成型工艺。
成型是将预制件制作成所需形状和尺寸的过程。
常用的成型方式有手工成型、模具定压成型和吹塑成型等。
手工成型适用于小型和复杂形状的制品,在制作过程中需要工人根据需要手工塑造。
模具定压成型是将预制件放入模具中施加压力,使其成型为所需形状。
吹塑成型是通过将熔化的树脂喷射到模具中,并通过气压使其充填整个模具空腔,从而形成产品。
最后是浸渍固化工艺。
浸渍固化是将成型好的产品浸泡在树脂中,使其充分吸收树脂并固化,以增加产品的强度和硬度。
浸渍固化一般通过真空浸渍和压力浸渍来完成。
在真空浸渍中,产品被放置在真空罐中,通过抽取空气形成真空环境,然后将树脂注入罐中,使产品充分吸收。
在压力浸渍中,产品被放置在密封容器中,然后加压使树脂进入产品。
浸渍后,产品需要经过一定时间的固化,以确保树脂完全硬化。
综上所述,玻璃钢生产过程包括纺丝、制备预制件、成型和浸渍固化等多个工艺环节。
每个环节都有其独特的操作要求和技术细节,通过一系列工序的协同作用,最终得到优质的玻璃钢制品。
玻璃钢生产工艺流程

玻璃钢生产工艺流程
玻璃钢是以玻璃纤维为增强材料,树脂为基体材料制成的一种复合材料,在建筑、汽车、船舶等领域都有广泛的应用。
下面将介绍玻璃钢的生产工艺流程。
首先,需要准备原材料。
玻璃钢的主要原材料包括玻璃纤维、树脂以及一些辅助材料,如固化剂、硬化剂等。
玻璃纤维是制作玻璃钢的增强材料,树脂则是制作玻璃钢的基体材料。
接下来,需要进行原材料的加工和配制。
首先,将玻璃纤维进行切割和整理,使其具有一定的长度和形状。
然后,将树脂和辅助材料按一定的比例混合,并搅拌均匀,形成树脂浆料。
然后,将玻璃纤维和树脂浆料进行复合。
一般情况下,会采用手工灌注或手工涂布的方法进行复合,也可以使用机械喷涂或预浸料的方法。
在复合过程中,需要保证玻璃纤维在树脂浆料中得到均匀分布,并且与树脂浆料充分接触和粘结。
接下来,需要进行固化和加固处理。
固化是将树脂浆料中的树脂进行硬化,使其具有一定的强度和刚性。
一般情况下,会使用温度和压力进行固化,也可以使用化学方法进行固化。
同时,根据产品的实际需求,还可以进行增强处理,如增加玻璃纤维的层压,增加产品的强度和耐久性。
最后,需要进行修整和表面处理。
修整是将制作出来的玻璃钢产品进行修整,使其具有一定的外观和尺寸精度。
表面处理一般包括抛光、喷漆等工艺,使其具有一定的美观性和防腐性。
以上就是玻璃钢的生产工艺流程。
通过以上的加工工艺,可以制作出质量稳定、强度高、耐腐蚀、耐老化的玻璃钢制品。
玻璃钢生产工艺流程图

玻璃钢生产工艺流程图
玻璃钢是一种由无机纤维和合成树脂制成的复合材料,具有轻质、高强度、耐腐蚀等优点,广泛应用于船舶、储罐、管道等领域。
下面是一份玻璃钢生产工艺流程图的描述。
玻璃钢生产工艺流程图
1. 材料准备
首先,准备玻璃纤维、树脂和助剂,其中玻璃纤维是玻璃钢的主要增强材料,树脂起到粘结纤维的作用,助剂用于调整树脂的流动性和固化速度。
2. 纤维预处理
将玻璃纤维进行预处理,例如去除杂质、润湿处理等,以提高纤维与树脂之间的粘结强度。
3. 成型
将处理好的玻璃纤维按照设计要求进行成型,常见的成型方式包括手工涂层成型、模压成型等。
4. 树脂涂布
将树脂溶液均匀地涂布在成型好的玻璃纤维上,使其充分浸润并与纤维粘结。
5. 固化
经过树脂涂布的玻璃纤维进入固化室,通过温度和湿度的调节,使树脂溶液逐渐固化成固体。
