熔融石英在硅溶胶型壳中的应用实践
熔融石英在硅溶胶型壳中的应用(1)
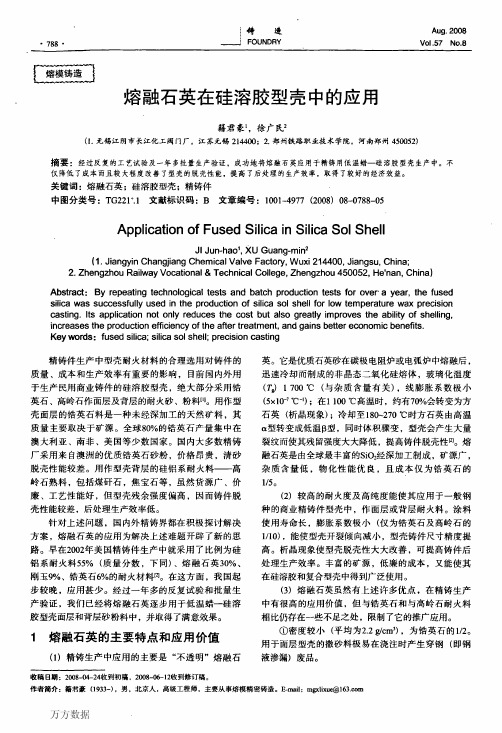
铸造籍君豪等:熔融石英在硅溶胶型壳中的应用·789·②熔融石英粉一硅溶胶涂料对蜡模表面的润湿性很差。
其涂挂性、覆盖性和流平性远不如锆英粉一硅溶胶涂料,也不及刚玉粉及精制石英一硅溶胶涂料,这些直接影响到铸件表面质量。
③相对于高岭石熟料其成本高3 ̄4倍。
阻碍了它在型壳背层中的推广应用(尤其对于附加值较低的商业铸件)。
如何扬长避短,在型壳中合理利用熔融石英解决硅溶胶型壳的两大难题是精铸工作者努力的方向。
2熔融石英在面层型壳中的应用美国2002年精铸型壳耐火料中熔融石英已占30%,铝硅系耐火料占55%回。
据统计背层耐火材料约占硅溶胶型壳的80%,面层耐火料占20%,故美国已使用的熔融石英30%中有25%用于背层,仅5%用于面层。
主要是在锆英粉涂料中加入5%~10%的熔融石英粉来改善深孔或复杂件脱壳性。
在国外典型面层涂料配方中均有此工艺。
生产实践也证实,在面层型壳中(砂或粉料)应用熔融石英比在背层型壳中困难得多。
2.1在面层型壳撒砂中的应用2.1.1面层型壳石英砂撒砂料的性能调整采用锆英石粉一硅溶胶涂料,只将撒砂由锆英石改为熔融石英砂(100/120目),经多次生产验证存在以下几方面质量问题。
(1)蒸汽脱蜡后型壳内表面有多处细长裂纹出现(同时脱蜡的撒锆英石砂型壳无裂纹)。
浇注后,型壳表面出现许多长条状飞翅(披锋)。
(2)浇注后铸件结构复杂处(直角凹槽处)有穿钢现象。
解剖脱蜡后的型壳,发现直角处有因硅溶胶回溶型壳开裂的孔洞。
同批、同一操作者撒锆英石砂,型壳此类废品极少(低于5%),而撒熔融石英砂相同零件同一部位穿钢数多达30%~50%,从而排除了操作不当因素。
使用的熔融石英砂,均经过150目筛网过筛,过150目的粉尘含量低于0.5%。
这也排除了砂中粉尘过多引起穿钢的原因。
由于熔融石英线膨胀系数很小,型壳在脱蜡及高温焙烧后,撒砂料与面层锆英石粉料膨胀系数相差过大而导致型壳裂纹及铸件表面产生飞翅缺陷。
数据-石英材料在碳钢硅溶胶精密铸造中的应用
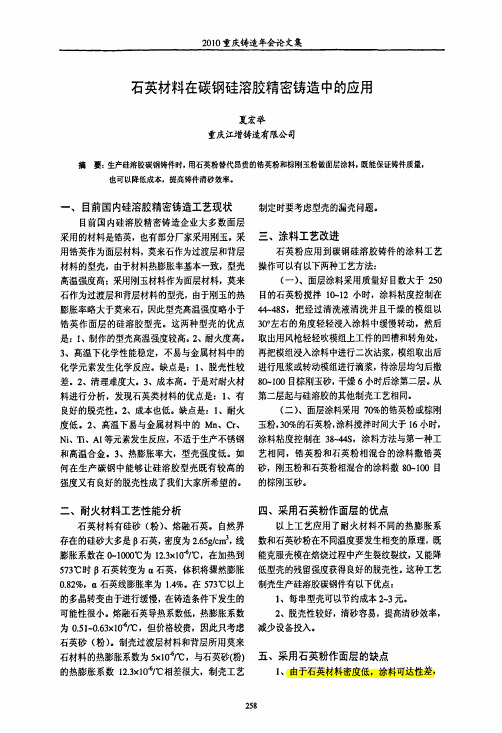
2010重庆铸造年会论文集石英材料在碳钢硅溶胶精密铸造中的应用夏宏举重庆江增铸造有限公司摘要:生产硅溶胶碳钢铸件时,用石英粉替代昂贵的锆英粉和棕刚玉粉做面层涂料,既能保证铸件质量,也可以降低成本,提高铸件清砂效率。
一、目前国内硅溶胶精密铸造工艺现状目前国内硅溶胶精密铸造企业大多数面层采用的材料是锆英,也有部分厂家采用刚玉。
采用锆英作为面层材料,莫来石作为过渡层和背层材料的型壳,由于材料热膨胀率基本一致,型壳高温强度高;采用刚玉材料作为面层材料,莫来石作为过渡层和背层材料的型壳,由于刚玉的热膨胀率略大于莫来石,因此型壳高温强度略小于锆英作面层的硅溶胶型壳。
这两种型壳的优点是:1、制作的型壳高温强度较高。
2、耐火度高。
3、高温下化学性能稳定,不易与金属材料中的化学元素发生化学反应。
缺点是:l、脱壳性较差。
2、清理难度大。
3、成本高。
于是对耐火材料进行分析,发现石英类材料的优点是:l、有良好的脱壳性。
2、成本也低。
缺点是:l、耐火度低。
2、高温下易与金属材料中的Mn、Cr、Ni、Ti、Al等元素发生反应,不适于生产不锈钢和高温合金。
3、热膨胀率大,型壳强度低。
如何在生产碳钢中能够让硅溶胶型壳既有较高的强度又有良好的脱壳性成了我们大家所希望的。
二、耐火材料工艺性能分析石英材料有硅砂(粉)、熔融石英。
自然界存在的硅砂大多是D石英,密度为2.659/em3,线膨胀系数在0-1000℃为12.3x10’℃,在加热到573℃时p石英转变为q石英,体积将骤然膨胀0。
82%,n石英线膨胀率为1A%。
在573℃以上的多晶转变由于进行缓慢,在铸造条件下发生的可能性很小。
熔融石英导热系数低,热膨胀系数为0.51-o.63xlO勺℃,但价格较贵,因此只考虑石英砂(粉)。
制壳过渡层材料和背层所用莫来石材料的热膨胀系数为5x10击/'C,与石英砂(粉)的热膨胀系数12.3×10勺℃相差很大,制壳工艺258制定时要考虑型壳的漏壳问题。
熔融石英的性能特点和使用资料
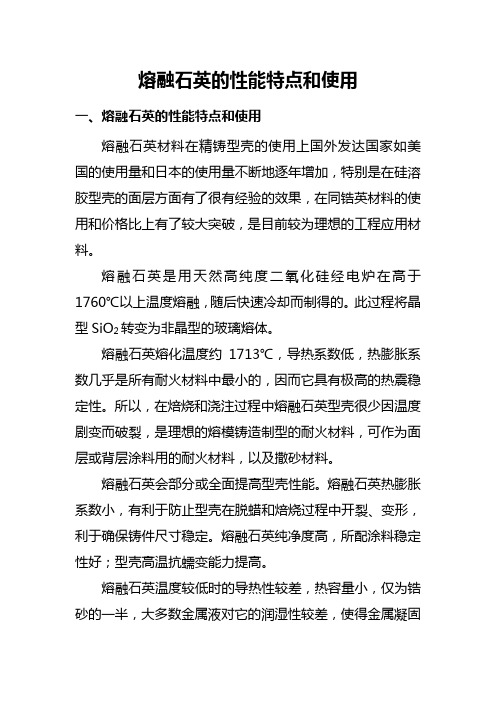
熔融石英的性能特点和使用一、熔融石英的性能特点和使用熔融石英材料在精铸型壳的使用上国外发达国家如美国的使用量和日本的使用量不断地逐年增加,特别是在硅溶胶型壳的面层方面有了很有经验的效果,在同锆英材料的使用和价格比上有了较大突破,是目前较为理想的工程应用材料。
