高炉自动控制系统技术方案
基于PLC控制的高炉自动化上料系统的应用与分析

基于PLC控制的高炉自动化上料系统的应用与分析随着工业的发展,高炉已经成为钢铁企业不可或缺的设备之一。
钢铁行业是国家经济的重要支柱产业,高炉的运行对于钢铁生产起着至关重要的作用。
传统的高炉上料方式存在一些问题,如运行效率低、操作风险大、能耗较高等。
如何实现高炉自动化上料成为了一个热门话题。
基于PLC控制的高炉自动化上料系统应运而生,它可以提高高炉上料的效率、降低操作风险、减少能源消耗,受到了广泛的关注和应用。
1. 高炉自动化上料系统的应用高炉自动化上料系统是基于PLC控制技术的一种新型自动化系统,它通过精确控制上料过程中的各个参数,实现了自动计量、自动送料、自动维护等功能。
在实际应用中,高炉自动化上料系统可以分为以下几个部分:1.1 PLC控制系统PLC控制系统是整个高炉自动化上料系统的核心部分,它可以通过编程实现对系统的自动控制。
PLC控制系统不仅具有高稳定性和可靠性,而且具有很强的抗干扰能力和自适应能力。
通过对PLC控制系统的良好设计和参数调整,可以使高炉自动化上料系统实现高效稳定的运行。
1.2 送料装置送料装置是高炉自动化上料系统中的一个重要组成部分,它通常由送料机、皮带输送机、料仓等设备组成。
送料机通过PLC控制系统实现对上料速度、连续送料、料流稳定等精确控制,实现对高炉的自动上料。
计量装置是保证高炉上料质量的关键部分,它通过PLC控制系统实现对上料的精确计量。
计量装置可以根据高炉的实际情况进行调整,确保上料量达到要求,并且可以实现对不同原料的准确计量,从而保证了高炉的正常运行。
监测装置是对高炉自动化上料系统进行实时监测和数据采集的装置。
通过PLC控制系统实现对设备的工作状态、上料量、物料变化等参数的实时监测,并将监测数据传输给上位机进行处理和分析,能够对高炉的运行状态进行实时监控,以及进行远程故障诊断和维护,保证了高炉自动化上料系统的安全稳定运行。
相比传统的高炉上料方式,基于PLC控制的高炉自动化上料系统具有以下几个优势: 2.1 提高了高炉的上料效率传统的高炉上料方式通常需要人工操作,操作繁琐、效率低下,而且容易出现误差。
酒钢1#高炉自动控制系统的开发与应用
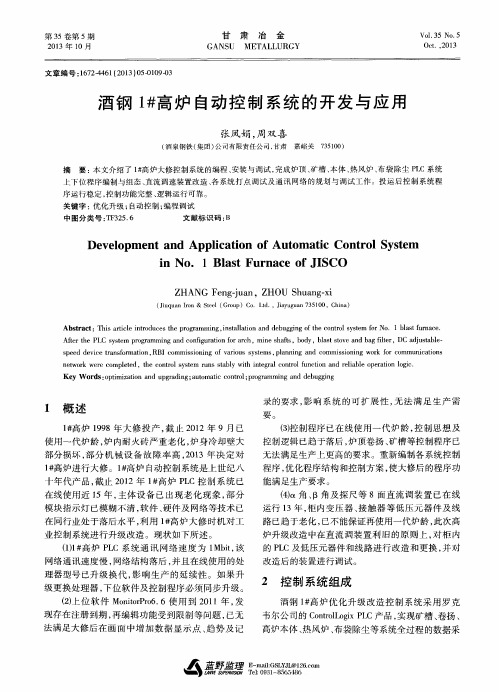
录的要 求 , 影 响 系 统 的可 扩展 性 , 无 法 满 足 生 产 需
要。
( 3 ) 控制 程序 已在 线 使 用 一 代 炉龄 , 控 制 思 想 及 控 制逻 辑 已趋 于落 后 , 炉顶 卷扬 、 矿槽 等控制 程序 已 无 法满 足生 产上更 高 的要求 。重新 编制 各 系统控 制 程序 , 优 化程 序结 构 和控制 方案 , 使大 修后 的程序 功
Ab s t r a c t : T h i s a r t i c l e i n t r o d u c e s t h e p r o g r a mmi n g, i n s t a l l a t i o n a n d d e b u g g i n g o f t h e c o n t r o l s y s t e m f o r No .1 b l a s t f u r n a c e .
