复合材料界面的表征_仪器分析技术_苏波
复合材料的界面相互作用研究
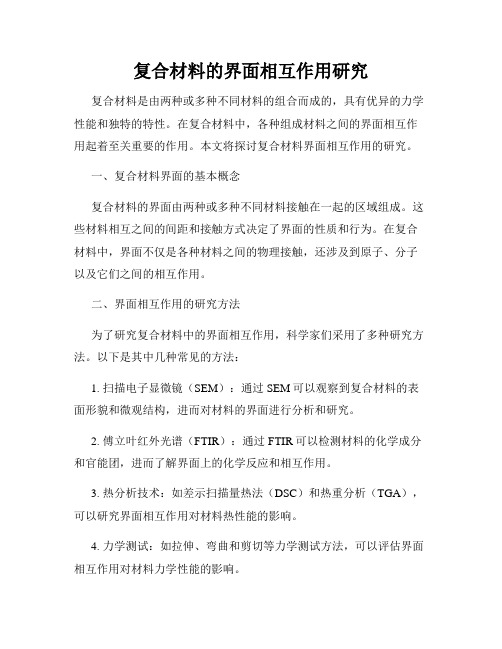
复合材料的界面相互作用研究复合材料是由两种或多种不同材料的组合而成的,具有优异的力学性能和独特的特性。
在复合材料中,各种组成材料之间的界面相互作用起着至关重要的作用。
本文将探讨复合材料界面相互作用的研究。
一、复合材料界面的基本概念复合材料的界面由两种或多种不同材料接触在一起的区域组成。
这些材料相互之间的间距和接触方式决定了界面的性质和行为。
在复合材料中,界面不仅是各种材料之间的物理接触,还涉及到原子、分子以及它们之间的相互作用。
二、界面相互作用的研究方法为了研究复合材料中的界面相互作用,科学家们采用了多种研究方法。
以下是其中几种常见的方法:1. 扫描电子显微镜(SEM):通过SEM可以观察到复合材料的表面形貌和微观结构,进而对材料的界面进行分析和研究。
2. 傅立叶红外光谱(FTIR):通过FTIR可以检测材料的化学成分和官能团,进而了解界面上的化学反应和相互作用。
3. 热分析技术:如差示扫描量热法(DSC)和热重分析(TGA),可以研究界面相互作用对材料热性能的影响。
4. 力学测试:如拉伸、弯曲和剪切等力学测试方法,可以评估界面相互作用对材料力学性能的影响。
三、界面相互作用的影响因素复合材料中界面相互作用的性质和行为受多种因素的影响。
以下是几个重要的影响因素:1. 材料选择:界面相互作用的性质受到组成材料的选择和特性的影响。
不同类型的材料在界面上的相互作用方式各不相同。
2. 温度和湿度:界面相互作用对温度和湿度的敏感性较强。
温湿度的变化会导致界面的物理和化学行为发生改变,进而影响材料的性能。
3. 表面处理:采用不同的表面处理方法可以改变界面的性质。
例如,化学处理、表面涂覆和增加粗糙度等方法可以改善界面的结合强度和相互作用性能。
四、界面相互作用的作用机制复合材料中的界面相互作用涉及到多种机制,其中最常见的包括物理吸附、化学键合和电荷转移等。
这些作用机制直接影响着界面的结构、力学性能和化学性质。
1. 物理吸附:界面上的物理吸附是材料间的非化学吸附,通过分子间的范德华力和静电作用产生。
第六章复合材料表界面的分析表征

41
不同处理碳纤维增强复合材料冲击 载荷与冲击时间的对应关系
A. 接枝聚丙烯酰胺碳纤维; B. 接枝聚丙烯 酸碳纤维; C. 氧等离子处理碳纤维; D. 未 处理碳纤维
氧等离子处理(曲线C)碳纤维 复合丝试样的冲击载荷曲线主 要弹性承载能U1差不多比未处 理者增加近3倍,表明基体变形 更大,也有更多的纤维发生形 变。相反塑性承载能U2却小到 可略视的地步,几乎没有什么 纤维拔出和与基体的脱粘,充 分表明了强结合的界面特征。
25
碳纤维表面官能团的分析
还原剂,消除自由基,证明等 离子处理产生的大部分是游离
基,不是酚羟基
图6-25 等离子处理时间对自由基浓度的影响
在等离子处理初期,自由基浓度迅速增加,处 理5分钟后,自由基浓度增加渐趋平缓。
27
图6-26 UHMWPE纤维表面活性的衰减
经等离子处理后的UHMWPE纤维暴露在空气中,表 面自由基的浓度随时间而衰减,表面活性在逐渐减小
36
6.4.2 复合材料界面的动态力学分析
a-接枝玻纤 b-未接枝玻纤 涂敷聚苯乙烯树脂的玻璃纤维辫子的动态
力学扭辫曲线
曲线b在92℃处出现一个 尖锐的聚苯乙烯玻璃化转变 损耗峰,而曲线a上,在聚 苯乙烯玻璃化转变损耗峰高 温一侧还有一个小峰,一般 称为α’峰,也叫做界面峰。
界面粘结强,则试样承 受周期负荷时界面的能力损 耗大,α’峰越明显。
复合材料界面受到因 热膨胀系数不同引起 的热残余应力。热残 余应力的大小正比于 两者的热膨胀系数之 差Δα和温差ΔT, 也与基体和纤维的模 量有关。
29
❖ 6.4 界面力学性能的分析表征
基于动态模量成像的碳纤维复合材料界面结构表征

