H型钢万能轧机辊缝自动检测系统的应用
TCS工艺控制系统在自动辊缝调节中的应用
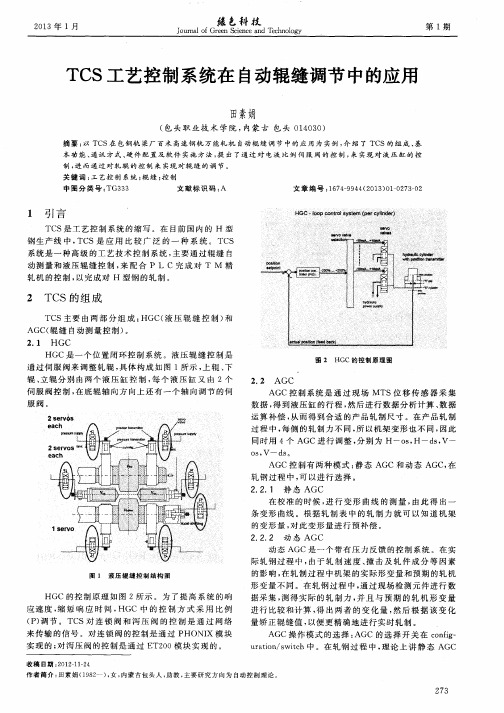
HGC 的控 制 原 理 如 图 2所 示 。 为 了提 高 系 统 的 响
据采 集 , 测 得 实 际 的 轧 制力 , 并 且 与 预 期 的 轧 机 形 变 量 进行 比较 和计 算 , 得 出两 者 的 变 化 量 , 然 后 根 据 该 变 化 量 矫 正 辊缝 值 , 以便 更 精 确 地 进行 实 时 轧 制 。
2 . 2 . 2 动 态 AGC
动 态 AGC是 一 个 带 有 压 力 反 馈 的控 制 系统 。在 实 际轧钢过程 中, 由于 轧 制 速 度 、 撞 击 及 轧 件 成 分 等 因 素
图 1 液 压 辊 缝 控 制 结 中机 架 的 实 际 形 变 量 和 预 期 的 轧 机 形 变 量 不 同 。在 轧 钢 过 程 中 , 通 过 现 场 检 测元 件 进行 数
AGC操 作 模 式 的选 择 : AGC的 选 择 开关 在 c o n i f g — u r a t i o n / s wi t c h中 。在 轧 钢 过 程 中 , 理 论 上 讲 静 态 AGC
应 速度 , 缩短 响 应 时 间, HG C 中 的 控 制 方 式 采 用 比例 ( P ) 调 节 。T C S对 连 锁 阀 和 泻 压 阀 的 控 制 是 通 过 网 络 来 传 输 的 信 号 。对 连 锁 阀 的控 制 是 通 过 P HON I X模 块
伺 服 阀控 制 , 在 底 辊 轴 向 方 向上 还 有 一 个 轴 向 调 节 的 伺
服 阀。
2. 2 A GC
AGC控 制 系统 是 通 过 现 场 MTS位 移 传 感 器 采 集
数据 , 得 到 液 压 缸 的行 程 , 然后进行数据分析计算 、 数 据 运算补偿 , 从 而 得 到 合 适 的产 品轧 制 尺寸 。在 产 品 轧 制 过程 中, 每 侧 的轧 制 力 不 同 , 所 以机 架 变 形 也 不 同 , 因此
小型H型钢万能机组快速换辊改造
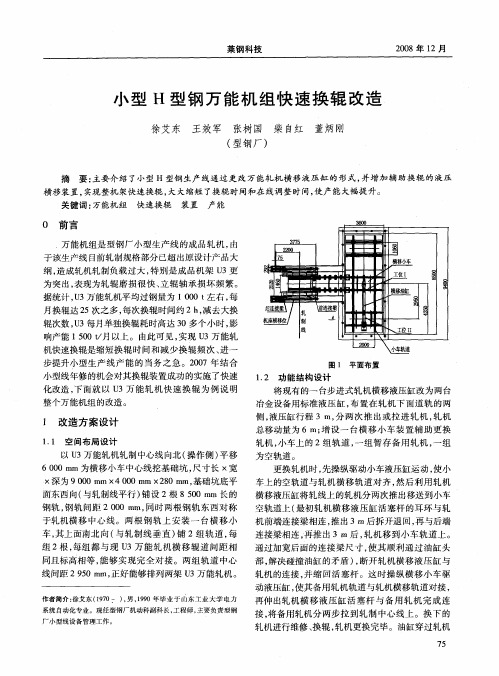
装了单向截流截止阀, 可以实现较精确的同步调整。
3 油 缸 选 型 及技 术 参 数 : 3万 能轧 机 快 速 换 ) u 辊 系 统改造 后 , 汰 了原 u 淘 3万 能 轧 机 的 横移 油 缸 ( 要反 复 操 作 才 能 把轧 机 拖 出 , 时 费力 ) 采 用 需 费 ,
月换辊达 2 次之多 , 5 每次换辊时间约 2h减去大换 , 辊次数 ,3 u 每月单独换辊耗时高达 3 0多个小时 , 影
响产能 150t月 以上 。 由此可 见 , 0 / 实现 u 3万能 轧 机快 速换 辊是 缩短 换 辊 时 间 和减 少 换 辊 频 次 、 进一 步提 升小 型 生 产 线 产 能 的 当务 之 急 。20 07年 结 合 小 型线 年修 的机会对 其换 辊装 置成 功 的实 施 了快速 化改 造 , 下面 就 以 u 3万 能 轧 机 快 速 换 辊 为 例 说 明
莱钢 科技
20 0 8年 1 2月
小 型 H 型 钢 万 能 机 组 快 速 换 辊 改 造
徐艾 东 王效军 张树 国 柴 自红 董炳 刚 ( 型钢厂)
摘
要: 主要 介绍 了小型 H型 钢生 产 线通 过 更 改 万 能轧 机横 移 液 压 缸 的形 式 , 增加 辅助 换 辊 的 液压 并 快速 换辊 装置 产 能
6000mm为横移小车中心线挖基础坑尺寸长x宽更换轧机时先操纵驱动小车液压缸运动使小深为9000mm4000mmx280mm基础坑底平车上的空轨道与轧机横移轨道对齐然后利用轧机面东西向与轧制线平行铺设2根8500mm长的横移液压缸将轧线上的轧机分两次推出移送到小车钢轨钢轨间距2000mm同时两根钢轨东西对称空轨道上最初轧机横移液压缸活塞杆的耳环与轧于轧机横移中心线
首钢长钢H型钢厂万能轧机液压伺服系统辊缝控制技术的研究与应用
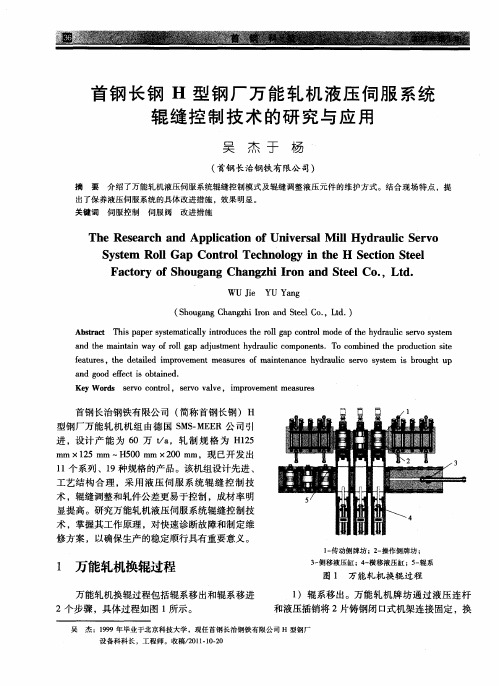
图 3 调整缸 的控 制过程 示意 图
万能轧机 液 压伺 服 系统辊 缝 控制 是现 代万 能 轧机 的核心技 术 ,系统 由 H C ( 压辊 缝 控 制 ) G 液 系统 和 A C ( G 自动辊缝 控制 ) 系统组 成 。万 能轧
机液压伺 服系统辊缝 控制原理如 图 2所 示 。
2 )辊 系 移 进 。 与 辊 系 移 出 步 骤 相 反 ,P C L ( 编程 序控 制器 )执行 装 辊程序 。 可
Th s a c n p ia i n o ie s lM i d a l e v e Re e r h a d Ap l t fUn v r a l Hy r u i S r o c o l c S se Ro lGa n r lTe h oo y i h S ci n S e l y t m l p Co to c n lg n t e H e t te o
至最大值。压力传感器的检测信号传送到压力控
制器 ,对 液压 缸进行 轧 制力 闭环控 制 ,同 时位 移
检测信号和压力检测信号也进入 A C系统 ,进 G 行 机 架变形 量计 算 ,从 而实现 对辊 缝开 度 的动 态