序运行 稳定 , 控制 功能完整 、 逻辑运行 可靠。
关键 宇 : 优化升级 ; 自动控制 ; 编程调试
中图分类号 : T F 3 2 5 . 6 文 献标 识 码 : B
De v e l o pm e n t a n d Ap p l i c a t i o n o f Au t o ma t i c Co n t r o l S y s t e m
( 1 ) 1 } } 高炉 P L C 系统 通 讯 网络 速 度 为 1 Mb i t , 该
( 4 ) 仅角 、 B角 及探 尺 等 8面 直 流调 装 置 已在 线 运行 1 3年 , 柜 内变 压 器 、 接 触 器 等 低压 元 器 件 及 线 路 已趋 于老化 , 已不能保 证再 使用 一代 炉龄 , 此次 高
1080m3高炉工程自控系统技术方案

各称量斗设定值以千克KG为单位填入各斗的设定值。焦炭设定为干焦值在
画面中进行焦炭水份设定程序自动转换成湿焦值。
附加焦设定在需要附加焦的放料批次中减小放料车次直到附加焦执行完。
称量及补偿的计算公式如下
6、7、8第一位不能是空格连续书写不能超过10个字母程序遇0或执行完10周
期后自动返回周期1执行。
料单修改标志设定料单上有一“料单传送”标志此标志为1说明修改过料单
当前放料料批执行完时重新按新设定的料单开始控制。
料批内料型设定A、B、C、D、E、F、G、H等八种料批每个批次均设1-4个车次1080m3高炉自动化控制系统技术方案
4、其他控制方案 .............................................................................. 16 第一章 方案综述
1、概述 1.1 系统范围
武安市裕华钢铁有限公司新建1080m3高炉工程基础自动化控制系统范围为高炉基础级自动化部分。主要有高炉供料控制高炉上料控制高炉热风炉控制高炉本体控
3/17 制高炉上料控制高炉热风炉控制高炉本体控制高炉水冲渣控制布袋除尘控制
喷煤控制高炉循环水控制以及各自的监控站通过工业以太网连接在一起。 第二章 主要环节方案简介
1、高炉上料控制方案 高炉上料部分采用S7-400系列控制器和ET200组成分布式控制系统 。设两台上位
1、高炉上料控制方案 ........................................................................ 3
钢铁高炉电气自动控制系统设计与分析
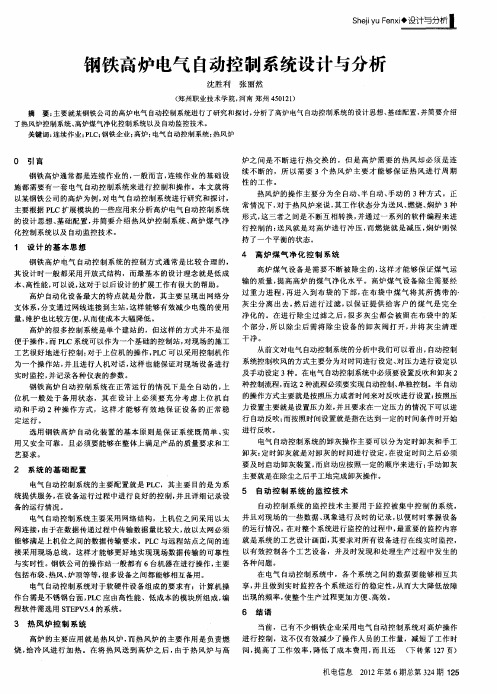
1 设 计 的 基 本 思 想
钢 铁 高炉 电气 自动 控 制系 统 的控 制 方式 通 常 是 比较 合 理 的 , 其 设计 时 一般 都 采用 开放 式 结 构 ,而最 基 本 的设 计理 念 就是 低 成
4 高 炉 煤 气 净 化 控 制 系统
高 炉 煤 气 设 备是 需要 不 断 被 除尘 的 , 这样 才 能够 保 证煤 气 运 输 的质 量 , 高 高炉 的煤 气 净 化水 平 。高炉 煤 气 设 备 除 尘 需 要经 提 过 重力 进 程 , 进 入 到 布袋 的 下 部 , 布 袋 中煤 气 将 其 所 携 带 的 再 在 灰 尘 分 离 出去 , 后进 行过 滤 , 然 以保 证 提 供 给 客 户 的 煤 气 是 完 全 净 化 的 。在 进 行 除尘 过 滤 之 后 , 多 灰 尘 都会 被 留在 布 袋 中 的某 很
了热风炉控制系统 、 炉煤气 净化控制系统 以及 自动 监控技 术。 高 关键 词: 连续作业 ;L 钢铁 企业: P C: 高炉 ; 电气 自动控制 系统; 热风炉
0 引 言
炉 之 间是 不 断 进 行 热 交 换 的 ,但 是 高 炉 需 要 的 热 风 却 必 须 是 连 续 不 断 的 ,所 以需 要 3个 热 风 炉 主 要才 能 够 保 证 热 风 进 行 周 期 性 的工 作 。 热 风炉 的操 作主 要 分为 全 自动 、 自动 、 半 手动 的 3 方 式 。正 种 常 情 况 下 , 于 热风 炉 来 说 , 对 其工 作状 态 分 为送 风 、 燃烧 、 炉 3 炯 种 形 式 , 三 者之 间是 不 断互 相 转换 , 通 过一 系 列 的软件 编 程 来进 这 并 行 控 制 的 : 风 就是 对 高炉 进 行 冲 压 , 燃 烧 就 是减 压 , 炉 则保 送 而 焖 持 了一个 平衡 的状 态 。
高炉上料自动控制系统

高炉上料自动控制系统【摘要】本文主要论述了罗克韦尔控制系统在包钢万腾钢铁1#高炉中的应用。
对自动控制系统的组成、硬件配置、控制过程及控制功能的实现进行了详细阐述。
【关键词】罗克韦尔控制系统;装料控制;布料控制0 概述高炉上料装置是生产中的重要环节,提高其自动化水平,可以大大减轻工人劳动强度,提高生产效率,同时通过原料的精确配比,又可提升产品的品质和质量。
高炉上料自动控制系统采用PLC完成所有的顺序控制过程、数据采集、自动调节、事故处理及报警等工作。
计算机负责监控和人机对话,PLC和计算机通过光纤进行通讯,进行动态数据交换,实现点对点通讯,控制与监控分开,可靠性高。
1 上料系统的控制方案万腾钢铁1#高炉上料控制系统分为槽下配料和小车上料及炉顶布料三部分构成,采用的是卷扬小车自动上料,炉顶是单罐式无料钟炉顶,槽下矿槽为单列左右对称布置,高炉料车卷扬采用的是两套变频传动,互为备用。
