内螺纹和外螺纹的铣削加工技巧
内螺纹铣削加工
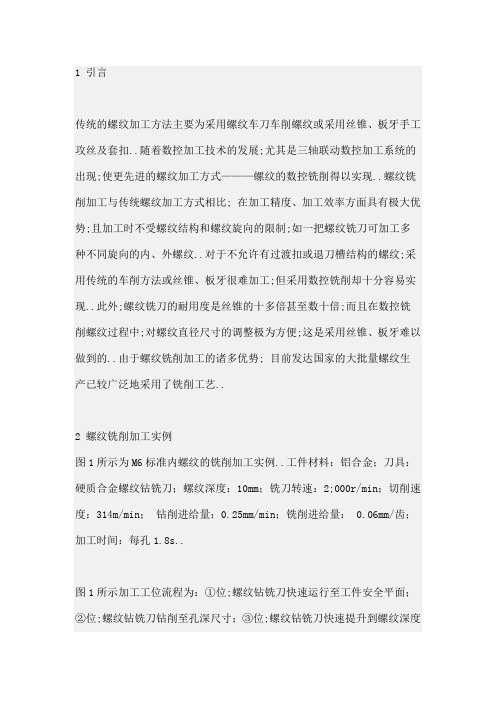
1 引言传统的螺纹加工方法主要为采用螺纹车刀车削螺纹或采用丝锥、板牙手工攻丝及套扣..随着数控加工技术的发展;尤其是三轴联动数控加工系统的出现;使更先进的螺纹加工方式———螺纹的数控铣削得以实现..螺纹铣削加工与传统螺纹加工方式相比; 在加工精度、加工效率方面具有极大优势;且加工时不受螺纹结构和螺纹旋向的限制;如一把螺纹铣刀可加工多种不同旋向的内、外螺纹..对于不允许有过渡扣或退刀槽结构的螺纹;采用传统的车削方法或丝锥、板牙很难加工;但采用数控铣削却十分容易实现..此外;螺纹铣刀的耐用度是丝锥的十多倍甚至数十倍;而且在数控铣削螺纹过程中;对螺纹直径尺寸的调整极为方便;这是采用丝锥、板牙难以做到的..由于螺纹铣削加工的诸多优势; 目前发达国家的大批量螺纹生产已较广泛地采用了铣削工艺..2 螺纹铣削加工实例图1所示为M6标准内螺纹的铣削加工实例..工件材料:铝合金;刀具:硬质合金螺纹钻铣刀;螺纹深度:10mm;铣刀转速:2;000r/min;切削速度:314m/min;钻削进给量:0.25mm/min;铣削进给量: 0.06mm/齿;加工时间:每孔1.8s..图1所示加工工位流程为:①位;螺纹钻铣刀快速运行至工件安全平面;②位;螺纹钻铣刀钻削至孔深尺寸;③位;螺纹钻铣刀快速提升到螺纹深度尺寸;④位;螺纹钻铣刀以圆弧切入螺纹起始点;⑤位;螺纹钻铣刀绕螺纹轴线作X、Y方向插补运动;同时作平行于轴线的+Z方向运动;即每绕螺纹轴线运行360°;沿+Z方向上升一个螺距;三轴联动运行轨迹为一螺旋线;⑥位;螺纹钻铣刀以圆弧从起始点也是结束点退刀;⑦位;螺纹钻铣刀快速退至工件安全平面;准备加工下一孔..该加工过程包括了钻孔、倒角、内螺纹铣削和螺纹清根槽铣削;采用一把刀具一次完成;加工效率极高..3 螺纹铣刀主要类型在螺纹铣削加工中;三轴联动数控机床和螺纹铣削刀具是必备的两要素..以下介绍几种常见的螺纹铣刀类型:1 圆柱螺纹铣刀圆柱螺纹铣刀的外形很像是圆柱立铣刀与螺纹丝锥的结合体见图2上;图2下为锥管螺纹铣刀;但它的螺纹切削刃与丝锥不同;刀具上无螺旋升程;加工中的螺旋升程靠机床运动实现..由于这种特殊结构;使该刀具既可加工右旋螺纹;也可加工左旋螺纹;但不适用于较大螺距螺纹的加工..常用的圆柱螺纹铣刀可分为粗牙螺纹和细牙螺纹两种..出于对加工效率和耐用度的考虑;螺纹铣刀大都采用硬质合金材料制造;并可涂覆各种涂层以适应特殊材料的加工需要..圆柱螺纹铣刀适用于钢、铸铁和有色金属材料的中小直径螺纹铣削;切削平稳;耐用度高..缺点是刀具制造成本较高;结构复杂;价格昂贵..2 机夹螺纹铣刀及刀片机夹螺纹铣刀适用于较大直径如D>25mm的螺纹加工..其特点是刀片易于制造;价格较低;有的螺纹刀片可双面切削;但抗冲击性能较整体螺纹铣刀稍差..因此;该刀具常推荐用于加工铝合金材料..图3 所示为两种机夹螺纹铣刀及刀片..图3a为机夹单刃螺纹铣刀及三角双面刀片;图 3b为机夹双刃螺纹铣刀及矩形双面刀片..3 组合式多工位专用螺纹镗铣刀组合式多工位专用螺纹镗铣刀的特点是一刀多刃; 一次完成多工位加工;可节省换刀等辅助时间;显着提高生产率..图4所示为组合式多工位专用螺纹镗铣刀加工实例..工件需加工内螺纹、倒角和平台d4..若采用单工位自动换刀方式加工;单件加工用时约30s..而采用组合式多工位专用螺纹镗铣刀加工;单件加工用时仅约5s..4 螺纹铣削轨迹螺纹铣削运动轨迹为一螺旋线;可通过数控机床的三轴联动来实现..图5为左旋和右旋外螺纹的铣削运动示意图..与一般轮廓的数控铣削一样;螺纹铣削开始进刀时也可采用1/4圆弧切入或直线切入..铣削时应尽量选用刀片宽度大于被加工螺纹长度的铣刀;这样; 铣刀只需旋转360°即可完成螺纹加工..螺纹铣刀的轨迹分析如图6所示..5 螺纹铣削编程现结合M30×1.5右旋内螺纹铣削加工实例说明螺纹铣削的编程方法..工件材料:42CrMo4;螺纹底孔直径:Di=28.38mm;螺纹直径:Do=30mm;螺纹长度L=20mm;螺距:P=1.5mm;机夹螺纹铣刀直径:D2=19mm;铣削方式:顺铣..1 参数计算主轴转速N为N=1000V/D2×p=1000×150/19×3.14=2512r/min铣刀齿数Z=1;每齿进给量f=0.1mm;铣刀切削刃处进给速度F1为F1=fz×N=0.1×1×2512=251.2mm/min铣刀中心进给速度F2为F2=F1D0-D2/D0=251.2×30-19/30=92.1mm/min设安全距离CL=0.5mm;切入圆弧半径Re为Re=Ri-CL2+R02/2R0=14.19-0.52+152/2×15=13.747mm切入圆弧角度b为b=180°-arcsinRi-CL/Re=180°-arcsin14.19-0.5/13.747=95.22°为便于计算; 可近似取值为90°..切入圆弧时的Z轴位移Za为Za=Pa/360°=1.5×90°/360°=0.375mm切入圆弧起始点坐标为2螺纹铣削程序Fanuc系统%N10 G90 G00 G57 X0. Y0.N20 G43 H10 Z0. M3 S2512N30 G91 G00 X0. Y0. Z-20.375N40 G41 D60 X0. Y-13.690 Z0.N50 G03 X15. Y13.69 Z0.375 R13.747 F92 N60 G03 X0. Y0. Z1.5 I-15. J0.N70 G03 X-15. Y13.69 Z0.375 R13.747N80 G00 G40 X0. Y-13.690 Z0.N90 G49 G57 G00 Z200. M5。
