基于有限元法的电机车驱动轴疲劳寿命预测_时慧焯
利用有限元法分析汽车后轴的疲劳失效

利用有限元法对汽车后轴套失效分析文章信息:文章历史:发表于2008年8 月14 日,文库公认于2008 年9 月12日,2008 年9 月25 日在网上刊登。
关键词:后轴套,应力集中,疲劳失效,有限元分析文章摘要:对汽车后轴轴套样品出现在预期的负载周期的早期疲劳失效的分析。
在这些试验中,裂纹主要出现在样品的同一区域。
为了确定失效的原因,对后轴套进行了详细的CAD 建模,轴套材料的力学性能通过拉伸试验确定。
通过这些资料来对应力和疲劳强度进行有限元分析。
在负载周期内疲劳裂纹产生的位置和最小数目决定了零件失效。
对试验结果进行了比较分析。
提出了解决现有问题的设计来提高轴套的疲劳寿命。
版权所有爱思唯尔(世界领先的科技及医学出版公司)2008 第一章前言由于其高负荷能力,通常固体轴用于重型商用车辆。
固体轴的结构可以从图1 中看到。
在车辆的使用寿命中,道路的表面粗糙度产生的动态力使轴套产生动态应力。
这些力将导致轴套的疲劳失效,也就是整个车辆的主要承载部分。
因此它是至关重要的,桥壳的疲劳破坏违背了可预测的使用寿命。
在批量生产前,轴套样品由于动态垂直力导致的负荷能力和疲劳寿命应该通过疲劳试验确定,如图2 所示。
这些试验中,一个可以检测液动执行机构采用循环垂直荷载作用于样品上,直到疲劳裂纹的产生。
根据一般标准,轴套样品必须承受5 x 105N的载荷循环而不产生疲劳失效。
在对一根非对称轴套的垂直方向疲劳测试中,如图3 所示,在极限载荷循环前,疲劳裂纹在某些轴上开始产生。
通过观察,最小的载荷循环为3.7x 105N 时,便产生疲劳失效。
在这些试验中,裂纹产生于E1到E2的班卓过度区域。
可以从失效的实例中看出,如图4 所示。
为了预测失效的原因,一份详细的轴套实体模型通过CATIA V5R15商业软件创建。
利用该模型,建立有限元模型。
应力和疲劳强度分析是在ANSYS V11.0 商业有限元软件中进行的。
轴套材料力学性能通过拉伸试验并由FE 分析获得。
纯电动车后轴的疲劳寿命预测分析
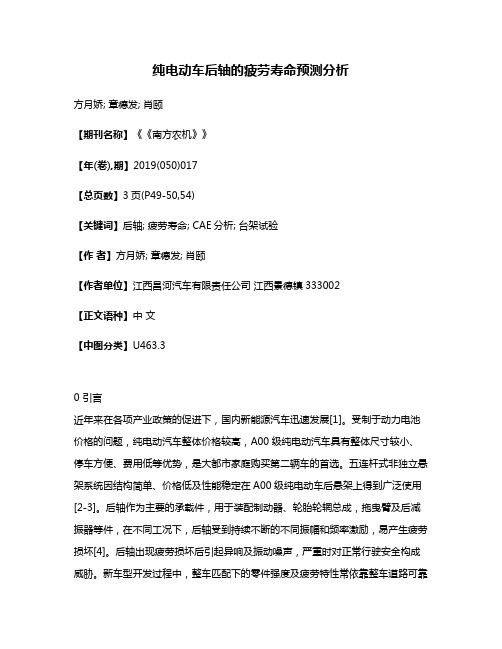
纯电动车后轴的疲劳寿命预测分析方月娇; 章德发; 肖颐【期刊名称】《《南方农机》》【年(卷),期】2019(050)017【总页数】3页(P49-50,54)【关键词】后轴; 疲劳寿命; CAE分析; 台架试验【作者】方月娇; 章德发; 肖颐【作者单位】江西昌河汽车有限责任公司江西景德镇333002【正文语种】中文【中图分类】U463.30 引言近年来在各项产业政策的促进下,国内新能源汽车迅速发展[1]。
受制于动力电池价格的问题,纯电动汽车整体价格较高,A00级纯电动汽车具有整体尺寸较小、停车方便、费用低等优势,是大都市家庭购买第二辆车的首选。
五连杆式非独立悬架系统因结构简单、价格低及性能稳定在A00级纯电动车后悬架上得到广泛使用[2-3]。
后轴作为主要的承载件,用于装配制动器、轮胎轮辋总成,拖曳臂及后减振器等件,在不同工况下,后轴受到持续不断的不同振幅和频率激励,易产生疲劳损坏[4]。
后轴出现疲劳损坏后引起异响及振动噪声,严重时对正常行驶安全构成威胁。
新车型开发过程中,整车匹配下的零件强度及疲劳特性常依靠整车道路可靠性试验来进行考核,多轮整车道路可靠性试验明显减慢研发周期及增加研发费用[5]。
因此,在计算机仿真技术快速发展的今天,采用虚拟仿真对后轴进行强度和疲劳寿命预测分析具有重要意义,有利于节省研发费用和加快车型研发周期,快速应对市场需求。
针对纯电动车后轴开发需要,本文采用HyperWorks软件建立了纯电动车后轴建立疲劳寿命分析模型,确定了边界条件,并进行了疲劳寿命CAE分析,最后与台架试验结果对比,以验证疲劳寿命分析模型的正确性,为后轴设计提供一定参考。
1 模型建立后轴三维模型,主要包含芯轴、法兰、轴管、拖曳臂支架及弹簧座5部分,其物理参数如表1所示。
采用HyperWorks建立后轴有限元模型,如图1(a)所示,采用的六面体网格单元,尺寸为3mm×3mm,网格单元数为7368,节点总数为56676,焊缝连接均采用shell单元模拟。
基于IIW标准的提速客车转向架焊接构架疲劳寿命预测
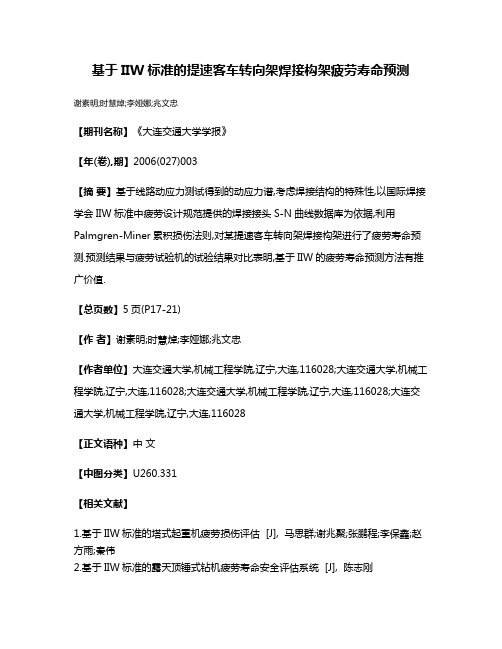
基于IIW标准的提速客车转向架焊接构架疲劳寿命预测
谢素明;时慧焯;李娅娜;兆文忠
【期刊名称】《大连交通大学学报》
【年(卷),期】2006(027)003
【摘要】基于线路动应力测试得到的动应力谱,考虑焊接结构的特殊性,以国际焊接学会IIW标准中疲劳设计规范提供的焊接接头S-N曲线数据库为依据,利用Palmgren-Miner累积损伤法则,对某提速客车转向架焊接构架进行了疲劳寿命预测.预测结果与疲劳试验机的试验结果对比表明,基于IIW的疲劳寿命预测方法有推广价值.
