制动系统设计计算书
(完整word版)制动系统设计
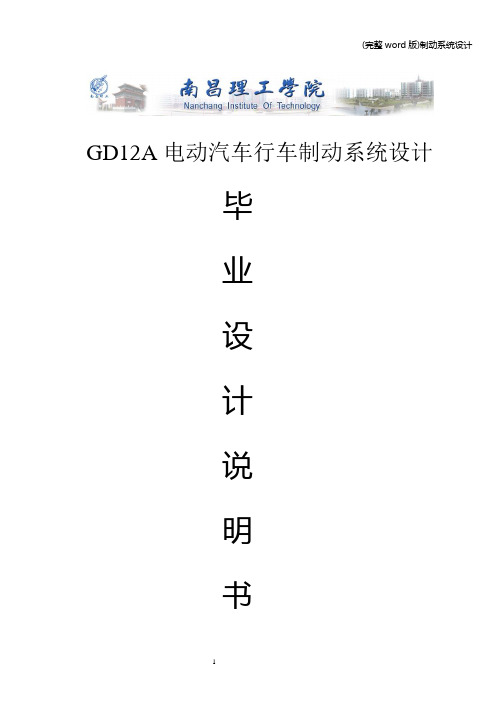
GD12A电动汽车行车制动系统设计毕业设计说明书姓名:俞翼鸿专业:汽车维修与检测班级:(2)指导老师: 邹章鸣南昌理工学院机械工程系1.。
目录摘要Troduction前言第一章绪论 (6)1。
1 制动系统设计的意义 (6)1。
2 制动系统研究现状 (6)1.3 本次制动系统应达到的目标 (6)1.4 本次制动系统设计要求 (6)第二章制动系统方案论证分析与选择 (7)2.1 制动器形式方案分析 (7)2。
1.1 鼓式制动器 (7)2。
1。
2 盘式制动器 (9)2。
2 制动驱动机构的结构形式选择 (10)2.2.1 简单制动系 (10)2。
2。
2 动力制动系 (10)2。
2。
3 伺服制动系 (11)2。
3 液压分路系统的形式的选择 (11)2.3.1 II型回路 (11)2.3.2 X型回/路 (12)2。
3。
3 其他类型回路 (12)2。
4 液压制动主缸的设计方案 (12)第三章制动系统设计计算 (15)3.1 制动系统主要参数数值 (15)3.1.1 相关主要技术参数 (15)3.1.2 同步附着系数的分析 (15)3.2 制动器有关计算 (16)3.2。
1 确定前后轴制动力矩分配系数β (16)3。
2。
2制动器制动力矩的确定 (16)3.2。
3 后轮制动器的结构参数与摩擦系数的选取 (17)3.2.4 前轮盘式制动器主要参数确定 (18)3。
3 制动器制动因数计算 (19)3.3.1 前轮盘式制动效能因数 (19)3.3。
2 后轮鼓式制动器效能因数 (19)3。
4 制动器主要零部件的结构设计 (20)第四章液压制动驱动机构的设计计算 (22)4。
1 后轮制动轮缸直径与工作容积的设计计算 (22)4.2 前轮盘式制动器液压驱动机构计算 (23)4.3 制动主缸与工作容积设计计算 (24)4.4 制动踏板力与踏板行程 (24)4.4。
1 制动踏板力 (24)4.4.2 制动踏板工作行程 (25)第五章制动性能分析 (26)5.1 制动性能评价指标 (26)5.2 制动距离S (26)5。
制动系统计算说明书
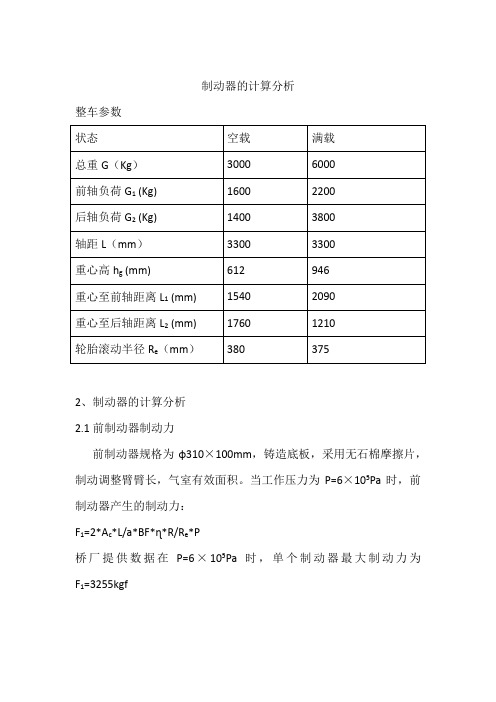
制动器的计算分析整车参数2、制动器的计算分析2.1前制动器制动力前制动器规格为ɸ310×100mm,铸造底板,采用无石棉摩擦片,制动调整臂臂长,气室有效面积。
当工作压力为P=6×105Pa时,前制动器产生的制动力:F1=2*A c*L/a*BF*ɳ*R/R e*P桥厂提供数据在P=6×105Pa时,单个制动器最大制动力为F1=3255kgf以上各式中:A c—气室有效面积L—调整臂长度a—凸轮基圆直径BF—制动器效能因数R—制动鼓半径R e—车轮滚动半径ɳ—制动系效率P—工作压力2.2后制动器制动力后制动器规格为ɸ310×100mm,铸造底板,采用无石棉摩擦片,制动调整臂臂长,气室有效面积。
当工作压力为P=6×105Pa时,前制动器产生的制动力:F2=2*A c*L/a*BF*ɳ*R/R e*P桥厂提供数据在P=6×105Pa时,单个制动器最大制动力为F2 =3467kgf2.3满载制动时的地面附着力满载制动时的地面附着力是地面能够提供给车轮的最大制动力,正常情况下制动气制动力大于地面附着力是判断整车制动力是否足够的一个标准。
地面附着力除了与整车参数有关之外,还与地面的附着系数有关,在正常的沥青路面上制动时,附着系数ϕ值一般在0.5~0.8之间,我们现在按照路面附着系数为0.7来计算前后地面附着力:F ϕ前=G 满1×ϕ+G hgL×ϕ2=2200×0.7+6000×6123300×0.72=2002kgfF ϕ后=G 满2×ϕ-GhgL×ϕ2=3800×0.7-6000×9463300×0.72=1487kgf因为前面计算的前后制动器最大制动力分别为F1=3255kgfF2=3467kgf3、制动器热容量、比摩擦力的计算分析 3.1单个制动器的比能量耗散率的计算分析 前制动器的衬片面积A 1=2×πR 1×w1180×L 1=mm 2式中(L 1=100mm 摩擦片的宽度 w 1=110°) 后制动器的衬片面积A 2=2×πR 2×w2180×L 2=mm 2式中(L 2=100m m 摩擦片的宽度 w2=) 比能量耗散率e 1=GV 124tA 1β= e 2=GV 124tA 2β=上式中:G —满载汽车总质量V 1—制动初速度,计算时取V 1=18m/s β—满载制动力分配系数 t —制动时间,计算时取t=3.06s鼓式制动器的比能量耗散率以不大于1.8W/mm 2为宜,故该制动器的比能量耗散率满足要求。
毕业设计制动系设计计算说明书
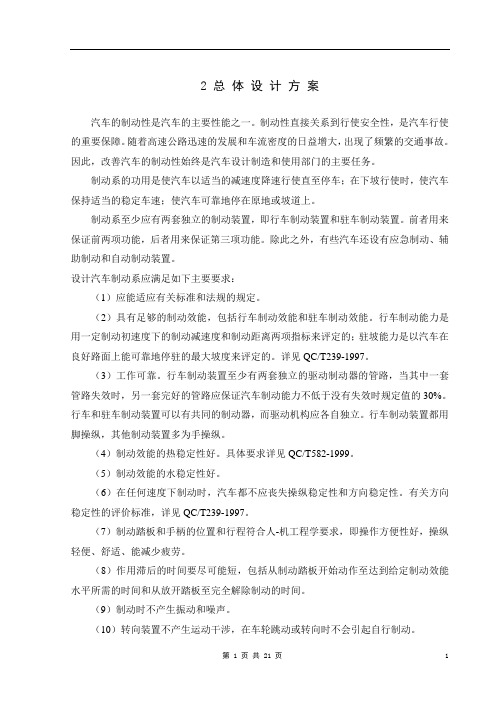
2.4.2 制动原理和工作过程
图 2-2
要使行使中的汽车减速,驾驶员应踩下制动踏板,通过推杆和主缸活塞,使主缸内 的油液在一定压力下流入轮缸,并通过两个轮缸活塞推动两制动蹄绕支撑销转动,上端 向两边分开而其摩擦片压紧在制动鼓的内圆面上。这样,不旋转的制动蹄就对旋转的制 动鼓作用一个摩擦力矩,其方向与车轮旋转方向相反。制动鼓将该力矩传到车轮后,由 于车轮与路面间有附着作用,车轮对路面作用一个向前的周缘力,同时路面也对车轮作 用一个向后的反作用力,即制动力。制动力由车轮经车桥和悬架传给车架和车身,迫使 整个汽车产生一定的减速度。制动力越大,制动减速度越大。当放开制动踏板时,复位 弹簧即将制动蹄拉回复位,摩擦力矩和制动力消失,制动作用即行终止。
第 5 页 共 21 页
5
第 6 页 共 21 页
6
3 制动系主要参数确定
3.1 CS1028 皮卡车型的基本参数
空 汽车质量 前 轴荷分配 质心高度 轴 距 后 轴 轴
载
满
载
1625kg 850kg 775kg 0.52m 2.7m 0.37m
