剪切试验
材料的剪切性能测试与分析

材料的剪切性能测试与分析材料的剪切性能是指材料在受到剪切力作用下的变形和破坏行为。
剪切性能的测试和分析对于材料的设计、生产和应用具有重要意义。
本文将介绍材料剪切性能测试的常用方法和分析过程,以帮助读者了解和应用该测试。
一、引言材料的剪切性能是材料力学性能的重要指标之一,对于了解材料的强度、韧性和可加工性具有重要意义。
因此,对于材料的剪切性能进行测试和分析,可以为材料研究和工程应用提供重要的数据和参考依据。
二、常用的剪切性能测试方法1. 剪切试验剪切试验是通过施加剪切力来测试材料的剪切性能。
在剪切试验中,常用的测试方法包括剪切强度、剪切模量和剪切变形等指标。
通过测量剪切载荷和变形,可以得到材料的剪切应力-应变曲线,进而评估材料的剪切性能。
2. 剪切切割试验剪切切割试验是通过刀具对材料进行切割来测试材料的剪切性能。
在剪切切割试验中,可以测量切割力和切割速度等指标。
通过改变刀具形状、切割速度和材料厚度等参数,可以评估材料的切割性能。
3. 剪切剥离试验剪切剥离试验是通过施加剪切力来测试材料的粘接性能。
在剪切剥离试验中,常用的测试方法包括剪切剥离强度和剪切剥离能等指标。
通过测量剪切剥离力和剥离长度,可以评估材料的粘接剪切性能。
三、剪切性能测试的分析过程剪切性能测试的分析过程主要包括数据处理和结果分析两个环节。
1. 数据处理在剪切性能测试中,需要对测试数据进行处理,以得到准确可靠的评估结果。
数据处理包括计算剪切应力、剪切应变、剪切模量等指标,以及绘制剪切应力-应变曲线等图表。
此外,还需要进行统计学处理,以消除测试误差对评估结果的影响。
2. 结果分析剪切性能测试的结果分析是对测试数据进行解读和评估,以获得对材料性能的认识和理解。
通过分析剪切应力-应变曲线的形状和特征,可以判断材料的强度、韧性和可加工性等性能。
此外,还可以与其他材料进行对比分析,以评估材料的优劣和适用范围。
四、剪切性能测试的应用剪切性能测试在材料工程和应用领域有着广泛的应用。
土的剪切试验和强度指标

工程常识之土的剪切试验和强度指标1、直接剪切试验在直剪仪中分别施加不同竖向压力,然后分别对施加水平剪切力进行剪切,求得破坏时的剪应力τ,根据库仑定律确定土的抗剪强度参数:内摩擦角ψ和黏聚力c。
试验方法分三种:(1)快剪Q(Quick shear):在试样上施加垂直压力后,立即加水平剪切力。
在整个试验中,不允许试样的原始含水率有所改变(试样两端敷以隔水纸),即在试验过程中孔隙水压力保持不变(3~5min内剪坏)。
对透水性强的土(渗透系数大于10-6cm/s)不适用。
(2)固结快剪CQ(Consolidation Quick shear):在垂直压力下土样完全排水固结稳定后,以很快速度施加水平剪力。
在剪切过程中不允许排水(规定在3~5min内剪坏)。
得到的强度指标适用于总应力法。
(3)慢剪S(Slow shear):在加垂直荷重后,使其充分排水(试样两端敷以滤纸),在土样达到完全固结时,再加水平剪力;每加一次水平剪力后,均需经过一段时间,待土样因剪切引起的孔隙水压力完全消失后,再继续加下一次水平剪力。
得到的强度指标适用于有效应力法。
上述三种试验方法的受力条件不同,所得抗剪强度值也不同。
因此,必须根据土所处的实际应力情况来选择试验方法。
