切削液的性能评定
11切削液的加工性能评价
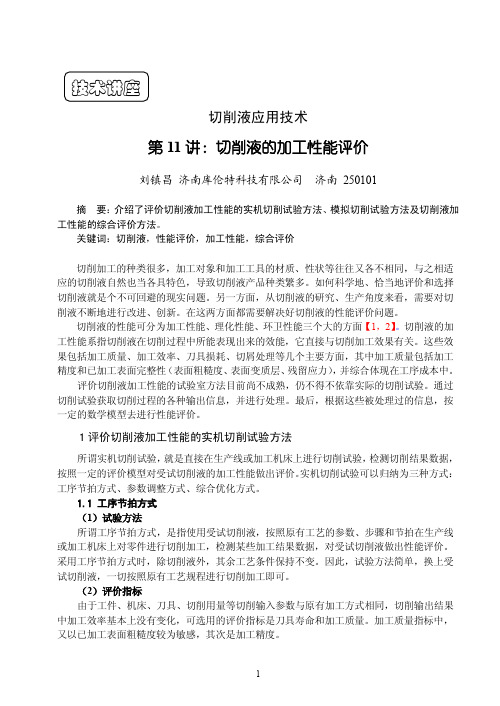
技术讲座切削液应用技术第11讲:切削液的加工性能评价刘镇昌济南库伦特科技有限公司济南250101摘要:介绍了评价切削液加工性能的实机切削试验方法、模拟切削试验方法及切削液加工性能的综合评价方法。
关键词:切削液,性能评价,加工性能,综合评价切削加工的种类很多,加工对象和加工工具的材质、性状等往往又各不相同,与之相适应的切削液自然也当各具特色,导致切削液产品种类繁多。
如何科学地、恰当地评价和选择切削液就是个不可回避的现实问题。
另一方面,从切削液的研究、生产角度来看,需要对切削液不断地进行改进、创新。
在这两方面都需要解决好切削液的性能评价问题。
切削液的性能可分为加工性能、理化性能、环卫性能三个大的方面【1,2】。
切削液的加工性能系指切削液在切削过程中所能表现出来的效能,它直接与切削加工效果有关。
这些效果包括加工质量、加工效率、刀具损耗、切屑处理等几个主要方面,其中加工质量包括加工精度和已加工表面完整性(表面粗糙度、表面变质层、残留应力),并综合体现在工序成本中。
评价切削液加工性能的试验室方法目前尚不成熟,仍不得不依靠实际的切削试验。
通过切削试验获取切削过程的各种输出信息,并进行处理。
最后,根据这些被处理过的信息,按一定的数学模型去进行性能评价。
1评价切削液加工性能的实机切削试验方法所谓实机切削试验,就是直接在生产线或加工机床上进行切削试验,检测切削结果数据,按照一定的评价模型对受试切削液的加工性能做出评价。
实机切削试验可以归纳为三种方式:工序节拍方式、参数调整方式、综合优化方式。
1.1 工序节拍方式(1)试验方法所谓工序节拍方式,是指使用受试切削液,按照原有工艺的参数、步骤和节拍在生产线或加工机床上对零件进行切削加工,检测某些加工结果数据,对受试切削液做出性能评价。
采用工序节拍方式时,除切削液外,其余工艺条件保持不变。
因此,试验方法简单,换上受试切削液,一切按照原有工艺规程进行切削加工即可。
(2)评价指标由于工件、机床、刀具、切削用量等切削输入参数与原有加工方式相同,切削输出结果中加工效率基本上没有变化,可选用的评价指标是刀具寿命和加工质量。
切削液性能的评定方法
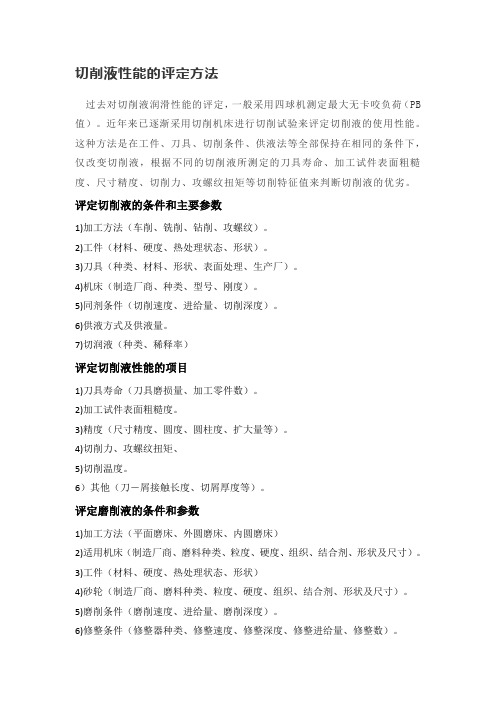
切削液性能的评定方法过去对切削液润滑性能的评定,一般采用四球机测定最大无卡咬负荷(PB 值)。
近年来已逐渐采用切削机床进行切削试验来评定切削液的使用性能。
这种方法是在工件、刀具、切削条件、供液法等全部保持在相同的条件下,仅改变切削液,根据不同的切削液所测定的刀具寿命、加工试件表面粗糙度、尺寸精度、切削力、攻螺纹扭矩等切削特征值来判断切削液的优劣。
评定切削液的条件和主要参数1)加工方法(车削、铣削、钻削、攻螺纹)。
2)工件(材料、硬度、热处理状态、形状)。
3)刀具(种类、材料、形状、表面处理、生产厂)。
4)机床(制造厂商、种类、型号、刚度)。
5)同剂条件(切削速度、进给量、切削深度)。
6)供液方式及供液量。
7)切润液(种类、稀释率)评定切削液性能的项目1)刀具寿命(刀具磨损量、加工零件数)。
2)加工试件表面粗糙度。
3)精度(尺寸精度、圆度、圆柱度、扩大量等)。
4)切削力、攻螺纹扭矩、5)切削温度。
6)其他(刀-屑接触长度、切屑厚度等)。
评定磨削液的条件和参数1)加工方法(平面磨床、外圆磨床、内圆磨床)2)适用机床(制造厂商、磨料种类、粒度、硬度、组织、结合剂、形状及尺寸)。
3)工件(材料、硬度、热处理状态、形状)4)砂轮(制造厂商、磨料种类、粒度、硬度、组织、结合剂、形状及尺寸)。
5)磨削条件(磨削速度、进给量、磨削深度)。
6)修整条件(修整器种类、修整速度、修整深度、修整进给量、修整数)。
7)供液方式及供液量。
8)磨削液(种类、稀释倍数)。
评定磨削液性能的项目1)砂轮寿命(砂轮磨损量、砂轮的磨损状态等)。
2)磨削力。
3)试件表面粗糙度及尺寸精度。
4)工件表面状态(磨削烧伤、磨削裂纹、加工变质层、残余应力)。
5)磨削温度。
6)磨削比。
磨削比的计算如下:磨削比=工件磨除量/砂轮磨损量砂轮磨损量=砂轮半径减少量x砂轮直径xπx工件宽度工件磨除量=(磨前工件高度-磨后工件高度)x 工件长度x工件宽度。
水性切削液

水性切削液
水性切削液是东莞美科所配制的一款高性能水性水性切削液,润滑性能好,防锈性能佳,对切削、磨削过程中产生的泡沫有效控制。
通用性强,适用于不锈钢、模具钢、铝合金、铸铁件等有色金属盒黑色金属多种切削、磨削加工。
一、水性切削液技术指标
原液外观:透明液体
稀释液外观:清澈液体