补偿 。
会根据反馈信号进行 自动分析,对辊缝开度进行 适 量 调 整 ,再 控 制 H C 系统 做 出相 应 的变 动 。 G
动 ,使辊缝减小到设定值 ,同时将两侧的调整缸
的位 移变 化量 进行 比较 , 自动 微调 ,消 除辊缝 倾
万能轧制
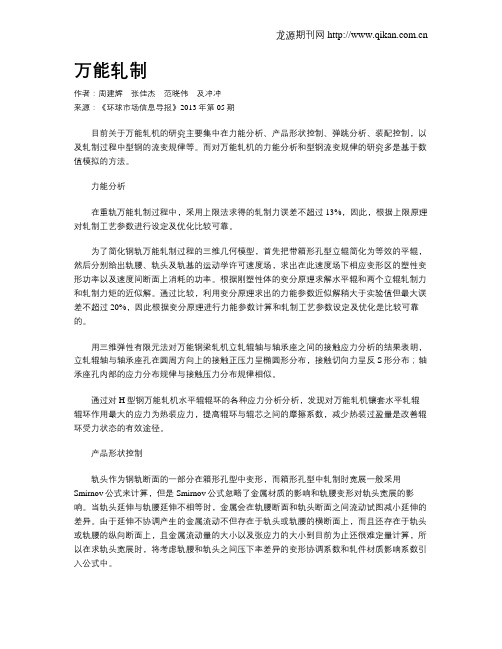
万能轧制作者:周建辉张佳杰范晓伟及冲冲来源:《环球市场信息导报》2013年第05期目前关于万能轧机的研究主要集中在力能分析、产品形状控制、弹跳分析、装配控制,以及轧制过程中型钢的流变规律等。
而对万能轧机的力能分析和型钢流变规律的研究多是基于数值模拟的方法。
力能分析在重轨万能轧制过程中,采用上限法求得的轧制力误差不超过13%,因此,根据上限原理对轧制工艺参数进行设定及优化比较可靠。
为了简化钢轨万能轧制过程的三维几何模型,首先把带箱形孔型立辊简化为等效的平辊,然后分别给出轨腰、轨头及轨基的运动学许可速度场,求出在此速度场下相应变形区的塑性变形功率以及速度间断面上消耗的功率。
根据刚塑性体的变分原理求解水平辊和两个立辊轧制力和轧制力矩的近似解。
通过比较,利用变分原理求出的力能参数近似解稍大于实验值但最大误差不超过20%,因此根据变分原理进行力能参数计算和轧制工艺参数设定及优化是比较可靠的。
用三维弹性有限元法对万能钢梁轧机立轧辊轴与轴承座之间的接触应力分析的结果表明,立轧辊轴与轴承座孔在圆周方向上的接触正压力呈椭圆形分布,接触切向力呈反S形分布;轴承座孔内部的应力分布规律与接触压力分布规律相似。
通过对H型钢万能轧机水平辊辊环的各种应力分析分析,发现对万能轧机镶套水平轧辊辊环作用最大的应力为热装应力,提高辊环与辊芯之间的摩擦系数,减少热装过盈量是改善辊环受力状态的有效途径。
产品形状控制轨头作为钢轨断面的一部分在箱形孔型中变形,而箱形孔型中轧制时宽展一般采用Smirnov公式来计算,但是Smirnov公式忽略了金属材质的影响和轨腰变形对轨头宽展的影响。
当轨头延伸与轨腰延伸不相等时,金属会在轨腰断面和轨头断面之间流动试图减小延伸的差异。
由于延伸不协调产生的金属流动不但存在于轨头或轨腰的横断面上,而且还存在于轨头或轨腰的纵向断面上,且金属流动量的大小以及张应力的大小到目前为止还很难定量计算,所以在求轨头宽展时,将考虑轨腰和轨头之间压下率差异的变形协调系数和轧件材质影响系数引入公式中。
轧辊检测原理及应用
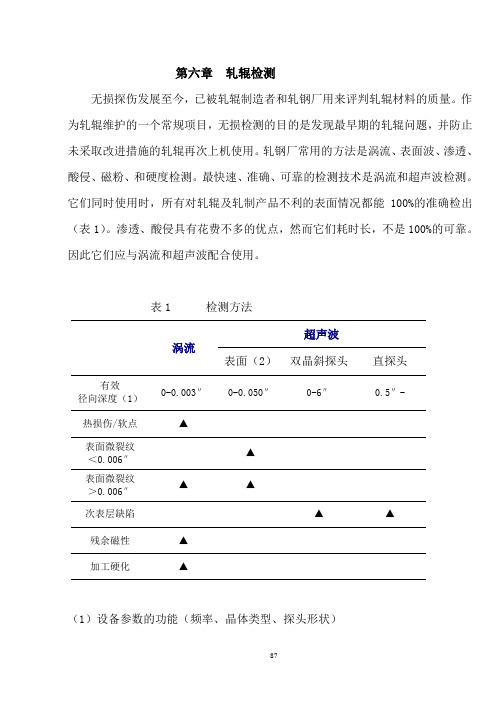
第六章轧辊检测无损探伤发展至今,已被轧辊制造者和轧钢厂用来评判轧辊材料的质量。
作为轧辊维护的一个常规项目,无损检测的目的是发现最早期的轧辊问题,并防止未采取改进措施的轧辊再次上机使用。
轧钢厂常用的方法是涡流、表面波、渗透、酸侵、磁粉、和硬度检测。
最快速、准确、可靠的检测技术是涡流和超声波检测。
它们同时使用时,所有对轧辊及轧制产品不利的表面情况都能100%的准确检出(表1)。
渗透、酸侵具有花费不多的优点,然而它们耗时长,不是100%的可靠。
因此它们应与涡流和超声波配合使用。
表1 检测方法超声波涡流表面(2)双晶斜探头直探头有效0-0.003″0-0.050″0-6″0.5″- 径向深度(1)热损伤/软点▲表面微裂纹▲<0.006″表面微裂纹▲▲>0.006″次表层缺陷▲▲残余磁性▲加工硬化▲(1)设备参数的功能(频率、晶体类型、探头形状)(2)圆周方向(要求扫描3次)轴向(要求扫描2次)一、涡流探伤涡流探伤是轧辊磨削之后,确定缺陷位置如软化区(热损伤)、宏观裂纹和磁化的一种方法。
磨床上,一个双线差分探头放置在辊身一端,靠近辊面处,随着轧辊以设定的速度转动,探头慢慢移动跨过整个辊身长度。
探头移动速度和轧辊转速的同步性是设定好的,以确保辊面的每一点都通过探头。
随着探头在辊身移动,在交流电流的作用下线圈间的辊面上产生涡流。
线圈间电流的导电性和路径长度的瞬间变化都能被检测出来,并显示在两个独立的频道。
一个称为压伤/热损伤频道,一个称为裂纹/剥落频道。
涡流探伤的特殊步骤取决于使用的涡流设备,由设备生产者提供。
导电率的变化可在压伤/热损伤频道上检出。
它是辊面相邻点间的硬度和显微组织变化的结果。
磁化区内所有相邻点间也会引起导电率的连续变化。
高斯通量可用来证实剩余磁性的存在。
(大于30Gauss)。
能引起辊面上导电性反复变化的一般条件包括(但不限于此)局部超温、局部工作硬化、表面粗化和外来夹杂物嵌入辊面。
这些情况在压伤/热损伤频道表现为超过噪音水平的单独的波峰或超过噪音水平的大面积的草状波峰(图2)。
万能轧机简介(下)

GM-AGC控制模型
特点二:全液压式的辊缝调节系统
PLC中输入产品数据
AGC中进行辊缝值计算 ,将产品数据转换成机 架数据
HPC根据AGC中的辊缝 值,控制伺服阀驱动液 压缸对辊子进行精确位 置控制和力控制
下 辊 轴 向 调 整 装 置 示 意 图
万能轧机区设备
4、万能轧机 闭口开轭式,两个铸造的闭式牌坊由拉杆连接,牌坊内衬有滑块。 可生产H型钢、工字钢和T型钢 ,更换成二辊辊系时可生产普通 型钢。轧边机为闭口式二辊轧机。 轧辊及导卫的更换是自动进行的。 水平辊和立辊的控制是通过液压系统和垫片来实现的。 液压系统提供:-轧制时设定理想的辊缝 -当发生事故时进行释放压力保护 -对轧机进行过载保护 -校正轧辊的轧制压力 -把轧辊的调整系统进行复位 -探测轧辊的弹跳值
