硅溶胶型壳常见缺陷及防止措施
硅溶胶水玻璃复合工艺易出现的问题

一、对硅溶胶水玻璃复合工艺的介绍硅溶胶水玻璃复合工艺是一种常见的玻璃加工工艺,通过将硅溶胶涂覆在玻璃表面后再进行固化处理,形成一层具有耐磨、防水、耐腐蚀等特性的材料。
这种工艺广泛应用于建筑、玻璃工艺制品、家居用品等领域。
二、硅溶胶水玻璃复合工艺易出现的问题1. 硅溶胶选择不当:硅溶胶的选择直接影响着复合后的玻璃表面性能,如果选择不当,可能导致复合膜的附着力不足、耐磨性差等问题。
2. 复合厚度不均匀:在复合过程中,如果涂覆的硅溶胶层厚度不均匀,可能导致玻璃表面出现凹凸不平的情况,降低美观度和使用寿命。
3. 固化温度不足:硅溶胶水玻璃复合后需要进行固化处理,如果固化温度不足,可能导致复合膜的硬度不足,影响其耐磨、耐腐蚀性能。
4. 固化时间不足:固化时间不足会导致硅溶胶水玻璃复合层未完全固化,使得其性能不稳定,容易出现开裂、剥离等问题。
5. 操作流程不规范:在硅溶胶水玻璃复合工艺中,如果操作人员在操作过程中存在疏忽大意、操作流程不规范等问题,可能导致复合效果不理想。
三、解决硅溶胶水玻璃复合工艺易出现的问题的建议1. 选择合适的硅溶胶:在进行硅溶胶水玻璃复合工艺时,应根据玻璃的具体用途和要求选择合适的硅溶胶,保证复合后的性能满足需求。
2. 控制涂覆厚度:在复合过程中,要严格控制涂覆厚度,确保复合膜的厚度均匀,避免出现凹凸不平的情况。
3. 严格控制固化条件:在固化过程中,要严格控制固化温度和固化时间,确保复合膜能够充分固化,保证其性能稳定。
4. 规范操作流程:在进行硅溶胶水玻璃复合工艺时,要制定规范的操作流程,严格按照操作规程进行操作,避免出现疏忽大意导致的问题。
四、结语硅溶胶水玻璃复合工艺是一种常见的玻璃加工工艺,在实际应用中容易出现一些问题。
通过选择合适的硅溶胶、严格控制涂覆厚度、固化条件和规范操作流程,可以有效解决这些问题,保证复合后的玻璃具有良好的性能和稳定的质量。
在进行硅溶胶水玻璃复合工艺时,除了上述提到的问题和解决建议外,还有一些其他容易出现的问题需要引起注意。
精铸硅溶胶型壳工艺的改进电子教案

5.由表十一,十二及十三实验结果得出以下结论:
⑴.在表面层涂料中加入少量“分散剂”能改变硅溶胶涂料的流变特性,增
加涂料的屈服值从而可提高涂挂性和覆盖性(涂层平均厚度)3可提高15-25%。同时由于
“分散剂”作用能使粉料“分散”不易“结团”。使平均粒径减小因而3增加。虽然粉液比
n略有下降,但致密性k%仍在要求范围之内(表七)。涂料的均匀性,悬浮性,涂挂性和流 平性均有提高。“板结”“老化”时间延长(稳定性提高)。
1.美国在2006年前面层涂料的典型工艺是在锆英粉中掺加5-10%(质量)的熔融石英粉。
其主要目的是:降低成本,提高铸件尺寸精度和改善脱壳性、透气性。国外重点工艺改进方 向是:充分利用熔融石英纯度高,杂质少,密度和热膨胀系数小,加上高温“析晶”,低温
“相变”的特点,使型壳在高温时保持高强度而在低温时因相变产生剧烈收缩(-3.7%)致
精铸硅溶胶型壳工艺的改进
前言:
众所周知,全球精铸界通用的硅溶胶型壳工艺存在三大缺点:
1.成本高。2.制壳周期长。3.铸件脱壳性差(型壳残留强度高)。
据统计,表面层型壳通用的耐火料锆英石砂、粉占型壳原辅材料成本的48%占总生产成本
的10%(平均值)[1]。优质锆英石资源稀缺,因而寻找它的代用品或减少其消耗量是当今 国内外精铸界共同关心,重点研究的课题之一。
2.混合涂料用粉料粒度要求应符合表五规定。
注:1•采用GSL-101BI型“激光颗粒度测定仪” 测定(丹东市辽宁仪器仪表研究所生产)
2.粒度判定以DV90, DV50及Wo三项指标为主要依据。DV98 DV84为参考指标。
3.无粒度检测条件时,可将待测粉料与“标准”硅溶胶配制成“标准”涂料来判定
硅溶胶涂料中气泡的解决办法
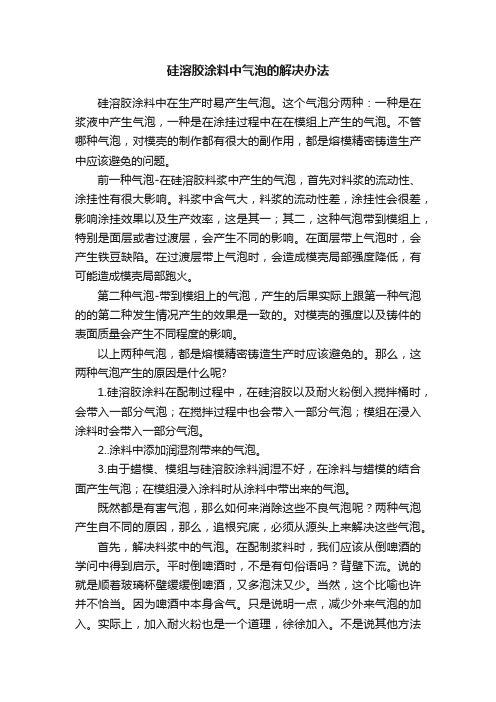
硅溶胶涂料中气泡的解决办法硅溶胶涂料中在生产时易产生气泡。
这个气泡分两种:一种是在浆液中产生气泡,一种是在涂挂过程中在在模组上产生的气泡。
不管哪种气泡,对模壳的制作都有很大的副作用,都是熔模精密铸造生产中应该避免的问题。
前一种气泡-在硅溶胶料浆中产生的气泡,首先对料浆的流动性、涂挂性有很大影响。
料浆中含气大,料浆的流动性差,涂挂性会很差,影响涂挂效果以及生产效率,这是其一;其二,这种气泡带到模组上,特别是面层或者过渡层,会产生不同的影响。
在面层带上气泡时,会产生铁豆缺陷。
在过渡层带上气泡时,会造成模壳局部强度降低,有可能造成模壳局部跑火。
第二种气泡-带到模组上的气泡,产生的后果实际上跟第一种气泡的的第二种发生情况产生的效果是一致的。
对模壳的强度以及铸件的表面质量会产生不同程度的影响。
以上两种气泡,都是熔模精密铸造生产时应该避免的。
那么,这两种气泡产生的原因是什么呢?1.硅溶胶涂料在配制过程中,在硅溶胶以及耐火粉倒入搅拌桶时,会带入一部分气泡;在搅拌过程中也会带入一部分气泡;模组在浸入涂料时会带入一部分气泡。
2..涂料中添加润湿剂带来的气泡。
3.由于蜡模、模组与硅溶胶涂料润湿不好,在涂料与蜡模的结合面产生气泡;在模组浸入涂料时从涂料中带出来的气泡。
既然都是有害气泡,那么如何来消除这些不良气泡呢?两种气泡产生自不同的原因,那么,追根究底,必须从源头上来解决这些气泡。
首先,解决料浆中的气泡。
在配制浆料时,我们应该从倒啤酒的学问中得到启示。
平时倒啤酒时,不是有句俗语吗?背壁下流。
说的就是顺着玻璃杯壁缓缓倒啤酒,又多泡沫又少。
当然,这个比喻也许并不恰当。
因为啤酒中本身含气。
只是说明一点,减少外来气泡的加入。
实际上,加入耐火粉也是一个道理,徐徐加入。
不是说其他方法不行,只是其他方法后期处理时间一点不会少。
另外,在模组浸入涂料时,也是要倾斜角度,慢慢浸入,缓缓回转。
这是配制过程中应该注意的。
料浆配制完后并不能立即使用,而必须有一个醒浆的过程。
对熔模铸造硅溶胶型壳清理问题的探讨申鹏帅

