第三章 压力铸造
压力铸造

将熔融或半熔融的金属以高速压射入金属铸型内,并在 压力下结晶的铸造方法
01 ห้องสมุดไป่ตู้述
03 工艺流程
目录
02 特点 04 应用
压力铸造是指将熔融或半熔融的金属以高速压射入金属铸型内,并在压力下结晶的铸造方法,简称压铸。常 用压射压力为30~70MPa,充填速度约为0.5~50 m/s,充填时间为0.01~0.2 s。
近些年来,高科技已应用于压铸领域.如采用三级压射机构控制压力、压射速度和型内气体。发展特殊压铸 工艺(如真空压铸、定向引气压铸、充氧压铸等)和应用计算机控制技术,有效地清除气孔,提高铸件致密度,同 时研制新型模具材料和热处理新工艺来延长压型寿命,使黑色金属压铸有了一定进展。
谢谢观看
简述
压力铸造是一种将液态或半固态金属或合金,或含有增强物相的液态金属或合金,在高压下以较高的速度填 充入压铸型的型腔内,并使金属或合金在压力下凝固形成铸件的铸造方法。压铸时常用的压力为4~500MPa,金 属充填速度为0.5—120m/s。因此,高压、高速是压铸法与其他铸造方法的根本区别,也是重要特点。1838年美 国人首次用压力铸造法生产印报的铅字,次年出现压力铸造专利。19世纪60年代以后,压力铸造法得到很大的发 展,不仅能生产锡铅合金压铸件、锌合金压铸件,也能生产铝合金、铜合金和镁合金压铸件。20世纪30年代后又 进行了钢铁压力铸造法的试验。
压力铸造的原理主要是金属液的压射成形原理。通常设定铸造条件是通过压铸机上速度、压力,以及速度的 切换位置来调整的,其他的在压铸型行进行选择。
特点
1、压力铸造的优点 1)生产率高,易于实现机械化和自动化,可以生产形状复杂的薄壁铸件。压铸锌合金最小壁厚仅为0.3mm, 压铸铝合金最小壁厚约为0.5mm,最小铸出孔径为0.7mm。 2)铸件尺寸精度高,表面粗糙度值小。压铸件尺寸公差等级可达CT3~CT6,表面粗糙度一般为Ra0.8~ 3.2μm。 3)压铸件中可嵌铸零件,既节省贵重材料和机加工工时,也替代了部件的装配过程,可以省去装配工序,简 化制造工艺。 2、压力铸造的缺点 1)压铸时液体金属充填速度高,型腔内气体难以完全排除,铸件易出现气孔和裂纹及氧化灾杂物等缺陷,压 铸件通常不能进行热处理。 2)压铸模的结构复杂、制造周期长,成本较高,不适合小批量铸件生产。 3)压铸机造价高、投资大,受到压铸机锁模力及装模尺寸的限制,不适宜生产大型压铸件。
第三章 铸造方法及其发展

1) 2) 3)
二)熔模铸造的特点和适用范围
1)
2)
3) 4) 5)
铸件的精度和表面质量较高,尺寸公差等级可达 IT11-IT13,表面粗糙度Ra值达1.6-2.5um。 合金种类不受限制,钢铁及有色合金均可适用。尤其 适用于高熔点及难加工的高合金钢。 可铸出形状较复杂的铸件,如铸件上宽度大于3mm的 凹槽、直径大于2mm的小孔均可直接铸出。 生产批量不受限制,单件、成批、大量生产均适用。 工艺过程较复杂,生产周期长,原材料价格贵,铸件 成本高,铸件不能太大、太长。 熔模铸造最适合25kg以下的高熔点、难以切削加工合 金铸件的成批大量生产。目前主要用于航天、飞机、 汽轮机、燃气轮机叶片、泵轮、复杂刀具、汽车、拖 拉机和机车上的小型精密铸件的生产。
②按模型特征分 整模造型 用于铸件最大截面靠一端且为平 面的铸件,不会错箱 挖砂造型 用于分型面是曲面的单件、小批 量生产的铸件 假箱造型 用于成批生产需要挖砂的铸件 活块造型 刮板造型 用于单件、小批量生产带有凸出 部分、难以起模的铸件 用于有等截面或回转体的大、中 型铸件,单件、小批生产
二、机器造型
压铸工艺过程
合型
浇注合金液
压入型腔
推出铸件
抽芯
压型分开
压力铸造示意图
压力铸造演示
二)压力铸造的特点和适用范围
1) 2)
压力铸造的优点:
3)
4)
5)
铸件尺寸精度和表面质量最高。公差等级一般为IT11IT13级,Ra为3.2-0.8um,可不经机加工而直接使用。 铸件晶粒细小、组织致密、表层紧实,强度和表面硬 度高,抗拉强度可比砂型铸造高25%-30%,但伸长率 有所下降。 可压铸出形状复杂的薄壁件。可铸出极强件,或可铸 出细小的螺纹、孔、齿、槽、凸纹及文字。 生产率高。国产压铸机每小时可铸50-150次,便于实 现机械化和自动化。 便于采用镶嵌法。对于复杂而无法取芯的铸件或局部 要求有特殊性能(耐磨、导电、导磁、绝缘等)的铸件, 可采用镶嵌法,扩大了压铸件的应用范围,可以将许 多小铸件合铸在一起,也可铸出十分复杂的铸件。
特种铸造之压力铸造

真空压铸镁合金
真空压铸铝件
4.1 铸造在压力下成形特征
但是在此机器上装斜和维护铸型比较麻烦,生产效率较 前两种冷压室压铸机低。
4.1.2 压铸时金属流的特征
压力铸造过程的主要特征就是金属在高压作用下的高速填充型腔。 因此欲掌握压铸件成型实质,主要就应了解压力铸造时金属充型过程中 的所受压力变化,充型时金属的流动形态,以便采取合适的技术措施, 充分运用压铸时金属充型特殊现象的有利方面,避免和克服此现象可能 带来的负面影响,高效地制造出质量符合要求的压铸件。
的致密度。此一增大的压力值一直保持到型内铸件完全凝固。
最终的压力值可为50~500MPa。
2、压铸时金属填充型腔的形态——理论假设
A 弗洛梅尔(Frommer)理论
Frommer 1932
1 当金属流经浇口进入型腔后,仍 保持浇口的断面直向型腔远端的对面型 壁射去;
2 待到达对面型壁厚,在此处的型 腔中聚积,消失了冲击力后,沿型壁在 整个型腔断面上反向移动。型腔中的空 气和随金属六进入型腔的空气依靠金属 液充型时的压力挤出型外: 如果浇口横截面积较小(浇口截面积 f/型腔截面积F>(1/3~1/4))反向流动平 稳,金属液以小的旋转涡流形式移动; 如果浇口截面积较大(f/F<1/3),则 液流速度高,返回流回呈现为强烈的涡 状紊流。
