冲裁工艺分析
冲裁工艺性分析

1设计任务书1.设计题目:设计《链板》冲孔落料模。
2.主要内容:2.1.设计《链板》冲孔落料模,工件图号是05,IT14,见下图所示2.2.模具类型为普通冲孔落料倒装式模,班产量80万件/年,凸模与凹模配作,手工送料。
3.具体要求:3.1.绘制该模具总装图(A4,图号为05/M09-1);3.2.绘制冲孔凸模、落料凹模或凸凹模工作图(按A4规格,竖排,零件图号分别为05/M09-1/1,05/M09-1/2,05/ M09-1/3);3.3.编制凸、凹模或凸凹模(05/ M09-1/3)的加工工艺过程卡(按A4规格,竖排)。
3.4.编写整理完善设计计算说明书;3.5.将任务书、说明书、工艺过程卡及三张图样装订成册。
4.进度安排:作业完成日期为2011年3月31 日下午6时。
5.成绩评定:指导教师2011年月日系主任2011年月日2设计任务分析本课题主要的目的是为了培养学生运用有关课程的基础理论和技能解决实际问题,进一步提高学生本专业必要的基本技能、方法和创新能力的重要环节之一。
2.1工件的冲压工艺性分析零件属于中等批量生产,尺寸公差较大,内外行简单对称,宽度尺寸为20mm,长度尺寸为80mm,冲压工艺性较好,适合少、无废料冲裁加工。
2.2分析比较和确定冲压工艺方案由零件冲压工艺分析可知,冲压基本工序为冲孔和落料。
根据工件特点和工艺要求,可以有以下冲压工艺方案:零件为冲孔落料件,可提出的加工方案如下:方案一:先落料,后冲孔。
采用两套单工序模生产。
方案二:冲孔—落料复合冲压,采用复合模生产。
方案三:落料—冲孔连续冲压,采用级进摸生产。
方案一模具结构简单,但两道工序,两道模具,生产效率较低,零件精度较差,在大批量生产中不使用。
方案二只需要一副模具,冲压件的行位精度和尺寸精度易保证,且生产效率高。
尽管模具结构较一方案复杂,但零件几何形状简单,模具制造并不困难。
方案三也只需要一副模具,生产效率也很高,但与方案二比生产的零件精度稍差,欲保证行位精度,结构比复合模复杂。
冲裁工艺与冲裁模冲裁工艺及冲裁件的工艺性

一、冲裁工艺及冲裁件的工艺性
1、概述
1)冲裁——利用装在压力机上的模具,将板料分离的冲压工 艺。 2)包括内容——冲孔、落料、修边、切口、切断等。 落料——从板料上冲下所需形状的零件或毛坯(要冲掉部分) 冲孔——从工件上冲出所需形状的孔(冲掉的部分是废料) 3)用途——可加工平板类零件;为弯曲、拉深、成形等工序 准备毛坯;在成形件上完成刨切、冲孔等。 4)模具
四、排样设计
排样:冲裁件在被冲材料上的布置方法。
在冲压生产中,零件的材料费用占制造成本 的60%以上,所以合理的排样不仅能提高冲 裁件的质量、提高模具寿命,而且时节约使 用材料降低成本的有效措施 。
冲裁工艺与冲裁模冲裁工艺及冲裁 件的工艺性
搭边:排样时零件与零件之间、零件与条料侧 边留下的工艺废料。
)配合加工法中凸、凹模刃口尺寸计算
对于形状复杂冲裁件,为保证凸、凹模 之间的合理间隙值,必须采用配 合加工方式。即首先加工凸、凹模中的一件作为基准件,然后以选定的间 隙配合加工另一件。
冲裁工艺与冲裁模冲裁工艺及冲裁 件的工艺性
冲裁工艺与冲裁模冲裁工艺及冲裁 件的工艺性
配合加工的计算公式
冲裁工艺与冲裁模冲裁工艺及冲裁 件的工艺性
冲裁工艺与冲裁模冲裁工艺及冲裁 件的工艺性
落料与冲孔:
冲裁工艺与冲裁模冲裁工艺及冲裁 件的工艺性
冲裁工艺与冲裁模冲裁工艺及冲裁 件的工艺性
模具图
冲裁工艺与冲裁模冲裁工艺及冲裁 件的工艺性
2、冲裁件的工艺性
冲裁件的工艺性: 指冲裁件在工艺上的适应性,即加工难易程度。良好的工艺性能使材
料消耗少、工序数量少、模具结构简单且使用寿命长、产品质量稳定。
冲裁时,搭边过大,会造成材料浪费,搭边太 小,则起不到搭边应有的作用,过小的搭边, 导致板料被拉进凸、凹模间隙,加剧模具的磨 损,甚至会损坏模具刃口。
第2章6-7节(冲裁工艺及冲裁模设计)
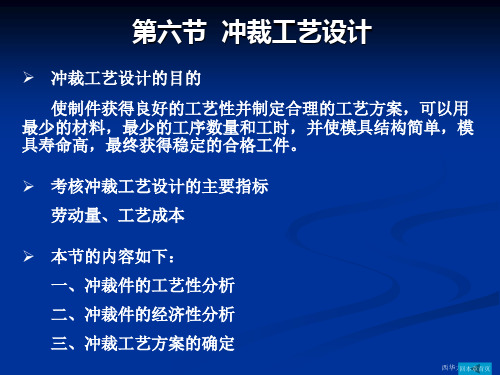
用途 薄件、平整要求高的零件、 薄件、平整要求高的零件、易分层的非金属件
西华大学 张晓洪
2、冲孔模 、
普通板坯冲孔模结构与落料模相似。 普通板坯冲孔模结构与落料模相似。 冲孔的多样性导致冲孔模有更多自己的特点。 冲孔的多样性导致冲孔模有更多自己的特点。
典型的冲孔模有: 典型的冲孔模有: (1)冲侧孔模 ) (2)单工序多凸模冲孔模 ) (3)导板式冲小孔模 )
西华大学 张晓洪
倒装复合模
冲制垫圈的复合冲裁模 适用条件 0.3mm以上低平直度要求件(刚性推件未压紧制件部分,卸 以上低平直度要求件(刚性推件未压紧制件部分, 以上低平直度要求件 料板也未压紧条料) 料板也未压紧条料) 特点 卸料板兼承料平面, 卸料板兼承料平面,冲前无法预压 凸凹模若直刃段长,则胀裂力大,须控制其最小壁厚 凸凹模若直刃段长,则胀裂力大, 条料废料部分: 条料废料部分:冲裁时有上下动作 改进 若上部改为弹性推件,则可加工 若上部改为弹性推件,则可加工0.3mm以下的冲件 以下的冲件
