复合材料界面及增强材料的表面处理.
复合材料 第七章 复合材料的复合原则及界面

另外,对于成分和相结构也很难作出全 面的分析。 因此,这今为止,对复合材料界面的认 识还是很不充分的,不能以一个通用的模型 来建立完整的理论。 尽管存在很大的困难,但由于界面的重 要性,所以吸引着大量研究者致力于认识界 面的工作,以便掌根其规律。
46
第三节 复合材料的界面设计原则
界面粘结强度是衡量复合材料中增 强体与基体间界面结合状态的一个指标。 界面粘结强度对复合材料整体力学 性能的影响很大,界面粘结过高或过弱 都是不利的。
的不连续性和界面摩擦出现的现象,如抗电性、 电感应性、磁性、耐热性、尺寸稳定性等。
(4)散射和吸收效应
光波、声波、热弹
性波、冲击波等在界面产生散射和吸收,如透 光性、隔热性、隔音性、耐机械冲击及耐热冲 击性等。
28
(5)诱导效应
一种物质(通常是增强物)
的表面结构使另一种(通常是聚合物基体)与 之接触的物质的结构由于诱导作用而发生改 变,由此产生一些现象,如强的弹性、低的
14
(3)纤维与基体的热膨胀系数不能相差过 大,否则在热胀冷缩过程中会自动削弱它们 之间的结合强度。
(4)纤维与基体之间不能发生有害的化学
反应,特别是不发生强烈的反应,否则将引 起纤维性能降低而失去强化作用。
15
(5)纤维所占的体积、纤维的尺寸和分布必 须适宜。
一般而言,基体中纤维的体积含量越高, 其增强效果越显著; 纤维直径越细,则缺陷越小,纤维强度也 越高;
制备具有高冲击强度的避弹衣。
43
由于界面尺寸很小且不均匀、化学
成分及结构复杂、力学环境复杂、对于
界面的结合强度、界面的厚度、界面的 应力状态尚无直接的、准确的定量分析 方法;
44
所以,对于界面结合状态、形态、结 构以及它对复合材料性能的影响尚没有适
复合材料表面处理方法综述
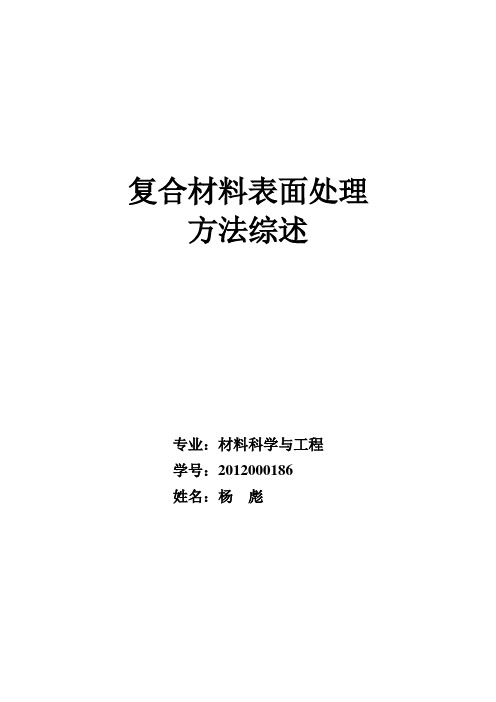
复合材料表面处理方法综述专业:材料科学与工程学号:2012000186姓名:杨彪摘要:界面是复合材料极为重要的微观结构,它作为增强体与基体连接的“桥梁”,对复合材料的物理机械性能有至关重要的影响。
复合材料的界面层及其优化设计,即复合材料界面工程,是复合材料研究的一个重要领域。
界面问题,在复合材料制备中起很大的作用,界面结合的好坏,直接影响复合材料的整体性能。
现针对国内外增强树脂用玻璃纤维、碳纤维以及芳纶纤维的表面处理方法,以强调界面问题的重要性。
关键词:界面,玻璃纤维,碳纤维,芳纶纤维Abstract:The interface is the microscopic structure of the composite material is extremely important, as a "bridge" to enhance and matrix connected, have a crucial impact on the physical and mechanical properties of the composites. The composite interface layer and its optimized design, the composite interface engineering, is an important area of research in the composite. Interface problems play a significant role in the preparation of composite materials, the interface combine the good and bad, a direct impact on the overall performance of the composite material. Now for domestic and reinforced resin with glass fibers, carbon fibers and aramid fibers of the surface treatment method, emphasizing the importance of the problem of the interface. Keywords: interface, glass fiber, carbon fiber, aramid fiber1 前言界面是复合材料极为重要的微观结构,它作为增强体与基体连接的“桥梁”,对复合材料的物理机械性能有重要的影响[1]。
增强材料的表面处理_六_

及所得结果直观性差 ,所以应用不太普遍 ,唯有最后 一种方法被普遍采用 。究其原因 ,其一不需大型仪 器设备 ,一般实验室都可以办得到 ;其二测试的结果 直观性好 。为此下面着重介绍接触角测定法的原理
及运作 。 当固体材料表面具有 Lewis 酸碱性时 ,可用γ+
表示酸性分量即电子接受体或质子给予体对表面自 由能的贡献 γ, - 表示碱性分量 ,即质子接受体或电子 给予体对表面自由能的贡献 ,两者与表面自由能酸 碱分量γAB有如下的关系 :
大部分复合材料复合工艺的固化制度都是根据