【总页数】5页(P17-21)
【作者】谢素明;时慧焯;李娅娜;兆文忠
【作者单位】大连交通大学,机械工程学院,辽宁,大连,116028;大连交通大学,机械工程学院,辽宁,大连,116028;大连交通大学,机械工程学院,辽宁,大连,116028;大连交通大学,机械工程学院,辽宁,大连,116028
【正文语种】中文
【中图分类】U260.331
【相关文献】
1.基于IIW标准的塔式起重机疲劳损伤评估 [J], 马思群;谢兆聚;张鹏程;李保鑫;赵方雨;秦伟
2.基于IIW标准的露天顶锤式钻机疲劳寿命安全评估系统 [J], 陈志刚
3.基于IIW标准的C80型敞车上心盘座疲劳失效研究及改进验证 [J], 李向伟;于跃斌;于连友;兆文忠
4.提速客车转向架焊接构架应力谱的试验研究 [J], 缪龙秀;孙守光
5.基于IIW标准的露天顶锤式钻机疲劳寿命安全评估系统∗ [J], 陈志刚
因版权原因,仅展示原文概要,查看原文内容请购买。
基于有限元法的机械疲劳寿命预测方法的研究_吕凯波
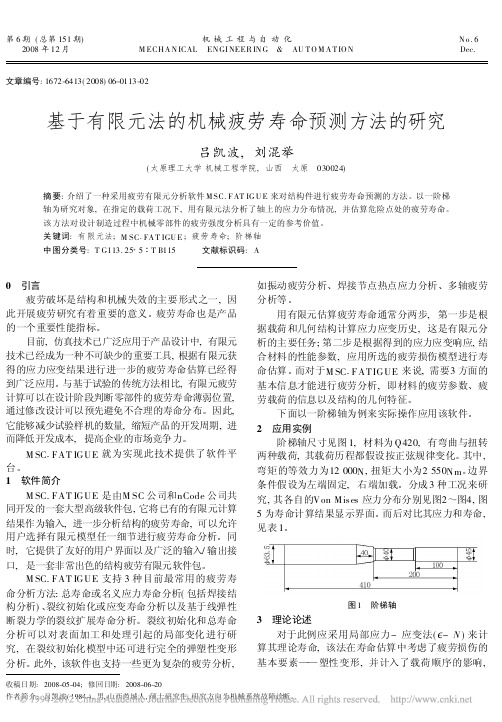
( 英文摘要转第 117 页)
2008 年第 6 期 机 械 工 程 与 自 动 化
·11 7·
形状与 3 阶类似, 呈一种垂直关系, 这里不再赘述。 第5 阶模态振型见图7, 它以2 条相互垂直的直径
式( 2) 、式( 4) 中的6 个材料常数K ′、n′、b、c、Ef ′、
Rf ′既可以通过试验得到, 也可以通过近似方法估算。
M SC. F AT IGUE 就提供了通过材料的强度极限与弹
性模量来估算循环特性参数。
图 2 弯矩作用时的 M ises 应力分布图
图 3 扭矩作用时的 M ises 应力分布图
下面以一阶梯轴为例来实际操作应用该软件。 2 应用实例
阶梯轴尺寸见图 1, 材料为 Q420, 有弯曲与扭转 两种载荷, 其载荷历程都假设按正弦规律变化。其中, 弯矩的等效力为12 000N, 扭矩大小为2 550Nm。边界 条件假设为左端固定, 右端加载。分成 3 种工况来研 究, 其各自的Von Mises 应力分布分别见图2~图4, 图 5 为寿命计算结果显示界面。而后对比其应力和寿命, 见表 1。
M SC. F AT IGUE 就为实现此技术提供了软件平 台。 1 软件简介
M SC. F AT IGUE 是由M SC 公司和nCode 公司共 同开发的一套大型高级软件包, 它将已有的有限元计算 结果作为输入, 进一步分析结构的疲劳寿命, 可以允许 用户选择有限元模型任一细节进行疲劳寿命分析。同
图 7 第 5 阶模态振型图
6 阶及更高模态由于转速非常高, 一般发动机中 很少出现, 但作为理论分析可以了解一下。第10 阶模 态的变形情况见图8, 可以看出, 整个涡轮都承受着比 较均匀的力, 但是有几个叶片( 包括故障叶片) 已发生 严重的振动过大现象, 所以说, 如果将来航空发动机 转子转速有大幅度提高的话, 那么叶片的结构、强度 方面也要重新作相应的设计。 3 结论
基于有限元方法的16PA6STC柴油机曲轴疲劳强度分析
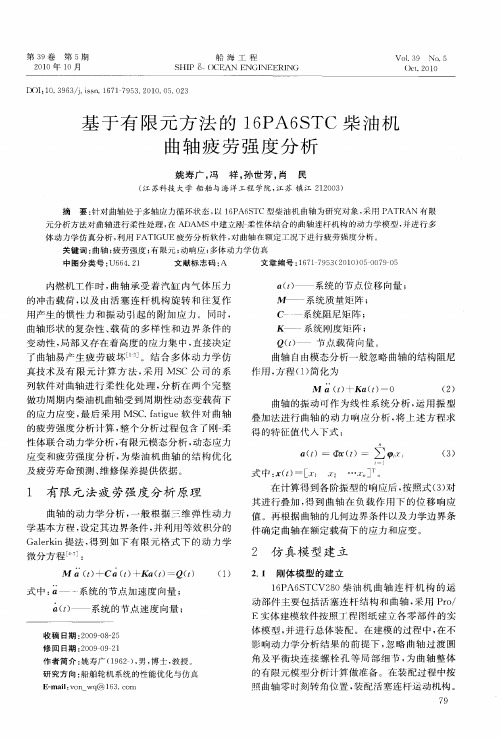
境下 的整体坐 标系 内 。仿真模 型及 各机构 的运 动
副关 系见 图 1 。
阻尼单元 , 模拟 机 体 与 曲轴 之 间润 滑 油膜 的 弹性 支 撑及 阻尼 作用 。原 刚体 的质 量 、 心等 固有 属 重
性均 转移 至柔性 体 曲轴 。
3 仿 真 结 果 分 析
1P S 6 A6 TC型柴 油机 为 四 冲程 中速 机 , 曲轴
曲柄臂过 渡 圆角处为 应 力集 中最严 重 的部位 。其
应 力值 为 30 5 5.2MP 。将 曲轴进 行柔性 2 . ̄4 79 a
化 以后 , 刚体模 型 的 固有特 性 离 散 为柔 性体 的 原
各 阶模 态特 性 ;受各缸 的气 体爆 发压 力及 连杆 惯
图 2 曲轴 的 有 限 元模 型
rn中设 置 曲轴 的外 接 节点 单 元 , MP — B 2 a 即 CR E 单元 , 图 2 见 。
图 3 曲轴 动 态 加 载及 应 力 云 图
可 以看 出在 各缸 发 火 做功 过 程 中 , 曲轴 应 力
最 大时刻 出现 在仿真 时 间为 0 1 92S 曲柄销 与 . 0 ,
』 Ⅵ
K Q() £
系统 质量 矩 阵 ;
系统 刚度矩 阵 ; 节 点载 荷 向量 。
C 系统 阻尼 矩 阵 ; _
变动性 , 部又存 在 着高 度 的应力 集 中 , 接决 定 局 直 了 曲轴 易 产生 疲 劳 破 坏 l 。结 合 多 体 动 力 学 仿 1 真技术 及 有 限 元 计 算 方 法 , 用 MS 采 C公 司 的 系
