全正变位齿轮副的设计计算
完整版变位齿轮的计算方法

变位齿轮的计算方法1 变位齿轮的功用及变位系数变位齿轮具有以下功用:(1) 避免根切;(2) 提高齿面的接触强度和弯曲强度;(3) 提高齿面的抗胶合和耐磨损能力;(4) 修复旧齿轮;(5) 配凑中心距。
对于齿数z = 8〜20的直齿圆柱齿轮,当顶圆直径d a=mz+2m+2xm寸,不产生根切的最小变位系数X min 以及齿顶厚S = 0.4m和S a= 0时的变位系数X sa = 0.4m和X sa= 0如表1所列。
2 变位齿轮的简易计算将变位齿轮无侧隙啮合方程式作如下变换:总变位系数中心距变动系数齿顶高变动系数表1齿数z = 8〜20圆柱齿轮的变位系数Z X min X sa= 0.4m X sa=8 0.53 0.18 0.569 0.47 0.22 0.6310 0.42 0.27 0.7011 0.36 0.31 0.7612 0.30 0.35 0.8213 0.24 0.39 0.8814 0.18 0.43 0.9315 0.12 0.46 0.9816 0.06 0.50 1.0317 0 0.53 1.0818 —0.05 0.56 1.1319 —0.11 0.59 1.1820 —0.17 0.62 1.23△ y= x s —y式中:a ----- 压力角,a= 20°;a'――啮合角;Z2、Z i 大、小齿轮的齿数将上述三式分别除以,则得:由上述公式可以看岀,当齿形角a 一定时,X z、y z和均只为啮合角a'的函数。
在设计计算时,只要已知X z、y z>Ay z和a'四个参数中的任一参数,即可由变位齿轮的X z、y z>Ay z和啮合角a'的数值表 ( 表 2) 中,查出其他三个参数,再进行下列计算。
一般齿轮手册上均列有此数值表。
式中正号用于外啮合,负号用于内啮合。
3 计算实例例 1:已知一对外啮合变位直齿轮,齿数Z 1= 18, Z 2= 32,压力角 a= 20°,啮合角 a'= 22° 18',试确定总变位系数 x z 、中心距变动系数 y 及齿顶高变动系数△ y 。
变位齿轮计算公式

变位齿轮计算公式变位齿轮是一种特殊的齿轮传动装置,由于其特殊的设计结构,在很多工程领域中被广泛应用。
变位齿轮的计算涉及到很多参数和公式,下面将介绍1200字以上的变位齿轮计算公式。
1.变位齿轮的模数计算公式:变位齿轮的模数实际上是齿轮的基本参数之一,是计算齿轮尺寸和性能的重要依据。
模数的计算公式如下:m=(π*d)/(z+2)其中,m为模数,d为齿轮的总直径,z为齿数。
2.变位齿轮的齿宽计算公式:变位齿轮的齿宽决定了齿轮的受力和传动能力,齿宽的计算公式如下:bw = K * m其中,bw为齿宽,K为齿宽系数,m为模数。
3.变位齿轮的中心距计算公式:变位齿轮的中心距是指两个齿轮中心线之间的距离,中心距的计算公式如下:a=(m*(z1+z2))/2其中,a为中心距,m为模数,z1和z2分别为两个齿轮的齿数。
4.变位齿轮的齿数比计算公式:齿数比是指两个齿轮齿数的比值,齿数比的计算公式如下:i=z2/z1其中,i为齿数比,z1为主动齿轮的齿数,z2为从动齿轮的齿数。
5.变位齿轮的齿侧间隙计算公式:齿侧间隙表示两个齿轮侧面的距离,可以通过以下计算公式进行计算:cg = 0.25 * m * (z1 + z2) + c其中,cg表示齿侧间隙,m表示模数,z1和z2表示两个齿轮的齿数,c表示一个修正系数。
6.变位齿轮的分度圆直径计算公式:分度圆直径是指齿轮两齿间的直径,可以通过以下计算公式进行计算:d=m*z其中,d表示分度圆直径,m表示模数,z表示齿轮的齿数。
7.变位齿轮的螺旋角计算公式:螺旋角表示齿轮齿槽相对于圆柱面的旋转角度,可以通过以下计算公式进行计算:φ = tan^(-1)((cosα1/sinα1)+((z1+z2)/(2m*tanα1)))其中,φ表示螺旋角,α1表示变位齿轮的压力角,z1和z2分别表示两个齿轮的齿数,m表示模数。
8.变位齿轮的齿形因数计算公式:齿形因数是表示齿轮齿形的一个参数,可以通过以下计算公式进行计算:X = (2*m*(cosα1+cosα2))/(π*tan(α1+α2))其中,X表示齿形因数,m表示模数,α1和α2分别表示两个齿轮的压力角。
变位齿轮参数及计算
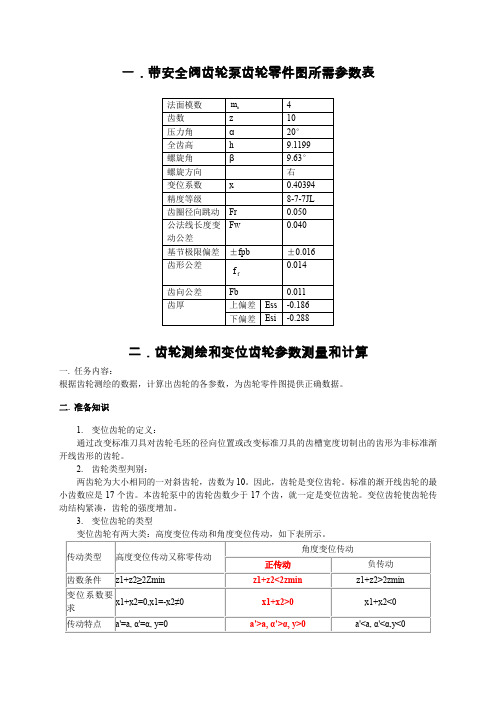
1 2
齿顶高变动系数 yt xt yt
固定弦齿厚 scn mn cos2 n ( 2 xn tan n )
2
五计算软件界面
z α h β
ff
Fb 上偏差 下偏差
二.齿轮测绘和变位齿轮参数测量和计算
一. 任务内容: 根据齿轮测绘的数据,计算出齿轮的各参数,为齿轮零件图提供正确数据。 二. 准备知识 1. 变位齿轮的定义: 通过改变标准刀具对齿轮毛坯的径向位置或改变标准刀具的齿槽宽度切制出的齿形为非标准渐 开线齿形的齿轮。 2. 齿轮类型判别: 两齿轮为大小相同的一对斜齿轮,齿数为 10。因此,齿轮是变位齿轮。标准的渐开线齿轮的最 小齿数应是 17 个齿。本齿轮泵中的齿轮齿数少于 17 个齿,就一定是变位齿轮。变位齿轮使齿轮传 动结构紧凑,齿轮的强度增加。 3. 变位齿轮的类型 变位齿轮有两大类:高度变位传动和角度变位传动,如下表所示。 传动类型 齿数条件 高度变位传动又称零传动 z1+z2≥2Zmin 角度变位传动 正传动 z1+z2<2zmin x1+x2>0 a'>a, α'>α, y>0 负传动 z1+z2>2zmin x1+x2<0 a'<a, α'<α,y<0
han* 1 c* 0.25
跨齿数 k 2 跨齿数 k 3
四. 计算流程: 对于斜齿轮, 应先计算法面参数, 然后计算端面各系数。 需要计算的参数有模数 m , 变位系数 xn , 啮合角 ' 和中心距变动系数 yt 等。 1.先计算模数,并选择标准系列。 模数是有标准系列的。系列如下表: 系列 第一系列 第二系列 (1)渐开线圆柱齿轮模数(GB/T1357-1987) 0.1 0.12 0.15 0.2 0.25 0.3 0.4 0.5 0.6 0.8 1 2 2.5 3 4 5 6 8 10 12 16 20 25 32 40 50 0.35 0.7 0.9 (6.5) 7 9 0.75 2.25 2.75 (3.25)3.5 (3.75) (11) 14 18 22 28 (30) 36 45 1.25 4.5 1.5 5.5
