炼铁炼钢工艺流程
炼钢生产过程以及流程图详解(全)
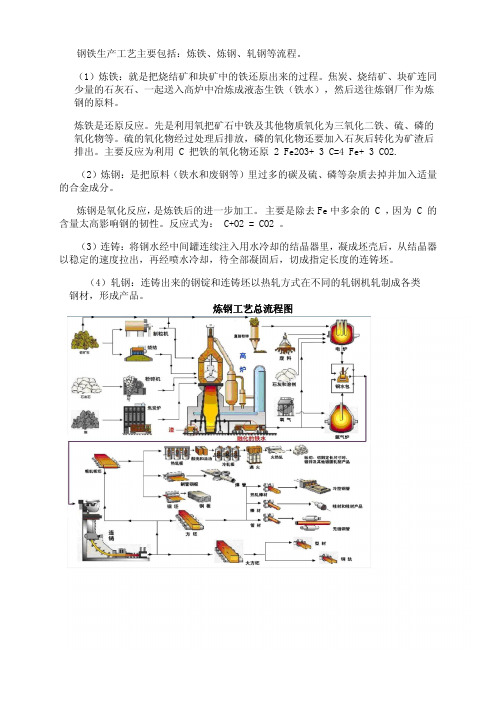
钢铁生产工艺主要包括:炼铁、炼钢、轧钢等流程。
(1)炼铁:就是把烧结矿和块矿中的铁还原出来的过程。
焦炭、烧结矿、块矿连同少量的石灰石、一起送入高炉中冶炼成液态生铁(铁水),然后送往炼钢厂作为炼钢的原料。
炼铁是还原反应。
先是利用氧把矿石中铁及其他物质氧化为三氧化二铁、硫、磷的氧化物等。
硫的氧化物经过处理后排放,磷的氧化物还要加入石灰后转化为矿渣后排出。
主要反应为利用 C 把铁的氧化物还原 2 Fe2O3+ 3 C=4 Fe+ 3 CO2.(2)炼钢:是把原料(铁水和废钢等)里过多的碳及硫、磷等杂质去掉并加入适量的合金成分。
炼钢是氧化反应,是炼铁后的进一步加工。
主要是除去Fe中多余的 C ,因为 C 的含量太高影响钢的韧性。
反应式为: C+O2 = CO2 。
(3)连铸:将钢水经中间罐连续注入用水冷却的结晶器里,凝成坯壳后,从结晶器以稳定的速度拉出,再经喷水冷却,待全部凝固后,切成指定长度的连铸坯。
(4)轧钢:连铸出来的钢锭和连铸坯以热轧方式在不同的轧钢机轧制成各类 钢材,形成产品。
炼钢工艺总流程图炼焦生产流程:炼焦作业是将焦煤经混合,破碎后加入炼焦炉内经干馏后产生热焦碳及粗焦炉气之制程。
烧结生产流程:烧结作业系将粉铁矿,各类助熔剂及细焦炭经由混拌、造粒后,经由布料系统加入烧结机,由点火炉点燃细焦炭,经由抽气风车抽风完成烧结反应,高热之烧结矿经破碎冷却、筛选后,送往高炉作为冶炼铁水之主要原料。
还原气体,还原铁矿石,产生熔融铁水与熔渣之炼铁制程。
转炉生产流程:炼钢厂先将熔铣送前处理站作脱硫脱磷处理,经转炉吹炼后,再依订单钢种特性及品质需求,送二次精炼处理站(RH真空脱气处理站、Ladle Injection盛桶吹射处理站、VOD真空吹氧脱碳处理站、STN搅拌站等)进行各种处理,调整钢液成份,最后送大钢胚及扁钢胚连续铸造机,浇铸成红热钢胚半成品,经检验、研磨或烧除表面缺陷,或直接送下游轧制成条钢、线材、钢板、钢卷及钢片等成品。
炼铁炼钢工艺流程

炼铁炼钢工艺流程炼铁炼钢是冶金工艺中的重要环节,通过对铁矿石的提炼和精炼,最终获得高质量的钢铁产品。
下面将详细介绍炼铁炼钢的工艺流程。
一、炼铁工艺流程1. 副矿材料预处理:将收集的副矿材料经过破碎、筛分、磁选等工序处理,去除杂质,得到纯净的副矿材料。
2. 铁矿石处理:将铁矿石破碎、浸泡于水中,去除表面的杂质,然后经过磁力分离、重力选矿等工序,将铁矿石中的有用成分提取出来。
3. 炼铁炉炼炉:将提取的铁矿石与焦炭、石灰石等原料混合,投入高炉中进行炼制。
高炉内温度达到1500℃以上,矿石中的铁含量经过还原反应被提取出来,形成生铁。
4. 生铁处理:将炼出的生铁经过浇铸或炼钢炉炉处理,去除其中的硫、磷等杂质,得到优质的铁合金。
二、炼钢工艺流程1. 炼钢炉前处理:将铁合金破碎、筛分,去除其中的杂质,得到纯净的铁合金。
2. 炼钢炉炼炉:将铁合金与适量的废钢、废铁加入炼钢炉中,进行炼制。
炼钢炉内温度高达1600℃以上,通过氧气吹吹炼,使废钢等物质被氧化,产生大量热,达到熔化的目的。
3. 炼钢炉后处理:炼钢完成后,钢水需要进行过滤、脱硫等处理,以去除其中的杂质。
此外,还需要根据不同的需求,添加适量的合金等元素,调整钢的成分和性能。
4. 连铸成型:将经过处理的钢水注入到连铸机中,通过涡轮旋转或摇摆,使钢水冷却凝固,形成钢坯。
钢坯可进一步进行轧制、锻造等加工,制成不同形状的钢材。
以上就是炼铁炼钢的工艺流程。
通过这个过程,铁矿石和副矿材料得到了有效的利用,矿石中的铁成分被提取出来,并经过加工得到高质量的钢材。
这个工艺流程不仅具有广泛的应用价值,还在很大程度上推动了工业化的进程。
炼钢工艺流程

炼钢工艺流程
炼钢工艺主要由选矿、烧结、炼铁、连铸及其他相关工艺组成,下文将对每个工艺进行详细分析讨论。
首先,选矿。
选矿是将原料矿石提纯为炼钢所需的铁矿石,在此过程中,铁矿石的比例必须保持在一定的范围内,在选矿工艺中,除开除杂、分离稀碱土等矿产加工外,还包括批次检验和最终评定矿石品质等程序。
其次,烧结。
烧结在选矿入料之后,炼钢厂进行烧结制备要加工的原料,在此过程中,原料经过施加一定压力的均匀加热,使原料中的物质发生变化,从而产生固态的铁矿粉,在这一工艺过程中,会减少后续运输的时间。
接着,炼铁。
炼铁是将烧结的固态铁矿粉及补充的碳素料放入反应炉内,经过一系列炉次操作,完成氧化物消除,使碳、氧及其他合金元素发生变化,得以制成铁液,炼铁工艺采用了大量的新技术及先进工艺,如斜顶轰击、差压鼓风等,以降低能耗及提高铁液的品质。
而后,连铸。
连铸特指将铁液倾泻至铸型中快速冷却,使其在短
时间内凝固成形的工艺,连铸所产生的产品具有韧性好,伸缩度好,
形质均匀等特点,且精度高,成品度高,在炼钢厂中得到了大量应用。
最后,还有一些其他工艺,如热处理、表面处理和炼钢成品等,
其主要作用是进一步提高钢铁材料的性能和强度,不仅改善了表面质