密度:1.06-1.07
Ph值:8-9
折射系数:3
执行标准:SGS
二、水性切削液知识分享:
在选用磨削加工切削液时,不仅要考虑其他切削加工的条件,而且还得考虑磨削加工本身的特点:磨削加工实际上是多刀切削;磨削加工的进给量较小,切削力不大;磨削速度较高(30——80m/s),因此磨削区域温度较高,可高达800——1000℃,容易引起工件表面局部烧伤;磨削加工热应力会使工件变形,直至使工件表面产生裂纹;磨削加工还会产生大量的细碎切屑和砂轮砂末,会影响工件表面粗糙度等。
因此,选择正确的磨削加工的切削液就非常的重要,要求具有较好的冷却性和润滑性,同时也应具有一定的清洗性和防锈性。
[超实用] 判断切削液性能和质量差异的简单方法
![[超实用] 判断切削液性能和质量差异的简单方法](https://img.taocdn.com/s3/m/247af489cc22bcd126ff0c93.png)
机械工厂如何简单判断不同切削液的性能和质量差异可按如下方法在工厂内对不同的切削液产品的主要性能指标进行简单可行的比较:1、润滑性能在相同设备、同样刀具并加工同样工件的情况下,比较刀具寿命(单把刀可加工的零件数或者切削距离)以及加工质量(表面光洁度)。
刀具寿命越长、加工表面光洁度越好,则切削液润滑性能越优秀。
润滑性能是切削液非常重要的指标。
直接影响加工质量和成本。
但是无法直观判断,因为你无法获知切削液的配方及其有效润滑成分的多少。
2、稳定性取原液适量放置在透明容器中静置24小时,观察原液是否有分层和杂质,是否均匀;取原液适量用自来水配制成5%稀释液在透明容器中静置15分钟,观察稀释液是否均匀,是否有分层和杂质。
上述两项有任何一项出现分层、杂质及不均匀现象。
即可判定切削液稳定性较差。
3、泡沫性能配置5%浓度稀释液并放置在透明的试剂瓶中,盖好盖子。
然后用正常力量上下摇动试剂瓶15秒钟然后静置在桌面上开始计时并观察:瓶中产生的泡沫如能在15秒内消失,则泡沫性能合格。
消失速度越快越好。
4、防锈性能及防腐蚀性能配置5%浓度稀释液适量,选取尺寸适中的所加工零件(有经过切削加工的加工面)在切削液中浸泡适当时间(半小时到数小时。
根据零件加工时间长短)后取出在空气中静置观察:多长时间以后零件出现锈蚀或者腐蚀。
基本的要求是3-5天。
时间越长,自然防锈防腐能力越长。
特别说明,对此性能用这种方法只能初略判断。
对一些特殊的材料(比如航空铝合金),往往需要严格的实验室验证。
5、抗菌能力配置5%浓度稀释液适量并在容器中静置,定期嗅闻切削液味的变化。
越早变味发臭的切削液,其抗菌能力越差。
这一项直接关系到切削液的使用寿命。
大部分产品的抑制细菌原理是靠产品配方中的杀菌剂,唯有极少量的产品(如巴索的Blasocut系列)使用先进的生物抑菌方式,有效解决了杀菌剂对皮肤的潜在危害问题。
6、抗杂油能力配置5%浓度稀释液适量并在透明容器中静置,然后在切削液中滴入适量液压油或导轨油。
水溶性金属切削液的性能和选取

水溶性金属切削液的性能和选取金属切削液,即金属及其合金在切削加工过程中使用的工艺润滑油。
金属切削液通常可分为以冷却为主的水溶性金属切削液和以润滑为主的纯油性金属切削液;水溶性金属切削液又可细分为可溶性油(乳化液)、半合成切削液(微乳化液)和合成切削液三种。
在所有润滑油中,金属切削液的用量视各国的具体情况不同,约占其润滑油总用量的2%-3%,我国金属切削液的年用量约为6万吨左右,其中水溶性金属切削液和纯油性金属切削液各占50%左右的份额。
金属的加工方法繁多,其中金属切削加工是金属加工中最常见、应用最广泛的一种。
根据工件的形状、精度及表面质量的不同要求,金属切削加工可分为车、铣、钻、刨、镗、铰、拉削、齿轮切削、螺纹加工及磨削等。
本文主要讲述金属切削液中水溶性金属切削液的性能和选取。
水溶性切削液的主要性能我们使用水溶性金属切削液的主要目的是:①延长刀具的使用寿命;②保证和提高工件的加工尺寸精度;③改善工件表面的光洁度;④及时排除金属屑,确保切削过程顺利进行; ⑤及时带走切削热,迅速均匀冷却刀具和工件等;⑥防止机床和工件产生腐蚀和锈蚀;⑦提高切削加工效率,降低成本。
为实现上述目的,要求水溶性金属切液必须具备下列几方面主要性能:冷却性能。
在金属切削加工过程中,所消耗的能量,绝大部分(90%以上)都转变成切削热,它不但使刀具容易磨损,而且使工件容易产生局部烧伤或发暗,影响工件的表面的加工精度及加工质量。
因此,要求水溶性金属切削液必须具有良好的冷却性能。
润滑性能。
刀具在切削工件的瞬间,通常承受着极大的切削力作用,水溶性金属切削液良好的润滑性能可以减小刀具前刀面与切屑、后刀面与工件表面之间的摩擦与磨损,延长刀具的使用寿命,从而使工件获得良好的加工精度和粗糙度;更重要的是减少切削过程中产生积屑瘤(即刀瘤)的机会。