在后续进入型腔金属的补充 下,沿型腔整个断面向正对 浇口的另一端型腔填充,直 至充满型腔。
压力铸造

压力铸造
•压铸(压力铸造)的实质:压铸是在高压作用下,将液态或半液态金属快速压入金属压铸型(也可称为压铸模或压型)中,并在高压作用下凝固而获得铸件的方法。
•压铸的两大特点:高压和高速充型。
区别于其它铸造方法的最基本特征。
•压铸所用的压射比压一般为30~70MPa(30~700atm);充填速度可达5~100m/s,有时高达120 m/s。
充型时间很短,一般在0.01~0.25s,最短时可达千分之几秒。
–压力铸造优点:
•(1) 铸件的精度高,表面光洁(CT4~CT8,Ral.6~6.3μm),并可直接铸出极薄件或带有小孔、螺纹的铸件。
•(2) 铸件冷却快,又是在压力下结晶,故晶粒细小,表层紧实,铸件的强度、表面硬度高。
压铸件的抗拉强度可比砂型铸件大25%~30%,但延伸率有所降低。
•(3) 生产率高,每小时可压铸50~150次,最高可达500次.且便于实现自动化、半自动化
•压力铸造优点:
•(4) 便于采用嵌铸(又称镶铸法)。
•嵌铸是将各种金属或非金属的零件嵌放在压铸型中,在压铸时与压铸件铸合成一体。
•嵌铸法利于制出一般压铸法难以制出的形状复杂件。
•嵌铸还可消除铸件局部热节,减少壁厚,防止缩孔;可改善和提高局部性能,如耐磨性、导热性、导磁性和绝缘性等;还可将许多小铸件合铸在一起,代替装配工序•压力铸造缺点:
•(1) 压铸型结构复杂,制造成本高,压铸机生产效率高,一般压铸只用于定型产品的大量生产。
•(2) 压铸高熔点铸件时,易降低压型寿命。
目前压铸尚不适于钢、铸铁等高熔点合金的铸造。
压力铸造及工艺特点
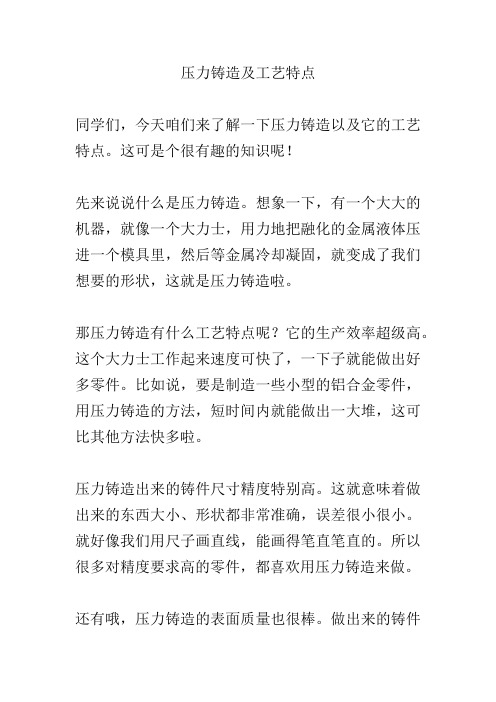
压力铸造及工艺特点同学们,今天咱们来了解一下压力铸造以及它的工艺特点。
这可是个很有趣的知识呢!先来说说什么是压力铸造。
想象一下,有一个大大的机器,就像一个大力士,用力地把融化的金属液体压进一个模具里,然后等金属冷却凝固,就变成了我们想要的形状,这就是压力铸造啦。
那压力铸造有什么工艺特点呢?它的生产效率超级高。
这个大力士工作起来速度可快了,一下子就能做出好多零件。
比如说,要是制造一些小型的铝合金零件,用压力铸造的方法,短时间内就能做出一大堆,这可比其他方法快多啦。
压力铸造出来的铸件尺寸精度特别高。
这就意味着做出来的东西大小、形状都非常准确,误差很小很小。
就好像我们用尺子画直线,能画得笔直笔直的。
所以很多对精度要求高的零件,都喜欢用压力铸造来做。
还有哦,压力铸造的表面质量也很棒。
做出来的铸件表面光滑平整,就像镜子一样。
比如说,一些汽车的零部件,用压力铸造做出来,表面又好看又光滑,质量杠杠的。
但是呢,压力铸造也有一些小缺点。
因为压力很大,模具很容易磨损,所以模具的成本就比较高啦。
而且,不是所有的金属都适合用压力铸造的方法,只有那些能在压力下快速凝固的金属才行。
压力铸造的时候,因为金属液是在高压下快速填充模具的,所以铸件内部容易产生气孔。
这就像我们吹气球,如果吹得太快太猛,气球里可能就会有一些小气泡。
在很多领域都发挥着重要的作用。
比如说,在航空航天领域,那些精密的零件很多都是通过压力铸造做出来的;在电子行业,像手机的外壳、电脑的配件,也经常用到压力铸造。
同学们,现在你们对压力铸造和它的工艺特点是不是有了更清楚的了解啦?希望大家以后在生活中看到相关的产品,能想到今天学到的知识哦!。
压力铸造的概念

压力铸造的概念压力铸造是一种高效的金属加工技术,通过在金属熔融状态下施加高压力,迫使熔融金属进入铸型腔,形成所需的零件或产品。
相对于传统的重力铸造,压力铸造具有许多优势,例如制造精度高、尺寸稳定性好、表面光洁度高等。
压力铸造的工艺过程主要包括模具设计、模具制造、材料预处理、注射及冷却等几个关键环节。
首先,需要根据产品的形状、尺寸和要求来设计模具。
模具的设计要考虑到产品的形状复杂性、冷却系统和脱模方式等因素。
然后,根据模具设计来制造模具。
模具通常由两个或多个零部件组成,其中包括模具壳体、注射系统和冷却系统等。
在开始压力铸造之前,需要对金属材料进行预处理。
预处理包括熔炼金属、净化金属、合金化调整以及调节金属温度等步骤。
这些预处理步骤可以保证金属在注射过程中具有较好的流动性和冷却性能。
在金属预处理完成后,可以开始注射过程。
注射过程通过在高温下将金属注入到模具腔中来实现。
注射过程分为两个阶段:注射和填充。
在注射阶段,将金属材料加热至液态,并通过柱塞或活塞等装置将金属材料注入模具腔中。
填充阶段是指金属材料在模具腔中充满过程,在该阶段需要克服金属表面张力和黏度的阻力,确保金属材料填充整个模具腔。
注射完成后,金属材料会在模具中冷却和凝固。
冷却速度对于金属的组织和性能具有重要影响。
因此,通常会在模具中设置冷却系统以控制冷却速度。
一般来说,冷却时间越短,金属晶粒越细,力学性能越好。
最后,完成冷却的金属零件可以脱模并进行后续的处理。
脱模是指将冷却凝固的金属零件与模具分离的过程。
脱模可以通过机械力、气体压力或抽真空等方式来实现。
脱模之后,还可以进行除毛刺、清洁和表面处理等工艺,以达到最终产品的质量要求。
总的来说,压力铸造是一种重要的金属成形技术,具有高效、高精度和高表面质量等优势。
随着科技的进步和工艺的改进,压力铸造在汽车、航空航天、通讯设备等各个领域得到广泛应用,并在产品的设计和制造过程中发挥重要作用。
压力铸造
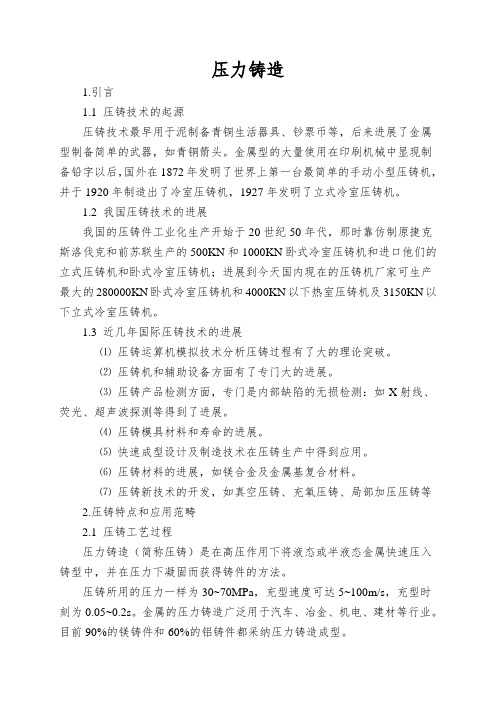
压力铸造1.引言1.1 压铸技术的起源压铸技术最早用于泥制备青铜生活器具、钞票币等,后来进展了金属型制备简单的武器,如青铜箭头。