× 256 个点 。 样品 表 面 受 到 动 态 正 弦 力 时, 材料的形变也随动态 且 两 者 的 频 率 相 同。但 是 材 料 的 黏 弹 性 使 得 力呈现周期的振荡, 位移与动态力之间存在 固 定 的 相 位 差 Ф , 相位的大小即可反映材 料的黏弹性行 为 。 动 态 模 量 成 像 的 测 试 结 构 可 以 用 两 个 KelvinVoigt 黏 弹 性 模 型 表 示 ( 图 1 ) 。 因 此, 针尖的振动方程可以表 示为: F ( t ) = mz″( t ) + ( D i + D s ) z' ( t ) + ( K s + S ) z ( t ) K s 为与针尖相并联的支持弹簧的刚度 。 接触阻尼,
iω t i( ω t - Ф ) 将动态力 F ( t ) = F 0 e 和位移 z ( t ) = z 0 e 代入针尖的振动方程( 1) , 则可以得到存储刚度 S [5] 和损失刚度 ω D s , 进一步计算即可得到储能模量 E' 、 损失模量 E″和损耗因子 tan δ :
( 1)
图1
2. 2. 1
静载荷大小的影响
[5]
系统所施加静载荷直接影响压针压入样品表面的深度 。 根据 弹 塑 性 变 形 理 论, 相邻压入之间的距 离至少是最大压入深度的 10 倍 。 本实验中测试是在 10 μ m × 10 μ m 尺度上压入 256 × 256 个点, 压坑 之间的距离在 40nm 左右 。 因此, 需要设定适当的静载荷使压入深度小于 4nm 。 另外, 对于不同力学性 能的材料, 静载 / 动载之比的设置也有不同 。 一般来说, 模量较大的材料选取较大的静载 / 动载比可以得 到离散度较小的结果, 而弹塑性体需要选取较小的静载 / 动 载 比 。 碳 纤 维 / 树 脂 复 合 材 料 中 的 纤 维 和 树 因此需要选择可以兼顾两者特性的参 数 来 进 行 测 试 。 结 合 以 上 分 析 分 脂力学性能存在着明显的差异, 3 μN 和 别在以下三种条 件 下 进 行 实 验: 在 保 持 其 他 实 验 参 数 一 致 的 情 况 下, 分 别 选 取 静 载 荷 2 μN 、 10 μ N 对试样进行测试 。 对测试结果进行直方图统计, 并进行拟合, 如图 6 所示 。 静载荷为 2 μ N 时, 纤维区和树脂区彼此分 离, 并且两个区域的数据离散性均较小; 静 载 在 3 μ N 时, 纤 维 区 和 树 脂 区 的 峰 有 部 分 交 叠, 并且纤维区 的数据离散性较大; 静载在 10 μ N 时, 纤维 区 和 树 脂 区 的 峰 发 生 严 重 交 叠, 并且纤维区的数据离散性非 常大 。
第5章复合材料界面力学
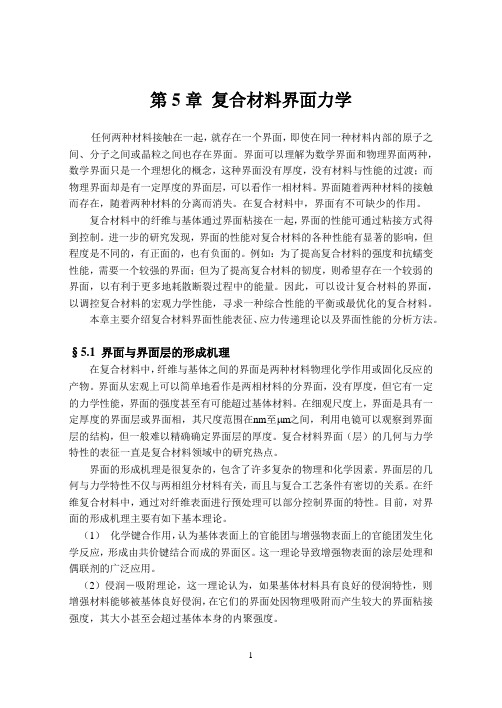
第5章复合材料界面力学任何两种材料接触在一起,就存在一个界面,即使在同一种材料内部的原子之间、分子之间或晶粒之间也存在界面。
界面可以理解为数学界面和物理界面两种,数学界面只是一个理想化的概念,这种界面没有厚度,没有材料与性能的过渡;而物理界面却是有一定厚度的界面层,可以看作一相材料。
界面随着两种材料的接触而存在,随着两种材料的分离而消失。
在复合材料中,界面有不可缺少的作用。
复合材料中的纤维与基体通过界面粘接在一起,界面的性能可通过粘接方式得到控制。
进一步的研究发现,界面的性能对复合材料的各种性能有显著的影响,但程度是不同的,有正面的,也有负面的。
例如:为了提高复合材料的强度和抗蠕变性能,需要一个较强的界面;但为了提高复合材料的韧度,则希望存在一个较弱的界面,以有利于更多地耗散断裂过程中的能量。
因此,可以设计复合材料的界面,以调控复合材料的宏观力学性能,寻求一种综合性能的平衡或最优化的复合材料。
本章主要介绍复合材料界面性能表征、应力传递理论以及界面性能的分析方法。
§5.1 界面与界面层的形成机理在复合材料中,纤维与基体之间的界面是两种材料物理化学作用或固化反应的产物。
界面从宏观上可以简单地看作是两相材料的分界面,没有厚度,但它有一定的力学性能,界面的强度甚至有可能超过基体材料。
在细观尺度上,界面是具有一定厚度的界面层或界面相,其尺度范围在nm至 m之间,利用电镜可以观察到界面层的结构,但一般难以精确确定界面层的厚度。
复合材料界面(层)的几何与力学特性的表征一直是复合材料领域中的研究热点。
界面的形成机理是很复杂的,包含了许多复杂的物理和化学因素。
界面层的几何与力学特性不仅与两相组分材料有关,而且与复合工艺条件有密切的关系。
在纤维复合材料中,通过对纤维表面进行预处理可以部分控制界面的特性。
目前,对界面的形成机理主要有如下基本理论。
