内部质量损失统计管理办法
质量损失管理办法
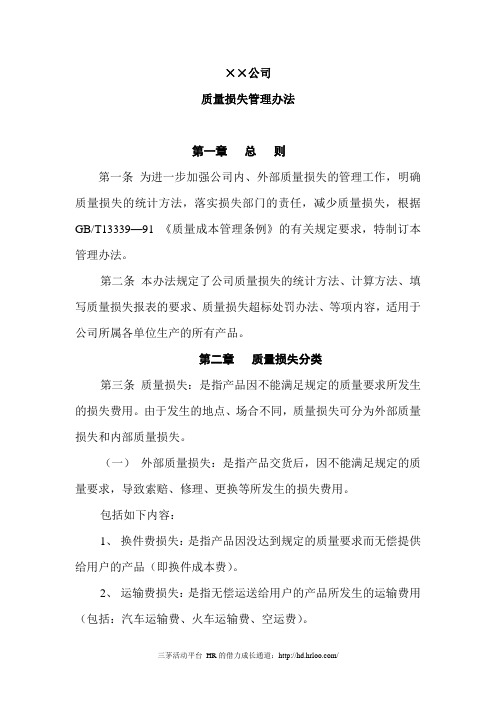
××公司质量损失管理办法第一章总则第一条为进一步加强公司内、外部质量损失的管理工作,明确质量损失的统计方法,落实损失部门的责任,减少质量损失,根据GB/T13339—91 《质量成本管理条例》的有关规定要求,特制订本管理办法。
第二条本办法规定了公司质量损失的统计方法、计算方法、填写质量损失报表的要求、质量损失超标处罚办法、等项内容,适用于公司所属各单位生产的所有产品。
第二章质量损失分类第三条质量损失:是指产品因不能满足规定的质量要求所发生的损失费用。
由于发生的地点、场合不同,质量损失可分为外部质量损失和内部质量损失。
(一)外部质量损失:是指产品交货后,因不能满足规定的质量要求,导致索赔、修理、更换等所发生的损失费用。
包括如下内容:1、换件费损失:是指产品因没达到规定的质量要求而无偿提供给用户的产品(即换件成本费)。
2、运输费损失:是指无偿运送给用户的产品所发生的运输费用(包括:汽车运输费、火车运输费、空运费)。
3、差旅费损失:是指赴用户进行售后服务人员发生的乘车费、住宿费(各服务站租房费)和出差补助费用。
4、话费损失:是指售后服务站和有关人员,在处理用户反映的质量问题时所发生的通讯费用(包括:移动电话通讯费和各服务站使用的非移动电话通讯费)。
(二)内部质量损失:是指产品交货前,因不能满足规定的质量要求所发生的损失费用。
包括如下内容:1、制造性质量损失:是指产品在生产制造过程中,由于管理不善、操作不当发生的损失费用。
由于制造性损失发生的责任不同可分为上工序损失和本工序损失。
上工序损失:是指由于上工序责任而发生的质量损失。
本工序损失:是指由于本单位责任而发生的质量损失。
2、技术性质量损失:是指产品因设计错漏、设计改进发生的损失费用。
第三章质量损失的统计方法第四条售后服务处负责外部质量损失的统计工作,对发生损失项目进行登记入帐。
按附表1《外部质量损失统计表》的要求,把发生的换件损失费、差旅费、运输费、话费逐项填写好后,报质量管理处。
质量损失管理办法
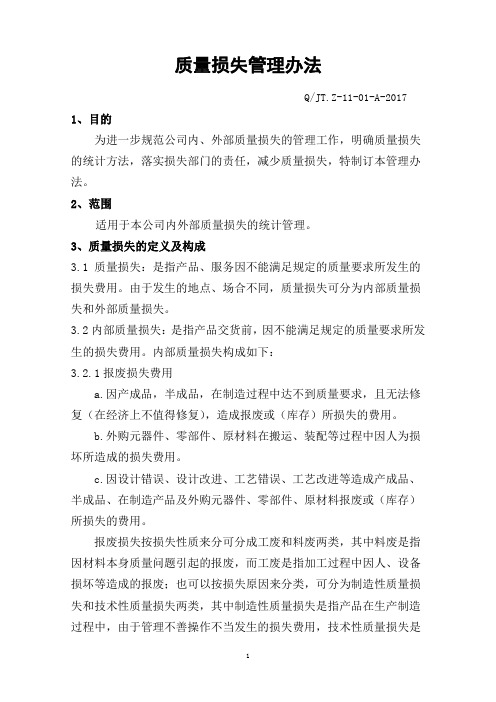
质量损失管理办法Q/JT.Z-11-01-A-2017 1、目的为进一步规范公司内、外部质量损失的管理工作,明确质量损失的统计方法,落实损失部门的责任,减少质量损失,特制订本管理办法。
2、范围适用于本公司内外部质量损失的统计管理。
3、质量损失的定义及构成3.1 质量损失:是指产品、服务因不能满足规定的质量要求所发生的损失费用。
由于发生的地点、场合不同,质量损失可分为内部质量损失和外部质量损失。
3.2内部质量损失:是指产品交货前,因不能满足规定的质量要求所发生的损失费用。
内部质量损失构成如下:3.2.1报废损失费用a.因产成品,半成品,在制造过程中达不到质量要求,且无法修复(在经济上不值得修复),造成报废或(库存)所损失的费用。
b.外购元器件、零部件、原材料在搬运、装配等过程中因人为损坏所造成的损失费用。
c.因设计错误、设计改进、工艺错误、工艺改进等造成产成品、半成品、在制造产品及外购元器件、零部件、原材料报废或(库存)所损失的费用。
报废损失按损失性质来分可分成工废和料废两类,其中料废是指因材料本身质量问题引起的报废,而工废是指加工过程中因人、设备损坏等造成的报废;也可以按损失原因来分类,可分为制造性质量损失和技术性质量损失两类,其中制造性质量损失是指产品在生产制造过程中,由于管理不善操作不当发生的损失费用,技术性质量损失是指产品因设计错误、设计改进、工艺错误、工艺改进等发生的损失费用。
3.2.2返修损失费为修复不合格品以及因设计错误、设计改进、工艺错误、工艺改进等造成在制品达不到预期要求,进行返修所需支付的费用,包括人工费、材料消耗、更换的零部件、原材料等的费用。
3.2.3因质量问题发生的停工损失:3.2.4质量事故处理费:3.2.5质量降级损失:3.3外部质量损失:是指产品交货后,因不能满足规定的质量要求,导致索赔、修理、更换等所发生的损失费用。
3.3.1换件费损失:是指产品因没达到规定的质量要求而无偿提供给用户的产品(即换件成本费)。
内部质量损失统计管理办法.

