浅论炼油厂气脱硫化氢工艺
石油化工脱硫方法
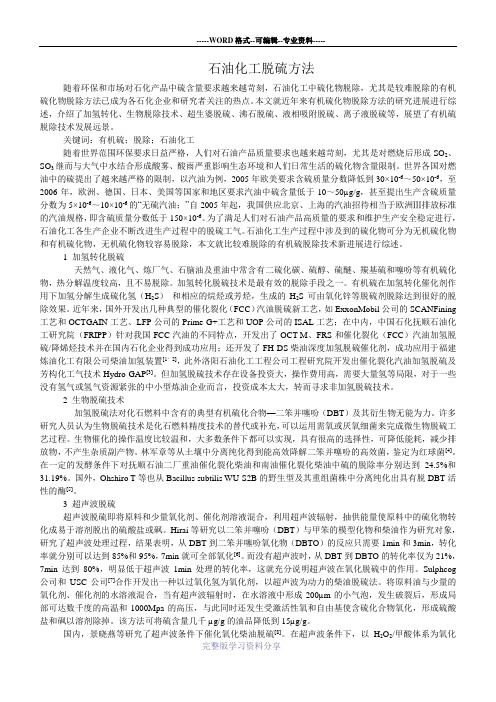
石油化工脱硫方法随着环保和市场对石化产品中硫含量要求越来越苛刻,石油化工中硫化物脱除,尤其是较难脱除的有机硫化物脱除方法已成为各石化企业和研究者关注的热点。
本文就近年来有机硫化物脱除方法的研究进展进行综述,介绍了加氢转化、生物脱除技术、超生婆脱硫、沸石脱硫、液相吸附脱硫、离子液脱硫等,展望了有机硫脱除技术发展远景。
关键词:有机硫;脱除;石油化工随着世界范围环保要求日益严格,人们对石油产品质量要求也越来越苛刻,尤其是对燃烧后形成SO2、SO3继而与大气中水结合形成酸雾、酸雨严重影响生态环境和人们日常生活的硫化物含量限制。
世界各国对燃油中的硫提出了越来越严格的限制,以汽油为例,2005年欧美要求含硫质量分数降低到30×10-6~50×10-6,至2006年,欧洲、德国、日本、美国等国家和地区要求汽油中硫含量低于10~50µg/g,甚至提出生产含硫质量分数为5×10-6~10×10-6的“无硫汽油;”自2005年起,我国供应北京、上海的汽油招待相当于欧洲Ⅲ排放标准的汽油规格,即含硫质量分数低于150×10-6。
为了满足人们对石油产品高质量的要求和维护生产安全稳定进行,石油化工各生产企业不断改进生产过程中的脱硫工气。
石油化工生产过程中涉及到的硫化物可分为无机硫化物和有机硫化物,无机硫化物较容易脱除,本文就比较难脱除的有机硫脱除技术新进展进行综述。
1 加氢转化脱硫天然气、液化气、炼厂气、石脑油及重油中常含有二硫化碳、硫醇、硫醚、羰基硫和噻吩等有机硫化物,热分解温度较高,且不易脱除。
加氢转化脱硫技术是最有效的脱除手段之一。
有机硫在加氢转化催化剂作用下加氢分解生成硫化氢(H2S)和相应的烷烃或芳烃,生成的H2S可由氧化锌等脱硫剂脱除达到很好的脱除效果。
近年来,国外开发出几种典型的催化裂化(FCC)汽油脱硫新工艺,如ExxonMobil公司的SCANFining 工艺和OCTGAIN工艺、LFP公司的Prime-G+工艺和UOP公司的ISAL工艺;在中内,中国石化抚顺石油化工研究院(FRIPP)针对我国FCC汽油的不同特点,开发出了OCT-M、FRS和催化裂化(FCC)汽油加氢脱硫/降烯烃技术并在国内石化企业得到成功应用;还开发了FH-DS柴油深度加氢脱硫催化剂,成功应用于福建炼油化工有限公司柴油加氢装置[1,2],此外洛阳石油化工工程公司工程研究院开发出催化裂化汽油加氢脱硫及芳构化工气技术Hydro-GAP[3]。
炼油化工中气体脱硫技术探分析

炼油化工中气体脱硫技术探分析目前,由于我国经济在飞速发展,炼油化工厂也在加快发展。
炼油化工生产过程中,气体脱硫技术的不断完善和发展,促进炼油化工企业的进步。
对气体脱硫技术措施进行优化,使其达到更高的标准,满足炼油化工企业生产的需要。
有必要研究炼油化工中气体脱硫的技术措施,达到环境保护的效果,而且有效地防止设备的腐蚀,提高炼油化工生产的经济效益。
标签:炼油化工;气体;脱硫技术引言工业生产是产生空气污染的主要原因,特别是炼油化工生产中的含硫气体对空气和环境有严重的污染,甚至会危害人们的身体健康,因此要解决炼油化工的含硫气体污染问题。
在炼油化工生产中采用气体脱硫技术可以有效地去除炼油化工中的硫化氢,起到保护环境和提高炼油化工经济效益的目的。
1目前脱硫技术概述炼油过程中的脱硫技术一直是国内炼油厂家和相关研究院所的研究重点,随着国内国际对于汽油、柴油的技术指标的提高,对汽油等油品种的脱硫技术研究比较主要有以下几个方面:(一)FCC汽油加氢脱硫技术采用传统的进行脱硫转化时,轻烃汽油馏分经常容易被饱和,导致石油中的烯烃很容易被饱和,导致汽油中的辛烷降低。
Mobil公司的OCTGAIN技术,能控制其中的硫含量的同时,还能够控制辛烷值。
(二)溶剂萃取脱硫技术该技术是利用萃取溶剂,通常用甘醇类和砜类溶剂作萃取剂,通过萃取,将硫化物转化到高沸点溶剂中,再经过蒸馏的方式将汽油分离,最后将萃取溶剂与硫化物分离,抽提出来的硫化物,主要是苯并噻吩和甲基苯并噻吩,这些硫化物可以作为化工产品的原料或中间产物使用,从而减少了环境污染。
(三)催化裂化脱硫技术Grace公司提出的直接减少催化裂化汽油硫含量的新催化技术,称为GSR技术。
目前应用的技术,是在第一代技术的基础上添加了含有锐钛矿型结构的TiO2组元而制得,主要组分为TiO2/Al2O3。
该技术的应用,可使汽油馏分中的硫含量降低20%~30%。
2炼油化工中气体脱硫技术措施2.1化学脱硫剂脱硫工艺技术措施的应用结合炼油化工生产的实际情况,选择最佳的化学脱硫剂,应用脱硫塔设备,结合再生塔,对脱硫剂进行再生利用,降低脱硫工艺的成本,满足炼油化工生产节能降耗的技术要求。
塔中油田汽提法原油脱硫化氢工艺技术

与 石 油 ,2010,28(6):38-41. [2] 田 静,刘 棋,苏广全,等. 火灾泄压防空时限流孔板的实
验 论 证 [J],天 然 气 与 石 油 ,2010,28(4):26-28. [3] GB 50160-2008,石油化工企业设计防火规范[S]. [4] SH/T 3092-1999,石油化工分散控制系统设计规范[S].
