外墙预制构件施工方案
混凝土预制构件的施工工艺及质量控制策略

混凝土预制构件的施工工艺及质量控制策略摘要:所谓预制混凝土构件,顾名思义,是指在施工现场组装之前已经生产出来的预制混凝土构件。
一般有预制混凝土楼板、公路桥梁预制混凝土箱梁、路石、污水排水沟、边界桩、街道警戒桩、树根石横截面桩、高标桩、车间预制混凝土钢屋梁、隧道框架剪力墙、基础基础预制混凝土桩等。
在工程基本建设中,主体工程的质量至关重要。
而在其他工程项目的建设中,中小型预制件的生产往往被视为补充工程,得不到足够的重视,质量无法保证。
因此,有必要对工程内外中小型预制混凝土构件的施工质量进行控制,使预制构件成为主体工程的亮点。
结合工程实例,对预制混凝土中小构件的施工工艺进行了探讨,并提出了相应的质量控制方法。
关键词:混凝土;预制构件;施工工艺;质量控制前言:在建筑施工中,预制混凝土构件已经广泛应用于每个作业阶段,具备着十分重要的实际意义。
现阶段,在我国建筑业已经步入转型升级期,逐渐呈现出向工业发展的方向发展趋势,建筑业的工业化慢慢进入现阶段建筑业的流行阶段。
预制混凝土构件作为建筑的主要构件,其质量的好坏直接影响到整个建筑的安全。
因此,对混凝土预制构件的施工工艺和质量控制方法进行详细的探讨具有重要的现实意义。
1混凝土预制构件的施工工艺1.1外墙施工工艺在混凝土预制外墙涂料施工的全过程中,施工人员必备的工程材料和专用工具具体有墙板、水准仪、密封条、防水砂浆等。
在实际作业时,最先要依靠水准仪开展相对应的施工放线工作,明确标高部位,随后依据标高部位开展墙板粘贴工作,保证墙板粘贴的稳定度和垂直角度达到作业规定[1];次之,用密封条开展夯实解决。
墙板组装后,墙板接口处很有可能会产生缝隙。
在这样的情况下,为了更好地有效地防止渗水,必须再次应用密封条开展严苛的密封解决。
房间内墙壁相对应部位运用防水砂浆密封,对于户外墙面,则采用硅酮密封胶进行密封。
1.2节点防水施工工艺在混凝土预制预制构件施工过程中,接缝处的防水工程施工也是一个重要的作业阶段。
装配式混凝土结构施工—预制混凝土竖向受力构件的现场施工
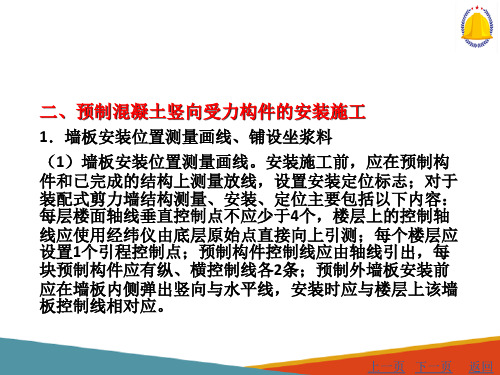
上一页 下一页 返回
图4-2-9 坐浆示意及现场图
返回
1)坐浆料坍落度不宜过高,一般在市场购买40~60 MPa 的灌浆料使用小型搅拌机(容积可容纳一包料即可)加适 当的水搅拌而成,不宜调制过稀,必须保证坐浆完成后成 中间高、两端低的形状。 2)在坐浆料采购前需要与厂家约定浆料内粗集料的最大 粒径为4~5 mm,且坐浆料必须具有微膨胀性。 3)坐浆料的强度等级应比相应的预制墙板混凝土的强度 提高一个等级。 4 )为防止坐浆料填充到外叶板之间,在苯板处补充50 mm×20 mm的苯板堵塞缝隙,如图4-2-10所示。 (4)剪力墙底部接回
搅拌时间从开始投料到搅拌结束应不少于3 min,应按产 品使用要求计量灌浆料和水的用量并搅拌均匀,搅拌时叶 片不得提至浆料液面之上,以免带入空气;拌置时需要按 照灌浆料使用说明的要求进行,严格控制水料比、拌置时 间,搅拌完成后应静置 3~5 min,待气泡排除后方可进行 施工。灌浆料拌合物应在制备后0.5 h内用完,灌浆料拌合 物的流动度应满足现行国家相关标准和设计要求。 4)灌浆及封堵(图4-2-15)。在预制墙板校正后、预制墙 板两侧现浇部分合模前进行灌浆操作。
上一页 下一页 返回
图4-2-11 预制墙板吊装示意图
返回
垂直坐落在准确的位置后拉线复核水平是否有偏差,无误 差后,利用预制墙板上的预埋螺栓和地面后置膨胀螺栓安 装斜支撑杆,复测墙顶标高后,方可松开吊钩,利用斜撑 杆调节好墙体的垂直度(注:在调节斜撑杆时必须两名工 人同时、同方向,分别调节两根斜撑杆);调节好墙体垂 直度后,刮平底部坐浆。
二、预制混凝土竖向受力构件的安装施工
PC预制构件生产施工方案
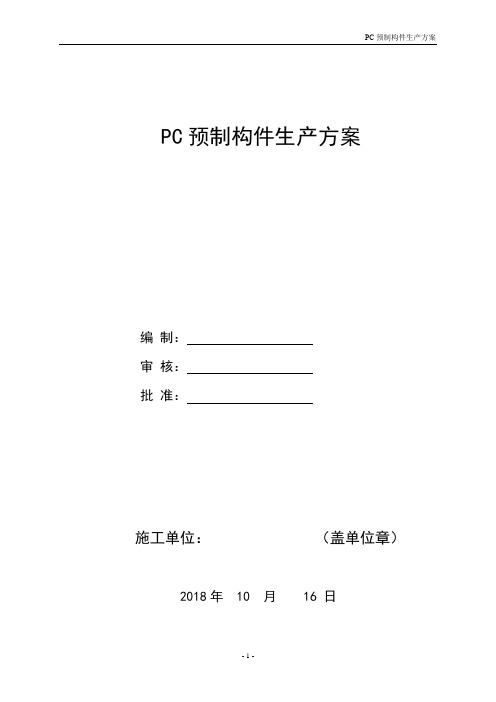
PC预制构件生产方案编制:审核:批准:施工单位:(盖单位章)2018年 10 月 16 日目录1.生产与运输............................................................................................................... - 7 -1.1图纸深化、生产与运输筹划.. (7)1.2编制依据 (7)2.生产总体布置 (7)2.1工程概况 (7)2.2生产总平面图布置(含平面布置)和选用的主要生产机械及其它设备的合理性、可靠性 .................................................................................. -7- 2.3构件制作工艺流程 .. (8)2.4选用的主要设备清单 (8)2.4.1生产设备 ...................................................................................... 错误!未定义书签。
