高频焊管焊接工艺培训
焊接技术培训
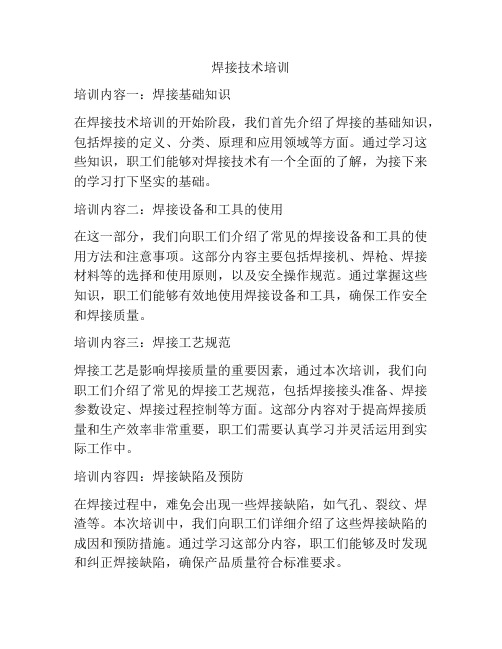
焊接技术培训培训内容一:焊接基础知识在焊接技术培训的开始阶段,我们首先介绍了焊接的基础知识,包括焊接的定义、分类、原理和应用领域等方面。
通过学习这些知识,职工们能够对焊接技术有一个全面的了解,为接下来的学习打下坚实的基础。
培训内容二:焊接设备和工具的使用在这一部分,我们向职工们介绍了常见的焊接设备和工具的使用方法和注意事项。
这部分内容主要包括焊接机、焊枪、焊接材料等的选择和使用原则,以及安全操作规范。
通过掌握这些知识,职工们能够有效地使用焊接设备和工具,确保工作安全和焊接质量。
培训内容三:焊接工艺规范焊接工艺是影响焊接质量的重要因素,通过本次培训,我们向职工们介绍了常见的焊接工艺规范,包括焊接接头准备、焊接参数设定、焊接过程控制等方面。
这部分内容对于提高焊接质量和生产效率非常重要,职工们需要认真学习并灵活运用到实际工作中。
培训内容四:焊接缺陷及预防在焊接过程中,难免会出现一些焊接缺陷,如气孔、裂纹、焊渣等。
本次培训中,我们向职工们详细介绍了这些焊接缺陷的成因和预防措施。
通过学习这部分内容,职工们能够及时发现和纠正焊接缺陷,确保产品质量符合标准要求。
培训内容五:焊接技术新发展及应用最后,我们向职工们介绍了焊接技术的新发展和应用,包括激光焊接、电子束焊接、摩擦搅拌焊接等先进的焊接技术。
这些新技术在提高焊接质量和生产效率方面都有着重要的作用,职工们需要密切关注并学习相关知识,以适应未来的发展需求。
通过本次焊接技术培训,我们相信职工们能够掌握更加丰富和实用的焊接知识,提高焊接技术水平,为企业的发展做出更大的贡献。
希望大家能够牢记培训内容,不断加强学习和实践,不断完善自己的焊接技术,为企业赢得更多的成果和荣誉。
培训内容六:焊接安全知识焊接作为一项高温高压的工艺活动,涉及到一系列安全隐患,比如火灾、爆炸、电击、放射性等问题。
因此,本次培训还专门对焊接安全知识进行了详细介绍。
我们向职工们强调了安全意识的重要性,提出了正确使用个人防护装备、遵守操作规程、参与安全培训等安全管理措施。
焊接详细的培训计划

焊接详细的培训计划一、培训目的焊接是一种非常重要的技能,广泛应用于制造业,建筑业,汽车制造业等领域。
正确的焊接技术可以保证产品的质量,提高生产效率,降低生产成本。
因此,进行焊接培训对于提高员工的技能水平,提高企业的竞争力是非常重要的。
二、培训对象本次培训主要面向生产一线的工人和技术人员,包括初级焊工,高级焊工,焊接监督员等。
三、培训内容1. 理论知识1.1 焊接的定义、分类和原理1.2 焊接设备的种类和工作原理1.3 焊接材料的种类和特性1.4 焊接工艺的概念和要求2. 实践操作2.1 焊接设备的操作和维护2.2 焊接材料的使用和存储2.3 不同类型的焊缝的焊接方法和技巧2.4 焊接质量的检验和评定标准3. 安全知识3.1 焊接作业的安全注意事项3.2 防护装备的使用和保养3.3 火灾事故的预防和处理四、学习要求1. 学员应具备一定的金属材料知识2. 对于焊接设备的操作有一定的了解3. 对于焊接操作有一定的实际经验4. 有一定的安全意识五、培训方式1. 由专业的焊接技术专家组织讲授理论知识2. 分组进行实践操作,现场指导3. 结合案例分析,让学员了解在实际生产中的应用六、培训时间本次培训计划为期一周,每天工作八个小时,包括四天的理论课程和三天的实践操作。
七、教学资源1. 焊接模拟器2. 焊接设备和材料3. 教学课件和案例分析八、培训评估1. 考试:理论考试和实践操作考试2. 评定标准:根据参训学员的学习表现和考试成绩综合评定3. 优秀学员奖励:对于表现突出的学员进行奖励和认定九、培训效果1. 学员掌握焊接的基本理论知识2. 学员掌握焊接设备的操作和维护技巧3. 学员掌握不同类型焊接方法和技巧4. 学员对于安全知识有所提高十、写在最后焊接技术是一门独特的技能,需要通过实践不断的进行学习和提高。
通过本次培训计划,希望能够提高学员的技能水平,为企业的发展做出更大的贡献。
同时,还要坚持安全第一的原则,保障员工的人身安全和生产设备的安全。
高频焊工艺操作规程
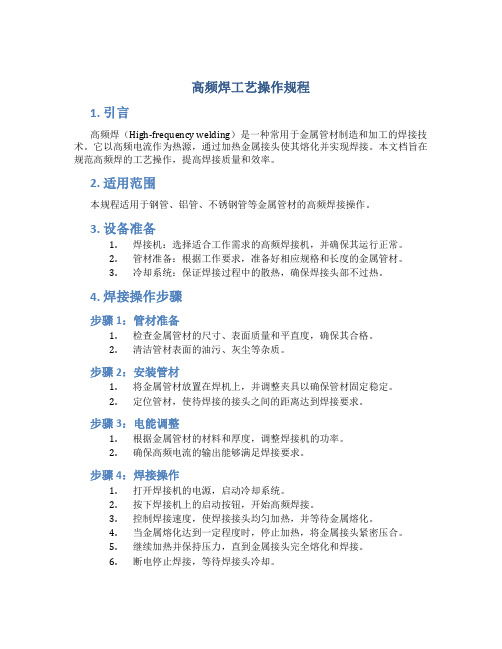
高频焊工艺操作规程1. 引言高频焊(High-frequency welding)是一种常用于金属管材制造和加工的焊接技术。
它以高频电流作为热源,通过加热金属接头使其熔化并实现焊接。
本文档旨在规范高频焊的工艺操作,提高焊接质量和效率。
2. 适用范围本规程适用于钢管、铝管、不锈钢管等金属管材的高频焊接操作。
3. 设备准备1.焊接机:选择适合工作需求的高频焊接机,并确保其运行正常。
2.管材准备:根据工作要求,准备好相应规格和长度的金属管材。
3.冷却系统:保证焊接过程中的散热,确保焊接头部不过热。
4. 焊接操作步骤步骤1:管材准备1.检查金属管材的尺寸、表面质量和平直度,确保其合格。
2.清洁管材表面的油污、灰尘等杂质。
步骤2:安装管材1.将金属管材放置在焊机上,并调整夹具以确保管材固定稳定。
2.定位管材,使待焊接的接头之间的距离达到焊接要求。
步骤3:电能调整1.根据金属管材的材料和厚度,调整焊接机的功率。
2.确保高频电流的输出能够满足焊接要求。
步骤4:焊接操作1.打开焊接机的电源,启动冷却系统。
2.按下焊接机上的启动按钮,开始高频焊接。
3.控制焊接速度,使焊接接头均匀加热,并等待金属熔化。
4.当金属熔化达到一定程度时,停止加热,将金属接头紧密压合。
5.继续加热并保持压力,直到金属接头完全熔化和焊接。
6.断电停止焊接,等待焊接头冷却。
步骤5:检测和质量控制1.使用合适的检测设备或方法,检测焊接接头的质量。
2.重复焊接操作步骤,直到焊接质量符合要求。
5. 安全注意事项1.使用个人防护装备,如安全帽、护目镜、耐热手套等。
2.在焊接操作时,保持操作区域清洁、整齐,防止绊倒和意外发生。
3.根据操作手册正确使用设备,避免设备故障和意外事故。