表1 汽提脱硫装置运行参数对照表
设计规模/ 设计温度 / 运行温度 / 设计压力 / 运行压力 /
(t·d- 1)
℃
℃
MPa
MPa
960~1 200 50~60 50~55 0.15~0.25 0.25
3 运行经验
汽提脱硫装置投产后,不断对运行温度、进液量 和汽提比等参数进行优化调整,逐步摸索出了一套行 之有效的运行管理模式。 3.1 温度
析[J]. 石油规划设计,2008,19(6):35-36.
!!!!!!!!!!!!!!!!!!!!!!!!!!!!!!!!!!!!!!!!!!!!!!!
(上接第 20 页) 器的氮气线阀门处全部增设了 8 字盲板。 国内引进装 置, 如镇海炼化引进荷兰 2 套 7×104 t/a 硫磺装置,进 容器的氮气线均设有 8 字盲板。8 字盲板非常直观,易 于分辨,判断准确,能够有效避免氮气中毒事故发生。
蚀,消除外输原油和天然气 H2S 浓度严重超标带来的安全隐患,中国石油塔里木油田公司借鉴国内 首套重质原油干法汽提脱硫装置在塔河油田三号联合站试验成功并且安全平稳运行的经验, 在塔 中作业区水平一转油站建成了日处理能力 1 000 t 的汽提法原油脱硫装置,对塔中一号气田试采单 井原油进行脱硫处理,通过对温度、进液量及汽提比等参数进行不断优化将装置调整到最佳运行状 态,采用 3018 固体脱硫剂对汽提脱硫装置中产生的高含 H2S 尾气进行全部回收,有效地防止了大 气污染。 关键词:
炼厂气脱硫技术改进措施
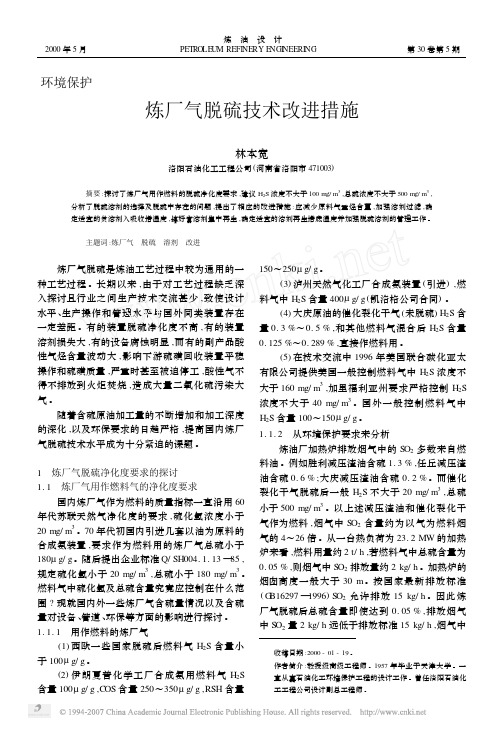
无硫的燃料烟气露点一般为 41~52 ℃。当用 含硫 1. 5 %的重油作燃料时其 烟 气 中 含 SO2 约 1 000μg/ g ,一般有 1 %~5 %的 SO2 转化为 SO3 ,即 烟气中 SO3 约 10~50 μg/ g ,烟气中 SO3 含量在 10 μg/ g 时露点约为 140 ℃,30μg/ g 时约为 160 ℃[2] , 可以推算 ,若炼厂气含硫 0. 05 % ,其烟气中 SO2 约 35μg/ g ,生成 SO3 约 2μg/ g ,相应的露点约 120 ℃。
收稿日期 :2000 - 01 - 19 。 作者简介 :教授级高级工程师 。1957 年毕业于天津大学 。一 直从事石油化工环境保护工程的设计工作 。曾任洛阳石油化 工工程公司设计副总工程师 。
— 44 —
炼 油 设 计 2000 年第 30 卷
SO2 约 100 mg/ m3 ,远低于排放浓度 960 mg/ m3 ,能 满足环境保护要求 。 1. 1. 3 从设备和管道腐蚀方面来分析
炼 油 设 计 2000 年 5 月 PETROLEUM REFINERY ENGINEERING 第 30 卷第 5 期
环境保护
炼厂气脱硫技术改进措施
海上油田天然气脱硫化氢工艺方法选择

第46卷 第1期 2019年1月天 津 科 技TIANJIN SCIENCE & TECHNOLOGYV ol.46 No.1Jan. 2019收稿日期:2018-12-05基础研究海上油田天然气脱硫化氢工艺方法选择肖峰超(中海油能源发展装备技术有限公司 天津300452)摘 要:介绍了海上油田伴生气高含硫化氢的危害以及油田伴生气脱除硫化氢的工艺方法。
海上油田生产过程的伴生气中高含硫化氢时,需要将伴生气中的硫化氢浓度降低到安全临界浓度,从而保护海上平台生产设施以及相关人员的安全。
通过对比分析,得出脱除伴生气中不同浓度硫化氢方法的适用性,并结合渤海某油田的实际生产数据,推荐出相应的处理工艺方案。
关键词:硫化氢 不同浓度 脱除方法 处理工艺中图分类号:TE86 文献标志码:A 文章编号:1006-8945(2019)01-0028-02Selection of Natural Gas Desulfation Process in Bohai OilfieldXIAO Fengchao(CNOOC EnerTech Equipment Technology Co.,Ltd.,Tianjin 300452,China )Abstract :The paper mainly introduces the harmfulness of high content of hydrogen