2325kg 920kg 1405kg 0.57m
Ff 1 Ff
0.565
空载条件: Ff 1 8630.3 N
Ff 2 4109.7 N
Ff 1 Ff
0.677
前、后制动器制动力分配的比例影响到汽车制动时方向稳定性和附着条件利用程 度。要确定 值首先就要选取同步附着系数 0 。一般来说,我们总是希望前轮先抱死 ( 0 ) 。 根据有关文献推荐以及我国道路条件, 车速不高, 所以本车型选取 0 0.6 。 为保证汽车制动时的方向稳定性和有足够的附着系数利用率,ECE 的制动法规规 定,在各种载荷条件下,轿车在 0.15 q 0.8,其他汽车在 0.15 q 0.3 的范围内,前 轮应先抱死;在车轮尚未抱死的情况下,在Байду номын сангаас0.15 0.8 的范围内,必须满足 q 0.1 0.85( 0.2)
FSAE制动系统的设计计算
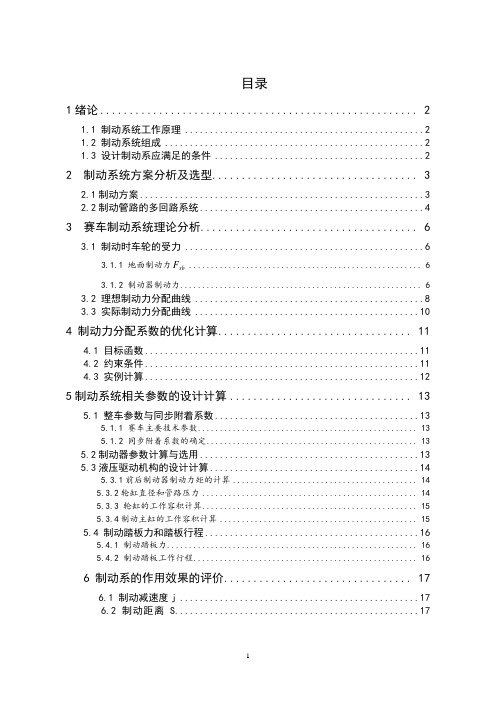
目录1绪论 (2)1.1 制动系统工作原理 (2)1.2 制动系统组成 (2)1.3 设计制动系应满足的条件 (2)2 制动系统方案分析及选型 (3)2.1制动方案 (3)2.2制动管路的多回路系统 (4)3 赛车制动系统理论分析 (6)3.1 制动时车轮的受力 (6)F (6)3.1.1 地面制动力xb3.1.2 制动器制动力 (6)3.2 理想制动力分配曲线 (8)3.3 实际制动力分配曲线 (10)4 制动力分配系数的优化计算 (11)4.1 目标函数 (11)4.2 约束条件 (11)4.3 实例计算 (12)5制动系统相关参数的设计计算 (13)5.1 整车参数与同步附着系数 (13)5.1.1 赛车主要技术参数 (13)5.1.2 同步附着系数的确定 (13)5.2制动器参数计算与选用 (13)5.3液压驱动机构的设计计算 (14)5.3.1前后制动器制动力矩的计算 (14)5.3.2轮缸直径和管路压力 (14)5.3.3 轮缸的工作容积计算 (15)5.3.4制动主缸的工作容积计算 (15)5.4 制动踏板力和踏板行程 (16)5.4.1 制动踏板力 (16)5.4.2 制动踏板工作行程 (16)6 制动系的作用效果的评价 (17)6.1 制动减速度j (17)6.2制动距离S (17)1绪论1.1 制动系统工作原理汽车上用以使外界(主要是路面)在汽车某些部分(主要是车轮)施加一定的力,从而对其进行一定强度的制动的一系列专门装置称为制动系统。
其作用是使行驶中的汽车按照驾驶员的要求强制减速甚至停车,和使已停止的汽车在各种道路条件下稳定驻车,及使下坡行驶的汽车速度保持稳定。
制动系统的一般工作原理:利用车身(或车架)相连的非旋转原件和与车轮(或传动轴)相连的旋转元件之间的相互摩擦来阻止车轮的转动或转动的趋势。
1.2 制动系统组成一般来说,每辆汽车的制动系都由供能装置,控制装置,传能装置,和制动器组成。
某车型制动系统设计计算书(后盘)
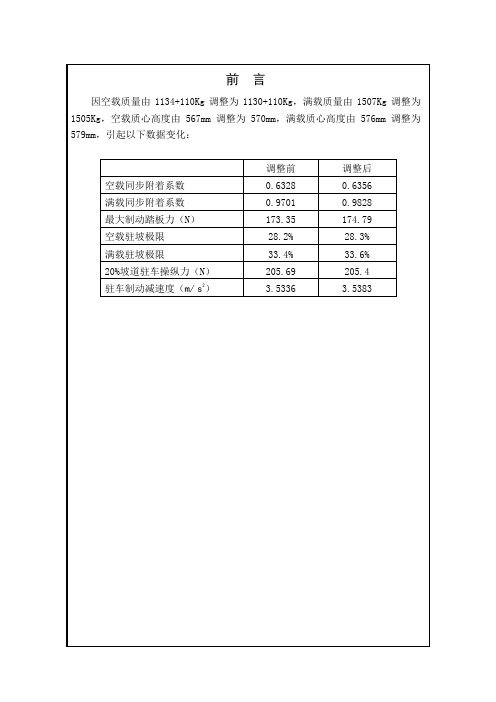
目录1 概述 (1)2 引用标准 (1)3 计算过程 (1)3.1整车参数 (1)3.2理想的前、后制动器制动力分配曲线 (1)3.3NA01制动系统性能校核 (3)3.3.1 NA01制动系统基本参数 (3)3.3.2 制动力分配曲线绘制及同步附着系数确定 (4)3.3.3 前、后轴利用附着系数曲线绘制 (5)3.3.4 空、满载制动距离校核 (7)3.3.5 真空助力器失效时制动减速度校核 (7)3.3.6 ESP系统失效制动减速度校核 (8)3.3.7 任一管路失效制动减速度校核 (8)3.3.8 制动踏板力校核 (8)3.3.9 制动主缸排量校核 (9)3.3.10 制动踏板行程校核 (9)3.3.11 驻车制动校核 (10)4 结论 (12)参考文献 (13)1 概述根据NA01乘用车设计开发目标,设计和开发NA01制动系统,要求尽量沿用M2零部件。
NA01制动系统共有三种配置:ESP+前盘后盘式制动器,ABS+前盘后鼓式制动器,比例阀+前盘后鼓式制动器,此三种配置需分别校核其法规要求符合性。
本计算书是根据整车室提供的NA01整车的设计参数(空载质量、满载质量、轴荷、轴距及质心高度),对经过局部改善(制动主缸直径由22.22mm 更改为20.64mm)的制动系统(ESP+前盘后盘式制动器)的适宜性进行校核计算,以选择合适的参数作为NA01制动系统的设计值。
2 引用标准GB 21670-2008 乘用车制动系统技术要求及试验方法。
GB 7258-2004 机动车运行安全技术条件 3 计算过程 3.1整车参数3.2 理想的前、后制动器制动力分配曲线制动时前、后车轮同时抱死,对附着条件的利用、制动时汽车方向稳定性均较为有利,此时的前、后轮制动器制动力1μF 和2μF 的关系曲线,常称为理想的前、后轮制动器制动力分配曲线。
在任何附着系数ϕ的路面上,前、后车轮同时抱死的条件是:前、后制动器制动力之和等于附着力,并且前、后轮制动器制动力分别等于各自的附着力,即:g F m F 21ϕμμ=+ (1)gg h L h L ϕϕμμ-+=1221F F (2)经计算得:221ϕϕμL h mg L L mg F g +=…………………………(3) 212ϕϕμLh mgLLmg F g -= (4)式中:1μF 、2μF ——前、后轮制动器制动力,N ;ϕ——路面附着系数;m ——整车质量,kg ; hg ——汽车质心高度,m; L ——汽车轴距,m;1L ——质心至前轴中心线的距离,m;2L ——质心至后轴中心线的距离,m。
制动系统毕业设计计算参考
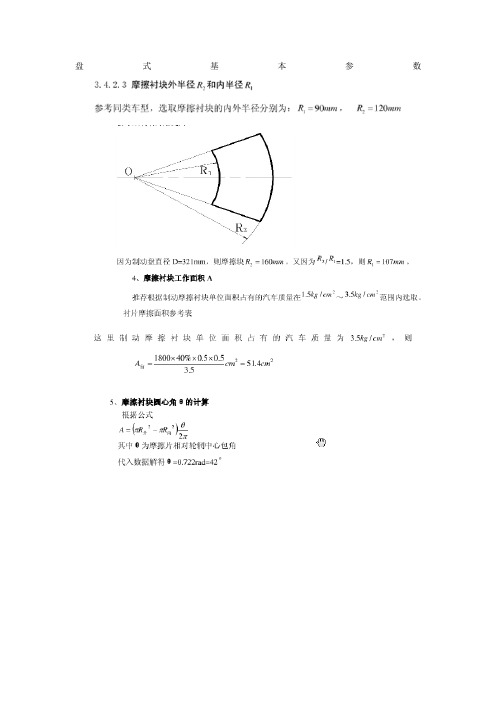
盘式基本参数5.2 凸轮张开力的确定及蹄自锁性校核5.2.1 张开力P1与P2的确定在计算鼓式制动器时,必须建立制动蹄对制动鼓的压紧力与所产生的制动力矩之间的关系。