西华大学 张晓洪
… … …冲裁件的形状和尺寸 冲裁件的形状和尺寸
6、孔径不能太小; 、孔径不能太小; 自由凸模的最小尺寸 带护套凸模的最小尺寸 最小孔间距
西华大学 张晓洪
(二)冲裁件的尺寸精度和表面粗糙度要求
冲裁件的经济精度:一般不高于 冲裁件的经济精度:一般不高于IT11,冲孔比落料高一级 , 1、冲裁件外形与内孔尺寸公差表 、 2、冲裁件两孔孔心距公差表 、 3、冲裁件断面表面粗糙度表 、 4、冲裁件断面允许的毛刺高度表 、
第六节
冲裁工艺设计的目的
冲裁工艺设计
使制件获得良好的工艺性并制定合理的工艺方案, 使制件获得良好的工艺性并制定合理的工艺方案,可以用 最少的材料,最少的工序数量和工时,并使模具结构简单, 最少的材料,最少的工序数量和工时,并使模具结构简单,模 具寿命高,最终获得稳定的合格工件。 具寿命高,最终获得稳定的合格工件。 考核冲裁工艺设计的主要指标 劳动量、 劳动量、工艺成本 本节的内容如下: 本节的内容如下: 一、冲裁件的工艺性分析 二、冲裁件的经济性分析 三、冲裁工艺方案的确定
冲裁工艺分析

4) 毛刺 毛刺的形成是由于在塑性变形阶段后期,凸模
和凹模的刃口切入被加工材料一定深度时,刃口正面 材料被压缩,使裂纹起点不会在刃尖处发生,而是在 模具侧面距刃尖不远的侧面
上,在拉应力作用下,裂纹
加长,材料断裂而产生毛刺。
μ是摩擦系数, μF1、μF2——凸、凹模侧面与板材间 的摩擦力
板材由于受到模具表面的力偶作用而弯曲,并从模具表面上翘起, 使模具表面和板材的接触面仅局限在刃口附近的狭小区域,宽度 约为板厚的0.2~0.4。接触面间相互作用的垂直压力分布并不均匀, 随着向模具刃口的逼近而急剧增大。
冲裁中,板材的变形是在以凸模与凹模刃口连线为中 心而形成的纺锤形区域内最大,即从模具刃口向板料 中心,变形区逐步扩大。
刺按磨损后的刃口形状,成为根部很厚的大毛 刺。
3 提高断面质量的措施
通过增加光亮带的高度或采用整修工序 来实现。
增加光亮带高度的关键是延长塑性变形阶段,推迟裂 纹的产生,要求材料的塑性好,对硬质材料要尽量进 行退火;
要选择合理的模具间隙值,并使间隙均匀分布,保持 模具刃口锋利。
当间隙过大时
材料的弯曲和拉伸增大,接近于胀形破裂状态,容易 产生裂纹,使光亮带所占比例减小。
材料在凸、凹模刃口处产生的裂纹会错开一段距离而 产生二次拉裂,断面的垂直度差,毛刺大而厚,难以 去除,使冲裁件断面质量下降。
3) 模具刃口状态的影响
刃口越锋利,拉力越集中,毛刺越小。 当刃口磨损后,压缩力增大,毛刺也增大。毛
便产生微裂纹。
3 断裂分离阶段
凸模继续压入,凸、凹模刃口附近产生的微裂 纹不断向板材内部扩展,若间隙合理,上、下 裂纹则相遇重合,板料被拉断分离。断面上形 成一个粗糙的区域。当凸模再下行,冲落部分 将克服摩擦阻力从板材中推出,全部挤入凹模
冲裁件的工艺性ppt
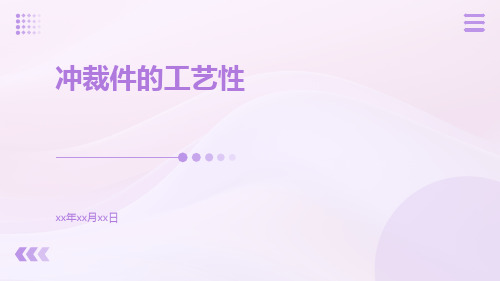
根据冲裁件的材料、厚度、尺寸和精度要求的不同,可以将 冲裁件分为多种类型,如普通冲裁件、硬质合金冲裁件、非 金属冲裁件、复杂形状冲裁件等。
冲裁件的应用范围
汽车制造
汽车车身、发动机、底盘等部件制 造。
家电制造
电视、冰箱、洗衣机、空调等家电 部件制造。
金属制品
钢桶、罐头盒、金属管件等金属制 品加工。
电子电器
电脑、手机、平板等各种电子电器 产品的零件制造。
冲裁件的设计原则
合理选择材料
优化零件结构
根据使用要求选择适当的材料,以满足使用 性能和工艺性能的要求。
考虑冲压工艺的特点,优化零件的结构设计 ,以简化模具结构,提高生产效率。
统一模数尺寸
标注清晰准确
尽量采用统一的模数尺寸,以简化模具制造 和降低生产成本。
详细描述:冲裁件的 结构工艺性主要考虑 以下几个方面
零件外形和结构是否 符合冲压模具的加工 特点,如模具的开模 距离、凹凸模间隙等 ;
零件的定位和导向是 否准确可靠,以保证 模具的精度和生产效 率;
零件的形状和结构是 否便于冲裁后的分离 和排出,如侧向抽芯 机构的设计等。
冲裁件的精度和表面质量分析
冲裁件精度高
冲裁件的精度通常较高,可达到IT10级以上,适 合于制造高精度的零件和制品。
适合大批量生产
冲裁件适合于大批量生产,生产效率高,生产成 本低,经济效益好。
材料的利用率高
冲裁件可利用材料的利用率较高,废料少,降低 了材料成本。
冲裁件工艺性的未来发展趋势
发展高精度冲裁技术
随着制造业的发展,对冲裁件的精度要求越来越高,因此,发展高精度冲裁技术是未来的 发展趋势。
冲裁件表面粗糙度是否 满足要求,如表面是否 有毛刺、划痕等缺陷。
冲裁工艺与排样设计