o. 8 oo
? 羞
一…
n n 85 1s 其值 为 一O ( 4 n 6 7 , ・)
风力发电机组轴承的滚道疲劳寿命预测方法研究

风力发电机组轴承的滚道疲劳寿命预测方法研究引言:随着清洁能源的需求不断增加,风力发电逐渐成为各国重要的能源转换方式之一。
然而,风力发电机组在运行过程中常常遭遇极端的环境条件和工作负荷,这对轴承的可靠性和寿命提出了严峻的要求。
滚道疲劳是导致轴承失效的主要原因之一,因此预测风力发电机组轴承的滚道疲劳寿命成为了当前研究的重点。
本文将介绍相关文献中的预测方法,并提出一种新的预测方法。
一、传统的滚道疲劳寿命预测方法1. 基于经验公式的预测方法经验公式是一种简化的预测方法,它基于理论和实验数据的分析,通过将轴承的工作负荷、转速、清洗频率等参数纳入考虑,得出滚道疲劳寿命的预测值。
这种方法具有较高的实用性,但仍存在一定的误差。
2. 基于有限元分析的预测方法有限元分析是一种基于数值计算的方法,它通过对轴承内部力学行为进行分析,得出滚道疲劳寿命的预测值。
该方法考虑了轴承的材料特性、几何结构和工作负荷等因素,能够提供较精确的预测结果。
然而,由于有限元分析需要大量的计算资源和时间,该方法在实际应用中存在一定的局限性。
二、新的滚道疲劳寿命预测方法考虑到传统方法的局限性,本文提出了一种新的滚道疲劳寿命预测方法,该方法结合了统计学和机器学习技术。
1. 基于统计学的预测方法统计学是一种强大的工具,它能够分析数据之间的关系,找出规律和趋势。
本文中,我们将通过收集大量的轴承运行数据,对滚道疲劳寿命进行统计分析。
通过分析工作负荷、转速、使用时间等因素与滚道疲劳寿命之间的关系,建立数学模型,从而预测轴承的寿命。
2. 基于机器学习的预测方法机器学习是一种人工智能的方法,它通过训练模型从数据中学习和预测。
我们将使用机器学习算法对轴承运行数据进行处理和分析,并建立预测模型。
通过输入轴承的工作负荷、转速等参数,模型可以输出滚道疲劳寿命的预测结果。
相比传统方法,机器学习方法能够更准确地捕捉到轴承寿命与各种因素之间的复杂关系。
三、实验验证和结果分析为了验证提出的方法,我们将运行一系列的实验。
研究高速动车组车轴的疲劳破坏机制及寿命预测
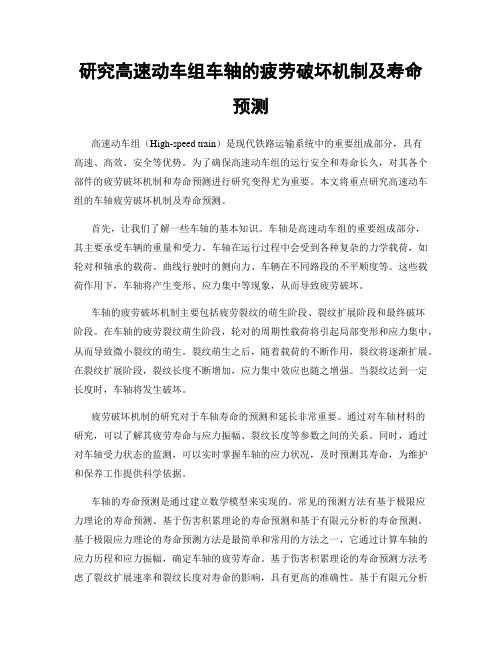
研究高速动车组车轴的疲劳破坏机制及寿命预测高速动车组(High-speed train)是现代铁路运输系统中的重要组成部分,具有高速、高效、安全等优势。
为了确保高速动车组的运行安全和寿命长久,对其各个部件的疲劳破坏机制和寿命预测进行研究变得尤为重要。
本文将重点研究高速动车组的车轴疲劳破坏机制及寿命预测。
首先,让我们了解一些车轴的基本知识。
车轴是高速动车组的重要组成部分,其主要承受车辆的重量和受力。
车轴在运行过程中会受到各种复杂的力学载荷,如轮对和轴承的载荷、曲线行驶时的侧向力、车辆在不同路段的不平顺度等。
这些载荷作用下,车轴将产生变形、应力集中等现象,从而导致疲劳破坏。
车轴的疲劳破坏机制主要包括疲劳裂纹的萌生阶段、裂纹扩展阶段和最终破坏阶段。
在车轴的疲劳裂纹萌生阶段,轮对的周期性载荷将引起局部变形和应力集中,从而导致微小裂纹的萌生。
裂纹萌生之后,随着载荷的不断作用,裂纹将逐渐扩展。
在裂纹扩展阶段,裂纹长度不断增加,应力集中效应也随之增强。
当裂纹达到一定长度时,车轴将发生破坏。
疲劳破坏机制的研究对于车轴寿命的预测和延长非常重要。
通过对车轴材料的研究,可以了解其疲劳寿命与应力振幅、裂纹长度等参数之间的关系。
同时,通过对车轴受力状态的监测,可以实时掌握车轴的应力状况,及时预测其寿命,为维护和保养工作提供科学依据。
车轴的寿命预测是通过建立数学模型来实现的。
常见的预测方法有基于极限应力理论的寿命预测、基于伤害积累理论的寿命预测和基于有限元分析的寿命预测。
基于极限应力理论的寿命预测方法是最简单和常用的方法之一,它通过计算车轴的应力历程和应力振幅,确定车轴的疲劳寿命。
基于伤害积累理论的寿命预测方法考虑了裂纹扩展速率和裂纹长度对寿命的影响,具有更高的准确性。
基于有限元分析的寿命预测方法能够考虑车轴的复杂几何形态和受力情况,可以提供更为精确的寿命预测结果。
除了疲劳破坏机制和寿命预测,还有其他方法可以延长车轴的使用寿命。
基于IIW标准的提速客车转向架焊接构架疲劳寿命预测
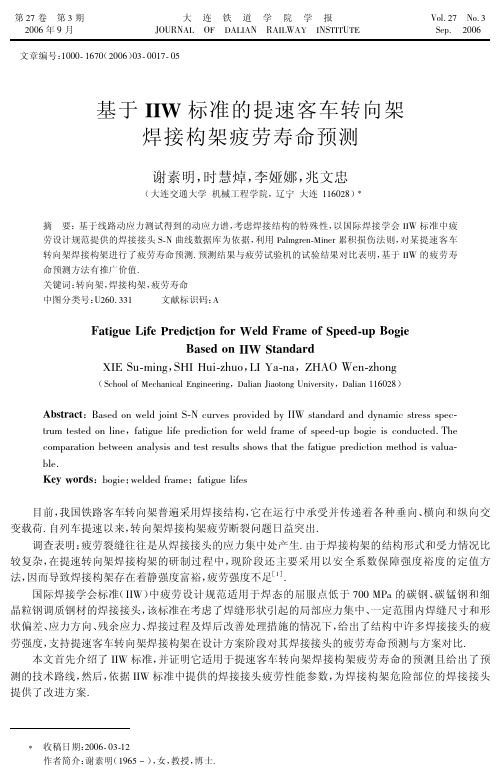
考虑了低于疲劳极限的小载荷应力范围对累积损伤的
贡献,这一点符合我国铁路机车车辆转向架焊接构架
的情况. 因为根据实测构架应力分布特征表明,车辆运
行过程中构架上的大应力循环较小,小应力循环所占
的比例较大,因此,小应力循环对构架疲劳损伤的贡献
是不能忽略的.
