高频焊管焊接挤压辊的调整
冷弯型钢高频直缝焊管机组的调整及常见生产故障的分析
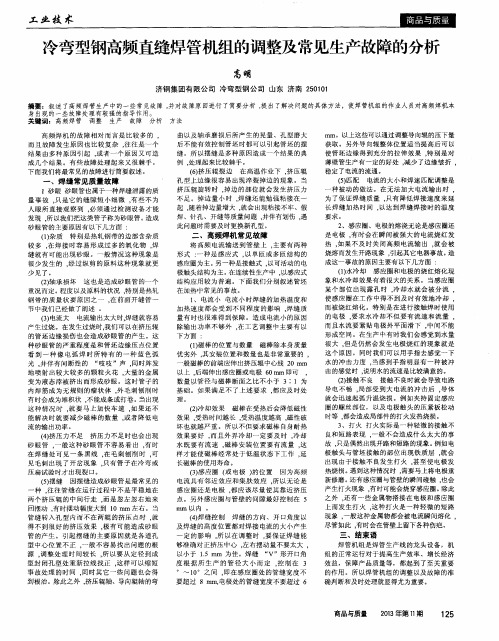
曲以及 轴承磨 损后所 产生 的晃量 、孔型磨 大 后 不能有效控 制管坯 时都可 以引起管坯 的摆 缝 。所 以摆缝 是多种 原因造成一 个结果 的典 例 , 处理起来 比较 棘手 。 ( 6 ) 挤压辊 裂边 在高温作 业下 , 挤压辊
m m。以上这些可以通过 调整 导向辊 的压下量 获取 。另 外导 向辊整体 位置适 当提 高后可 以 使管坯边 缘得 到充分 的拉伸效 果 , 特 别是对 薄壁管生产有一定 的好 处 , 减少 了边缘皱折 稳定了电流 的流通 。
工 业 技 术
冷弯型钢高频直缝焊管机组的调整及常见生产故障的分析
高明
济钢 集团有限公司 冷弯型钢 公司 山东 济南 2 5 0 1 0 1
摘要 :叙述 了高频焊管生产 中的一些常见故障 , 并对故 障原 因进行 了简要分析 , 提 出了解决 问题 的具体方 法,使 焊管机 组的作 业人 员对高频焊机本 身 出现 的一些故障处 理有较强的指导作用。 关键词 :高频焊管 调整 生产 故障 分析 方法 高频焊 机 的故 障相对 而言 是 比较 多的 , 而且故 障发 生原 因也 比较复杂 , 往 往是一 个 结果 由多种 原因 引起 , 或者一 个原 因又可 造 成 几个 结果 。有 些故障 处理起来 又很棘手 。 下 面我们将最常见 的故障进行简要叙述 。
f l 1 杂质 特别是热轧钢带的边部含杂质
较多 , 在 焊接 时容 易形 成过 多 的氧 化物 , 焊 缝 就有 可能 出现 砂眼 。一般情况 这种现象 是 很 少发 生的 , 经过 纵剪 的原料 这种现 象就 更 少见了 。 ( 2 1 轴承 损坏 这 也是造成砂 眼管 的一个 重况而定。程度 以及原料 的状况 , 特别 是热 轧 钢 带 的质 量状 要原 因之~ , 在 前面开 缝管一 节 中我们 已经做 了阐述 。 ( 3 ) 电流大 电流输 出太大时, 焊缝 就容易 产 生过烧 。在 发生过烧时, 我们 可 以在挤压辊 的管坯边 缘损伤 也会造成 砂眼 管的产生 。这 种 砂眼管 的严重程 度是和 管坯边 缘压点位 置 看 到 一 种 像 电弧 焊 时 所特 有 的 一种 蓝 色 弧 光 . 并 伴有间断 性的 “ 吱吱 ”声 , 同时 阵发 地 喷射 出较 大较 多的颗粒 火花 , 大量 的金 属 变 为液态 滓被挤 出而形成 砂眼 。这时管子 的 内焊筋 成为无 规则 的瘤状 体 , 外毛刺 刨削 时 有 时会 成为堆积状 , 不能成条或打卷 。当出现 这 种情 况 时 , 就要 马上加 快车 速 , 如 果还不 能解决 时就要 减少磁 棒 的数量 , 或者 降低 电 流 的输 出功率 。 f 4 ) 挤压 力不足 挤压 力不足 时也会 出现 砂 眼管 , 一般 这种砂 眼管 不容 易看 出 , 有 时 在 焊缝 处可 见一条 黑线 , 在毛刺 刨 削时 , 可 见 毛刺 出现 了开岔现象 , 只有 管子在冷 弯或 压扁试验 时才 出现裂 口。 ( 5 ) 摆缝 因摆缝造 成砂眼管 是最常见 的 种 , 往往 管缝在 运行过 程 中不是平 稳地在 两 个挤压 辊 的中间行走 , 而是忽 左忽右 地来 回摆动 , 有时摆动幅度大到 l 0 n l m左右 。当 管缝 转入孔 型 内而不在 两辊 的挤压 点 时 , 就 得 不到很 好 的挤压效 果 , 极有可 能造成 砂眼
高频直缝焊管机组的调整及常见生产故障分析

高频直缝焊管机组的调整及常见生产故障分析(三)高频直缝焊管机组的调整及常见生产故障分析(三)4定径机常见故障相比之下,定径机的故障率最低,而且处理起来也较简单,定径机常见的生产事故有以下几种类型。
4.1划伤定径的划伤主要发生在管子断面的横向和纵向轴线两侧,多由平辊和立辊孔型的边缘造成。
特别是孔型边缘R圆角磨锐后,一旦出现下列问题都可能引起划伤。
(1)轧辊位移轧辊轴向位移后,使孔型错位不能吻合。
但有时轧辊轴向位移后,没有定位锁紧,可以自由式找正,在生产中通过管子的作用自行吻合后,也不会造成管壁划伤。