纯树脂基体的固化条件而制定的 。这与实际的复合 材料固化体系有较大的差别 ,因此很难保证产品达 到最佳性能 。尤其是加入大量的增强剂后 ,由于其 表面状态的不同 ,对体系的固化过程影响必须予以 考虑 ,因为增强材料的比表面高 ,故它在体系中所占
的界面积比份较大 。在这大比份的界面积中 ,引入 一些促进 (或减慢) 固化反应的基团 ,不能不影响复 合材料体系的固化过程 。孙慕瑾等[57 ]采用动态力学 的扭辫分析技术 ( TBA) 研究了碳纤维表面等离子体 处理对 CFRP 固化过程的影响 ,发现表面处理后固 化 反 应 活 化 能 变 小 , 从 11152kcal/ mol 下 降 到 11132kcal/ mol , CFRP 的 Tg 从 218 ℃上升到 220 ℃, 说明 CF 表面处理后 ,表面上生成的 - COOH、- OH 促进了固化反应 ,减低了固化反应活化能 ,加快了反 应速度 ,增加交联度 ,使 Tg 上升 。此外孙慕瑾等[58 ] 采用同样技术又研究了芳纤表面接枝与不接枝丙烯 酸对 AFRP 固化过程的影响 。结果表明 ,固化活化 能从 10185kcal/ mol 下降到 9128kcal/ mol ,反应速度 常数 从 814 ×10 - 3 分 - 1 升 到 2173 ×10 - 2 分 - 1 。 AFRP 的 Tg 从 212 ℃升到 215 ℃。这些结果充分说 明增强材料表面处理与否 ,即表面状态的不同对复 合材料固化过程有影响 ,当然最终会影响复合材料 的性能 。为了确定这种影响 ,为复合工艺提供较科 学合理的固化制度 ,对这种影响进行表征是十分必 要的 。从目前的技术水平来看 ,采用动态力学的扭 辫分析 ( TBA) 来表征是最好的 ,因为分析的试样与 复合材料实体是一致的 ,而且试样制备简单 ,用量 少 ,测试灵敏度与精度高 。 41317 界面粘接强度的表征
复合材料的界面性能与优化分析
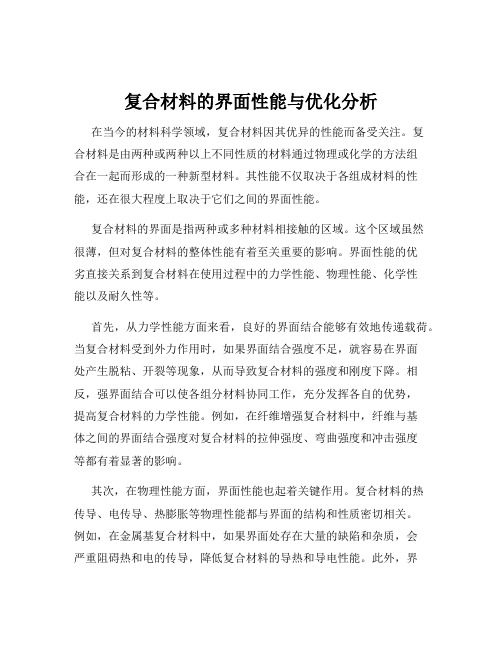
复合材料的界面性能与优化分析在当今的材料科学领域,复合材料因其优异的性能而备受关注。
复合材料是由两种或两种以上不同性质的材料通过物理或化学的方法组合在一起而形成的一种新型材料。
其性能不仅取决于各组成材料的性能,还在很大程度上取决于它们之间的界面性能。
复合材料的界面是指两种或多种材料相接触的区域。
这个区域虽然很薄,但对复合材料的整体性能有着至关重要的影响。
界面性能的优劣直接关系到复合材料在使用过程中的力学性能、物理性能、化学性能以及耐久性等。
首先,从力学性能方面来看,良好的界面结合能够有效地传递载荷。
当复合材料受到外力作用时,如果界面结合强度不足,就容易在界面处产生脱粘、开裂等现象,从而导致复合材料的强度和刚度下降。
相反,强界面结合可以使各组分材料协同工作,充分发挥各自的优势,提高复合材料的力学性能。
例如,在纤维增强复合材料中,纤维与基体之间的界面结合强度对复合材料的拉伸强度、弯曲强度和冲击强度等都有着显著的影响。
其次,在物理性能方面,界面性能也起着关键作用。
复合材料的热传导、电传导、热膨胀等物理性能都与界面的结构和性质密切相关。
例如,在金属基复合材料中,如果界面处存在大量的缺陷和杂质,会严重阻碍热和电的传导,降低复合材料的导热和导电性能。
此外,界面的存在还会影响复合材料的热膨胀系数,如果界面结合不良,在温度变化时容易产生热应力,导致复合材料的变形和破坏。
化学性能方面,界面是复合材料与外界环境相互作用的前沿阵地。
界面的化学稳定性决定了复合材料的耐腐蚀性、抗氧化性等化学性能。
如果界面处容易发生化学反应,如氧化、腐蚀等,就会削弱复合材料的性能,缩短其使用寿命。
例如,在聚合物基复合材料中,界面的亲水性或疏水性会影响其对水分的吸收和扩散,进而影响复合材料的耐湿性和耐老化性能。
那么,如何优化复合材料的界面性能呢?这需要从多个方面入手。
一方面,可以通过对原材料的表面处理来改善界面性能。
例如,对于纤维增强复合材料,可以对纤维表面进行氧化、涂层等处理,增加纤维与基体之间的化学键合和物理结合,提高界面结合强度。
复合材料材料的界面理论

R X Si X X H2O HO R Si R OH + 3HX
(ⅱ)玻璃纤维表面吸水,生成羟基。
OH Si O OH Si O
10
(ⅲ)硅醇与吸水的玻璃纤维表面反应,又分三步 第一步:硅酸与吸水的玻璃纤维表面生成氢键;
5
3.3.2增强材料的表面处理
1.碳纤维的表面处理 表面处理的作用:使复合材料不仅具有良好的界面粘接力、 层间剪切强度,而且其界面的抗水性、断裂韧性及尺寸稳 定性均有明显的改进。此外,通过碳纤维表面改性处理, 还可制得具有某种特殊功能的复合材料。
1)氧化法 (1)气相法(或干法):以空气、氧气、臭氧等氧化剂,采用 等离子表面氧化或催化氧化法。 (2)液相法(或湿法):有硝酸、次氯酸钠加硫酸、重铬 酸钾加硫酸、高锰酸钾加硝酸钠加硫酸氧化剂及电解氧化 法等。
2
3.3增强材料的表面性质与处理
3.3.1表面性质
表面性质:表面的物理特性、化学特性和表面自由能。 表面性质与材料的组成和结构有关。 1. 物理持性: 指材料的表面形态和比表面积。 2. 化学特性: 指材料表面化学组成和表面反应活性。 增强材料表面的化学组成及结构,决定了增强材料 表面自由能的大小、润湿性及化学反应活性。关系 到增强材料是否需进行表面处理,其表面是否容易 与环境接触物反应(如与氧、水、有机物等反应),表 面与基体材料间是否能形成化学键。 增强纤维内部的化学组成与其表面层的化学组成不 完全相同。 3
