产品缺陷管理表
产品缺陷等级分类表

糊金
烫金压力过重/温度过高导致糊版
※
D15
28
烫击穿纸 击凹/烫金过程中导致穿纸
※
D16
29
压纹浅 产品表面效果浅/样品不一致
※
D17
30 浮雕/击凸浅 产品表面效果浅/样品不一致
※
D18
31
短坑/超坑 裱坑见坑纸与面纸位置造成
※
D19
32
甩坑
裱纸干后容易撕开/分层/脱落
※
D20
33 裱纸上下粘连 裱纸胶水粘到上下物料造成粘坏粘烂
※
D8
21
丝印飞油 丝印油墨飞溅到印张其他地方
※
D9
22
丝印糊版 丝印图文模糊变粗
※
D10
23 丝印套位不准 过程中位置不准≥0.5mm
※
D11
24
金纸色差 烫金纸颜色与样品颜色不一致
※
D12
25
掉金/沙眼 烫金面掉金或颗粒状掉金
※
D13
26 烫金套位不准 烫金过程中位置不准≥0.5mm
※
D14
27
※
C6
7
水干/水大 印张水墨失衡导致
※
C7
8
水墨杠/鬼影 印张表面有杠印/花印
※
C8
9
擦花/拖花 印张表面有刮擦/拖擦痕迹/油墨花
※
C9
10
过底粘花 印张下面一张油墨带起粘到上面一张
※
C10
11
错字/缺字 印张残字/字体错误等
※
C11
12
皱纸/烂纸 印张有皱烂
※
C12
13
覆错膜 光膜/哑膜/触感膜等使用错误
3 GMP检查常见缺陷评定表
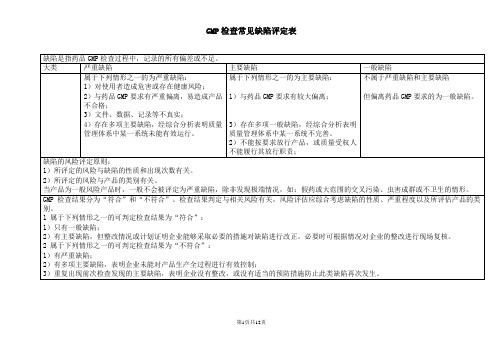
无菌灌装产品在灌装期间无环境控制/未监控微生物。
房间洁净度等级测试的采样点不够/采样方法不正确。
微粒与缺陷的检查不当。
采用无菌工艺灌装的产品在无菌灌装时,环境控制/微生物监控不充分。
培养基灌装验证失败后仍继续进行无菌灌装生产。
厂房与设备的设计或维护未将污染/尘粒产生降到最小的限度。
未考虑灭菌前的微生物污染水平。
生产开始到灭菌或过滤之间的间隔时限未经验证。
培养基灌装规程不正确。
培养基灌装数量不足。
培养基灌装未模拟实际的生产情况。
培养基支持广谱微生物生长的有效性未经证实。
培养基灌装的结果判定错误。
未做安瓿检漏试验。
无菌检查样品数量不足或不能代表一个完整的生产周期。
未将灭菌柜每次装载的产品视为一个单独的批次进行无菌检查。
一次接收的物料由多个批次构成,未考虑分开取样、检验与批准放行。
成品检验
批准放行销售前,未按照所适用的质量标准完成对成品的检验。
质量标准内容不完整/不正确。
物理指标的检验项目不全。
伪造或篡改检验结果/伪造检验报告
成品质量标准未经质量管理部门批准。
检验项目不全。
检验方法未经验证。
运输和贮存条件无SOP规定。
-
未根据需要控制或监测温湿度(如未按标示的要求贮存)。
-
与生产区或产品暴露的设备直接相邻或位于其上方的墙面/天棚有损坏(破洞、裂缝或油漆剥落)。
不与暴露产品直接相邻或不直接位于暴露产品上方的表面有损坏。
因管道或固定设备造成有无法清洁的表面,或有灰尘直接位于产品或生产设备的上方。
-
休息、更衣、洗手和盥洗设施设置不当。
产品审核缺陷严重度分级评定表