为计算有一个自由度的制动蹄片上的力矩1Tf T ,在摩擦衬片表面上取一横向单元面积,并使其位于与1y 轴的交角为α处,单元面积为αbRd 。
,其中b 为摩擦衬片宽度,R 为制动鼓半径,αd 为单元面积的包角,如图4-1所示。
由制动鼓作用在摩擦衬片单元面积的法向力为:αααd bR q qbRd dN sin max == (5-1)而摩擦力fdN 产生的制动力矩为ααd f bR q dNfR dT Tf sin 2max ==在由α'至α''区段上积分上式,得)cos (cos 2max αα''-'=f bR q T Tf (5-2) 当法向压力均匀分布时,αbRd q dN p = )(2αα'-''=f bR q T p Tf (5-3)由式(46)和式(47)可求出不均匀系数)cos /(cos )(αααα''-''-''=∆式(46)和式(47)给出的由压力计算制动力矩的方法,但在实际计算中采用由张开力P 计算制动力矩1Tf T 的方法则更为方便。
增势蹄产生的制动力矩1Tf T 可表达如下:111ρfN T Tf = (5-4)式中 1N ——单元法向力的合力;1ρ——摩擦力1fN 的作用半径(见图5-3)。
如果已知制动蹄的几何参数和法向压力的大小,便可用式(17—46)算出蹄的制动力矩。
1N 与张开力1P 的关系式,写出为了求得力制动蹄上力的平衡方程式:0)sin (cos cos 111101=+-+δδαf N S P x01111=+'-N f C S a P x ρ (5-5)式中 1δ——1x 轴与力1N 的作用线之间的夹角;x S 1——支承反力在x1轴上的投影。
BJ1039E2制动系统设计计算word文档
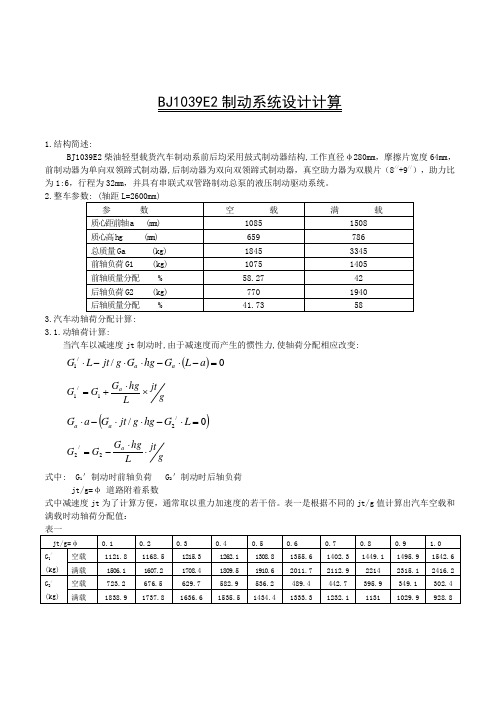
BJ1039E2制动系统设计计算1.结构简述:BJ1039E2柴油轻型载货汽车制动系前后均采用鼓式制动器结构,工作直径φ280mm ,摩擦片宽度64mm ,前制动器为单向双领蹄式制动器,后制动器为双向双领蹄式制动器,真空助力器为双膜片(8//+9//),助力比为1:6,行程为32mm ,并具有串联式双管路制动总泵的液压制动驱动系统。
2.3.汽车动轴荷分配计算: 3.1.动轴荷计算:当汽车以减速度jt 制动时,由于减速度而产生的惯性力,使轴荷分配相应改变:()0//1=-⋅-⋅⋅-⋅a L G hg G g jt L G a ag jtLhg G G G a ⨯⋅+=1/1()0//2=⋅-⋅⋅-⋅L G hg g jt G a G a a g jt Lhg G G G a ⋅⋅-=2/2式中: G 1'制动时前轴负荷 G 2'制动时后轴负荷jt/g=φ 道路附着系数式中减速度jt 为了计算方便,通常取以重力加速度的若干倍。
表一是根据不同的jt/g 值计算出汽车空载和满载时动轴荷分配值:3.2动载荷分配比:对汽车在不同的减速度jt/g 值时前后轴动载荷分配比按下式计算: 前轴动轴荷:G 1'/Ga ×100% 后轴动轴荷:G 2'/Ga×100%表二为汽车制动时前后在不同减速度jt/g 值时动轴荷分配比:4.汽车制动力的计算:4.1.汽车制动时所需的制动力P τ(轴制动力)当汽车以减速度jt/g 制动时,前后各自所需的制动力为: 前轴: P τ1=G 1'×jt/g ×9.8 (N) 后轴: P τ2=G 2'×jt/g ×9.8 (N)4.2制动器实际所产生的制动力及制动力分配比: 4.2.1.汽车前轴制动器所产生的制动力P τ1':前轴制动扭矩: 0211/142P R d BEF Mt ⨯⨯⨯⨯=π()0214.0032.040.32P ⨯⨯⨯⨯⨯=π()m N P •⨯=-041075.6()N P P R Mt Pt k 0304/1/11001.210336.075.6--⨯=⨯==式中: T 1:单个前轮能发出的制动扭矩BEF 1:前制动器效率因数(3.0) d 1:前制动器分泵直径(φ=32mm) R k :前轮滚动半径(336mm)4.2.2.汽车后轴制动器所能产生的制动力P τ2': 后轴制动扭矩:0222/242P R d BEF Mt ⨯⨯⨯⨯=π0214.00254.040.32P ⨯⨯⨯⨯⨯=π()m N P •⨯=-041025.4()N P P R Mt Pt k 0304/2/21026.110336.025.4--⨯=⨯==式中: T2:单个后轮能发出的制动扭矩BEF2:后制动器效率因数(3.0) d2:后制动器分泵直径(φ25.4mm) Rk:后轮滚动半径(336mm)4.2.3.前后制动器实际制动力分配比:615.010)26.101.2(1001.233'2'1'1=⨯+⨯=+=--t t t P P P β 4.3 同步附着系数: 645.0786)15082600(615.026000=--⨯=-=hg b L βϕ 4.4 满载时前后轴附着力矩:(道路附着系数Φ=0.7时的附着力矩)前轴附着力矩: 1.4870336.02.14494=⨯=前ϕM 后轴附着力矩: 2840336.05.8452=⨯=后ϕM 4.5 最大管路压力max 0P :产生最大管路压力矩时(Φ=0.7)的管路压力为最大管路压力,故:当Φ=0.7时,后轮先抱死,此时前轮制动所需的油压大于后轮制动所需油压:即: at MP P P M M 2.71.48701075.6004'1=∴=⨯=-前ϕ4.6 制动踏板力计算:I P S P m p /0⨯=式中:Pp:制动踏板力Sm:制动总泵活塞面积 P0:制动管路压力 I :踏板杠杆比故: )(1055.12.51032440062N P P P p --⨯=⨯⨯⨯=π汽车满载时制动管路油压P0为(Φ=0.7): P τ1=G 1'×jt/g ×9.8 8.97.0)7.0260078633451405(8.9/)/(1001.2103⨯⨯⨯⨯+=⋅⋅⋅+=⨯-g jt g jt Lh G G P ga)(7.1117N P p =∴因BJ1039E2制动系统采用真空助力机构,所以实际踏板力取决于真空助力器的助力因数K,现该车型采用的真空助力器的K=6,所以实际踏板力如表四(KP P pF =):从上表可以得出:制动踏板力PF ≤700N ,完全符合GB7258-1997《机动车运行安全技术条件》的规定和要求。