sulfide in associated gas in offshore oilfields and the methods of hydrogen sulfide removal from associated gas.It is necessary to reduce the concentration of hy-drogen sulfide in associated gas to a safe critical concentration ,so as to protect the safety of equipment and personnel. In-view of different concentrations of hydrogen sulfide ,the corresponding treatment process is recommended. Key words :hydrogen sulfide ;different concentrations ;removal method ;treatment process0 引 言近年来渤海油田逐渐发现了高含硫油田,高含硫油田中当硫以硫化氢形态存在时,对管网和装置的腐蚀均会产生较大影响。
石油炼制过程硫及氮资源化回收技术探析

石油炼制过程硫及氮资源化回收技术探析摘要:原油中硫、氧、氮、碳、氢形成的硫化物、氮化物、氧化物、胶质等非烃类化合物约占10~20%,对原油加工的安全、环境、产品质量等有很大影响。
本文分析了石油炼制过程硫及氮资源化回收技术。
关键词:石油炼制;硫;氮;资源化硫、高氮原油的加工带来了新的环保问题,需采取多种措施使其废气、污水排放达到《石油化工企业污染物排放标准》要求,或满足项目所在地污染物排放限值要求。
国家对环保提出了更严格的要求,提高了原油中硫、氮资源的回收率,减少硫氧化物等气体污染物及氨氮等液体污染物的排放,从而最大限度地回收原油中的硫、氮资源。
降低原油加工损耗率,也是节能减排和环保的客观要求。
一、炼化企业主要含硫及氮尾气处理技术1、硫化氢回收技术1)酸性水汽提。
其是以上游工艺装置的含硫污水为原料的集中处理装置,常用的工艺有单塔常压汽提工艺、单塔加压侧线抽氨工艺和双塔加压汽提工艺。
单塔常压汽提工艺产品为净化水及酸性气,单塔加压侧线抽氨工艺与双塔加压汽提工艺产品为净化水、酸性气、液氨。
2)溶剂再生。
它采用上游生产装置脱硫单元(包括循环氢、加氢低分气、干气、液化石油气等脱硫单元)产生的脱硫富胺液为原料,脱硫富胺液采用集中再生处理,主要产品为贫胺液,副产高浓度HS酸性气。
通常采用常规蒸汽加热再2生工艺。
2、二氧化硫回收技术1)可再生湿法烟气脱硫。
该技术可脱除烟气中的二氧化硫,回收高浓度二氧化硫,可直接用于生产液体二氧化硫或硫酸,也可与硫磺回收装置联合生产工业硫磺。
介绍了自主研发的Rasoc工艺等多种可再生湿法烟气脱硫技术,Rasoc工艺是一种资源化(回收)烟气脱硫技术,采用高选择性的专用LAS吸收剂从烟气中回收高浓度SO2酸性气,富吸收剂再生后循环利用,可在多套烟气脱硫装置中实现富吸收剂的集中再生,适用于高质量浓度二氧化硫(大于3000mg/m3)的烟气净化。
2)活性焦干法烟气脱硫。
活性焦烟气处理技术是一种资源(回收)烟气脱硫技术,利用活性焦的吸附催化作用脱除烟气中的SOx、NOx、烟尘,回收利用硫资源。
海上油田天然气脱硫化氢工艺方法选择
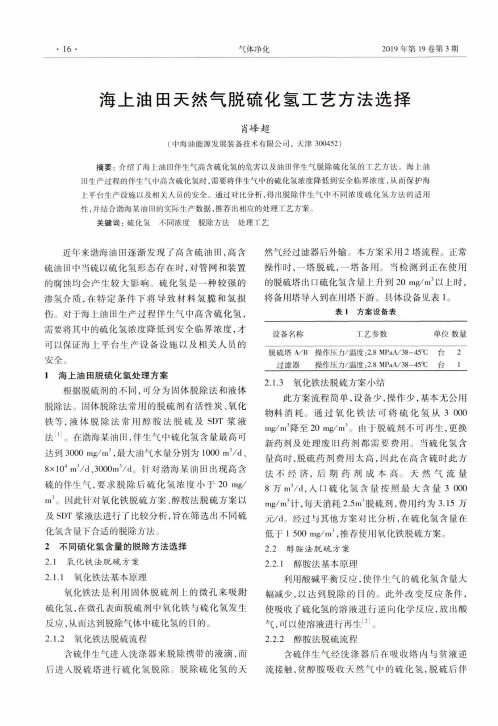
•16•气体净化2019年第19卷第3期海上油田天然气脱硫化氢工艺方法选择肖峰超(中海油能源发展装备技术有限公司,天津300452)摘要:介绍了海上油田伴生气高含硫化氢的危害以及油田伴生气脱除硫化氢的工艺方法。
海上油田生产过程的伴生气中高含硫化氢时,需要将伴生气中的硫化氢浓度降低到安全临界浓度,从而保护海上平台生产设施以及相关人员的安全。
通过对比分析,得出脱除伴生气中不同浓度硫化氢方法的适用性,并结合渤海某油田的实际生产数据,推荐出相应的处理工艺方案。
关键词:硫化氢不同浓度脱除方法处理工艺近年来渤海油田逐渐发现了高含硫油田,高含硫油田中当硫以硫化氢形态存在时,对管网和装置的腐蚀均会产生较大影响。
硫化氢是一种较强的渗氢介质,在特定条件下将导致材料氢脆和氢损伤。