4.在使用设备前,检查电源线路、保险丝等电气部件是否正常,确保操作安全。
6. 维护和保养1.确保设备周围环境干净整洁,避免灰尘等杂质进入设备内部。
2.定期清洁焊接机表面,保持设备的正常运行。
高频焊管工艺流程
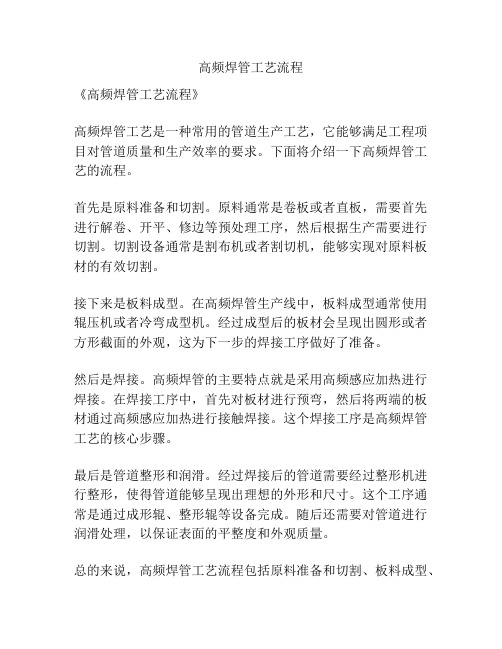
高频焊管工艺流程
《高频焊管工艺流程》
高频焊管工艺是一种常用的管道生产工艺,它能够满足工程项目对管道质量和生产效率的要求。
下面将介绍一下高频焊管工艺的流程。
首先是原料准备和切割。
原料通常是卷板或者直板,需要首先进行解卷、开平、修边等预处理工序,然后根据生产需要进行切割。
切割设备通常是割布机或者割切机,能够实现对原料板材的有效切割。
接下来是板料成型。
在高频焊管生产线中,板料成型通常使用辊压机或者冷弯成型机。
经过成型后的板材会呈现出圆形或者方形截面的外观,这为下一步的焊接工序做好了准备。
然后是焊接。
高频焊管的主要特点就是采用高频感应加热进行焊接。
在焊接工序中,首先对板材进行预弯,然后将两端的板材通过高频感应加热进行接触焊接。
这个焊接工序是高频焊管工艺的核心步骤。
最后是管道整形和润滑。
经过焊接后的管道需要经过整形机进行整形,使得管道能够呈现出理想的外形和尺寸。
这个工序通常是通过成形辊、整形辊等设备完成。
随后还需要对管道进行润滑处理,以保证表面的平整度和外观质量。
总的来说,高频焊管工艺流程包括原料准备和切割、板料成型、
焊接、管道整形和润滑等几个主要步骤。
每一步工序都需要进行严格的控制和管理,以保证最终产品的质量和性能。
随着科技的进步,高频焊管工艺也在不断创新和发展,为各种工程项目的管道生产提供了可靠的解决方案。
焊接培训工作重点及计划
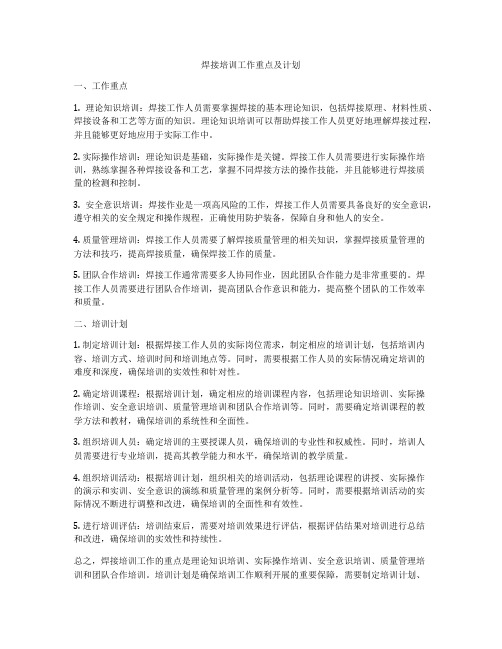
焊接培训工作重点及计划一、工作重点1. 理论知识培训:焊接工作人员需要掌握焊接的基本理论知识,包括焊接原理、材料性质、焊接设备和工艺等方面的知识。
理论知识培训可以帮助焊接工作人员更好地理解焊接过程,并且能够更好地应用于实际工作中。
2. 实际操作培训:理论知识是基础,实际操作是关键。
焊接工作人员需要进行实际操作培训,熟练掌握各种焊接设备和工艺,掌握不同焊接方法的操作技能,并且能够进行焊接质量的检测和控制。
3. 安全意识培训:焊接作业是一项高风险的工作,焊接工作人员需要具备良好的安全意识,遵守相关的安全规定和操作规程,正确使用防护装备,保障自身和他人的安全。
4. 质量管理培训:焊接工作人员需要了解焊接质量管理的相关知识,掌握焊接质量管理的方法和技巧,提高焊接质量,确保焊接工作的质量。
5. 团队合作培训:焊接工作通常需要多人协同作业,因此团队合作能力是非常重要的。
焊接工作人员需要进行团队合作培训,提高团队合作意识和能力,提高整个团队的工作效率和质量。
二、培训计划1. 制定培训计划:根据焊接工作人员的实际岗位需求,制定相应的培训计划,包括培训内容、培训方式、培训时间和培训地点等。
同时,需要根据工作人员的实际情况确定培训的难度和深度,确保培训的实效性和针对性。
2. 确定培训课程:根据培训计划,确定相应的培训课程内容,包括理论知识培训、实际操作培训、安全意识培训、质量管理培训和团队合作培训等。
同时,需要确定培训课程的教学方法和教材,确保培训的系统性和全面性。
3. 组织培训人员:确定培训的主要授课人员,确保培训的专业性和权威性。
同时,培训人员需要进行专业培训,提高其教学能力和水平,确保培训的教学质量。
4. 组织培训活动:根据培训计划,组织相关的培训活动,包括理论课程的讲授、实际操作的演示和实训、安全意识的演练和质量管理的案例分析等。
同时,需要根据培训活动的实际情况不断进行调整和改进,确保培训的全面性和有效性。
焊接工艺知识培训教程

焊接工艺知识培训教程一、焊接工艺知识1. 焊接原理焊接是通过加热金属材料,在一定压力下使其熔化,然后冷却后形成牢固的连接。
焊接的原理是利用电弧能量和熔化的焊条将要连接的金属材料熔化,并形成连接。
2. 焊接分类按照焊接方式的不同,焊接可以分为手工焊接、自动焊接和半自动焊接。
按照焊接材料的不同,可以分为电弧焊、气体保护焊、激光焊等。
3. 焊接设备常见的焊接设备包括电弧焊机、气体保护焊机、激光焊机等。
不同的焊接设备适用于不同的焊接方式和材料。
4. 焊接安全焊接时需要注意安全,包括佩戴防护眼镜、手套、面具等个人防护装备,确保焊接作业环境通风良好,避免产生有害气体。
二、焊接工艺培训教程1. 熟悉焊接设备学习焊接首先需要熟悉各种焊接设备的使用方法和操作规程,包括电弧焊机、气体保护焊机等设备的使用方式和维护方法。
2. 学习焊接材料的选择和准备了解各种焊接材料的类型和特点,包括焊条、焊丝、气体保护剂等,学会正确选择和准备焊接材料。
3. 掌握焊接技术学习焊接技术是焊接培训的关键。
包括焊接姿势、焊接速度、焊接电流和电压的调节等技术要点。
4. 实践操作通过实际操作,掌握焊接技术,熟练掌握不同种类的焊接工艺,提高焊接质量和效率。
5. 安全意识培养焊接作业需要非常严格的安全措施,包括个人防护和作业环境的安全。
要培养焊接工作者的安全意识,确保在焊接过程中避免发生安全事故。
在焊接工艺培训教程中,学员除了需要掌握以上基本知识和技能外,还需要了解焊接工艺标准和规范,以及各种不同工况下的焊接质量要求和检验方法。
通过系统的培训教程,焊接工作者可以快速掌握焊接技能,提高工作效率和质量。
6. 焊接工艺标准和规范在焊接培训教程中,学员需要了解国家和行业制定的相关焊接工艺标准和规范,包括焊接工艺规范、焊接接头设计规范、焊接检测标准等。
掌握这些标准和规范可以帮助焊接工作者更好地理解焊接工艺要求,保证焊接质量。
7. 焊接质量要求和检验方法学员需要了解各种不同工况下的焊接质量要求和检验方法,包括焊缝外观、焊缝密度、焊接强度等方面的要求和检验方法。
高频焊管焊接工艺培训
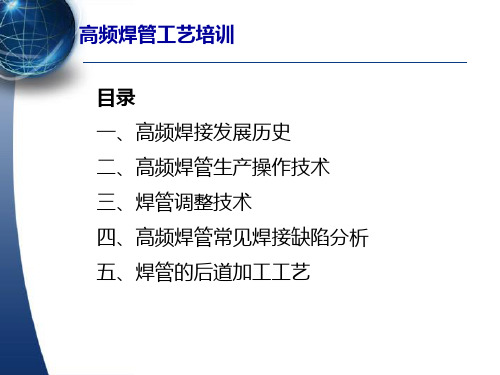
二、高频焊管生产操作技术