特点二全液压式的辊缝调节系统hgcgmagc控制模型万能轧机agc技术可以看成为板带轧机agc的移植但由于h型钢的翼缘和腹板尺寸测量比较困难所以只采用gmagc它是以厚度计模型为基础在控制中实ห้องสมุดไป่ตู้出轧制力和辊缝值间接计算出轧件出口厚度再求出与目标厚度之差以此为根据改变辊缝值使轧出厚度恒定
液压AGC系统的核心 任务就是通过补偿轧机 的弹跳和调整压下系统 的位置来保持带载辊缝 和轧件出口厚度的恒定 。
万能轧机组技术参数
项目 参数 功率 主电机 转速 额定转矩 喷嘴压力 冷却水 水平辊流量 立辊流量 万能总流量 水平辊压下系统 立辊侧向压下系 统 工作行程 单位 kW rpm kNm MPa m3/h m3/h m3/h mm 万能粗轧机 4000 0~65/190 1616 5 85 85 2×85 2×155/2×155 轧边机 1500 0~100/275 394 5 85 85 2×85 120 万能精轧机 4000 0~65/1902 1616 5 85 85 2×85 2×155/2×155
利用自动控制系统实现钢板在辊道上的精确定位

能在钢板前进 方 向的尾部标 印 , 由于每块钢 板 的规
格不同 , 短不一 , 长 就无 法 在 钢 板 前 进 方 向加 挡 板 而
实现尾部的定位 。
方案二 : 将该组辊道的传 动改为变频调速控 制 ,
21 00年第 3期
南钢 科技 与 管理
4 9
现 场 增 加 检 测 装 置 , 用 原 有 的 P C系 统 , 现 钢 板 利 L 实
关键 词 : - 0P C B ¥ 4 L A B变频器 自 70 动定位
Ac u at sto i g o e lPl t s o he Ro lTa l y Aut m a i n r lSy t m c r e Po ii n n fSte a e n t l be b o tc Co t o s e
d ii g s se rvn y t m.
Ke ywo ds: 7-0 P r ¥ 4 0 LC ;ABB fe e c o v re ;a tm ai o i o ig rqu n y c n et r uo tc p st nn i
l 概 述 为提 高产 品质量 , 提升工 厂 自动化水平 , 中板厂 在精整线新增加 自动标印机 以替代 原有的液压式钢 印机和人工喷印 , 台设备分 别安装 在两条 精整线 两 的成品收集 冷床处 , 钢板经辊 道传输 到位后 由拉钢 机将其拉上成品收 集冷床 然后进行 喷 印, 标 印设 该 备要求钢板离设 备之 间 的距 离 固定 , 且误差 不超过
上 的精 确 定 位 。
线处 , 此时将 钢板拉上收集 冷床就可以进 行标 印了。
图 2
现 场 布 置 示 意 图
3 具体 实施
3 1 将 2 线收集冷 床输 入辊道 的传 动部分 即可控 . # 硅无触点开关 控制 改 为全数 字交 流变 频调 速控 制 ,
轧辊表面检测在实际生产中的重要意义
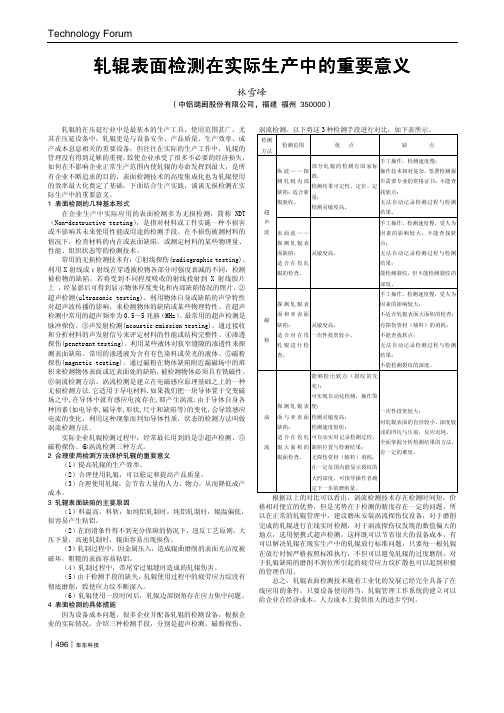
Technology Forum︱496︱华东科技轧辊表面检测在实际生产中的重要意义轧辊表面检测在实际生产中的重要意义林雪峰(中铝瑞闽股份有限公司,福建 福州 350000)轧辊的在压延行业中是最基本的生产工具,使用范围甚广,尤其在压延设备中,轧辊更是与设备安全、产品质量、生产效率、成产成本息息相关的重要设备,但往往在实际的生产工作中,轧辊的管理没有得到足够的重视,致使企业承受了很多不必要的经济损失,如何在不影响企业正常生产范围内使轧辊的寿命发挥到最大,是所有企业不断追求的目的,表面检测技术的高度集成化也为轧辊使用的效率最大化奠定了基础。
下面结合生产实践,谈谈无损检测在实际生产中的重要意义。
1 表面检测的几种基本形式在企业生产中实际应用的表面检测多为无损检测,简称 NDT (Non-destructive testing),是指对材料或工件实施一种不损害或不影响其未来使用性能或用途的检测手段。
在不损伤被测材料的情况下,检查材料的内在或表面缺陷,或测定材料的某些物理量、性能、组织状态等的检测技术。
常用的无损检测技术有:①射线探伤(radiographic testing)。
利用X 射线或γ射线在穿透被检物各部分时强度衰减的不同,检测被检物的缺陷。
若将受到不同程度吸收的射线投射到X 射线胶片上 ,经显影后可得到显示物体厚度变化和内部缺陷情况的照片。
②超声检测(ultrasonic testing)。
利用物体自身或缺陷的声学特性对超声波传播的影响,来检测物体的缺陷或某些物理特性。
在超声检测中常用的超声频率为0.5~5兆赫(MHz)。
最常用的超声检测是脉冲探伤。
③声发射检测(acoustic emission testing)。
通过接收和分析材料的声发射信号来评定材料的性能或结构完整性。
④渗透探伤(penetrant testing)。
利用某些液体对狭窄缝隙的渗透性来探测表面缺陷。
常用的渗透液为含有有色染料或荧光的液体。
带钢冷连轧机组中的自动辊缝控制系统