清洗性能。
金属在切削(或磨削)过程中,油污、细小的切屑、金属粉末和砂轮砂粒等互相粘结,并粘附在工件、刀具和机床上,影响工件的加工质量,降低刀具和砂轮的使用寿命,影响机床的精度。
切削加工过程中切削液的加工性能研究

切削加工过程中切削液的加工性能研究摘要:切削液的加工性能是指切削液在切削加工过程中所表现出来的效能,它与切削加工效果直接相关。
这些效果包括加工质量、机床功率消耗、加工效率、切屑处理等几个方面。
本文对切削加工过程中切削液的加工性能进行研究。
摘要:切削加工;切削液;加工性能切削液的应用领域非常广泛,可以说,凡是有机械加工的地方都或多或少的使用切削液。
随着电子技术的高速发展,切削液已不再局限于金属材料的加工,如电视机的显像管、计算机的显示器等主要设备的生产、半导体单晶体工件切割等都需要切削液。
1.切削液的性能与作用1.1切削液的第一性能人们使用切削液的主要口的是希望起到润滑、冷却、清洗三方面作用。
一般称之为切削液的第一性能。
A.切削液的润滑作用切削液的润滑作用是指其减少前刀面与切屑、后刀面与已加工表面的摩擦,以防止刀具与切屑、工件间的粘着,所以良好的润滑可以减少功率消耗、刀具磨损和获得良好的表而光洁度。
B.冷却作用在切削过程中产生的热量使工件、刀具温度升高。
过高的温度可降低刀具的强度和硬度而使刀具寿命缩短,而且因热变形会影响工件的尺寸精度,同时也给工件的及时检测及拆卸带来不便,因此切削加工时必须进行有效的冷却。
切削液通过减小摩擦和带走热量可以有效地降低切削温度。
因切削过程的热量主要是塑性变形产生的,故降低温度主要靠冷却,不是靠减少摩擦。
切削液的冷却性能与其导热系数、比热、汽化潜热、粘度等因素有关。
水的比热较油约大一倍,汽化温度低,汽化潜热大,粘度小,因此其冷却性能比油好。
对油基切削液来说,粘度越小其流动性也越好,越容易将热量带走,所以冷却效果也越好。
C.清洗作用金属加工产生的细小切屑、粉末等会互相粘结或附着在机床、刀具(砂轮)、工件上。
清洗性能就是指切削液防止这些细颗粒粘结和利用液流的机械冲洗作用将其冲走的能力。
清洗性能与切削液的渗透性和粘度有密切关系,为了提高切削液的清洗性经常采用粘度较小的油或向水基切削液中加入较多的表面活性剂。
加工中心切削液浓度标准

加工中心切削液浓度标准
加工中心切削液在加工过程中起着极为重要的作用。
为了保证切削液的良好性能,必须控制其浓度。
那么,加工中心切削液浓度的标准是什么呢?
切削液浓度指的是切削液中润滑剂、防锈剂、乳化剂等添加剂的含量。
一般来说,加工中心切削液的浓度在5%~10%之间为最佳。
如
果浓度过低,会导致切削液的润滑和冷却能力下降,从而影响加工质量和刀具寿命;如果浓度过高,会导致切削液的黏度增加,不易流动,从而影响加工效率。
在实际应用中,根据不同的加工材料和加工方式,切削液的浓度也会有所不同。
一般来说,加工硬度较高的金属材料时,浓度可以适当提高;加工软度较高的材料时,浓度可以适当降低。
另外,切削液浓度的检测也是非常重要的。
一般来说,可以通过测量切削液的折光率或电导率来确定其浓度。
如果浓度超过标准范围,需要加入水或添加剂来调整浓度,保证加工质量和效率。
- 1 -。
切削液参数 -回复
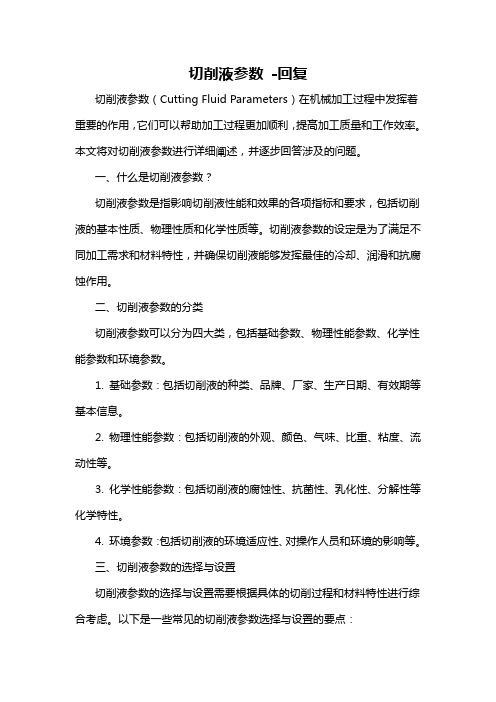
切削液参数-回复切削液参数(Cutting Fluid Parameters)在机械加工过程中发挥着重要的作用,它们可以帮助加工过程更加顺利,提高加工质量和工作效率。
本文将对切削液参数进行详细阐述,并逐步回答涉及的问题。
一、什么是切削液参数?切削液参数是指影响切削液性能和效果的各项指标和要求,包括切削液的基本性质、物理性质和化学性质等。
切削液参数的设定是为了满足不同加工需求和材料特性,并确保切削液能够发挥最佳的冷却、润滑和抗腐蚀作用。
二、切削液参数的分类切削液参数可以分为四大类,包括基础参数、物理性能参数、化学性能参数和环境参数。
1. 基础参数:包括切削液的种类、品牌、厂家、生产日期、有效期等基本信息。
2. 物理性能参数:包括切削液的外观、颜色、气味、比重、粘度、流动性等。
3. 化学性能参数:包括切削液的腐蚀性、抗菌性、乳化性、分解性等化学特性。
4. 环境参数:包括切削液的环境适应性、对操作人员和环境的影响等。
三、切削液参数的选择与设置切削液参数的选择与设置需要根据具体的切削过程和材料特性进行综合考虑。
以下是一些常见的切削液参数选择与设置的要点:1. 切削液的种类:根据加工材料的不同,可以选择适合的切削液种类,如水溶性切削液、溶剂型切削液、涂料型切削液等。
