FCVA镀膜及其应用
FCVA镀膜及其应用

在中国缝制机械行业“十二五”时期主要技术攻关方向中,新材料、新工艺是一个重要领域。
在“十一五”期间的行业科技开发实施指南中,新材料、新工艺在产品中的开发与应用就已经是重要内容,主要体现在无油、微油润滑材料和特种材料涂覆工艺的应用与开发,通过在缝制机械的高速运转部件采用耐磨材料涂覆技术,实现无油或微油润滑。
材料及其涂覆工艺的发展与进步,对缝制机械的性能、品质的提升有积极的促进作用。
尤其在高速自动化缝纫机的品种和数量均大幅增加的情况下,如何通过新材料、新工艺的应用满足和提升高速自动化缝纫机的各项性能要求,是缝制机械制造商正在考虑的事情。
目前应用于缝制机械的新材料很多,比如多元填充高分子材料、陶瓷、金属钛、特氟龙、低温液态化油脂等。
而陶瓷、金刚石粉、钛合金、多元填充高分子材料等特种材料的涂覆工艺也在不断改进并且越来越多地应用于缝制机械中。
镀膜,是应用新的材料及新的涂覆工艺较多的一道工序。
已经有不少高速自动化缝纫机的零部件在镀膜时采用了新膜层材料和新镀膜方式。
我们知道,镀膜涉及两项基本内容,一是镀膜的技术与方法,二是所镀膜层的材料。
不同的镀膜方式,所达到的镀膜效果不同,膜层的性能发挥情况也随之有差异,而采用不同的镀层材料也有不同的性能表现。
1 不同的镀膜技术在微观环境下看,镀膜就是将一些物质(反应物)的分子、原子或者离子通过一定的方式被分解出来在其所具有的能量作用下涂覆(沉积)在需要镀膜的工件(基体)上。
镀膜时,要考虑膜层、工件材料的物理或化学性质,选择合适的镀膜方法将膜层紧紧地附着于工件上并且要产生好的性能效果。
真空镀膜技术就是在真空环境下,通过化学、物理方式将反应物或者靶材沉积到基体上的薄膜气相沉积技术。
镀膜通常需要在干净、纯粹的真空环境下进行,既为了避免污染(减少成膜过程中气体分子进入薄膜中成为杂质的量),也在于膜层材料的分子、原子化学性活跃,在常温常态下容易出现问题(比如分子间的碰撞、氧化反应)。
ald镀膜工艺
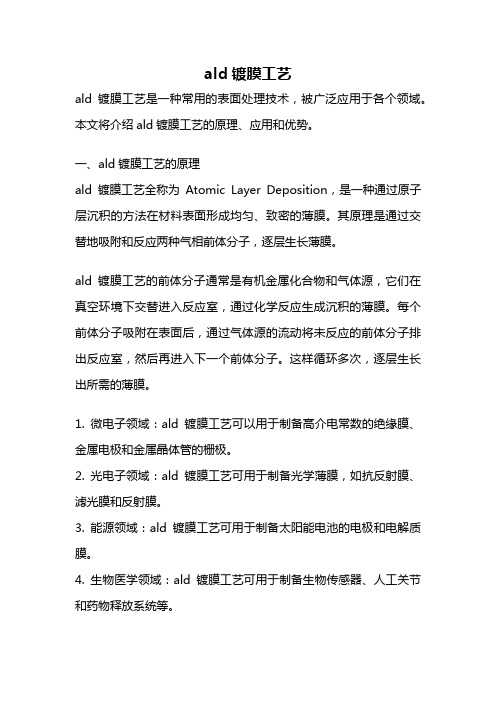
ald镀膜工艺ald镀膜工艺是一种常用的表面处理技术,被广泛应用于各个领域。
本文将介绍ald镀膜工艺的原理、应用和优势。
一、ald镀膜工艺的原理ald镀膜工艺全称为Atomic Layer Deposition,是一种通过原子层沉积的方法在材料表面形成均匀、致密的薄膜。
其原理是通过交替地吸附和反应两种气相前体分子,逐层生长薄膜。
ald镀膜工艺的前体分子通常是有机金属化合物和气体源,它们在真空环境下交替进入反应室,通过化学反应生成沉积的薄膜。
每个前体分子吸附在表面后,通过气体源的流动将未反应的前体分子排出反应室,然后再进入下一个前体分子。
这样循环多次,逐层生长出所需的薄膜。
1. 微电子领域:ald镀膜工艺可以用于制备高介电常数的绝缘膜、金属电极和金属晶体管的栅极。
2. 光电子领域:ald镀膜工艺可用于制备光学薄膜,如抗反射膜、滤光膜和反射膜。
3. 能源领域:ald镀膜工艺可用于制备太阳能电池的电极和电解质膜。
4. 生物医学领域:ald镀膜工艺可用于制备生物传感器、人工关节和药物释放系统等。
三、ald镀膜工艺的优势1. 高均匀性:ald镀膜工艺可以在几个原子层的尺度上控制薄膜的生长,使得薄膜厚度均匀性非常高。
2. 高精度:ald镀膜工艺可以通过控制前体分子的进入时间和反应时间来实现对薄膜厚度的精确控制。
3. 低温生长:ald镀膜工艺通常在较低的温度下进行,不会对底层材料产生热损伤,适用于对温度敏感的材料。
4. 薄膜质量优良:ald镀膜工艺可以得到致密、均匀、无孔隙的薄膜,具有优异的光学、电学和机械性能。
ald镀膜工艺是一种先进的表面处理技术,具有高均匀性、高精度、低温生长和薄膜质量优良等优点。
它在微电子、光电子、能源和生物医学等领域有着广泛的应用前景。
随着科技的不断发展,ald镀膜工艺将进一步完善和应用,为各个领域的发展提供更多可能性。
DLC薄膜制备和检测技术综述
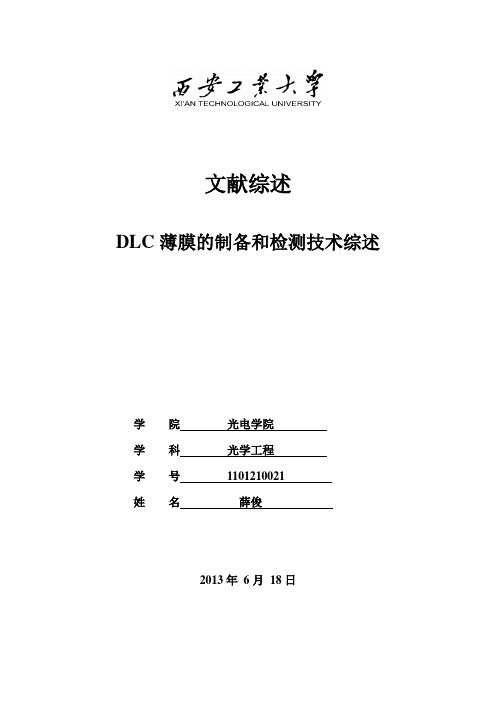
文献综述DLC薄膜的制备和检测技术综述学院光电学院学科光学工程学号1101210021姓名薛俊2013年6月18日前言20世纪70年代初,Aisenberg[1]和E.Gspenc[2]分别次采用离子束沉积技术(IBD)和碳气相离子束增强沉积(IBED)技术制备了绝缘碳膜,命名该膜为DLC[1]。
20世纪70年代末,前苏联研制的DLC膜的硬度已经达到15000(维氏硬度)[3]。
DLC薄膜具有生产工艺简单,性能优良等特点。
20世纪80年代中期,在世界范围内掀起了研究、制备、开发和应用DLC膜的热潮。
厚度为100μm、表面粗糙度<10nm的DLC膜己经被美国通用原子公司(GA)利用PECVD制造出来[3]。
我国在制备DLC膜研究、应用方面也去得了长足的进展,不过与发达国家相比,差距还是存在的。
现在DLC膜还有很多问题存在争议或尚未解决。
这也问题严重制约了DLC膜的研究发展,现在,随着DLC制备技术的日益完善以及社会对DLC膜的需求量的增加,DLC 膜的应用研究价值也日益凸显。
1 DLC薄膜概况1971年德国的Aisenberg 采用碳离子束首次制备出了具有金刚石特征的非晶态碳膜,由于所制备的薄膜具有与金刚石相似的优异性能,Aisenberg于1973年首次把它称之为类金刚石(DLC)膜[1]。