熔融石英是用天然高纯度二氧化硅经电炉在高于1760℃以上温度熔融,随后快速冷却而制得的。
此过程将晶型SiO2转变为非晶型的玻璃熔体。
熔融石英熔化温度约1713℃,导热系数低,热膨胀系数几乎是所有耐火材料中最小的,因而它具有极高的热震稳定性。
所以,在焙烧和浇注过程中熔融石英型壳很少因温度剧变而破裂,是理想的熔模铸造制型的耐火材料,可作为面层或背层涂料用的耐火材料,以及撒砂材料。
熔融石英会部分或全面提高型壳性能。
熔融石英热膨胀系数小,有利于防止型壳在脱蜡和焙烧过程中开裂、变形,利于确保铸件尺寸稳定。
熔融石英纯净度高,所配涂料稳定性好;型壳高温抗蠕变能力提高。
熔融石英温度较低时的导热性较差,热容量小,仅为锆砂的一半,大多数金属液对它的润湿性较差,使得金属凝固层与型壳内表面间易产生间隙,热导率进一步减小,有利于壁薄铸件充型。
在高温下熔融石英的透明度高,能通过辐射传热,使其导热能力超过硅酸铝类壳。
而使铸件冷却较快,更易获得健全铸件。
铸件冷却时方石英又从高温型转变为低温型,同时体积产生骤变,使型壳出现无数裂纹,强度剧降,有利于脱壳进行。
熔融石英为酸性,能采用碱煮、碱爆等化学清砂方法去除型壳。
熔模铸造用熔融石英,其中SiO2所占的质量分数应为99.5%,配涂料用的粉料最好是270目或320目细粉占50%(质量分数),200目和120目粉各占25%(质量分数)。
①为0℃~1200℃间的膨胀系数平均值。
②400℃的热导率。
③1200℃热导率。
熔融石英及制品有三大特点:在所有耐火材料中,线膨胀系数最小(在1000℃的热胀率0.05);热导率最低,在1000℃热导率0.836W/(m·K)(0.02cal/cm·s·℃);抗热震性最好(在1200℃~水冷的抗震性),10次都不产生裂纹。
熔融石英的性能特点和使用解读

熔融石英的性能特点和使用一、熔融石英的性能特点和使用熔融石英材料在精铸型壳的使用上国外发达国家如美国的使用量和日本的使用量不断地逐年增加,特别是在硅溶胶型壳的面层方面有了很有经验的效果,在同锆英材料的使用和价格比上有了较大突破,是目前较为理想的工程应用材料。
熔融石英是用天然高纯度二氧化硅经电炉在高于1760℃以上温度熔融,随后快速冷却而制得的。
此过程将晶型SiO2转变为非晶型的玻璃熔体。
熔融石英熔化温度约1713℃,导热系数低,热膨胀系数几乎是所有耐火材料中最小的,因而它具有极高的热震稳定性。
所以,在焙烧和浇注过程中熔融石英型壳很少因温度剧变而破裂,是理想的熔模铸造制型的耐火材料,可作为面层或背层涂料用的耐火材料,以及撒砂材料。
熔融石英会部分或全面提高型壳性能。
熔融石英热膨胀系数小,有利于防止型壳在脱蜡和焙烧过程中开裂、变形,利于确保铸件尺寸稳定。
熔融石英纯净度高,所配涂料稳定性好;型壳高温抗蠕变能力提高。
熔融石英温度较低时的导热性较差,热容量小,仅为锆砂的一半,大多数金属液对它的润湿性较差,使得金属凝固层与型壳内表面间易产生间隙,热导率进一步减小,有利于壁薄铸件充型。
在高温下熔融石英的透明度高,能通过辐射传热,使其导热能力超过硅酸铝类壳。
而使铸件冷却较快,更易获得健全铸件。
铸件冷却时方石英又从高温型转变为低温型,同时体积产生骤变,使型壳出现无数裂纹,强度剧降,有利于脱壳进行。
熔融石英为酸性,能采用碱煮、碱爆等化学清砂方法去除型壳。
熔模铸造用熔融石英,其中SiO 2所占的质量分数应为99.5%,配涂料用的粉料最好是270目或320目细粉占50%(质量分数),200目和120目粉各占25%(质量分数)。
①为0℃~1200℃间的膨胀系数平均值。
耐火材料 化学组成 化学性质熔点/℃莫氏硬度 密度/(g/cm 3)膨胀系数①/×10-71/℃ 热导率/[W/(m 2.k)] 浸出性比较 颜色熔融石英 SiO 2 酸性 1713 7 2.251.951②在热浓碱和氢酸条件下有良好的可溶性 白色电熔刚玉 Al 2O 3 两性 2030 9 3.99~4.0 86 12.560②在热碱条件下反应很差 白色 莫来石 3Al 2O 3·2SiO 2 两性2030 6~72.7~2.9541.214② 在热碱条件下有轻微反应 灰色到棕黄色 高岭石 熟料 弱酸性 1700~1790 ~5 2.4~2.6 50- 在热碱条件下有轻微反应 灰色到棕黄色 锆砂 ZrSiO 4 弱酸性 <1948 7~8 4.5~4.9 46 2.094③在热碱条件下有中等反应 白色到棕黄色 氧化锆ZriO 2碱性26007~85.760-②400℃的热导率。
熔融石英的性能特点和使用解读

熔融石英的性能特点和使用一、熔融石英的性能特点和使用熔融石英材料在精铸型壳的使用上国外发达国家如美国的使用量和日本的使用量不断地逐年增加,特别是在硅溶胶型壳的面层方面有了很有经验的效果,在同锆英材料的使用和价格比上有了较大突破,是目前较为理想的工程应用材料。