2. 切削液的浓度:切削液的浓度直接影响切削液的冷却和润滑效果。
一般来说,浓度过低会导致切削液性能不足,浓度过高会增加加工成本和处理难度。
3. 切削液的pH值:切削液的pH值对切削液的抗腐蚀性能和润滑效果有重要影响。
一般来说,切削液的pH值应在合理范围内,避免过酸或过碱。
4. 切削液的稳定性:切削液稳定性是指切削液在加工过程中的稳定性能。
液面变化、沉淀、乳化分解等问题都可能会影响加工质量和切削液的使用寿命。
四、切削液参数的优化与控制为了保证切削液参数的合理选择和设置,需要进行切削液参数的优化与控制。
以下是一些常用的方法和技巧:1. 切削液参数的测试与调整:通过对切削液参数的测试与调整,可以判断切削液的性能和效果,从而针对具体的切削需求进行参数的优化和控制。
金属切削液的作用及性能要求

金属切削液的作用及性能要求金属切削液在金属切削、磨削加工过程中具有相当重要的作用。
实践证明,选用合适的金属切削液,能降低切削温度60~150?,降低表面粗糙度,1~2级,减少切削阻力15~30%,成倍地提高刀具和砂轮的使用寿命。
并能把铁屑和灰末从切削区冲走,因而提高了生产效率和产品质量。
故它在机械加工中应用极为广泛。
切削液应具备以下几方面的作用:1.冷却作用在工件切削加工过程中,能及时而迅速的降低切削区的温度,即降低通常因摩擦引起的温升、冷却也影响切削效率,切削质量及刀具寿命。
2.润滑作用能减少切削刀具与工件间摩擦。
润滑液能浸润到刀具与工件及其切屑之间,减少摩擦和粘结,降低切削阻力,保证切削质量,延长刀具寿命。
3.洗涤作用使切屑或磨料粒子被冲洗而离开刀具和工件的加工区,以防它们相互粘结及粘附在工件、刀具和机床上妨碍4.防锈作用应有一定的防锈性能,防止工件和机床生锈。
如提高防锈性能,还可部分取代工序间防锈。
上述的冷却、润滑、洗涤、防锈四个性能不是完全孤立的,它们有统一的方面,又有对立方面。
如切削油的润滑、防锈性能较好,但冷却、清洗性能差;水溶液的冷却、洗涤性能较好,但润滑、和防锈性能差。
因此,在选用切削液时要全面权衡利弊。
切削液性能要达到以下要求:1.热容量大,导热性好,具有较好的冷却作用。
2.具有较高的油性或在金属表面的吸附作用。
能使形成的吸附薄膜具有较高的强度,牢固的吸附在金属表面,起到良好的润滑作用。
3.防锈性好,对金属不起腐蚀作用,不会因腐蚀而损坏机床和工件的精度及表面粗糙度。
4.表面张力低,易于均匀扩散,有利于冷却和洗涤作用并具有较好的润滑性。
5.使用方便,价格低廉,要求容易配置并最好适用于多种金属材料和多种加工方式(如车、磨、刨等),有一定的透明度,在提高切削速度时不冒烟。
6.对人体无害,无毒、无异味。
不会伤害皮肤及鼻腔粘膜,不刺激眼睛等。
7.稳定性好,使用寿命长。
在长期使用和贮存期间,不分层、不析出沉淀物,不发霉变质。
数控机床切削液的质量检测与评估方法
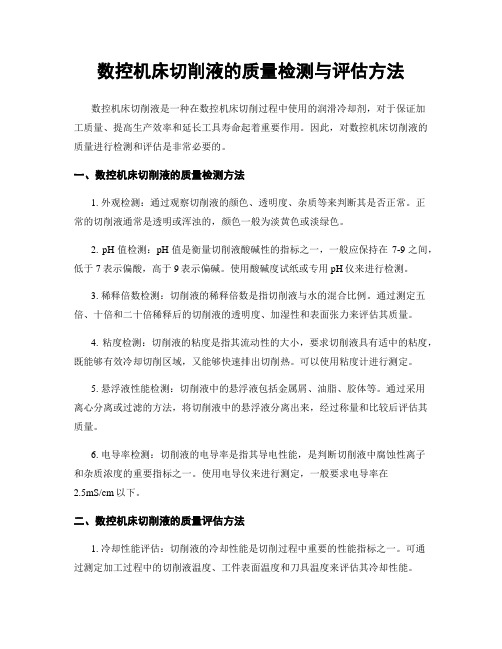
数控机床切削液的质量检测与评估方法数控机床切削液是一种在数控机床切削过程中使用的润滑冷却剂,对于保证加工质量、提高生产效率和延长工具寿命起着重要作用。
因此,对数控机床切削液的质量进行检测和评估是非常必要的。
一、数控机床切削液的质量检测方法1. 外观检测:通过观察切削液的颜色、透明度、杂质等来判断其是否正常。
正常的切削液通常是透明或浑浊的,颜色一般为淡黄色或淡绿色。
2. pH值检测:pH值是衡量切削液酸碱性的指标之一,一般应保持在7-9之间,低于7表示偏酸,高于9表示偏碱。
使用酸碱度试纸或专用pH仪来进行检测。
3. 稀释倍数检测:切削液的稀释倍数是指切削液与水的混合比例。
通过测定五倍、十倍和二十倍稀释后的切削液的透明度、加湿性和表面张力来评估其质量。
4. 粘度检测:切削液的粘度是指其流动性的大小,要求切削液具有适中的粘度,既能够有效冷却切削区域,又能够快速排出切削热。
可以使用粘度计进行测定。
5. 悬浮液性能检测:切削液中的悬浮液包括金属屑、油脂、胶体等。
通过采用离心分离或过滤的方法,将切削液中的悬浮液分离出来,经过称量和比较后评估其质量。
6. 电导率检测:切削液的电导率是指其导电性能,是判断切削液中腐蚀性离子和杂质浓度的重要指标之一。
使用电导仪来进行测定,一般要求电导率在2.5mS/cm以下。
二、数控机床切削液的质量评估方法1. 冷却性能评估:切削液的冷却性能是切削过程中重要的性能指标之一。
可通过测定加工过程中的切削液温度、工件表面温度和刀具温度来评估其冷却性能。
2. 润滑性能评估:切削液的润滑性能对机床切削过程中的摩擦和磨损起着重要作用。
可以通过测定摩擦系数和刀具磨损量来评估其润滑性能。
