整合版 电炉炼钢计算部分要点
炼铁常用计算

炼铁常用计算一、 安全容铁量:一般以渣口中心线至铁口中心线间炉缸容积的60%所容铁量为安全容铁量,无渣口高炉以风口中心线与铁口中心线的距离减0.5m 计算,计算公式:240.6d T h πγ=安铁 T 安—炉缸安全容铁量,t ;d-炉缸直径,m ;γ铁-铁水密度,(7.0t/m 3)h-风口中心线到铁口中心线之间距离减0.5m 后的距离。
例如:846m 3高炉安全容铁量为:T 安=0.6×23.147.24⨯×2.7×7≈461(吨)二、 冶炼周期:指炉料在炉内停留时间,这个指标可以反映炉料下降速度,计算公式:或12"u V V N ε-=(V +V )(1-)T-冶炼周期(时间); N-一个冶炼周期的料批数;P-生铁日产量(吨); V u -高炉有效容积(m 3);'V -每吨生铁所需炉料体积; V 1-炉喉料面上的体积(m 3); ε-炉料在炉内压缩率; V 2-炉缸风口中心线以下容间体积; V n -高炉有效容积。
"V —每批炉料的炉外容积。
例如:846m 3高炉,假定日产生铁2500吨,每批料焦批6.5t ,矿批18.5t ,焦批比重1.8,压缩比13%,冶炼周期248462500 2.17 4.3T ⨯⨯==(1-13%)(小时)一个冶炼周期的料批数:'24n V PV T ε=(1-)84624.831.6N -==(18.9+130.2)(1-13%)(批) 取32批三、 鼓风动能计算公式:221430324.20110Q E -⨯⨯=⨯⨯T p (n F )E-鼓风动能 Kg (f )·m/s;n-风口数量 个;F-工作风口平均面积 m 2/个;P-热风压力MPa (0.1013+表);Q 0=2IV n ,Nm 3/min;Vn-高炉有效容积 m 3。
例如:846m 3高炉风口个数20个,平均风口面积0.0138,热风压力330KPa ,风量2700,风温1100℃,求鼓风动能。
电炉炼钢的配料计算_装料方法及操作要点
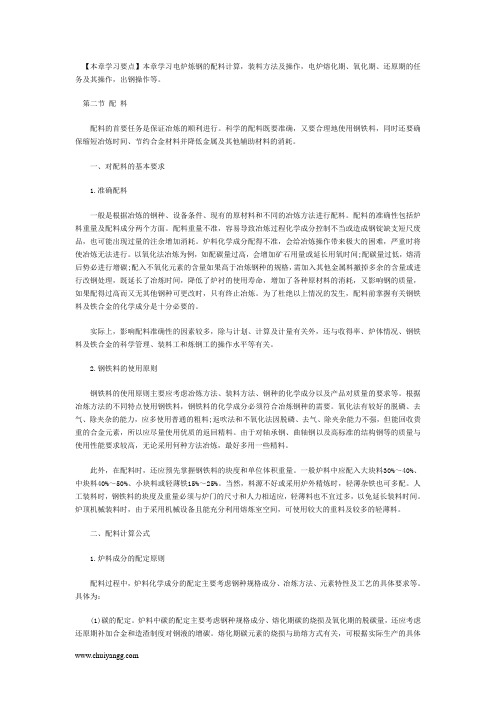
【本章学习要点】本章学习电炉炼钢的配料计算,装料方法及操作,电炉熔化期、氧化期、还原期的任务及其操作,出钢操作等。
第二节配料配料的首要任务是保证冶炼的顺利进行。
科学的配料既要准确,又要合理地使用钢铁料,同时还要确保缩短冶炼时间、节约合金材料并降低金属及其他辅助材料的消耗。
一、对配料的基本要求1.准确配料一般是根据冶炼的钢种、设备条件、现有的原材料和不同的冶炼方法进行配料。
配料的准确性包括炉料重量及配料成分两个方面。
配料重量不准,容易导致冶炼过程化学成分控制不当或造成钢锭缺支短尺废品,也可能出现过量的注余增加消耗。
炉料化学成分配得不准,会给冶炼操作带来极大的困难,严重时将使冶炼无法进行。
以氧化法冶炼为例,如配碳量过高,会增加矿石用量或延长用氧时间;配碳量过低,熔清后势必进行增碳;配入不氧化元素的含量如果高于冶炼钢种的规格,需加入其他金属料撤掉多余的含量或进行改钢处理,既延长了冶炼时间,降低了炉衬的使用寿命,增加了各种原材料的消耗,又影响钢的质量,如果配得过高而又无其他钢种可更改时,只有终止冶炼。
为了杜绝以上情况的发生,配料前掌握有关钢铁料及铁合金的化学成分是十分必要的。
实际上,影响配料准确性的因素较多,除与计划、计算及计量有关外,还与收得率、炉体情况、钢铁料及铁合金的科学管理、装料工和炼钢工的操作水平等有关。
2.钢铁料的使用原则钢铁料的使用原则主要应考虑冶炼方法、装料方法、钢种的化学成分以及产品对质量的要求等。
根据冶炼方法的不同特点使用钢铁料,钢铁料的化学成分必须符合冶炼钢种的需要。
氧化法有较好的脱磷、去气、除夹杂的能力,应多使用普通的粗料;返吹法和不氧化法因脱磷、去气、除夹杂能力不强,但能回收贵重的合金元素,所以应尽量使用优质的返回精料。
由于对轴承钢、曲轴钢以及高标准的结构钢等的质量与使用性能要求较高,无论采用何种方法冶炼,最好多用一些精料。
此外,在配料时,还应预先掌握钢铁料的块度和单位体积重量。
电炉冶炼配料与计算

电炉冶炼配料与计算配料的要求与计算配料的首要任务是保证冶炼的顺利进行。
科学的配料既要准确,又要合理地使用钢铁料,同时还要确保缩短冶炼时间、节约合金材料并降低金属及其他辅助材料的消耗。
一、对配料的基本要求1、准确配料配料的准确性包括炉料重量及配料成分两个方面。
配料重量不准,容易导致冶炼过程化学成分控制不当或造成铸件浇不足,也可能出现过量而增加消耗。
炉料化学成分配得不准,会给冶炼操作带来困难,严重时将使冶炼无法进行。
以氧化法冶炼为例,如配碳量过高,会增加矿石用量或延长用氧时间;配碳量过低,熔清后势必进行增碳;如炉料中S、P太高,给炉前操作带来极大困难,不仅延长冶炼时间,而且对炉衬侵蚀严重,有时甚至要终止冶炼。
为了杜绝以上情况,配料前掌握有关钢铁料及铁合金的化学成分是十分必要的。
2、钢铁料的使用原则钢铁料的使用原则主要考虑冶炼方法、装料方法、钢种的化学成分以及产品对质量的要求等。
此外,在配料时,还应预先掌握好钢铁的块度和单位体积重量。
一般炉料中应配入大块料30~40%、中块料40~50%、小块料或轻薄料15~25%。