熔融石英是用天然高纯度二氧化硅经电炉在高于1760℃以上温度熔融,随后快速冷却而制得的。
此过程将晶型SiO2转变为非晶型的玻璃熔体。
熔融石英熔化温度约1713℃,导热系数低,热膨胀系数几乎是所有耐火材料中最小的,因而它具有极高的热震稳定性。
所以,在焙烧和浇注过程中熔融石英型壳很少因温度剧变而破裂,是理想的熔模铸造制型的耐火材料,可作为面层或背层涂料用的耐火材料,以及撒砂材料。
熔融石英会部分或全面提高型壳性能。
熔融石英热膨胀系数小,有利于防止型壳在脱蜡和焙烧过程中开裂、变形,利于确保铸件尺寸稳定。
熔融石英纯净度高,所配涂料稳定性好;型壳高温抗蠕变能力提高。
熔融石英温度较低时的导热性较差,热容量小,仅为锆砂的一半,大多数金属液对它的润湿性较差,使得金属凝固层与型壳内表面间易产生间隙,热导率进一步减小,有利于壁薄铸件充型。
在高温下熔融石英的透明度高,能通过辐射传热,使其导热能力超过硅酸铝类壳。
而使铸件冷却较快,更易获得健全铸件。
铸件冷却时方石英又从高温型转变为低温型,同时体积产生骤变,使型壳出现无数裂纹,强度剧降,有利于脱壳进行。
熔融石英为酸性,能采用碱煮、碱爆等化学清砂方法去除型壳。
熔模铸造用熔融石英,其中SiO 2所占的质量分数应为99.5%,配涂料用的粉料最好是270目或320目细粉占50%(质量分数),200目和120目粉各占25%(质量分数)。
①为0℃~1200℃间的膨胀系数平均值。
耐火材料 化学组成 化学性质熔点/℃莫氏硬度 密度/(g/cm 3)膨胀系数①/×10-71/℃ 热导率/[W/(m 2.k)] 浸出性比较 颜色熔融石英 SiO 2 酸性 1713 7 2.251.951②在热浓碱和氢酸条件下有良好的可溶性 白色电熔刚玉 Al 2O 3 两性 2030 9 3.99~4.0 86 12.560②在热碱条件下反应很差 白色 莫来石 3Al 2O 3·2SiO 2 两性2030 6~72.7~2.9541.214② 在热碱条件下有轻微反应 灰色到棕黄色 高岭石 熟料 弱酸性 1700~1790 ~5 2.4~2.6 50- 在热碱条件下有轻微反应 灰色到棕黄色 锆砂 ZrSiO 4 弱酸性 <1948 7~8 4.5~4.9 46 2.094③在热碱条件下有中等反应 白色到棕黄色 氧化锆ZriO 2碱性26007~85.760-②400℃的热导率。
熔融石英的性能特点和使用
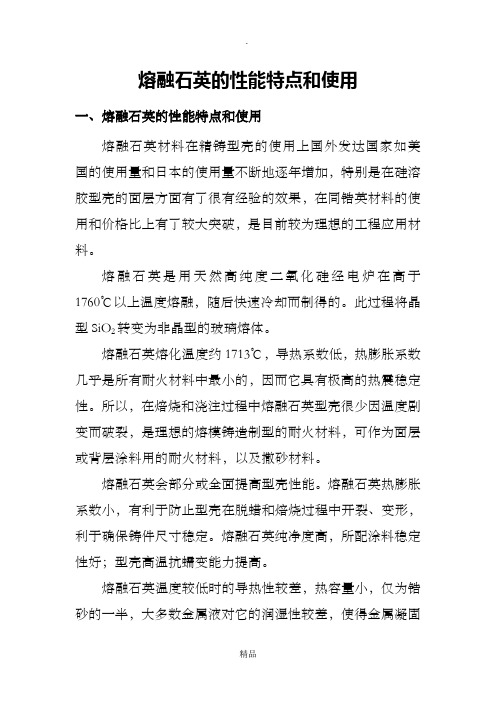
熔融石英的性能特点和使用一、熔融石英的性能特点和使用熔融石英材料在精铸型壳的使用上国外发达国家如美国的使用量和日本的使用量不断地逐年增加,特别是在硅溶胶型壳的面层方面有了很有经验的效果,在同锆英材料的使用和价格比上有了较大突破,是目前较为理想的工程应用材料。
熔融石英是用天然高纯度二氧化硅经电炉在高于1760℃以上温度熔融,随后快速冷却而制得的。
此过程将晶型SiO2转变为非晶型的玻璃熔体。
熔融石英熔化温度约1713℃,导热系数低,热膨胀系数几乎是所有耐火材料中最小的,因而它具有极高的热震稳定性。
所以,在焙烧和浇注过程中熔融石英型壳很少因温度剧变而破裂,是理想的熔模铸造制型的耐火材料,可作为面层或背层涂料用的耐火材料,以及撒砂材料。
熔融石英会部分或全面提高型壳性能。
熔融石英热膨胀系数小,有利于防止型壳在脱蜡和焙烧过程中开裂、变形,利于确保铸件尺寸稳定。
熔融石英纯净度高,所配涂料稳定性好;型壳高温抗蠕变能力提高。
熔融石英温度较低时的导热性较差,热容量小,仅为锆砂的一半,大多数金属液对它的润湿性较差,使得金属凝固层与型壳内表面间易产生间隙,热导率进一步减小,有利于壁薄铸件充型。
在高温下熔融石英的透明度高,能通过辐射传热,使其导热能力超过硅酸铝类壳。
而使铸件冷却较快,更易获得健全铸件。
铸件冷却时方石英又从高温型转变为低温型,同时体积产生骤变,使型壳出现无数裂纹,强度剧降,有利于脱壳进行。
熔融石英为酸性,能采用碱煮、碱爆等化学清砂方法去除型壳。
熔模铸造用熔融石英,其中SiO2所占的质量分数应为99.5%,配涂料用的粉料最好是270目或320目细粉占50%(质量分数),200目和120目粉各占25%(质量分数)。
①为0℃~1200℃间的膨胀系数平均值。
②400℃的热导率。
③1200℃热导率。
熔融石英及制品有三大特点:在所有耐火材料中,线膨胀系数最小(在1000℃的热胀率0.05);热导率最低,在1000℃热导率0.836W/(m·K)(0.02cal/cm·s·℃);抗热震性最好(在1200℃~水冷的抗震性),10次都不产生裂纹。
05 熔融石英