内部质量损失统计管理办法1 总则内部质量损失是质量指标体系中一个重要的经济指标,确定和核算内部质量损失目的是降低内部损失,寻求经济合理、用户满意的产品质量水平,优化资源配置,促进,完善公司成本工作,不断提高经济效益和社会效益。
2 目的为加强内部质量损失的管理工作,明确质量损失的统计方法,落实质量损失的责任部门,促使责任部门提高工作质量,减少质量损失,特制定本办法。
3 适用范围适用于本公司内部质量损失统计管理。
4 内部质量损失的定义及构成4.1内部质量损失的定义:指产品交货前,因不能满足规定的质量要求所发生的损失费用。
4.2内部质量损失的构成4.2.1报废损失费用a.因产成品,半成品,在制造过程中达不到质量要求,且无法修复(在经济上不值得修复),造成报废或(库存)所损失的费用。
b.外购元器件、零部件、原材料在搬运、装备等过程中因人为损坏所造成的损失费用。
c.因设计错误、设计改进、工艺错误、工艺改进等造成产成品、半成品、在制造产品及外购元器件、零部件、原材料报废或(库存)所损失的费用。
4.2.2返修损失费为修复不合格品以及因设计错误、设计改进、工艺错误、工艺改进等造成在制品达不到预期要求,进行返修所需支付的费用,包括人工费、材料消耗、更换的零部件、原材料等的费用。
4.3内部质量损失的分类4.3.1制造性质量损失类:指产品在生产制造过程中,由于管理不善操作不当发生的损失费用。
4.3.2技术性质量损失类:指产品因设计错误、设计改进、工艺错误、工艺改进等发生的损失费用。
5 内部质量损失的计算方法5.1报废品损失费用的计算自制报废品损失费=材料费+制造成本-废铁处理价格;外购损失费=采购价格+运输价格+延期损失费;外协、扩散件损失费=材料+运输+延期损失费。
(注:材料价格、外购、扩散延期损失费(由采购部提供);废铁处理价格、运输价格、外协损失费(由计划物控部提供);制造成本(由工艺部提供)。
)5.2返修品损失费用的计算自制返修损失费用=工时费+材料损失费+能耗+运输5.3焊接一次合格率、探伤一次合格率损失费用的计算焊接一次合格率损失费用=返修数×(目标值-实现率)×单价探伤一次合格率损失费=返修数×(目标值-实现率)×单价6 内部质量损失统计规定内部质量损失的统计,按不同类别发生的报废品、返修品,分别由相关部门收集、计算、填报。
关于内外质量损失索赔的有关规定
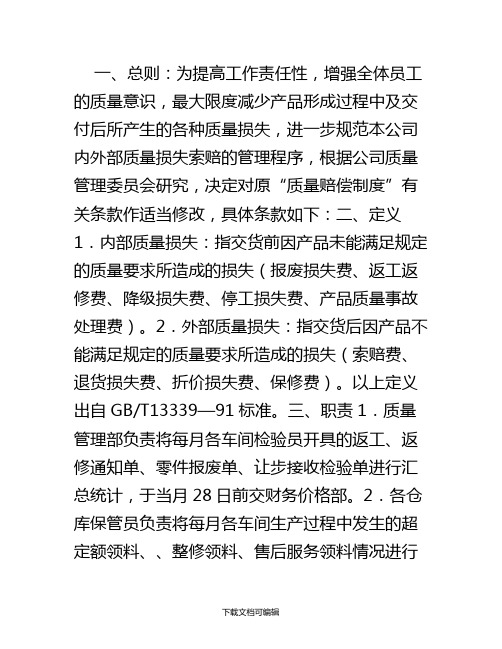
一、总则:为提高工作责任性,增强全体员工的质量意识,最大限度减少产品形成过程中及交付后所产生的各种质量损失,进一步规范本公司内外部质量损失索赔的管理程序,根据公司质量管理委员会研究,决定对原“质量赔偿制度”有关条款作适当修改,具体条款如下:二、定义1.内部质量损失:指交货前因产品未能满足规定的质量要求所造成的损失(报废损失费、返工返修费、降级损失费、停工损失费、产品质量事故处理费)。
2.外部质量损失:指交货后因产品不能满足规定的质量要求所造成的损失(索赔费、退货损失费、折价损失费、保修费)。
以上定义出自GB/T13339—91标准。
三、职责1.质量管理部负责将每月各车间检验员开具的返工、返修通知单、零件报废单、让步接收检验单进行汇总统计,于当月28日前交财务价格部。
2.各仓库保管员负责将每月各车间生产过程中发生的超定额领料、、整修领料、售后服务领料情况进行汇总统计,于当月28日前报财务价格部。
3.销售部负责将每月售后服务所发生的费用进行汇总统计(差旅费、人工费、退货损失费、保修费等)报质量管理部.由质量管理部统计、列出损失费索赔额,填写报表并于当月28日前报财务价格部。
4.财务价格部根据质管部、仓库、销售部反馈的统计数据进行内外质量损失的统计,形成详细的项目报表于次月5日前报公司质量管理委员会工作小组。
四、内外部损失计算1.凡因设计、制造及供方产品质量问题或因销售指令传递失误所造成的材料报废需超定额领料时,必须由所在车间检验员对其报废原因进行判定,并开具报废单。
车间凭检验员签字认可的报废单及领料单方可重新领料,否则仓库不予发料。
对于车间超定额领料同时各仓库保管员将每月各车间超定额领料情况进行汇总统计,于当月28日前报财务价格部,由财务价格部进行核价,统计损失情况。
2.凡因销售指令传递失误或设计、上道工序质量问题所造成的返工、返修,其返工、返修损失按14元/小时计价;属供方厂质量问题所造成的返工返修,则返工、返修损失按其影响程度的大小,分别以5倍、3倍、2倍的14元/小时计价;若供方厂有能力对自已的质量问题进行返工返修的,则按因其停工所带来的损失的大小,分别以5倍、3倍、2倍14元/小时计价;因供方质量问题,但经有关部门和领导批准让步接收的,其损失根据该质量问题的影响程度的大小,按本批物资总额5~10计价。
关于内外质量损失索赔的有关规定
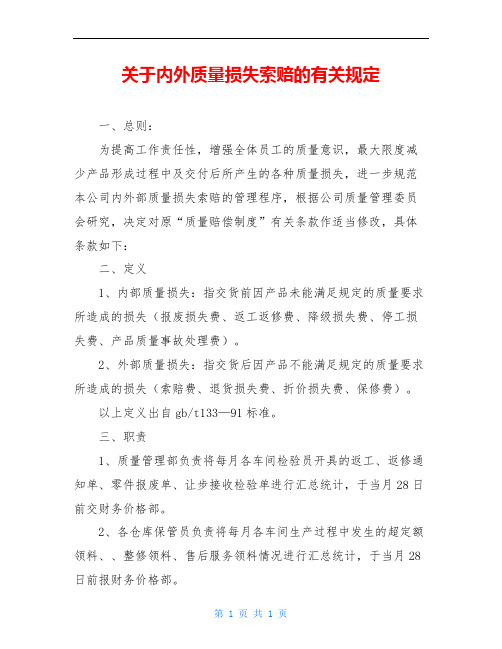