量和拉伸性能,而且增加了钢的耐磨度和耐腐蚀性等。
钢铁的冶炼原理及生产工艺流程

炼铁方法主要有高炉法、直接还原法、熔融还原法等,其原理是矿石在特定的气氛中(还原物质CO、H2、C;适宜温度等)通过物化反应获取还原后的生铁。
生铁除了少部分用于铸造外,绝大部分是作为炼钢原料。
1、高炉炼铁的冶炼原理(应用最多的)
1)炼铁的原理:用还原剂将铁矿石中的铁氧化物还原成金属铁。
铁氧化物(Fe2O3、Fe3O4、FeO)+还原剂(C、CO、H2)铁(Fe)
2) 炼铁的方法
(1)直接还原法(非高炉炼铁法)
(2)高炉炼铁法(主要方法)
3)高炉炼铁的原料及其作用
(1)铁矿石:(烧结矿、球团矿)提供铁元素。
(2)焦碳:提供热量;提供还原剂;作料柱的骨架。
(3)熔剂:(石灰石、白云石、萤石)
使炉渣熔化为液体;去除有害元素硫(S)。
(4)空气:为焦碳燃烧提供氧。
2、工艺流程
生铁的冶炼虽原理相同,但由于方法不同、冶炼设备不同,所以工艺流程也不同。
下面分别简单予以介绍。
高炉生产是连续进行的
从炉顶(一般炉顶是由料种与料斗组成,现代化高炉是钟阀炉顶和无料钟炉顶)不断地装入铁矿石、焦炭、熔剂,从高炉下部的风口吹进热风(1000~1300摄氏度),喷入油、煤或天然气等燃料。
装入高炉中的铁矿石,主要是铁和氧的化合物。
在高温下,焦炭中和喷吹物中的碳及碳燃烧生成的一氧化碳将铁矿石中的氧夺取出来,得到铁,。
炼钢工艺步骤和流程

炼钢工艺步骤和流程炼钢是将生铁或钢水经过一系列工艺步骤,使其成分、温度、质量等指标达到一定要求的过程。
炼钢工艺步骤和流程对于钢铁生产至关重要,下面将介绍炼钢的一般工艺步骤和流程。
1. 原料准备。
炼钢的原料主要包括铁矿石、焦炭和石灰石。
在炼钢工艺开始之前,首先需要对原料进行准备。
铁矿石经过破碎、磨矿、浸出等工艺处理,得到高品位的铁矿石粉末;焦炭经过煤泥浸出、煤泥干燥、粉碎等工艺处理,得到高品位的焦炭粉末;石灰石经过破碎、磨矿、煅烧等工艺处理,得到高品位的石灰石粉末。
原料准备工作的好坏将直接影响炼钢的成品质量。
2. 炼铁。
炼钢的第一步是炼铁。
炼铁是将铁矿石还原成生铁的过程。
首先将原料铁矿石、焦炭和石灰石按一定比例混合,然后经过高温煅烧,使铁矿石中的氧化铁还原成金属铁。
炼铁的质量和效率对后续的炼钢过程有着直接的影响。
3. 转炉炼钢。
转炉炼钢是目前主要的炼钢方法之一。
在转炉炼钢过程中,首先将炼铁和废钢放入转炉中,然后加入适量的废钢、铁合金和石灰石。
通过高温燃烧,将废钢中的杂质燃尽,使废钢中的铁与炼铁混合,形成合金。
在燃烧的同时,石灰石中的氧化钙与炼铁中的磷、硫等杂质反应生成渣,将杂质排除。
经过一系列处理,最终得到合格的炼钢产品。
4. 电弧炼钢。
电弧炼钢是另一种常用的炼钢方法。
在电弧炼钢过程中,首先将炼铁和废钢放入电弧炉中,然后通过高压电弧加热炉内物料,使其熔化。
然后加入适量的废钢、铁合金和石灰石。
通过高温燃烧和电弧加热,将废钢中的杂质燃尽,使废钢中的铁与炼铁混合,形成合金。
在燃烧和电弧加热的同时,石灰石中的氧化钙与炼铁中的磷、硫等杂质反应生成渣,将杂质排除。
经过一系列处理,最终得到合格的炼钢产品。
5. 连铸。
连铸是炼钢的最后一道工艺环节。
在连铸过程中,将炼钢液体倒入连铸机中,经过连铸机的一系列处理,将炼钢液体冷却凝固成坯料。
然后通过切割、冷却等工艺处理,得到成品钢材。
总结。
炼钢工艺步骤和流程是一个复杂而又精密的过程,需要各个环节的配合和协调。
炼钢厂的工艺流程
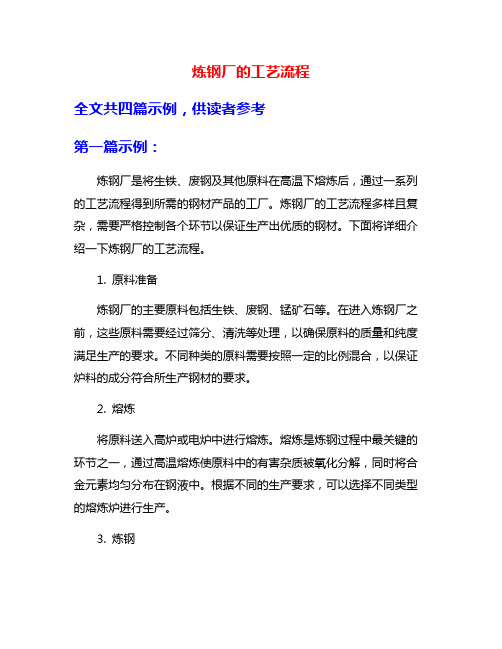
炼钢厂的工艺流程全文共四篇示例,供读者参考第一篇示例:炼钢厂是将生铁、废钢及其他原料在高温下熔炼后,通过一系列的工艺流程得到所需的钢材产品的工厂。
炼钢厂的工艺流程多样且复杂,需要严格控制各个环节以保证生产出优质的钢材。
下面将详细介绍一下炼钢厂的工艺流程。
1. 原料准备炼钢厂的主要原料包括生铁、废钢、锰矿石等。
在进入炼钢厂之前,这些原料需要经过筛分、清洗等处理,以确保原料的质量和纯度满足生产的要求。
不同种类的原料需要按照一定的比例混合,以保证炉料的成分符合所生产钢材的要求。
2. 熔炼将原料送入高炉或电炉中进行熔炼。
熔炼是炼钢过程中最关键的环节之一,通过高温熔炼使原料中的有害杂质被氧化分解,同时将合金元素均匀分布在钢液中。
根据不同的生产要求,可以选择不同类型的熔炼炉进行生产。
3. 炼钢将熔炼后的熔铁进行炼钢处理。
炼钢是将熔铁中的碳含量、硫、磷等有害元素降低,同时添加适量的合金元素和脱氧剂,以调整钢液的成分和性能。
在炼钢过程中需要控制好炉温、时间、搅拌等参数,确保炼钢的过程充分、均匀。
4. 过程处理在炼钢过程中,会产生大量废气、废渣和废水等副产品。
为了减少环境污染,炼钢厂需要配备相应的废气处理设备、废渣处理设备等,对排放的废气、废渣进行处理,以达到环保标准。
5. 钢材成品经过炼钢处理后,钢水会被铸造成坯料,再通过轧制、淬火、酸洗、镀锌等工艺加工成成品钢材。