1 因为焊接工艺的主要参数之一,即焊接电流(或焊接温度)难 以测量,所以用输入热量来代替,而输入热量又可用振荡器输出功率来表示: N = Ep· Ip 式中 N——输出功率,kW; Ep——屏压,kV; Ip——屏流,A〔1 。 当振荡器、感应器和阻抗器确定后,振荡管槽路、输出变压器、感应器的效率 也就确定了,输入功率的变化同输入热量的变化大致是成比例的。 当输入热量 不足时,被加热边缘达不到焊接温度,仍保持固态组织而焊不上,形成焊合裂缝;当输 入热量大时,被加热边缘超过焊接温度易产生过热,甚至过烧,受力后产生开裂;当输 入热量过大时,焊接温度过高,使焊缝击穿,造成熔化金属飞溅,形成孔洞。熔化焊接 温度一般在1350~1400℃为宜。
二、高频焊管生产操作技术
2 焊接压力是焊接工艺的主要参数之一,管坯的两边缘加热到焊接温度后,在挤压力 作用下形成共同的金属晶粒即相互结晶而产生焊接。焊接压力的大小影响着焊缝 的强度和韧性。若所施加的焊接压力小,使金属焊接边缘不能充分压合,焊缝中残 留的非金属夹杂物因压力小不易排出,焊缝强度降低,受力后易开裂;压力过大时,达 到焊接温度的金属大部分被挤出,不但降低焊缝强度,而且产生内外毛刺过大或 搭 焊等缺陷。因此应根据不同的品种规格在实际中求得与之相适应的最佳焊接压力 。根据实践经验单位焊接压力一般为20~40MPa 由于管坯宽度及厚度可能 存在的公差,以及焊接温度和焊接速度的波动,都有可能涉及到焊接挤压力的变化 。焊接挤压量一般通过调整挤压辊之间的距离进行控制,也可以用挤压辊前后管 筒周差来控制。
实际生产经验表明,可移动导向辊的纵向位置来调整开口角大小,通常在2~6°之间变 化。在导向辊不能纵向调整的情况下,可用导向环厚度或压下封闭孔型来调整开口角 的大小。
高频焊接工艺技术方法

焊接温度因素 焊接温度受电源系统(高频功率、频率、 效率)、加热介质(热容量,电阻率,温 度扩散率,热传导系数,导磁率等)和操 作条件(焊接速度,感应圈位臵,阻抗器, 开口角等)等的影响。
高频焊机焊接方式
1、高频接触焊基本原理
一对电极腿与管筒两边缘接触,直接向管筒边缘
输入高频电流,利用高频电流的集肤效应与邻近效应,使电流高度集中在管 筒边缘的焊合面上,依靠金属自身的电阻,将钢带边缘迅速加热至焊接温度, 在挤压辊的挤压下完成力焊接。
阻抗器的放臵位臵对焊接的影响 位臵对焊接速度有影响。阻抗器应放臵在V 形区加热段,中心线与管筒中心线一致, 管筒边缘上方应放臵铁淦氧;b、对焊接质 量有影响。阻抗器前端在挤压辊中心位臵 处时,焊管的压扁试验和扩口试验为最好, 超出或不到挤压辊中心时,焊接强度都有 下降。
开口角对高频焊接的影响
开口角指钢带在挤压辊成型时形成的V形区 的夹角,对焊接效果也有影响。角度小时 邻近效应强,增加了电流的密度,使热量 增高,有利于焊接。但角度也不宜过小, 过小时缝隙过狭,容易跳火放电,影响焊 缝质量。一般开口角在4°—7°范围内。
厚度的一半与渗透深度之比愈大,邻近效应愈强。在此值很大的情况下,全
部电流将集中到一个面上(由电流方向决定)汇流条其余部分就没有电流。 假如,在离开通有高频电流的导体若干距离的地方,放一些金属零件,那么
由于导体四周所产生的交变磁场的作用,另件中就会感应出涡流来,二者的
电流方向在任一瞬间都是相反的,并且都集中在导体和另件邻近的面上。这 种现象叫做邻近效应。
注:根据实际需要可选择相近规格磁棒,或定尺其它长度磁棒,磁棒应尽量放置在钢管内壁 中心位置。
冷却水的控制
磁棒、感应圈及相邻挤压辊装臵因高频效 应产生较大热量,必须加强流水予以冷却, 冷却后温度<400C。输出变压器或感应圈装 臵也应通入循环冷却水,并保证在运行过 程循环水出口处中长期流水。
管道焊接教育培训计划

管道焊接教育培训计划一、培训目标管道焊接是一项需要专业技能和技巧的工作,因此对焊接人员的培训非常重要。
本培训计划的目标是为参加培训的人员提供全面的焊接知识和技能培训,使其能够胜任工作,并且具备较强的团队协作能力。
二、培训内容1. 焊接安全知识- 焊接操作中的安全注意事项- 焊接操作中的应急处理措施- 焊接材料的安全性及防护措施2. 焊接理论知识- 焊接原理和焊接方法- 焊接材料的性能和用途- 焊接工艺参数的确定方法3. 焊接技能训练- 焊接设备的操作与维护- 焊接工艺的实际操作- 焊接质量检验方法4. 团队协作培训- 理解团队工作的重要性- 学习与他人合作的技巧- 团队协作案例分析三、培训方式1. 现场教学- 利用现场实际工作环境进行教学,使学员能够真实地感受到焊接工作的特点和要求。
- 利用实际焊接案例进行教学,让学员在实践中学习,掌握焊接技术。
2. 理论授课- 通过专业老师的讲解,学习焊接理论知识。
- 使用多媒体技术进行授课,以便学员更好地理解和记忆知识。
3. 案例分析- 分析一些真实的案例,让学员了解不同情况下的焊接技术和方法。
- 分析成功或失败的案例,总结经验教训,为学员提供指导。
四、培训流程1. 课前准备- 准备好教学材料- 对培训场地进行检查和准备2. 开班仪式- 介绍课程内容和培训目标- 介绍培训师资力量3. 焊接安全知识的培训- 介绍焊接操作中的安全注意事项- 模拟事故场景并进行紧急处理演练4. 焊接理论知识的培训- 讲解焊接原理和方法- 介绍焊接材料的性能和用途5. 焊接技能训练- 操作与维护焊接设备- 实际操作焊接工艺6. 团队协作培训- 理解团队工作的重要性- 学习与他人合作的技巧7. 课程总结- 学员提交培训反馈意见- 进行课程总结和学习成果评定五、培训效果的评估1. 学员考核- 学员需要通过笔试和实操考核来检验学习效果- 合格考生将会获得培训结业证书2. 学员反馈- 收集学员对培训的反馈,以便对培训进行调整和改进 - 通过学员反馈评估培训效果3. 培训成效评估- 观察学员在实际工作中的表现- 对培训的整体效果进行评估六、绩效评估1. 学员通过率- 观察学员的通过率,以衡量整体培训效果2. 培训后实际操作表现- 对参加培训的学员在实际工作中的表现进行评估3. 反馈调查- 收集学员的培训反馈,了解学员对培训的真实看法七、培训费用1. 培训费用- 培训费用将由公司承担- 培训期间的食宿费用由公司承担2. 学员的时间成本- 学员在参加培训期间的工作时间将得到相应的补偿以上是管道焊接教育培训计划的一些基本内容,希望通过全面的培训,能够为学员提供更好的技术与知识。