对产品功能的影响
对外观质量的影响
对包装质量的影响
A
严重
能引起产品丧失功能的或会造成安全事故的
顾客会拒收产品,或会提出申诉的
错、漏装产品,包装差,在运输中会造成损坏的,用户会申诉的
B
重大
可能严重影响产品功能或引起产品局部功能
顾客可能会发现,并可能会申诉的。
D
一、
功能
√
1
产品关键特性不符合产品标准
√
2
产品关键特性不符合内控标准
√
3
产品重要特性不符合产品标准
√
4
产品重要特性不符合内控标准
√
5
产品一般特性不符合产品标准
√
6
产品中属用户要求的特殊要求的特殊项目不符合内控标准
√
二
包装
7
错装或漏装产品
√
8
内、外包装箱损坏
√
9
缺少辅助零件
√
10
标记错误
√
11
标记模糊
包装、涂封不良有可能引起损伤或锈蚀,顾客不满意,可能会申诉的
C
一般
可能轻度影响功能的
用户可能会发现,但不会申诉的
漏装一般小件,用户可自己解决,一般不会申诉的
D
轻微
不影响产品在使用时的运转、保养或寿命的
外形、涂层或工艺上小毛病,例如涂层轻微划伤
用户不会申诉的
产品缺陷分级评定表
序号
缺陷情况
缺陷等级
A
B
C
√
三
外观
√
1
产品密封面有明显碰伤可划伤
√
2
产品辅助零件损坏
产品缺陷检查表

按照相应质量检查标准检查200件样本对规定的IL-II(G-II)的项目进行检验, 然后再从这
200件样本中抽出8件进行(S-2)项目的检验(如所检测的项目对样本有损害时, 最好从进
行(G-II)项检验时之不合格品中抽出样本进行这项测试, 以减少废品损失), 做完这两项检
测后, 如果发现:
1) 具有严重缺陷的不合格品数少于或等于接收数5, 具有主要缺陷的不合格品数少于或
等于7,同时具有轻微缺陷的不合格品数少于或等于14, 则该批产品可接受入库;
2) 具有严重缺陷的不合格品数多于或等于拒收数6, 或者具有主要缺陷的不合格品数多
于或等于8, 或者具有轻微缺陷的不合格品数多于或等于15, 则该批产品须拒收;
4.8 如果一个产品经检查既有严重缺陷, 又有主要缺陷和轻微缺陷, 应判为有严重缺陷的产
品.
4.9 样本的选取:
为了达到抽样检验的目的, 样本应能较完善地代表被检验的产品的总体, 即满足代表性和
保证抽检合格的全批产品的质量水平. 因此, 抽样要根据要求和实际情况进行. 应从检验
批中随机抽样(即从不同堆放部位, 不同箱号中抽取样本); 如果产品有编号,可采用抽签法
或随机抽样数字表法抽取样本
4.10 如抽检不合格, 而出货又紧急的情况下, 可由抽检转为全检, 剔除所有不合格品.。
质量缺陷、隐患处理表

日期:
工程部位/工序存在的质量缺陷/隐患经复查,已经按要求整改完毕,质量缺陷/隐患已经消除,同意进入下一部位/工序施工。
项目监理机构:(章)
总/专业监理工程师:
日期:
质量缺陷/隐患处理表
工程名称:编号:
致:(承包单位)
你单位施工的工程的部位/工序存在以下质量缺陷/隐患,请按规定进行整改,整改结束后通知监理工程师进场复查:
项目监理机构:(章)
总/专业监理工程师:
日期:患,我单位已经按要求整改完毕,请进场进场复查。
承包单位:(章)
产品缺陷记录表