制壳耐火材料新秀——熔融石英—国外精铸技术进展述评(5)—原载《特种铸造及有色合金》,2005(5):294~298熔融石英在精铸中应用虽然已有相当长的历史,但以往主要用作陶瓷型芯,用作型壳则主要用于面层,背层很少使用。
这种状况近10 年来在美、欧各国有很大改变。
2001年美国著名耐火材料生产厂商Minco 公司,公布了对美国熔模铸造行业制壳耐火材料使用现况的调查统计数据,各种耐火材料消耗量所占比例的大致如下[1]:铝-硅系耐火材料55%、熔融石英30%、刚玉9%、锆石6%可见在美国精铸业中,熔融石英异军突起,在精铸制壳耐火材料的使用量中,已仅次于铝-硅系材料,远远超过锆石等其他耐火材料,迅速成为制壳耐火材料的一枝新秀。
一.熔融石英与铝-硅系材料的比较2000年美国Minco Inc.在美国第48 届精铸年会和INCAST 2001(3)发表的论文[1][2],对熔融石英和铝-硅系耐火材料进行了全面的分析对比。
主要结果如下:1)型壳重量熔融石英密度2.2g/cm3,铝-硅系材料约2.7g/cm3,故同样厚度型壳,前者重量明显轻于后者,有利于减轻工人劳动强度和机械手操作[1][2]。
2)热膨胀率图5-1 和图5-2 所示分别为脱蜡和焙烧过程中,这二种材料热膨胀率的比较[1][2]。
热膨胀系数小是熔融石英的一个很大的优点,有利于减小加热时,型壳内外因温度差造成的热应力,因而有利于防止脱蜡和焙烧过程中型壳开裂和变形。
同时,对提高铸件尺寸精度甚为有利。
所以,尺寸精度要求高的产品,就更适合采用熔融石英。
图5-1 脱蜡过程中二种材料热膨胀率的比较图5-2 焙烧过程中二种材料热膨胀率的比较3)力学性能和透气性表5-1所列为二种材料制得型壳的力学性能和透气性比较,结果显示,湿强度和断裂韧度,熔融石英型壳稍低于铝-硅系型壳,但透气性却远高于铝-硅系型壳[1][2]。
4)高温抗蠕变能力当采用熔融石英撒砂料代替硅酸铝时型壳高温抗蠕变能力提高(图5-3)[1][2] 。
熔融石英的性能特点和使用
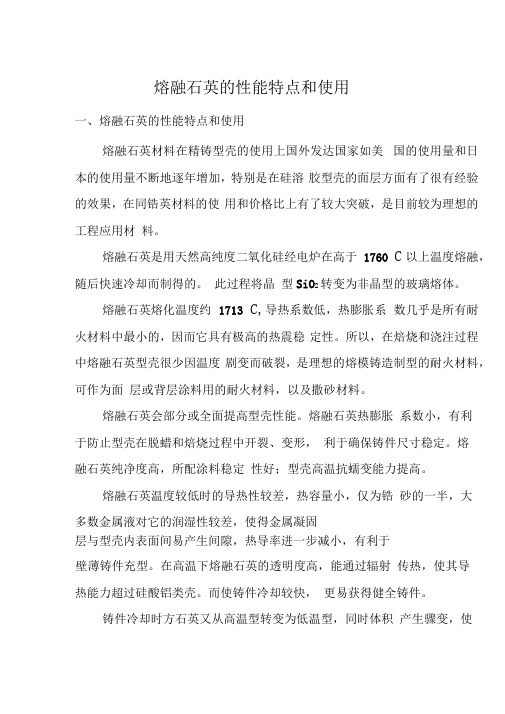
熔融石英的性能特点和使用一、熔融石英的性能特点和使用熔融石英材料在精铸型壳的使用上国外发达国家如美国的使用量和日本的使用量不断地逐年增加,特别是在硅溶胶型壳的面层方面有了很有经验的效果,在同锆英材料的使用和价格比上有了较大突破,是目前较为理想的工程应用材料。
熔融石英是用天然高纯度二氧化硅经电炉在高于1760 C以上温度熔融,随后快速冷却而制得的。
此过程将晶型SiO2转变为非晶型的玻璃熔体。
熔融石英熔化温度约1713 C,导热系数低,热膨胀系数几乎是所有耐火材料中最小的,因而它具有极高的热震稳定性。
所以,在焙烧和浇注过程中熔融石英型壳很少因温度剧变而破裂,是理想的熔模铸造制型的耐火材料,可作为面层或背层涂料用的耐火材料,以及撒砂材料。
熔融石英会部分或全面提高型壳性能。
熔融石英热膨胀系数小,有利于防止型壳在脱蜡和焙烧过程中开裂、变形,利于确保铸件尺寸稳定。
熔融石英纯净度高,所配涂料稳定性好;型壳高温抗蠕变能力提高。
熔融石英温度较低时的导热性较差,热容量小,仅为锆砂的一半,大多数金属液对它的润湿性较差,使得金属凝固层与型壳内表面间易产生间隙,热导率进一步减小,有利于壁薄铸件充型。
在高温下熔融石英的透明度高,能通过辐射传热,使其导热能力超过硅酸铝类壳。
而使铸件冷却较快,更易获得健全铸件。
铸件冷却时方石英又从高温型转变为低温型,同时体积产生骤变,使型壳出现无数裂纹,强度剧降,有利于脱壳进行。
熔融石英为酸性,能采用碱煮、碱爆等化学清砂方法去除型壳。
熔模铸造用熔融石英,其中SiO2所占的质量分数应为99.5%,配涂料用的粉料最好是270目或320目细粉占50%(质量分数),200目和120目粉各占25% (质量分数)。
①为0 C〜1200 C间的膨胀系数平均值。
②400 C的热导率。
③1200 C热导率。
熔融石英及制品有三大特点:在所有耐火材料中,线膨胀系数最小(在1000 C的热胀率0.05 );热导率最低,在1000 C热导率0.836W/ (m • K)(0.02cal/cm • s ・C);抗热震性最好(在1200 °C〜水冷的抗震性),10次都不产生裂纹。
硅溶胶在熔模精密铸造中的应用

粘结 ,且在室温配制涂料时又不会引起料浆胶凝 。常
使用粒径为 0. 075 mm 左右的氧化铝 、氧化锆 、莫来
石 、铝矿石及石英玻璃粉 ,为了改善涂料的浸涂性 ,往
往还要加入悬浮剂 、矿化剂 、渗透剂 、流平剂等辅助材
料 。稀释剂常用去离子水或酒精 。粉料的加入必须是 边加入边搅拌 ,防止局部粉料过多吸水导致硅溶胶胶 凝 。选定配方后 ,涂料的性能由其粘度和密度来决定 。 表 2 列出铸造镍基高温合金定向凝固铸件用壳型涂料 的典型配方及其性能 。