对于海上油田生产过程伴生气中高含硫化氢,需要将其中的硫化氢浓度降低到安全临界浓度,才可以保证海上平台生产设备设施以及相关人员的安全。
1海上油田脱硫化氢处理方案根据脱硫剂的不同,可分为固体脱除法和液体脱除法。
固体脱除法常用的脱硫剂有活性炭、氧化铁等,液体脱除法常用醇胺法脱硫及SDT浆液法⑴。
在渤海某油田,伴生气中硫化氢含量最高可达到3000mg/m',最大油气水量分别为1000m'/d、8xl04mVdJOOOm'Vdo针对渤海某油田出现高含硫的伴生气,要求脱除后硫化氢浓度小于20mg/因此针对氧化铁脱硫方案、醇胺法脱硫方案以及SDT浆液法进行了比较分析,旨在筛选出不同硫化氢含量下合适的脱除方法。
2不同硫化氢含量的脱除方法选择2.1氧化铁法脱硫方案2.1.1氧化铁法基本原理氧化铁法是利用固体脱硫剂上的微孔来吸附硫化氢,在微孔表面脱硫剂中氧化铁与硫化氢发生反应,从而达到脱除气体中硫化氢的目的。
2.1.2氧化铁法脱硫流程含硫伴生气进入洗涤器来脱除携带的液滴,而后进入脱硫塔进行硫化氢脱除。
脱除硫化氢的天然气经过滤器后外输。
本方案采用2塔流程。
浅析液化石油天然气脱硫技术

浅析液化石油天然气脱硫技术作者:游海兵来源:《科技资讯》 2011年第30期游海兵(陕西延长石油(集团)公司油气勘探公司陕西延安 716000)摘要:近年来,我国的石油天然气等化工行业发展速度加快,液化石油天然气在化工生产应用的过程中必须要先进行脱硫处理,因此液化石油天然气脱硫技术的发展与改进正成为我国化工行业生产的关键。
未处理过的液化石油天然气中存在许多的杂质,这些杂质中除了含有H2S和CO2等酸性成分外,还包含硫醇等有机硫成分,这些硫成分会对石油天然气的提炼产品的加工和生产环境保护工作造成不利的影响。
液化石油天然气的脱硫以及对其所含的硫化物的检验成为液化石油天然气生产过程中的重要环节。
目前,国内外脱硫和硫化物检验方法正在不断的发展,对液化石油天然气进行脱硫的方法日益增多,本文将简单分析目前较常用的几种石油天然气脱硫方法。
关键词:石油天然气脱硫技术硫化物中图分类号:TE62 文献标识码:A 文章编号:1672-3791(2011)10(c)-0064-011 干法脱硫液化石油天然气的干法脱硫技术是目前在生产过程较为常用的脱硫方法之一,其主要的脱硫原理是利用特殊的固体吸附剂与液化气体中所包含的H2S、CO2等硫化物进行吸附并与之发生化学反应,以此完成脱硫。
较为常见的固体吸附剂有铁系、锌系、锰系氧化物较为活泼氧化物。
干法脱硫方法有许多优点,主要表现在液化石油天然气脱化后的气体硫含量较低;但是,干法脱硫还是存在一些缺陷,一般进行干法脱硫所需的设备一般较为庞大,而且所应用的脱硫剂不能再生或再次利用,只能直接废弃,在这就会降低生产环境质量并且增加脱硫技术的成本,因此这种干法脱硫技术目前主要应用于含硫成分较低的气体的精细脱硫生产环节中。
近年来,液化石油天然气干法脱硫技术由于其简单的操作工业和成熟的技术得到了广泛的应用,最为常用的脱硫剂就是氢氧化铁,也就是多种结晶形态的水和氧化铁。
但是,干法脱硫方法所采用的脱硫剂一般是非再生的,因此他的应用受到了一定的限制。
石化工程中的气体脱硫技术使用方法

石化工程中的气体脱硫技术使用方法随着环保意识的增强和对大气污染的关注度的加深,石化工程中的气体脱硫技术变得越来越重要。
气体脱硫是指通过一系列化学反应,将燃烧过程中产生的气体中的有害物质去除或转化为无害物质的过程。
本文将简要介绍石化工程中常用的气体脱硫技术使用方法,包括湿法脱硫技术、干法脱硫技术和生物脱硫技术。
1. 湿法脱硫技术湿法脱硫技术是目前最为成熟和广泛应用的气体脱硫方法之一。
该技术通过将含有硫化物的烟气与吸收剂接触,使硫化物与吸收剂反应生成易降解的硫酸盐或硫化钙等物质,从而达到脱硫的目的。
常用的吸收剂包括氧化钙、氢氧化钠和碱性碳酸盐等。
湿法脱硫技术的使用方法主要有两种。
第一种是常压湿法脱硫,烟气在常压下与吸收剂接触进行脱硫反应。
这种方法简单易行,并且适用于大规模工况,但脱硫效率相对较低。
第二种是加压湿法脱硫,烟气在高压下与吸收剂接触进行脱硫反应。
该方法具有较高的脱硫效率,适用于高硫燃烧气体的处理,但设备复杂,运行成本较高。
2. 干法脱硫技术干法脱硫技术是另一种常用的气体脱硫方法。