有时因某种原因,轧辊位移后并被自行锁定在一个位置上,使孔型不能吻合,就会造成管壁划伤,特别是立辊,这种现象尤为突出。
(2)轴承损坏轴承损坏后就容易出现两个孔型不吻合的现象,在轴承轻度损坏时管壁划伤比较严重,而轴承损坏严重时,一般就不会再发生划伤的问题,而是其它的事故,例如钻管,压扁管子等更严重的问题。
(3)调偏调偏完全是一种人为现象,如同成型上平辊压力不均匀一样。
在成型中通过对上辊两侧的不同压力作用,可以解决因某些特殊原因而造成的管坯跑偏问题。
在定径机上辊轻微调偏后,可以解决一些转缝和管子不圆的问题,但是调偏力度太大时,就会使两孔型不吻合,而使管壁产生划伤。
立辊的上下端受力也应该均匀,如果立辊出现上下仰角时,同样也会破坏孔型的吻合效果,使管壁出现划伤。
特别是在孔型的R圆角磨锐后,调偏程度严重时,管壁划伤会更加严重。
同时调偏的做法,也会使孔型的弧面磨损更加不均匀,产生不良循环。
4.2钻管钻管问题是不多见的,一般薄壁管生产时发生的几率比较多,这主要是因为薄壁管的刚性较差,且因管壁较薄容易被轧辊咬入。
所以在生产中出现下列问题都会造成钻管的事故。
(1)轴承损坏下平辊轴承损坏后,在上平辊的压力作用下,管子的轧制线高度就会下降,这时管子就很容易钻入立辊孔型的下辊缘。
如果是立辊轴承损坏后,上下辊缘的间隙加大,管子也同样会随时钻入缝隙中。
焊管机组高频焊接常见的问题及解决方法
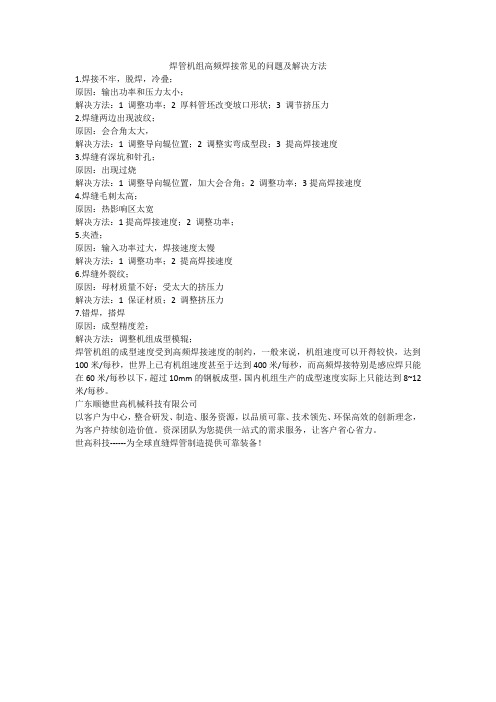
焊管机组高频焊接常见的问题及解决方法
1.焊接不牢,脱焊,冷叠;
原因:输出功率和压力太小;
解决方法:1 调整功率;2 厚料管坯改变坡口形状;3 调节挤压力
2.焊缝两边出现波纹;
原因:会合角太大,
解决方法:1 调整导向辊位置;2 调整实弯成型段;3 提高焊接速度
3.焊缝有深坑和针孔;
原因:出现过烧
解决方法:1 调整导向辊位置,加大会合角;2 调整功率;3提高焊接速度
4.焊缝毛刺太高;
原因:热影响区太宽
解决方法:1提高焊接速度;2 调整功率;
5.夹渣;
原因:输入功率过大,焊接速度太慢
解决方法:1 调整功率;2 提高焊接速度
6.焊缝外裂纹;
原因:母材质量不好;受太大的挤压力
解决方法:1 保证材质;2 调整挤压力
7.错焊,搭焊
原因:成型精度差;
解决方法:调整机组成型模辊;
焊管机组的成型速度受到高频焊接速度的制约,一般来说,机组速度可以开得较快,达到100米/每秒,世界上已有机组速度甚至于达到400米/每秒,而高频焊接特别是感应焊只能在60米/每秒以下,超过10mm的钢板成型,国内机组生产的成型速度实际上只能达到8~12米/每秒。
广东顺德世高机械科技有限公司
以客户为中心,整合研发、制造、服务资源,以品质可靠、技术领先、环保高效的创新理念,为客户持续创造价值。
资深团队为您提供一站式的需求服务,让客户省心省力。
世高科技------为全球直缝焊管制造提供可靠装备!。
高频焊管成型调整技术方法
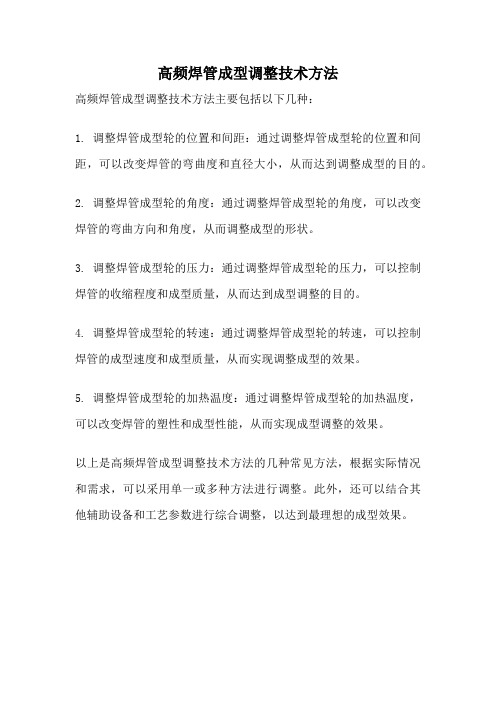
高频焊管成型调整技术方法
高频焊管成型调整技术方法主要包括以下几种:
1. 调整焊管成型轮的位置和间距:通过调整焊管成型轮的位置和间距,可以改变焊管的弯曲度和直径大小,从而达到调整成型的目的。
2. 调整焊管成型轮的角度:通过调整焊管成型轮的角度,可以改变焊管的弯曲方向和角度,从而调整成型的形状。
3. 调整焊管成型轮的压力:通过调整焊管成型轮的压力,可以控制焊管的收缩程度和成型质量,从而达到成型调整的目的。
4. 调整焊管成型轮的转速:通过调整焊管成型轮的转速,可以控制焊管的成型速度和成型质量,从而实现调整成型的效果。
5. 调整焊管成型轮的加热温度:通过调整焊管成型轮的加热温度,可以改变焊管的塑性和成型性能,从而实现成型调整的效果。
以上是高频焊管成型调整技术方法的几种常见方法,根据实际情况和需求,可以采用单一或多种方法进行调整。
此外,还可以结合其他辅助设备和工艺参数进行综合调整,以达到最理想的成型效果。
焊管调整技术教程
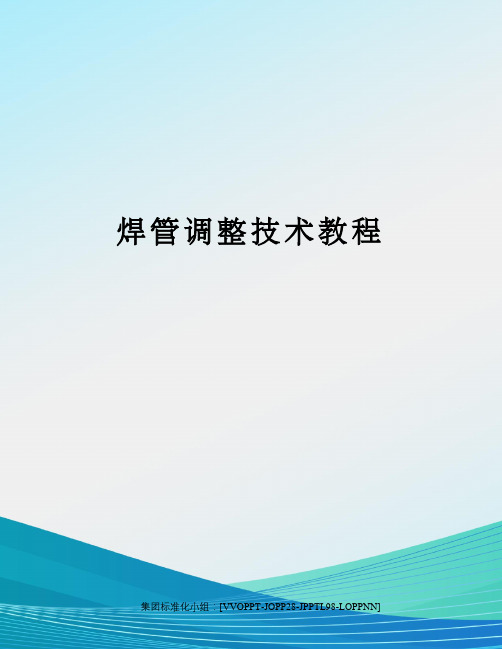