带钢冷连轧机组中的自动辊缝控制系统引言带钢冷连轧机是带钢生产线中的重要设备,用于将热轧带钢进行冷轧加工,以获得符合市场需求的产品。
自动辊缝控制系统是冷连轧机组的关键部件之一,其主要作用是保证冷连轧机在加工带钢时能够实现准确的辊缝尺寸控制,保证产品的质量和生产效率。
本文将介绍带钢冷连轧机组中的自动辊缝控制系统的工作原理、主要构成及其优势。
一、自动辊缝控制系统的工作原理1. 辊缝控制原理带钢冷连轧机组中的自动辊缝控制系统采用了先进的控制原理,主要包括两种控制方式:开环控制和闭环控制。
开环控制是指通过对冷连轧机的机械结构进行静态分析,确定辊缝尺寸与轧机驱动系统参数之间的关系,通过相应的控制系统来调整轧机的运行参数,以实现辊缝尺寸的控制。
而闭环控制则是在开环控制的基础上,通过传感器对辊缝进行实时监测和反馈,从而实现对辊缝尺寸的闭环控制,保证辊缝的稳定性和精度。
2. 控制器控制器是自动辊缝控制系统的核心部件,主要包括数据采集、数据处理和控制算法等模块。
控制器通过传感器实时采集的数据,根据预设的控制策略和控制算法进行数据处理和分析,再通过执行机构来调整冷连轧机的运行参数,以实现对轧机的闭环控制。
控制器既可以采用硬件控制,也可以采用软件控制,其控制算法可以包括PID控制、模糊控制、神经网络控制等,以实现对辊缝尺寸的准确控制。
3. 执行机构执行机构是自动辊缝控制系统的输出部件,主要包括轧机的传动系统、辊形调整机构等。
在控制器的控制下,执行机构根据调整信号来实时调节冷连轧机的运行参数,确保辊缝尺寸能够稳定在预设的标准范围内,从而保证产品的质量和生产效率。
三、自动辊缝控制系统的优势1. 精度高自动辊缝控制系统采用了先进的控制算法和控制器,能够实现对辊缝尺寸的精确控制,保证辊缝的稳定性和精度,从而获得高质量的产品。
2. 稳定性好自动辊缝控制系统采用了闭环控制原理,通过对辊缝的实时监测和反馈,能够及时调整轧机的运行参数,保证辊缝的稳定性和一致性,保证产品的稳定质量。
带钢冷连轧机组中的自动辊缝控制系统

带钢冷连轧机组中的自动辊缝控制系统带钢冷连轧机组中的自动辊缝控制系统是现代钢铁生产中的重要设备之一,它能够对带钢进行精确的轧制加工,确保产品质量的稳定和一致。
本文将介绍带钢冷连轧机组中自动辊缝控制系统的工作原理、特点和应用前景。
一、工作原理带钢冷连轧机组中的自动辊缝控制系统主要由传感器、数据采集系统、控制算法和执行机构等组成。
在设备运行过程中,传感器采集到带钢的各项物理参数,如温度、厚度、张力等,然后将这些数据传输至数据采集系统进行处理和分析。
控制算法根据这些数据和预设的轧制参数,计算出最佳的辊缝尺寸和调整方案,并将调整指令发送给执行机构,使得辊缝能够按照预设的轧制参数进行自动调整,以保证带钢的轧制质量。
二、特点1. 精准调整:自动辊缝控制系统能够实时监测带钢的各项物理参数,并根据轧制要求进行精确的辊缝调整,确保产品的尺寸和质量达到设计要求。
2. 高效运行:自动辊缝控制系统能够实现快速的辊缝调整,并且能够根据不同轧制要求进行自动切换,提高了设备的运行效率和生产能力。
3. 自适应性强:自动辊缝控制系统能够根据带钢的不同规格和轧制要求进行智能调整,具有很强的自适应性,能够适应多种轧制工艺和产品要求。
4. 可靠稳定:自动辊缝控制系统采用先进的传感器和控制算法,能够实现高精度的辊缝调整,并且保持设备的稳定运行,确保产品质量和设备安全。
三、应用前景自动辊缝控制系统在带钢冷连轧机组中具有广阔的应用前景。
随着钢铁行业的不断发展和需求的增加,对带钢产品质量和生产效率的要求也越来越高,自动辊缝控制系统能够满足这一需求,提高轧制质量和生产效率,降低生产成本,具有广泛的市场前景和应用前景。
在今后的发展中,随着自动化技术和智能控制技术的不断进步,带钢冷连轧机组中的自动辊缝控制系统将会更加智能化、精准化和稳定化,进一步提高设备的自动化水平和智能化程度,为钢铁行业的发展做出更大的贡献。
H型钢万能轧机轧辊孔型设计
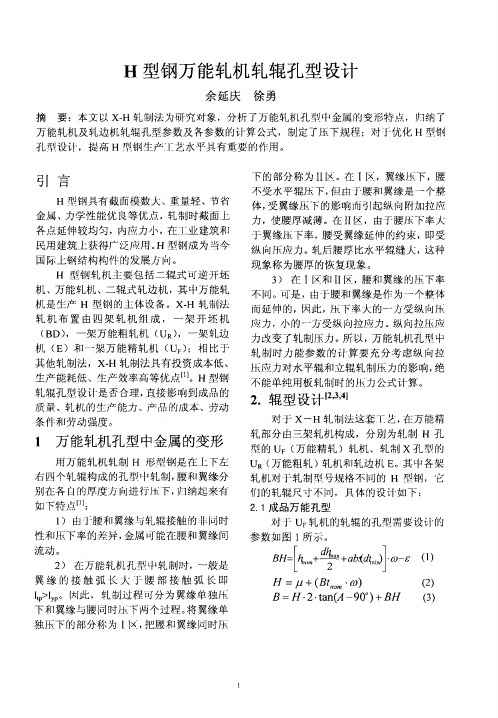
如下特 点 …: 1 由于腰和 翼缘 与轧 辊接 触 的非 同时 ) 性利 压下 率 的差异 , 属 町能在 腰和 翼缘 问 金
流动 。
2 在万 能 轧机孔 型 L 轧制 时 ,一般是 ) } J 翼 缘 的 接 触 弧 长 人 于 腰 部 接 触 弧 长 即
B = + 十6 i 一 ( HI 口 1 L - 』 )
右 四个轧 辊构 成 的T I 中轧 制 , L ̄ - 腰和 翼缘 分 别在 各 白的厚度 方 向进 行 下 , 归纳 起来 有
轧部 分 由三 架 ̄ I构 成 ,分别 为轧 制 H 孔 LI
型 的 U 万 能精轧 )轧 机 、轧制 x孔 型 的 ( U 万 能粗 轧 ) ( 轧机 和 轧边机 E 。其 中各架 轧 机对 - 轧制 犁号规 格不 同 的 H 型钢 ,它 I 们 的轧 辊尺 寸不 同 ,具体 的设 计如 下 : 2 1成品 万能 子 型 . L 对 于 U 轧机 的轧 辊 的孔型需 要 设计 的 参 数如 图 1 示 。 所
离 ,mm; A — 对于 U 轧机 一般取 9 . ; — F O5 。
调整余 量 ,一般 为 1  ̄2 m 5 0 m;
B
度 ,1 T TI U:
—— u F轧 机 的 轧 辊 槽 底 的 宽
2 2成 品前万 能孔型 .