该标准疲劳寿命评估时首先要基于焊接接头的初
始信息,定义并确定在疲劳评估中适用的应力类别,并
以疲劳强度来给出温度上升后的疲劳强度,但对机车车辆焊接结构而言,工作温度较低,不必修正;尽管
当焊接接头残余应力被释放后,焊接接头的疲劳强度应当提高且提高程度与应力循环特性相关,但对于
复杂的二、三维构件、高残余应力构件、厚壁构件,均不要修正. 同时由于残余应力的释放很难彻底,在实
际工程问题中,各种焊接接头装配后也可能导致相当长时间驻留的残余应力,因此,仅在极其特殊的情
性、不确定性导致疲劳寿命难于估计;焊接过程中,任何一个相关因素的微小变化对疲劳寿命的影响极
其敏感,这种高敏感性导致疲劳寿命难于可靠估计;即使是采取热处理的方法以消除焊接残余应力,由
于焊缝的实际受力状态的多样性,其效果也不能一概而论. 国际焊接学会标准( IIW)评定焊接接头疲劳特性时,用应力范围来表述 S-N 曲线[3]如图 1 所示,它
该标准焊接接头疲劳数据是基于一定条件建立的,当实际问题的条件与其不一致时,要进行相应的
修正. 例如:从焊趾处产生疲劳裂纹的接头的疲劳强度随板厚增加而降低时,考虑板厚影响疲劳强度的
修正公式为
( ) !"i
= !"
tbase t
I
(4)
式中,!" 为板厚为标准值 tbase 时的疲劳强度,!"t 为实际板厚为 t 时通过修正得到的疲劳强度,I 厚度指 数;当焊接接头处于高温工作状态时,由于其疲劳强度将下降,该标准通过疲劳强度的温度矫正系数乘
某涡轮盘低循环疲劳寿命预测及试验验证
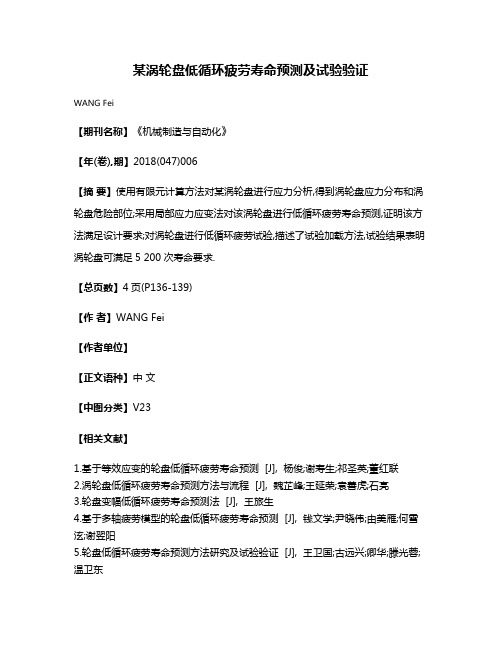
某涡轮盘低循环疲劳寿命预测及试验验证
WANG Fei
【期刊名称】《机械制造与自动化》
【年(卷),期】2018(047)006
【摘要】使用有限元计算方法对某涡轮盘进行应力分析,得到涡轮盘应力分布和涡轮盘危险部位;采用局部应力应变法对该涡轮盘进行低循环疲劳寿命预测,证明该方法满足设计要求;对涡轮盘进行低循环疲劳试验,描述了试验加载方法,试验结果表明涡轮盘可满足5 200次寿命要求.
【总页数】4页(P136-139)
【作者】WANG Fei
【作者单位】
【正文语种】中文
【中图分类】V23
【相关文献】
1.基于等效应变的轮盘低循环疲劳寿命预测 [J], 杨俊;谢寿生;祁圣英;董红联
2.涡轮盘低循环疲劳寿命预测方法与流程 [J], 魏芷峰;王延荣;袁善虎;石亮
3.轮盘变幅低循环疲劳寿命预测法 [J], 王旅生
4.基于多轴疲劳模型的轮盘低循环疲劳寿命预测 [J], 钱文学;尹晓伟;由美雁;何雪泫;谢翌阳
5.轮盘低循环疲劳寿命预测方法研究及试验验证 [J], 王卫国;古远兴;卿华;滕光蓉;温卫东
因版权原因,仅展示原文概要,查看原文内容请购买。
基于有限元法的机械零部件疲劳寿命预测

基于有限元法的机械零部件疲劳寿命预测随着机械工业的快速发展,机械零部件的质量和寿命成为了制造业中的重要问题。
疲劳寿命是机械零部件能够经受多少次加载循环而不发生破坏的能力,因此对于机械设计和工程分析来说,疲劳寿命预测至关重要。
为了准确预测机械零部件的疲劳寿命,工程师们常常使用有限元法。
有限元法是一种基于数值计算的工程分析方法,通过将结构分割成小的有限元单元,利用单元边界上的位移和力的关系来求解整个结构的应力和变形。
在疲劳分析中,有限元法能够考虑到复杂的载荷作用、材料非线性和结构几何非线性等方面的影响,因此被广泛应用于机械零部件的寿命预测。
首先,疲劳寿命预测需要建立合适的有限元模型。
模型的准确性和精度直接影响到预测的结果。
在建立模型时,需要将机械零部件的几何形状、材料性质和加载条件等因素考虑进去,并进行合理的简化和理想化。
同时,还需要选取合适的网格划分和单元类型,以确保模型的数值计算稳定和精确。
其次,疲劳寿命预测需要确定适当的疲劳损伤准则。
疲劳损伤准则描述了当应力历程超过材料疲劳极限时所产生的损伤情况。
常见的疲劳损伤准则包括极值法、线性累积法和稳态强度法等。
其中,极值法是一种简化的方法,假设疲劳寿命与最大应力的幂律关系,但对于不同的材料和零部件来说,这种假设并不总是准确的。
因此,选择适当的疲劳损伤准则十分重要。
然后,疲劳寿命预测需要获取真实的加载历程。
实际工作条件下的零部件往往会受到多种复杂的加载作用,如振动、冲击和变温等。
因此,在预测中需要获取到真实的加载历程,并将其作为输入数据来模拟零部件在实际工作中的疲劳行为。
可以通过传感器和数据采集系统来获取实验数据,或利用计算机辅助工程软件来模拟真实的工作环境。
最后,疲劳寿命预测需要进行合理的结果分析和验证。
通过对预测结果的分析和比对,可以评估模型的准确性和可信度。
与实验结果进行对比可以发现潜在的差异和偏差,并进行模型修正和调整。
此外,还可以通过实验验证的方法来进一步验证模型的可靠性和适用性。
基于有限元法的摩托车车架疲劳寿命分析
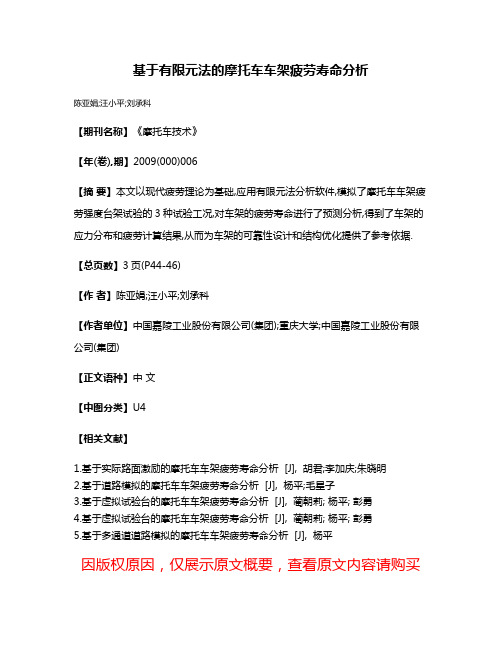