对熔模铸造硅溶胶型壳清理问题的探讨申鹏帅发布时间:2023-06-15T01:59:17.468Z 来源:《中国电业与能源》2023年7期作者:申鹏帅[导读] 本文就熔模铸造硅溶胶型壳清理进行探究,最先阐述了熔模铸造硅溶胶型壳的常见清理方法,之后对影响熔模铸造硅溶胶型壳的清理因素进行分析,对制备过程与焙烧过程中的工艺进行分析,进一步降低清理难度,提高清理效率,实现良好的型壳清理。
上海万泽精密铸造有限公司 201400摘要:本文就熔模铸造硅溶胶型壳清理进行探究,最先阐述了熔模铸造硅溶胶型壳的常见清理方法,之后对影响熔模铸造硅溶胶型壳的清理因素进行分析,对制备过程与焙烧过程中的工艺进行分析,进一步降低清理难度,提高清理效率,实现良好的型壳清理。
关键词:熔模铸造;硅溶胶型壳;型壳焙烧引言铸造型壳是熔模铸造的关键部件,其性能好坏直接影响到铸件质量。
由于硅溶胶型壳的高强度、低密度、耐热性、耐腐蚀性和高耐磨性等优点,在熔模铸造中得到广泛应用。
但是,硅溶胶型壳在使用过程中,会产生一些缺陷,如型壳表面的积粉、粘砂、气孔等。
如果处理不当,会导致铸件质量下降。
因此,如何有效地清除型壳上的积粉和粘砂是非常重要的。
1.型壳清理的方法为了解决硅溶胶型壳清理的问题,人们进行了大量的研究,但目前还没有比较有效的方法。
目前,最常用的型壳清理方法有湿法、干法、化学法和机械法四种。
(1)湿法是用水、化学试剂或机械力去除型壳上的积粉和粘砂。
湿法清理型壳的主要特点是:(1)用水或化学试剂清除型壳上的积粉和粘砂很方便,一般用水就能达到目的。
(2)可以不留型壳上的残余涂料,因为在清理后型壳表面基本没有残留涂料。
(3)对于大直径的型壳,湿法清理成本很低。
干法清理型壳的主要特点是:(1)型壳上残留有大量的粉尘颗粒,有时会产生积粉和粘砂。
(2)清理后型壳表面很干净,不会留下残余涂料。
(3)由于型壳表面无残留涂料,因此型壳在使用过程中不易产生裂纹或裂纹倾向。
常见涂装缺陷及应对措施
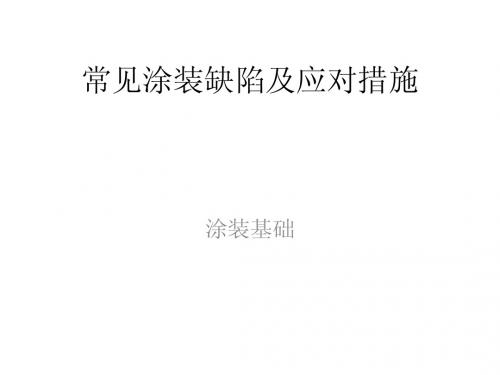
涂装基础
缩孔 凹陷 鱼眼
涂面产生涂膜被压扁的凹状,由于上下两层的涂膜表面 张力不同,湿膜上层的表面张力低于下层,产生缩孔。 1.喷涂环境原因:周围使用了有机硅类或蜡等物质。应检 查所有设备辅料,绝对不能使用硅酮类等物质。 2.设备,人员:调漆工具,手套,工作服等不干净。 3.素材清洗:脱脂效果不良,有水,油,打膜灰,脱模剂 等异物。应检查前处理工艺参数:热脱脂温度,清洗剂 浓度,喷淋冲洗喷头口压力,堵塞情况等。 4.材料原因:所选涂料表面张力偏低,对缩孔的敏感性大, 涂料或溶剂等受污染,涂料不匹配。应检查湿膜表面张 力,跟换涂料。 5.返工件打磨:对原有类缺陷的问题打磨不彻底。
失光
涂膜干燥后没有达到应有的光泽,或出现雾状朦胧现象. 1.涂料方面:溶剂或固化剂等添加剂配套问题,混合比例 问题。应选择正确的配套溶剂,固化剂,添加剂及混合 比例。 2.膜厚不够:涂料干燥后没有形成完整的涂膜。 3.油漆吸收:素材或下层油漆对上层油漆吸收,因下层油 漆的粗糙,不均匀,2C1B的底漆没有表干等均会引起对 清漆的吸收。 4.漆雾干扰:喷房风速低,风向问题,漆雾过大,落至漆 膜表面,影响光泽。
橘皮
涂层如桔子表皮状凹凸不平,涂料湿膜因溶剂挥发内部 产生对流现象,流动过早停止而产生凹凸不平状. 1.环境原因:喷房,流平区温度高,风速快,导致溶剂挥 发过快。应设定最佳的稳定的喷房温度和风速。 2.涂料,溶剂:稀释剂挥发速度快,涂料粘度高,流平性 差。应降低溶剂挥发速度,降低涂料粘度,以改善涂料 的流动性。 3.喷涂工艺:喷涂压力低,雾化效果差导致涂料颗粒大, 不易流平,膜厚过薄,干燥过快。应调整适当的喷涂参 数设置。 4.被涂物温度高:零件温度过高,导致湿膜溶剂挥发过快。 应降低被涂物零件温度。
硅溶胶型壳常见缺陷及防止措施

硅溶胶型壳常见缺陷及防止措施1.型壳表面粗糙:2.型壳面层裂纹:特征产生原因防止措施型壳表面层出现不规则的裂纹,或出现极细小的龟状裂纹这些裂纹是型壳干燥时产生的,主要是由丁面层干燥过快,或涂料干燥收缩过大引起的,或由丁蜡模热膨胀使面层型壳被胀裂.及型模焙烧不当引起.具体产生原因:1.环境相对湿度太低2.面层干燥时间过长3.空气流动不均匀而且过大4.环境温度变化过大5.壳模焙烧不当.1.面层干燥区相对湿度宜在RH60〜70咆问.2.面层干燥时间以4〜6h为宜,特殊产品不要超过10h.3.风不要正对模组吹,应降低直接吹到模组上的气流量.4.制壳间温度应严格控制,保持在22〜25C之间.5.脱蜡后壳模应在至少4h后装炉焙烧.尽量避免高温-低温-高温焙烧及二次焙烧.3.型壳面层鼓裂:特征型壳面层局部与蜡模分开向外鼓起(图a),或鼓起后破裂导致背层涂料流到蜡模和面层之间,但未将空隙填满(图b、图c).,产生原因防止措施1.面层型壳与蜡模问附着力大差1.确保蜡模活洗好.2.面层涂料润湿剂加入量合适.2.面层型壳外表面干燥过度、内表面干燥不足.1.控制好环境相对湿度、面层干燥时间和风速,确保面层型壳外、内表面干燥合适.2.应使面层涂料厚合适,不要过厚.3.面层型壳湿强度』、足,特别是在蜡模锐角处其强度低1.保证面层型壳湿强度.为此,要保证硅溶胶和耐火材料的质量,按工艺规范保持涂料正确配方,配制方法及确保涂料性能合格.2.要保证蜡模锐角处有一定厚度的涂料,且涂料不要滴得过干.4.制壳|可温度不均匀保持制壳问温湿度均匀.4.型壳内孔搭桥:5.型壳面层剥落:6.型壳强度低:温度变化不均型壳脱蜡时面层剥落.原因是面层和 第二层型壳问结合力太差而赞成的.1. 面层太太厚.2. 第二层涂料粘度太大,难丁渗入 面层. 3. 面层撒砂太细,一二层很难形成 牢固的镶嵌结构. 4. 撒砂中粉尘量及含水量过大,造 成分层.5. 面层撒砂过慢等引起撒砂未能嵌 入涂层内部.而是浮贴在涂层上, 或根本未撒上砂子形成涂料与涂 料接触,产生分层.6. 上第二层涂料前未去除面层型壳 上松散的浮砂.7. 未使用预湿剂,导致个别地方涂 挂不良.确保除湿问的绝热性与温度的均衡性.1. 面层太厚的原因导之丁面浆过浓,粘砂时,耐火材料仅在浆的表面而无法 深入浆层,失去键销阻绝大面收缩的 效果,使浆层干燥后产生微裂,因此,可 适当降低浆液的浓度.2. 第二层涂料粘度不能太大. 焙烧时型壳面层剥落,则是由丁两涂层间热胀系数不同而造成的.4. 控制砂的质量,将粉尘含量列入管制 标准.撒砂中粉尘含量与水的含量均 应低丁0.5%.5. 滴回浆不可过干,撒砂不应过慢.6. 在制第二层型壳前以柔和风吹去表面 松散砂粒.7. 制第二层型壳前,把模组浸入硅溶胶 预湿剂中(不超过2S ),取出甩干或滴干(表面无明显滴落胶液),再上第二层涂 料.尽量使面层和二层的材料热膨胀系数相 近.7.型壳裂纹:8.气泡、毛刺:9.未润湿:10.壳模破裂:11.壳模层间剥落:12.壳模鼓胀变形、强度不足:。