UR
口
O-
图2 U R轧辊孔型
( D) B ,一 架万 能粗 轧机 ( ) UR ,一架 轧边 机 ( )和 一 架万 能精 轧 机 ( :相 比于 E U)
3 在 I 和 I区 ,腰和 翼缘 的压 下率 ) I 不 同。可是 ,由 J 和 翼缘是 作 为一个 整体 二 腰
而 延伸 的 ,冈此 , 下率 大 的一方 受纵 向 应 力 ,小的一 方受纵 向拉应力 。纵 向拉压应 力 改变 了轧制 压力 。 以 , I  ̄ I T 中 所 万 I L LL
实现TCS冗余系统的数字化控制策略
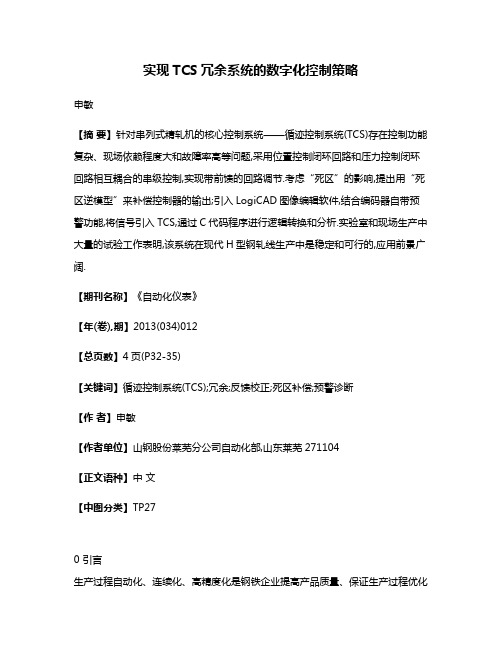
实现TCS冗余系统的数字化控制策略申敏【摘要】针对串列式精轧机的核心控制系统——循迹控制系统(TCS)存在控制功能复杂、现场依赖程度大和故障率高等问题,采用位置控制闭环回路和压力控制闭环回路相互耦合的串级控制,实现带前馈的回路调节.考虑“死区”的影响,提出用“死区逆模型”来补偿控制器的输出;引入LogiCAD图像编辑软件,结合编码器自带预警功能,将信号引入TCS,通过C代码程序进行逻辑转换和分析.实验室和现场生产中大量的试验工作表明,该系统在现代H型钢轧线生产中是稳定和可行的,应用前景广阔.【期刊名称】《自动化仪表》【年(卷),期】2013(034)012【总页数】4页(P32-35)【关键词】循迹控制系统(TCS);冗余;反馈校正;死区补偿;预警诊断【作者】申敏【作者单位】山钢股份莱芜分公司自动化部,山东莱芜271104【正文语种】中文【中图分类】TP270 引言生产过程自动化、连续化、高精度化是钢铁企业提高产品质量、保证生产过程优化控制的重要环节。
钢铁企业自动化控制系统—般由过程控制计算机系统完成。
影响系统稳定可靠性的因素有很多,其中,检测元件故障率高和维修效率低成为制约生产顺行的瓶颈因素。
因此,提高系统的稳定可靠性、降低废钢率,是轧钢企业首要考虑的问题。
在现代轧钢自动化控制领域,采用循迹控制系统(traction control system,TCS)控制技术、静态自动增益控制(automatic gain control,AGC)、动态 AGC、液压辊缝控制(hydraulic roll gap control,HGC)相结合的方式,计算辊缝位置和静态补偿量,并根据辊缝校准时采样轧制力点与轧辊、机架形变量构造的弹性曲线,计算实时形变补偿量,可迅速实现精轧机过程控制。
TCS系统在响应速度、精度等方面具有很强的优势,满足现代轧钢企业自动化控制的要求。
本文在充分研究现有TCS控制系统的基础上,将带前馈的回路调节控制、热备冗余技术、编码器预警诊断技术应用到该系统中,并通过现场的应用验证了该策略的可行性。
现代化H型钢精轧机控制系统说明

现代化H型钢精轧机控制系统说明摘要H型钢生产线在冶金行业作为一个完整、复杂的控制系统。
生产线要求采用成熟、先进、稳定、可靠性高并且经济实用的先进自动化控制系统,才能使生产线具有当今世界先进水平,满足生产线的工艺要求和技术指标,使产品在质量、成本上都具有较强的竞争力。
关键词H型钢;精轧机;西门子PLC系统介绍:我方根据用户的实际需求,为客户配置了即经济实用又能保证系统可靠稳定的一套自动控制系统。
精轧机控制系统选用西门子S7-400系列PLC,其中CPU选用416-2DP的高性能CPU,并配有远程IO通过IM153与主CPU进行数据通信。
通过Profibus DP 协议,能够获得高速、稳定的数据通信,而PLC与上位机之间通过光纤+以太网的模式,使生产人员可以在主控室在上位机中操作相应的规程。
1 精轧区操作台控制系统说明首先为了安全起见,将控制台的旋钮选为主控操作,将现场操作箱的旋钮也选为主控,此时为主控操作台控制模式。
按下台面上的“开车鸣笛”按钮,可以实现全线轧机启动前的预警功能。
通过控制台上的“手动-自动”选择开关,选择以手动或者自动方式进行操作台远程操作。
手动方式下,可以实现各台轧机货精轧区各设备的单独控制,例如精轧入口、出口辊道和九台精轧机的点动控制,每次检修完毕和单体调试时,在正式生产前多用此方式。
自动方式用于正常生产时的自动操作,此时精轧机通过操作台上的“单调-联调”选择旋钮,可以实现生产过程中的轧机单体调速或者级联调速,单体调速是指只改变某一台指定轧机的转速,其他轧机速度不变。
联级调速是指当改变某一台轧机的速度时,此轧机及其下游轧机的速度同时跟随变化,保证其线速度的变化率是相同的。
单调或者联调的调速范围均为设定速度的15%,精轧出口辊道的设定速度则跟随与其相邻的末架轧机,其速度可通过画面上的辊道超前系数进行调整,入口辊道、出口辊道的速度均有辊道速度设定窗口进行设置。
当要实现轧机的单体调速或级联调速时,先将“单调-联调”选择到要控制的方式,再按下操作台上轧机选择按钮,选择相应的轧机,然后旋转速度调节的“增加-减少”旋钮进行调速控制。
浅谈热轧H型钢的工程应用
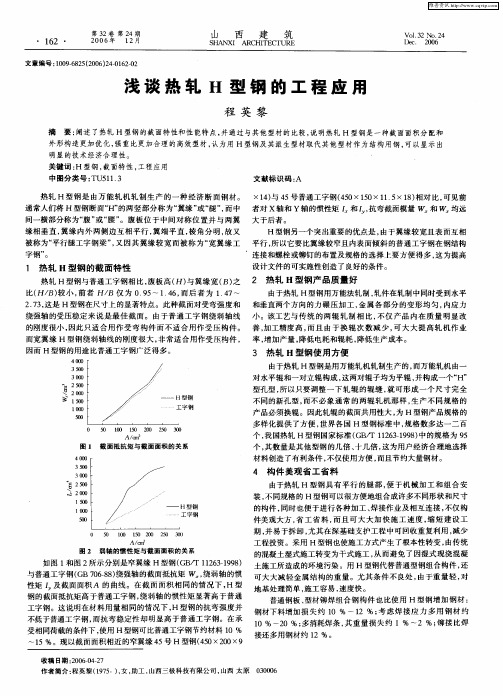
的刚度很小 , 因此 只适 合 用作受 弯构件 而不适 合用作 受压 构件 。 善 , 加工精度 高 , 而且 由于换 辊次 数减 少 , 大大 提高轧 机作 业 可 而宽翼缘 H型钢绕 弱轴 线 的刚度 很大 , 非常适合 用作 受压构件 , 率 , 加产 量 , 增 降低 电耗和辊耗 , 降低生产成本 。
35 o 0 30 0 0
25 0 0 20 0 0
譬 l0 0 5
lO 0 0 5o 0
A,
图 1 截 面 抵 抗 矩 与截 面 面积 的 关 系
材料创造了有利条件 , 不仅使用方便 , 而且节约大量钢材 。
4 构件 美观省 工省 料