轻型汽车制动系统设计计算书
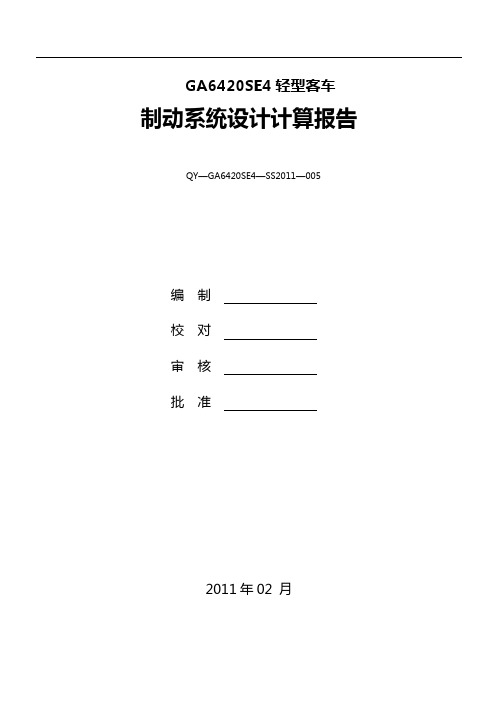
由公式(8)和(9)可得 :
F1 F
F1 F1 F 2
(9)
由于
d12 BF1 r1 2 d12 BF1 r1 d 2 BF2 r2
F (1 ) F 1
(10)
F1 F 2
(11)
故
图1
GA6420SE4 感载比例阀配置制动系统结构简图
4.制动管路 5.制动轮缸 6.六通阀 7.感载比例阀
1. 带制动主缸的真空助力器总成 2.制动踏板 3.车轮
1.4
计算目的
制动系统计算的目的在于校核前、后制动力是否足够,最大制动距离、制动踏板力、驻车制 动手柄力及驻坡极限倾角等是否符合法规及标准要求、制动系统匹配是否合理。 2 制动法规基本要求 1、满足国内最新制动法规对制动效能,包括行车制动系、应急制动系、驻车制动系性能要求, 如表 1 所示:
版本
日期
作者
更改记录
Байду номын сангаас
批准
制动系统设计计算报告
1 1.1 发。 1.2 GA6420SE4 制动系统基本介绍 GA6420SE4 车型的行车制动系统采用液压制动系统, 前制动器为空心盘式制动器, 后制动器为 鼓式制动器,制动踏板为吊挂式踏板,真空助力器为非贯穿式单膜片结构,制动主缸结构为补偿 孔式。基本车型为带六通阀及感载比例阀的双 I 型制动管路布置,配备的感载比例阀具有液压保 护结构,当制动主缸后腔及管路正常工作时,后腔管路液压与前制动器管路不通,当后腔管路失 效时,主缸前腔液压将与后制动器相通,保证后制动器正常工作。驻车制动系统为机械式后鼓式 制动,采用远距离棘轮拉索操纵机构。 1.3 GA6420SE4 制动系统的结构简图 对于装配感载比例阀的制动系统结构,见图 1: 概述 任务来源 根据 xx 汽车有限公司产品规划及新车型开发项目的要求, 进行 GA6420SE4 项目车型的设计开
制动系统设计说明书
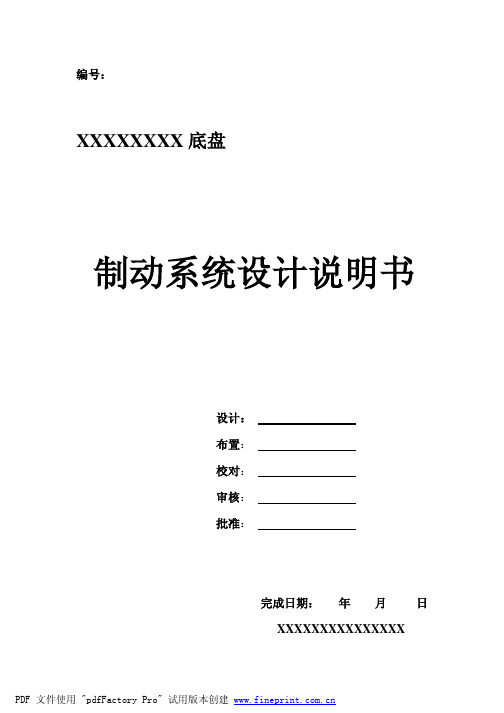
PDF 文件使用 "pdfFactory Pro" 试用版本创建
前轴荷:6500Kg
后轴荷:11500Kg
将相关参数代入制动系计算程序
得到:(以下所称标准均为中国汽车标准) ---------------制动过程模拟计算分析-------------
1.空载同步系数. 0.702951652069104 2.满载同步系数. 0.487450622408438 3.驻车制动力符合实验要求. 4.空载时制动力与轴荷比符合标准. 5.满载时制动力与轴荷比符合标准. 6.空载时前制动力与前轴荷比符合标准. 7.满载时前制动力与前轴荷比符合标准. 8.在初速度 30Km/h 情况下制动距离符合制动标准.
13.在初速度 60Km/h 情况下平均减速度符合 ECE 标准
14.上坡驻车角度. 28.301318090934
15.下坡驻车角度. 20.9464441425081
************************** 一.在 30Km/h 制动初速度下地面附着系数为:0.3,0.4,0.5,0.6,0.7 时的制动平均减速度: 2.23812423873325 2.76419706656638 3.21803852889667 3.61356932153392 3.96134893748075
六.结论
根据以上分析可以得出选用的制动系统制动力大小和前后分配符合本底盘的制动要求,并满 足制动法规。同时制动器的左右制动差要满足要求,如在实验中不能满足左右制动差要求请 对制动间隙进行调整。(左右轮制动力差与该轴左右轮中制动力大者之比对前轴应≤20%,对 后轴应≤24%)
制动系统设计计算分析
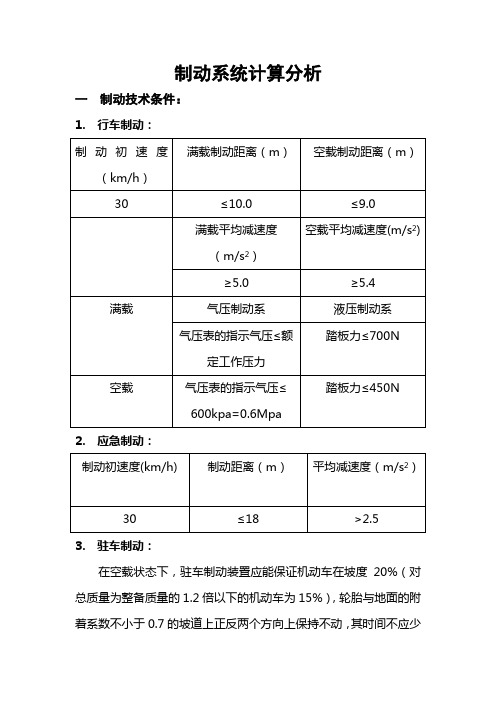
制动系统计算分析一制动技术条件:1. 行车制动:2. 应急制动:3. 驻车制动:在空载状态下,驻车制动装置应能保证机动车在坡度20%(对总质量为整备质量的1.2倍以下的机动车为15%),轮胎与地面的附着系数不小于0.7的坡道上正反两个方向上保持不动,其时间不应少于5分钟。
二制动器选型1.最大制动力矩的确定根据同步附着系数和整车参数,确定前后轴所需制动力矩的范围,最大制动力是汽车附着质量被完全利用的条件下获得的,设良好路面附着系数φ=0.7。
满载情况下,确定前后轴制动器所需要的最大制动力矩。
为:前轴Mu1=G*φ(b+φ*h g)*r e /L (N.m)后轴Mu2=G*φ(a-φ*h g)*r e /L (N.m)或者Mu1=β/(1-β)* Mu2 【β=(φ*h g+b)/L】其中r e -轮胎有效半径a-质心到前轴的距离b-质心到后轴的距离h g -质心高度L-轴距φ-良好路面附着系数G-满载总重量(N;g=9.8m/s2)同理:空载亦如此。
前轴;Mu11 后轴:Mu21根据满载和空载的情况,确定最大制动力矩,此力满足最大值。
所以:前轮制动器制动力矩(单个)≥Mu1或Mu11/2后轮制动器制动力矩(单个)≥Mu2或Mu21/22.行车制动性能计算(满载情况下)已知参数:前桥最大制动力矩Tu1(N.m) 单个制动器后桥最大制动力矩Tu2(N.m) 单个制动器满载整车总质量M(kg)①整车制动力Mu1= Tu1*φ*2 (N.m)Mu2= Tu2*φ*2 (N.m)Fu= (Mu1+ Mu2)/r e (N)②制动减速度a b=Fu/M (m/s2)③制动距离S= U a0*(t21+ t211 /2)/3.6+ U a02 /25.92* a b其中:U a0 (km/h)-制动初速度,t21+ t211 /2 为气压制动系制动系作用时间(一般在0.3-0.9s)3.驻车制动性能计算满载下坡停驻时后轴车轮的附着力矩:MfMf=M*g*φ(a*cosα/L -h g*sinα/L)*r e (N.m)其中附着系数φ=0.7 坡度20%(α=11.31o)在20%坡上的下滑力矩:M滑M滑=M*g*sinα*r e (N.m)驻车度α=11.31o则Mf>M滑时,满足驻车要求。