螺 纹 加 工

金属切削方法
❖ 螺纹加工
4. 螺纹滚压
图8.118 螺纹滚压
金属切削方法
❖ 螺纹加工
5. 螺纹磨削
根据所用砂轮形状,外螺纹有以下两种磨削方法:
1)单线砂轮磨削,如图8.119(a)所示 2)多线砂轮磨削,如图8.119(b)所示
金属切削方法
❖ 螺纹加工
5. 螺纹磨削
图8.119 螺纹磨削
金属切削方法
1)盘形铣刀铣削螺纹(如图8.115所示) 2)梳形螺纹铣刀铣削螺纹(如图8.116所示) 3)旋风法铣削螺纹(如图8.117所示)
金属切削方法
❖ 螺纹加工
2. 螺纹铣削
图8.115 盘形铣刀加工螺纹
金属切削方法
❖ 螺纹加工
2. 螺纹铣削
图8.116 梳形螺纹铣刀加工螺纹
金属切削方法
❖ 螺纹加工
❖ 螺纹加工
6. 螺纹加工方法的选择
螺纹加工方法的选择,主要取决于螺纹的种类、精度等级、生产批 量及螺纹件的结构特点,如书中表8.7所示。
机械制造基础
2. 螺纹铣削图8.117 Nhomakorabea旋风法铣削螺纹
金属切削方法
❖ 螺纹加工
3. 攻螺纹和套螺纹
攻螺纹是用丝锥加工内螺纹 套螺纹是用板牙加工外螺纹 攻螺纹和套螺纹加工精度较低,主要用于精度要求不高的、直径较 小的普通连接螺纹
金属切削方法
❖ 螺纹加工
4. 螺纹滚压
螺纹滚压方法有搓丝板滚压和滚丝轮滚压两种
1)搓丝板滚压,如图8.118(a)所示 2)滚丝机滚压,如图8.118(b)所示
机械制造基础
金属切削方法
❖ 螺纹加工
螺纹的应用非常广泛,根据其用途不同,可分为两大类:
螺纹铣削
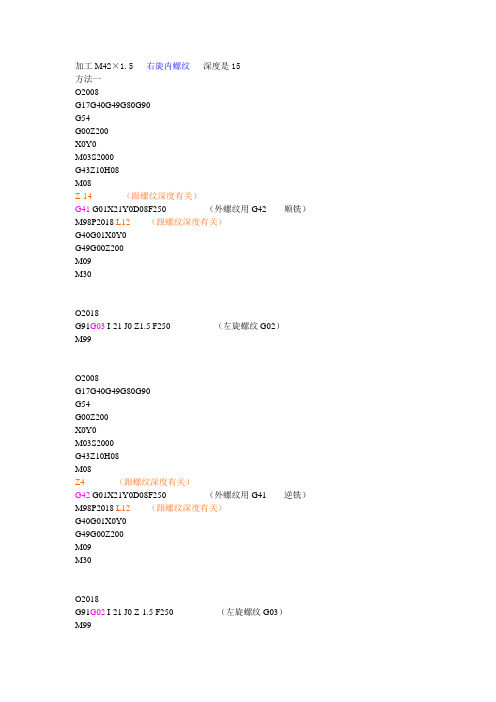
加工M42×1.5 右旋内螺纹深度是15方法一O2008G17G40G49G80G90G54G00Z200X0Y0M03S2000G43Z10H08M08Z-14 (跟螺纹深度有关)G41 G01X21Y0D08F250 (外螺纹用G42 顺铣)M98P2018 L12 (跟螺纹深度有关)G40G01X0Y0G49G00Z200M09M30O2018G91G03 I-21 J0 Z1.5 F250 (左旋螺纹G02)M99O2008G17G40G49G80G90G54G00Z200X0Y0M03S2000G43Z10H08M08Z4 (跟螺纹深度有关)G42 G01X21Y0D08F250 (外螺纹用G41 逆铣)M98P2018 L12 (跟螺纹深度有关)G40G01X0Y0G49G00Z200M09M30O2018G91G02 I-21 J0 Z-1.5 F250 (左旋螺纹G03)M99从上往下铣右旋内螺纹:G42 G02 逆铣从下往上铣右旋内螺纹:G41 G03 顺铣(一般优先采用顺铣)从上往下铣右旋外螺纹:G42 G02 顺铣从下往上铣右旋外螺纹:G41 G03 逆铣螺纹精度通过修改刀具半径补偿值来实现,一般3~4次调整方法二O2008G17G40G49G80G90G54G00Z200X0Y0M03S2000G43Z10H08M08#1= -14 (从下往上顺铣) G01Z#1F100G41 X21Y0D08WHILE [#1 LE 0] DO1G03 I-21 J0 Z [#1+1.5]#1= #1+1.5END 1G40G01X0Y0G49G00Z200M09M30用铣刀精镗孔的技巧采用螺旋式铣削孔轮廓,配合连续下刀循环控制。
加工刃为端面刃,比走圆加工侧刃加工精度要高。
把螺纹铣刀换成端铣刀,用螺纹加工程序就可以加工,只是要注意顺铣方向。
有些箱体类工件的螺纹不适合车床,用铣床最方便,用三轴联动的数铣加工螺纹用宏程序很方便。
在加工中心上实现内外螺纹的铣削加工
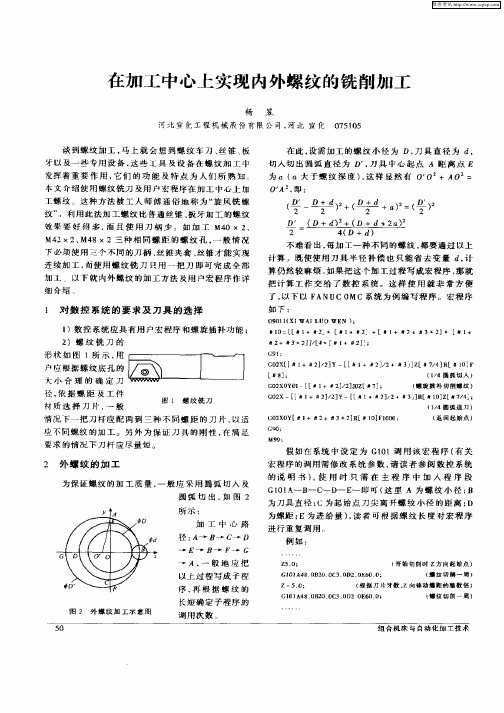
牙 以及一 些专 用 设 备 , 这些 工 具 及 设 备 在 螺纹 加 工 中 发挥 着重 要 作用 , 们 的 功 能 及 特 点 为 人 们 所 熟 知 。 它
本 文 介 绍 使 用 螺 纹 铣 刀 及 用 户 宏 程 序 在 加 工 中心 上 加 工 螺 纹 。 这 种 方 法 被 工 人 师 傅 通 俗 地 称 为 “ 风 铣 螺 旋
(/ 1 4圆 弧 退 刀 )
情 况 下 一 把 刀 杆 应 配 两 到 三 种 不 同 螺 距 的 刀 片 , 适 以 应 不 同 螺 纹 的 加 工 。 另 外 为 保 证 刀 具 的 刚 性 , 满 足 在 要 求 的情 况 下 刀 杆 应 尽 量 短 。
C 2 O 1+ 2+ 3*2 R[ 0 F 0 O O X Y【 J #i  ̄ 10
G9 0
( 回起始点) 逅
M9 9:
假 如 在 系 统 中 设 定 为 G 0 调 用 该 宏 程 序 ( 关 11 有 宏 程 序 的 调 用 需 修 改 系 统 参 数 , 读 者 参 阅 数 控 系 统 请 的 说 明 书 ) 使 用 时 只 需 在 主 程 序 中 加 入 程 序 段 , G1 1 — B c D E 即 可 ( 里 A 为 螺 纹 小 径 ; 0A — — — 一 这 B 为 刀具 直径 ; 为起 始 点 刀尖 离 开 螺 纹 小 径 的距离 ; c D 为螺 距 ; E为 进 给 量 ) 读 者 可 根 据 螺 纹 长 度 对 宏 程 序 ,
算 仍 然较 麻烦 , 果 把这个 加 工过程 写 成宏 程序 , 就 如 那
把 计 算 工 作 交 给 了 数 控 系 统 。 这 样 使 用 就 非 常 方 便
了, 以下 以 F ANUC0 MC系统 为 例编 写 程 序 。宏程 序
螺纹铣削

图1所示为M6标准内螺纹的铣削加工实例。
工件材料:铝合金;刀具:硬质合金螺纹钻铣刀;螺纹深度:10mm;铣刀转速:2,000r/mi n;切削速度:314m/min;钻削进给量:0.25mm/min;铣削进给量:0.06mm/齿;加工时间:每孔1.8s。
图1所示加工工位流程为:①位,螺纹钻铣刀快速运行至工件安全平面;②位,螺纹钻铣刀钻削至孔深尺寸;③位,螺纹钻铣刀快速提升到螺纹深度尺寸;④位,螺纹钻铣刀以圆弧切入螺纹起始点;⑤位,螺纹钻铣刀绕螺纹轴线作X、Y方向插补运动,同时作平行于轴线的+Z方向运动,即每绕螺纹轴线运行360°,沿+Z方向上升一个螺距,三轴联动运行轨迹为一螺旋线;⑥位,螺纹钻铣刀以圆弧从起始点(也是结束点)退刀;⑦位,螺纹钻铣刀快速退至工件安全平面,准备加工下一孔。
该加工过程包括了钻孔、倒角、内螺纹铣削和螺纹清根槽铣削,采用一把刀具一次完成,加工效率极高。
3 螺纹铣刀主要类型在螺纹铣削加工中,三轴联动数控机床和螺纹铣削刀具是必备的两要素。
以下介绍几种常见的螺纹铣刀类型:(1) 圆柱螺纹铣刀圆柱螺纹铣刀的外形很像是圆柱立铣刀与螺纹丝锥的结合体(见图2上,图2下为锥管螺纹铣刀),但它的螺纹切削刃与丝锥不同,刀具上无螺旋升程,加工中的螺旋升程靠机床运动实现。
由于这种特殊结构,使该刀具既可加工右旋螺纹,也可加工左旋螺纹,但不适用于较大螺距螺纹的加工。
常用的圆柱螺纹铣刀可分为粗牙螺纹和细牙螺纹两种。
出于对加工效率和耐用度的考虑,螺纹铣刀大都采用硬质合金材料制造,并可涂覆各种涂层以适应特殊材料的加工需要。
圆柱螺纹铣刀适用于钢、铸铁和有色金属材料的中小直径螺纹铣削,切削平稳,耐用度高。
缺点是刀具制造成本较高,结构复杂,价格昂贵。
(2) 机夹螺纹铣刀及刀片机夹螺纹铣刀适用于较大直径(如D>25mm)的螺纹加工。
其特点是刀片易于制造,价格较低,有的螺纹刀片可双面切削,但抗冲击性能较整体螺纹铣刀稍差。
内螺纹盲孔加工方法
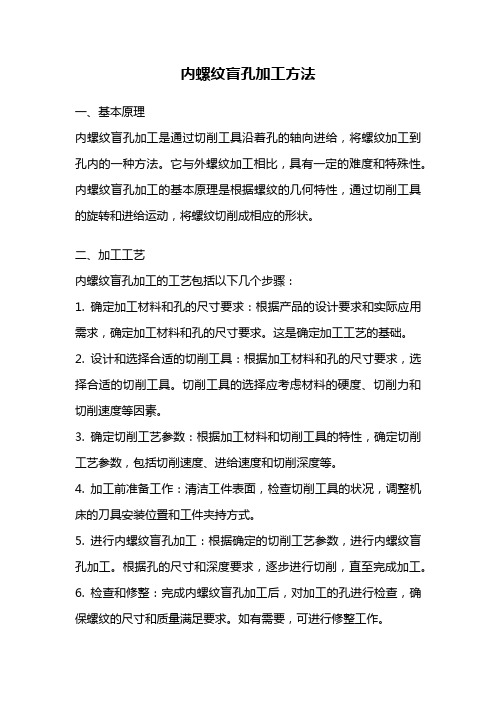
内螺纹盲孔加工方法一、基本原理内螺纹盲孔加工是通过切削工具沿着孔的轴向进给,将螺纹加工到孔内的一种方法。
它与外螺纹加工相比,具有一定的难度和特殊性。
内螺纹盲孔加工的基本原理是根据螺纹的几何特性,通过切削工具的旋转和进给运动,将螺纹切削成相应的形状。
二、加工工艺内螺纹盲孔加工的工艺包括以下几个步骤:1. 确定加工材料和孔的尺寸要求:根据产品的设计要求和实际应用需求,确定加工材料和孔的尺寸要求。
这是确定加工工艺的基础。
2. 设计和选择合适的切削工具:根据加工材料和孔的尺寸要求,选择合适的切削工具。
切削工具的选择应考虑材料的硬度、切削力和切削速度等因素。
3. 确定切削工艺参数:根据加工材料和切削工具的特性,确定切削工艺参数,包括切削速度、进给速度和切削深度等。
4. 加工前准备工作:清洁工件表面,检查切削工具的状况,调整机床的刀具安装位置和工件夹持方式。
5. 进行内螺纹盲孔加工:根据确定的切削工艺参数,进行内螺纹盲孔加工。
根据孔的尺寸和深度要求,逐步进行切削,直至完成加工。
6. 检查和修整:完成内螺纹盲孔加工后,对加工的孔进行检查,确保螺纹的尺寸和质量满足要求。
如有需要,可进行修整工作。
三、常见的加工方法内螺纹盲孔加工有多种方法,常见的包括以下几种:1. 铣削法:通过铣床等机床上的铣刀进行切削,将螺纹加工到孔内。
这种方法适用于孔径较大的孔加工,可以一次完成螺纹的加工。
2. 钻孔加工法:先通过钻床等机床进行钻孔,然后使用螺纹攻丝刀进行攻丝加工。
这种方法适用于孔径较小的孔加工,可以提高加工效率。
3. 拉削法:通过拉削刀具进行切削,将螺纹加工到孔内。
这种方法适用于孔径较大的孔加工,可以一次完成螺纹的加工。
4. 螺纹铣削法:通过螺纹铣刀进行切削,将螺纹加工到孔内。
这种方法适用于孔径较大的孔加工,可以一次完成螺纹的加工。
总结:内螺纹盲孔加工是一种常见的加工工艺,用于加工螺纹内孔。
在内螺纹盲孔加工过程中,需要根据加工材料和孔的尺寸要求,选择合适的切削工具和切削工艺参数。
内螺纹的铣削加工程序
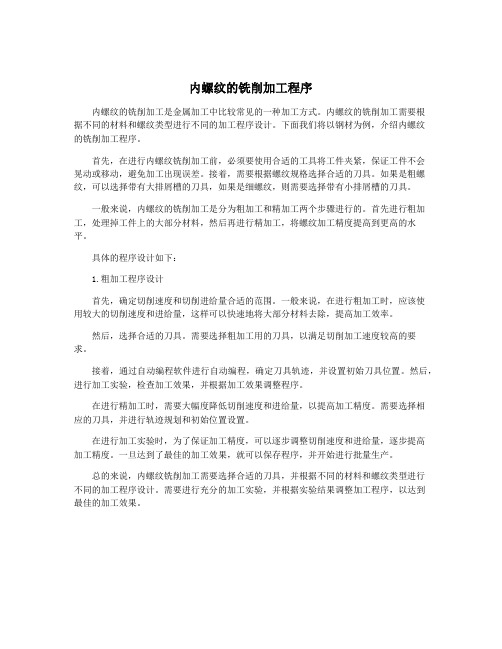
内螺纹的铣削加工程序内螺纹的铣削加工是金属加工中比较常见的一种加工方式。
内螺纹的铣削加工需要根据不同的材料和螺纹类型进行不同的加工程序设计。
下面我们将以钢材为例,介绍内螺纹的铣削加工程序。
首先,在进行内螺纹铣削加工前,必须要使用合适的工具将工件夹紧,保证工件不会晃动或移动,避免加工出现误差。
接着,需要根据螺纹规格选择合适的刀具。
如果是粗螺纹,可以选择带有大排屑槽的刀具,如果是细螺纹,则需要选择带有小排屑槽的刀具。