随着涂料浸渍使用 ,其性能必然发生变化 。水分 蒸发减少 ,粘度提高 ,故需按计算量补加少许硅溶胶和 去离子水 ,以保证原涂料 SiO2 含量及粘度 。冬季使用 硅溶胶粘结剂时 ,如果室内温度过低 ,配制涂料时粘度 会偏高 ,易产生气泡而影响型壳品质 。
表 2 定向凝固壳型涂料的典型配方及性能[3 ] Tab. 2 Typical component and properties of shell casting for di2
我国从 60 年代起开始生产和使用硅溶胶 ,近年来 用于熔模铸造的国产硅溶胶 ,品质日趋稳定并逐步向 国际商业品类靠拢 。北京航空材料学院从60年代末
收稿日期 :2001206220 ; 修订日期 :2001207218 作者简介 :肖 克 (19622 ) ,北京人 ,工程师 ,工学学士 1
作为熔模铸造壳型粘结剂的硅溶胶的性能指标包 括 SiO2 含量 、密度 、稳定剂的含量 、p H 值 、SiO2 粒径 。 表 1 列出熔模铸造行业常用的硅溶胶及其性能 。
表 1 熔模铸造行业常用的硅溶胶[1 、3 ] Tab. 1 Silica sol using for investment cast vocation
面层制壳工艺研究

涂料干燥工艺:自干1.5~2h;风干1.5~2h;氨干0.5 h,氨气流量:表面层10~15 L/min; 加固层10~20 L/min。
采用中国标准杯体积测定粘度。
再将电熔刚玉的主要成分及杂质与锆英砂作一个比较,见表2:
电熔刚玉 Al2O3≥98.5 Fe2O3≤0.10 1级锆砂 ZrO2≥65 Fe2O3≤0.30 2级锆砂 ZrO2≥63 Fe2O3≤0.70 3级锆砂 ZrO2≥60 Fe2O3≤1.00 表2 电熔刚玉与锆英砂成分比较表
2.1 锆英粉-熔融石英粉混合浆-撒锆英砂
面层配浆工艺如下:
锆英粉:熔融石英粉 = 85%:15%
粉液比: 1:3.2
粘度值(詹氏4#):42~45s
润湿剂:10kg面层硅溶胶加30ml
消泡剂:10kg面层硅溶胶加22ml
面层撒砂:100~120目锆英砂
面层干燥时间:6~7h
环境条件:温度22~25℃;湿度22~25%
该工艺适用于生产汽车零件和精密机械零件,面层制壳成本比全锆英粉降低约25%左右。
图3A左 锆英粉+熔融石英粉混合浆,撒锆英砂
Fig.3 Left Zircon-powder + Melting Quartz Powder Admixture pulp,Caesar Zircon-Sand
1.2莫来砂做面层撒砂材料
锆英石与高岭石这两种耐火材料有着良好的兼容性和复合性,所以,面层砂采用以莫来砂替代锆英砂。
面层配浆工艺如下:
粉液比(325目锆英粉): 1:3.3~3.4
粘度值(詹氏4#):42~45s
润湿剂:10kg面层硅溶胶加28ml
对熔模铸造硅溶胶型壳清理问题的探讨申鹏帅

对熔模铸造硅溶胶型壳清理问题的探讨申鹏帅发布时间:2023-06-15T01:59:17.468Z 来源:《中国电业与能源》2023年7期作者:申鹏帅[导读] 本文就熔模铸造硅溶胶型壳清理进行探究,最先阐述了熔模铸造硅溶胶型壳的常见清理方法,之后对影响熔模铸造硅溶胶型壳的清理因素进行分析,对制备过程与焙烧过程中的工艺进行分析,进一步降低清理难度,提高清理效率,实现良好的型壳清理。
上海万泽精密铸造有限公司 201400摘要:本文就熔模铸造硅溶胶型壳清理进行探究,最先阐述了熔模铸造硅溶胶型壳的常见清理方法,之后对影响熔模铸造硅溶胶型壳的清理因素进行分析,对制备过程与焙烧过程中的工艺进行分析,进一步降低清理难度,提高清理效率,实现良好的型壳清理。
关键词:熔模铸造;硅溶胶型壳;型壳焙烧引言铸造型壳是熔模铸造的关键部件,其性能好坏直接影响到铸件质量。
由于硅溶胶型壳的高强度、低密度、耐热性、耐腐蚀性和高耐磨性等优点,在熔模铸造中得到广泛应用。
但是,硅溶胶型壳在使用过程中,会产生一些缺陷,如型壳表面的积粉、粘砂、气孔等。
如果处理不当,会导致铸件质量下降。
因此,如何有效地清除型壳上的积粉和粘砂是非常重要的。
1.型壳清理的方法为了解决硅溶胶型壳清理的问题,人们进行了大量的研究,但目前还没有比较有效的方法。
目前,最常用的型壳清理方法有湿法、干法、化学法和机械法四种。
(1)湿法是用水、化学试剂或机械力去除型壳上的积粉和粘砂。
湿法清理型壳的主要特点是:(1)用水或化学试剂清除型壳上的积粉和粘砂很方便,一般用水就能达到目的。
(2)可以不留型壳上的残余涂料,因为在清理后型壳表面基本没有残留涂料。
