铸铁件配料方法
如何获得优质铁水1配料计算

有许多工厂采用铸铁屑压块法,效果很好。 如有的工厂用160t摩擦压力机将铸铁屑冷压 成块,压后即可入炉熔化,回收率达90%以 上。
(4)铁合金
铁合金主要用于调整铸铁中的化学成分。铁 合金种类很多,常用的有硅铁、锰铁、磷铁、 钛铁、铬铁、钼铁等。
配料时常用FeSi45硅铁来调整铁液成分,而 孕育处理则用FeSi75硅铁,可在出铁槽,铁 水包中加入。硅钙合金多用于炉前孕育处理。
(1)铸造用原生铁
原生铁是由铁矿石在炼铁厂高炉中冶炼出来 的的生铁锭。铸铁配料所用的原生铁主要是 铸造用生铁,个别情况下也适当搭配少量的 炼钢用生铁。铸造用生铁的规格见表11.4。 牌号如铸26(Z26)的“铸”字或“Z”代表 铸造用生铁,后面的数字“26”代表生铁中平 均含硅量为2.6%。其次是以生铁中含锰量、 含磷量和含硫量进行分类。
配料表格核算法是生产中常用的一种方法, 其步骤为先按铸铁要求和生产条件,以选择 法确定炉料配比;然后对所搭配炉料中的主 要成分进行核算。
(1)确定炉料配比
在生产中,当冲天炉状况和炉料成分相对稳 定时(日常生产中每日炉料配比虽有变化, 但一般波动范围不大),则配料工作可适当 简化。根据当日原料和铸件生产情况,可用 选择法确定炉料配比,然后对铁料的主要成 份进行核算,并计算出硅铁、锰铁等铁合金 的加入量。
其次确定新生铁与废钢的配比,设新生铁的配比为 x%,而回炉料的配比为y%,则废钢的配比为 100%-y%-x%。设炉料所需含碳量为w%,而 新生铁、废钢、回炉料的含碳量分别为a%、b%、 c%则可按下式计算出新生铁的配比:
第三步,确定配比并计算铁合金补加量。
第四步,根据以上计算,最后确定配料比, 写出配料单。
球墨铸铁用生铁规格见表11.5,其含硅、锰 量低,对磷、硫要求也更严格。炼钢生铁主 要用于配低硅铸铁。常用的炼钢生铁有炼08 (L10)等牌号(GB717—82),其含硅量 分别大于0.45%~0.85%和0.85%~1.25%。
合成球墨铸铁生产工艺
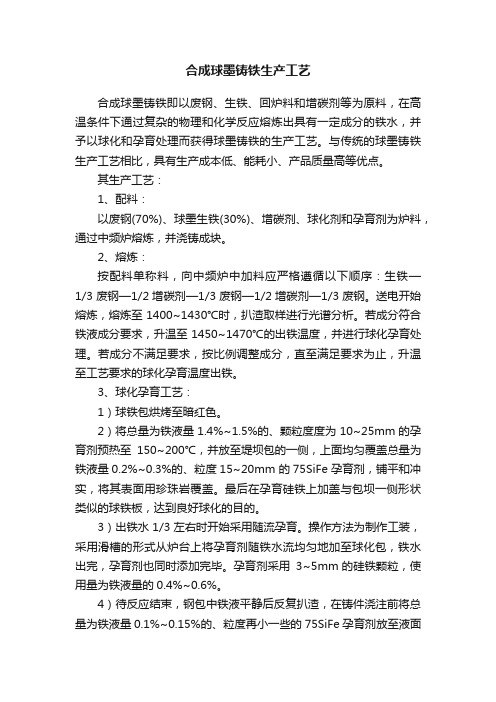
合成球墨铸铁生产工艺合成球墨铸铁即以废钢、生铁、回炉料和增碳剂等为原料,在高温条件下通过复杂的物理和化学反应熔炼出具有一定成分的铁水,并予以球化和孕育处理而获得球墨铸铁的生产工艺。
与传统的球墨铸铁生产工艺相比,具有生产成本低、能耗小、产品质量高等优点。
其生产工艺:1、配料:以废钢(70%)、球墨生铁(30%)、增碳剂、球化剂和孕育剂为炉料,通过中频炉熔炼,并浇铸成块。
2、熔炼:按配料单称料,向中频炉中加料应严格遵循以下顺序:生铁—1/3 废钢—1/2增碳剂—1/3废钢—1/2增碳剂—1/3 废钢。
送电开始熔炼,熔炼至1400~1430℃时,扒渣取样进行光谱分析。
若成分符合铁液成分要求,升温至1450~1470℃的出铁温度,并进行球化孕育处理。
若成分不满足要求,按比例调整成分,直至满足要求为止,升温至工艺要求的球化孕育温度出铁。
3、球化孕育工艺:1)球铁包烘烤至暗红色。
2)将总量为铁液量1.4%~1.5%的、颗粒度度为10~25mm的孕育剂预热至150~200℃,并放至堤坝包的一侧,上面均匀覆盖总量为铁液量0.2%~0.3%的、粒度15~20mm 的75SiFe 孕育剂,铺平和冲实,将其表面用珍珠岩覆盖。
最后在孕育硅铁上加盖与包坝一侧形状类似的球铁板,达到良好球化的目的。
3)出铁水1/3左右时开始采用随流孕育。
操作方法为制作工装,采用滑槽的形式从炉台上将孕育剂随铁水流均匀地加至球化包,铁水出完,孕育剂也同时添加完毕。
孕育剂采用3~5mm 的硅铁颗粒,使用量为铁液量的0.4%~0.6%。
4)待反应结束,钢包中铁液平静后反复扒渣,在铸件浇注前将总量为铁液量0.1%~0.15%的、粒度再小一些的75SiFe孕育剂放至液面上,并反复搅拌,进行瞬时孕育。
4、浇注:按要求将铁液浇注成块。
5、热处理工艺:为避免采用了连续退火工艺对球墨铸铁件进行热处理,出现了产品质量不稳定等问题。
采用更合适的分段退火热处理工艺,即高温石墨化和低温组织转变两阶段退火,以消除白口、降低硬度、改善切削性能。
球墨铸铁铸件的铸造过程及要点注意

球墨铸铁铸件的铸造过程及要点注意球墨铸铁铸件是一种使用球墨铸铁材料制造的重要铸件,广泛应用于工程机械、汽车及石油天然气等行业。
为了保证球墨铸铁铸件的质量和性能,铸造过程中需遵循一定的要点和注意事项。
本文将详细介绍球墨铸铁铸件的铸造过程及要点注意。
一、球墨铸铁铸件的铸造过程1. 原料配制:球墨铸铁的主要原材料包括铁水、石墨、球墨化剂等。
在铸造过程中,按照一定比例将这些原料进行配制,以确保最终产品的质量。
2. 铸型制作:根据铸件的形状和尺寸要求,采用砂型铸造或金属型铸造的方式制作铸型。
其中,砂型铸造是最常用的方法,通过将铁水注入砂型中,使其在砂型中凝固形成铸件。
3. 浇注:在铸造过程中,通过将预热后的铁水倒入铸型中,使铁水充分充塞铸型的腔体,并保证铸件的内部结构均匀。
4. 固化:在浇注完成后,铁水逐渐冷却凝固形成球墨铸铁铸件。
在固化过程中,需要确保铸件充分冷却,以避免产生缺陷和应力集中。
5. 毛坯处理:将固化成型的球墨铸铁铸件进行下线、分条、去砂等处理,得到初步的球墨铸铁毛坯。
6. 热处理:对球墨铸铁毛坯进行正火或表面淬火等热处理,以改善其组织和性能,并消除内部应力。
7. 机械加工:对热处理后的球墨铸铁铸件进行车削、铣削、钻孔等机械加工工艺,使其达到最终的尺寸和形状要求。
8. 表面处理:球墨铸铁铸件表面通常需要进行喷砂、研磨或喷漆等处理,以提高其外观质量和耐腐蚀性能。
9. 检验及修磨:通过对球墨铸铁铸件进行尺寸、硬度、力学性能等多项检测,确保其符合设计要求。
如有不合格的铸件,需要进行修磨或返工处理。
二、球墨铸铁铸件铸造的要点注意1. 熔炼与浇注温度控制:在整个铸造过程中,熔炼温度和浇注温度的控制至关重要。
熔炼温度过高会导致铸件孔洞增加,熔炼温度过低则容易形成夹杂物,浇注温度过高会导致铸件变形,浇注温度过低则容易导致铸件凝固不完全。
2. 浇注方式:合理选择适当的浇注方式对于球墨铸铁铸件的质量具有重要影响。
铁铸件制作配方介绍

铁铸件制作配方介绍全文共四篇示例,供读者参考第一篇示例:铁铸件在工业生产中扮演着非常重要的角色,它们被广泛应用于汽车、机械设备、建筑物以及其他领域。