(1)化学键合作用,认为基体表面上的官能团与增强物表面上的官能团发生化学反应,形成由共价键结合而成的界面区。
聚合物复合材料的界面强度分析

聚合物复合材料的界面强度分析聚合物复合材料是由两种或两种以上不同性质的材料通过物理或化学方法组合而成的多相材料。
其中,聚合物基体和增强相之间的界面区域对于材料的整体性能起着至关重要的作用。
界面强度的大小直接影响着复合材料的力学性能、热性能、电性能等诸多方面。
因此,对聚合物复合材料界面强度的深入分析具有重要的理论和实际意义。
聚合物复合材料的界面是一个复杂的区域,其结构和性能与基体和增强相均有所不同。
在界面区域,由于两种材料的化学组成、物理结构和性能的差异,会产生一系列的物理和化学相互作用,如化学键合、范德华力、氢键、机械嵌合等。
这些相互作用共同决定了界面的强度。
影响聚合物复合材料界面强度的因素众多。
首先,基体和增强相的化学性质是关键因素之一。
如果两者的化学结构相似,能够形成较强的化学键合,如共价键或离子键,那么界面强度通常会较高。
反之,如果化学性质差异较大,难以形成有效的化学键合,界面强度则可能较低。
其次,界面的物理结构也对强度产生重要影响。
例如,界面的粗糙度、孔隙率等都会改变界面的接触面积和应力分布,从而影响界面强度。
较粗糙的界面可能会增加机械嵌合作用,提高界面强度;而过多的孔隙则可能成为应力集中点,降低界面强度。
再者,制备工艺条件也在很大程度上决定了界面强度。
复合材料的制备过程,如成型温度、压力、时间等,都会影响基体和增强相之间的相互扩散和化学反应,进而影响界面的结合情况。
为了准确评估聚合物复合材料的界面强度,研究人员开发了多种测试方法。
其中,单纤维拔出试验是一种常用的方法。
在该试验中,将一根纤维埋入基体中,然后施加外力将纤维拔出,通过测量拔出力和纤维的埋入长度等参数,可以计算出界面的剪切强度。
此外,还有微脱粘试验、短梁剪切试验等方法。
微脱粘试验通过施加微小的力使纤维与基体局部脱粘,从而测量界面的粘结强度;短梁剪切试验则是对复合材料的短梁进行剪切加载,通过分析破坏模式和强度来间接评估界面强度。
多层复合材料的界面表征与优化

多层复合材料的界面表征与优化随着科学技术的不断进步,多层复合材料在现代工程中得到了广泛的应用。
多层复合材料由不同种类的材料层叠组合而成,每一层材料都有其独特的特性和功能。
其中,界面是多层复合材料中至关重要的部分,它直接影响着多层复合材料的性能和强度。
因此,对多层复合材料的界面进行表征与优化,对于提高材料的整体性能具有重要意义。
一、界面表征多层复合材料的界面是由两个不同材料的层之间的接触面形成的。
在界面处,两种材料的性质和结构会发生变化,这种变化直接影响着材料的性能。
因此,了解和表征多层复合材料的界面是非常必要的。
1. 宏观表征宏观表征方法主要通过对多层复合材料整体性能的测试和分析来了解界面的特性。
例如,通过静态拉力试验、冲击试验、疲劳试验等,可以测量材料的强度、韧性、疲劳寿命等指标,并通过对测试结果的分析,得到界面的性能和结构信息。
2. 微观表征微观表征方法主要通过显微观察和材料表面分析技术来了解多层复合材料界面的结构和组成。
例如,使用电子显微镜观察多层复合材料的交界面,可以观察到不同材料间的结合情况、界面的致密性以及可能存在的缺陷等信息。
此外,还可以利用X射线光电子能谱(XPS)、傅里叶变换红外光谱(FTIR)等技术,分析界面的化学成分和表面结构,进一步了解界面的特性。
二、界面优化多层复合材料的界面优化是指通过改变界面结构和性质,提高多层复合材料的整体性能和强度。
界面优化可以从多个方面进行,下面介绍几种常用的优化方法。
1. 表面处理表面处理是指通过改变材料表面的化学性质和结构,提高多层复合材料界面的粘结强度和界面结构的致密性。
表面处理包括物理方法和化学方法两种。
常用的物理方法有喷砂、电火花加工等,而化学方法则包括溶液浸泡、化学涂覆等。
通过表面处理,可以增加材料界面的接触面积,提高界面的亲和力,从而增强界面的结合力。
2. 加强剂应用在多层复合材料的界面中添加适量的加强剂能够有效地提高界面的强度和韧性。
复合材料的界面相互作用分析
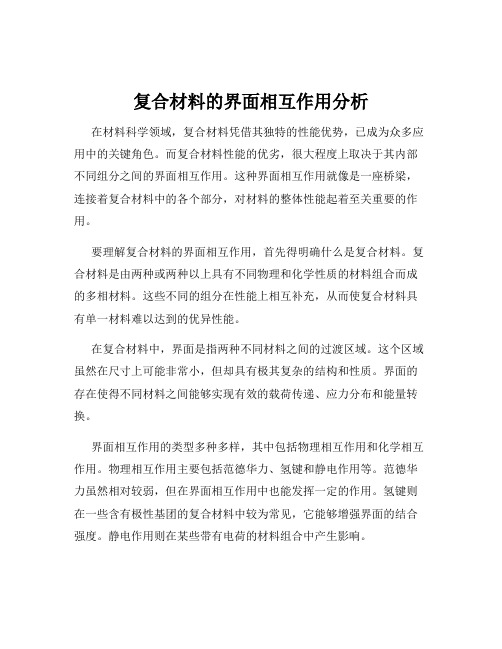