3. 抗菌性能评估:切削液中的细菌和真菌对切削液的质量和稳定性有一定的影响。
通过采用平皿计数法或培养法来评估切削液中的微生物数量,了解切削液的抗菌性能。
4. 稳定性评估:切削液的稳定性是指在切削过程中,切削液能够稳定地提供冷却和润滑功能。
钨钢磨削液
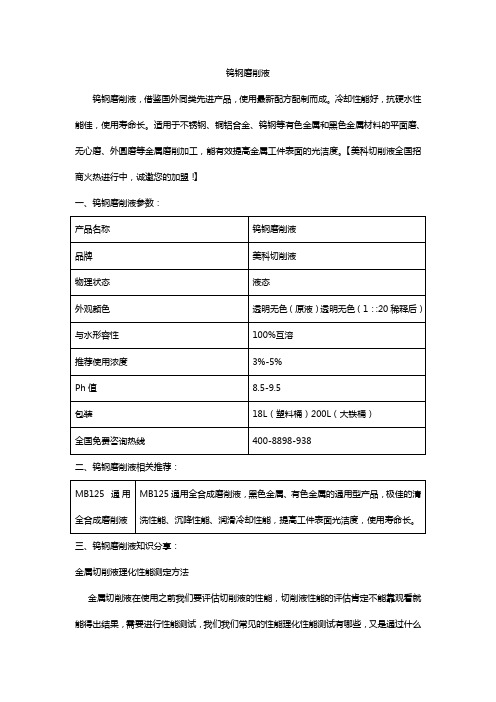
钨钢磨削液
钨钢磨削液,借鉴国外同类先进产品,使用最新配方配制而成。
冷却性能好,抗硬水性能佳,使用寿命长。
适用于不锈钢、铜铝合金、钨钢等有色金属和黑色金属材料的平面磨、无心磨、外圆磨等金属磨削加工,能有效提高金属工件表面的光洁度。
【美科切削液全国招商火热进行中,诚邀您的加盟!】
一、钨钢磨削液参数:
二、钨钢磨削液相关推荐:
三、钨钢磨削液知识分享:
金属切削液理化性能测定方法
金属切削液在使用之前我们要评估切削液的性能,切削液性能的评估肯定不能靠观看就能得出结果,需要进行性能测试,我们我们常见的性能理化性能测试有哪些,又是通过什么
方法进行测定,玖城润滑油为您解答。
1、试液制备本方法所用的试液,均用蒸馏水按各产品规定的使用浓度配制;
2、外观评定本方法用以检查液态切削液浓缩物外观。
在15~35℃温度下,用lOOml具塞量筒量取100mL被测浓缩物,静置24h后,检查外观,应无分层、沉淀,呈均匀液相;
3、储存安定性测定本方法以加速试验条件,考核合成切削渣液状浓缩物在储存、运输中的安定性。
将50mL浓缩物置于100mL具塞量筒中,量筒放于70±3℃恒温干燥箱中5h。
取出冷至室温(15~35℃),静置3h。
再置于-12±3℃:的低温冰箱中24h。
取出静置回复到室温1h后,进行评定。
无分层、相变及胶状现象,恢复原状为合格;。
切削液ph值测量方法
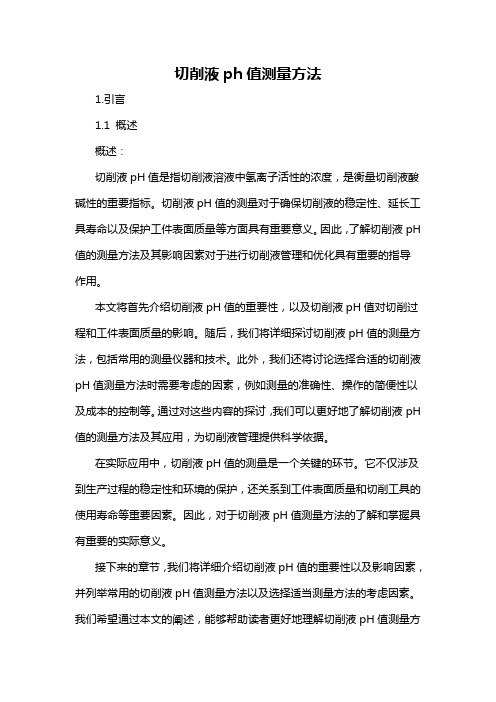
切削液ph值测量方法1.引言1.1 概述概述:切削液pH值是指切削液溶液中氢离子活性的浓度,是衡量切削液酸碱性的重要指标。
切削液pH值的测量对于确保切削液的稳定性、延长工具寿命以及保护工件表面质量等方面具有重要意义。
因此,了解切削液pH 值的测量方法及其影响因素对于进行切削液管理和优化具有重要的指导作用。
本文将首先介绍切削液pH值的重要性,以及切削液pH值对切削过程和工件表面质量的影响。
随后,我们将详细探讨切削液pH值的测量方法,包括常用的测量仪器和技术。
此外,我们还将讨论选择合适的切削液pH值测量方法时需要考虑的因素,例如测量的准确性、操作的简便性以及成本的控制等。
通过对这些内容的探讨,我们可以更好地了解切削液pH 值的测量方法及其应用,为切削液管理提供科学依据。
在实际应用中,切削液pH值的测量是一个关键的环节。
它不仅涉及到生产过程的稳定性和环境的保护,还关系到工件表面质量和切削工具的使用寿命等重要因素。
因此,对于切削液pH值测量方法的了解和掌握具有重要的实际意义。
接下来的章节,我们将详细介绍切削液pH值的重要性以及影响因素,并列举常用的切削液pH值测量方法以及选择适当测量方法的考虑因素。
我们希望通过本文的阐述,能够帮助读者更好地理解切削液pH值测量方法的原理和应用,为切削液管理提供科学的参考依据。
文章结构部分的内容应包括对整篇文章的组织和内容进行概括性介绍。
下面是1.2文章结构部分的内容示例:文章结构:本文主要分为引言、正文和结论三个部分。
引言部分首先概述了切削液pH值的测量方法的重要性和影响因素,并明确了本文的目的。
正文部分分为两个小节,分别介绍了切削液pH值的重要性和影响因素。
在重要性部分,将从提高切削液质量、提升生产效率和延长工具寿命等角度探讨切削液pH值的重要性。
在影响因素部分,将列举切削液成分、工艺参数和环境等因素对pH值的影响进行详细阐述。
结论部分首先介绍了常用的切削液pH值测量方法,包括酸碱指示纸、电子pH计和离子选择性电极等,然后进一步讨论了选择合适的切削液pH值测量方法时需要考虑的因素,包括准确性、便捷性和成本等。
切削油性能及主要检测项目简介
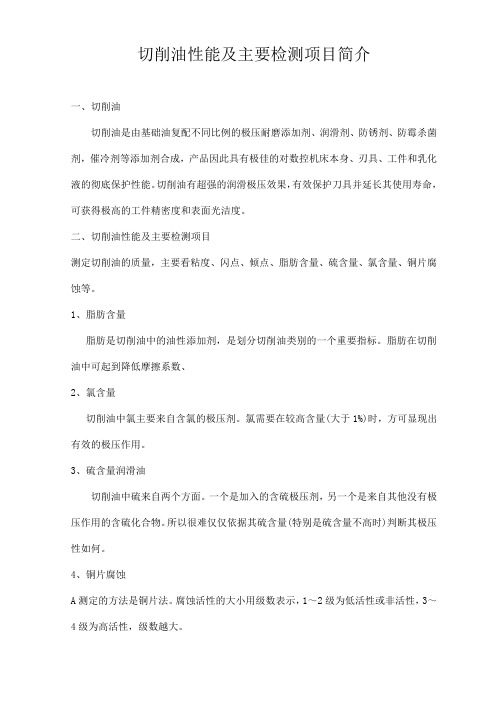
切削油性能及主要检测项目简介
一、切削油
切削油是由基础油复配不同比例的极压耐磨添加剂、润滑剂、防锈剂、防霉杀菌剂,催冷剂等添加剂合成,产品因此具有极佳的对数控机床本身、刃具、工件和乳化液的彻底保护性能。
切削油有超强的润滑极压效果,有效保护刀具并延长其使用寿命,可获得极高的工件精密度和表面光洁度。
二、切削油性能及主要检测项目
测定切削油的质量,主要看粘度、闪点、倾点、脂肪含量、硫含量、氯含量、铜片腐蚀等。
1、脂肪含量
脂肪是切削油中的油性添加剂,是划分切削油类别的一个重要指标。