DLC膜有着和金刚石几乎一样的性质,如高硬度、耐磨损、高表面光洁度、高电阻率、优良的场发射性能,高透光率及化学惰性等,它的产品广泛应用在机械、电子、光学和生物医学等各个领域。
尤其在光学领域,该技术在光学薄膜制造及其应用方面, 突破了大面积、高均匀性、高透射比、抗激光兼容的红外减反射膜镀制关键技术, 并在军事和民用上得以应用。
DLC膜的沉积温度低、表面平滑,具有比金刚石膜更高的性价比,且在相当广泛的领域内可以代替金刚石膜,所以自80年代以来一直是研究的热点。
碳是类金刚石膜的主要成分。
碳元素有3种同素异形体,即金刚石、石墨和各种无定形碳。
6.第六讲-正确选用类DLC涂层工艺

第六节正确选用DLC (类金刚石)涂层类金刚石diamond-like carbon,简称DLC薄膜,涂层的主要成分为碳,是以sp3、sp2键结合为主体,并混合有少量sp1键的远程无序立体网状非晶态结构,这种结构使得DLC薄膜具有一系列优良的物理化学性能,如红外波段透明、硬度高、摩擦系数小、化学性能稳定、热膨胀系数小等,从而使该薄膜在光学、电学、材料、机械、医学、航空航天等领域广泛应用。
由于制备技术和方法不同,DLC膜可能完全由碳元素组成,也可能含有大量的氢,因此一般来说,可将DLC薄膜分为含氢碳膜和不含氢碳膜。
根据薄膜中原子的键合方式(C-H、C-C、sp3、sp2等)及各种键比例不同,DLC膜又有不同的称谓:◎非晶碳(amorphous carbon,a-C)膜,膜中sp2键含量较高;◎含氢非晶碳(hydrogenated amor-phous carbon,a-C:H)膜;◎四面体非晶碳(tetra-hedral amorphous carbon,ta-C)膜,sp3键含量超过70%,也称非晶金刚石膜。
事实上,目前对DLC薄膜尚无明确的定义和统一的概念,但若以其宏观性质而论,国际上广为接受的标准为硬度达到天然金刚石硬度20%的绝缘无定形碳膜就称为DLC薄膜。
一、DLC膜的制备技术:DLC薄膜已经开发了许多种沉积方法,大体上可以分为物理气相沉积(PVD)和化学气相沉积(CVD)两大类。
PVD方法是在真空下加热或离化蒸发材料(石墨),使蒸发粒子沉积在基片表面形成薄膜的一种方法。
按照加热方式不同,热蒸发有激光蒸发、电弧蒸发、电子束加热等方法。
溅射沉积是用高能离子轰击靶物质(石墨),与靶表面原子发生弹性或非弹性碰撞,结果部分靶表面原子或原子团溅射出来,沉积在基板上形成薄膜。
CVD方法是在真空室内通入碳的氢化物、卤化物、氧化物,通过气体放电,在一定条件下促使它们发生分解、聚合、氧化、还原等化学反应过程,在基板上形成DLC薄膜的方法。
镀膜技术介绍范文
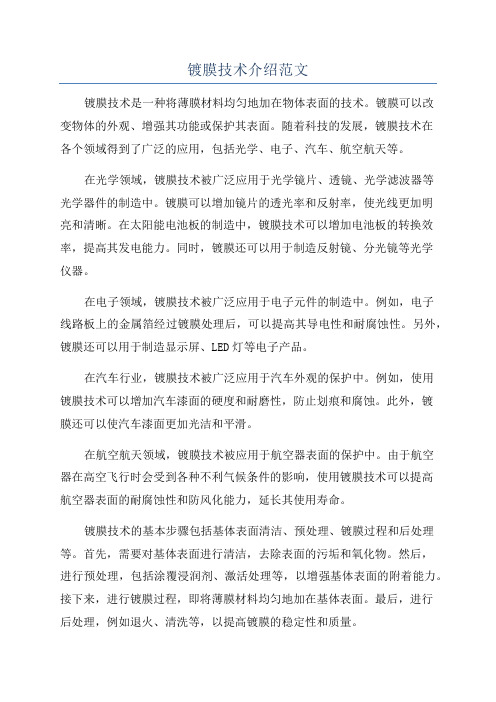
镀膜技术介绍范文镀膜技术是一种将薄膜材料均匀地加在物体表面的技术。
镀膜可以改变物体的外观、增强其功能或保护其表面。
随着科技的发展,镀膜技术在各个领域得到了广泛的应用,包括光学、电子、汽车、航空航天等。
在光学领域,镀膜技术被广泛应用于光学镜片、透镜、光学滤波器等光学器件的制造中。
镀膜可以增加镜片的透光率和反射率,使光线更加明亮和清晰。
在太阳能电池板的制造中,镀膜技术可以增加电池板的转换效率,提高其发电能力。
同时,镀膜还可以用于制造反射镜、分光镜等光学仪器。
在电子领域,镀膜技术被广泛应用于电子元件的制造中。
例如,电子线路板上的金属箔经过镀膜处理后,可以提高其导电性和耐腐蚀性。
另外,镀膜还可以用于制造显示屏、LED灯等电子产品。
在汽车行业,镀膜技术被广泛应用于汽车外观的保护中。
例如,使用镀膜技术可以增加汽车漆面的硬度和耐磨性,防止划痕和腐蚀。
此外,镀膜还可以使汽车漆面更加光洁和平滑。
在航空航天领域,镀膜技术被应用于航空器表面的保护中。
由于航空器在高空飞行时会受到各种不利气候条件的影响,使用镀膜技术可以提高航空器表面的耐腐蚀性和防风化能力,延长其使用寿命。
镀膜技术的基本步骤包括基体表面清洁、预处理、镀膜过程和后处理等。
首先,需要对基体表面进行清洁,去除表面的污垢和氧化物。
然后,进行预处理,包括涂覆浸润剂、激活处理等,以增强基体表面的附着能力。
接下来,进行镀膜过程,即将薄膜材料均匀地加在基体表面。
最后,进行后处理,例如退火、清洗等,以提高镀膜的稳定性和质量。
常见的镀膜材料包括金属薄膜、陶瓷薄膜、聚合物薄膜等。
金属薄膜可以提供优异的导电性和耐腐蚀性,适用于电子元件和光学器件的制造。
陶瓷薄膜具有优异的耐磨性和耐高温性,适用于汽车外观的保护和航空航天器表面的防护。
聚合物薄膜具有良好的柔韧性和耐候性,适用于建筑领域的防水和防紫外线处理等。
总而言之,镀膜技术是一种重要的表面处理技术,可以改变物体的外观、增强其功能或保护其表面。
三氟化镧镀膜材料

三氟化镧(LaF3)是一种常用的镀膜材料,具有优异的光学性能和化学稳定性。
以下是关于三氟化镧作为镀膜材料的一些特点和应用:
光学性能:三氟化镧具有较高的折射率和透明度,对可见光和近红外光具有良好的透过性。
它还表现出较低的散射和吸收特性,使其成为制备高质量光学薄膜的理想选择。
化学稳定性:三氟化镧具有较高的化学稳定性,在常规环境下不易受到氧化或腐蚀。
这使得它在多种条件下都能保持镀膜的性能和外观。
应用领域:由于其优秀的光学性能和化学稳定性,三氟化镧常用于光学涂层、反射镜、滤光器、激光器窗口、太阳能电池等领域。