6. 后处理
对固化后的玻璃钢制品进行后处理,包括修磨、打磨、去除毛刺、涂装等工序,以提高表面质量和光泽度。
7. 检验
对生产出的玻璃钢制品进行检验,包括物理性能测试、外观质量检查等,确保产品符合相关标准和要求。
8. 包装与出厂
经过检验合格的玻璃钢制品按照规定的方式进行包装,并出厂销售或存储。
以上就是玻璃钢生产工艺流程图的描述。
通过此流程,可以生产出具有优良性能的玻璃钢制品,在不同领域得到广泛的应用。
玻璃钢制作工艺范文

玻璃钢制作工艺范文玻璃钢,又称玻璃纤维增强塑料(GFRP),是一种由玻璃纤维和树脂组合制成的复合材料。
它具有优异的物理性能,如高强度、耐腐蚀、耐高温、耐老化等,被广泛应用于建筑、船舶、汽车、储罐等领域。
下面将介绍玻璃钢制作的工艺流程。
1.原材料准备:玻璃纤维布、树脂、固化剂、溶剂等。
玻璃纤维布按照设计要求进行裁剪。
2.表面处理:根据需要,对待加工的物体表面进行处理,常见的方法有清洗、打磨、喷砂等。
目的是确保表面干净、粗糙度适合树脂的粘附。
3.接触模具制作:根据产品设计要求制作接触模具,包括底模和上模。
接触模具的材料可以选择为木材、塑料、石膏等。
4.上光剂涂布:使用喷涂或刷涂的方式将上光剂均匀地涂布在接触模具的表面上,以防止玻璃纤维和树脂之间的粘结。
5.层叠:将玻璃纤维布放置在接触模具上,根据设计要求进行层叠。
层叠时要确保纤维均匀分布,并注意布料的平整。
6.树脂涂布:使用刷涂、滚涂或喷涂等方式将树脂均匀地涂布在层叠的玻璃纤维布上,确保树脂与纤维的充分浸润和粘结。
7.固化:根据树脂和固化剂的配比和工艺要求,将接触模具放置在恰当的环境条件下进行固化。
固化的温度和时间根据具体工艺来确定。
8.脱模:固化完成后,将接触模具拆除,得到成型的玻璃钢制品。
脱模时需要小心操作,以避免制品的损坏。
9.后处理:对成型的玻璃钢制品进行切割、打磨、抛光等处理,使其达到所需的外观和尺寸要求。
10.检验:对制作完成的玻璃钢制品进行质量检验,检查外观、尺寸、强度等指标是否符合设计要求。
以上为玻璃钢制作的主要工艺流程。
当然,实际制作过程中还会根据具体产品的要求进行一些特殊处理,如增加钢筋加强、辅助固化等。
在制作过程中需要注意材料的配比、施工环境条件和安全操作,以确保制品的质量和性能。
玻璃钢工艺流程图

〔一〕玻璃钢模具手糊成型工艺流程:玻璃钢模具手糊成型工艺是先在模型上涂一层脱模剂,然后将配好的树脂混合料用刮刀或刷子涂刷到模型上,再在其上铺裁好的玻璃布或其它增强材料,用刮刀或毛刷迫使树脂浸入玻璃布,排出气泡,待树脂浸透增强材料后,再铺放第2层增强材料,如此反复涂刷树脂和铺放增强材料,直至到达所需要的设计层数,然后进展固化、脱模和修整。
〔玻璃钢手糊成型工艺流程图见表一〕〔二〕玻璃钢模具原材料的选择:玻璃钢手糊成型模具的原材料主要是树脂、增强材料和辅助材料等。
合理地选择原材料是保证产品质量,降低本钱的重要环节。
选择原材料时,必须满足以下条件:⑴满足产品设计的性能要求;⑵适应手糊成型工艺的特点;⑶价格廉价,货源充分。
目前我司采购的原材料主要有:树脂、增强纤维〔玻纤布、外表毡〕、胶衣、固化剂、促进剂、脱模剂、色料、增韧剂、填料〔石英粉、金刚石粉、铸石粉、石棉粉〕等。
1.树脂的选择:选择手糊成型用的树脂品种十分重要,它直接关系到产品质量和生产工艺。