第三步:高温干燥(水分蒸发),硅醇与吸水玻璃纤维间进行 醚化反应;
R HO H O Si O Si O H O H H R O O H O Si O Si O H OH -H2O O R Si O Si O O R Si O Si
多层复合材料的界面表征与优化

多层复合材料的界面表征与优化随着科学技术的不断进步,多层复合材料在现代工程中得到了广泛的应用。
多层复合材料由不同种类的材料层叠组合而成,每一层材料都有其独特的特性和功能。
其中,界面是多层复合材料中至关重要的部分,它直接影响着多层复合材料的性能和强度。
因此,对多层复合材料的界面进行表征与优化,对于提高材料的整体性能具有重要意义。
一、界面表征多层复合材料的界面是由两个不同材料的层之间的接触面形成的。
在界面处,两种材料的性质和结构会发生变化,这种变化直接影响着材料的性能。
因此,了解和表征多层复合材料的界面是非常必要的。
1. 宏观表征宏观表征方法主要通过对多层复合材料整体性能的测试和分析来了解界面的特性。
例如,通过静态拉力试验、冲击试验、疲劳试验等,可以测量材料的强度、韧性、疲劳寿命等指标,并通过对测试结果的分析,得到界面的性能和结构信息。
2. 微观表征微观表征方法主要通过显微观察和材料表面分析技术来了解多层复合材料界面的结构和组成。
例如,使用电子显微镜观察多层复合材料的交界面,可以观察到不同材料间的结合情况、界面的致密性以及可能存在的缺陷等信息。
此外,还可以利用X射线光电子能谱(XPS)、傅里叶变换红外光谱(FTIR)等技术,分析界面的化学成分和表面结构,进一步了解界面的特性。
二、界面优化多层复合材料的界面优化是指通过改变界面结构和性质,提高多层复合材料的整体性能和强度。
界面优化可以从多个方面进行,下面介绍几种常用的优化方法。
1. 表面处理表面处理是指通过改变材料表面的化学性质和结构,提高多层复合材料界面的粘结强度和界面结构的致密性。
表面处理包括物理方法和化学方法两种。
常用的物理方法有喷砂、电火花加工等,而化学方法则包括溶液浸泡、化学涂覆等。
通过表面处理,可以增加材料界面的接触面积,提高界面的亲和力,从而增强界面的结合力。
2. 加强剂应用在多层复合材料的界面中添加适量的加强剂能够有效地提高界面的强度和韧性。
《无机复合材料及工艺》第二章——增强材料

3、碳纤维(Carbon fiber) (1)、引言
碳纤维属于高新技术产品,它不仅具有炭素材料的特性,如质量轻, 强度高,耐热,耐腐蚀,还具有金属材料的某些特性,具有良好的 导电和导热性,在各类复合材料(PMC、MMC、CMC和C/C)中得到广 泛应用。 碳纤维增强复合材料广泛应用于航空航天、军事、交通运输、机械 制造、电子工业、体育用品、建筑材料(修补)、生物材料、医疗 器具等各行各业。 碳纤维的大量和广泛应用与其价格的不断降低有关。随着碳纤维的 生产规模的扩大、其价格由原来的数千元/kg,降至数百元/kg。 碳纤维与玻璃纤维一样,可以进行编织成各种碳纤维布,或制成碳 纤维毡使用。
(4)玻璃纤维的特性和应用
特性:
典型性能: 密度:2.4~2.8 g/cm3 抗拉强度:3~4.6 GPa(为高强度钢的2~3倍) 弹性模量:70~110 GPa(与铝和钛合金模量相当) 比强度为:12.5~18.4×106 cm(为高强度钢的6~10倍) 比模量为:2.8~4.0×107 cm(略高于高强度钢) 不燃、不腐、耐热、高拉伸强度、小断裂延伸率、化学稳定性好、 电绝缘性能好;但不耐磨、脆而易折。 可加工成纱、布、带、毡等形状; 可作为有机高聚物基或无机非金属材料(如水泥)复合材料的增 强材料。
对结构复合材料而言,首先考虑的是增强材料的强度、模量和密度。 其与基体物理及化学相容性主要反映界面作用和影响。
二、纤 维(fiber)
直径细到几微米或几十微米,而长度比直径大许多倍的 材料。 其长径比(aspect ratio)一般大于1000。 作为增强材料使用时,纤维一般都具有高模量、高强度。 大多数是有机高分子纤维,也有无机纤维和金属纤维。 重点介绍:
(2)、碳纤维分类
9. 聚合物复合材料与增强体表面改性-2015
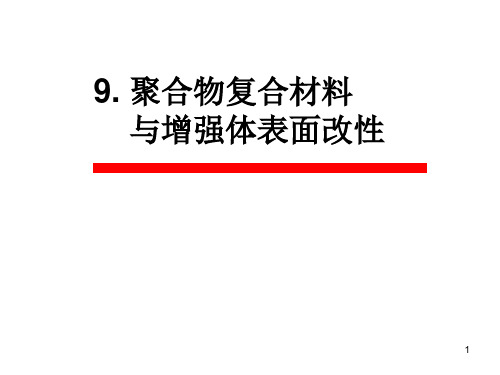
9.2.2 玻璃纤维表面处理技术
(1)热处理 就是利用高温使玻璃纤维表面的原有胶料氧 化分解,同时除去玻璃纤维由于储存而吸附的水。 如果是纺织型浸润剂处理的玻璃纤维,高温下 还可除去其润滑油。
王赫,等. 绝缘材料,2007
20
9.2.2 玻璃纤维表面处理技术
(2)酸碱刻蚀处理
酸碱刻蚀处理 是通过酸碱在玻纤表面进行化学反应形成一些凹陷或微孔。
(4). 玻璃纤维增强聚碳酸酯 聚碳酸酯是一种钢韧相兼的工程塑料,但容易产生应力开裂、 耐疲劳性能差。加入玻璃纤维后疲劳强度提高2-3倍,耐应 力开裂性能提高6-8倍,耐热性提高10-20oC,线膨胀系 数减少,适合做耐热的机械零件。
9
(5). 玻璃纤维增强聚酯 机械强度较其他玻璃纤维增强热塑性塑料均高耐热性提高 幅度最大,85oC-240oC,耐热度最高在高温下易水解, 不适合在高温水蒸气下使用