制动系统设计与计算

从上述计 算和图表 中可以看 到,该车 的制动器 附着系数 利用曲线 负荷ECE 标准。
空载
附着系数利用法规线 GB21670
GB21670 -2008中要求:在车辆所有载荷状态下,当制动强度z处于0.15~0.80之间时,后轴附着系数利用 于前轴上方;当附着系数ψ在0.2~0.8之间时,制动强度z≥0.1+0.7(ψ-0.2)。
G* (b+z*hg )/L 10457.36 N
φ*Fz1
8124.393 N 2372.323 N.m G*(az*hg)/L 7079.145 φ*Fz2 5499.833 N 1605.951 N.m
空载
G*
汽车前轮最大法向反作用力Fz1‘
(b+z*hg )/L
8768.286 N
汽车前轮空载最大地面附着力Fxb1' φ*Fz1
7077.212377 3255.907623
0.9
2.46178968
8266.739706 3358.020294
1
2.807471264
9524.017208 3392.382792
β曲线(与制动系统的参数有关,制动系统参数定义完成后,β曲线就定义完成)
前制动器所能提供的最大制动力
后制动器所能提供的最大制动力
制动强度 前轴的利用附着系数 0
后轴的利用附着系数
0.1
0.2
0.3
0.4
0.5
0.6
同上
0.7
0.8
0.9
同上 空载
1
1.1
满载 制动强度 前轴的利用附着系数
0 0.1
0.2
0.3
0.4
汽车制动系统计算
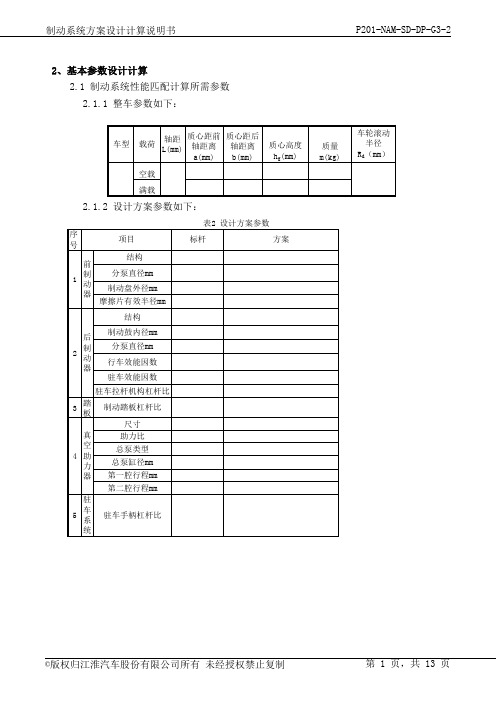
2、基本参数设计计算2.1 制动系统性能匹配计算所需参数2.1.1 整车参数如下:2.1.2 设计方案参数如下:2.2 制动系统性能目标整车制动性能目标要求如下:2.3 制动系统性能参数匹配计算 2.3.1 整车理论制动力计算Z 1——汽车制动时水平地面对前轴车轮的法向反力,N;Z 2——汽车制动时水平地面对后轴车轮的法向反力,N;L——汽车轴距,mm;a——汽车质心离前轴的距离,mm;b——汽车质心离后轴的距离,mm;h g ——汽车质心高度,mm;G——汽车所受重力,N;m——汽车质量,kg;静态驻坡驻坡度≥18%制动减速度(m/s 2)≥2.2制动减速度(m/s 2)≥2.2满载失效制动(70km/h)前失效制动距离(m)≤95.7后失效制动距离(m)≤95.7后失效制动距离(m)≤95.7空载失效制动(70km/h)前失效制动距离(m)≤95.7制动减速度(m/s 2)≥2.2满载制动(80km/h)冷态制动距离-O型(m)≤61.2制动减速度(m/s 2)≥5.0设计要求空载制动(80km/h)冷态制动距离-O型(m)≤61.2制动减速度(m/s 2)≥5.0图1 整车受力简图制动减速度(m/s 2)≥2.2项目制动安全性能法规要求整车前、后轴理论需要的制动力计算公式如下:前、后制动器制动力计算式:其中: 、 ——前、后制动器制动力,NP 1、P 2——前、后制动器管路压力,MPa d 1、d 2——前、后制动器轮缸直径,mm ——前、后制动器单侧油缸数目r 1、r 2——前、后制动器有效半径,mm BF 1、BF 2——后制动器效能因数R——前、后轮滚动半径,mm制动器制动力分配系数:整车同步附着系数 计算式:其中:L L ——汽车轴距,mm;b ——汽车质心离后轴的距离,mm;h g ——汽车质心高度,mm;β——制动力分配系数根据整车参数,计算得出在各种状况下整车需要的理论制动力如下:表4 各附着系数路面下空、满载前、后轴理想制动力n 1、n2Rr BF n d p F 111211142⋅⋅⋅⋅⋅=πμ ()μμμg if h L G Z F +==b 1()μμμg ir h a LGZ F -==20ϕgh b L -=βϕ0211u u u F F F +=β1μF 2μF Rr BF n d p F 222222242⋅⋅⋅⋅⋅=πμ根据前、后制动器参数,计算出在不同管路压力下,前、后制动器输出制动力如下:此时,整车的同步附着系数计算如下:车型方案一的I曲线和β曲线图如下:标杆名称代号图2 车型的I曲线与β线压强MPa 标杆12空载同步附着系数满载同步附着系数表6 制动力分配系数和同步附着系数方案6783491011125方案选配方案(四轮盘式)irF if F 0ϕ'0ϕirF ifF if F irF通过对比整车理论制动力需求和制动器实际输出力,可以得出:2.3.2 整车利用附着系数与制动强度校核前、后轴利用附着系数:式中: ——前轴利用附着系数;——后轴利用附着系数;——前轴到质心水平距离,m;——后轴到质心水平距离,m;——制动强度。
制动系统设计计算书
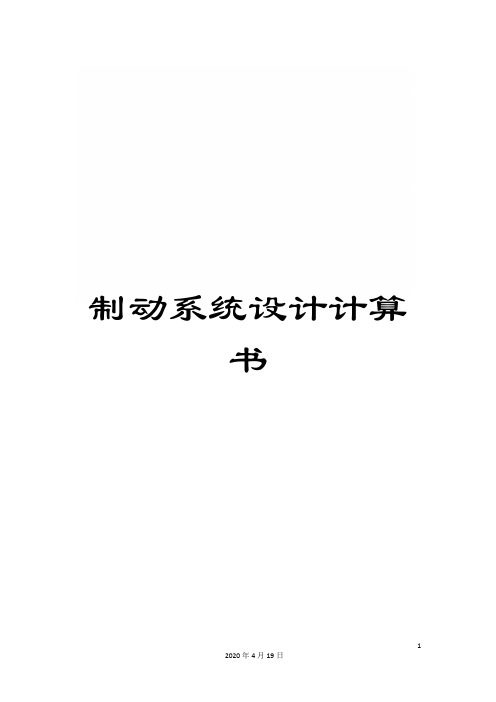