溜槽布料倾角和节流调节采用比例阀控制,炉顶探测料面采用2根变频调速垂直探尺。
炉顶其它设备采用的是液压传动。
溜槽、料溜调节阀的位置检测装置采用的是三个增量型编码器。
在上料过程中,炉料先投进受料斗里,随后放入料罐中,在这个过程中,由于高炉不能和大气相通,通过控制炉顶放散阀、均压阀、上密阀、料斗翻板、下密阀、料流阀的顺序开关来实现高炉的正常下料,通过控制α、β、γ来实现高炉布料。
根据高炉上料系统的工艺要求,综合考虑控制的可靠性及实用性,其设计方案如下。
高炉上料自动控制系统由一套冗余PLC及三个远程I/O站组成。
CPU机头及高炉炉顶I/O位于高炉主控楼PLC室,CPU、电源模块及通讯模块采用冗余方式。
炉顶远程I/O主要控制炉顶设备及布料器、探尺等炉顶设备。
槽下设备远程I/O站位于矿槽主控楼,主要控制槽下配料设备以及槽下液压站设备。
卷扬远程I/O站位于卷扬液压站,主要控制炉顶液压站及与卷扬西门子300PLC的硬连接控制。
矿槽除尘远程I/O站,主要控制矿槽除尘风机、仓壁振动器及刮板机等除尘系统设备。
高炉自动化控制系统的设计与实现

高炉自动化控制系统的设计与实现近年来,随着科技的进步和工业自动化的推进,高炉自动化控制系统得到了越来越广泛的应用。
高炉作为传统制铁工业的核心设备,其生产效率和产品质量直接影响着制铁行业的发展。
因此,为了实现高炉生产的自动化、智能化和高效化,需采用一系列先进的自动化控制技术,对高炉进行全方位控制和监测,从而保证高炉生产的稳定性、安全性和经济性,在提升生产质量和效益的同时降低生产成本。
一、高炉自动化控制系统概述高炉自动化控制系统是指采用计算机等现代化信息技术手段,对高炉全过程进行自动化控制和监测的系统,用于实现高炉生产过程中的数据采集、处理、分析和反馈。
其主要包括硬件设备和软件系统两个方面。
硬件设备包括各种传感器、执行器和可编程控制器等;软件系统则涉及到数据采集、处理与分析,控制命令的下达和反馈等一系列程序。
二、高炉自动化控制系统设计原则高炉自动化控制系统的设计需要符合以下原则:1.稳定性原则:保证高炉生产的稳定性和安全性。
2.高效性原则:提高生产效率,降低生产成本。
3.可靠性原则:保证自动化控制系统的可靠性和稳定性,减少故障率。
4.智能化原则:采用人工智能技术,实现自动化控制系统的智能化和自适应性。
5.可扩展性原则:考虑自动化控制系统的可扩展性,方便未来的升级和改造。
三、高炉自动化控制系统设计内容高炉自动化控制系统设计内容主要包括以下几方面:1.数据采集和处理:采用各类传感器对高炉运行参数进行实时采集,对采集到的数据进行预处理、计算和分析,并将处理后的结果反馈到自动化控制器中,从而实现对高炉全过程的监测和控制。
2.控制命令下达:将处理后的数据转化为控制命令,下达给各电气控制器和执行器,实现对高炉生产的自动化控制。
3.控制系统反馈:控制系统反馈是指将高炉生产过程中产生的各种控制参数作为输入信号反馈给控制系统,通过控制系统中的处理程序对各类参数进行分析,从而实现对高炉全过程的控制和监测。
4.自适应控制:采用自适应控制算法,根据实时采集到的高炉运行数据和自身学习能力,不断调整自动化控制系统的控制策略,以实现最优控制。
高炉喷煤自动控制系统

高炉喷煤自动控制系统姚瑞英喷煤控制系统由烟气炉、原煤储运、制粉、喷吹四部分组成,主要实现了生产工艺设备的自动/手动控制及保护、工艺数据的自动采集和处理、PID回路的自动调节、工艺画面动态显示、历史和实时趋势显示纪录、紧急停喷报警等功能。
系统介绍 1 硬件配置系统采用Modicon TSX Quantum系列可编程控制器,烟气炉有一套单独的PLC系统,原煤储运、制粉、喷吹公用一套PLC系统,并采用远程I/O网络结构,原煤储运为主站,通过同轴电缆连接制粉、喷吹两个远程站。
两套PLC均通过以太网进行通讯。
2 软件配置运用Concept2.5软件对PLC系统组态编程,画面监控软件选用IFIX软件。
3 网络结构喷煤PLC系统包括烟气炉PLC系统和高炉喷煤PLC系统,如图1所示。
每个控制系统通过以太网进行数据传输和现场设备的控制。
共设两个控制室,5台上位机,其中烟气炉、制粉、喷吹以及主引风机高压变频监控站在一个控制室,原煤储运单独在一个控制室,各上位机之间通过交换机互联,其中由于原煤储运控制室距另外的控制室较远,为确保数据传输的准确性,两台交换机通过光纤介质互联,其他上位机及PLC之间通过双绞线互联。
高压变频监控站通过MB+网控制变频器的频率。
图1 喷煤系统网络拓扑该网络结构有两种方式可以为将来与高炉联网做准备,一是交换机预留光纤口,通过光纤与高炉进行数据通讯;二是通过CPU的MB+口进行数据通讯,实现数据的透明化。
工艺控制 1 原煤储运系统该系统包括8条皮带机、1#~4#圆盘给料机,1#、2#电磁分离器、犁式卸料器,主要负责向1#、2#原煤仓上煤。
根据现场设备情况,可以选择4个圆盘给料机中任何一个或两个圆盘给料机同时给1#或2#煤仓供料,这样共有12个料流可以选择,被选中的皮带则根据料流的方向逆启顺停。
操作人员根据原煤仓需煤量的大小选择相应的料流。
当某一料流运转时,从画面将程序打在“联动”位,若该料流的任一设备出现故障,则系统联停,设备停止顺序与启动顺序相反。
湖南涟源钢铁集团公司 2200m3 高炉控制系统简介

