(完整版)小方坯连铸拉矫机控制系统设计毕业设计
毕业设计指导书连铸车间设计
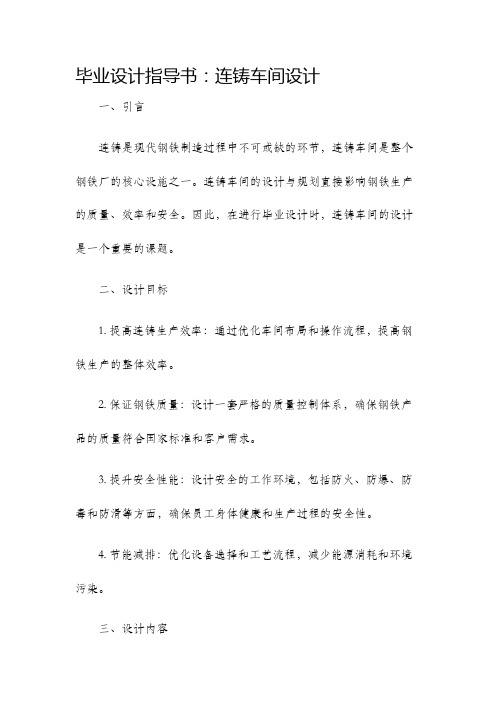
毕业设计指导书:连铸车间设计一、引言连铸是现代钢铁制造过程中不可或缺的环节,连铸车间是整个钢铁厂的核心设施之一。
连铸车间的设计与规划直接影响钢铁生产的质量、效率和安全。
因此,在进行毕业设计时,连铸车间的设计是一个重要的课题。
二、设计目标1. 提高连铸生产效率:通过优化车间布局和操作流程,提高钢铁生产的整体效率。
2. 保证钢铁质量:设计一套严格的质量控制体系,确保钢铁产品的质量符合国家标准和客户需求。
3. 提升安全性能:设计安全的工作环境,包括防火、防爆、防毒和防滑等方面,确保员工身体健康和生产过程的安全性。
4. 节能减排:优化设备选择和工艺流程,减少能源消耗和环境污染。
三、设计内容1. 连铸机布局:根据钢铁生产能力和市场需求确定连铸机的数量和类型,并合理安排连铸机的布局,以提高生产效率。
2. 冷却设备设计:设计一套高效的冷却设备系统,以确保连铸过程中钢水的快速冷却,使得钢铁产品具有理想的结晶组织。
3. 钢包设计:设计合理的钢包结构和钢包维护系统,确保钢水的顺利过渡和保持稳定的温度。
4. 水处理设备:设计适用于连铸车间的水处理设备,包括废水处理和循环水处理,以保护环境并节约水资源。
5. 环境控制:确保车间内的温度、湿度和清洁度达到要求,保证钢铁生产的稳定性和产品质量。
6. 周边设施:考虑到员工的工作环境和生活需求,设计合理的办公区、员工休息区、更衣室等周边设施。
四、设计方法1. 研究现有连铸车间的设计案例和经验,了解行业发展趋势和技术创新。
2. 布置车间:根据设备尺寸、工艺流程和人员活动等因素,对车间进行布局规划,遵循人机工程学原理。
3. 控制系统设计:设计合理的自动化控制系统,包括数据采集、监控和调控等方面,提高生产效率和质量控制水平。
4. 设备选择:根据连铸车间的生产能力、钢铁种类和产品要求,选择合适的连铸机、冷却设备、钢包等设备。
5. 安全设计:根据相关标准和法规,设计合理的安全措施,保障员工的人身安全和生产过程的安全性。
毕业设计指导书连铸车间设计

毕业设计指导书:连铸车间设计一、引言连铸车间作为钢铁生产过程中至关重要的环节,其设计直接关系到生产效率和产品质量。
本文旨在对连铸车间的设计进行指导,以确保其功能完备、安全高效。
首先,我们将介绍连铸工艺流程和其在钢铁生产中的重要性。
然后,我们将讨论连铸车间设计的基本原则和注意事项。
最后,我们将给出几个实用的设计建议。
二、连铸工艺流程1. 连铸工艺流程的基本原理连铸(Continuous Casting)是一种将钢水连续倾注到铸机中,并通过一系列工艺步骤将其冷却凝固成坯料的工艺。
该工艺相较于传统的离散式铸造具有许多优点,如高效率、节能、减少不良品产生率等。
2. 连铸工艺流程的步骤连铸工艺流程主要包括以下几个步骤:(1)钢水倾注:将冶炼好的钢水通过铸机倾注到浇注罐中。
(2)结晶器冷却:通过冷却水冷却结晶器,使钢水在结晶器中凝固成坯料。
(3)出坯:将凝固完成的坯料连续从结晶器中取出。
(4)切割:根据需要将连铸坯切割成合适的长度。
(5)过热处理:对切割后的连铸坯进行过热处理,以提高其应变能力。
(6)尺寸修整:对过热处理后的连铸坯进行尺寸修整,达到产品要求。
三、连铸车间设计的基本原则1. 安全性连铸车间工作环境应具备良好的安全性,包括防火、防爆、通风和紧急疏散设施等。
熟悉并遵守相关的安全操作规程和流程,有效减少事故的发生。
2. 空间布局合理的空间布局是连铸车间设计的关键。
要确保设备之间的间距足够,以便操作人员轻松进出及维修设备。
同时,为保证作业人员的视野和通道的畅通,需适当安排设备的位置。
3. 噪音和防护连铸车间通常会产生噪音,因此需要合理设计消声设备,降低噪音对工人的影响。
另外,还需设置适当的防护设施,如安全带、安全栏杆等,确保工人的人身安全。
4. 运输和搬运设备连铸车间需要合理规划运输和搬运设备,以保证钢坯的顺利流动。
需要考虑到设备的数量、容量和布局,使得整个运输和搬运过程高效可靠。
5. 环境保护钢铁生产过程中产生的废气、废水等污染物需要进行合理的收集和处理,以避免对环境造成污染。
机械毕业设计(论文)-板坯连铸横移机设计【全套图纸】

Keywords: continuous casting, improved, the quality of the slab, the slab
transverse moving
III
目录