2.4.2测量设备 (10)2.4.4试验室设备(B类) (11)3.构件制作的总体方案和施工工艺及保证措施......................................................... - 12 -3.1施工组织措施 (12)3.1.1安全控制组织 (12)3.1.2质量控制组织 (14)3.1.3生产管理组织 (14)3.2保证产品质量的主要技术措施 (14)3.2.1采用新工艺,投入新设备 (15)3.2.2全面实现三级检查,加强产品生产过程控制 (15)3.2.3质量控制点 (16)3.2.4质量管理及保证体系 (19)3.3环境保护的主要技术措施 (21)4.产品质量管理及控制措施....................................................................................... - 21 -4.1质量目标及保证措施 (21)4.1.1质量承诺书 (21)4.2质量检验标准 (22)5.构件原材料、制作、标识、堆放发货等保证措施 (21)5.1原材料及配件保证措施 (28)5.1.1水泥 (28)5.1.2骨料 (28)5.1.3水 (29)5.1.4外加剂 (29)5.1.5钢筋和点焊钢筋网 (29)5.1.6钢材 (29)5.1.7连接用金属件 (29)5.2制作、标识、堆放发货等保证措施 (30)5.2.1模具 (30)5.2.2钢筋 (31)5.2.3混凝土 (32)5.2.4构件成型 (33)5.2.5构件养护 (33)5.2.6构件脱模 (34)5.2.7构件编号 (34)5.2.8运输与堆放 (34)6、运输方案.............................................................................................................. - 35 -7、安全管理、文明生产、综合治理、环境保护的主要措施 ................................... - 36 -7.1安全管理.. (36)7.2文明生产 (37)7.3综合治理 (38)7.4环境保护 (38)8、项目组织管理机构 ............................................................................................... - 38 -8.1项目经理及主要管理人员简介 (38)8.2项目经理简历表 (38)8.3人员相应资质的复印件 (39)9.工期保证措施 ......................................................................................................... - 39 -9.1进度计划.. (39)9.2工期保证体系 (39)9.2.1组织管理体系 (39)9.2.2快速反应措施 (39)1.生产与运输1.1本项目PC构件的图纸深化、生产、运输筹划、图纸深化筹划本预制装配式设计满足上海市有关预制装配式建筑的政策要求。
预制构件安装方案
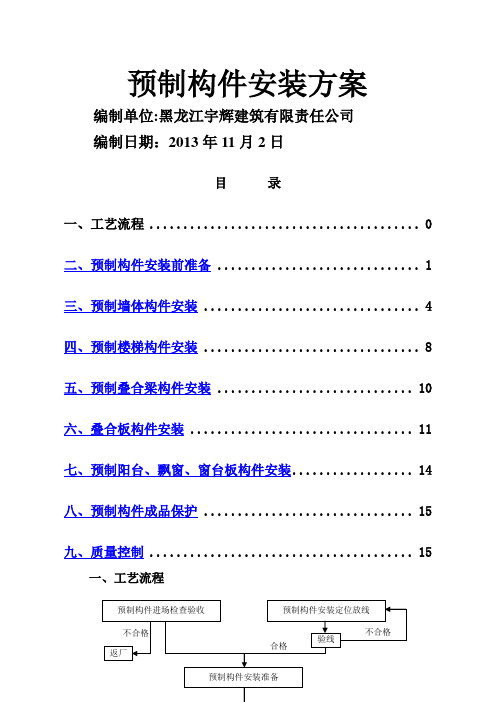
预制构件安装方案编制单位:黑龙江宇辉建筑有限责任公司编制日期:2013年11月2日目录一、工艺流程 0二、预制构件安装前准备 (1)三、预制墙体构件安装 (4)四、预制楼梯构件安装 (8)五、预制叠合梁构件安装 (10)六、叠合板构件安装 (11)七、预制阳台、飘窗、窗台板构件安装 (14)八、预制构件成品保护 (15)九、质量控制 (15)一、工艺流程二、预制构件安装前准备1.预制构件安装前现场准备1)根据施工现场平面情况,确定吊装方案。
规划场内运输道路,并确定现场构件临时堆场的位置。
2)根据预制构件吊装及施工要求,确定现场外脚手架采用形式。
如采用外挑架,给定预留槽钢位置和洞口位置,墙体现浇位置.3)楼板中预留放线洞口位置,在当前楼层四个基准外角点相对应的正上方预留一个20cm×20cm方洞,以便于上层轴线定位放线时,经纬仪对下层基准点的引用。
根据规划给定的基准线及基准点,对引入楼层的控制线、控制点的轴线及标高进行复合检查.4)在预制构件上标出轴线位置,以便于安装方向的控制.5)确定首层预制剪力墙插筋位置。
底层内、外墙构件安装前先与构件加工厂确认墙体预留插筋位置,根据工厂预制墙体上部模具固定插筋位置,用与剪力墙设计相同的主筋规格焊接做成梯子筋,现场施工时控制梯子筋第一排主筋位置,焊接固定后对插筋的品种、规格,位置、间距及外露长度进行验收,合格后方可进行构件安装。
梯子筋大样6)预制构件与混凝土基础结合面在构件安装前进行凿毛、剔除表面浮浆并洒水湿润等工作,即按混凝土施工缝进行处理。
2.预制构件进场验收1)预制构件进场首先检查构件合格证并附构件出厂混凝土同条件抗压强度报告。
2)预制构件进场检查构件标识是否准确、齐全。
(1)型号标识:类别、连接方式、混凝土强度等级、尺寸。
(2)安装标识:构件位置、连接位置。
3)预制构件质量验收(1)预制混凝土构件观感质量检验是否满足要求(2)预制混凝土构件尺寸及其误差是否满足要求(3)预制混凝土构件间结合构造是否满足要求(4)预留连接孔洞的深度及垂直度是否满足要求(5)灌浆孔与排气孔是否畅通,并作一一对应标识。
预制施工方案(3篇)
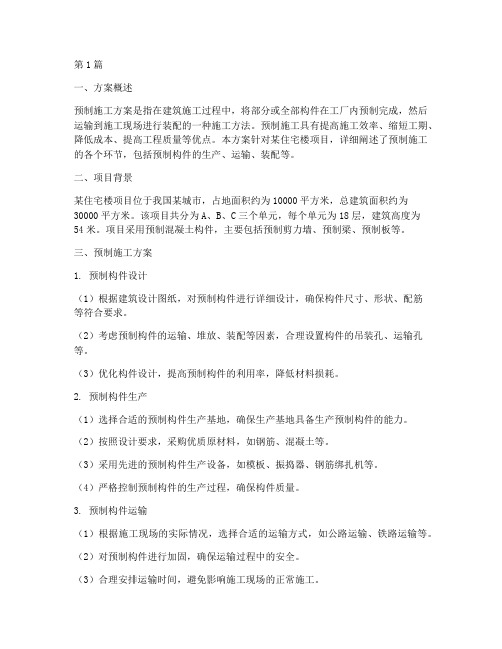
第1篇一、方案概述预制施工方案是指在建筑施工过程中,将部分或全部构件在工厂内预制完成,然后运输到施工现场进行装配的一种施工方法。
预制施工具有提高施工效率、缩短工期、降低成本、提高工程质量等优点。