5
Байду номын сангаас
各种玻璃钢与金属性能的比较
6
B. 玻璃纤维增强热塑性塑料(FR-TP)
热塑性塑料:聚酰胺、聚丙烯、低压聚乙烯、ABS树脂、聚甲醛、聚碳酸酯 聚苯醚
几种典型金属及FR-TP的强度对比
7
(1). 玻璃纤维增强聚丙烯(FR-PP)
玻璃纤维大大提高聚丙烯的机械强度,短切玻璃纤维增加到30 -40%时,强度达到100MPa,并能改善聚丙烯的低温脆性。 FR-PP吸水率小,在水中长时间煮对强度影响不大。
颗粒等)
层压
粘合
2
9.1.1 聚合物基复合材料的种类和性能
1、聚合物基复合材料的优点 a. 具有比较高的比强度和比模量,可以和常用的金属材料进行比较,
力学性能相当出色。 b. 抗疲劳性能好, 纤维与基体的界面能够阻止裂纹的扩展,在破坏
复合材料的界面性能与优化

复合材料的界面性能与优化在现代材料科学领域,复合材料因其出色的性能而备受关注。
复合材料是由两种或两种以上具有不同物理和化学性质的材料组合而成,其性能并非各个组分材料性能的简单加和,而是通过各组分之间的协同作用实现了性能的优化和提升。
而在这其中,复合材料的界面性能起着至关重要的作用。
复合材料的界面,简单来说,就是不同组分材料之间相互接触和作用的区域。
这个区域虽然在尺寸上相对较小,但却对复合材料的整体性能产生着深远的影响。
就好像一个团队中各个成员之间的沟通与协作环节,虽然看似细微,却决定着整个团队的运作效率和成果。
首先,我们来探讨一下复合材料界面性能的重要性。
良好的界面性能能够有效地传递载荷。
当复合材料受到外力作用时,如果界面能够将应力从一种材料传递到另一种材料,那么整个复合材料就能更好地承受外力,从而表现出更高的强度和韧性。
界面性能还对复合材料的热性能有着重要影响。
不同的材料具有不同的热膨胀系数,如果界面结合不好,在温度变化时就容易产生热应力,导致材料性能下降甚至失效。
此外,界面性能也会影响复合材料的耐腐蚀性能和电性能等。
那么,复合材料的界面性能具体包括哪些方面呢?界面的结合强度是一个关键因素。
如果结合强度过低,在使用过程中容易出现界面脱粘,从而降低材料的性能;而结合强度过高,又可能导致材料在受到冲击时无法通过界面的解离来吸收能量,造成脆性断裂。
界面的化学稳定性也是不容忽视的。
在一些恶劣的环境中,界面处容易发生化学反应,从而影响材料的长期使用性能。
界面的微观结构同样重要,它决定了界面的物理和化学性质,进而影响复合材料的整体性能。
接下来,我们看看影响复合材料界面性能的因素。
材料的表面处理方式是一个重要方面。
通过对增强材料表面进行化学处理、物理处理或者涂层处理,可以改变其表面的化学组成和物理形貌,从而提高与基体材料的相容性和结合力。
制备工艺条件也会对界面性能产生影响。
例如,在复合材料的制备过程中,温度、压力、时间等参数的控制都会影响界面的形成和性能。
复合材料的界面状态解析了解界面的分类掌握复
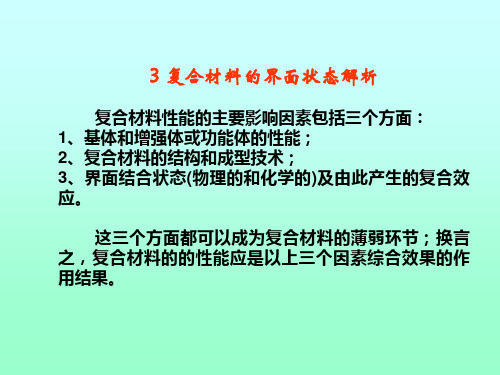
(3)表面处理的最优化技术。 (4)粉体材料在基体中的分散:
①、分散状态的评价; ②、分散技术及机理; ③、分散状态与复合材料性能。 (5)复合技术的优化及其机理。
图3.3 材料粘接的破坏形式
作业: 6、复合材料的界面层,除了在性能和结构上不同于相邻 两组分相外,还具有哪些特点; 7、简述复合材料界面的研究对象; 8、简述与表面张力有关的因素。 9、吸附按作用力的性质可分为哪几类?各有什么特点? 10、利用接触角的知识,讨论固体被液体的浸润性。 11、界面的相容性指什么?如何确定?
当固体表面的原子的原子价被相邻的原子所饱和, 表面分子与吸附物之间的作用力是分子间引力(范德华 力)。
特点:
1)、无选择性,吸附量相差较大;
2)、吸附可呈单分子层或多分子层;
3)、物理吸附、解吸速度较快,易平衡。
一般在低温下进行的吸附是物理吸附。
3.3.2.2 化学吸附
当固体表面的原子的原子价被相邻的原子所饱和,
根据物质的聚集态,可以得到五种类型的界面,即气-液 (g-l)、气-固(g-s)、液-液(l-l)、液-固(l-s)、固-固 (s-s)界面。
通常的研究中,习惯于把气-液(g-l) 、气-固(g-s) 界面分别称为液相表面、固相表面。
注意: 对于复合材料来说,界面并非是一个理想的几何面。
实验证明: 复合材料中相与相之间的两相交接区是一个具有相当厚
增强体 F
表面处理技术
增强体
F 表面 F/I 界面
表面处理物质层
I 表面 I 结构
增强体
F/I 界面
表面处理物质层
复合技术
基体
I/M 界面
基体 M
增强体 基体
F/M 界面
材料表面处理对复合材料界面性能的影响研究

材料表面处理对复合材料界面性能的影响研究复合材料广泛应用于航空航天、汽车制造和建筑等领域,因为它们具有优异的力学性能和轻质化特征。
然而,复合材料的界面区域对整体性能至关重要。
为了增强界面性能,材料表面处理技术成为研究的热点之一。
本文将探讨材料表面处理对复合材料界面性能的影响。
一、材料表面处理方法材料表面处理方法广泛应用于改善复合材料的界面性能。
其中包括物理方法和化学方法。
物理方法主要包括射线辐照、机械磨削和喷砂等,旨在提高材料表面的粗糙度和附着力。
