一种新型的液冷机箱及冷板散热系统的研究
液冷机箱散热性能数值研究
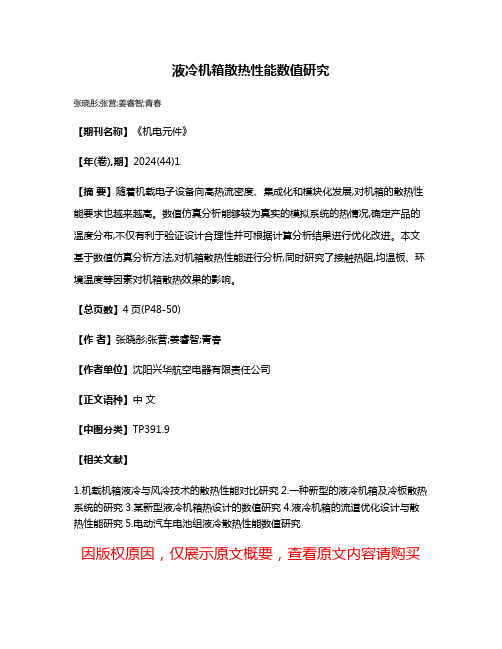
液冷机箱散热性能数值研究
张晓彤;张营;姜睿智;青春
【期刊名称】《机电元件》
【年(卷),期】2024(44)1
【摘要】随着机载电子设备向高热流密度、集成化和模块化发展,对机箱的散热性能要求也越来越高。
数值仿真分析能够较为真实的模拟系统的热情况,确定产品的温度分布,不仅有利于验证设计合理性并可根据计算分析结果进行优化改进。
本文基于数值仿真分析方法,对机箱散热性能进行分析,同时研究了接触热阻,均温板、环境温度等因素对机箱散热效果的影响。
【总页数】4页(P48-50)
【作者】张晓彤;张营;姜睿智;青春
【作者单位】沈阳兴华航空电器有限责任公司
【正文语种】中文
【中图分类】TP391.9
【相关文献】
1.机载机箱液冷与风冷技术的散热性能对比研究
2.一种新型的液冷机箱及冷板散热系统的研究
3.某新型液冷机箱热设计的数值研究
4.液冷机箱的流道优化设计与散热性能研究
5.电动汽车电池组液冷散热性能数值研究
因版权原因,仅展示原文概要,查看原文内容请购买。
机载机箱液冷与风冷技术的散热性能对比研究

机载机箱液冷与风冷技术的散热性能对比研究赵波【摘要】随着机载机箱内部的热密度越来越高以及安装空间的有限性,对机箱的散热性能和外形尺寸也提出了更高的要求. 首先分析了强迫风冷的散热方式,其次运用Flotherm软件对液冷机箱的散热性能进行了仿真验证,结果表明液冷机箱能更好地满足高热流密度的散热要求和结构外形要求.%With heat density inside the airborne cabinet rapidly improves higher and higher, and considering the limited instal-lation space, we propose higher request to the heat dissipation and the boundary dimension of cabinet. In this paper, we firstly introduce the heat dissipation pattern of forced-air cooling, and then use the software FLOTHERM to conduct simulation veri-fication on the heat dissipation performance of the liquid-cooled chassis. The results show that liquid-cooled chassis can bet-ter satisfies requirements on aspects of the heat dissipation and the structure appearance of high heating flux density.【期刊名称】《机械研究与应用》【年(卷),期】2015(028)006【总页数】3页(P10-11,13)【关键词】液冷机箱;热设计;强迫风冷【作者】赵波【作者单位】中国电子科技集团公司第三十六研究所,浙江嘉兴 314033【正文语种】中文【中图分类】V243.2随着电子技术的发展,高功耗电子器件的增多,且目前机箱基本都采用标准模块,热流密度大,散热空间小,随之带来的问题就是对电子设备的散热性能要求越来越高,器件过热已成为电子产品实效的主要原因之一,严重影响了电子设备的可靠性和工作寿命。
计算机液气一体式CPU散热器设计研究

计算机液气一体式CPU散热器设计研究作者:***来源:《电脑知识与技术》2022年第36期关键词:CPU 散热器;液气一体式;水冷(液冷);风冷中图分类号:TP311 文献标识码:A文章编号:1009-3044(2022)36-0118-03计算机经过半个多世纪的发展,已在各行各业被广泛应用,引起了产业结构、产品结构、经营管理和服务方式等方面的重大变革。
计算机的运算核心和控制核心是一块超大规模的集成电路,被称为中央处理器(CPU,Central Processing Unit)[1]。
随着计算机在性能、计算量以及体积等方面的革新与进步,CPU朝高集成化、小型化和高频化趋势发展,导致CPU运算产生的热量不断增加。
由于CPU主要以硅或硅化合物为材料制造,而硅的导热性不佳,因此CPU产生的热量无法及时散出,轻则导致死机,重则可能将CPU烧毁,给电脑带来潜在的隐患[2]。
总之,散热对CPU的稳定运行和使用寿命起着决定性的作用。
所谓散热,就是想办法将热源的热量带走。
就散热方式而言,CPU冷却可分为主动散热和被动散热两种方式。
目前市面的风冷和液冷散热技术属于被动散热。
两种散热技术各有优缺点,如风冷体积小,价格低,是现在普通家庭计算机使用的首选。
但风冷主要是铜管和风扇联用,而铜的比热容较小,导致当CPU超频工作过热时,铜管无法及时散热,热量堆积,损坏CPU。
液冷散热效率高,但是冷排与液泵的体积过于庞大,严重占用机箱体积,而且使用塑胶管运水,在CPU过热时会导致胶管老化,出现漏液等[1-4]。
因此,设计体积小且散热效率高的散热器已成CPU亟待解决的关键问题。
鉴于液冷和风冷散热器各有千秋,本研究试图设计出一款融二者为一体的液气一体式CPU散热器,发挥出风冷散热器体积小,液冷散热器散热效率高的优点。
1 材料与方法1.1 组成材料本研究设计所需要的材料主要包括1个水泵、大小两种规格的铜管,2台风扇、铜板、铝块、空心铝管。
一种数据中心冷却系统以及数据中心实用新型专利

通过自动调节温度和控制装置的智能算法 ,确保数据中心稳定运行,减少因温度波 动引起的故障。
可维护性高
相比传统冷却系统,该系统具有更低的能 耗和碳排放,符合绿色环保理念。
采用模块化设计,便于安装与维护,降低 运营成本。
04
实用新型专利的优点与效 果
高效冷却效果
冷却效率高
该实用新型专利的冷却系统采用了先进的冷凝技术和高效的 散热器,能够快速将服务器产生的热量散发出去,保持数据 中心内部的适宜温度。
附图说明与具体实施方式