焊管调整技术教程集团标准化小组:[VVOPPT-JOPP28-JPPTL98-LOPPNN]一:换辊:1,基准面距离:轴瓦一端有一固定端,此固定端有一基准面,或在牌坊架上,或在轴瓦上,以此确定轧制中心基准面与轧制中心的垂直距离。
2,为保证轧辊预装位置正确,必须保证各水平机架的基准面在同一平面内,不得松动。
3,水平下轴的水平高度各架应严格一致,以保证轧辊水平位置准确。
4,机架组装的注意事项。
A,开口机架下轴瓦注意方向,避免装反,上下轴不准装反。
B,各调整部位保证滑动,调整方便。
C,各紧固部件不得松动。
D, 检查轧辊尺寸和表面.检查各封闭孔导向环的尺寸和表面.E, 轧辊安装固定要紧固,不允许有轴向串动和径向跳动,检查轴承是否损坏,松动.二:换辊后的调整:1, 校验轧制中心线:A,以水平下辊为基准面校验轧制中心线是调整机组的原则。
B, 拉一中心细线通过成型第一架到定径最后一架,保持一定张力,并靠合孔型槽底,注意中心线不得与水平下辊外的任何部件接触。
C,各架水平下辊的孔型中心均与中心线位置相符。
D,各架水平下辊孔型槽底均与中心线靠合。
E,正确调整轧辊的水平位置.从横向检查成型机各架水平辊的上下辊轴的中心线是否水平,是否有一头高一头低的倾斜现象,通过压下装置调整水平.F,正确调整各架的辊缝.按照孔型图和工艺规程调整各水平辊和立辊的辊缝,一般为带钢的厚度.辊缝过大则照成变形不充分,带钢在孔型内左右滑动和扭转,辊缝过小使成型负荷增加,机架损坏.2, 立辊调整:A, 与轧制中心对称。
B, 端面水平。
C, 成型2,3,4架立辊下沿高于轧制中心线。
D, 其他的按椭圆到圆应略底于轧制中心线。
3, 调整原则:A, 立辊偏高:使变形带钢头部上翘,严重的造成跑头,还将使运行带钢在立辊间构成弓型,使孔型下部磨损增大,边缘刻伤带钢。
B, 立辊偏低:对变形带钢进入孔型不利,易跑头,并刻伤带钢边缘或出现横向墩粗,造成焊接质量缺陷。
焊管调整技术教程

焊管调整技术教程一:换辊:1,基准面距离:轴瓦一端有一固定端,此固定端有一基准面,或在牌坊架上,或在轴瓦上,以此确定轧制中心基准面与轧制中心的垂直距离。
2,为保证轧辊预装位置正确,必须保证各水平机架的基准面在同一平面内,不得松动。
3,水平下轴的水平高度各架应严格一致,以保证轧辊水平位置准确。
4,机架组装的注意事项。
A,开口机架下轴瓦注意方向,避免装反,上下轴不准装反。
B,各调整部位保证滑动,调整方便。
C,各紧固部件不得松动。
D, 检查轧辊尺寸和表面.检查各封闭孔导向环的尺寸和表面.E, 轧辊安装固定要紧固,不允许有轴向串动和径向跳动,检查轴承是否损坏,松动.二:换辊后的调整:1, 校验轧制中心线:A,以水平下辊为基准面校验轧制中心线是调整机组的原则。
B, 拉一中心细线通过成型第一架到定径最后一架,保持一定张力,并靠合孔型槽底,注意中心线不得与水平下辊外的任何部件接触。
C,各架水平下辊的孔型中心均与中心线位置相符。
D,各架水平下辊孔型槽底均与中心线靠合。
E,正确调整轧辊的水平位置.从横向检查成型机各架水平辊的上下辊轴的中心线是否水平,是否有一头高一头低的倾斜现象,通过压下装置调整水平.F,正确调整各架的辊缝.按照孔型图和工艺规程调整各水平辊和立辊的辊缝,一般为带钢的厚度.辊缝过大则照成变形不充分,带钢在孔型内左右滑动和扭转,辊缝过小使成型负荷增加,机架损坏.2, 立辊调整:A, 与轧制中心对称。
B, 端面水平。
C, 成型2,3,4架立辊下沿高于轧制中心线。
D, 其他的按椭圆到圆应略底于轧制中心线。
3, 调整原则:A, 立辊偏高:使变形带钢头部上翘,严重的造成跑头,还将使运行带钢在立辊间构成弓型,使孔型下部磨损增大,边缘刻伤带钢。
B, 立辊偏低:对变形带钢进入孔型不利,易跑头,并刻伤带钢边缘或出现横向墩粗,造成焊接质量缺陷。
C, 导向辊:按中心线高度将下辊孔型槽底调至略高与中心线。
作用:消皱,电流集中增大。
高频焊管焊接挤压辊的调整

高频焊管焊接挤压辊的调整在高频焊管生产中,管坯的成型合缝状态直接影响焊缝的质量,其中焊接接头对接面的平行度尤为重要。
在钢管合缝焊接过程中,主要通过调整挤压辊上辊下量与两上辊之间的间隙来保证合缝的平行程度。
1焊接挤压辊的孔型特点焊接挤压机架上的挤压辊的扎型半径比其他挤压辊大10%左右,因此,上挤压辊的外侧辊面与钢管理想圆形断面之间产生了间隙,该间隙俗称"后跟隙"。