化学方法如表面活性剂的引入、化学改性和表面微结构的修饰等,以提高界面的亲合力和粘附力。
二、材料表面处理对界面粘附强度的影响表面处理对复合材料界面的粘附强度具有显著影响。
一方面,物理方法如机械磨削和喷砂可以增加界面的粗糙度,增强了界面的机械锁合效应,从而提高了复合材料的粘附强度。
另一方面,化学方法如引入表面活性剂可以增加界面的化学键数量,提高了界面的粘附强度。
研究发现,采用化学方法处理复合材料的表面,能够使界面粘附强度相较于未处理表面提高10%-20%。
三、材料表面处理对界面能量耗散的影响界面能量耗散是衡量界面性能的重要指标之一。
表面处理能够有效提高复合材料的界面能量耗散能力。
通过物理方法处理复合材料表面,如喷砂或机械磨削,能够增加界面的粗糙度,增加位移钳合阻力,从而提高界面的能量耗散能力。
此外,通过化学方法处理表面,如引入表面活性剂,可以增加界面的摩擦阻尼,提高能量的耗散。
实验证明,经过表面处理的复合材料界面能量耗散能力相比未处理表面提高了15%-30%。
四、材料表面处理对界面的耐久性的影响表面处理技术在提高界面的耐久性方面发挥了重要作用。
物理方法处理表面,如射线辐照或喷砂处理,可以去除材料表面的污染和氧化层,减少界面的缺陷和腐蚀,从而提高界面的耐久性。
化学方法可以改变表面的化学特性,增加界面的抗腐蚀性能。
实验研究表明,经过表面处理的复合材料界面耐久性相较于未处理表面有所提高,延长了复合材料的使用寿命。
复合材料工艺流程

复合材料工艺流程复合材料是由两种或两种以上的不同材料按照一定方式组合而成的新材料。
它具有轻量化、高强度、耐疲劳、耐腐蚀等优点,广泛应用于航空航天、汽车、建筑等领域。
下面将为大家介绍一下复合材料的工艺流程。
首先是原材料的准备。
复合材料的主要组成部分是基体材料和增强材料。
基体材料一般是有机树脂,如环氧树脂、聚酯树脂等;增强材料可以是玻璃纤维、碳纤维、蛙纹石等。
在准备原材料时,需要对其进行测量和筛选,确保质量稳定和合格。
接下来是预处理过程。
首先需要对增强材料进行表面处理,以提高其与基体材料的粘接性能。
常见的表面处理方法有打磨、清洗、化学处理等。
然后需要对基体材料进行配比和加热处理,使其能够流动和固化。
然后是制备复合材料的成型工艺。
常见的成型工艺有手工层叠成型、压缩成型、注塑成型等。
手工层叠成型是最基本和简单的方法,适用于少量生产和特殊形状的制品。
压缩成型是将纤维预浸料放入模具中,经过热压固化形成制品。
注塑成型是将预浸料注入模具中,经过高温和高压形成制品。
不同的成型工艺有不同的适用范围和工艺参数,需要根据具体情况进行选择。
接下来是固化过程。
成型后的复合材料需要进行固化处理,以使其达到预期的力学性能。
固化过程一般通过加热和化学反应来完成。
具体的固化温度、时间和环境条件需要根据基体材料和增强材料的特性来确定,以确保固化的充分和均匀。
最后是后处理过程。
成型和固化后的复合材料需要进行修整和表面处理,以使其达到美观和使用要求。
修整过程一般包括切割、打磨、打孔等,表面处理一般包括涂装、清洗、抛光等。
这些过程需要经过严格的操作和控制,以确保最终产品的质量和性能。
以上就是复合材料的工艺流程。
这个过程需要经过多个步骤和环节的精细操作,以确保最终产品的质量和性能。
复合材料的制备工艺在不断创新和发展,为各个领域的应用提供了更多的可能性。
同时,也需要注意整个过程中的环境保护和安全生产,以促进可持续发展和健康发展。
复合材料的界面
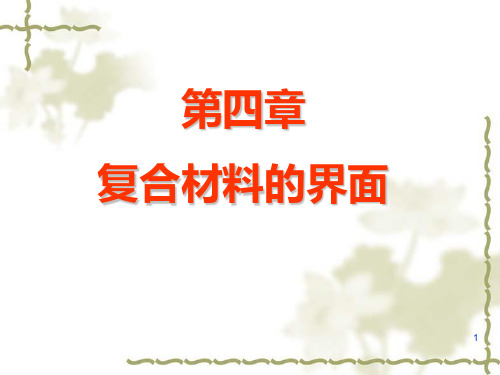
28
物理相容性中最重要的是要求纤维与基体的 物理相容性中最重要的是要求纤维与基体的 热膨胀系数匹配。 热膨胀系数匹配。 当纤维中残余应力是压应力时,应注意纤维 纤维中残余应力是压应力时 中残余应力是压应力 的屈曲;当基体的残余应力为拉应力时,应考虑 屈曲; 基体的残余应力为拉应力时 的残余应力为拉应力 界面和基体中的裂纹扩展 界面和基体中的裂纹扩展。 裂纹扩展。
8
界面最佳态的衡量是当受力发生开裂时, 界面最佳态的衡量是当受力发生开裂时, 的衡量是当受力发生开裂时 这一裂纹能转为区域化而不产生近一步界面 脱粘。即这时的复合材料具有最大断裂能 脱粘。即这时的复合材料具有最大断裂能和 最大断裂能和 一定的韧性。 一定的韧性。
9
由此可见, 研究和设计界面时 由此可见,在研究和设计界面时, 不应只追求界面粘结而应考虑到最优化 界面粘结而应考虑到 不应只追求界面粘结而应考虑到最优化 和最佳综合性能。 和最佳综合性能。
27
3. 残余应力
物理相容性要求金属基体有足够的韧性和 物理相容性要求金属基体有足够的韧性和强 要求金属基体有足够的韧性 度,还要求在材料中出现裂纹和位错移动时基体 还要求在材料中出现裂纹 位错移动时基体 裂纹和 上产生的局部应力不在增强纤维上形成高应力 上产生的局部应力不在增强纤维上形成高应力。 高应力。
29
在选择金属复合材料的组分材料时, 在选择金属复合材料的组分材料时,为避免 过高的残余应力,要求增强纤维与基体的热膨胀 过高的残余应力,要求增强纤维与基体的热膨胀 系数不要相差很大。 系数不要相差很大。
30
4.2.3 陶瓷基复合材料的界面