铁铸件的制作过程需要严格遵循一定的配方,并且需要经过多道工艺流程来完成。
本文将介绍铁铸件制作的配方和工艺流程,帮助读者了解铁铸件的制作过程。
铁铸件的主要成分是铁和碳,其中碳的含量通常在2%~4%之间。
铁铸件通常通过熔铁炉熔炼铁水,然后倒入铸型中进行冷却凝固,最终制成所需形状的铁铸件。
下面将详细介绍铁铸件的制作配方和工艺流程。
1. 铁铸件的配方包括铁水、造型砂、脱模剂等材料。
铁水是最重要的原材料,其含有铁和碳,通过添加其他合金元素来改变铸件的性能。
造型砂是模具的主要材料,用于制作铸件的外形和内部结构。
脱模剂用于减少砂型和铸件之间的粘附力,便于取出铸件。
2. 制作铁铸件的工艺流程包括模具制作、熔炼铁水、浇铸、冷却凝固、清理等步骤。
首先在模具中制作出铸件的外形和内部结构,然后将铁水熔铸到模具中,待冷却凝固后取出铸件,最后清理表面和修整尺寸。
3. 铁铸件的制作过程需要严格控制制度参数,包括铁水的温度、流速和压力,模具的温度和湿度,冷却速度等。
这些参数直接影响铸件的质量和性能,需要经验丰富的操作人员进行控制。
4. 铁铸件的质量和性能受到许多因素的影响,如原材料、工艺流程、设备等。
在选择配方和制度参数时需要考虑这些因素,以确保铁铸件的质量达标。
铁铸件制作是一个复杂的工艺过程,需要严格遵循配方和工艺流程,并且需要经验丰富的操作人员来进行控制。
只有在掌握了铁铸件制作的技术要点和经验后,才能生产出质量优良的铁铸件,满足各种工业领域的需求。
希望本文能够为读者提供一些关于铁铸件制作配方和工艺流程方面的参考,帮助读者更好地了解铁铸件的制作过程。
【2000字】第二篇示例:铁铸件,又称为铸铁件,是一种由铁水铸造而成的金属零部件,它广泛应用于机械设备、汽车工业、建筑工程等领域。
铁铸件具有成本低廉、制造工艺简单、性能稳定可靠等优点,因此在工业生产中得到了广泛的应用。
高铬铸铁配料方法

高铬铸铁配料方法高铬铸铁是一种含有较高铬量的铸铁合金,具有良好的抗腐蚀性能和高温强度,广泛应用于化工、冶金、矿山等领域。
高铬铸铁的配料方法对其性能和质量有着重要影响,下面将详细介绍高铬铸铁的配料方法。
高铬铸铁的配料主要包括铸铁母铁、铬铁、锰铁、石墨、硅铁、硅合金等。
铸铁母铁是高铬铸铁的主要成分,其含量占配料的大部分。
铸铁母铁一般采用优质的生铁和废铁进行配比,以保证合金成分的均匀和稳定。
铬铁是制备高铬铸铁的主要合金原料,其铬含量一般在50%以上。
锰铁主要是为了提高高铬铸铁的硬度和强度,其含量一般在10%-20%之间。
石墨是高铬铸铁中的重要成分,可以提高合金的耐磨性和耐高温性能。
硅铁和硅合金的主要作用是脱氧、增强高铬铸铁的抗氧化性能。
高铬铸铁的配料方法首先需要根据合金的成分要求确定每种原料的配比,然后将各种原料按配比加入炉子中熔化。
在炉子中加入的铸铁母铁应该先起化,然后加入合金原料,保持一定的熔化温度和时间,使得原料充分混合和溶解。
在加入硅铁和硅合金时,需要控制好加入的速度和温度,防止因为速度过快或温度过高引起的剧烈反应和喷溅。
最后将炉子中的合金液体倒入模具中进行冷却,得到成型的高铬铸铁。
高铬铸铁的配料方法还需要考虑原料的纯度和质量问题,选择合适的原料供应商进行采购。
对于一些含有杂质的原料,需要进行预处理和精炼,以保证高铬铸铁的成分均匀和稳定。
同时,还需要根据生产工艺和设备条件合理选择原料的粒度和形态,以便于炉内熔化和混合。
另外,还需要根据合金成分的要求和产品性能的要求对配料方法进行调整和优化,以获得满足客户需求的高铬铸铁产品。
总之,高铬铸铁的配料方法是制备优质高铬铸铁产品的基础,合理选择原料的配比和加工工艺是保证产品质量和性能的关键。
配料过程中还需要注意原料的质量和纯度,进行合适的预处理和精炼,保证高铬铸铁的成分均匀和稳定。
通过不断的优化和改进配料方法,可以获得更优质的高铬铸铁产品,满足不同领域的使用需求。
球墨铸铁生产要点(精)

球墨铸铁生产要点关键字:球墨铸铁一、原材料:1.球墨铸铁用生铁,Q16或Q12。
2.硅铁:75%硅铁。
3.球化剂:稀土镁硅铁合金,FeSiMg10RE7或FeSiMg9RE9。
4.优质低硫焦炭。
二、配料:废钢0~20%、球墨铸铁用生铁80~95%、回炉料0~10%应使化学成分在:3.3~3.8%C;2.5~3.0%Si; Mn≤0.40%; P≤0.07%;S≤0.03%范围。
三、关键点:1.铁水包:冲入法采用的球化处理包应搪成上下直径相同的圆桶形,并使其深度H与内径D之比H/D=1.5~2,在局部适当地方修出包嘴。
包底可修成堤坝式或凹坑式。
普通浇包不宜使用。
2.球化处理:(1)加入量为1.0~2.2%,原铁液硫含量为0.04%时取下限;硫含量为0.08%时取上限。
应保证沸腾反应持续1~2分钟,时间短则可以肯定球化不良。
(2)加入方法:球化剂不可松散地放在包底或放在铁液冲得着的地方。
球化剂应集中地放在包底紧靠出铁口的一例,并用砂冲子(平头)适度地将其上表面舂平,覆盖一层无油、无锈的球铁屑或孕育剂再撒上适量的珍珠岩,或者盖以红热的带有铸造小孔的铁板。
(3)出铁后,应扒除球化处理残渣,撒上足够厚的一层珍珠岩或草灰。
3.孕育处理:球化处理后的铁液需加0.8~1.6%的75%硅铁,粒度10~20mm,最终应使碳当量在4.6~4.7%为好。
附注:球化剂:包钢产XtMg8-7 球化工艺:冲入法、堤坝式加入顺序:脱硫剂——XtMg 合金——硅铁——草灰(珍珠岩),然后在其上盖4~5mm铁板,冲入包内的铁水达2/3时,暂停冲入,待球化反应渐趋平稳时,再补充另1/3铁水,同时将孕育剂加入。
脱硫剂为Na2CO3,加入量0.2~0.3%. 孕育剂SiFe75:块度10~20mm,加入前150~200℃预热1h,1.2~1.3%以三种方式加入:(1)包内孕育:加入0.6~0.65%;(2)随流孕育:加入0.55~0.65% ;(3)为防止孕育衰退,在浇注过程中,在包内进行浮硅孕育,0.05~0.10%;根据生产实践的总结,Mg和Xt的衰退速度为0.001~0.004%/分;0.0006~0.001%/分。
铸件配料实用技术(生铁锭与废钢铁)

一、生铁锭生铁锭是熔制铸铁和铸钢的最主要金属炉料,约占配料重量的20%~100%,它的化学成分是否稳定、硫磷含量和有害杂质含量是否低,直接关系到所熔制铸铁和铸钢的质量。
合理的选用生铁锭也是获得低成本配料的有效方法之一。