(3)对于大直径的型壳,湿法清理成本很低。
干法清理型壳的主要特点是:(1)型壳上残留有大量的粉尘颗粒,有时会产生积粉和粘砂。
(2)清理后型壳表面很干净,不会留下残余涂料。
(3)由于型壳表面无残留涂料,因此型壳在使用过程中不易产生裂纹或裂纹倾向。
精密铸造制壳工艺特点及改进方向探讨
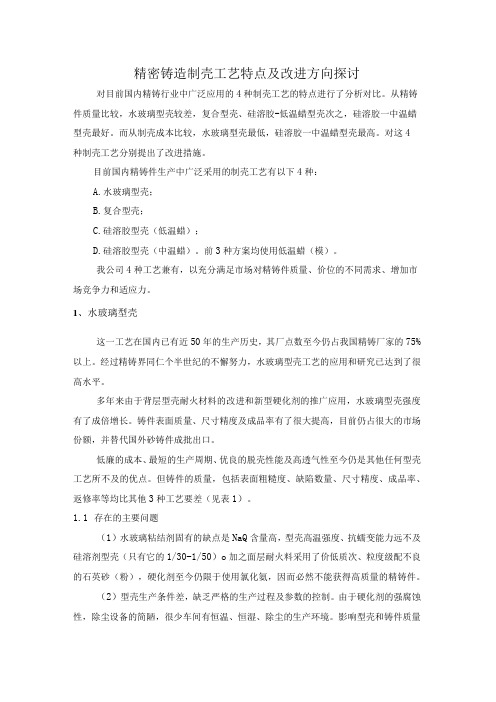
精密铸造制壳工艺特点及改进方向探讨对目前国内精铸行业中广泛应用的4种制壳工艺的特点进行了分析对比。
从精铸件质量比较,水玻璃型壳较差,复合型壳、硅溶胶-低温蜡型壳次之,硅溶胶一中温蜡型壳最好。
而从制壳成本比较,水玻璃型壳最低,硅溶胶一中温蜡型壳最高。
对这4种制壳工艺分别提出了改进措施。
目前国内精铸件生产中广泛采用的制壳工艺有以下4种:A.水玻璃型壳;B.复合型壳;C.硅溶胶型壳(低温蜡);D.硅溶胶型壳(中温蜡)。
前3种方案均使用低温蜡(模)。
我公司4种工艺兼有,以充分满足市场对精铸件质量、价位的不同需求、增加市场竞争力和适应力。
1、水玻璃型壳这一工艺在国内已有近50年的生产历史,其厂点数至今仍占我国精铸厂家的75%以上。
经过精铸界同仁个半世纪的不懈努力,水玻璃型壳工艺的应用和研究已达到了很高水平。
多年来由于背层型壳耐火材料的改进和新型硬化剂的推广应用,水玻璃型壳强度有了成倍增长。
铸件表面质量、尺寸精度及成品率有了很大提高,目前仍占很大的市场份额,并替代国外砂铸件成批出口。
低廉的成本、最短的生产周期、优良的脱壳性能及高透气性至今仍是其他任何型壳工艺所不及的优点。
但铸件的质量,包括表面粗糙度、缺陷数量、尺寸精度、成品率、返修率等均比其他3种工艺要差(见表1)。
1.1存在的主要问题(1)水玻璃粘结剂固有的缺点是NaQ含量高,型壳高温强度、抗蠕变能力远不及硅溶剂型壳(只有它的1/30-1/50)o加之面层耐火料采用了价低质次、粒度级配不良的石英砂(粉),硬化剂至今仍限于使用氯化氨,因而必然不能获得高质量的精铸件。
(2)型壳生产条件差,缺乏严格的生产过程及参数的控制。
由于硬化剂的强腐蚀性,除尘设备的简陋,很少车间有恒温、恒湿、除尘的生产环境。
影响型壳和铸件质量的涂料配制、硬化、风干、脱蜡等工序,极少按行业规定的操作规范严格控制。
如定期检测涂料粘度、涂片重、硬化剂浓度、PH值等。
型壳风干处的温度、湿度、风速等更是不加控制,故常在高、低温或梅雨季节发生批量报废的质量事故。
锆英粉与熔融石英粉混合浆料在熔模铸造生产中的应用

J u n . 2 O1 5 V o1 . 6 4 N0 . 6
铸
F O
造
R Y
锆 英 粉 与熔 融 石 英 粉 混 合 浆 料在 熔 模 铸 造 生产 中的应 用
景 宗梁 ,吴耀祖 ,孙 新
f 1 . 郑州大禹化 工产品有限公 司 ,河南郑州 4 5 0 0 0 8 ;2 . 深圳千里行新材料有 限公 司,广 东深圳 5 1 8 1 7 2 ;
d e n s i t y p o wd e r wa s s u ic f i e n t l y mi x e d , t h e p r o p e r t i e s o f l f u i d i y, t t h e s p r e a d a b i l i t y a n d d i s p e r s i t y o f s l u r r y a r e
g o o d. Th e pr o d u c t i o n t r i a l s ho w t h a t t he s u r f a c e r o ug h ne s s a nd d i me ns i o na l a c c u r a c y o f c a s t i ng s pr od uc e d by mi x e d s l u r r y a r e s i mi l a r t o t h e c a s t i n gs p r od u c e d b y 1 0 0 % z i r c o n po wde r s l u r r y , c l e a n i n g i s s i mp l e a nd t he c o s t
复晶砂、粉在硅溶胶精密铸造面层制壳中的应用
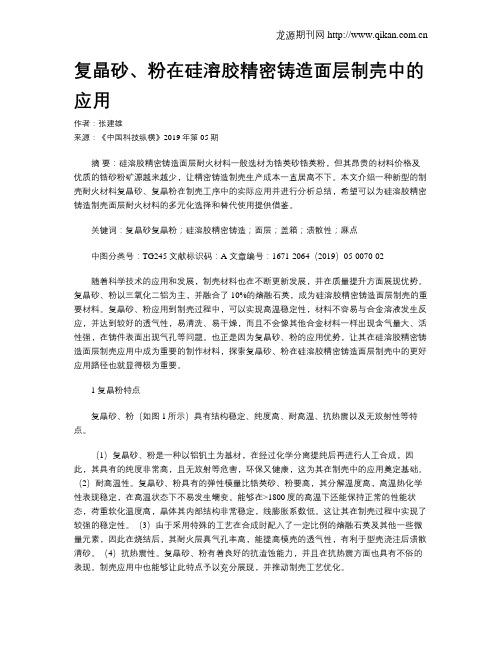
复晶砂、粉在硅溶胶精密铸造面层制壳中的应用作者:张建雄来源:《中国科技纵横》2019年第05期摘要:硅溶胶精密铸造面层耐火材料一般选材为锆英砂锆英粉,但其昂贵的材料价格及优质的锆砂粉矿源越来越少,让精密铸造制壳生产成本一直居高不下。
本文介绍一种新型的制壳耐火材料复晶砂、复晶粉在制壳工序中的实际应用并进行分析总结,希望可以为硅溶胶精密铸造制壳面层耐火材料的多元化选择和替代使用提供借鉴。