金属型的大量使用在印刷机械中显现制备铅字以后,国外在1872年发明了世界上第一台最简单的手动小型压铸机,并于1920年制造出了冷室压铸机,1927年发明了立式冷室压铸机。
1.2 我国压铸技术的进展我国的压铸件工业化生产开始于20世纪50年代,那时靠仿制原捷克斯洛伐克和前苏联生产的500KN和1000KN卧式冷室压铸机和进口他们的立式压铸机和卧式冷室压铸机;进展到今天国内现在的压铸机厂家可生产最大的280000KN卧式冷室压铸机和4000KN以下热室压铸机及3150KN以下立式冷室压铸机。
1.3 近几年国际压铸技术的进展⑴压铸运算机模拟技术分析压铸过程有了大的理论突破。
⑵压铸机和辅助设备方面有了专门大的进展。
⑶压铸产品检测方面,专门是内部缺陷的无损检测:如X射线、荧光、超声波探测等得到了进展。
⑷压铸模具材料和寿命的进展。
⑸快速成型设计及制造技术在压铸生产中得到应用。
⑹压铸材料的进展,如镁合金及金属基复合材料。
⑺压铸新技术的开发,如真空压铸、充氧压铸、局部加压压铸等2.压铸特点和应用范畴2.1 压铸工艺过程压力铸造(简称压铸)是在高压作用下将液态或半液态金属快速压入铸型中,并在压力下凝固而获得铸件的方法。
压铸所用的压力一样为30~70MPa,充型速度可达5~100m/s,充型时刻为0.05~0.2s。
金属的压力铸造广泛用于汽车、冶金、机电、建材等行业。
目前90%的镁铸件和60%的铝铸件都采纳压力铸造成型。
金属液在高压下以高速填充铸型,并在压力下冷却,是压铸区不于其他铸造工艺的重要特点。
压力铸造的要紧工序可分为:合型、压射、顶出三个时期。
压铸机的要紧结构简图如图2-1所示。
图2-1 压铸机要紧结构简图拉杆;2—合模座;3—动模座;4—定模座;5—压铸模2.2 压铸的特点(1)优点①生产率高,压铸机没小时可压铸50~150次,甚至有的可达5 00次;便于实现自动化或半自动化;②铸件的尺寸精度高,标准公差可达IT8~11;表面粗糙度低,R a=0.8~3.2,可直截了当铸造出螺纹;③由于在压力下凝固,且速度快,因此,铸件晶粒细小、表面紧实、强度和硬度高;④便于采纳镶铸法(嵌铸法)。
特种铸造之压力铸造
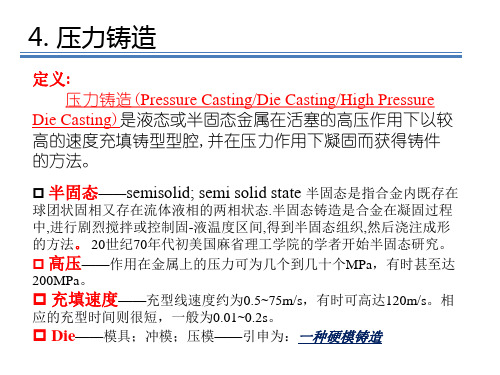
徐州科比特开发生产的管道型轴流通风机, 叶轮采用铝合金压力铸造
压铸是最先进的金属成型方法之一,是实现少切屑,无切屑的有效 途径,应用很广,发展很快。目前压铸合金不再局限于有色金属的锌、 铝、镁和铜,而且也逐渐扩大用来压铸铸铁和铸钢件。压力铸造法适用 于大批量生产的铸件,生产效率高,生产过程容易实现机械化和自动化。 压铸件也不再局限于汽车工业和仪表工业,逐步扩大到其它各个工 业部门,如农业机械、机床工业、电子工业、国防工业、计算 机、医疗 器械、钟表、照相机和日用五金等几十个行业。在压铸技术方面又出现 了真空压铸、加氧压铸、精速密压铸以及可溶型芯的应用等新工艺。
在活塞端面前可能会形成液流 的波峰,它也会把空气裹入金属液, 在铸件中形成气孔。
C 活塞移动速度适当
随着活塞的移动,在活塞端面 前形成充满压室整个断面的液面 抬高短,随着活塞的继续前进, 一次增加抬高段的程度,把压室 内空气向左挤,进入型腔,通过 排气通道进入大气。
瑞士已有技术实现活塞移动的等加速压射系统,可获得理 想压室全断面的充满过程。
热压室压铸机(简称热空压铸机)压室浸在保温溶化坩埚的液态 金属中,压射部件不直接与机座连接,而是装在坩埚上面。这种压铸 机的优点是生产工序简单,效率 高;金属消耗少,工艺稳定。但压 室,压射冲头长期浸在液体金属中,影响使用寿命。并易增加合金的 含铁量。热压室压铸机目前大多用于压铸锌合金等低熔点合金 铸件, 但也有用于压铸小型铝、镁合金压铸件。
A 活塞式热压室压铸机
喷嘴左端和压铸型上的直浇道口相接, 坩埚和压室(压力容器)一般都用铸铁铸 成一体,在坩埚外面用燃气或电阻丝加热。 压铸时,活塞式热压室压铸机上的活塞上 提,金属液从坩埚流入压室,活塞下压, 把压室内金属液经鹅颈、喷嘴压入铸型。
压力铸造工艺介绍

压力铸造工艺介绍压力铸造是一种将熔融金属通过压力注入模具中形成所需零件的工艺。
它通常用于生产具有复杂几何形状的零部件,比如汽车发动机缸体、航空航天部件和电子设备外壳等。
本文将介绍压力铸造的工艺流程、设备和应用。
压力铸造的工艺流程包括准备工作、注射、凝固和取模四个主要步骤。
首先,需要准备好模具,并在其内表面涂上涂料或涂腻子,以防止金属液渗透。
然后,将金属锭放入熔炉中进行熔化。
一旦金属达到所需温度,就可以开始注射。
注射是指将熔融金属通过高压注射机注入预先准备好的模具中。
在注射期间,金属会快速充满整个模腔,并且根据模具的形状形成所需零件。
完成注射后,金属将开始凝固。
在凝固过程中,金属会从熔融态变为固态,并逐渐获得足够的强度。
最后,完成凝固后,可以取出铸件,并进行进一步的处理和加工。
为了实现高质量的压力铸造,必须使用特定的设备。
注射机是压力铸造的核心设备。
它通常由注射缸、注射橡胶、压力缸和压力橡胶组成。
注射缸和压力缸之间通过活塞连接,活塞由液压系统提供动力。
注射缸的功能是将金属注射到模具中,而压力缸则用于施加额外的压力,以确保金属充实整个模具。
此外,还需要一些辅助设备,如熔炉、模具加热系统和模具翻转装置等。
压力铸造具有许多优点,使其成为制造业中广泛应用的一种工艺。
首先,由于金属在高压下被迫充实整个模具,因此可以得到高密度、无缺陷的铸件。
其次,压力铸造可以生产具有复杂几何形状的零件,这是其他铸造工艺无法达到的。
此外,压力铸造具有较高的生产效率和较短的周期时间,适用于大规模生产。
最后,压力铸造能够使用各种金属材料,如铝合金、镁合金、铜合金和锌合金等。
在汽车制造、航空航天和电子行业,压力铸造被广泛应用于生产各种零件。
在汽车制造领域,凭借其高度精密的加工能力,压力铸造可以生产出轻型、高强度的发动机缸体、曲轴壳体和转向器等零件。