一般来说,内螺纹的铣削加工是分为粗加工和精加工两个步骤进行的。
首先进行粗加工,处理掉工件上的大部分材料,然后再进行精加工,将螺纹加工精度提高到更高的水平。
具体的程序设计如下:1.粗加工程序设计首先,确定切削速度和切削进给量合适的范围。
一般来说,在进行粗加工时,应该使用较大的切削速度和进给量,这样可以快速地将大部分材料去除,提高加工效率。
然后,选择合适的刀具。
需要选择粗加工用的刀具,以满足切削加工速度较高的要求。
接着,通过自动编程软件进行自动编程,确定刀具轨迹,并设置初始刀具位置。
然后,进行加工实验,检查加工效果,并根据加工效果调整程序。
在进行精加工时,需要大幅度降低切削速度和进给量,以提高加工精度。
需要选择相应的刀具,并进行轨迹规划和初始位置设置。
在进行加工实验时,为了保证加工精度,可以逐步调整切削速度和进给量,逐步提高加工精度。
一旦达到了最佳的加工效果,就可以保存程序,并开始进行批量生产。
总的来说,内螺纹铣削加工需要选择合适的刀具,并根据不同的材料和螺纹类型进行不同的加工程序设计。
需要进行充分的加工实验,并根据实验结果调整加工程序,以达到最佳的加工效果。
内锥管螺纹的铣削加工

内锥管螺纹的铣削加工一、背景内锥管螺纹是一种常见的管方式,用于连接管道与管件之间。
在此背景下,当我们需要对内锥管螺纹的管件进行加工时,铣削是一种常见的工艺。
本文将介绍内锥管螺纹的铣削加工。
二、铣削工艺2.1 铣削原理铣削是一种用刀具旋转磨削工件表面进行加工的方法。
刀具在旋转的同时,在工件的表面不断地磨削,将工件上一定量的材料去除,从而使工件表面形状、尺寸和粗糙度达到所需的要求。
2.2 铣削加工流程内锥管螺纹的铣削加工流程如下:1.首先,需要选择一台适用的铣床。
2.将内锥管螺纹的管件固定在机台台面上。
3.调整铣床等工具,使得铣刀能够持续的铣削管件的内壁。
4.开始铣削,通过调整铣刀和工件的相对位置和角度,来确保铣削过程中的质量。
2.3 铣削类型铣削根据刀具移动方式的不同,可以分为手动铣削和数控铣削两种类型。
在实际应用中,数控铣床的使用正日益普及。
三、内锥管螺纹的铣削加工要点在内锥管螺纹的铣削加工中,需要注意以下几个要点:3.1 切削角度切削角度决定了铣刀接触到工件内壁的面数,应确保切削角度在合适范围内,一般大于60°。
3.2 精度和表面质量在铣削加工过程中,需要根据实际需求,确保工件内壁的精度和表面质量。
一般来说,精度越高,表面质量就越好。
3.3 刀具选择选择合适的刀具是内锥管螺纹铣削加工过程中的关键之一。
按照不同需求,可以选用不同类型的铣刀来完成铣削加工。
3.4 内冷却液为了确保内锥管螺纹铣削加工过程中的顺利进行,可以采用内冷却液来提高工具寿命、降低表面质量,并减少切屑对工件的影响。
四、安全注意事项内锥管螺纹铣削加工过程中,需要注意以下安全事项:1.操作前需要确认机台和工件的固定情况,避免意外事故发生;2.穿戴好防护工具,避免铣刀对人身造成伤害;3.铣削至深度过大时,需要逐步进行,并注意切削力的变化以确保安全。
五、总结内锥管螺纹铣削加工是一种重要的加工方式,需要注意切削角度、精度和表面质量、刀具选择、内冷却液和安全事项等问题。
螺纹加工方法

螺纹加工方法
螺纹是一种常见的机械零件,用于连接、固定等方面。
下面介绍几种常见的螺纹加工方法:
1. 铣削法。
利用铣床来加工螺纹,先将工件固定在工作台上,然后选择适当的铣刀,按照要求的螺距和角度进行铣削。
这种方法适合中小型批量生产,可以保证螺纹的精度和表面质量。
2. 滚齿法。
滚齿法是通过专门的滚齿车床来加工螺纹,先将工件装夹在车床上,然后使用精密的滚轮对工件进行滚压,形成螺纹。
这种方法适用于大批量生产,可以提高生产效率和降低成本。
3. 切削法。
切削法是通过螺纹车床或普通车床来加工螺纹,利用车刀沿着螺旋线轨迹进行切削,形成螺纹。
这种方法适合对螺纹尺寸和精度要求较高的情况。
4. 跳动切割法。
跳动切割法是通过专门的切削刀具来加工螺纹,刀具在跳动的同时进行切割,从而形成螺旋线条。
这种方法适用于一些复杂的非标准螺纹加工。
总之,不同的螺纹加工方法各有优缺点,需要根据实际生产需要选择合适的方法。
在加工过程中还需注意选用合适的切削参数,控制切削速度和深度,以确保加工质量和效率。
加工中心铣螺纹编程实例
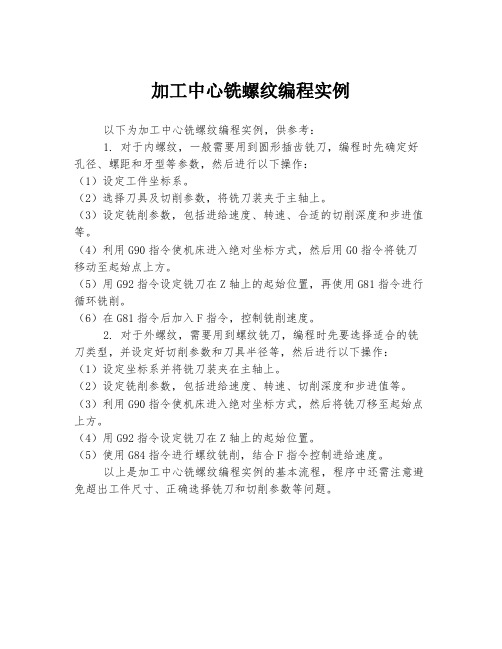
加工中心铣螺纹编程实例
以下为加工中心铣螺纹编程实例,供参考:
1. 对于内螺纹,一般需要用到圆形插齿铣刀,编程时先确定好孔径、螺距和牙型等参数,然后进行以下操作:
(1)设定工件坐标系。
(2)选择刀具及切削参数,将铣刀装夹于主轴上。
(3)设定铣削参数,包括进给速度、转速、合适的切削深度和步进值等。
(4)利用G90指令使机床进入绝对坐标方式,然后用G0指令将铣刀移动至起始点上方。
(5)用G92指令设定铣刀在Z轴上的起始位置,再使用G81指令进行循环铣削。
(6)在G81指令后加入F指令,控制铣削速度。
2. 对于外螺纹,需要用到螺纹铣刀,编程时先要选择适合的铣刀类型,并设定好切削参数和刀具半径等,然后进行以下操作:(1)设定坐标系并将铣刀装夹在主轴上。
(2)设定铣削参数,包括进给速度、转速、切削深度和步进值等。
(3)利用G90指令使机床进入绝对坐标方式,然后将铣刀移至起始点上方。