本方案针对某住宅楼项目,详细阐述了预制施工的各个环节,包括预制构件的生产、运输、装配等。
二、项目背景某住宅楼项目位于我国某城市,占地面积约为10000平方米,总建筑面积约为30000平方米。
该项目共分为A、B、C三个单元,每个单元为18层,建筑高度为54米。
项目采用预制混凝土构件,主要包括预制剪力墙、预制梁、预制板等。
三、预制施工方案1. 预制构件设计(1)根据建筑设计图纸,对预制构件进行详细设计,确保构件尺寸、形状、配筋等符合要求。
(2)考虑预制构件的运输、堆放、装配等因素,合理设置构件的吊装孔、运输孔等。
(3)优化构件设计,提高预制构件的利用率,降低材料损耗。
2. 预制构件生产(1)选择合适的预制构件生产基地,确保生产基地具备生产预制构件的能力。
(2)按照设计要求,采购优质原材料,如钢筋、混凝土等。
(3)采用先进的预制构件生产设备,如模板、振捣器、钢筋绑扎机等。
(4)严格控制预制构件的生产过程,确保构件质量。
3. 预制构件运输(1)根据施工现场的实际情况,选择合适的运输方式,如公路运输、铁路运输等。
(2)对预制构件进行加固,确保运输过程中的安全。
(3)合理安排运输时间,避免影响施工现场的正常施工。
4. 预制构件装配(1)在施工现场设置预制构件堆场,确保构件的堆放整齐、安全。
(2)按照设计要求,进行预制构件的装配,确保装配精度。
(3)采用先进的装配技术,提高装配效率。
5. 施工现场管理(1)加强施工现场的安全管理,确保施工人员的人身安全。
(2)严格控制施工现场的环保措施,减少对周边环境的影响。
(3)加强施工现场的文明施工管理,提高施工现场的整体形象。
四、预制施工方案实施步骤1. 项目前期准备(1)组织相关人员对预制施工方案进行讨论,确保方案的科学性、可行性。
预制安装法施工方案
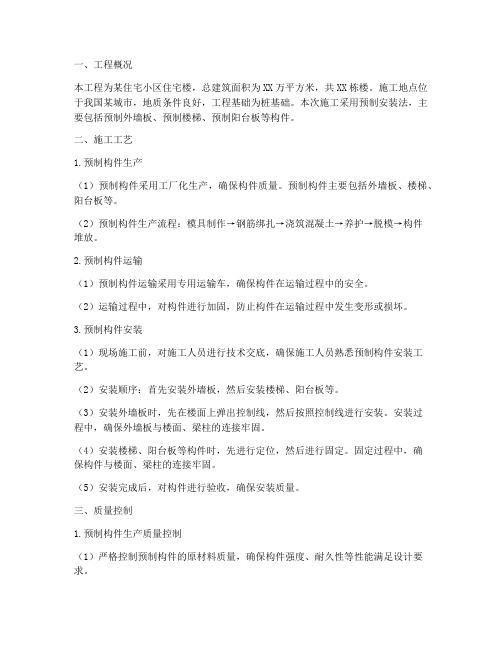
一、工程概况本工程为某住宅小区住宅楼,总建筑面积为XX万平方米,共XX栋楼。
施工地点位于我国某城市,地质条件良好,工程基础为桩基础。
本次施工采用预制安装法,主要包括预制外墙板、预制楼梯、预制阳台板等构件。
二、施工工艺1.预制构件生产(1)预制构件采用工厂化生产,确保构件质量。
预制构件主要包括外墙板、楼梯、阳台板等。
(2)预制构件生产流程:模具制作→钢筋绑扎→浇筑混凝土→养护→脱模→构件堆放。
2.预制构件运输(1)预制构件运输采用专用运输车,确保构件在运输过程中的安全。
(2)运输过程中,对构件进行加固,防止构件在运输过程中发生变形或损坏。
3.预制构件安装(1)现场施工前,对施工人员进行技术交底,确保施工人员熟悉预制构件安装工艺。
(2)安装顺序:首先安装外墙板,然后安装楼梯、阳台板等。
(3)安装外墙板时,先在楼面上弹出控制线,然后按照控制线进行安装。
安装过程中,确保外墙板与楼面、梁柱的连接牢固。
(4)安装楼梯、阳台板等构件时,先进行定位,然后进行固定。
固定过程中,确保构件与楼面、梁柱的连接牢固。
(5)安装完成后,对构件进行验收,确保安装质量。
三、质量控制1.预制构件生产质量控制(1)严格控制预制构件的原材料质量,确保构件强度、耐久性等性能满足设计要求。
(2)严格控制预制构件生产过程中的各个环节,确保构件尺寸、形状、表面质量等符合设计要求。
2.预制构件运输质量控制(1)确保运输过程中的安全,防止构件在运输过程中发生变形或损坏。
(2)对运输过程中的构件进行检查,发现问题及时处理。
3.预制构件安装质量控制(1)严格控制安装过程中的施工质量,确保构件与楼面、梁柱的连接牢固。
(2)对安装完成的构件进行验收,确保安装质量。
四、安全措施1.施工现场设置安全警示标志,确保施工人员安全。
2.施工现场设置安全通道,确保施工人员通行畅通。
3.施工过程中,严格遵守操作规程,防止安全事故发生。
4.对施工人员进行安全教育培训,提高施工人员的安全意识。
预制构件施工方案

君御世家房地产开发项目预制构件安装施工方案编制单位:山东平安建设集团有限公司编制时间:目录一、工程概况本工程为装配整体式剪力墙结构,外剪力墙、框架梁、卫生间楼板、公共部位楼板采用现浇形式,预制部分包括预制叠合楼板、预制楼梯段、预制成品轻质内墙。
预制叠合板通过现浇梁连接成整体,使整个体系形成统一的受力体系。
二、总体施工工艺流程1、施工方法预制构件及配套材料进场验收方法构件进场后,由专人负责进行检查,根据预制构件质量验收标准,进行逐块到场验收,检查内容包括构件类型、编号、数量、构件资料以及构件外观、尺寸、裂缝等,对发现的问题进行记录。
(1)进入现场的预制构件应具有出厂合格证及相关质量证明文件,产品质量应符合设计及相关技术标准要求。
(2)预制构件应在明显部位标明生产单位、项目名称、构件型号、生产日期、安装方向及质量合格标志。
(3)预制构件吊装预留吊环、预留焊接埋件应安装牢固、无松动。
(4)预制构件的外观质量不应有严重缺陷,对已经出现的严重缺陷,应按技术处理方案进行处理,并重新检查验收。
(5)除上述检查内容外,对构件进场时叠放不易检查的叠合板起吊后板底裂缝进行专项检查,板吊起后在空中悬停,检查板底裂缝,确认后方可上楼。
具体检查要求如下:①进入现场的预制构件及安装用材料、配件等按国家现行相关标准的规定进行进场验收,未经检验或不合格的产品不得使用。
②构件及配件进场检查内容:检查型号、质量证明资料检查数量:全数检查。
检验方法:检查出厂合格证及相关质量证明文件。
③外观检查:外观质量不应有严重缺陷,且不应有影响结构性能和安装、使用功能的尺寸偏差。