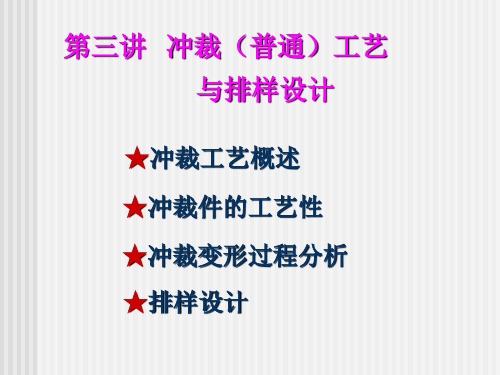
2.冲裁件断面特征—四个特征区
(1)塌角(圆角)区
①板料弯曲、拉伸作 用形成; ②冲孔、落料工序中, 塌角区分别位于孔
断面的小端和工件
断面的大端;
③板料塑性越好,凸、
凹模间的间隙越大, 形成的塌角区越大。
(2)光亮带
①因剪切变形而形成,光
亮带垂直于板料平面;
②冲孔、落料工序中,
光亮带分别位于孔断 面的小端和工件断面
(5)材料利用率计算
S1
100%
S1
100%
S0 AB mm 2 式中: s1—一个进距内冲裁件实际面积,
s0—一个距内所需毛坯面积, 2 mm
A—送料进距,mm B—条料宽度,mm。
提高材料利用率的有力措施是: 选择合适的板料规格和合理的裁板法; 利用废料作小零件;
设计合理的排样方案,例如:
⑵ 改善操作性 排样应使操作方便、安全、劳动强度低。具体
地,应尽量减少条料翻动次数,利用率相近时应选
用条料宽度和进距小的排样方式。
⑶ 使模具结构简单合理,使用寿命高。
⑷ 保证冲裁件质量。 有废料排样
3.排样的类型
少废料排样
无废料排样 (1)有废料排样 冲裁件与冲裁件之间、
冲裁件与条料侧边之间均有
工艺废料,冲裁是沿冲裁件 的封闭轮廓进行的。
经验确定的低碳钢冲裁时常用最小搭边值/mm
⑵ 条料进距 模具每冲裁一次,条料在模具上前进的距离。 当单个进距内只冲裁一个零件时,送料进距的
大小等于条料上两个零件对应点之间的距离。
A D a1
式中:
A —送料进距,mm; D —平行于送料方向的冲裁件宽度,mm; a1—冲裁件之间的搭边值,mm。
第三章 冲裁冲裁变形过程分析

第三章 冲裁
垫圈的落料与冲孔 a)落料 b)冲孔
第三章 冲裁
落 料 冲 孔 复 合 模
1-下模板 2-卸料螺钉 3-导柱 4-固定板 5-橡胶 6-导料销
7-落料凹模
8-推件块 9-固定板 10-导套 11-垫板 12、20-销钉 13-上模板 14-模柄 15-打杆 16、21-螺钉 17 冲孔凸模 18 凸凹模 19 卸料板 22-挡料销
不可避免。此外,间隙不正常、刃口
不锋利,还会加大毛刺。
第三章 冲裁
第二节 冲裁变形过程分析
二、冲裁件质量及其影响因素(续)
1.冲裁件断面质量影响因素 (1)材料性能的影响 a、b、d大,c小 (2)模具间隙的影响
间隙小,出现二次剪裂,产生第二光亮带
间隙大,出现二次拉裂,产生二个斜度 (3)模具刃口状态的影响
第二章 冲裁工艺与冲裁模设计
第三章 冲裁
冲裁变形过程
第三章 冲裁
冲裁区应力、变形和冲裁件正常的断面状况
a)冲孔件
b)落料件
第三章 冲裁
间隙对剪切裂纹与断面质量的影响 a )间隙过小 b)间隙合理 c)间隙过大
第三章 冲裁
凸、凹模刃口磨钝时毛刺的形成情况 a) 凹模磨钝 b) 凸模磨钝 c) 凸、凹模均磨钝
当凸模刃口磨钝时,则会在落料件上端产生毛刺; 当凹模刃口磨钝时,则会在冲孔件的孔口下端产 生毛刺; 当凸、凹模刃口同时磨钝时,则冲程分析
二、冲裁件质量及其影响因素(续)
2.冲裁件尺寸精度及其影响因素 冲裁件的尺寸精度:
指冲裁件的实际尺寸与图纸上基本尺寸之差。 该差值包括两方面的偏差:
扭曲:冲裁件呈扭歪现象。它是由于材料的不平、 间隙不均匀、凹模后角对材料摩擦不均匀等 造成的。
冲裁工艺的力学分析

減少沖裁力的方 法
減少沖裁力的方法
1﹒階梯沖裁(長短公沖 裁) 由于沖孔數量較多﹐造成總沖裁力大。我們可以將沖頭做成長短不一﹐
使得發生沖裁的時間錯開﹐實際用到的總沖裁力減小。但要注意下列問題﹕ A﹐長短公高度差最好大与料厚。 B﹐同一沖裁時間的沖頭要与其它沖裁時間的沖頭﹐盡量均勻間隔。 C﹐要註意最短沖頭的長度﹐不要短過沖裁高程。
分類
純鐵 低碳鋼 中碳鋼
對應牌號
經驗取值
25Kg/mm² 30 ~ 35Kg/mm² 35 ~ 40Kg/mm²
硅鋼
不銹鋼 彈簧鋼 軟呂 硬呂 黃銅 青銅
190~560
320~480 600~720 80~100 105~150 240~300 240 ~480 未硬化 半硬 SUS301﹐SUS304 35 ~ 45Kg/mm² 65Kg/mm² 20Kg/mm² 25 ~30 Kg/mm² 28Kg/mm² 35 ~ 40Kg/mm²
Ke值
0.35~0.15 0.15~0.06 0.06 ~0.05 0.05~0.04 0.04~0.035 0.035~0.03 0.03~0.025
P2=KeP1
3.0~4.0
4.0~6.5 >6.5
0.025~0.020
0.02 ~0.015 0.015
五﹐冲裁工艺的力学分析
推出力(P3)的 計算 影響P3大小的因素:
減少沖裁力的方法
4﹒跳孔沖裁
沖件上的孔較密集時﹐孔与孔的間隔少﹐就算單個沖孔面積小﹑沖裁力
也小﹐但是薄弱的模具間隔厚度仍然承受不了。為了增加模具間隔厚度﹐使 沖裁相對減小﹐我們可以將沖孔均勻分開在若干個步距或若干道工序中進行。 這种相對減小沖裁力的方法稱之為跳孔沖裁。注意﹕勿漏沖或重复沖。