关于内外质量损失索赔的有关规定一、总则:为提高工作责任性,增强全体员工的质量意识,最大限度减少产品形成过程中及交付后所产生的各种质量损失,进一步规范本公司内外部质量损失索赔的管理程序,根据公司质量管理委员会研究,决定对原“质量赔偿制度”有关条款作适当修改,具体条款如下:二、定义1、内部质量损失:指交货前因产品未能满足规定的质量要求所造成的损失(报废损失费、返工返修费、降级损失费、停工损失费、产品质量事故处理费)。
2、外部质量损失:指交货后因产品不能满足规定的质量要求所造成的损失(索赔费、退货损失费、折价损失费、保修费)。
以上定义出自gb/t133—91标准。
三、职责1、质量管理部负责将每月各车间检验员开具的返工、返修通知单、零件报废单、让步接收检验单进行汇总统计,于当月28日前交财务价格部。
2、各仓库保管员负责将每月各车间生产过程中发生的超定额领料、、整修领料、售后服务领料情况进行汇总统计,于当月28日前报财务价格部。
3、销售部负责将每月售后服务所发生的费用进行汇总统计(差旅费、人工费、退货损失费、保修费等)报质量管理部、由质量管理部统计、列出损失费索赔额,填写报表并于当月28日前报财务价格部。
4、财务价格部根据质管部、仓库、销售部反馈的统计数据进行内外质量损失的统计,形成详细的项目报表于次月5日前报公司质量管理委员会工作小组。
四、内外部损失计算1、凡因设计、制造及供方产品质量问题或因销售指令传递失误所造成的材料报废需超定额领料时,必须由所在车间检验员对其报废原因进行判定,并开具报废单。
车间凭检验员签字认可的报废单及领料单方可重新领料,否则仓库不予发料。
对于车间超定额领料同时各仓库保管员将每月各车间超定额领料情况进行汇总统计,于当月28日前报财务价格部,由财务价格部进行核价,统计损失情况。
2、凡因销售指令传递失误或设计、上道工序质量问题所造成的返工、返修,其返工、返修损失按14元/小时计价;属供方厂质量问题所造成的返工返修,则返工、返修损失按其影响程度的大小,分别以5倍、3倍、2倍的14元/小时计价;若供方厂有能力对自已的质量问题进行返工返修的,则按因其停工所带来的损失的大小,分别以5倍、3倍、2倍14元/小时计价;因供方质量问题,但经有关部门和领导批准让步接收的,其损失根据该质量问题的影响程度的大小,按本批物资总额5~10%计价。
关于内外质量损失索赔的有关规定
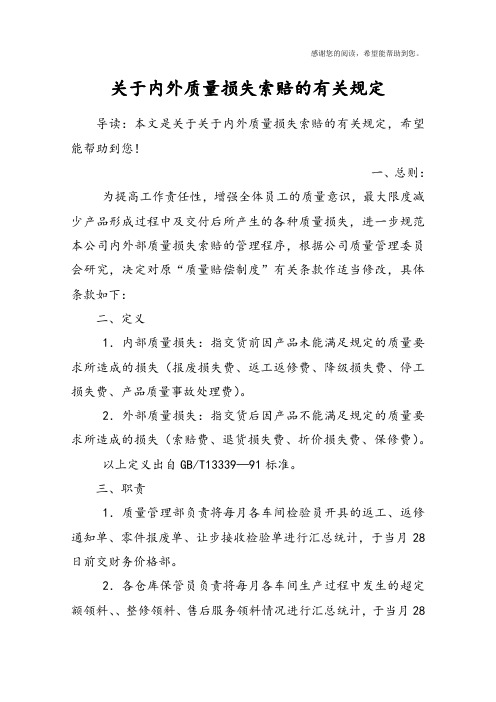
关于内外质量损失索赔的有关规定导读:本文是关于关于内外质量损失索赔的有关规定,希望能帮助到您!一、总则:为提高工作责任性,增强全体员工的质量意识,最大限度减少产品形成过程中及交付后所产生的各种质量损失,进一步规范本公司内外部质量损失索赔的管理程序,根据公司质量管理委员会研究,决定对原“质量赔偿制度”有关条款作适当修改,具体条款如下:二、定义1.内部质量损失:指交货前因产品未能满足规定的质量要求所造成的损失(报废损失费、返工返修费、降级损失费、停工损失费、产品质量事故处理费)。
2.外部质量损失:指交货后因产品不能满足规定的质量要求所造成的损失(索赔费、退货损失费、折价损失费、保修费)。
以上定义出自GB/T13339—91标准。
三、职责1.质量管理部负责将每月各车间检验员开具的返工、返修通知单、零件报废单、让步接收检验单进行汇总统计,于当月28日前交财务价格部。
2.各仓库保管员负责将每月各车间生产过程中发生的超定额领料、、整修领料、售后服务领料情况进行汇总统计,于当月28日前报财务价格部。
3.销售部负责将每月售后服务所发生的费用进行汇总统计(差旅费、人工费、退货损失费、保修费等)报质量管理部.由质量管理部统计、列出损失费索赔额,填写报表并于当月28日前报财务价格部。
4.财务价格部根据质管部、仓库、销售部反馈的统计数据进行内外质量损失的统计,形成详细的项目报表于次月5日前报公司质量管理委员会工作小组。
四、内外部损失计算1.凡因设计、制造及供方产品质量问题或因销售指令传递失误所造成的材料报废需超定额领料时,必须由所在车间检验员对其报废原因进行判定,并开具报废单。
车间凭检验员签字认可的报废单及领料单方可重新领料,否则仓库不予发料。
对于车间超定额领料同时各仓库保管员将每月各车间超定额领料情况进行汇总统计,于当月28日前报财务价格部,由财务价格部进行核价,统计损失情况。
2.凡因销售指令传递失误或设计、上道工序质量问题所造成的返工、返修,其返工、返修损失按14元/小时计价;属供方厂质量问题所造成的返工返修,则返工、返修损失按其影响程度的大小,分别以5倍、3倍、2倍的14元/小时计价;若供方厂有能力对自已的质量问题进行返工返修的,则按因其停工所带来的损失的大小,分别以5倍、3倍、2倍14元/小时计价;因供方质量问题,但经有关部门和领导批准让步接收的,其损失根据该质量问题的影响程度的大小,按本批物资总额5~10%计价。
质量损失管理办法
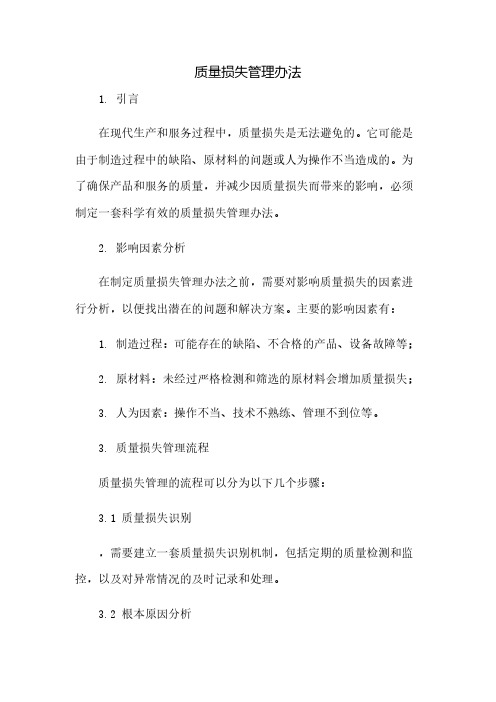