二、配料计算公式1、装入量=出钢量/钢铁综合收得率2、配料量=装入量—铁合金总量—矿石进铁量—余钢回炉量3、铁矿石进铁量=铁矿石加入量某含铁量某铁的收入率矿石加入量一般按出钢量的4%计算,矿石含铁量为55%,铁的收得率按80%回收,炉料总的综合收得率波动于92~96%,一般按94%计算。
装料方法及要求一、装料方法电炉炼钢最常见的是冷装料,按其入炉方式不同分为人工装料和机械装料。
人工装料多用于公称容量小于3t的电炉,缺点是装料时间长、生产率低、劳动强度大。
料筐顶装料是目前最理想的装料方法,速度快、热损失小,且炉料可事先提前装好,布料合理。
二、对装料的要求为了缩短时间,保证合金元素的收得率,降低电耗和提高炉衬的使用寿命,装料时要求做到:准确无误、装得致密、布料合理及快速入炉。
装料前,配料工要认真按计划炉号、钢种的要求配料,依据不同钢种工艺的要求,认真分析计算,准确配料。
整合版转炉炼钢计算部分

整合版转炉炼钢计算部分转炉炼钢是一种常用的工业炼钢方法,通过氧气吹炼可以去除钢中的杂质,得到高品质的钢材。
在转炉炼钢中,有一些重要的计算部分,包括吹炼时间、温度控制、钢水负荷等。
接下来将详细介绍这些计算部分。
1.吹炼时间的计算:吹炼时间是指从氧气吹入开始到钢水净化结束的时间。
吹炼时间的长短直接影响到钢水净化的效果和转炉的生产能力。
一般来说,吹炼时间可以通过下式计算:吹炼时间=钢水重量/(氧气流量×氧气纯度×铁素量)其中,钢水重量是指待净化的钢水的质量,氧气流量是指进入转炉的氧气的流量,氧气纯度是指进入转炉的氧气的纯度,铁素量是指待净化的钢中的铁含量。
2.温度控制的计算:在转炉炼钢过程中,温度的控制非常重要。
温度的过高或过低都会对钢水的成分和性能产生负面影响。
温度的控制主要通过加入适量的生铁和废钢来实现。
具体的计算方法如下:温度=(钢水质量×钢水温度+生铁质量×生铁温度+废钢质量×废钢温度)/(钢水质量+生铁质量+废钢质量)其中,钢水质量是指待净化的钢水的质量,钢水温度是指待净化的钢水的温度,生铁质量是指加入的生铁的质量,生铁温度是指加入的生铁的温度,废钢质量是指加入的废钢的质量,废钢温度是指加入的废钢的温度。
3.钢水负荷的计算:钢水负荷是指转炉的产能,即单位时间内可以生产的钢水的质量。
钢水负荷的计算可以通过下式得到:钢水负荷=吹炼时间×钢水重量吹炼时间已经在第一部分进行了介绍,钢水重量是指待净化的钢水的质量。
4.吸收剂的计算:在转炉炼钢中,为了提高钢水中的硫含量,常常需要加入吸收剂。
吸收剂的计算可以通过如下方式进行:吸收剂重量=钢水重量×(目标硫含量-初始硫含量)/吸收剂含硫量其中,钢水重量是指待净化的钢水的质量,目标硫含量是希望得到的钢水的硫含量,初始硫含量是待净化的钢水的硫含量,吸收剂含硫量是吸收剂中的硫含量。
以上是转炉炼钢计算部分的详细介绍。
整合版 转炉炼钢 计算部分要点

转炉炼钢部分1.>已知转炉造渣碱度要求为3.0,铁水中含Si为1.2%,石灰有效CaO为70%,试计算吨钢石灰加入量是多少?解:石灰加入量= (2.14[%Si]/%CaO有效)×R×100= (2.14×1.2%/70)×3×100=110kg/t答:吨钢加入石灰110kg。
2.>某钢厂2000年生产Q235A80万吨,Q215B60万吨,另外还生产60Si2Mn45万吨。
该厂的优质钢比是多少?解:优质钢比(%)=优质钢产量(吨)/钢总产量(吨)×100%=45/(80+60+45)×100%=24.32%答:该厂的优钢比为24.32%。
3.>出钢量按73t,钢中氧为700ppm,理论计算钢水全脱氧需要加多少kg铝?(铝原子量为27,氧原子量为16)解:反应方程式:2Al+3[O]=(Al2O3)73t钢中700ppm[0]折合钢水含氧量:73×1000×0.07%=51.1kg设:51.1kg氧消耗X kg铝则:2×27/(3×16)=X/51.1得:X=2×27×51.1/(3×16)=57.5kg答:理论计算钢水全脱氧需要加57.5kg铝。
4.>已知在钢液中,元素百分含量(xi):碳0.11%,硅0.21%,锰0.42%,磷0.02%,硫0.03%,铜0.06%,其余成分不计。
各元素含1%对钢液凝固影响值(△ti)为:碳90,硅6.2,锰1.7,磷28,硫40,铜2.6;纯铁凝点为1539℃。
计算Q195的液相线温度(T液)。
解:T液=1539-∑(xi·△ti)=1539-0.11×90-0.21×6.2-0.42×1.7-0.02×28-0.03×40-0.06×2.6=1525℃答:Q195的液相线温度ΔT为1525℃5.>已知:铁水含硅0.80%,硅铁含硅74%,铁水装入量50t,要求配后铁水含硅1.2%,求硅铁配加量(kg)。
炼钢部分各种计算公式汇总
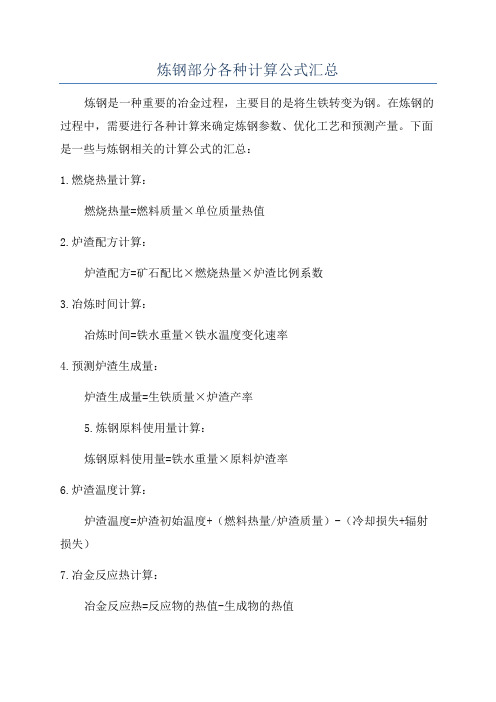
炼钢部分各种计算公式汇总炼钢是一种重要的冶金过程,主要目的是将生铁转变为钢。
在炼钢的过程中,需要进行各种计算来确定炼钢参数、优化工艺和预测产量。