高频焊接的工艺
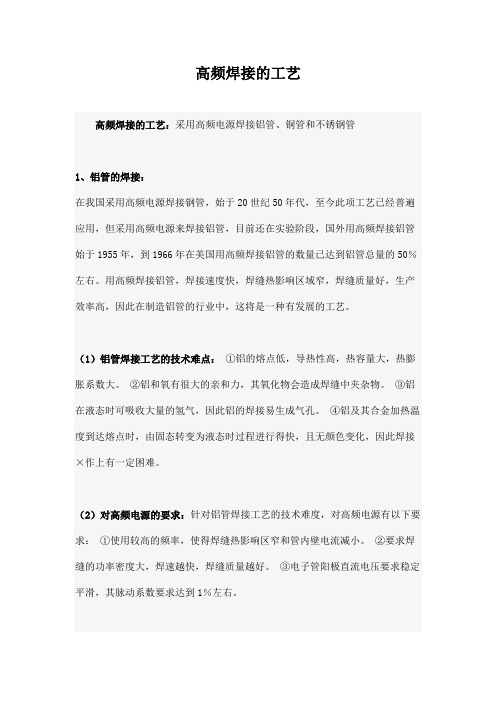
高频焊接的工艺高频焊接的工艺:采用高频电源焊接铝管、铜管和不锈钢管1、铝管的焊接:在我国采用高频电源焊接钢管,始于20世纪50年代,至今此项工艺已经普遍应用,但采用高频电源来焊接铝管,目前还在实验阶段,国外用高频焊接铝管始于1955年,到1966年在美国用高频焊接铝管的数量已达到铝管总量的50%左右。
用高频焊接铝管,焊接速度快,焊缝热影响区域窄,焊缝质量好,生产效率高,因此在制造铝管的行业中,这将是一种有发展的工艺。
(1)铝管焊接工艺的技术难点:①铝的熔点低,导热性高,热容量大,热膨胀系数大。
②铝和氧有很大的亲和力,其氧化物会造成焊缝中夹杂物。
③铝在液态时可吸收大量的氢气,因此铝的焊接易生成气孔。
④铝及其合金加热温度到达熔点时,由固态转变为液态时过程进行得快,且无颜色变化,因此焊接×作上有一定困难。
(2)对高频电源的要求:针对铝管焊接工艺的技术难度,对高频电源有以下要求:①使用较高的频率,使得焊缝热影响区窄和管内壁电流减小。
②要求焊缝的功率密度大,焊速越快,焊缝质量越好。
③电子管阳极直流电压要求稳定平滑,其脉动系数要求达到1%左右。
(3)焊接铝管高频电源采用的几项措施:①采用较高的频率,对于100KW设备采用600~700KHz,60KW设备采用700~800KHz。
②电子管阳极电源采用12相整流,并加装平滑滤波器,由于采用可控硅调压,应使其工作在较小的导通角状态,以减小整流后的脉动系数。
③有较高的输出功率,使铝管有较高的焊接速度。
④合理的振荡电路,应做到负载调整方便。
(4)应用前景:1、铝具有蕴藏量大、比强高、质轻、耐腐蚀等特点,因此产量大、成本低的焊接铝管,大量应用于农业喷灌系统、化工、轻纺、轻型建筑及家具等场合以替代钢管。
目前国内焊接铝管多采用氩弧焊,速度很低,应用高频焊代替,可达到很高的速度。
我公司制造的设备,对小口径薄壁管,焊速可达到120m/min以上。
另外,高频焊接也可用于焊接不锈钢管、铜管、黄铜管等,及非导磁体金属管材。
焊管制造工艺培训

: 1.5A
频率: 50Hz
输出 : 4A
直流电压: 11.5kV 直流电流 频率: 120000Hz节: 根据焊接线能量的变化及时调节输出 电压和焊接速度。参数固定后一般不用调整。
第二章 高频焊管机组
➢第一节 用途 ➢第二节 排列与布置 ➢第三节 主要结构 ➢第四节 调整与故障处理 ➢第五节 维护与保养
5.2 焊接温度控制 焊接温度主要受高频涡流热功率的影响,根据公式(2)可知,高频涡
流热功率主要受电流频率的影响,涡流热功率与电流激励频率的平方成 正比;而电流激励频率又受激励电压、电流和电容、电感的影响。激励 频率公式为:
f=1/[2π(CL)1/2]...(1) 式中: f-激励频率(Hz);C-激励回路中的电容(F),电容=电量/电压; L-激励回路中的电感,电感=磁通量/电流 上式可知,激励频率与激励回路中的电容、电感平方根成反比、或者与 电压、电流的平方根成正比,只要改变回路中的电容、电感或电压、电流 即可改变激励频率的大小,从而达到控制焊接温度的目的。对于低碳钢, 焊接温度控制在1250~1460℃,可满足管壁厚3~5mm焊透要求。另外 ,焊接温度亦可通过调节焊接速度来实现。
车管。 7 锅炉管用来制造蒸汽发生器管, 过热蒸汽管、水管、烟管、空
气预热器官、热交换器官。 8 石油管用作油管、套管、输油管。 9 螺旋焊管、大直径直缝焊管用作输送管线。 10 变断面锥形焊管用作灯柱灯杆。 11 复合管、有机涂层管用作耐各种腐蚀的特殊用途中。 12 不锈钢管主要用于化工、食品等
二、高频焊接
三、钢管生产过程中的重要环节
1.在高频焊管生产过程中 , 如何确保产品质量符合技
术标准的要求和顾客的需要 , 则要对钢管生产过程中影响
2024年管道焊接培训计划方案

2024年管道焊接培训计划方案一、培训目标本培训计划的目标是提供高质量的管道焊接培训,培养具备扎实的焊接技术和安全意识的技术工人。
通过培训,使学员能够掌握管道焊接的理论知识和实际操作技能,熟悉各种焊接工艺和焊接设备的使用,能够独立完成常见管道的焊接任务,并具备良好的安全意识和团队合作精神。
二、培训内容1. 理论知识培训(1)焊接工艺和焊缝的分类(2)焊接材料的选择和性能要求(3)焊接工艺参数的确定与计量(4)焊接变形与焊缝质量控制(5)焊接缺陷的产生原因与防范措施2. 实际操作培训(1)焊接设备的使用和维护(2)管道焊接前的准备工作(3)各种焊接工艺的实施方法与技巧(4)焊接质量控制与检测方法(5)常见焊接缺陷的处理与修复3. 安全意识培训(1)焊接作业安全规范(2)焊接作业中的常见危险及相应的预防措施(3)急救知识与应急处理技巧三、培训方式1. 理论知识培训(1)采用课堂讲授的方式,结合教材、案例分析、多媒体展示等形式进行。
(2)邀请有相关领域经验的专家进行授课,确保培训内容的权威性和实用性。
2. 实际操作培训(1)在工业实践基地或模拟训练场进行实操培训,提供真实的训练环境。
(2)由经验丰富的技术人员进行指导和实际操作演练,确保学员能够熟练掌握操作技巧。
3. 安全意识培训(1)组织安全培训课程,包括理论授课和实际演练。
(2)请专业的安全培训机构或相关部门进行培训,确保培训内容的专业性和有效性。
四、培训流程1. 预备阶段(1)招募学员并进行初步筛选,确保符合培训要求。
(2)确定培训地点和时间,并配备所需的培训设备和教材。
2. 理论知识培训阶段(1)开展理论知识培训课程,注重基础知识的讲解和理解。
(2)组织学员进行理论考试,评估学员的学习情况。