最终形成各种不同规格、用途的钢材产品,供应给不同行业的客户,如建筑、汽车制造、机械加工等领域。
炼钢厂的工艺流程经过原料准备、熔炼、炼钢、过程处理、成品制造等环节,全过程需要严格控制各个环节,确保生产出符合标准和客户需求的高质量钢材产品。
在生产过程中还需要关注环保问题,处理好废气、废渣等副产品,保护环境和人民的健康。
希望通过对炼钢厂工艺流程的介绍,让更多人了解钢铁行业的生产过程,关注环保和可持续发展。
第二篇示例:炼钢是将铁水经过一系列工艺处理,使其脱除杂质,提高纯度,最终得到符合要求的钢材的过程。
不锈钢冶炼工艺流程的分析比较
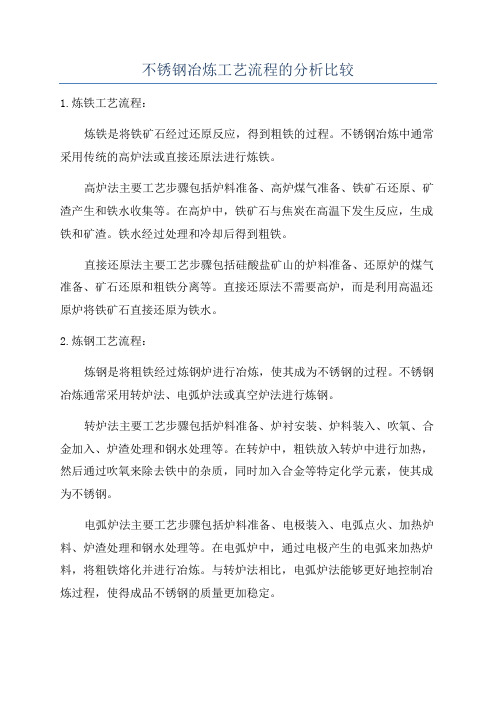
不锈钢冶炼工艺流程的分析比较1.炼铁工艺流程:炼铁是将铁矿石经过还原反应,得到粗铁的过程。
不锈钢冶炼中通常采用传统的高炉法或直接还原法进行炼铁。
高炉法主要工艺步骤包括炉料准备、高炉煤气准备、铁矿石还原、矿渣产生和铁水收集等。
在高炉中,铁矿石与焦炭在高温下发生反应,生成铁和矿渣。
铁水经过处理和冷却后得到粗铁。
直接还原法主要工艺步骤包括硅酸盐矿山的炉料准备、还原炉的煤气准备、矿石还原和粗铁分离等。
直接还原法不需要高炉,而是利用高温还原炉将铁矿石直接还原为铁水。
2.炼钢工艺流程:炼钢是将粗铁经过炼钢炉进行冶炼,使其成为不锈钢的过程。
不锈钢冶炼通常采用转炉法、电弧炉法或真空炉法进行炼钢。
转炉法主要工艺步骤包括炉料准备、炉衬安装、炉料装入、吹氧、合金加入、炉渣处理和钢水处理等。
在转炉中,粗铁放入转炉中进行加热,然后通过吹氧来除去铁中的杂质,同时加入合金等特定化学元素,使其成为不锈钢。
电弧炉法主要工艺步骤包括炉料准备、电极装入、电弧点火、加热炉料、炉渣处理和钢水处理等。
在电弧炉中,通过电极产生的电弧来加热炉料,将粗铁熔化并进行冶炼。
与转炉法相比,电弧炉法能够更好地控制冶炼过程,使得成品不锈钢的质量更加稳定。
真空炉法主要工艺步骤包括炉料准备、炉膛抽真空、加热炉料、炉渣处理和钢水处理等。
真空炉法通过在高真空下进行加热和冶炼,可以有效去除炉料中的杂质和氧化物,制造高纯度的不锈钢。
以上是常用的不锈钢冶炼工艺流程进行的简要比较。
具体的工艺选择取决于炼钢厂的设备情况、产品质量要求和成本考虑。
不同的工艺流程会影响到不锈钢的成品质量、生产效率和能源消耗等方面,因此需要综合考虑各种因素,选择适合的冶炼工艺。
武钢炼铁厂工艺流程

武钢炼铁厂工艺流程武钢炼铁厂是中国最大的钢铁企业之一,其工艺流程是指在炼铁过程中所采用的一系列工艺步骤和方法。
下面将详细介绍武钢炼铁厂的工艺流程。
一、炼铁前的准备工作炼铁前的准备工作主要包括原料准备、设备检修和人员培训等方面。
首先,需要准备足够的铁矿石、焦炭和石灰石等原料,并对原料进行筛分、破碎和配料等处理。
其次,要对炼铁设备进行检修和维护,确保设备正常运行。
最后,需要对工作人员进行相关培训,熟悉工艺流程和操作规程。
二、炼铁工艺流程1. 原料预处理在炼铁过程中,首先需要对原料进行预处理。
铁矿石经过破碎、磨矿、磁选等工艺处理,将矿石中的杂质和有害元素去除,以提高炼铁的质量和效率。
2. 焙烧还原焙烧还原是炼铁过程中的关键步骤之一。
将经过预处理的铁矿石和焦炭按一定比例混合后,放入高炉中进行热还原反应。
在高炉中,焦炭被氧化生成一氧化碳等还原气体,与铁矿石中的氧化铁反应,生成金属铁。
3. 高炉冶炼在高炉冶炼过程中,经过焙烧还原得到的金属铁和渣进行分离。
金属铁下沉至炉底,形成铁水,而渣浮于金属铁上,形成炉渣。
通过合理的操作控制,使金属铁和炉渣达到理想的分离效果。
4. 铁水处理铁水处理是指对高炉产出的铁水进行脱硫、脱磷、除渣等处理。
这些处理方式可以提高铁水的质量,并减少对后续工艺的影响。
脱硫和脱磷主要通过加入适量的脱硫剂和脱磷剂来实现,而除渣则是通过物理或化学方法将炉渣与铁水分离。
5. 炼钢炼钢是将炼铁产出的铁水进一步加工,以获得更高质量的钢材。
炼钢过程包括转炉炼钢、电炉炼钢、连铸等工艺。
在转炉炼钢过程中,将铁水和废钢等原料放入转炉中,通过吹氧和加入合适的合金元素,调整铁水的成分和温度,最终得到符合要求的钢水。
电炉炼钢则是利用电能将废钢和铁水加热融化,再进行合金化处理。
连铸是将炼钢得到的钢水注入连铸机,通过结晶器冷却凝固,形成钢坯。
6. 热处理热处理是提高钢材性能的重要工艺。
通过加热和冷却的方式,改变钢材的组织结构和性能。
炼钢8步工艺流程
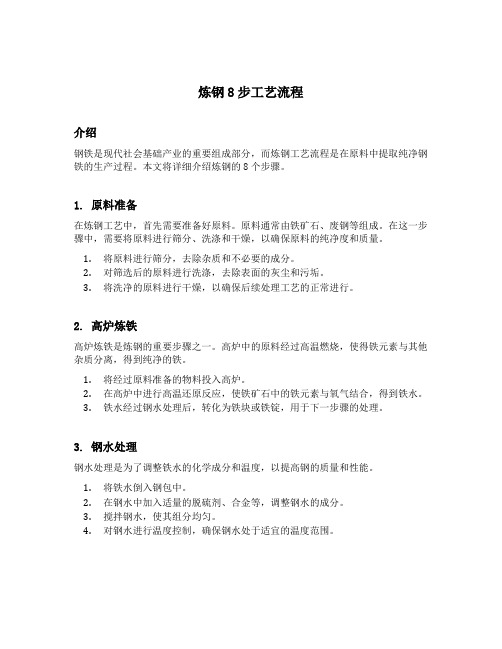
炼钢8步工艺流程介绍钢铁是现代社会基础产业的重要组成部分,而炼钢工艺流程是在原料中提取纯净钢铁的生产过程。
本文将详细介绍炼钢的8个步骤。
1. 原料准备在炼钢工艺中,首先需要准备好原料。
原料通常由铁矿石、废钢等组成。
在这一步骤中,需要将原料进行筛分、洗涤和干燥,以确保原料的纯净度和质量。
1.将原料进行筛分,去除杂质和不必要的成分。
2.对筛选后的原料进行洗涤,去除表面的灰尘和污垢。
3.将洗净的原料进行干燥,以确保后续处理工艺的正常进行。