它可以提供更好的光线传输、反射和抗反射性能。
电子技术:三氟化镧也被广泛应用于电子技术领域,如薄膜晶体管、显示器件和光电二极管等。
它可以作为电子器件的保护层或导电层,提供额外的性能和稳定性。
需要注意的是,三氟化镧的应用范围还有很多其他领域,取决于具体的需求和材料特性。
在实际应用中,根据具体要求选择合适的镀膜材料和工艺非常重要。
低压蒸气氢镀膜

低压蒸气氢镀膜
低压蒸气氢镀膜是一种表面处理技术,通常用于对材料表面进行氢化处理。
这个过程通常在相对较低的气压下进行,以确保更均匀的涂层沉积在材料表面上。
以下是该过程的一般步骤:
1.基材准备:待处理的材料表面需要经过清洗和
处理,确保表面没有油脂、灰尘或其他污染物。
这可以通过溶剂清洗、酸洗或其他适当的表面处理方法来完成。
2.真空室:材料置于真空室内,真空室通常具有
控制温度和气压的能力。
真空室中的气压被降低到相对较低的水平,以确保气体能够均匀地沉积在材料表面上。
3.氢气注入:在真空室中引入氢气。
氢气是用于
氢化处理的关键气体。
其作用是与基材表面的金属原子结合,形成金属-氢化物复合层。
4.低压蒸气氢镀膜:通过加热源或其他方法,在
低气压下进行蒸气氢镀膜。
在这个过程中,氢气和基材表面的金属原子反应,形成氢化合物的薄膜覆盖在基材表面上。
5.气压和温度控制:过程中需要控制气压和温
度,以确保薄膜的均匀性和一致性。
低压蒸气氢镀膜常用于改善材料的表面性能,例如提高耐腐蚀性、增加硬度等。
这个过程在一些工业应用中,如制造光学镀膜、电子器件和材料科学等领域得到广泛应用。
常用的镀膜方法

常用的镀膜方法
1.溅射镀膜法
溅射镀膜法是利用高能离子束轰击样品表面,产生的微小粒子将目标表面的物质释放出来,再沉积至基底表面,形成薄膜。
溅射镀膜法因其可在高真空下进行,所以适用于制备金属、半导体、氧化物及其他无机化合物薄膜。
此外,该技术还可用于制备具有特定性质的晶体结构薄膜,例如具有分子化合物的多层体系。
溅射镀膜法是当前常用的薄膜制备方法之一。
2.磁控溅射镀膜法
磁控溅射镀膜法也是一种广泛使用的薄膜制备方法,其原理同溅射镀膜法相似。
区别在于磁控溅射镀膜法使用磁场来控制离子束,从而增强溅射效率,提高沉积速度。
该技术适用于制备高品质的多层结构、重金属、氧化物和非晶态薄膜等。
3.化学气相沉积法
化学气相沉积法是通过将含有金属有机物等原料的气体送入反应室中,利用化学反应在基片表面上生长薄膜。
该技术适用于大面积,均一薄膜的制备。
化学气相沉积法可用于制备二氧化硅、硅胶、氮化硅、碳化硅等材料的薄膜。
4.热蒸发镀膜法
热蒸发镀膜法是利用高温加热金属或化合物材料,使之蒸发并沉积在基底表面。
该方法简便、容易操作,广泛应用于制备单层和多层金属薄膜,如铬、钼、铜、银和铝等金属薄膜。
此外,该技术还可用于制备非晶态薄膜,例如氧化铝薄膜、TiO2薄膜等。
5.电化学沉积法
电化学沉积法是将金属投入含有所需离子的溶液中作为阴极,通电后,溶液中的阳离子被还原成金属沉积在阴极表面上。
该技术操作简单,可制备所需厚度的纯金属或合金薄膜,并可控制薄膜的粗糙度。
电化学沉积法适用于制备黄金、银、铜等高纯度金属薄膜,也可用于制备复杂的多层材料和表面修饰。
DLC膜——精选推荐

DLC膜类金刚石膜(Diamond-Like-Carbon,DLC),是一种非晶碳膜,它具有类似天然金刚石的许多性质,如高硬度、低摩擦系数、高电阻率、良好的光学性能、高化学稳定性等[1,2]。
因此,DLC膜广泛应用于机械、磁记录技术、光电、激光等领域,从20世纪80年代以来一直是薄膜技术领域研究的热点之一。
由于制备方法和采用的碳原子载气相沉积(PVD)制备的。
体不同,生成的DLC 膜中原子的键合方式(有C-H、C- C)及碳原子之间的键合方式(有sp2、sp3等)有所不同,并且各种键合方式的比例不同。
因此DLC膜是范围很大的一类非晶碳膜,为sp2、sp3键共存(石墨为sp2键、金刚石为sp3键)。
根据膜中含氢与否可分为无氢和含氢DLC,即ta-C和ta-C:H。
含氢的类金刚石膜是通过化学气相沉积(CVD)制备的,而不含氢的类金刚石膜是通过物理不同工艺制备的DLC的成分、结构和性能相差较大,一般把硬度超过金刚石硬度20%的绝缘无定型非晶碳膜称为类金刚石膜。
图1是类金刚石的C-H相图[3],可以看出,只有相图的上半部分才能形成DLC,图中ta-C和ta-C:H的区域即DLC的形成区域,它们均是含sp3键较多的区域。
典型的ta-C:H膜含sp3部分要少于50%,而ta-C膜(即四面体碳ta-C)包含85%甚至更高含量的sp3键。
图1 类金刚石C-H图在直流放电等离子体中,Whitmell和Williamson首次用碳氢气体制备了DLC 膜。
此后,DLC膜已被多种方法制备,它们的主要共同特征都是在粒子轰击的条件下成膜的,荷能离子对膜生长表面的轰击对其sp3键结构的形成起着关键的作用,故又称之为离子碳膜,并记为i-C。
到目前为止,类金刚石膜的制备方法大致可以分为两大类:物理气相沉积法和等离子体辅助化学气相沉积法(PECVD)。
前者包括蒸发镀膜、磁控溅射、离子束镀膜、脉冲激光沉积、激光-离子束沉积、磁过滤真空弧沉积方法等。
镀膜应用场景
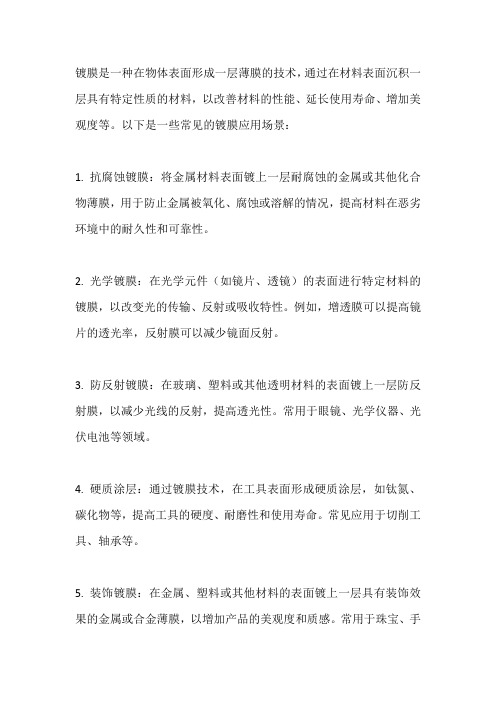