检查数量:全数检查检查方法:观察、尺量检查2、现场存放工程施工前,根据工程项目总体进度计划编制构件总体需求计划,根据各层各段进度要求确定每批进场数量。
施工过程中提前2天向构件厂发送构件需求计划表,标明构件名称、类型、数量、使用部位和到场时间,考虑到运输条件限制,现场应至少存放一个施工段的构件量。
安装方案

预制构件安装方案一、现场规划布置1、吊车选型应考虑最重墙板的重量,预制墙板临时堆放场地需在吊车作业范围内,且应在吊车一侧避免在吊车工盲区作业。
2、临时存放区域应与其他工种作业区之间设置隔离带或做成封闭式存放区域,尽量避免吊装过程中在其他工种工作区内经过,影响其他工种正常工作。
3、应该设置警示牌及标识牌,与其他工种要有安全作业距离。
二、构件现场存放1、现场存放1)卸车前需检查墙板专用横梁吊具是否存在缺陷,是否有开裂,腐蚀严重等问题,且需检查墙板预埋吊环是否存在起吊问题2)现场卸车时应认真检查吊具与墙板预埋吊环是否扣牢,确认无误后方可缓慢起吊,且需检查吊具是否存在裂缝、腐蚀等严重影响起吊的问题。
3)起吊过程中保证墙板垂直起吊,可采用吊运钢梁均衡起吊,防止构件起吊时单点起吊引起构件变形,并满足吊环设计时角度要求。
如果采用角度起吊,对吊环、吊具额定吊载需乘以角度系数1.4,且如发现墙板严重偏斜及重心偏位要及时处理,避免因受力不均导致安全事故。
4)堆放时应按吊装顺序、规格、品种、所用幢号房等分区配套堆放,不同构件堆放之间宜设宽度为0.8~1.2m的通道,并有良好的排水措施;5)临时存放区域应与其他工种作业区之间设置隔离带或做成封闭式存放区域,避免墙板吊装转运过程中影响其他工种正常工作防止发生安全事故。
6)平放码垛时,每垛不超过六块且不超过1.5M,底部垫2根100X100mm通长木方且支垫位置在墙板平吊埋件位置下方,做到上下对齐。
(外墙板禁止平放);7)外墙板与内墙板可采用竖立插放或靠放,插放时通过专门设计的插放架,应有足够的刚度,并需支垫稳固,防止倾倒或下沉;8)墙板宜升高离地存放,确保根部面饰、高低口构造、软质缝条和墙体转角等保持质量不受损;对连接止水条、高低口、墙体转角等易损部位应加强保护。
三、预制墙板吊装前准备预制墙板吊装顺序的确定,需遵循便于施工,利于安装的原则,可采用从一侧到另一侧的吊装顺序。
装配式建筑施工——预制构件安装施工方案
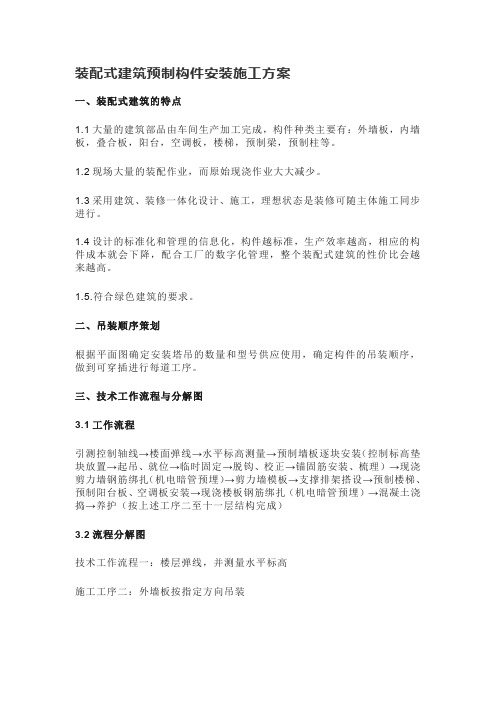
装配式建筑预制构件安装施工方案一、装配式建筑的特点1.1大量的建筑部品由车间生产加工完成,构件种类主要有:外墙板,内墙板,叠合板,阳台,空调板,楼梯,预制梁,预制柱等。
1.2现场大量的装配作业,而原始现浇作业大大减少。
1.3采用建筑、装修一体化设计、施工,理想状态是装修可随主体施工同步进行。
1.4设计的标准化和管理的信息化,构件越标准,生产效率越高,相应的构件成本就会下降,配合工厂的数字化管理,整个装配式建筑的性价比会越来越高。
1.5.符合绿色建筑的要求。
二、吊装顺序策划根据平面图确定安装塔吊的数量和型号供应使用,确定构件的吊装顺序,做到可穿插进行每道工序。
三、技术工作流程与分解图3.1工作流程引测控制轴线→楼面弹线→水平标高测量→预制墙板逐块安装(控制标高垫块放置→起吊、就位→临时固定→脱钩、校正→锚固筋安装、梳理)→现浇剪力墙钢筋绑扎(机电暗管预埋)→剪力墙模板→支撑排架搭设→预制楼梯、预制阳台板、空调板安装→现浇楼板钢筋绑扎(机电暗管预埋)→混凝土浇捣→养护(按上述工序二至十一层结构完成)3.2流程分解图技术工作流程一:楼层弹线,并测量水平标高施工工序二:外墙板按指定方向吊装施工工序三:外墙板吊装、校正完毕施工工序四:绑扎剪力墙、柱钢筋施工工序五:剪力墙后浇段、粱支模,搭设楼板和预制梁排架施工工序六:吊装预制梁、叠合板构件施工工序七:楼层内其他后续施工(梁、板钢筋)施工工序八:楼层砼浇捣并养护施工工序九:重复以上工序,进行上一楼层施工四、预制内外墙吊装施工4.1起吊本工程设计,采用塔吊吊装,为防止单点起吊引起构件变形,采用钢扁担起吊就位。
构件的起吊点应合理设置,保证构件能水平起吊,避免磕碰构件边角。
构件起吊平稳后再匀速移动吊臂,靠近建筑物后由人工对中就装配式建筑位。
墙板吊装示意图4.2预埋吊点预制混凝土外墙构件吊点、支撑件预埋。
4.3墙装配构件施工工况工况一:装配式构件进场、编号、按吊装流程清点数量。
预制构件吊装工程施工设计方案
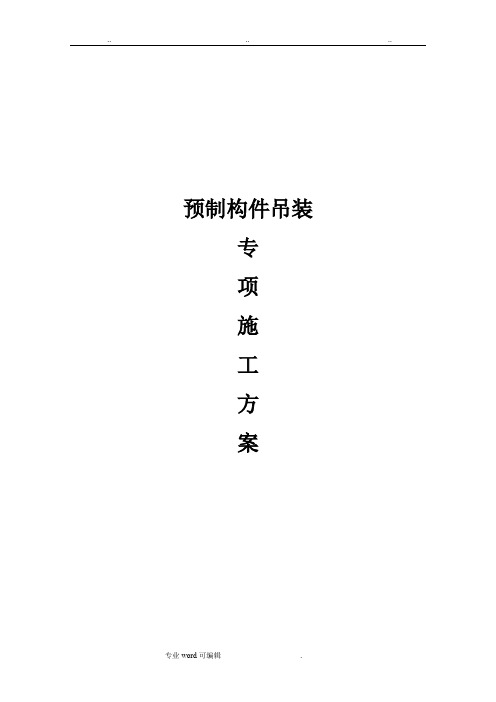
预制构件吊装专项施工方案一、编制依据二、工程概况三、总体施工流程:四、施工准备4.1技术准备熟悉、审查施工图纸和有关的设计资料,检查图纸是否齐全,图纸本身有无错误和矛盾,设计内容与施工条件能否一致,各工种之间搭接配合有否问题等。
同时熟悉有关设计数据,结构特点及土层、地质、水文、工期要求等资料。
根据图纸及公司吊装手册,按照:外墙板→内隔墙板→叠合楼板的原则,合理的编排吊装顺序图表(具体顺序图表待深化设计后施工前制作完成)。
编排叠合楼板吊装顺序时,应考虑先吊楼梯梯段和楼梯平台,方便施工人员上下楼层,然后从梯段向四周吊装,应先吊中间位置楼板,再吊临边楼板,避免安全隐患,从中间开始时应从有柱、梁、剪力墙边开始,方便楼板定位。
4.2物质准备1 预制构件准备现场施工进度计划、工厂构件生产计划、构件运输计划三者应协调一致。