2、三轴剪切试验在三轴仪中,分别在不同的恒定周围压力(即小主应力)下,施加轴向压力(即产生主应力差-),进行剪切直至破坏,然后根据摩尔-库伦理论确定土的抗剪强度参数:内摩擦角ψ和黏聚力c。
试验方法分三种:(1)不固结不排水剪UU(Unconsolidation Undrained):试样在施加周围压力和随后施加轴向压力力直至剪坏的整个试验过程中都不允许排水,这样从开始加压直至试样剪坏,土中的含水量始终保持不变,孔隙水压力也不可能消散,可以测得总应力抗剪强度指标c u,φu。
(2)固结不排水剪CU(Consolidation Undrained):试样在施加周围压力时,允许试样充分排水,待固结稳定后,再在不排水的条件下施加轴向压力,直至试样剪切破坏,同时在受剪过程中测定土体的孔隙水压力,可以测得总应力抗剪强度指标c cu,φcu和有效应力抗剪强度指标c’,φ’。
金属剪切试验标准

金属剪切试验标准一、目的本标准规定了金属材料剪切试验的方法、试验原理、试验设备、试样制备、试验程序、数据分析和试验报告。
本标准适用于金属材料在室温或高温条件下的剪切强度和变形行为的测试。
二、术语和定义1.剪切强度:材料在剪切应力作用下,单位面积上所能承受的最大剪切力。
2.剪切变形:材料在剪切应力作用下,发生的剪切变形量。
三、试验原理剪切试验是通过在试样上施加剪切应力,使试样在剪切面上产生剪切变形,从而测定材料的剪切强度和变形行为。
剪切试验一般分为单向剪切和双向剪切两种类型。
四、试验设备1.试验机:应具有足够的刚性和精度,能够施加恒定的载荷并测量试样的变形。
2.剪切装置:包括上下压板、试样夹持器和剪切刀具等,应确保试样在试验过程中不会发生移动或偏移。
3.测量仪器:如千分尺、量具等,用于测量试样的尺寸和变形。
4.环境控制设备:如加热炉、冷却水浴等,用于控制试验温度。
五、试样制备1.试样尺寸:试样应具有足够的尺寸,以避免在试验过程中发生弯曲或失稳。
一般情况下,试样的宽度应至少是厚度的两倍。
2.试样形状:试样一般采用矩形或圆形,表面应平整光滑,无划痕、裂纹等缺陷。
3.试样处理:如热处理、表面处理等,应根据材料性质和试验要求进行。
六、试验程序1.安装试样:将试样放置在剪切装置中,确保上下压板与试样紧密接触,无间隙。
2.加载:根据试验要求,逐渐增加载荷至指定值,并保持稳定。
3.测量变形:在载荷作用下,观察试样的变形情况,使用测量仪器记录变形量。
4.卸载:卸载载荷后,观察试样的残余变形。
5.重复试验:为保证试验结果的可靠性和可比性,应进行多次试验,取平均值。
七、数据分析1.绘制应力-应变曲线:将载荷与变形量绘制成曲线,从而得到材料的应力-应变曲线。
2.计算剪切强度:从应力-应变曲线上读取剪切应力,并计算出剪切强度。
剪切强度一般取最大剪切应力值。
3.分析变形行为:观察试样在载荷作用下的变形过程,分析材料的变形机制和行为。
简述直接剪切试验的优缺点
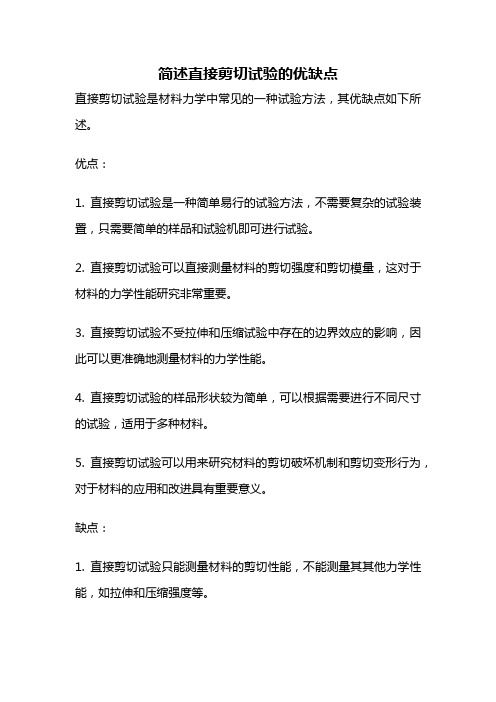
简述直接剪切试验的优缺点
直接剪切试验是材料力学中常见的一种试验方法,其优缺点如下所述。
优点:
1. 直接剪切试验是一种简单易行的试验方法,不需要复杂的试验装置,只需要简单的样品和试验机即可进行试验。
2. 直接剪切试验可以直接测量材料的剪切强度和剪切模量,这对于材料的力学性能研究非常重要。
3. 直接剪切试验不受拉伸和压缩试验中存在的边界效应的影响,因此可以更准确地测量材料的力学性能。