下面是一些与炼钢相关的计算公式的汇总:1.燃烧热量计算:燃烧热量=燃料质量×单位质量热值2.炉渣配方计算:炉渣配方=矿石配比×燃烧热量×炉渣比例系数3.冶炼时间计算:冶炼时间=铁水重量×铁水温度变化速率4.预测炉渣生成量:炉渣生成量=生铁质量×炉渣产率5.炼钢原料使用量计算:炼钢原料使用量=铁水重量×原料炉渣率6.炉渣温度计算:炉渣温度=炉渣初始温度+(燃料热量/炉渣质量)-(冷却损失+辐射损失)7.冶金反应热计算:冶金反应热=反应物的热值-生成物的热值8.炉温控制计算:炉温控制=炉温目标值-炉温测量值9.耗氧量计算:耗氧量=氧气流量×氧浓度×燃烧公式系数10.炉渣替代率计算:炉渣替代率=炉渣替代量/炉渣生成量11.冷却水量计算:冷却水量=冷却热量/剪切热12.制氧气量计算:制氧气量=铁水含氧量×铁水重量×(氧气纯度/100)13.吹氧流量计算:吹氧流量=制氧气量/铁水供氧时间14.坩埚温度计算:坩埚温度=铁水温度+气氛温度15.炉水质量计算:炉水质量=炉水比例×矿石质量以上是一些与炼钢相关的计算公式的汇总。
当然,实际的炼钢过程非常复杂,还需要考虑其他因素如温度、压力、流量等等。
这些公式只是提供了一些基本的计算方法,实际应用中还需要根据具体情况进行适当的调整和修正。
电炉炼钢铁合金加入量计算法

电炉炼钢铁合金加入量计算法一、计算公式算法举例计算中有关问题的说明1、炉料的收得率炉料的收得率与炉料的好坏,炉料中能被氧化元素的含量以及冶炼方法等有关。
一般而言,炉料的收处率如下:氧化法为95~96%,不氧化法为96~97%,返回吹氧法为95~97%。
炉料的收处率简称收得率。
计算铁合金加入量时以炉料实重进行计算。
炉料实重=炉料重×收得率。
2、铁合金中合金元素的回收率炼钢中使用的镍、钴、铜、钼钨铁、铬铁、锰铁、钒铁、铌铁、矽铁等,作为合金化材料有冶炼操作规程规定的时期加入时,由于这些铁合金元素的回收率相当高,在计算中为了简化起见其回收率均可按100%计算。
在回收率低的元素有硼、钛、铝。
硼铁中硼的回收率一般为30~50%。
钛铁中钛的回收率一般为40~60%。
铝的回收率:当冶炼含铝量为1%左右的钢种时,铝在氧化渣扒出后加入时一般为50~60%,在还末期扒渣后加入时一般为65~80%,当冶炼含铝量较高的钢种时铝的回收率有所升高。
当冶炼含铝量高达5%左右的高铝钢时,铝的回收率可大于95%。
即使是对于硼铁、钛铁和铝,在计算时为了简便起见,同样可以把回收充的因素考虑在所控制的成分之上。
如以冶炼38CrMoAIA钢为例,铝的规格范围为0.70~1.10%,当采用扒还元渣后加入的工艺时,铝按1.20~1.30%加入,而将铝的回收率皆当作100%。
又比如冶炼高矽钢时,出钢前加入矽铁后不再分析矽的含量,这时虽将矽铁中矽的回收率当作100%,但控制成分时应将矽量偏上限控制。
铁合金中合金元素的回收率简称回收率。
收得率与回收率的意义相当,但为了使炉料与铁合金相区别故分别名为收得率与回收率。
在实际冶炼中控制钢的化学成分时,对于冶炼含铬、含锰而对炭量有规格要求的钢种时,为了便于炭量的调整,在加入铬铁锰铁进行合金化时,不宜一下就把铬、锰加到要求达到的成分,而应稍低于要求达到的成分,以便在补加铬铁、锰铁时,可使用高炭铬铁、高炭锰铁来补足不足的炭量。
电炉炼钢设计

0.523
0.811
0.012
0.095
0.017
4.319
0.171
0
H2O全部消耗
合计
1.15
1.764
4.279
0
0.008
0.047
7.248
质量分数
15.86
24.33
59.03
0.11
0.67
100
1计算条件是:常温(20C)、常压(0.1MPa)下空气相对湿度为70%;20C的饱和蒸汽压为0.0023;露点14C。先求湿空气体积4.302*(273+20)/(0.1-0.0023)=4.732m3;再算含水量。
.0.500
合计
2.891
0.827
0.281
0.332
0.192
0.347
0.129
0.086
0.059
5.144
%
56.20
16.08
5.46
6.45
3.73
6.75
2.51
1.67
1.15
100.01
1石灰中CaO被自身S还原,消耗0.003kgCaO
4)造新渣时加入石灰和火砖块带人的渣量。见表8-35.
8.1计算所需原始数据
基本原始数据有:冶炼钢种及其成分(见表8-24);原材料成分(见表8-25),炉料中元素烧损率(见8-26);合金元素回收率(见8-27);其他数据(见8-28)。
表8-24冶炼钢种及其成分
钢种
成分/%
备注
C
Si
Mn
P
S
Cr
Fe
Q235
0.14~0.22
Si<=0.30
整合版 电炉炼钢计算部分要点
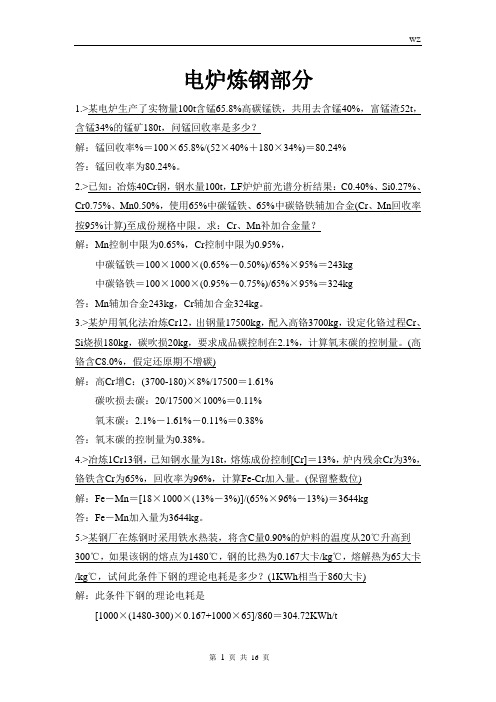
电炉炼钢部分1.>某电炉生产了实物量100t含锰65.8%高碳锰铁,共用去含锰40%,富锰渣52t,含锰34%的锰矿180t,问锰回收率是多少?解:锰回收率%=100×65.8%/(52×40%+180×34%)=80.24%答:锰回收率为80.24%。
2.>已知:冶炼40Cr钢,钢水量100t,LF炉炉前光谱分析结果:C0.40%、Si0.27%、Cr0.75%、Mn0.50%,使用65%中碳锰铁、65%中碳铬铁辅加合金(Cr、Mn回收率按95%计算)至成份规格中限。
求:Cr、Mn补加合金量?解:Mn控制中限为0.65%,Cr控制中限为0.95%,中碳锰铁=100×1000×(0.65%-0.50%)/65%×95%=243kg中碳铬铁=100×1000×(0.95%-0.75%)/65%×95%=324kg答:Mn辅加合金243kg,Cr辅加合金324kg。
