铝型材生产工艺技术 2分析
6082铝合金挤压铝型材生产工艺研究

6082铝合金挤压铝型材生产工艺研究1.前言本文对6082铝合金应用于挤压型材生产进行了试验研究,以确定合适的熔铸和挤压工艺制度。
2.熔铸工艺2.1化学成分GB/T3190 -1996中6082铝合金化学成分见表1image2.2成分控制6082铝合金成分具有两个主要特点:第一,含有适量的Mn和Cr;第二,Mg、Si含量相对较高。
其中,Mn、Cr等合金元素可阻碍挤压时和挤压后发生再结晶或再结晶晶粒长大,细化晶粒。
但(Mn + Cr) 总量过高可能形成分别含Mn、Cr的粗大第二相,削弱Mg2Si相的沉淀强化效果,抵消其阻碍再结晶和细化晶粒的作用。
同时,Mn、Cr元素会增大6082铝合金的淬火敏感性。
且易在α(Al)相中产生严重的晶内偏析,造成挤压制品粗晶组织,降低型材氧化着色效果。
对于Mg、Si成分,6082铝合金在Mg2Si强化的同时,通过增加适量过剩Si来促进强化。
因此,重点对Mn的含量进行试验确定:以Mn含量为0.6% ~0.65%及0.9%~0.95%进行对比。
发现Mn含量偏上限时,制品尾部粗晶组织较多,且力学性能偏低,所以对比确定Mn含量的优化范围为0. 6% ~0.65%。
Cr的含量宜控制在0.15%以下,(Mn + Cr)总量控制在0.70% ~0.80%范围内。
Mg2Si含量宜控制在1.5% ~ 1.6%,过剩Si含量控制在0.3%左右。
2.3工艺控制由于6082铝合金最大的特点是含难熔金属Mn,Mn的适量存在易引起晶内偏析及固液区塑性降低,导致抗裂能力不足,故熔铸工艺主要需注意三点:第一,熔炼应注意控制温度在740 760℃间并搅拌均匀,保证金属完全熔化、温度准确、成分均匀。
第二,铸造应考虑金属Mn增大了合金的粘度,使其流动性下降,影响了合金铸造性能。
铸造速度要适当降低,控制在80100mm/min范围内。
第三,加大冷却强度,加快冷却速度,以利于消除晶内偏析现象。
控制一次冷却强度,加大二次冷却强度以减少铸造时产生的应力集中,避免产生铸锭裂纹缺陷。
(工艺技术)铝材加工工艺
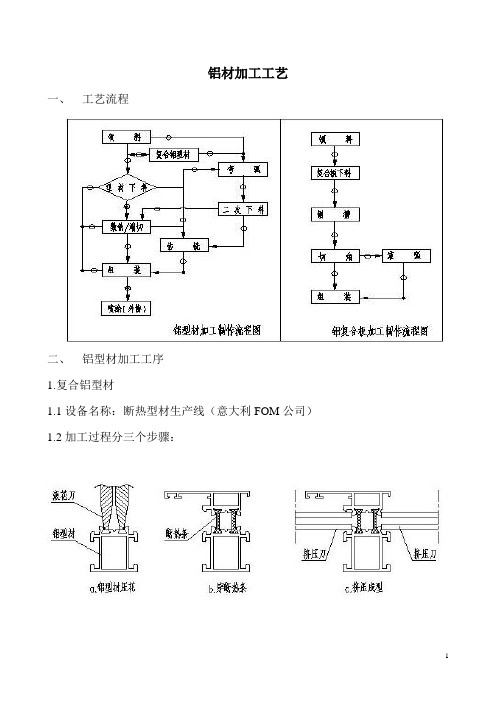
铝材加工工艺一、工艺流程二、铝型材加工工序1.复合铝型材1.1设备名称:断热型材生产线(意大利FOM公司)1.2加工过程分三个步骤:a.型材压花:用滚花刀在铝型材槽口上压花。
b.穿断热条:将断热条穿在已压花的铝型材槽口内。
c.挤压成型:将铝型材和断热条用挤压刀复合后在一起。
1.3检验1.3.1检验设备:抗剪实验机1.3.2取样:在距型材端头200mm以外取样L=100mm。
1.3.3标准:剪切力H(Kg)符合250≤H≤6001.4注意事项:1.4.1铝型材截面尺寸:宽240mm,高180mm。
1.4.2挤压刀具有效尺寸:60mm,即铝型材外端距挤压部位尺寸L<60mm。
1.4.3铝型材不能与刀具干涉,一般挤压部位应高出2mm。
2.铝型材下料2.1设备:双头锯型号:DG244适用范围:加工长度335~6000 加工角度90°~45°任意角调整范围:锯片调整角度90°~45°工作台调整角度22.5°~90°~140°加工精度:尺寸允差±0.2 角度允差±6′其他:锯片最大直径φ550 锯片升起最大高度200主要用途:铝型材切断、切角。
2.2设备:单头锯型号:MGS205适用范围:加工长度15~450 加工角度90°~45°任意角调整范围:锯片调整角度90°~45°工作台调整角度22.5°~90°~140°加工精度:尺寸允差±0.5 角度允差±15′其他:锯片最大直径φ550 锯片升起最大高度200主要用途:铝型材切断、切角。
2.3设备:单头自动送料切割机型号:SA142适用范围:加工长度5.5~150加工精度:尺寸允差±0.3主要用途:铝型材切断(自动送料、切料)。
3.铝型材端切3.1设备:端铣机型号:AKS134适用范围:最大切削高度160;最大切削深度135;最大切削长度250。
铝型材年度总结报告(3篇)

第1篇一、前言随着我国经济的快速发展,铝型材行业作为国家重要的基础材料产业,近年来取得了显著的成绩。
本报告旨在总结过去一年铝型材行业的发展情况,分析存在的问题,并提出未来发展的建议。
二、行业发展概况1. 市场规模稳步增长:据统计,我国铝型材市场在过去一年保持了稳步增长的趋势,产量达到XX万吨,同比增长XX%。
其中,建筑型材、交通运输型材、装饰型材等细分市场均有所提升。
2. 技术创新不断突破:行业企业在技术创新方面取得了显著成果,如高性能铝合金、复合材料等新型材料的研发与应用,以及生产设备的升级换代。
3. 产业布局逐步优化:铝型材行业产业布局逐渐优化,区域集中度提高,优势企业不断扩大市场份额,产业竞争力增强。
三、存在的问题1. 原材料价格波动:受国际市场影响,铝锭等原材料价格波动较大,给企业生产带来一定压力。
2. 产能过剩:部分地区铝型材产能过剩,市场竞争激烈,导致产品价格下降,企业盈利能力减弱。
3. 环保压力:随着国家对环保要求的提高,铝型材企业面临较大的环保压力,生产成本上升。
四、应对措施1. 加强行业自律:企业应加强行业自律,共同维护市场秩序,避免恶性竞争。