系统架构图与工作流程
系统架构图
该数据中心冷却系统包括热交换器、风 扇、温度传感器、控制模块等组件。
VS
工作流程
数据中心产生的热量通过热交换器进行热 量交换,同时风扇对热交换器进行散热, 温度传感器监测温度,并将信息反馈给控 制模块,控制模块根据温度调节风扇转速 ,以实现数据中心冷却。
提高数据处理效率与稳定性
提高数据处理效率
该实用新型专利的冷却系统能够保持数据中心内部的适宜温度,使得服务器等数 据处理设备能够更好地运行,提高数据处理效率和性能。
提高数据稳定性
由于该冷却系统能够保持稳定的温度和湿度,可以减少因环境因素导致的服务器 故障和数据丢失,提高数据中心的可靠性和稳定性。
05
当前,随着电子信息技术的快速发展,数据中心的高密度化、大型化及高可靠性运行已成趋 势,但随之而来的散热问题亦日益突出,解决该问题已成为亟待解决的难题。因此,需要设 计一种数据中心冷却系统以解决此问题。
本实用新型专利涉及一种数据中心冷却系统,采用液冷与风冷相结合的方式进行散热,具有 高效、可靠、安全的特点,能够有效解决数据中心在高负荷运行时的散热问题。
感谢您的观看
《冷板液冷系统设计参考》白皮书
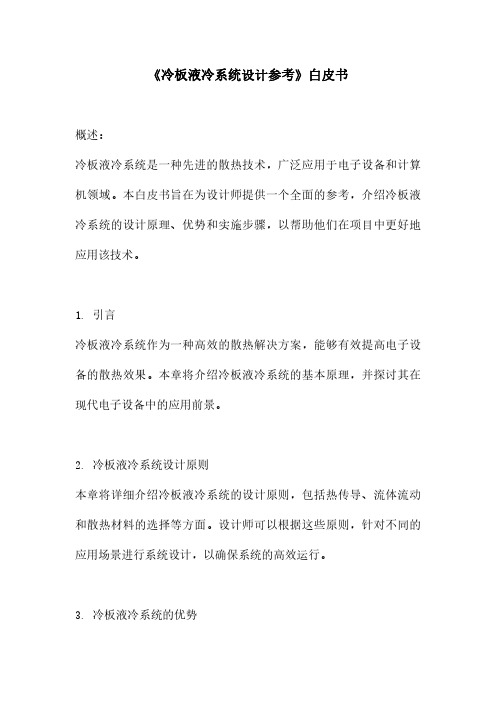
《冷板液冷系统设计参考》白皮书
概述:
冷板液冷系统是一种先进的散热技术,广泛应用于电子设备和计算机领域。
本白皮书旨在为设计师提供一个全面的参考,介绍冷板液冷系统的设计原理、优势和实施步骤,以帮助他们在项目中更好地应用该技术。
1.引言
冷板液冷系统作为一种高效的散热解决方案,能够有效提高电子设备的散热效果。
本章将介绍冷板液冷系统的基本原理,并探讨其在现代电子设备中的应用前景。
2.冷板液冷系统设计原则
本章将详细介绍冷板液冷系统的设计原则,包括热传导、流体流动和散热材料的选择等方面。
设计师可以根据这些原则,针对不同的应用场景进行系统设计,以确保系统的高效运行。
3.冷板液冷系统的优势
本章将阐述冷板液冷系统相对于传统散热方案的优势。
这些优势包括更好的散热性能、节能环保、噪音低等。
设计师可以通过了解这些优势,更好地权衡采用冷板液冷系统的利弊。
4.冷板液冷系统的实施步骤
本章将介绍冷板液冷系统的实施步骤,包括系统设计、组件选型、安装调试和维护等方面。
设计师可以按照这些步骤,有序地进行系统的实施,以确保系统的稳定运行。
5.冷板液冷系统应用案例
本章将介绍一些冷板液冷系统的应用案例,包括服务器散热、电子设备散热等。
这些案例将展示冷板液冷系统在不同领域的成功应用,为设计师提供实际参考。
结论:
本白皮书从冷板液冷系统设计原则、优势和实施步骤等方面全面介绍了该技术。
设计师可以根据这些参考,更好地应用冷板液冷系统,提高电子设备的散热效果。
同时,本白皮书也呼吁行业从业者
遵循文章中提到的内容,确保文章的质量和规范,以促进技术的良性发展。
冷板式液冷电源冷却结构方案

冷板式液冷电源冷却结构方案一、引言随着科技的不断发展,电子设备的性能越来越强大,功率密度也在不断提高。
然而,高功率密度的电子设备在运行过程中会产生大量的热量,如果不能有效地散热,将会对设备的稳定运行和使用寿命产生严重影响。
因此,如何有效地降低电子设备的温度,提高其散热性能,已经成为了当前电子技术发展的一个重要课题。
液冷技术作为一种高效的散热方式,已经在许多领域得到了广泛的应用。
本文将对冷板式液冷电源冷却结构方案进行详细的介绍。
二、冷板式液冷电源冷却结构方案冷板式液冷电源冷却结构方案主要包括以下几个部分:冷板、冷却液、水泵、散热器和温度控制系统。
1. 冷板冷板是液冷电源冷却结构的核心部件,其主要作用是将热量从电源内部传导到冷却液中。
冷板通常采用高导热性能的材料制成,如铜、铝等。
为了提高冷板的散热效果,可以采用微通道、热管等技术对冷板进行优化设计。
2. 冷却液冷却液是液冷系统中的传热介质,其主要作用是将热量从冷板传递到散热器。
常用的冷却液有水、油、氟化碳等。
在选择冷却液时,需要考虑其导热性能、化学稳定性、热膨胀系数等因素。
此外,为了提高冷却液的散热效果,还可以采用添加纳米颗粒、表面活性剂等方法对冷却液进行处理。
3. 水泵水泵是液冷系统中的循环动力设备,其主要作用是驱动冷却液在冷板、散热器之间循环流动。
水泵的选择需要考虑其流量、扬程、效率等因素。
为了提高水泵的运行效率,可以采用变频调速、永磁同步电机等技术对水泵进行优化设计。
4. 散热器散热器是液冷系统中的散热设备,其主要作用是将冷却液中的热量散发到环境中。
散热器的类型有很多,如风冷散热器、水冷散热器等。
在选择散热器时,需要考虑其散热面积、散热效率、噪音等因素。
为了提高散热器的散热效果,可以采用增加散热翅片、改变散热器形状等方法对散热器进行优化设计。
5. 温度控制系统温度控制系统是液冷电源冷却结构的重要组成部分,其主要作用是根据电源的温度变化自动调节冷却系统的运行状态。
液冷集装箱式储能系统设计开发研究
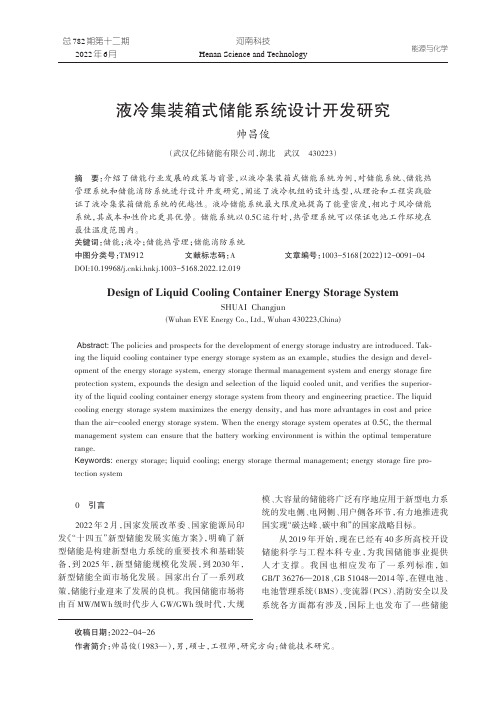
河南科技Henan Science and Technology 能源与化学总782期第十二期2022年6月液冷集装箱式储能系统设计开发研究帅昌俊(武汉亿纬储能有限公司,湖北武汉430223)摘要:介绍了储能行业发展的政策与前景,以液冷集装箱式储能系统为例,对储能系统、储能热管理系统和储能消防系统进行设计开发研究,阐述了液冷机组的设计选型,从理论和工程实践验证了液冷集装箱储能系统的优越性。
液冷储能系统最大限度地提高了能量密度,相比于风冷储能系统,其成本和性价比更具优势。
储能系统以0.5C运行时,热管理系统可以保证电池工作环境在最佳温度范围内。