熔模精密铸造过程疑难问题解答

熔模精密铸造过程疑难问题解答熔模精密铸造过程疑难问题解答前言三百六十行,行行出人才。
各行各业都有自己的特长。
各从业人员必须熟练地掌握本行业、本岗位的职业技能,具备一定的包括职业技能在内的职业素质,才能胜任工作,把工作做好,为本行业做出应有的贡献,实现自己的人生价值。
熔模铸造业是技术密集型的行业。
本行业对其职工职业素质的要求比较高。
在科学技术迅速发展的今天,更是这样。
精铸业的职工队伍中,大部分是技术员工。
他们是企业的主力军,是振兴和发展本企业的技术力量。
技术人员素质如何,直接关系到本企业的生存和发展。
在市场经济条件下,企业之间的竞争,是质量之竞争;价格之竞争;也是技术之竞争;归根结底是人才的竞争。
优秀的技术员工是企业各类人才中重要的组成部分。
企业必须有这样一支高素质的技术工人队伍,有这样一批技术过硬、技艺精湛的能工巧匠,才能保证产品质量,提高生产效率,降低物料消耗,使企业获得经济效益;才能支持企业不断生产出高难度的产品,去发掘市场、占领市场;才能在激烈的市场竞争中立于不败之地!由于本人水平有限,加之时间仓促,难免存在不足和错误,诚恳希望专家,工程师和同仁批评指正。
吴光来第一章熔模铸件工艺设计与模具设计§1、熔模铸件工艺设计1.1、熔模铸件的尺寸精度受到哪些因素的影响?答:铸件尺寸精度受铸件结构、材质、制模、制壳、焙烧、浇注等多种因素的影响。
1)、铸件结构的影响:(1)、铸件壁厚,收缩率大;铸件壁薄,收缩率小;(2)、自由收缩率大,阻碍收缩率小。
2)、材质的影响:(1)、材料中含碳量越高,线收缩率越小,含碳量越低,线收缩率越大;(2)常见材质的铸造收缩率如下:铸造收缩率K=(LM-LJ)/LJ×100%LM—型腔尺寸;LJ—铸件尺寸K受以下因素的影响:蜡模K1、铸件结构K2、合金种类K3、浇注温度K4。
合金种类收缩率自由收缩受阻收缩铸铁件 0.8% 0.7%碳钢及低合金钢 1.6-2.0% 1.3-1.7%不锈钢 2.0-2.3% 1.7-2.0%3)、制模对铸件线收缩率的影响:(1)蜡(模)料的线收缩率约为0.9-1.1%;(2)蜡模径向(受阻)收缩率仅为长度方向(自由)收缩率的30-40%,射蜡温度对自由收缩率的影响远远大于对受阻收缩率的影响。
硅溶胶型壳之我见

硅溶胶型壳之我见硅溶胶型壳尽管大部分人都知道是怎么回事。
但是,仔细一深究,好像又不知道是怎么回事。
利用今天这个机会,结合一些朋友的提问,我想把我对硅溶胶型壳的一些认识跟大家聊聊。
当然,再次声明,这些认识仅仅是个人观点,仅供参考。
第一点,硅溶胶型壳为层与层之间镶嵌并通过硅溶胶涂料来粘结构成的。
这个镶嵌就是砂与砂之间镶嵌,在砂与砂之间是硅溶胶涂料。
硅溶胶涂料就像一种胶,把两个毛面连接起来。
现在的年轻人可能很少补鞋,但是补轮胎肯定是见过。
修车师傅先是用锉把轮胎漏气处锉毛,然后再把补丁贴上去。
实际上锉毛的道理跟硅溶胶型壳两层之间的毛面由于,就是为了结合更好。
那么,为什么会有面层、过渡层以及背层砂之分?实际上就是粒度接近的毛面会镶嵌的比较好,也就是结合紧密。
你比如,面层100目的砂子与过渡层30~60目的砂子比较接近,(当然还有更接近的)过渡层30~60目的砂子跟背层16~30目的砂子比较接近,同规格的砂子镶嵌更是最佳组合。
不知道大家注意到没有,砂子一般要求不能有粉尘,或者说粉尘量要少于多少。
这是为什么呢?实际上就是在有粉的情况下层与层之间结合不好,那么型壳的强度自然会大打折扣,甚至出现分层现象。
另外,浮砂也是这个道理。
浮砂就等于在层与层之间形成一个滑移带,因此,制壳时浮砂是必须要清理掉的。
第二点,型壳各层的作用。
面层自不必说,它起到的作用主要是形成铸件的表面,抗击熔融金属的侵蚀。
因此,面层耐火材料首先要化学稳定好,耐火度高,纯度高,另外,砂子粒度要小,比如一般所用都是100目的,砂粉也要相对细点300目,为的就是让铸件表面粗糙度好。
过渡层它主要是起连接作用,承上启下。
因此,它的砂子粒度要在面砂与背砂之间。
型壳的强度主要靠背层来实现。
我们经常会讲这一句,面层是负责铸件表面质量,而背层是负责尺寸精度的。
这句话可以说是型壳各层作用的一个概括。
第三点,型壳的预湿。
实际上预湿的作用就是加强层与层之间连接的紧密性。
硅溶胶制壳及型壳质量
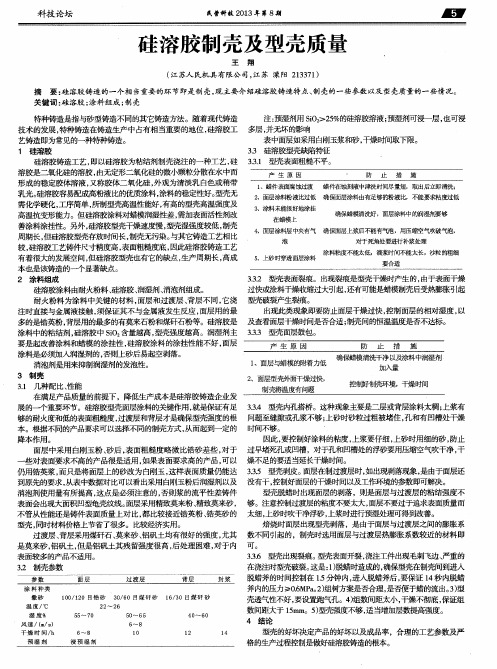
关键词 : 硅 溶胶 ; 涂料组成 ; 制壳
特种铸造是指与砂型铸造不 同的其它铸造方法 。随着现代铸造 注: 预湿剂用 S i O : >2 5 %的硅溶胶溶液; 预湿剂可浸一层 , 也可浸 技术的发展 , 特种铸造在铸造生产 中占有相当重要的地位 , 硅溶胶工 多层 , 并无坏的影响 表 中面层如采用白刚玉浆和砂 , 干燥时间取下限。 艺铸造即为常见的一种特种铸造。
多的是锆英粉 , 背层用 的最多的有莫来石粉和煤矸石粉等。硅溶胶是 及查看面层干燥时间是否合适 ; 制壳间的恒温温度是否不达标。 涂料中的粘结剂 , 硅溶胶中 S i O 含量越高 , 型壳强度越高。润湿剂主 3 . 3 . 3 型壳面层鼓包。 要是起改善涂料和蜡模的涂挂 陛, 硅溶胶涂料 的涂挂性能不好 , 面层 产 生 原 因 防 止 措 施