2. 优化产品结构:企业应加大研发投入,提高产品附加值,拓展高端市场。
3. 提高资源利用效率:企业应采用先进的生产工艺和设备,提高资源利用效率,降低生产成本。
4. 加强环保治理:企业应加大环保投入,采用环保技术,减少污染物排放。
五、未来展望展望未来,铝型材行业将继续保持稳定发展态势。
随着国家政策的支持和市场需求的增长,铝型材行业有望实现以下目标:1. 市场占有率提升:铝型材在建筑、交通运输、装饰等领域的应用将更加广泛,市场占有率有望进一步提升。
2. 技术创新取得突破:企业将加大技术创新力度,开发更多高性能、环保型铝型材产品。
3. 产业格局优化:行业集中度将进一步提高,优势企业将占据更大的市场份额。
总之,铝型材行业在过去一年取得了显著成绩,但也面临着诸多挑战。
高强度中空铝型材成形工艺研究

高强度中空铝型材成形工艺研究一、引言介绍中空铝型材的发展背景及其在工程领域的应用价值,指出存在的成形难题及本文研究的目的和意义。
二、相关技术综述对现有的中空铝型材成形工艺进行总结和评价,包括传统的挤压成形、拉伸成形、壳模成形,以及近年来出现的多弯曲工艺、高压水流冲压和粉末沉积成型技术。
三、中空铝型材成形工艺设计介绍基于中空铝型材的特性和应用要求,以及各种成形工艺的优缺点,设计出适合中空铝型材成形的工艺流程,详细论述流程中每一个环节的实现方法。
四、高强度中空铝型材成形实验根据之前设计出的工艺流程,进行成形实验,检验各项参数的合理性和成形效果。
对结果进行数据统计分析,得出关键参数对成形结果的影响规律,并进行实验验证。
五、结论与展望总结本文的研究内容及实验结果,指出其在实际应用中的针对性和可行性。
进一步提出未来中空铝型材成形方面的发展方向和研究重点,为相关产业的发展提供指导意见。
注:以上仅为提纲,具体内容和细节需要根据研究内容具体情况进行拓展。
一、引言随着现代工业技术的不断发展,中空铝型材作为一种轻质、高强度、高刚度的新型材料,已经得到广泛的应用。
在建筑、汽车、电子、航空航天等行业中,中空铝型材产品已成为不可替代的材料之一。
然而,中空铝型材的成形仍然是一个存在着许多技术难题的领域。
传统的成形技术往往无法满足高质量、高效率的需求。
因此,本文旨在研究中空铝型材的高强度成形工艺,为中空铝型材的应用推广和提高提供技术支持。
在本文中,我们将全面调研和综述目前已有的中空铝型材成形技术,并探讨了不同技术的优缺点及其适用范围。
在此基础上,我们设计了一种针对中空铝型材成形的高强度工艺,并进行了成形实验。
最后,我们总结了本文研究的过程和结论,并对中空铝型材成形技术未来的发展方向和研究重点进行了探讨。
二、相关技术综述目前,中空铝型材的成形技术已经得到了广泛的应用,主要包括传统的挤压成形、拉伸成形、壳模成形,以及近年来出现的多弯曲工艺、高压水流冲压和粉末沉积成型技术等。
铝型材的表面处理工艺

铝型材的表面处理工艺铝型材的表面处理工艺1. 介绍铝型材的表面处理工艺是指对铝型材进行一系列的物理、化学处理,以改善其表面性能和外观质量的一项重要工艺。
通过表面处理,可以增加铝型材的耐腐蚀性、耐磨性,提高其整体美观度和装饰效果。
2. 表面处理工艺分类铝型材的表面处理工艺主要包括以下几种分类:电化学氧化•阴极电泳涂装:采用直流电极化的方式,将阴极涂料溶解于水中,通过电解沉积在阳极氧化膜上。
•阳极氧化:将铝型材浸泡在电解液中,使其成为阳极,通过电流使表面氧化形成氧化膜。
化学处理•酸洗:通过浸泡在酸溶液中,去除表面油污、氧化皮、锈蚀物等杂质。
•碱洗:用碱性溶液对铝型材表面进行清洁、脱脂、除去氧化层等处理。
机械处理•抛光:通过机械磨削和抛光,使铝材表面获得高光泽度和光洁度。
•刷砂:通过金刚砂轮刷刷砂,使铝材表面呈现一定的纹理和粗糙度。
3. 表面处理工艺的应用表面处理工艺在铝型材的生产和应用中起到至关重要的作用。
•建筑领域:铝型材作为建筑材料广泛应用,经过表面处理可以提高其美观度和耐候性。
•汽车零部件:铝型材作为汽车零部件应用广泛,经过表面处理可以提高其耐腐蚀性和耐磨性。
•电子电器:铝型材在电子电器行业中也有重要应用,经过表面处理可以提高其导电性。
4. 注意事项在进行铝型材表面处理时,需要注意以下几点:•操作规范:需要严格按照处理工艺要求进行操作,确保处理效果的稳定性和一致性。
•处理环境:处理过程需要在相应的环境条件下进行,如温度、湿度等。
•安全措施:处理过程中需要注意安全事项,避免酸碱溶液的直接接触皮肤和眼睛。
5. 结论铝型材的表面处理工艺在提高其性能、外观和质量方面起着重要的作用。
通过选择合适的表面处理工艺,可以满足不同领域对铝型材的需求,并提供优质的铝型材产品。
值得注意的是,合理的操作规范和安全措施都是保证处理效果和人员安全的关键。
6. 表面处理工艺的发展趋势随着科技的不断进步和市场对高品质产品的需求,铝型材的表面处理工艺也在不断发展和创新。
大型铝合金型材的热挤压方法
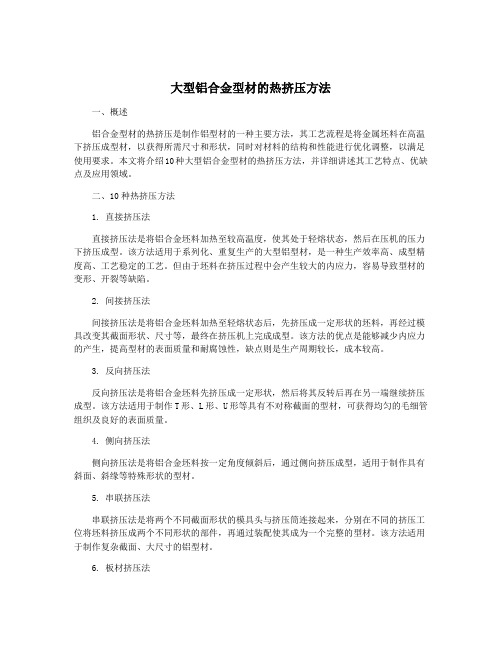
大型铝合金型材的热挤压方法一、概述铝合金型材的热挤压是制作铝型材的一种主要方法,其工艺流程是将金属坯料在高温下挤压成型材,以获得所需尺寸和形状,同时对材料的结构和性能进行优化调整,以满足使用要求。
本文将介绍10种大型铝合金型材的热挤压方法,并详细讲述其工艺特点、优缺点及应用领域。