第2章-冲裁工艺

B类尺寸,随凹模磨损,尺寸↓:
C类尺寸,随凹模磨损,尺寸不变:
34
2.3 冲裁模刃口尺寸计算
3)冲孔
第 2 章
冲
冲孔件
裁
工
艺
A类尺寸,随凸模磨损,尺寸↑:
B类尺寸,随凸模磨损,尺寸↓: C类尺寸,随凸模磨损,尺寸不变:
冲孔凸模刃口轮廓
35
2.3 冲裁模刃口尺寸计算
4)总之
第
2
第
2
非圆形工件x值
圆形工件x值
材料
章
厚度
1
0.75
0.5
0.75
0.5
t/mm
工 件 公 差 Δ/mm
冲
裁
1 <0.16 0.17~0.35 ≥0.36 <0.16 ≥0.16
工
1~2 <0.20 0.21~0.41 ≥0.42 <0.20 ≥0.20
艺
2~4 <0.24 0.25~0.49 ≥0.50 <0.24 ≥0.24
1、冲裁时的力态分析
第 普通冲裁示意图
2
模具工作部分有两个基
章
本特征:
冲
凸、凹模有锋利刃口
裁
凸、凹模有间隙
工
C - 单面间隙
艺
Z - 双面间隙
冲裁板料受力图
6
2.1 冲裁工艺分析
第
2
变形区位置
章
冲
裁
工
艺
变形区的应力状态
7
2.1 冲裁工艺分析
2、冲裁变形过程
第
2
1)弹性变形阶段
第2章 冲裁工艺
第
2.1 冲裁工艺分析
冲裁工艺设计

第二章 冲裁工艺与冲裁模设计
一、冲裁件的工艺性分析
1.冲裁件的结构工艺性(续) (3) 冲裁件上凸出的悬臂和凹槽不能过窄、过长; (4) 冲裁件的孔边距与孔间距不能过小; (5) 在弯曲件或拉深件上冲孔时,孔壁与工件直壁应保持一定距 离。
第二章 冲裁工艺与冲裁模设计
第七节 冲裁的工艺设计
一、冲裁件的工艺性分析
复合模冲裁的工件精度高 级进模冲裁的工件精度较低 单工序模冲裁的工件精度最低
第二章 冲裁工艺与冲裁模设计
第七节 冲裁的工艺设计
二、冲裁工艺方案的确定
1.冲裁工序的组合
(3)根据对冲裁件尺寸形状的适应性来确定
(4)根据模具制造安装调整的难易和成本的高低来确定 (5)根据操作是否方便与安全来确定
第二章 冲裁工艺与冲裁模设计
医疗
图标元素
第七节 冲裁的工艺设计
二、冲裁工艺方案的确定
2、冲裁顺序的安排
(1)级进冲裁顺序的安排
1)先冲孔或冲缺口,最后落料或切断,将冲裁件与条料分离。 2)采用定距侧刃时,定距侧刃切边工序安排与首次冲孔同时进 行,以便控制送料进距。
(2)多工序冲裁件用单工序冲裁时的顺序安排
1)先落料使坯料与条料分离,再冲孔或冲缺口。 2)冲裁大小不同、相距较近的孔时,为减少孔的变形,应先冲 大孔后冲小孔。
(1) 冲裁件的经济公差等级不高于IT11级,一般要求落料件 公差等级最好低于IT10级,冲孔件最好低于IT9级。 (2) 冲裁件的断面粗糙度与材料塑性、材料厚度、冲裁模间 隙、刃口锐钝以及冲模结构等有关。当冲裁厚度为2mm以下的 金属板料时,其断面粗糙度Ra一般可达12.5~3.2μm。
第二章 冲裁工艺与冲裁模设计
第二章 冲裁工艺与冲裁模设计
一)冲裁件工艺分析
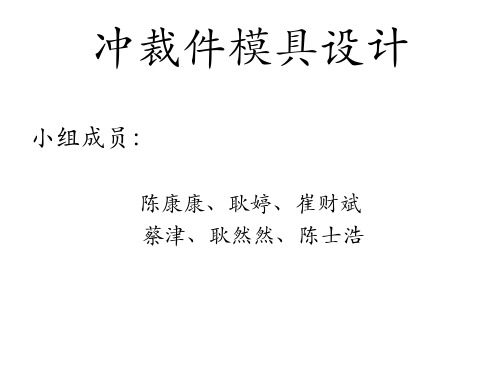
4.该零件的生产批量为大批量,因此在制定方案时, 应充分考虑如何提高生产率。 5.该零件形状对称,冲裁时手里均匀。 6.该零件精度等级为IT11,因此,模具的制造精度等 级为IT7级。 (二).确定工艺方案及模具结构形式 1.经分析,工件尺寸精度要求较高,形状不大,产量 较大,根据材料较厚的特点,为保证孔位精度,较 高的生产率。比较一下,如果采用单工序模,不符 合大批量生产的要求;如果采用级进模,需先冲孔 后落料,为保证精度要求,需要增加导正销,使结 构复杂化;如采用复合模,既可以提高生产率,又 可以使模具简单,精度也得以保证。故采用复合模 生产。
故∣ δp ∣ + ∣ δd ∣ ≥ Zmax –Zmin 所以采用配做的加工方式。利用 线切割也较容易较高。 落料,基准模为凹模,根据公式: *变小的尺寸(A类) A p =(A-x △ )-δp *变大的尺寸(B类) Bp =(B-x △)+δd *无变化的尺寸(C类) Cp =C± δp 可得数据如下表 b)加工内形冲孔 方法同上,但满足∣ δp ∣ + ∣ δd ∣ ≤ Zmax –Zmin 故可采用分别加工方法。 冲孔,基准模为凸模,根据公式: dp =(d+x △ )-δp dd =(dp + Zmin)+δd 所得数据如下表
c)横裁长直排 条料数为2000 ÷34=58 每条条料可冲1250÷60.2=20 零件总数为20 ×58=1160件
c)纵裁长直排 条料数为2000 ÷60.2=33 每条条料可冲1250÷34=36 零件总数为33 ×36=1188件