1.绪论............................................................................................................................. 1 1.1 连铸发展历史简介.......................................................................................... 1 1.2 连铸及连铸机简介.......................................................................................... 1 1.2.1 连铸机的组成..................................................................................... 1 1.2.2 连铸工艺概述..................................................................................... 2 1.2 板坯连铸工艺流程图............................................................................. 3 1.3 连铸技术的优越特性...................................................................................... 4 1.4 鞍钢连铸技术的概况...................................................................................... 5 1.5 设计对象.......................................................................................................... 6
年产400万吨合格连铸坯的连铸系统设计(可编辑)

年产400万吨合格连铸坯的连铸系统设计高等职业技术学院毕业设计说明书设计题目:年产400万吨合格连铸坯的连铸系统设计学号:_________________________姓名:_________________________专业班级:_________________________2012年06月日摘要本次设计的是年产400万吨钢的方坯连铸工程,主要对连铸生产的工艺流程、车间组成和工艺布置进行设计,并对连铸机的几个主要工艺设备:钢包及其运载设备、中间包及其运载设备、结晶器及振动装置、拉矫和引锭装置、切割装置进行了设计计算。
设计中对板坯连铸车间作了综合经济指标分析和合理的布局。
并绘制了车间平面和设备图。
为了提高连铸机生产率和提高产品质量,在设计中采用了一些新技术。
设计中选用弧型连铸机,大容量和深熔池的中间包,结晶器漏钢预报技术,电磁搅拌技术和轻压下技术等,使以上生产方案具有科学性、先进性,经济合理,适应当前社会发展的需要。
目录- 1 -高等职业技术学院 - 1 -毕业设计说明书- 1 -摘要- 1 -1 文献综述 11.1 连铸主要设备 31.1.1 大包回转台 41.1.2 中间包车 41.1.3 中间包烘烤装置51.1.4 二冷室及风机 51.1.5 结晶器 51.2 车间设计的依据71.3 厂址选择72 设计方案82.1连铸机型的选择和特点82.1.1连铸机设计原则 82.1.2连铸机机型的选择原则8 2.1.3连铸机机型的确定82.2产品规模82.2.1产品方案82.2.2钢水供应条件92.2.3生产规模103连铸车间的平面布置 103.1主要工艺参数的确定103.1.1拉速的确定103.1.2冶金长度的计算: 113.1.3作业率的确定113.1.4钢包允许的最大浇注时间123.1.5连铸机流数的确定123.2连铸机生产能力的计算133.2.1连铸机与转炉的匹配计算133.2.2连铸机生产能力计算134生产工艺流程及车间组成154.1生产工艺流程图154.2车间组成及工艺布置164.2.1车间组成164.2.2车间工艺布置164.2.3连铸机区域的主要尺寸175主要工艺设备选择及其主要技术性能参数19 5.1连铸机长度的确定 195.2连铸机弧形半径195.3钢包及钢包运载设备205.3.1钢包回转台205.3.2钢包尺寸、质量和中心的计算205.4中间包及其运载设备235.4.1中间包容量的确定235.4.2中间包的类型构造及其主要尺寸 235.5结晶器及振动装置 255.5.1结晶器尺寸的确定255.5.2结晶器的振动机构275.5.3结晶器的类型285.6二次冷却系统295.6.1二冷区的设计305.6.2二冷段冷却区的划分315.7拉矫装置315.8铸坯切割区的设计 32参考文献35致谢361 文献综述亨利?贝塞麦是提出连铸思想的第一人。