生铁锭可分为铸造生铁、球墨铸铁专用生铁、炼钢生铁、高纯生铁和特种生铁等,均有标准,见表2-1-1至表2-1-7。
生产上常用生铁的化学成分和微量元素含量,见表2-1-8至表2-1-13。
通常:熔制灰铸铁时,应选用铸造生铁。
硅的质量分数为2.0%~3.0%的铸造生铁可用于熔制低牌号灰铸铁;硅的质量分数为1.2%~2.0%的铸造生铁可用于熔制高牌号灰铸铁。
熔制球墨铸铁时,应选用球墨铸铁专用生铁,但也可选用低硅、低锰和低磷硫的铸造生铁或炼钢生铁。
对于要求特别高的球墨铸铁也可选用高纯生铁。
球墨铸铁所用新生铁的硅的质量分数一般在0.8%~1.75%的范围内选择。
熔制大断面球墨铸铁件或铸态铁索体球墨铸铁件时,生铁的锰含量希望低于0.3%,不应超过0.5%,越低越好;熔制珠光体、贝氏体、退火铁索体球墨铸铁体时,生铁的锰的质量分数应小于0.6%;熔制正火珠光体球墨铸铁的中小型铸件时,生铁的锰的质量分数可适当放宽,一般也不要超过0.8%。
对于低温下工作的铁素体韧性球墨铸铁件和其他要求韧性较高的球墨铸铁件,应选用磷的质量分数小于0.07%的生铁。
一般球墨铸铁件用生铁磷的质量分数不应大于0.1%;硫的质量分数应限制在0.05以下;反球化元素不得过量ωTe<0.01%、ωTi<0.3%、ωSn<0.09%、ωSb<0.2%、ωPb<0.2%、ωBi<0.05%。
熔制蠕墨铸铁时,应参照熔制球墨铸铁的要求选用生铁。
熔制可锻铸铁时,一般只加入10%左右的生铁量,主要是为了提高碳含量,因此含磷、硫和铬低的铸造生铁、炼钢生铁和再生铁均能使用。
熔制特种铸铁时,应尽量选用含相应元素高的铸造生铁或特种生铁。
电炉灰铁铸件生产配料指导

HT300 成分名称 壁厚 配料实例 10-30 30-60
C 3.0-3.3 2.8-3.1
Si 1.5-1.8 1.3-1.6
Mn 0.8-1.0 1.0-1.2
P <0.15
S ≤0.12
1. 12﹟新生300 块旧生250 碎回生300 废钢150 锰9-11 硅孕育4-7 2. 12﹟新生300 块旧生250 碎回生250 废钢200 65锰11-13 硅孕育3-6
电炉灰铁铸件生产配料指导
HT200 成分名称 壁厚 配料实例 10-30 30-60 C 3.2-3.5 3.0-3.3 Si 1.7-2.0 1.4-1.7 Mn 0.5-.07 0.7-0.9 P <0.15 S ≤0.12 65锰3-5 65锰5-7 硅孕育2-4 硅孕育1-3
1. 22﹟新生300 块旧生250 碎回生350 废钢100 2. 22﹟新生300 块旧生250 碎回生320 废钢130
1.原则厚大件成分:C﹑Si取下限,锰取上限,小件反之。 2.本表配料原则以电炉熔炼计算,冲天炉还需考虑炉况变化因素。 3.浇注温度原则在1400℃左右,小件可略高,大件可略低。
HT250 成分名称 壁厚 配料实例 10-30 30-60
C 3.1-3.4 2.9-3.2
Si 1.6-1.9 1.4-1.7
Mn 0.7-0.9 0.9-1.1
P <0.15
S ≤0.12 65锰5-7 65锰7-9 硅孕育2-4 硅孕育1-3
1. 22﹟新生300 块旧生250 碎回生320 废钢130 2. 22﹟新生300 块旧生250 碎回生300 废钢150
球墨铸铁铸件配料实用技术

球铁铁液表面有一 铁 液 表 面 膜 观 察 层很 厚 的 氧 化 膜, 因 为球铁的表面张力比 灰铁 大, 净化效果较 大, 铁液表面与灰铸 铁有明显区别 稀土镁球铁的表面 特征较纯镁球铁差 铁液表面平静, 覆盖 一层皱皮, 温度下降 后 会出现五颜六色的浮皮 表面现象介于两者之间 表面翻腾严重, 氧化皮极 少, 并集中在中央
小火苗
不球化
看不到火苗
无火苗
火花判别球化的方法
炉 前 快 速 金 相 检 查
以 直 径 !&" ’ &" 或 !(" ’ (" 试棒, 凝 固后 淬 水 冷 却, 在砂 轮上 磨 去 表 面, 经粗 磨和 抛 光, 用显微镜 观察。但 要 注 意, 由 于铸 件 比 试 棒 大, 试 棒球化级别要订的比 铸件高一些 按球化标准评级 此法可在 &#)* 内完成, 比较准确可靠
磷
稍有降低
一般降低 #有降低
一般降低 # ’ ( 0 ’
由于加镁处理后, 铁液温度下降和搅拌作 用, 促进了锰的脱硫作用和锰夹渣的上浮
锰 球化剂中锰几乎全 部转入铁液 当生产珠光体球铁时, 有时球化剂中配有 ! .2 $%’ ( !%’
增加
硅
增加
一般增加 % & ) ’ ( % & 3’
第三章 表 ! " # " $%
方法名称 方法简述
铸铁件配料实用技术
球墨铸铁铁液质量的炉前控制
球 化 鉴 别
中间有明显的缩松, 三角试样两边有凹缩 $ * 球化良好的断口是银白色, 三 角 试 样 观 察 待试样冷至暗红色 (&’’ ( %’’) ) 取出淬 火, 打断后看三角试 样上 的 断 面 颜 色、 中 心缩松等情况 激水后砸开有电石气味 ! * 敲击时有钢声,
淬火铸件的配料分析

淬火铸件的配料分析对于此种材料一般按照HT300~HT350配料,现有的主料配料两种:1│废钢│生铁│回炉铁││60% │5% │35% │─┼──┼──┼───┤2│废钢│生铁│ │├──┼──┼───┤│80%│20%│ │─┴──┴──┴───┘由于第1种配料充分的利用了回炉铁,所以有效地降低了成本。
需要注意的是,如果使用第二种配比,由于后序需要加入辅料炭精比例较大。
所以,一定要选择经过高温处理的石墨,C(碳)成片状排列的高质量炭精。
否则,未溶的石墨会在铸件的加工面上留下质点,影响加工后铸件的质量和美观。
现有的HT300料级配料单(如下),每批料827kga。
┌───┬──┬───┬──┬───┬───┐│生铁│废钊│回炉铁│炭精│75SiFe│65MnFe│├───┼──┼───┼──┼───┼───┤│32 │480 │288 │18 │6 │3 │└───┴──┴───┴──┴───┴───┘废钢的作用是提供一定量的微量元素,如N,等,这些元素虽然含量特别低,但对于铸铁的作用却不可忽视,它的另一个作用是降碳。
生铁的作用是增碳和增加核心,且提供一部分的微量元素。
回炉铁可以有效的降低成本,并且有利于环境保护。
一般来说,炉料配比的选择可以根据材料的市场价格及铁级决定,这样既可以降低成本,又可满足要求。
HT300料级的炉前,炉后成分(见表3) 。