合格数量
返工信息 零件
线长确认签字:
替换零件 分总成
审核/日期:
班组长确认签 字:
其他
产品确认
质量员 确认签
确认信息 标识确认 确认人及工号
说明: 1. 返工序号请和缺陷 序号相对应。 2. 替换零件栏需完整 填写所有被替换零件 。 3. 被替换零件必须报 废处理。 4. 返工产品确认时, 除完成正常项目确认 外,必须追加确认所 有回用零件状态是否 OK,返工标识是否 OK。
生产线:
序号
零件名称
1 2 3 4 5 6 7 8 9 10
返工 序号
返工数量
编制 /日 期:
零件代码
时间: 工位
年 工号
产品缺陷记录表
月 姓名
日
Байду номын сангаас
人为因素
设备/系统因素
缺陷分类 原材料因素
班次:
早□
其他因素描述 缺陷代码
中□
晚□
缺陷品状态 (打“√”) 零件 组件
缺陷分类代码 A 操作不当
A1 错装 A2 漏装 B 新员工培训 C 脏污、疵点 D 尺寸不良 E 开裂、破损 F 缺料、多料 G 变形 X 设备调试 Z 其他
产品缺陷分析表
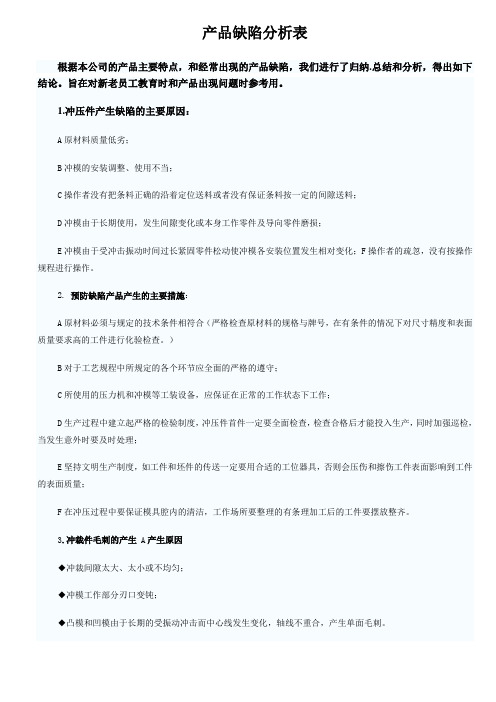
产品缺陷分析表根据本公司的产品主要特点,和经常出现的产品缺陷,我们进行了归纳.总结和分析,得出如下结论。
旨在对新老员工教育时和产品出现问题时参考用。
1.冲压件产生缺陷的主要原因:A原材料质量低劣;B冲模的安装调整、使用不当;C操作者没有把条料正确的沿着定位送料或者没有保证条料按一定的间隙送料;D冲模由于长期使用,发生间隙变化或本身工作零件及导向零件磨损;E冲模由于受冲击振动时间过长紧固零件松动使冲模各安装位置发生相对变化;F操作者的疏忽,没有按操作规程进行操作。
2. 预防缺陷产品产生的主要措施:A原材料必须与规定的技术条件相符合(严格检查原材料的规格与牌号,在有条件的情况下对尺寸精度和表面质量要求高的工件进行化验检查。
)B对于工艺规程中所规定的各个环节应全面的严格的遵守;C所使用的压力机和冲模等工装设备,应保证在正常的工作状态下工作;D生产过程中建立起严格的检验制度,冲压件首件一定要全面检查,检查合格后才能投入生产,同时加强巡检,当发生意外时要及时处理;E坚持文明生产制度,如工件和坯件的传送一定要用合适的工位器具,否则会压伤和擦伤工件表面影响到工件的表面质量;F在冲压过程中要保证模具腔内的清洁,工作场所要整理的有条理加工后的工件要摆放整齐。
3.冲裁件毛刺的产生 A产生原因◆冲裁间隙太大、太小或不均匀;◆冲模工作部分刃口变钝;◆凸模和凹模由于长期的受振动冲击而中心线发生变化,轴线不重合,产生单面毛刺。
B对策◇保证凸凹模的加工精度和装配质量,保证凸模的垂直度和承受侧压力及整个冲模要有足够的刚性;◇在安装凸模时一定要保证凸凹模的正确间隙并使的凸凹模在模具固定板上安装牢固没,上下模的端面要与压力机的工作台面保持相互平行。
◇要求压力机的刚性要好,弹性变形小,道轨的精度以及垫板与滑块的平行度等要求要高;◇要求压力机要有足够的冲裁力。
冲裁件剪裂断面允许毛刺的高度4冲裁件产生翘曲变形原因:有间隙作用力和反作用力不在一条线上产生力矩。
缺陷跟踪管控表(每周)
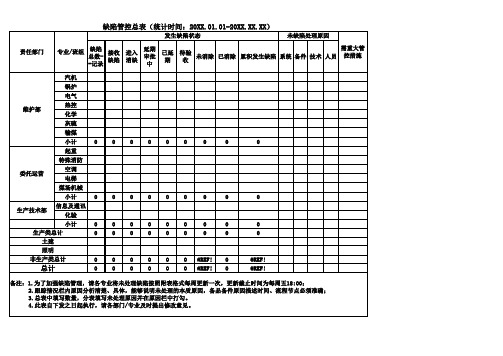
发生缺陷状态 责任部门 专业/班组 缺陷 接收 进入 延期 总数审批 缺陷 消缺 -记录 中 汽机 锅炉 电气 维护部 热控 化学 灰硫 输煤 小计 起重 特殊消防 委托运营 空调 电梯 煤场机械 小计 生产技术部 信息及通讯 化验 小计 生产类总计 土建 照明 非生产类总计 0 0 0 0 0 0 0 0 0 0 0 0 0 0 0 0 0 0 0 0 0 0 0 0 0 0 0 0 0 0 0 0 0 0 0 0 已延 期 未缺陷处理原因 需重大管 控措施
待验 未消除 已消除 累积发生缺陷 系统 备件 技术 人员 收
总计
0 0
0 0
0 0
0 0
0 0
0 0
#REF! #REF!
0 0
#REF! #REF!
备注:1.为了加强缺陷管理,请各专业将未处理缺陷按照附表格式每周更新一次,更新截止时间为每周五18:00; 2.跟踪情况栏内原因分析清楚、具体,能够说明未处理的本质原因,备品备件原因描述时间、流程节点必须准确; 3.总表中填写数量,分表填写未处理原因并在原因栏中打勾。 4.此表自下发之日起执行,请各部门/专业及时提出修改意见。