小方坯连铸机拉矫机驱动系统改造

d o i : 1 0. 1 3 6 3 0 / j . c n k i . 1 3—1 1 7 2. 2 0 1 4 . 0 71 8
REFORM ATI ON OF DRⅣ E S YS TEM OF S TRETCHI NG S TRAI GHTENRE I N BI LLET CAS TER
Cu i Gu a n g y u
( No . 2 S t e e l Ro l l i n g Mi l l ,Xu a n h u a I r o n a n d S t e e l Co mp a n y,He b e i I r o n a n d S t e e l Gr o u p,Xu a n h u a ,He b e i ,
0 7 5 1 0 0)
Ab s t r a c t :I t i s i n t r o d uc e d t h e p r ob l e ms o f d r i ve s y s t e m o f s t r e t c h i ng s t r a i g ht e n e r o f 1 2 f l o w bi l l e t c a s t e r i n p r od u c t i o n i n No. 2 St e e l Ro l l i ng Mi l l of Xu a n St e e 1 . Ba s e d o n t h e a n a l ys i s a b o ut t he r e a s o n o f d a ma g e o f e — q ui p me n t ,t h e r e f o r ma t i o n pl a n i s s e t t l e d o u t:a dd i ng wa t e r— r e s i s t a nc e f o r i n p ut a x i s,i n c r e a s i n g a hi gh— l o — c a t i o n o i l c u p i n r e d u c t i o n bo x a nd l owe r i n g wo r k e n vi r on me n t t e mp e r a t u r e.A f t e r i t c a  ̄i e d ou t ,t h e wo r k l i f e
银山前区5 #方坯连铸机自动化控制系统的设计和实现

Z a gJa g n h n in a g W u Z a c e g Wa gYa h oh n n n
中 出现 的 问题 进行 了控 制措 施 的 改进 。
关键词 :方坯连铸机
Th sg fAu o t n r lS se o h . i e se n t m p e e t t n eDe in o t mai Co to y t m ft e No 5 B l tCa t ra d i I lm n ai c l s o
张建 刚。等 :银山前区 5方坯连铸机自动化控制系统的设计和实现 PC L ,并通过 WI C N C画面在主控室 M I M 上显示 出
一
第6 ( 期 总第 16 ) 2期
D P网进行来 自系统之电气控制部分 ,均通过大 包 回转台中间的一套滑环装置来实现 。
两个 中间罐车均采用变频控制 ,车上装有 4个
控制系统外 围还采用 了各类 传感器 、光 电感应 限 位 ,红外线感应控制 自动摄像定尺切割系统、位置 传感器等,所有信号全部送入 P C进行集 中控制 。 L 整个控制系统见图 1 。
一
升降液压缸和称重装置 ,两车均采用轻轨行走 ,当 个中间包工作时 , 一个 中间包 可作烤 包准备 另
4 ~ 氧压机的润滑油 系统多数连接部位均有 不 同程度 的渗、漏油现象 ,虽然经过多方努力 ,此 问题仍没有得到妥善的解决 ,只得采用不断擦拭的
Get清风毕业设计 年产200万吨小方坯炼钢连铸系统设计

毕业设计--- 年产200万吨小方坯炼钢-连铸系统设计内蒙古科技大学本科生毕业设计说明书题目:学生姓名:学号:专业:班级:指导教师:目录摘要ABSTRACT第一章文献综述国内外炼钢及连铸的开展概况第二章炼钢厂生产规模及产品方案确定第三章炼钢车间设计方案第四章金属平衡计算炼钢厂的物料平衡计算第五章炼钢设备选型及技术性能第六章连铸机主要设计决定、特点和规划第七章连铸机主要工艺参数7.2 连铸机生产能力确实定第八章连铸机主要设备的选择8.1 钢包及钢包载运设备8.2 中间包及其载运设备8.4 二冷区设计8.5 拉矫和引锭装置8.6 铸坯切割装置8.7 辊列设计及后步工序其它设备第九章连铸系统工艺布置及主要流程9.1 主要流程9.2 连铸系统工艺布置第十章环境保护与平安卫生设计第十一章投资估算及技术经济分析概述年产200万吨小方坯炼钢-连铸系统设计摘要连铸技术比传统的铸造技术有着很高的优越性,使得其在现代钢铁工业中占据着不可替代的位置。