镀膜是一种在物体表面形成一层薄膜的技术,通过在材料表面沉积一层具有特定性质的材料,以改善材料的性能、延长使用寿命、增加美观度等。
以下是一些常见的镀膜应用场景:
1. 抗腐蚀镀膜:将金属材料表面镀上一层耐腐蚀的金属或其他化合物薄膜,用于防止金属被氧化、腐蚀或溶解的情况,提高材料在恶劣环境中的耐久性和可靠性。
2. 光学镀膜:在光学元件(如镜片、透镜)的表面进行特定材料的镀膜,以改变光的传输、反射或吸收特性。
例如,增透膜可以提高镜片的透光率,反射膜可以减少镜面反射。
3. 防反射镀膜:在玻璃、塑料或其他透明材料的表面镀上一层防反射膜,以减少光线的反射,提高透光性。
常用于眼镜、光学仪器、光伏电池等领域。
4. 硬质涂层:通过镀膜技术,在工具表面形成硬质涂层,如钛氮、碳化物等,提高工具的硬度、耐磨性和使用寿命。
常见应用于切削工具、轴承等。
5. 装饰镀膜:在金属、塑料或其他材料的表面镀上一层具有装饰效果的金属或合金薄膜,以增加产品的美观度和质感。
常用于珠宝、手
表、汽车零部件等领域。
6. 防尘防污镀膜:在物体表面形成一层防尘、防污的涂层,减少灰尘、污渍的附着,便于清洁和维护。
常见于玻璃、墙面涂料等领域。
7. 导电镀膜:在非导电材料表面镀上一层导电材料(如银、金属氧化物等),以提供导电性能,常见于电子元件、触摸屏、太阳能电池等领域。
这些只是一些镀膜的常见应用场景,实际上镀膜技术在许多领域都有广泛的应用,如航空航天、汽车制造、电子电器等。
不同的镀膜材料和工艺可以满足不同的需求,提升物体的功能性和附加值。
溅射镀膜原理及其应用
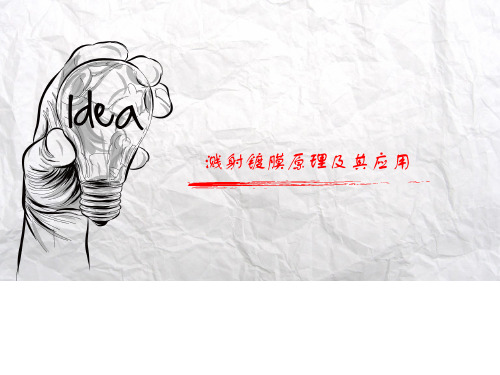
磁控溅射常见技术
射频磁控溅射
用来进行介质膜的溅射, 如在玻璃上镀ITO膜之前需镀 上一层SiO2扩散隔离层,该 SiO2膜就是采用射频溅射。
通常在溅镀过程中辉光 放电中的离子撞击到阴极时, 会与阴极的电子中和,使得 溅射现象可以继续进行。但 若靶材本身不导电的话,离 子撞击到靶材上没有电子中 和,正电荷一直累积,便与 后来的离子排斥,这会造成 离子撞击现象的停顿。高周波电源 取代直流电源,便可解决此 问题。
溅射镀膜原理及其应用
磁控溅射原理
原理: 为了提高离化率,增加溅射沉积的速率,在靶背面增加磁场
是个有效的方法----电场与磁场的交互作用,使得二次电子在靶面 做螺旋式运动,大大延长了二次电子的运动行程,从而大大增加 了它同气体分子碰撞的机会,从而大大地提高了离化率,增加了 溅射速率。
磁控溅射常见技术
偏压溅射磁控
在基片上加100-300V的负电压,使得Ar2+轰击靶材的同时也轰 击基片的膜层,使用偏压具有以下作用:
1. 改善附着力:1)将沉积过程中附着力不好的晶粒打掉;2)促 进膜层与基片的扩散,增加扩散层的厚度。
2. 提高耐磨性能:偏压的使用使得膜层更致密。 3. 改善膜层结构:偏压使得膜层由柱状晶变为更好的球状晶粒。 但偏压也有缺点: 1. 偏压的使用会降低沉积速率。 2. 过大的偏压使用会增加膜层的内应力。
矩形平面靶安装结构示意图
磁控溅射原理
平衡磁场磁控溅射
非平衡磁场磁控溅射
磁控溅射原理
孪生靶磁场分布示意图
磁控溅射原理
封闭非平衡磁场示意图
溅射靶材
溅射靶材按形状分类:矩形平面靶才、圆形平面靶才、圆柱靶材; 溅射靶材按成分分类:单质金属靶材、合金靶材、陶瓷靶材;
电弧蒸发沉积法镀膜

电弧蒸发沉积法(Arc-evaporation deposition)主要应用于为机械加工工具提供耐磨涂层。
但是,镀膜过程中会产生大量的宏观粒子,膜层的质量得不到保证。
为了解决这个问题,纳峰科技私人有限公司创新了FCVA镀膜技术。
采用我们的专利技术可以生产出高质量的非晶四面体碳(ta-C)膜以及在较为严苛的条件下工作的膜层,例如金属、金属氧化物等其他硬质膜层。
在阴极真空电弧镀膜过程中,阴极电弧会发射出等离子束(参杂了宏观颗粒和中性原子)。
电磁过滤弯管负责滤除那些不必要的宏观颗粒和中性原子,只有那些具有一定能量的离子可以到达基片。
这个特别的技术可以产生硬度更高,密度更大,更纯净的薄膜。
用FCVA方法镀出的薄膜:与基片结合力更高且具有良好的光学、化学、电子和机械性能;并且重复性好,完全满足各种实际生产,除此之外,在镀膜过程中,基片的表面温度一般可以保持在70°C以下。
因此,可以对塑料或橡胶进行FCVA镀膜。
与传统方法(比如:化学汽相沉积法,物理汽相沉积法)不同,FCVA技术产生能量稳定的电弧和100%纯离子束流,能量可以根据不同的要求精确控制。
通过这项科技我们可以生产独特的ta-C膜,并可产生高品质的Al2O3膜和金属膜。
纳峰真空镀膜(上海)有限公司是镀膜、Ta-c、Tin、ALTin、cr-n、MICC等产品专业生产加工的外资企业,公司总部设在上海市青浦区华纺路99弄99号,纳峰真空镀膜(上海)有限公司拥有完整、科学的质量管理体系。
纳峰真空镀膜(上海)有限公司的诚信、实力和产品质量获得业界的认可。
欢迎各界朋友莅临纳峰真空镀膜(上海)有限公司参观、指导和业务洽谈.TA-C非晶态四面体碳膜顏色黑色硬度HV3000 - 5000膜厚1.5um摩擦系数0.1制程温度80 ºC耐氧化温度300 ºC使用场合减少摩擦系数、脱模性佳,超高硬度,高耐磨性应用工业注塑模具、IC、工具导线架模具、刀具、导杆、陶瓷膜、冲压模、光学成型模具、粉末冶金模具、CDR模...等.氮化铝钛膜(ALTiN)颜色: 灰黑色硬度HV: 3000-3500膜厚: 1-5um摩擦系数: 0.4制程温度: 450 ºc耐氧化温度: 850 - 1000 ºC使用场合: 抗磨耗、耐酸(氧)化应用工业:铝压铸模、玻璃成型模、高速干式切削用刀具、螺丝用冲模具 ...等。