┌───┬─────┬────┬────┐│ │C │Si │Mn │├───┼─────┼────┼────┤│炉前%│3.02-3.22 │1.4-1.5 │0.8-0.9 │├───┼─────┼────┼────┤│炉后%│3.06-3.15 │1.7-1.8 │0.8-0.9 │└───┴─────┴────┴────┘此种成分对于一般厚度为在45mm以下的机床铸件导轨,可以使其硬度达到170HBS 以上,基体组织珠光体大于95%。
但对于那些厚大导轨铸件且需要后序淬火处理的床身和立柱,显得不足。
铁铸件制作配方介绍

铁铸件制作配方介绍全文共四篇示例,供读者参考第一篇示例:铁铸件是一种常见的金属制品,具有良好的耐磨、耐腐蚀和强度高的特点,在机械制造、建筑工程、汽车制造等领域有着广泛的应用。
铁铸件的制作过程中关键的一步就是铁铸件制作配方的确定,这直接影响到铁铸件的质量和性能。
接下来,我们就来详细介绍一下铁铸件制作配方的相关知识。
一、铁铸件制作配方概述铁铸件的原料主要由铁和一定量的碳组成,碳的含量在2%-4%左右。
通常情况下,还会加入少量的硅、锰、磷等元素,以提高铁铸件的硬度、韧性和耐磨性。
铁铸件制作配方的选择取决于具体使用要求,不同的配方会影响铁铸件的材质和性能。
1. 铁料:铁是铁铸件的主要原料,可选用生铁、废钢等。
生铁主要包括灰口铸铁、球墨铸铁等,灰口铸铁具有优良的流动性和耐磨性,球墨铸铁则具有良好的韧性和强度。
废钢也是一种常用的铁铸件原料,主要包括废钢丝、废钢板等,可以降低成本。
2. 碳含量:碳是铁铸件中的重要元素,对铁铸件的硬度和强度有着重要影响。
通常情况下,铁铸件中的碳含量控制在2%-4%之间,过高或者过低都会影响铁铸件的性能。
3. 硅、锰等元素:硅和锰是常用的合金元素,可以提高铁铸件的硬度和强度,同时还可以改善铁的流动性和耐磨性。
磷是一种常见的杂质元素,过高的磷含量会导致铁铸件的脆性增加。
4. 其他合金元素:除了上述的元素外,还可以根据需要添加其他合金元素,如铬、钼等,以满足不同领域的使用要求。
确定铁铸件制作配方需要考虑以下几个方面:1. 使用要求:根据铁铸件的具体使用要求确定碳含量、硅含量、锰含量等元素的含量,以满足不同领域的需求。
2. 原料选择:根据铁料的品种和质量选择合适的原料,如生铁、废钢等。
3. 合金元素的选择:根据铁铸件的使用环境和要求选择合适的合金元素,以提高铁铸件的性能。
4. 配方调整:在确定了铁铸件的基本配方后,需要进行小规模试验,不断调整配方,以获得最佳的铁铸件制作配方。
四、铁铸件制作过程铁铸件的制作过程主要包括原料准备、熔炼、浇注、冷却、清理等步骤。
铸造配料计算
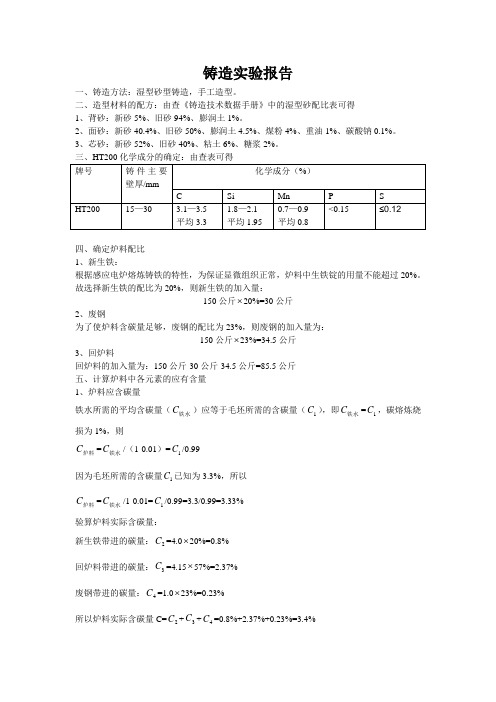
铸造实验报告一、铸造方法:湿型砂型铸造,手工造型。
二、造型材料的配方:由查《铸造技术数据手册》中的湿型砂配比表可得 1、背砂:新砂5%、旧砂94%、膨润土1%。
2、面砂:新砂40.4%、旧砂50%、膨润土4.5%、煤粉4%、重油1%、碳酸钠0.1%。
3、芯砂:新砂52%、旧砂40%、粘土6%、糖浆2%。
四、确定炉料配比 1、新生铁:根据感应电炉熔炼铸铁的特性,为保证显微组织正常,炉料中生铁锭的用量不能超过20%。
故选择新生铁的配比为20%,则新生铁的加入量:150公斤⨯20%=30公斤2、废钢为了使炉料含碳量足够,废钢的配比为23%,则废钢的加入量为:150公斤⨯23%=34.5公斤3、回炉料回炉料的加入量为:150公斤-30公斤-34.5公斤=85.5公斤 五、计算炉料中各元素的应有含量 1、炉料应含碳量铁水所需的平均含碳量(铁水C )应等于毛坯所需的含碳量(1C ),即铁水C =1C ,碳熔炼烧损为1%,则炉料C =铁水C /(1-0.01)=1C /0.99因为毛坯所需的含碳量1C 已知为3.3%,所以炉料C =铁水C /1-0.01=1C /0.99=3.3/0.99=3.33%验算炉料实际含碳量:新生铁带进的碳量:2C =4.0⨯20%=0.8% 回炉料带进的碳量:3C =4.15⨯57%=2.37% 废钢带进的碳量:4C =1.0⨯23%=0.23%所以炉料实际含碳量C=2C +3C +4C =0.8%+2.37%+0.23%=3.4%2、炉料应含硅量:铁水所需的平均含硅量(铁水Si )应等于毛坯所需的含硅量(1Si ),即铁水Si =1Si ,硅熔炼烧损为6%,则炉料Si =铁水Si /(1-0.06)=1Si /0.94因为毛坯所需的含硅量1Si 已知为1.95%,所以炉料Si =铁水Si /(1-0.06)=1Si /0.94=1.95/0.94=2.07%验算炉料实际含硅量:新生铁带进的含硅量:2Si =1.85%⨯20%=0.37% 回炉料带进的含硅量:3Si =1.5%⨯57%=0.855% 废钢带进的含硅量:4Si =0.26%⨯23%=0.05%所以炉料实际含硅量Si =2Si +3Si +4Si =0.37%+0.855%+0.06%=1.285% 炉料中尚缺硅量=炉料应含硅量-炉料中实际含硅量=2.07%-1.285%=0.785% 3、炉料应含锰量铁水所需的平均含锰量(铁水Mn )应等于毛坯所需的含锰量(1Mn ),即铁水Mn =1Mn ,锰熔炼烧损为8%,则因为毛坯所需的含锰量1Mn 已知为0.8%,所以炉料Mn =铁水Mn /(1-0.08)=0.8//0.92=0.87%验算炉料实际含锰量:新生铁带进的锰量:2Mn =0.03%⨯20%=0.006% 回炉料带进的锰量:3Mn =0.7%⨯57%=0.399% 废钢带进的锰量:4Mn =0.25%⨯23%=0.058%所以炉料中实际含锰量Mn =2Mn +3Mn +4Mn =0.006%+0.399%+0.058%=0.463%炉料中尚缺锰量=炉料应含锰量-炉料实际含锰量=0.87%-0.463%=0.407% 六、计算铁合金加入量 1、硅铁加入量补加含硅75%的硅铁的百分数=炉料中尚缺的硅量(%)/硅铁的含硅量(%)=0.785/75%=1.05% 即每100公斤炉料补加1.05公斤含硅75%的硅铁 则150公斤炉料补加含硅75%的硅铁量为: 1.5⨯1.05公斤=1.57公斤2、锰铁加入量补加含锰65%的锰铁的百分数=炉料中尚缺的锰铁(%)/锰铁的含量(%)=0.407%/65%=0.626%即每100公斤炉料补加0.626公斤含锰65%锰铁则则150公斤炉料补加含锰65的锰铁量为:1.5 0.626公斤=0.939公斤。