变位齿轮机构设计(Ⅰ)
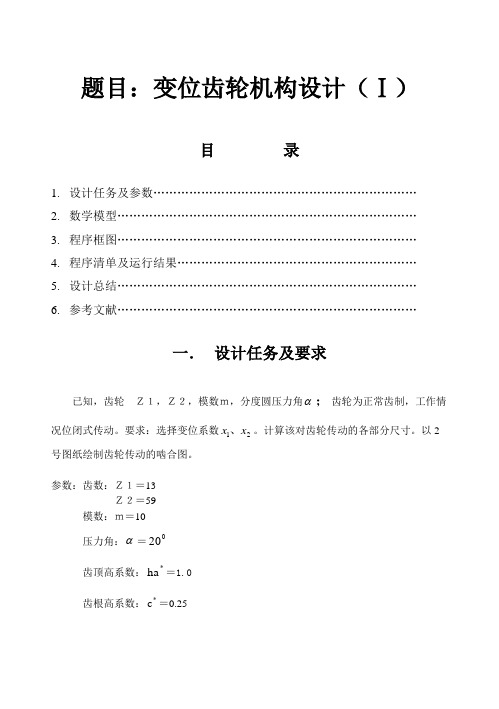
题目:变位齿轮机构设计(Ⅰ)目录1. 设计任务及参数…………………………………………………………2. 数学模型…………………………………………………………………3. 程序框图…………………………………………………………………4. 程序清单及运行结果……………………………………………………5. 设计总结…………………………………………………………………6. 参考文献…………………………………………………………………一. 设计任务及要求已知,齿轮 Z1,Z2,模数m,分度圆压力角α;齿轮为正常齿制,工作情况位闭式传动。
要求:选择变位系数21x x 、。
计算该对齿轮传动的各部分尺寸。
以2号图纸绘制齿轮传动的啮合图。
参数:齿数:Z1=13 Z2=59 模数:m=10压力角:α=020齿顶高系数:*ha =1.0齿根高系数:*c =0.25二.数学模型(一)渐开线直齿轮圆柱齿轮基本公式1.传动比: 12/z z i =2.啮合角α': ;ααcos '2)(cos 21⨯⨯+='a z z mαααinv z z x x inv +++=')()(2tan 2121;3.中心距:2)(21z z ma += ; a '='cos cos )(2121ααz z m +;4.分度圆分离系数: )1'c o s c o s )((2121-+=ααz z y ; 5.齿顶高变动系数:y x x -+=21σ6.分度圆直径; 11mz d = 22mz d =7.基圆直径; αc o s 11mz d b =αcos 22mz d b =8.齿顶高: )(1*1σ-+=x h m h a a )(2*2σ-+=x h m h a a 9.齿根高: )(1**1x c h m h a f -+= )(2**2x c h m h a f -+= 10.齿顶圆直径: 1112a a h d d +=2222a a h d d += 11.齿根圆直径; 1112f f h d d -=2222f f h d d -=12.节圆直径: 'cos cos '11ααd d = 'cos cos '22ααd d =13.齿距: m p π= 14.节圆齿距: 'cos cos ααpp =' 15.基圆齿距: απcos m p b = 16.分度圆齿厚: απtan 22111m x m s += απt a n22122m x m s +=(二)齿轮副传动质量指标1.齿轮是否根切(1)标准齿轮不根切的最小齿数 α2*min sin 2a h z = (2)不根切最小变位系数min 1min *min 1/)(z z z h x a -=; min 2min *min 2/)(z z z h x a -=;2.重合度)]tan (tan )tan (tan [212211ααααπε'-+'-=a a z z其中)/(cos 1111a b a d d -=α )/(c o s 2212a b a d d -=α一般情况应保证ε≥1.23. 齿顶圆齿厚:)(2111111ααinv inv r r r s s a a a a --=)(2222222ααinv inv r r r s s a a a a --= 一般取25.0≥a s m4.滑动系数:)(tan 'tan )1('tan tan α1221221a2z z z z z u a +-+-=ααα)1(tan 'tan )1('tan tan α221121a1z z z z z u a +-+-=ααα5.不发生干涉 (T ≥E) 其中:)'tan (tan 'tan 2121ααα--=a z z T )'tan (tan 'tan 1212ααα--=a z z T αα2sin )(4tan 11*1z x h E a --= αα2sin )(4tan 22*2z x h E a --=三.程序框图四.程序清单及运行结果(一)程序清单:#include"math.h"#include"stdio.h"#define z1 13.0#define z2 59.0#define t 20*3.14/180#define m 10#define hax 1.0#define cx 0.25#define Zmin 17.0#define pi 3.14main(){int a,ai; double ti; *啮合角*/double x1,x2,xh;double db1,db2; /*基圆直径*/double d1,d2; /*分度圆直径*/double ha1,ha2; /*齿顶高*/double hf1,hf2; /*齿根高*/double df1,df2; /*齿根圆直径*/ double di1,di2; /*节圆直径*/ double da1,da2; /*齿顶圆直径*/ double p; /*齿距*/double p1; /*节圆齿距*/ double pb; /*基圆齿距*/ double S1,S2; /*齿厚*/double Sa1,Sa2; /*齿顶后*/ double e; /*重合度*/ double y,Xmin1,Xmin2;double cdb;double bx; /*齿顶高变动系数*/ double u1,u2;double T1,T2,E1,E2;int i;int j;a=m*(z1+z2)/2;printf("a=%d \n",a);i=a/5;ai=(i+1)*5;printf("ai=%d (mm)\n",ai);ti=acos(a*cos(t)/ai);printf("ti=%4.3f (rad)\n",ti);cdb=z2/z1;printf("\n cdb=%5.3f \n",cdb);y=0.5*(z1+z2)*(cos(t)/cos(ti)-1);printf("y=%5.3f \n",y);d1=m*z1;d2=m*z2;printf("d1=%5.3f,d2=%5.3f (mm)\n",d1,d2);db1=m*z1*cos(t);db2=m*z2*cos(t);di1=d1*cos(t)/cos(ti);di2=d2*cos(t)/cos(ti);printf("di1=%5.3f,di2=%5.3f (mm)\n",di1,di2);p=m*pi;p1=p*cos(t)/cos(ti);pb=pi*m*cos(t);printf("p=%5.3f,p1=%5.3f,pb=%5.3f \n",p,p1,pb);Xmin1=hax*(Zmin-z1)/Zmin;printf("Xmin1=%3.4f (mm)\n\n",Xmin1);Xmin2=hax*(Zmin-z2)/Zmin;printf("Xmin2=%3.4f (mm)\n\n",Xmin2);xh=0.5*(tan(ti)-ti-(tan(t)-t))*(z1+z2)/tan(t);printf("xh=x1+x2=%5.3f \n",xh);for(j=0;j<10;j++){ x1=Xmin1+0.04*j;x2=xh-x1;if(x2<Xmin2)break;bx=xh-y;ha1=m*(hax+x1-bx);ha2=m*(hax+x2-bx);hf1=(hax+cx-x1)*m;hf2=(hax+cx-x2)*m;da1=d1+2*ha1;da2=d2+2*ha2;df1=d1-2*hf1;df2=d2-2*hf2;S1=0.5*pi*m+2*x1*m*tan(t);S2=0.5*pi*m+2*x2*m*tan(t);Sa1=S1*da1/d1-da1*(tan(acos(db1/da1))-acos(db1/da1)-(tan(t)-t));Sa2=S2*db2/d2-da2*(tan(acos(db2/da2))-acos(db2/da2)-(tan(t)-t));e=(z1*(tan(acos(db1/da1))-tan(ti))+z2*(tan(acos(db2/da2))-tan(ti)))/(2*pi);u1=((tan(acos(db2/da2))-tan(ti))*((z1+z2)/z2))/(((1+z1/z2)*tan(ti))-tan(acos(db2/da2))) ;u2=((tan(acos(db1/da1))-tan(ti))*((z1+z2)/z1))/(((1+z1/z2)*tan(ti))-tan(acos(db1/da1))) ;T1=tan(ti)-(z2/z1)*(tan(acos(db2/da2))-tan(ti));T2=tan(ti)-(z1/z2)*(tan(acos(db1/da1))-tan(ti));E1=tan(t)-(4*(hax-x1))/(z1*sin(2*t));E2=tan(t)-(4*(hax-x2))/(z2*sin(2*t));if(e>=1.2)printf("重合度满足要求\n");elseprintf("重合度不满足要求\n");if((Sa1>=0.25*m)&&(Sa2>=0.25*m))printf("齿顶厚满足要求\n");elseprintf("齿顶厚不满足要求\n");if((T1>=E1)&&(T2>=E2))printf("不发生干涉\n");elseprintf("发生干涉\n");if((Sa1>=0.25*m)&&(Sa2>=0.25*m)&&(e>1.2)&&(T1>=E1)&&(T2>=E2)){ printf("d1=%4.3f,d2=%4.3f (mm)\n",d1,d2);printf("x1=%4.3f,x2=%4.3f (mm)\n",x1,x2);printf("bx=%4.3f \n",bx);printf("ha1=%4.3f,ha2=%4.3f (mm)\n",ha1,ha2);printf("hf1=%4.3f,hf2=%4.3f (mm)\n",hf1,hf2);printf("da1=%4.3f,da2=%4.3f (mm)\n",da1,da2);printf("df1=%4.3f,df2=%4.3f (mm)\n",df1,df2);printf("S1=%4.3f,S2=%4.3f (mm)\n",S1,S2);printf("Sa1=%4.3f,Sa2=%4.3f (mm)\n",Sa1,Sa2);printf("e=%4.3f \n",e);printf("db1=%4.3f,db2=%4.3f (mm)\n",db1,db2); printf("u1=%4.3f,u2=%4.3f \n",u1,u2);printf("T1=%4.3f,T2=%4.3f (mm)\n",T1,T2); printf("E1=%4.3f,E2=%4.3f (mm)\n",E1,E2);}}}(二)运行结果a=360ai=365 (mm)ti=0.385 (rad)cdb=4.538y=0.500d1=130.000,d2=590.000 (mm)di1=131.806,di2=598.194 (mm)p=31.400,p1=31.836,pb=29.508Xmin1=0.2353 (mm)Xmin2=-2.4706 (mm)xh=x1+x2=0.525重合度满足要求齿顶厚满足要求不发生干涉d1=130.000,d2=590.000 (mm)x1=0.235,x2=0.290 (mm)bx=0.025ha1=12.102,ha2=12.647 (mm)hf1=10.147,hf2=9.602 (mm)da1=154.205,da2=615.294 (mm)df1=109.706,df2=570.795 (mm)S1=17.412,S2=17.808 (mm)Sa1=5.384,Sa2=5.775 (mm)e=1.472db1=122.168,db2=554.454 (mm)u1=7.119,u2=-7.329T1=0.059,T2=0.324 (mm)E1=-0.002,E2=0.289 (mm)五.设计总结(一)避免根切的设计如果小齿轮的齿数能减小,则大齿轮的齿数就能减小更多,使得结构变得紧凑。
变位齿轮设计计算

变位齿轮设计计算一、引言变位齿轮是一种常见的传动装置,它主要通过齿轮的齿槽形状变化,实现转动方向和速度的改变。