该技术主要通过将吸收剂直接添加到燃烧过程中,使吸收剂与煤粉或烟气中的硫化物发生反应生成易降解的化合物,达到脱硫的目的。
常用的吸收剂包括石灰石、活性炭和硅酸盐等。
干法脱硫技术的使用方法主要有两种。
第一种是喷射干法脱硫,吸收剂与煤粉混合后喷射到燃烧区域,与硫化物反应进行脱硫。
该方法适用于小型和中型燃烧设备,具有简单、经济的特点,但脱硫效率相对较低。
第二种是流化床干法脱硫,吸收剂在流化床中与硫化物进行反应,形成易降解的化合物。
该方法适用于大型燃烧设备,具有较高的脱硫效率,但设备复杂,投资成本较高。
3. 生物脱硫技术生物脱硫技术是一种环保友好型的气体脱硫方法。
该技术利用微生物的作用,将燃烧过程中产生的硫化物转化为无害的元素硫或硫酸盐等物质。
生物脱硫技术具有高效、节能、无二次污染等特点。
生物脱硫技术的使用方法主要包括硫氧化细菌和硫还原细菌两个环节。
炼油化工中气体脱硫技术

炼油化工中气体脱硫技术摘要:近几年我国石油行业迅速发展,在炼油化工中也有需要重点关注的问题。
在炼油的过程中会产生定量的硫化物,硫化物需要进行脱硫技术处理,不然其会对空气产生污染与破坏,另外硫化氢也会造成管道损坏,人们也会导致中毒。
近几年我国对节能环保要求更加严格,如何提高炼油化工中气体脱硫技术为其行业所面临的重点技术之一,本文主要对气体脱硫技术进行探究,为其行业的发展提供有效的措施,进而促使其行业的可持续性发展。
关键词:炼油化工;气体脱硫;技术应用气体脱硫技术主要是炼油化工过程中较为常见的技术工艺,但对炼油化工行业却极为重要。
在炼油化工的过程中如若其气体脱硫技术不高,脱硫效果达不到标准,会对以后的加工环节产生严重的影响,对环境也会造成污染,管道也会受到破坏腐蚀的问题。
炼油化工厂的硫含量不同,所运用的脱硫技术也不相同。
如若硫含量较低就可以运用简单的碱洗方法完成脱硫,如若硫含量较高,用碱洗的方式成本过大,就需要使用其他脱硫技术工艺,对此,气体脱硫技术为炼油化工厂中所面临的主要问题。
1 炼油化工生产概述炼油化工生产的主要工作就是对石油或者渣油进行炼制与生产,从而获得供各个行业使用的成品油,其可以成为炼油化工的主要生产概述。
在炼油化工生产过程中,一方面要保证炼油的质量,另一方面还要确保其炼油的效率,对此,炼油化工生产过程中的脱硫技术极为重要,能够直接影响炼油化工厂的经济效益。
气体脱硫技术会影响成品油的质量,脱硫技术的提高也能够保证炼油厂的进步与发展。
炼油的过程极为法扎,其主要是利用催化裂化技术完成蒸油,而蒸油过程中会产生大量的蒸汽,蒸汽中含有的硫和碳会对空气产生污染,也会对管道进行腐蚀,对此要将其进行脱硫处理,脱硫完成后也更能够提高成品油的纯度,炼油化工市场的需求更便于满足。
炼油化工生产的环境较为恶劣,其生产的过程要较为复杂,生产中多数为高温作业,例如在其生产中使用反应器或者加注催化剂等都是其生产的主要操作步骤,确保其操作质量与安全才能够满足炼油化工生产的需要。
加氢精制脱硫反应机理浅析

加氢精制脱硫反应机理浅析作者:谭新九来源:《中国化工贸易·下旬刊》2019年第11期摘要:燃料油中所含有的硫元素在燃烧使用过程中会产生二氧化硫、三氧化硫,氮元素在燃烧使用过程中会产生氮氧化合物,这些杂原子气体不仅会造成机械设备腐蚀,还是引起酸雨的重要因素。
本文分析了炼厂加氢精制装置燃料油加氢脱硫反应机理研究进展。
关键词:汽油;柴油;加氢脱硫;反应机理1 前言石油炼制加工是一个国家经济发展的重要支撑产业,其产出的各种燃料油和石油化工中间原料不仅是国家各种交通运输的重要保障,也为很多下游化工加工产业提供必须要的生产原料。
因此,我国在能源结构产业构建、升级、转型的发展阶段都非常重视炼厂加工能力、燃料油产品结构、燃料油产品质量、生态环境建设、资源利用率等方面的技术完善。
随着生态环境日益恶化,各个国家政府和国家相关组织都严格限定了燃料油中的硫、氮元素的含量。
因此,各大炼厂不得不加强汽油、柴油加氢精制装置反应深度,降低汽油、柴油产品中的硫、氮含量。
本文,以汽柴油加氢精制装置中的加氢脱硫为例,对加氢脱硫反应机理的各类研究进行梳理总结。
2 汽油柴油中含硫化合物類型柴油中的含硫化合物包括硫醇、硫醚、噻吩、烷基取代噻吩、苯并噻吩及其衍生物,其中收到柴油馏程限制,柴油中的苯并噻吩及其衍生物占到了总硫含量的75%以上,这也是柴油加氢脱硫技术重点脱除的组成。