制动系统设计计算书12020年4月19日批准:日期:上海同济同捷科技股份有限公司长春孔辉汽车科技有限公司年 12 月中国高水平汽车自主创新能力建设底盘制动系统设计计算书目录1基本参数输入 ......................................................................................................................- 1 -2制动系统的相关法规 ..........................................................................................................- 2 -3整车制动力分配计算 ..........................................................................................................- 2 -3.1汽车质心距前后轴中心线距离的计算 ...........................................................................- 2 -3.2理想前后地面制动力的计算 ............................................................................................- 2 -3.3前后制动器缸径的确定 ..................................................................................................- 4 -3.4确定制动力分配系数 ......................................................................................................- 5 -3.5确定同步附着系数Φ0 ....................................................................................................- 5 -4制动力分配曲线的分析 ......................................................................................................- 5 -4.1绘制I曲线和β曲线 ......................................................................................................- 5 -4.2前后制动器制动力分配的合理性分析 ...........................................................................- 6 -4.2.1制动法规要求 ................................................................................................................- 7 -4.2.2前后轴利用附着系数曲线的分析 ................................................................................- 7 -5制动系统结构参数的确定 ..................................................................................................- 9 -5.1制动管路的选择 ..............................................................................................................- 9 -5.2制动主缸的结构参数的确定 ..........................................................................................- 9 -5.2.1轮缸容积的确定 ........................................................................................................- 10 -5.2.2软管容积增量的确定 ................................................................................................- 10 -5.2.3主缸容积的确定 ........................................................................................................- 10 -5.2.4主缸活塞直径的确定 ................................................................................................- 11 -5.2.5主缸行程的确定 ..........................................................................................................- 11 -5.3踏板机构的选择 ............................................................................................................- 11 -5.4制动踏板杠杆比的确定 ................................................................................................