涂料是必须加入润湿剂的, 否则上砂后易起空剥落。 消泡剂是用来抑制润湿剂的发泡 l 生。 3 制 壳 3 . 1 几种 配 比 、 性能
1 、面层与蜡模的附着力低
2 、面层型壳外面干燥过 陕,
确保蜡模清洗干诤 以 及涂料中润湿剂
加入量
制壳将温度有 问 题
控带 子 制壳环境, 干燥时间
1 硅溶胶 3 . 3 硅溶胶型壳缺陷特征 硅溶胶铸造工艺 , 即以硅溶胶为粘结剂制壳浇注的一种工艺 , 硅 3 . 3 . 1 型壳表面粗糙不平。 溶胶是二氧化硅的溶胶 , 由无定形二氧化硅 的微小颗粒分散在水中而 产 生 原 因 防 止 措 施 形成的稳定胶体溶液, 又称胶体二氧化硅 , 外观为清淡乳白色或稍带 1 、蜡件表面腐蚀过渡 蜡 件在蚀刻液中津冼时间尽量短,取出后立即清洗 ; 乳光。 硅溶胶容易配成高粉液比的优质涂料 , 涂料的稳定性好。 型壳无 2 、面层涂料粉 液比过低 确 保面层涂料 由有足够的粉液比,不能要求粘度过低 需化学硬化, 工序简单, 所制型壳高温陛能好, 有高的型壳高温强度及
硅溶胶型壳精铸件生产经验点滴

硅溶胶型壳精铸件生产经验点滴(一)(2015-05-28 13:46:15)转载▼标签:硅溶胶金晟远科技精密铸造硅溶胶铸造化工自上世纪九十年代初引进硅溶胶型壳生产精铸件后,我国熔模精密铸造生产获得了飞速发展和长足进步。
至今采用中、低温蜡硅溶胶型壳工艺的工厂已近600多家,许多先进的工艺,高效的设备和优质的材料在精铸件生产中得到了应用和推广,铸件质量和生产率有了很大的提高。
近年来由于市场竞争,精铸行业的技术交流受到一定影响,许多工厂的技术革新和宝贵的生产实践经验未能及时推广和交流。
为此,作者收集了近年来国内部分硅溶胶型壳工艺精铸厂的生产经验、技术创造和小改小革,简要地向精铸同行介绍和推荐,希望有助于我国精铸件质量生产效率和工艺水平的提高。
限于篇幅和阅历,仅将在生产中已投入应用并取得实效的点滴经验摘要列出,期望能“抛砖引玉”,起到促进国内精铸业的经验交流广泛开展的作用。
以下内容按精铸件生产工序逐项进行介绍。
Ⅰ制蜡模(组)工序一.防止浇口杯“落砂”的措施1.“翻边”浇口杯的制作。
为减少铸件“砂孔”缺陷,无论中、低温蜡硅溶胶型壳均应采用“翻边”浇口(图一),在浇口(杯)模具上安放两个半圆镶圈,压蜡后浇口杯端面会形成凹槽(图二)。
制壳后浇口会形成光滑的“翻边”,能有效防止浇口杯边缘的砂壳落入型腔内造成铸件“落砂”。
2.“防砂盖”的合理结构。
大部分工厂应用碳钢平板(厚2毫米的冲压件)作浇口杯上的“防砂盖”。
在制壳后脱蜡前取下,经抛丸处理去除粘砂后再回用。
平板形盖易在抛丸后翘曲、变形。
若按图三形式采用凹凸的“帽式”盖,刚性大大提高,与浇口杯上平面接触面减少,制壳时不易出现缝隙防落砂效果更好,使用寿命可提高一倍以上。
3.低温蜡模组的浇口吊具。
由于硅溶胶型壳大多采用蒸汽脱蜡,故低温蜡组不宜沿用水玻璃型壳的木制浇口棒。
为能按放“防砂盖”及在脱蜡釜中便于安放模组,应与中温蜡一样采用可卸式手柄作浇口吊具。
低温蜡强度比中温蜡低,应根据浇口棒形式(直棒或丁字形、多叉型等)在制蜡棒时使用耐酸不锈钢制芯骨进行加固(图四、五、六),在使用长型芯骨时应在浇口棒模具上两端定位,防止芯骨移位。
精铸硅溶胶型壳工艺的改进
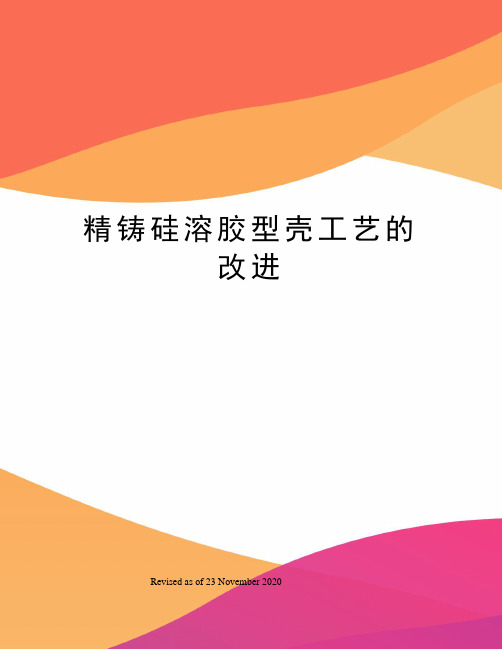
精铸硅溶胶型壳工艺的改进Revised as of 23 November 2020一.前言:众所周知,全球精铸界通用的硅溶胶型壳工艺存在三大缺点:1.成本高。
2.制壳周期长。
3.铸件脱壳性差(型壳残留强度高)。
据统计,表面层型壳通用的耐火料锆英石砂、粉占型壳原辅材料成本的4 8%,占总生产成本的10%(平均值)[1] 。
优质锆英石资源稀缺,因而寻找它的代用品或减少其消耗量是当今国内外精铸界共同关心,重点研究的课题之一。
“快干”硅溶胶的推广应用和真空干燥设备的逐步完善,缓解了制壳周期长的缺点。
由于硅溶胶型壳高温强度高(是水玻璃型壳的倍),其相应的残留强度也高(是水玻璃型壳的倍),因而铸件的脱壳性能比水玻璃差得多。
加之大部分生产的精铸件是结构复杂的中小件,型壳残留强度高会严重影响后处理工序生产效率和增加材料工时成本、降低铸件表面质量,延误交货期。
我们通过学习国内外同行的先进经验,经过多年的努力研究和实践,在降低硅溶胶型壳生产成本和改善脱壳性方面取得了一定成效,特向精铸界同仁作一介绍,以期达到抛砖引玉的目的。
二.表面层制壳工艺的改进:〈一〉. 锆英石粉料的代用—长期以来锆英石是全球精铸业首选的型壳表面层耐火料。
正如2007年美国精铸学会(ICI)第54届年会论文所言:“锆英石与多种合金反应低、密度高、热化学性能好,要寻找替代用品是困难的”。
[2]1.美国在2006年前面层涂料的典型工艺是在锆英粉中掺加5-10%(质量)的熔融石英粉。
其主要目的是:降低成本,提高铸件尺寸精度和改善脱壳性、透气性。
国外重点工艺改进方向是:充分利用熔融石英纯度高,杂质少,密度和热膨胀系数小,加上高温“析晶”,低温“相变”的特点,使型壳在高温时保持高强度而在低温时因相变产生剧烈收缩(%)致使型壳残留强度大大降低,从而使铸件脱壳性、透气性、尺寸精度提高。
自2007年起,通过技术改进美国已有80%的精铸企业表面层涂料中的熔融石英粉掺入量已提高至50%(按体积比为%)。
涂料制壳工序存在的几个常见的不足

涂料制壳工序存在的几个常见的不足硅溶胶模壳的缺点就是干燥时间长,而且越到后面越难干燥。
因此,干燥是硅溶胶涂料制壳的一道重要工序。
硅溶胶模壳通过干燥获取湿强度。
但是,在实际生产中,制壳现场经常存在一下一些不当之处,影响制壳干燥。
1.模壳摆放稠密,导致模壳干燥时间变长或者干燥不良。
在模壳干燥中,湿度是影响模壳干燥的第一大要素。
正是因为模壳内部涂料的湿度与外部环境有湿度差,才能保证模壳中水分蒸发。
模壳稠密堆积,局部湿度大,影响模壳内部水分蒸发速度。
对有些深腔,窄槽,不通孔类产品,可能还会造成同样干燥时间但干燥不良的情况。
2.有干燥线,但形同摆设。