在实际的成型中,钢管断面不可能是理想的圆形。
一般情况下,由于带钢边部的变形不充分,断面容易呈桃形,如果不进行调整则会形成焊接对接面不平行对接,严重影响焊缝质量。
如果上挤压辊与其他挤压辊辊采用同样的扎型半径,当通过调整上挤压辊的压下量来消除V型合缝时,上挤压辊的外侧辊面将强力压在钢管表面上,容易造成管面伤痕,并形成严重的V形合缝。
因此"后跟隙"的设定,就是根据管坯成型的实际特点,通过上挤压辊的压下量调整来有效地消除V形合缝现象。
2上挤压辊的调整方法按照标准孔型设定挤压辊位置时,如果发现成型合缝呈V形,可以在"后跟隙"的范围内,对上挤压辊的压下量进行调整。
上挤压辊的压下量的极限,是上挤压辊外侧辊面在钢管表面造成较浅的压痕。
按照经验,当达到这个压下限度时,即使强度较高的管材,通常也能够成平形的成型合缝。
在应用上述经验时,必须严格按照设计值来设定两个上挤压辊之间的间隙。
这个间隙的变化将直接引起"后跟隙"的变化。
如果每次换辊时不对该间隙按设计值进行严格的设定,那么孔型的调整就很难实现再现性。
出于同样的理由,在进行上辊的不对称调整消除错边时,务必只对操作台侧的上辊进行调整,而让别一侧的上辊始终固定作为基准。
如果随意调整两侧上辊,则有可能会使上辊间隙逐渐远离设定值。
3特殊情况下的调整技巧3.1厚壁高强度管材的孔型调整钢管的壁厚越大,材料强度越高,焊接时出现的V形合缝越不容易消除。
高频直缝焊管机组的调整及常见生产故障的分析

高频直缝焊管机组的调整及常见生产故障的分析本文由()整理,如有转载,请注明出处。
叙述了高频焊管生产前的准备工作和轧辊安装方法 , 以及在生产中的一些常见故障 ,并对故障原因进行了简要分析 , 提出了解决问题的具体方法 , 对焊管机组的作业人员有较强的指导作用。
1 焊接机常见故障焊接机的故障相对而言是比较多的 , 而且故障发生原因也比较复杂 , 往往是一个结果由多种原因引起 , 或者一个原因又可造成几个结果。
有些故障处理起来又很棘手。
下面我们先将划伤事故做个简要叙述。
1. 1 划伤在焊接机出现的管坯划伤主要由两个部位造成 , 一是导向机构 , 二是挤压焊接机构。
1. 1. 1 导向机构的划伤导向部位的划伤一般发生在管坯的两侧 , 如果装有导向套的导向结构调整不合理,管坯的上下两表面也会出现磨擦性的划伤,这种划伤的特点为创面比较大,连续性较强。
主要是因为导向套的高度位置不正确,或者是上下导向辊轴承损坏后,不能很好的控制管坯,使之与导向套产生磨擦后形成。
除此之外 ,当导向辊偏离轧制中心线太大时,导向套和导向辊的轴线相对差太大时 , 也都会造成管坯两侧的划伤。
1. 1. 2 挤压焊接机构划伤挤压辊所造成的划伤,主要发生在管坯的底部,原因大致有以下几点:(1 ) 孔型不吻合焊缝挤压结构有两辊式、三辊式和四辊式,只要组合的孔型不吻合 ,就很容易造成管坯表面划伤,两辊式结构尤为突出。
造成孔型不吻合的因素又很多,以两辊式结构为例 , 诸如轴承损坏;辊子轴向窜动;孔型大小不一样;两辊子高度位置不相同;轴弯曲以及装配不稳定等等。
(2) 高度匹配挤压辊孔型的下边缘应与轧制线的高度一致,而导向辊的高度是由管坯壁厚决定的。
如果导向辊的高度降低到一定极限时,挤压辊孔型的边缘圆角就会对管坯的底部造成划伤,特别是在挤压辊孔型的 R 圆角磨锐后,划伤就更容易发生。
(3) 挤压辊上挤压力不足特别是两辊结构的挤压辊装置 , 当上挤压力不足时 , 在管坯的张力用下 ,辊轴就会出现上仰角,使孔型边缘 R圆角突出,从而造成管坯下部的划伤。
高频焊管轧辊孔型改进的设计

高频焊管轧辊孔型改进的设计摘要:近年来,随着我国高频焊管工业的迅速发展,焊管厂家有如百舸争流,焊管从业队伍的迅速扩大。
为适应焊管从业人员的技术进步,提升生产工艺规范要求。
全面掌握了焊管轧辊孔型改进的基本要求和生产知识,分析了单半径变形法和双半径变法有哪些区别和在生产过程中会产生哪些问题。
为提高操作工人在生产过程中的技术水平和应变能力,推进焊管技术人员的发展作出应有的贡献。
关键词:只有不但的技术创新,才能够降低生产成本;严格按新工艺规范要求操作,产品的质量才有保证;客户的满意度,就是我们的宗旨。
引言:二十世纪九十年代,金洲就开始生产高频焊管。