在设计变位齿轮时,需要进行一系列的计算来确定齿轮的参数和齿形。
二、变位齿轮设计参数的确定1.传动比:传动比是指在变位齿轮传动装置中,输入轴的转速与输出轴的转速之间的比值。
传动比的确定需要考虑传动装置的具体要求,如输入轴和输出轴的转速、扭矩等。
2.等分线数:等分线数是指齿轮齿槽等分成的线数。
等分线数的确定需要考虑齿轮的尺寸和使用要求。
通常情况下,等分线数取10~30之间的整数值。
3.基本齿数:基本齿数是指齿轮的齿数,用符号Z表示。
基本齿数的确定需要考虑传动比和等分线数。
4.各轴同轴度:变位齿轮传动的轴线必须准确的同轴。
同轴度是指轴线与同一直线的距离误差。
同轴度误差必须满足传动装置的要求。
三、齿轮齿形参数计算1.齿顶圆直径:齿顶圆直径是指齿轮齿槽顶部的圆的直径,用符号D 表示。
齿顶圆直径的计算需要考虑基本齿数和模数。
2.齿根圆直径:齿根圆直径是指齿轮齿槽底部的圆的直径,用符号Dg表示。
齿根圆直径的计算需要考虑基本齿数和模数。
3.等距角:等距角是指相邻齿的齿槽中心线之间的夹角。
等距角的计算需要考虑基本齿数和齿槽等分线数。
4.工作压力角:工作压力角是指齿轮齿槽中心线与齿轮轴线之间的夹角,用符号α表示。
工作压力角的计算可以根据传动要求和齿轮材料的选择来确定。
5. 齿顶高:齿顶高是指齿轮齿槽顶部到齿轮轴线的距离,用符号ha 表示。
齿顶高的计算可以根据工作压力角和模数来确定。
6. 齿根高:齿根高是指齿轮齿槽底部到齿轮轴线的距离,用符号hf 表示。
齿根高的计算可以根据工作压力角和模数来确定。
7.齿宽:齿宽是指齿轮齿槽的宽度,用符号b表示。
齿宽的计算可以根据传动扭矩和材料强度来确定。
四、变位齿轮齿槽形状计算1.齿槽高度:齿槽高度是指齿轮齿槽的深度,用符号h表示。
齿槽高度的计算需要考虑齿顶高和齿根高。
2.齿槽角:齿槽角是指齿轮齿槽的侧面与齿轮轴线之间的夹角,用符号β表示。
变位齿轮参数计算公式
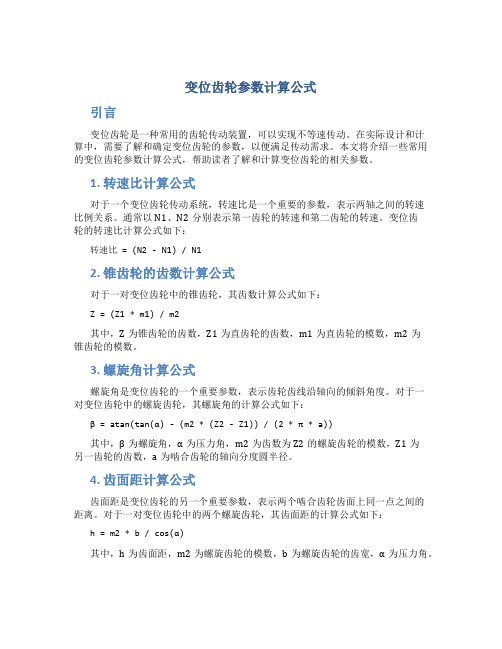
变位齿轮参数计算公式引言变位齿轮是一种常用的齿轮传动装置,可以实现不等速传动。
在实际设计和计算中,需要了解和确定变位齿轮的参数,以便满足传动需求。
本文将介绍一些常用的变位齿轮参数计算公式,帮助读者了解和计算变位齿轮的相关参数。
1. 转速比计算公式对于一个变位齿轮传动系统,转速比是一个重要的参数,表示两轴之间的转速比例关系。
通常以N1、N2分别表示第一齿轮的转速和第二齿轮的转速。
变位齿轮的转速比计算公式如下:转速比 = (N2 - N1) / N12. 锥齿轮的齿数计算公式对于一对变位齿轮中的锥齿轮,其齿数计算公式如下:Z = (Z1 * m1) / m2其中,Z为锥齿轮的齿数,Z1为直齿轮的齿数,m1为直齿轮的模数,m2为锥齿轮的模数。
3. 螺旋角计算公式螺旋角是变位齿轮的一个重要参数,表示齿轮齿线沿轴向的倾斜角度。
对于一对变位齿轮中的螺旋齿轮,其螺旋角的计算公式如下:β = atan(tan(α) - (m2 * (Z2 - Z1)) / (2 * π * a))其中,β为螺旋角,α为压力角,m2为齿数为Z2的螺旋齿轮的模数,Z1为另一齿轮的齿数,a为啮合齿轮的轴向分度圆半径。
4. 齿面距计算公式齿面距是变位齿轮的另一个重要参数,表示两个啮合齿轮齿面上同一点之间的距离。
对于一对变位齿轮中的两个螺旋齿轮,其齿面距的计算公式如下:h = m2 * b / cos(α)其中,h为齿面距,m2为螺旋齿轮的模数,b为螺旋齿轮的齿宽,α为压力角。
5. 压力角计算公式压力角是变位齿轮设计中的一个重要参数,表示齿形曲线的锋角与轴线的夹角。
通常使用以下计算公式得到压力角的值:cos(α) = (Z1 + Z2) / (2 * m2 * a)其中,α为压力角,Z1和Z2分别为两个啮合齿轮的齿数,m2为螺旋齿轮的模数,a为啮合齿轮的轴向分度圆半径。
结论本文介绍了几个重要的变位齿轮参数计算公式,包括转速比、锥齿轮的齿数、螺旋角、齿面距和压力角的计算公式。
变位齿轮几何尺寸计算

变位齿轮几何尺寸计算
变位齿轮是齿轮传动系统中常用的一种齿轮,主要用于传递旋转运动和扭矩。
其特点是在齿轮齿条的侧面具有斜面,能够实现平滑传动和减小齿轮传动时的冲击和噪声。
在设计变位齿轮时,需要进行几何尺寸的计算来保证齿轮的运转性能。
变位齿轮的几何尺寸计算主要包括齿轮的模数、齿数、齿顶高和齿根深等参数。
下面将详细介绍每个参数的计算方法。
1.模数(m)的计算:
模数是齿轮齿条的基本尺寸,它表示齿轮齿条的大小。
模数的计算根据传动所需的扭矩和功率来确定,通常使用公式:
m=K∛(T/P)
其中,m为模数,K为系数(一般取20),T为传动所需扭矩,P为传动功率。
2.齿数(z)的计算:
齿数表示齿轮上的齿的数量。
齿数的计算根据传动比和模数来确定,一般使用公式:
z=m×i
其中,i为传动比。
3.齿顶高(h_a)和齿根深(h_f)的计算:
齿顶高表示齿轮齿条的最高点到齿顶的距离,齿根深表示齿轮齿条的最低点到齿底的距离。
它们的计算可以使用公式:
h_a=1.25×m
h_f=1.35×m
上述是变位齿轮几何尺寸计算的基本方法,但实际设计中还需要考虑齿轮的齿向角、齿轮间的啮合角、齿轮侧隙等因素。
此外,变位齿轮的几何尺寸还需要满足一些额外的要求,如齿轮的强度和刚度等。
关于变位齿轮几何尺寸计算的更详细内容可以参考相关的齿轮设计手册和专业参考书籍。
变位齿轮参数及计算
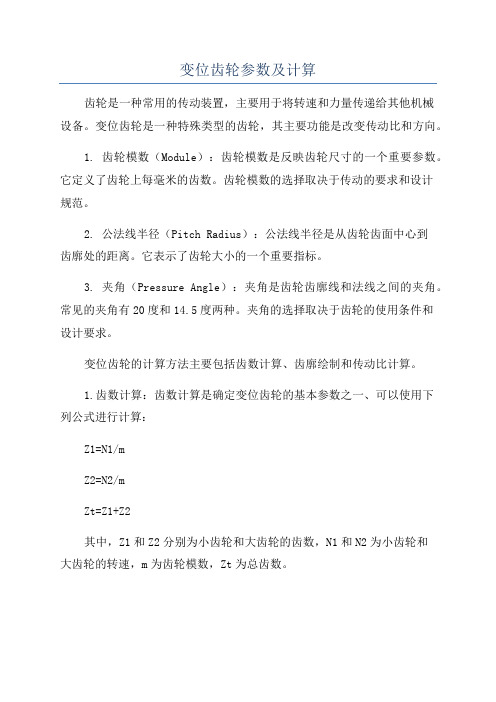
变位齿轮参数及计算齿轮是一种常用的传动装置,主要用于将转速和力量传递给其他机械设备。
变位齿轮是一种特殊类型的齿轮,其主要功能是改变传动比和方向。
1. 齿轮模数(Module):齿轮模数是反映齿轮尺寸的一个重要参数。
它定义了齿轮上每毫米的齿数。
齿轮模数的选择取决于传动的要求和设计规范。
2. 公法线半径(Pitch Radius):公法线半径是从齿轮齿面中心到齿廓处的距离。
它表示了齿轮大小的一个重要指标。
3. 夹角(Pressure Angle):夹角是齿轮齿廓线和法线之间的夹角。
常见的夹角有20度和14.5度两种。
夹角的选择取决于齿轮的使用条件和设计要求。