二、10种热挤压方法1. 直接挤压法直接挤压法是将铝合金坯料加热至较高温度,使其处于轻熔状态,然后在压机的压力下挤压成型。
该方法适用于系列化、重复生产的大型铝型材,是一种生产效率高、成型精度高、工艺稳定的工艺。
但由于坯料在挤压过程中会产生较大的内应力,容易导致型材的变形、开裂等缺陷。
2. 间接挤压法间接挤压法是将铝合金坯料加热至轻熔状态后,先挤压成一定形状的坯料,再经过模具改变其截面形状、尺寸等,最终在挤压机上完成成型。
该方法的优点是能够减少内应力的产生,提高型材的表面质量和耐腐蚀性,缺点则是生产周期较长,成本较高。
3. 反向挤压法反向挤压法是将铝合金坯料先挤压成一定形状,然后将其反转后再在另一端继续挤压成型。
该方法适用于制作T形、L形、U形等具有不对称截面的型材,可获得均匀的毛细管组织及良好的表面质量。
4. 侧向挤压法侧向挤压法是将铝合金坯料按一定角度倾斜后,通过侧向挤压成型,适用于制作具有斜面、斜缘等特殊形状的型材。
5. 串联挤压法串联挤压法是将两个不同截面形状的模具头与挤压筒连接起来,分别在不同的挤压工位将坯料挤压成两个不同形状的部件,再通过装配使其成为一个完整的型材。
该方法适用于制作复杂截面、大尺寸的铝型材。
6. 板材挤压法板材挤压法是将板材加热后,在挤压机中通过辊式挤压成型,该方法适用于制作厚壁型材,具有成型精度高、产品密度均匀、机械性能优良等优点。
7. 双挤压法双挤压法是将两个不同截面形状的模具头安装在同一挤压机内,同时对坯料进行两次挤压成型。
该方法适用于制作较复杂的型材,如圆形、方形、六边形等复杂几何形状的铝型材。
铝型材的简介及生产工艺

铝型材的简介及生产工艺铝型材的简介及生产工艺一、铝型材性能要求A.铝材1.以下的合金种类及硬度的组合若符合生产加工、表面处理及性能要求的规定,则可用于制作铝型材:6063-T5、6063-T6、6105-T5、6061-T6。
其它6xxx系列的合金若达到本技术要求的规定亦可送审供核准。
铝型材的厚度在满足性能要求的基础上不能低于下列要求:a.主要铝型材:3.0mm。
b.玻璃周边的盖板及非结构性装饰条:1.5mm。
c.所有铝型材必须为建筑用高级产品,其容许加工误差应满足《GB/T 5237 - 铝合金建筑型材的规定》。
其材料应达到《GB/T 3190 - 变形铝及铝合金化学成分》的要求。
d.所有送审的铝型材应一并附上模具图显示满足上述材料壁厚的要求,并存档。
2.以下的合金种类及硬度的组合若符合加工、表面处理及性能要求的规定,则可用与制作铝板或铝片:3003-H14,5005-H14。
其它3xxx,5xxx或6xxx系列的合金若达到本技术要求的规定亦可送审供核准。
板材应符合《GB/T 5237》的要求。
板材的厚度在满足性能要求的基础上不能低于下列要求:a.铝板成型的构件:3.0mm。
b.除非建筑图纸特别要求,铝板厚度为3mm。
根据要求使用加强措施保证铝板外部平整度不大于0.1%或1.5mm(在1.5米内),并以较小值为准。
用于雨棚和吊顶的铝板厚度应为5mm。
c.盖板厚度最小应为3.0mm。
B.表面处理-铝材铝材表面的颜色和处理方式应在铝材制造商标准色卡范围内与经审核的送审样品一致。
1.氟碳喷涂或其他同等做法须经建筑师认可。
2.室外外露的铝材a.所有室外可见的铝材表面皆应在工厂施加Duranar XL涂层,所用氟碳漆应基于PPG公司或其他有授权配方的配制厂所供应的Kynar 500氟化聚合物树脂。
外幕墙分包商应在喷涂前将书面授权证明递交业主和建筑师审核,证明其漆配方和喷涂操作满足要求。
b.Duranar XL涂层包含三涂三烤。
铝合金型材挤压工艺

铝合金型材挤压工艺一、引言铝合金型材在现代制造业中扮演着重要的角色,其具有重量轻、强度高、耐腐蚀等优点,因此在建筑、交通、电子、航空等领域得到广泛应用。
而铝合金型材的生产加工采用挤压工艺成为主流趋势,因为挤压工艺可以实现高效率、低成本、灵活性强等优势。
本文将就铝合金型材挤压工艺进行详细的介绍,包括挤压工艺的原理和流程,工艺参数的优化,设备的选择和维护等方面,旨在为相关行业提供指导和参考。
二、挤压工艺的原理和流程挤压是一种将金属通过压力挤压成型的加工方法,它是铝合金型材的常用生产工艺。
挤压过程通过金属在一定条件下受到挤压力而发生形变,从而获得所需的截面形状。
一般来说,挤压工艺包括以下几个步骤:1.模具设计和制造挤压工艺的第一步是进行模具设计和制造。
模具的设计要满足产品的形状和尺寸要求,同时考虑金属的流动性和挤压后的变形情况。
模具的制造需要选用耐磨、高强度的材料,以确保模具的稳定性和寿命。
2.铝合金型材的选择在挤压工艺中,选择合适的铝合金型材是非常关键的一步。
不同的合金成分会影响挤压的难易程度和成品的性能。
通常使用的铝合金包括6000系列和7000系列,它们具有良好的挤压性能和机械性能。
3.挤压过程挤压过程是铝合金型材生产中最关键的一步。
在挤压过程中,铝型材通过挤压机的挤压头部分受到一定的挤压力,从而在模具中形成所需的截面形状。
挤压速度、挤压力和温度是影响挤压质量的重要工艺参数,需要严格控制。
4.后处理工艺挤压成型后的铝合金型材还需要进行后处理工艺,包括去毛刺、锯切、拉伸、热处理等。