本设计为年产200万吨小方坯炼钢-连铸系统,主要内容包括生产规模及产品方案确定、炼钢车间工艺布置、主要流程及工艺技术特点、金属平衡计算、主要设备选型及技术性能、环境保护与平安卫生、投资估计及技术经济分析概述。
设计过程中本着投资省、经济效益佳、多品种、高质量、生产平安、操作顺利、维修方便和符合国家产业政策的原那么,对连铸机工艺参数、设备参数以及设备的选择进行了详细的计算和说明。
设计中充分借鉴了国内外先进企业生产经验,并参阅了相关文献资料,采用了一些先进、可靠、适用、经济的技术和先进设备,而且明确阐述了所选用生产设备的原那么、优点和相应技术特点。
为顺应国家提出的节能减排、环保及劳动平安方面的要求,设计中对连铸车间的环境保护、劳动平安采取了有利措施,同时对该连铸系统投资和技术经济进行了分析。
本连铸机是具有高拉速、高生产率及生产高质量铸坯的高效连铸机,因此该连铸机适合当前社会开展的需要。
0008 方坯小矩形坯圆坯连铸机自动控制说明

方坯小矩形坯圆坯连铸机自动控制说明1.连铸机工艺流程:连铸机浇注前,先进行上引锭操作。
在确保液压站正常工作的前提下可进行送引锭操作:首先拔出防止引锭杆下滑的定位销子,确认销子拔到位以后送引锭,拉矫辊和脱锭辊会自动抬起经10秒延时后引锭存放电机启动,送引锭杆入拉矫机拉矫上辊下,当引锭杆送达拉矫机下时,引锭杆停止,跟踪位灯点亮,拉矫辊自动压下且一压压紧,10秒后,确保一压完成,引锭电机和拉矫机同时启动并保持线速度一致。
开始送引锭至结晶器下口。
当引锭杆送至结晶器下1000mm左右时,停止送引锭。
拉矫台的操作权交给结晶器操作箱,由机旁箱的按钮盒点动按钮把引锭杆送入结晶器内,送引锭过程完成。
经过预热的中间包由位于浇注平台一侧的中间包车运行至结晶器上方,通过中间包车上的对中机构对位。
合格钢水由出钢跨吊车吊运至钢包回转台上,操作工在钢包操作台上操作转台,钢包回转台经转动、减速、停止,回转180°后,钢包置于中间包上方。
操作工开启钢包滑动水口,钢水进入中间包;待中间包钢水液位达到一定高度后,加入保温剂,打开定径水口,开始浇注;钢水液位在结晶器内上升,当钢水液位达到一定高度时,启动结晶器振动装置和拉矫机,拉坯开始,二冷水阀门打开,对铸坯进行二次冷却。
当引锭杆头部到拉坯辊,存放电机慢速启动,此时电气控制使拉矫机的速度不能低于存放电机速度,延时,拉坯辊压力由引锭杆压力转为热坯压力,当引锭头出拉矫机的矫直辊时(取引锭杆尾端的行程开关信号),矫直辊以高压压力向热坯头部压下,将引锭杆与铸坯脱离,压下到位后,延时,矫直辊压力转为热坯压力。
脱离热坯后的引锭杆由存放电机继续驱动到达引锭杆存放位时,存放电机停转(取引锭杆尾端的行程开关信号),引锭杆停在存放位,等待下一次浇钢。
当铸坯头部触及定尺检测装置的吊链,发出电信号时,切割机抱夹夹紧铸坯,进行定尺切割操作,当切割机完成定尺切割操作时,该流的切割后辊道启动,同时横移区X流公用辊道启动,切断后的铸坯经切割后辊道输送至钢坯横移区前的升降档板位置。
连铸机毕业设计论文

摘要高效连铸通常定义为五高:即整个连铸坯生产过程是高拉速、高质量、高效率、高作业率、高温铸坯。
本设计的内容主要包括简单的介绍了我国及世界铸钢技术的发展轨迹及未来连铸技术的发展方向。
简单的介绍连铸机机型特点及选择使用的方法。
本设计主要是从提高连铸机拉速和提高连铸机作业率两方面着手。
从而提高连铸机设备的坚固性、可靠性和自动化水平,达到长时间的无故障在线作业,提高连铸机作业率水平。
连铸工序采用多项先进技术,使得单线布置紧凑,使产品质量、生产成本、生产效率得到了优化。
关键词:连铸机型方坯连铸铸坯质量结晶器优化AbstractEfficient continuous casting is usually defined as five high : that the entire billet production process is high speed, high quality, high efficiencyhigh operating rates. High temperature slab.The design covers the brief introduction to China and the world steel technology development path and future direction of continuous casting technology. Brief characteristics of continuous casting machine models