3. 实际操作培训阶段(1)进行实际操作培训,注重实操技能的训练和提升。
(2)组织学员进行实操考核,评估学员的操作水平和能力。
4. 安全意识培训阶段(1)开展安全意识培训课程,注重安全知识的传授和安全技能的培养。
焊接工艺培训操作教学大纲
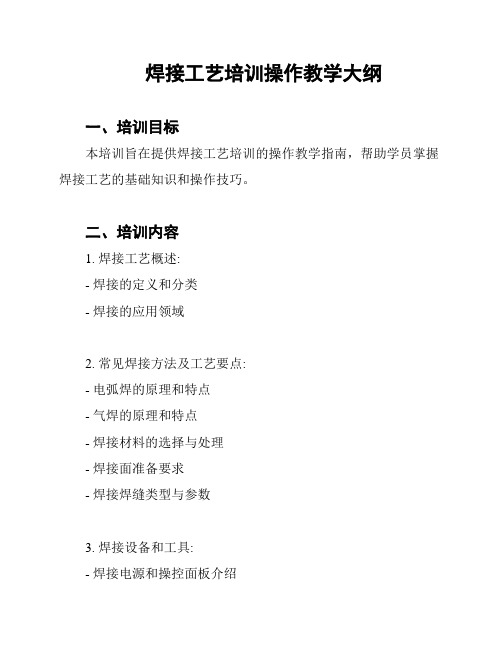
焊接工艺培训操作教学大纲一、培训目标本培训旨在提供焊接工艺培训的操作教学指南,帮助学员掌握焊接工艺的基础知识和操作技巧。
二、培训内容1. 焊接工艺概述:- 焊接的定义和分类- 焊接的应用领域2. 常见焊接方法及工艺要点:- 电弧焊的原理和特点- 气焊的原理和特点- 焊接材料的选择与处理- 焊接面准备要求- 焊接焊缝类型与参数3. 焊接设备和工具:- 焊接电源和操控面板介绍- 焊接工具的种类和用途- 焊接辅助设备的使用4. 焊接操作规程:- 焊接安全操作规程- 焊接步骤和注意事项- 焊接质量检验标准5. 焊接故障分析与解决:- 常见焊接故障及产生原因- 故障排除和解决方法6. 焊接实操课程安排:- 使用不同焊接方法进行实操练- 综合性焊接项目实践三、培训时间和地点- 培训时间: 每周三晚上7:00-9:00,共8周- 培训地点: 公司培训室四、培训对象- 公司员工,特别是与焊接工艺相关的技术人员和操作人员五、培训方式- 理论课程: 使用PPT进行讲解,示范和案例分析- 实操课程: 使用真实设备和材料进行操作演练- 互动讨论: 鼓励学员提问和参与讨论,加强研究效果六、培训评估- 考试: 培训结束后进行理论和实操考试- 满意度调查: 培训结束后进行学员满意度调查,反馈意见和建议七、培训费用- 公司负责培训费用,包括教材、设备和场地费用八、培训师资- 公司内部焊接工程师和经验丰富的技术人员九、培训效果- 学员能够掌握焊接工艺的基本原理和操作要点- 学员能够独立进行常见焊接操作- 学员能够识别和解决常见焊接故障十、备注- 培训期间,学员需佩戴相应的个人防护装备,注意安全事项- 学员对培训内容有任何意见和建议,可随时联系培训负责人以上为焊接工艺培训操作教学大纲,如有任何更改,将提前通知学员。
祝大家顺利完成培训!。
焊接工艺培训教程(焊接控制培训)

焊接速度决定了焊接效率,过快可能导致 焊缝不熔合,过慢则可能使焊缝过热。
多层多道焊接有助于减小焊接变形和提高 焊缝质量。
焊接操作技巧
引弧与熄弧
正确引弧可以避免电弧不 稳或烧蚀,熄弧时应将电 弧慢慢收起,防止产生弧 坑。
运条方法
焊条沿焊缝方向的移动应 均匀,速度适中,避免忽 快忽慢。
接头与收尾
接头处应预热,收尾时应 将弧坑填满,避免出现裂 纹。
电子行业
在电子行业中,焊接用于 电路板、电子元件的连接 和固定。
02 焊接工艺技术
焊接工艺参数
焊接电流
焊接电压
电流的大小直接影响焊接熔池的形成和焊 缝的成型,电流过大可能导致焊缝过热、 焊穿,电流过小则可能导致焊缝不熔合。
电压是电弧燃烧的必要条件,合适的电压 有助于稳定电弧和熔池。
焊接速度
焊接层数与厚度
压力容器属于特种设备,其焊接工艺要求非常高, 需要满足安全性能和使用性能的要求。
焊接接头的质量控制
压力容器焊接过程中,需要严格控制焊接接头的 质量,确保无缺陷、无泄漏,保证容器的安全性 能。
焊接工艺评定
在压力容器制造过程中,需要进行焊接工艺评定, 确保焊接工艺的可靠性和可行性。
桥梁焊接工艺实例
桥梁焊接工艺特点
船舶焊接工艺要求高,需要考虑 到船体的特殊结构和环境因素,
如防腐蚀、防震等。
焊接材料选择
根据船体材料和结构特点,选择 合适的焊接材料,如不锈钢、高
强度钢等。
焊接工艺流程
船舶焊接工艺流程复杂,需要经 过多道工序,如预热、焊接、后 热等,确保焊缝质量和船体结构
的稳定性。
压力容器焊接工艺实例
1 2 3
压力容器焊接工艺要求
2023年管道焊接培训计划方案
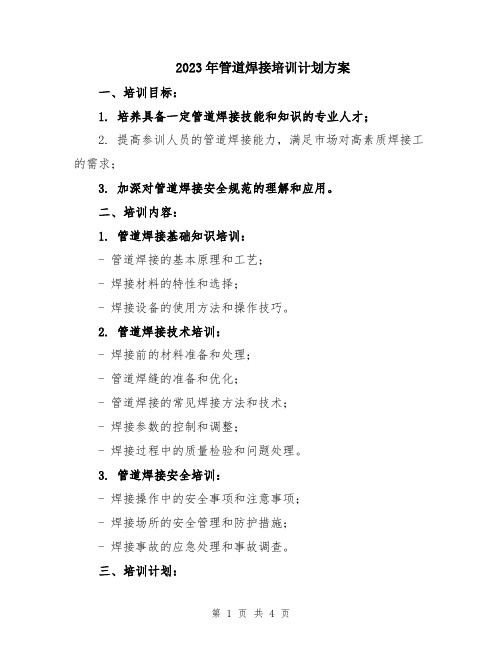
2023年管道焊接培训计划方案一、培训目标:1. 培养具备一定管道焊接技能和知识的专业人才;2. 提高参训人员的管道焊接能力,满足市场对高素质焊接工的需求;3. 加深对管道焊接安全规范的理解和应用。
二、培训内容:1. 管道焊接基础知识培训:- 管道焊接的基本原理和工艺;- 焊接材料的特性和选择;- 焊接设备的使用方法和操作技巧。
2. 管道焊接技术培训:- 焊接前的材料准备和处理;- 管道焊缝的准备和优化;- 管道焊接的常见焊接方法和技术;- 焊接参数的控制和调整;- 焊接过程中的质量检验和问题处理。
3. 管道焊接安全培训:- 焊接操作中的安全事项和注意事项;- 焊接场所的安全管理和防护措施;- 焊接事故的应急处理和事故调查。
三、培训计划:1. 培训对象:主要针对从事或有意从事管道焊接工作的人员,包括初级、中级和高级焊工。
2. 培训方式:理论学习结合实际操作,采取课堂教学和实训相结合的方式进行培训。
3. 培训周期:全程培训周期为2个月,其中课堂教学为1个月,实训为1个月。
4. 培训安排:- 第一阶段:理论学习(1个月)- 第1周:管道焊接基础知识培训;- 第2-3周:管道焊接技术培训;- 第4周:管道焊接安全培训。
- 第二阶段:实训操作(1个月)- 第1-2周:实训基地安全培训和实操训练;- 第3-4周:实训基地实际工作模拟训练;- 第5-6周:实训基地实际工作任务分配和完成;- 第7-8周:实训基地实际工作反馈和总结。
5. 培训评估:- 参训人员按照培训计划完成学习和实训任务;- 定期组织理论考试和实操测试,评估参训人员的学习效果;- 根据考试和测试结果进行综合评估,对合格者颁发培训合格证书。
四、培训师资:1. 管道焊接专家:负责理论知识的讲解和技术指导;2. 业界专业人士:负责实训操作的指导和实践经验分享。
五、培训设施和资源:1. 实训基地:配置合适的焊接设备和实际工作场景,提供实际工作模拟和实操训练;2. 理论教室:配备多媒体教学设备,提供理论知识的讲解和学习。
直缝高频电阻焊钢管焊接工艺
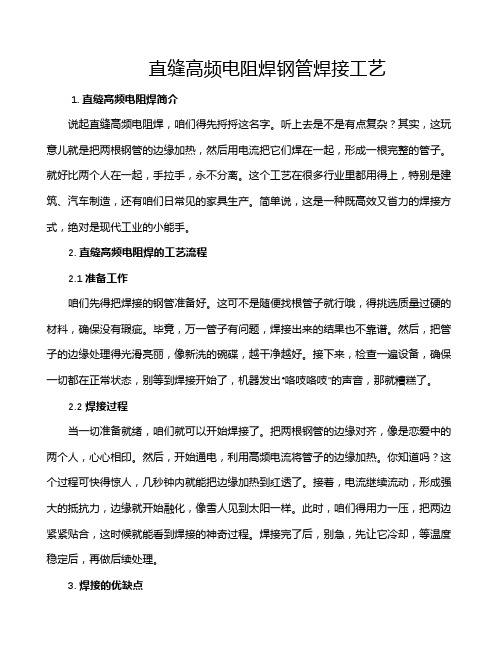