- 12 -5.4.1真空助力比的确定 ....................................................................................................- 12 -5.4.2踏板行程的确定 ........................................................................................................- 12 -5.4.3主缸最大压力的确定 ................................................................................................- 12 -5.4.4主缸工作压力的确定 ................................................................................................- 13 -中国高水平汽车自主创新能力建设制动系统设计计算书5.4.5 最大踏板力的确定......................................................................................................- 13 -- 13 -6驻车性能的计算 ................................................................................................................- 14 -7制动性能的校核 ..................................................................................................................- 15 -7.1制动减速度的计算 ..........................................................................................................7.2错误!未定义书签。
制动系统匹配设计计算
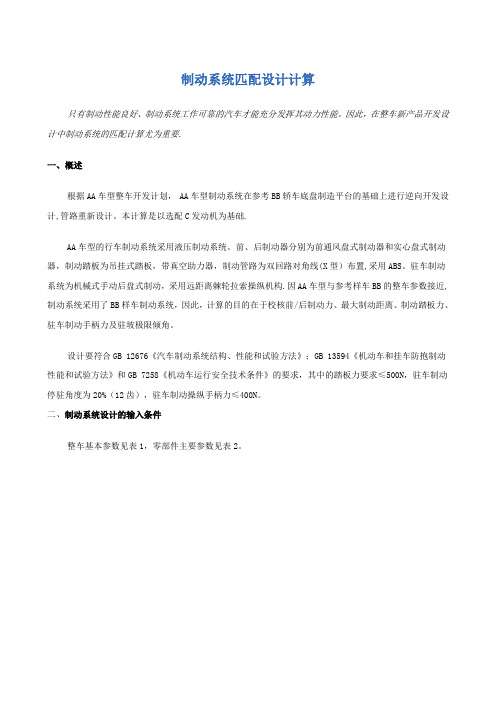
制动系统匹配设计计算只有制动性能良好、制动系统工作可靠的汽车才能充分发挥其动力性能。
因此,在整车新产品开发设计中制动系统的匹配计算尤为重要.一、概述根据AA车型整车开发计划, AA车型制动系统在参考BB轿车底盘制造平台的基础上进行逆向开发设计,管路重新设计。
本计算是以选配C发动机为基础.AA车型的行车制动系统采用液压制动系统。
前、后制动器分别为前通风盘式制动器和实心盘式制动器,制动踏板为吊挂式踏板,带真空助力器,制动管路为双回路对角线(X型)布置,采用ABS。
驻车制动系统为机械式手动后盘式制动,采用远距离棘轮拉索操纵机构.因AA车型与参考样车BB的整车参数接近,制动系统采用了BB样车制动系统,因此,计算的目的在于校核前/后制动力、最大制动距离、制动踏板力、驻车制动手柄力及驻坡极限倾角。
设计要符合GB 12676《汽车制动系统结构、性能和试验方法》;GB 13594《机动车和挂车防抱制动性能和试验方法》和GB 7258《机动车运行安全技术条件》的要求,其中的踏板力要求≤500N,驻车制动停驻角度为20%(12齿),驻车制动操纵手柄力≤400N。
二、制动系统设计的输入条件整车基本参数见表1,零部件主要参数见表2。
表1 整车基本参数表2 零部件主要参数三、制动系统设计计算(法规校核)1、地面对前、后车轮的法向反作用力地面对前、后车轮的法向反作用力如图1所示.图1 制动工况受力简图由图1,对后轮接地点取力矩得:(1)式中: FZ1(N):地面对前轮的法向反作用力;G(N):汽车重力;b(m):汽车质心至后轴中心线的水平距离;m(kg):汽车质量;hg(m):汽车质心高度;L(m):轴距;du/dt(m/s2):汽车减速度.对前轮接地点取力矩,得:(2)式中:FZ2(N):地面对后轮的法向反作用力;a(m):汽车质心至前轴中心线的距离.2、理想前后制动力分配在附着系数为ψ的路面上,前、后车轮同步抱死的条件是:前、后轮制动器制动力之和等于汽车的地面附着力;并且前、后轮制动器制动力Fμ1、Fμ2分别等于各自的附着力,即:(3)根据式(1)、(2)及(3),消去变量ψ,得:(4)由(1)、(2)、(3)及此时du/dt=z*g,z=ψ=ψ0,可得:前轴:(5)后轴:(6)由此可以建立由Fu1和Fu2的关系曲线,即I曲线。
- 1、下载文档前请自行甄别文档内容的完整性,平台不提供额外的编辑、内容补充、找答案等附加服务。
- 2、"仅部分预览"的文档,不可在线预览部分如存在完整性等问题,可反馈申请退款(可完整预览的文档不适用该条件!)。
- 3、如文档侵犯您的权益,请联系客服反馈,我们会尽快为您处理(人工客服工作时间:9:00-18:30)。
制动系统设计计算书
(Φ 式制动器,前:后= :)
1.结构简述:
XX 系列车型制动系统前后均采用X 式制动器结构,且前后制动器均为XX 式,并具有X 联式双管路制动总泵(阀)的液(气)压制动驱动系统。
3.1 动轴荷计算:
当汽车以减速度jt制动时,由于减速度而产生的惯性力,使轴荷分配相应改变:
式中: G1'制动时前轴负荷 G2'制动时后轴负荷 jt/g=φ 道路附着系数
其中减速度jt为了计算方便,通常取以重力加速度的若干倍。
表一是根据不同的jt/g值计算出汽车空载和满载时动轴荷分配值: 对汽车在不同的减速度jt/g值时前后轴动载荷分配比按下式计算: 前轴动轴荷:G1'/Ga ×100% 后轴动轴荷:G2'/Ga ×100%