质量损失管理办法1. 引言在现代生产和服务过程中,质量损失是无法避免的。
它可能是由于制造过程中的缺陷、原材料的问题或人为操作不当造成的。
为了确保产品和服务的质量,并减少因质量损失而带来的影响,必须制定一套科学有效的质量损失管理办法。
2. 影响因素分析在制定质量损失管理办法之前,需要对影响质量损失的因素进行分析,以便找出潜在的问题和解决方案。
主要的影响因素有:1. 制造过程:可能存在的缺陷、不合格的产品、设备故障等;2. 原材料:未经过严格检测和筛选的原材料会增加质量损失;3. 人为因素:操作不当、技术不熟练、管理不到位等。
3. 质量损失管理流程质量损失管理的流程可以分为以下几个步骤:3.1 质量损失识别,需要建立一套质量损失识别机制,包括定期的质量检测和监控,以及对异常情况的及时记录和处理。
3.2 根本原因分析一旦质量损失发生,就需要对其根本原因进行深入的分析。
这包括从制造过程、原材料和人为因素等多个角度进行调查和研究,找出问题的真正原因。
3.3 解决方案制定根据根本原因分析的结果,制定相应的解决方案。
这可能包括改进制造工艺、优化原材料选择、培训员工等一系列措施。
3.4 执行及跟踪将制定的解决方案付诸实施,并对其执行情况进行跟踪和监控。
如果发现解决方案效果不佳,及时调整并重新执行。
4. 监控和评估为了确保质量损失管理办法的有效性,需要建立一套监控和评估机制。
定期进行质量损失的统计分析和绩效评估,及时发现问题并采取相应措施。
5. 持续改进质量损失管理办法需要不断改进和完善。
通过对质量损失案例的和经验的积累,制定更加科学和有效的管理办法,提高产品和服务的质量。
6.质量损失是企业无法避免的问题,但通过科学有效的质量损失管理办法,可以减少质量损失的发生和影响。
企业应该建立起完善的质量管理制度,不断提高产品和服务的质量,以满足客户的需求和期望。
质量损失管理办法
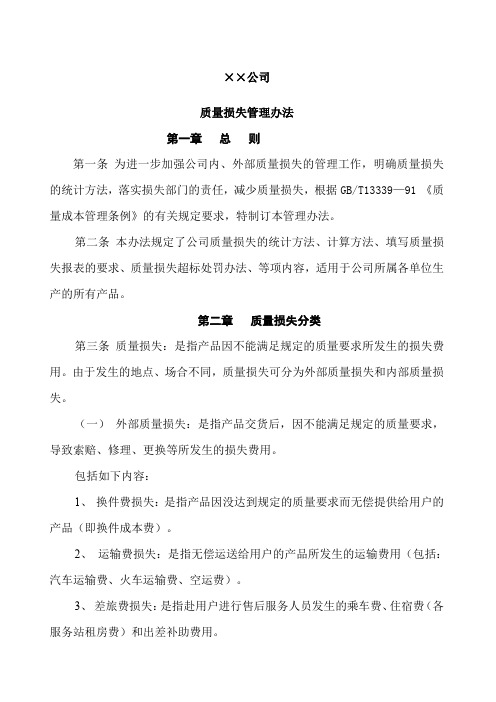
××公司质量损失管理办法第一章总则第一条为进一步加强公司内、外部质量损失的管理工作,明确质量损失的统计方法,落实损失部门的责任,减少质量损失,根据GB/T13339—91 《质量成本管理条例》的有关规定要求,特制订本管理办法。
第二条本办法规定了公司质量损失的统计方法、计算方法、填写质量损失报表的要求、质量损失超标处罚办法、等项内容,适用于公司所属各单位生产的所有产品。
第二章质量损失分类第三条质量损失:是指产品因不能满足规定的质量要求所发生的损失费用。
由于发生的地点、场合不同,质量损失可分为外部质量损失和内部质量损失。
(一)外部质量损失:是指产品交货后,因不能满足规定的质量要求,导致索赔、修理、更换等所发生的损失费用。
包括如下内容:1、换件费损失:是指产品因没达到规定的质量要求而无偿提供给用户的产品(即换件成本费)。
2、运输费损失:是指无偿运送给用户的产品所发生的运输费用(包括:汽车运输费、火车运输费、空运费)。
3、差旅费损失:是指赴用户进行售后服务人员发生的乘车费、住宿费(各服务站租房费)和出差补助费用。
4、话费损失:是指售后服务站和有关人员,在处理用户反映的质量问题时所发生的通讯费用(包括:移动电话通讯费和各服务站使用的非移动电话通讯费)。
(二)内部质量损失:是指产品交货前,因不能满足规定的质量要求所发生的损失费用。
包括如下内容:1、制造性质量损失:是指产品在生产制造过程中,由于管理不善、操作不当发生的损失费用。
由于制造性损失发生的责任不同可分为上工序损失和本工序损失。
上工序损失:是指由于上工序责任而发生的质量损失。
本工序损失:是指由于本单位责任而发生的质量损失。
2、技术性质量损失:是指产品因设计错漏、设计改进发生的损失费用。
第三章质量损失的统计方法第四条售后服务处负责外部质量损失的统计工作,对发生损失项目进行登记入帐。
按附表1《外部质量损失统计表》的要求,把发生的换件损失费、差旅费、运输费、话费逐项填写好后,报质量管理处。
产品质量损失内部索赔管理办法

产品质量损失内部索赔管理办法某某公司管理制度——————————————★———————————————产品质量损失内部索赔管理方法20某某年8月20日发布河北某某公司股份1.目的通过对质量问题造成的损失的责任分解与内部索赔,以促进设计、制造、管理等各环节的质量保持与改善。
2.适用范围本管理制度适用于某某公司产品内部故障损失、外部故障损失的内部索赔。
3.引用文件 FTOP.231034.004.0-20某某《效劳费用索赔管理方法》 FTOP.231010.004.0-20某某《质量考核实施细那么》 4.术语4.1 内部故障损失:指产品在出厂前由于发生质量缺陷而造成的损失,以及为处理质量故障所支付的费用。
4.2外部故障损失:指产品出厂后用户在使用中发现质量缺陷而导致索赔、修理、更换等支付的一切费用和损失总和。