这些工艺主要是为了改善铝合金型材的表面质量和性能。
三、挤压工艺参数的优化挤压工艺参数的优化是铝合金型材生产中非常重要的一环。
通过合理的工艺参数优化,可以提高型材的表面质量、机械性能和成品率,降低能耗和生产成本。
1.挤压速度挤压速度是影响挤压成品质量的重要参数。
过快的挤压速度会导致金属晶粒的变形和拉伸,从而影响型材的表面质量;而过慢的挤压速度则会增加挤压力,增加能耗和降低生产效率。
铝型材行业分析报告

铝型材行业分析报告铝型材行业分析报告一、定义铝型材是一种可以制备成不同截面形状和长度的铝合金材料。
铝型材广泛应用于建筑、交通、电力、机械制造、电子等领域。
二、分类特点按照生产工艺不同,铝型材可分为挤压型、拉伸型(铝板带)和铸造型(铸铝合金)三大类。
其中,挤压型铝型材是目前市场主流产品,占据了大部分市场份额。
铝型材的主要特点包括轻质、高强度、耐腐蚀、易加工和优良的导电性、导热性等。
三、产业链铝型材产业链包括铝合金原材料生产、铝型材加工生产、铝型材配套加工、零部件加工和组装、销售和售后服务等环节。
四、发展历程铝型材行业自上世纪80年代开始逐步兴起,并在不断完善工艺和提高质量的过程中,得到了快速发展。
近年来,随着国家对环境保护和节能减排的要求日益提高,铝型材市场需求呈现快速增长的趋势。
五、行业政策文件及其主要内容1、《铝型材工业控制标准》该标准规定了铝型材的分类、术语、尺寸及允许偏差、化学成分和机械性能、标志、包装、检验和评定等方面的内容。
2、《铝材行业“十三五”规划》该规划提出了未来五年铝型材行业的发展目标和总体路线,指导行业朝向高质量、高效率、低污染的方向发展。
3、《工程建设项目环境影响评价技术导则(铝、镁冶炼及加工)》该技术导则规定了铝型材生产企业在环境保护方面的要求和标准,对企业开展环境影响评价提供了指导。
六、经济环境近年来,国家大力改善城市和乡村空气环境,铝型材行业在利用轻质、高强度铝材制造车身、车门等车辆部件方面具有较大优势。
同时,建筑领域的快速发展也促进了铝型材市场的增长。
七、社会环境社会环境的变化主要表现在消费者对于环保、节能等方面的需求日益提高,这对铝型材企业提出了更高的要求。
八、技术环境挤压工艺是目前铝型材生产的主要工艺,虽然已经相当成熟,但在提高铝型材精度、提升生产效率等方面,仍需要进一步研究和发展。
九、发展驱动因素1、国家政策支持国家在促进新能源汽车、建筑节能领域的政策支持下,铝型材应用市场得到了极大的推动。
铝型材挤压工艺流程

铝型材挤压工艺流程铝型材挤压工艺是一种常见的金属加工方法,通过对铝型材进行挤压,可以生产出各种形状和规格的铝型材产品,广泛应用于建筑、交通运输、电子、家具等领域。
本文将介绍铝型材挤压工艺的流程及相关知识。
首先,铝型材挤压工艺的流程包括原料准备、型材设计、模具制造、挤压成型、表面处理和成品检验等几个主要步骤。
在原料准备阶段,需要选用优质的铝合金材料,并进行熔炼、挤压棒材等加工工序,以保证挤压成型的质量。
型材设计是根据客户需求和产品用途,进行截面形状、尺寸、壁厚等参数的设计,以确定挤压模具的结构和尺寸。
模具制造是根据型材设计要求,制造出适用于挤压生产的模具,通常采用优质的模具钢材料,并通过数控加工等工艺进行加工制造。
挤压成型是将加热后的铝合金棒材放入挤压机中,通过一定的挤压力将其挤压成型,成为具有一定截面形状的铝型材。
表面处理是对挤压后的铝型材进行氧化、阳极氧化、喷涂等处理,以增加产品的表面硬度、耐腐蚀性和美观度。
成品检验是对挤压后的铝型材进行尺寸、外观、力学性能等方面的检测,以确保产品达到客户要求的质量标准。
其次,铝型材挤压工艺的优点主要包括高效率、节能环保、产品精度高、材料利用率高等特点。
挤压工艺可以实现对铝型材的高效率加工,生产效率高,能够满足大批量生产的需求。
同时,挤压过程中不需要进行切削,减少了材料的浪费,节约了能源,符合可持续发展的环保理念。
由于挤压成型的铝型材表面光滑,尺寸精度高,可以减少后续加工工序,提高了产品的加工精度和成品率。
另外,挤压工艺还可以利用铝合金材料的优势,提高材料的利用率,降低生产成本,具有较高的经济效益。
最后,铝型材挤压工艺在实际应用中需要注意一些技术细节和质量控制。
例如,在挤压成型过程中,需要控制好挤压速度、温度和挤压力的参数,以确保产品的成型质量。
在模具制造过程中,需要根据产品的设计要求,选择合适的模具材料和加工工艺,以保证模具的寿命和精度。
在表面处理过程中,需要选择合适的处理方法和工艺,以确保产品的表面质量和耐腐蚀性能。
挤压铝型材工艺总结报告范文(3篇)
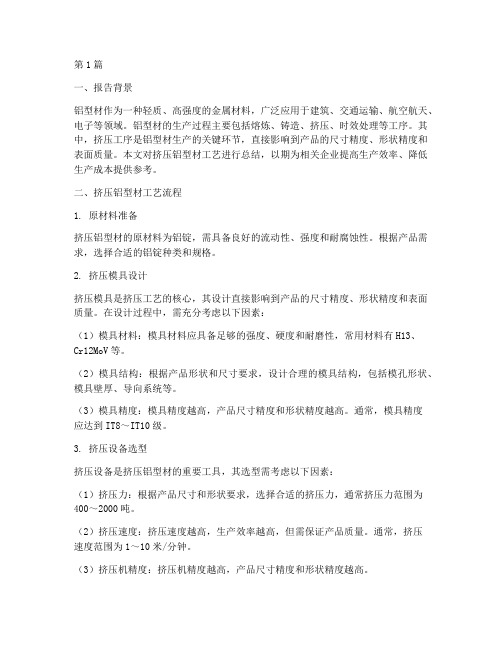
第1篇一、报告背景铝型材作为一种轻质、高强度的金属材料,广泛应用于建筑、交通运输、航空航天、电子等领域。
铝型材的生产过程主要包括熔炼、铸造、挤压、时效处理等工序。
其中,挤压工序是铝型材生产的关键环节,直接影响到产品的尺寸精度、形状精度和表面质量。
本文对挤压铝型材工艺进行总结,以期为相关企业提高生产效率、降低生产成本提供参考。
二、挤压铝型材工艺流程1. 原材料准备挤压铝型材的原材料为铝锭,需具备良好的流动性、强度和耐腐蚀性。
根据产品需求,选择合适的铝锭种类和规格。
2. 挤压模具设计挤压模具是挤压工艺的核心,其设计直接影响到产品的尺寸精度、形状精度和表面质量。