复合材料的界面相互作用分析在材料科学领域,复合材料凭借其独特的性能优势,已成为众多应用中的关键角色。
而复合材料性能的优劣,很大程度上取决于其内部不同组分之间的界面相互作用。
这种界面相互作用就像是一座桥梁,连接着复合材料中的各个部分,对材料的整体性能起着至关重要的作用。
要理解复合材料的界面相互作用,首先得明确什么是复合材料。
复合材料是由两种或两种以上具有不同物理和化学性质的材料组合而成的多相材料。
这些不同的组分在性能上相互补充,从而使复合材料具有单一材料难以达到的优异性能。
在复合材料中,界面是指两种不同材料之间的过渡区域。
这个区域虽然在尺寸上可能非常小,但却具有极其复杂的结构和性质。
界面的存在使得不同材料之间能够实现有效的载荷传递、应力分布和能量转换。
界面相互作用的类型多种多样,其中包括物理相互作用和化学相互作用。
物理相互作用主要包括范德华力、氢键和静电作用等。
范德华力虽然相对较弱,但在界面相互作用中也能发挥一定的作用。
氢键则在一些含有极性基团的复合材料中较为常见,它能够增强界面的结合强度。
静电作用则在某些带有电荷的材料组合中产生影响。
化学相互作用在复合材料的界面结合中往往起着更为关键的作用。
例如,在一些复合材料中,不同组分之间可能会发生化学反应,形成化学键,如共价键、离子键等。
这些化学键的形成极大地提高了界面的结合强度,使得复合材料在承受外力时能够更加稳定地传递载荷。
复合材料的界面相互作用对其性能的影响是多方面的。
在力学性能方面,良好的界面结合能够提高复合材料的强度、刚度和韧性。
当载荷施加到复合材料上时,界面能够有效地将应力从一个组分传递到另一个组分,避免局部应力集中,从而提高材料的整体承载能力。
如果界面结合不良,就容易在界面处产生裂纹和脱粘,导致材料过早失效。
在热性能方面,界面相互作用也起着重要的作用。
不同材料的热膨胀系数往往不同,当温度发生变化时,界面处可能会产生热应力。
良好的界面结合能够缓解这种热应力,提高复合材料的热稳定性。
碳纤维表面和复合材料界面表征及理论知识

碳纤维表面和复合材料界面表征及理论知识以下是张博在碳纤维研习社交流的讲解:大家好很开心再次和大家交流。
今天主要想和大家交流下复合材料界面这方面的知识或许会比较枯燥希望砖头来得温柔些哈哈。
复合材料是基体与增强材料符合而成的,它克服了单一材料的局限性:如陶瓷的脆性、高分子材料的弹性模量低,显示出比单一材料有较多的优越性但是这种优越性只有在两种或多种材料复合后,相界面具有良好的界面粘结强度,各种材料结合成一个整体的情况下,才能显示出来。
碳纤维以及有机纤维,与树脂基体的性能都有较大的差异,尤其是碳纤维作为无机类增强材料,一般来说极性与基体树脂相差大,表面化学组成也与基体树脂不同,二者存在着一定的差距,因此它们的相容性不好。
由此可见,对增强材料表面进行处理改性是很有意义的,而且十分必要。
关于纤维表面改性,之前已经有老师讲过了,在此不再赘述。
有一点是可以肯定的,表面改性对复合材料性能的影响是很大的,这主要是由于表面改性直接关系到界面的粘结强度所致。
不同粘结强度的界面,其界面层的结构和性能是不同的。
复合材料中增强体与基体接触构成的界面,是一层具有一定厚度(纳米以上)、结构随基体和增强体而异的、与基体有明显差别的新相——界面相(界面层),它是增强相与基体连接的纽带,也是应力及其他信息传递的桥梁。
因此界面是复合材料组成的重要组成部分,它的组成、性质、结合方式以及界面结合强度的大小直接对复合材料的力学性能以及破坏行为有着重大的影响,所以对复合材料的界面进行研究有着十分重要的意义。
纤维与树脂的界面相结构是表面反应的产物,是纤维固态表面与液态树脂接触界面上各种相互作用力平衡结果,是一个依赖时间的过程。
复合材料的成型工艺对界面相结构有着重要的影响,不同的升温速率、停留温度和停留时间等,都会对材料的最终性能产生影响,自然也会对界面有着或大或小的影响。
所以,复合材料工程师可以利用工艺条件和工艺窗口,适当地调节和改变界面相结构。
复合材料界面3

纤维的表面浸润性主要通过接触角和表面能来 表征。
1、纤维对液体接触角测定
单丝浸润法
将纤维单丝用胶带粘在试样夹头上,然后悬挂在试样
架上,纤维下端挂一重吹,使纤维与液面接触,由于
表面张力作用,与纤维接触部分液面会上升,呈弯月
面,在放大机下读液面上升最大高度hmax弯月,则可