基于有限元法的摩托车车架疲劳寿命分析
陈亚娟;汪小平;刘承科
【期刊名称】《摩托车技术》
【年(卷),期】2009(000)006
【摘要】本文以现代疲劳理论为基础,应用有限元法分析软件,模拟了摩托车车架疲劳强度台架试验的3种试验工况,对车架的疲劳寿命进行了预测分析,得到了车架的应力分布和疲劳计算结果,从而为车架的可靠性设计和结构优化提供了参考依据.【总页数】3页(P44-46)
【作者】陈亚娟;汪小平;刘承科
【作者单位】中国嘉陵工业股份有限公司(集团);重庆大学;中国嘉陵工业股份有限公司(集团)
【正文语种】中文
【中图分类】U4
【相关文献】
1.基于实际路面激励的摩托车车架疲劳寿命分析 [J], 胡君;李加庆;朱晓明
2.基于道路模拟的摩托车车架疲劳寿命分析 [J], 杨平;毛星子
3.基于虚拟试验台的摩托车车架疲劳寿命分析 [J], 蔺朝莉; 杨平; 彭勇
4.基于虚拟试验台的摩托车车架疲劳寿命分析 [J], 蔺朝莉; 杨平; 彭勇
5.基于多通道道路模拟的摩托车车架疲劳寿命分析 [J], 杨平
因版权原因,仅展示原文概要,查看原文内容请购买。
疲劳寿命预测方法综述

疲劳寿命预测方法综述
董月香;高增梁
【期刊名称】《大型铸锻件》
【年(卷),期】2006(000)003
【摘要】综述了疲劳裂纹形成寿命和疲劳裂纹扩展寿命的预测方法,评述了各种不同预测方法的基本假设、估算步骤和特点,并对疲劳寿命预测方法进一步的发展方向作了展望.
【总页数】4页(P39-41,52)
【作者】董月香;高增梁
【作者单位】荆门职业技术学院,湖北,448000;浙江工业大学,浙江,310014
【正文语种】中文
【中图分类】TG113.25+5
【相关文献】
1.多轴低周非比例加载下疲劳寿命预测方法综述 [J], 刘灵灵;聂辉
2.预腐蚀铝基复合材料疲劳寿命的预测方法 [J], 陈亚萍;曾本银;喻溅鉴;袁璐
3.基于损伤力学的金属构件概率疲劳寿命预测方法 [J], 刘潇然;孙秦
4.考虑应变比影响的车用隔振橡胶疲劳寿命预测方法 [J], 吕向飞;黄帅
5.基于最大应变能密度幅值的胎圈疲劳寿命预测方法 [J], 曹雷天;王国林;梁晨;柏林;王伟斌
因版权原因,仅展示原文概要,查看原文内容请购买。
转K6型转向架侧架疲劳寿命估算

转K6型转向架侧架疲劳寿命估算华杨;赵云生;汤劲松;贾万鹏【摘要】利用有限元分析软件对转K6型转向架侧架进行有限元分析,分别以AAR 载荷谱和实测载荷谱对侧架进行疲劳寿命估算,并对比结果.【期刊名称】《铁道机车车辆》【年(卷),期】2011(031)006【总页数】4页(P49-52)【关键词】侧架;载荷谱;疲劳寿命【作者】华杨;赵云生;汤劲松;贾万鹏【作者单位】青岛理工大学机械工程学院,山东青岛266033;青岛四方车辆研究所有限公司技术研究部,山东青岛266031;青岛四方车辆研究所有限公司技术研究部,山东青岛266031;青岛理工大学机械工程学院,山东青岛266033【正文语种】中文【中图分类】U272.331.+8我国铁路货车广泛使用三大件式转向架[1]。
侧架作为转向架的部件之一,有着极为关键的作用。
如果在运行中侧架出现疲劳断裂,将严重威胁列车运行安全,因此,侧架的疲劳问题一直是铁道货车行业极为关注的问题之一。
随着我国铁道货运向重载高速方向的快速发展,转向架的受力更加恶劣,给转向架提出了更加苛刻的要求。
目前,我国铁路货车开始大量使用轴重25 t、最高运营速度120km/h的转K6型转向架,有必要对其疲劳性能进行研究。
1 转K6型转向架侧架有限元静强度计算使用PROE软件建立侧架的三维模型实体,见图1。
根据几何结构和载荷的对称性,取侧架的1/2模型进行分析。
在ABAQUS软件中采用二阶四面体单元划分有限元网格,侧架的1/2模型共划分为104 899个单元,产生177 776个节点,其有限元模型见图2。
实际运行中侧架承受的载荷较复杂,有限元分析时一般将其简化为简单的垂向载荷和横向载荷。
参照TB/T 1335-1996《铁道车辆强度设计及试验鉴定规范》(以下简称规范),在进行应力分析时,侧架的垂向载荷取349.9kN(1.5C),横向载荷取93.3kN(0.4C),分别作用在弹簧承台面和立柱面上。
缺口件疲劳寿命预测新方法

缺口件疲劳寿命预测新方法
金丹;缑之飞
【期刊名称】《航空材料学报》
【年(卷),期】2017(037)002
【摘要】采用有限元方法针对缺口件多轴疲劳实验结果进行模拟.结果表明,相同路径条件下,随着缺口半径减小缺口根部附近的应力梯度显著增加.基于缺口根部应变值,采用等效应变法进行疲劳寿命预测,预测结果随缺口半径的减小而偏于保守.采用应力梯度法确定有效距离,相同路径下,随着缺口半径的减小有效距离减小;依据该有效距离处的等效应变进行疲劳寿命预测,总体预测结果较为分散且偏于不安全.基于实验及有限元模拟结果,提出了基于应变梯度的有效距离确定的新方法,大部分疲劳寿命预测结果位于2倍分散带内.