3.>某炉用氧化法冶炼Cr12,出钢量17500kg,配入高铬3700kg,设定化铬过程Cr、Si烧损180kg,碳吹损20kg,要求成品碳控制在2.1%,计算氧末碳的控制量。
(高铬含C8.0%,假定还原期不增碳)解:高Cr增C:(3700-180)×8%/17500=1.61%碳吹损去碳:20/17500×100%=0.11%氧末碳:2.1%-1.61%-0.11%=0.38%答:氧末碳的控制量为0.38%。
4.>冶炼1Cr13钢,已知钢水量为18t,熔炼成份控制[Cr]=13%,炉内残余Cr为3%,铬铁含Cr为65%,回收率为96%,计算Fe-Cr加入量。
(保留整数位)解:Fe-Mn=[18×1000×(13%-3%)]/(65%×96%-13%)=3644kg答:Fe-Mn加入量为3644kg。
炼钢部分各种计算公式汇总
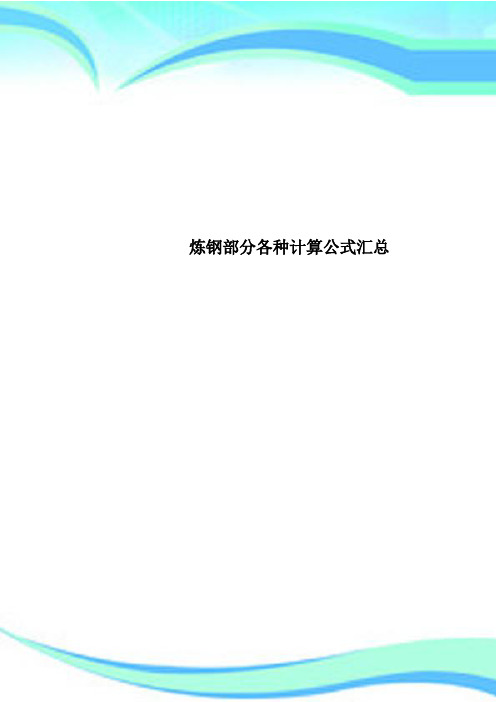
炼钢部分各种计算公式汇总————————————————————————————————作者: ————————————————————————————————日期:炼钢部分各种计算公式汇总1、转炉装入量装入量=错误!未定义书签。
2、氧气流量Q=错误!Q-氧气流量(标态),错误!或 错误!V-1炉钢的氧气耗量(标态),m3; t-1炉钢吹炼时间,min 或h 3、供氧强度 I=错误!I-供氧强度(标态),错误!未定义书签。
; Q -氧气流量(标态),错误!;T-出钢量,t注:氧气理论计算值仅为总耗氧量的75%~85%。
氧枪音速计算 α=(κgR T)1/2m/sα—当地条件下的音速,m/s ;κ—气体的热容比,对于空气和氧气,κ=1.4;g —重力加速度,9.81m/s 2;R —气体常数,26.49m/κ。
马赫数计算 M=ν/αM —马赫数;ν—气体流速,m/s ;α—音速,m/s。
冲击深度计算h冲=K 错误!未定义书签。
h 冲—冲击深度,m ;P0—氧气的滞止压力(绝对),㎏/㎝2;d0—喷管出口直径,m ;H 枪—枪位,m;ρ金—金属的密度,㎏/m 3;d c —候口直径,m ;B —常数,对低粘度液体取作40;K —考虑到转炉实际吹炼特点的系数,等于40。
在淹没吹炼的情况下,H=0,冲击深度达到最大值,即 hma x=P 00.5·d00.6ρ金0.4有效冲击面积计算R=2.41×104(错误!未定义书签。
)2R—有效冲击半径,m ;νmax —液面氧射流中心流速,m/s; νm ax =ν出错误!·错误!未定义书签。
ν出—氧射流在出口处的流速,m/s 。
金属-氧接触面积计算在淹没吹炼时,射流中的金属液滴重是氧气重量的3倍,吹入1m3氧气的液滴总表面积(金属-氧气的接触面积): S Σ=\f (3G 金,r 平均·ρ金)G金—1标米3氧气中的金属液滴重量=3×1.43㎏;r 平均—液滴的平均半径,m ;ρ金—金属液的密度,7×103㎏/m 3。
电炉铁合金冶炼主要技术经济指标计算方法

电炉铁合金冶炼主要技术经济指标计算方法一、电炉铁合金产品质量指标电炉铁合金产品质量是反映电炉铁合金产品和冶炼技术水平的指标。
凡符合国家标准、部颁标准、企业标准及用户协议标准的产品均为合格品。
有标准成分的铁合金产品的合格品和废品均按标准量计算。
(一)电炉铁合金合格率(指一次合格率)电炉铁合金合格率是指在报告期内,该产品合格量占总检验量的百分比。
其计算公式为:铁合金产品合格率(%)= 铁合金检验合格量(吨)×100%铁合金送检总量(吨)对于生产多品种的企业,还要考核全厂综合合格率。
其计算公式为:电炉铁合金综合合格率(%)=分品种铁合金检验合格量之和(吨)×100%分品种铁合金检验总量之和(吨)计算说明:(l)产品合格率要分品种、分炉进行计算;式中子、母项单位为标准吨。
(2)正常情况下,产品出炉后即参加产品质量考核。
(3)停开炉:1)新开电炉,经过大、中修和硅钙炉的周期停炉或外部原因连续停炉36小时以上又恢复生产的电炉所产出的第一炉产品,不参加质量指标考核(精炼电炉除外)。
钨铁头两炉产品不参加质量考核。
2)新开炉的洗炉或停炉前的洗炉,从加入洗炉料后所产生的废品,一律不计炉号,不作废品考核。
但洗炉过程中所消耗的电、物料不应扣除,要参加消耗指标计算。
3)计划检修,企业外部原因造成5000千伏安及5000千伏安以上电炉连续停电48小时以下,5000千伏安以下电炉停炉在36小时以下所产生的废品,一律参加质量考核。
(4)产品转炼:1)前一种产品炉料,对后一种产品有用或至少是无害的转炼,所产生的过渡产品只要符合质量标准就算合格品。
对不符合任何牌号规定的废品,参加转炼后的产品质量计算。
2)前一种产品炉料对后一种产品有害的不同元素产品的转炼(如硅铬转炼硅铁)可参照新开炉的规定计算。
3)转炼的时间界限,原则上应以变料时间或变料后出第一炉铁堵炉眼时间进行划分。
所出的第一炉产品如果合乎转炼前的产品质量标准,那么转炼前产品作业时间应该截止到转炼后的第一炉出铁堵炉眼时间为止;如果转炼后第一炉产品不符合质量标准或符合后一种产品质量标准,那么转炼时间和耗电以变料时间划分。
炼钢部分各种计算公式汇总