变位齿轮的计算方法主要包括齿数计算、齿廓绘制和传动比计算。
1.齿数计算:齿数计算是确定变位齿轮的基本参数之一、可以使用下列公式进行计算:Z1=N1/mZ2=N2/mZt=Z1+Z2其中,Z1和Z2分别为小齿轮和大齿轮的齿数,N1和N2为小齿轮和大齿轮的转速,m为齿轮模数,Zt为总齿数。
2.齿廓绘制:变位齿轮的齿廓是根据齿轮参数和齿轮轴心位置绘制出来的。
可以使用软件进行计算和绘制,也可以使用手动计算和绘图方法。
绘制齿廓时需要考虑齿轮的齿顶高度、齿根高度和齿廓曲线。
3.传动比计算:传动比是指变位齿轮传动时输出轴的转速与输入轴的转速之比。
可以用下列公式进行计算:i=Z2/Z1其中,i为传动比,Z1和Z2分别为小齿轮和大齿轮的齿数。
通过以上参数和计算步骤,可以确定变位齿轮的设计参数和计算结果。
齿轮的设计和计算是齿轮传动工程中的重要内容,合理的设计和计算可以保证齿轮传动的安全和可靠性。
(完整版)变位齿轮的计算方法
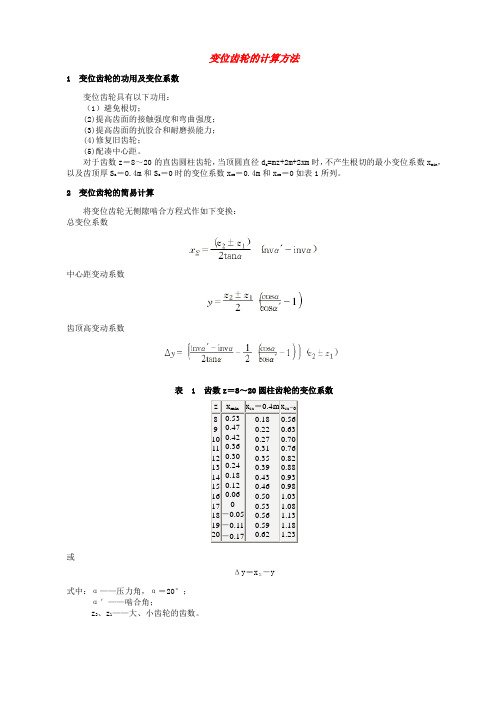
Wk=Wk*m+0.684xm
式中:Wk*——某齿数齿轮跨测k齿时,模数m=1的公法线长度。
表 2 变位齿轮的yz、xz、Δyz和啮合角α′(α=2ห้องสมุดไป่ตู้°)
α′
(分)
19°
20°
21°
yz
xz
Δyz
yz
xz
Δyz
yz
xz
Δyz
0
1
2
3
4
5
6
7
8
9
-0.00616
606
596
0.00107
118
129
139
150
161
172
183
194
205
0.00001
001
001
001
001
001
001
001
002
002
0.00768
779
790
802
813
825
836
847
859
870
0.00789
801
814
825
837
850
862
874
886
898
0.00022
023
023
024
236
246
257
268
279
290
301
312
0.00216
227
238
249
260
271
282
293
304
315
0.00002
002
002
003
003
变位齿轮公式

变位齿轮公式变位齿轮传动的设计步骤设计变位齿轮时,根据不同的已知条件,可采用不同的设计步骤。
(1)已知z1、z2、m、α、ha*和c*时,其设计步骤为:1)选择传动类型,若z1+z2 < 2zmin,必须采用正传动,否则可考虑其它传动类型;2)选择两齿轮的变位系数;3)计算两齿轮的几何尺寸;4)验算重合度及轮齿强度。
(2)已知z1、z2、m、a'、α、ha*和c*时,其设计步骤为:1)计算啮合角α'cosα'=(a/a')cosα2)选择两齿轮的变位系数invα'=2tgα(x1+x2)/(z1+z2) + invαx1+x2=(z1+z2)(invα'-invα)/2tgαx1≥ha*(zmin-z)/zmin,x2≥ha*(zmin-z)/zmin3)计算两齿轮的几何尺寸4)验算重合度及轮齿强度(3)已知i、m、a'、α、ha*和c*时,其设计步骤为:1)确定两齿轮的齿数因a'=acosα/cosα'=[m(z1+z2)/2]cosα/cosα'=[mz1(1+i)/2]cosα/cosα' 故z1≈2a'/(i+1)m 取整数,z2=iz1 取整数。
思考题:1)某机器中的一对外啮合标准圆柱直齿轮,小齿轮轮齿严重磨损,拟报废,大齿轮轮齿磨损较轻,拟修复。
试问采用什么方法可使传动能恢复使用?2)图示为一单联滑移齿轮机构,已知基本参数为m=3mm,z1=18,z2=30,z3=27。
试问有几种设计方案?哪种方案较好?3)吊车行走机构中有一对标准直齿轮传动,已知z1=13,z2=47,m=3mm,齿轮1因根切经常断齿。
试问采用什么方案来解决这个问题?例用齿条插刀加工一个直齿圆柱齿轮。
已知被加工齿轮轮坯的角速度ω1=5 rad/s,刀具的移动速度为0.375m/s,刀具的模数m=10mm,压力角α=200。
变位齿轮设计计算
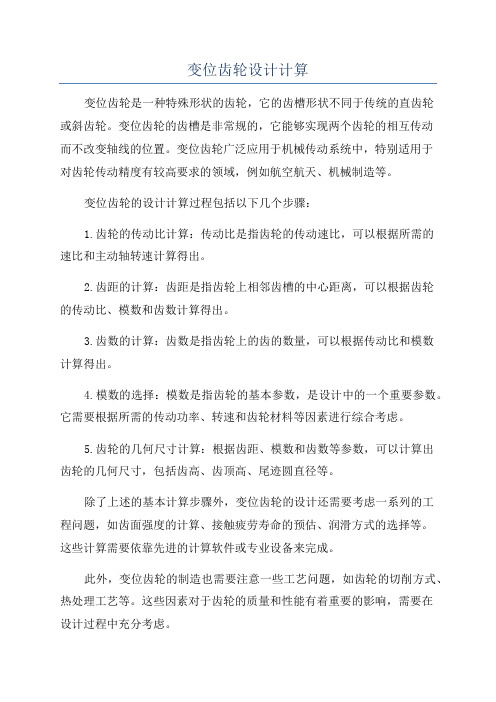
变位齿轮设计计算
变位齿轮是一种特殊形状的齿轮,它的齿槽形状不同于传统的直齿轮
或斜齿轮。
变位齿轮的齿槽是非常规的,它能够实现两个齿轮的相互传动
而不改变轴线的位置。
变位齿轮广泛应用于机械传动系统中,特别适用于
对齿轮传动精度有较高要求的领域,例如航空航天、机械制造等。
变位齿轮的设计计算过程包括以下几个步骤:
1.齿轮的传动比计算:传动比是指齿轮的传动速比,可以根据所需的
速比和主动轴转速计算得出。
2.齿距的计算:齿距是指齿轮上相邻齿槽的中心距离,可以根据齿轮
的传动比、模数和齿数计算得出。
3.齿数的计算:齿数是指齿轮上的齿的数量,可以根据传动比和模数
计算得出。
4.模数的选择:模数是指齿轮的基本参数,是设计中的一个重要参数。
它需要根据所需的传动功率、转速和齿轮材料等因素进行综合考虑。
5.齿轮的几何尺寸计算:根据齿距、模数和齿数等参数,可以计算出
齿轮的几何尺寸,包括齿高、齿顶高、尾迹圆直径等。
除了上述的基本计算步骤外,变位齿轮的设计还需要考虑一系列的工
程问题,如齿面强度的计算、接触疲劳寿命的预估、润滑方式的选择等。
这些计算需要依靠先进的计算软件或专业设备来完成。
此外,变位齿轮的制造也需要注意一些工艺问题,如齿轮的切削方式、热处理工艺等。
这些因素对于齿轮的质量和性能有着重要的影响,需要在
设计过程中充分考虑。
正负变位齿轮参数计算公式
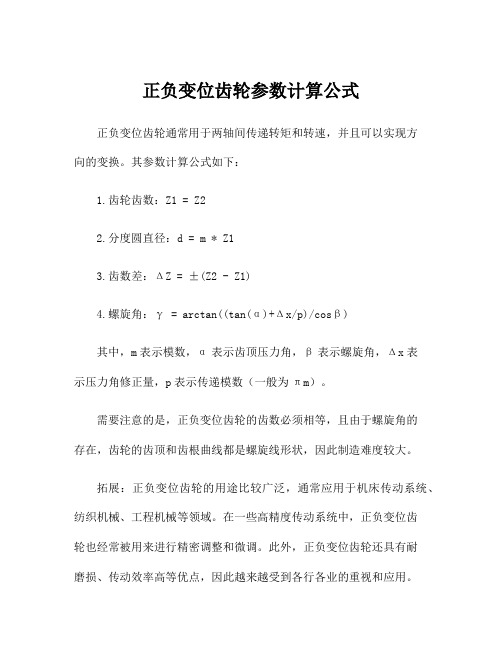
正负变位齿轮参数计算公式
正负变位齿轮通常用于两轴间传递转矩和转速,并且可以实现方
向的变换。
其参数计算公式如下:
1.齿轮齿数:Z1 = Z2
2.分度圆直径:d = m * Z1
3.齿数差:ΔZ = ±(Z2 - Z1)
4.螺旋角:γ = arctan((tan(α)+Δx/p)/cosβ)
其中,m表示模数,α表示齿顶压力角,β表示螺旋角,Δx表
示压力角修正量,p表示传递模数(一般为πm)。
需要注意的是,正负变位齿轮的齿数必须相等,且由于螺旋角的
存在,齿轮的齿顶和齿根曲线都是螺旋线形状,因此制造难度较大。