关键词:复晶砂复晶粉;硅溶胶精密铸造;面层;盖箱;溃散性;麻点中图分类号:TG245 文献标识码:A 文章编号:1671-2064(2019)05-0070-02随着科学技术的应用和发展,制壳材料也在不断更新发展,并在质量提升方面展现优势。
复晶砂、粉以三氧化二铝为主,并融合了10%的熔融石英,成为硅溶胶精密铸造面层制壳的重要材料。
复晶砂、粉应用到制壳过程中,可以实现高温稳定性,材料不容易与合金溶液发生反应,并达到较好的透气性,易清洗、易干燥,而且不会像其他合金材料一样出现含气量大、活性强,在铸件表面出现气孔等问题。
也正是因为复晶砂、粉的应用优势,让其在硅溶胶精密铸造面层制壳应用中成为重要的制作材料,探索复晶砂、粉在硅溶胶精密铸造面层制壳中的更好应用路径也就显得极为重要。
1 复晶粉特点复晶砂、粉(如图1所示)具有结构稳定、纯度高、耐高温、抗热震以及无放射性等特点。
(1)复晶砂、粉是一种以铝钒土为基材,在经过化学分离提纯后再进行人工合成,因此,其具有的纯度非常高,且无放射等危害,环保又健康,这为其在制壳中的应用奠定基础。
(2)耐高温性。
复晶砂、粉具有的弹性模量比锆英砂、粉要高,其分解温度高,高温热化学性表现稳定,在高温状态下不易发生蠕变。
能够在>1800度的高温下还能保持正常的性能状态,荷重软化温度高,晶体其内部结构非常稳定,线膨胀系数低。
这让其在制壳过程中实现了较强的稳定性。
(3)由于采用特殊的工艺在合成时配入了一定比例的熔融石英及其他一些微量元素,因此在烧结后,其耐火层真气孔率高,能提高模壳的透气性,有利于型壳浇注后溃散清砂。
熔融石英的性能特点和使用
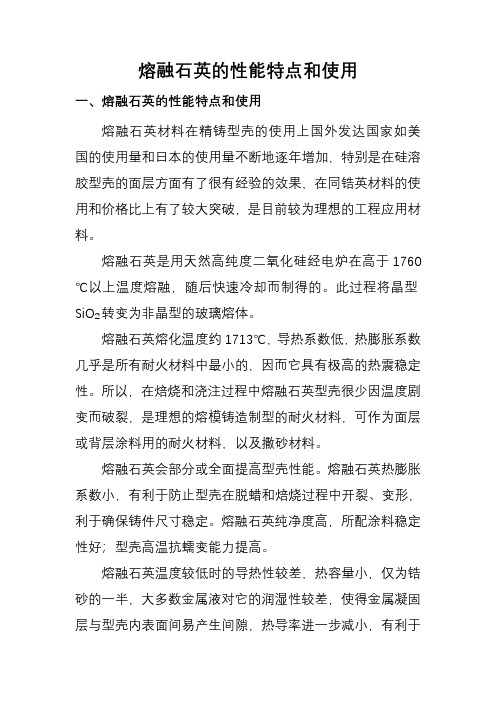
熔融石英的性能特点和使用一、熔融石英的性能特点和使用熔融石英材料在精铸型壳的使用上国外发达国家如美国的使用量和日本的使用量不断地逐年增加,特别是在硅溶胶型壳的面层方面有了很有经验的效果,在同锆英材料的使用和价格比上有了较大突破,是目前较为理想的工程应用材料。
熔融石英是用天然高纯度二氧化硅经电炉在高于1760℃以上温度熔融,随后快速冷却而制得的。
此过程将晶型SiO2转变为非晶型的玻璃熔体。
熔融石英熔化温度约1713℃,导热系数低,热膨胀系数几乎是所有耐火材料中最小的,因而它具有极高的热震稳定性。
所以,在焙烧和浇注过程中熔融石英型壳很少因温度剧变而破裂,是理想的熔模铸造制型的耐火材料,可作为面层或背层涂料用的耐火材料,以及撒砂材料。
熔融石英会部分或全面提高型壳性能。
熔融石英热膨胀系数小,有利于防止型壳在脱蜡和焙烧过程中开裂、变形,利于确保铸件尺寸稳定。
熔融石英纯净度高,所配涂料稳定性好;型壳高温抗蠕变能力提高。
熔融石英温度较低时的导热性较差,热容量小,仅为锆砂的一半,大多数金属液对它的润湿性较差,使得金属凝固层与型壳内表面间易产生间隙,热导率进一步减小,有利于②400℃的热导率。
③1200℃热导率。
熔融石英及制品有三大特点:在所有耐火材料中,线膨胀系数最小(在1000℃的热胀率0.05);热导率最低,在1000℃热导率0.836W/(m·K)(0.02cal/cm·s·℃);抗热震性最好(在1200℃~水冷的抗震性),10次都不产生裂纹。
二、熔融石英涂料配制使用操作工艺(一)本操作工艺适用于硅溶胶,制壳的表面层或过渡层。
(二)本工艺使用的硅溶胶同锆英粉涂料即SiO230%。
(三)本工艺操作中的润湿剂,消泡剂同锆英粉涂料。
(四)本操作中使用的流杯粘度计为詹氏(Zahn)5#杯,出口孔径为Φ5.28mm。
(五)涂料配制:1、熔融石英粉的配制,320目(网号:0.044)275目(网号:0.052)200目(网号:0.076)120目(网号:0.125)熔融石英粉中的SiO2的质量分数为99.5%以上。
精铸硅溶胶型壳工艺的改进
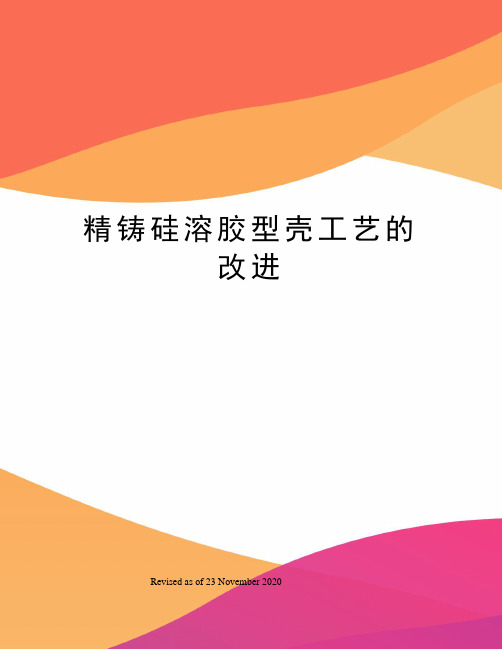
精铸硅溶胶型壳工艺的改进Revised as of 23 November 2020一.前言:众所周知,全球精铸界通用的硅溶胶型壳工艺存在三大缺点:1.成本高。
2.制壳周期长。
3.铸件脱壳性差(型壳残留强度高)。
据统计,表面层型壳通用的耐火料锆英石砂、粉占型壳原辅材料成本的4 8%,占总生产成本的10%(平均值)[1] 。
优质锆英石资源稀缺,因而寻找它的代用品或减少其消耗量是当今国内外精铸界共同关心,重点研究的课题之一。
“快干”硅溶胶的推广应用和真空干燥设备的逐步完善,缓解了制壳周期长的缺点。
由于硅溶胶型壳高温强度高(是水玻璃型壳的倍),其相应的残留强度也高(是水玻璃型壳的倍),因而铸件的脱壳性能比水玻璃差得多。