关键词:储能;液冷;储能热管理;储能消防系统中图分类号:TM912文献标志码:A文章编号:1003-5168(2022)12-0091-04 DOI:10.19968/ki.hnkj.1003-5168.2022.12.019Design of Liquid Cooling Container Energy Storage SystemSHUAI Changjun(Wuhan EVE Energy Co.,Ltd.,Wuhan430223,China)Abstract:The policies and prospects for the development of energy storage industry are introduced.Tak‑ing the liquid cooling container type energy storage system as an example,studies the design and devel‑opment of the energy storage system,energy storage thermal management system and energy storage fire protection system,expounds the design and selection of the liquid cooled unit,and verifies the superior‑ity of the liquid cooling container energy storage system from theory and engineering practice.The liquid cooling energy storage system maximizes the energy density,and has more advantages in cost and price than the air-cooled energy storage system.When the energy storage system operates at0.5C,the thermal management system can ensure that the battery working environment is within the optimal temperature range.Keywords:energy storage;liquid cooling;energy storage thermal management;energy storage fire pro‑tection system0引言2022年2月,国家发展改革委、国家能源局印发《“十四五”新型储能发展实施方案》,明确了新型储能是构建新型电力系统的重要技术和基础装备,到2025年,新型储能规模化发展,到2030年,新型储能全面市场化发展。
微通道液冷冷板技术研究进展
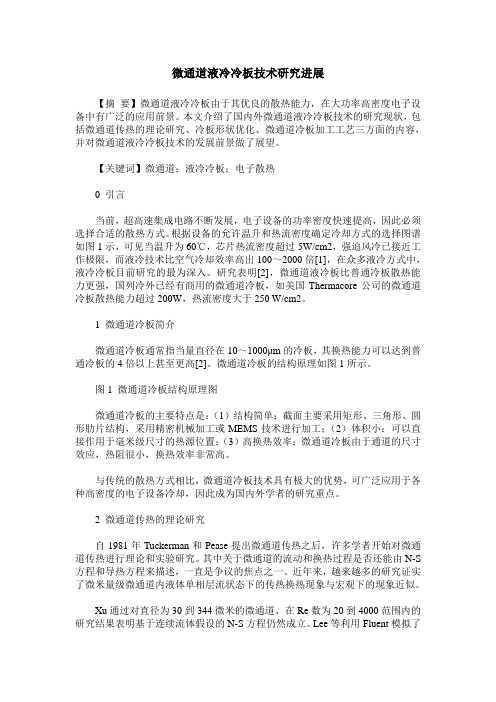
微通道液冷冷板技术研究进展【摘要】微通道液冷冷板由于其优良的散热能力,在大功率高密度电子设备中有广泛的应用前景。
本文介绍了国内外微通道液冷冷板技术的研究现状,包括微通道传热的理论研究、冷板形状优化、微通道冷板加工工艺三方面的内容,并对微通道液冷冷板技术的发展前景做了展望。
【关键词】微通道;液冷冷板;电子散热0 引言当前,超高速集成电路不断发展,电子设备的功率密度快速提高,因此必须选择合适的散热方式。
根据设备的允许温升和热流密度确定冷却方式的选择图谱如图1示,可见当温升为60℃,芯片热流密度超过5W/cm2,强迫风冷已接近工作极限,而液冷技术比空气冷却效率高出100~2000倍[1],在众多液冷方式中,液冷冷板目前研究的最为深入。
研究表明[2],微通道液冷板比普通冷板散热能力更强,国列冷外已经有商用的微通道冷板,如美国Thermacore公司的微通道冷板散热能力超过200W,热流密度大于250 W/cm2。
1 微通道冷板简介微通道冷板通常指当量直径在10~1000μm的冷板,其换热能力可以达到普通冷板的4倍以上甚至更高[2]。
微通道冷板的结构原理如图1所示。
图1 微通道冷板结构原理图微通道冷板的主要特点是:(1)结构简单:截面主要采用矩形、三角形、圆形肋片结构,采用精密机械加工或MEMS技术进行加工;(2)体积小:可以直接作用于毫米级尺寸的热源位置;(3)高换热效率:微通道冷板由于通道的尺寸效应,热阻很小,换热效率非常高。
与传统的散热方式相比,微通道冷板技术具有极大的优势,可广泛应用于各种高密度的电子设备冷却,因此成为国内外学者的研究重点。
2 微通道传热的理论研究自1981年Tuckerman和Pease提出微通道传热之后,许多学者开始对微通道传热进行理论和实验研究。
其中关于微通道的流动和换热过程是否还能由N-S 方程和导热方程来描述,一直是争议的焦点之一。
近年来,越来越多的研究证实了微米量级微通道内液体单相层流状态下的传热换热现象与宏观下的现象近似。
液冷储能电池冷却系统的研究
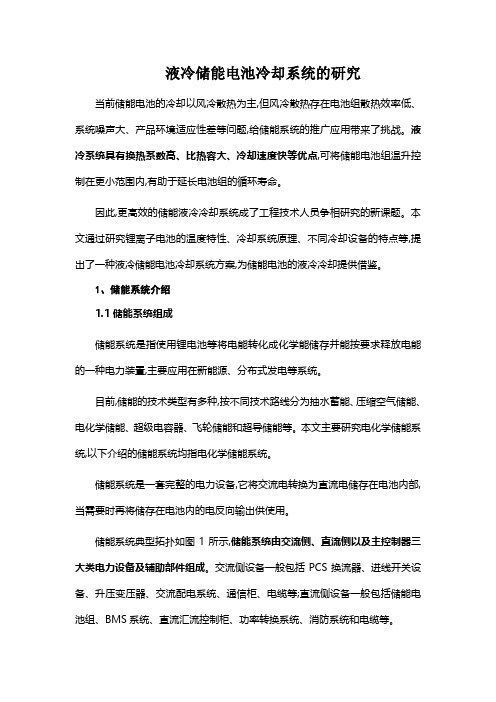
液冷储能电池冷却系统的研究当前储能电池的冷却以风冷散热为主,但风冷散热存在电池组散热效率低、系统噪声大、产品环境适应性差等问题,给储能系统的推广应用带来了挑战。
液冷系统具有换热系数高、比热容大、冷却速度快等优点,可将储能电池组温升控制在更小范围内,有助于延长电池组的循环寿命。
因此,更高效的储能液冷冷却系统成了工程技术人员争相研究的新课题。
本文通过研究锂离子电池的温度特性、冷却系统原理、不同冷却设备的特点等,提出了一种液冷储能电池冷却系统方案,为储能电池的液冷冷却提供借鉴。
1、储能系统介绍1.1储能系统组成储能系统是指使用锂电池等将电能转化成化学能储存并能按要求释放电能的一种电力装置,主要应用在新能源、分布式发电等系统。
目前,储能的技术类型有多种,按不同技术路线分为抽水蓄能、压缩空气储能、电化学储能、超级电容器、飞轮储能和超导储能等。
本文主要研究电化学储能系统,以下介绍的储能系统均指电化学储能系统。
储能系统是一套完整的电力设备,它将交流电转换为直流电储存在电池内部,当需要时再将储存在电池内的电反向输出供使用。
储能系统典型拓扑如图1所示,储能系统由交流侧、直流侧以及主控制器三大类电力设备及辅助部件组成。
交流侧设备一般包括PCS换流器、进线开关设备、升压变压器、交流配电系统、通信柜、电缆等;直流侧设备一般包括储能电池组、BMS系统、直流汇流控制柜、功率转换系统、消防系统和电缆等。