因此,必须根据产品性能、使用条件及工艺要求确定树脂的品种。
⑴从产品性能考虑,要注意:①树脂固化收缩问题:应选用低收缩树脂。
②断裂延伸率:应选用延伸性好的树脂,提高玻璃钢开裂时的强度。
⑵从工艺角度考虑,树脂应满足:①良好的浸润性。
树脂对纤维的浸润是保证玻璃钢质量的一个重要因素,也是手糊工艺的先决条件。
如浸润不好,不仅使玻璃钢制品成型困难,也会使树脂——纤维间出现气泡;②适当的粘度。
手糊成型时的树脂粘度过低,会出现流胶现象,粘度过大,又会使成型浸润困难;③能在室温或低温下凝胶、固化,并要求固化时无低分子物产生;④无毒或低毒;⑤价格廉价,货源充足。
目前手糊成型工艺中最常用的树脂为不饱和聚酯树脂和环氧树脂,而酚醛树脂很少单独使用。
2.增强材料的选择:纤维品种一般要根据使用条件和工艺设计来进展选择。
⑴从使用条件考虑,要考虑制品的使用温度、强度、韧性、比重、绝缘性等因素。
玻璃钢工艺流程
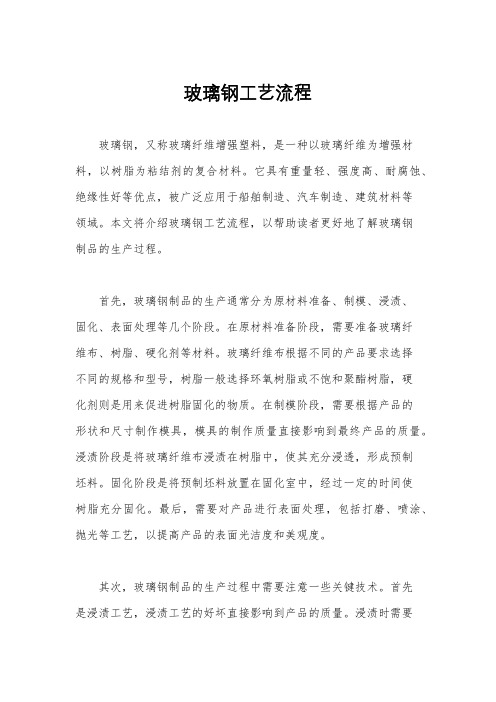
玻璃钢工艺流程玻璃钢,又称玻璃纤维增强塑料,是一种以玻璃纤维为增强材料,以树脂为粘结剂的复合材料。
它具有重量轻、强度高、耐腐蚀、绝缘性好等优点,被广泛应用于船舶制造、汽车制造、建筑材料等领域。
本文将介绍玻璃钢工艺流程,以帮助读者更好地了解玻璃钢制品的生产过程。
首先,玻璃钢制品的生产通常分为原材料准备、制模、浸渍、固化、表面处理等几个阶段。
在原材料准备阶段,需要准备玻璃纤维布、树脂、硬化剂等材料。
玻璃纤维布根据不同的产品要求选择不同的规格和型号,树脂一般选择环氧树脂或不饱和聚酯树脂,硬化剂则是用来促进树脂固化的物质。
在制模阶段,需要根据产品的形状和尺寸制作模具,模具的制作质量直接影响到最终产品的质量。
浸渍阶段是将玻璃纤维布浸渍在树脂中,使其充分浸透,形成预制坯料。
固化阶段是将预制坯料放置在固化室中,经过一定的时间使树脂充分固化。
最后,需要对产品进行表面处理,包括打磨、喷涂、抛光等工艺,以提高产品的表面光洁度和美观度。
其次,玻璃钢制品的生产过程中需要注意一些关键技术。
首先是浸渍工艺,浸渍工艺的好坏直接影响到产品的质量。
浸渍时需要保证玻璃纤维布充分浸透,但又不能使其过度浸透,以免浪费树脂。
其次是固化工艺,固化的温度、时间和湿度都会对产品的性能产生影响,需要根据具体情况进行合理的控制。
另外,模具的制作也是一个关键环节,模具的表面光洁度和精度会直接影响到最终产品的表面质量。
因此,在制作模具时需要严格控制制作工艺,确保模具的质量。
最后,玻璃钢制品的生产过程需要严格遵守相关的安全操作规程。
在浸渍和固化过程中,需要注意通风排气,以免有害气体对人体造成危害。
另外,需要使用个人防护装备,如手套、口罩、护目镜等,以保护工人的安全。
在操作过程中,需要严格按照操作规程进行,禁止随意更改操作步骤,以免造成事故。
总之,玻璃钢工艺流程是一个复杂而又精细的过程,需要严格控制各个环节,确保产品的质量和安全。
希望本文能够帮助读者更好地了解玻璃钢制品的生产过程,为相关行业的从业者提供参考和借鉴。
玻璃钢井盖生产工艺

玻璃钢井盖生产工艺
玻璃钢井盖是一种广泛应用于道路、人行道和城市建设中的井盖产品。
它具有重量轻、强度高、耐腐蚀、防滑等特点,成为市政设施建设的首选材料之一。
那么,玻璃钢井盖的生产工艺是怎样的呢?