湖南涟源钢铁集团公司2200m3高炉PCS7自动控制系统方案简介涟钢2200m3高炉项目简介涟钢2200m3高炉是涟钢的第6座高炉,目前最大的也是唯一一座容积大于2000 m3的高炉高。
它于2002年初动工,2003年12月正式投产,经过将近一年的运行,目前生产稳定,运行平稳,日产铁水约5000吨,完全达到了预期的设计要求和目标。
西门子公司以PCS7系统通过公开招标于2002年9月获得该项目的供货合同。
在整个项目的实施过程中,西门子公司以优秀的产品质量和售后服务,为整个项目的顺利投产做出了自己的贡献,赢得了业主和总包方的好评。
PCS7主要优势在于:•系统具备“三电一体化”功能即控制系统不但要善于处理逻辑控制也要善于完成模拟量的控制,同时要能够方便的同过程计算机相连。
同时,系统具有硬件、软件平台一致性,不应是多种控制系统、多个系列产品的直接并列、网络连接,而是有机的统一即全集成系统。
•系统具有高度的开放性,无论是系统的工作平台(Windows)、系统的骨干网络(工业以太网)以及现场总线系统(PROFIBUS),都是目前的市场主流和发展方向.•系统能够支持客户机-服务器结构,特别是多服务器结构,这是目前MES、ERP等高级管理系统对基础自动化系统的基本要求。
•系统能够支持工艺系统的分布实施,由于在高炉项目建设中,部分子项的投入运行是其他子项实施的前提,在系统的应用软件设计中必须切块考虑,在客户机服务器结构中必须具备项目的分解与合并功能。
•系统具备冗余功能,无论是控制系统的操作站(OS)、控制器(AS)、骨干通讯网络还是现场总线都应具备冗余功能,这是高炉连续工作和高可靠性要求所决定的。
PCS系统配置简介根据高炉工艺的特点西门子公司推荐采用PCS7过程控制系统,经过与业主和总包方的技术交流,最后确定的系统配置如图所示:热风录流程画面系统的主要组成部分、功能及安装位置如下:•系统共设置工程师站2台负责整个项目的编程与组态,项目完成后在工程师室设置一台工程师站用于系统的维护,硬件采用西门子工业控制计算机PC840。
高炉热风炉自动化控制系统

高炉热风炉自动化控制系统作者:谢彬修来源:《城市建设理论研究》2013年第23期摘要:高炉热风炉自动化控制系统主要包含热风炉本体控制、外围设备控制以及液压站控制等。
高炉热风炉自动化控制系统要求保证炼铁生产过程中向高炉供风的连续性以及实时监控性,进而保证高炉炼铁工艺稳定持续进行。
关键词:热风炉自动化控制系统;西门子PLC控制系统;热风炉工艺中图分类号: TF578 文献标识码: A 文章编号:热风炉自动化控制系统具有控制设备多、设备位置分散、工艺操作顺序严格,设备间联锁关系强、设备运行环境恶劣、安全可靠性要求高等特点。
基于PLC的高炉热风炉控制系统,在考虑高炉炼铁系统特点和要求的基础上,充分利用了PLC可靠性、稳定性、功能多样性和扩展性好、易于使用等特点,为高炉冶金自动化提供了良好的个性化解决方案。
系统设计热风炉控制是集机械、液压、电气控制和计算机应用为一体的技术。
以PLC为核心,集中与分散相结合,组成三电一体控制系统。
本文依据某钢铁厂工艺要求组织设计,其热风炉自动控制系统由1个西门子S7-400的PLC做控制核心,两台上位机做操作平台。
S7-400PLC通过强大的以太网通讯功能与上位机进行通讯,接收上位机的操作指令。
通过快速的扫描内部程序逻辑判断需要执行的动作,发出命令,从而实现PLC核心控制作用。
热风炉自动化监控系统主要包括煤气、助燃空气、烟气以冷风及热风等管道阀门设备的监控,液压站油泵、助燃风机等电气设备监控,仪器仪表温度、压力、流量等参数的显示与报警,自动换炉等部分。
上位机的人机交互系统包括热风炉操作系统、液压站操作系统、附属设备操作系统、仪表参数趋势系统以及参数报警系统等五个子系统组成。
利用西门子WINCC6.2组态软件的强大功能实时高效的与S7-400PLC配合完成热风炉系统的自动化监控任务。
为了确保操作的安全可靠性,在主要依托PLC控制的基础上增加电气回路控制,便于应急就地操作与检修时的设备操作。
高炉热风温度自动控制系统介绍

高炉热风温度自动控制系统介绍摘要:在高炉生产中,稳定热风温度(以下简称风温),能够提升高炉运行的安全性与稳定性,并且提高生产效率,并对高炉操作具有积极的作用。
应用自动控制策略并配合高精度混风调节阀,能够有效地实现风温的自动控制,将风温波动控制在较小范围之内。
本文对风温自动控制系统进行了详细的介绍。
关键词:高炉;热风炉;风温;自动控制目前,国内大部分热风温度控制采用人工操作的方式,一般情况下,风温设定在1150℃。
由于工人的经验、水平差异,风温控制效果也有较大差异,有的风温波动甚至达30℃。
本文介绍的自动控制方式,不仅稳定了风温,也降低了工人的劳动强度。
1高炉风温自动控制系统介绍1.1原理为了保证高炉热风温度稳定,对混风阀进行调节。
由于冷风总量恒定,通过调节混风阀改变混风管道的风量,从而间接改变通过热风炉的风量,达到调节风温的目的。
混风阀调节根据送风过程一般可以分为3个过程,即混风初始时刻、中期和末期。
初始时刻,即换炉开始的初始时刻,此时热风炉蓄热值为最高,混风阀初始值可根据拱顶温度设定,此后进入中期时刻,开度根据自动控制策略计算而得;末期,由于热风炉蓄热降低,所有冷风经热风炉在送至高炉,风温也略低于设定值,此时混风阀处于全关闭状态。