赵志发等人使用气相色谱-质谱仪检测器分析了三种不同炼厂催化裂化柴油的硫化物种类及对应的含量。
催化裂化柴油中几乎不含有噻吩和饱和含硫化合物,主要以芳烃类噻吩化合物为主,占到了总硫质量分数的85%以上。
3 含硫化合物加氢脱硫机理虽然有研究人员研究表明,催化裂化反应和热裂化反应都可以一定程度上使得燃料油中的含硫化合物分解生成硫化氢进行脱除,但是总体上来说炼厂在降低汽柴油硫含量工艺上主要以加氢精制装置为主,脱硫反应遵循的加氢脱硫反应机理。
3.1 饱和类含硫化合物硫醇、二硫化物和硫醚属于比较容易脱除的化合物,其特点是硫以C-S方式存在,在加氢精制条件下,C-S直接裂化成饱和烃和硫化氢。
炼油厂采用的主流石油加工工艺——催化加氢工艺详解

3、反应空速
空速的大小反映了反应器的处理能力和反应时间。空速越大,装置的 处理能力越大,但原料与催化剂的接触时间则越短,相应的反应时间 也就越短。因此,空速的大小最终影响原料的转化率和反应的深度。
1、加氢处理催化剂 加氢处理催化剂中常用的加氢活性组分有铂、钯、镍等金属和钨、钼、 镍、钴的混合硫化物,它们对各类反应的活性顺序为: 加氢饱和 Pt,Pb﹥Ni﹥W-Ni﹥Mo-Ni﹥Mo-Co﹥W-Co 加氢脱硫 Mo-Co﹥Mo-Ni﹥W-Ni﹥W-Co 加氢脱氮 W-Ni﹥Mo-Ni﹥Mo-Co﹥W-Co 加氢活性主要取决于金属的种类、含量、化合物状态及在载体表面的 分散度等。 活性氧化铝是加氢处理催化剂常用的载体。
目前炼油厂采用的加氢过程主要分为两类:一类是加氢处理,一 类是加氢裂化。
用这种技术的目的在于脱除油品中的硫、氮、氧及金属等杂质, 同时还使烯烃、二烯烃、芳烃和稠环芳烃选择加氢饱和,从而改善原 料的品质和产品的使用性能。此外,加氢裂化的目的在于将大分子裂 化为小分子以提高轻质油收率,同时还除去一些杂志。其特点是轻质 油收率高,产品饱和度高,杂质含量少。 作用机理 吸附在催化剂上的氢分子生成活泼的氢原子与被催化剂削弱了键的 烯、炔加成。烯烃在铂、钯或镍等金属催化剂的存在下,可以与氢加 成而生成烷烃。加氢过程可分为两大类:
4、催化剂再生 国内加氢装置一般采用催化剂器内再生方式,有蒸汽-空气烧焦法和 氮气-空气烧焦法两种。 再生过程包括以下两个阶段: ①再生前的预处理 在反应器烧焦之前,需先进行催化剂脱油与加热炉清焦。 ②烧焦再生 通过逐步提高烧焦温度和降低氧浓度,并控制烧焦过程分三个阶段完 成。
炼油厂加氢脱硫工艺的夹点与节能探寻

炼油厂加氢脱硫工艺的夹点与节能探寻摘要:多数炼油厂加氢脱硫工艺内部网络能量较高,因此对该工艺进行集成节能研究将会发挥重要的作用。
通过对加氢脱硫工艺换热网络内部的夹点进行分析,可以看出该换热网络存在夹点热量传递的现象。
本文结合具体案例分析炼油厂加氢脱硫工艺的夹点和节能技术。
关键词:炼油厂;加氢脱硫工艺;节能技术引言:夹点技术作为一种常见的分析方法一直都在工业生产中被广泛应用,并取得更好的效果。
从日常实践过程可以看出,有效地运用夹点技术不仅能够提升系统的能量,更能够有效地降低投资的成本。
本文重点探寻炼油厂加氢脱硫工艺节能技术的运用。
1.研究背景当前,夹点分析已经广泛地被运用于炼油厂原油减压的过程中。
这进一步说明,如果换热网内部回收夹点的温差较小,其回收的热量就会变大。
如果确定要采用柴油加氢技术进行加工时,换热网内部并不需要额外的并入加热源就可以发挥实际的作用。
常规的夹点技术已经被运用改造节能装置过程中[1]。
但是,正由于多数节能装置的过程和内部条件存在差异,目前还没有显示较为明显的规律。
实际关于炼油厂汽油脱硫加氢工艺耗能方面的研究一直都相对较为薄弱,在使用该工艺时会耗费大量的蒸汽,但是这样一部分能量其实是要从公用工程内部来获取的。
本文通过采用集成的方式来分析炼油厂内部的加氢技术,进而才能够从冷热物流内部找出较为差劲的部分,最终降低公用工程的用量。
2.加氢脱硫工艺换热网络夹点分析2.1加氢工艺换热网络分析某炼油厂内部的脱硫工艺主要可以由预分馏部分、反应步骤和其他几个步骤共同组成。
可以在分析加氢脱硫工艺流程和数据之后提取出12个不同的物流数据和2种不同的加热公用工程,整体物流参数如表1所示:图1显示了整个图1显示了整个氢脱硫工艺的使用过程如下:重汽油和混合氢内部确实存在交换热量的现象。