综上所述,选用b)方案。 3.确定压力中心 因为零件对称,且采用复合模,故压力中心在 几何中心上。 4.冲模刃口尺寸及公差的计算 a)首先加工外形落料部分 厚度为2mm,查表2-1得Zmax =0.26mm、Zmin =0.22mm,则Zmax –Zmin =0.04mm 查表2-3得 在30mm方向上 δp =0.02mm, δd =0.25mm 在58和38方向上 δp =0.02mm, δd =0.25mm
冲裁工艺及冲裁模设计

工艺性原则
冲裁模设计应满足生产 工艺要求,确保冲裁件
的质量和精度。
安全性原则
设计应确保操作安全, 防止模具使用过程中出
现危险。
经济性原则
在满足功能和安全性的 前提下,降低模具成本
。
维护性原则
设计应便于模具的安装 、调试、维修和保养。
冲裁模设计的步骤与方法
明确设计任务
了解冲裁件的结构、尺寸、材料和生产批量 等要求。
。
强度和韧性
选择具有良好强度和韧性的材 料,以确保模具在使用过程中 不易开裂或断裂。
热处理性能
选择适合的热处理工艺,以提 高模具的硬度和耐久性。
经济性
在满足性能要求的前提下,尽 量选择价格较低的材料,降低
模具成本。
03 冲裁模结构设计
冲裁模结构的选择
根据产品要求选择合适的冲裁模结构,如简单模 、连续模、复合模等。
03
固定方式。
冲裁模的装配与调试
01
根据设计图纸,正确装 配凸模、凹模、压板、 螺栓等零件。
02
检查装配后的冲裁模是 否符合设计要求,并进 行必要的调整。
03
进行试冲,检查冲裁件 的质量、尺寸精度和模 具的稳定性,对模具进 行调整优化。
04
对冲裁模进行保养和维 护,确保其长期稳定运 行。
04 冲裁模设计实例分析
Байду номын сангаас
实例一:简单冲裁模设计
总结词
结构简单、成本低、适用于中小批量生产
详细描述
简单冲裁模设计通常采用单工序模具,结构相对简单,制造成本较低,适用于中小批量生产。这种模具一般由上 模和下模组成,通过压力机将上模压下,使板料分离,完成冲裁工序。
实例二:复杂冲裁模设计
3-4 冲裁工艺分析

3-4 冲裁工艺分析
内容提纲:
一、冲裁件工艺性分析 二、冲裁工艺方案的确定
冲压工艺与模具设计
冲压工艺与模具设计
一、冲裁件工艺性分析
1、冲裁工艺性的概念
冲裁件的工艺性是指冲裁件对冲裁工艺的适应性,即冲裁加工的难易程 度。
冲裁工艺性好是指能用普通冲裁方法、材料消耗少、工序数目少、生产 率高、模具结构简单,而且寿命长,产品质量稳定、操作方便,生产效率 高等。
与之对应的模具分别是单工序冲裁模、复合冲裁模和级进冲裁模。
冲压工艺与模具设计
1)单工序模
特点: ➢ 结构简单、设计加工装配容易、成本低、操作简便; ➢ 效率低、寿命短; ➢ 适合小批量生产或试制品的加工;
常用的: 单工序落料模、单工序切边模、单工序拉深模等。
冲压工艺与模具设计
单工序落料模
冲压工艺与模具设计
冲压工艺与模具设计
项目 工件尺寸精度
工件形位公差 送料方式 冲压速度 生产效率 材料要求 安全性 模具制造难度
应用
三种类型模具的比较
单工序模
较低
复合模
IT9-IT11
级进模
IT11-IT13
工件不平整,同轴度、 工件平整,孔边距、同 对称度及位置度误差大 轴度、对称度和位置度
误差小
手动、自动送料均可 不适合自动送料
综上所述,该冲裁件的冲裁工艺性良好,适合冲压。
冲压工艺与模具设计
二、冲裁工艺方案的确定
冲裁工艺方案,是指工件的冲制要进行哪些工序,这些工序的组合方式 以及先后顺序安排。
冲裁工艺方案是在工艺分析的基础上,从结构、精度、尺寸、批量等方 面综合考虑,需确定基本冲裁工序、冲裁工序的组合方式、冲裁顺序的安排。
第三章-冲裁工艺课件

冲模
板料厚度t(mm)
制造
精度 0.5 0.8 1.0 1.5 2 3 4 5 6 7 8 10 12
IT6~7 IT8 IT8 IT9 IT10 IT10
IT7~8
IT9 IT10 IT10 IT12 IT12 IT12
IT9
IT12 IT12 IT12 IT12 IT12 IT14 IT14 IT14 IT14 IT14
0.25 0
将尺寸转化为标准尺寸:A0 ,则其设计公式为:
A模 ( Ax) 0 0.2 5
三类尺寸的设计之二
第二类:模具磨损后,制件尺寸减小。
按一般冲孔凸模公式设计计算,制造公差取
0 0.25
将尺寸转化为标准尺寸:B
0
,则其设计公式为:
B模 ( Bx) 0 0.2 5
三类尺寸的设计之三
配合加工法:用凸模和凹模相互单配的方法来保 证合理间隙
分别加工法适用于简单件,用于间隙较大,精度要求低的模 具,凸、凹模具有互换性。
配合加工法用于复杂件,用于精度要求高,间隙较小的模具, 凸、凹模之间无互换性。
2、分别加工法的尺寸计算
对于分别加工法, 我们必须给出凸、 凹模的设计尺寸以 及它们的公差
体反方向胀大
落料件尺寸大于凹模尺寸;冲孔件尺寸小于凸模尺寸
2、断面质量
断面质量取决于冲裁间隙。 间隙合理:由凸、凹模刃口所产生的裂纹重合 间隙不合理:则上下裂纹不重合