在设计过程中,需充分考虑以下因素:(1)模具材料:模具材料应具备足够的强度、硬度和耐磨性,常用材料有H13、Cr12MoV等。
(2)模具结构:根据产品形状和尺寸要求,设计合理的模具结构,包括模孔形状、模具壁厚、导向系统等。
(3)模具精度:模具精度越高,产品尺寸精度和形状精度越高。
通常,模具精度应达到IT8~IT10级。
3. 挤压设备选型挤压设备是挤压铝型材的重要工具,其选型需考虑以下因素:(1)挤压力:根据产品尺寸和形状要求,选择合适的挤压力,通常挤压力范围为400~2000吨。
(2)挤压速度:挤压速度越高,生产效率越高,但需保证产品质量。
通常,挤压速度范围为1~10米/分钟。
(3)挤压机精度:挤压机精度越高,产品尺寸精度和形状精度越高。
4. 挤压工艺参数确定挤压工艺参数包括挤压温度、挤压速度、润滑剂、挤压压力等。
确定挤压工艺参数需考虑以下因素:(1)挤压温度:挤压温度对产品的尺寸精度、形状精度和表面质量有重要影响。
通常,挤压温度范围为380~480℃。
(2)挤压速度:挤压速度对产品的尺寸精度、形状精度和表面质量有重要影响。
通常,挤压速度范围为1~10米/分钟。
(3)润滑剂:润滑剂可降低模具磨损,提高生产效率。
常用润滑剂有硬脂酸、机油、石墨等。
铝型材的生产工艺

铝型材的生产工艺铝型材是一种重要的工业材料,被广泛应用于电子、机械、建筑等领域。
它具有重量轻、强度高、耐腐蚀性好等特点,因此受到了越来越多的关注和使用。
本文将介绍铝型材的生产工艺。
铝型材的生产工艺主要包括原料处理、熔炼、挤压、表面处理和精加工等环节。
首先是原料处理。
铝型材的原料主要是铝合金,它通常是由铝、硅、锰、镁等元素组成。
原料的品质对最终产品的质量有直接影响,因此在生产过程中需要对原料进行筛选和预处理,确保其质量稳定。
接下来是熔炼。
将经过处理的铝合金原料加入到熔炉中进行熔化。
熔炉通常采用电炉或燃料炉,通过高温将原料熔化为液态铝合金,以便后续的挤压工艺。
然后是挤压。
将熔化的铝合金注入到挤压机中,通过高压将其挤出模具,得到所需的铝型材截面形状。
挤压工艺是铝型材制造中最常用的工艺,通过控制挤压速度、温度和压力等参数,可以得到各种不同形状和尺寸的铝型材。
接下来是表面处理。
铝型材经过挤压后,其表面通常会有氧化膜和不均匀的颜色,需要经过表面处理才能满足使用要求。
常用的表面处理方法包括阳极氧化、喷涂、电泳涂装等。
这些处理能够增加铝型材的耐腐蚀性、耐磨性和装饰性。
最后是精加工。
铝型材经过挤压和表面处理后,需要经过切割、钻孔、弯曲等工艺来加工成最终的产品。
这些精加工工艺通常由机械加工或数控加工完成,能够使铝型材实现更精密的尺寸和形状。
综上所述,铝型材的生产工艺包括原料处理、熔炼、挤压、表面处理和精加工等环节。
这些工艺环节相互配合,能够生产出各种形状和尺寸的铝型材,满足不同行业的需求。
随着科技的不断进步,铝型材的生产工艺也在不断完善,将为其应用带来更多的可能性。
铝型材生产企业工艺介绍和污染源分析探讨

铝型材生产企业工艺介绍和污染源分析探讨我国的铝型材工业起于20世纪50年代。
1954年4月,我国第一个铝镁合金加工基地——东北轻合金加工厂(现名东北轻合金有限责任公司)动工建设,从此开始了中国铝型材加工的历史。
我国铝型材工业于80~90年代進入兴盛时期,华北铝加工厂、广东省有色金属加工厂、华东铝加工厂、青岛铝加工厂、渤海铝加工厂等一些知名铝型材生产企业相继建成。
现今,我国铝型材产量已突破130万吨/年,已成为世界的铝型材工业大国,但还不是铝型材强国。
铝型材生产和加工过程会产生废气、废水、噪声、固体废物等环境问题。
本文以某典型铝型材生产企业为例,介绍铝型材生产和加工工艺,分析生产过程的主要环境污染源并提出防治措施。
1 铝型材生产和加工工艺介绍铝型材生产和加工工艺一般包括熔炼和铸造工序、挤压工序和表面处理工序。
1.1 熔炼和铸造工序熔炼和铸造工序主要是对铝型材产品的合金成份进行调配,是保证铝型材产品质量的关键步骤。
一般生产过程中,铝锭或收集来的废铝被装入熔铝炉,加热熔化成铝熔体。
为了提高产品某些特殊性能,一般还会向熔铝炉加入少量的镁、硅和稀土元素进行成份调整,并加入精炼剂和少量惰性气体除去铝熔体中的少量H2,确保铝型材产品的质量。
典型铝型材生产企业的熔炼和铸造工序详见图1。
1.2 挤压工序挤压工序主要是借助各种各样的模具并施加一定的压力,从而获得各种形状铝型材产品。
现今较为先进的铝型材的挤压成型工艺主要有高速挤压、液压成型、无残料挤压等。
一般来说,挤压工艺的参数主要有金属变形程度(或挤压系数)、填充系数、挤压温度、挤压速度、铸锭长度等,它们与设备能力、挤压方法、合金种类、制品规格等因素有关。
典型铝型材生产企业的挤压工序详见图2。
1.3 表面处理工序为了提高铝型材产品的耐蚀、耐候、耐磨、外观装饰好和使用寿命长等较高的综合性能,必须对铝型材进行表面处理加工。
铝型材表面保护方法,当前不外乎3种:(1) 阳极氧化和着色,20世纪50年代已引入铝合金门窗,至今仍是铝门窗方面常用的表面处理措施;(2) 阳极氧化后电泳涂装,主要以丙烯酸树脂作为涂装液。
铝合金型材挤压工艺解析

2.1铝合金型材挤压工艺铝及铝合金型材被广泛应用于建筑、交通运输、电子、航天航空等部门。