玻璃钢井盖的生产工艺包括原材料配比、制模、成型、固化和后期处理等步骤。
其中,原材料的配比是关键的一步。
通常,玻璃钢井盖的主要原材料包括玻璃纤维、环氧树脂、填料和助剂等。
这些原材料需要按照一定比例混合,在配比过程中需要考虑到强度、耐腐蚀性和成本等因素,以确保最终产品的质量。
制模是生产玻璃钢井盖的重要环节。
制模是将原材料混合后的浆料倒入模具中,经过一定的振动和压实工艺,使浆料填充模具的每个角落。
制模过程需要控制好浆料的流动性和粘度,以确保浆料能够均匀地填充模具,形成坚固的井盖结构。
然后,成型是制作玻璃钢井盖的关键步骤。
成型是将填充好浆料的模具进行加热和固化的过程,通过加热可以促进树脂的固化反应,使浆料形成坚硬的结构。
成型时需要控制好温度和固化时间,以确保井盖的强度和稳定性。
固化完成后,玻璃钢井盖还需要进行后期处理。
后期处理包括清洁、修整和光洁处理等环节,以使井盖表面平整光滑,并增加其美观性和耐久性。
总的来说,玻璃钢井盖的生产工艺是一个复杂的过程,需要严格控制每个环节的参数和质量。
只有通过科学合理的工艺流程,才能生产出质量优良、性能稳定的玻璃钢井盖产品。
玻璃钢井盖作为市政设施建设的重要组成部分,其生产工艺的完善和提升,不仅可以提高产品质量,也能够满足城市建设对井盖产品的需求,为人们的出行和生活提供更好的保障。
全面解析玻璃钢施工流程与精湛工艺技巧指南

温馨小提示:本文主要介绍的是关于全面解析玻璃钢施工流程与精湛工艺技巧指南的文章,文章是由本店铺通过查阅资料,经过精心整理撰写而成。
文章的内容不一定符合大家的期望需求,还请各位根据自己的需求进行下载。
本文档下载后可以根据自己的实际情况进行任意改写,从而已达到各位的需求。
愿本篇全面解析玻璃钢施工流程与精湛工艺技巧指南能真实确切的帮助各位。
本店铺将会继续努力、改进、创新,给大家提供更加优质符合大家需求的文档。
感谢支持!(Thank you for downloading and checking it out!)全面解析玻璃钢施工流程与精湛工艺技巧指南一、玻璃钢施工流程总述玻璃钢简介玻璃钢,全名为玻璃纤维增强塑料,是一种以玻璃纤维为增强材料,合成树脂为基体的复合材料。
它具有轻质、高强、耐腐蚀、绝缘性能好等特点,广泛应用于船舶、汽车、建筑、化工、环保等领域。
玻璃钢施工流程是指在施工过程中,按照一定的施工工艺和程序,完成玻璃钢材料铺设、固化、修整等作业的过程。
施工流程概述玻璃钢施工流程主要包括以下几个环节:1)基层处理:对施工基层进行清理、平整、打磨,确保基层表面干净、无油污、无水分、无浮尘,以提高玻璃钢与基层的粘结力。
2)底漆施工:在基层表面涂刷玻璃钢底漆,底漆的作用是提高玻璃钢与基层的附着力,防止基层吸收树脂,导致玻璃钢层间空鼓。
3)铺设玻璃纤维布:按照设计要求,在底漆实干后,均匀铺设玻璃纤维布,并采用树脂涂覆,确保玻璃纤维布与基层紧密粘结。
4)固化:铺设完毕后,进行固化处理,固化时间根据树脂类型和环境温度而定。
固化过程中,要注意保持环境通风,避免紫外线直射。
5)修整:固化完成后,对玻璃钢表面进行修整,去除毛边、毛刺,确保表面光滑、整洁。
6)涂装面漆:在修整好的玻璃钢表面涂刷面漆,面漆可提高玻璃钢的耐候性、耐腐蚀性,增强美观度。
施工前准备工作施工前准备工作是保证玻璃钢施工质量的关键,主要包括以下几个方面:1)材料准备:检查玻璃钢材料的质量,确保符合设计要求。
最新FRP玻璃钢产品车间生产流程