由于热轧 H 型钢具 有平 行的腿 部 , 便于 机械加 工 和组合 安 装 , 同规格 的 H 型钢 可以很方便地组合成许多不 同形状和尺寸 不 的构件 , 同时也便于进行各种加工 、 焊接作业及相 互连接 , 不仅构
27 , .3 这是 H型钢在尺寸上 的显著特点。此种截面对受弯强度 和 和垂 直两个 方向的力碾 压加工 , 属各部 分 的变 形均匀 , 金 内应 力 绕强轴的受压稳定来说 是最 佳截 面。 由于 普通工 字钢绕 弱轴线 小。该工 艺与传统 的两辊 轧制 相 比 , 不仅 产 品 内在质量 明显 改
a\
浅 谈 热 轧 H 型 钢 的 工 程 应 用
程 英 黎
摘 要: 阐述 了热轧 H型钢 的截面特性和性 能特 点, 并通过与其他 型材的比较, 明热轧 H型钢是一种截面面积分配和 说 外形构 造更加优 化, 强重 比更加合理 的高效型材 , 认为用 H 型钢及 其派生型材取代其 他型材作 为结构用钢 , 以显示 出 可
维普资讯
轧机自动辊缝标定技术

TECHNo Lo GY F RoLL O GAP AU TOM ATI CALI C BRATI oN
Ca e h o oW n a
( iy o X nuI n& S e C . t. X n u3 8 0 , i gi r t l o ,Ld , iy 3 0 1 J n x) e a
为 K。 当某种 因素 影 响 轧 件 塑 性 线 由 曰 变 化 到 日 时, 为保证 轧机 出 口带 钢厚 度 h不 变 , 调整轧 机辊 需 缝 A 使 轧机 弹性线 由 A变 化到 A 。厚度 控制 的基 S, 本原 理是 : 无论 轧制过 程如 何 变化 , 总使 轧机 弹性线
第 1 期
总第 1 l 9 期
2 月
冶 金 丛 刊
M ETALLURGI CAL COL LECTI ONS
Su . 9J m 1
NO.1
2 0 1 年 1
Fe r a y 2 0 1 b u r l
轧机 自动 辊 缝 标 定 技 术
曹文 豪
( 新余 钢铁 股份 有 限公 司 , 江西 新 余 3 80 ) 30 1
3种 变 量 的 零 点 标 准 , 机 才 能 实 现 正 常 轧 制 时 轧 HG C系统 的 自动控 制 功 能 。可 以说 机 架 液 压 辊 缝 标 定是 轧机 进行 液压 HG C的前 提 , 实现 冷连轧 生 是
见 图 1 轧 件塑性 线 斜率 为 , , 轧机 弹 性线 斜 率
生 了改 变 , 以必 须 对 轧 机 液压 辊 缝 控制 系统 进 行 所 机 架液 压辊 缝 零 点 标 定 。通 过 标 定 可 以 获 得 轧 制
P —— 影 响辊 缝 的轧制 力极 限值 ;
北京科技大学科技成果——轧机工况在线监测系统
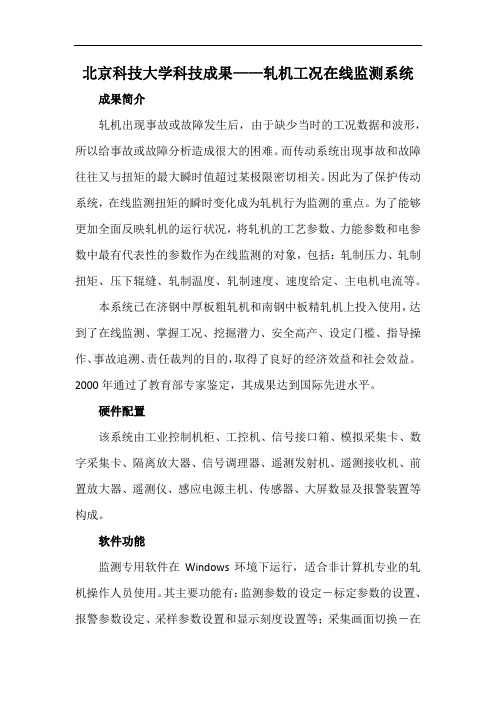
北京科技大学科技成果——轧机工况在线监测系统成果简介轧机出现事故或故障发生后,由于缺少当时的工况数据和波形,所以给事故或故障分析造成很大的困难。
而传动系统出现事故和故障往往又与扭矩的最大瞬时值超过某极限密切相关。
因此为了保护传动系统,在线监测扭矩的瞬时变化成为轧机行为监测的重点。
为了能够更加全面反映轧机的运行状况,将轧机的工艺参数、力能参数和电参数中最有代表性的参数作为在线监测的对象,包括:轧制压力、轧制扭矩、压下辊缝、轧制温度、轧制速度、速度给定、主电机电流等。
本系统已在济钢中厚板粗轧机和南钢中板精轧机上投入使用,达到了在线监测、掌握工况、挖掘潜力、安全高产、设定门槛、指导操作、事故追溯、责任裁判的目的,取得了良好的经济效益和社会效益。
2000年通过了教育部专家鉴定,其成果达到国际先进水平。
硬件配置该系统由工业控制机柜、工控机、信号接口箱、模拟采集卡、数字采集卡、隔离放大器、信号调理器、遥测发射机、遥测接收机、前置放大器、遥测仪、感应电源主机、传感器、大屏数显及报警装置等构成。
软件功能监测专用软件在Windows环境下运行,适合非计算机专业的轧机操作人员使用。
其主要功能有:监测参数的设定-标定参数的设置、报警参数设定、采样参数设置和显示刻度设置等;采集画面切换-在线采集波形显示、数字显示、负荷柱形图、轧制工况表等;数据库及查询-一般数据库查询和事件库查询。
频谱分析-功率谱分析和相关分析等。
技术特点采用高频感应电源供电技术,成功解决了被监测轴上在线长期供电的难题,使轴上发射机和传感器等获得了所需要的直流电源。
利用调制、解调和抗干扰技术,实现了被监测轴扭矩信号的无线传输。
改变了过去主要靠经验和分立的监测仪表来操作轧机的落后状态,使操作工能够在监测系统的指导下科学操作轧机。
经济效益及市场分析可用于中(厚)板轧机和同类大型轧机上,具有很好的推广价值。
该套监测系统售价为30万元,每套可获纯利12万元人民币。
带钢冷连轧机组中的自动辊缝控制系统

带钢冷连轧机组中的自动辊缝控制系统带钢冷连轧机组中的自动辊缝控制系统,是指一套用于控制机组辊缝间距的自动化系统,主要用于确保带钢冷连轧过程中的辊缝间距的精确控制。
带钢冷连轧机组是用于加工带钢的设备,其工作原理是通过一系列辊子的旋转将带钢进行轧制,从而使其具备所需的厚度和形状。
辊缝是指两个相邻辊子表面之间的间隙,它的大小直接影响到带钢的轧制效果和质量。
在传统的冷连轧机组中,辊缝的调整通常是由人工完成的,这种方式存在着调整不准确、效率低下、劳动强度大等问题。
为了解决这些问题,自动辊缝控制系统应运而生。
自动辊缝控制系统主要由计算机、传感器、执行器等组成,通过收集和处理来自传感器的辊缝间距信息,控制执行器调整辊子位置,从而实现对辊缝的自动控制。
自动辊缝控制系统的优势主要体现在以下几个方面:1. 精度高:自动辊缝控制系统能够根据工艺要求对辊缝进行精确控制,确保带钢的轧制质量。
2. 稳定性好:系统能够实时监测辊缝间距,并根据测量结果自动调整辊子位置,保持辊缝的稳定状态。