在开工前应将PC构件需求计划及运输相关事宜协商好如:装车顺序、车载数量,吊装进度计划、装车所需时间、从构件厂到施工现场所需时间、需求计划、到货周期等;每个施工区域最低保证有1辆装满PC构件平板拖车箱停放在施工现场,PC构件供应满足吊装施工要求,直接从车上起吊,避免材料的二次吊装。
预制PC构件计划必须提前一个月向工厂提供,并同时提供装车顺序表,装车顺序表应与吊装顺序对应,避免吊装作业时构件二次吊装。
2 吊装设备准备本工程塔吊全部覆盖施工区域,塔吊满足工程吊装需要(详见现场平面布置图及本工程塔吊吊装方案)。
3 加工工具、吊装材料准备主要工具、设备、辅材有:斜支撑、钢梁、金属垫块、吊爪、吊钩、防坠器、卸扣、对讲机、电动扳手、手动扳手、靠尺、撬棍等。
应在开工前,准确计算所有机械设备工具用量,根据施工日期,提前定制,以免耽误施工。
4.3劳动力准备安全生产管理人员吊装过程中,因处在施工交叉作业中,故应加强安全监控力度,现场设定安全监控员。
吊装作业人员:每个吊装队人员配备:起重、吊装工3人,塔吊司机1人,塔吊信号工2人,吊装队长1人。
GRC预制构件安装专项施工方案

成功是失败之母,全部都是努力的结果河南科技大学开元校区三期建设项目医学组团外墙 GRC构件施工方案审批:审查:编制:河南城建建设企业有限责任企业2016年 4月 10日目录一、工程概略 (2)二、施工工艺及流程 (2)三、注意事项 (3)四、质量保证举措 (4)五、安全文明 (4)一、工程概略1、项目名称:河南科技大学开元校区三期建设项目医学组团2-6# 楼2、建设单位:河南科技大学洛阳天健房地产开发有限企业3、设计单位:河南从头规划设计研究总院有限企业4、施工单位:河南城建建设企业有限责任企业5、工程地点 :河南科技大学开元校区内二、施工工艺及工作的流程1、施工准备:依据建筑装修的设计图纸,对原有建筑物进行丈量,联合图纸部署的地点和对GRC构件形状的要求,进行GRC构件的设计,使GRC构件与网片尺寸,地点相切合,并知足装修设计中的外观要求。
GRC 构件进场第一进行查收,查收合格后按品种规格进行分类,码放齐整,做好防备,以防损坏。
2、工艺流程施工准备→进场构件查验→各种铁件、支架制作→找准外墙土建基准线→按 GRC构件规格定位放线→ GRC构件就位安装→堵缝、修理→保养→分项查收。
3、施工方法:4、在混凝土墙、梁上用φ80×100的膨胀螺栓间距不大于500mm将骨架固定,而后在骨架上用自钻丝固定GRC构件。
骨架由主次龙骨构成,主、次龙骨均为热镀锌角钢,规格型号为L30×3,主龙骨固定在阴、阳角等主要受力处,次龙骨间距不大于500mm焊接坚固在主龙骨间,形成一个完好的钢架网。
4、GRC接缝的施工:在 GRC构件之间的空隙处固定玻璃纤维布,用水泥砂浆抹面。
在GRC与墙体的空隙处也用相同方法办理。
三、注意事项1、构件安装前应付建筑物连结构造表面进行办理,保证其平坦、坚实。
2、构件表面出缺棱掉角等缺点时,安装后应采纳水泥拌合资料进行修理。
3、安装前应依据施工图纸在外墙上弹好标高线、水平、垂直和构件中心控制线以控制GRC构件安装在同一水平线上。
预制构件吊装施工方案
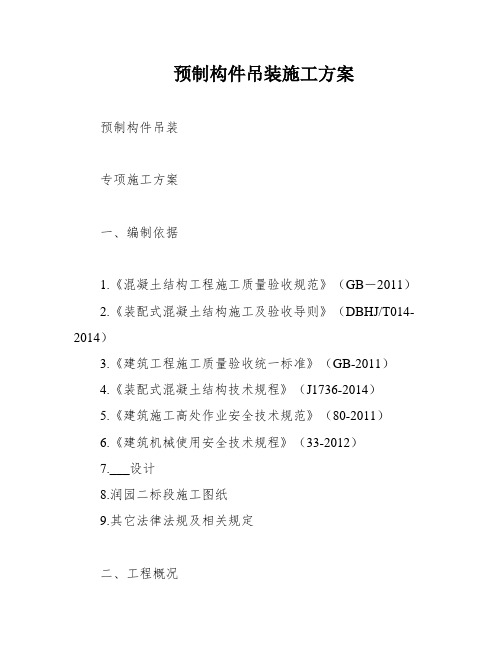
预制构件吊装施工方案预制构件吊装专项施工方案一、编制依据1.《混凝土结构工程施工质量验收规范》(GB-2011)2.《装配式混凝土结构施工及验收导则》(DBHJ/T014-2014)3.《建筑工程施工质量验收统一标准》(GB-2011)4.《装配式混凝土结构技术规程》(J1736-2014)5.《建筑施工高处作业安全技术规范》(80-2011)6.《建筑机械使用安全技术规程》(33-2012)7.___设计8.润园二标段施工图纸9.其它法律法规及相关规定二、工程概况本工程预制构件吊装包括外墙板、内隔墙板、叠合楼板等。
总体施工流程包括现浇部位模板、钢筋安装、拼缝处理、封仓、灌浆、装配式套筒墙板安装、测量放线、支撑搭设预制楼板、阳台、楼梯安装、水管线敷设、检查验收现浇部位楼板安装、预制楼板底部拼缝处理、楼板钢筋安装、混凝土浇筑养护、二层测量放线等。
三、施工准备4.1 技术准备在施工前,要熟悉、审查施工图纸和有关的设计资料,检查图纸是否齐全,图纸本身有无错误和矛盾,设计内容与施工条件能否一致,各工种之间搭接配合有否问题等。
同时熟悉有关设计数据,结构特点及土层、地质、水文、工期要求等资料。
根据图纸及公司吊装手册,按照外墙板→内隔墙板→叠合楼板的原则,合理编排吊装顺序图表。
编排叠合楼板吊装顺序时,应考虑先吊楼梯梯段和楼梯平台,方便施工人员上下楼层,然后从梯段向四周吊装,应先吊中间位置楼板,再吊临边楼板,避免安全隐患,从中间开始时应从有柱、梁、剪力墙边开始,方便楼板定位。
4.2 物质准备1.预制构件准备现场施工进度计划、工厂构件生产计划、构件运输计划三者应协调一致。
在开工前应将PC构件需求计划及运输相关事宜协商好,如装车顺序、车载数量,吊装进度计划、装车所需时间、从构件厂到施工现场所需时间、需求计划、到货周期等。
每个施工区域最低保证有1辆装满PC构件平板拖车箱停放在施工现场,PC构件供应满足吊装施工要求,直接从车上起吊,避免材料的二次吊装。
装配式预制高性能泡沫混凝土保温外墙体系施工工法(2)

装配式预制高性能泡沫混凝土保温外墙体系施工工法装配式预制高性能泡沫混凝土保温外墙体系施工工法一、前言装配式预制高性能泡沫混凝土保温外墙体系是一种新型的保温墙体施工技术,其具有施工速度快、保温性能好、工艺简单等特点,广泛应用于现代建筑领域。
本文将详细介绍该工法的特点、适应范围、工艺原理、施工工艺、劳动组织、机具设备、质量控制、安全措施、经济技术分析等内容。