6、层间剪切强度
➢ 压剪法 可参见GB1450.1—83,对试 样施加均匀连续的剪应力,直至破坏。 层间剪切强度可按下式计算:
短梁弯曲法
参见GB3357—82 ASTM D2544—84装置示 意如图,连续加载至试样破坏,记录最大载荷 值及试样破坏形式。层间剪切强度按下式 计 算:
7、动态力学分析
求出接触角:
cos
r (hmax0.809)
er
1sin
式中, / g ,σl为液体表面张力,ρ为密度, r为纤维半径
单丝浸润力法
用电子天平测试纤维脱 离液面瞬间表面张力变 化ΔP, ΔP=2лr σl cosθ 可求出接触角θ
互不相溶液体界面张力与接触角 用铂金作纤维,则液体完全润湿纤
聚丙烯酸接枝碳纤维复合丝试样的弹性承栽能E2很大(b),其时间对应上与氧等离子 处理者相近,也没有明显表现出纤维滑移的征状。与氧等离子处理者所不同的是接 枝纤维样品的E2部分也比较大,表明在界面上也容许有一定量的纤维产生滑移和脱 粘。与E1相比E2占有较大的比例,因此整个冲击承载能大大增加.超过了氧等离子 处理者。
聚丙烯酰胺接枝碳纤强复合丝试样的冲击承裁曲线,冲击韧始基线与冲击结束基线 没有重合(a)。这是由于聚丙烯酰胺接枝层过厚所致。因为在冲击过程中不仅纤维表 层界面产生应变,而且接技层中的分子链也会产生蠕变或滑移,两者综合的结果,
复合材料的界面特性与力学性能

复合材料的界面特性与力学性能关键信息项:1、复合材料的种类及组成成分2、界面特性的具体描述及相关参数3、力学性能的测试方法与指标4、实验条件与环境设定5、数据采集与分析方式6、质量控制标准7、违约责任与争议解决方式1、引言11 本协议旨在明确复合材料的界面特性与力学性能相关的各项事宜,以确保研究、生产或应用过程中的一致性和可靠性。
2、复合材料的种类及组成成分21 详细列举所涉及的复合材料的类型,包括但不限于纤维增强复合材料、颗粒增强复合材料等。
211 明确每种复合材料的主要组成成分,如纤维的种类、颗粒的材质等。
212 给出各成分的比例范围及具体数值。
3、界面特性的具体描述及相关参数31 对复合材料界面的物理化学性质进行详细描述,包括界面的粗糙度、结合强度等。
311 确定用于表征界面特性的相关参数,如界面能、界面张力等。
312 说明获取这些界面特性参数的测试方法和仪器设备。
4、力学性能的测试方法与指标41 阐述用于评估复合材料力学性能的测试方法,如拉伸试验、弯曲试验、冲击试验等。
411 明确各项力学性能指标,如抗拉强度、屈服强度、弹性模量等。
412 规定测试的样本数量、尺寸及制备要求。
5、实验条件与环境设定51 设定实验过程中的温度、湿度等环境条件。
511 说明加载速率、试验频率等实验参数。
512 强调实验设备的校准与维护要求。
6、数据采集与分析方式61 描述数据采集的频率和精度要求。
611 规定数据处理和分析的方法,包括统计分析、曲线拟合等。
612 明确如何判断数据的有效性和可靠性。
7、质量控制标准71 制定复合材料的质量控制标准,包括原材料的质量要求、生产过程中的监控指标等。
711 说明不合格产品的处理方式和预防措施。
8、违约责任与争议解决方式81 若一方违反本协议的规定,应承担相应的违约责任,包括但不限于赔偿损失、重新履行义务等。
811 约定争议解决的方式,如协商、仲裁或诉讼,并明确适用的法律法规。
复合材料界面粘接性能的监测与分析

复合材料界面粘接性能的监测与分析复合材料在工程领域中得到广泛应用,其独特的物理性质使其成为制造飞机、汽车和结构材料的理想选择。
然而,复合材料的性能很大程度上取决于其界面粘接性能。
因此,监测和分析复合材料界面粘接性能对于确保产品质量和使用寿命具有重要意义。
为了监测复合材料界面粘接性能,一种常用的方法是通过力学试验来评估粘接强度。
拉伸、剪切和剥离试验是常见的评估技术。
在拉伸试验中,施加纵向的压力来测试界面强度。
剪切试验则通过在两个相邻表面上施加剪切力来评估界面黏结强度。
剥离试验则是通过施加拉力来测试粘接层的强度。
这些试验方法能够提供一些关于复合材料粘接性能的基本信息,但是缺乏深入的分析。
为了更好地理解界面胶粘剂的性能,还可以进行界面形态分析。
电镜技术(如扫描电镜和透射电镜)能够提供关于复合材料界面形态的详细信息。