拓展:正负变位齿轮的用途比较广泛,通常应用于机床传动系统、纺织机械、工程机械等领域。
在一些高精度传动系统中,正负变位齿
轮也经常被用来进行精密调整和微调。
此外,正负变位齿轮还具有耐
磨损、传动效率高等优点,因此越来越受到各行各业的重视和应用。
变位齿轮的计算方法
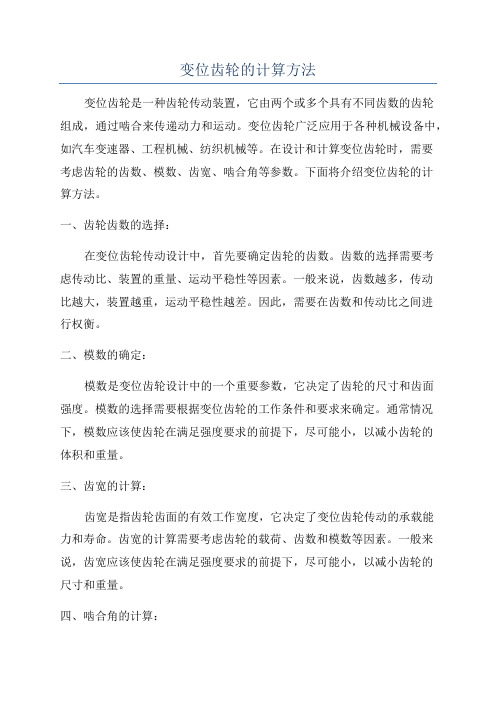
变位齿轮的计算方法变位齿轮是一种齿轮传动装置,它由两个或多个具有不同齿数的齿轮组成,通过啮合来传递动力和运动。
变位齿轮广泛应用于各种机械设备中,如汽车变速器、工程机械、纺织机械等。
在设计和计算变位齿轮时,需要考虑齿轮的齿数、模数、齿宽、啮合角等参数。
下面将介绍变位齿轮的计算方法。
一、齿轮齿数的选择:在变位齿轮传动设计中,首先要确定齿轮的齿数。
齿数的选择需要考虑传动比、装置的重量、运动平稳性等因素。
一般来说,齿数越多,传动比越大,装置越重,运动平稳性越差。
因此,需要在齿数和传动比之间进行权衡。
二、模数的确定:模数是变位齿轮设计中的一个重要参数,它决定了齿轮的尺寸和齿面强度。
模数的选择需要根据变位齿轮的工作条件和要求来确定。
通常情况下,模数应该使齿轮在满足强度要求的前提下,尽可能小,以减小齿轮的体积和重量。
三、齿宽的计算:齿宽是指齿轮齿面的有效工作宽度,它决定了变位齿轮传动的承载能力和寿命。
齿宽的计算需要考虑齿轮的载荷、齿数和模数等因素。
一般来说,齿宽应该使齿轮在满足强度要求的前提下,尽可能小,以减小齿轮的尺寸和重量。
四、啮合角的计算:啮合角是指变位齿轮齿面的啮合角度,它决定了齿轮传动的配合性能和工作平稳性。
啮合角的计算需要考虑齿轮的齿数、齿宽和模数等因素。
一般来说,啮合角应该使齿轮在满足配合性能要求的前提下,尽可能小,以减小齿轮的摩擦和磨损。
以上是变位齿轮的基本计算方法。
在实际设计和计算中,还需要考虑齿面的修形、齿轮的加工精度、齿轮的轴向力和径向力等因素。
设计变位齿轮需要综合考虑齿轮传动的强度、齿轮的尺寸和重量、齿轮的运动平稳性和配合性能等因素,以满足机械设备的要求。
变位齿轮几何参数计算

变位齿轮几何参数计算变位齿轮是一种能够实现传动的机械装置,其特点是能够传递转矩和变速的功能。
变位齿轮几何参数计算是设计变位齿轮传动的重要步骤之一,本文将对变位齿轮几何参数计算进行详细介绍。
主要内容涵盖变位齿轮的基本概念、几何参数的计算方法以及相关的应用举例。
一、变位齿轮的基本概念变位齿轮是由一对轴平行并且具有相同模数的齿轮组成的,其中一只齿轮的齿数是固定不变的,称为定齿轮;另一只齿轮的齿数是可变的,称为动齿轮。
变位齿轮传动通过改变动齿轮的齿数来实现变速。
二、几何参数的计算方法1.变位齿轮的齿数计算变位齿轮的齿数计算需要确定定齿轮的模数和动齿轮的模数变化量。
固定的定齿轮齿数N1可根据传动比和任意选定的动齿轮齿数N2计算得到。
变位齿轮的齿轮传动比等于定齿轮的齿数除以动齿轮的齿数,即传动比i=N1/N22.变位齿轮的齿廓计算变位齿轮的齿廓计算需要根据变位齿轮的齿数、螺旋角和压力角来确定。
变位齿轮的齿形是沿齿轮直齿廓方向逐渐变化的。
在变位齿轮的齿廓计算中,首先需要确定变位齿轮的基圆半径和齿顶高,然后根据基圆半径和齿顶高计算齿根高和齿根圆半径。
最后,根据齿根高、齿根圆半径和变位齿轮的螺旋角、压力角来计算出齿廓。
三、相关应用举例1.变位齿轮传动装置的设计根据给定的传动比和传动功率,可以利用变位齿轮几何参数计算的结果设计出适合的变位齿轮传动装置,以实现所需的变速和传动效果。
2.变位齿轮传动的优化通过调整变位齿轮的几何参数,如齿数、齿廓等,可以优化传动装置的性能,比如降低传动中的噪音和振动,提高传动效率等。
3.变位齿轮的制造利用变位齿轮几何参数计算的结果可以指导齿轮的加工制造,保证制造出的变位齿轮符合设计要求。
总结:变位齿轮几何参数计算是设计变位齿轮传动的基本步骤之一,通过计算齿数和齿廓等参数可以实现变位齿轮传动的设计、优化和制造。
变位齿轮传动在机械装置中具有重要的应用和发展前景,对于提高传动效果和性能具有重要意义。
变位齿轮参数及计算
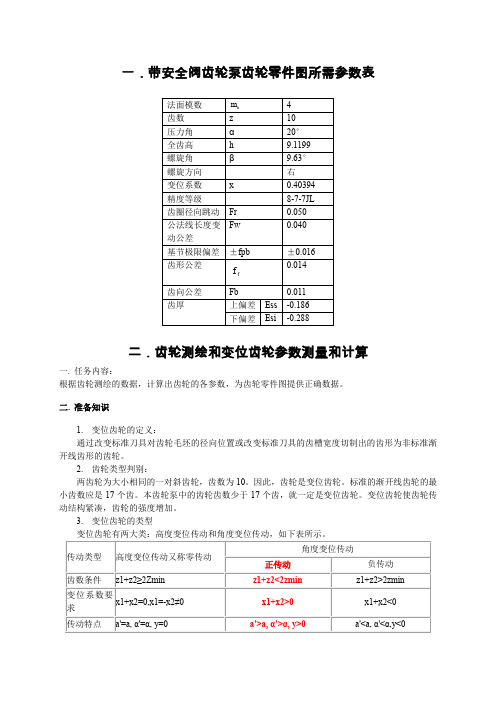
一.带安全阀齿轮泵齿轮零件图所需参数表法面模数nm 4齿数z 10压力角α20°全齿高h 9.1199螺旋角β9.63°螺旋方向右变位系数x 0.40394精度等级8-7-7JL齿圈径向跳动Fr 0.050公法线长度变动公差Fw 0.040基节极限偏差±fpb ±0.016齿形公差ff0.014齿向公差Fb 0.011齿厚上偏差Ess -0.186下偏差Esi -0.288二.齿轮测绘和变位齿轮参数测量和计算一.任务内容:根据齿轮测绘的数据,计算出齿轮的各参数,为齿轮零件图提供正确数据。
二.准备知识1.变位齿轮的定义:通过改变标准刀具对齿轮毛坯的径向位置或改变标准刀具的齿槽宽度切制出的齿形为非标准渐开线齿形的齿轮。
2.齿轮类型判别:两齿轮为大小相同的一对斜齿轮,齿数为10。
因此,齿轮是变位齿轮。
标准的渐开线齿轮的最小齿数应是17个齿。
本齿轮泵中的齿轮齿数少于17个齿,就一定是变位齿轮。
变位齿轮使齿轮传动结构紧凑,齿轮的强度增加。
3.变位齿轮的类型变位齿轮有两大类:高度变位传动和角度变位传动,如下表所示。
传动类型高度变位传动又称零传动角度变位传动正传动负传动齿数条件z1+z2≥2Zmin z1+z2<2zmin z1+z2>2zmin 变位系数要求x1+x2=0,x1=-x2≠0x1+x2>0 x1+x2<0 传动特点a'=a, α'=α, y=0 a'>a, α'>α, y>0 a'<a, α'<α,y<0主要优点小齿轮取正变位,允许z1<zmin ,减小传动尺寸。
提高了小齿轮齿根强度,减小了小齿轮齿面磨损,可成对替换标准齿轮。
传动机构更加紧凑,提高了抗弯强度和接触强度,提高了耐磨性能,可满足a'>a 的中心距要求。
重合度略有提高,满足a'<a 的中心距要求。
变位齿轮参数及计算
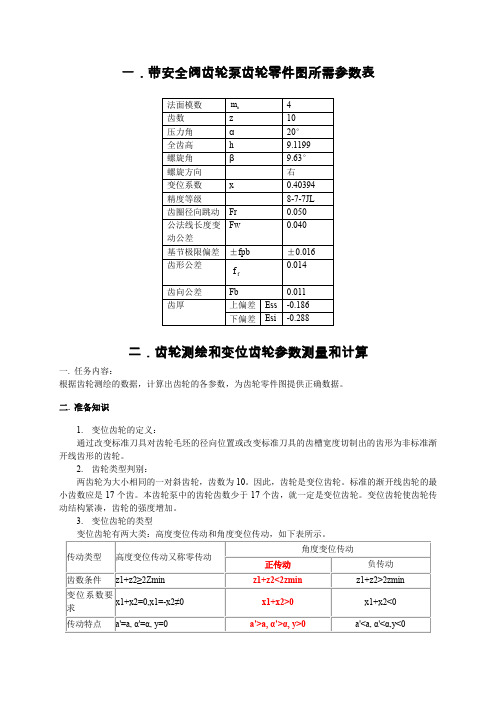
x 0.40394
3.计算其他参数的公式 端面模数 mt mn / cos 啮合角 cos '
a cos a'
总变位系数: xt