顾名思义,模壳干燥线是用来干燥模壳的。
但是在有些企业中,由于工作习惯以及产品结构方面的原因,存在干燥线上悬挂的产品很少,而且结构相对简单,易干燥。
而真正需要上干燥线难干燥的产品,却放在架子上。
这是非常不合理的。
3.风扇数量不足或者有风扇不充分利用。
在涂料制壳背层模壳干燥时,风速是一个干燥的重要因素,而且要求立体风。
何谓立体风,就是四面八方都有风,促进模壳中的水分蒸发。
在生产现场经常存在风扇不开或者只开部分,这些都是造成模壳干燥不良的隐患。
另外,风扇分布也是制壳工序需注意的一个重要内容。
4.模组吊钩盖板不能正确使用。
模组使用吊钩盖板有两个作用。
一是便于悬挂,二是减少蜡污染。
但在现场经常存在两种情况:一是盖板是变形的,不能彻底盖住模组浇口杯的顶部;而是在沾浆时浆料进入模头的内部,既难清理而且污染蜡,给后面的蜡处理带来很大的麻烦。
5.涂料制壳现场是个环绕立体风的地方。
水分蒸发比较快。
但是好多单位设计时将浆桶(操作现场)与干燥室放在一起,而且经常不盖浆桶,很容易导致硅溶胶水分失去产生胶凝,进而变质,而且存在不补加水分(蒸发)。
6.涂料制壳现场经常是粉尘比较大,对干燥线以及浆桶、空调等设备性能发挥产生很大的副作用,必须及时对现场设备除尘,加油等。
如果做不到这点,可能会对设备的正常使用产生影响。
硅溶胶模壳脱蜡

硅溶胶模壳脱蜡
硅溶胶模壳在涂完所有层数后,经历至少24小时的干燥后,面临的下一道工序就是脱蜡。
脱蜡也是熔模精密铸造的一项重要工序,因为它涉及模壳的质量,所以不容小视。
硅溶胶模壳脱蜡的原理是:利用高压蒸汽产生的热量快速通过模壳表面,使蜡模表面瞬间熔化进而产生间隙,避免蜡模因加热膨胀从而导致模壳产生裂纹。
这里面重点是一个“快”字。
蒸汽压力要在模壳进入脱蜡釜内后短时间(10s-15s)升压到0.5-0.6MPa,只有这样,才能快速在模壳与蜡模的界面上熔化一部分蜡模,以使蜡模受热膨胀有足够的间隙,避免蜡模膨胀造成模壳破裂。
模壳脱蜡的效果与模壳本身的质量密切相关。
如果,模壳干燥不充分,脱蜡时也会造成模壳破裂。
这就是上面提到的,每层都要充分干燥,最后挂完料后还要至少干燥24小时,有深孔,窄槽等特殊结构的产品还要放置更长时间,使模壳充分干燥,避免脱蜡导致模壳破裂。
另外,出蜡不畅也会造成模壳破裂。
对于异型,脱蜡不畅的产品,厚大的产品除了增加模壳厚度外,还必须多设置出蜡口来减少脱蜡缺陷。
再者,脱蜡的残余有时焙烧不干净,会对铸件质量有影响。
因此,影响模壳脱蜡质量的因素有蜡模浇注系统设计(主要是排蜡),模壳的厚度,模壳的干燥质量以及脱蜡釜升压速度等几个方面,需要各方面综合考虑。
硅溶胶的危险分析方法是
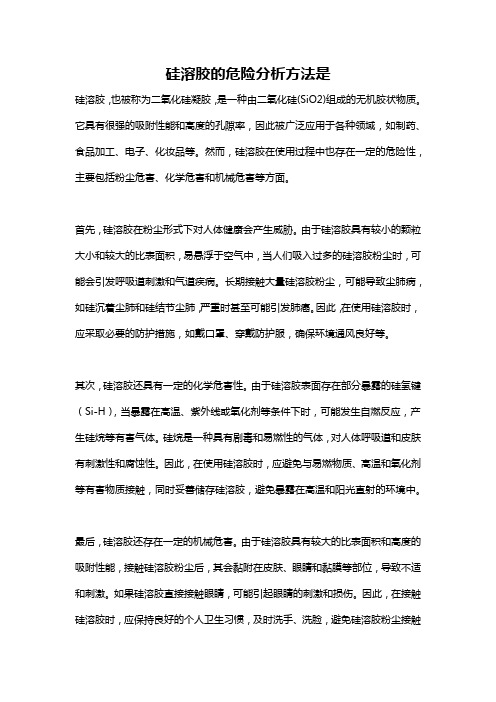
硅溶胶的危险分析方法是硅溶胶,也被称为二氧化硅凝胶,是一种由二氧化硅(SiO2)组成的无机胶状物质。
它具有很强的吸附性能和高度的孔隙率,因此被广泛应用于各种领域,如制药、食品加工、电子、化妆品等。
然而,硅溶胶在使用过程中也存在一定的危险性,主要包括粉尘危害、化学危害和机械危害等方面。
首先,硅溶胶在粉尘形式下对人体健康会产生威胁。
由于硅溶胶具有较小的颗粒大小和较大的比表面积,易悬浮于空气中,当人们吸入过多的硅溶胶粉尘时,可能会引发呼吸道刺激和气道疾病。
长期接触大量硅溶胶粉尘,可能导致尘肺病,如硅沉着尘肺和硅结节尘肺,严重时甚至可能引发肺癌。
因此,在使用硅溶胶时,应采取必要的防护措施,如戴口罩、穿戴防护服,确保环境通风良好等。
其次,硅溶胶还具有一定的化学危害性。
由于硅溶胶表面存在部分暴露的硅氢键(Si-H),当暴露在高温、紫外线或氧化剂等条件下时,可能发生自燃反应,产生硅烷等有害气体。
硅烷是一种具有剧毒和易燃性的气体,对人体呼吸道和皮肤有刺激性和腐蚀性。
因此,在使用硅溶胶时,应避免与易燃物质、高温和氧化剂等有害物质接触,同时妥善储存硅溶胶,避免暴露在高温和阳光直射的环境中。
最后,硅溶胶还存在一定的机械危害。
由于硅溶胶具有较大的比表面积和高度的吸附性能,接触硅溶胶粉尘后,其会黏附在皮肤、眼睛和黏膜等部位,导致不适和刺激。
如果硅溶胶直接接触眼睛,可能引起眼睛的刺激和损伤。
因此,在接触硅溶胶时,应保持良好的个人卫生习惯,及时洗手、洗脸,避免硅溶胶粉尘接触眼睛等敏感部位。
总的来说,对硅溶胶的危险分析方法包括了对其粉尘危害、化学危害和机械危害的分析。
合理使用和管理硅溶胶,采取必要的防护措施和个人卫生措施,可以有效降低其危害对人体健康的风险。
硅溶胶模壳的强度

硅溶胶模壳的强度
硅溶胶模壳的强度一般来讲,取决于硅溶胶中SiO2含量的多少,一般硅溶胶精密铸造使用的硅溶胶有两种规格,Si02含量为30%和26%o 硅溶胶模壳的强度分为三种:湿强度,高温强度以及残余强度。
在这三个强度中,湿强度也称为模壳的常温强度,它取决于模壳的干燥程度,可以说模壳的常温强度高,那么它就经得起转运以及脱蜡的考验。
高温强度指的是模壳区空焙烧或浇注时模壳的强度,它取决于硅溶胶在高温下形成的硅氧键以及粘结剂与耐火材料的反应产物。
高温强度低,模壳在焙烧和浇注时会发生变形和破坏。
残余强度指的是模壳浇注后清壳时的强度,模壳残余强度低,铸件清理时效率高。
一般来讲,模壳的残余强度与高温强度成正相关关系,模壳的高温强度高,残余强度也高。
理想的状况是模壳的湿强度高,高温强度足够,残余强度低。
当然这要综合考量。
硅溶胶精密铸造缺陷分析
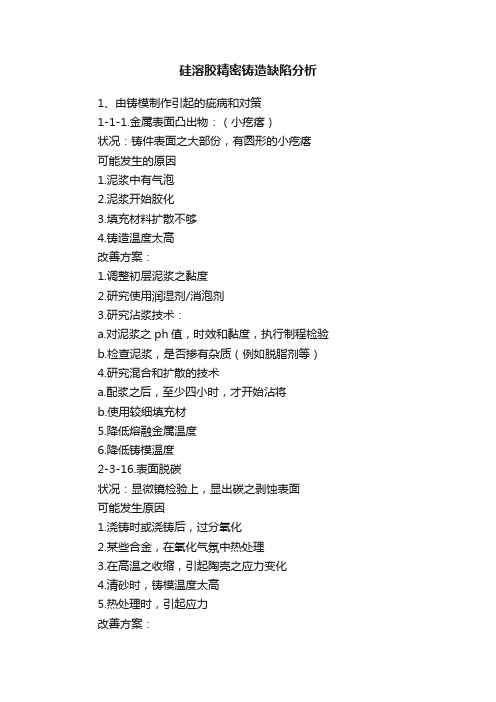