焊管是钢带通过孔型变形为一定的形状,通过一个系列连续的孔型变形,便成型为焊接钢管。
对于这一个系列化的孔型形状和尺寸的选择、计算和确定。
并最终绘制成轧辊图纸整个过程我们称为孔型设计。
一、原孔型设计的原理结构与存在的问题原孔型设计是按“单半径变形法成型”的设计原理。
单半径孔型设计示图如下:在实际操作和机组设备修理的过程中,充分总结和探讨了单半径变形法孔型设计在生产过程中存在设计上的几种不合理的因素。
一、单半径孔型成型首先轧辊的外径很大,钢带边缘升起高度大,因而增加成型轧辊的切入深度,使轧辊直径相应增大,轧辊材料成本高,在结构上造成成型机架相应减少了上辊的升降调整距离,从而影响了轧辊的使用寿命,增加生产成本。
二、单半径变形法边缘延伸大,容易产生边缘鼓包,所造成边缘变形不充分,成型质量不好,管缝容易产生尖嘴形和桃子形。
所造成钢管圆度不好。
产生钢管一边厚一边薄(如车螺纹容易破裂),使用钢管寿命短等缺点。
三、钢带从上料盘进入第一架时钢带咬入困难,使钢带上料断续生产时产生操作不方便,成型质量难于保证的现象。
二、改进孔型的设计方案这些问题的存在,不难发现单半径变形法孔型设计已经不适合我们企业生产技术和工艺规范要求。
只有对原来的孔型进行重新设计,才能有效解决上述在生产中发现的问题。
高频直缝焊管机组的调整及常见生产故障的分析(一)

高频焊管焊接缺陷及其分析

高频焊管焊接缺陷及其分析焊接缺陷及其分析高频直缝焊接钢管的焊接质量缺陷有裂缝、搭焊、漏水、划伤等等。
下面仅对裂缝、搭焊这两个主要缺陷进行分析:一、裂缝裂缝是焊管的主要缺陷,其表现形式可以由通常的裂缝,局部的周期性裂缝,不规则出现的断续裂缝。
也有的钢管焊后表面未见裂缝,但经压扁、矫直或水压试验后出现裂缝。
裂缝严重时便漏水。
产生裂缝的原因很多。
消除裂缝是焊接调整操作中最困难的问题之一。
下面分别从原料方面、成型焊接孔型方面和工艺参数选择方面进行分析。
1.原料方面(1)钢种,即钢的化学成分对焊接性能有明显的影响,钢中所含的化学元素都或多或少、或好或坏地影响着焊接性能。
高频焊由于焊接温度高,挤压力大等原因,比低频焊允许的化学范围要广些,可以焊接碳素钢、低合金钢等。
碳素钢主要含有碳、硅、锰、磷、硫五种元素。
低合金钢还可以含有锰、钛、钒、铝、镍等各种元素。
下面分述各种元素对焊接性能的影响。
1)碳碳含量增加,是焊接性能降低,硬度升高,容易脆裂。
低碳钢容易焊接。
2)硅硅降低钢的焊接性,主要是容易生成低镕点的SiO2 夹杂物;增加了熔渣和溶化金属的流动性,引起严重的喷溅现象,从而影响质量。
3)锰锰使钢的强度、硬度增加,焊接性能降低,容易造成脆裂。
4)磷磷对钢的焊接性不利。
磷是造成蓝脆的主要原因。
5)铜含量小于 0.75% 时,不影响钢的焊接性。
含量再高时,使钢的流动性增加,不利于焊接。
6) 镍镍对钢的焊接性没有显著的不利影响。
7) 铬铬使钢的焊接性能降低,高熔点氧化物很难从焊缝中排除。
8) 钛钛能细化晶粒,钛增加钢的焊接性能,钛能使钢的流动性变差,粘度大。
9)硫硫导致焊缝的热裂。
在焊接过程中硫易于氧化,生成气体逸出,以致在焊缝中产生很多气孔和疏松。
硫不利于焊接并且降低钢的机械性能,通常钢中硫被限制在规定的微量以下。
10) 钒钒能显著改善普通低合金钢的焊接性能。
钒能细化晶粒、防止热影响区的晶粒长大和粗化,并能固定钢中一部分碳,降低钢的淬透性。
高频焊管生产操作技术二

高频焊管生产操作技术(二)摘要:高频焊管生产中,操作对焊管质量的影响因素包括输入热量、焊接压力、焊接速度、开口角、感应器和阻抗器的放置位置、管坯的几何尺寸及形状等几方面。
在生产中掌握操作是提高焊管质量的重要途径之一。
关键词:高频焊管;焊接质量;焊接压力;焊接速度;汉高机械1.开口角开口角是指挤压辊前管坯两边缘的夹角,开口角的大小与烧化过程的稳定性有关,对焊接质量的影响很大。
减小开口角时,边缘之间的距离也减小,从而使邻近效应加强,在其它条件相同的情况下便可增大边缘的加热温度,从而提高焊接速度。
开口角如果过小时,将使会合点到挤压辊中心线的距离加长,从而导致边缘并非在最高温度下受到挤压,这样便使焊接质量降低,功率消耗增加。
实际生产经验表明,可移动导向辊的纵向位置来调整开口角大小,通常在2~6°之间变化。