【总页数】7页(P81-87)
【作者】金丹;缑之飞
【作者单位】沈阳化工大学能源与动力工程学院,沈阳 110142;沈阳化工大学能源与动力工程学院,沈阳 110142
【正文语种】中文
【中图分类】TG155.5
【相关文献】
1.铝合金缺口试样疲劳寿命预测新方法研究 [J], 刘潮涛;王悦东;兆文忠
2.一种考虑尺寸效应的缺口件疲劳寿命预测方法 [J], 奚蔚;姚卫星
3.映射网格在缺口件多轴疲劳寿命预测中的应用 [J], 孙然;金丹;
4.映射网格在缺口件多轴疲劳寿命预测中的应用 [J], 孙然;金丹
5.多轴变幅载荷下基于载荷支配模式的缺口件疲劳寿命预测方法 [J], 陶志强; 张鸣; 朱煜; 成荣; 王磊杰; 李鑫
因版权原因,仅展示原文概要,查看原文内容请购买。
基于有限元法的汽车座椅疲劳寿命预测研究

基于有限元法的汽车座椅疲劳寿命预测研究随着汽车工业的不断发展,安全和舒适性成为了汽车设计中不可或缺的考量因素。
而汽车座椅作为车内主要的接触点,其设计合理与否直接影响着乘客的体验和安全。
特别是长时间驾驶和乘坐,座椅的设计更需要考虑到疲劳寿命,即在一定时间内座椅是否能够保持正常的使用性能,不产生塌陷和裂纹等缺陷。
因此,对于座椅结构以及材料的疲劳寿命进行预测和评估,对于汽车座椅的设计和制造具有重要意义。
有限元方法是一种数值计算方法,广泛应用于结构分析领域。
在汽车座椅设计与评估中,有限元方法也是一种较为常用的分析手段。
有限元方法的实质是将待分析的结构离散成许多有限个小部分,然后通过数值计算逐步求解整个结构。
因此,基于有限元法对汽车座椅进行疲劳寿命预测,需要首先对座椅进行三维建模,然后通过计算机模拟座椅的载荷、位移、应变等参数,在疲劳载荷作用下分析座椅的疲劳寿命,从而得到座椅的疲劳寿命预测结果。
在座椅疲劳寿命预测中,座椅的材料是一个重要的因素,它影响着座椅的强度和刚度等机械性能。
不同材料的性能不同,需要对应不同的疲劳寿命预测方法。
如钢材的疲劳寿命预测可以基于S-N曲线,而塑料材料的预测需要考虑到裂纹扩展等因素。
除了材料因素外,座椅的结构也是影响其疲劳寿命的重要因素。
座椅的结构包括骨架、填充物、面料等部分,在不同的结构部分应用不同的有限元分析方法。
例如,在座椅骨架部分可以采用动态模态分析方法,以及疲劳周期分析、应变互作用方法等分析方法;在填充物部分可以采用三维模型与有限元模拟方法,以及静态分析、动态分析等方法;在面料部分可以采用逆向有限元方法,对座垫和座背表面的应力分布等参数进行分析。
在疲劳寿命预测中,还需要考虑到座椅使用过程中不同的载荷状况,例如静态载荷、动态载荷、剪切载荷、扭转载荷等。
同时,在座椅使用过程中,不可避免地会产生各种因素的影响,如温度、湿度、振动、磨损等,这些因素也需要考虑到,从而精确地评估座椅的疲劳寿命。
考虑车轮谐波磨耗的动车组车轴疲劳寿命
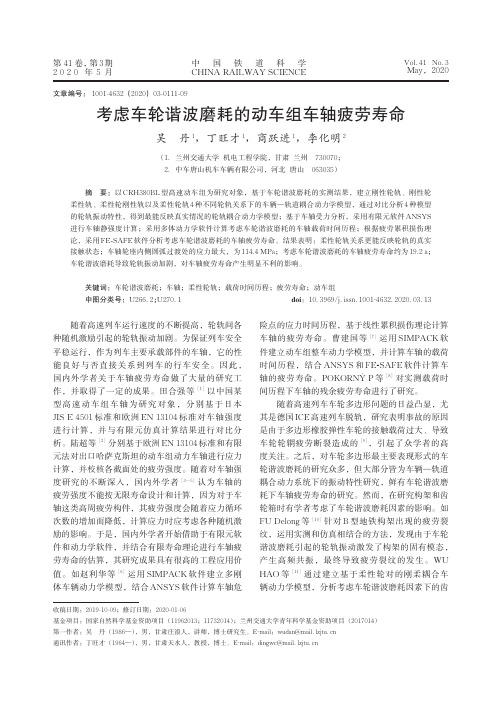
Vol.41No.3May ,2020中国铁道科学CHINA RAILWAY SCIENCE第41卷,第3期2020年5月考虑车轮谐波磨耗的动车组车轴疲劳寿命吴丹1,丁旺才1,商跃进1,李化明2(1.兰州交通大学机电工程学院,甘肃兰州730070;2.中车唐山机车车辆有限公司,河北唐山063035)摘要:以CRH380BL 型高速动车组为研究对象,基于车轮谐波磨耗的实测结果,建立刚性轮轨、刚性轮柔性轨、柔性轮刚性轨以及柔性轮轨4种不同轮轨关系下的车辆—轨道耦合动力学模型,通过对比分析4种模型的轮轨振动特性,得到最能反映真实情况的轮轨耦合动力学模型;基于车轴受力分析,采用有限元软件ANSYS 进行车轴静强度计算;采用多体动力学软件计算考虑车轮谐波磨耗的车轴载荷时间历程;根据疲劳累积损伤理论,采用FE -SAFE 软件分析考虑车轮谐波磨耗的车轴疲劳寿命。
结果表明:柔性轮轨关系更能反映轮轨的真实接触状态;车轴轮座内侧圆弧过渡处的应力最大,为114.4MPa ;考虑车轮谐波磨耗的车轴疲劳寿命约为19.2a ;车轮谐波磨耗导致轮轨振动加剧,对车轴疲劳寿命产生明显不利的影响。
关键词:车轮谐波磨耗;车轴;柔性轮轨;载荷时间历程;疲劳寿命;动车组中图分类号:U266.2;U270.1doi :10.3969/j.issn.1001-4632.2020.03.13随着高速列车运行速度的不断提高,轮轨间各种随机激励引起的轮轨振动加剧。
为保证列车安全平稳运行,作为列车主要承载部件的车轴,它的性能良好与否直接关系到列车的行车安全。
因此,国内外学者关于车轴疲劳寿命做了大量的研究工作,并取得了一定的成果。
田合强等[1]以中国某型高速动车组车轴为研究对象,分别基于日本JIS E 4501标准和欧洲EN 13104标准对车轴强度进行计算,并与有限元仿真计算结果进行对比分析。
陆超等[2]分别基于欧洲EN 13104标准和有限元法对出口哈萨克斯坦的动车组动力车轴进行应力计算,并校核各截面处的疲劳强度。
基于Ⅰ-DEAS的翻车机可靠性疲劳寿命预测
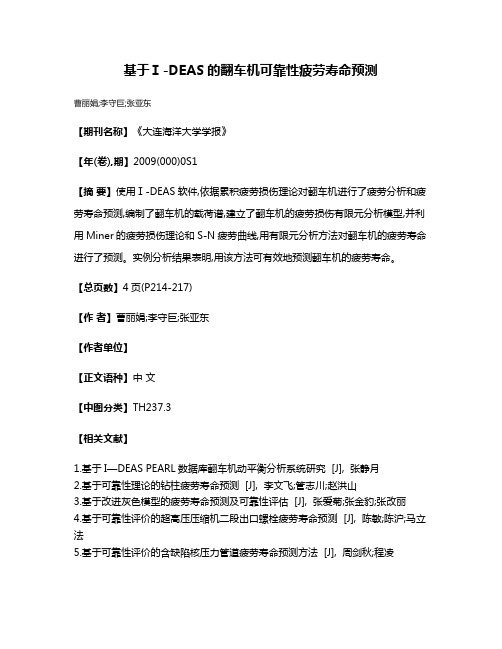
基于Ⅰ-DEAS的翻车机可靠性疲劳寿命预测
曹丽娟;李守巨;张亚东
【期刊名称】《大连海洋大学学报》
【年(卷),期】2009(000)0S1
【摘要】使用Ⅰ-DEAS软件,依据累积疲劳损伤理论对翻车机进行了疲劳分析和疲劳寿命预测,编制了翻车机的载荷谱,建立了翻车机的疲劳损伤有限元分析模型,并利用Miner的疲劳损伤理论和S-N疲劳曲线,用有限元分析方法对翻车机的疲劳寿命进行了预测。
实例分析结果表明,用该方法可有效地预测翻车机的疲劳寿命。
【总页数】4页(P214-217)
【作者】曹丽娟;李守巨;张亚东
【作者单位】
【正文语种】中文
【中图分类】TH237.3
【相关文献】