在航空航天领域,压力铸造可以制造出复杂的涡轮叶片、喷气发动机零件和飞机外壳等关键部件。
压力铸造

简述压力铸造技术1.引言1.1压铸技术的起源压铸技术最早用于泥制备青铜生活器具、钱币等,后来发展了金属型制备简单的武器,如青铜箭头。
金属型的大量使用在印刷机械中出现制备铅字以后,国外在1872年发明了世界上第一台最简单的手动小型压铸机,并于1920年制造出了冷室压铸机,1927年发明了立式冷室压铸机。
1.2 我国压铸技术的发展我国的压铸件工业化生产开始于20世纪50年代,那时靠仿制原捷克斯洛伐克和前苏联生产的500KN和1000KN卧式冷室压铸机和进口他们的立式压铸机和卧式冷室压铸机;发展到今天国内现在的压铸机厂家可生产最大的280000KN 卧式冷室压铸机和4000KN以下热室压铸机及3150KN以下立式冷室压铸机。
1.3近几年国际压铸技术的发展⑴压铸计算机模拟技术分析压铸过程有了大的理论突破。
⑵压铸机和辅助设备方面有了很大的发展。
⑶压铸产品检测方面,特别是内部缺陷的无损检测:如X射线、荧光、超声波探测等得到了发展。
⑷压铸模具材料和寿命的发展。
⑸快速成型设计及制造技术在压铸生产中得到应用。
⑹压铸材料的发展,如镁合金及金属基复合材料。
⑺压铸新技术的开发,如真空压铸、充氧压铸、局部加压压铸等2.压铸特点和应用范围2.1 压铸工艺过程压力铸造(简称压铸)是在高压作用下将液态或半液态金属快速压入铸型中,并在压力下凝固而获得铸件的方法。
压铸所用的压力一般为30~70MPa,充型速度可达5~100m/s,充型时间为0.05~0.2s。
金属的压力铸造广泛用于汽车、冶金、机电、建材等行业。
目前90%的镁铸件和60%的铝铸件都采用压力铸造成型。
金属液在高压下以高速填充铸型,并在压力下冷却,是压铸区别于其他铸造工艺的重要特征。
压力铸造的主要工序可分为:合型、压射、顶出三个阶段。
压铸机的主要结构简图如图2-1所示。
图2-1 压铸机主要结构简图1—拉杆;2—合模座;3—动模座;4—定模座;5—压铸模2.2压铸的特点(1)优点①生产率高,压铸机没小时可压铸50~150次,甚至有的可达500次;便于实现自动化或半自动化;②铸件的尺寸精度高,标准公差可达IT8~11;表面粗糙度低,Ra=0.8~3.2,可直接铸造出螺纹;③由于在压力下凝固,且速度快,因此,铸件晶粒细小、表面紧实、强度和硬度高;④便于采用镶铸法(嵌铸法)。
第三章 压力铸造
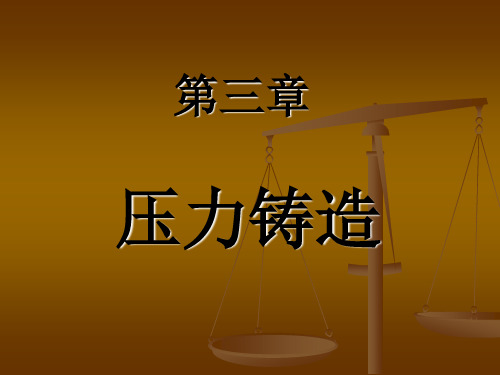
• 3.1.1 压力铸造特点 (1)产品质量好高25%—30%,但延 伸率低70%。可以制得薄壁复杂且轮廓清晰的铸 件。现代超薄铝合金压铸技术可制造0.5mm厚的 铸件,如铝合金笔记本电脑外壳。最小铸出孔 0.7mm。 (2)生产效率高。 压力铸造的生产周期短,一次操作的循环时间约 为5s~3min,且易实现机械化和自动化。这种 方法适于大批量的生产。
2. 压铸件精度高,光洁度高,尺寸稳定,一致性好, 加工余量很少。 压铸模型腔具有较高的精度和很高的表面光洁度, 故压铸件与其它铸造方法比,不但具有更高的精度 和表面光洁度,而且在生产过程中,各个铸件尺寸 一致性好,稳定性也好,从而具有很好的装配互换 性。
各种铸件精度比较 压铸 尺寸精度 表面光洁度 熔模 砂型 ZJ7-ZJ6 12.5
压力铸造的实质、特点及应用
一、压力铸造的实质:
压力铸造(简称压铸)的实质,是在高压作用下, 使液态或半固态金属以较高的速度充填压铸型型腔,并 在压力作用下凝固而获得铸件的方法。即压力下浇注和 压力下凝固。
两大特征: 高压 高速
这也是压铸区别于其它铸造方法的最基本特征。
高压:
比压:作用在铸件上单位面积上的压力称为比压。 一般在40-200MPa Max=500MPa。 实际上,并非在如此大的压力下凝固,因内浇口很 小,压力都转化为极高的充填速度,随后冷凝 高速: 充填速度为0.5~120m/s,一般为5~50m/s,充填时 间很短,一般为0.01~0.2秒。最短为千分之几秒。 由于金属充填型腔的这种特点,使压力铸造的工艺 和生产过程,压铸件的结构和其它性能都具有自己的特 征。
由于存在着上述压铸过程的工艺特性,因而决定了压铸 生产和压铸出的零件便具有一系列特点: 优点: 1. 铸件壁可很薄, 形状可极复杂,轮廓清晰。即可清晰地铸 出壁极薄,形状极复杂的铸件。 压铸零件的轮廓极为清晰,对薄壁键槽、凸凹多变的部 位都能得到完整无缺的形状。通常壁厚为1~6mm,小件还可 更薄。 最小壁厚 锌 0.3mm 铝 0.5mm 最小铸孔 0.75mm 最小螺纹距 0.75mm 从所得铸件的形状和结构的复杂程度来说,压铸比其它铸 造方法具有更为显著的优越性。
压铸工艺及模具设计

2003年
2004年
23
2005年我国压铸件主要用户行业需求量和比
81400 t例
一般机械及其
101900 t
他领域 9.40%
电器、电子
和电脑
11.80%
138200 t 五金、玩具
、车模 16.00%
542700 t 汽车和摩
托车, 62.80%
24
25
26
27
28
2、发展展望
➢自主开发先进压铸机、熔炼设备和其他 辅助装备; ➢压铸模CAD/CAM/CAE技术; ➢注重薄壁、复杂形状和高性能铝合金压 铸技术的开发与应用; ➢镁合金压铸的发展及应用; ➢半固态成形技术。
20
(二)国内压铸的发展
21
1、发展现状
中国模具行业发展迅猛,1996年~2004年其 产量年均增长率为14%,2003年压铸模行业的 产值达38亿元。
目前,国产模具只能满足市场需求的80%左 右,其中又以中、低档模具为主;在生产大型、 复杂的精密模具方面,其工艺技术、模具质量、 使用寿命以及生产能力等均不能满足国民经济发 展的需要。
22