脂肪在切削油中可起到降低摩擦系数、
2、氯含量
切削油中氯主要来自含氯的极压剂。
氯需要在较高含量(大于1%)时,方可显现出有效的极压作用。
3、硫含量润滑油
切削油中硫来自两个方面。
一个是加入的含硫极压剂,另一个是来自其他没有极压作用的含硫化合物。
所以很难仅仅依据其硫含量(特别是硫含量不高时)判断其极压性如何。
4、铜片腐蚀
A测定的方法是铜片法。
腐蚀活性的大小用级数表示,1~2级为低活性或非活性,3~4级为高活性,级数越大。
切削液

选用
1
工具钢
2
高速钢
3
硬质合金
4
陶瓷
5
金刚石
其耐热温度约在200-300℃之间,只能适用于一般材料的切削,在高温下会失去硬度。由于这种刀具耐热性 能差,要求冷却液的冷却效果要好,一般采用乳化液为宜。
19世纪80年代,美国科学家就已首先进行了切削液的评价工作。 F·W·Taylor发现并阐明了使用泵供给碳 酸钠水溶液可使切削速度提高30%~40%的现象和机理。针对当时使用的刀具材料是碳素工具钢,切削液的主要作 用是冷却,故提出“冷却剂”一词。从那时起,人们把切削液称为冷却润滑液。
随着人们对切削液认识水平的不断提高以及实践经验的不断丰富,发现在切削区域中注入油剂能获得良好的 加工表面。最早,人们采用动植物油来作为切削液,但动植物油易变质,使用周期短。20世纪初,人们开始从原 油中提炼润滑油,并发明了各种性能优异的润滑添加剂。在第一次世界大战之后,开始研究和使用矿物油和动植 物油合成的复合油。1924年,含硫、氯的切削油获得专利并应用于重切削、拉削、螺纹和齿轮加工。
除了以上4种作用外,所使用的切削液应具备良好的稳定性,在贮存和使用中不产生沉淀或分层、析油、析皂 和老化等现象。对细菌和霉菌有一定抵抗能力,不易长霉及生物降解而导致发臭、变质。不损坏涂漆零件,对人 体无危害,无刺激性气味。在使用过程中无烟、雾或少烟雾。便于回收,低污染,排放的废液处理简便,经处理 后能达到国家规定的工业污水排放标准等。
切削液的性质与用途选择研究及切削效果分析

切削液的性质与用途选择研究及切削效果分析切削液是现代制造业中不可或缺的重要工艺液体。
它具有降温、润滑、冷却、清洁等多种功能,能够有效改善切削过程中的摩擦热、摩擦磨损以及切削产生的刀具磨损,提高加工效率和质量。
本文将以切削液的性质和用途选择为切入点,探讨切削液的相关研究和切削效果分析。
首先,切削液的性质是影响切削效果的重要因素之一。
切削液的性质涉及其化学成分、物理性质以及稳定性等方面。
切削液的化学成分应选择适合材料加工的油品或水溶性液体,可根据切削液与材料的相容性、润滑性和冷却性来进行选择。
切削液的物理性质包括黏度、表面张力和密度等,这些因素与切削液在加工过程中的传热与传质有直接关系。
此外,切削液的稳定性特别重要,它涉及到切削液的抗菌性和抗氧化性能,能够延长切削液的使用寿命,减少维护成本。
因此,在选择切削液的性质时,需综合考虑其与加工材料的相容性、润滑性、冷却性、传热传质性以及稳定性等方面的因素。
其次,切削液的用途选择也是研究的重要方向之一。
切削液在不同的切削加工过程中具有不同的使用需求。
例如,对于高速切削,切削液应具备良好的冷却和润滑性能,以稳定温度,减少摩擦热和切削力。
而对于重载切削,切削液应具备较高的润滑性能,以减少切削阻力和磨损。
此外,在特殊切削过程中,如硬质合金切削、铸铁切削等,切削液还应具备防腐蚀、抗氧化等特殊性能,以保证加工质量和工具寿命。
根据不同的使用需求,选择适合的切削液可以进一步提高切削效果和加工质量。
最后,切削效果分析是评价切削液性能的关键指标之一。
切削液的选择会直接影响切削效果,因此,对切削液的性能进行有效的分析与评估是至关重要的。
切削效果分析旨在评估切削液在实际切削加工过程中的效果,包括表面质量、加工精度、切屑形态、工具寿命、切削力等指标。
通过对比不同切削液的实际加工表现,可以判断切削液的适用范围和优劣势,为切削液的改进和优化提供科学依据。
综上所述,切削液的性质与用途选择是研究的重点之一。
机床切削液的理化性能与评价方法概述
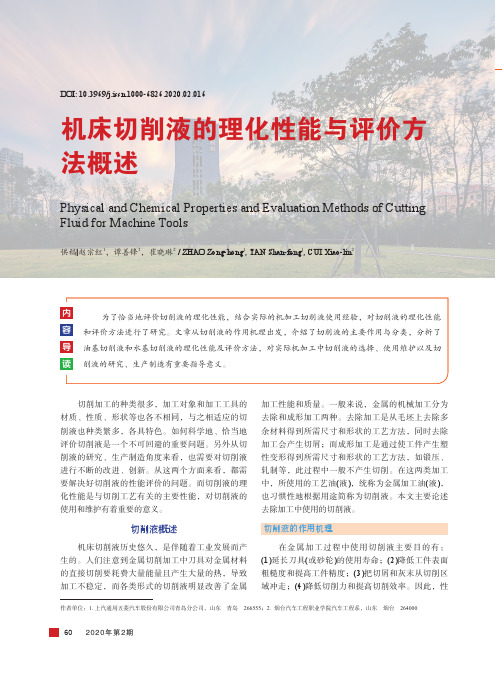
机床切削液的理化性能与评价方法概述Physical and Chemical Properties and Evaluation Methods of Cutting Fluid for Machine Tools供稿|赵宗红1,谭善锋1,崔晓琳2 / ZHAO Zong-hong1, TAN Shan-feng1, CUI Xiao-lin2DOI: 10.3969/j.issn.1000-6826.2020.02.016切削加工的种类很多,加工对象和加工工具的材质、性质、形状等也各不相同,与之相适应的切削液也种类繁多,各具特色。