4. 直接剪切试验的样品形状较为简单,可以根据需要进行不同尺寸的试验,适用于多种材料。
5. 直接剪切试验可以用来研究材料的剪切破坏机制和剪切变形行为,对于材料的应用和改进具有重要意义。
缺点:
1. 直接剪切试验只能测量材料的剪切性能,不能测量其其他力学性能,如拉伸和压缩强度等。
2. 直接剪切试验中样品的几何形状和试验条件对试验结果有很大影响,因此需要进行精确的试验设计和数据处理。
3. 直接剪切试验中样品的边缘效应会对试验结果产生影响,特别是在小尺寸样品试验中。
4. 直接剪切试验需要进行多次试验以获得可靠的结果,因此需要较长的试验时间。
5. 直接剪切试验中样品的制备和夹持需要一定的技术和经验,如果操作不当会影响试验结果。
直接剪切试验作为一种简单易行的试验方法,可以用来测量材料的剪切性能,并对材料的力学性能研究和应用具有重要意义。
但是,其也存在一些缺点需要注意,例如需要进行多次试验、样品制备和夹持需要一定的技术和经验等。
因此,在进行直接剪切试验时,需要认真设计试验方案,精确处理数据,以获得准确可靠的试验结果。
剪切试验实验报告
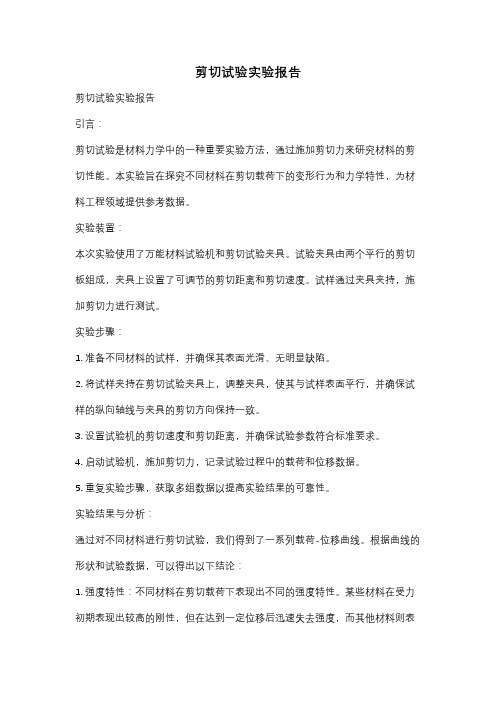
剪切试验实验报告剪切试验实验报告引言:剪切试验是材料力学中的一种重要实验方法,通过施加剪切力来研究材料的剪切性能。
本实验旨在探究不同材料在剪切载荷下的变形行为和力学特性,为材料工程领域提供参考数据。
实验装置:本次实验使用了万能材料试验机和剪切试验夹具。
试验夹具由两个平行的剪切板组成,夹具上设置了可调节的剪切距离和剪切速度。
试样通过夹具夹持,施加剪切力进行测试。
实验步骤:1. 准备不同材料的试样,并确保其表面光滑、无明显缺陷。
2. 将试样夹持在剪切试验夹具上,调整夹具,使其与试样表面平行,并确保试样的纵向轴线与夹具的剪切方向保持一致。
3. 设置试验机的剪切速度和剪切距离,并确保试验参数符合标准要求。
4. 启动试验机,施加剪切力,记录试验过程中的载荷和位移数据。
5. 重复实验步骤,获取多组数据以提高实验结果的可靠性。
实验结果与分析:通过对不同材料进行剪切试验,我们得到了一系列载荷-位移曲线。
根据曲线的形状和试验数据,可以得出以下结论:1. 强度特性:不同材料在剪切载荷下表现出不同的强度特性。
某些材料在受力初期表现出较高的刚性,但在达到一定位移后迅速失去强度,而其他材料则表现出较为均匀的强度分布。
2. 变形行为:剪切试验中,材料的变形行为也是一个重要的研究对象。
某些材料在受力过程中呈现出明显的塑性变形,而其他材料则表现出较为脆性的断裂特征。
这种差异主要取决于材料的晶体结构和内部组织。
3. 断裂特征:根据试验结果,我们可以观察到不同材料的断裂特征也存在差异。
一些材料在剪切载荷下呈现出光滑的断口,而其他材料则表现出粗糙和多孔的断口。
这些特征可以反映材料的韧性和断裂韧度。
结论:通过剪切试验,我们可以得到不同材料在剪切载荷下的力学特性和变形行为。
这些数据对于材料工程的设计和应用具有重要意义。
在今后的研究中,我们可以进一步探索不同材料的剪切性能和断裂机制,以提高材料的力学性能和可靠性。
附录:本次实验所使用的材料包括金属、塑料和复合材料等。
面内剪切试验标准

面内剪切试验标准一、试验目的面内剪切试验的目的是测定材料在剪切应力作用下的行为,了解材料的剪切强度、剪切模量、屈服点等力学性能指标,为工程应用提供可靠的依据。