近年来,由于对汽车空调设备小型化、轻量化的要求,热交换器用管材及空心型材中铝挤压制品的比例迅速增加。
据资料介绍,挤压加工制品中铝及铝合金制品约占70%以上。
铝合金型材挤压技术发展也因此带动了现代挤压技术的发展。
2.1.1挤压工艺概述(1)挤压工艺原理挤压工艺是将金属毛坯放入装在塑性成形设备上的模具型腔内,在一定的压力和速度作用下,迫使金属毛坯产生塑性流动,从型腔中特定的模孔挤出,从而获得所需断面形状及尺寸,并具有一定力学性能挤压件的工艺技术,如图2.1所示。
图2.1 金属挤压的基本原理(2)挤压工艺特点挤压作为零件少、无切削加工工艺之一,是近代金属塑性加工中一种先进的加工方法。
挤压工艺是利用模具来控制金属流动,靠软化金属体积的大量转移来成形所需的零件。
因此,挤压工艺的成败与模具结构设计、模具材料以及金属毛坯的软化处理等密切相关。
挤压工艺既可用于生产成批的有色合金及黑色金属的零件,也可加工各种模具的型腔。
挤压加工的成形速度范围很广,可以在专用的挤压压力机上进行,也可以在一般的曲柄压力机(如冲床)或液压机、摩擦压力机以及高速锤上进行。
挤压加工具有许多特点,主要表现在挤压变形过程的应力应变状态、金属流动行为、产品的综合质量、生产的灵活性与多样性、生产效率与成本等一些方面。
挤压加工的优点如下:1)提高金属的变形能力。
金属在挤压变形区中处于强烈的三向压应力状态,可以充分发挥其塑性,获得大变形量。
例如,纯铝的挤压比(挤压筒断面积与制品断面积之比)可以达到500,纯铜的挤压比可达400,钢的挤压比可达40-50。
对于一些采用轧制、锻压等其他方法加工困难乃至不能加工的低塑性难变形金属和合金,甚至有如铸铁一类脆性材料,也可采用挤压法进行加工。
2)制品综合质量高。
挤压变形可以改善金属材料的组织,提高其力学性能,特别是对于一些具有挤压效应的铝合金,其挤压制品在淬火时效后,纵向(挤压方向)力学性能远高于其他加工方法生产的同类产品。
铝型材制造工艺介绍
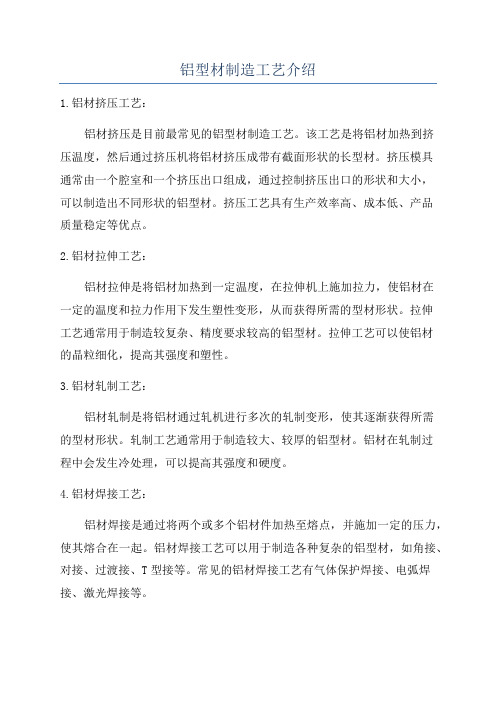
铝型材制造工艺介绍
1.铝材挤压工艺:
铝材挤压是目前最常见的铝型材制造工艺。
该工艺是将铝材加热到挤
压温度,然后通过挤压机将铝材挤压成带有截面形状的长型材。
挤压模具
通常由一个腔室和一个挤压出口组成,通过控制挤压出口的形状和大小,
可以制造出不同形状的铝型材。
挤压工艺具有生产效率高、成本低、产品
质量稳定等优点。
2.铝材拉伸工艺:
铝材拉伸是将铝材加热到一定温度,在拉伸机上施加拉力,使铝材在
一定的温度和拉力作用下发生塑性变形,从而获得所需的型材形状。
拉伸
工艺通常用于制造较复杂、精度要求较高的铝型材。
拉伸工艺可以使铝材
的晶粒细化,提高其强度和塑性。
3.铝材轧制工艺:
铝材轧制是将铝材通过轧机进行多次的轧制变形,使其逐渐获得所需
的型材形状。
轧制工艺通常用于制造较大、较厚的铝型材。
铝材在轧制过
程中会发生冷处理,可以提高其强度和硬度。
4.铝材焊接工艺:
铝材焊接是通过将两个或多个铝材件加热至熔点,并施加一定的压力,使其熔合在一起。
铝材焊接工艺可以用于制造各种复杂的铝型材,如角接、对接、过渡接、T型接等。
常见的铝材焊接工艺有气体保护焊接、电弧焊接、激光焊接等。
总结起来,铝型材制造工艺包括挤压、拉伸、轧制和焊接等多种方法。
每种工艺都有其特点和适用范围,可以根据铝型材的形状、尺寸和技术要
求来选择适合的制造工艺。
随着科技的不断进步,铝型材制造工艺也在不
断发展创新,为各行业提供更多更好的铝型材产品。
铝型材生产工艺

铝型材生产工艺铝型材是一种常用的工业材料,广泛用于建筑、电子、汽车等各行各业。
铝型材的生产工艺主要包括原料选材、熔炼、挤压、淬火和表面处理等环节。
首先,原料选材是铝型材生产的首要环节。
铝合金中主要包含铝、硅、锰、镁等元素。
不同的合金元素含量和种类决定了铝型材的不同性能。
生产厂家根据产品的需求和用户的要求选择不同的合金原料,以确保产品达到设计要求。
接下来是熔炼工艺。
铝型材的熔炼通常使用熔炼炉进行,将选好的铝合金材料加热至熔点后进行熔炼。
熔炼的过程需要控制温度和熔炼时间,以保证熔炼出均匀的铝合金液态材料。
挤压是铝型材生产的核心工艺。
熔融的铝合金经过熔炼炉熔炼后,被送入挤压机的压力室。
在高温下,通过挤压头将铝合金挤压成型,通过模具设计的空隙来获得不同形状和尺寸的铝型材。
挤压机的挤压速度和温度需要根据不同铝合金的特性进行调整,确保产品的质量。
挤压后的铝型材需要进行淬火工艺。
淬火是通过快速冷却的方式,使铝型材达到硬度和强度的要求。
淬火的方法主要有水淬、油淬和空气淬,不同的方法有不同的淬火速度和效果。
淬火的温度和时间也需要根据铝型材的要求进行调整。
最后是表面处理工艺。
铝型材的表面处理主要是为了提高产品的耐腐蚀性和装饰性。
常见的表面处理方法有阳极氧化、涂装和电泳涂装等。
阳极氧化是通过在铝型材表面形成一层氧化膜,提高了材料的耐蚀性和硬度。
涂装和电泳涂装则是通过在铝型材表面涂覆一层涂料,增加了产品的装饰性和耐用性。
总之,铝型材的生产工艺包括原料选材、熔炼、挤压、淬火和表面处理等环节。
这些环节之间相互配合,共同确定了铝型材的质量和性能。