2000年至2004年全国压铸件总产量与汽车 产量增长情况
5000000 4500000 4000000 3500000 3000000 2500000 2000000 1500000 1000000 500000
0
汽车总产量/辆 其中轿车产量/辆 压铸件总产量/t
2000年 2001年
2002年
4
压铸工艺过程演示
5
产品图 工艺设计 模具设计 模具制造
模具安装
模具预热
喷刷涂料 合模 浇注
压铸成形 开模取件
压力铸造工艺概述总结(必备3篇)

压力铸造工艺概述总结第1篇压铸分为以下四个过程:a、合模b、压射c、开模d、推出及复位其中最关键的是压射过程:从压射冲头开始移动到型腔充满保压(热室压铸机),或者至增压结束(冷室压铸机)为止压力、速度是压射过程中两个重要工艺参数,记录压射过程中压力和速度的动态特性曲线称为压射过程曲线压射过程中,随着压射冲头的位移,速度和压力都是按设定的模式变化液态金属在压室与型腔中的运动可分解成四个阶段,目前使用的大中型压铸机为四级压射,中小型压铸机多为三级压射(将第二、第三阶段合为一个阶段),而热室压铸主要以两个阶段压射为主(一速升液和二速填充)第一阶段 τ_1 :从压射冲头起始位置至越过浇料口位置特征:低压低速、运动平稳,防止金属液从浇料口溢出,有利于气体排出第二阶段 τ_2 :从越过浇料口位置到金属液充满至内浇口处特征:压力增大,压射冲头速度加快,越过浇料口位置后,压射压力提高,压射冲头速度加快,金属液充满压室至浇注系统,该阶段应防止卷气,尽量避免金属液提前进入型腔第三阶段 τ_3 :从金属液充满内浇口处至型腔完成充满特征:压射压力再次升高,压射速度略有下降,充型速度最快,由于内浇口处截面积大幅度缩小,流动阻力剧增,压射速度略有下降,但此时充型速度最快第四阶段 τ_4 :充型结束特征:压射冲头停止运动,压力剧增,达到全过程的最高值,充满型腔后,增压压力对凝固中的金属液进行压室,压射冲头可能稍有前移,金属液凝固后,增压压力撤除,压射过程结束压铸时,影响金属液充填成型的因素很多,主要有压力、速度、温度、时间等参数压射力:压铸机压射缸内工作液作用于压射冲头,使其推动金属液充填模具型腔的力,称为压射力压射力 F_y=P_g×(πD^2)/4Pg-压射缸内的工作压力,Pa D-压射缸直径,m比压:压室内压铸合金液单位面积上所受的力,即压铸机的压射力与压射冲头截面积之比,充填时的比压称为压射比压,有增压机构时,增压后的比压称为增压比压,它决定了压铸件最终所受压力和这时所形成的胀模力的大小压射比压 P_b=(4F_y)/(πd^2 )胀模力:压铸过程中,金属液充填型腔时,给型腔壁和分型面的压力称为胀模力,压铸过程中,最后阶段的增压比压通过金属液传给压铸模,此时的胀模力最大,为了防止压铸模被胀开,锁模力要大于胀模力在合模方向上的合力胀模力 F_z=P_b×AA-压铸件、浇口、排溢系统在分型面上的投影面积之和选择合适的比压可以改善压铸件的力学性能铸件在较高的比压下凝固,其内部微小孔隙或气泡被压缩,内部组织的致密度和强度较高,但随着比压过高,铸件的塑性指标下降,强度也会下降,力学性能下降较高的压射比压可以提高金属液的充模能力,防止铸件产生冷隔或充填不足的缺陷,轮廓较为清晰,但比压过大,会加剧金属液对型腔的冲击,加速模具的磨损,一般在保证压铸件成形和使用要求的前提下,选用较低的比压速度有压射速度和内浇口速度两种形式压射速度(冲头速度):压射冲头推动金属液的移动速度,也就是压射冲头的速度内浇口速度(充型速度):金属液通过内浇口处的线速度称为内浇口速度内浇口速度 v_n=\frac{πd^2}{4A_n} v_y=η \sqrt{\frac{2P_b}{ρ}}v_n -内浇口速度(m/s)v_y -压射速度(m/s)d-压射冲头(或压室)直径(m)A_n -内浇口截面积( m^2 )η-阻力系数,一般取ρ -合金的液态密度(kg/ m^3 )压射力大,内浇口速度高;合金液密度大,内浇口截面积大,内浇口速度低,在压铸过程中,通过调整压射速度,改变压射冲头直径、比压及内浇口截面积等,都可以直接或间接调整内浇口速度压铸的温度主要指合金浇注温度和压铸模的温度合金浇注温度指的是从压室进入型腔时压铸合金液的平均温度,经验证明,在压力较高的情况下,应尽可能降低浇注温度,最好在压铸合金液呈粘稠“粥状”时压铸,这样可以减少型腔表面温度的波动和压铸合金液对型腔的冲蚀,但对含硅量高的铝合金,则不宜使压铸合金液呈“粥状”时压铸,否则硅将大量析出,以游离状态存在于铸件内部,使加工性能变坏。
压力铸造设备及其工艺PPT资料(完整版)

常见问题与解决方案
金属液流动不畅或填充不满
可能是由于金属温度过低、压力不足或模具设计不合理等原因导致。
产品表面质量差
可能是由于模具表面粗糙、金属液温度过高或冷却不充分等原因导致。
常见问题与解决方案
• 产品尺寸精度低:可能是由于模具磨损、温度变 化或注射压力不稳定等原因导致。
常见问题与解决方案
01
清理检查
对取出的金属件进行清 理和检查,确保质量符
合要求。
模具设计与制造技术
模具设计
01
04
制造技术
根据产品形状和尺寸要求,设计合理的模 具结构。
02
05
采用先进的加工设备和工艺,确保模具的 加工精度和表面质量。
选择适当的模具材料和制造工艺,确保模 具的耐用性和精度。
03
06
对模具进行必要的热处理和表面处理,提 高其耐磨性和耐腐蚀性。
用效率,降低生产成本。
智能化、自动化压力铸造设备
02
引入人工智能、机器学习等先进技术,实现压力铸造设备的智
能化、自动化生产,提高生产精度和效率。
多功能、复合型压力铸造设备
03
开发具有多种功能和复合型的压力铸造设备,满足不同领域和
行业的多样化需求。
行业应用拓展空间分析
航空航天领域
轻质、高强度的铝合金、钛合金等材 料的压力铸造技术在航空航天领域具 有广阔的应用前景。
应用领域与市场需求