1.2储能电池组用于储能系统的电池主要有锂离子电池、钠硫电池、铅酸电池、液流电池和钠离子电池。
其中,锂离子电池具有能量密度高、循环次数多、转换效率高、响应速度快等优点,是目前综合性能最优的一种储能电池、。
当前应用的储能电池大多以电池舱供货,厂内制造集成,方便现场快速安装,同时缩短项目周期和土建费用。
一般电池舱由多个电池簇组成,电池簇又由多个电池模块组成,而电池模块又由多个电池单体组成。
一般根据电芯单体容量、项目装机容量,综合考虑电池电芯、电池模块、电池簇的数量,最终组成电池舱。
高效散热微通道液冷冷板焊接技术及成形工艺研究

高效散热微通道液冷冷板焊接技术及成形工艺研究3赵仁祥(南京电子技术研究所, 江苏南京210013)摘 要:通过分析微通道冷板的结构特点及技术要求,对微通道冷板的焊接方法、焊接工艺进行了分析研究。
采用气保护炉钎焊方法,通过巧妙地采用过渡材料与接头设计,既突破了6063铝合金气保护炉钎焊的钎焊性较差的技术难题,满足了钎焊缝密封性要求,又可有效地避免钎料流入微通道。
通过焊接工装及接头设计,在合理的工艺及气氛条件下,实现了6063铝合金微通道冷板的整体焊接成形,解决了微通道冷板的焊接技术难题。
关键词:气保护钎焊;6063铝合金;微通道冷板中图分类号:TG44 文献标识码:A 文章编号:1008-5300(2008)04-0033-04Study on B razing Technique and For mati on Technol ogy of Cold Plates with Efficiently Radiating Liquid CoolingM icr ochannels Syste mZHAO R e n2xi a ng(N anjing R esea rch Institute of E lectronics Technology, N anjing210013,Ch ina) Abstract:It were studied the welding method and welding technol ogy of cold p lates with m icr ochannels in this paper,according t o its′structure and technique require ment.Based on gas shield brazing method,j oint design and transiti onal material were app lied skillfully in p ractice.The technol ogy not only s olved the traditi onal p r oble m of brazing6063alu m iniu m all oy in p r otective gas,but als o avoided the filler metal fr om infl ooding in2 t o m icr ochannel.After designing welding cla mp ing fixture and the j oint f or m,cold p late was brazed in p r oper technol ogy and p r otective at m os phere.It s olved the p r oble m of brazing the whole cold p late of6063alum inium all oy.Key words:gas shield brazing;6063alu m inium all oy;cold p late with m icr ochannels0 引 言冷板是一种单流体(气体、水或其它冷却器)的热交换器。
冷板液冷1
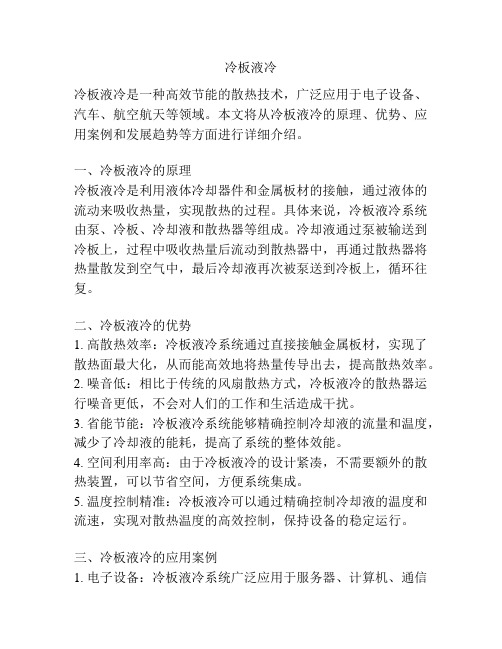
冷板液冷冷板液冷是一种高效节能的散热技术,广泛应用于电子设备、汽车、航空航天等领域。
本文将从冷板液冷的原理、优势、应用案例和发展趋势等方面进行详细介绍。
一、冷板液冷的原理冷板液冷是利用液体冷却器件和金属板材的接触,通过液体的流动来吸收热量,实现散热的过程。
具体来说,冷板液冷系统由泵、冷板、冷却液和散热器等组成。
冷却液通过泵被输送到冷板上,过程中吸收热量后流动到散热器中,再通过散热器将热量散发到空气中,最后冷却液再次被泵送到冷板上,循环往复。
二、冷板液冷的优势1. 高散热效率:冷板液冷系统通过直接接触金属板材,实现了散热面最大化,从而能高效地将热量传导出去,提高散热效率。
2. 噪音低:相比于传统的风扇散热方式,冷板液冷的散热器运行噪音更低,不会对人们的工作和生活造成干扰。
3. 省能节能:冷板液冷系统能够精确控制冷却液的流量和温度,减少了冷却液的能耗,提高了系统的整体效能。
4. 空间利用率高:由于冷板液冷的设计紧凑,不需要额外的散热装置,可以节省空间,方便系统集成。
5. 温度控制精准:冷板液冷可以通过精确控制冷却液的温度和流速,实现对散热温度的高效控制,保持设备的稳定运行。
三、冷板液冷的应用案例1. 电子设备:冷板液冷系统广泛应用于服务器、计算机、通信设备等电子设备的散热中。
由于这些设备的功耗较大,采用冷板液冷可以提供更好的散热效果,保证设备的稳定运行。
2. 汽车:汽车引擎、变速器等部件在工作时会产生大量的热量,如果不能及时散热会导致设备过热。
利用冷板液冷技术,可以有效地将热量从引擎和变速器传导出去,保持汽车的正常运行。
3. 航空航天:航空航天领域的设备要面临更加苛刻的环境条件,使用冷板液冷技术可以保证设备在极端温度下的正常运行。
同时,冷板液冷的高散热效率也有助于减轻设备的重量,提高飞行性能。
四、冷板液冷的发展趋势1. 融合其他技术:冷板液冷正在与其他相关技术如人工智能、材料科学等进行融合,以提高冷却系统的自动化和智能化水平,满足复杂多样的散热需求。
冷板式液冷风液比
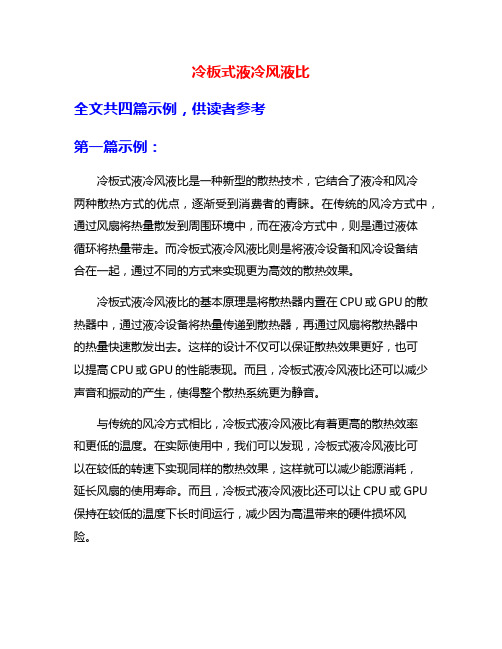
冷板式液冷风液比全文共四篇示例,供读者参考第一篇示例:冷板式液冷风液比是一种新型的散热技术,它结合了液冷和风冷两种散热方式的优点,逐渐受到消费者的青睐。