表二为汽车制动时前后在不同减速度jt/g值时动轴荷分配比:
表二(见下页):
()0
//
1=-×-××-×a L G hg G g jt L G a a ()
//
2=×-××-×L G hg g jt G a G a a
4.1.汽车制动时所需的制动力P τ(轴制动力)
当汽车以减速度jt/g制动时,前后各自所需的制动力为: 前轴: P τ1=G1'×jt/g ×9.8 (N) 后轴: P τ2=G2'×jt/g ×9.8 (N)
4.2.1.汽车前轴制动器所产生的制动力P τ1': 前轴制动扭矩: #######P 0(Nm)
#VALUE!P 0(N)
式中: M T1:单个前轮能发出的制动扭矩 BEF1:前制动器效率因数X d1:前制动器分泵直径(φ) m X R k1:前轮滚动半径(m)X
R r1:前制动器有效半径(m)X
4.2.2.汽车后轴制动器所能产生的制动力P τ2':#VALUE!P 0(Nm)
#VALUE!P 0(Nm)
式中: M T2:单个后轮能发出的制动扭矩 BEF2:后制动器效率因数X d2:后制动器分泵直径m X R k2:后轮滚动半径m X
R r2:后制动器有效半径(m)X
#VALUE!
4.3 同步附着系数:
#VALUE!#VALUE!4.4 满载时前后轴附着力矩:(道路附着系数Φ=0.65时的附着力矩)前轴附着力矩:
######(N)后轴附着力矩:
######(N)
4.5 最大管路压力 :
产生最大管路压力矩时(Φ=0.65)的管路压力为最大管路压力,故当Φ=0.65时,#VALUE!
此时前轮制动所需的油压大于后轮制动所需油压: 即:######P 0 =
#VALUE!
P 0=######(Pa)
4.6 制动踏板力计算:
式中:P p :制动踏板力 S m :制动总泵活塞面积
总泵直径为: d=X
m
S m =π/4×d 2=
######m 2
P 0:制动管路压力 I :踏板杠杆比I=X 故:Pp=######P 0(N)
汽车满载时制动管路油压P0为(Φ=0.65):
P τ2=G 2'×jt/g ×9.8
######P 0 =
#VALUE!
P p =######(N)
因BJ1043VBPE7制动系统采用真空助力机构,所以实际踏板力取决于真空助力器的助力比K,因而实际踏板力为P =P /K(见表四),现该车型真空助力器的K=X 表四:=´=1'
1k t R P M ǰj I
P S P m p /0´==´=2'2k t R P M ºó
j Ç
°j M
M t ='1
式中: Va:汽车制动时的初速度(Km/h)
jt:制动减速度 jt=g ·Φ
实际上,在汽车制动时,由踏下踏板到开始产生制动力尚有一段作用时间,取此值为0.2秒,所以际制动距离St必须考虑这一作用时间。
计算时取制动初速度50Km/h
#VALUE!则:
######m ≤22m
所以,制动距离符合GB7258-1997《机动车运行安全技术条件》的规定和要求。
4.8 总泵容量及踏板行程的计算:4.8.1前后轴管路所需的排量:4.8.1.1前制动回路所需的排量:
其中:——前制动分泵截面积
——活塞行程
2.5——前制动管路膨胀量——前制动软管的长度L=X
m ——前制动软管的数量n=2
则:
######mm 3######mm 3
4.8.1.2后制动回路所需的排量:
其中:——后制动分泵截面积
——活塞行程 2.5
——后制动管路膨胀量——后制动软管的长度L=X m ——后制动软管的数量n=
1
则:
######mm 3L n =t S =Va =j 1
1114p i V S V +´´=d 1S 1d 1p V 1000
38.11´´´=L n V P L =1p V n =\1i V 2
114/d S ´=p =1d 2
2
224p i V
S V +´´=d
100038.12´´´=L n V P 2
2
24/d S ´=p =1d 2S 2d 2p V =2p V
######mm 3
4.8.1.3实际总泵排量:
总泵的行程为: 前腔L 前=X
m 后腔L 后=X
m
前腔:
#VALUE!mm 3 ≤#VALUE!mm
3
不符合(调行程)后腔:
#VALUE!mm 3 ≥#VALUE!mm
3符合
4.8.1.4排量的匹配结果:
总泵的排量在调整行程后可以满足使用要求。
4.8.2踏板行程Lp的计算: 踏板杠杆比: I=X 总泵最大空行程: 2mm
######mm ≤150mm
制动踏板行程符合标准规定和要求。
5. 制动器容量的计算
用磨擦片的比能量耗散率[每单位衬片(衬块)磨擦面积的每单位时间耗散的能量]、比磨擦力[每单位衬片(衬块)磨擦面积的制动器的磨擦力]来衡量制动器的热容量和磨损容量。
计算结果见表五:
式中:
Vmax——制动初速度 Vmax=6518.1 jt——制动减速度 取 jt=0.6g
A 1、A 2——前、后制动器衬片(衬块)的磨擦面积
B 1、B 2——前、后制动器衬片(衬块)的宽度B 1=B 2=X
A 1
=2×π×R r1×B 1×δ1/360=######mm 2 A 2=2×π×R r2×B 2×δ2/360=
######mm
2
=
2p V =\2i V =´=ǰǰL S V =´=ºóºóL S V =h Km /s m /mm
δ1、δ2——前、后制动器摩擦片包角 δ1=δ2=224
β1、β2——前、后制动力分配比
β1=######β2=1-β1=#VALUE!
从计算结果来看,前、后制动器的热容量和磨损容量均足够。
6. 计算结果分析:
通过以上分析计算可以看出,整车制动系统的匹配均符合标准的要求,只是踏板行程稍大。
另上述计算结果均与整车参数有关,且计算大都是理想化、理论上的计算,具体情况尚待整车动态试验进一步验证。
助力比K,因而
≤700N)。
,所以实
比磨擦力。
计算结果见
大。
情况尚待整车。