在陶瓷基复合材料中,增强纤维与基体之间形 在陶瓷基复合材料中, 质地均匀, 成的反应层质地均匀 对纤维和基体都能很好地结 成的反应层质地均匀,对纤维和基体都能很好地结 合,但通常是脆性的。因增强纤维的横截面多为圆 但通常是脆性 脆性的 故界面反应层常为空心圆筒状 空心圆筒状, 厚度可控。 形,故界面反应层常为空心圆筒状,其厚度可控。
玻璃纤维增强复合材料的表面处理及涂装工艺

玻璃纤维增强复合材料的表面处理及涂装工艺玻璃纤维增强复合材料是种具有优异力学、物理、化学、热特性的新型材料,常被用于航空、汽车等领域的制造。
而对于玻璃纤维增强复合材料进行表面处理和涂装是十分必要的,可以有效地改善材料的外观和性能,也能提高其耐用性和稳定性。
本文将介绍玻璃纤维增强复合材料的表面处理和涂装工艺,以及其实现的优点和应用。
一、表面处理工艺1、材料清洗表面处理第一步是进行清洗,以去除材料表面的油脂、尘土和其他污渍。
尤其这一步极其关键,过程中不能出现任何失误,否则会影响后续表面处理的效果。
常用的清洗方法有溶液清洗、高压水清洗、喷雾清洗等。
清洗后,使用风扇、热空气或其他干燥器具对表面进行烘干,以确保表面完全干燥。
2、表面粗化和研磨粗糙表面有助于附着力和表面涂层的牢固度。
针对不同的表面要求,可采用喷砂、砂纸、钢丝刷等方法进行表面粗糙度控制。
需要注意的是,过度研磨可能会使表面产生损伤,造成表面的非均匀性和腐蚀等不良后果。
3、产品预处理产品预处理是一项必需的表面处理过程,在这个过程中需要进行去水、酸洗、放镀等操作,以满足表面涂装或镀层的要求。
常用的处理方法有碱洗、电解处理等。
二、涂装工艺涂装工艺是表面处理的下一步,需要根据不同需求制定相应的处理方法和材质选择。
具体的工艺流程有:1、底涂(基涂料)底涂能够为表面提供化学稳定性、抗水解性和耐磨性等特性,能够产生沉积于材料表面的薄膜。
底涂料的选择是根据复合材料的种类、表面应力、耐久性、抗剥离等特征进行选择。
2、面涂面涂是涂装工艺的最后一步,主要目的是提供更美观的表面外观和增强耐久性。
不同的面涂材料有不同的特点,可以根据实际需求进行选择,如丙烯酸、环氧树脂等。
三、优点与应用1、优点玻璃纤维增强复合材料的表面处理和涂装能够有效提高其外观和性能,使其具有更好的耐久性和稳定性。
此外,表面处理和涂装工艺也可以为产业界提供更多的选择,从而推动玻璃纤维增强复合材料在更广泛的领域中得到广泛应用。
复合材料第3章----复合材料的界面

钨丝/ 铜 Al2O3纤维 / 铜 Al2O3纤维 / 银 硼纤维(表面涂BN)/ 铝 不锈钢丝/ 铝 SiC纤维(CVD)/ 铝
硼纤维 / 铝
镀铬的钨丝/ 铜 碳纤维 / 镍 钨丝/ 镍
合金共晶体丝/ 同一合金
钨丝/铜-钛合金 碳纤维/ 铝(>580℃)
Al2O3纤维/ 钛 硼纤维/ 钛
硼纤维/ 钛-铝 SiC纤维/强材料与含有两种以上元素的金属基体之间发生化学反应, 形成反应产物后,反应产物还会与其它基体元素发生交换反应,产 生界面不稳定。
例如硼纤维/钛合金(Ti-Al-1V-1Mo),硼与钛在界面首先发 生反应:
Ti(Al) + B → (Ti·Al)B2 再发生交换反应:
(Ti·Al)B2 + Ti → TiB2 + Ti(Al) 电子探针证实了界面反应的最终产物是TiB2。
总体要求:
4①面.均希金匀望属、增有强基效材复地料传与合递基材应体力之料;间界具有面良设好的计润湿性,粘着强,有利于界
②增强材料与基体润湿后互相间发生一定程度的溶解,保持适宜的 界面结合力,提高复合材料的强韧性;
③产生适量的界面反应,而界面反应物质地均匀、无脆性异物、 不成为复合材料内部缺陷(裂纹)源,界面反应能够得到一定控制。
2金属基复合材料的界面
金属基复合材料由于基体与增强物复合的温度较高,基体与增强物 易发生相互作用而生成化合物,而基体与增强物互相扩散而形成扩散层.
复合材料的界面
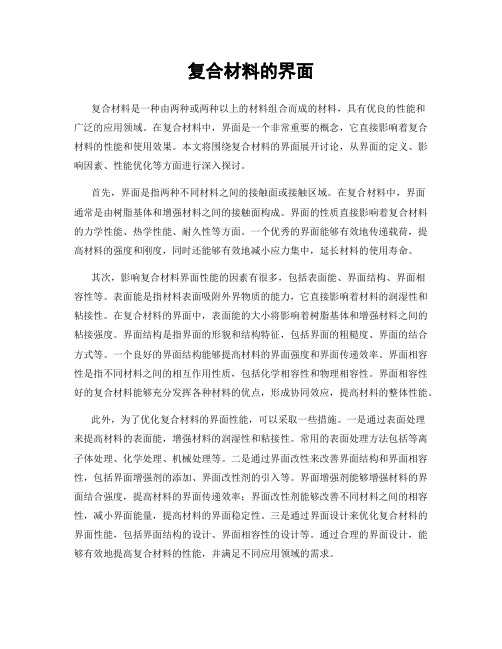
复合材料的界面复合材料是一种由两种或两种以上的材料组合而成的材料,具有优良的性能和广泛的应用领域。
在复合材料中,界面是一个非常重要的概念,它直接影响着复合材料的性能和使用效果。
本文将围绕复合材料的界面展开讨论,从界面的定义、影响因素、性能优化等方面进行深入探讨。
首先,界面是指两种不同材料之间的接触面或接触区域。
在复合材料中,界面通常是由树脂基体和增强材料之间的接触面构成。
界面的性质直接影响着复合材料的力学性能、热学性能、耐久性等方面。
一个优秀的界面能够有效地传递载荷,提高材料的强度和刚度,同时还能够有效地减小应力集中,延长材料的使用寿命。
其次,影响复合材料界面性能的因素有很多,包括表面能、界面结构、界面相容性等。
表面能是指材料表面吸附外界物质的能力,它直接影响着材料的润湿性和粘接性。
在复合材料的界面中,表面能的大小将影响着树脂基体和增强材料之间的粘接强度。
界面结构是指界面的形貌和结构特征,包括界面的粗糙度、界面的结合方式等。
一个良好的界面结构能够提高材料的界面强度和界面传递效率。
界面相容性是指不同材料之间的相互作用性质,包括化学相容性和物理相容性。
界面相容性好的复合材料能够充分发挥各种材料的优点,形成协同效应,提高材料的整体性能。
此外,为了优化复合材料的界面性能,可以采取一些措施。
一是通过表面处理来提高材料的表面能,增强材料的润湿性和粘接性。