应用领域
汽车制造、航空航天、电子电器、建筑五金、玩具礼品等行业。
市场需求
随着制造业的快速发展,对压力铸造设备的需求不断增加。市场需要更高效、更精密、更自动化的压力铸造设备 ,以满足不断提高的产品质量和生产效率要求。同时,随着环保意识的提高,市场对环保型压力铸造设备的需求 也在逐步增加。
第3章熔炼和铸造
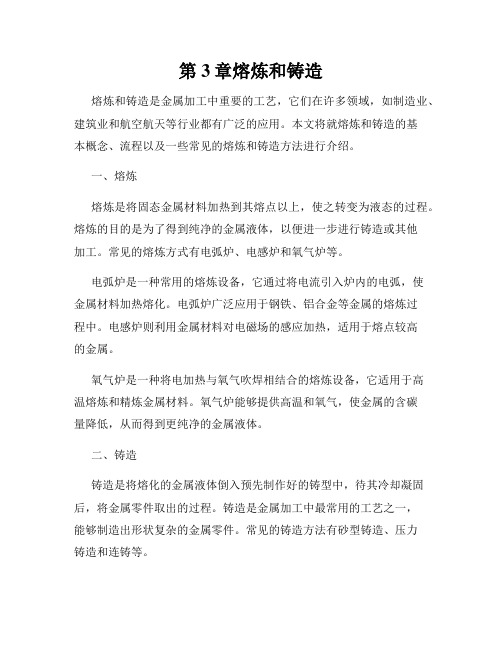
第3章熔炼和铸造熔炼和铸造是金属加工中重要的工艺,它们在许多领域,如制造业、建筑业和航空航天等行业都有广泛的应用。
本文将就熔炼和铸造的基本概念、流程以及一些常见的熔炼和铸造方法进行介绍。
一、熔炼熔炼是将固态金属材料加热到其熔点以上,使之转变为液态的过程。
熔炼的目的是为了得到纯净的金属液体,以便进一步进行铸造或其他加工。
常见的熔炼方式有电弧炉、电感炉和氧气炉等。
电弧炉是一种常用的熔炼设备,它通过将电流引入炉内的电弧,使金属材料加热熔化。
电弧炉广泛应用于钢铁、铝合金等金属的熔炼过程中。
电感炉则利用金属材料对电磁场的感应加热,适用于熔点较高的金属。
氧气炉是一种将电加热与氧气吹焊相结合的熔炼设备,它适用于高温熔炼和精炼金属材料。
氧气炉能够提供高温和氧气,使金属的含碳量降低,从而得到更纯净的金属液体。
二、铸造铸造是将熔化的金属液体倒入预先制作好的铸型中,待其冷却凝固后,将金属零件取出的过程。
铸造是金属加工中最常用的工艺之一,能够制造出形状复杂的金属零件。
常见的铸造方法有砂型铸造、压力铸造和连铸等。
砂型铸造是一种常见的铸造方法,其原理是在铸型中填充一定湿度的砂料,然后将熔化的金属液体倒入铸型中,待其冷却凝固后,取出金属零件。
砂型铸造通常用于制造大型、形状复杂的金属零件。
压力铸造是一种高效、高精度的铸造方法,能够制造出高质量的金属零件。
在压力铸造过程中,金属液体通过压力喷射进入铸型,然后通过压力固化和冷却,最终得到所需的金属零件。
连铸是一种连续铸造的方法,可以实现高效的金属生产。
在连铸过程中,金属液体连续地流过冷却水口,形成连续的结晶体,最后拉出所需的金属线材、板材或型材。
三、总结熔炼和铸造是金属加工中不可或缺的工艺。
熔炼通过加热金属材料使之熔化,得到金属液体;铸造则是将熔化的金属液体倒入铸型中,最终得到所需的金属零件。
熔炼和铸造通常采用不同的设备和工艺,如电弧炉、砂型铸造等。
随着科技的进步,熔炼和铸造工艺得到了不断的改进和创新,新的设备和工艺也被应用于熔炼和铸造过程中。
压力铸造
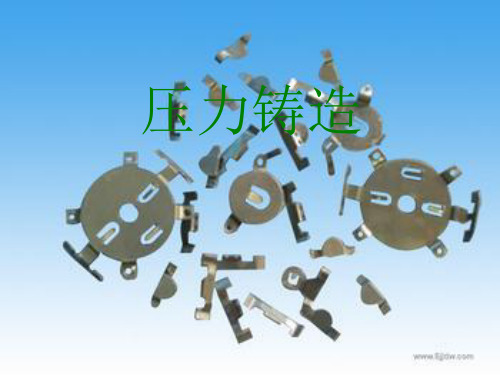
二、压铸定义及特点
1. 压铸定义及特点 压力铸造(简称压铸)是在压铸机的压室内,浇入 液态或半液态的金属或合金,使它在高压和高速下 充填型腔,并且在高压下成型和结晶而获得铸件的 一种铸造方法。 由于金属液受到很高比压的作用,因而流速很高, 充型时间极短。高压力和高速度是压铸时液体金属 充填成型过程的两大特点,也是压铸与其他铸造方 法最根本区别之所在。 比如压射比压在几兆帕至几十兆帕范围内,甚至高 达500MPa;充填速度为0.5—120m/s,充型时间很 短,一般为0.01-0.2s,最短只有干分之几秒。
六、压铸的应用范围
压铸是近代金属加工工艺中发展较快的一种高效率、少无切削的 金属成型精密铸造方法,是一种“好、快、省”高经济双效益的 铸造方法。 压铸零件的形状大体可以分为六类: 1)圆盘类——号盘座等; 2)圆盖类——表盖、机盖、底盘等; 3)圆环类——接插件、轴承保持器、方向盘等; 4)筒体类——凸缘外套、导管、壳体形状的罩壳盖、上盖、仪表 盖、探控仪表罩、照像机壳与化油器等; 5)多孔缸体、壳体类——汽缸体、汽缸盖及油泵体等多腔的结构 较为复杂的壳体(这类零件对机械性能和气密性均有较高的要求, 材料一般为铝合金)。例如汽车与摩托车的汽缸体、汽缸盖; 6)特殊形状类——叶轮,喇叭、字体由筋条组成的装饰性压铸件 等。
缺点: 1) 压铸型结构复杂,制造费用高,准备周期长,所以, 只适用于定型产品的大量生产; 2) 压铸速度高,型腔中的气体很难完全排出,加之金属 型在型中凝固快,实际上不可能补缩,致使铸件容易产生 细小的气孔和缩松,铸件壁越厚,这种缺陷越严重,因此, 压铸一般只适合于壁厚在6mm以下的铸件; 3) 压铸件的塑性低,不宜在冲击载荷及有震动的情况下 工作; 4) 另外,高熔点合金压铸时,铸型寿命低,影响压铸生 产的扩大应用。 综上所述,压力铸造适用于有色合金,小型、薄壁、复杂 铸件的生产,考虑到压铸其它技术上的优点,铸件需要量 为2000-3000件时,即可考虑采用压铸。
材料成型工艺学二复习思考题
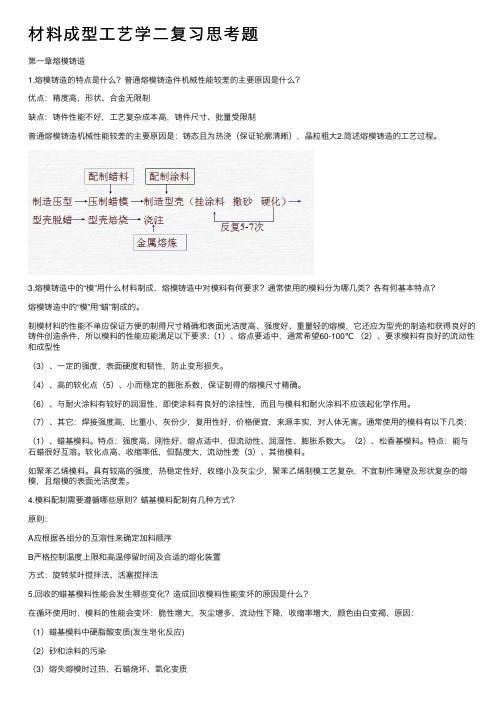
材料成型⼯艺学⼆复习思考题第⼀章熔模铸造1.熔模铸造的特点是什么?普通熔模铸造件机械性能较差的主要原因是什么?优点:精度⾼,形状、合⾦⽆限制缺点:铸件性能不好,⼯艺复杂成本⾼,铸件尺⼨、批量受限制普通熔模铸造机械性能较差的主要原因是:铸态且为热浇(保证轮廓清晰),晶粒粗⼤2.简述熔模铸造的⼯艺过程。
3.熔模铸造中的“模”⽤什么材料制成,熔模铸造中对模料有何要求?通常使⽤的模料分为哪⼏类?各有何基本特点?熔模铸造中的“模”⽤“蜡”制成的。
制模材料的性能不单应保证⽅便的制得尺⼨精确和表⾯光洁度⾼、强度好、重量轻的熔模,它还应为型壳的制造和获得良好的铸件创造条件,所以模料的性能应能满⾜以下要求:(1)、熔点要适中,通常希望60-100℃(2)、要求模料有良好的流动性和成型性(3)、⼀定的强度,表⾯硬度和韧性,防⽌变形损失。
(4)、⾼的软化点(5)、⼩⽽稳定的膨胀系数,保证制得的熔模尺⼨精确。
(6)、与耐⽕涂料有较好的润湿性,即使涂料有良好的涂挂性,⽽且与模料和耐⽕涂料不应该起化学作⽤。