在传统的风冷方式中,通过风扇将热量散发到周围环境中,而在液冷方式中,则是通过液体循环将热量带走。
而冷板式液冷风液比则是将液冷设备和风冷设备结合在一起,通过不同的方式来实现更为高效的散热效果。
冷板式液冷风液比的基本原理是将散热器内置在CPU或GPU的散热器中,通过液冷设备将热量传递到散热器,再通过风扇将散热器中的热量快速散发出去。
这样的设计不仅可以保证散热效果更好,也可以提高CPU或GPU的性能表现。
而且,冷板式液冷风液比还可以减少声音和振动的产生,使得整个散热系统更为静音。
与传统的风冷方式相比,冷板式液冷风液比有着更高的散热效率和更低的温度。
在实际使用中,我们可以发现,冷板式液冷风液比可以在较低的转速下实现同样的散热效果,这样就可以减少能源消耗,延长风扇的使用寿命。
而且,冷板式液冷风液比还可以让CPU或GPU 保持在较低的温度下长时间运行,减少因为高温带来的硬件损坏风险。
冷板式液冷风液比还有着更好的外观设计和更为便捷的安装方式。
一般来说,冷板式液冷风液比的散热器设计更为精致,可以提高整个电脑机箱的美观度。
而且,冷板式液冷风液比的安装方式也相对简单,只需要将液冷设备和风冷设备连接好,然后安装在CPU或GPU上即可。
这样的设计可以降低用户的安装成本,也可以方便用户进行一些DIY改装。
在使用冷板式液冷风液比时,用户需要注意一些维护保养的方法。
定期清洁散热器和风扇,避免灰尘和杂物堵塞散热器,影响散热效果。
定期检查液冷设备的冷却液是否还有足够的量,需要及时更换冷却液,保持液冷设备的工作正常。
还需要注意不要在高温环境中使用电脑,避免因为高温导致的故障。
冷板式液冷风液比是一种高效、节能、静音的散热方式,可以为用户带来更好的使用体验。
它的独特设计结合了液冷和风冷两种方式的优点,使得散热效果得到了进一步的提升。
新能源汽车PCU液冷冷板的结构及性能分析

新能源汽车PCU液冷冷板的结构及性能分析随着环保意识的提高和对能源消耗的关注,新能源汽车逐渐成为人们关注的焦点。
为了提高新能源汽车的性能和安全性,PCU液冷冷板作为一种重要的散热装置被广泛应用于新能源汽车中。
PCU液冷冷板是一种采用液冷技术散热的装置,由冷板、水管和冷却液组成。
其结构简单,具有散热效果好、重量轻、体积小等优点。
冷板作为核心部件,通常采用高导热材料制成,如铜或铝。
冷板表面设计有多个散热片,以增加表面积,提高散热效果。
水管则用于将冷却液引入冷板,通过冷却液的循环来吸收PCU产生的热量,然后将热量带走,保持PCU的工作温度在合理范围内。
PCU液冷冷板的性能主要体现在散热效果和能耗方面。
散热效果直接影响PCU的工作温度和性能稳定性。
冷板的散热效果受到冷板材料、散热片数量和冷却液流速等因素的影响。
一般来说,导热性能好的材料和较多的散热片能够提高散热效果。
冷却液的流速也是影响散热效果的重要因素,流速过大会导致散热不均匀,过小则可能无法及时带走热量。
因此,在设计PCU液冷冷板时需要综合考虑这些因素,以提高散热效果。
另外,能耗也是PCU液冷冷板的一个重要性能指标。
能耗主要包括冷却液的能耗和冷板材料的能耗。
为了降低能耗,可以采用低能耗的冷却液和导热性能好的材料制成冷板。
同时,优化冷却液的流速和冷板的设计也可以降低能耗。
总之,PCU液冷冷板作为新能源汽车的重要散热装置,其结构和性能对于提高新能源汽车的性能和安全性起着至关重要的作用。
通过合理设计冷板结构和优化冷却液的流速,可以提高散热效果和降低能耗,进而提高新能源汽车的整体性能。
随着技术的不断进步和研究的深入,相信PCU液冷冷板的性能会不断提升,为新能源汽车的发展做出更大的贡献。
一种液冷机箱[实用新型专利]
![一种液冷机箱[实用新型专利]](https://img.taocdn.com/s3/m/faa1260a4a73f242336c1eb91a37f111f1850daf.png)
专利名称:一种液冷机箱
专利类型:实用新型专利
发明人:蔡艳召,李世龙,郑善伟,范永良,钱子颢申请号:CN202121967899.6
申请日:20210820
公开号:CN216134766U
公开日:
20220325
专利内容由知识产权出版社提供
摘要:本实用新型关于一种液冷机箱,包括机箱外壳和固定装配在该机箱外壳内的至少一个通液隔板,上述通液隔板将机箱壳体内的空间分隔为若干部分,每个通液隔板内均设有隔板流道,每个隔板流道的隔板进液口均与机箱外壳上的进液通道连接导通,隔板回液口均与机箱外壳上的回液流道连接导通,所述进液流道和回液流道上分别设有与外部管道连接的进液口和出液口。
本实用新型液冷机箱的侧板具有进液口和出液,用于流通和回收冷却液,在侧板内布置进出液体流道,通过进液流道将流体分配至机箱内部通液隔板内,从而取消了机箱内部的流体分配器,为机箱内部器件节省了一定的空间,有效提高机箱内的空间利用率。
申请人:中航光电科技股份有限公司
地址:471003 河南省洛阳市高新区周山路10号
国籍:CN
代理机构:洛阳华和知识产权代理事务所(普通合伙)
代理人:刘亚莉
更多信息请下载全文后查看。
冷板液冷文档

冷板液冷简介冷板液冷(Cold Plate Liquid Cooling)是一种应用在电子设备散热技术中的液体冷却方法。
与传统的风扇散热相比,冷板液冷具有更高的散热效果和更低的噪音。
本文将介绍冷板液冷的原理、优势以及在不同领域的应用。
原理冷板液冷的原理是利用液体通过冷板,将热量从电子设备中带走。
液体一般为导热性能较好的介质,如水或者工业冷却剂。
冷板通常位于电子设备的导热部件上,通过与其直接接触并吸收热量来实现散热效果。
液体通常在冷却系统中循环流动,通过稳定的循环流动,冷板能够将热量逐步传递给液体并带走。
冷却系统一般包括冷板、液体循环泵、散热器以及一系列的管道和接头。
优势与传统的风扇散热相比,冷板液冷具有以下几个明显的优势:更高的散热效果冷板液冷能够更有效地带走电子设备产生的热量。
相比于风扇散热,液体的热传导能力更强,因此可以更快地带走设备产生的热量,保持设备的温度较低。
这对于一些高性能的电子设备来说尤为重要,能够有效提高设备的稳定性和性能。
较低的噪音由于冷板液冷不需要使用风扇,因此相比于传统的风扇散热方法,它产生的噪音更低。