加之大部分生产的精铸件是结构复杂的中小件,型壳残留强度高会严重影响后处理工序生产效率和增加材料工时成本、降低铸件表面质量,延误交货期。
我们通过学习国内外同行的先进经验,经过多年的努力研究和实践,在降低硅溶胶型壳生产成本和改善脱壳性方面取得了一定成效,特向精铸界同仁作一介绍,以期达到抛砖引玉的目的。
二.表面层制壳工艺的改进:〈一〉. 锆英石粉料的代用—长期以来锆英石是全球精铸业首选的型壳表面层耐火料。
正如2007年美国精铸学会(ICI)第54届年会论文所言:“锆英石与多种合金反应低、密度高、热化学性能好,要寻找替代用品是困难的”。
[2]1.美国在2006年前面层涂料的典型工艺是在锆英粉中掺加5-10%(质量)的熔融石英粉。
其主要目的是:降低成本,提高铸件尺寸精度和改善脱壳性、透气性。
国外重点工艺改进方向是:充分利用熔融石英纯度高,杂质少,密度和热膨胀系数小,加上高温“析晶”,低温“相变”的特点,使型壳在高温时保持高强度而在低温时因相变产生剧烈收缩(%)致使型壳残留强度大大降低,从而使铸件脱壳性、透气性、尺寸精度提高。
自2007年起,通过技术改进美国已有80%的精铸企业表面层涂料中的熔融石英粉掺入量已提高至50%(按体积比为%)。
石英材料在精铸制壳中的应用
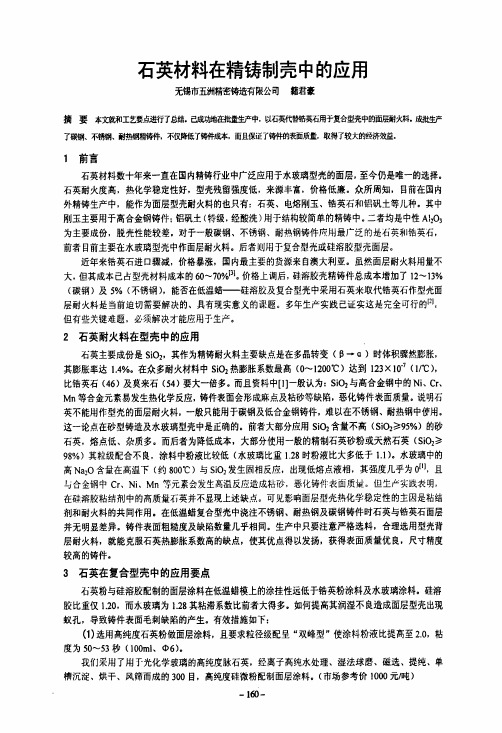
4几点体会
(1)锆英石比重大约为3.9~4.99/cm3(平均4.59/cm3)石英为2.659/cm3配制面层涂料时锆英 粉涂料粉液比约为3.4而石英粉最大为2.0(硅溶胶涂料)。两者在相同容积时重量差约1.7倍。用砂 也如此,因而,不仅锆英砂粉单价(平均市价为10000元,吨)比石英石(粉为1000元/吨,砂400 元/吨,耗量相同,平均单价为700元/吨)高出14倍。按重量计其实际差价高达24倍。据统计:复 合型壳采用锆英石成本单价为3000元/吨(铸件),而石英石成本单价为126元/吨(铸件)13】,即每 公斤铸件其成本相差约3元。用石英代替锆英石铸件成本可大辐下降,经济效益十分可观。
(4)石英——硅溶胶面层在干燥时即使采用风干或湿度较低时(RH≤50%),也不出现裂缝或面 层脱壳现象。尤其是尖角.锐边处也无开裂现象。大平面铸件上也无锆英石——砖溶胶面层特有的
缺陷“表面凹槽”出现,这是其优点之一,原因还有待进一步探讨。
(5)按相同原理,正在试验此工艺在低温模料——全硅溶胶型壳中应用,初步已获成功。 (6)应加强研究熔融石英在硅溶胶型壳中的应用。其热膨胀系数仅为5×10订(1,℃)比锆英石
胶型壳工艺,采用价昂,稀缺的锆英石。对于l---60公斤的中大件而言,尺寸精度也不会要求甚高, 一般为CT4"--CT6(GB6414.86)这一要求复合型壳完全能够达到。 实践表明,此工艺除个别钢种(高锰钢等)外。碳钢、不锈钢、耐热钢、低合金钢、合金工具 钢等均可应用。铸件表面质量良好,返修率很低。与锆英石面层壳生产的铸件并无差异。
PH
≤0.03
7+0.5
烧热I粒度 ≤o.10 I 300目
- 1、下载文档前请自行甄别文档内容的完整性,平台不提供额外的编辑、内容补充、找答案等附加服务。
- 2、"仅部分预览"的文档,不可在线预览部分如存在完整性等问题,可反馈申请退款(可完整预览的文档不适用该条件!)。
- 3、如文档侵犯您的权益,请联系客服反馈,我们会尽快为您处理(人工客服工作时间:9:00-18:30)。
熔融石英在硅溶胶型壳中的应用实践
作者:籍君豪
作者单位:苏州华宏精密铸造有限公司
1.籍君豪.徐广民.JI Jun-hao.XU Guang-min熔融石英在硅溶胶型壳中的应用[期刊论文]-铸造2008,57(8)
2.籍君豪精铸硅溶胶型壳质量的生产现场控制[会议论文]-2007
3.董茵.DONG Yin燃气轮机导流板精铸件型壳面层裂纹分析及改进[期刊论文]-铸造2009,58(2)
4.董茵大平面精铸件型壳面层裂纹分析及改进[会议论文]-2008
5.李彦平精密铸造硅溶胶浆料的质量控制[会议论文]-2008
6.籍君豪提高精铸件后处理质量及效率的有效措施[会议论文]-2003
7.李磊锤击法清除铸件浇冒口的研究与拓展[会议论文]-2009
8.陈冰.Chen Bing制壳过程自动化--国外精铸技术进展述评(6)[期刊论文]-特种铸造及有色合金2005,25(6)
9.闫双景.吕志刚.崔旭龙.姜不居.宿运招.马幼华.蔡俊茹用电熔刚玉代替锆英做型壳面层[会议论文]-2005
10.李彦平.Li Yanping精密铸造硅溶胶浆料品质的控制[期刊论文]-铸造工程2009,33(3)
引用本文格式:籍君豪熔融石英在硅溶胶型壳中的应用实践[会议论文] 2007。