2. 高炉炼铁高炉炼铁是炼钢的重要步骤之一。
高炉中的原料经过高温燃烧,使得铁元素与其他杂质分离,得到纯净的铁。
1.将经过原料准备的物料投入高炉。
2.在高炉中进行高温还原反应,使铁矿石中的铁元素与氧气结合,得到铁水。
3.铁水经过钢水处理后,转化为铁块或铁锭,用于下一步骤的处理。
3. 钢水处理钢水处理是为了调整铁水的化学成分和温度,以提高钢的质量和性能。
1.将铁水倒入钢包中。
2.在钢水中加入适量的脱硫剂、合金等,调整钢水的成分。
3.搅拌钢水,使其组分均匀。
4.对钢水进行温度控制,确保钢水处于适宜的温度范围。
4. 脱氧脱氧是为了去除钢水中的氧气,以防止铁水氧化,提高钢的质量。
1.在钢水中加入脱氧剂,如硅、锰等。
2.脱氧剂与氧气发生反应,将氧气从钢水中去除。
5. 过真空处理过真空处理是为了去除钢水中的杂质和气泡,提高钢的纯度和致密性。
1.将钢水放入真空室中。
2.通过真空泵将真空室抽空,去除钢水中的杂质和气泡。
6. 连铸成型连铸是将炼制好的钢水连续浇铸成坯料的过程。
1.将钢水倒入连铸机的浇铸容器中。
2.控制浇铸速度,使得钢水逐渐冷却凝固。
3.在钢水冷却和凝固的同时,进行拉拔和切割,将连续产生的坯料切割成所需长度。
7. 热加工热加工是将连铸坯进行加热和变形加工的过程,以改变钢的形状和尺寸,并提高钢的力学性能。
1.将连铸坯加热至适宜的工作温度。
2.通过轧制、锻造等热加工工艺,将连铸坯变形成所需的形状和尺寸。
炼钢厂的工艺流程

炼钢厂的工艺流程全文共四篇示例,供读者参考第一篇示例:炼钢厂是将生铁或废钢通过高温熔炼、除杂质、合金和成型等工艺过程,生产出各种钢材产品的厂家。
炼钢厂的工艺流程包括原料准备、炼钢、连铸、轧钢等多个环节,下面就来详细介绍一下炼钢厂的工艺流程。
一、原料准备炼钢厂的原料主要包括铁矿石、煤炭、废钢和废铁等。
在炼钢的过程中,铁矿石是最主要的原料,其含铁量高低直接影响到生产效率和产品质量。
煤炭在高炉燃烧时提供热量,促使铁矿石还原为生铁。
而废钢和废铁则是通过熔融再生钢材的重要原料,对环保和资源循环利用起着重要作用。
二、炼钢炼钢是指将生铁或废钢加热至熔化状态,并通过除渣、除氧化物、合金和调节成分等工艺过程,生产出符合标准的钢材产品。
在炼钢过程中,生铁首先通过高炉冶炼得到熔融铁水,然后经过转炉、电炉或其他炼钢设备进行炼钢操作。
转炉炼钢是较常用的工艺,通过转炉炼钢可有效去除生铁中的杂质,调节成分,得到合格的钢材产品。
三、连铸连铸是将炼钢得到的熔钢直接注入到结晶器中,通过凝固成形,制成长方坯或圆坯等半成品,在后续的轧钢工艺中进行进一步加工。
连铸工艺具有生产效率高、能耗低的特点,对提高钢铁生产效率、减少能源消耗具有重要意义。
四、轧钢轧钢是将半成品坯料通过热轧、冷轧等工艺进行成形,生产出各种规格的钢材产品。
热轧是利用高温将坯料连续轧制,消除残余应力,得到粗毛坯的工艺;而冷轧是在室温下对热轧坯料进行轧制,得到较为平整光滑的表面,提高产品的表面质量。
炼钢厂的工艺流程是一个复杂的系统工程,需要各种设备、技术和人才协同作业,才能保证生产出高质量的钢材产品。
炼钢厂在生产过程中要注意环保、安全、节能等方面的要求,促进炼钢产业的可持续发展。
希望通过对炼钢厂工艺流程的介绍,让更多人了解炼钢产业的重要性和复杂性,支持和关注炼钢生产的发展。
第二篇示例:炼钢厂是生产钢材的重要工业设施,其工艺流程复杂且关键,涉及多个生产环节和工艺参数的控制。
本文将详细介绍炼钢厂的工艺流程,希望能够为读者提供更深入的了解。
钢的冶炼工艺流程

钢的冶炼工艺流程
《钢的冶炼工艺流程》
钢是一种重要的金属材料,广泛用于建筑、机械制造、船舶建造等领域。
它的生产需要经过一系列复杂的冶炼工艺流程。
首先,钢的生产原料主要包括铁矿石、焦炭和石灰石。
这些原料在高炉中被加热,其中焦炭将铁矿石还原成铁,石灰石则用来吸收硫和磷等杂质。
在高炉中产生的熔融铁水被称为生铁,含有较高的碳含量。
接下来,生铁被送入转炉或电炉中进行炼钢。
在转炉中,将生铁与废钢材料一起放入炉内,通入熔化的废钢液体。
通过吹氧和搅拌炉内气流,去除杂质和调整成分,最终得到符合要求的钢水。
在电炉中,生铁和废钢被放入炉内,并通过加热电极产生电弧,使废钢和铁水熔化。
然后通过氧气吹混、搅拌、加入合金等操作,进行精炼和合金化,最终获得所需的钢水。
最后,钢水被浇铸成各种形状的钢锭或钢坯,然后经过轧制、锻造、拉拔等加工工艺,得到符合不同需要的钢材产品。
总的来说,钢的冶炼工艺流程经历了高炉炼铁和转炉或电炉炼钢两个阶段,包括原料处理、熔炼、精炼和成形等多个环节。
这些工艺流程的优化和改进,对于提高钢的质量和生产效率具有重要意义。
钢铁冶炼工艺流程
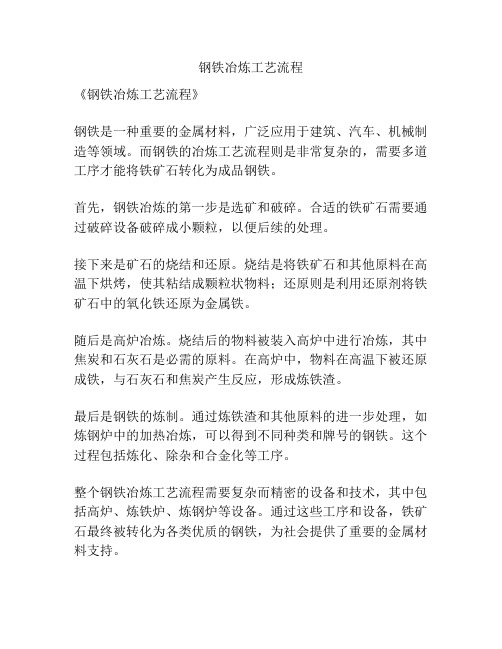
钢铁冶炼工艺流程
《钢铁冶炼工艺流程》
钢铁是一种重要的金属材料,广泛应用于建筑、汽车、机械制造等领域。
而钢铁的冶炼工艺流程则是非常复杂的,需要多道工序才能将铁矿石转化为成品钢铁。
首先,钢铁冶炼的第一步是选矿和破碎。