镀膜及用途
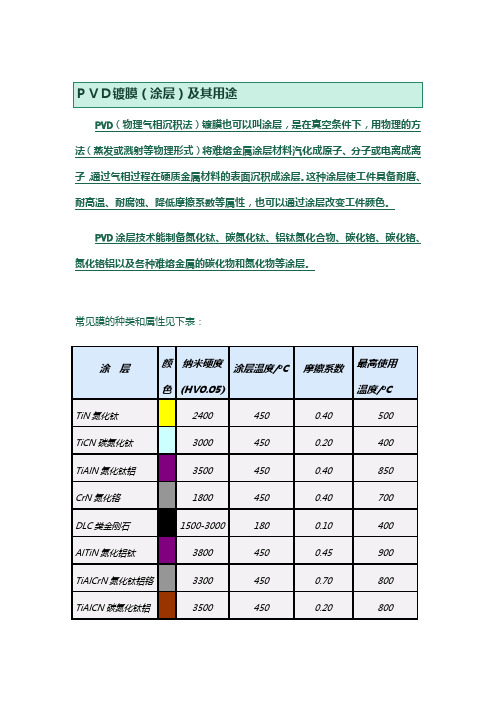
PVD(物理气相沉积法)镀膜也可以叫涂层,是在真空条件下,用物理的方法(蒸发或溅射等物理形式)将难熔金属涂层材料汽化成原子、分子或电离成离子,通过气相过程在硬质金属材料的表面沉积成涂层。
这种涂层使工件具备耐磨、耐高温、耐腐蚀、降低摩擦系数等属性,也可以通过涂层改变工件颜色。
PVD涂层技术能制备氮化钛、碳氮化钛、铝钛氮化合物、碳化铬、碳化铬、氮化铬铝以及各种难熔金属的碳化物和氮化物等涂层。
常见膜的种类和属性见下表:
在刀具基体上涂覆一层或多层硬度高、耐磨性好的金属或非金属化合物薄膜的过程叫镀膜,镀膜能较好的解决刀具存在的强度和硬度之间的矛盾。
经过镀膜之后的刀具叫做镀膜刀具或者涂层刀具。
常用镀膜种类和加工对象对照表:。
超级类金刚石DLC膜---TAC-ON非晶钻石膜

FCVA 离子 20 to 5000eV 1E -3 Pa 很好 ~ 3.4g/cm3 可调 固体 室温
1
TAC-ONTM 非晶钻石膜 (超级类金刚石DLC膜) Tetrahedral Amorphous Carbon Coating (Premier DLC)
TAC-ONTM (非晶钻石膜) 薄膜具有稳定 的钻石结构,可形成钻石成分高达 88%的sp3 斜四方键合。该膜层具有低 温沉积、超高硬度,超强附着力、低摩 擦系数、化学性质稳定、耐磨损等特点。 由FCVA技术产生的特殊无氢结构类钻 石膜层可显著延长各类模具、工具、部 件的使用寿命,并大幅降低生产维护成 本,从而显著提高产能。
Al2O3 Ball Substrate
N型 C型 TAC-ONTM
W (N) 10 10 10
Ax(mm2) 3.98E-05 7.89E-06 1.23E-06
L (m) 188.495 188.495 188.495
V(mm3) K(mm3/Nm) 7502.1 4E-07 1487.2 8E-08 231.85 1E-08
TAC-ONTM
DLC
G石墨峰
Id/Ig = 0.3
高钻石成分
D无序峰
Id/Ig = 0.7
高石墨成分
主要应用
硬盘读写磁头及盘片 切削刀具 PCB 钻头钻针
精密模具 汽车部件 耐磨部件
缝纫部件 表面处理
2
TAC-ONTM 非晶钻石膜 (超级类金刚石DLC膜) Tetrahedral Amorphous Carbon Coating (Premier DLC)
DLC ~ 25 ~2 ~ 15 ~ 8 x 10-8 ~ 0.14 ~ 200 ~ 500 ~ 2000 ~ 10-2 < 5 eV
可见光截止镀膜
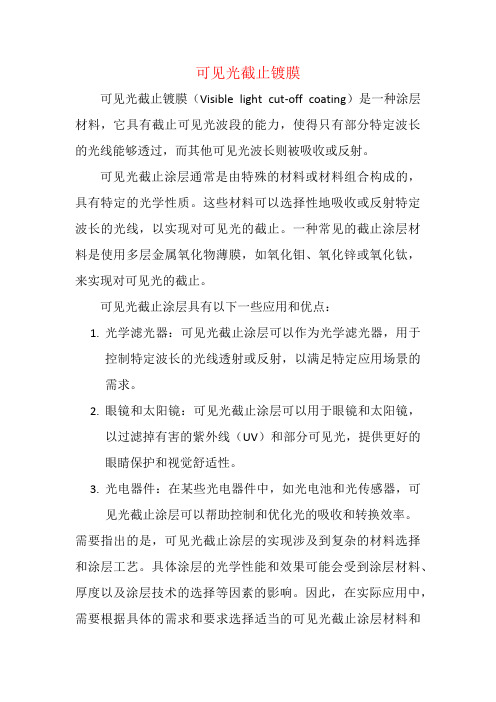
可见光截止镀膜
可见光截止镀膜(Visible light cut-off coating)是一种涂层材料,它具有截止可见光波段的能力,使得只有部分特定波长的光线能够透过,而其他可见光波长则被吸收或反射。
可见光截止涂层通常是由特殊的材料或材料组合构成的,具有特定的光学性质。
这些材料可以选择性地吸收或反射特定波长的光线,以实现对可见光的截止。
一种常见的截止涂层材料是使用多层金属氧化物薄膜,如氧化钼、氧化锌或氧化钛,来实现对可见光的截止。
可见光截止涂层具有以下一些应用和优点:
1.光学滤光器:可见光截止涂层可以作为光学滤光器,用于
控制特定波长的光线透射或反射,以满足特定应用场景的
需求。
2.眼镜和太阳镜:可见光截止涂层可以用于眼镜和太阳镜,
以过滤掉有害的紫外线(UV)和部分可见光,提供更好的
眼睛保护和视觉舒适性。
3.光电器件:在某些光电器件中,如光电池和光传感器,可
见光截止涂层可以帮助控制和优化光的吸收和转换效率。
需要指出的是,可见光截止涂层的实现涉及到复杂的材料选择和涂层工艺。
具体涂层的光学性能和效果可能会受到涂层材料、厚度以及涂层技术的选择等因素的影响。
因此,在实际应用中,需要根据具体的需求和要求选择适当的可见光截止涂层材料和
工艺。
DLC薄膜性能、应用及制备方法介绍

DLC|类金刚石薄膜制备方法简介
(5)直接光化学气相沉积(DPCVD),是利用光子促进气体的分解来沉积类金刚石薄膜。成膜时无高能粒 子辐射等问题,基片温度可降的很低,因而在低温成膜方面比较有优势;
(6)等离子体增强化学气相沉积(PECVD),是指通过低气压等离子体放电使气体碳源分解生成各种含碳 的离子基团(如CH3、CH2、CH+、C2等)和原子(或离子)氢(H、H+),并在基片负偏压的作用下使含碳基团 轰击、吸附在基片表面,同时原子氢对结构中sp2碳成分产生刻蚀作用,从而形成由sp2和sp3碳混杂结构 的氢化类金刚石薄膜。该方法提高了原料气体的分解率,降低了沉积温度,而且可以通过改变沉积参数 来获得所需质量的薄膜;
陈智顺 2016/07/27
CONTENT
1.表面处理技术简介 2.DLC薄膜特性 3.不同的DLC性能对比 4.测试/试验 5.应用领域
DLC|表面处理技术简介
常规表面处理
渗氮( 气体~,盐浴~,离子~) 发黑/发蓝(表面快速氧化) 阳极氧化 钝化 抛丸/喷砂 电镀/电泳 UV固化 粉末喷涂 活化和涂层等离子处理