5.职责 5.1质量控制部 5.1.1质量管理科负责《产品质量损失内部索赔管理方法》的制定与索赔争议的协调解决;5.1.2分析改良科负责对客户关系部提出的内部效劳费用信息进行确认,并通知相关责任单位再进行确认。
5.1.3负责宣化工厂相关责任单位的责任分解以及落实、改良;5.1.4质检科负责内部故障损失相关责任单位确实认。
5.1.5质量管理科负责考核额度标准确实定与考核建议的提出。
5.2客户关系部 5.2.1负责对市场实际发生的效劳费用进行统计、汇总、责任划分并对信息和数量的准确性负责;5.3综合管理部 5.3.1北京厂区综合管理部负责技术中心等北京厂区各部门索赔考核建议的执行并在工资里表达; 5.3.2厂部办公室负责宣化工厂索赔建议的执行并在工资里表达。
5.4 制造部 5.4.1各车间、科室负责对市场反应的与本车间、科室有关的质量信息落实相关责任,并采取及时的改良措施。
5.4.2各车间负责本部门内部故障损失的费用核算。
5.5技术中心 5.5.1技术中心产品工程部负责对市场反应的质量信息〔设计责任局部〕落实相关责任,分解到各专业所以及试制试验部。
质量损失管理办法
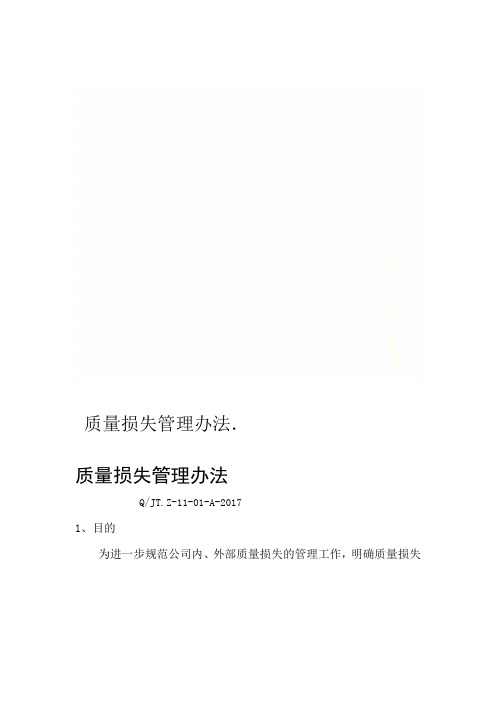
质量损失管理办法.质量损失管理办法Q/JT.Z-11-01-A-20171、目的为进一步规范公司内、外部质量损失的管理工作,明确质量损失的统计方法,落实损失部门的责任,减少质量损失,特制订本管理办法。
2、范围适用于本公司内外部质量损失的统计管理。
3、质量损失的定义及构成3.1 质量损失:是指产品、服务因不能满足规定的质量要求所发生的损失费用。
由于发生的地点、场合不同,质量损失可分为内部质量损失和外部质量损失。
3.2内部质量损失:是指产品交货前,因不能满足规定的质量要求所发生的损失费用。
内部质量损失构成如下:3.2.1报废损失费用a.因产成品,半成品,在制造过程中达不到质量要求,且无法修复(在经济上不值得修复),造成报废或(库存)所损失的费用。
b.外购元器件、零部件、原材料在搬运、装配等过程中因人为损坏所造成的损失费用。
c.因设计错误、设计改进、工艺错误、工艺改进等造成产成品、半成品、在制造产品及外购元器件、零部件、原材料报废或(库存)所损失的费用。
报废损失按损失性质来分可分成工废和料废两类,其中料废是指因材料本身质量问题引起的报废,而工废是指加工过程中因人、设备损坏等造成的报废;也可以按损失原因来分类,可分为制造性质量损失和技术性质量损失两类,其中制造性质量损失是指产品在生产制造过程中,由于管理不善操作不当发生的损失费用,技术性质量损失是2指产品因设计错误、设计改进、工艺错误、工艺改进等发生的损失费用。
3.2.2返修损失费为修复不合格品以及因设计错误、设计改进、工艺错误、工艺改进等造成在制品达不到预期要求,进行返修所需支付的费用,包括人工费、材料消耗、更换的零部件、原材料等的费用。
3.2.3因质量问题发生的停工损失:3.2.4质量事故处理费:3.2.5质量降级损失:3.3外部质量损失:是指产品交货后,因不能满足规定的质量要求,导致索赔、修理、更换等所发生的损失费用。
3.3.1换件费损失:是指产品因没达到规定的质量要求而无偿提供给用户的产品(即换件成本费)。
产品质量等级品率和质量损失率管理办法

产品质量等级品率和质量损失率管理办法1目的产品质量等级品率是质量指标体系的重要指标之一。
该指标反应企业产品的质量水平及变化情况,有利于促进企业技术进步,促进调整产品结构,满足消费者不同档次的需求,同时有利于优化资源配置和企业的投资方向,为企业制定质量政策提供依据。
与此同时,企业为降低产品质量损失率,寻求经济合理、用户满意的产品质量水平,促进、完善本公司内部损失成本和外部损失成本的管理工作,特制定并执行本办法。
2范围本办法规定了质量等级品率(包括优等品产值率、一等品产值率、合格品产值率)的确定原则、计算公式、统计范围及判定原则。
本办法规定了质量损失率的确定原则、计算公式、内部损失成本和外部损失成本的核算范围,以及内部损失和外部损失数据的采集、核算、分析及传递的途径;规定了质量损失率的考核办法。
本办法适用于本公司对产品质量等级品率的确定和计算。
本办法适用于本公司内部损失成本、外部损失成本统计,质量损失率的核算、分析、报告及考核。
3规范性引用文件下列文件中的条款通过本标准的引用而成为本标准的条款。
凡是注日期的引用文件,其随后所有的修改单(不包括勘误的内容)或修订版均不适用于本标准,然而,鼓励根据本标准达成协议的各方研究是否可使用这些文件的最新版本。
凡是不注日期的引用文件,其最新版本适用于本标准。
GB/T 19000质量管理体系基础和术语GB/T 13340-1991产品质量等级品率的确定和计算方法GB/T 13341-1991产品质量损失率的确定和计算方法GB/T 12707-1991工业产品质量分等导则4术语4.1产品质量等级品率报告期加权分等产品产值之和(即加权优等品产值、加权一等品产值和加权合格品产值之和)与同期分等产品总产值(即优等品产值、一等品产值与合格品产值之和)之比。