在导向辊不能纵向调整的情况下,可用导向环厚度或压下封闭孔型来调整开口角的大小。
2.感应器及阻抗器的放置位置2.1感应器的放置位置感应器的放置位置(距挤压辊中心线的距离)对焊接质量影响很大。
距挤压辊中心线较远时,有效加热时间长,热影响区宽,使焊缝强度降低;反之边缘加热不足,也使焊缝强度降低。
感应器应与管同心放置,其前端与挤压辊中心线距离大约等于或小于管径(小管是1.5倍的管径)为最佳状态。
2.2 阻抗器的放置位置阻抗器(磁棒)的放置位置不但对焊接速度有很大影响,而且对焊接质量也有影响。
如图2所示[2]。
实践证明,阻抗器前端位置正好在挤压辊中心线处时,扩口强度和压扁强度最好。
当超过挤压辊中心线伸向定径机一侧时,扩口强度和压偏强度明显下降。
不到中心线而在成型机一侧时,也使焊接强度降低。
最佳位置即阻抗器放在感应器下面的管坯内,其头部与挤压辊中心线重合或向成型方向调节20~40mm,能增加管内背阻抗,减少其循环电流损失,提高焊接电压。
在用单匝感应器时,在感应器左右两边各挂一个小阻抗器,这样既增加了焊缝磁场,还使管坯边缘邻近效应加强,焊速每分钟可提高4~5m。
高频焊接的常见问题分析冯宝仲大港
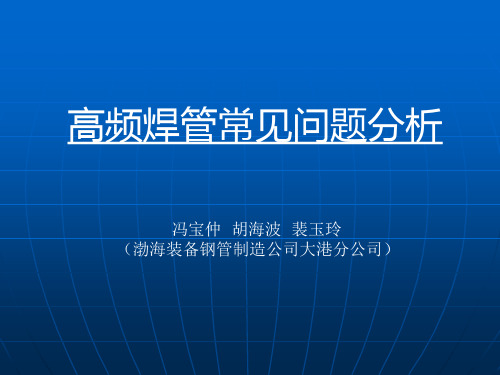
图8压扁后半焊接试样
使用压扁试验机,将半焊接试样沿焊缝方向压裂,露出颜色鲜明的两区:焊接融合区和
未融合区(图8),熔合区断口呈银白色,未熔合区呈蓝黑色。两区的交界处呈C型曲线。
C型曲线顶点位置
½ 板厚的处 ½ 板厚的上部 ½ 板厚的下部
成型质量 板边受力情况 带钢边缘成型形态形状
好
内=外
I型
差
内>外
结束语
判断焊管成型焊接质量的因素很多,如带钢边缘成型形态、错边量、内外
毛刺的形态、焊接挤压量、焊接温度、阻抗器、冷却水、高频焊接金相试验等,
只有对成型焊接各个影响因素做到十分全面的了解,才能够快速、准确的判断焊
接的状况。
参考文献
【1】王如涛、张艳军、白春生、张海军 高频焊管焊接质量分析[J]. 承钢技术, 2000(2):16-18.
2、倾斜状外毛刺
产生原因: 两板边对接时存在错边,导致两板边的受力状态不同,造成熔融金属被挤 出后偏离原来位置(如图5) 。
图5 倾斜状外毛刺
二、带钢边缘形态对焊接质量的影响
1、带钢边缘成型形态
(a) I型
(b)正V型
(c)倒V型
图6带钢边缘成型三种形态
带钢边缘成型 形态形状
成型质量
板边接触情况
原因2 两挤压边辊高度不同或者挤压辊框倾斜
原因3
板边质量原因。带钢存在镰刀弯、波浪弯等缺陷,或者带钢单侧板边发生磨 损。
(4)焊缝的扭转 。
图13焊缝的扭转
原因1 两焊接边辊高度不同,可以通过在水平辊辊框底部或侧部增减金属垫片校正。
原因2
两挤压边辊辊位沿焊管轧制中心不对称,导致两挤压边辊对管坯施力不等, 造成管坯发生扭转。
轧辊调整
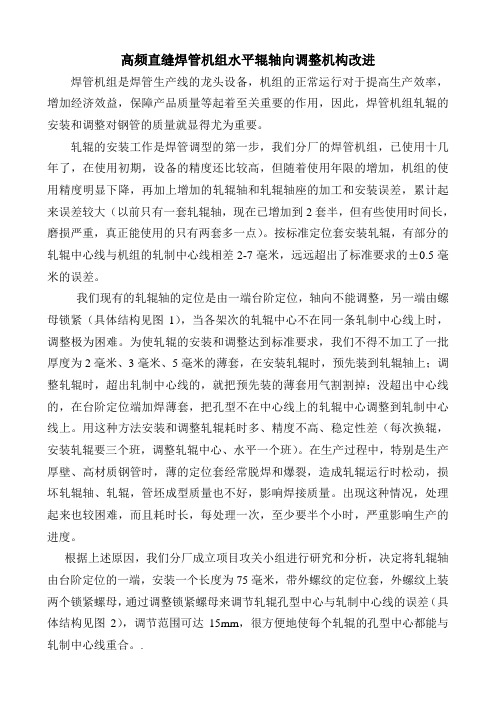
高频直缝焊管机组水平辊轴向调整机构改进焊管机组是焊管生产线的龙头设备,机组的正常运行对于提高生产效率,增加经济效益,保障产品质量等起着至关重要的作用,因此,焊管机组轧辊的安装和调整对钢管的质量就显得尤为重要。
轧辊的安装工作是焊管调型的第一步,我们分厂的焊管机组,已使用十几年了,在使用初期,设备的精度还比较高,但随着使用年限的增加,机组的使用精度明显下降,再加上增加的轧辊轴和轧辊轴座的加工和安装误差,累计起来误差较大(以前只有一套轧辊轴,现在已增加到2套半,但有些使用时间长,磨损严重,真正能使用的只有两套多一点)。
按标准定位套安装轧辊,有部分的轧辊中心线与机组的轧制中心线相差2-7毫米,远远超出了标准要求的±0.5毫米的误差。
我们现有的轧辊轴的定位是由一端台阶定位,轴向不能调整,另一端由螺母锁紧(具体结构见图1),当各架次的轧辊中心不在同一条轧制中心线上时,调整极为困难。
为使轧辊的安装和调整达到标准要求,我们不得不加工了一批厚度为2毫米、3毫米、5毫米的薄套,在安装轧辊时,预先装到轧辊轴上;调整轧辊时,超出轧制中心线的,就把预先装的薄套用气割割掉;没超出中心线的,在台阶定位端加焊薄套,把孔型不在中心线上的轧辊中心调整到轧制中心线上。