这对于一些需要安静工作环境的场景来说非常重要,例如音频制作工作室、影音设备、服务器房等。
空间利用率高由于冷板液冷不需要使用大型的传统散热器和风扇,因此可以节省大量的空间。
这对于一些空间有限的场景来说特别有用,例如嵌入式设备、移动设备等。
可定制性强冷板液冷的结构相对灵活,可以根据实际需求进行设计和定制。
可以根据设备的形状、尺寸以及散热需求来制定冷板的形状和材料,从而最大程度地提高散热效果。
应用领域冷板液冷技术在各个领域都有广泛的应用,以下是几个常见的应用领域:电子设备冷板液冷在电子设备中应用广泛,特别是一些高性能的电子设备,如服务器、超级计算机、图形处理器等。
这些设备通常需要更高效的散热方法来保证其性能和稳定性。
光电设备光电设备往往需要在较高温度下工作,如激光器、光纤通信设备等。
冷板式液冷技术 储能标准

冷板式液冷技术储能标准1. 引言1.1 背景介绍随着全球能源需求的不断增加和环境污染问题的日益加剧,人们对可再生能源的需求越来越迫切。
储能技术作为可再生能源的重要支撑,受到了广泛关注。
在储能技术中,冷板式液冷技术是一种新型且高效的方式,可以有效提高能源利用率和系统稳定性。
传统的储能技术往往存在能源损耗大、效率低和环境污染等问题,而冷板式液冷技术则能够有效解决这些问题。
它通过将储能设备与液冷系统相结合,实现对储能设备的有效冷却和散热,使设备运行更加稳定可靠,延长设备的使用寿命,提高系统的运行效率。
了解冷板式液冷技术的原理和储能标准的制定对于推动可再生能源的发展具有重要意义。
本文将从冷板式液冷技术的原理、储能标准的制定、冷板式液冷技术在储能领域的应用等方面进行探讨,旨在为推动储能技术的发展提供参考和借鉴。
1.2 研究意义液冷技术是一种高效的散热方式,可以有效降低设备运行温度,提高设备的性能和稳定性。
而冷板式液冷技术在储能领域中的应用具有重要意义。
通过液冷技术可以提高储能装置的能量密度和功率密度,使储能系统在有限的空间内实现更大的储能容量和更高的放电速率。
液冷技术可以有效降低储能装置的工作温度,提高系统的循环效率和寿命,减少能量损耗和故障率,降低运行成本。
液冷技术还可以提高储能系统的安全性,减少火灾和爆炸的风险,保障设备和人员的安全。
深入研究冷板式液冷技术在储能领域的应用,探讨储能标准的制定和实施,对提高储能系统的能源利用效率,促进绿色能源发展,推动能源转型具有重要意义。
通过本研究,可以为储能领域的技术创新和产业发展提供理论支撑和技术指导,推动冷板式液冷技术和储能标准的进一步完善和应用推广。
1.3 研究目的研究目的是为了深入探讨冷板式液冷技术在储能领域的应用potential。
通过制定储能标准,规范和统一行业发展方向,促进冷板式液冷技术的应用和推广。
通过对冷板式液冷技术与储能标准的发展趋势进行分析,为未来的技术研究和产业发展提供参考,推动相关技术的创新和进步。
冷板冷却技术
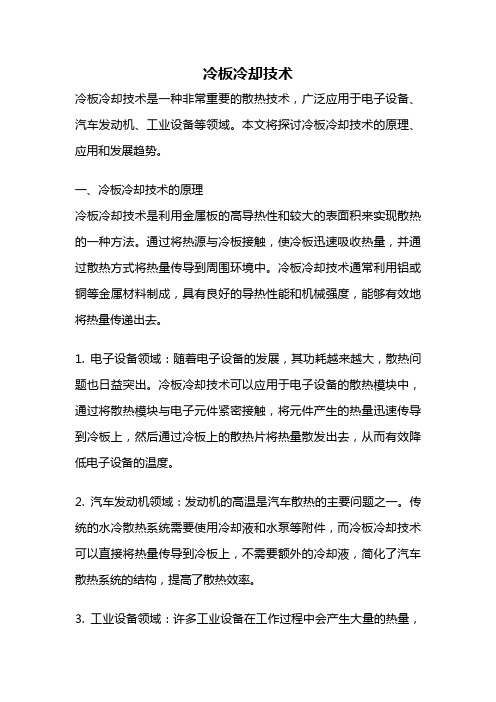
冷板冷却技术冷板冷却技术是一种非常重要的散热技术,广泛应用于电子设备、汽车发动机、工业设备等领域。
本文将探讨冷板冷却技术的原理、应用和发展趋势。
一、冷板冷却技术的原理冷板冷却技术是利用金属板的高导热性和较大的表面积来实现散热的一种方法。
通过将热源与冷板接触,使冷板迅速吸收热量,并通过散热方式将热量传导到周围环境中。
冷板冷却技术通常利用铝或铜等金属材料制成,具有良好的导热性能和机械强度,能够有效地将热量传递出去。
1. 电子设备领域:随着电子设备的发展,其功耗越来越大,散热问题也日益突出。
冷板冷却技术可以应用于电子设备的散热模块中,通过将散热模块与电子元件紧密接触,将元件产生的热量迅速传导到冷板上,然后通过冷板上的散热片将热量散发出去,从而有效降低电子设备的温度。
2. 汽车发动机领域:发动机的高温是汽车散热的主要问题之一。
传统的水冷散热系统需要使用冷却液和水泵等附件,而冷板冷却技术可以直接将热量传导到冷板上,不需要额外的冷却液,简化了汽车散热系统的结构,提高了散热效率。
3. 工业设备领域:许多工业设备在工作过程中会产生大量的热量,如果不能及时散热,会导致设备的性能下降甚至损坏。
冷板冷却技术可以应用于工业设备的散热模块中,通过将热源与冷板接触,将热量迅速传导到冷板上,再通过散热片将热量散发出去,确保设备的正常运行。
三、冷板冷却技术的发展趋势1. 材料的发展:目前常用的冷板材料主要是铝和铜,但随着新材料的研发,如石墨烯、碳纳米管等,将会有更好的导热性能和机械强度,从而提高冷板冷却技术的散热效率。
2. 结构的优化:冷板冷却技术的结构也在不断优化,例如增加冷板的表面积、优化散热片的形状等,以提高散热效果。
3. 智能化的应用:随着物联网技术的发展,冷板冷却技术也可以与传感器、控制系统等智能设备结合,实现散热系统的实时监测和调控,提高散热效率的同时降低能耗。
四、总结冷板冷却技术是一种重要的散热技术,具有广泛的应用前景。
对液冷技术及其发展的探讨
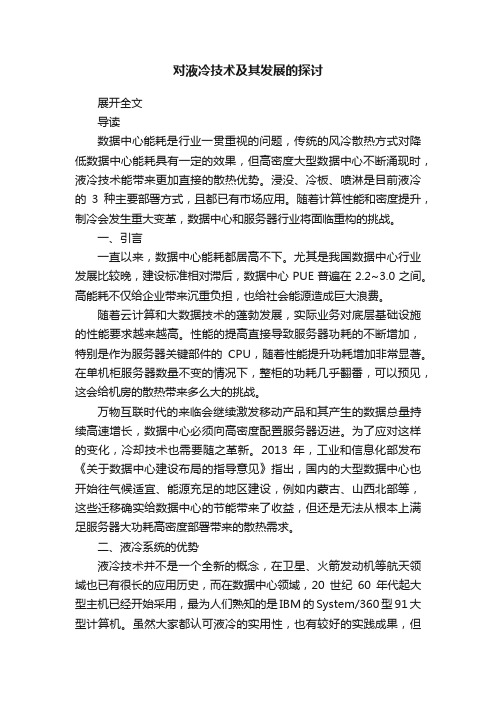
对液冷技术及其发展的探讨展开全文导读数据中心能耗是行业一贯重视的问题,传统的风冷散热方式对降低数据中心能耗具有一定的效果,但高密度大型数据中心不断涌现时,液冷技术能带来更加直接的散热优势。
浸没、冷板、喷淋是目前液冷的3种主要部署方式,且都已有市场应用。
随着计算性能和密度提升,制冷会发生重大变革,数据中心和服务器行业将面临重构的挑战。
一、引言一直以来,数据中心能耗都居高不下。
尤其是我国数据中心行业发展比较晚,建设标准相对滞后,数据中心PUE普遍在2.2~3.0之间。
高能耗不仅给企业带来沉重负担,也给社会能源造成巨大浪费。
随着云计算和大数据技术的蓬勃发展,实际业务对底层基础设施的性能要求越来越高。
性能的提高直接导致服务器功耗的不断增加,特别是作为服务器关键部件的CPU,随着性能提升功耗增加非常显著。
在单机柜服务器数量不变的情况下,整柜的功耗几乎翻番,可以预见,这会给机房的散热带来多么大的挑战。
万物互联时代的来临会继续激发移动产品和其产生的数据总量持续高速增长,数据中心必须向高密度配置服务器迈进。