合适的铁矿石需要通过破碎设备破碎成小颗粒,以便后续的处理。
接下来是矿石的烧结和还原。
烧结是将铁矿石和其他原料在高温下烘烤,使其粘结成颗粒状物料;还原则是利用还原剂将铁矿石中的氧化铁还原为金属铁。
随后是高炉冶炼。
烧结后的物料被装入高炉中进行冶炼,其中焦炭和石灰石是必需的原料。
在高炉中,物料在高温下被还原成铁,与石灰石和焦炭产生反应,形成炼铁渣。
最后是钢铁的炼制。
通过炼铁渣和其他原料的进一步处理,如炼钢炉中的加热冶炼,可以得到不同种类和牌号的钢铁。
这个过程包括炼化、除杂和合金化等工序。
整个钢铁冶炼工艺流程需要复杂而精密的设备和技术,其中包括高炉、炼铁炉、炼钢炉等设备。
通过这些工序和设备,铁矿石最终被转化为各类优质的钢铁,为社会提供了重要的金属材料支持。
炼铁工艺流程
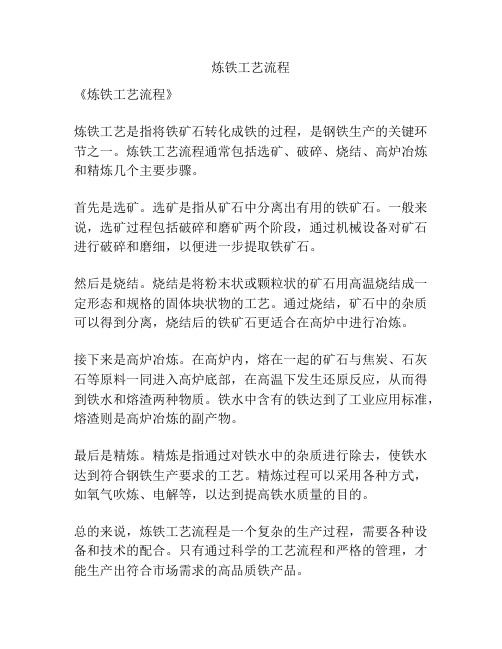
炼铁工艺流程
《炼铁工艺流程》
炼铁工艺是指将铁矿石转化成铁的过程,是钢铁生产的关键环节之一。
炼铁工艺流程通常包括选矿、破碎、烧结、高炉冶炼和精炼几个主要步骤。
首先是选矿。
选矿是指从矿石中分离出有用的铁矿石。
一般来说,选矿过程包括破碎和磨矿两个阶段,通过机械设备对矿石进行破碎和磨细,以便进一步提取铁矿石。
然后是烧结。
烧结是将粉末状或颗粒状的矿石用高温烧结成一定形态和规格的固体块状物的工艺。
通过烧结,矿石中的杂质可以得到分离,烧结后的铁矿石更适合在高炉中进行冶炼。
接下来是高炉冶炼。
在高炉内,熔在一起的矿石与焦炭、石灰石等原料一同进入高炉底部,在高温下发生还原反应,从而得到铁水和熔渣两种物质。
铁水中含有的铁达到了工业应用标准,熔渣则是高炉冶炼的副产物。
最后是精炼。
精炼是指通过对铁水中的杂质进行除去,使铁水达到符合钢铁生产要求的工艺。
精炼过程可以采用各种方式,如氧气吹炼、电解等,以达到提高铁水质量的目的。
总的来说,炼铁工艺流程是一个复杂的生产过程,需要各种设备和技术的配合。
只有通过科学的工艺流程和严格的管理,才能生产出符合市场需求的高品质铁产品。
炼钢厂的工艺流程

炼钢厂的工艺流程一般包括以下几个主要步骤:
1. 原料准备:炼钢厂的原料主要包括铁矿石、焦炭、废钢等。
在工艺流程开始前,需要对原料进行筛选、破碎和预处理,确保原料的质量和适用性。
2. 炼铁过程:炼钢厂首先进行炼铁过程,将铁矿石还原为铁。
这一过程通常包括矿石的破碎、磨矿、浸出等步骤,最终得到铁矿石的还原产物-生铁。
3. 炼钢过程:在炼钢过程中,将生铁中的杂质去除,并进行合金添加,以调整钢的成分和性能。
主要的炼钢方法包括转炉法、电弧炉法和氧气炼钢法等。
其中,转炉法是最常用的炼钢方法,通过将生铁和废钢放入转炉中进行冶炼,控制炉温和加入适量的合金元素,最终得到合格的钢水。
4. 精炼过程:在炼钢过程中,还需要进行精炼操作,以进一步提高钢的质量。
精炼过程主要包括脱硫、脱磷、脱氧等操作,通过添加适量的脱硫剂、脱磷剂和脱氧剂,去除钢中的杂质和氧化物。
5. 钢水处理:在炼钢过程中,还需要对钢水进行处理,以满足不同用途的钢的要求。
钢水处理主要包括温度调节、除渣、捞渣、浇铸等操
作,确保钢水的质量和适用性。
6. 连铸过程:炼钢厂中的连铸工艺是将炼得的钢水注入连铸机中,通过结晶器和冷却装置使钢水迅速凝固成坯料,再通过切割、冷却、定尺等操作,最终得到符合要求的钢坯。
7. 后续加工:钢坯经过连铸后,还需要进行后续加工,如热轧、冷轧、锻造、热处理等,以得到最终的钢材产品。
以上是炼钢厂的一般工艺流程,具体的流程会根据不同的炼钢厂和产品要求有所差异。
炼钢厂工艺流程

炼钢厂工艺流程
《炼钢厂工艺流程》
炼钢是一项复杂的工艺,通过各种操作和工序将生铁转化为高质量的钢铁。
炼钢厂工艺流程包括了多个步骤,每一个步骤都非常重要,需要严格控制和操作。
首先,生铁将会被装载到高炉中进行初步冶炼。
在这个阶段,矿石和焦炭会被加入到高炉中,经过高温的燃烧和还原,将生铁的矿石中的杂质转化为炼铁。
随后,炼铁会被送入转炉或电炉中进行精炼,其中杂质将被进一步去除,从而得到高品质的炼钢。
在转炉或电炉中,炼钢师会加入适量的废钢、锰、铬等合金元素,以调整钢铁的化学成分,以满足特定的用途和要求。
随后,炼钢师会通过吹氧和搅拌钢液的方式,控制炉温和杂质的去除,从而得到所需品质的炼钢。
最后,炼钢会被倒入浇注包或连铸机中,进行成形和冷却,得到半成品或成品钢材。
在整个流程中,需要精密的控制和操作,以确保炼钢的质量和性能。
总的来说,《炼钢厂工艺流程》是一个对工艺和操作要求非常严格的工艺,需要炼钢师有着丰富的经验和技术,才能确保生产出高质量的钢材。
炼钢工艺及流程

1)高炉冶炼用的原料
主要由铁矿石、燃料(焦炭)和熔剂(石灰石)三部分组成。
通常,冶炼1吨生铁需要1.5-2.0吨铁矿石,0.4-0.6吨焦炭,0.2-0.4吨熔剂,总计需要2-3吨原料。为了保证高炉生产的连续性,要求有足够数量的原料供应。
2)工艺流程
生铁的冶炼虽原理相同,但由于方法不同、冶炼设备不同,所以工艺流程也不同。下面分别简单予以介绍。