FRP玻璃钢产品生产流程1. 模具清理:将模具上脱模后遗留的残胶,用扁铲小心铲除,注意不能损坏模具表面,将处理好的模具,安放在生产现场,必要时用压缩空气、软布、毛刷等工具对模具表面进行清理杂物的工作,并在糊制前先检查模具表面质量状况是否合格,如果有损坏,需进行修补,修补方法如下:先将破损处清除,刮除受损伤表面,露出新的表面;用丙酮清洗缺损处,待干燥后再作业;如果缺损处比较大,可以用树脂腻子加少量短切纤维填补,使表面低于原表面并固化;用胶衣树脂加入与模具相同的颜料糊进行二次修补,并固化;用水砂纸打磨表面,并抛光,如果不满意可进行二次、三次修补。
模具的修补是一项技术性要求很高的工作,需要有丰富实践经验的人才能完成。
如果模具由多块组成,则需要组装在一起,要注意组装定位,合模缝隙不能过大,必要时用胶带贴封,防止流胶粘模,脱模部件要装好,顶出块要放平。
对于组合模具或阴阳模,块与块之间、阴模与阳模之间的拼装与组合,为了保证拼装尺寸的准确,定位对接部分一定要准确,以保证模具拼装合模到位。
模具表面及周边的灰尘.杂物清理干净后并洗擦脱模蜡,全部清理干净完毕后第一时间告知相关人员要涂抹胶衣。
2. 层糊材料裁剪:增强层的材料应根据产品的技术要求事先选好,所用的短切毡、方格布的类型(即中碱、无碱),厚度以及所用树脂的牌号、种类等在糊制前要严格核对,以免将材料用错,造成不必要的损失。
层糊材料的裁剪需要经过以下步骤:一、裁布台增强材料的裁剪需要一个适当面积的裁布台,把玻璃钢材料铺在台面上量尺寸裁剪。
二、裁布工具主要是尺子、剪刀和裁布刀。
三、检查裁布前应检查原材料的规格、厚度是否满足要求;观察表面是否有油污、杂物、不均等;用手感觉是否已经吸湿,若已吸湿则需烘干后再使用。
四、裁剪根据产品的形状、面积,设定好裁剪尺寸,再在台上裁剪。
布边过硬时要裁掉。
形状复杂或单片的可用剪刀。
现状单一,数量大的布片,特别是短切毡片,可以将毡叠在一起,用裁剪刀一次切割数层。
玻璃钢管道制作工艺

玻璃钢管道制造工艺说明一、玻璃钢管壁结构说明:玻璃钢管壁结构从内到外分别为:玻璃钢内衬层、玻璃钢次内衬层、玻璃钢缠绕层、玻璃钢外部保护层。
玻璃钢内衬层、玻璃钢次内衬层起防腐、防渗作用,缠绕层担负起管道的强度和刚度作用,外保护层起抗老化、防腐蚀、抗日晒的作用。
二、玻璃钢管道制作工艺流程→玻璃钢模具准备→设备调试、原材料准备→玻璃钢管道内衬制作→远红外固化站内衬固化→玻璃钢管道内衬质量检验→玻璃钢管道增强层缠绕→远红外管道整体固化→玻璃钢管道外观及主要尺寸检验→玻璃钢管道脱模→1.5倍工作压力水压试验及其它标准要求的检测项目→玻璃钢管道包装入库三、玻璃钢管道工艺详细说明:(1)准备工序a、设备调试。
首先认真检查设备运转及工作部位是否正常,特别要细心检查树脂-固化剂双组分泵是否有堵塞现象,之间配比是否达到设计要求;要确保制衬、缠绕、修整、脱模等设备的运行稳定和工作精度;b、清理模具。
要求模具表面无坑凹、粉尘、杂物及其他附着物,模具要作到表面平滑,有问题及时修理、维护;c、缠聚酯薄膜。
为方便管道脱模,在模具表面应包覆1层聚酯薄膜,薄膜搭接宽度1~2㎝,厚度为40um之间。
要求薄膜无破损,无皱折,两面光滑洁净。
薄膜产品质量满足GB 13950-1992的要求。
(2)制衬工序a、内衬树脂配制。
按质检部门根据当时的工作环境、温度条件作出的树脂配方体系进行内衬树脂配兑,配料量要根据制造进度合理掌握。
当现场情况发生变化时,质检部门和制造部门应及时调整配方,并按新配方配制需用的树脂;b、增强材料准备。
按设计要求将制作内衬需用的增强材料运送到指定位置,并对一些宽幅面的增强材料先裁切加工到设计宽度;c、内衬层制作。
按设计要求的铺层步骤进行内衬层制作,各单层铺设过程中应施加合理的张力,相互之间适量搭接,并用组合压辊反复滚压赶出气泡以保证纤维完全浸透。
并要求各增强材料层达到设计的树脂含量要求;d、初步自检。