通过观察界面微观结构,可以评估胶粘剂的分布、界面的亲和性以及粘接层的完整性。
此外,原子力显微镜也可以用来研究表面的纳米级别特征,以便更好地理解复合材料界面的性能。
除了力学试验和界面形态分析外,热分析技术也可以用于评估复合材料界面粘接性能。
差示扫描量热法(DSC)可以用来分析胶粘剂的玻璃化转变温度,这对于界面黏结的稳定性和长期使用寿命非常重要。
动态热机械分析(DMA)则可以评估界面的弹性和黏弹性特性,从而了解胶粘剂对于应力和温度变化的响应。
在监测和分析复合材料界面粘接性能的过程中,还需要考虑界面预处理和环境因素。
界面预处理包括清洗、脱脂和粗糙化等步骤,以确保胶粘剂可以牢固地附着在基材上。
此外,湿度、温度和化学环境等因素也会对界面粘接性能产生影响。
因此,在测试和分析过程中,需要保持恒定的环境条件,以获得准确可靠的结果。
总之,复合材料界面粘接性能的监测与分析对于确保产品质量和使用寿命至关重要。
通过力学试验、界面形态分析和热分析等多种方法,可以全面了解胶粘剂的性能特征和界面的质量状况。
此外,还需要考虑界面预处理和环境因素对粘接性能的影响。
复合材料-第四章复合材料界面

(1)物理因素
例1 粉末冶金制备的W丝/Ni,钨在镍中有很大的固溶度,在1100℃左右使用50小时后,钨丝发生溶解,造成钨丝直径仅为原来的60%,大大影响钨丝的增强作用,如不采取措施,将产生严重后果。为此,可采用钨丝涂覆阻挡层或在镍基合金中添加少量合金元素,如钛和铝,可以起到一定的防止钨丝溶入镍基合金的作用。
如何防止碳在镍中先溶解后析出的问题,就成为获得性能稳定的Cf / Ni的关键。
例2 碳纤维增强镍基复合材料。在800℃高温下,在界面碳先溶入镍,而后又析出,析出的碳是石墨结构,密度增大而在界面留下空隙,给镍提供了渗入碳纤维扩散聚集的位置。而且随温度的提高镍渗入量增加,在碳纤维表层产生镍环,严重损伤了碳纤维,使其强度严重下降。
4.2.1 聚合物基复合材料的界面
1.界面的形成 聚合物基复合材料界面的形成可以分成两个阶段: ①基体与增强纤维的接触与浸润过程; 增强纤维优先吸附能较多降低其表面能的组分,因此界面聚合物在结构上与聚合物基体是不同的。 ②聚合物的固化阶段。聚合物通过物理的或化学的变化而固化,形成固定的界面层。
1
2
复合材料中的界面并不是一个单纯的几何面,而是一个多层结构的过渡区域,这一区域由五个亚层组成。
界面是复合材料的特征,可将界面的机能归为以下几种效应。……P61
复合材料界面设计的原则(总的原则)
界面粘结强度要保证所受的力由基体通过界面传递给增强物,但界面粘结强度过高或过弱都会降低复合材料的强度。
复合材料的界面强度与性能评估

复合材料的界面强度与性能评估在当今的材料科学领域,复合材料因其出色的性能表现而备受关注。
复合材料由两种或两种以上具有不同物理和化学性质的材料组合而成,其性能并非各组分材料性能的简单加和,而是在很大程度上取决于各组分之间的界面相互作用。
其中,界面强度是评估复合材料性能的关键因素之一。
要理解复合材料的界面强度,首先得明白什么是复合材料的界面。
简单来说,复合材料的界面就是两种或多种材料相接触的区域。
这个区域虽然很薄,但对复合材料的性能却有着至关重要的影响。
界面就像是桥梁的连接处,如果连接不牢固,整个桥梁就容易出现问题;同理,如果复合材料的界面结合强度不够,那么在使用过程中就可能会出现分层、开裂等失效现象。
那么,如何评估复合材料的界面强度呢?这可不是一件简单的事情。
目前,常用的方法有很多种。
比如,微观力学测试方法,其中包括微柱压缩试验、纤维拔出试验等。
以纤维拔出试验为例,将纤维埋入基体中,然后施加外力将纤维拔出,通过测量拔出过程中的力和位移,就可以计算出界面的剪切强度。
这种方法能够直接反映界面的结合强度,但操作相对复杂,对实验设备和技术要求较高。
另外,还有宏观力学性能测试方法。
比如,通过拉伸、弯曲、冲击等试验,来间接评估界面强度对复合材料整体性能的影响。
虽然这种方法不能直接得到界面强度的数值,但可以从复合材料的宏观力学性能变化中推断出界面结合的好坏。
除了实验方法,数值模拟也是评估复合材料界面强度的重要手段。
通过建立复合材料的微观结构模型,利用有限元等方法模拟外力作用下界面的应力分布和变形情况,从而预测界面强度和复合材料的性能。