炼钢部分各种计算公式汇总1、转炉装入量装入量=钢坯(锭)单重×钢坯(锭)支数+浇注必要损失钢水收得率(%)-合金用量×合金收得率(%)2、氧气流量Q=V tQ-氧气流量(标态),m 3min 或 m3hV-1炉钢的氧气耗量(标态),m 3; t-1炉钢吹炼时间,min 或h 3、供氧强度 I=Q TI-供氧强度(标态),m3t ·min ;Q-氧气流量(标态),m3min;T-出钢量,t注:氧气理论计算值仅为总耗氧量的75%~85%。
氧枪音速计算α=(κgRT)1/2m/sα—当地条件下的音速,m/s ;κ—气体的热容比,对于空气和氧气,κ=1.4;g —重力加速度,9.81m/s 2;R —气体常数,26.49m/κ。
马赫数计算 M=ν/αM —马赫数;ν—气体流速,m/s ;α—音速,m/s 。
冲击深度计算h 冲=K P 00.5·d 00.6ρ金0.4(1+H 枪/d c ·B)h 冲—冲击深度,m ;P 0—氧气的滞止压力(绝对),㎏/㎝2;d 0—喷管出口直径,m ;H 枪—枪位,m ;ρ金—金属的密度,㎏/m 3;d c —候口直径,m ;B —常数,对低粘度液体取作40;K —考虑到转炉实际吹炼特点的系数,等于40。
在淹没吹炼的情况下,H=0,冲击深度达到最大值,即 h max =P 00.5·d 00.6ρ金0.4有效冲击面积计算 R=2.41×104(h νmax)2R —有效冲击半径,m ;νmax —液面氧射流中心流速,m/s ;νmax =ν出d 出H ·P 00.404ν出—氧射流在出口处的流速,m/s 。
金属-氧接触面积计算在淹没吹炼时,射流中的金属液滴重是氧气重量的3倍,吹入1m3氧气的液滴总表面积(金属-氧气的接触面积): S Σ=3G 金r 平均·ρ金G 金—1标米3氧气中的金属液滴重量=3×1.43㎏;r 平均—液滴的平均半径,m ;ρ金—金属液的密度,7×103㎏/m 3。
电炉钢成本计算详解

电炉钢成本计算详解集团企业公司编码:(LL3698-KKI1269-TM2483-LUI12689-ITT289-电炉总生产成本的构成:一、关于建设成本:对于新建一个80吨的连续生产的康斯迪水平加料的超高功率电炉,总成本基本上在5000万元左右,即:1、新建厂房费用(有的企业利旧原厂房);2、康斯迪连续加料系统(以河南太行全利重工为代表)3、电弧炉主体设备(新上电炉基本上在75-120吨之间,超100吨的不多);4、精炼炉主体设备(基本与电弧炉配套)5、连铸设备(多数利旧)6、除尘系统(这是一项大工程,由于环保政策的紧张,必须过关)7、水路系统;8、电力辅助系统。
以上八项基本上可以说涵盖了电弧炉整个生产系统。
对于轧钢系统则不用进行资金投入,基本上利旧原有设备。
对于建设速度,民营企业的假设速度可以说神速,仅用半年时间便拔地而起一座年产100万吨的电炉炼钢生产企业。
二、各电炉钢铁企业在建设过程中便着手进行生产方面的准备了,这期间,各钢企的老板们看到长流程钢企吨钢过1000元的利润,那真是眼睛都鸡红了。
为了能使电炉炼钢早一天投产,老板们恨不得轮着膀子自己搞建设。
建设尾声时,准备生产的过程也是历尽千辛万苦,波澜壮阔。
对于电极的采购是最有意思的,2017年以前,电极市场售价10000-20000元每吨,在2017年的年底竟然涨到无耻的200000元每吨,其无耻程度无人可敌。
俗话说:巧妇难为无米之炊。
老板们仍义无反顾的花巨资采购电极,一车电极的售价达到惊人的700多万元。
对于电弧炉生产技术人员的招录上各个企业也是尽显其挖人墙角之能事。
把电弧炉炉长的这一岗位工资炒到5万/月,仍是招不到人。
炉前一助手、炉前工、维修工、精炼炉长工资也跟着水涨船高,工资过万都找不上来人。
三、说到前期试产,因为国内电炉炼钢技术相对长流程技术上可谓是相当薄弱,技术人员奇缺,尤其是康斯迪水平上料,连续生产,相关技术人员更是奇缺,在试生产过程中,困难重重,安全事故、生产事故、人员伤亡不断爆出,从2018年2月份到目前,可以说电炉生产企业经历了生与死的考验,基本上实现了顺产、稳产。
电炉熔炼能力计算公式

电炉熔炼能力计算公式电炉熔炼是一种常见的冶金工艺,广泛应用于钢铁、有色金属等行业。
在进行电炉熔炼时,了解熔炼能力的计算公式是非常重要的。
本文将介绍电炉熔炼能力的计算方法,并探讨其在实际生产中的应用。
一、电炉熔炼能力计算公式的基本原理电炉熔炼能力的计算公式主要基于能量平衡原理。
在电炉熔炼过程中,电能通过电极传导到熔池中,使熔池中的金属材料加热熔化。
而电能的传导是通过电阻加热的方式进行的。
因此,电炉熔炼能力的计算公式主要涉及电阻加热的相关参数。
二、电炉熔炼能力计算公式的具体内容电炉熔炼能力的计算公式包括以下几个方面的参数:1. 熔炼能力(Q):表示单位时间内熔炼的能力,通常以千克或吨为单位;2. 电功率(P):表示电炉使用的电能,通常以千瓦或兆瓦为单位;3. 熔化热(H):表示单位质量的金属材料从室温熔化所需要的热量,通常以焦耳/克或千焦/千克为单位;4. 熔炼时间(t):表示完成一次熔炼所需要的时间,通常以小时为单位;5. 熔池温度(T):表示熔池的温度,通常以摄氏度为单位。
根据能量平衡原理,可以得到电炉熔炼能力的计算公式如下:Q = P * t = m * H * (T - T0)其中,Q表示熔炼能力,P表示电功率,t表示熔炼时间,m表示熔炼的金属材料质量,H表示熔化热,T表示熔池温度,T0表示室温。
三、电炉熔炼能力计算公式的应用电炉熔炼能力的计算公式在实际生产中具有重要的应用价值。