and select the method used. This design is mainly to increase speed and improve the continuous casting machine continuous casting machine of two aspects Continuous casting machine equipment to enhance the robustness, reliability and automation level, to achieve long trouble-free online operations and increase the rate of horizontal continuous casting machine operation. Continuous casting process uses a combination of advanced technology, making single compact layout, product quality, production costs, production efficiency has been optimized.Key words:continuous casting billet Slab quality Mold Optimization第一章绪论1.1毕业设计的目的毕业设计是在机械设计与制造专业理论教学之后进行的实践性教学环节,是对所学知识的一次总检验,是走向工作岗位前的一次实战演习,其目的是:1、综合运用本专业所学课程的理论和实践知识,通过设计一个零件的外观和结构,绘制出三维立体图,完成装配图,培养和提高学生独立的工作能力。
课程设计--小方坯连铸机设计 二

课程设计--小方坯连铸机的设计一引言连铸技术是现代炼钢生产中最具有革命性的技术之一,其特点是节约能源、提高成材率和便于机械化、自动化操作,在过去的三十年中连铸技术得到了快速的发展与推广,特别是在两次世界石油危机的推动下,连铸生产规模空前扩大,涌现了许多实现全连铸的钢铁联合企业,连铸比的高低已经成为一个国家钢铁工业发展水平的标志。
随着现代工业对特殊钢、高质量钢的需求不断扩大,以及连续铸钢技术的迅速发展,对连铸工艺过程也有了更高的要求。
连续铸钢工艺从原料到成品的过程中起着关键性作用。
连铸工艺的优与劣直接影响钢产品的质量、性能和企业的经济效益。
且随着炼钢和轧钢技术的进展,钢铁工业结构的变化和对产品的规格、质量的新要求,这使得采用常规和铸锭—开坯工艺难以满足一些大型钢铁企业的生产和发展,为此,研究连铸的新工艺和新技术是必要的。
本文在阅读大量文献基础上,着重介绍了小方坯连续铸钢的发展概况、连铸机的选型,以及连铸机的工艺参数确定、设备的选型和相关参数进行了设计,并对连铸车间进行布置,使其保证连铸稳定、持续的进行。
最后本文还介绍了一些方坯连铸的新技术。
第一章绪论1.1我国方坯连铸发展的状况我国是在炼钢生产中研究、应用连铸技术较早的国家之一。
20世纪50年代中期,当连铸技术在前苏联、英国、意大利、加拿大等国进入工业性试验阶段时,我国即着手进行试验研究工作。
1956年我国在当时的重工业部钢铁综合研究所建成了直径80mm的圆坯半连铸试验装置。
1957年在上海钢铁公司中心试验室建成一台高架立式方坯连铸机;1958年在唐山钢铁厂建成了第一台工业生产的立式连铸机,同年在重庆第三钢铁厂建成投产一台两机两流,配合30t转炉,浇铸175mm×250mm矩形坯的立式连铸机。
1960年在唐山钢铁厂建成一机一流,配合5t转炉浇铸150mm×150mm小方坯的立式连铸机。
我国发展的连铸机型大多为立式连铸机,生产效率低。
板坯连铸机自动控制系统设计

本项目旨在设计一套板坯连铸机自动控制系统,以实现连铸过程的自动化、智 能化和高效化,提高生产效率和产品质量,降低生产成本和能耗,提升企业竞 争力。
设计目标与要求
设计目标
设计一套稳定、可靠、高效的板坯连铸机自动控制系统,实现连铸过程的自动化 控制,提高铸坯质量和产量。
要求
系统应具备高精度、高速度、高可靠性的控制性能,能够适应不同的生产工艺要 求;同时,系统应具备良好的人机交互界面和远程监控功能,方便操作和维护。
通讯设备
选用稳定、高速的通讯设备, 实现各控制单元之间的数据传
输和通讯。
软件功能模块划分与实现途径
数据采集与处理模块
实现对传感器数据的实时采集、处理 和分析,为控制算法提供准确的数据 支持。
控制算法模块
采用先进的控制算法,如模糊控制、 神经网络控制等,实现对铸坯的精确 控制。
顺序控制模块
根据铸坯生产工艺要求,实现对铸机 各种动作和顺序的精确控制。
03
关键技术与难点攻关
连铸机工艺流程特点分析
工艺流程概述