aCH
腐蚀测试: 浸入 0.1 N HNO3 2 小时
无腐蚀现象
被腐蚀 (扩散腐蚀)
Source: Disk forum 2002
SHIMADZU
Solution for science
since 1875
DLC| COF (Coefficient of Friction) Comparison
Measurement on Tribo-tester (Bruker TriboLab System) Friction between DLC SST pin With/without lubricant oil (Castrol engine oil 5w-30) Normal force between SST pin & DLC = 10 Newton Moving velocity of pin = 0.84mm/sec (0.03Hz, 14mm stroke)
三氟化镧镀膜材料
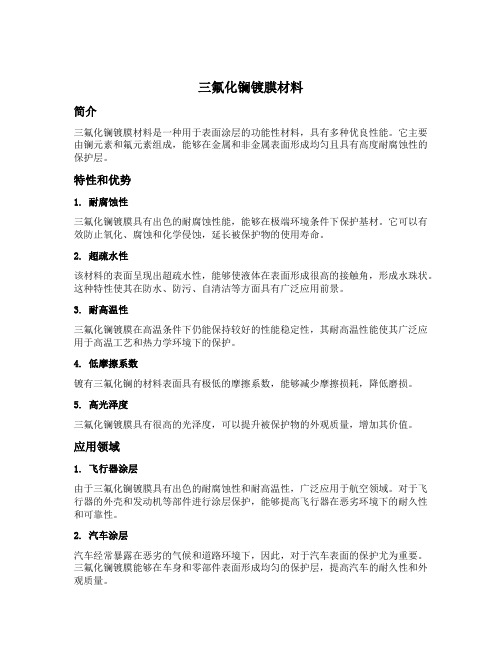
三氟化镧镀膜材料简介三氟化镧镀膜材料是一种用于表面涂层的功能性材料,具有多种优良性能。
它主要由镧元素和氟元素组成,能够在金属和非金属表面形成均匀且具有高度耐腐蚀性的保护层。
特性和优势1. 耐腐蚀性三氟化镧镀膜具有出色的耐腐蚀性能,能够在极端环境条件下保护基材。
它可以有效防止氧化、腐蚀和化学侵蚀,延长被保护物的使用寿命。
2. 超疏水性该材料的表面呈现出超疏水性,能够使液体在表面形成很高的接触角,形成水珠状。
这种特性使其在防水、防污、自清洁等方面具有广泛应用前景。
3. 耐高温性三氟化镧镀膜在高温条件下仍能保持较好的性能稳定性,其耐高温性能使其广泛应用于高温工艺和热力学环境下的保护。
4. 低摩擦系数镀有三氟化镧的材料表面具有极低的摩擦系数,能够减少摩擦损耗,降低磨损。
5. 高光泽度三氟化镧镀膜具有很高的光泽度,可以提升被保护物的外观质量,增加其价值。
应用领域1. 飞行器涂层由于三氟化镧镀膜具有出色的耐腐蚀性和耐高温性,广泛应用于航空领域。
对于飞行器的外壳和发动机等部件进行涂层保护,能够提高飞行器在恶劣环境下的耐久性和可靠性。
2. 汽车涂层汽车经常暴露在恶劣的气候和道路环境下,因此,对于汽车表面的保护尤为重要。
三氟化镧镀膜能够在车身和零部件表面形成均匀的保护层,提高汽车的耐久性和外观质量。
3. 船舶涂层船舶在海水中长时间运行容易受到海水的腐蚀。
镀有三氟化镧的涂层能够有效防止海水的腐蚀,延长船舶的使用寿命。
4. 电子产品涂层三氟化镧镀膜广泛应用于电子产品的涂层中,如智能手机、平板电脑等。
它不仅能够提供优异的保护性能,还能提高产品的外观质量和触感。
5. 太阳能电池板涂层三氟化镧镀膜具有超疏水性和高光泽度,常用于太阳能电池板的涂层中。
它能够降低污染物在电池板表面的附着,提高光电转换效率。
制备方法三氟化镧镀膜的制备方法主要包括物理气相沉积(PVD)和化学气相沉积(CVD)两种。
1. 物理气相沉积(PVD)物理气相沉积是通过在真空环境下,将三氟化镧固体源加热,使其蒸发并沉积在基材表面形成薄膜。
氟化镁镀膜材料的应用介绍

氟化镁镀膜材料的应用介绍任何玻璃都会产生反光,包括平板和有弧度的玻璃,因此,像许多光学仪器的镜头(也包括眼镜片)一样,为了减少反光和增加透射比,就需要在玻璃上面做镀膜处理。
经过镀膜处理的玻璃上面,会呈现出一种淡淡的蓝紫颜色,典型的就是照相机或望远镜镜头,通常的镀膜处理都是用氟化镁(MgF2),氟化镁的折射率是1.38,均远低于一般玻璃的折射率,更低于蓝宝石玻璃的,(普通玻璃折射率为1.52,蓝宝石的为1.76),凡折射率越高的,反光则就越强。
因此,蓝宝石的手表玻璃镀膜后的效果会更好。
在目前可用的光学薄膜材料中,氟化镁(MgF2)的折射率大概最小,只为1.38,利用氟化镁镀膜可以使光的反射率由4%降至1.8%,也就同时增加了透射比,当然为了提高透射率,也还可以采用多层镀膜来增透,那就是在玻璃内外双侧都镀膜。
爱特斯氟化镁镀膜材料:椐资料介绍,氟化镁(MgF2)晶体的莫氏硬度为6级,是一般硬度,但由于镀膜厚度极薄,所以很容易被磨损掉。
常见的眼镜片上的镀膜也非常容易被磨掉,这个也要看具体使用情况,比如,眼镜片平时只用洗涤灵加清水清洗的,就要比直接用布来擦的保持时间要长的多,手表玻璃也是一样。
尤其是玻璃直径比较大和有弧度的手表,更需要去增加镀膜处理,镀膜并不能完全消除反光,只能减少。
有些手表会造出个标记,以表示手表玻璃是经过镀膜处理的,比如像欧米茄手表,在手表的卡上或吊牌上,用一个圆圈,内有一个A字母来表示,而有AA的则表示手表玻璃内外两面均有镀膜。
手表上本来反光点就多,包括表壳、表盘、表针,不是金光灿灿,就是银光灿灿的,因此,镀膜也是为了使用佩带手表更加方便的措施之一,手表玻璃的镀膜也不会像照相机镜头哪样明显,有的很难看出来。
手表玻璃内侧镀膜不会被磨损,当玻璃镀膜损伤后,仔细看上去会有一种班驳花样的情况,另外需要引起注意的是,手表在长期保管储藏下,一定要注意防潮,长期处于潮湿环境下,玻璃表面也会发霉,同时也破坏了镀膜层。
- 1、下载文档前请自行甄别文档内容的完整性,平台不提供额外的编辑、内容补充、找答案等附加服务。
- 2、"仅部分预览"的文档,不可在线预览部分如存在完整性等问题,可反馈申请退款(可完整预览的文档不适用该条件!)。