间隙对剪切裂纹与断面质量的影响 a)间隙过小 b)间隙合理 c)间隙过大
3、毛刺
a、由冲裁的过程可以知道,冲裁件产生微小的
0.0160.0250.0410.032
分别加工法简单模工作零件设计
凹0.6(ZmaxZm)in0.60.0320.019 凸0.4(ZmaxZm)in0.40.0320.013
冲裁工艺和冲裁模具设计

冲裁工艺和冲裁模具设计冲裁工艺和冲裁模具设计作为一种常见的金属加工技术,冲裁被广泛应用于制造汽车、电子设备、家电等各种产品。
冲裁过程包括剪切、拉伸、冲压等操作,通过模具对金属材料进行形状变化和剪切,来达到制造出所需产品的目的。
因此,冲裁工艺和冲裁模具设计对于产品的品质和生产效率至关重要。
一、冲裁工艺冲裁工艺是指冲裁操作的完整过程,包括模具设计、材料选择、冲裁机的选择、生产线的设计、冲裁参数设置、操作人员的技术水平等。
在整个冲裁工艺中,模具设计是决定产品精度和质量的关键因素之一。
而材料的选择则是根据需求而来,决定了产品的强度和耐用度。
同时,冲裁机的选择和生产线设计,也对质量和效率有很大的影响。
在冲裁参数设置方面,操作人员需要根据需要的产品要求选择适当的切削速度、切削深度、冲切速度和氧化器的温度,以确保工艺的高效性和安全性。
操作人员的技术水平和经验也是冲裁工艺中不可或缺的一环,只有经过深入的培训和实践才能熟练掌握冲裁操作技术,保证产品质量。
二、冲裁模具设计冲裁模具是冲裁过程中的中心部分,它能够使原材料按照特定的形状和尺寸被切割和改变。
因此,冲裁模具设计必须按照以下原则:1.符合产品尺寸和形状的需求冲裁模具的设计必须符合目标产品的需求,确保可靠和准确地达到预期的尺寸和形状。
特别是在生产大批量产品时,模具的稳定表现和可维护性是至关重要的。
2.优化切削、加工和生产速度冲裁模具设计必须考虑切削、加工和生产速度。
为获得最佳性能和保持稳定生产,冲裁模具必须经过详细的工程分析、优化和调整,以确保指定的材料厚度、切割宽度和其他冲裁过程条件。
这些是实现制造优化和节约时间的关键。
3.确保模具寿命和可靠性模具的设计必须考虑预计的使用寿命和维护要求,以确保高度的可靠性和生产效率。
根据产品需求,选择合适的材料和表面处理方法,以有效地提高模具寿命和耐久度,降低生产成本和维护费用。
4.考虑生产过程中的人工干预冲裁模具设计必须考虑生产过程中的人工干预,以确保操作人员的安全和效率。
第二章冲裁工艺分析5-6
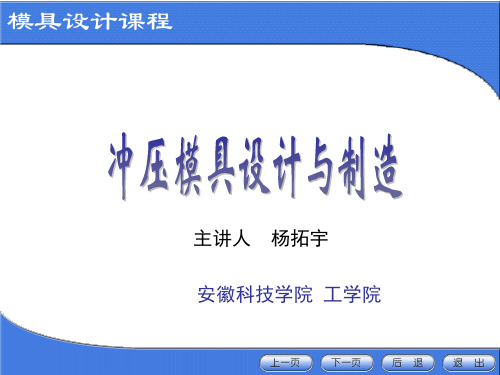
第二章 冲裁工艺与冲裁模
11导板,5凸模,在圆筒侧面冲孔。
导板式侧面冲孔模 1-摇臂2-定位销3-上模座4-螺钉5-凸模 6-凹模7-凹模体8-支架9-底座10-螺钉 11-导板12-销钉13-压缩弹簧
第二章 冲裁工艺与冲裁模
在筒形件的侧壁进 行冲孔,工作位置水 平。 斜楔1,随压力机向 下运动,推动滑块4和 凸模5向前运动,进行 冲孔,
补充:当采用弹压卸料板时,其凸模长度按下式计算:
L = H1 + H 2 + t + A '
第二章 冲裁工艺与冲裁模
第六节 冲裁模零部件结构设计
二、凹模结构设计
1.凹模结构形式 1)整体式:图2.29a 优点:结构简单,强度好;
缺点:整体采用模具刚成本高,适用于高精度小件。 刃口损坏如不能修补,需整体更换。
倒装式复合模
第二章 冲裁工艺与冲裁模
第二章 冲裁工艺与冲裁模
第六节 冲裁模零部件结构设计
第二章 冲裁工艺与冲裁模
第六节 冲裁模零部件结构设计
冲裁模零部件的分类:
工作零件
工艺零件 冲裁模零部件 结构零件 连接与固定零件 定位零件 卸料与推件零部件 模架
第二章 冲裁工艺与冲裁模
第六节 冲裁模零部件结构设计
全长导向结构的小孔冲模
第二章 冲裁工艺与冲裁模
局 部 放 大 图
第二章 冲裁工艺与冲裁模
第二章 冲裁工艺与冲裁模
1、9-定位板 2、3、4-小凸模 5-冲击块 7-小压板 8-大压板 10-侧压块 超 短 凸 模 的 小 孔 冲 模
第二章 冲裁工艺与冲裁模
局 部 放 大 图
第二章 冲裁工艺与冲裁模
第二章 冲裁工艺与冲裁模
冲裁工艺概述

冲裁时作用于板料的力
Fp,Fd 分别是凸、凹模对板料的垂直作用力;
F1,F2 是凸、凹模对板料的侧压力;
μFp,μFd 是凸、凹模断面与板料之间的摩擦 力,其方向和间隙的大小有关; μF1,μF2 是凸、凹模侧面与板料之间的摩擦 力。
3.冲裁变形时的应力状态
冲裁时,由于板料弯曲的影响,其剪切区的应力状态复杂,与变形过程有 关。其裁剪区板料的应力状态如图所示。
冲裁变形过程
(a)弹性变形阶段 (b)塑性变形阶段 (c)裂纹扩展阶段 (d)断裂分离阶段
弹性变形阶段 弹性变形阶段