按设计要求铺覆完各层后,要求操作工人进行初步的质量检测:内衬是否达到设计厚度,局部是否有贫胶、挂胶现象,是否有白斑、气泡,是否有等,若发生上述情况应及时汇报并采取处理措施;e、进入内衬远红外深度固化工序。
- 1、下载文档前请自行甄别文档内容的完整性,平台不提供额外的编辑、内容补充、找答案等附加服务。
- 2、"仅部分预览"的文档,不可在线预览部分如存在完整性等问题,可反馈申请退款(可完整预览的文档不适用该条件!)。
- 3、如文档侵犯您的权益,请联系客服反馈,我们会尽快为您处理(人工客服工作时间:9:00-18:30)。
玻璃钢生产流程工艺(一)离型剂涂擦工艺;(二)胶衣涂刷工艺;(三)糊制工艺;(四)脱模工艺;(五)切边、打磨工艺;(六)模具保养及修补工艺;(七)玻纤的剪裁工艺;(八)树脂配料工艺;(九)油漆工艺工艺。
(一)离型剂涂擦工艺(1)、聚乙烯醇溶液(俗称脱模剂)1、用洗净、不掉丝的纯棉布饱浸透脱模剂,在已完成抛光及二度固态蜡擦拭作业后的作业面上,用力往复均匀地依次涂擦,使其形成膜状。
被作业面均涂一遍为一度。
2、待一度涂拭的脱模剂彻底干燥后,在被作业面上用以上方法顺向(注意:不能往复)适度地依次均匀涂拭完全,为二度涂拭。
3、三度、四度……涂拭方法与二度相同,依次类推。
作业标准:成膜完全、膜厚均匀、无杂质、无灰尘、无粘连。
作业目的:使被作业面形成一层聚乙烯醇薄膜,以利于脱模。
作业要点:1、涂擦必须均匀、全面。
2、成膜必须全面、无漏点、网状。
注意事项:1、材料选择要便于操作,根据气候环境等实际情况用清水稀释脱模剂。
2、环境、容器、擦拭布必须清洁无尘。
3、角度擦拭须在30分钟内干燥,如不干燥须采用人工催干,以免长时间不干造成落尘。
4、胶衣涂刷须在脱模剂干燥后20分钟内施工。
(2)、固体离型剂(脱模蜡)1、涂蜡:用纯棉柔性织物沾取适量蜡,用力以旋转形式依次对作业面进行涂拭,使蜡能均匀地渗入作业面的微孔中。
2、擦蜡:涂拭蜡层后的作业面经5—20分钟的干燥即用干净的纯棉或纯毛织物对其进行往复擦拭,直到被作业面清晰、光亮、无蜡痕为止。
此为一度。
3、二度、三度……上蜡。
以重复以上作业进行,以此类推。
4、新模具或重新保养过的模具,首制产品的生产,上蜡必须五遍以上,并用液态脱模剂二度,以确保脱模顺利。
5、首制产品,应没脱模一次,擦蜡一次。
二、三次顺利脱模后,视脱模难易程度,可适当脱二、三次擦蜡一次。
作业标准:表面光洁、无蜡痕、脱模无粘模现象。
作业目的:使蜡能均匀粘附在模具表面,形成一层隔离膜。
作业要点:1、不得漏涂、漏擦或涂蜡过度。
2、擦蜡必须彻底,不留蜡痕。
注意事项:1、擦蜡布必须清洁干净,使用过的须随时清洗。
2、脱模蜡使用完毕须立即盖紧密封,以防止时间长敞口干燥。
(二)胶衣涂刷作业流程一、准备:1、根据产品的技术要求,选用相应的主辅材料及施工工艺。
2、配制彩色胶衣:取无色胶衣100份、颜料糊2-15份,混合后顺向、逆向交叉搅拌,使其混合充分。
搅拌过程中,应将容器四周及底部的胶衣不断向中间翻动,使其不留有未曾搅拌的死角;然后提起搅拌器械,查看流淌面的透光性,以较宽部分不透光为宜。
(实际效果为约0.4mm厚的流淌面有较好的遮盖性。
)3、检查被作业面的前一道工序的完成情况。
(如:模具摆放是否妥当、牢固;离型剂涂刷是否完好;作业现场是否可行等。
)二、配料:1、取彩色胶衣100份,根据材料特性、环境温湿度、预计施工时间等,投入0.1-4份的促进剂,充分搅拌后。
再投入1-4份的固化剂充分彻底搅拌后,即可涂刷作业。
三、涂刷:1、将完成配料的胶衣分成若干点,均布在被作业面上。
然后用毛刷初步均匀布刷分散。
2、将初步分散的胶衣用毛刷单向往复用力涂刷充分,然后涂刷方向变向90度往复涂刷至胶衣基本均匀的遮盖整个作业面。
再逐步依次单向顺刷,减少刷痕至完全覆盖;无透色点、无明显刷痕、无堆积区。