如果汽油和氢内部确实存在一个换热器。
此时,换热器的存在可以让混合氢和重汽油更好地进行换热。
等到达到一定的温度之后自然可以提升混合的效率。
工艺过程的叙述、加氢脱硫过程《重油文库》
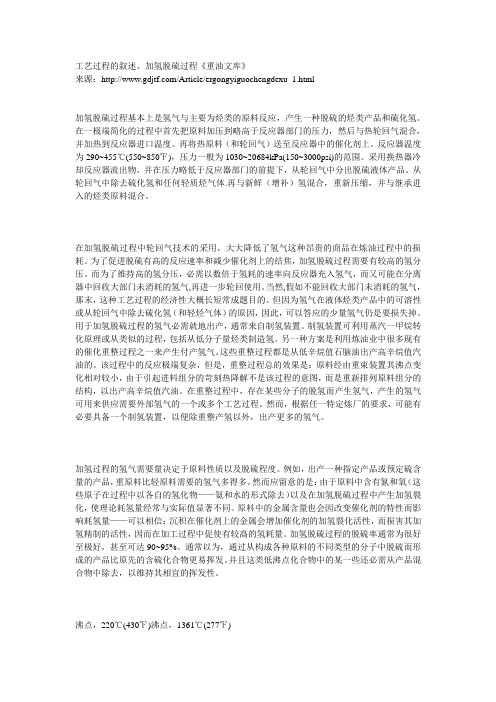
工艺过程的叙述、加氢脱硫过程《重油文库》来源:/Article/ergongyiguochengdexu_1.html加氢脱硫过程基本上是氢气与主要为烃类的原料反应,产生一种脱硫的烃类产品和硫化氢。
在一极端简化的过程中首先把原料加压到略高于反应器部门的压力,然后与热轮回气混合,并加热到反应器进口温度。
再将热原料(和轮回气)送至反应器中的催化剂上。
反应器温度为290~455℃(550~850℉),压力一般为1030~20684kPa(150~3000psi)的范围。
采用换热器冷却反应器流出物,并在压力略低于反应器部门的前提下,从轮回气中分出脱硫液体产品。
从轮回气中除去硫化氢和任何轻质烃气体.再与新鲜(增补)氢混合,重新压缩,并与继承进入的烃类原料混合。
在加氢脱硫过程中轮回气技术的采用,大大降低了氢气这种昂贵的商品在炼油过程中的损耗。
为了促进脱硫有高的反应速率和减少催化剂上的结焦,加氢脱硫过程需要有较高的氢分压。
而为了维持高的氢分压,必需以数倍于氢耗的速率向反应器充入氢气,而又可能在分离器中回收大部门未消耗的氢气,再进一步轮回使用。
当然,假如不能回收大部门未消耗的氢气,那末,这种工艺过程的经济性大概长短常成题目的。
但因为氢气在液体烃类产品中的可溶性或从轮回气中除去硫化氢(和轻烃气体)的原因,因此,可以答应的少量氢气仍是要损失掉。
用于加氢脱硫过程的氢气必需就地出产,通常来自制氢装置。
制氢装置可利用蒸汽一甲烷转化原理或从类似的过程,包括从低分子量烃类制造氢。
另一种方案是利用炼油业中很多现有的催化重整过程之一来产生付产氢气。
这些重整过程都是从低辛烷值石脑油出产高辛烷值汽油的。
该过程中的反应极端复杂,但是,重整过程总的效果是:原料经由重束装置其沸点变化相对较小,由于引起进料组分的苛刻热降解不是该过程的意图,而是重新排列原料组分的结构,以出产高辛烷值汽油。
在重整过程中,存在某些分子的脱氢而产生氢气,产生的氢气可用来供应需要外部氢气的一个或多个工艺过程。
- 1、下载文档前请自行甄别文档内容的完整性,平台不提供额外的编辑、内容补充、找答案等附加服务。
- 2、"仅部分预览"的文档,不可在线预览部分如存在完整性等问题,可反馈申请退款(可完整预览的文档不适用该条件!)。
- 3、如文档侵犯您的权益,请联系客服反馈,我们会尽快为您处理(人工客服工作时间:9:00-18:30)。
浅论炼油厂气脱硫化氢工艺
摘要:炼油技术的发展和提高致使炼油过程中的硫含量逐渐增大,炼油厂以及相关石油产品的脱硫工艺逐渐成为了石油企业的重要工艺和关键技术,通过对脱硫溶剂的选择以及减少胺液跑损以及建立完善的脱硫化氢系统结构等措施来实现对炼油厂气的脱硫,达到了较好的效果,在提高了炼油厂企业产品质量的前提之下同时也实现了环境保护,为类似炼油厂气脱硫化氢工艺的研究和应用提供了参考的经验。
关键词:炼油厂气脱硫化氢工艺
随着当前炼油企业对炼油技术的不断研究和升级,渣油在炼油过程中所掺杂的比例逐步增加,炼油企业的相关装置厂气硫化氢的含量也逐渐增加,为炼油厂以及当地的环境造成了一定的压力,同时也影响了企业石油产品的优化升级。
由此可了解到,对炼厂气以及石油产品的脱硫工艺逐渐成为了企业重视的重要工艺,同时也是保证企业产品质量的关键技术。
炼厂气的脱硫效果不好,将不利于下道工序的加工,不利于环境保护以及造成加工设备的腐蚀等。
炼厂气中硫含量的不同导致了不同企业具有不同的脱硫工艺。
硫的含量较低时,可通过简单的碱洗则可实现脱硫,而当硫的含量逐渐提高,若是使用碱洗将导致脱硫处理的成本过高。
当前,大多数都使用HZS,胺法脱硫化氢以及催化氧化法等工艺实现炼厂气的脱硫。
1 选择溶剂
脱硫工艺中的类型应选择环保、节能和经济的溶剂。
随着脱硫工艺的发展,脱硫剂从MEA、DEA逐渐向着复合型的溶剂发展,例如MDEA,复合型的溶剂脱硫效果较好。
选择性佳且性能稳定,不容易降解、发泡,具有较高的酸性气负荷性,同时能耗较低,使用便利。