4.2质量损失率产品质量成本中的内部损失成本、外部损失成本之和与工业总产值之比。
4.3质量成本将产品质量保持在规定的水平上所需的费用。
汽车企业质量管理部门制度--质量损失统计考核管理规定

质量损失统计考核管理规定一、目的为了明确质量损失的统计方法,加强质量损失的管理工作,落实质量损失的责任车间、部室,促使车间、部室提高工作质量,减少质量损失,特制定本制度。
二、适用范围适用于xxxxxxx汽车内外部质量损失统计管理与考核。
三、职责(职责见附件1)四、关键控制点(流程见附件2)质量损失是指产品因不能满足规定的质量要求或用户需求,所发生的损失费用。
由于发生的地点、场合、性质不同,质量损失分为外部质量损失和内部质量损失,索赔费用由供应商或责任单位赔付的只做统计,不纳入公司质量损失。
(一)外部质量损失:是指产品出厂后因不能满足规定的质量要求,导致索赔、修复、更换等所发生的损失费用,包括以下内容:1.用户或客户索赔费用损失:是指因质量事故造成,通过鉴定、确认赔付的费用(包括:更换车辆、相关损失等)。
2.换件费损失:是指产品因没达到规定的质量要求而无偿提供给用户的零部件(即换件成本费)。
3.运输费损失:是指因产品质量问题无偿运送给用户所发生的运输费用(包括:汽车运输费、大车运输费、空运费)。
4.差旅费损失:是指赴用户进行售后服务人员发生的乘车费、住宿费和出差补助费用。
5.话费损失:是指服务部和有关人员,在处理用户反映的质量问题时所发生的通讯费用。
(二)内部质量损失:是指产品出厂前,因不能满足规定的质量要求所发生的损失费用。
1.报废损失费用(1)因成品、半成品,在制造过程中达不到质量要求,且无法修复或在经济上不值得修复,造成直接报废或封存所损失的费用。
(2)外购零部件、原材料在搬运、装配等过程中因人为损坏所造成的损失费用。
(3)因设计错误、设计改进、工艺错误、工艺改进等造成产品、半成品、在制品及零部件、原材料直接报废或封存所损失的费用。
2.返修损失费用为修复不合格品以及因设计错误、设计改进、工艺错误、工艺改进等造成在制品达不到预期要求,进行返修所需支付的费用,包括人工费、材料消耗、更换的零部件、原材料等费用。
质量损失核算管理办法

STL/QB有限公司企业标准质量损失核算管理办法广东史特牢紧扣系统有限公司发布前言本标准由总经理室提出。
本标准由总经理室负责起草。
本标准由总经理室归口管理并负责解释。
本标准已由管理者代表组织各单位负责人评审、检讨修正,呈阅总经理批准。
本标准于2021年6月5日首次发布。
质量损失核算管理办法1、目的和范围:1.1明确质量成本管理的基本原则和实施质量成本预测、计划、核算、分析、控制、考核和报告等环节的方法、内容和程序。
1.2 适用于对各项质量成本的收集、汇总、分析、改进控制活动。
2、定义:2.1 质量成本:将产品质量保持在规定的质量水平上所需的费用。
它是企业生产总成本的一个组成部分。
2.2 预防成本:用于预防产生不合格品或发生故障所需的各项费用。
2.3 鉴定成本:评定产品是否满足规定的质量要求所需的费用。
2.4 内部损失成本:产品交货前因不满足规定的质量要求而支付的有关费用。
2.5 外部损失成本:产品交货后因不满足规定的质量要求,导致索赔、修理、更换或信誉损失等而支付的费用。
2.6 外部质量保证成本:为提供用户要求的客观证据所支付的费用。
它包括特殊的和附加的质量保证措施、程序、数据、证实试验和评定的费用。
3、管理职责:3.1 财务部为质量成本管理的归口综合部门:3.1.1 制订年度质量成本目标;3.1.2 确定质量成本科目;3.1.3 组织收集质量成本数据,并进行统计、核算;3.1.4 组织质量成本经济分析,定期向总/副经理提供质量成本经济分析报告和有关资料;3.1.5 编制并提供质量成本数据收集、统计、核算及经济分析所需报表。
3.2 管理者代表:3.2.1 组织落实、监督、考核质量成本目标;3.2.2 负责质量成本的综合分析工作,定期向领导提供质量成本报告;3.2.3 根据质量成本综合分析结果,制订质量改进计划。
3.3 总经理:3.3.1 负责改进计划的审批和组织落实;3.3.2 对有争议的质量成本责任作出仲裁。
对质量损失的考核办法
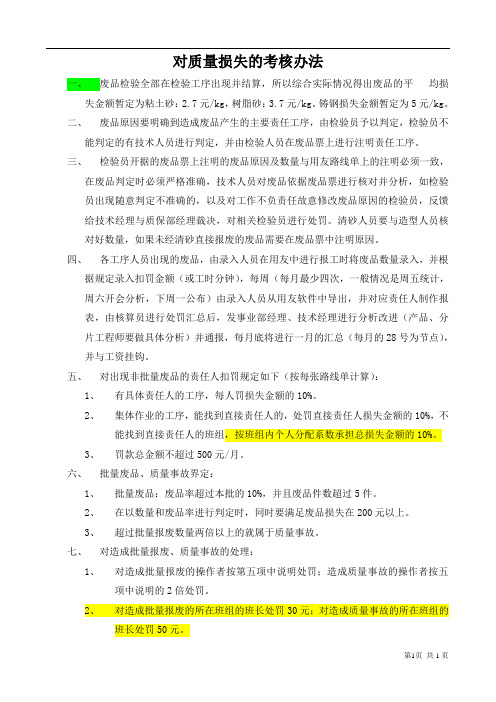
对质量损失的考核办法一、废品检验全部在检验工序出现并结算,所以综合实际情况得出废品的平均损失金额暂定为粘土砂:2.7元/kg,树脂砂:3.7元/kg。
铸钢损失金额暂定为5元/kg。
二、废品原因要明确到造成废品产生的主要责任工序,由检验员予以判定,检验员不能判定的有技术人员进行判定,并由检验人员在废品票上进行注明责任工序。
三、检验员开据的废品票上注明的废品原因及数量与用友路线单上的注明必须一致,在废品判定时必须严格准确,技术人员对废品依据废品票进行核对并分析,如检验员出现随意判定不准确的,以及对工作不负责任故意修改废品原因的检验员,反馈给技术经理与质保部经理裁决,对相关检验员进行处罚。