连铸机将液态金属连续浇铸成板坯, 涉及钢水供应、结晶器振动、二冷配 水、拉矫机拉速控制等多个环节。
工艺流程特点
关键点分析
结晶器液位控制、二冷配水模型、拉 速与温度的协同控制等是连铸机工艺 流程中的关键控制点。
高温、高速、连续性强,对设备精度 和控制稳定性要求高。
故障诊断与处理模块
实现对铸机各部件的实时监测和故障 诊断,及时发现并处理故障,保障铸 机稳定运行。
通讯网络布局规划及协议选择
网络布局规划
根据铸机控制要求和现场环境,合理规划通讯网络布局,确 保数据传输的稳定性和可靠性。
通讯协议选择
连铸机自动控制系统设计
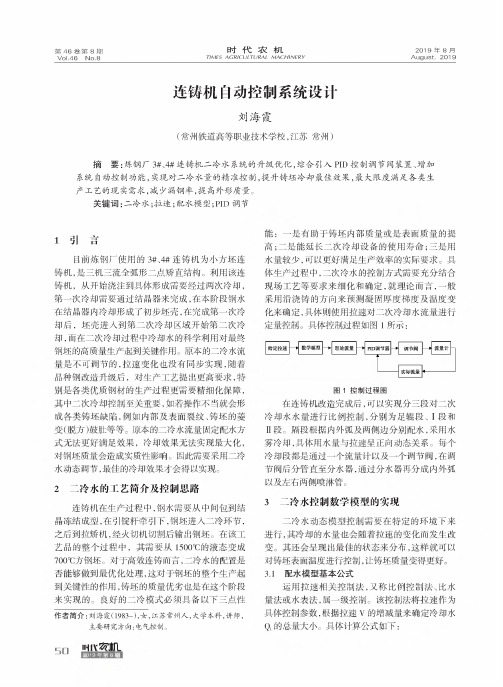
连铸机自动控制系统设计刘海霞(常州铁道高等职业技术学校,江苏常州)摘要:炼钢厂3#、4#连铸机二冷水系统的升级优化,综合引入PID控制调节阀装置、增加系统自动控制功能,实现对二冷水量的精准控制,提升铸坯冷却最佳效果,最大限度满足各类生产工艺的现实需求,减少漏钢率,提高外形质量。
关键词:二冷水;拉速;配水模型;PID调节1引言目前炼钢厂使用的3#、4#连铸机为小方坯连铸机,是三机三流全弧形二点矫直结构。
利用该连铸机,从开始浇注到具体形成需要经过两次冷却,第一次冷却需要通过结晶器来完成,在本阶段钢水在结晶器内冷却形成了初步坯壳,在完成第一次冷却后,坯壳进入到第二次冷却区域开始第二次冷却,而在二次冷却过程中冷却水的科学利用对最终钢坯的高质到用。
本的二冷水流是的,没有同步实现,随着种钢后,对高要,是质钢的过程需要,中二次冷却要,形成铸坯,内、铸坯的方等等本的二冷水流水方,冷却实现最,对钢坯质成实质需要采用二冷水,最佳的冷却实现。
2二冷水的工艺简介及控制思路连铸机在过程中,钢水需要从中到结晶结成,在,钢坯进入二冷,后到矫机,经机后钢坯在该艺品的过程中,需要从1500!的成700!方钢坯。
对高连铸而言,二冷水的是到最,对钢坯的到的用,铸坯的质是在阶段来实现的的二冷必须具备三点性作者简介:刘海霞(1983-),女,江苏常州人,大学本科,讲师,控制。
:一是有助于铸坯内部质量或是质量的提高;二是能延长二次冷却设备的使用寿命;三是用水较少,率的实际要具体过程中,二次冷水的方需要充分结合现场等要来和确,论而言,一般用沿浇铸的方向来预测凝厚度梯度温度来确,具体则使用对二次冷却水流量进行具体过程如图1所示:图1控制过程图在连铸机完成后,实现分三段对二次冷却水水进行比,分为辐段、I段和"段。
隔段根据内外弧两侧边分水,采用水雾冷却,具体用水与呈正向系。
每冷却段都是通过一流量计一阀,在调阀后分管直分水器,通过分水器再分成内外弧左右两侧喷淋管。
方坯连铸拉矫机液压控制系统新设计模型

方坯连铸拉矫机液压控制系统新设计模型
闫岩
【期刊名称】《设备管理与维修》
【年(卷),期】2013(000)0z2
【摘要】大方坯连铸拉矫机液压系统一种新的设计模型,解决拉矫机底部大量管网密排,施工困难与拉矫机周围大量线路布置,维护、检修困难的问题。
可以在生产过程中处理液压、电气故障,防止该流断浇,手动阀设置在阀架上,电气元件布置在两边走台,改善了工作环境。
【总页数】2页(P117-118)
【作者】闫岩
【作者单位】四川省攀枝花新钢钒维检中心四川攀枝花市
【正文语种】中文
【中图分类】TF341.6
【相关文献】
1.小方坯连铸机液压控制系统分析
2.方坯连铸拉矫机液压系统设计与分析
3.方坯连铸机液压控制系统剖析
4.变频器在方坯连铸机拉矫机驱动控制系统的应用
5.大方坯连铸机拉矫机控制系统优化
因版权原因,仅展示原文概要,查看原文内容请购买。
- 1、下载文档前请自行甄别文档内容的完整性,平台不提供额外的编辑、内容补充、找答案等附加服务。
- 2、"仅部分预览"的文档,不可在线预览部分如存在完整性等问题,可反馈申请退款(可完整预览的文档不适用该条件!)。
- 3、如文档侵犯您的权益,请联系客服反馈,我们会尽快为您处理(人工客服工作时间:9:00-18:30)。
毕业设计(论文)题目小方坯连铸拉矫机控制系统设计专业自动化班级电气101学生沙玉楠指导教师李好文2014 年小方坯连铸拉矫机控制系统设计专业:电气工程及其自动化班级:电气101作者:指导老师:职称:答辩日期:摘要近年来,板坯连铸机成为大型钢铁公司的主要设备,它提高了钢铁的综合成材率,降低了能源消耗,并且更容易实现机械自动化。
而小方坯连铸机则以其良好的投资回报,赢得了国营中小钢铁公司和私营钢铁企业的青睐。
拉矫机作为连铸机的核心设备,它是连铸机的指挥中心,其他设备的工作状态都必须与拉矫机相协调。
本设计的内容是通过PLC对拉矫机进行控制,完成连铸过程中送引锭、拉坯、拉尾坯三个工作流程。
其中用到两台电动机,其速度控制由变频器完成;拉矫辊的压下和抬起动作由电磁阀控制。