3. 效率高:相比传统的人工调整方式,自动辊缝控制系统可以实现辊缝的快速调整,提高机组的生产效率。
4. 劳动强度低:自动辊缝控制系统将人工操作减少到最低限度,可以减轻操作人员的劳动强度。
在使用自动辊缝控制系统时,需要对其进行定期维护和保养,以确保其正常工作。
还需要对系统的数据进行监测分析,及时发现问题并进行修复。
带钢冷连轧机组中的自动辊缝控制系统具有精度高、稳定性好、效率高和劳动强度低的优势,对于提高机组的生产效率和产品质量具有重要意义。
随着科技的不断进步,自动辊缝控制系统将会得到进一步的优化和发展。
- 1、下载文档前请自行甄别文档内容的完整性,平台不提供额外的编辑、内容补充、找答案等附加服务。
- 2、"仅部分预览"的文档,不可在线预览部分如存在完整性等问题,可反馈申请退款(可完整预览的文档不适用该条件!)。
- 3、如文档侵犯您的权益,请联系客服反馈,我们会尽快为您处理(人工客服工作时间:9:00-18:30)。
H型钢万能轧机辊缝自动检测系统的应用李仲华①1邹叔峰2(1:北京中冶设备研究设计总院有限公司北京100029;2:唐山盛达钢铁有限公司河北唐山063000)摘要详细阐述了H型钢万能轧机离线组装编码器与磁尺在消除机械间隙时的应用,万能轧机在线辊缝的显示,编码器与磁尺维护要点。
重点探讨H型钢辊缝检测要点及特点,分析了H型钢轧制过程中如何控制腹板与翼缘压延配合的方法,把实验室模拟轧制取得的数据应用到实际生产中,通过修正液压辊缝控制系统(HAGC)数学模型,取得了理想的效果。
关键词H型钢万能轧机辊缝自动监测与控制编码器与磁尺磁环中图分类号TG335.4文献标识码Bdoi:10.3969/j.issn.1001-1269.2013.z2.052Application of theRoll Gap Automatic DetectionSystem for the H-beam Universal MillLi Zhonghua Zou Sufeng(1:Beijing CentralResearch&Design Institute for Metallurgical Equipment of MCC Group,Beijing100029;2:Tangshan Shengda Iron and Steel Co.,Ltd.,Tangshan063000)ABSTRACT This paper describes the application of encoders and magnetic feet to eliminate mechanical gap when were assembled offline on H-beam universal mill,and the shows about Universal mill roll gap online;and the ma-intenance points of the encoders and magnetic tape.The main points and characteristics of the detection for the H-beam rool gap is main described,which analysis the method to control the webs match to flange rolling on the H-beam rolling process and apply the data obtained from laboratory simulation of the rolling to the actual production.It finally achieved the desired results by modifying the hydraulic roll gap control system(HAGC)mathematical model.KEYWORDS H-beam universal millRoll gap Automatic monitoring and control Encoders and magnetic tape Magnetic ring1引言H型钢万能轧机为四辊轧机,孔型较为复杂,另外H 型钢为复杂断面型轧材,对轧机辊缝调整及弹跳有较高的要求。
为了有效解决在线轧钢时的轧辊弹跳,要求在离线轧机组装时对轧机进行预先的压靠和清零;在线轧钢时,为及时、快捷、准确地调整轧机辊缝,要求实时地把辊缝数据显示在远程的显示屏上。
为提高轧制质量,必须以辊缝自动检测为基础,实现平立辊缝的在线联调。
2H型钢轧机辊缝自动检测传感器的选型以及检测原理H型钢万能轧机辊系如图1所示。
2.1水平辊辊缝值测量水平辊辊缝检测传感器选择绝对值编码器,考虑到辊缝检测精确度需求,结合工程经验并综合比较,4096ˑ8192绝对值编码器最为适宜。
4096ˑ8192的意思代表编码器每旋转一圈计数4096,编码器最大可以旋转8192圈,编码器总的计数范围就是从0到33554432。
因为万能轧机是丝杠压下,需要通过编码器旋转一圈对应的辊缝变化量来计算出一个系数(也称为斜率),编码器发出的数值除以这个系数就是当前的水平辊辊缝量。
绝对值编码器发出的数值需要传送到PLC进行处理器,有两种类型,一种是SSI类型的,需要将编码器的数值和时钟连接到SM338位置输入模块;另外一种是总线型、直接将编码器连Total No.208 Extra Edtion(2)2013冶金设备METALLURGICAL EQUIPMENT总第208期2013年特刊(2)①作者简介:李仲华,男,1966年出生,山东大学自动控制专业,本科,学士,高级工程师图1H 型钢万能轧机辊系示意图接到PLC 的DP 网络系统。