- 3、如文档侵犯您的权益,请联系客服反馈,我们会尽快为您处理(人工客服工作时间:9:00-18:30)。
在中国缝制机械行业“十二五”时期主要技术攻关方向中,新材料、新工艺是一个重要领域。
在“十一五”期间的行业科技开发实施指南中,新材料、新工艺在产品中的开发与应用就已经是重要内容,主要体现在无油、微油润滑材料和特种材料涂覆工艺的应用与开发,通过在缝制机械的高速运转部件采用耐磨材料涂覆技术,实现无油或微油润滑。
材料及其涂覆工艺的发展与进步,对缝制机械的性能、品质的提升有积极的促进作用。
尤其在高速自动化缝纫机的品种和数量均大幅增加的情况下,如何通过新材料、新工艺的应用满足和提升高速自动化缝纫机的各项性能要求,是缝制机械制造商正在考虑的事情。
目前应用于缝制机械的新材料很多,比如多元填充高分子材料、陶瓷、金属钛、特氟龙、低温液态化油脂等。
而陶瓷、金刚石粉、钛合金、多元填充高分子材料等特种材料的涂覆工艺也在不断改进并且越来越多地应用于缝制机械中。
镀膜,是应用新的材料及新的涂覆工艺较多的一道工序。
已经有不少高速自动化缝纫机的零部件在镀膜时采用了新膜层材料和新镀膜方式。
我们知道,镀膜涉及两项基本内容,一是镀膜的技术与方法,二是所镀膜层的材料。
不同的镀膜方式,所达到的镀膜效果不同,膜层的性能发挥情况也随之有差异,而采用不同的镀层材料也有不同的性能表现。
1 不同的镀膜技术在微观环境下看,镀膜就是将一些物质(反应物)的分子、原子或者离子通过一定的方式被分解出来在其所具有的能量作用下涂覆(沉积)在需要镀膜的工件(基体)上。
镀膜时,要考虑膜层、工件材料的物理或化学性质,选择合适的镀膜方法将膜层紧紧地附着于工件上并且要产生好的性能效果。
真空镀膜技术就是在真空环境下,通过化学、物理方式将反应物或者靶材沉积到基体上的薄膜气相沉积技术。
镀膜通常需要在干净、纯粹的真空环境下进行,既为了避免污染(减少成膜过程中气体分子进入薄膜中成为杂质的量),也在于膜层材料的分子、原子化学性活跃,在常温常态下容易出现问题(比如分子间的碰撞、氧化反应)。
根据反应方式分,真空镀膜技术有PVD(物理气相沉积)、CVD(化学气相沉积)以及FCVA等。
1.1 PVDPVD是英文Physical Vapor Deposition(物理气相沉积)的缩写,是指在真空条件下,采用低电压、大电流的电弧放电技术,利用气体放电使靶材蒸发并使被蒸发物质与气体都发生电离,利用电场的加速作用,使被蒸发物质及其反应产物沉积在工件上。
PVD镀膜技术主要分真空蒸发镀膜、真空溅射镀膜和真空离子镀膜三类。
真空蒸发镀膜是通过加热蒸发某种物质(比如金属、化合物等)使其原子或分子以冷凝方式沉积在作为基体的固体表面;溅射镀膜是用高能粒子轰击固体表面时能使固体表面的粒子获得能量并逸出表面,沉积在基体上;离子镀膜是蒸发物质的分子被电子碰撞电离后以离子沉积在固体表面,是真空蒸发与阴极溅射技术的结合。
1.2 CVDCVD是Chemical Vapor Deposition(化学气相沉积)的缩写,很多反应物质在通常条件下是液态或固态,经过汽化成蒸汽再参与反应,通常是通过化学反应的方式,利用加热、等离子激励或光辐射等各种能源,在反应器内使气态或蒸汽状态的化学物质在气相或气固界面上经化学反应形成固态沉积物。
CVD是现代半导体工业中应用最为广泛的用来沉积多种材料的技术,包括大范围的绝缘材料,大多数金属材料和金属合金材料。
近年来,等离子体增强化学气相沉积法(PECVD)发展起来,最早也是用于半导体材料的加工,将沉积温度从1000℃降到600℃以下,最低的只有300℃左右。
1.3 FCVAFCVA镀膜是英文Filtered Cathodic Vacuum Arc的缩写,即“过滤阴极真空电弧技术镀膜”,对缝制机械行业而言还算是新事物。
这种镀膜技术正在为朝高速、无油环保方向发展的缝制机械提供助力。
图1 FDVE原理示意图如图1所示,FCVA使用异面双弯过滤器以及高能电、磁场过滤除去多余宏观颗粒和不带电的离子,其膜层表面形貌方面的质量可以与CVD膜层相比。
FCVA技术产生能像稳定的电弧和纯离子束流,能量可以根据不同的工艺要求精确控制,由FCVA技术沉积的碳膜和金属膜质量高,其等离子扫描技术可以使镀膜沉积面积提高到直径12英寸以上。
FCVA 的镀膜过程可以在低温下(小于80摄氏度)进行,可广泛应用于包括塑料和橡胶在内的各种领域,这点对缝制机械元器件来说也特别重要。
FCVA技术的核心点是:原体是百分百的等离子体——除了电子、原子外还有正离子,这些是所需要镀膜的材料本身产生的,比如镀碳,就是碳正离子,而镀铜则就是铜正离子,与工件上的电子合并成为中性的原子。
它采用起弧方式产生100%离化的镀膜粒子,这些镀膜离子在到达镀膜基体之前,通过外加电磁场来调节镀膜离子的能量,而不像普通的磁控溅射镀膜方式只能通过加热的方法来增加镀膜粒子的能量。
过滤阴极电弧(FCA)配有高效的电磁过滤系统,可将离子源产生的等离子体中的宏观粒子、离子团过滤干净,经过磁过滤后沉积粒子的离化率为100%,并且可以过滤掉大颗粒,因此制备的薄膜非常致密和平整光滑,抗腐蚀性能好,与机体的结合力很强。
为了达到良好的效果,FCVA镀膜对各工艺环节有严格的管理要求。
镀膜之前,要对待镀膜的基体进行清洗,因为这些基体带有空隙、空洞、油脂、污迹等,可通过真空加热和清洗加热去掉这些“脏东西”——镀膜的基体一定要干净无杂质。