1.基于I—DEAS PEARL数据库翻车机动平衡分析系统研究 [J], 张静月
2.基于可靠性理论的钻柱疲劳寿命预测 [J], 李文飞;管志川;赵洪山
3.基于改进灰色模型的疲劳寿命预测及可靠性评估 [J], 张爱菊;张金豹;张改丽
4.基于可靠性评价的超高压压缩机二段出口螺栓疲劳寿命预测 [J], 陈敏;陈沪;马立法
5.基于可靠性评价的含缺陷核压力管道疲劳寿命预测方法 [J], 周剑秋;程凌
因版权原因,仅展示原文概要,查看原文内容请购买。
基于响应面法传动直轴疲劳寿命优化
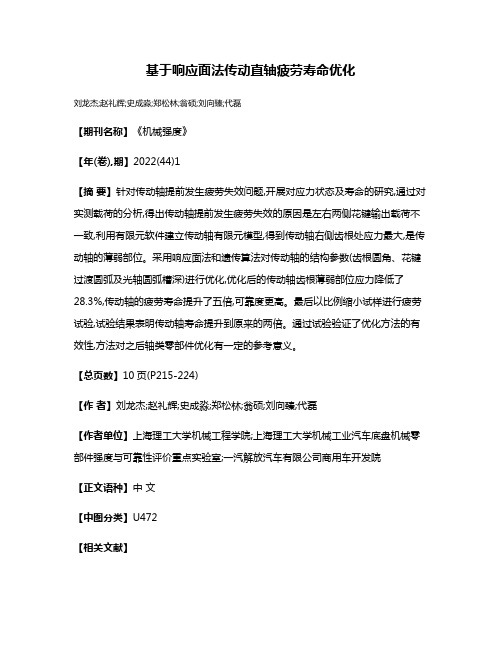
基于响应面法传动直轴疲劳寿命优化
刘龙杰;赵礼辉;史成淼;郑松林;翁硕;刘向臻;代磊
【期刊名称】《机械强度》
【年(卷),期】2022(44)1
【摘要】针对传动轴提前发生疲劳失效问题,开展对应力状态及寿命的研究,通过对实测载荷的分析,得出传动轴提前发生疲劳失效的原因是左右两侧花键输出载荷不一致,利用有限元软件建立传动轴有限元模型,得到传动轴右侧齿根处应力最大,是传动轴的薄弱部位。
采用响应面法和遗传算法对传动轴的结构参数(齿根圆角、花键过渡圆弧及光轴圆弧槽深)进行优化,优化后的传动轴齿根薄弱部位应力降低了28.3%,传动轴的疲劳寿命提升了五倍,可靠度更高。
最后以比例缩小试样进行疲劳试验,试验结果表明传动轴寿命提升到原来的两倍。
通过试验验证了优化方法的有效性,方法对之后轴类零部件优化有一定的参考意义。
【总页数】10页(P215-224)
【作者】刘龙杰;赵礼辉;史成淼;郑松林;翁硕;刘向臻;代磊
【作者单位】上海理工大学机械工程学院;上海理工大学机械工业汽车底盘机械零部件强度与可靠性评价重点实验室;一汽解放汽车有限公司商用车开发院
【正文语种】中文
【中图分类】U472
【相关文献】
1.基于响应面法的梯形直肋散热板优化设计
2.基于响应面法优化的苦荞多糖提取工艺及其抗疲劳作用研究
3.基于响应面模型的结构疲劳寿命优化方法
4.基于实测载荷的传动轴疲劳寿命分析
5.基于改进的响应面法的双激波套筒活齿传动接触疲劳强度模糊可靠性分析
因版权原因,仅展示原文概要,查看原文内容请购买。
- 1、下载文档前请自行甄别文档内容的完整性,平台不提供额外的编辑、内容补充、找答案等附加服务。
- 2、"仅部分预览"的文档,不可在线预览部分如存在完整性等问题,可反馈申请退款(可完整预览的文档不适用该条件!)。
- 3、如文档侵犯您的权益,请联系客服反馈,我们会尽快为您处理(人工客服工作时间:9:00-18:30)。
因此, 本文采用基于有限元法的疲劳寿命预 测方法对驱动轴进行疲劳寿命预测, 具体流程如 下:首先建立完整的三维有限元模型;然后根据实 际运行工况, 通过有限元计算分析, 获得驱动轴的
* 收稿日期:20140217
作者简介:时慧焯 ( 1980 - ) , 男, 工程师, 博士, 主要从事结构有限元分析及优化设计的研究 E-mail:wangjianchao8099@ 126. com.
表1
节点 117 328 130 805 140 016
构钢, 主要用于制造承受大的载荷零件, 如主轴、 齿轮等. 该材料具有强度高、 耐磨和抗疲劳等特
[6 ] 点, 非常适用于电机车驱动轴的工作条件 . N 曲线正确与否, 材料的 S将直接决定疲劳
疲劳寿命预测结果
循环次数 1E + 10 1E + 10 1E + 10 使用系数 0. 035 0. 035 0. 035
图2
疲劳寿命分析流程图
图4
模型载荷与约束示意图
2
2. 1
驱动轴静强度分析
有限元模型
其中: M 为电机传递给轴的扭矩, 其值为 16 452 N · m; F 为作用在轴上的载荷, F1 为 67 810 N, F2 F3 为 18 2021 N, F4 为 134 424 N; S 为 23 000 N, 为轴的约束. 2. 3 静强度分析结果 利用 Ansys 有限元分析软件 对 驱 动 轴 进 行
54
大
连
交
通
大
学
学
报
第 35 卷
损伤法则, 对驱动轴的危险部位进行疲劳寿命预 测. 采用该方法可以在设计阶段对驱动轴进行静 强度及疲劳强度校核, 能缩短产品的设计周期, 降 低生产成本. 另外, 该分析方法还可以应用于其它 类似产品的设计中; ( 2 ) 由计算结果得出, 驱动轴的垂向位移为 1. 84 mm, 最大等效应力为 107 MPa, 最大等效应 力处的疲劳使用系数为 0. 035 , 均满足设计要求. 从而为结构改进和优化设计提供理论依据 . 参考文献:
DOI:10.13291/ki.djdxac.2014.s1.012
Байду номын сангаас
0
引言
生产和运行提供良好的预测.
车轴是机车车辆转向架的关键承载部件 , 其 疲劳强度 决 定 了 机 车 的 行 车 安 全 . 大 多 数 车 轴 都是在交 变 应 力 下 工 作 的 , 车轴在这种交变载 荷作用下 , 经过较长时间工作就会发生疲劳断 裂 . 疲劳断裂与静载荷下的断裂不同 , 无论在静 载荷下显 示 脆 性 或 韧 性 的 材 料 , 在疲劳断裂时 都不产生明显的塑性变形 , 断裂是突然发生的 , 所以常造 成 严 重 的 事 故 . 为 确 保 机 车 车 辆 的 运 行安全 , 车轴必须具有足够的疲劳安全系数 . 因 , 此 在车轴 设 计 阶 段 利 用 有 效 的 分 析 技 术 预 测
σ -1
10 4 ≤ N ≤ 10 7 = 12 022 × N -0. 1672 , 10 < N ≤ 10
7 10
(1) (2)
4
结论
( 1 ) 确定一种适合电机车驱动轴的静强度及
式中: σ -1 为对称循环载荷的弯曲疲劳强度应力幅; N 为该应力幅下发生疲劳破坏时载荷循环周次.