z1 z2 (invt' invt ) 2 tan t
z α h β
ff
Fb 上偏差 下偏差
二.齿轮测绘和变位齿轮参数测量和计算
一. 任务内容: 根据齿轮测绘的数据,计算出齿轮的各参数,为齿轮零件图提供正确数据。 二. 准备知识 1. 变位齿轮的定义: 通过改变标准刀具对齿轮毛坯的径向位置或改变标准刀具的齿槽宽度切制出的齿形为非标准渐 开线齿形的齿轮。 2. 齿轮类型判别: 两齿轮为大小相同的一对斜齿轮,齿数为 10。因此,齿轮是变位齿轮。标准的渐开线齿轮的最 小齿数应是 17 个齿。本齿轮泵中的齿轮齿数少于 17 个齿,就一定是变位齿轮。变位齿轮使齿轮传 动结构紧凑,齿轮的强度增加。 3. 变位齿轮的类型 变位齿轮有两大类:高度变位传动和角度变位传动,如下表所示。 传动类型 齿数条件 高度变位传动又称零传动 z1+z2≥2Zmin 角度变位传动 正传动 z1+z2<2zmin x1+x2>0 a'>a, α'>α, y>0 负传动 z1+z2>2zmin x1+x2<0 a'<a, α'<α,y<0
变位齿轮的分度圆直径未知,只能从其他参数的计算公式中作出估算,然后从标准系列中查找最接 近的标准值。 ① 首先从测量所得的啮合中心距计算模数:
m 2a 2 42 4.2 z1 z2 20 2a (49.94 31.81) / 2 4.0289 * 2 1 0.25 2h c
- 1、下载文档前请自行甄别文档内容的完整性,平台不提供额外的编辑、内容补充、找答案等附加服务。
- 2、"仅部分预览"的文档,不可在线预览部分如存在完整性等问题,可反馈申请退款(可完整预览的文档不适用该条件!)。
- 3、如文档侵犯您的权益,请联系客服反馈,我们会尽快为您处理(人工客服工作时间:9:00-18:30)。
《装备制造技术》2013年第1期变位齿轮一般用于调整中心距,改进齿轮啮合情况以及提高齿轮的抗弯强度。
在实际使用中,对于一对相互啮合的齿轮副,往往是其中的一个齿轮采用正变位,而另一个齿轮采用负变位,并且正负变位量的绝对值相等。
这样,我们在加强了一个齿轮强度的同时,又削弱了与其相啮合的另外一个齿轮的强度,无法达到提高整个齿轮副强度的效果。
下面就针对一般正、负变位齿轮副存在的不足,进行了对齿轮副全正变位的设计计算。
1设计计算的方案要实现全正变位的方案,有两个途径:一是,减小齿数,即通过减小齿数先将中心距减小,再通过正变位将中心距增加到原有尺寸,这样还有一个齿轮参数要改变,即啮合角α;二是,齿数不变,但要改变螺旋角β和啮合角α两个参数,以调整中心距。
现分别计算如下:1.1减少齿数我们假定一对齿轮副的原始参数为:齿数:Z1=28,Z2=54,传动比I=Z2/Z1=54/28=1.92857,压力角α=20°,螺旋角β=27.726°,齿顶高系数h a=1,齿根高系数h f=1.25,中心距a=555.818mm,模数m=12mm。
现取Z1=27,Z2=52,则传动比I=Z2/Z1=52/27=1.92593。
(1)计算速比偏差ε:ε=(I-i)/I×100%=0.137%传动比改变很小,说明齿数选择合适。
(2)根据变位齿轮基本公式:a'=acosα/cosα'(1)其中,a为齿数改变后的中心距;a'为改进后的中心距,由于中心距不变,因此a'=a=555.818mm;α为分度圆与节圆重合时的啮合角,取20°;α'为改进后的啮合角。
根据斜齿轮副中心距计算公式:a=m(Z1+Z2)/2COSβ则a'=(m(Z1+Z2)/2COSβ)cosα/cosα'其中:a'=a=555.818mm,m=12,Z2=52,Z1=27,α=20°,β=27.726°。
则cosα'=(m(Z1+Z2)/2COSβ)cosα/a'=0.90531284901α'=25.1345°(25°8'4")根据变位齿轮无侧隙啮合方程:invα'=invα+2tgα((X1+X2)/(Z1+Z2))(2)查表得:inv25.1345°=0.030809,inv20°=0.014904则(X1+X2)=(invα'-invα)(Z1+Z2)/2tgα(X1+X2)=1.7917我们试取X1=0.8,X2=1进行核算:(3)通过计算,我们可以得出齿轮变位后齿形的变化情况:Z1齿根厚度由21.7mm增加到了28.15mm,增加了6.55mm;齿顶厚由8.77mm减小到了5.06mm,减小了3.71mm。
Z2齿根厚度也由26.1mm增加到了29.39mm,增全正变位齿轮副的设计计算张新顺(新疆八一钢铁股份有限公司轧钢厂,新疆乌鲁木齐830022)摘要:变位齿轮一般用于调整中心距,改进齿轮啮合情况以及提高齿轮的抗弯强度。
针对原始的正负变位存在的不足,以及在不改变中心距的情况下,对齿轮副全正变位设计的可行性进行了探索。
经过设计计算和比较,找到了一种新的全正变位齿轮副的设计计算方法,为如何提高齿轮副的整体强度和使用寿命提供了新的途径。
关键词:齿轮副;正变位;负变位;全正变位;提高抗弯强度中图分类号:TH132.41文献标识码:A文章编号:1672-545X(2013)01-0025-02收稿日期:2012-10-05作者简介:张新顺(1975—),男,甘肃古浪人,专业工程师,冶金机械工程师,研究方向:机械设备设计制造与维护。
25Equipment Manufacturing Technology No.1,2013加了3.29mm;齿顶厚由9.36mm减小到了6.48mm,减小了2.91mm。
我们按齿顶厚S=0.4m(模数)极限曲线,判断该变位系数仍在允许范围内。
并且两齿轮的齿根厚度都得到了比较明显的增加,但齿顶厚都过于减小。