直缝高频电阻焊钢管焊接工艺1. 直缝高频电阻焊简介说起直缝高频电阻焊,咱们得先捋捋这名字。
听上去是不是有点复杂?其实,这玩意儿就是把两根钢管的边缘加热,然后用电流把它们焊在一起,形成一根完整的管子。
就好比两个人在一起,手拉手,永不分离。
这个工艺在很多行业里都用得上,特别是建筑、汽车制造,还有咱们日常见的家具生产。
简单说,这是一种既高效又省力的焊接方式,绝对是现代工业的小能手。
2. 直缝高频电阻焊的工艺流程2.1 准备工作咱们先得把焊接的钢管准备好。
这可不是随便找根管子就行哦,得挑选质量过硬的材料,确保没有瑕疵。
毕竟,万一管子有问题,焊接出来的结果也不靠谱。
然后,把管子的边缘处理得光滑亮丽,像新洗的碗碟,越干净越好。
接下来,检查一遍设备,确保一切都在正常状态,别等到焊接开始了,机器发出“咯吱咯吱”的声音,那就糟糕了。
2.2 焊接过程当一切准备就绪,咱们就可以开始焊接了。
把两根钢管的边缘对齐,像是恋爱中的两个人,心心相印。
然后,开始通电,利用高频电流将管子的边缘加热。
你知道吗?这个过程可快得惊人,几秒钟内就能把边缘加热到红透了。
接着,电流继续流动,形成强大的抵抗力,边缘就开始融化,像雪人见到太阳一样。
此时,咱们得用力一压,把两边紧紧贴合,这时候就能看到焊接的神奇过程。
焊接完了后,别急,先让它冷却,等温度稳定后,再做后续处理。
3. 焊接的优缺点3.1 优点说到优点,直缝高频电阻焊可谓是“脱颖而出”。
首先,焊接速度快,效率高,几乎是“一马当先”,省时省力。
其次,焊接的接头强度高,绝对不是“纸糊的”!这种焊接方式还节能环保,减少了焊接过程中的废气和焊渣,简直是对环境的小爱心。
此外,设备操作相对简单,新手上手也不难,真是老少皆宜,人人可学。
3.2 缺点当然,没有十全十美的事儿。
直缝高频电阻焊也有一些小缺点。
比如,对于厚度较大的钢管,焊接效果就不那么理想,可能需要其他方法补救。
而且,这种焊接对设备的要求比较高,如果设备维护不好,焊接质量也会大打折扣。
焊管岗位培训计划

焊管岗位培训计划一、培训目标1.1、确保培训对象能够掌握焊管技术的基本知识和操作技能,有能力独立完成焊管工作。
1.2、帮助培训对象了解焊管操作的安全规范和注意事项,提高对工作环境的安全意识。
1.3、培养培训对象对焊管工作的责任心和团队合作意识,提高整体工作效率。
1.4、通过培训,提高公司的员工素质和技术水平,为公司的发展和项目实施提供有力的保障。
1.5、培训结束后,培训对象应能够根据工程要求熟练进行焊管工作,提供高质量的服务。
二、培训内容2.1、焊管技术基础知识- 焊接原理- 焊接工艺- 焊接设备及工具的使用- 焊接材料及其性能- 焊接质量控制2.2、焊管操作技能- 焊管前期准备- 焊接设备的使用和维护- 焊接班组协作- 焊接虚焊和修补- 焊接质量检测2.3、焊管安全管理- 焊接现场安全规范- 焊接操作的安全注意事项- 焊接相关设备的安全使用- 焊接事故的应急处理2.4、焊管质量管理- 焊管质量控制要点- 焊管质量检测方法- 焊管质量不良原因分析- 焊管质量改进措施2.5、焊管工程实例分析- 焊接工程案例讲解- 焊接工程中的问题解决- 焊接工程实践操作三、培训方法3.1、理论讲授- 采用专业教材和资料,配合图文并茂的教学内容,进行系统的理论课程讲解,帮助培训对象掌握焊管技术的基本知识。
3.2、操作演示- 培训对象进行焊管设备的操作演示,由专业的操作人员现场演示操作步骤和注意事项,培训对象可在安全的指导下进行反复练习。
3.3、现场实践- 安排培训对象到真实的工程现场进行实践操作,直接参与焊管工程项目,了解实际工程操作需求和技术要求。
3.4、讨论交流- 安排培训对象进行技术交流和讨论,分享焊管工作中的实际操作经验和技术心得,互相学习和帮助提高工作水平。
3.5、学员考核- 定期进行培训学员的考核测试,评估学员的掌握程度和技术水平,为学员提供成长反馈和技能提升指导。
四、培训时间安排4.1、培训时间:预计为期一个月(30天)4.2、培训内容及时间安排:- 第一周:理论讲授、基础知识学习- 第二周:操作演示、实践操作练习- 第三周:安全管理、质量控制学习- 第四周:实践操作、工程案例分析- 最后一周:集中复习、学员考核五、培训师资力量5.1、培训师资:专业焊管工程师、焊接技术专家5.2、培训师资力量丰富,具有丰富的焊管工程实践经验和丰富的教学经验,能够为学员提供专业的知识传授和实践指导。
直缝钢管高频焊接工艺

直缝钢管高频焊接工艺1、焊缝间隙的控制将带钢送入焊管机组,经多道轧辊滚压,带钢逐渐卷起,形成有开口间隙的圆形管坯,调整挤压辊的压下量,使焊缝间隙控制在1~3mm,并使焊口两端齐平。
如间隙过大,则造成邻近效应减少,涡流热量不足,焊缝晶间接合不良而产生未熔合或开裂。
如间隙过小则造成邻近效应增大,焊接热量过大,造成焊缝烧损;或者焊缝经挤压、滚压后形成深坑,影响焊缝表面质量。
2、焊接温度控制焊接温度主要受高频涡流热功率的影响,根据公式(2)可知,高频涡流热功率主要受电流频率的影响,涡流热功率与电流激励频率的平方成正比;而电流激励频率又受激励电压、电流和电容、电感的影响。
激励频率公式为:f=1/[2π(CL)1/2] (1)式中:f-激励频率(Hz);C-激励回路中的电容(F),电容=电量/电压;L-激励回路中的电感,电感=磁通量/电流上式可知,激励频率与激励回路中的电容、电感平方根成反比、或者与电压、电流的平方根成正比,只要改变回路中的电容、电感或电压、电流即可改变激励频率的大小,从而达到控制焊接温度的目的。
对于低碳钢,焊接温度控制在1250~1460℃,可满足管壁厚3~5mm焊透要求。
另外,焊接温度亦可通过调节焊接速度来实现。
当输入热量不足时,被加热的焊缝边缘达不到焊接温度,金属组织仍然保持固态,形成未熔合或未焊透;当输入热时不足时,被加热的焊缝边缘超过焊接温度,产生过烧或熔滴,使焊缝形成熔洞。
3、挤压力的控制管坯的两个边缘加热到焊接温度后,在挤压辊的挤压下,形成共同的金属晶粒互相渗透、结晶,最终形成牢固的焊缝。