二、工法特点装配式预制高性能泡沫混凝土保温外墙体系施工工法具有以下特点:1. 高效施工:通过预制构件的使用,可以大幅缩短施工周期,提高施工效率。
2. 优异保温性能:采用高性能泡沫混凝土制作保温板材料,具有较好的保温隔热效果,可以有效降低建筑的能耗。
3. 结构轻便:由于泡沫混凝土的轻质特性,整个保温外墙体系的自重较小,可以减轻建筑物的结构荷载。
4. 环保可持续:泡沫混凝土的生产过程中不需要使用大量的天然资源,且施工过程中减少了大量的水泥使用,对环境友好。
三、适应范围装配式预制高性能泡沫混凝土保温外墙体系适用于各类低层建筑、别墅、仓库等建筑物的外墙保温工程。
特别适用于建筑密度较大、周期较短的项目,如集合住宅小区等。
四、工艺原理装配式预制高性能泡沫混凝土保温外墙体系的施工工法与实际工程之间存在紧密联系。
通过采取以下技术措施,实现了该工法的理论依据和实际应用:1. 预制保温板制作:将高性能泡沫混凝土按照设计要求制作成规定尺寸的保温板。
2. 墙体安装:根据建筑物的设计图纸,将预制保温板进行组合装配,固定在建筑结构的外墙上。
3. 防水层施工:在保温板表面涂刷防水涂料,形成一层防水层,提供墙体的防水功能。
4. 外墙装饰层施工:根据设计要求,在保温板外侧装饰装修,形成美观的外观效果。
五、施工工艺1. 提前准备工作:包括施工机具设备的准备、材料准备、场地布置等。
2. 基础处理:对于存在问题的基础进行处理,保证墙体的稳定和平整。
3. 预制保温板安装:按照设计要求,将预制保温板进行装配并固定在建筑物外墙上。
预制构件安装劳务施工方案

一、工程概况1.1 工程简介本工程为某住宅小区项目,总建筑面积约10万平方米,建筑高度约18米,结构形式为框架结构。
本工程采用预制构件安装施工方式,以提高施工质量和效率。
1.2 项目概况本工程共需安装预制构件包括:预制外墙板、预制楼板、预制楼梯、预制阳台板等。
预制构件在工厂生产完成后,运输至施工现场进行安装。
二、施工准备2.1 施工组织成立预制构件安装施工小组,明确各成员职责,确保施工顺利进行。
2.2 施工材料(1)预制构件:根据设计图纸要求,提前订购预制构件,确保构件质量符合标准。
(2)施工工具:吊装设备、电动工具、测量仪器等。
2.3 施工技术(1)预制构件的运输与存放:确保运输过程中的安全,合理堆放,避免损坏。
(2)预制构件的安装:按照设计图纸要求,进行构件的吊装、就位、校正、锚固等工序。
三、施工工艺流程3.1 预制构件运输与存放(1)运输:采用汽车运输,确保构件在运输过程中的安全。
(2)存放:按照设计要求,合理堆放预制构件,避免损坏。
3.2 预制构件安装(1)吊装:使用吊装设备将预制构件吊装至指定位置。
(2)就位:将预制构件放置在正确位置,确保垂直度和平整度。
(3)校正:对预制构件进行校正,确保其符合设计要求。
(4)锚固:将预制构件与主体结构进行锚固,确保连接牢固。
3.3 预制构件连接(1)采用专用连接件,将预制构件与主体结构连接。
(2)连接件应满足设计要求,确保连接牢固。
四、质量控制措施4.1 材料质量控制(1)严格控制预制构件的采购,确保其质量符合标准。
(2)对进场材料进行检验,不合格材料不得使用。
4.2 施工过程质量控制(1)严格按照施工工艺流程进行施工,确保施工质量。
(2)加强施工过程中的监督检查,发现问题及时整改。
4.3 成品保护(1)在施工过程中,采取有效措施保护预制构件,避免损坏。
(2)对已安装的预制构件进行防护,防止污染和损坏。
五、安全措施5.1 人员安全(1)对施工人员进行安全培训,提高安全意识。
装配式混凝土建筑预制外墙孔洞封堵施工工法(2)

装配式混凝土建筑预制外墙孔洞封堵施工工法装配式混凝土建筑预制外墙孔洞封堵施工工法一、前言装配式混凝土建筑是近年来发展迅速的一种建筑方式,其特点是在工厂预制构件,然后通过现场装配组装而成。
在装配过程中,需要对预制构件的孔洞进行封堵,以确保墙体的承载力和防火性能。
本文将详细介绍预制外墙孔洞封堵的施工工法及相关内容。
二、工法特点预制外墙孔洞封堵施工工法具有以下特点:1. 孔洞封堵灵活方便:施工过程中,可以根据预制构件的设计要求,预先在工厂中进行孔洞的预留和封堵,减少现场施工工期和工程难度。
2. 施工速度快:由于预制构件工厂化生产,现场施工只需要进行组装和封堵,大大缩短了施工周期。
3.施工质量可控:预制构件在工厂中进行生产,质量受到严格控制,封堵过程中可以进行全程监控,保证了施工的质量。
4.提高施工安全性:封堵过程中,可以采用安全防护措施,减少人员高空作业,降低施工中的安全风险。
三、适应范围预制外墙孔洞封堵施工工法适用于各类装配式混凝土建筑的外墙结构,特别适用于高层建筑和大型公共建筑,包括商业综合体、医院、学校等。
四、工艺原理预制外墙孔洞封堵施工工法的原理是将预制构件进行组装时预留的孔洞进行封堵,以达到防火和承载力的要求。
具体分析如下:1. 施工工法与实际工程之间的联系:根据实际设计和构件制作要求,在工厂预制构件时进行孔洞的预留,并制定封堵方案。
2. 采取的技术措施:根据封堵的要求,选择合适的材料进行孔洞封堵,如混凝土、砂浆、阻燃材料等。
封堵过程中,严格控制施工工艺和材料的使用,确保封堵效果和质量。
五、施工工艺预制外墙孔洞封堵施工工艺包括以下阶段:1. 准备工作:将预制构件运至现场,进行准确定位和固定。
2. 孔洞清理:清理孔洞内的杂物和灰尘,确保封堵材料能够充分填充孔洞。