硅溶胶精密铸造缺陷分析1、由铸模制作引起的疵病和对策1-1-1.金属表面凸出物:(小疙瘩)状况:铸件表面之大部份,有圆形的小疙瘩可能发生的原因1.泥浆中有气泡2.泥浆开始胶化3.填充材料扩散不够4.铸造温度太高改善方案:1.调整初层泥浆之黏度2.研究使用润湿剂/消泡剂3.研究沾浆技术:a.对泥浆之ph值,时效和黏度,执行制程检验b.检查泥浆,是否掺有杂质(例如脱脂剂等)4.研究混合和扩散的技术a.配浆之后,至少四小时,才开始沾将b.使用较细填充材5.降低熔融金属温度6.降低铸模温度2-3-16.表面脱碳状况:显微镜检验上,显出碳之剥蚀表面可能发生原因1.浇铸时或浇铸后,过分氧化2.某些合金,在氧化气氛中热处理3.在高温之收缩,引起陶壳之应力变化4.清砂时,铸模温度太高5.热处理时,引起应力改善方案:1.筹模内或其周围,使用含碳之物质2.浇铸后立即将铸模置于还原气氛中3.在真空或保护性气氛中,进行浇铸和冷却4.执处理时,避免氧化气氛5.使用复碳热处理6.再渗碜7.容器中掺杂缓冲之物质,如起纹石棉8.在较低温度清砂9.热处理时,确使铸件,有正确的支撑,并使用正确的淬火技术1-2变形状况:铸件之几何外形,志蓝图不符可能发生原因1.几何外形及/或浇道系统,引起不均匀之收缩2.浇口收缩或铸件部份受到拉力3.高强度铸模,阻止均匀之收缩4.由于玻质之背砂材料,跟其容器改善方案1.以下术方法,将不均匀之应力,减至最小程度a.改善铸造方案b.使用腹板、圆角及击棒等2.检查浇道系统并改善之,以减少应力,如:a.网液由铸件之一端流入b.环件使用多浇口设计或内十字浇道c.降低铸模之强度d.使用不玻化之背砂材料2-3-14熔融点或麻点状况:许多重复暗色之凹点,分布在整个铸件表面可能发生原因1.高铬铁合金之表面氧化改善方案1.浇铸之时,或一浇铸完毕,采取下术方法:a.铸模材料内,或铸模周围,使用含碳材料b.浇铸后随即将铸模置于还原气氛中c.在真空或保护性氯氛中,进行浇铸及冷却2-1气孔(金属与铸模反应)状况:圆凹孔通常呈现光亮之表面可能发生原因a.不正确的烧成操作b.铸模或铸模材料的不洁改善方案:a.增加铸模烧成温度及/或时间b.检查并在必要时调整烘模炉内的气氛c.避免铸模或铸模材料的污染2-2气孔(金属本身)状况:圆凹孔通常呈现光亮之表面可能发生原因:a.脏湿的装炉材料b.脱氧不够改善方案:a..保护装炉材料与熔液表面接触的物作,必须清净和干燥b.修正脱氧程序2-3气孔(卷入空气)状况:平滑之凹孔,通常呈现被氧化之表面(一般发生于表面之最上端)可能发生原因:a.铸模内扰流过多b.铸模透气性太差改善方案:1.改善烧口技术,以减少扰流2.采用能够自动通气之铸模3.增加铸模透气性4.使用失压浇铸5.增加铁水静压力,方法如下a.空气压力b.增加浇口杯高度c.离心浇口3-1流不到状况:铸件不完整,流不到的地方呈圆边可能发生原因:1.缺乏断面太薄2.浇道设计不良3.铸模透气性太差4.浇铸透气性太差5.浇铸速率太低6.浇铸时液流停顿改善方案:1.增加铸模及/或金属温度2.考虑修正金属成份,以增加流动性3.假如可能,增加铸件断面4.延伸断面,浇铸后修整5.改善浇铸设计6.增加铸模透气性7.薄肉处设通气孔8.增加浇铸速率,但避免卷入空气9.浇铸时,液流不可中断4-1冷断状况:金属液流会合处,发生圆接边之裂缝可能发生原因:1.两股金属液流,未能融合2.缺乏流动性3.浓稠炉滓,致增加表面张力4.金属液对模穴表面张力太高5.金属液滴未能与整体金融合改善方案:1.改善浇口技术2.增加浇铸速率3.增高金属及/或铸模温度4.考虑修正金属成份,以增加流动性5.在控制下的大气或真空中,熔解和浇铸6.改变初层壳之材料,例如将氧化铝改为锆粉7.铸模内之金属液流,要避免飞溅2-3-8 收缩应力拉裂状况:晶粒间之裂痕,呈现光亮结晶之表面可能发生原因:1.铸件收缩之拘束2.铸件形状特殊,引起内部的应力3.某些合金,异常的冷却速率,造成脆弱构造改善方案:1.降低铸造强度2.改善铸造方案,避免收缩之拘束3.改善铸造方案,减少应力4.改善铸造情况,如提高模温5.铸件仍温热时,进行清砂和切断作业6.清砂和切断作业前,先消弛应力7.改善冷却速率,以适应某些特殊合金4-2热裂状况:粒间崩裂,呈现出被氧化的断口面可能发生原因:1.有内部尖角2.不正确的补给系统设计3.高温时铸件的收缩,受到拘束4.铸造方案断面变化过大5.不正确的铸造情况6铸造过后早移动改善方案:1.确使有适当的圆角2.检查并改善补给系统,使铸造应力,降至最小3.降低铸模强度4.改善铸造方案,避免收缩之拘束5.利用较慢之冷却速率6.改善铸造方案和铸件设计7.改善铸造情况,如提高模温8.确实完全凝固后才移动2-3-6大的内部缩孔状况:以放射线检验或切片,现出大的、不规则的内部缩孔可能发生原因:1.不适当或不正确的补给2.不正确的铸造情况3.不正确的凝固速率改善方案:1.有关之区域,确使有适当的补给,以改善方向性凝固2.建立正确的铸造情况,例如铸模和浇铸温度3.检查制模技术4.改良铸造方案,以改善方向性凝固5.在浇口杯或冒口,使用发热材料5-1内部缩孔状况:以放射线检验及/或目检/微视检查,现出散开或直线型孔洞可能发生原因:1.不适当或不正确的补给2.不正确的铸造情况3.不正确的凝固速率改善方案:1.有关之区域,确实有适当的补给,改善方向性凝固2.建立正确的铸造情况,例如铸模和浇铸温度3.检查制模技术4.改良铸造方案,以改善方向性凝固5.在浇口杯和冒口,使用发热材料6-1表面收缩状况:表面凹凸陷或不规则凹穴,有时呈现树枝状可能发生原因:1.铸模内发生热点2.不适当的补给3.铸模及/或金属熔液之温度过高改善方案:1.消除锐角2.减少铸件内较大的断面变化3.确使模型之间,适当的间隙4.尽可能使浇口,能让熔液以切线方式,流入模穴5.确使有适当的金属熔液之补给6.降低铸模温度,假如可能,也降低金属熔液之温度7-1表面夹滓状况:不规则孔穴,可能有包含耐火材料之痕迹可能发生原因:1.耐火物进入铸模之模穴,造成夹滓a.来源为:b.坩埚c.铸模;背砂材料;不洁的制程情况d.熔解材料中,含有耐火物改善方案:1.确实运用正确坩埚2.确实运用正确操作技能3.以正确的铸模运作技术及制程情况,避免多余材料,进入模穴4.确实供应干净的熔解材料8-1表面夹滓状况:薄黑膜或飘带纹,在铸件表面形成不规则图案可能发生原因:1.装炉材料太脏2.熔解中,如钛和铝等活性元素的氧化改善方案:1.确实使用不含氧化物的熔解材料2.以真空或保护性气氛熔解,避免活性元素的氧化2-3冶金学上的疵病和对策8-2表面夹滓状况:通常为平滑的表面凹穴,有或没有黑色的玻璃质包住的材料痕迹可能发生原因:1.