不同产品的要求和用户的需求,会对工艺的具体参数进行调整,以满足不同的需求。
随着科学技术的不断发展,铝型材生产工艺也在不断改进和创新,以提高产品的质量和市场竞争力。
铝型材电泳涂漆工艺及常见问题分析
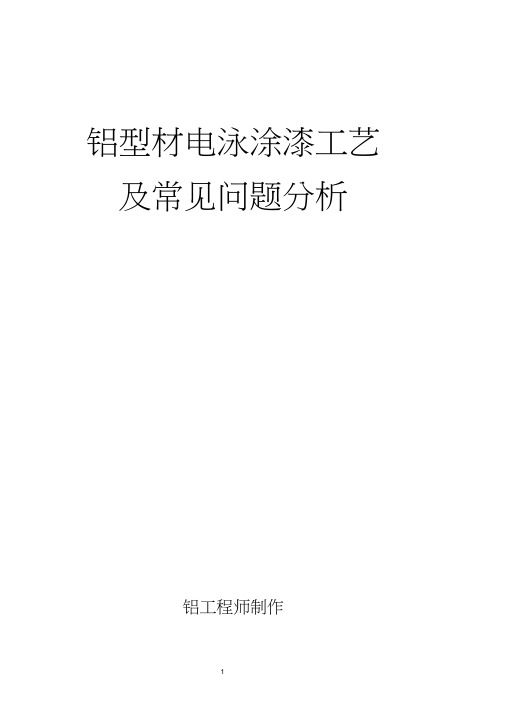
铝型材电泳涂漆工艺及常见问题分析铝工程师制作目第一部分:电泳涂漆工艺 第一:工艺规程及工艺要点1、电泳工艺 2 3、固化炉灰处理4第二:槽液管理 1、槽液调整 23、离子交换处理 4第三:槽液的控制和品质分析 1、现场检验管理23、槽液检测化验方法 第四:生产现场管理 1、装料上架管理 2 3、电泳槽液管理4第二部分:电泳涂漆的缺陷分析与对策1、起泡 2 、电泳无漆 3 、异常电解 4 、凹坑12、漆膜薄 13 、漆膜薄厚14 、漆膜不均匀 15、滴形水滴16、皮膜裂纹 17 、条纹18 、漆料迹19 、接触痕20、颗粒状异常 21 、桔皮22 、粗糙失光 23 、灰尘附着 24、 成品表面混浊不透彻25 、漆膜表面有夹杂物 26、水斑(水点、水印)27、漆膜黄变、28 、雾斑9、漆斑及漆流痕10 、低光泽 11 、乳白、固化工艺 、重加工工艺、槽液补给 、回收、槽液检测的控制、电泳前的检查、电泳漆烘烤管理 5、胶着 6 、表面粗糙 7 、酸痕 、针孔或缩孔第一部分电泳涂漆工艺第一:工艺规程及工艺要点1、电泳工艺1.1主要工艺参数:热水洗和纯水洗1.1.4电泳后水洗1.2操作要求:1.2.1电泳前必须经过一道低纯水,二道热纯水,三道高冷纯水的洗涤,充分洗尽型材表面、内孔和膜孔中的酸水和污物。
A)低纯水洗:为高纯水洗的溢流水;B )热纯水洗:热纯水洗的主要作用是使铝合金阳极氧化膜扩张以利于彻底清洗工件,避免前处理工序中杂质离子尤其是硫酸根离子污染电泳槽液,同时对阳极氧化膜有一定的封闭作用,以提高工件的耐腐蚀性能。
由于硫酸阳极氧化膜的多孔结构,热水清洗不彻底,吸附于氧化膜孔内的硫酸电解液带入电泳槽,与电泳槽中的电泳漆发生反应,局部产生凝胶,也会产生浮漆。
因此,在电泳涂装前,需进行热纯水洗涤。
热水洗效果与水温和水质有关,通常温热纯水温度应达到70C以上,最好控制在70- 80C之间,电导率小于550ps/cm,浸泡时间为3—5分钟。
铝材基本生产工艺流程

铝材基本生产工艺流程铝材作为一种轻量、高强度、耐腐蚀的金属材料,在现代工业中得到了广泛应用。
它的广泛应用离不开铝材的生产工艺流程,下面就让我们来深入探讨一下铝材的基本生产工艺流程。
铝材的生产工艺流程可概括为以下几个步骤:铝矿的开采与制取、氧化铝的制取、电解制铝、铝材的初加工和精加工等。
一、铝矿的开采与制取1. 开采铝矿:铝矿是铝的原料,常见的铝矿有白云石、赤铁矿和石膏矿等。
铝矿的开采主要通过露天开采和地下矿井开采两种方式进行。
2. 制取氧化铝:在铝矿经过破碎、磨矿和浸出等工艺后,得到含有氧化铝的浸出液。
通过氢氧化铝的沉淀、沉降和过滤等步骤,将氧化铝从浸出液中分离出来。
二、电解制铝1. 制取铝电解用的氟化铝:氟化铝是铝电解工艺中的重要原料。
它通常是通过氢氟酸与铝氢氧化物反应制取而成。
2. 铝电解槽工艺:铝电解是将氧化铝还原成金属铝的重要过程。
电解槽由阴极、阳极和电解质组成,通过电解质中的电解,将氧化铝分解成铝离子,并通过电解槽中的电流沉积在阴极上,形成金属铝。
三、铝材的初加工1. 铝锭的熔炼和浇铸:通过将电解槽中得到的金属铝熔炼,并通过浇铸成型,得到铝锭。
铝锭是铝材加工的基础。
2. 铝锭的轧制:铝锭经过预热后,通过轧机的轧制作用,将铝锭轧制成所需的金属板、金属卷、铝型材等。
四、铝材的精加工1. 铝材的切割、冲孔和弯曲:根据所需的形状和尺寸要求,对铝材进行切割、冲孔和弯曲等加工操作。
2. 表面处理:为了提高铝材的表面性能,可进行阳极氧化、电泳涂漆、电镀和喷涂等表面处理工艺。
3. 成品制取:根据客户的需求,对铝材进行切割、冲压、钻孔和焊接等工艺,最终制取成所需的铝制品,如铝制门窗、铝合金车辆构件等。
铝材的基本生产工艺流程就是以上所述。
通过这些工艺步骤,我们可以将铝矿制取成金属铝,并加工成各种形状和尺寸的铝制品。
铝材的生产工艺需要严格遵循标准操作规程,确保产品的质量和性能。
在这个过程中,我个人认为铝材生产工艺中最重要的一环是电解制铝过程。
- 1、下载文档前请自行甄别文档内容的完整性,平台不提供额外的编辑、内容补充、找答案等附加服务。
- 2、"仅部分预览"的文档,不可在线预览部分如存在完整性等问题,可反馈申请退款(可完整预览的文档不适用该条件!)。
- 3、如文档侵犯您的权益,请联系客服反馈,我们会尽快为您处理(人工客服工作时间:9:00-18:30)。
朔州丰泰实业有限公司
翟春槐
2013.12.9
主要内容
1.铝金属及应用 2.铝及铝合金成型工艺 3.铝型材生产 ▲ 铝型材生产工艺流程 ▲ 铝合金铸棒工艺 ▲ 铝型材挤压工艺 ▲ 铝型材表面处理工艺 ▲ 铝型材包装技术
1.铝金属及应用 (1)铝的属性
银白色轻金属。有延展性。一般制成棒、带、板、 箔、型、粉和丝。在潮湿空气中能形成一层防止 金属腐蚀的氧化膜。易溶于稀硫酸、硝酸、盐酸、 氢氧化钠和氢氧化钾溶液,不溶于水。密度2.70 3 g/cm 。熔点660℃。 是地壳中分布最广、储量最多的金属元素,含量 8.3%, 仅次于氧和硅。 高强度/密度之比率、抗腐蚀性和重量功效而得到 广泛应用。