(4)用G92指令设定铣刀在Z轴上的起始位置。
(5)使用G84指令进行螺纹铣削,结合F指令控制进给速度。
以上是加工中心铣螺纹编程实例的基本流程,程序中还需注意避免超出工件尺寸、正确选择铣刀和切削参数等问题。
螺纹的加工方法

螺纹的加工方法
一、螺纹加工的基本方法:
1.外螺纹加工:
(1)车削方式:
利用专用车削机和专用刀具,安装在车床上,在车床转动时,螺纹刀具在工件表面车削,从而形成螺纹,这是最常用的加工方法,其优点是螺纹加工质量可靠,可在实际工作中实现大批量生产。
(2)滚压方式:
利用滚压机,将工件与滚压刀具固定,然后通过滚压冲头的转动,将滚压刀具和工件压缩,从而形成螺纹,这种方法可以一次性滚压出多个螺纹,适用于大批量生产,但螺纹加工质量不如车削质量高。
2.内螺纹加工:
(1)切削方式:
利用专用内螺纹切削机,安装在切削机上,利用内螺纹切削刀具,在工件表面切削,从而形成内螺纹,这种方法质量较高,但速度较慢,只适用于小批量生产。
(2)孔铣方式:
利用孔铣机,安装在孔铣机上,利用专用立铣刀具,在工件表面铣削,从而形成内螺纹,这种方法可以一次性完成大量内螺纹的加工,适用于大批量生产,但螺纹加工质量不如切削质量高。
二、螺纹加工的其他方法:
1.螺纹铸造:
利用特殊的铸造模具,将合金锻件铸入模具中,然后冷却后,就可以得到铸造出来的螺纹,这种方法可以有效的提高螺纹加工质量,但适用于小批量生产。
2.冷冲压螺纹:
利用冷冲压螺纹模具,在模具中将金属材料压制成螺纹,这种方法也可以有效的提高螺纹加工质量,但也只适用于小批量生产。
螺纹铣刀的铣螺纹加工详解
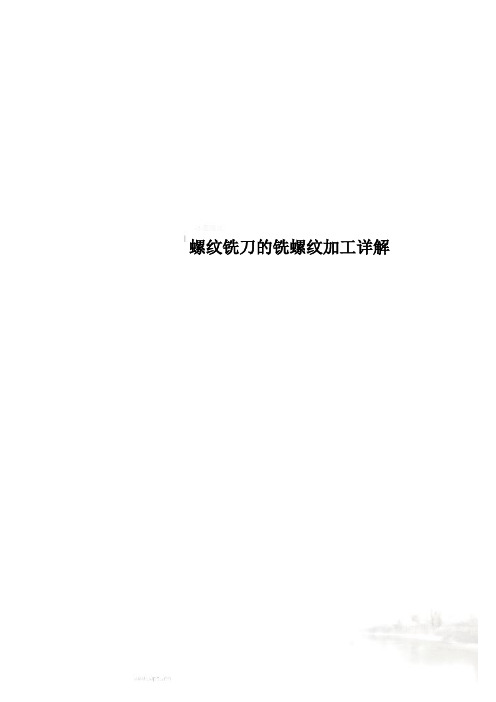
螺纹铣刀的铣螺纹加工详解螺纹铣刀的铣螺纹加工详解编辑:洛希尔螺纹刀具随着时代的进步,数控行业在我国大中型机械加工业用得越来越广泛,一些大型零件的螺纹加工,传统的螺纹车削和丝锥、板牙已无法满足生产的需要。
而在数控铣床或加工中心得到广泛应用的今天,采用三轴联动机床进行螺纹加工,改变了螺纹的加工工艺方法,取得了良好的效果。
一、螺旋铣削内孔1.加工范围孔径较大的盲孔或通孔,由于麻花钻加工太慢或不能加工,往往选择螺旋铣削的方式。
而且由于该方式选择的刀具不带底刃,所以更适合小切深、高转速及大进给的加工情况。
2.加工特点螺旋铣削加工孔是建立在螺旋式下刀方法基础上的加工方法,螺旋铣孔时有一个特点:每螺旋铣削一周,刀具的Z轴方向移动一个下刀高度。
3.螺纹铣刀的选择选择16mm 的三刃转位铣刀,刀具转速S=3000r/min,进给量F=2500mm/min。
4.说明这种方法在螺旋铣削内孔上很有特色,其程序编写的实质就是将一个下刀高度作为螺旋线高度编成一个子程序,通过循环调Z5.0;(快速移动点定位)G01Z0F50;(工进到)G41D01G01X-6.875Y10.0;(D01=8.0,在0A 段建立刀补)G03X-16.875Y0R10;(圆弧导入R10)M98P100L16;(调用子程序O100,调用次数16 次) G90G03X-6.875Y-10R10.0;(光整轮廓一周)G40G01X0Y0;(取消刀补)G0Z50.0;(退出)M05;(主轴停止)M30;(程序结束并返回程序头)%(程序结束符)子程序如下。
%(程序开始符)O100;(子程序)G91G03I16.875Z-2.0F2500;(运用增量坐标值编写,每运行一周刀具在Z轴方向向下移动2mm)M99;(返回主程序)%(程序结束符)通过螺旋式下刀的方法加工内孔,同时也可以按照这种编程思路加工圆柱类工件。
二、单刃螺纹铣刀加工螺纹1.加工范围同一把螺纹铣刀既可以铣削左旋螺纹又可以铣削右旋螺纹,既可以铣削内旋螺纹又可以铣削外螺纹,同时不受螺距和螺纹规格的影响。
螺纹的宏程序铣削加工分析
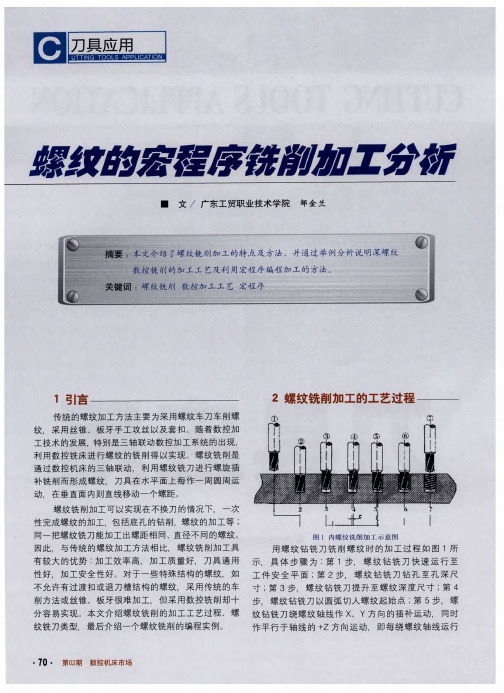
合 适的螺纹底 孔对于螺纹加工是十分重要的。一 个尺 寸稍 大的螺纹底孔能 有效降低攻丝过程 中产 生的
3螺 纹铣 削轨 迹
切 削热和 切削力。但 它也会减 小螺纹的接触率。 国家
螺 纹 铣 削运 动 轨 迹 为 一螺 旋 线 ,可 通过 数 控机 床 标 准 和技 术 委 员会 规 定 : 深 孔 中, 允 许 在 孔 壁 上 只 在 的三轴联动来 实现 。图 2为左旋 和右旋外螺纹 的铣削 攻 出螺纹 全高 的 5 %。这一 点在 对特 殊材 料 和难加 O
%
1 1 .2 = 69 2 1 = 8
‘ 螺纹底孔半径 。 螺纹公称半径 。 螺纹长度
长 度 L 2 mm: =5 螺距 := mr: P 2 整体 圆柱 螺纹 铣刀直 # = 5 n 32 径 : 2 1 mm, D =4 切削刃长 为 3 mm: 削方式 : 4 铣 顺铣。 42 = 切 削速度 :0 5 mm/ n m_1每齿进给量 f0 1 = .mm。 ()参数计算 1
的螺纹 时,这种情况通 常称 为深孔攻丝。 加工 一个深 孔螺纹,意味 着刀具 与工件之间需长
时要 求丝锥后 角为 4 。 0 。在 加工钛金 属时,在丝锥 上 磨 出大的后角,有利于排 屑。另外,全磨制 丝锥和刃 背铲磨 的丝锥也有利于攻丝。
D、冷 却 液
时间的接触。 同时,在加工过程 中会产生更 多的切 削
42深螺纹加工实例 .