这种方法可以节省实验成本,并且能够对复杂的界面结构进行分析,但模型的准确性和可靠性需要大量的实验数据进行验证。
在评估复合材料界面强度的过程中,还需要考虑界面的化学性质。
界面处的化学键合、物理吸附等都会影响界面强度。
例如,在一些复合材料中,通过对纤维表面进行化学处理,引入特定的官能团,可以增强纤维与基体之间的化学键合,从而提高界面强度。
复合材料的界面状态解析了解界面的分类掌握复
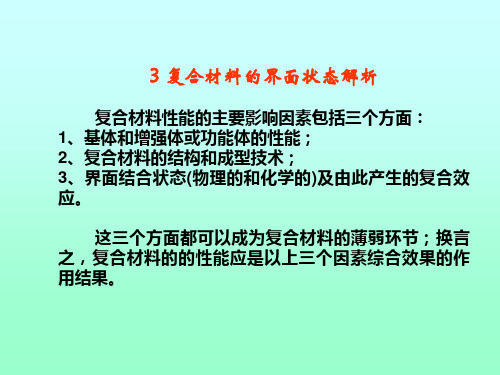
(3)表面处理的最优化技术。 (4)粉体材料在基体中的分散:
①、分散状态的评价; ②、分散技术及机理; ③、分散状态与复合材料性能。 (5)复合技术的优化及其机理。
图3.3 材料粘接的破坏形式
作业: 6、复合材料的界面层,除了在性能和结构上不同于相邻 两组分相外,还具有哪些特点; 7、简述复合材料界面的研究对象; 8、简述与表面张力有关的因素。 9、吸附按作用力的性质可分为哪几类?各有什么特点? 10、利用接触角的知识,讨论固体被液体的浸润性。 11、界面的相容性指什么?如何确定?
当固体表面的原子的原子价被相邻的原子所饱和, 表面分子与吸附物之间的作用力是分子间引力(范德华 力)。
特点:
1)、无选择性,吸附量相差较大;
2)、吸附可呈单分子层或多分子层;
3)、物理吸附、解吸速度较快,易平衡。
一般在低温下进行的吸附是物理吸附。
3.3.2.2 化学吸附
当固体表面的原子的原子价被相邻的原子所饱和,
根据物质的聚集态,可以得到五种类型的界面,即气-液 (g-l)、气-固(g-s)、液-液(l-l)、液-固(l-s)、固-固 (s-s)界面。
通常的研究中,习惯于把气-液(g-l) 、气-固(g-s) 界面分别称为液相表面、固相表面。
注意: 对于复合材料来说,界面并非是一个理想的几何面。
实验证明: 复合材料中相与相之间的两相交接区是一个具有相当厚
增强体 F
表面处理技术
增强体
F 表面 F/I 界面
表面处理物质层
I 表面 I 结构
增强体
F/I 界面
表面处理物质层
复合技术
基体
I/M 界面
基体 M
增强体 基体
F/M 界面
纤维树脂基复合材料微观界面性能表征方法的进展

纤维树脂基复合材料微观界面性能表征方法的进展刘政;翟哲;刘东杰;冯拉俊;刘赟姿【摘要】纤维树脂基复合材料中界面微观结构和性质对材料的宏观性能起着关键性作用。
为了能够准确地测试纤维树脂间的界面粘结力,表征纤维与树脂之间界面剪切应力传递效率,人们一直试图找到一种方法能够真实全面反映界面性能,以及纤维断裂、界面脱粘、树脂横向断裂等因素对界面性能的影响。
为此作者对现有微观界面表征方法进行介绍与分析,包括:微珠试验、单纤维拉出试验、压入试验、单纤维断裂试验、激光拉曼(或荧光)色谱法、光弹分析法,全面剖析它们的适用范围。
%The property of a fiber composite depends crucially upon the interfacial micro-structure and properties be-tween the fiber and polymer matrix .To accurately characterize the interfacial adhesion ,and interfacial shear stress transfer efficiency.Many attempts were dedicated to find a method to clarify the interfacial properties ,and the effects of the fiber break,the interfacial debonding and matrix crack on the interfacial properties .Here the authors introduced and analyzed cur-rent approaches ,and tried to find their limits .【期刊名称】《纤维复合材料》【年(卷),期】2014(000)002【总页数】5页(P36-40)【关键词】微珠试验;拉出试验;压入试验;单纤维断裂试验;拉曼法;光弹试验;微观界面表征方法【作者】刘政;翟哲;刘东杰;冯拉俊;刘赟姿【作者单位】西安理工大学,材料科学与工程学院,西安710048;西安理工大学,材料科学与工程学院,西安710048;西安理工大学,材料科学与工程学院,西安710048;西安理工大学,材料科学与工程学院,西安710048;西安理工大学,材料科学与工程学院,西安710048【正文语种】中文纤维复合材料作为先进材料,质量轻,强度高等特点使其在航空、航天、船舶、汽车等工程领域应用越来越发挥其重要性。