如何科学地、恰当地评价切削液是一个不可回避的重要问题。
另外从切削液的研究、生产制造角度来看,也需要对切削液进行不断的改进、创新。
从这两个方面来看,都需要解决好切削液的性能评价的问题。
而切削液的理化性能是与切削工艺有关的主要性能,对切削液的使用和维护有着重要的意义。
切削液概述机床切削液历史悠久,是伴随着工业发展而产生的。
人们注意到金属切削加工中刀具对金属材料的直接切削要耗费大量能量且产生大量的热,导致加工不稳定,而各类形式的切削液明显改善了金属加工性能和质量。
一般来说,金属的机械加工分为去除和成形加工两种。
去除加工是从毛坯上去除多余材料得到所需尺寸和形状的工艺方法,同时去除加工会产生切屑;而成形加工是通过使工件产生塑性变形得到所需尺寸和形状的工艺方法,如锻压、轧制等,此过程中一般不产生切削。
在这两类加工中,所使用的工艺油(液),统称为金属加工油(液),也习惯性地根据用途简称为切削液。
本文主要论述去除加工中使用的切削液。
切削液的作用机理在金属加工过程中使用切削液主要目的有:(1)延长刀具(或砂轮)的使用寿命;(2)降低工件表面粗糙度和提高工件精度;(3)把切屑和灰末从切削区域冲走;(4)降低切削力和提高切削效率。
因此,性作者单位:1. 上汽通用五菱汽车股份有限公司青岛分公司,山东青岛 266555;2. 烟台汽车工程职业学院汽车工程系,山东烟台 264000工艺与装备Apparatus and Equipments金属加工能良好的切削液必须具有润滑、冷却、清洗和防锈等作用。
切削液的性能评定

切削液的性能评定切削液的性能评定要选择一个标准来判定切削液性能优劣是较困难的,而根据这个标准建立一个评价切削液效率的试验过程同样是一件难事。
这个问题从实验室转移到车间中会更复杂,但也可通过下述方法对切削液的性能作出评价。
刀具寿命评定采用刀具寿命评价切削液性能时,存在的主要问题是试验结果与工厂所测数据间的相关性常常很差。
因为对直刃刀具有效的切削液对成型刃刀具并不一定同样有效,反之亦然。
此外,切屑厚度对切削液的适应性也有影响。
若在同一特定加工条件下对几种切削液进行评价则要容易得多,因为通过测定刀具锐利度的变化值可得到刀具的平均寿命。
此评定即便简化了过程,但试验费用却很昂贵。
表面光洁度试验面光洁度试验不如刀具寿命试验复杂,可采用一根试验长棒,用同一刀具进行切削加工,通过表面粗糙度测量仪获得试验数据来评价切削液的性能优劣。
此评定试验,切削类型是很重要的。
如在平面铣削中,光洁的表面是由第二切削刃形成的,而在外圆铣削中,则是由主切削刃(轴向平行)形成新生面。
因而由一种加工方法获得的数据不能用于另一种加工的评定。
冷却性能评定采用某些专业技术测量切削液在实际加工中的冷却能力可判定其效率。
由于刀-屑界面的温度与刀具寿命有很好的相关性,因而刀具工作热电偶是一项非常有用的技术。
但其不足之处是不能区分温度降低是由于切削液的热传递还是由于加工中所产生热量少所致。
润滑效率评定切削液润滑效率的测定需采用一台机床刀具测力计。
在切削加工试验中,切削液的润滑作用降低了进刀力和切削力。
通过测定力的变化可计算切削液的润精效率。
切削力随进刀量的增加而增加,随切削液润滑效率的提高而降低。
若对刀具施加恒定的进刀力,则切削液的润滑效率越高,进刀量越大。
这套试验评定装置对刀屑之间的摩擦变化十分灵敏,但需一台设备以保证施加在切屑刀具上的进刀力恒定。
生理影响评价生理影响评价可通过操作人员来进行,如采用类似于过敏试验的医学研究技术进行皮肤刺激反应等。
精密机床切削液

精密机床切削液
精密机床切削液是一款针对精密机床加工方式而配制的环保型精密机床切削液,润滑、防锈、冷却性能优秀,对机床设备保护性好,使用寿命长。
适用于不锈钢、铝合金、铜合金、合金钢等金属材料在车床上的加工上使用。
一、精密机床切削液技术指标:
原液外观:透明无色
Ph值:8.5-9
密度:1.07
折射系数:2.8
执行标准:SGS
二、东莞美科精密机床切削液小知识分享:
目前,在切削加工方面,我国各类金属切刘机床已超过200万台,其中包括引进的柔性制造单元等先进的自动化机械制造系统。
在成形加工方面,我国拥有的冲压设备超过90万台,其中包括引进16台黑色金属高速线材札机、91套钥材成形加工设备、220多套铝材成形加工设备。
这些机械设备,一方面提高了我国整体金属加工工艺水平,另一方面也推动了我国金属加工液的研究工作走上新的台阶。
切削油的主要质量控制指标
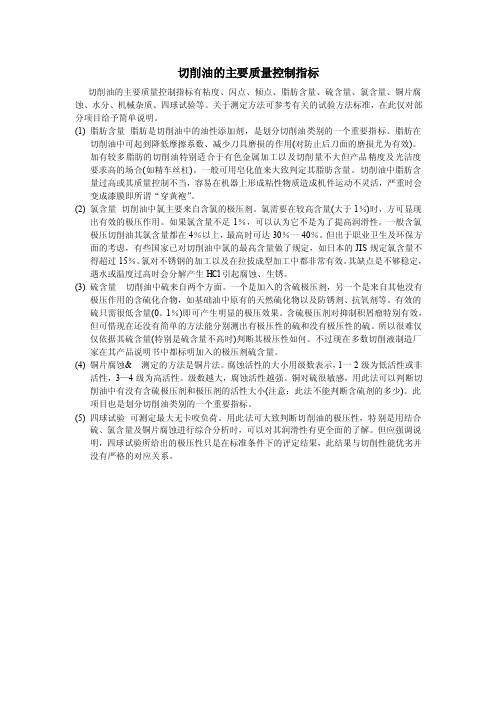
切削油的主要质量控制指标切削油的主要质量控制指标有粘度、闪点、倾点、脂肪含量、硫含量、氯含量、铜片腐蚀、水分、机械杂质、四球试验等。