f.上轧辊平衡装置:用于抬升上辊和防止轧件进出轧辊时受冲击的装置。形式有﹕弹簧式﹑多用在型材轧机上﹔重锤式﹐常用在轧辊移动量大的初轧机上﹔液压式﹐多用在四辊板带轧机上。
g.为提高作业率﹐要求轧机换辊迅速﹑方便。换辊方式有 C 形钩式﹑套筒式﹑小车式和整机架换辊式四种。用前两种方式换辊靠吊车辅助操作﹐而整机架换辊需有两套机架﹐此法多用于小的轧机。小车换辊适合于大的轧机﹐有利于自动化。目前﹐轧机上均采用快速自动换辊装置﹐换一次轧辊只需 5 ~ 8 分钟。
中国于1871 年在福州船政局所属拉铁厂( 轧钢厂 ) 开始使用轧机﹔轧制厚15mm 以下的铁板﹐ 6 ~ 120mm 的方﹑圆钢。 1890 年汉冶萍公司汉阳铁厂装有蒸汽机拖动的横列双机架 2450mm 二辊中板轧机和蒸汽机拖动的三机架横列二辊式轨梁轧机以及 350/300mm 小型轧机。随着冶金工业的发展﹐现已有多种类型轧机。
1、什么是轧机?
轧机是实现金属轧制过程的设备。泛指完成轧材生产全过程的装备﹐包括有主要设备﹑辅助设备﹑起重运输设备和附属设备等。但一般所说的轧机往往仅指主要设备。
2、轧机的发展史
据说在14 世纪欧洲就有轧机﹐但有记载的是1480 年意大利人 达 ' 芬奇 (Leonardo da Vinci) 设计出轧机的草图。1553 年法国人布律列尔 (Brulier) 轧制出金和银板材﹐用以制造钱币。此后在西班牙﹑比利时和英国相继出现轧机。1728 年设计的生产圆棒材用的轧机为英国设计的生产圆棒材用的轧机。英国于1766 年有了串行式小型轧机﹐19 世纪中叶﹐第一台可逆式板材轧机在英国投产﹐并轧出了船用铁板。1848 年德国发明了万能式轧机﹐ 1853 年美国开始用三辊式的型材轧机﹐并用蒸汽机传动的升降台实现机械化。接着美国出现了劳特式轧机。1859 年建造了第一台连轧机。万能式型材轧机是在1872 年出现的﹔20 世纪初制成半连续式带钢轧机﹐由两架三辊粗轧机和五架四辊精轧机组成。
炼钢工艺流程简介
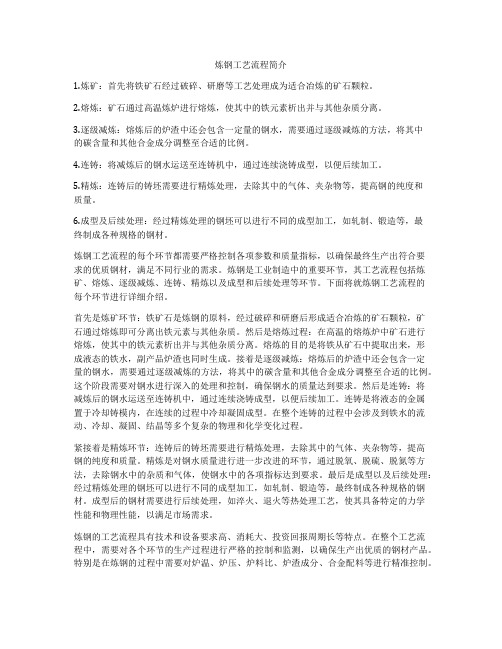
炼钢工艺流程简介1.炼矿:首先将铁矿石经过破碎、研磨等工艺处理成为适合冶炼的矿石颗粒。
2.熔炼:矿石通过高温炼炉进行熔炼,使其中的铁元素析出并与其他杂质分离。
3.逐级减炼:熔炼后的炉渣中还会包含一定量的钢水,需要通过逐级减炼的方法,将其中的碳含量和其他合金成分调整至合适的比例。
4.连铸:将减炼后的钢水运送至连铸机中,通过连续浇铸成型,以便后续加工。
5.精炼:连铸后的铸坯需要进行精炼处理,去除其中的气体、夹杂物等,提高钢的纯度和质量。
6.成型及后续处理:经过精炼处理的钢坯可以进行不同的成型加工,如轧制、锻造等,最终制成各种规格的钢材。
炼钢工艺流程的每个环节都需要严格控制各项参数和质量指标,以确保最终生产出符合要求的优质钢材,满足不同行业的需求。
炼钢是工业制造中的重要环节,其工艺流程包括炼矿、熔炼、逐级减炼、连铸、精炼以及成型和后续处理等环节。
下面将就炼钢工艺流程的每个环节进行详细介绍。
首先是炼矿环节:铁矿石是炼钢的原料,经过破碎和研磨后形成适合冶炼的矿石颗粒,矿石通过熔炼即可分离出铁元素与其他杂质。
然后是熔炼过程:在高温的熔炼炉中矿石进行熔炼,使其中的铁元素析出并与其他杂质分离。
熔炼的目的是将铁从矿石中提取出来,形成液态的铁水,副产品炉渣也同时生成。
接着是逐级减炼:熔炼后的炉渣中还会包含一定量的钢水,需要通过逐级减炼的方法,将其中的碳含量和其他合金成分调整至合适的比例。
这个阶段需要对钢水进行深入的处理和控制,确保钢水的质量达到要求。
然后是连铸:将减炼后的钢水运送至连铸机中,通过连续浇铸成型,以便后续加工。
连铸是将液态的金属置于冷却铸模内,在连续的过程中冷却凝固成型。
在整个连铸的过程中会涉及到铁水的流动、冷却、凝固、结晶等多个复杂的物理和化学变化过程。
紧接着是精炼环节:连铸后的铸坯需要进行精炼处理,去除其中的气体、夹杂物等,提高钢的纯度和质量。
精炼是对钢水质量进行进一步改进的环节,通过脱氧、脱硫、脱氮等方法,去除钢水中的杂质和气体,使钢水中的各项指标达到要求。
- 1、下载文档前请自行甄别文档内容的完整性,平台不提供额外的编辑、内容补充、找答案等附加服务。
- 2、"仅部分预览"的文档,不可在线预览部分如存在完整性等问题,可反馈申请退款(可完整预览的文档不适用该条件!)。
- 3、如文档侵犯您的权益,请联系客服反馈,我们会尽快为您处理(人工客服工作时间:9:00-18:30)。
1.3 企业基本情况新绛县祥益工贸有限公司根据山西省发展和改革委员会(晋发改备案【2007】146号)批文,建设450m3高炉,并配套建设90m3带式烧结机等。
新绛县祥益工贸有限公司位于运城市新绛县煤化工业园区,厂址距新绛县城10km, 距离同蒲铁路侯马北货站10km距大运高速公路出口2.5km,距晋韩高速公路出口3km交通运输十分便利,地理位置非常优越。