经过处理的基体还应该在无菌的环境中上到夹具上,如果短时间不能镀膜则会放到设置了一定温度的保温箱中,使其处于良好的状态。
1.4 几种镀膜技术的参数比较表1 不同的镀膜技术比较注:EV表示电子伏特表1反映了不同的镀膜技术的各项指标情况。
PVD (溅射)的镀膜微粒是原子,而CVD(PECVD)的镀膜微粒是原子团(反应分子),而FCVA输出是一束等离子,该等离子束可以被扫描,可以对该离子束加偏压,该等离子束可通过镀膜技术加以控制。
镀膜需要产生完全独立、自由的分子、原子,通常要采用加热、蒸发等方式把粒子从束缚中解脱出来,才能做一些改变。
此时,镀铝、镀铜甚至是镀铬等都没有问题,但要镀陶瓷、氮化膜、氧化膜等硬膜,要将反应物烧沸很难。
尤其是镀硬膜时,若采用溅射方式,将固体变为原子或者分子几乎不能做到,而是在真空环境中形成离子团,加入负电压,以正离子去轰击要镀膜的物件(让通氩气的原子加热,用氩离子告诉轰击靶面),效率低下(可能1000次轰击后有才1~2个原子出来),且如果冲击时真空环境不好,其分子疏松。
若采用蒸发方式,则容易产生空洞,需要加高温让分子利用能量去填补空洞——这点对做镀膜不好,镀膜要求不存在空洞,其所加温度要在400摄氏度及以上,这种情况对原子、分子的要求不高,但对材料的要求高,比如需要高速钢、工具钢之类,其它的材料则不太好。
FCVA技术既不是溅射也不是热蒸发,由于用的是百分百等离子,其正离子带电,外加电磁场的方式使其加速(像光速),不用热能而是用动能(速度)来完成镀膜。
溅射和蒸发时的动能速度是每秒几百米,约1个电子福特的能量,而FCVA的速度是每秒几十公里,有50、60个电子福特的能量且可变、可控。
通常,要克服物体表面张力需要30、40个电子辐特。
如果能很好穿透表面张力,则膜层的附着力和密实度高,能形成超硬膜,因为决定镀膜优劣的关键因素是镀膜粒子能量,当镀膜粒子的能量增加后,膜层的密度也将随之增加,附着力大大改善。
传统镀膜技术只能通过升高基体温度来改善镀膜质量,但存在一定局限性。
此外,FCVA镀膜时的离子能量可控,这些等离子体有了能量和可控性,其膜层的致密性也就更好。
2FCVA可镀的膜层从应用分,目前FCVA镀膜层分为两大类:一类是在表面装饰镀膜方面,主要是(钛金、锆金)镀覆于钟表、锁具五金、厨房卫浴五金等各种五金制品表面;一类是在工具镀膜方面,主要是(硬质膜层、摩擦系数)镀覆于各种金属加工模具(冲压模具)、电子半导体类模具(成型刀)、粉末冶金模具、刀具(切纸刀、铣刀、绞刀等各类刀具)、车削刀具以及各种注塑模具(塑料成型注塑模具活动部件,零件上的应用)。
采用FCVA技术可在多种材质的工具、模具和刀具上涂上TAC-ONTM(类金刚石)、AITiN(铝氧化钛)、CrN(氧化铬)、TiN(氧化钛)等单层及多层优质硬质膜层,其膜层硬度高(2 000~5 000HV),结合强度高(最高达到100N),摩擦系数低(可降低到0.08),表面粗糙度低(最高达到球面)。
下面介绍几种膜层的特点。
2.1 TiN(氧化钛)薄膜TiN膜层具有高熔点、高硬度和良好热传导率的特性,且耐磨损,具有适中的耐氧化性,适用于高速切割,已成功用于刀具和模具耐磨保护涂层和装饰涂层。
其膜层颜色为金黄色,硬度在2 000HV~2 500HV之间,摩擦系数最大0.65,典型厚度在1~4微米,镀膜温度在400摄氏度,其工作温度在800摄氏度。
2.2 CrN(氧化铬)薄膜CrN膜层有良好的附着性、耐腐蚀性和耐氧化性,在机械部件和模具上采用此膜层是为了增强其润滑性和耐磨性,与TiN膜层相比,它对水质溶液的抗腐蚀性更强,其较高的表面硬度、较低的摩擦系数和残余应力使其适用于抗磨损、摩擦的场合。
其膜层颜色为银灰色,硬度在2 100HV及以下,摩擦系数最大0.3,典型厚度在1~4微米,镀膜温度在200到400摄氏度,其工作温度在500摄氏度。
2.3 TAC-ON非晶态四面体碳膜碳膜在缝制机械行业的应用已经多起来,主要应用的是类金刚石(也称为DLC)碳膜。
碳元素因碳原子和碳原子之间的不同结合方式,从而使其最终产生不同的物质,一类是碳碳以sp3键的形式结合的金刚石,一类是碳碳以sp2键的形式结合的石墨,一类则是碳碳以sp3和sp2键的形式结合生成的无定形碳的一种亚稳定形态,即类金刚石。
类金刚石没有严格的定义,可以包括很宽性质范围的非晶碳,兼具了金刚石和石墨的优良特性,由类金刚石而来的DLC膜同样是一种亚稳态长程无序的非晶材料,可分为无氢类金刚石碳膜和氢化类金刚石碳膜两类。
TAC-ON(非晶的四面体碳薄膜,ta-C)是一种无氢的类金刚石碳膜,是由超过80%的sp3键碳原子为骨架构成,其硬度仅次于钻石。
金刚石成膜的难度高(SP3键,合体含大量氢与碳,氢多了疏松,经不起分解),必须经过高压,通常是千兆帕以上。
FCVA给予热能之外的能量,形成瞬时高压使碳元素瞬时形成金刚石键(原子与原子间形成SP3键)且非晶的薄膜,摩擦系数低。
采用FCVA技术沉积的TAC-ON薄膜在附着力和耐磨性方面比传统的DLC薄膜强,有粘油性,润滑性能优越,可减少摩擦,并能减少润滑油污染。
TAC-ON膜层的硬度也高于传统的DLC膜层。
由于没有氢和氧键在TAC-ON膜形成,其膜层可以完全透明(膜厚薄)。
TAC-ON薄膜的膜层颜色为轻碳黑色,其膜层密度小于3,膜层硬度在3 000HV~5 000HV之间,摩擦系数最大0.1,典型厚度在0.1~2微米,镀膜温度小于80摄氏度,其工作温度小于350摄氏度。