现结合 M3 x2右旋 内螺纹铣削加工实例说 明螺 6 纹铣 削的编程 方法。工 件材料 :5钢 , 4 调质 : 螺纹底 孔 直 径 : i3 .4 D= 38 mm: 纹 直 径 : 0 3 mm: 纹 螺 D=6 螺
螺纹加工方法

螺纹加工方法在工件上加工出内﹑外螺纹的方法,主要有切削加工和滚压加工两类。
螺纹原理的应用可追溯到公元前 220年希腊学者阿基米德创造的螺旋提水工具。
公元4世纪,地中海沿岸国家在酿酒用的压力机上开始应用螺栓和螺母的原理。
当时的外螺纹都是用一条绳子缠绕到一根圆柱形棒料上,然后按此标记刻制而成的。
而内螺纹则往往是用较软材料围裹在外螺纹上经锤打成形的。
1500年左右,意大利人列奥纳多‧达芬奇绘制的螺纹加工装置草图中,已有应用母丝杠和交换齿轮加工不同螺距螺纹的设想。
此后,机械切削螺纹的方法在欧洲钟表制造业中有所发展。
1760年,英国人J.怀亚特和W.怀亚特兄弟获得了用专门装置切制木螺钉的专利。
1778年,英国人J.拉姆斯登曾制造一台用蜗轮副传动的螺纹切削装置,能加工出精度很高的长螺纹。
1797年,英国人莫兹利,H.在由他改进的车床上,利用母丝杠和交换齿轮车削出不同螺距的金属螺纹,奠定了车削螺纹的基本方法。
19世纪20年代,莫兹利制造出第一批加工螺纹用的丝锥和板牙。
20世纪初,汽车工业的发展进一步促进了螺纹的标准化和各种精密﹑高效螺纹加工方法的发展,各种自动张开板牙头和自动收缩丝锥相继发明,螺纹铣削开始应用。
30年代初,出现了螺纹磨削。
螺纹滚压技术虽在19世纪初期就有专利,但因模具制造困难,发展很慢,直到第二次世界大战时期(1942~1945),由于军火生产的需要和螺纹磨削技术的发展解决了模具制造的精度问题,才获得迅速发展。
1) 螺纹切削一般指用成形刀具或磨具在工件上加工螺纹的方法,主要有车削﹑铣削﹑攻丝﹑套丝﹑磨削﹑研磨和旋风切削等。
车削﹑铣削和磨削螺纹时,工件每转一转,机床的传动链保证车刀﹑铣刀或砂轮沿工件轴向准确而均匀地移动一个导程。
在攻丝或套丝时,刀具(丝锥或板牙)与工件作相对旋转运动,并由先形成的螺纹沟槽引导着刀具(或工件)作轴向移动。
螺纹车削 (图1 螺纹车削) 在车床上车削螺纹可采用成形车刀或螺纹梳刀(见螺纹加工工具)。
内锥螺纹加工方法
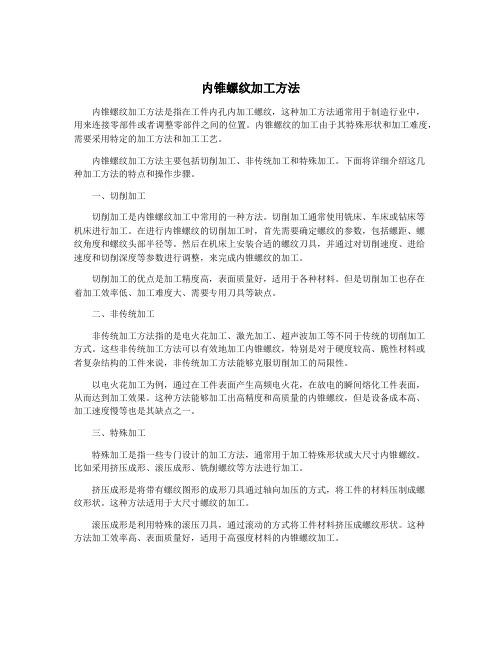
内锥螺纹加工方法内锥螺纹加工方法是指在工件内孔内加工螺纹,这种加工方法通常用于制造行业中,用来连接零部件或者调整零部件之间的位置。
内锥螺纹的加工由于其特殊形状和加工难度,需要采用特定的加工方法和加工工艺。
内锥螺纹加工方法主要包括切削加工、非传统加工和特殊加工。
下面将详细介绍这几种加工方法的特点和操作步骤。
一、切削加工切削加工是内锥螺纹加工中常用的一种方法。
切削加工通常使用铣床、车床或钻床等机床进行加工。
在进行内锥螺纹的切削加工时,首先需要确定螺纹的参数,包括螺距、螺纹角度和螺纹头部半径等。
然后在机床上安装合适的螺纹刀具,并通过对切削速度、进给速度和切削深度等参数进行调整,来完成内锥螺纹的加工。
切削加工的优点是加工精度高,表面质量好,适用于各种材料。
但是切削加工也存在着加工效率低、加工难度大、需要专用刀具等缺点。
二、非传统加工非传统加工方法指的是电火花加工、激光加工、超声波加工等不同于传统的切削加工方式。
这些非传统加工方法可以有效地加工内锥螺纹,特别是对于硬度较高、脆性材料或者复杂结构的工件来说,非传统加工方法能够克服切削加工的局限性。
以电火花加工为例,通过在工件表面产生高频电火花,在放电的瞬间熔化工件表面,从而达到加工效果。
这种方法能够加工出高精度和高质量的内锥螺纹,但是设备成本高、加工速度慢等也是其缺点之一。
三、特殊加工特殊加工是指一些专门设计的加工方法,通常用于加工特殊形状或大尺寸内锥螺纹。
比如采用挤压成形、滚压成形、铣削螺纹等方法进行加工。
挤压成形是将带有螺纹图形的成形刀具通过轴向加压的方式,将工件的材料压制成螺纹形状。
这种方法适用于大尺寸螺纹的加工。
滚压成形是利用特殊的滚压刀具,通过滚动的方式将工件材料挤压成螺纹形状。
这种方法加工效率高、表面质量好,适用于高强度材料的内锥螺纹加工。
铣削螺纹是利用铣削工具在内孔上进行切削,在达到螺纹要求尺寸后,再在螺纹顶部和螺纹底部分别用倒角铣刀做成倒角,以减小螺纹头或底部造成的应力集中。
如何进行内螺纹和外螺纹的铣削加工?