由S7-300PLC 模块构建控制系统,采用西门子公司的STEP7编程软件完成拉矫机控制系统梯形图的程序编制。
变频器既可以实现电机速度连续可调,也可以控制电机以固定速度运转:PLC通过0-10V或4-20M A的模拟量信号来控制变频器频率输出为0-50Hz,即可完成电机速度连续可调的控制;用几个数字量输出点控制变频器的高、中、低速,电机即可按所需的固定速度运转。
关键词:连铸拉矫机、PLC控制、梯形图、变频器AbstractIn recent years, the slab casting machine equipment of a large Steel Corp, it improves the steel finished product rate, reducing energy consumption, and easier to realize mechanical automation. While the small billet continuous casting machine with its good investment returns, won the state and Steel Corp and private iron and steel enterprises. Straightening machine as the core equipment of continuous casting machine, it is the continuous casting machine command center, other equipment working state must be coordinated with the straightening machine.The contents of this design is through the PLC to control the tension leveller, completed in the process of continuous casting, casting, feeding dummy ingots pull tail billet three working process.Which uses two motors, its speed is controlled by the inverter; pulling straightening roller pressure and lift the action is controlledby electromagnetic valve. Construction control system is composedof S7-300PLC module, the Siemens company STEP7 programming software to complete the withdrawal straightener control system trapezoidal chart programming.Frequency converter can realize a continuous and adjustable speed motor, can control the machine running at a fixed speed: PLC through the analog signal 0-10V or 4-20MA to control the inverter output frequency is 0-50Hz, to complete the control of motor speed adjustable; several digital output control frequency converter, motor, speed, can according to fixed speed required for the operation. Keywords: continuous casting machine, plc control, ladder diagram目录前言 (1)第1章绪论 (3)1.1 连铸机研究的意义 (3)1.2 国外连铸技术的发展近况 (3)1.3 我国连铸技术的发展近况 (4)1.4 小方坯连铸的发展近况 (5)第2章连铸拉矫机主要设备简介 (7)2.1 S7-300系列PLC系统特性及硬件构成 (7)2.1.1 S7-300系列PLC硬件系统 (7)2.1.2 S7-300系列PLC模块性能简介 (9)2.2 变频器简介 (10)2.2.1 概述 (10)2.2.2 基本组成 (11)2.2.3 工作原理 (11)2.3 光电开关简介 (12)第3章硬件设计 (13)3.1 PLC硬件组态及地址分配 (13)3.2 PLC系统各模块电路图 (13)3.3 变频器控制速度原理 (15)第4章 PLC梯形图程序 (16)4.1 程序流程图 (16)4.2 IO口地址分配 (18)4.3 部分梯形图程序 (20)第5章总结 (21)第一章绪论1.1 连铸机研究的意义钢铁工业在国民经济中的巨大作用,在于它能够提供一切工具和机器设备的原材料,它是现代社会生产和扩大再生产的物质基础。