为了应对这样的变化,冷却技术也需要随之革新。
2013年,工业和信息化部发布《关于数据中心建设布局的指导意见》指出,国内的大型数据中心也开始往气候适宜、能源充足的地区建设,例如内蒙古、山西北部等,这些迁移确实给数据中心的节能带来了收益,但还是无法从根本上满足服务器大功耗高密度部署带来的散热需求。
二、液冷系统的优势液冷技术并不是一个全新的概念,在卫星、火箭发动机等航天领域也已有很长的应用历史,而在数据中心领域,20世纪60年代起大型主机已经开始采用,最为人们熟知的是IBM的System/360型91大型计算机。
虽然大家都认可液冷的实用性,也有较好的实践成果,但由于在较低热度负荷时风冷的成本很低,且安装部署更为简单,所以IT产业在随后的60多年里大规模使用的是风冷散热系统。
随着时间的推移和技术的进步,计算机芯片的密度越来越高,所要处理的计算工作也越来越复杂,热度负荷节节攀升,液冷技术逐渐被产业界拉出来“救火”。
- 1、下载文档前请自行甄别文档内容的完整性,平台不提供额外的编辑、内容补充、找答案等附加服务。
- 2、"仅部分预览"的文档,不可在线预览部分如存在完整性等问题,可反馈申请退款(可完整预览的文档不适用该条件!)。
- 3、如文档侵犯您的权益,请联系客服反馈,我们会尽快为您处理(人工客服工作时间:9:00-18:30)。
一种新型的液冷机箱及冷板散热系统的研究摘要:针对目前军用计算机数据处理系统集成化、高功率的发展趋势,液冷散热在数据处理系统热设计中的需求越来越必要。
本文结合实际研究的项目,详细介绍了冷板、液冷机箱、液冷散热系统架构的设计模式、流道的设计及仿真分析、试验及测试验证等项目设计中的关键技术,形成一套具有高效散热的一体化解决方案。
【关键词】液冷散热液冷机箱冷板流道1 引言电子技术微型化、高集成度、大功率电子器件应用的发展趋势,使得电子设备要求体积越来越小,元器件数量增加,这就使得电子设备功率密度和热流密度大幅度提高,热量集中,局部温度过高,如果热量不能及时散出,就会导致电子设备性能下降甚至失效。
一般而言,温度每上升10℃,可靠度可能就会降低为原来的一半,而温度从75℃升高至125℃,可靠度则变为原来的20%。
有效的热设计模式是对电子设备的发热元器件及散热系统采用合适的冷却技术和结构设计,对它们的温升进行控制,从而保证电子设备或系统正常可靠地工作。
根据应用环境的不同,传统的风冷散热会带来多余物及增大系统空间,而导冷式散热面对功率较大系统时则出现散热了瓶颈,而液冷散热技术的出现,由于液体介质比空气及常规散热铝材有更好的换热系数,使得液冷系统散热量级甚至为传统风冷式、导冷式散热的100倍以上。
2 散热系统的建立及组成一般液冷系统的建立都是强制液冷、金属传导散热的结合,而一个完整的液冷系统而言,其主要由液冷机箱、液冷冷板及液冷提供系统组成,液冷冷板直接吸收发热模块的功耗,通过液冷机箱循环到液冷系统,将热量传递给液冷提供系统中的液泵,再经过液泵送至换热器,液冷换热器与外部环境热交换,对冷却液制冷并返回液冷机箱完成一个循环,而单考虑散热系统部分,液冷机箱及液冷冷板的设计成为了系统的关键。
图1所示为笔者研究的液冷散热系统,主要由冷板模块1~5、液冷机箱、流体连接器、信号传输连接器等组成。
其中冷板模块用于对印制板电路单元机械支撑和对流换热的作用;液冷机箱是整个散热系统的架构基础,也是整个散热系统中流道的枢纽;流体连接器是与液冷提供系统的接口,起着进液与出液的作用,要求在一定的管道流压下,无漏液现象。
3 冷板模块的设计图2所示为所设计的冷板模块组成示意图,包括冷板、楔形条、起拔器、后盖板、印制电路板、流体连接器。
其中楔形条由三节式滑块、螺杆及螺套组成,用于冷板模块与机箱进行配合时由于滑块与机箱插槽产生摩擦防止冷板模块产生晃动,同时也用于将印制板散发的热量通过滑块传递给机箱;起拔器用于冷板模块与机箱插槽配合的插拔;后盖板通过与冷板配合,将印制板夹住,通过螺钉固定,用于对印制电路板加固,也起着部分传导辐射散热的作用,也可作为屏蔽作用的屏蔽板;流体连接器用于与图3中的内流体连接器进行配合,从而将外部流体引入冷板流道循环,将印制电路板发热元件所产生的热量带走。
散热系统中发热源为冷板模块中的印制板单元,冷板作为印制板上各热耗单元的基础,即作为电子器件的安装基座,又作为一次换热载体,是液冷模块的核心,要求其结构简单紧凑,表面传热系统高,温度梯度小,均温性好,能有效降低热源温度。
在冷板设计中考虑了以下几个因素:(1)冷板与发热器件的接触面要平整光滑;(2)冷板与发热器件要有一定的结合压紧力,尽量减少接触热阻;(3)流道的设计应尽量多经过冷板吸热面,即与发热元件布局进行对应;(4)流道应尽量采用短的长度尺度,流道全程流动均匀,有良好的导向性,以减少压损,流道自身应具有尽可能大的换热面积,以提高对流换热系数;(5)流道设计应考虑工艺性,便于焊接后的后续加工,加工流道畅通均匀,同时具有良好的气密性。
对于上述(1)、(2)条主要采取了在发热元件与冷板接触面采取导热硅脂为导热界面材料,考虑一定的装配压力从而降低其接触热阻,提高传热效率。
对于上述(3)、(4)条,见图3所示。
由于冷板直接面对的是印制板上的发热器件,发热点较多且局部发热量较大,在流道设计时整体依旧采用蛇形流道,流道腔体内增加翅片,形成微通道冷板。
对于流道弯道处,翅片进行了导流设计,对于直道处翅片成队列式排列,相邻队列形成交错式布局,流体进入流道时增强其紊流状态,增加紊流度的同时增加了对流换热系数,同时冷板流体连接器进出口与蛇形流道接口处采用梯度式的流道设计,对于进液口增加了流体紊流度,对于出液口加速流体流动,提高散热效率。
对于上述(5)条,微通道翅片宽度同换热性能密切相关,随着通道宽度尺寸的缩小,换热系数随之增大,因此尽量保证翅片强度情况下尽量缩小其宽度尺寸,翅片宽度设计为1mm;同时通道占空比对换热性能也有较大的影响,在冷板体积不变的情况下,微通道冷板中槽道的高宽比越大,则换热性能越好,翅片高度设计为5.5mm,通道间距为1.5mm 通道占空比为0.67,高宽比为5.5,以现有可实现工艺结构形成最优的换热性能。
4 液冷机箱的设计图4所示整个液冷机箱主要由盖板、左右侧板、前壁板、后壁板、底座支架、后IO面板、内流体连接器及外流体连接器组成。