如何进行内螺纹和外螺纹的铣削加工?谢谢邀请回答我们以常见的加工中心操作系统:FANU0I来讲解。
现以加工M30X1.5的内螺纹与M27×3的外螺纹为例。
一、根据通用工艺的加工方法,确定加工内外螺纹的方法,并根据加工工艺准备工量具。
然后编程。
二、刀具1.内螺纹的铣削如图所示,加工零件几何中心的M30X1.5内螺纹。
单齿螺纹铣刀的螺纹加工原理是:刀具每固定旋转一周,在Z轴负方向上下降一个螺距。
计算螺纹M30×1.5的底孔直径:公称直径-1.08P=30-1.62=28.38mm,所以螺纹底孔孔径为28.38mm的通孔。
选用⌀12mm两齿立铣刀,主轴S=700r/min,刀具材料为高速钢,进给F=120mm/min,刀具伸出长度为28mm,编写程序如下:O0005M06T01G54G90G40M03S1250G00X0Y0Z100Z5G01Z0F40#1=-4N10G01Z[#1]F100G41D01G01X14.25F120G03I-14.25J0G40G01X0#1=#1-4IF[#1GE-20]GOTOG00Z100Y150M05M302、底孔加工完成后,用⌀32钻倒C1.5mm的角,用⌀14mm的单刃螺纹铣刀铣削,转速S=1250r/min,F=120mm/min程序编写如下:O0006M06T02G54G90G40M03S1250G0X0Y0Z100Z5G01Z0F40#1=0N10#2=#1-1.5G42D02G01X14,.19G02Z[#2]I-14.19#1=#1-1.5IF[#1GE-21]GOTO10G40G01X0G00Z100Y150MO5M303、用9齿螺纹梳刀(T03)铣削螺纹,主轴转速S=1250r/min,F=120mm/min。
应用实例编程如下:O0007M06T03G54G90G40M3S1250G00X0Y0Z100Z5G01Z0F40#1=-12N10G01Z[#1]F120G42D01X14.25G02Z[#1-1.5]I-14.25G40G01X0#1=#1-13.5IF[#1GE-22.5]GOTO10G00Z100Y150M05M302.外螺纹的铣削O0008M06T04G54G90G40M03S1200 G00X35Y0Z100Z5G01Z0F50G41G01X13.5F160G02Z[#2]l13.5G40G01X35G00Z100M05M30对于螺距P=3mm的外螺纹,根据背吃刀量的不同,一般选择7-8刀加工成型。
螺纹铣刀的铣螺纹加工详解

编辑:洛希尔螺纹刀具随着时代的进步,数控行业在我国大中型机械加工业用得越来越广泛,一些大型零件的螺纹加工,传统的螺纹车削和丝锥、板牙已无法满足生产的需要。
而在数控铣床或加工中心得到广泛应用的今天,采用三轴联动机床进行螺纹加工,改变了螺纹的加工工艺方法,取得了良好的效果。
一、螺旋铣削内孔1.加工范围孔径较大的盲孔或通孔,由于麻花钻加工太慢或不能加工,往往选择螺旋铣削的方式。
而且由于该方式选择的刀具不带底刃,所以更适合小切深、高转速及大进给的加工情况。
2.加工特点螺旋铣削加工孔是建立在螺旋式下刀方法基础上的加工方法,螺旋铣孔时有一个特点:每螺旋铣削一周,刀具的Z轴方向移动一个下刀高度。
3.螺纹铣刀的选择选择16mm 的三刃转位铣刀,刀具转速S=3000r/min,进给量F=2500mm/min。
4.说明这种方法在螺旋铣削内孔上很有特色,其程序编写的实质就是将一个下刀高度作为螺旋线高度编成一个子程序,通过循环调用该螺旋线子程序,完成整个孔的铣削加工。
该方法加工孔不受铣刀规格等因素影响,所以在数控铣床和加工中心上应用比较理想。
5.应用实例及程序编写如图1所示的零件图中,要加工螺纹M36×的底孔通孔。
首先,计算螺纹M36×的底孔直径为:公称直径×P(螺距)=×=。
确认该零件的加工毛坯为80mm ×80mm ×30mm的45钢,选定刀具为16mm三刃转位铣刀,刀具转速S=3000r/min,进给量F=2500mm/min。
圆弧导入点为A(图2),在0A段建立刀补,圆弧导出点为B,在0B段取消刀补。
参考程序编写如下(本文涉及到的参考程序均在FANUC系统中验证使用)。
主程序如下。
%(程序开始符)O0001;(主程序名)T1;(刀具为16mm的立铣刀)G80G40G69 ;(取消固定循环、刀具半径补偿和旋转指令)G90G54G00X0Y0M03S3000;(程序初始化)H01;(1 号刀具长度补偿);(快速移动点定位)G01Z0F50;(工进到),在 0A 段建立刀补);(圆弧导入 R10)M98P100L16;(调用子程序 O100,调用次数 16 次)光整轮廓一周)G40G01X0Y0;(取消刀补);(退出)M05;(主轴停止)M30;(程序结束并返回程序头)%(程序结束符)子程序如下。
螺纹铣刀的铣螺纹加工详解

螺纹铣刀的铣螺纹加工详解Document serial number【KKGB-LBS98YT-BS8CB-BSUT-BST108】螺纹铣刀的铣螺纹加工详解编辑:洛希尔螺纹刀具随着时代的进步,数控行业在我国大中型机械加工业用得越来越广泛,一些大型零件的螺纹加工,传统的螺纹车削和丝锥、板牙已无法满足生产的需要。
而在数控铣床或加工中心得到广泛应用的今天,采用三轴联动机床进行螺纹加工,改变了螺纹的加工工艺方法,取得了良好的效果。
一、内孔1.加工范围孔径较大的盲孔或通孔,由于麻花钻加工太慢或不能加工,往往选择螺旋铣削的方式。
而且由于该方式选择的刀具不带底刃,所以更适合小切深、高转速及大进给的加工情况。
2.加工特点螺旋铣削加工孔是建立在螺旋式下刀方法基础上的加工方法,螺旋铣孔时有一个特点:每螺旋铣削一周,刀具的Z轴方向移动一个下刀高度。
3.螺纹铣刀的选择选择16mm 的三刃转位铣刀,刀具转速S=3000r/min,进给量F=2500mm/min。
4.说明这种方法在螺旋铣削内孔上很有特色,其程序编写的实质就是将一个下刀高度作为螺旋线高度编成一个子程序,通过循环调用该螺旋线子程序,完成整个孔的铣削加工。
该方法加工孔不受铣刀规格等因素影响,所以在数控铣床和加工中心上应用比较理想。
5.应用实例及程序编写如图1所示的零件图中,要加工螺纹M36×的底孔通孔。
首先,计算螺纹M36×的底孔直径为:公称直径×P(螺距)=×=。
确认该零件的加工毛坯为80mm ×80mm ×30mm的45钢,选定刀具为16mm三刃转位铣刀,刀具转速S=3000r/min,进给量F=2500mm/min。
圆弧导入点为A(图2),在0A段建立刀补,圆弧导出点为B,在0B段取消刀补。
参考程序编写如下(本文涉及到的参考程序均在FANUC系统中验证使用)。
主程序如下。