装炉材料太脏2.熔解中易受强氧化气影响的材料3.坩埚与金属作用4.浇铸当中,炉滓陷入改善方案:1.确实采用干净的熔解材料2.除去所有外来杂物,如锈皮3.确实运用正确的熔解技术,如以炉滓覆盖,降低氧化气4.采用正确的的坩埚5.采用正确的熔解技巧6.浇铸前,尽可能在最低温度除滓7.改善脱氧操作8.使用茶壶式浇斗9.研究撇滓方法(除渣剂)9-1剥砂痕状况:铸件之表面,有狭窄之圆角槽沟,喷砂之前,沟内可见到氧化物存在可能发生原因:1.初层壳相对于整个陶壳,具有较高的膨胀2.初层与次层陶壳,结合性不良3.铸件表面或初层壳耐火材料,缺乏应力消除的因素4.铸模温度太高5.金属与铸模发生反应6.熔液脱氧中,产生硅酸物改善方案:1.初层壳使用较低膨胀之填充材,或背砂层使用较高者2.初层壳使用之敷砂粒,要较为多角形、较粗及较为均匀的粒度分布,其膨胀系数,要在初层泥浆与背砂层泥浆之填充之间3.铸件表面,以绫纹线或加强筋,来解除大平面,但必须易于处理磨掉4.降低铸模温度5.改善浇道系统,降低扰流6.尽可能以最低的铸模与金属熔液之温度,进行浇铸7.增加初层壳之耐火度8.改善脱氧之操作10-1初层壳之夹滓状况:于铸件表面,有不规则之板状印痕,喷砂后常有耐火材料黏附其上可能发生原因:1.初层壳的剥裂2.组树焊黏太差,致在接合处,渗入初层浆改善方案:1.沾浆前,确使腊簇有效的脱脂2.确使初层壳,正确干燥3.确使初层与次层包模材料,热膨胀兼容4.初层与次层,确能楔住,例如初层勿用太细敷砂粒;次层作业之前,确使初层,获得适当湿润5.初层浆黏度正确,以免干裂6.注意品质10-2铸模破裂状况:铸件表面上,有不规则之多余金属飞边可能发生原因:铸模的破裂,由于:1.铸模制作及/或干燥过程中,腊的膨胀2.脱腊中腊型的膨胀(注意:PS塑料之模型,大小需要限制,才能成功的脱腊)3.腊簇上有部分陶壳太薄4.不适当的铸模强度改善方案:1.避免温度变化过大2.避免初层壳干燥过速3.脱腊时,保证有足够的初始热量,施于铸模4.检查黏结剂与脱腊媒质,是否要容5.脱腊操作之系统中,保证有高的热容量,也有快速的动作6.确使覆盖均匀7.易成薄壳之处,施以特别的沾敷作业8.增多层数,补充陶壳强度9.调整黏结剂的成分10.确使陶壳的厚度均匀11.研究陶壳强化技术10-3砂心崩溃状况:砂心孔穴之尺寸,超出要求公差,且通常含有金属可能发生原因:1.预先成型陶心的拱弯2.射腊中预先成型陶心的破裂3.铸模烧成或浇铸时破裂改善方案:1.确使预先成型陶心,有适当的耐火度2.烧铸中避免金属液道接冲击砂心3.在陶心之一端或两端,加上腊垫,以缓冲任何轻微的膨胀差异4.检查陶心和砂心头,会不会造成压碎5.改善射腊技术11-1砂心崩溃状况:砂心孔穴之部分,突出多余金属(通常在铸件上,有耐火材料之夹滓)可能发生原因:1.砂心长度与其截面积之比太大,致无法以一般沾浆制模技术,制出完整的砂心2.腊型上狭小的内部孔槽,其沾敷之困难,令人不满意改善方案:1.使用预先成型之陶心2.采用简易砂心成形之胶化法(请参考拙著第三编<精密铸造模的制作>,第十二章陶心制造方法)3.使用较稀之泥浆和较细的敷砂粒4.使用预先成型之陶心12-1疤痕状况:铸件表面岛状之多余金属,在多余金属与铸件之间,可能夹有耐火材料可能发生原因:1.与背砂层之黏结较差2.初层壳吸入湿气3.初层和次层壳之间,具有不同的膨胀应力4.陶壳的烧成强度,不足以承担金属熔液的压力5.腊型中的沟槽或孔洞,或者组树之间隙,太过狭小,致在进行下层之间,业已“结桥”6.砂心未干,次层沾浆中,已埋没者补溶出改善方案:1.确有适当的敷砂,将初层与次层楔住2.使用较粗或更多颗粒之敷砂粒3.增加干燥时间及/或改善干燥设备4.保证脱腊前,适当干燥5.确使初层壳与背砂层之热膨胀,不相冲突6.增多陶壳层数,或采用成分含量,更高的黏结剂,以增加陶壳强度7.确使陶壳厚度均匀8.重新设计腊簇的组合,增加腊型的间隙,以帮助泥浆的流通9.使用较稀的泥浆与细小的敷砂粒10.使用预先成型之陶心11.确保各层之砂心孔,完全硬化与干燥13-1金属表面凸出物:状况:金属表面凸出可能发生原因:1.陶壳湿态强度太低,无法承受脱腊时的热膨胀2.初层浆由模型尖角处流失,致引起剥落3.初层浆太厚4.初层浆老化(由于逐渐胶化,使黏结剂之黏度增加)改善方案:1.增长每一层陶壳的干燥时间2.增加陶壳之层数3.最后层的干燥时间延长4.重新设计腊簇之组合,俾能在脱腊时,更快速传热,到达陶壳模之所有部份5.使腊型之孔穴,形成的砂心,含有通气孔6.脱腊时,确有适当的初始传热速率,注意升压时间7.确使初层浆,分布均匀8.采用正确的润湿剂及/或悬浮剂,以使浆液之流动性正确9.模型倒角10.降低黏度11.检查浆液之PH值随兴时效14-1金属表面凸出物状况:铸件表面上岛形多余金属,常与铸件边角上之飞边同时出现可能发生原因:1.初层壳的破裂,使背砂层之泥浆,穿入于腊型与初层壳之间,未将其间空隙占满2.初层陶壳厚薄不均,造成不同的干燥速率3.敷砂前初层浆已经干燥改善方案:1.确实将腊型清洗干净,且使其沾浆时,具有良好的润湿性2.确使敷砂粒,黏着于初层浆的整个区域,且在进行下一层之前,将虚悬之颗粒振落3.铸模制作区,要控制温度与温度,以减少浆层破裂机会4.使用较粗或较多角形颗粒之敷砂粒15-1金属表面凸出物状况:耐火材料烧结的一般的铸件表面粗糙可能发生原因:1.金属熔液与初层陶壳,发生反应2.初层陶壳之填充材或敷砂材,有外来物质或杂质,会与熔融金属起反应改善方案:1.使用更耐火之初层浆填充材及或黏结剂2.降低铸模或金属熔液温度3.以磁铁检查铸模材料,是否含有游离铁或氧化铁4.检查材料之储存区域5.检查浆桶之状况6.确使搅伴设备不生锈16-1金属表面凸出物状况:在水口附近有小圆疙瘩可能发生原因:1.在浇口附近有热点,而使其恶化改善方案:1.增长浇口及/或组树中,使腊型间隙宽些,俾能加快冷却速度2.使用较细之浇道3.使陶壳稍薄(减少层数)4.降低浇铸温度5.降低铸模温度。
硅溶胶稳定性问题

高纯硅溶胶成分标准物质稳定性研究(2009-12-07 14:13:10)注:本文原发表于《功能材料》2005年9月,如需PDF原文,请留下邮箱,注明所需文章即可。