手刷胶衣厚度以0.6mm为佳。
四、喷涂:1、将配制完成的胶衣装入已完成试喷枪。
对准被作业面,由远而近、由深而浅、由难而易依次逐步喷涂,以至完全覆盖被作业面。
2、遇有凹槽或喷射死角的作业面,应先用软毛刷涂刷后再用喷枪补射。
喷涂胶衣厚度以0.4mm为佳。
喷枪与作业面距离为35-50cm,压力为4P。
压缩空气应清洁无水。
作业标准:1、涂刷中应无漏点、无透光点、少刷痕、无积料、固化时间合理。
2、涂刷要重、用力充分、均匀;顺刷要两头轻中间重,即下刷和收刷要轻,中途运刷要重。
3、喷涂胶衣一定要十分注意胶衣的清洁度及胶凝时间的控制,以免出现中途堵枪事故。
注意事项:1、胶衣选择要正确,称量要精确,配比要合理,遮盖率要高。
2、被作业面、容器、搅拌器要清洁。
3、喷涂作业要穿戴防护用具,合理选用喷涂气源。
1、在有胶衣的作业面上进行层糊施工,就在胶衣胶凝后0.5-24小时内完成层糊作业。
2、胶凝后的胶衣能否进行层糊作业。
应检查胶衣胶凝是否充分。
一般为:两手指按一下不重要部位的胶衣面,感到有粘联感,但不粘在后上,并略有结实感,即可施工作业。
施工前应检查作业面,如发现有胶衣透色或现象,应及时用同色胶衣进行补刷,方可进行层糊作业。
3、层糊作业的树脂胶凝时间,应控制在30-60分钟。
一般应在完成后20分钟胶凝。
时间过长容易引起胶衣皱皮现象。
4、层糊作业应选择纤维较浅或排列不规则易浸渍的织物,一般为0.18布、表面毡或300g短切纤维毡。
5、铺覆玻纤前,应在作业面上涂一层配制好的树脂,然后整齐、平服地铺覆玻纤织物;再用毛刷或滚筒将其压紧、压实。
并用树脂充分浸渍,完全彻底排除吊空部位及气泡。
形胶复杂及高低不平的部位可采用45度斜条或塞丝和填料等方法解决吊空现象,也可用剪刀切断部分纤维解决上述情况。
6、玻纤织物的铺覆,一定要平整、服帖。
铺覆时,先用力将织物绷紧,准确地轻轻放下,然后用毛刷从织物中心向四周慢慢地轻柔地成放射状——刷平,再进行上胶、浸渍。
7、浸渍施工中,应注意树脂不能过多,因为多余的树脂使织物浮在表面,不易排除气泡,给施工带来不便。
特别是低洼处应及时用毛刷将多余的树脂从积余处吸出,移为它用。
另外,树脂富余层也给积层作业带来不利,降低后续作业的层面粘接强度和产品的物理性能。
注意事项:1、层糊作业应完全杜空泡现象。
如出现空泡,应待树脂胶凝后,立即用力将其挑开,进行注胶补救。
2、层糊作业完成后的表面,应平整、光顺、无毛刺、无空泡、无余料、无漏渍。
作业标准:无空泡、无富树脂层、表面平整、无毛刺、浸渍完全、无漏糊处。
二、积层:1、待层糊作业面胶凝后,即可进行积层作业。
作业前应首先检查层糊作业的质量情况,如发现问题,应采取相应措施,解决隐患后,方可施工。
2、施工前,应用粗砂纸将毛刺及腊层排除,并用吹尘枪或毛刷掸去杂质。
3、积层用首层织物,应与层糊用材相同。
一般采用短切纤维毡。
4、在经过处理达到施工要求的作业面上刷上配制合理的树脂,然后铺上一层织物,将其从中间向四周或由上而下铺平、压实、排除吊空及气泡,并浸渍完全。
5、在以上作业完成后,连续进行织物的累积铺覆糊制。
直至达到产品的设计要求。
注意事项:Ⅰ、积层作业每层作业不超过1mm;每次作业,累积厚度不得超过5mm。
Ⅱ、积层作业必须100%完全彻底的浸渍,杜绝树脂余料。
6、积层施工中玻纤搭接作业面不得少于50mm,受力产品及运动产品不少于10mm。
平接作业,应交叉铺层,交叉层不得少于3层。
7、搭接作业中的搭接区域应尽量避免在同一位置,以免积层过厚。
8、局部区域需加强或旋转肋骨的产品,应严格按设计要求施工,局部加强原则上应在铺层中进行、9、胶架糊制应考虑粘接强度。
施工中应尽量与主体增加粘接面积。