新绛县祥益工贸有限公司占地面积约28万m2 目前拥有职工600余人,其中中层管理人员20人,各类专业技术人员40余人(其中高级技术人员3人,中级技术人员20人),职工队伍稳定,职工素质普遍提高。
公司紧紧依托当地丰富的矿产资源优势,艰苦创业,我稳步发展。
新绛县祥益工贸有限公司始终坚持质量第一、信誉为本的宗旨,依靠全体员工团结拼搏、积极开拓、艰苦创业、自强不息的努力,企业迅速发展壮大,为新绛县经济发展做出贡献。
1.4 高炉生产工艺简述高炉冶炼用的焦炭、含铁原料、溶剂在原料厂和烧结厂加工处理合格后,用皮带机运至料仓贮存使用。
各种炉料在仓下经二次筛分、计量后,按程序由仓下皮带机送到高炉料坑,由料车将炉料至炉顶加入炉内进行冶炼。
高炉冶炼的热源主要来源于焦炭和煤粉的燃烧。
各种原料在炉内进行复杂的理化反应,炉内承受着高温高压作用。
为此,高炉内要砌耐火材料,并在高温区和重要部位设冷却壁,确保高炉安全生产。
高炉冶炼用风由鼓风机站供给,冷风以热风炉加热后送入高炉。
高炉冶炼主要产品是生铁,副产品为煤气、炉渣、炉尘等。
高炉的铁水用铁水罐拉至铸铁机进行铸铁,或用汽车将铁水罐直接送至铸铁机进行铸铁,或用汽车将铁水罐直接送至炼钢厂进行炼钢。
高炉煤气经除尘、净化后一部分供热风炉烧炉,余下部分供烧结机、喷煤和6000kw 发电机组。
高炉炉渣在炉前进行水冲渣,水渣送至建材厂制砖,或送至水泥厂作为制作水泥的原料。
高炉产生的各种原料、重力除尘拉到烧结厂进行配料烧结,煤气除尘的布袋拉到建材厂进行综合利用。
高炉生产工艺流程见图二。
1.6 烧结生产工艺简述90m 3烧结机主要包括烧结机及相应配套的原料系统、配料系统、混料系统、破碎、筛分系统、鼓风冷却系统、成品贮存系统以及供风、供水、供电等辅助设施。
该工程主要由生产设施、辅助设施和生活设施三大部分组成,其中生活设施由建设单位同意考虑,故本设计只考虑生产设施和辅助设施。
生产设施包括原料及配料系统,主烧结室、带冷几室、风机房、烟卤,一混合室、二混合室、成品中间仓等。
辅助设施包括原料及配料系统除尘及配套风机,机头除尘室及配套风机、烟卤,机尾布袋出尘室及配套风机、变配电室、水泵房等。
生产设施的总图布置为带冷机室在、主烧结室东西方向布置,除尘室的南侧。
原料上料及配料系统布置在主烧机室的东侧,一混合室、二混合室布置在主烧机室的南侧。
成品中间仓布置在带冷机室的南侧,距高炉储矿槽100余米,由成品皮带将成品烧结矿送至高炉储矿槽上。
烧结生产工艺流程见图三。
1.8 高炉喷煤生产工艺简述高炉喷煤配套工程,是节约焦炭、降低高炉炼铁生产成本的重要措施。
自从六十年代我国鞍钢、首钢高炉喷煤会的成功以来很快在国内普遍推广应用,并且高炉喷煤在工艺及其相关技术得到了迅速发展。
尤其是近几年发展的富氧大喷煤技术(宝钢喷煤煤比打达到》200kg/Tfe水平)给高炉生产注入县的生机。
国内炼铁生产规模不断扩大与高炉生产效率的提高,对焦炭需求量业日趋增加,由于国内1) 中压、专用煤气锅沪一台, 额定蒸发量:35t/h蒸汽出口温度:450 C 给水温度:104 C2) 汽轮机一台额定蒸汽压力: 3.82MPa 排烟温度:w 161 C 设计燃料:高炉煤气新绛县主要地表水体为汾河及其支流浍河。
焦炭煤资源逐渐减少造成冶金焦价格不断上涨。
因此, 高炉喷吹煤粉是现代高炉炼铁生产降低成本的重要技术之一。
高炉喷煤配套工程主要由以下系统组成:1.8.1 原煤供配系统:包括原煤场、卸装倒推设备、原煤棚、配煤设施、输送及相应配套设施。
1.8.2 煤粉制备系统:包括升温炉、高炉热风炉废气管路、原煤仓、给煤机、磨机、布袋收粉器、 排烟风机及相应配套设施。
1.8.3 喷吹系统:包括配吹罐、储气罐、喷煤管道、控制系统及相应配套设施。
1.8.4空压站:包括空压机、脱水设备、储气罐及相应附属设备。
1.9 发电厂生产工艺简述发电厂配备两套 6000KW 煤气发电机组。
33450m 高炉每小时产煤气量为 10〜11万m ,其中40%用于热风炉,15%用于烧结机和喷煤,其余用 于6000KW 发电机组。
1.9.1生产工艺流程6000KW 煤气发电机组生产工艺流程见图五。
1.9.2 主要设备选型(一台6000kw 发电机组)机组型式、;中压凝汽式打孔抽汽机组规定功率: 6MW主汽门前压力: 3.43MPa 主汽门前温度:435 C 额定进气量: 35t/h 最大进气量: 38.5t/h 额定抽气量: 8〜 10t/h 最大抽气量: 13t/h3)发电机一台型号: QF-6-2 额定功率: 6MW 额定转速: 3000rPm 出线电压: 10KV 功率因数: 0.82.2 水文气象 2.2.1地表水汾河自县境东北南梁村入境, 流经 39 个村庄由县西的周流村出境,境内流程 22.5Km 。
河床上为泥沙,下为岩石,河床宽 200m左右。
浍河于县境内南中村 北入境,向西北流至县城西三林镇东汇入汾河,境内流程11.5Km ,河床宽20〜40m,汾河新绛段为复式河槽,主河槽宽60〜80m 平时汾河水量较小时走主河槽,付河槽用于行洪。