用这种方法安装和调整轧辊耗时多、精度不高、稳定性差(每次换辊,安装轧辊要三个班,调整轧辊中心、水平一个班)。
在生产过程中,特别是生产厚壁、高材质钢管时,薄的定位套经常脱焊和爆裂,造成轧辊运行时松动,损坏轧辊轴、轧辊,管坯成型质量也不好,影响焊接质量。
出现这种情况,处理起来也较困难,而且耗时长,每处理一次,至少要半个小时,严重影响生产的进度。
根据上述原因,我们分厂成立项目攻关小组进行研究和分析,决定将轧辊轴由台阶定位的一端,安装一个长度为75毫米,带外螺纹的定位套,外螺纹上装两个锁紧螺母,通过调整锁紧螺母来调节轧辊孔型中心与轧制中心线的误差(具体结构见图2),调节范围可达15mm,很方便地使每个轧辊的孔型中心都能与轧制中心线重合。
一种高频焊机上挤压辊调整驱动装置[实用新型专利]
![一种高频焊机上挤压辊调整驱动装置[实用新型专利]](https://img.taocdn.com/s3/m/aaf7bc9727284b73f34250cc.png)
专利名称:一种高频焊机上挤压辊调整驱动装置专利类型:实用新型专利
发明人:张海涛
申请号:CN201320288158.4
申请日:20130524
公开号:CN203343622U
公开日:
20131218
专利内容由知识产权出版社提供
摘要:本实用新型涉及一种高频焊机上挤压辊调整驱动装置,其特征在于:该驱动装置主要包括安装板、伺服电机和减速机,所述安装板固定安装在高频焊机机身的侧面,所述安装板上固定安装有伺服电机,所述伺服电机的控制线缆连接高频焊机自动化控制电控系统,所述伺服电机的输出端连接减速机,所述减速机通过紧固件固定安装在高频焊机机身上,所述减速机的输出端连接高频焊机上挤压辊水平移动调整装置。
综上所述高频焊机部分只需一个操作人员即可完整,当需要调整时很方便的就可以根据偏移量的大小进行调整,而且随时可以调整,从而避免了由于人工调整而和行进速度不匹配的问题,进而提高产品的焊接质量。
另外,节省了人力,降低了生产成本。
申请人:天津立业河山冷弯型钢有限公司
地址:301500 天津市宁河县经济开发区滨河路8号
国籍:CN
代理机构:天津市鼎和专利商标代理有限公司
代理人:李凤
更多信息请下载全文后查看。
- 1、下载文档前请自行甄别文档内容的完整性,平台不提供额外的编辑、内容补充、找答案等附加服务。
- 2、"仅部分预览"的文档,不可在线预览部分如存在完整性等问题,可反馈申请退款(可完整预览的文档不适用该条件!)。
- 3、如文档侵犯您的权益,请联系客服反馈,我们会尽快为您处理(人工客服工作时间:9:00-18:30)。
摘要:针对高频焊管焊接挤压辊的孔型特点,介绍了生产不同规格焊管时焊接挤压辊的调整方法。
结合高频焊管的成型工艺特点,提出了通过观察断面焊接区的金属流线方法,判定带钢边部端面焊接过程中合缝状态,并给出了不同合缝状态下调整挤压辊的具体办法。
在高频焊管生产中,管坯的成型合缝状态直接影响焊缝的质量,其中焊接接头对接面的平行度尤为重要。
在钢管合缝焊接过程中,主要通过调整挤压辊上辊的压下量与两上辊之间的间隙来保证合缝的平行程度。
1 焊接挤压辊的孔型特点焊接挤压机架的上挤压辊的孔型半径比其他挤压辊大10%左右,因此,上挤压辊的外侧辊面与钢管理想圆形断面之间产生了间隙,该间隙俗称为“后跟隙”。
在实际的成型中,钢管断面不可能是理想的圆形。
一般情况下,由于带钢边部的变形不充分,断面容易呈桃形,如果不进行调整则会形成焊接对接面不平行对接,严重影响焊缝质量。
如果上挤压辊与其他挤压辊采用同样的孔型半径,当通过调整上挤压辊的压下量来消除V形合缝时,上挤压辊的外侧辊面将强力压在钢管表面上,容易造成管面伤痕,并形成更严重的V形合缝。
因此“后跟隙”的设定,就是根据管坯成型的实际特点,通过上挤压辊的压下量调整来有效地消除V形合缝现象。
“后跟隙”位置及形状如图1所示。
2 上挤压辊的调整方法按
照标准孔型设定挤压辊位置时,如果发现成型合缝呈V形,可以在“后跟隙”的范围内,对上挤压辊的压下量进行调整,调整方法如图2所示。
上挤压辊的压下量的极限,是上挤压辊外侧辊面在钢管表面造成较浅的压痕。
按照经验,当达到这个压下限度时,即使是强度较高的管材,通常也能够形成平行(I形)的成型合缝。