关于测定方法可参考有关的试验方法标准,在此仅对部分项目给予简单说明。
(1)脂肪含量脂肪是切削油中的油性添加剂,是划分切削油类别的一个重要指标。
脂肪在切削油中可起到降低摩擦系数、减少刀具磨损的作用(对防止后刀面的磨损尤为有效)。
加有较多脂肪的切削油特别适合于有色金属加工以及切削量不大但产品精度及光洁度要求高的场合(如精车丝杠)。
一般可用皂化值来大致判定其脂肪含量。
切削油中脂肪含量过高或其质量控制不当,容易在机器上形成粘性物质造成机件运动不灵活,严重时会变成漆膜即所谓“穿黄袍”。
(2)氯含量切削油中氯主要来自含氯的极压剂。
氯需要在较高含量(大于1%)时,方可显现出有效的极压作用。
如果氯含量不足1%,可以认为它不是为了提高润滑性。
一般含氯极压切削油其氯含量都在4%以上,最高时可达30%一40%。
但出于职业卫生及环保方面的考虑,有些国家已对切削油中氯的最高含量做了规定,如日本的JIS规定氯含量不得超过15%。
氯对不锈钢的加工以及在拉拔成型加工中都非常有效。
其缺点是不够稳定,遇水或温度过高时会分解产生HCl引起腐蚀、生锈。
(3)硫含量切削油中硫来自两个方面。
一个是加入的含硫极压剂,另一个是来自其他没有极压作用的含硫化合物,如基础油中原有的天然硫化物以及防锈剂、抗氧剂等。
有效的硫只需很低含量(0。
1%)即可产生明显的极压效果。
含硫极压剂对抑制积屑瘤特别有效,但可惜现在还没有简单的方法能分别测出有极压性的硫和没有极压性的硫。
所以很难仅仅依据其硫含量(特别是硫含量不高时)判断其极压性如何。
不过现在多数切削液制造厂家在其产品说明书中都标明加入的极压剂硫含量。
(4)铜片腐蚀& 测定的方法是铜片法。
腐蚀活性的大小用级数表示,l一2级为低活性或非活性,3—4级为高活性。
级数越大,腐蚀活性越强。
- 1、下载文档前请自行甄别文档内容的完整性,平台不提供额外的编辑、内容补充、找答案等附加服务。
- 2、"仅部分预览"的文档,不可在线预览部分如存在完整性等问题,可反馈申请退款(可完整预览的文档不适用该条件!)。
- 3、如文档侵犯您的权益,请联系客服反馈,我们会尽快为您处理(人工客服工作时间:9:00-18:30)。
切削液的性能评定
要选择一个标准来判定切削液性能优劣是较困难的,而根据这个标准建立一个评价切削液效率的试验过程同样是一件难事。
这个问题从实验室转移到车间中会更复杂,但也可通过下述方法对切削液的性能作出评价。
刀具寿命评定
采用刀具寿命评价切削液性能时,存在的主要问题是试验结果与工厂所测数据间的相关性常常很差。
因为对直刃刀具有效的切削液对成型刃刀具并不一定同样有效,反之亦然。
此外,切屑厚度对切削液的适应性也有影响。
若在同一特定加工条件下对几种切削液进行评价则要容易得多,因为通过测定刀具锐利度的变化值可得到刀具的平均寿命。
此评定即便简化了过程,但试验费用却很昂贵。
表面光洁度试验
面光洁度试验不如刀具寿命试验复杂,可采用一根试验长棒,用同一刀具进行切削加工,通过表面粗糙度测量仪获得试验数据来评价切削液的性能优劣。
此评定试验,切削类型是很重要的。
如在平面铣削中,光洁的表面是由第二切削刃形成的,而在外圆铣削中,则是由主切削刃(轴向平行)形成新生面。
因而由一种加工方法获得的数据不能用于另一种加工的评定。
冷却性能评定
采用某些专业技术测量切削液在实际加工中的冷却能力可判定其效率。
由于刀-屑界面的温度与刀具寿命有很好的相关性,因而刀具工作热电偶是一项非常有用的技术。
但其不足之处是不能区分温度降低是由于切削液的热传递还是由于加工中所产生热量少所致。
润滑效率评定
切削液润滑效率的测定需采用一台机床刀具测力计。
在切削加工试验中,切削液的润滑作用降低了进刀力和切削力。
通过测定力的变化可计算切削液的润精效率。
切削力随进刀量的增加而增加,随切削液润滑效率的提高而降低。
若对刀具施加恒定的进刀力,则切削液的润滑效率越高,进刀量越大。
这套试验评定装置对刀屑之间的摩擦变化十分灵敏,但需一台设备以保证施加在切屑刀具上的进刀力恒定。
生理影响评价
生理影响评价可通过操作人员来进行,如采用类似于过敏试验的医学研究技术进行皮肤刺激反应等。
操作人员的不同生理反应会影响到他对切削液的评价。
金属切削液对皮肤的刺激
人在金属加工车间工作,频繁接触到金属加工液。
市场上很多的切削液成分对人体皮肤的刺激严重,造成手部皮肤发红,瘙痒,接触性皮炎和蜕皮。
长期的接触到有毒性成分的切削液,有毒物质从人体的皮肤吸收,导致慢性毒。
故在使用金属切削液时企业应选用安全环保,无毒和高性能的切削液。
同时在生产时配备安防产品,维护员工的身体健康。
本文由营口康如科技有限公司整理。