总线型编码器的接线大大简化,事故率降低,事故判断更加容易,因此选用总线型绝对值编码器。
2.2立辊辊缝测量立辊辊缝检测传感器选择磁尺,磁尺的精度为千分之一毫米,也就是说每1000个码值对应1mm 的距离。
磁尺的工作方式是将磁尺安装在立辊箱上,磁环安装在立辊箱内部与立辊共同进退的设备上,当调整立辊辊缝时通过磁环与磁尺位置的改变达到码值的改变。
与绝对值编码器一样,磁尺的码值也需要传送到PLC 处理器中,相同的原因也是选择总线型的磁尺。
3H 型钢万能轧机离线组装时的压靠和标定H 型钢万能轧机在装配间组装完毕后,需要对轧机水平辊和两个立辊进行压靠和对编码器、磁尺进行清零操作。
由于编码器与磁尺的工作原理不同,所以清零的方式也不同。
另外,立辊分为操作侧和传动侧两部分,因此要对两部分分别清零。
3.1水平辊压靠与标定首先将水平辊进行压靠,压靠的目的是消除机械间隙。
压靠完成后对编码器进行清零操作。
编码器的特性决定对编码器即可以做读操作也可以做写操作。
清零操作就是将一个固定的码值写入到编码器中,作为零点。
为了避免在实际应用过程中出现溢出错误,作为零点的码值应取编码器的中间值(最大码值的一半)。
清零操作完成后将水平辊打开,显示的数值应该与实际测量的数值一样。
最后,将水平辊打开到设定辊缝,标定操作完成(打开后的码值减去清零点码值的绝对值除以斜率即为实际辊缝值)。
水平辊压靠与标定控制流程如图2所示。
图2水平辊压靠与标定控制流程图3.2立辊压靠与标定将其中一侧立辊与水平辊压靠,记录压靠后对应磁尺的码值作为清零点。
打开立辊,测量的辊缝值应与显示的辊缝值一致。
将立辊打开到设定辊缝(打开后的码值减去清零点码值的绝对值除以1000即为实际辊缝值),另一侧的立辊清零与此相同,重要的是需要把清零数值记录下来,这个数值在轧机上线轧制时还要应用。
立辊压靠与标定控制流程如图3所示。
2013年特刊(2)总第208期冶金设备图3立辊压靠与标定控制流程图4H型钢万能轧机在线辊缝的显示H型钢万能轧机上线后辊缝显示的数值要与离线调整后显示的数值相同。
要做到这一点还要在上线后做很多工作。
对于水平辊来说,要保证同一架轧机的斜率相同和清零时的固定码值相同。
在具备以上两点后,绝对值编码器在线与离线显示的数值就应该是相同的,如果不相同说明轧机装备压靠过程存在问题或轧机吊装过程中因变形导致辊缝发生了变化。
对于立辊来说,要想使在线显示数值与离线显示数值相同,要将在离线清零时记录的清零数值写入到在线对应的立辊辊缝显示的程序中,因为在离线调整完立辊辊缝后,磁尺与磁环的位置未发生改变,因此在线显示的码值与离线显示的码值相同。
但是清零点码值的不同导致在线显示数值与离线不同,所以必须将离线清零点码值写入到程序中。
以保证显示辊缝的准确。
5现场总线分配箱的应用H型钢万能轧机在轧钢生产线中用在联轧部分,轧机较多。
每架万能轧机都有一个编码器和两个磁尺,因此在整条生产线中会用很多个编码器和磁尺。
如果将这么多的编码器和磁尺串到DP网络中就会出现一系列的问题:布线难度大、易出现断路和短路现象、其中一个编码器或磁尺出现问题会影响后面所有编码器和磁尺的正常使用,并会增大问题解决的难度、延长处理问题的时间。
为了解决以上问题和隐患,使用了现场总线分配箱。
这样就将线形网络结构变成树状网络结构。
每个分配箱中有一个分配器,分配器使每架轧机的编码器和磁尺与其它轧机的编码器和磁尺之间相互独立,互不影响,解决了以上问题。
6编码器及磁尺的维护要点由于现场环境比较复杂,给编码器和磁尺的维护增加了难度,但做好以下几点会对编码器和磁尺的维护起到重要的帮助:1)做好防护,避免编码器和磁尺直接受到外力撞击、避免编码器和磁尺进油,进水。
由于轧钢生产线的工作环境复杂,在轧机吊运和其它生产过程中应避免对编码器和磁尺的直接撞击。
编码器和磁尺内部是电路板,当受到外力撞击时会导致内部电子元件损坏。
由于轧机需要润滑、轧辊在生产过程中需要冷却,难免有油污和水,编码器和磁尺进油、进水会导致短路,造成编码器和磁尺烧毁。
2)做好屏蔽,轧钢生产线会有大量的变频设备,产生大量的电磁干扰。
因为编码器和磁尺是低压数字检测设备,对电磁干扰比较敏感,会使编码器和磁尺显示数值有跳变现象发生。
做好屏蔽可避免此现象发生。
3)做好离线检查,每次轧机下线要将编码器和磁尺在轧机上拆除,避免在拆装轧机过程中损坏,并在此时对编码器和磁尺进行检查、清理、维护工作,每次使用前都能保证编码器和磁尺是可用的、完好的。
7H型钢辊缝自动控制随着计算机技术及液压技术的快速发展,自动液压辊缝控制(HAGC)日臻成熟。
不管对于热轧还是冷轧,二辊轧机的辊缝测量及实时控制已经有了成熟的理论支撑,容易建立精确数学模型,产品应用取得了非常好的效果。
而对于H型钢万能轧机,轧制时,单独调节水平辊辊缝会对立辊辊缝产生影响,反之亦然,轧制结果表现为:水平辊缝相对过调时,H型钢翼缘易产生波浪;立辊辊缝相对过调时,H型钢腹板易产生波浪。
由于存在着平辊与立辊的这种相互作用,对产品的精度产生不利影响,几年来,始终在摸索平辊辊缝与立辊辊缝相互作用的数学模型,但是由于缺乏成熟理论的支撑,纯粹靠经验数据,一直没有取得理想的效果。
国内许多科研院所通过仿真实验,对复杂断面型钢轧制过程中水平辊缝与立辊辊缝间的相互影响进行研究,取得大量实验数据。
目前大部分生产企业利用这些数据来指导H型钢轧制时辊缝的人工调节,虽然取得了一定效果,但是基于经验数据的人工调节,在精度及响应时间上存在缺陷。
以数学模型为依据,通过自动监测与控制实现H型钢轧制辊缝调节是当务之急。
H型钢平、立辊缝联调的基本思路是:以水平辊缝调节为主,立辊辊缝通过匹配腹板压延量进行跟随性调节。
调节的关键在于,立辊辊缝控制要把水平辊缝调节量作为非线性扰动量纳入。