铸造球铁熔铁配料规范
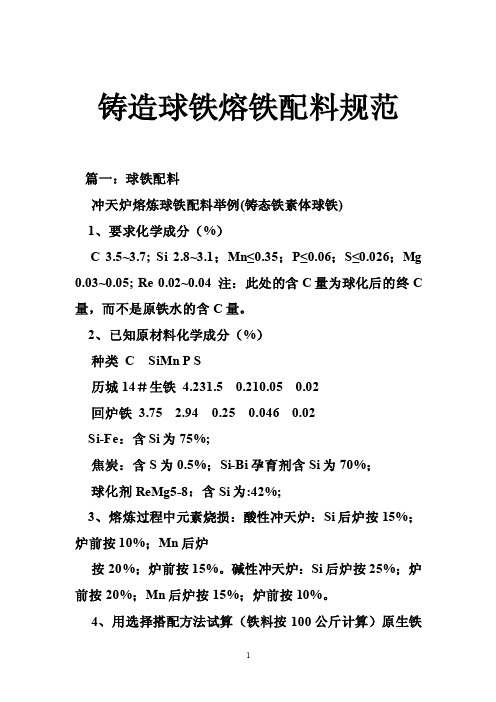
铸造球铁熔铁配料规范篇一:球铁配料冲天炉熔炼球铁配料举例(铸态铁素体球铁)1、要求化学成分(%)C 3.5~3.7; Si 2.8~3.1;Mn≤0.35;P≤0.06;S≤0.026;Mg0.03~0.05; Re 0.02~0.04 注:此处的含C量为球化后的终C 量,而不是原铁水的含C量。
2、已知原材料化学成分(%)种类C SiMn P S历城14#生铁4.231.5 0.210.05 0.02回炉铁3.75 2.94 0.25 0.046 0.02Si-Fe:含Si为75%;焦炭:含S为0.5%;Si-Bi孕育剂含Si为70%;球化剂ReMg5-8:含Si为:42%;3、熔炼过程中元素烧损:酸性冲天炉:Si后炉按15%;炉前按10%;Mn后炉按20%;炉前按15%。
碱性冲天炉:Si后炉按25%;炉前按20%;Mn后炉按15%;炉前按10%。
4、用选择搭配方法试算(铁料按100公斤计算)原生铁65%;回炉铁35%。
5、核算炉料中的含C量C炉料=4.23%×65%+3.75×35%=4.06%由于球铁中碳当量比较高,在冲天炉熔炼条件下要减碳(当碳当量>3.6%时一般要减碳3~8%),如按5.5%计算,则从炉内出来的铁水含C量为:4.06%1×(1-5.5%)=3.84%;同时在球化处理过程中还要降碳0.1~0.2%(原因:○2一部分过饱和C以石墨形式析出,上浮进入熔渣)如球化反应使碳烧损;○按0.15%计算,则铁水最终含C量为:3.84%—0.15%=3.69%(符合3.5~3.7%的要求)6、含Si量的计算铁水最终含Si量包括以下几个部分:1)炉料中的含Si量Si炉料:Si炉料=1.5%×65%+2.94×35%=2.0%,烧损按15%计算,则从炉内出来的铁水含Si量为:2.0%×(1-15%)=1.7%; 2)一次孕育按0.2% 75 Si-Fe(覆盖在球化剂上),进入铁水的硅量Si孕育Ⅰ=0.2%×75%×(1-10%)=0.14%;3)二次孕育按0.4% 75 Si-Fe(在出铁槽加入),进入铁水的硅量Si孕育Ⅱ=0.4%×75%×(1-10%)=0.27%;4)三次孕育按0.2% Si-Bi(浇包孕育),进入铁水的硅量Si孕育Ⅲ=0.2%×70%×(1-10%)=0.13%;5)球化剂加入量按 1.7%,则球化剂进入铁水的硅量Si 球化=1.7%×42%×(1-10%)=0.64%;6)铁水终Si含量为上述1)~5)之和(如果生产管卡,还要计入0.1~0.2%的小颗粒75 Si-Fe浇包四次孕育)即Si 终=1.7%+0.14%+0.27%+0.13%+0.64%=2.88%(符合2.8~3.1%的要求)7、含Mn量的计算炉料中的含Mn量Mn炉料:Mn炉料=0.21%×65%+0.25×35%=0.224%,去掉烧损,则从炉内出来的铁水含Mn量为:0.224%×(1-20%)=0.18%;另外,稀土镁合金中一般允许含Mn≤4%,若以4%计(实际应根据验收化验的具体含量计算),并去掉烧损,则进入铁水的Mn量为:1.7%×4%×(1-15%)=0.058%,铁水中的总Mn量为两者之和即0.18%+0.058%=0.238%,在球化处理过程中由于Mn与S作用和Mn夹渣上浮,一般Mn含量要下降3%~5%,若以4%计算,则铁水的终Mn量Mn 终=0.238%×(1-4%)=0.228%(符合终Mn≤0.35的要求)。
铸造配料计算
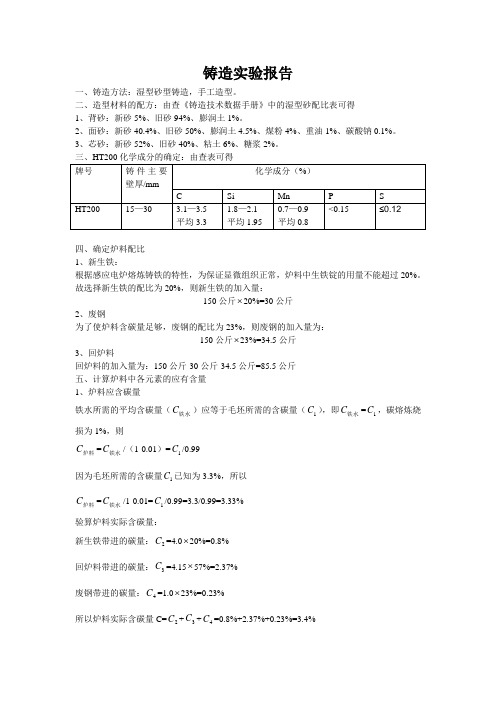
铸造实验报告一、铸造方法:湿型砂型铸造,手工造型。
二、造型材料的配方:由查《铸造技术数据手册》中的湿型砂配比表可得 1、背砂:新砂5%、旧砂94%、膨润土1%。
2、面砂:新砂40.4%、旧砂50%、膨润土4.5%、煤粉4%、重油1%、碳酸钠0.1%。
3、芯砂:新砂52%、旧砂40%、粘土6%、糖浆2%。
四、确定炉料配比 1、新生铁:根据感应电炉熔炼铸铁的特性,为保证显微组织正常,炉料中生铁锭的用量不能超过20%。
故选择新生铁的配比为20%,则新生铁的加入量:150公斤⨯20%=30公斤2、废钢为了使炉料含碳量足够,废钢的配比为23%,则废钢的加入量为:150公斤⨯23%=34.5公斤3、回炉料回炉料的加入量为:150公斤-30公斤-34.5公斤=85.5公斤 五、计算炉料中各元素的应有含量 1、炉料应含碳量铁水所需的平均含碳量(铁水C )应等于毛坯所需的含碳量(1C ),即铁水C =1C ,碳熔炼烧损为1%,则炉料C =铁水C /(1-0.01)=1C /0.99因为毛坯所需的含碳量1C 已知为3.3%,所以炉料C =铁水C /1-0.01=1C /0.99=3.3/0.99=3.33%验算炉料实际含碳量:新生铁带进的碳量:2C =4.0⨯20%=0.8% 回炉料带进的碳量:3C =4.15⨯57%=2.37% 废钢带进的碳量:4C =1.0⨯23%=0.23%所以炉料实际含碳量C=2C +3C +4C =0.8%+2.37%+0.23%=3.4%2、炉料应含硅量:铁水所需的平均含硅量(铁水Si )应等于毛坯所需的含硅量(1Si ),即铁水Si =1Si ,硅熔炼烧损为6%,则炉料Si =铁水Si /(1-0.06)=1Si /0.94因为毛坯所需的含硅量1Si 已知为1.95%,所以炉料Si =铁水Si /(1-0.06)=1Si /0.94=1.95/0.94=2.07%验算炉料实际含硅量:新生铁带进的含硅量:2Si =1.85%⨯20%=0.37% 回炉料带进的含硅量:3Si =1.5%⨯57%=0.855% 废钢带进的含硅量:4Si =0.26%⨯23%=0.05%所以炉料实际含硅量Si =2Si +3Si +4Si =0.37%+0.855%+0.06%=1.285% 炉料中尚缺硅量=炉料应含硅量-炉料中实际含硅量=2.07%-1.285%=0.785% 3、炉料应含锰量铁水所需的平均含锰量(铁水Mn )应等于毛坯所需的含锰量(1Mn ),即铁水Mn =1Mn ,锰熔炼烧损为8%,则因为毛坯所需的含锰量1Mn 已知为0.8%,所以炉料Mn =铁水Mn /(1-0.08)=0.8//0.92=0.87%验算炉料实际含锰量:新生铁带进的锰量:2Mn =0.03%⨯20%=0.006% 回炉料带进的锰量:3Mn =0.7%⨯57%=0.399% 废钢带进的锰量:4Mn =0.25%⨯23%=0.058%所以炉料中实际含锰量Mn =2Mn +3Mn +4Mn =0.006%+0.399%+0.058%=0.463%炉料中尚缺锰量=炉料应含锰量-炉料实际含锰量=0.87%-0.463%=0.407% 六、计算铁合金加入量 1、硅铁加入量补加含硅75%的硅铁的百分数=炉料中尚缺的硅量(%)/硅铁的含硅量(%)=0.785/75%=1.05% 即每100公斤炉料补加1.05公斤含硅75%的硅铁 则150公斤炉料补加含硅75%的硅铁量为: 1.5⨯1.05公斤=1.57公斤2、锰铁加入量补加含锰65%的锰铁的百分数=炉料中尚缺的锰铁(%)/锰铁的含量(%)=0.407%/65%=0.626%即每100公斤炉料补加0.626公斤含锰65%锰铁则则150公斤炉料补加含锰65的锰铁量为:1.5 0.626公斤=0.939公斤。
铸造配料计算
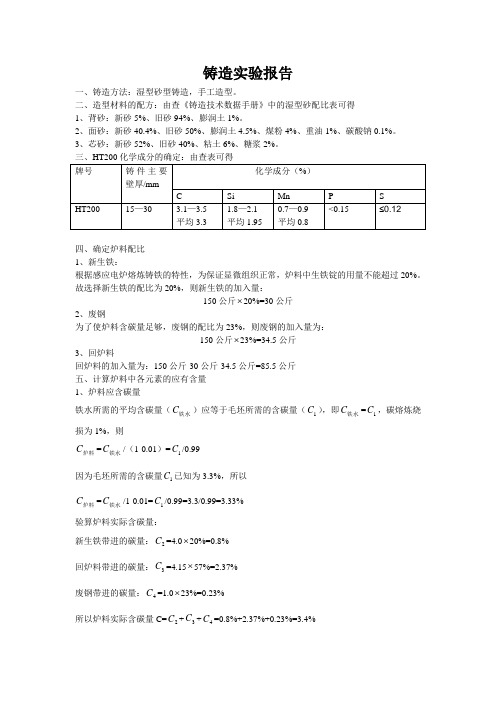
铸造实验报告一、铸造方法:湿型砂型铸造,手工造型。
二、造型材料的配方:由查《铸造技术数据手册》中的湿型砂配比表可得 1、背砂:新砂5%、旧砂94%、膨润土1%。
2、面砂:新砂40.4%、旧砂50%、膨润土4.5%、煤粉4%、重油1%、碳酸钠0.1%。
3、芯砂:新砂52%、旧砂40%、粘土6%、糖浆2%。
四、确定炉料配比 1、新生铁:根据感应电炉熔炼铸铁的特性,为保证显微组织正常,炉料中生铁锭的用量不能超过20%。
故选择新生铁的配比为20%,则新生铁的加入量:150公斤⨯20%=30公斤2、废钢为了使炉料含碳量足够,废钢的配比为23%,则废钢的加入量为:150公斤⨯23%=34.5公斤3、回炉料回炉料的加入量为:150公斤-30公斤-34.5公斤=85.5公斤 五、计算炉料中各元素的应有含量 1、炉料应含碳量铁水所需的平均含碳量(铁水C )应等于毛坯所需的含碳量(1C ),即铁水C =1C ,碳熔炼烧损为1%,则炉料C =铁水C /(1-0.01)=1C /0.99因为毛坯所需的含碳量1C 已知为3.3%,所以炉料C =铁水C /1-0.01=1C /0.99=3.3/0.99=3.33%验算炉料实际含碳量:新生铁带进的碳量:2C =4.0⨯20%=0.8% 回炉料带进的碳量:3C =4.15⨯57%=2.37% 废钢带进的碳量:4C =1.0⨯23%=0.23%所以炉料实际含碳量C=2C +3C +4C =0.8%+2.37%+0.23%=3.4%2、炉料应含硅量:铁水所需的平均含硅量(铁水Si )应等于毛坯所需的含硅量(1Si ),即铁水Si =1Si ,硅熔炼烧损为6%,则炉料Si =铁水Si /(1-0.06)=1Si /0.94因为毛坯所需的含硅量1Si 已知为1.95%,所以炉料Si =铁水Si /(1-0.06)=1Si /0.94=1.95/0.94=2.07%验算炉料实际含硅量:新生铁带进的含硅量:2Si =1.85%⨯20%=0.37% 回炉料带进的含硅量:3Si =1.5%⨯57%=0.855% 废钢带进的含硅量:4Si =0.26%⨯23%=0.05%所以炉料实际含硅量Si =2Si +3Si +4Si =0.37%+0.855%+0.06%=1.285% 炉料中尚缺硅量=炉料应含硅量-炉料中实际含硅量=2.07%-1.285%=0.785% 3、炉料应含锰量铁水所需的平均含锰量(铁水Mn )应等于毛坯所需的含锰量(1Mn ),即铁水Mn =1Mn ,锰熔炼烧损为8%,则因为毛坯所需的含锰量1Mn 已知为0.8%,所以炉料Mn =铁水Mn /(1-0.08)=0.8//0.92=0.87%验算炉料实际含锰量:新生铁带进的锰量:2Mn =0.03%⨯20%=0.006% 回炉料带进的锰量:3Mn =0.7%⨯57%=0.399% 废钢带进的锰量:4Mn =0.25%⨯23%=0.058%所以炉料中实际含锰量Mn =2Mn +3Mn +4Mn =0.006%+0.399%+0.058%=0.463%炉料中尚缺锰量=炉料应含锰量-炉料实际含锰量=0.87%-0.463%=0.407% 六、计算铁合金加入量 1、硅铁加入量补加含硅75%的硅铁的百分数=炉料中尚缺的硅量(%)/硅铁的含硅量(%)=0.785/75%=1.05% 即每100公斤炉料补加1.05公斤含硅75%的硅铁 则150公斤炉料补加含硅75%的硅铁量为: 1.5⨯1.05公斤=1.57公斤2、锰铁加入量补加含锰65%的锰铁的百分数=炉料中尚缺的锰铁(%)/锰铁的含量(%)=0.407%/65%=0.626%即每100公斤炉料补加0.626公斤含锰65%锰铁则则150公斤炉料补加含锰65的锰铁量为:1.5 0.626公斤=0.939公斤。
球墨铸铁生产方法

一.球墨铸铁生产计算方法
1.铸造`球铁用料a生铁:含硫低生铁通常用本溪产地Q10 Q12。
b回炉料:自己家已知成分水冒口。
C废钢。
最好用牌号一直的。
2.球化剂。
一般用7-8XTMg 3-8XtMg(小件多用)
3.孕育剂。
Si75粒度3-5小件硅钡孕育剂2-5粒度(做二次孕育作用)
二.球墨铸铁配料计算法
1.生铁硅的计算方法。
比如配料Q10生铁50% 回炉料40% 废钢10%
已知生铁含硅Si生=0.89%si 回炉料(根据化验或者前一天配料数)si回=2.6% si球化剂中含硅量(大部分含40-45%si)
Si终=si生*50+si回*40%+si球*球化剂用量(根据用包大小加入量1.2-1.4%)
其它成分炉料计算方法大致相同
三.装料方法
1.把称好的炉料按顺序投放依次投放炉中增碳剂-废钢-生铁-回炉料。
2.炉料装入要少100kg.溶化化后浇注碳硅仪浇注调整炉料。
3.炉温升到1530-1580出炉
4.球化包包底要按如图方式(底坑必须大于球化剂堆积体积)
1)装球化剂按比例投入摊平,捣实。
2)盖上球铁铁削(块度越小越好)均与捣实。
3)撒入少许聚渣剂(不要全盖上防止凝死)
2)铁水温度达到要求时开始倾转炉。
按图5方向注入2/3水停住。
球化包开始反应同时盖上铁盖(防止溅出)。
3)待反应接近尾声时倒入剩余铁水同时把孕育剂顺流加到包里,撒上集渣剂搅拌打渣。
4)浇注三角试片,暗红色取出用水极冷。
取出看两边缩凹中间有缩松。