每年的 5〜9 月份为汾河的丰水期,平均流量 80 〜 1 50m 3/s ,洪水期流量达到 1680m 3/s ;9〜月份为汾河的平水期,平均流量 30〜80 m 3/s ,流量较小;3〜5月份为汾河的枯水期,流量小于30 m 3/s ,有时出现断流情况。
本工程厂址周围无地表水体。
2.2.2 气候与气象新绛县气候属暖温带大陆性疾风气候,昼夜温差大,四季分明。
冬季寒冷干燥,春季少雨多风,夏季炎热,余量集中,秋季多情朗凉爽天气。
据新绛县气象站几年来统计资料,主要气候特征统计如下年平均气温:12.8 C最低平均气温:-2.7 C最高平均气温:26.0 C极端最高气温:40.9 C极端最低气温:-12.3 C冬季平均相对湿度:59% 夏季平均相对湿度:73% 年平均降水量:496.2mm年最大降水量:946.9mm年平均风速:1.9m/s 全年主盛行风向/ 频率:S/16.6% 全年次盛行风向/ 频率:N/12.5%全年静风频率:18.6%年平均大风日数: 2.9d年平均无霜期:209d年平均日照时数:2253.5h新绛县近三年年主导风向为N风,年风频10.03%,年次主导风向为NNE风,年风频9.51%。
四季的主导风向为N风,风频分别为春9.44、夏10.57%、秋9.98%、冬10.15%。
多年平均风速为3m/s。
2.2.3 地震新绛县属山西地震活动强烈地区,也是国家重点监视地区,地震基本烈度为7 度。
但据历史记载,新绛县范围内几百年来未发生过5 级以上破坏性地震,当地主要自然灾害以旱、涝和虫害为主。
2.3 自然地址条件2.3.1 地形地貌新绛县境北部为吕梁山区,南部为峨眉丘陵区,中不为汾河高低阶地够成的冲、湖积平面区。
总的地形是南北两侧高中间低,东部高西部低。
全线一般海拔400-600 米,最高处为县西北的姑射峰,海拔1438.4 米。
最低处为万安乡的赵村度,海拔381.9 米。
根据地质构造、地貌特点,岩性及成因类型,全境可分为四大地貌单元。
本项目厂址处较为平坦,海拔高度412-415 米。
2.3.2 文水地质根据地貌形态和含水层性质,全县地下水可划分为4 个大区:基岩山区裂隙水区、山前倾斜平面孔隙山区、冲湖积平原孔隙水区及峨眉领黄土丘陵孔隙水区。
新绛县祥益工贸有限公司宇丰冶炼分公司所处水域为山前倾斜平面孔隙水区。
地下水较丰富。
当地出露的地层具有中朝陆台的特征,由太古界、元古界、新生界等几类。
厂区周围地质状况为太古界涑水杂岩、元古界霍山砂岩、古生界寒武系、奥陶系灰岩、石炭砂页岩上第四系松散岩。
5.1 对火灾危险的防范措施本工程存在火灾危险的场所主要有高炉区、热风炉区、煤气布袋区除尘区、烧结机区、高炉喷煤区、变压器室、电缆沟等,按生产火灾危险性分类:高炉区、热风炉区、烧结区为丁类,煤气布袋除尘区和高炉喷煤区为乙类、变压器室、高低压配电室、液压站、电缆沟等均分为丙类。
各主项工程建(构)筑物等耐火等级分类:高炉、热风炉、布袋除尘刚结构框架、烧结机主厂房、喷煤主厂房为四级,其余建筑物均为二级。
在生产过程中,爆炸于火灾危险性分析如下:①高炉除渣、出铁时易产生喷溅,引燃周围的易燃物品,引起着火。
②高炉生产的煤气经重力除尘布袋除尘处理后使用,如管道和阀门不严造成泄漏煤气时,能引起燃烧爆炸。
③高构筑物易遭雷击引起火灾。
④喷煤工艺中煤粉容器内煤粉堆积时间长了易产生自然。
对上述各级爆炸、火灾危险场所,本设计采用以下防火措施:5.1.1 总图布置按生产场所的危险性,分类集中布置。
本设计严格按《建筑设计防火规范》及其他规定,并根据生产性质、火灾危险性、建筑物耐火等级、防火分隔和安全通道等方面要求进行总图布置,其道路间距、各设施、建(构)筑物的防火间距均满足防火要求。
为便于安全消防,场内道路呈环形和尽头两种形式布置,主干道宽9m次干道宽6m在道路尽头处均设置了回车场。
架空管线布置,考虑通行对净高的要求,在道路或引道口处,遇有管架、管廊时,其净高均不小于5m。
5.1.2建、构筑物布置本工程所有建、构筑的平面布置、结构材料的选用均按《建筑设计防火规范》进行设计,厂房的防火要求根据工艺生产火灾危险性分类的不同而采用不同措施,各单位建筑的结构类型、耐火等级规格及依据详见主要生产场所及建、构筑物火灾危险特征表(表5-1)建筑平面考虑竖向布置设计,在满足工艺生产的提前下,尽量使平面整齐、层次清楚,消防通道畅通,楼梯出入口醒目,高炉、热风炉、布袋除尘器采用露天布置。
建筑物内设置疏通和安全出口,出规范中允许设一个安全出口的建筑物外,均设有不少于两个安全出口,建筑物均为钢筋混凝土承重结构或砖混结构,楼面层顶均为钢筋混凝土板,具有良好的耐火性能。
5.1.3消防给水消防给水设计执行《建筑设计防火规范》,消防用水量按同一时间的火灾次数和一次灭火用水量确定,室外消防用水量为25L/S,室内为5L/S,合计30L/S,高炉生产区域消防用水量按25001/设计,3 3烧结生产区域消防用水量按140mh设计,高炉喷煤生产区域消防用水量按120140mh设计.本工程生产用水与消防给水采用一个管网,在厂区内呈环形布置,管径DN159厂内设有室外消火栓,其间距不大于120m其保护半径为150m,数量为10个。