1.2系统构成1.2.1自动控制策略(初始、中期)由于每次烧炉,热风拱顶温度都不相同,因此混风阀初始开度也不相同。
混风阀初始值的设定需要根据工人的操作经验,将各个范围的初始拱顶温度T0和混风阀初始开度统计汇总,形成相应的规则库。
为混风阀初始开度∮0提供依据。
具体如下:将初始拱顶温度分为5个档,HH(高高)、H(高)、N(正常)、L(低)、LL(低低)。
正常温度按照工艺要求确定,高于N温度5℃,定为H;高于10℃,定为HH;低于5℃,定为L;低于10℃,定为LL。
结合现场实际情况,记录各个温度工况下的混风阀初始开度值,找出对应关系。
根据此对应关系,形成一对一的逻辑控制程序。
高炉自动化控制系统

3 系统特 点
高炉 自动 化控 制 系统 , 用 冗 余的 以太 采 网络 、 ROFBUS D 总 线 网络 将 中 心控 P I - P 制 室计 算 机和 P C 统主 站 、 L 系统 主站 L 系 P C 与远 程 IO分站 联 系 起来 , 成 一个 分 布 式 / 构 的控 制 系统 , 体 特点 如 下 : 具
3 2 高炉 自动化控 制系统介 绍 的 高 炉程 控 系 统 设 计 为 冗 点都 采用 继 电器 与 外 部设 备进 行 电气 隔 离 , 制系统 。 对生产上所用到的电动机和阀门等 模 拟 量 输入 输 出信 号 都 采用 带 光 电隔 离 的 连带相关成套机电设备的开关量控制, 包括 余 配 置 , 中包 括 电源 冗 余 , P 其 C U冗 余 , 以 模块。 各 个 部 分 的联 锁 起 动 , 锁 关 机 , 联 自动联 锁 太 网 络 冗 余 ,ROF B — P 线 网 络 冗 P I US D 总 1 1 通信 网络 . 控制, 单步联 锁 控 制 , 系统 单步 调试 于 一 体 。 余等等。 无论生产过程 中哪个环节 出现 问题 都 可 以不 影响 生 产 , 因此 可 以认 为这 个 系 也 统最大限度地保证了系统的可靠性以及 安 全性 。
3 1 高炉 自动化控 制系统完善 、 . 强
大 的功 能
支 持 冗 余 C U配 置 , 能 更 强 、 度 更 P 功 速 快。 同时 , 品 种齐 全 的功 能模 块 , 满 配有 充分 足 用 户各 种 类 型 的 现场 需 求 。 即使 在 恶 劣 、 不 稳定 的工 业 环 境 下 , 然 可正 常 工 作 ; 依 无 风扇设计提高了系统的可靠性 ; 在运行过程 中 , 可进 行带 电热插 拔 。 模块
高炉自动化介绍

高炉自动化介绍一、引言高炉自动化是指利用先进的控制系统和自动化设备,对高炉的生产过程进行智能化管理和控制,以提高生产效率、降低能耗和减少人为误差。
本文将详细介绍高炉自动化的原理、优势、应用领域以及相关的技术和设备。
二、原理高炉自动化的原理是通过传感器、控制器和执行器等设备,将高炉内部的各个参数进行实时监测和控制。
传感器可以测量高炉内的温度、压力、流量等参数,控制器根据传感器的反馈信号,通过控制执行器,调节高炉内的气体流量、料层厚度等参数,从而实现对高炉生产过程的精确控制。
三、优势1. 提高生产效率:高炉自动化可以实现对高炉生产过程的精确控制,减少人为误差,提高生产效率。
自动化系统可以根据实时数据进行智能调控,使高炉运行更加稳定和高效。
2. 降低能耗:高炉自动化可以通过优化控制策略和参数,降低高炉的能耗。
自动化系统可以根据炉内温度、压力等参数进行智能调节,使高炉的能耗达到最低。
3. 提高安全性:高炉自动化可以对高炉生产过程进行实时监测,及时发现和处理异常情况,提高高炉的安全性。
自动化系统可以通过报警和紧急停机等措施,保护高炉和操作人员的安全。
4. 减少人工劳动:高炉自动化可以减少人工劳动,降低人力成本。
自动化系统可以代替人工进行繁琐的操作和监测,提高工作效率,减少人力投入。
四、应用领域高炉自动化广泛应用于钢铁行业的高炉生产过程中。
高炉是钢铁生产的核心设备,自动化技术的应用可以提高钢铁生产的质量和效率,降低生产成本。
同时,高炉自动化也可以应用于其他行业的高温熔炼和炼化过程中,如冶金、化工等领域。
五、相关技术和设备1. 传感器:高炉自动化中常用的传感器包括温度传感器、压力传感器、流量传感器等。
这些传感器可以将高炉内部的参数转化为电信号,供控制器进行处理和分析。
2. 控制器:高炉自动化中常用的控制器包括PLC(可编程逻辑控制器)、DCS (分布式控制系统)等。
控制器根据传感器的反馈信号,通过控制执行器,实现对高炉生产过程的控制。
高炉智慧系统设计方案,1200字

高炉智慧系统设计方案智能高炉系统设计方案一、引言高炉是钢铁冶炼中非常重要的设备,其性能的优劣直接关系到冶炼质量和生产效率。
随着人工智能和物联网技术的不断发展,智能高炉系统的设计和应用已经成为了钢铁行业的研究热点。
本文将介绍一种智能高炉系统的设计方案,以提升高炉的冶炼效率和降低能耗。
二、系统结构智能高炉系统包括传感器、信号采集模块、数据处理模块、控制模块和人机界面等组件。
1. 传感器:通过安装在高炉的各个部位的传感器,实时采集高炉的各种参数,包括高炉温度、煤气成分、压力、风温风量、物料厚度等。
2. 信号采集模块:负责将传感器采集到的数据进行采集和转换,将模拟信号转换成数字信号,并通过通信接口传送给数据处理模块。
3. 数据处理模块:主要负责对采集到的数据进行分析和处理,通过算法模型对高炉的状态进行监测和预测。