通过该公式,可以预估电炉在一定时间内能够熔炼的金属材料的质量。
这对于生产计划的制定和生产能力的评估非常有帮助。
通过计算公式可以得知,熔炼能力与电功率、熔池温度和熔化热等参数密切相关。
在实际生产中,可以通过调整这些参数来提高熔炼能力,从而提高生产效率。
四、电炉熔炼能力计算公式的局限性虽然电炉熔炼能力的计算公式在实际生产中有一定的应用价值,但也存在一些局限性。
首先,该公式假设了电炉熔炼过程中能量损失可以忽略不计,但实际上电炉熔炼过程中会有一定的能量损失。
电炉钢成本计算详解

电炉钢成本计算详解集团企业公司编码:(LL3698-KKI1269-TM2483-LUI12689-ITT289-电炉总生产成本的构成:一、关于建设成本:对于新建一个80吨的连续生产的康斯迪水平加料的超高功率电炉,总成本基本上在5000万元左右,即:1、新建厂房费用(有的企业利旧原厂房);2、康斯迪连续加料系统(以河南太行全利重工为代表)3、电弧炉主体设备(新上电炉基本上在75-120吨之间,超100吨的不多);4、精炼炉主体设备(基本与电弧炉配套)5、连铸设备(多数利旧)6、除尘系统(这是一项大工程,由于环保政策的紧张,必须过关)7、水路系统;8、电力辅助系统。
以上八项基本上可以说涵盖了电弧炉整个生产系统。
对于轧钢系统则不用进行资金投入,基本上利旧原有设备。
对于建设速度,民营企业的假设速度可以说神速,仅用半年时间便拔地而起一座年产100万吨的电炉炼钢生产企业。
二、各电炉钢铁企业在建设过程中便着手进行生产方面的准备了,这期间,各钢企的老板们看到长流程钢企吨钢过1000元的利润,那真是眼睛都鸡红了。
为了能使电炉炼钢早一天投产,老板们恨不得轮着膀子自己搞建设。
建设尾声时,准备生产的过程也是历尽千辛万苦,波澜壮阔。
对于电极的采购是最有意思的,2017年以前,电极市场售价10000-20000元每吨,在2017年的年底竟然涨到无耻的200000元每吨,其无耻程度无人可敌。
俗话说:巧妇难为无米之炊。
老板们仍义无反顾的花巨资采购电极,一车电极的售价达到惊人的700多万元。
对于电弧炉生产技术人员的招录上各个企业也是尽显其挖人墙角之能事。
把电弧炉炉长的这一岗位工资炒到5万/月,仍是招不到人。
炉前一助手、炉前工、维修工、精炼炉长工资也跟着水涨船高,工资过万都找不上来人。
三、说到前期试产,因为国内电炉炼钢技术相对长流程技术上可谓是相当薄弱,技术人员奇缺,尤其是康斯迪水平上料,连续生产,相关技术人员更是奇缺,在试生产过程中,困难重重,安全事故、生产事故、人员伤亡不断爆出,从2018年2月份到目前,可以说电炉生产企业经历了生与死的考验,基本上实现了顺产、稳产。
高炉炼铁技术关于计算内容大全

高炉炼铁技术关于计算内容大全
1.炉料配比计算:
高炉的炉料配比是指将各种原料按一定比例混合,形成炉料,以满足
高炉内冶炼的要求。
炉料配比计算需要考虑铁矿石的品位、配加量、还原
性能等因素。
根据不同的炉况和冶炼目标,可以通过计算确定最佳的炉料
配比。
2.铁矿石还原率计算:
铁矿石还原率是指在高炉内,铁矿石中铁的还原程度,一般用还原率
来表示。
铁矿石还原率的计算需要考虑还原剂的种类、配加量、还原反应
的温度、压力等因素。
可以通过测定高炉内不同位置的铁矿石成分和炉渣
成分,来计算铁矿石的还原率。
3.高炉燃烧计算:
高炉燃烧计算主要是针对炉顶燃烧系统进行的,包括风口、鼓风机、
燃料气等相关参数的计算。
通过计算一系列参数,可以确定合适的鼓风量、燃料气使用量,以实现高炉内燃烧过程的最佳效果。
4.炉渣成分计算:
高炉冶炼过程中,炉渣是一种重要的冶炼剂。
炉渣成分计算可以通过
测定高炉内炉渣中的各种成分来实现。
炉渣成分的计算需要考虑各种原料
的配加量、还原反应的程度等因素,以确保炉渣成分符合冶炼的要求。
5.高炉出铁量计算:
高炉出铁量是指高炉每天或每小时生产的铁水量。
高炉出铁量的计算需要考虑炉顶风量、炉渣成分、炉渣重量、料温等因素。
通过测定高炉出铁口的温度和流量,可以计算出高炉出铁量。
以上是高炉炼铁技术中一些常见的计算内容,这些计算内容是为了优化高炉冶炼过程,提高冶炼效率和质量,减少能耗和环境污染而进行的。
高炉炼铁技术的计算内容综合考虑了多个因素,通过科学的计算方法,可以更好地指导高炉运行和冶炼生产。
电炉炼钢设计(物料平衡+热平衡)
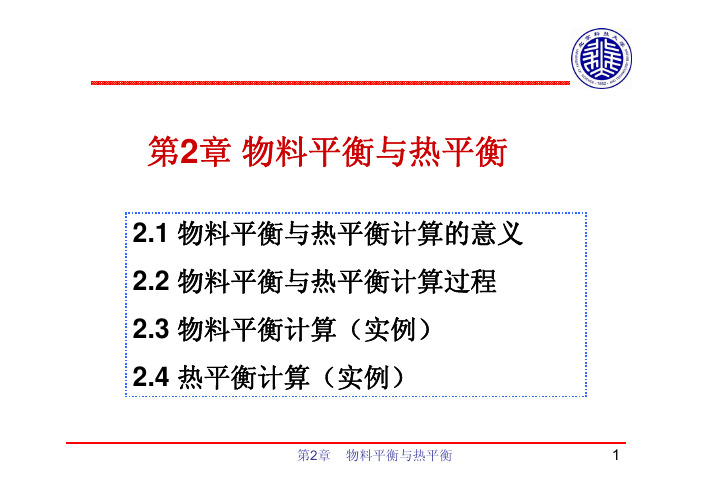
7
电炉冶炼过程(三段式)
还原期(精炼期):
还原期是指氧化末期扒渣完毕到出钢阶段,还原期是转 炉炼钢所没有的。 还原期的主要任务是: (1)去除钢液中的氧 (2)去除钢液中的硫 (3)调整钢液的温度,成份到规定成分; (4 )合金化 还原期操作:(1)扒除氧化渣后加石灰和莹石 化渣 (2)加碳粉造白渣或电石渣,脱氧、脱硫(3)成份温 度合格、加合金测温度、看脱氧、出钢。
第2章 物料平衡与热平衡
23
氧化期物料平衡计算
(2)确定金属量:根据熔化期的金属量以及表 7-35中的元素烧损量和矿石还原出来的铁量,即 可以得到氧化末期金属量。 (3)确定炉气量:计算方法如同熔化期。先求 静耗氧量(表7-36),再确定氧气与空气消耗量 (表7-37),最后将各种物料或化学反应带入的 气态产物归类,而得其结果(表7-38)。具体的 算法可参照表7-33.