(7)、其它:焊接强度⾼,⽐重⼩,灰份少,复⽤性好,价格便宜,来源丰实,对⼈体⽆害。
通常使⽤的模料有以下⼏类:(1)、蜡基模料。
特点:强度⾼、刚性好、熔点适中,但流动性、润湿性、膨胀系数⼤。
(2)、松⾹基模料。
特点:能与⽯蜡很好互溶。
软化点⾼、收缩率低,但黏度⼤,流动性差(3)、其他模料。
如聚苯⼄烯模料。
具有较⾼的强度,热稳定性好,收缩⼩及灰尘少,聚苯⼄烯制模⼯艺复杂,不宜制作薄壁及形状复杂的熔模,且熔模的表⾯光洁度差。
4.模料配制需要遵循哪些原则?蜡基模料配制有⼏种⽅式?原则:A应根据各组分的互溶性来确定加料顺序B严格控制温度上限和⾼温停留时间及合适的熔化装置⽅式:旋转浆叶搅拌法、活塞搅拌法5.回收的蜡基模料性能会发⽣哪些变化?造成回收模料性能变坏的原因是什么?在循环使⽤时,模料的性能会变坏:脆性增⼤,灰尘增多,流动性下降,收缩率增⼤,颜⾊由⽩变褐,原因:(1)蜡基模料中硬脂酸变质(发⽣皂化反应)(2)砂和涂料的污染(3)熔失熔模时过热,⽯蜡烧坏、氧化变质6.哪⼏种处理⽅法可以使旧的蜡基模料的性能得到⼀定程度的恢复?(1)盐酸(硫酸)处理法(2)活性⽩⼟处理法(3)电解法7.熔模铸造的型壳是如何制造的(由哪三个基本步骤组成)?熔模铸造制造⼀般铸件时型壳需要涂挂⼏层?型壳的制造⼯艺:涂覆涂料→撒砂→⼲燥硬化8.熔模铸造制造型壳时可以采⽤哪⼏种粘结剂,各种粘结剂有何特点?它们的硬化机理是什么,⼯业上分别采⽤什么⽅法硬化?第⼀种是硅酸⼄脂⽔解液。
压力铸造工艺介绍
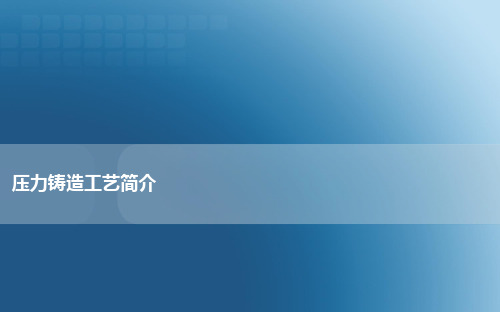
•
8、业余生活要有意义,不要越轨。20 20年12 月13日 星期日 5时39 分40秒0 5:39:40 13 December 2020
•
9、一个人即使已登上顶峰,也仍要自 强不息 。上午 5时39 分40秒 上午5时 39分05 :39:402 0.12.13
• 10、你要做多大的事情,就该承受多大的压力。12/13/
2020 5:39:40 AM05:39:402020/12/13
• 11、自己要先看得起自己,别人才会看得起你。12/13/
谢 谢 大 家 2020 5:39 AM12/13/2020 5:39 AM20.12.1320.12.13
4
3.压铸工艺三大要素
主要压铸合金 铝合金
锌合金
镁合金 铅锡合金 铜合金
浇铸温度 650~680℃
420~440℃
640~680℃ 200℃左右 900~980℃
特点及性能
1. 密度低,可生产要求减轻质量的零部件 2. 强度高,塑性好 3. 抗氧化腐蚀性能好
1. 良好的压铸特性:容易压铸形状复杂,尺寸精度高的产品 2. 抗拉强度高和硬度高,冲击韧性和伸长率较好 3. 良好的加工性能:产品表面,容易做各种表面处理 4. 生产高效
1. 密度低,比强度高 2. 流动性好 3. 减震性、磁屏蔽性能好
1.熔点低,流动性好,收缩小 2.可塑性好 3.铸件表面光滑,易做各种表面处理 因熔点高,模具寿命低,应减少使用
5
3.压铸工艺三大要素
3.2 压铸机
压铸机一般分为冷压室压铸机和热压室压铸机两大类。 冷压室压铸机按其压室结构和布置方式分为卧式压铸机和立式压铸机两种。
2
2.压力铸造
2.1 定义
压力铸造工艺介绍-PPT
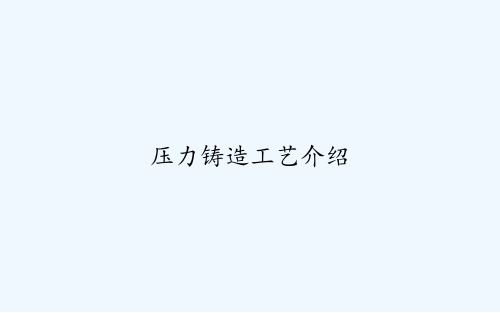
1. 铸造简介
1.1 定义
材料成型工艺:焊接、铸造、压力加工(锻造和冲压) 铸造:熔炼金属,制造铸型,并将熔融金属浇入铸型,凝固后获得具有一定形状、尺寸和性能金属零件毛坯的成型方法
1.2 铸造分类
按造型分类:① 砂型铸造;② 特种铸造——金属模铸造;脱蜡铸造 按成型工艺分类:① 重力浇铸;② 压力铸造
4.压铸工艺的工艺参数
4.1 压铸各阶段
t1:金属液在压室中未承受压力的时间 t2:金属液于压室中在压射冲头的作用下,通过内 浇口充填型腔的时间 t3:充填刚刚结束时的瞬间 t4:保压凝固结晶时间
4.压铸工艺的工艺参数
4.2 压铸图识别
3.1 压铸合金
压铸合金应具备的特性: 易于压铸:流动性、收缩性、出模性等尽可能满足压铸的要求。 机械性能:强度、延伸性、脆性等满足产品的设计要求。 机械加工性:易于加工及加工表面的质量能达到产品设计的要求。 表面处理性:抛光、电镀、喷漆、氧化等要求能达到产品设计的要求。 抗腐蚀性:产品在最终的使用环境下具有一定的抗腐蚀性。
卧式压铸机
热压室压铸机
3.压铸工艺三大要素
3.2.1 卧式压铸机工作原理
3.压铸工艺三大要素
3.2.2 立式压铸机工作原理
大家应该也有点累了,稍作休息
大家有疑问的,可以询问和交流
3.压铸工艺三大要素
3.2.3 热压室压铸机工作原理
3.压铸工艺三大要素
3.2.4 各压铸的压铸特点
卧式压铸: ①结构简单,操作程序少,生产效率高,易实现自动化 ②金属消耗少; ③能量损失少,使用更为广泛。 立式压铸: ①有余料切断、顶出功能; ②空气不易随金属进入压室; ③金属液进入型腔经过转折,压力消耗大~缺点 热压室压铸: ①生产工序简单、生产效率高、易实现自动化 ②金属消耗少、工艺稳定、无氧化杂物、铸件质量好; ③压室和冲头长时间浸泡在高温金属液中,影响使用寿命,常用 于锌合金压铸。
- 1、下载文档前请自行甄别文档内容的完整性,平台不提供额外的编辑、内容补充、找答案等附加服务。
- 2、"仅部分预览"的文档,不可在线预览部分如存在完整性等问题,可反馈申请退款(可完整预览的文档不适用该条件!)。
- 3、如文档侵犯您的权益,请联系客服反馈,我们会尽快为您处理(人工客服工作时间:9:00-18:30)。
压力铸造
--
❖3.1 概述
压力铸造(定义):简称压铸,它是将液态金属 或半固态金属在高压下快速充填到金属模的型 腔,并在压力下快速凝固而获得铸件的一种成 形方法。