3. 封堵材料的搅拌和配制:按照设计要求,将封堵材料进行搅拌和配制,确保材料性能和质量。
4. 封堵施工:使用适当的工具和设备,将封堵材料填充到孔洞中,确保封堵牢固且与周围构件连接紧密。
- 1、下载文档前请自行甄别文档内容的完整性,平台不提供额外的编辑、内容补充、找答案等附加服务。
- 2、"仅部分预览"的文档,不可在线预览部分如存在完整性等问题,可反馈申请退款(可完整预览的文档不适用该条件!)。
- 3、如文档侵犯您的权益,请联系客服反馈,我们会尽快为您处理(人工客服工作时间:9:00-18:30)。
一编制依据外墙板(PC板)应满足国家验收标准GB50204-92《砼结构工程施工及验收规范》,北京市标准DBJ01-1-92《预制混凝土构件质量检验评定标准》。
一、工程概况1.面积:( m2)。
2.层高间的外墙板原设计为现浇,因工期及现场模板配制量过大,现改为预制PC墙板。
3.墙板为清水砼外挂板,简称PC板,1—4层板厚度一般为150mm厚;5层及5层以上板厚一般为120mm 厚。
较重板因生产运输及现场塔吊吊距等原因需分成2—3块生产,现场安装拼接,每块板重一般为3吨—7吨。
4.PC板在构件厂内进行生产,生产完成后根据施工进度运至现场进行安装。
5.PC板与砼结构连接方式主要采用:5.1 首层:(1)地面梁须设埋件,PC板底部埋件与地面梁埋件焊接连接;(2)PC板顶部竖向筋甩出作拉锚筋(胡子筋)锚入现浇楼板砼内。
5.2 其它层PC板与楼面、柱面予埋铁件连接后,板顶面锚筋锚入现浇楼板内。
6.按项目要求制作试装板,发现问题由项目出面组织制作厂方人员,确定其它PC板的调整。
7.首层板约54块,30种型号(实际生产待调整),板高一般为5120mm。
8.首层板生产日期约为7天,平均日产量8块,模板现制不宜少于16套。
二、加工制作篇1.PC板生产准备1.1 施工组织管理与技术准备:1.1.1 施工生产管理体系:该批混凝土外墙挂板(以下简称PC板)产品质量要求高、工期紧、技术难度大,因此,组建PC板专项生产管理班子,建立严格的PC板生产管理体系(图示1):1.1.2 技术准备:为正确指导墙板生产,组织编制《东黎大厦外墙板生产技术方案》,提出生产进度、材料、埋件计划和生产要素配置以及调整计划、主要过程控制措施等,进行专项技术交底和技术培训,并在生产过程中严格执行。
1.2 主要材料准备1.2.1 水泥:1.2.1.1 普通水泥:采用P0525#普通硅酸盐水泥,质量应符合国标《硅酸盐水泥、普通硅酸盐》GB175的有关规定;1.2.1.2 进厂水泥须有质量检验证明,同时材料进厂后必须执行厂《检验和试验程序细则》质量管理文件,进行复试检验,合格后方可使用;1.2.2 细骨料:采用中砂。
质量应符合部颁标准《普通混凝土用砂质量标准及检验办法》JGJ52的有关规定;1.2.3 粗骨料:采用5-20mm混合级配卵石,质量应符合部颁标准《普通混凝土用碎石或卵石质量标准及检验办法》JGJ53的有关规定;1.2.4 拌合水:饮用水;1.2.5 混凝土:普通混凝土、设计强度等级为C40。
1.2.6 钢筋:Ⅱ级螺纹钢筋;Ⅰ级A3光圆钢筋;埋件锚筋采用Ⅱ级螺纹钢筋或Ⅰ级光圆钢筋。
1.2.7 起吊、安装用吊环:1.2.7.1 PC板内预埋吊环主要规格为:φ22、φ20、φ18、φ16等四种。
板顶面一般安设两个安装吊环,板背面安放4个施工吊环,便于脱模和起吊。
1.3 人员配备:PC板施工人员需进行技术交底及技术培训合格后方可上岗施工。
1.3.1 钢筋加工:(图示2)1.3.2 PC板生产:(图示3)图示2 图示31.4 主要生产要素配置(场地、机械设备)(见表1)主要生产要素配置表1项目生产要素数量生产能力备注生产场地PC板预制堆放场地1万m2混凝土搅拌站1750m2蒸汽养护池720m2钢筋加工场地5300m2模板加工场地400m2设备龙门吊4台20吨-台、5吨3台搅拌机2台350升/台强制式装载机1台5吨混凝土振动棒6台平板振动器3台附着式振动器12台水箱1座1T与搅拌机配套汽车4辆10吨以上挂车万能材料试验机2台60吨,200吨各一台.4.1 场地平面布置;图示42.生产工艺2.1 生产工艺:采用钢底模和邦模,主要采用反打工艺生产:图示52.2 工艺流程:2.3 主要技术措施和质量保证措施2.3.1 模板制作:2.3.1.1 模板采用钢模。
根据工期和分层配套量首批配制模板约20套,在生产过程中采取同型号构件连续生产完成后,再改制其它模板的原则实施生产,并根据施工进度状况来增、减模板量。
2.3.1.2 底模角板采用8mm厚钢板,主肋采用[16#,侧模采用-5钢板做面板,L50*4做肋,支模时用木方或角钢做支撑,与侧与底模采用螺栓连接固定,模具方案参见图纸。
2.3.1.3 钢底板拼装时应尽量无拼缝,对面积大的PC板,钢板必须拼接时,板面应拼接平整,表面高差控制在1mm范围内,拼缝处必须打磨平整。
模板固定埋件位置的螺丝孔要求准确,其误差不得大于3mm。
(挂板制作尺寸允许偏差参见表2)模板制作尺寸允许偏差表2检验项目允许偏差(mm)长0、-3宽(高)0、-3厚0、-2对角线差5表面平整3侧向弯曲L/1000且10扭翘L/1500拼板表面高低差1钢筋保护层0、+5定位中心线位置预埋件、锚固件2吊环10安装孔5预留孔洞5侧模垂直度H/1000且52.3.1.4 加工完成的模板在组装完成后,必须按照图纸设计要求和模板质量控制标准,经检验确认无误后,方可移交生产使用。
2.3.1.5 经过多次使用的模板,若表面出现较大面积的凹凸不平现象时,必须用2M靠尺实测检查,当凹凸面在2mm之内,且整块钢模板无扭翘变形方可继续使用。