复合材料界面分析技术

复合材料界面分析技术简介复合材料是由两种或多种不同组分组成的新材料,其界面是影响复合材料性能的关键因素之一。
复合材料界面分析技术是一种研究复合材料界面特性和相互作用的方法,该技术可以帮助科学家和工程师深入了解复合材料界面的结构、性质和失效机理,从而改进复合材料设计和应用。
表面分析技术1.扫描电子显微镜(SEM)–SEM是一种常见的界面分析技术,通过扫描样品表面的电子束,可以获取高分辨率的表面形貌信息,以及界面的形貌特征、粗糙度和孔隙度等参数。
–SEM还可以结合能谱分析技术(EDS)进行元素分析,从而了解不同相的分布情况以及界面处元素的交互作用。
2.X射线光电子能谱(XPS)–XPS是一种表面分析技术,可以获得化学计量比和能态信息,用于表征复合材料界面的化学成分和界面能态特性。
–XPS可以通过改变束流能量和角度,分析不同深度处的界面化学成分。
3.傅里叶变换红外光谱(FTIR)–FTIR可以用于分析复合材料界面的化学成分和功能团,从而研究界面的相互作用机制和性能调控方式。
–FTIR还可以通过差示扫描量热仪(DSC)等技术,研究界面反应的热性质和动力学。
界面力学性能测试技术1.力学性能测试–拉伸试验、弯曲试验等是常见的检测界面力学性能(如粘结强度、界面剪切强度等)的方法,可以评估复合材料界面的耐久性和力学强度。
2.微纳力学测试技术–原子力显微镜(AFM)可以测量复合材料界面的力-位移曲线,用于评估界面的强度和粘附力。
–AFM还可以进行纳米压痕测试,研究复合材料界面的硬度、弹性模量等力学性能。
3.界面失效分析–界面失效是复合材料在使用过程中的常见问题,界面失效分析技术可以帮助确定界面破坏机理和失效形式,从而指导提升界面的耐久性和可靠性。
–最常用的界面失效分析技术包括断口分析、断裂力学分析和失效模式分析等。
数值模拟方法复合材料界面分析技术不仅包括实验方法,还有数值模拟方法。
通过建立界面模型和适当的界面模型参数,可以对复合材料界面的结构和性能进行预测和优化。
复合材料材料的界面理论 ppt课件

ppt课件
6
3.3.2增强材料的表面处理
1.碳纤维的表面处理
表面处理的作用:使复合材料不仅具有良好的界面粘接力、 层间剪切强度,而且其界面的抗水性、断裂韧性及尺寸稳 定性均有明显的改进。此外,通过碳纤维表面改性处理, 还可制得具有某种特殊功能的复合材料。
1)氧化法
(1)气相法(或干法):以空气、氧气、臭氧等氧化剂,采用 等离子表面氧化或催化氧化法。
基体表面上的官能团与纤维表面上的官能团起化学反应, 因此在基体与纤维间产生化学键的结合,形成界面。如:偶 联剂的应用而得到证实,故也称“偶联”理论。
(2)液相法(或湿法):有硝酸、次氯酸钠加硫酸、重铬 酸钾加硫酸、高锰酸钾加硝酸钠加硫酸氧化剂及电解氧化 法等。
ppt课件
7
2)涂层法
(1)有机聚合物涂层:树脂涂层、接枝涂层、电 沉积与电聚合等。
(2)无机聚合物涂层:经有机聚合物涂层后碳化、 碳氢化合物化学气相沉积、碳化硅或氧化铁涂层、 生长晶须涂层等。
网状结构是指在复合材料组分中,一相是三维连续,另 一相为二维连续的或者两相都是三维连续的。
ppt课件
21
2.层状结构
两组分均为二维连续相。所形成的材料在垂直于增强相和 平行于增强相的方向上,其力学等性质是不同的,特别是层 间剪切强度低。
3.单向结构
纤维单向增强及筒状结构的复合材料。
4.分散状结构
(1) 浸润剂会影响复合材料性能(妨碍了纤维与基 体材料的粘接),用前去除浸润剂,
(2)采用偶联剂对纤维表面进行处理。偶联剂的分 子结构中,一般都带有两种性质不同的极性基团, 一种基团与玻璃纤维结合,另一种基团能与基体树 脂结合,从而使纤维和基体这两类性质差异很大的 材料牢固地连接起来。