常用的表面处理方法包括等离子体处理、化学处理、机械处理等。
二是通过界面改性来改善界面结构和界面相容性,包括界面增强剂的添加、界面改性剂的引入等。
界面增强剂能够增强材料的界面结合强度,提高材料的界面传递效率;界面改性剂能够改善不同材料之间的相容性,减小界面能量,提高材料的界面稳定性。
三是通过界面设计来优化复合材料的界面性能,包括界面结构的设计、界面相容性的设计等。
通过合理的界面设计,能够有效地提高复合材料的性能,并满足不同应用领域的需求。
综上所述,复合材料的界面是一个非常重要的概念,它直接影响着复合材料的性能和使用效果。
材料表面与界面-第四章-复合材料的界面及界面优化
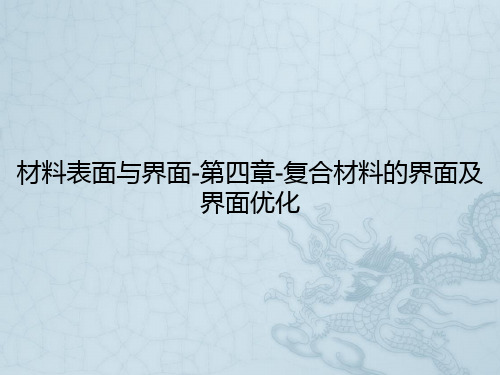
复合材料的增强机制及性能
1. 纤维增强复合材料的增强机制
在纤维增强复合材料中,纤维是材料主要 承载组分,其增强效果主要取决于纤维的 特征、纤维与基体间的结合强度、纤维的 体积分数、尺寸和分布。
在纤维增强复合材料中,纤维是材料主要
碳
承载组分,其增强效果主要取决于纤维的 纤
维
特征、纤维与基体间的结合强度、纤维的 体积分数、尺寸和分布。
环氧树脂 / 碳纤维(高弹性)
1240
环氧树脂 / 芳纶纤维(49) 1380
环氧树脂 / 硼纤维(70 % Vf ) 1400-2100
纵向弹性模 量 GPa
6.9
45
145 76
210-280
聚合物基纤维增强复合材料零件
碳纤维增强聚酰亚胺复合材料制航空 发动机高温构件
芳纶刹车片
3. 纤维--金属(或合金)复合材料
1电子显微镜观测法基材表面形貌分析尤其是经表面处理的基材未处理碳纤维的表面形态低温等离子处理碳纤维表面形态增强体材料表面形貌分析氧等离子处理后经80与苯乙烯反应4小时接枝聚苯乙烯分子链的碳纤维照片复合材料的断面形貌分析碳铝复合材料不同界面结合时的强度与断口特征结合状态拉伸强度mpa断口形貌不良结合206纤维大量拔出长度很大呈刷子状结合适中612纤维有拔出现象并有一定长度铝基体有缩颈现象并可发现劈裂状结合稍强470出现不规则断面并可看到很短的拔出纤维结合太强224典型脆断形式平断口2红外光谱与拉曼光谱波长为25m区间的波谱称为红外光谱它是分子键的振动光谱
Al2O3片
(2) 粒子增强复合材料
(3)叠层复合材料。
Al2O3纤维
三、复合材料的命名
(1)以基体为主来命名 例如金属基复合材料。 (2)以增强材料来命名 如碳纤维增强复合材料。 (3)基体与增强相并用 如“C/Al复合材料”即
复合材料的界面
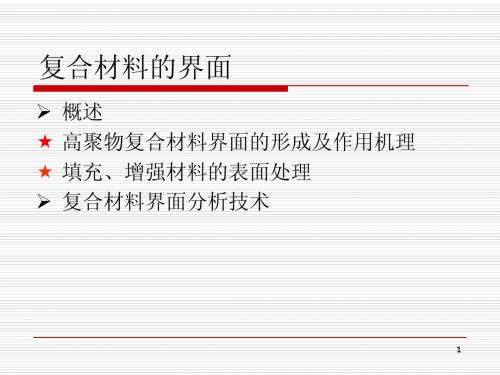
w F dx 2 ldx dA
w
dA
10
表示使液体增加单位面积所需作的(非体积)功,
单位为 J m2 ,称为比表面能。 由于恒T.p下,可逆非体积功等于吉布斯函变
W dGT , P dA
G ( )T , P A
等于系统增加单位面积时所增加的吉布斯函数,
即
sv sl lv cos
——杨氏方程
sv sl lv时, cos 1, 0 ,完全润湿,粘附功最大
14
sv sl时, cos 0, 90 , 不润湿 lv sv sl 0时,0< cos 1,0 90 , 润湿
24
2、A-151、A-172: 1,2-聚丁二烯树脂,丁苯树脂
A-151 化学名称:乙烯基三乙氧基硅烷 分子式:CH2=CHSi(OC2H5)3 A-172 化学名称:乙烯基三(2-甲氧基乙氧基) 硅烷 分子式:CH2=CHSi (OCH2CH2OCH3)
25
3、KH-560: 环氧树脂
化学名称:γ-缩水甘油醚氧丙基三甲氧基硅烷 OCH3 分子式: CH2 Si OCH3 OCH3 O
43
21
22
R基团与树脂基体的作用机理: 以R基团为乙烯基—CH=CH2与不饱和聚酯树脂中的不饱 和双键的反应为例:
23
偶联剂的品种及其应用范围 1、KH-570: 不饱和聚配树脂
化学名称:γ-(甲基丙烯酰氧)丙基三甲氧基硅烷 分子式:CH2=C(CH3)COOC3H6Si(OCH3)3 国外对应牌号: A-174(美国联合碳化物公司) KBM-503(日本信越化学工业株式会社) SH-6030(美国道康宁化学公司)
- 1、下载文档前请自行甄别文档内容的完整性,平台不提供额外的编辑、内容补充、找答案等附加服务。
- 2、"仅部分预览"的文档,不可在线预览部分如存在完整性等问题,可反馈申请退款(可完整预览的文档不适用该条件!)。
- 3、如文档侵犯您的权益,请联系客服反馈,我们会尽快为您处理(人工客服工作时间:9:00-18:30)。
则:γL /γS <1,即γL <γS
也即:当摩尔容积相近时,当液体表面张力<固 体表面张力时,液体就可在固体表面得到铺展。
例:玻纤γS≈250×10-5N/cm UPγL≈35×10-5N/cm
即γS >γL
所以树脂基体在玻纤表面能很好铺展,当玻纤表面经硅 烷偶联剂处理后,下降到28~4010-5N/cm ,这时虽然树 脂不能自动铺展,但一般也能达到θ<90°的浸润要求。
界面示意图:
界面相内的化学组分、分子排列、 热性能、力学性能,呈现连续的梯 度性变化,界面相很薄,只有µm级, 却有极其复杂的结构。 在两相复合过程中,会出现热应力 (导热系数、膨胀系数的不同)界 面化学效应(官能团之间的作用或 反应)和界面结晶效应(成核诱发 结晶、横晶),这些效应引起的界 面微观结构和性能特征,对CM的 宏观性能产生直接影响。