该模块可以具备机器学习和深度学习的能力,通过训练模型对高炉的运行状态进行预测和优化。
4. 控制模块:根据数据处理模块的分析结果和预测结果,实时调节高炉的工艺参数,包括风温风量、喷煤量、加料量等,以实现高炉的自动化控制。
5. 人机界面:提供给操作人员进行设置参数、监控状态和报警等功能的界面,可以通过计算机、手机或者触摸屏等方式实现。
三、主要功能和特点1. 实时监测和预测:智能高炉系统通过传感器实时采集高炉的各种参数,并通过数据处理模块对高炉的状态进行监测和预测,可以及时发现并解决潜在问题,提高高炉的冶炼效率。
2. 自动调节控制:智能高炉系统根据数据处理模块的分析结果和预测结果,自动调节高炉的工艺参数,实现高炉的自动化控制,减少人为干预,降低操作风险,提高冶炼效率和产品质量。
3. 数据分析和优化:智能高炉系统通过机器学习和深度学习的算法模型对高炉的运行数据进行分析和优化,通过精确的预测和优化,调节高炉的工艺参数,提高冶炼效率,降低能耗。
4. 实时报警和故障诊断:智能高炉系统可以根据数据处理模块的分析结果,实时监测高炉的运行状态,并发出报警信号,及时预警和处理潜在问题;同时,还可以通过故障诊断模块对高炉的故障进行诊断,并给出相应的解决方案。
高炉上料自动控制系统
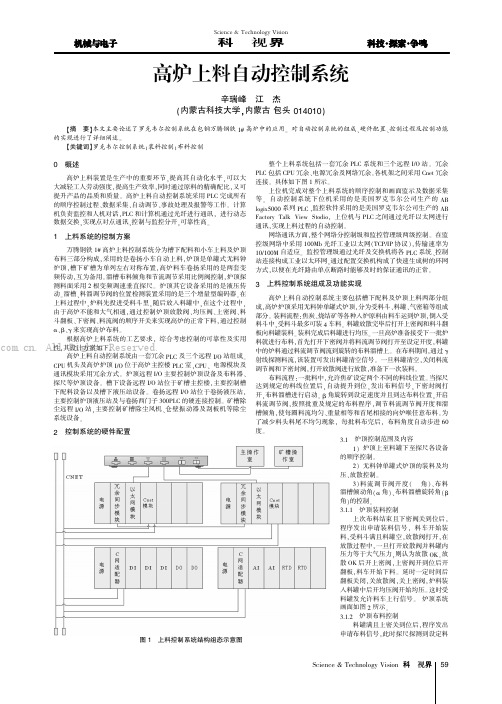
Science &Technology Vision 科技视界0概述高炉上料装置是生产中的重要环节,提高其自动化水平,可以大大减轻工人劳动强度,提高生产效率,同时通过原料的精确配比,又可提升产品的品质和质量。
高炉上料自动控制系统采用PLC 完成所有的顺序控制过程、数据采集、自动调节、事故处理及报警等工作。
计算机负责监控和人机对话,PLC 和计算机通过光纤进行通讯,进行动态数据交换,实现点对点通讯,控制与监控分开,可靠性高。
1上料系统的控制方案万腾钢铁1#高炉上料控制系统分为槽下配料和小车上料及炉顶布料三部分构成,采用的是卷扬小车自动上料,炉顶是单罐式无料钟炉顶,槽下矿槽为单列左右对称布置,高炉料车卷扬采用的是两套变频传动,互为备用。
溜槽布料倾角和节流调节采用比例阀控制,炉顶探测料面采用2根变频调速垂直探尺。
炉顶其它设备采用的是液压传动。
溜槽、料溜调节阀的位置检测装置采用的是三个增量型编码器。
在上料过程中,炉料先投进受料斗里,随后放入料罐中,在这个过程中,由于高炉不能和大气相通,通过控制炉顶放散阀、均压阀、上密阀、料斗翻板、下密阀、料流阀的顺序开关来实现高炉的正常下料,通过控制α、β、γ来实现高炉布料。
根据高炉上料系统的工艺要求,综合考虑控制的可靠性及实用性,其设计方案如下。
高炉上料自动控制系统由一套冗余PLC 及三个远程I/O 站组成。
CPU 机头及高炉炉顶I/O 位于高炉主控楼PLC 室,CPU、电源模块及通讯模块采用冗余方式。
炉顶远程I/O 主要控制炉顶设备及布料器、探尺等炉顶设备。
槽下设备远程I/O 站位于矿槽主控楼,主要控制槽下配料设备以及槽下液压站设备。
卷扬远程I/O 站位于卷扬液压站,主要控制炉顶液压站及与卷扬西门子300PLC 的硬连接控制。
矿槽除尘远程I/O 站,主要控制矿槽除尘风机、仓壁振动器及刮板机等除尘系统设备。
2控制系统的硬件配置整个上料系统包括一套冗余PLC 系统和三个远程I/O 站。
4000级高炉热风炉自动控制系统的设计与实现

( 2 ) 集 中手 动 控 制 ( 远程 控 制 方 式 )在 主 控 室 H MI 操 作 台上 对 热 风 炉 各 阀 门进 行 远 程 操 作 , 保 存 连锁 关 系 。
( 3 ) 半 自动 控 制 此 控 制 方 式 要 求 在 热 风 炉 系 统 状 态 转 换 时 , 必须在 H MI 操作 台 上 按 下 “ 送风” 、 “ 燃烧” 、 “ 闷炉” 按键, 程 序 按 照 选 择 的方 式 通 过 P L C 自动 控 制 单 座 热 风 炉 所 有 阀 门按 照 顺 序 开 启 或关 闭 , 实 现 半 自动 换 炉 。 ( 4 ) 自动控 制 此 控 制 方 式 各 热 风 炉 自动 进 行 “ 燃 烧一 闷炉一 送风” 或者“ 送风. 闷炉一燃烧 ” 换 炉 控 制 。 自动 换 炉 可 以 按 照 时 间换 炉 、 也可根据温度换炉 。
4 0 0 0级高炉热风炉 自动控制 系统的设 计与实现
王永康 牛 继 凯
4 5 5 0 0 4 ) ( 安 阳钢 铁 公 司计 控 处
【 摘 要】 安钢 4 0 0 0级 高 炉 热 风 炉 共 四 座 , 在 2 0 1 3年 建 成 并 投 入 使 用 ,
自动 控 制 系统 采 用 施 耐 德 昆 腾 P L C 控 制 系 统 。 本 文 主 要 介 绍 四 座 热
3控 制 方 式
3 . 1单 座 热 风 炉 的 控 制 方 式
单 座 热 风 炉 的控 制 方 式 有 四种 , 可在高炉 主控室的 H MI 操 作 台上 Fra bibliotek 行 选 择 。
( 1 ) 机旁手动 此控 制方 式用于 热风 炉休风 时, 此 时 除 调 节 阀
外 的所 有 阀 门均 由就 地 控 制 箱 控 制 , 并无安全连锁 。
- 1、下载文档前请自行甄别文档内容的完整性,平台不提供额外的编辑、内容补充、找答案等附加服务。