清砂人员要与造型人员核对好数量,如果未经清砂直接报废的废品需要在废品票中注明原因。
四、各工序人员出现的废品,由录入人员在用友中进行报工时将废品数量录入,并根据规定录入扣罚金额(或工时分钟),每周(每月最少四次,一般情况是周五统计,周六开会分析,下周一公布)由录入人员从用友软件中导出,并对应责任人制作报表,由核算员进行处罚汇总后,发事业部经理、技术经理进行分析改进(产品、分片工程师要做具体分析)并通报,每月底将进行一月的汇总(每月的28号为节点),并与工资挂钩。
五、对出现非批量废品的责任人扣罚规定如下(按每张路线单计算):1、有具体责任人的工序,每人罚损失金额的10%。
2、集体作业的工序,能找到直接责任人的,处罚直接责任人损失金额的10%,不能找到直接责任人的班组,按班组内个人分配系数承担总损失金额的10%。
3、罚款总金额不超过500元/月。
六、批量废品、质量事故界定:1、批量废品:废品率超过本批的10%,并且废品件数超过5件。
2、在以数量和废品率进行判定时,同时要满足废品损失在200元以上。
3、超过批量报废数量两倍以上的就属于质量事故。
七、对造成批量报废、质量事故的处理:1、对造成批量报废的操作者按第五项中说明处罚;造成质量事故的操作者按五项中说明的2倍处罚。
产品质量等级品率和质量损失率管理规定

产品质量等级品率和质量损失率管理规定This model paper was revised by the Standardization Office on December 10, 2020产品质量等级品率和质量损失率管理办法1 目的产品质量等级品率是质量指标体系的重要指标之一。
该指标反应企业产品的质量水平及变化情况,有利于促进企业技术进步,促进调整产品结构,满足消费者不同档次的需求,同时有利于优化资源配置和企业的投资方向,为企业制定质量政策提供依据。
与此同时,企业为降低产品质量损失率,寻求经济合理、用户满意的产品质量水平,促进、完善本公司内部损失成本和外部损失成本的管理工作,特制定并执行本办法。
2 范围本办法规定了质量等级品率(包括优等品产值率、一等品产值率、合格品产值率)的确定原则、计算公式、统计范围及判定原则。
本办法规定了质量损失率的确定原则、计算公式、内部损失成本和外部损失成本的核算范围,以及内部损失和外部损失数据的采集、核算、分析及传递的途径;规定了质量损失率的考核办法。
本办法适用于本公司对产品质量等级品率的确定和计算。
本办法适用于本公司内部损失成本、外部损失成本统计,质量损失率的核算、分析、报告及考核。
3 规范性引用文件下列文件中的条款通过本标准的引用而成为本标准的条款。
凡是注日期的引用文件,其随后所有的修改单(不包括勘误的内容)或修订版均不适用于本标准,然而,鼓励根据本标准达成协议的各方研究是否可使用这些文件的最新版本。
凡是不注日期的引用文件,其最新版本适用于本标准。
GB/T 19000 质量管理体系基础和术语GB/T 13340-1991 产品质量等级品率的确定和计算方法GB/T 13341-1991 产品质量损失率的确定和计算方法GB/T 12707-1991 工业产品质量分等导则4 术语4.1产品质量等级品率报告期加权分等产品产值之和(即加权优等品产值、加权一等品产值和加权合格品产值之和)与同期分等产品总产值(即优等品产值、一等品产值与合格品产值之和)之比。
内部质量损失统计与索赔办法

受控编号:内部质量损失统计与索赔办法编制审核批准发布实施文件说明内部质量损失统计与索赔办法1 目的为了进一步贯彻“谁干谁负责”的工作理念,落实质量责任并形成责任赔偿机制,从而提高员工在产品制造过程中的工作质量,特制定本管理办法。
本办法是公司对于在生产制造过程中发生的因工作质量、配套件质量等原因造成的质量损失的一种责任赔偿规定。
2 范围本办法适用于公司生产流程内部(不包括进厂检验)质量损失的统计和工序间质量索赔。
3 职责3.1 资产财务部负责内部质量损失费用的核对、汇总、建账,确保费用清晰。
3.2 各单位负责各自区域发生的因不合格造成的质量损失的计算、统计汇总、分类和上报,对质量损失统计的正确性和完整性负责。
负责分厂内各工序及工序间质量损失责任的落实,同时承担分厂间质量索赔的分析和具体责任人的落实。
3.3 质量保证部负责内部质量损失信息的汇总、统计及分类,以及对分厂上报的内部损失报表的监督和核实,负责分厂间质量索赔考核。
3.4 企业管理部负责损失索赔的兑现管理。
3.5 物资供应部负责与供方签订《质量服务保证协议》,明确质量损失索赔要求,负责对因供方质量问题造成损失向供方索赔,对索赔工作的完成效果负责。
4 内部质量损失的核算统计方法4.1 公司内部质量损失包括报废损失、返工返修损失、误工损失及异常批量质量问题处理费损失四项内容,结合公司各部门的生产实际,同时考虑质量损失统计的可操作性,确定以下核算方法:4.1.1 报废损失包括直接材料损失和废品加工工时损失,直接材料损失以分厂开出的注明工废或料废的领料单进行核算,统计表中不再重复核算;废品加工工时损失根据工时单价和损失工时进行核算。