1.2齿数不变,改变螺旋角β和啮合角α(1)根据公式1:a'=acosα/cosα'即555.818=(12×(54+28)/2cosβ)cos20°/cosα'式中,β与α、都是未知数,因此先假定β=26°(只能比原值小,否则需要负变位),则cosα'=(12×(54+28)/2cos26°)cos20°/555.818;α'=22.262°(22°15'43")根据公式2:invα'=invα+2tgα((X1+X2)/(Z1+Z2))及查表(渐开线函数表),得inv22.262°=0.020810inv20°=0.014904则:X1+X2=(invα'-invα)×(Z1+Z2)/2tgα=0.665我们取X1+X2=0.7,再重新验算α'还是根据无侧吸啮合方程:invα’=invα+2tgα((X1+X2)/(Z1+Z2))=0.014904+2tg20°×0.7/82=0.021118根据渐开线函数表反推得:α'=22.3654°(22°21'55")再验算螺旋角β根据公式1:a'=acosα/cosα'即555.818=12×(54+28)/2cosβ)cos20°/cos22.3654°β=25.913°(25°54'47")(2)分配变位系数试取X1=0.4,X2=0.3通过计算,我们可以得出齿轮变位后齿形的变化情况:第一,Z1齿根厚度由21.7mm增加到了27.5mm,增加了5.8mm;齿顶厚由8.77mm减小到了7.22mm,仅减小了1.55mm。
第二,Z2齿根厚度也由26.1mm增加到了29mm,增加了2.9mm;齿顶厚由9.36mm减小到了8.73mm,仅减小了0.63mm。
从上述计算可以初步判定变位系数选择分配比较合理。
1.3两种途径的比较两种途径所选择的变位系数虽然都满足齿顶厚S=0.4m(模数)极限条件,但第一种途径,齿数减少后,齿轮的承载能力会有所下降,而且所需的变位系数较大,导致齿顶厚明显减小,容易出现顶部齿面剥落的损坏现象。
通过以上对比,从增强齿轮整体强度考虑,第二种途径较为理想。
2变位后对齿轮使用寿命的影响2.1齿厚增大齿厚增大直接增强了轮齿的抗弯强度,可以有效避免轮齿折断事故。
一般将轮齿的受力情况看作是一个宽度为齿宽b的悬臂梁,齿根部就是危险截面,则危险截面系数w=bS f2/6。
公式中S f即危险截面宽度,其值与齿根宽度成正比关系并与齿根宽度尺寸基本相同。
所以危险截面的弯曲应力为:σf=M/W=6M/bS f2可以看出,轮齿所受的弯曲应力与齿根宽度的平方成反比关系,即在相同力矩的情况下,轮齿根部所受到的弯曲应力会随着齿根厚度的增加而得到明显的减小,从而有效提高齿轮的承载能力。
2.2啮合角增大变位后,啮合角由20°增加到了22°15'43",这有利于增大综合曲率半径,提高齿轮强度,改善齿面磨损条件。
2.3验算重合度ε因为齿轮正变位后会降低齿轮副的重合度,因此需要对重合度进行验算。
根据重合度计算公式:ε={Z1(tga a1-tga')+Z2(tga a2-tga')}/2π式中:α'=22.3654°;a a1、a a2为齿顶圆压力角。
经过计算得ε=2.572,完全满足使用要求。
3结束语通过这种新的变位方式,一对齿轮副中两个齿轮的抗弯强度可以同时得到提高,解决了以往一正一负变位存在的两个不足,即:一是在提高一个齿轮强度的同时,又降低了另一个齿轮的强度;二是正变位系数不能取的过大,因为如果正变位系数去的过大,那么负变位系数也会很大,负变位齿轮的强度降低严重,也会影响到整个齿轮副的使用寿命。
因此这种新的全正变位齿轮副的设计计算方法,为齿轮传动的设计提供了一种全新的设计理念途径。
参考文献:[1]蔡春源.机械零件设计手册[M].北京:冶金工业出版社,1995.[2]江旭昌.大变位齿轮[M].北京:中国建材工业出版社,1997.[3]朱景梓,张展,张焕武.渐开线变位系数的选择[M].北京:北京人民教育出版社,1985.(下转第51页)26《装备制造技术》2013年第1期AllPositiveDisplacementGearDesignCalculationZHANGXin-shun(XinjiangBayiIronandSteelCo.,Ltd.,SteelRollingMill,UrumqiXinjiang830022,China)Abstract:Modifiedgeargenerallyusedtoadjustthecenterdistance,improvegearmeshingconditionandimprovethebendingstrengthofgear.Inthispapertheoriginalpositiveandnegativeshiftdeficiency,andnotchangingthecenterdistanceofgearsismodifieddesignallthefeasibilityoftheresearch.Throughthedesigncalculationandcomparison,findanewfullisshiftgeardesigncalculationmethodsforhowtoimprovethewholestrengthofthegearpairandservicelifeprovidesanewway.Keywords:gearpair;positiveaddendummodification;negativeaddendummodification;Allpositivedisplacement;ImprovethebendingstrengthApplicationofPro/ENGINEERDesignedontheSurfaceYEXuan-lin(CollegeofmechanicalandElectronicEngineering,YunnanRadio&TVUniversity,Kunming650223,China)Abstract:ThroughtheteapotdesignasexampleintroducedtheapplicationofPro/Esoftwaredesignedonthesurfaceentity,throughpractice,elaboratedthepartssurfacemodeling,surfaceeditingfunctionssuchastheapplicationmethod,whichprovesthissoftwarenotonlycanimprovethemodelingspeed,butalsocanshortenthedesigncycle.Keywords:Pro/Esoftware;curvedsurface;solidModeling创建壶把后,在属性命令菜单中选择合并,再在菜单中选择插入→拉伸命令,在拉伸特征操控栏上按下减切按钮,设置特征为减切特征。