断口银白色为合格。
铸铁配料计算公式表

铸铁配料计算公式表
以下是常见的铸铁配料计算公式表,用于计算铸铁材料中各种元素或化合物的配料比例:
1. 石墨含量计算:
石墨含量 = (石墨重量 / 总重量) * 100%
2. 硅含量计算:
硅含量 = (硅重量 / 总重量) * 100%
3. 碳当量计算:
碳当量 = 碳含量 + (硅含量 / 3.5) + (磷含量 / 10) + (硫含量 / 32)
4. 硫含量计算:
硫含量 = (硫重量 / 总重量) * 100%
5. 磷含量计算:
磷含量 = (磷重量 / 总重量) * 100%
6. 碳含量计算:
碳含量 = (碳重量 / 总重量) * 100%
以上公式中,总重量指的是铸铁材料的总重量,而各种元素(如碳、硅、磷、硫)的重量指的是这些元素在配料中的重量。
具体的配料比例和配方可能因不同的铸铁材料类型(如灰铁、球墨铸铁)以及工艺要求而有所不同。
因此,在实际应用中,应根据具体的铸铁材料和要求来选择合适的配方和计算公式。
铸造铁的制作方法

铸造铁的制作方法
铸造铁是一种重要的金属加工技术,其制作过程可以分为以下几个步骤:
1. 原料准备:首先需要准备铁矿石、焦炭和石灰石等原料。
将铁矿石破碎并加入高炉中,在高温下与焦炭反应,产生还原气体,使铁矿石还原成铁;同时,加入石灰石可以减少杂质的生成。
2. 炼铁:将原料在高炉中加热到1500℃以上,使铁矿石还原成液态铁,并将杂质转化为熔渣。
熔渣会浮在铁水上,可以通过炉底的出渣口排出。
3. 铸造:将炼制好的液态铁倒入铸型中,待铁水凝固后,取出铸件。
铸造过程需要注意温度、铸型的设计以及液态铁的流动性等因素。
4. 热处理:铸件在铸造后需要进行热处理,以改善其组织和性能。
常见的热处理方法包括退火、淬火、正火等。
以上就是铸造铁的制作方法,这种技术广泛应用于机械制造、汽车制造、建筑等领域。
- 1 -。
- 1、下载文档前请自行甄别文档内容的完整性,平台不提供额外的编辑、内容补充、找答案等附加服务。
- 2、"仅部分预览"的文档,不可在线预览部分如存在完整性等问题,可反馈申请退款(可完整预览的文档不适用该条件!)。
- 3、如文档侵犯您的权益,请联系客服反馈,我们会尽快为您处理(人工客服工作时间:9:00-18:30)。
铸铁件配料方法,及锰铁铬铁加入量配比HT250是珠光体灰铸铁。
化学成分:碳C :3.16~3.30硅Si:1.79~1.93锰Mn:0.89~1.04硫S :0.094~0.125磷P :0.120~0.170根据化学成分考虑原料的成分及烧损就可以知道配料了影响铸铁、铸钢件组织和性能的因素,有化学成分、孕育(变质)处理、冷却速度、炉料的“遗传性”、铁水过热温度等,在这几个因素中,化学成分含量的高低对铸件物理性能的影响相对更大些,而且是第一因素。
所以在生产过程中,根据铸件物理性能的要求,正确的配料或调料,严格控制材质的各化学成分含量尤为重要。
在生产实践中,作为冶炼技术人员和炉工来说,配料和调料应该是熟练掌握的一般性技术问题。
但是对予刚毕业的学生和大多数炉工来说,欲能系统、灵活的掌握,也确非易事。
要想控制铸件的化学成分与配料,必须事先了解以下几下问题:1、铸件的目标化学成分。
2、库存各种金属炉料的化学成分。
3、各种炉料在冶炼过程中化学成分的增减变化率。
4、配料方法。
一、目标化学成分现在大部分铸件,根据其牌号要求的不同,国标中已做出了相应的要求,从铸造手册中即可查到。
但是随着科技的进步,根据铸件的服役状况,市场需要更多物理性能各不相同的铸件,并对铸件的综合性能质量提出了更高的要求,科研单位也不断研究出新材质而取代旧材质,例如某水泥研究设计院研究的“中碳多元合金钢”,成功的代替了原需进口的球磨机衬板,代替了高锰钢,用该材质生产直径φ2.4甚至直径φ4.2的中大型球磨机衬板上,降低了生产成本,取得了良好的经济效益。
另外,如某厂生产出口国外石油钻井用的泥浆泵高铬双金属缸套及采石场600×900破碎机用的锤头,都是超高铬铸铁,这些材质的详细化学成分要求,在铸造手册中是查不到的。
在接受生产绪如上述产品时,如果自己没有完全掌握铸件化学成分要求,以及没有详细了解铸件的服役状况时,应让用户提供尽可能详细的化学成分要求范围及热处理工艺。
当然作为生产厂家来说,必须尽多详细掌握自己产品所要求的化学成分范围及物理性能。
以便生产出用户满意的优质产品。
总之在生产配料之前,应了解所产铸件的目标化学成分,做到心中有数。
二、原材料的化学成分原材料的化学成分,指的是投炉所用的新生铁、废钢、回炉料的主要化学成分,以及硅铁、锰铁等铁合金的牌号或化学成分含量。
三、在冶炼过程中化学成分的增减变化要想掌握各种炉料在冶炼过程中化学成分的变化规律,将是一个较为复杂的问题。
冶炼设备的不同,如冲天炉(热、冷风)三节炉,中频感应电炉等,其化学成分的变化都各不相同。
即便是同一个炉子,因修炉所用材料的不同,以及操作方法的不同,冶炼过程中化学成分的变化也不相同。
以冲天炉为例,热风与冷风,风压的高低,风眼直径的大小,焦碳质量及块度的大小,修炉衬材料是酸性,中性或是碱性,对材质化学成分的变化都不尽相同。
1、碳量的变化碳量的变化大体上可分为四种:(1)炉料中含碳量高低的不同,碳量的增减率不同。
(2)炉料中硅、锰含量高低对碳量的影响。
(3)炉温高低和炉气氧化性强弱对碳量的影响。
(4)其它因素。
(1)炉料的平均含碳愈低,碳向金属中的溶解度愈大,铁水就会发生增碳,废钢用量越大,这种现象越明显。
炉料中平均含碳量愈高(例如在3.6%以上),铁水从焦炭中吸收碳量愈少,而碳的氧化烧损增加,铁水含碳量不仅不增加反而减少。
如果炉料中的含碳量高达3.6~3.8%时,冶炼中铁水的含碳量就基本不再变化了。
(2)铁水中含硅量越高,增碳量越少,这是因为硅可以溶解于铁内,降低了碳在铁中的溶解度。
锰则相反,含锰量增加时,铁水增碳量也有所增加。
(3)加大焦炭用量,或者使用的焦炭块度小,都会使增碳量加大,这是由于增加了铁水与焦炭的接触时间和接触面积。
铁料熔化成铁水滴下落,当流经赤热的底焦时,焦炭中的碳会慢慢溶到铁水滴中去,使铁水含碳量增加,这叫作增碳作用。
这种作用主要发生在过热区和炉缸区。
铁水与焦炭接触的时间越长,接触面积越大,温度越高,铁水增碳就越多。
冲天炉设有前炉,因为铁水能及时从炉缸中流入前炉,所以增碳较少。
搀炉无前炉缸,铁水只能存在炉锅内而与焦炭接触的机率多,所以增碳量就越较大。