当凸模开始接触板料并且下压时,变 形区内产生弹性压缩、拉深、弯曲等变形, 板料被稍微挤入凹模洞孔中,凸模下端面 的板料产生弯曲,凹模断面的板料向上翘 曲。间隙越大,弯曲和翘曲就越严重。随 着凸、凹模刃口压入板料,刃口处的材料 所受到的应力逐渐变大,直到达到板料的 弹性接线。若卸去凸模压力,板料能够恢 复原状,不会产生永久变形。
塑性变形阶段
凸模继续下压,板料的内应力达 到屈服极限,板料在与凸、凹模刃口 接触处产生塑性变形,此时凸模切入 板料,板料挤入凹模,产生塑性剪切 变形,形成光亮的剪切断面。随着塑 性变形加大,变形区的材料硬化加剧, 冲裁变形力不断增大,当刃口附近的 材料由于拉应力的作用出现微裂纹时, 说明塑性变形阶段结束。
冲裁变形过程弹性变形阶段弹性变形阶段当凸模开始接触板料并且下压时变形区内产生弹性压缩拉深弯曲等变形板料被稍微挤入凹模洞孔中凸模下端面的板料产生弯曲凹模断面的板料向上翘曲
冲裁工艺概述
3.2 冲裁工艺
冲裁加工示意图
冲裁工艺是冲压分离工序 的总称,是利用模具在压力机 上使板料的一部分沿着一定的 轮廓形状与另一部分产生分离 的一种冲压工序。
- 1、下载文档前请自行甄别文档内容的完整性,平台不提供额外的编辑、内容补充、找答案等附加服务。
- 2、"仅部分预览"的文档,不可在线预览部分如存在完整性等问题,可反馈申请退款(可完整预览的文档不适用该条件!)。
- 3、如文档侵犯您的权益,请联系客服反馈,我们会尽快为您处理(人工客服工作时间:9:00-18:30)。
科l技}论{坛科耥
厚板料冷冲压模具设计及冲裁工艺分析
魏圣坤
(泸州职业技术学院,四川泸州646000)
摘要:随着我国机械工业生产的稳定、快速发展和技术水准的提高,各种新技艺、设备亦同时得到了广泛的应用与发展。
与此同时,各种产品的更新换代速度也加快.对其质量的要求更是日益增长。
就模具材料的选择以及厚材料冲裁的特点和冲裁工艺进行了分析。
关键词:厚材料;冷冲压;模具设计;冲裁工艺
根据现代工业的发展趋势,工业产品的特下降的趋势,引起材料承载能力及耐磨损能力2.1.3冲裁时,由于材料本身具有的弹性,征表现为:大型产品和小型化多功能产品的结下降。
因此,对于高速冲载货剧烈摩擦磨损的冷刃口周边的材料首先发生弹性穹弯现象,然后构越来越复杂,告诉、高温、高摩擦及腐蚀性工作模具,宜选择一些具有二次硬化能力的高合完成冲裁的全过程。
冲裁工作完成后,这种弹性作环境的产品,对高性能材料的需求越来越迫金钢。
穹弯不可能全部恢复,因而使重裁件不平整。
当切。
对模具制造业也提出了更高更新的要求,要
1.1.7咬合抗力。
咬合抗力实际就是对发产品设计对冲压零件有一定平直度要求时.应
模具有更高的性能和精度,模具结构和工作生“冷焊”的抵抗能力。
模具材料的咬合抗力与采取适当的工艺来提高重建表面的平直度。
更复杂,工作温度更高,寿命也需求更长。
材料的性质和模具润滑条件有关,如奥氏体不
2.2精冲工艺的设计
在模具是小的诸多因素中,材料的热处理已经锈钢、精密合金等材料易发生咬合及粘结现象。
如果产品设计时对工件的平直度和冲裁成为影响模具寿命的主要因素。
因此,根据模具1.2模具材料的选用断面质量均有严格的要求,又不希望增加后续的工作条件,合理选用模具材料,是保证模具既模具材料的选用,不仅关系到模具的使用校平、整修等工序.就可以采用精冲工艺保证产安全可靠又经济合理的关键因素。
寿命,而且也直接影响到模具的制造成本,因此品设计要求。
1对模具材料性能的要求是模具设计中的一项重要工作。
在冲压过程中,精冲是指采用强力齿圈压边加压冲裁,
获1.1模具材料的使用性能模具承受冲击负荷且连续工作,使凸、凹模受到得高精度高冲裁断面质量的冲裁文艺。
其与一不同的冲压方法,模具类型也不相同;工强大压力和剧烈摩擦,工作条件极其恶劣。
因此般冲裁的主要区别有:作条件有差异,对模具材料的要求也有所不同。
选择模具材料应遵循如下原则: n一般冲裁时,材料处于自由状态,即使采
要根据模具的工作条件和使用寿命要求,
1.2.1根据模具种类极其工作条件,选用用压料板、推件板因为是弹性压料,压料力有地选择模具材料和热处理工艺,使之达到主要材料要满足使用要求.应具有较高的强度、硬限,不能很好的限制材料的穹弯现象。
这是精冲性能蕞优,而其它性能损失最小的最佳状态。
对度、耐磨性、耐冲击、耐疲劳等。
与一般冲裁的本质区别。
、模具材料提出的使用性能要求,主要包括强度、
1.2.2根据冲压材料和冲压件生产批量选b精冲时冲裁间隙为材料厚度的l%左
右,硬度、韧性及耐磨性等。
用材料。
材料冲裁区域处于三向受压的应力状态,只产
1.1.1强度。
强度是表征材料变抗力和断
1.2‘3满足加工要求,应具有良好的加工生塑性剪切.不会出现一般冲裁时的撕裂现象,
裂抗力的性能指标。
冷作模具的设计和使用.必工艺性能,便于切削加工,淬透性好、热处理变因而冲裁件的整个断面都是剪切的光亮带。
须保证其具有足够的强度,以防止由于冲击、偏形小。
a精冲时,因为需要提供强力的压料力,所心弯曲载荷、重载荷、应力集中等,引起模具的