一般在复合型MDEA使用的基础上添加一定的添加剂作为脱硫剂。
在脱硫剂的选择过程中,不但应注重溶剂的质量以及适应的场合,更应注意其发泡的高度以及消泡的时间。
不同品质的脱硫剂发泡高度相差较大,高度越大,消泡所需要的时间就越长,那么所需要的带胺量也就有所增加,容易导致胺液的泡损,提高了生产的成本。
由此,对溶剂的选择十分重要。
溶剂浓度的选择又是另一项重要的指标。
由于复合型的MDEA 粘度较小,对输送影响较小,同时腐蚀性也较小,从理论上而言,MDEA 使用浓度可达到50%。
但由于溶剂种类不同,生产流程以及生产设备设计等多方面的原因,溶剂浓度较高时较为严重,胺液跑损较大。
但只要选择了合适种类的溶剂,从而在实际的流程设计和过程中尽量减少发泡,通过提高溶剂浓度,减少溶剂的循环量,最终降低了工程项目的投资,减少了生产的成本。
2 减轻胺液跑损
2.1 预处理原料
在进入净化系统前,应首先经过预处理系统排除原料中的杂质,进入吸收塔的杂质容易导致溶剂的发泡现象。
而干气最为关键的处理设备在于冷却器以及带有泡沫装置的分离器,可有效脱离出中烃类,通过将过滤器以及分离器联合起来使用,有效提高液体以及固体杂质的分离。
例如,原料气中不仅具有HZS以及CO,同时还具有HCN、HCI以及氨、天然气、焦化干气等,在进入吸收塔前,应设置水洗塔,那么则可减少杂质进入主系统而导致在脱硫过程中造成的障碍,而液化的石油气,则可通过体积较大的沉降罐实现重组分烃类的分离,防止重烃类进入吸收系统。
2.2 控制操作温度
胺吸收HZS或者CO的化学反应为放热反应,而较低的溶剂温度有利于吸收反应的进行。
但加入吸收系统的溶剂温度的确定还应考虑到防止气体当中的重烃冷凝而导致的溶剂发泡现象,甚至对正常的生产产生了障碍,而对于干气吸收塔,为了防止溶剂温度过低而导致的干气中重烃冷凝,溶剂发泡,应将温度设定为高于干气温度的5~10℃。
对于液化的石油气而言,温度的控制是十分重要且关键的,合适的温度能保证胺以及LPG的分离效果最佳,从而有效减少了炼厂气中胺的夹带量。
贫液的温度控制应保持与LPG界面有2×10-3Pa·s的粘度,从而
保证了分离反应的持续进行。
2.3 选择合适的过滤系统
胺法净化系统中,最为重要的操作单元是溶剂的过滤系统,通过正常的过滤,溶剂的发泡趋势可降低到最小,机械过滤的方式可将产品中的杂质脱离出来,从而避免了由于颗粒物的杂质而导致的发泡腐蚀以及不合格的产品现象,可使用活性炭的过滤器吸附夹带烃类,游离铁以及阻泡剂等,同时也能有效实现腐蚀剂、发泡剂和色素的脱离。
为了实现富液的全过滤要求,通过设置精度为50μm的机械过滤器,从而避免了富液中包括较多的杂质,同时在解吸塔的高温作用下将导致溶剂热降解以及吸收塔内部的发泡现象。
在开工初期管线以及设备中的灰渣等杂质以及脱硫后期产生的大量腐蚀产物带入了吸收系统,从而导致了发泡现象。
应通过贫溶液全过滤,第一级机械的过滤精度设置为50μm,而二级机械过滤器的精度则提高了很多,设置为5~10μm。
采取贫溶液的全过滤将在很大程度上增加生产项目的投资,但对于维持脱硫系统的持续正常运行,减少胺液的跑损而言是十分必要的。
同时也应重视活性炭种类的选择和定期的更换,果壳、椰子壳以及普通的煤质等具有较大的吸附性能差异,高碘值的活性炭尤为适合脱硫溶剂的过滤,由此可了解到,脱硫溶剂过滤可使用褐煤或者烟煤基炭。
同时根据实际的生产状况实现对活性炭的定期更换,从而保证其过滤的效果。
2.4 减少净化炼厂气带胺
在吸收塔顶净化炼厂气过程中,容易夹带胺液,从而导致了胺液的跑损,可通过设置有效的分离设备,减少胺液的损失现象。
LPG胺液跑损现象相对于干气而言较为严重,一般可使用稀胺水溶液进行循环的洗涤,同时以体积较大的沉降罐进行沉降分离,从而在很大程度上减少了胺液的损失,但这种方式的运行成本较高,也需要较大的面积。
参考文献
[1] 栗元文.原油脱硫化氢方法的改进和优化[J].中国科技信息,2008(3).
[2] 兰梅,杨林,林杰.硫化氢治理技术研究进展[J].甘肃石油和化工,2008(1).
[3] 张春燕,刘宇红,赵文辉.生物脱硫技术在炼厂气中的应用[J].化学工业,2008(3).
[4] 程豪奇,王秋灵,裴季红.脱硫化氢汽提塔塔顶腐蚀原因分析与对策[J].石油化工环境保护,2006(3).。