由方程式:W=γL+γS+γSL —— <1> COSθ=(γS -γSL)/ γL —— <2> W:润湿时粘附力(液体在固体表面的粘合功) γL γS γSL 分别为液体、固体、固液的表面张力 θ:基体与粉粒填料、纤维间的接触角
由<2>式得出下列结论: <1>若γS <γSL则COSθ< 0,θ>90°,此时液体不能润湿固体,特别 当θ=180°时,表示完全不润湿,液滴此时呈球状; <2>若γL >γS -γSL>0,则1>COSθ>0,0°<θ<90°,此时液体能润湿固 体; <3>若γL=γS—γSL,则COSθ=1,θ=0°,此时液体能完全润湿固 体。
第四章 界面及增强材料的表面处理
4.1 概述:
1、影响复合材料力学性能主要的三因素: <1>增强体的强度及模量;
<2>树脂基体的强度及化学稳定性;
<3>应力在界面间传递时树脂与基体间的粘接效能。
2、CM性能除与基体增强剂密切有关外,界面也起至关重要 作用,CM性能并不能其组分材料的简单加和,而是产生了 1+1>2的协同效应。
例:纤维材料纵向是不能承压的,而复合后的压缩强度 得到充分发挥。 例:玻纤的断裂能约为10 J/m2 聚酯的断裂能约为100 J/m2
复合后的玻璃钢断裂能达105 J/m2
3.CM为什么会产生协同效应?
未复合前,基体与纤维各自 分散,未结合在一起 复合后,基体与纤维粘接 在一起,产生了界面
比较纤维增强塑料 复合前后的结构
∴界面是复合材料产生协同效应的根本原因。
4.为什么CM断裂能比其组成材料树脂和纤维大很多倍?
首先是在应力作用下产生裂纹,裂纹的 尖端是应力集中点,促使裂纹在基体中 发展,遇到纤维:
<1>因为纤维强度高,阻止裂纹前进,裂纹被迫沿界面发展,
使界面脱粘;
<2>裂纹在发展中若遇到纤维的薄弱部分,也可导致纤维断裂,
毫无疑问,浸润性好有利于两相界面接触,但浸润性不是界面 粘接的唯一条件。例如:EP对新鲜E玻纤表面浸润性好,但粘 接性却不好,界面耐水老化性也差,但若用胺丙基硅烷处理E 玻纤,对环氧浸润性下降,但界面粘接性提高。 所以浸润性理论虽对CM界面有一定指导意义,但对许多界面 现象单凭浸润理论是难以解释的,所以人们提出了其它理论。
三、复合材料界面的作用力:
一般是两种或以上综合力综合起作用。
机械合力:犹如钉、钩、铆、锲等的机械连接力;
包括
物理结合力:指范德华力和氢键力 单界面结合力:增强体与基体 通过化学键直接结合。 复界面结合力:通过偶联剂分别与 CM的增强体及基体相结合。
化学结合力
4.3复合材料界面作用机理:
一、界面浸润理论(浸润性理论) 理论认为:两相间地结合模式属于机械粘接与物理吸附。 机械粘附样式是一种机械铰合现象,即与树脂固化 后,大分子物进入粉粒、纤维的空隙和不平的凹陷 之中形成机械铰链 物理吸附,主要是范德华力的作用,使两相间进行 粘附
<1>寻求新型CM的基体和基材 所以 <2>探讨界面粘接机理 <3>设法提高界面粘接强度 日益为人们所重视
4.2树脂基复合材料界面结构与组成
一、树脂基复合材料对界面的要求:
应具有足够的润湿性和界面粘接强度、一定的界面厚度和减 弱固化过程中界面层的应力集中,所以界面的好坏是直接影 响复合材料性能的关键因素之一。 二、复合材料界面区的结构、组成: 这是一个多层结构的过渡区域,并非一单纯几何面,界 面区是从与粉粒填料性质不同的某点开始至与树脂基体 整体性质相一致的点间的区域。
γ值的量度:每单位长度力或每单位面积的能,通常用测定临界表 面张力的方法来研究CM中填料的γ。固液间界面张力估算的公式: γSL=γS +γL-2Ф(γS×γL)1/2式中Ф是固体和液体摩尔体积有关的量。 适用于:两相异种分子间引力介于两相各自同种分子引力之间。 由γS=γSL +γL COSθ代入上式: 得:γL(1+ COSθ)=2Ф(γS×γL)1/2 整理得:γS=γL(1+COSθ)2/4Ф2或COSθ=2Ф(γS /γSL)1/2-1 当摩尔体积相近时Ф≈1 又由前面讨论中液体在固体表面铺展得条件:γS-γSL >γL 所以γS -[γS +γL -2Ф(γS×γL)1/2]> γL 即2Ф(γS×γL)1/2>2γL γL /γS <Ф2 在大多数情况下,固、液的摩尔体积相差不同,此时Ф≈1
断裂的纤维可能裂等过程,吸收了大 量能量,并且裂纹发展未必在一个平面上,可沿着材料中 不同的平面发生如上的界面脱粘,纤维拔出,基体和纤维 断裂等过程,直到裂纹贯穿了某一平面,材料才破坏。 ∴使得CM断裂能>>各组分材料的断裂能的加和,充分体 现出CM的协同效应。 5.界面的粘接强度不仅对其力学性能有影响,且对其耐水 性、耐热性,耐腐蚀性也有很大影响。
两种作用 同时存在
粉粒填料、纤维被基体良好的润湿至关重要。
若润湿不良,在界面上会产生空隙,易使应力集中而导致复合材料 开裂; 则由物理吸附所产生的粘附力能>树脂的内聚能 若要完全润湿 另外一个液体或熔体的表面张力<固体的表面张 力,则能很好地润湿该固体表面 液体对固体浸润情况,可以用浸润角(或称接触角) θ表示,液体在固体表面浸润角的大小与固体和液体 各自的表面张力和固-液间界面张力有关。