10、胶接作业的主体是增加粘接强度。
因此,作业前应检查作业面的作业条件:1、清除毛刺及铺层;2、作业面应尽量平整,合缝并固定牢固;3、控制胶凝时间,不得发生流胶现象。
作业标准:1、用木锤或橡胶锤从模具四周沿口起,至整个模具的可击部分,自然敲击。
不得猛敲及用金属锤敲击,以免击伤模具。
2、用圆口起子,插入产品与模具的结合部四周,使其分离。
二、气压法:1、在模具最底处(离脱模口最远处),打一个5mm的孔,糊制产品前用胶带将其封住,以免树脂灌入,使之无法使用。
2、在产品固化后2小时,用圆头充插入充气孔中,轻轻敲击,将充气孔周围的产品与模具首先剥离;3、将高压空气用吹尘枪冲入产品与模具之间,并从外部轻轻锤击,使高压空气在冲击作用下,不断扩张,以达到脱模的目的。
4、充气前,应首先清除沿口四周模具与产品的粘接部分。
三、注水法(限于五面封闭的产品):1、用起子沿模具口四周逐一剥离产品。
2、用斜锲使模具与产品产生一个区域剥离口。
3、沿剥离口注入清水。
边注边用木锤轻轻顺注水口向前延伸敲击,使水在振动下不断扩张至整个模具。
4、产品脱离后,立即清除模具积水,并用布擦干,备用。
四。
锲涨法(限有法兰边及有开口支撑平面的产品):1、用起子插入产品法兰边四周,使其与模具部分产生剥离口。
2、用斜锲插入剥离口,并用木锤轻轻敲击产品四周。
产生振动,使其剥离。
4、斜锲的切入点要选择产品与模具的共同受力点上,否则效果不明显。
注意事项:1、脱模时,应十分小心每一个动作,避免将产品或模具损坏。
2、严禁用任何带利口的硬质器具参与脱模作业,以免造成损伤。
3、严禁强力脱模、野蛮作业。
作业标准:产品及模具无损伤。
(五)切边、打磨作业流程(1)切边一、软切法:1、在作业完成胶凝,进入固化阶段初期(即FRP已产生刚性,尚未完全强硬的短期内)用事先准备好的锋利的单边锋铡刀或侧刀等利刃,沿模具法兰边内侧,向外侧前方用力推进,切下多余溢边。
注意事项:1、掌握好时间,过早将产生脱层及切割不清的现象;过迟则切不动,无法施工。
2、糊制作业应完全彻底将边缘部分浸渍,并压紧、坚实。
3、掌握好切边角度,一定要由内侧向外侧前方用力,并保持刀的刃口与法兰边沿口平行。
4、注意姿势。
右手握刀,左手提起被切下的溢边,并保持左手臂应高于刀口上方10cm。
5、工作必须固定摆放牢固,以免经不起失去而摆动。
二、硬切法1、在需作业的工件上划出清晰的切割线。
2、用双手操纵Ф100的电动切割机,沿切割线切下溢边的直线部分。
3、用曲线?沿切割线割下曲线部分。
4、溢边零乱或者较?的溢边,应先割去妨碍作业的部分,再进行以上作业。
注意事项:1、检查施工机械是否安全可靠,工具选用是否合理。
2、工件摆放是否安全、牢固、排尘措施采用是否得当。
作业标准:边缘线光顺、平直、打磨区平整、均匀,产品无损伤。
(2)打磨一、手工打磨:根据技术要求,选用相应的磨料,将相应衬块包起,在被作业面上来回往复活动,不断??,改变作业面,逐一延伸。
注意事项:1、正确选用磨料及衬块。
2、打磨时应执行先高后低,先难后易的原则。
二、机械打磨:1、用角向砂轮机,装配相应的砂磨片,在被作业面上,往复运动,并不断改变作业面,逐一延伸。
2、用气动振磨机作业时,应用力适当,移动缓慢,不停检查被作业面的磨砂情况,及时调整砂磨区域。
注意事项:采用防尘措施。
作业标准:作业面无手感凹凸,不平度小于1%。
(3)研磨、抛光一、水研磨:根据技术要求,选用砂纸及相应开关的衬块,在被作业面上用水浸渍后,往复运动,并不断改变作业区域。
注意事项:1、使用清洁、干净、无泥沙杂质的水。
2、每次更换标号砂纸前,应清洗掉上一标号砂纸留下的残余砂粒。
3、研磨作业要均匀进行。
避免研磨过度或硬度不足的现象。