其中盖板、左右侧板均采用导热条的设计模式,将机箱内部环境部分热量进行传导式散热;前壁板及后壁板为机箱应用时与子板进行配合的机械固定板,同时也将冷板模块传导到机箱的热量进行对流换热的主要部件,设计时均采用了蛇形流道的设计模式;机箱的底座支架为整个液冷机箱的关键,起着架构机箱零部件的作用,同时也是将外流体连接器、前后壁板流道、内流体连接器形成一个循环流道的中转站及分支机构;后IO面板用于固定信号传输连接器。
对机箱前后壁板的流道设计,由于流道的结构和流道的弯曲部分对其散热和流道的流阻、压降有着直接的影响。
流道的直道部分越长,流道的流阻就越小,流道的压降就越小;流道的弯道越多,散热性能越好,但流阻越大,压降也就越大;流道的截面积越大,散热性能越好,流阻越小,压降越小。
在实际设计时采用了12个弯道,流道方向的改变增加了流体流动的扰动,增大了冷板表面的传热系数,在一定程度上改善了散热效果,同时保证了直道部分长度的较大比例,减小流道阻力,降低流道压降,同时也降低了工艺难度。
同时对于液冷机箱的设计还考虑了如下几点要素:(1)对于流体连接器,不仅要保证在连接状态下承受一定压力并严格密封,而且在对接、分离时也能快速自封,避免制冷液对电路板的污染;(2)机箱插槽进行了导向设计,保证模块和底板之间、模块液冷接头和机箱液冷接头之间插拔的垂直度和可靠度;(3)液冷机箱的设计考虑了配合公差,连接器插头及插座的对接、助拔器的有效固定、流体连接器有效对接及背板固定配合等;(4)液冷机箱前后壁板直流道腔正好正对到导槽侧壁,方便冷板模块插入后传导到前后壁板导槽侧壁后进行对流换热。
5 流道分析图5所示为冷板与液冷机箱进行组装时示意图(隐藏了前壁板、右侧板及盖板),通过冷板模块的流体连接器与液冷机箱的内流体连接器进行配合,即可将整个散热系统的流道进行贯通,同时冷板模块上的信号传输连接器与液冷机箱内背板上的信号传输连接器进行配合,保证信号传输。
如图6所示液冷机箱底座支架示意图,整个散热系统的流道分为两个分支,具体如下:(1)液冷机箱流道:外流体连接器(进)→进液口→1→前壁板蛇形流道→3→4→5→9→后壁板蛇形流道→10→出液口→外流体连接器(出);(2)冷板与机箱配合后的流道:外流体连接器(进)→进液口→1→前壁板蛇形流道→3→7→2→内流体连接器(进)→冷板流体连接器(进)→冷板蛇形微通道→冷板流体连接器(出)→内流体连接器(出)→6→8→出液口→外流体连接器(出)。
其中在3处出现两路主流分支,一路分支通过4腔体供液给后壁板流道,另一路分支通过7腔体供液给5块冷板。
流过5块冷板的流体于8腔体汇合,流过后壁板的流体通过10开孔与8腔体内5块冷板的流体进行汇合,最后通过出液口及外流体连接器(出)流出,整个散热系统的流道分配示意图见图7所示。
6 热仿真验证图8所示为散热系统的仿真流程图,在仿真时首先对单块冷板的散热能力进行了仿真,然后再对整个液冷系统进行仿真。
仿真中设定流体为常物性,且为定常流动;忽略辐射和空气自然对流散热。
边界条件设置如下:(1)流动液体:水。
(2)液冷槽设计:S型流道带翅片。
(3)单块冷板热源总功率:200W。
(4)进液温度:20℃。
(5)环境温度:25℃。
(6)是否考虑重力影响:Y。
(7)进液口速度:5m/s。
由图9可知得到最高温度32.1℃,完全满足芯片工作温度的要求,而图10液冷系统在仿真时最高温度稍有上升,达到了45.1℃。
后在多次仿真后总结出在相同条件下,由于整个液冷系统结构较为复杂,考虑了机箱与冷板的流道结合,系统会有相应的压力损失,从而影响其换热系数,后经过多次的参数及结构微调,得到本系统的最佳流速为6m/s,通过仿真最高温度达到37.6℃,与冷板仿真效果相当。
通过对液冷系统的仿真分析,在对流道的结构调整过程中发现如下特点:(1)流道道宽度同换热性能息息相关,通道宽度越小,换热系数越大;(2)微通道冷板中的通道占空比对换热性能影响较大;(3)若不计冷板体积的影响,微通道冷板中槽道的高宽比越大,换热性能越好;(4)在不显著增加加工难度的前提下,增大流道数目可有效提高冷板换热系数和效率。
在冷板及液冷机箱流道一定的情况下,换热性能还需要综合考虑流量、流体温度、流道宽度、环境温度等因素的影响。
7 测试及试验验证在对液冷系统进行测试及试验前,需要对冷板及液冷机箱进行气密性检查,通过2.0MPa的耐压测试,证明了其设计的密封性和耐压实用性。
图11所示为测试验证系统。
液冷散热测试系统主要包括泵、换热器、散热器、储液罐和管道。
主要工作过程为:冷却液经过增压泵升压后,经过液体管路,按照一定的压力和温度进入液冷机箱及液冷冷板,与电子设备进行热交换,带走电路板热量,冷却液从冷板出来后温度升高,然后进入换热器,与冷却空气进行换热,将热量传给冷却空气,换热器出来后的冷却液再进入储液罐,然后再经过泵进入下一个循环。
而完整的测试系统不光是要考虑如何将冷却液循环起来,还得考虑温度环境的变化、冷却液的温度、散热器的工作模式、冷板及机箱的流道压力、循环冷却液的流量等参数收集问题。
因此在测试系统中增加了传感器的采集及信息收集功能,从而能够有效的对试验过程中的测试进行综合评价。
试验部分,通过了高低温工作、高低温贮存、随机振动、湿热、温度冲击、机械冲击等试验,得到所研究的液冷机箱及冷板散热系统的性能参数为:液冷系统流量≤1.5L/min,总耗散功率超过1000W,工作环境温度为-45℃~+85℃,耐压值≤2.5MPa。
通过上述的测试及试验分析,得出了以下的规律总结:(1)环境温度对液冷系统影响较小,在供液温度及流量一定的情况下,外界环境的变化对内部温度结构体温度变化影响不大,但随着印制板模块整体功率增大时模块对外辐射换热增强,温差会有所增高;(2)冷却液入口温度对印制板模块器件温度有着直接影响,器件温度与冷却液温度变化基本一致;(3)液冷系统对于流量十分敏感,对流量变化响应很快;(4)在环境温度变化而流体温度保持不变时,只需相应增加流量;(5)在流体温度保持不变,由于液冷系统中环境温度变大会使得流体带出的热量增大,导致高温时的热阻较低温时高;(6)在外界环境较为恶劣时,液冷系统可将温度控制在比较低的范围,且响应速度比较快,充分体现了液冷的优势。