从最简单的手工劳动工具直到最复杂的航天技术,没有一个工业部门不和钢铁工业发生直接和间接的关系。
而连铸机大大的提高了钢铁的生产效率,所以连铸机的研究与设计意义重大。
钢铁冶金技术发展的趋势与时代要求是高效、优质、低消耗与低排放。
连铸作为钢铁生产流程中承上启下的关键环节,是当前国家钢铁生产结构调整与技术升级战略中值得重点关注的核心环节【1】。
1.2 国外连铸技术的发展近况钢铁全连铸的实现是连铸技术成熟发展的体现。
建立在炼钢——钢水炉外处理——连铸组合优化基础上的全连铸生产体制已成为高水平现代化钢铁工业生产的综合标志。
1966年前苏联的新里别茨克钢铁厂新建了第一转炉车间,并最早开创了连铸与氧气转炉相结合的先例。
1979年,该厂又新建了第二转炉车间,并配置了弧形连铸机,使两个转炉车间实现了全连铸,年产量达到了800万吨。
但是,由于前苏联的炼钢生产一直以平炉为主,氧气转炉炼钢发展迟缓,因此,限制了连铸的发展。
70年代以后日本,德国等工业发达国家后来居上。
尤其是日本,60年代后期才从前苏联、德国等国家引进连铸技术,接着投入大量的人力物力进行消化吸收和研究开发,促进了连铸技术的应用和发展。
但是,日本在70年代前,连铸主要设置在电炉钢厂,以生产小方坯为主,大型钢铁联合企业几乎没有连铸机,因此,连铸比很低。
70年代后,经过两次能源危机,使连铸技术得到迅速的发展【2】。
法国也是开发研究连铸技术较早的国家。
但在70年代以前发展非常缓慢。
70年以后发展加快,连铸比迅速提高。
美国的连铸技术是与康卡斯特公司和日本设备制造厂家合作发展起来的。
80年代以来发展速度缓慢。
80年代以后,美国政府开始重视连铸技术的发展,首先是增加连铸投资,其次是把发展重点放在大型钢铁联合企业的板坯、大方坯及组合式连铸机的建设上,使大型钢铁联合企业的连铸比很快得到提高,从而也提高了全国的连铸比【3】。
国外连铸钢厂的特点:(1)以最少或较少的连铸机实现全连铸(2)改造旧连铸机,提高作业率。
(3)配备炉外精炼设备。
国外的全连铸钢厂都配有炉外精炼设备,这样既可以满足钢种和钢水质量要求,又可以以多炉连铸作缓冲,并且还可以进行钢水温度补偿和为挽救事故而避免将钢水回炉或冻结在钢包中。
(4)增设计算机。
增设的计算机用于生产组织、管理、调度、控制工艺过程,使各环操作处于最佳状态,减少任务的失误【4】。
1.3 国内连铸技术的发展近况近年来,我国钢铁冶金精炼技术得到大力发展,钢坯冷轧成形加工技术也取得快速发展。
作为钢材生产流程的中间环节,连铸技术的发展表现出如下几个明显特征:(1)流程紧凑。
如各类近终形铸机与常规连铸的带液芯压下和动态轻压下技术的发展与应用;(2)技术密集。
浇注与凝固、机械与液压、自动控制、过程检测与多级通讯的技术集成度大大提高。
(3)功能扩大。
钢水精炼、浇注与凝固控制、近终形、铸轧与组织控制等系统集成技术受到重视。
可以说,现代连铸技术在冶金工业中的作用与地位已愈发重要。
采用连续铸造方法,可以使全连续和自动化操作成为可能,提高了铸坯质量,减少了生产工序,降低生产成本,故在大型的钢铁企业中得到广泛地推广应用。
近年来,通过自主开发、跟踪转化以及联台设计,国内连铸设计水平取得了较大的进步。
尤其是些先进的单体技术装备设计基本都实现了国产化,如结晶器液面控制、自动下渣监测、电磁搅拌(箱式与辊式)、漏钢预报、动态配水、动态轻压下、质量跟踪与判定等。
整体装备水平以及性能的稳定性还有待提高。
我国冶金企业投放的技改资金比较大,新上项目较多,连铸项目也较多。
但先进铸机设备和技术还是多习惯于引进,其中我国薄板坯连铸连轧已经引进了10多条生产线。
自2000年,我国先后全部引进或引进核心部位设备与技术的常规扳坯连铸机共有24台27流。
还有继续引进的趋势:中薄板坯连铸机、异型坯连铸机几乎全部引进。
大方坯连铸机也有引进的倾向。
此外,国内新上的高规格铸机多采用国外知名连铸商(VAI、DANIELI、CONCAST、SMS德马克等)和国内设计单位联合设计。
实际上,国内合作单位主要工作为利润很少的详细设计,一些关键装备的制造也由国外公司所控制。
这种局面促进了国内相关技术水平的提高,但不利于自主知识产权品牌的应用与提升。
可喜的是,随着国内设计水平的提高,尤其是新技术开发及其成熟度的提高,加之投资和后期维护成本优势,一些钢铁生产用户开始陆续使用全套国产装置,铸机配置水平也逐渐提高。