疲劳寿命预测的计算分析方法. 该方法首先利用 Ansys 有限元分析软件, 对驱动轴进行静强度分 析. 然后基于静强度计算结果, 采用疲劳强度分析 N 曲线和 Miner 疲劳累积 理论, 结合材料疲劳 S-
分析结果的正确性. 近些年来, 许多学者致力于 42CrMo 钢的 SN 曲线实验研究[7-10], 本文基于这 些实验数据, 再经过处理得到了适用于本文的 SN 曲线和 Goodman 等寿命曲线. 可以用 Basquin 方程式描述 42CrMo 钢的弯 N 曲线. 由于 42CrMo 钢 SN 曲线 曲载荷疲劳 S具有两段连续下降的曲线, 见图 7 所示, 所以用分 段公式表示为:
52
大
连
交
通
大
学
学
报
第 35 卷
应力分布情况、 危险部位信息;最后采用疲劳强度 N 曲线和 Miner 疲劳 分析理论, 结合材料疲劳 S累积损伤法则, 对驱动轴的危险部位进行疲劳强 度分析, 预测出驱动轴的疲劳使用寿命. 疲劳寿命 分析流程, 见图 2 所示.
42CrMo, 抗 拉 强 度 为 750 MPa, 屈 服 极 限 为 550 MPa, 安全系数为 2 , 许用应力为 275 MPa, 弹性模 量 210 GPa、 泊松比 0. 3. 有限元模型如图 3 所示. 2 . 2 边界条件与载荷确定 电机车驱动轴力学模型可以简化为连续梁结 构, 采用简化的载荷施加方法. 基于 TB / T 2705 - 1996 标准, 结合电机车实际运行状况, 在静强度 [4 ] 分析中, 主要考虑扭转、 垂向、 横向 3 种载荷 . 驱 动轴的动力输入端与电机联轴器相连接 , 此处有 一扭矩, 施加在轴端部; 垂向载荷施加在轴承处; 横向载荷施加在轴端中心部位; 约束施加在车轮 安装部位. 载荷及约束详见图 4 所示.
基于有限元法的电机车驱动轴疲劳寿命预测
时慧焯, 孙金辉
( 大连华锐重工集团股份有限公司 ,辽宁 大连 116013 ) * 摘 通过 Ansys 软件建立其有限元模型, 基于 TB / T 2705 - 1996 标 要:以某电机车驱动轴为研究对象,
准, 对其进行静强度分析, 获得轴的应力分布情况及结构薄弱区 . 在此基础上, 利用 Ansys 通用后处理的 疲劳分析模块, 结合材料疲劳 S - N 曲线和 Miner 累积损伤法则, 预测其疲劳寿命, 从而为驱动轴的结构 改进及优化设计提供有价值的参考依据 . N 曲线 关键词:驱动轴;有限元;疲劳寿命;S文献标识码:A
图5 图3 驱动轴有限元模型
驱动轴垂向位移云图
增刊 1
时慧焯 , 等:基于有限元法的电机车驱动轴疲劳寿命预测
53
图6
驱动轴 Von Mises 应力云图
图7
42 CrMo 的 SN 曲线
3
3. 1
驱动轴疲劳寿命预测
Ansys 疲劳分析模块
Goodman 等寿命曲线公式为: σ a = σ -1 ( 1 - σm ) σb (3)
式中: σ a 为含非零平均应力的疲劳强度应力幅; σ -1 为对称循环载荷的疲劳强度应力幅 ; σ m 为非 对称循环的平均应力; σ b 为材料的拉伸强度. 3 . 3 疲劳寿命预测结果 基于 TB / T2705 - 1996 标准, 结合电机车实际 运行状况, 在疲劳分析中, 仅考虑垂向载荷, 载荷特 性为对称循环载荷, 载荷及约束见图 4 所示. 基于 静强度计算分析结果, 找到图 5 中所示的应力最大 点位置( 节点号 117 328 ), 该位置正好与现实中易 发生疲劳破坏的位置相符. 因此, 选取此节点作为 疲劳分析的一个对象. 另外, 把几个应力较大且位 置在圆周直径突变部位的点也作为分析对象. 根据 设计要求, 驱动轴的使用寿命为 20 年, 许用疲劳循 环次数为 0. 35E9. 疲劳计算结果见表 1.
第 35 卷 增刊 1 2014 年 10 月
JOURNAL
大 连 交 通 大 学 学 报 OF DALIAN JIAOTONG UNIVERSITY
Vol. 35 Supp. 1 Oct. 2014
文章编号:1673-9590 ( 2014 ) 增刊 1-0051-04
[1] 车轴寿命具有重要的意义 . 目前, 用于轴类疲劳寿命研究分析的方法有
1
驱动轴疲劳寿命分析流程
疲劳是指结构在低于静态极限强度载荷的交 变作用下出现断裂破坏现象, 断裂具有突发性, 不 可预测性, 常常会造成严重的后果. 某电机车的驱 动轴在交变载荷下, 经过较长时间工作发生疲劳断 裂, 断裂实物图如图 1 所示. 目前, 传统的驱动轴校 核方法通常为:有限元静强度校核;采用经验公式 形式的疲劳强度校核, 采用这两种方法对驱动轴进 [ 3 ] 行校核常常会造成强度富裕, 疲劳不足 .
- 0 . 0616 , σ -1 = 1772 × N
应力幅值 / MPa 103. 16 82. 11 80. 08
由表 1 计算结果表明, 驱动轴在疲劳载荷工 1E10. 况下的疲劳循环次数为 疲劳使用系数 ( 许 用疲劳循环次数 / 疲劳循环次数 ) 为 0. 035 , 不但 满足设计要求, 而且有很大的优化空间.
很多种, 但有的方法可靠性差, 有的方法参数难以 估算. 实际应用中最可靠的方法是疲劳试验 , 但进 行疲劳试验不仅耗资费时, 且做完试验的试件也 已经破坏. 另外, 结构疲劳寿命同试件的尺寸大 小、 试验环境有关, 具有一定的局限性
[2 ]
.
图1 驱动轴断裂实物图
本文采用基于有限元法的疲劳寿命预测方法 对驱动轴进行疲劳寿命预测. 首先利用 Ansys 有 限元分析软件对某 7 m 电机车驱动轴进行静强度 分析, 并在静强度分析的基础上对驱动轴进行疲 劳寿命分析, 以到达缩短研发时间, 降低开发成 本, 为结构的优化设计提供可靠的依据 , 并为安全
在 Ansys 有限元分析软件中, 有疲劳分析模 . , 块 它是基于应力疲劳理论 适用于高周疲劳, 在 , 静力分析的基础之上 能通过设计仿真自动执行. 该程序可以通过对现有的应力结果进行后处理来 确定任何实体单元和壳单元的疲劳寿命使用系数 ( 对线单元模型的应力必须人工输入 ) . 可以在预 先选定的位置上, 确定一定数目的事件, 每一事件 的循环次数及所受的载荷, 然后把这些位置上的 应力存储起来. 可以在每个位置上定义应力集中 [5 ] 系数和每个事件定义比例系数 . 3. 2 N 曲线 材料的 S驱动轴材料选用 42CrMo, 该材料属于合金结