否则必须重新铺设钢板,并经找平处理后方可投入使用。
重新铺设的模板质量必须符合表3“模板制作尺寸允许偏差”质量要求。
2.3.1.6 组装好的模板必须拼装严密,防止因浇筑混凝土时漏浆而影响整块板的板面外观质量。
在模板的拼装过程中,可采用加垫泡沫密封条或用玻璃胶嵌缝等方法进行密封,防止混凝土浇注时漏浆。
2.3.1.7 脱模剂:采用高分子脱模剂,用滚子将脱模剂涂抹模板上以均匀薄层为度,但不得有漏刷现象,否则会引起粘模,造成板面有麻面、气泡等质量缺陷。
模板表面和边角涂抹脱模剂也不得过多,否则易使构件板面和边角麻面、缺楞等严重质量缺陷,直接影响挂板的外观质量。
2.3.2 钢筋加工与铺放:2.3.2.1 钢筋网片的主筋主要采用螺纹@200分布筋φ8@200双层网片,拐板处另加Φ8八字筋@200,网片间加Φ8撑铁,每平米不少于3个。
2.3.2.2 如埋件较大或埋件锚筋较长,与网片筋相碰时应以埋件位置为准,相应调整钢筋网片的位置,并将埋件预先固定在钢筋网片内。
2.3.2.3 钢筋保护层15mm,入模时网片采用铅丝吊挂或加垫预制垫块,用以控制保护层的厚度。
2.3.3 埋件、吊件的准备及安放:2.3.3.1 埋件安装与固定:在安装埋件时,认真对照图纸控制尺寸并固定牢固。
2.3.3.2 混凝土浇注完毕后设专人及时对埋件型号、外型、尺寸及埋设位置进行复核校正,以保证埋件型号、位置的正确。
确保安装工作顺利进行。
2.3.4 混凝土浇筑、振捣:2.3.4.1 混凝土浇筑前,必须对模板尺寸、钢筋及埋件位置经质检核对无误后再浇筑混凝土。
2.3.4.2 混凝土强度等级:C40,坍落度6-8cm。
2.3.4.3 试验室须根据当天气和施工条件对配合比进行调整以满足混凝土的施工要求,搅拌站严格执行施工配合比搅拌混凝土。
2.3.4.4 混凝土浇注下料应从一个方向均匀向另一个方向伸展,或从中心位置向边缘均匀扩展,以防止板面产生气泡。
2.3.4.5 混凝土振捣时,采用附着式振动器与Φ50振动捧相结合方式振捣,并安排专人操作。
当采用振捣捧振捣砼时应做到快插慢拨,各振点必须满足在有效振幅半径范围内,振捣时间以气泡排尽且结构密实为度。
2.3.4.6 混凝土浇筑完成后,随即拍实表面,用刮板刮平后,抹平压光二遍即可。
同时注意校正因振捣造成移位、扭翘的埋件;对采取正打工艺生产的PC板,在浇筑完成后,板面用刮板刮平压实,经一定时间的静停后压光,压光时严禁随意向板面洒水或撒干灰,以防止造成板面起皮、脱层、开裂和表面色差不一致等质量缺陷。
2.3.5 养护:PC板进行蒸气养护时,池内温度一般控制50ºC以内,养护温度和时间控制示意如下:图示62.3.6 起吊出池:2.3.6.1 PC板经蒸养后,起吊条件以同条件养护试块强度达到设计强度50%以上方可拆侧模,拆除侧模板时,应注意必须先将全部螺丝拆除后,再轻拆侧模板,防止因拆模不当损坏构件边角。
PC板强度达到设计强度70%以上时方可起吊出池。
起吊时各吊点受力应均匀一致,确保平衡。
2.3.6.2 对少量截面形状特殊、面积较大不能直接起吊的PC板,采取临时增强加固措施来保证起吊、倒运质量,加强起吊时板薄弱部位的刚度,起吊强度必须满足90%设计强度以上才能起吊,2.3.7 待验构件码放:PC板出模后,先摆放在待验区进行检查验收,将合格板做好标识后,码放在成品堆放区,需返修的板吊至修补区。
2.3.8 码放平板和槽型板时,可平放码放;对于L型拐角板或“”一般采取立放;以便于检查、修补,也可采取平放,平放后对水平板下面须采用厚木方加橡胶板垫实。
2.3.9 脱模出池的PC板,必须在当天进行外观缺陷检查,对有轻微外观质量缺陷的部位必须在当天进行修复,经修复后,采取同样的养护方法养护至起吊要求。
2.3.10 PC板成品板面应平整,无油渍,外形尺寸符合质量标准。
2.3.11 PC板出厂前用毛笔沾墨汁做好型号、出产日期等标识,且在板背面和板侧边均应标识。
3. 成品检验3.1 PC板逐块进行检查验收。
3.2 修复后的PC板由专检员进行复验,确认合格后,做出质量标识。
3.3 经项目指派质量监理最终验收合格并做出合格标识后,方可转入成品码放。
4.运输4.1 PC板采用平板汽车运输,装车时板与板之间必须垫实、垫牢。
4.2 PC板运输由车间安排专人负责,对运输司机做好专项交底,确保PC板运输的安全。
4.3 超高、超宽PC板在运输前必须作好标识,按照交通部门规定的允许通行时间运输。
4.4 在运输时执行现场施工安装进度及型号计划按顺序装运,避免现场积压或二次倒运。
4.5 装车后应捆绑牢固,板与捆绳接合处采用软物或木板包角垫实,防止在运输过程中脱落、移位,损坏板面或边角。
5.质量标准质量标准表3序号项目质量标准(mm)备注1长度± 52宽度± 53对角线偏差± 104厚度± 55表面平整46预留孔中心线位移57预埋件定位线位移58外观质量执行市标DBJ01-1-92表6.2.2-2《予制砼构件质量检验评定标准》6.质量控制措施6.1 按照ISO9002质量保证体系,编制并实施质量管理程序和相关工艺标准,完善岗位质量责任制,将质量责任落实到人。
6.2 施工前,主管工长对班组作业人员进行专项技术交底、及安全和质量交底。
6.3 施工生产过程中,严格落实“三检制”和“专检制”,并实施质量否决权。
6.4 模板在组装前必须抄平检验并校正底模,严禁使用扭翘、变形的模板。
7.安全生产措施7.1 进入现场人员必须遵守安全生产制度。