在压力铸造中,一般作用于金属上的压力在20~ 200MPa范围,充型的初始速度为15~70m/s,充型 时间仅为0.01~0.2s。因此,高压和高速是压铸成形 的重要特征,也是与其他铸造成形法的根本区别。压 力铸造是所有铸造成形方法中生产速度最快的,在汽 车、摩托车、电器仪表、电信器材、医疗器械、日用 五金以及航天航空工业等方-- 面都有广泛的应用。
(立体形状)来说,一般的成形工艺方法是不易达到的,所 以压铸法不仅适合于形状复杂的铸件的生产,更适合于大批 量的生产。
王家压铸厂 八小时,500件 = 60±x个/小时
--
缺点
6. 压铸件内部有气孔,对于有要求的零件要采取特 殊的工艺措施才能满足要求。
由于压铸过程中,熔融金属在充填时的流动速度大,致使 型腔中气体来不及全部排出而卷入铸件中,处于内部的即为内 部气孔。
压力铸造的实质、特点及应用
一、压力铸造的实质:
压力铸造(简称压铸)的实质,是在高压作用下, 使液态或半固态金属以较高的速度充填压铸型型腔,并 在压力作用下凝固而获得铸件的方法。即压力下浇注和 压力下凝固。
两大特征: 高压 高速
这也是压铸区别于其它铸造方法的最基本特征。
--
高压:
比压:作用在铸件上单位面积上的压力称为比压。 一般在40-200MPa Max=500MPa。
--
(3)经济效果优良
由于铸件精度高,尺寸稳定,加工余量少, 表面光洁。压铸件的加工余量一般在0.2~ 0.5mm范围,表面粗度在Ra3.2μm以下。 只要对零件进行少量加工便可进行装配,有 的零件甚至不用机械加工就能直接装配使用。 减少后续加工费用。同时金属利用率高。
其他: 采用镶铸法可省去装配工序并简化制造工艺。镶铸的材料一 般为钢、铸铁、铜、绝缘材料等,镶铸体的形状有圆形、管 形、薄片等。利用镶铸法可制备出有特殊要求的铸件。 铸件表面可进行涂覆处理、压铸出螺纹、线条、文字、图案 等
2. 压铸件精度高,光洁度高,尺寸稳定,一致性好, 加工余量很少。
压铸模型腔具有较高的精度和很高的表面光洁度, 故压铸件与其它铸造方法比,不但具有更高的精度 和表面光洁度,而且在生产过程中,各个铸件尺寸 一致性好,稳定性也好,从而具有很好的装配互换 性。
各种铸件精度比较
压铸
熔模
砂型
尺寸精度 表面光洁度
实际上,并非在如此大的压力下凝固,因内浇口很 小,压力都转化为极高的充填速度,随后冷凝
高速: 充填速度为0.5~120m/s,一般为5~50m/s,充填时
间很短,一般为0.01~0.2秒。最短为千分之几秒。
由于金属充填型腔的这种特点,使压力铸造的工艺
和生产过程,压铸件的结构和其它性能都具有自己的特
征。
--
• 压力铸造存在的问题:
• ① 由于液体金属充型速度极快,型腔中的气体很难排除,便 以气孔形式存留于铸件中,因此普通压铸法压铸的铸件不能 进行热处理或焊接(加热时气体膨胀将导致铸件鼓泡而报 废),也不适于比较深的机加工,以免铸件表面显出气孔。
• ② 现有模具材料主要适应于低熔点的合金,如锌、铝、镁等 合金。生产铜合金、黑色金属等高熔点合金,其模具材料存 在着较大的问题,主要是模具的寿命非常短。
• ③ 压铸设备投资高,压铸模制造复杂,周期较长,费用较高, 一般不适用于小批量生产。
• ④ 由于充填型腔时金属液的冲击力大,一般压铸不能使用砂 芯,因此不能压铸具有复杂内腔(内凹)结构的铸件,如闭 舵结构的铝合金发动机缸体。--
由于存在着上述压铸过程的工艺特性,因而决定了压铸 生产和压铸出的零件便具有一系列特点:
优点: 1. 铸件壁可很薄, 形状可极复杂,轮廓清晰。即可清晰地铸 出壁极薄,形状极复杂的铸件。
压铸零件的轮廓极为清晰,对薄壁键槽、凸凹多变的部 位都能得到完整无缺的形状。通常壁厚为1~6mm,小件还可 更薄。
最小壁厚 锌 0.3mm 铝 0.5mm
最小铸孔 0.75mm 最小螺纹距 0.75mm
从所得铸件的形状和结构的复杂程度来说,压铸比其它铸 造方法具有更为显著的优越性-。-
镶铸法就是在压铸零件的特殊部位上铸入(嵌入)所需的其它材 料的制件如铸入磁铁、铜套,钢衬垫,金属管,绝缘材料等,既 满足特殊部位的使用性能要求。又省略了装配工序,简化了制造 工艺。
--
--
5. 压铸生产效率很高 压铸生产时,每一次操作循环时间约为5秒~3分钟。一
般10秒~1分钟。 小机器,每小时达300次。这样高的效率,对于结构零件
3. 压铸件表面组织致密。具有较高的强度和表面硬度
压铸件
充填时间很短, 金属型中冷凝
速度极快
压力下结晶
故压铸件组织致密,晶粒细化,有较高的强度和表面硬 度(σb比砂铸件高25-30%,但延伸率较低),特别是壁的厚 度适当而均匀时,强度更高,又因表层激冷,故表层更是坚
--
实耐磨。
4. 在压铸中采用镶铸法可以省略装配工序,简化制造工艺。 在压铸中,可以采用镶铸法,来制造出有特殊要求的零件。
ZJ2-ZJ1
ZJ3-ZJ2
(▽5~▽7、▽8) (▽3~▽6)
3.2-0.8
6.3-1.6
ZJ7-ZJ6 12.5
--
所有铸造方法中,该法的精度,光洁度最高,可达精车 和磨床加工程度。因此,压铸件大多数情况下,只经少量机 加工(打磨)就可以装配使用,加工余量一般在0.2-0.5mm. 加工部位也是很少几个部分。有些件,可不经任何机加工就 可装配使用,充分体现了压铸的少切削或无切削成型工艺的 特点。
--
• 3.1.1 压力铸造特点 (1)产品质量好
尺寸精度高,CT6—7级。表面粗糙度低,5—8 级。强度和硬度高,比砂型高25%—30%,但延 伸率低70%。可以制得薄壁复杂且轮廓清晰的铸 件。现代超薄铝合金压铸技术可制造0.5mm厚的 铸件,如铝合金笔记本电脑外壳。最小铸出孔 0.7mm。
(2)生产效率高。 压力铸造的生产周期短,一次操作的循环时间约 为5s~3min,且易实现机械化和自动化。这种 方法适于大批量的生产。