王少明,赵华,王爱萍,荀其宁,云俊鲜摘要:考察了高纯硅溶胶成分标准物质研制过程中影响稳定性的因素。
根据高纯硅溶胶的物理化学性质,研究了影响高纯硅溶胶稳定的pH值、粒度分布、电解质等主要因素。
提出了保持高纯硅溶胶稳定的措施,解决了高纯硅溶胶成分标准物质的稳定性问题,使标准物质稳定保存1年以上。
关键词:高纯硅溶胶;标准物质;稳定性;粒度分布;电解质硅溶胶也称胶体二氧化硅,是无定性二氧化硅胶体粒子在水溶液中的稳定分散系,其分子式可表示为:m SiO2 ·H2O,它是由硅酸分子聚合成的带电荷分子团簇,单体之间通过扩散快速聚合成交联的SiO2颗粒结构。
在单体浓度很高时,聚合速度很快并形成SiO2凝胶;当单体浓度较低时,可形成SiO2颗粒的悬浮体系即胶体。
高纯硅溶胶可用于复合材料的填充、增密,大大地提高材料的耐高温性,并具有透波性好、抗激光辐射等特点。
主要用于电子制造业、国防科技工业等行业。
国外在航天飞行器和中远程导弹导引头的三向石英天线窗中已有应用。
由于自身特性的原因,高纯硅溶胶稳定周期一般比较短,要将其作为标准物质使用,必须解决稳定性的问题。
要保证高纯硅溶胶成分标准物质的稳定性,首先要解决高纯硅溶胶物料的稳定性。
笔者采用工业水玻璃(硅酸钠)为原料制备高纯硅溶胶,通过添加中性盐制备高纯硅溶胶成分标准物质。
在此基础上,研究了影响高纯硅溶胶稳定性的pH 值、粒度分布、电解质、温度、SiO2浓度等主要因素。
提出了保持高纯硅溶胶稳定性的措施,使高纯硅溶胶能稳定地保存1 a以上,满足了标准物质使用、储存、运输的技术要求。
在16个月内对标准物质特性成分量进行了考察,考察结果表明满足标准物质稳定性的要求。
1 高纯硅溶胶成分标准物质的制备选用适当粘度和浓度的硅酸钠溶液,将其稀释过滤后的清液依次顺流通过再生、淋洗合格的阳离子树脂床和阴离子树脂床,依次除去硅酸钠溶液中的金属离子和酸根离子,形成硅酸溶液。
- 1、下载文档前请自行甄别文档内容的完整性,平台不提供额外的编辑、内容补充、找答案等附加服务。
- 2、"仅部分预览"的文档,不可在线预览部分如存在完整性等问题,可反馈申请退款(可完整预览的文档不适用该条件!)。
- 3、如文档侵犯您的权益,请联系客服反馈,我们会尽快为您处理(人工客服工作时间:9:00-18:30)。
硅溶胶型壳常见缺陷及防止措施1.型壳表面粗糙:
2.型壳面层裂纹:
特征产生原因防止措施
型壳表面层出现不规则的裂纹,或出现极细小的龟状裂纹这些裂纹是型壳干燥时产生的,主
要是由于面层干燥过快,或涂料干
燥收缩过大引起的,或由于蜡模热
膨胀使面层型壳被胀裂.及型模焙
烧不当引起.具体产生原因:
1.环境相对湿度太低
2.面层干燥时间过长
3.空气流动不均匀而且过大
4.环境温度变化过大
5.壳模焙烧不当.
1.面层干燥区相对湿度宜在RH60~
70%之间.
2.面层干燥时间以4~6h为宜,特殊
产品不要超过10h.
3.风不要正对模组吹,应降低直接吹
到模组上的气流量.
4.制壳间温度应严格控制,保持在
22~25℃之间.
5.脱蜡后壳模应在至少4h后装炉焙
烧.尽量避免高温-低温-高温焙烧
及二次焙烧.
3.型壳面层鼓裂:
特征产生原因防止措施
型壳面层局部与蜡模分开向外鼓起(图a),或鼓起后破裂导致背层涂料流到蜡模和面层之间,但未将空
隙填满(图b、图c)., 1.面层型壳与蜡模间附着力太
差
1.确保蜡模清洗好.
2.面层涂料润湿剂加入量合适.
2.面层型壳外表面干燥过度、内
表面干燥不足.
1.控制好环境相对湿度、面层干燥时
间和风速,确保面层型壳外、内表面
干燥合适.
2.应使面层涂料厚合适,不要过厚.
3.面层型壳湿强度不足,特别是
在蜡模锐角处其强度低
1.保证面层型壳湿强度.为此,要保证
硅溶胶和耐火材料的质量,按工艺规
范保持涂料正确配方,配制方法及确
保涂料性能合格.
2.要保证蜡模锐角处有一定厚度的
涂料,且涂料不要滴得过干.
4.制壳间温度不均匀保持制壳间温湿度均匀.
4.型壳内孔搭桥:
特征产生原因防止措施内孔、凹槽处的型壳不致
密,局部有未上好涂料,未撒上砂使该处型壳存在孔隙搭桥. 1.第一层或背层涂料太稠.
2.孔洞或狭缝处浸浆不足.
3.撒砂过粗,以致孔洞或狭缝
处很快就被塞住.
4.孔洞或狭缝处松散砂粒在
浸下层浆时未被清除掉.
5.内孔或凹槽处型壳干燥不
足.
1.控制好第二层和背层涂料粘度.
2.细致地上孔洞或狭缝处的涂料.
3.撒砂使用较细的砂,防止孔洞或
狭缝处过早被塞住.
4.注意将孔洞或狭缝处松散的浮
砂吹除,再上下层涂料.
5.注意内孔或凹槽处型壳干燥情
况,不干时不能制作下层模壳.
5.型壳面层剥落:
特征产生原因防止措施
型壳型腔尺寸变大,表面不光洁. 面浆与蜡型的附着力太差
1.改善蜡模蚀刻清洗,利用溶剂轻微腐
蚀蜡模表面以增强其与浆层的吸附
力.
2.破坏宽大之平面,在宽广平面上加上
若干凸出物或筋,减少平面宽广程度,
以利浆附着.
3.在型蜡中添加一些亲水性物质,改善
蜡的亲水性,也可有效增强面浆与蜡
型的吸附力.
面层在制下层型壳过程中剥落,这是
由于面层还没有干燥就制第二层型
壳,硅溶胶发生回溶现象,使面层型壳
剥落.
控制好环境相对湿度、温度、风速和干燥
时间,确保面层干燥后再做第二层.
面层干燥过快或过度
增加面层干燥区的的湿度,一般为
RH60~70%,但在特殊有深穴如盒状铸件
内部不易干燥的状况,甚至相对湿度设定
为70~80%.减少空气的流速,避免内外
速率相差太大,外部本就较易干燥,若再
加风吹,则外部已干燥过度,而内部尚未
干燥,因此减少空气流动,对拉动内外干
燥一致有较大助益.
相对湿度愈高,风速愈小,则室内的干湿
球温差愈小,如此,可避免壳型在干燥初
期,因为快速干燥蒸发水汽,温度急降而
使蜡型收缩,待干燥后,蜡型又因吸收室
内温度而而升温膨胀,如此缩胀,轻则龟
裂,重则剥落.
6.型壳强度低:
7.型壳裂纹:
8.气泡、毛刺:
9.未润湿:
10.壳模破裂:
11.壳模层间剥落:
12.壳模鼓胀变形、强度不足:。