炉内温度升高会促使碳更快更多地溶解在铁水中,使增碳显著。
因此,如果其它条件不变而采用热风冲天炉,就会因为提高了炉内温度,使增碳量加大。
在炉内还存在着使碳减少的因素,如铁水滴接近风口,或者风量很大,风压很高时,炉气中的氧会氧化铁水而使含碳量减少(或称脱碳)。
增加风量,提高铁水温度,也会促使增碳。
但是增加风量后,由于加强了铁水氧化,又有促使脱碳的作用,不过,在这种状态下,脱碳作用大于增碳作用。
(4)除以上因素之外,还有其它具体因素也影响着碳量。
提高底焦高度,铁水的过热路程延长,铁水温度提高的同时,也促使了碳向铁水中的溶解。
因此,底焦高度过高时,铸铁的增碳量也大。
如果炉底高度垫的高,铁水下落流经的路程短,铁水及时流入前炉缸,减少了与焦炭的接触时间,增碳率就小。
反之增碳量就大。
炉料过碎小而且配用量大时,易出现熔化速度快、铁水下落快、增碳量很小的现象。
伴随着这种现象的同时,铸铁件也易出现白口缺陷。
在用冲天炉冶炼时,增碳和减碳这两个矛盾着过程,是同时进行的,影响含碳量的因素太多,很难精密的确定。
用中频感应电炉冶炼时,无论是酸性、中性、或者是碱性炉,对碳量均有烧损。
如果操作不当,碳量的烧损更大,当炉温达到浇注温度时,应及时降低功率,保温浇注。
金属液在炉内随着高温时间的延长,碳的烧损量增大,自发晶核减少,应添加增碳剂并加入接力脱氧剂。
2、硅量的变化硅量的变化,主要取决于两个因素,(1)炉衬的属性(酸性、中性或碱性)。
(2)炉温的高低以及在炉内的停留时间。
用石英砂(SiO2)作修炉料,即用酸性炉冶炼钢铁时。
硅量的烧损不明显,如果颗粒细小的石英砂或石英粉用量大时,硅量不但不减少,反而会增加。
用镁砂(碱性)或铝钒土(中性)修炉衬时,硅的烧损量就大,其烧损率一般可按10—15%计算,硅铁合金中硅的烧损率还要更高一些。
3、锰量的烧损无论在任何炉中冶炼,锰量均有烧损,炉温越高,金属液在炉中的停留时间越长,铁水含硫量越高,锰的烧损率就越高,其烧损率一般按15—25%计算,锰铁合金中锰的烧损率还要更高一些。
在冶炼过程中,除铜、钼等元素烧损量极少,在配料时可以不考虑其烧损率,其它元素都有不同程度的烧损。
四、配料配料前在选择原材料时,即要照顾到铸件的质量要求,还要注意到各材料的价格,以及库存量,尽可能多的利用本厂的回炉料、废钢、废杂铁,以降低库存积压和降低铸件的生产成本。
配料方法及工式,除碳的配料计算方法是两个以上外,其它元素的配比计算方法,均是累积法。
1、碳的计算工式一、C=1.8%+CL 2式中C——铁水的含碳量(%)CL ——炉料中的平均含碳量(%)1.8%——在用冲天炉冶炼时,炉料经预热、熔化、过热、还原过程中,脱碳量和增碳量的(估算)中间值。
该式只适应用于冲天炉碳量的计算,不适用于电炉配料的计算,且为了计算结果符合本单位设备的冶炼情况,1.8%系数须根据多次熔炼经验的修正选取。
例如:HT250牌号灰铸铁的含碳量为3.1—3.4%,所用新生铁的含碳量3.8%,回炉料的含碳量3.2%,废钢的含碳量0.4%。
估算配比,新生铁加入量40%,回炉料加入量35%,废钢加入量25%。
C=1.8%+3.8×0.4+3.2×0.35+0.4×0.25 2 ×100%=3.17%2、累积计算法就是将按比例投入的各种炉料,各自代入成分的量,相加在一起,把冶炼过程中的增减率计算在其中,再调整到目标成分的范围,该计算方法适应于冲天炉的配料,也适应于电炉的配料。
当然每次配料,不可能一次配料计算成功,需多次调整配料比,方能达到理想,对于初掌握者来说,尤其是这样。
3、碳的计算方法三,列方程式该配料方法的优点是,在掌握了冲天炉增碳率之后,可一次配料成功,不需要试调配几次。
原材料的化学成分含量如表二所示;铸件材质HT200,各化学成分要求范围如表三所示;冲天炉增碳率为10%。
先确定回炉料的加入量为40%,回炉料代入碳:3.2%×0.4=1.28%总入炉料应代入碳(即未增碳10%以前的量):3.2%(要求碳量中线)1+10%(增碳量)≈2.91%生铁和废钢共需代入碳:2.91%-1.28%=1.63%列方程式:设生铁加入量为x3.5%(生铁含碳量)×x+0.4%(废钢含碳量)×[(1-40%)-x]=1.63% x=45%废钢加入量:(1-40%)-45%=15%以上配料,碳达到了预期目的,但硅、锰仍达不到要求,需要补加硅铁和锰铁,补加硅铁、锰铁及其它任何铁合金,均可用下式求得。
补加量(%)=要求% 合金含量%×收得率%×100%目标中线硅含量是1.95%,炉料中代入硅是1.37%,还差0.58%的硅量,需要添加硅铁来补充其差,硅铁的需补加量即可用上式算出。
硅铁75#补加量(%)=0.58% 75%×0.8×100%≈1%目标中线锰含量应是0.8%,炉料代入的锰是0.568%,还差0.232的锰量,需添加锰铁来补充。
锰铁65#补加量(%)=0.232% 65%×0.75×100%≈0.5%在生产普通铸铁或者普通钢时,掌握了以上方法基本可以指导生产了,但是,在生产合金钢,特别是高合金钢时,还要考虑到,为保证材质有足够的合金成分含量,在添加铁合金时,随之而代入的其它成分,另外还要考虑到如何降低生产成本。
在配料过程中,铬含量取中线5%,就需要加入上表两类铬铁共计8%(因为低碳铬铁和高碳铬铁的含铬量接近,所以先混在一起计算其加入量),才能接近中线要求。
由于铬铁中含有一定量的碳和硅,加入8%铬铁的同时,势必引起碳和硅的增加。
另外,在保证铬含量5%时,如果全部用高碳铬铁,碳量必超。
如果全部用低碳铬铁,再用增碳剂调碳,又会因为低碳铬铁的价格比高碳铬铁的价格高的太多,而使生产成本上升。
在保证化学成分合格又要降低生产成本的情况下,采用低碳铬铁和高碳铬铁的搭配使用。
在实际生产中,当炉前化验结果出来后(碳、硅),要想很快的正确的搭配投料比,确有一定困难,而且往往容易忙中出错,所以要不断总结经验,作到熟中生巧。
为了便于配料,我们列制一个如表五的常规配料表,操作起来就方便、快捷、准确了。
在了解上述配料基本知识和注意事项之后,虽然可以指导生产了。
但是,想要使自己的产品质量更加稳定,使铸件化学成分稳定在最佳含量范围内,从而达到铸件最佳物理性能的匹配,作到物尽其用,还是不足到,还要进一步了解,并懂理以下因素:(1)即便是同一材质要求的铸件,由于铸件自身几何形状不同,以及铸件服役工况条件的差异,而有意把其中某个成分控制在上线,或某个成分应控制在下线。