- 2、"仅部分预览"的文档,不可在线预览部分如存在完整性等问题,可反馈申请退款(可完整预览的文档不适用该条件!)。
- 3、如文档侵犯您的权益,请联系客服反馈,我们会尽快为您处理(人工客服工作时间:9:00-18:30)。
450m3高炉自动控制系统技术方案第一章方案综述1、概述1.1 系统范围:该系统范围为高炉基础级自动化三电控制部分,即:仪表、电气、计算机。
主要有:槽下高炉上料、炉顶控制系统,高炉本体测控系统,热风炉控制系统,煤气干式净化控制系统,供料控制系统,系统网络通讯等系统的基础级自动化控制。
1.2 设计选型原则(1)尽量采用先进、成熟、可靠的控制技术,本着经济实用、安全可靠及先进的原则,集多年冶金自动化系统设计、维护之经验,进行系统优化设计,实现低成本、高效率自动化系统;(2)采用三电(EIC)一体化控制,主体工艺采用三电合一(EIC)的控制思想,实现仪表、电气及自动控制系统的集成控制。
系统采用集散型PLC实现分布式网络控制,确保系统运行稳定可靠;(3)为确保系统具有良好的匹配性,PLC系统、电气及标书内的仪表设备分别尽量选用同一厂家产品;(4)上位机、PLC之间的通讯采用工业以太网结构,确保系统具有良好的开放性;(5)方案设计充分考虑节能降耗,减少电磁干扰,提高系统的稳定性;(6)在完成基础级自动化的基础上,统一规划网络结构,预留与企业管理级系统的通讯接口。
对于本项目共分为高炉本体、高炉炉顶上料、热风炉、煤气干法除尘、供料控制系统等五个部分,涉及到仪表、电气和PLC自动化系统等三个方面。
2、PLC系统配置PLC控制系统由4套单独PLC构成,按工艺流程分:槽下上料、炉顶布料系统;高炉本体工艺参数采集和控制系统;热风炉数据采集与功能控制系统;煤气净化系统;上料系统、高炉本体系统、热风炉系统的PLC以及各自的监控站通过工业以太网连接在一起。
热风炉PLC本体PLC上料PLC热风炉监控站本体监控站上料监控站除尘监控站除尘PLC热风炉操作室炉长操作室工业以太网组网结构图系统采用西门子S7-400/S7-300系列PLC,编程软件采用STEP7 V5.3,监控软件采用WINCC6.0中文版。
PLC与上位机间采用以太网通讯模式,PLC与PLC之间同样采用以太网通讯模式总线结构。
在高炉上料值班室、高炉工长值班室之间采用双绞线以太网,高炉工长值班室与热风炉值班室、除尘值班室通过光纤连接,采用Dlink工业光纤口以太网交换机,高炉上料值班、热风炉值班室设置工业以太网交换机。
PLC系统I/O余量大于10% 。
HMI操作配备7台操作站。
上料控制室安装2台上位监控机;高炉本体2台上位监控机放于工长值班室内;热风炉2台上位机放置于热风炉控制室内;煤气净化系统上位机1台放置于煤气净化控制室。
上位机采用研华工控机,21吋飞利浦纯平显示器,均采用当前流行配置。
针对现场的实际情况,上料值班室安置1个仪表柜,主要是10台称量斗和两个中间仓的重量变送;还设有上料远程PLC柜和继电器柜组成分布式系统,通过Profibus与炉长室的上料本地PLC柜通讯。
炉长室设有上料本地PLC柜,负责上料和炉顶设备的控制;还设有本体PLC 柜和信号隔离柜负责高炉本体的监控;HMI操作包括两台上料系统操作站和两台本体监控用操作站;HMI与PLC之间通过以太网通讯。
在热风炉值班室有热风炉PLC柜及热风炉隔离柜,负责热风炉的控制;还有除尘本地PLC柜和除尘隔离柜,负责除尘系统的控制;HMI操作包括两台热风炉系统操作站和一台除尘系统监控操作站。
在除尘配电室设有除尘远程PLC柜和继电器柜,通过Profibus与除尘本地PLC柜通讯,组成分布式系统。
3、电气部分电气部分包括高炉本体、高炉矿槽、高炉炉顶的供配电。
主要电气元件选用国内外著名公司产品。
其中,主卷扬变频器采用西门子6SE70系列变频器,功率400KW。
4、西门子系统简介4.1 硬件性能SIEMENS自动化系统具有强大的信号处理和逻辑运算能力,具有模板化、可扩充的体系结构,适用于工业实时控制和制造过程控制。
高性能:(1)高吞吐量,使得更多的程序运行时间更短。
(2)附加的数学协处理器能满足更多的控制要求,提供更多的可能性及更高的产品质量。
高完备性:(1)适于苛刻的工业环境,例如复杂的电气设备及环境温度。
(2)SIMENS符合UL.CSA和工厂等级FM1,Div2的要求,给用户提供一个安全的选择。
(3)可选的冗余电源、电缆,为重要场合提供安全保障。
(4) SIEMENS专利的段调度技术使得I/O更新和程序扫描同步进行,从而实现安全,可预测的控制。
方便使用:(1)SIEMENS系统中不使用DIP开关,全部地址用转换开关设定,SIEMENS 控制器提供了所有下装模块的配置特征。
(2)十进制地址方式排除了在编程,检查系统时记忆转换的繁琐过程。
(3)○所有的I/O模板使用同样的I/O接线端子,这样不必考虑板子与接线端子的对应关系。
(4)运行时每块模板都有正常信息显示,使用户维护更容易。
(5)扩展总线的LED组,能够减少诊断故障时间。
(6)所有模板均可插入底板的任一槽中,对于除了电源模板外的所有模板,没有对所在槽位的配置限制。
(7)所有模板均有LED显示灯指示操作状态。
(8)允许模板带电插拔。
(9)用于现场接线的端子排插于模板前部。
4.2 WINCC 功能结构4.2.1 基本功能WINCC 自动化软件为操作人员和贯穿整个管理的应用软件提供实时的数据。
实时数据的处理是如何更加有效的利用资源、人力,最终提高自动化程度的关键。