若挤压力过小,形成共同晶体的数量就小,焊缝金属强度下降,受力后会产生开裂;如果挤压力过大,将会使熔融状态的金属被挤出焊缝,不但降低了焊缝强度,而且会产生大量的内外毛刺,甚至造成焊接搭缝等缺陷。
3.1 高频感应圈位置的调控高频感应圈应尽量接近挤压辊位置。
若感应圈距挤压辊较远时,有效加热时间较长,热影响区较宽,焊缝强度下降;反之,焊缝边缘加热不足,挤压后成型不良。
高频直缝焊接钢管PPT课件

第1页/共5页
高频直缝焊接钢管
高频焊又叫高频感应加热,高频焊是利用 10~500KHz高频电流流经金属连接面产生
电阻 热并施加(或不施加)压力达到金属结合
的 一种焊接方法。其特点是:焊接速度大,焊接
热 影响区小,焊接对工件可以不清理,可焊薄壁
第2页/共5页
高频直缝焊接钢管
生产工艺流程主要取决于产品品种,从原料到成品 需要经过一系列工序,完成这些工艺过程需要相应 的各种机械设备和焊接、电气控制、检测装置,这 些设备和装置按照不同的工艺流程要求有多种合理 布置,高频焊管典型流程:纵剪―开卷―带钢矫平― 头尾剪切―带钢对焊―活套储料―成型―焊接―清 除毛刺―定径―探伤―飞切―初检―钢管矫直―管 段加工―水压试验―探伤页/共5页
感谢您的观看!
第5页/共5页
- 1、下载文档前请自行甄别文档内容的完整性,平台不提供额外的编辑、内容补充、找答案等附加服务。
- 2、"仅部分预览"的文档,不可在线预览部分如存在完整性等问题,可反馈申请退款(可完整预览的文档不适用该条件!)。
- 3、如文档侵犯您的权益,请联系客服反馈,我们会尽快为您处理(人工客服工作时间:9:00-18:30)。
一、高频焊接发展历史
因此,随后在电阻焊管生产中使用120-360赫的较高频率。与此同时还出现了用直流 电阻焊,感应焊和电弧焊来生产焊接钢管,但这些焊接方法的焊速都很低。 频率为60-360赫的低频电阻焊在这一时期得了最广泛的应用,在这个时期,全世界 差不多80%的焊接钢管都是采用这种方法生产的,因为这种方法最简单,焊接质量也 有显著提高,不仅可以生产一般的输送管和结构管,而且可以生产要求比较高的锅 炉管,直径从114-500毫米,壁厚从4.75到14.3毫米的石油管也可以采用这种方法进 行生产,所用的焊机容量达4400千伏安,焊速可达60米/分,交流最阴对材料的化学 和物理生能限制较少,但对带钢表面,特别是同焊接电极接触的带钢边缘部分要求 较严,不允许有氧化铁皮和铁锈,油污等。因此,低频电阻焊一般都需要用酸洗或 喷砂的方法对带钢进行处理。这种焊接方法直到今天仍在应用。 由于直流电阻焊的供电设备费用太大,应用范围受到限制,它只能用于碳素钢的焊 接,特别是适用焊接质量要求高,焊接毛刺小,表面光滑的焊管生产。例如小直径 的冷却器管用直流电阻焊生产,不需要清除内毛刺,其外表面可以同冷拔管相比, 直径大于76或102毫米,壁厚大于4毫米的钢管生产一般不采用这种方法,因为直径 较大的钢管内毛刺的清除比较容易,同时对表面质量的要求也不像对小直径管那样 高,因而可以采用交流电阻焊接。
二、高频焊管生产操作技术
4. 开口角是指挤压辊前管坯两边缘的夹角,开口角的大小与烧化过程的稳定性有关,对焊
பைடு நூலகம்
减小开口角时,边缘之间的距离也减小,从而使邻近效应加强,在其它条件相同的情况 下便可增大边缘的加热温度,从而提高焊接速度。开口角如果过小时,将使会合点到挤 压辊中心线的距离加长,从而导致边缘并非在最高温度下受到挤压,这样便使焊接质量 降低,
二、高频焊管生产操作技术
1 因为焊接工艺的主要参数之一,即焊接电流(或焊接温度)难 以测量,所以用输入热量来代替,而输入热量又可用振荡器输出功率来表示: N = Ep· Ip 式中 N——输出功率,kW; Ep——屏压,kV; Ip——屏流,A〔1 。 当振荡器、感应器和阻抗器确定后,振荡管槽路、输出变压器、感应器的效率 也就确定了,输入功率的变化同输入热量的变化大致是成比例的。 当输入热量 不足时,被加热边缘达不到焊接温度,仍保持固态组织而焊不上,形成焊合裂缝;当输 入热量大时,被加热边缘超过焊接温度易产生过热,甚至过烧,受力后产生开裂;当输 入热量过大时,焊接温度过高,使焊缝击穿,造成熔化金属飞溅,形成孔洞。熔化焊接 温度一般在1350~1400℃为宜。
高频焊管工艺培训
目录 一、高频焊接发展历史 二、高频焊管生产操作技术
三、焊管调整技术
四、高频焊管常见焊接缺陷分析
五、焊管的后道加工工艺
一、高频焊接发展历史
钢管的生产和使用距今大约有一百多年的历史。十九世纪初期,由于战争的需要,人们 用钢板弯成管筒,然后在其搭接的边缘上加热,并在短心棒上锻接成管子,用以制造炮 筒,随后,这种方法得了较大的发展,1825年左右出现了炉焊钢管法,这种方法是将 金属带加热到焊接温度以后,从碗模中拉出,从此,焊管才开始了工业规模的生产。 1843年以后,无缝管的生产有了很大的发展,到1896年,各种生产无缝管的技术和设 备相继出现,使无缝管的生产从基础理论,生产工艺到各种辅助设备都建立了一套比较 完整的体系。
二、高频焊管生产操作技术
3 焊接速度也是焊接工艺主要参数之一,它与加热制度、焊缝变形速度以及相互结晶速 度有关。在高频焊管时,焊接质量随焊接速度的加快而提高。这是因为加热时间的缩 短使边缘加热区宽度变窄,缩短了形成金属氧化物的时间,如果焊接速度降低时,不仅 加热区变宽,而且熔化区宽度随输入热量的变化而变化,形成内毛刺较大。在低速焊时 ,输入热量少使焊接困难, 因此在高频焊管时,应 在机组的机械设备和焊接装置所允许的最大速度下,根据不同规格品种选择合适的焊 速。
与此同时,由于焊接和成型的技术不良,焊接钢管的质量不好,加之作为焊管原料的带 钢和钢板产量供不应求,焊管生产的发展远远落后于无缝管的生产,焊管产量只占整个 钢管产量的很小部分。