1.2.4满足经济性的要求。
以需要选用专用的精冲压力机。
如使用普通压变形、破裂和折断。
在材料选定的情况下,高强2厚版料冲裁的特点及冲裁工艺分析力机时,则需要选用液压模架,液压模架是普通度的获得,主要通过适当的热处理工艺。
厚材料冲裁与一般冲裁相比,由于在冲裁压力机上使用的
上下模板中心各
1.1.2硬度、模具零件硬度的高低,对模具间隙和冲裁力等方面有明显差别,因而在设计有一个液压缸,缸内安装有活动柱塞用以提供的使用寿命影响很大,因此也是模具设计的重冲裁零件、制定冲裁工艺、设计冲裁模具时应采齿圈压力和顶件力,精冲模具直接安装与模架要指标。
模具的最佳工作硬度和模具材料的种取相应的措施。
中即可使用。
类及具体的服役条件有关,模具的硬度一般应厚材料一般是指厚度在5mm以上的版厚材料冲裁的关键是在于使用合理的冲裁在
60HRc左右。
料,厚材料冲裁时冲裁力大。
模具易损伤,特别裁工艺来保证冲裁质量,从冲裁件质量、模具使
1.1.3韧性。
韧性是材料在冲击载荷作用是尖角处和凸模刃口处,由于材料受挤压力大,用寿命、模具髓i造成本等方面综合考虑,使厚材下抵抗产生裂纹的一个特征,反映了模具的脆易发生崩刃和剥层现象,使刃磨周期缩短,刃磨料冲裁质量稳定,安全可靠,经济合理。
断抗力,是模真钢的一种重要性能指标。
对韧性量大,大大降低模具使用寿命。
厚材料冲裁时选结束语的具体要求,应根据模具的工作条件考虑。
对冲用偏大的冲裁问隙。
有助于降低冲裁力,但却使随着机械领域科学技术的发展,人们的欣击载荷较大,受偏心弯曲载荷或应力集中等的所冲零件断面斜度增大。
单面斜度可达5。
赏水平和使用要求越来越高,对汽车尤其是轿模具。
都需要足够的任性。
~8。
,工件尖角处塌角更大。
而且由于冲裁时车等机械的外观造型有更高的要求,即对机械
1.1.4耐磨性。
耐磨性除影响模具寿命外,的材料弹性弯弯现象,一般冲裁件的平面平直外覆盖件的表面质量及造型有更高的要求,所还影响产品尺寸精度和表面粗糙度。
模具的耐度会超过o.5一lmm,严重影响工件的质量。
同时以,机械产品若要占领市场,那么就必须加快机磨性不仅取决于材料的成分、组织和性能,而且由于厚材料冲裁时的高冲击载荷,对模具的强械的改型换代速度。
为了满足这一要求,进一步
与模具的工作温度、压力状态、润滑状态等因素度、刚度以及凸、凹模的抗疲劳能力均有较高的说就是冲压工艺、模具设计、制造是相当重要有很大关系、一般模具材料的硬度要求,应高于要求。
针对厚材料冲裁的特点,采用适当的工艺的。
冲压工艺、冲模设计必须以模具制造周期胚料硬度的30%.5%,模具材料的金相组织要措施以提高冲裁件质量,延长模具使用寿命,以短、成本低、产品(冲压件)质量好为目的。
而产求,为基体上分布着细小、弥散的细颗粒状碳化下枚
举几条,供参考。
品(冲压件)的质量是由模具的精度保证的,冲物的下贝氏体或回火马氏体。
2.1延长模具寿命压工艺必须以满足产品要求并使模具操作方
1.1.5抗疲劳性。
抗疲劳力是反映材料在
2.I.1产品设计时对厚材料冲裁件应避免便,结构可靠、使用安全为目的。
交变载荷作用下,抵抗疲劳破坏的性能指标。
根出现清角、锐角、窄边和窄槽等结构,角部圆角参_______考文献据不同的应用场合,分为疲劳强度、疲劳裂纹萌半径不小于1/2【,锐角不小于60。
,窄边、窄槽[1】扬建华.厚材料冲裁工艺分析及模具设计[J].生力、疲劳裂纹扩展抗力、小能量多冲抗力等。
宽度不小于5倍料厚,以减轻工件塌角和延长模具制造,2006(5).
1.1.6热稳定性。
热稳定性标示模具在使模具使用寿命。
.【2】刘晓飞,关连峰.冷冲压模具材料的合理选择用过程中,工作部位因受热而保持组织和性能2.1.2当对工件断面质量无特殊要求时, [J].装备制造技术,2009(6).稳定的能力。
受温度影响时,材料内部院子的活建议采用大间隙冲裁,以便降低冲裁力、提高模[3】孟少明.《冷冲压工艺及模具设计》教学改革
动能力增加,使材料产生塑性提高而强度、硬度具的使用寿命。
浅谈们.科技咨询,2008(30).
万方数据
厚板料冷冲压模具设计及冲裁工艺分析
作者:魏圣坤
作者单位:泸州职业技术学院,四川,泸州,646000
刊名:
黑龙江科技信息
英文刊名:HEILONGJIANG SCIENCE AND TECHNOLOGY INFORMATION
年,卷(期): 2010,""(20)
被引用次数: 0次
1.杨建华厚材料冲裁工艺分析及模具设计2006(5)
2.刘晓飞.关连峰冷冲压模具材料的合理选择2009(6)
3.孟少明《冷冲压工艺及模具设计》教学改革浅谈2008(30)
本文链接:
/Periodical_hljkjxx201020043.aspx
授权使用:湖南农业大学(hunannydx),授权号:
daa0abad-267f-479c-a048-9e3b00af298b
下载时间:2010年11月27日__。