%(程序开始符)O0001;(主程序名)T1;(刀具为16mm的立铣刀)G80G40G69 ;(取消固定循环、刀具半径补偿和旋转指令)G90G54G00X0Y0M03S3000;(程序初始化)H01;(1 号刀具长度补偿);(快速移动点定位)G01Z0F50;(工进到),在 0A 段建立刀补);(圆弧导入 R10)M98P100L16;(调用子程序 O100,调用次数 16 次)光整轮廓一周)G40G01X0Y0;(取消刀补);(退出)M05;(主轴停止)M30;(程序结束并返回程序头)%(程序结束符)子程序如下。
- 1、下载文档前请自行甄别文档内容的完整性,平台不提供额外的编辑、内容补充、找答案等附加服务。
- 2、"仅部分预览"的文档,不可在线预览部分如存在完整性等问题,可反馈申请退款(可完整预览的文档不适用该条件!)。
- 3、如文档侵犯您的权益,请联系客服反馈,我们会尽快为您处理(人工客服工作时间:9:00-18:30)。
以加工M30×1.5的内螺纹和M27×3的外螺纹为例,来介绍内螺纹和外螺纹的铣削加工方法。
一、加工准备
根据通用工艺方法,确定内外螺纹的铣削方法,并根据加工方法准备工量具,编制程序。
二、刀具清单
1、内螺纹的铣削
如下图所示,加工零件图几何中心的M30×1.5的内螺纹。
1)工件材料:45钢正火,模锻。
90mm×90mm×20mm 2)加工要求:螺纹表面粗糙度值Rp=1.6;牙形角为60度3)加工中心操作系统:FANUC0I
4)刀具:单齿螺纹铣刀,9齿螺纹梳刀
在用螺纹铣刀铣削螺纹之前,要先完成螺纹底孔的加工,继而进行螺纹加工。
单齿螺纹铣刀的螺纹加工原理是:
刀具每固定旋转一周,在Z轴负方向上下降一个螺距。
计算螺纹M30×1.5的底孔直径:公称直径-1.08P=30-1.62=28.38mm,所以螺纹底孔孔径为28.38mm的通孔。
选用⌀12mm两齿立铣刀,主轴S=700r/min,刀具材料为高速钢,进给F=120mm/min,刀具伸出长度为
28mm,编写程序如下:
O0001(程序名)
M06T01(使用1号刀)
G54G90G40M03S1200(程序初始化)
G00X0Y0Z100(刀具快速定位)
Z5
G01Z0F40(刀具工进到工件表面)
#1=-4(将-4赋值于局部变量#1)
N10G01Z[#1]F100(刀具工进到Z-4)
G41D01G01X14.25F120(固定循环,刀具半径补偿)
G03I-14.25J0(逆时针铣圆一周)
G40G01X0(取消刀具半径补偿)
#1=#1-4(将#1-4赋值于局部变量#1)
IF[#1GE-20]GOTO(条件判别语句,如果#1大于-20,则跳转至N10继续加工)
G00Z100(快速抬刀)
Y150
M05(主轴停止)
M30(程序结束)
2、确认底孔加工完成,并用⌀32倒角钻倒C1.5mm的角以后,选择⌀14mm的单刃螺纹铣刀铣削,转速
S=1200r/min,F=120mm/min程序编写如下:
O0002(程序名)
M06T02(换2号刀)
G54G90G40M03S1200(程序初始化)
G0X0Y0Z100
Z5(刀具快速移动到定位点)
G01Z0F40(刀具工进到工件表面)
#1=0(将0赋值于局部变量#1)
N10#2=#1-1.5(将#1-1.5赋值于局部变量#2)
G42D02G01X14,.19
G02Z[#2]I-14.19(圆弧导入半径)
#1=#1-1.5
IF[#1GE-21]GOTO10(条件判别语句,如果#1大于-21,则跳转至N10继续执行程序)
G40G01X0(取消刀具半径补偿)
G00Z100(快速抬刀)
Y150
MO5(主轴停止)
M30(程序结束)
3、选择9齿螺纹梳刀(T03)铣削螺纹,主轴转速
S=1200r/min,F=120mm/min,这种加工效率非常高,加工时间大大缩短,在大批量加工螺纹中,具有很大优势。
对于不同规格的螺纹,只要选择不同的刀具即可。
应用实例编程如下:
O0003(程序名)
M06T03(换3号刀)
G54G90G40M3S1200(程序初始化)
G00X0Y0Z100
Z5(刀具快速定位)
G01Z0F40(工进到工件表面)
#1=-12(将-12赋值于局部变量#1)
N10G01Z[#1]F120
G42D01X14.25(刀具半径补偿)
G02Z[#1-1.5]I-14.25(圆弧切入)
G40G01X0(取消刀补)
#1=#1-13.5(将#1-13.5赋值于局部变量#1)
IF[#1GE-22.5]GOTO10(条件判别语句,如果#1大于-22.5,则跳转至N10继续执行程序)
G00Z100
Y150(快速抬刀)
M05(主轴停止)
M30(程序结束)
2. 外螺纹的铣削
螺纹在加工中心上的铣削,相比较板牙套扣丝锥等加工螺纹方法,受刀具等限制较小,对于同一把螺纹铣刀,即可加工相同螺距的内螺纹,也可加以外螺纹,如下图所示,以加工M27×3的外螺纹为例。
O0004(程序名)
M06T04(换4号刀)
G54G90G40M03S1200(程序初始化)
G00X35Y0Z100(刀具快速定位)
Z5
G01Z0F50(刀具工进到工件表面)
G41G01X13.5F120(刀具半径补偿)
#1=0(将0赋值于局部变量#1)
N10#2=#1-3(将#1-3赋值于局部变量#2)
G02Z[#2]I13.5(圆弧切入)
#1=#1-3(将#1-3赋值于局部变量#1)
IF[#1GE-39]GOTO10(条件判别语句,如果#1大于-39,则跳转至N10继续执行程序)
G40G01X35(取消刀补)
G00Z100(快速抬刀)
M05(主轴停止)
M30(程序结束)
对于螺距P=3mm的外螺纹,牙深为1.949Mmm,根据背吃刀量的不同,故一般选择6-8刀加工完成。
每次加工的背吃刀量大致可选择:
0.6mm,0.35mm,0.3mm,0.2mm,0.2mm,0.2mm,0.1mm,每加工一刀,测量一次,逐步控制尺寸。
选用6齿螺纹梳刀:
O0005(程序名)
M06T05(换5号刀)
G54G90G40M03S1200(程序初始化)
G00X35Y0Z100()
Z5(刀具快速定位)
G01Z0F50(工进到工件表面)
G41D04G01X13.5F120(刀具半径补偿)
#1=-15(将-15赋值于局部变量#1)
N10#2=#1-3(将#1-3赋值于局部变量#2)
G02Z[#2]I13.5(圆弧切入)
#1=#1-18(将-18赋值于局部变量#1)
IF[#1GE-39]GOTO10(条件判别语句,如果#1大于-39,则跳转至N10继续执行程序)
G40G01X35(取消刀补)
G00Z100(快速抬刀)
M05(主轴停止)
M30(程序结束)。