二十世纪初,利用霍耳效应的电阻焊接技术开始用于焊管生产,约斯特等对于电阻焊的 焊接温度,焊接压力,焊接速度及其相互关系,以及对焊缝金相组织和机械性能的影响 等,均作了认真的研究,同时,对于其他成型和焊接工艺问题也进行了一系列的研究, 从而使焊管的质量有了明显的提高。到了三十年代,电焊管生产获得了普遍的发展,在 这个期间,焊管的成型技术也有了很大的改进,出现了连续式直缝焊管成型机,并得了 逐步改进与完善。 1938 年,卡尔。荷尔泽设计的接触电阻焊管机(如下图)已具有现代电焊管机的规模 ,它具有六架成型机架,一套带导向辊的焊接装置,其中包括挤压辊和毛刺清理装置, 随后是三架定径机和飞剪。
一、高频焊接发展历史
第二次世界大战后,接触电焊管生产得到了迅速的发展,特别是在美国, 首先开始了电焊管机的系列设计,美国最初的系列是以M为代号的四个规 格。分别如下:
一、高频焊接发展历史
该系列的设备外形如图所示
M系列焊管机采用旋转焊接变压器,其输出功率为125 300 和500千伏安,电流频 率为50~60赫兹,后来提高到150-180赫,旋转焊接变压器的结构如下图1-8所示 ,其工作原理如图1-9所示,当强度为I的电流沿电阻为R欧姆的导体流动时,t秒 后在导体中所产生的热量为Q=0.24I² RT卡。在焊接过程中,管坯开缝处的电阻大 于电流流过管坯圆周的电阻,因此,在开缝处的带钢边缘便会产生很大的热量, 这一热量可以将带钢边缘加热到焊接温度。电流通过旋转焊接变压器,通过被绝 缘体2隔开的环形电极1 送到管坏的边缘,将边缘加热,随后在掠夺辊的压力作用 下,加热到焊管温度的管坯边缘被焊接在一起
二、高频焊管生产操作技术
2 焊接压力是焊接工艺的主要参数之一,管坯的两边缘加热到焊接温度后,在挤压力 作用下形成共同的金属晶粒即相互结晶而产生焊接。焊接压力的大小影响着焊缝 的强度和韧性。若所施加的焊接压力小,使金属焊接边缘不能充分压合,焊缝中残 留的非金属夹杂物因压力小不易排出,焊缝强度降低,受力后易开裂;压力过大时,达 到焊接温度的金属大部分被挤出,不但降低焊缝强度,而且产生内外毛刺过大或 搭 焊等缺陷。因此应根据不同的品种规格在实际中求得与之相适应的最佳焊接压力 。根据实践经验单位焊接压力一般为20~40MPa 由于管坯宽度及厚度可能 存在的公差,以及焊接温度和焊接速度的波动,都有可能涉及到焊接挤压力的变化 。焊接挤压量一般通过调整挤压辊之间的距离进行控制,也可以用挤压辊前后管 筒周差来控制。
一、高频焊接发展历史
1950年后,生产发生了一系列变化,特别是1953年,频率达450千赫的高频接触电阻 焊开始用于焊管生产,但初期发展缓慢,直到1960年,世界各国采用高频焊的焊管机 组尚为数不多,1960年以后,高频接触电阻焊管生产获得了极为迅速的发展,高频焊 管机组在各国大量的建设起来,随后,借助于环形感应器传递能量的高频感应也开始 用于焊管生产。当高频接触取得了公认的良好效果以后,高频感应焊的应用仍然是极 其有限的,在高频焊管生产中,只起到次要的作用。 高频焊接具有一系列的优点:焊缝热影响小,加热速度快,在百分之一时间内就可以 使金属加热到焊接温度,(1130-1350℃)因而可以大大提高焊接速度和质量,可以 焊接不经酸洗或喷丸处理的带钢,同时,不便可以焊接碳素钢,而且可以焊接不锈钢 ,铝合金,铜合金等多种材料,此外,高频钢管的能量消耗低,效率高,由于高频焊 所具有的这些优点,因而在70年代,不但新建的中小直径电焊管机组普遍采用这种焊 接的方法,而且各国对原有的低频焊管机组也改造为高频,使机组的生产能力和产品 质量有了明显的提高,产品的规格和使用范围也在不断扩大。 1960年以后,中小直径电焊管的成型技术,质量控制与检验技术,精整设备等各方 面都有许多重大的改进和革新, 高频直缝焊管在近二十年来获得了巨大的发展的主要原因是: 1 成本低廉,建厂投资少 2 焊缝质量的显著提高 3 非破坏性检验技术的广泛使用 4 品种和规格范围的扩大。 此外,焊接钢管的发展是以板带钢材生产的发展相适应,钢板卷的大量供应是焊管发 展的前提。
一、高频焊接发展历史
焊缝内各焊点之间的距离,与焊接速度成正比,而与电流的频率成反比, 各个焊点之间的距离越小,则焊缝的气密性越好,焊缝质量越高,在相同 的焊接速度情况下,提高电流频率有利用焊缝质量,同理,当电流为50赫 时,焊接速度可达30-32米/分,此时相应的各个焊点之间的距离分为为5 和5.33毫米,在此基础上,如果进一步提高焊接速度,将使焊缝质量大大 变坏,不能满足实际需求。
二、高频焊管生产操作技术
6. 管坯的几何尺寸及形状要求 6.1焊管坯的几何尺寸 管坯的宽度和厚度偏差大,会改变边缘的加热温度和挤压量 ,合格的产品必须要求管 坯的宽度和厚度在公差范围之内。 6.2管坯形状及相接形式 如果管坯边缘存在挠曲、镰刀弯及波皱等现象, 通过成型机时就会偏离孔型中心, 造成带钢两边弯曲。轧辊调整不良也会造成带钢跑偏或管坯扭曲等缺陷,造成影响 焊接质量或根本无法焊接的后果。 管坯两端焊接时要求两端全部厚度相接, 管坯两边缘不但要平直而且要平行。 纵剪 带钢时圆盘剪刃间隙过大或刀刃磨损严重造成带钢边缘毛刺过大,也易产生焊接后 裂纹。 焊管坯上有缩孔、干裂、夹层、非金属夹杂物和偏析、气泡等内部缺陷, 将对焊管 的质量和使用带来严重后果。如果发现焊管坯有划伤、结疤、压痕、表面裂纹、 破边等外部缺陷,应及时处理, 以免影响产品质量及成材。 在生产中要保持焊管表面光洁度,轧辊表面光洁度Ra 必须达到0.32,并检查成对辊是 否受到均匀磨损, 否则产品的规格和表面质量均会受到影响。 综上所述,高频焊管生产操作,其管坯质量、操作水平等对焊管的焊接质量影响 较大。 关于产品的规格尺寸(直径壁厚公差)和形状,根据不同品种都制定有规范 标准, 厂家必须遵循国家标准及客户要求组织生产。
一、高频焊接发展历史
由于交流电电流强度的周期性变化,因而沿焊缝长度不可能得到均匀的加热,当电流 强度到达最大值时,焊缝上各相应点即被加热到温度或者高于焊接温度,而当电流为 零值时,焊缝上相应各点则加热不足或者达不到焊接温度,因而沿焊缝长度将另一面 焊接与未焊接,或者通过烧与焊接部分相互交替分布的情况,即形成所谓的周期性分 布焊点,