WINCC最基本的功能就是数据采集和数据管理。
(1)数据采集:WINCC软件采集数据时无需特定的硬件,它可以通过高性能、高速I/O驱动程序与硬件通讯。
(2)数据管理:一旦接收到数据,应用程序对数据进行处理与引导。
(3)数据完整性:数据采集与数据管理为WINCC 执行的所有自动化任务提供了基础。
数据的完整性是WINCC软件的核心,并且是WINCC 开发体系的固有部分。
4.2.2 人机界面及监控与数据采集功能(1)显示:WINCC强大的数字、文本、图像格式提供了最友善的人机界面。
(2)监控:操作人员直接从计算机改变设定值和其它关键值的功能与监视数据显示相配合。
(3)报警:WINCC以多种途径(包括多媒体)将得到的报警通知操作人员。
(4)控制:WINCC软件包括连续控制、批处理控制、统计控制功能,利用算法调整过程量。
留有用户程序接口,方便诸如优化、模糊控制的嵌入。
4.2.3 报表功能及数据存档系统中能够以用户指定的速率采样数据并将数据存储在数据文件中。
任何时候,都能从数据文件中检索数据,创建历史数据的趋势显示。
已存储的数据是正确处理和优化过程的强大工具。
报表:WINCC 支持操作人员通过工业标准数据交换协议如DDE 和ODBC SQL双向访问WINCC 数据。
操作人员能够用如Microsoft 的Excel电子表格建详细报表。
4.2.4 开放式结构功能WINCC 提供了用VB 、C 、C++和VC 等一系列语言对系统中任何数据点、报警及历史数据进行读写访问功能。
系统的开放式结构提供给现场工程师丰富的工具,使他们编写应用软件解决特定的自控需求。
开放式的结构也允许工程师编写应用程序为操作管理软件和现场其它数据平台提供重要的实时数据。
第二章 高炉本体方案1、PLC 系统硬件高炉本体部分采用S7-400系列控制器412-2DP ,以太网通讯模式 。
高炉本体主要是各种参数的检测报警以及部分设备的控制。
系统配置如下表:2、控制功能2.1实现温度、流量、冷却水压力等检测数据的报警功能例如:温度报警,在检测超过某一设定值时,进行判断并进行报警功能,如在监控画面闪烁或变色。
炉身温度报警示意图:2.2实现炉顶压力的手动/自动调节功能2.3监控画面功能监控画面包括整个高炉本体工艺流程的形象描绘,画面和谐统一,操作简单安全可靠。
监控画面包括所有模拟量输入数字量输入信号的显示和所有模拟量输出数字量输出的操作。
对于数据显示都有根据工艺要求的上下限报警显示,对于调节系统都有根据实际请况的手自动切换。
对一些重要数据还有报表打印功能。
对于冷风流量、冷风压力、热风温度、炉顶压力等参数都有实时趋势和历史趋势显示。
第三章高炉上料方案1、PLC系统配置及设备高炉上料部分采用S7-400系列控制器414-2DP和ET200组成分布式控制系统。
设两台上位机互为备用。
高炉上料系统包括了槽下备料、卷扬上料、炉顶布料等三部分的逻辑顺序控制,并且和工长值班室通过以太网相连,并进行直接的数据交换。
量斗称重设有称重仪表柜,并具有远程复位功能。
2、控制功能2.1槽下配料功能槽下控制能够根据料单内容实现振筛、给料机、斗闸门、翻板、皮带等的完全自动化逻辑控制。
并根据槽下料单的填写内容实现自动称量补偿等计算累计功能:振筛的手/自动启停斗闸门的手/自动开关皮带的手/自动启停翻板的自动定位中间斗的自动排料称重远程复位2.1.1料单设定:高炉自动控制系统技术方案周期设定:料单设A、B、C、D、E、F、G、H等八种料批,根据需要可设其中的一种或几种,故周期设定中只允许填写A、B、C、D、E、F、G、H对应的代号1、2、3、4、5、6、7、8,第一位不能是空格,连续书写,不能超过10个字母,程序遇0或执行完10周期后自动返回周期1执行。
料单修改标志设定:料单上有一“料单传送”标志,此标志为1,说明修改过料单,当前放料料批执行完时,重新按新设定的料单开始控制。
料批内料型设定:A、B、C、D、E、F、G、H等八种料批,每个批次均设1-4个车次,相应位置填入料型组合代码,而每一种料型组合代码又对应着所选料仓代号组合。
各称量斗设定值以千克(KG)为单位,填入各斗的设定值。
焦炭设定为干焦值,在画面中进行焦炭水份设定,程序自动转换成湿焦值。
附加焦设定:在需要附加焦的放料批次中减小放料车次,直到附加焦执行完。
称量及补偿的计算公式如下:本次称量值=本次实际称量值*30%+上次称量值*70%本次余振量=本次满值-本次控制值下次余振量=70%*上次提前量+30%*本次提前量本次入炉量=本次满值-本次空值本次误差值=本次设定值-本次入炉量累计误差=累计误差+本次误差下次设定值=设定值+本次误差下次控制值=下次设定值-下次余振量2.1.2振筛的自动启停控制高炉自动控制系统技术方案根据料单的设定情况,被选择的仓在设定好后,检测下面的称量斗闸门已经关好,并且称量未满,则启动振筛振料,待称量斗发出满信号,则停止振动给料。
振动筛或给料机启动T秒后,还未发出斗“满”信号,就发出上卡料报警信号。
2.1.3称量斗的称量和排料控制当排料程序发出后,矿石称量斗闸门开,料排出。
当称量值为控制值(初始时为设定值的95%)的5%时,发出料空信号并关闭闸门,当闸门关好并称空好后,振动筛或给料机开始启动。
称量值到控制值(经补正)时,振动筛或给料机停机,进行满称量。
若达110%控制值(经补正)时发出报警信号。