配碳比钢种规格中线高0.70%,焦炭的收得率按75%计(7-28)
第2章 物料平衡与热平衡
15
熔化期物料平衡计算
(2)确定氧气和空气消耗量 耗氧项包括炉料中元素的氧化,焦炭和电极中 碳的氧化;而矿石则带来部分氧,石灰中CaO被 自身S还原出部分氧(CaO+S=CaS+O)。前后二 者之差即为所需净氧量2.815kg,详见表7-30. 根据表7-28中的假定,应由氧气供给的氧气为 50%,即3.085×50%=1.543kg,空气应该供氧为 1.543-0.270=1.273kg。由此可以求出氧气与空气 的实际消耗量。详见表7-31.
第2章 物料平衡与热平衡
39
第2章
物料平衡与热平衡
40
第2章
物料平衡与热平衡
41
电炉平均出钢量计算公式
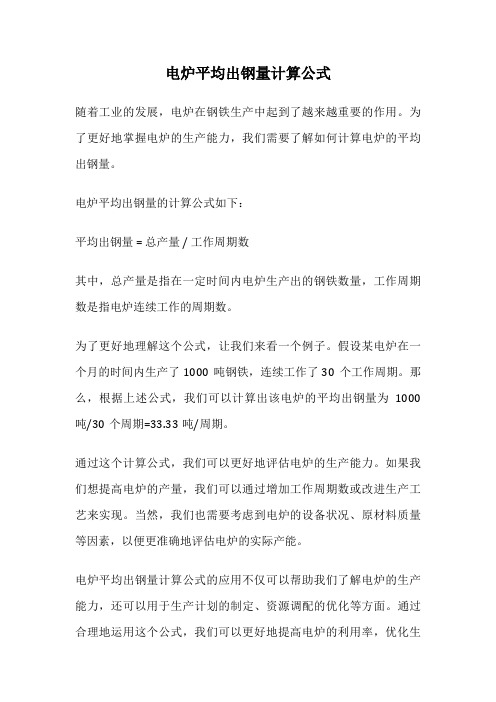
电炉平均出钢量计算公式
随着工业的发展,电炉在钢铁生产中起到了越来越重要的作用。
为了更好地掌握电炉的生产能力,我们需要了解如何计算电炉的平均出钢量。
电炉平均出钢量的计算公式如下:
平均出钢量 = 总产量 / 工作周期数
其中,总产量是指在一定时间内电炉生产出的钢铁数量,工作周期数是指电炉连续工作的周期数。
为了更好地理解这个公式,让我们来看一个例子。
假设某电炉在一个月的时间内生产了1000吨钢铁,连续工作了30个工作周期。
那么,根据上述公式,我们可以计算出该电炉的平均出钢量为1000吨/30个周期=33.33吨/周期。
通过这个计算公式,我们可以更好地评估电炉的生产能力。
如果我们想提高电炉的产量,我们可以通过增加工作周期数或改进生产工艺来实现。
当然,我们也需要考虑到电炉的设备状况、原材料质量等因素,以便更准确地评估电炉的实际产能。
电炉平均出钢量计算公式的应用不仅可以帮助我们了解电炉的生产能力,还可以用于生产计划的制定、资源调配的优化等方面。
通过合理地运用这个公式,我们可以更好地提高电炉的利用率,优化生
产过程,提高企业的经济效益。
电炉平均出钢量计算公式是钢铁生产中重要的衡量指标之一。
通过合理运用这个公式,我们可以更好地评估电炉的生产能力,并采取相应的措施来提高电炉的产量和效率。
这对于企业的发展和经济效益都具有重要意义。
让我们共同努力,不断探索电炉生产的新方法,为钢铁行业的发展贡献力量。
- 1、下载文档前请自行甄别文档内容的完整性,平台不提供额外的编辑、内容补充、找答案等附加服务。
- 2、"仅部分预览"的文档,不可在线预览部分如存在完整性等问题,可反馈申请退款(可完整预览的文档不适用该条件!)。
- 3、如文档侵犯您的权益,请联系客服反馈,我们会尽快为您处理(人工客服工作时间:9:00-18:30)。
电炉炼钢部分1.>某电炉生产了实物量100t含锰65.8%高碳锰铁,共用去含锰40%,富锰渣52t,含锰34%的锰矿180t,问锰回收率是多少?解:锰回收率%=100×65.8%/(52×40%+180×34%)=80.24%答:锰回收率为80.24%。
2.>已知:冶炼40Cr钢,钢水量100t,LF炉炉前光谱分析结果:C0.40%、Si0.27%、Cr0.75%、Mn0.50%,使用65%中碳锰铁、65%中碳铬铁辅加合金(Cr、Mn回收率按95%计算)至成份规格中限。
求:Cr、Mn补加合金量?解:Mn控制中限为0.65%,Cr控制中限为0.95%,中碳锰铁=100×1000×(0.65%-0.50%)/65%×95%=243kg中碳铬铁=100×1000×(0.95%-0.75%)/65%×95%=324kg答:Mn辅加合金243kg,Cr辅加合金324kg。
3.>某炉用氧化法冶炼Cr12,出钢量17500kg,配入高铬3700kg,设定化铬过程Cr、Si烧损180kg,碳吹损20kg,要求成品碳控制在2.1%,计算氧末碳的控制量。
(高铬含C8.0%,假定还原期不增碳)解:高Cr增C:(3700-180)×8%/17500=1.61%碳吹损去碳:20/17500×100%=0.11%氧末碳:2.1%-1.61%-0.11%=0.38%答:氧末碳的控制量为0.38%。
4.>冶炼1Cr13钢,已知钢水量为18t,熔炼成份控制[Cr]=13%,炉内残余Cr为3%,铬铁含Cr为65%,回收率为96%,计算Fe-Cr加入量。
(保留整数位)解:Fe-Mn=[18×1000×(13%-3%)]/(65%×96%-13%)=3644kg答:Fe-Mn加入量为3644kg。
5.>某钢厂在炼钢时采用铁水热装,将含C量0.90%的炉料的温度从20℃升高到300℃,如果该钢的熔点为1480℃,钢的比热为0.167大卡/kg℃,熔解热为65大卡/kg℃,试问此条件下钢的理论电耗是多少?(1KWh相当于860大卡)解:此条件下钢的理论电耗是[1000×(1480-300)×0.167+1000×65]/860=304.72KWh/t答:此条件下钢的理论电耗是304.72KWh/t。
6.>返回吹氧冶炼1Cr18Ni9ti,装入量15t,吹氧毕倒入Fe-Cr为3.75t,还原取样分析成份如下(钢水收得率为95%)求出钢前补加的合金数量及总出钢量。
解:(1)计算出各合金的补加系数①各项合金占有量%:Fe-Cr占有:17.5%/62%×100%=28.23%Ni的占有:9%/99.99%×100%=9%金属MN占有:1.5%/99%×100%=1.52%Fe-Ti占有:0.5%/30%×100%=1.67%②纯钢水占有量=100%-(28.23+9+1.52+1.67)%=59.58%③各合金补加系数Fe-Cr补加系数=28.23/59.58=0.474Ni补加系数=9/59.58=0.151金属Mn的补加系数=1.52/59.58=0.025Fe-Ti的补加系数=1.67/59.58=0.028(2)计算出需加的合金量①加合金前炉内实际钢水量:15000×95%+3750=18000(kg)②按单元合金计算需加入的铁合金量:Fe-Cr=18000×(17.5-16.5)/62%=290(kg)Ni=18000×(9-8.7)%/99.99%=54(kg)金属Mn=18000×(1.5-1.2)%/99%=55(kg)Fe-Ti=18000×0.5%/(30%×60%)=500(kg)总计:290+54+55+500=899(kg)③补加899kg合金应补加量:Fe-Cr=899×0.474=426(kg)Ni=899×0