4.1.2 工时损失的统计包括零部件生产需要的人工成本、设备损耗、照明、水电等成本,考虑质量损失统计的可操作性,将各部门工资、设备损耗、照明、水电等成本与人工工时进行平均,确定各部门(分厂)平均工时单价为:下料分厂:10元/小时,钢结构分厂:15 元/小时,结构分厂:15 元/小时,机加工分厂:15 元/小时,零部件分厂:15 元/小时,齿轮分厂:15元/小时,各装配分厂:20元/小时,涂装分厂:20 元/小时。
- 1、下载文档前请自行甄别文档内容的完整性,平台不提供额外的编辑、内容补充、找答案等附加服务。
- 2、"仅部分预览"的文档,不可在线预览部分如存在完整性等问题,可反馈申请退款(可完整预览的文档不适用该条件!)。
- 3、如文档侵犯您的权益,请联系客服反馈,我们会尽快为您处理(人工客服工作时间:9:00-18:30)。
内部质量损失统计管理办法
1 总则
内部质量损失是质量指标体系中一个重要的经济指标,确定和核算内部质量损失目的是降低内部损失,寻求经济合理、用户满意的产品质量水平,优化资源配置,促进,完善公司成本工作,不断提高经济效益和社会效益。
2 目的
为加强内部质量损失的管理工作,明确质量损失的统计方法,落实质量损失的责任部门,促使责任部门提高工作质量,减少质量损失,特制定本办法。
3 适用范围
适用于本公司内部质量损失统计管理。
4 内部质量损失的定义及构成
4.1内部质量损失的定义:指产品交货前,因不能满足规定的质量要求所发生的损失费用。
4.2内部质量损失的构成
4.2.1报废损失费用
a.因产成品,半成品,在制造过程中达不到质量要求,且无法修复(在经济上不值得修复),造成报废或(库存)所损失的费用。
b.外购元器件、零部件、原材料在搬运、装备等过程中因人为损坏所造成的损失费用。
c.因设计错误、设计改进、工艺错误、工艺改进等造成产成品、半成品、在制造产品及外购元器件、零部件、原材料报废或(库存)所损失的费用。
4.2.2返修损失费
为修复不合格品以及因设计错误、设计改进、工艺错误、工艺改进等造成在制品达不到预期要求,进行返修所需支付的费用,包括人工费、材料消耗、更换的零部件、原材料等的费用。
4.3内部质量损失的分类
4.3.1制造性质量损失类:指产品在生产制造过程中,由于管理不善操作不当发生的损失费用。
4.3.2技术性质量损失类:指产品因设计错误、设计改进、工艺错误、工艺改进等发生的损失费用。
5 内部质量损失的计算方法
5.1报废品损失费用的计算
自制报废品损失费=材料费+制造成本-废铁处理价格;
外购损失费=采购价格+运输价格+延期损失费;
外协、扩散件损失费=材料+运输+延期损失费。
(注:材料价格、外购、扩散延期损失费(由采购部提供);废铁处理价格、运输价格、外协损失费(由计划物控部提供);制造成本(由工艺部提供)。
)
5.2返修品损失费用的计算
自制返修损失费用=工时费+材料损失费+能耗+运输
5.3焊接一次合格率、探伤一次合格率损失费用的计算
焊接一次合格率损失费用=返修数×(目标值-实现率)×单价
探伤一次合格率损失费=返修数×(目标值-实现率)×单价
6 内部质量损失统计规定
内部质量损失的统计,按不同类别发生的报废品、返修品,分别由相关部门收集、计算、填报。
6.1因分厂造成的报废、返修,由工艺部负责收集、计算,按附件1:内部质量损失统计表填报。
6.2因设计错误、设计改进造成的报废、返修,由分厂负责收集、计算,按附件1:内部质量损失统计表填报。
6.3因工艺错误、工艺改进造成的报废、返修,由分厂负责收集、计算,按附件1:内部质量损失统计表填报。
6.4各分厂的焊接一次合格率、探伤一次合格率未达目标而造成的质量损失,由质管部各质检站负责收集、计算,按附件2:焊接、探伤损失统计表填报。
6.5内部质量损失统计表和焊接、探伤损失统计表按月进行统计,各责任部门于次月4日前将统计表发质管部汇总备案,质管部将汇总的统计表报财务部。
7 责任追究
7.1填报质量损失的部门,应认真对待,事实求是,如实、准确、按时填写相关的内部质量损失统计表和焊接、探伤损失统计表。
7.2对故意夸大事实填报或包庇隐瞒未填报损失的责任部门或个人视情节轻重每次考核100-500元。
7.3对填报损失表不认真,出现较多错漏,对责任部门或个人每次考核50元。
7.4对不按时填表损失表,每拖延一天考核责任部门或个人20元。
8 本办法从2011年9月1日起执行。
9、附件:
附件1、内部质量损失统计表
4附件2、焊接、探伤损失统计表
四川川润动力设备有限公司
二0一一年八月九日拟制:丁惠审核:陈申明批准:王辉
附件1
内部质量损失统计表
填写部门:年月日
页脚内容4
页脚内容5
附件2
焊接、探伤损失统计表
填写部门:年月日
页脚内容6
页脚内容7。