(2)铝的应用
▲发现该金属不过200年,到1886年发明将氧化铝溶解在冰晶
石(Na3AlF6)中电解的方法,沿用至今。1940年不到100 万吨,2012年仅中国电解铝产量已突破1000万吨,约占世 界产量的一半。是仅次于钢铁的第二大金属。 ▲应用广泛(民用、国防军事) 建筑:桥梁、塔楼、储罐、门窗 包装:软包装、食品容器、瓶盖、饮料罐与食品罐。 交通:汽车、火车、轨道交通、船舶、舰艇 电力电子:电线电缆、电子箔、散热器 航空航天:飞机、航天器 耐用消费品及家具:电冰箱、 机械与设备:
4XXX 5XXX
6XXX 7XXX 8XXX
9XXX
2.铝及铝合金成型工艺
(1)铸造铝合金、变形铝合金 压延类分为轧制、挤压 轧制:供坯方式:辊式铸轧、热轧、履带式铸轧,再进行冷轧 、箔轧,期间精整,包括退火、拉弯矫直、纵横剪切、表面 涂层,形成卷材或板材。投资较大,忠旺天津项目220亿元 (2)挤压: ▲挤压的概念: 用压杆对放置在压筒中的坯料加压,使之产生塑性流动, 从而获得相应于模具的型孔形状的制件方法。挤压时,坯料 产生三向压应力,即使是塑性较低的坯料,也可被挤压成形 。挤压,特别是冷挤压,材料利用率高,材料的组织和机械 性能得到改善,操作简单,生产率高,可制作长杆、深孔、薄 壁、异型断面零件,是重要的少无切削加工工艺。挤压主要 用于金属的成形,也可用于塑料、橡胶、石墨和粘土坯料等 非金属的成形。
48.27
166.24 106.77 103.33 96.07 95.20 76.98
-7.44
-10.33 7.5 -3.83 20.67 188.07 2.45
山西
山东 河南 广东 江苏 辽宁
1.65
779.74 660.91 457.65 212.55 114.68
9.24
407.54 362.61 229.39 109.80 58.38 增长最快省份
4)挤压速度的影响。
5)摩擦条件的影响 挤压筒内表面的状态、润滑条 件影响锭坯与筒壁间的摩擦状况 ,从而会影响挤压力大小。 6)挤压筒温度的影响 挤压筒预热适当们可以降低锭 坯的冷却速率,减小挤压力。 7)挤压温度的影响 金属在挤压时必须考虑适宜的 挤压温度。
▲挤压时金属的流动
(4)铝的牌号:
铸造铝合金(略) 变形铝合金(易拉罐:罐体与罐底3004铝合金,罐盖5182铝合金,拉环5042铝合金) 组 别 牌号系列 1XXX 纯铝 (铝含量不小于99.00%) 2XXX 以铜为主要合金元素的铝合金 3XXX 以锰为主要合金元素的铝合金
以硅为主要合金元素的铝合金 以镁为主要合金元素的铝合金 以镁和硅为主要合金元素并以Mg2Si相为强 化相的铝合金(美国牌号6063=LD31) 以锌为主要合金元素的铝合金 以其他合金元素为主要合金元素的铝合金 备用合金组
金属挤压示意图
▲挤压分类: 按金属塑变流动方向可分为: 正挤压:挤压时,金属流动方向与凸模运动方向相同 反挤压:挤压时,金属流动方向与凸模运动方向相反 复合挤压:挤压时,坯料一部分金属流动方向与凸模运动方向相 同,另一部分则相反 径向挤压:挤压时,金属流动方向与凸模运动方013年1-6月份铝材产量(万吨) 原铝(电解铝)产量 地区 合计 本 月 184.31
本月止累计 同比增长 (%)
铝材产量大省 地区 全国 本月 355.83
本月止累计 同比增长(%)
1058.04
7.94
1821.79
24.58
山西
河南 青海 山东 甘肃 新疆 宁夏
8.06
26.74 18.63 16.69 17.24 17.83 13.57
▲挤压实例:
▲影响挤压力大小的因素:
1)变形抗力(金属的屈服限)越大,所需挤压力越高,
高温时,变形抗力降低,挤压力随之降低。
2)加工率的影响。加工率越大,所需挤压力越大。
3)锭坯长度的影响 长度越长,挤压过程越长,挤压终了时温度变 化大,变形抗力变大。正挤压时,要克服锭坯 与挤压筒壁的摩擦力,故挤压力增加,反挤压 时,挤压力与锭坯长无关。
-50.42
37.67 19.16 17.49 21.2 0.63
2012年 1440
建筑型
万吨
地区
产品
本月止累计
同比增长(%)
(3)铝的分类: 从成份分:高纯铝、纯铝、合金铝 从成型分:铸造(铸造铝合金) 压延(变形铝合金) 分为轧制、挤压(重点) 从使用分: 通用:薄板、厚板、箔、棒材、线材、管 材 非通用:型材、拉拔、锻件、冲挤件、铸 件、冲压件、粉末冶金零件、机加工件和铝 基复合材料(如铝塑)
▲挤压工艺条件 : 1)使金属处于三向压应力状态; 2)建立足够的应力值,使金属能够产生塑性变 形; 3)有能使金属流出的孔或间隙,提供一个阻力 最小的方向。
▲挤压工艺特点 : 挤压时金属坯料处于三向压应力状态下变形,因此
可提高金属坯料的塑性,有利于扩大金属材料的塑 性加工范围。 可挤压出各种形状复杂、深孔、薄壁和异型截面的 零件,且零件尺寸精度高,表面质量好,尤其是冷 挤压成形。 零件内部的纤维组织基本沿零件外形分布且连续, 有利于提高零件的力学性能。 生产率较高,只需更换模具就能在同一台设备上生 产形状,尺寸规格和品种不同的产品。 节约原材料,挤压属于少(无)切削加工,大大节 约了原材料。