在应用上述经验时,必须严格按照设计值来设定两个上挤压辊之间的间隙。
这个间隙的变化将直接引起“后跟隙”的变化。
如果每次换辊时不对该间隙按设计值进行严格的设定,那么孔型的调整就很难实现再现性。
出于同样的理由,在进行上辊的不对称调整消除错边时,务必只对操作台侧的上辊进行调整,而让另一侧的上辊始终固定作为基准。
如果随意调整两侧上辊,则有可能会使上辊间隙逐渐远离设定值。
3 特殊情况下的调整技巧
3.1 厚壁高强度管材的孔型调整
钢管的壁厚越大,材料强度越高,焊接时出现的V形合缝越不容易消除。
如果上辊外侧辊面已经造成了明显的压痕但仍无法实现I形合缝时,说明调整己经达到了极限,继续下压上辊不仅会造成严重的压痕,而且会形成更严重的V形对接合缝。
上述现象表明需要更大的“后跟隙”来容许更大的压下调整量。
为此,可以采用扩大两上辊之间的间隙来达到这一目的。
需要说明的是,理想的上辊间隙值是随钢管壁厚和强度的不同而不同的。
例如,壁厚较薄的情况一般需要设定较小的上辊间隙,以提高焊接的稳定性。
如壁厚较厚,则即便上辊间隙适当扩大,也不会影响焊接的稳定性。
因此,在厚壁或高强度钢管成型时为了获取更大的“后跟隙”而扩大上辊间隙的做法,只要扩大适当就不会影响焊接的稳定性。
孔型图上的标准设定值是设计者根据长年实践经验而选取的,通常情况下可以兼顾不同的壁厚和强度。
但如果出现上述的调整范围不足的情况,则适当扩大上辊间隙,可以在很大程度上解决问题。
这种调整方法的极限有两种情况,或是上辊外侧已经与立辊干涉,无法继续扩大间隙;或是上辊间隙过大,已经造成焊接的不稳定。
无论出现哪种情况,都说明需要修改挤压辊的结构设计,以获得更大的设定“后跟隙”。
厚壁高强度钢管情况下的调整如图3所示。
3.2 薄壁钢管的孔型调整对于薄壁钢管,通常情况下无需过大的上辊压下量就能获得I 形对接合缝。
经常出现的问题是焊接时成型合缝的稳定性。
薄壁钢管孔型调整如图4所示。
成型合缝的稳定性与很多因素有关,但适当减小上辊间隙一般都会起到提高成型合缝稳定性的效果。
因此,可以利用薄壁钢管不需要大的“后跟隙”的特性,在出现成型合缝不稳定的时候可以采用适当减少上辊间隙的方法来解决。
4 成型合缝对接状态的确认方法
观察断面焊接区的金属流线是确认焊接时成型合缝状态最准确的方法。
该方法不仅可以判断合缝状态,还可以判断焊接挤压量和焊接输出功率的合理与否。
为了便于流线的观察,试样应在焊缝热处理前采取。
如果焊缝上下部的金属流线角度基本对称的话,可以判断对接面的合缝是平行的(I形)。
以壁厚中部为对称面,上下对称部位的流线角的差通常需要限制在5°以内,而且热影响区的“腰鼓”形状也应基本上下对称。
焊缝区金属流线如图5所示。
现场最简易的确认方法是比较焊接后的内外毛刺的形状和大小,如图6所示。
如果合缝呈I形的话,内外毛刺的大小和形状是基本相同的。
但是这种方法无法量化,只能作为大致的判断。
使用流线观察法时,试样的制作一般需要较长的时间,等待结果往往会严重影响现场的作业效率。
为此,以下相对简易的合缝状态确认方法经常被使用,该方法虽不能够获得十分准确的结果,但一般可据此对合缝状态做出较准确的判断,可以大大减少流线观察法等待结果的时间。
首先按图7所示的方法进行取样。
应注意,必须先停止焊机的功率输出后再停车。
否则,得到合缝的接触模式和加热模式将不同于稳态焊接时的模式。
图8和图9显示了接触和加热模式与合缝状态之间的关系,据此可以进行合缝状态的判断。
接触形态与加热形态原则上是一致的。
接触模式的界限分明,而加热模式较为模糊,判断者需要有一定的经验。
但当焊接挤压量较大时,接触模式在纵向上的分布会短到难以判断的程度,而加热模式则不受这种影响。
5 结论
在高频焊管调型与焊接中,通过对接触和加热模式与对接面合缝状态关系的分析,采用调整焊接挤压辊上辊间隙和压下量的方法,能准确及时地保证钢管的板边焊接达到良好的焊接状态。
(1)当合缝呈I形时,说明此时对接面在焊接过程中处于基本平行状态,不需要进行挤压辊压下调整;
(2)当合缝呈V形时,说明此时对接面在焊接过程中,下部表面先接触,可以通过加大挤压辊上辊压下量达到I形状态;
(3)当合缝呈倒V形时,说明此时对接面在焊接过程中,上部表面先接触,可以通过减小挤压辊压下量达到I形状态。