.151=136(kg)金属Mn=899×0.025=22(kg)Fe-Ti=899×0.028=25(kg)(3)总出钢量为:18000+899+609=19508(kg)(4)各合金加入总量:Fe-Cr=290+426=716(kg)Ni=54+136=190(kg)金属Mn=55+22=77(kg)Fe-Ti=500+25=525(kg)(5)验算①炉中Cr的成份:(18000×16.5%+716×62)/19508×100%=17.5%②炉中Ni的成份:(18000×8.7%+190×99.99%)/19508×100%=9%③金属Mn的成份:(18000×1.2%+77×99%)/19508×100%=1.5%④Ti的成份:525×30%/19508×60%×100%=0.5%答:炉中总出钢量为19508kg,需加Fe-Cr为716kg,Ni为190kg,金属Mn为77kg,Fe-Ti为525kg。
7.>冶炼一钢种时,出钢量为100t,LF样(1)C0.14%、Mn0.57%、Cr0.84%,要怎样加,加多少合金,才能使钢水成份达到C0.20%、Mn0.90%、Cr1.10%,并成本最低?(假定合金回收率100%,不考虑合金加入后钢水重量变化)已知:合金名称合金含碳量(%) 合金含量(%) 单价(元/t)高碳Mn-Fe 7.5 65 3000中碳Mn-Fe 0 70 6000高碳Cr-Fe 7.5 65 5000中碳Cr-Fe 0 70 10000解:从成本来考虑,由于中、高碳Cr-Fe比中、高碳Mn-Fe的单价差价大,因此要先满足Cr含量的配入,这样成本最低。
加入的高碳Cr-Fe量计算如下:100×1000×(1.1%-0.84%)/65%=400(kg)加入的高碳Cr-Fe增碳量为:400×7.5%/(100×1000)=0.03%此时钢水中的碳含量为0.17%,如果Mn含量全部由高碳Mn-Fe配入,钢水中的碳就要超出,因此先要计算把碳配至0.20%所需的高碳Mn-Fe量0.03%×100×100/7.5%=400(kg)高碳Mn-Fe增Mn量为:400×65%/(100×1000)=0.26%此时钢中含Mn量为0.26%+0.57%=0.83%,离目标0.90%-0.83%=0.07%的Mn量由中碳Mn-Fe来补,需加入的中碳Mn-Fe量为:100×1000×0.07%/70%=100(kg)答:向钢水中一共要加入高碳Cr-Fe为400kg,高碳Mn-Fe为400kg,中碳Mn-Fe为100kg。
8.>某厂冶炼16MnL钢时装入量40t,还原渣为料重的3%,其配比是石灰:萤石:矽石=6:1:1脱氧剂Si总用量为0.60%回收率为50%,求还原渣的碱度?(炉料收得率为95%,Si、O的原子量分别为28、16,石灰中含CaO90%)解:[Si]+[O]=(SiO2) ①因为Si、O的原子量分别是28和16,由①式可得:SiO2的分子量是60,又由①式可知0.6%的Si用量回收率为50%时在40吨炉料中可生(SiO2)量为:(SiO2)=60×0.60%×50%×40000×95%/28=244(kg)又因为还原渣为料重的3%,其配比已定,所以还原渣中:石灰=40000×3%[6/(6+1+1)]=9000(kg)矽石=40000×3%[1/(6+1+1)]=150(kg)而碱度R是CaO/SiO2 ②CaO=900×90%=810(kg)SiO2=244+150=394(kg)∴R=810/394=2.05答:还原渣的碱度过为2.05。
9.>氧化期使[C]从0.6%降到0.2%,若脱碳速度为每分钟0.04%,需多长时间?若每降低0.1%的C温度上升20℃,则脱碳结束后温度升高多少度?解:所需时间t=△[C]/Vc=0.4%/0.04%=10min升高温度△T=20℃×(0.4/0.1%)=80℃答:若脱碳速度为每分钟0.04%,需10min;若每降低0.1%的C温度上升20℃,则脱碳结束后温度升高80℃。
10.>往炉中加入Fe-Mo13kg,(钼铁成分为67%)炉中钼由0.2%增加到0.25%,求炉中钢水量。
(回收率按100%计算)解:钢水量=13×0.67%/(0.25-0.2)%=17420kg答:钢水量为17420kg。
11.>20t钢水量,出金刚前Mn达到0.83%,若将Mn撤到0.78%,问需要加入多少料?解:需补加量=(0.83-0.78)/0.78×20000=1.282t答:需补加1.282t。
12.>原计划钢液的重量为20t,加钢前钼的含量为0.16%,加钼后计算钼的含量为0.25%,实际分析为0.26%,求钢液的实际重量。
解:钢液的实际重量=20×(0.25-0.16)%/(0.26-0.16)%=18t答:钢液的实际重量为18t。
13.>冶炼45#钢,炉中分析C=0.39%,Mn=0.45%;估计钢水量20吨,成份按C =0.44%、Mn=0.65%控制,试求高锰(Mn=65%、C=7%,回收率98%)和增碳生铁(4%碳)加入量?解:高锰加入量=(0.65%-0.45%)×20×1000/(65%×98%)=62.79kg 高锰带入碳=62.79×7%/(20×1000)=0.022%需加入生铁=20×1000×[(0.44%-0.39%-0.022%)/(4%-0.44%)]=157.30kg 答:高锰加入量为62.79kg,增碳生铁加入量为157.30kg。
14.>冶炼T12钢水量为30t,炉中分析碳成份为1.12%,控制规格碳成份为1.16%,求增碳生铁(含4%碳)加入量?解:需加生铁=30×(1.16%-1.12%)/(4%-1.16%)×1000=42kg答:增碳生铁加入量为42kg。
15.>冶炼45#钢,炉中分析Mn=0.55%,Si=0.12%,要求控制[Mn]=0.65%,[Si]=0.25%,补加Si-Mn合金含Mn=65%,Si=25%,Si-Fe含[Si]=75%,Si回收率按80%,Mn回收率按100%计算,求需加入Si-Mn合金、Si-Fe各多少?(钢水量20t) 解:硅锰加入量=(0.65%-0.55%)×20×1000/(65%×100%)=30.76kg 硅锰带入硅=30.76×25%/(20×1000)=0.038%需加入硅铁=20×1000×(0.25%-0.12%-0.038%) /(75%×80%)=30.67kg答:需加入硅锰合金30.76kg,硅铁合金30.67kg。