二、试验设备进行面内剪切试验需要用到以下设备:1. 剪切试验机:用于施加剪切力,应具备高精度测力和测位移系统。
2. 试样夹具:用于固定试样,保证试样在试验过程中不会发生移动或偏转。
3. 加载系统:用于施加剪切力,可以是砝码、液压或气压系统等。
4. 数据采集系统:用于采集试验过程中的力和位移数据。
三、试样制备试样制备是面内剪切试验的重要环节,其步骤如下:1. 根据试验要求选择合适的材料和尺寸,制作试样。
2. 对试样进行加工和打磨,保证试样的表面质量和尺寸精度。
3. 在试样的中心位置进行标识,以便后续的测量和数据处理。
四、试验步骤1. 将试样安装到夹具中,确保试样固定牢固。
2. 调整试验机的初始位置,使剪切力处于初始状态。
3. 以恒定的速度施加剪切力,直至试样断裂或屈服。
4. 在试验过程中,记录力和位移数据,绘制应力-应变曲线。
5. 对试验结果进行分析和处理,得出材料的剪切强度、剪切模量等性能指标。
五、试验数据处理在面内剪切试验中,需要对采集到的数据进行处理和分析,以得出材料的力学性能指标。
数据处理的具体步骤如下:1. 对采集到的力和位移数据进行整理和筛选,排除异常数据。
2. 根据试验目的和要求,选择合适的处理方法,如弹性分析、非线性分析等。
六、试验结果分析1. 绘制应力-应变曲线,分析材料在剪切力作用下的应力响应特性。
2. 根据应力-应变曲线,确定材料的剪切强度、屈服点和剪切模量等性能指标。
3. 将试验结果与理论模型进行对比,验证模型的正确性和适用性。
4. 分析材料的剪切性能与微观结构、温度、应变率等参数的关系,为材料设计和优化提供依据。
七、试验报告编写在编写面内剪切试验报告时,应包括以下内容:1. 试验目的和背景:简要说明试验的意图和相关背景。
剪切实验报告

剪切实验报告剪切实验报告引言:剪切实验是一种常见的力学实验,通过施加剪切力来研究材料的变形和破坏行为。
本次实验旨在探究剪切力对不同材料的影响,了解材料的剪切性能以及其在工程应用中的重要性。
材料与方法:本次实验选取了三种不同材料进行剪切实验,分别是金属材料、塑料材料和纸质材料。
实验所需的仪器设备有剪切试验机、标尺、计时器等。
实验过程:首先,将待测材料切割成一定大小的试样,确保试样的尺寸一致。
然后,将试样夹持在剪切试验机上,调整机器的参数,使其适应不同材料的特性。
接下来,施加剪切力并记录下试样的变形情况和剪切力的大小。
每种材料进行三次实验,取平均值作为最终结果。
结果与讨论:在实验中,我们观察到不同材料在受到剪切力作用下表现出不同的变形行为。
金属材料在受到剪切力后,往往呈现出塑性变形,即试样会发生塑性流动,但不会破裂。
这是由于金属材料的结构特性决定的,金属内部的晶粒可以滑动和变形,从而使整个材料发生塑性变形。
塑料材料则会发生较大的变形,而且在受到剪切力后往往会破裂。
这是因为塑料材料的分子结构较为松散,容易发生断裂。
纸质材料在受到剪切力后也会发生较大的变形,但相对于塑料材料,纸质材料的断裂性较差,不容易破裂。
通过对实验结果的分析,我们可以得出以下结论:1. 不同材料在受到剪切力后表现出不同的变形行为,这是由于材料的结构和特性不同所致。
2. 剪切实验可以用来评估材料的剪切性能,为工程应用提供参考依据。
3. 在工程设计中,需要根据材料的剪切性能选择合适的材料,以确保结构的稳定性和安全性。
结论:剪切实验是一种重要的力学实验,可以帮助我们了解材料的剪切性能和变形行为。
通过实验,我们可以发现不同材料在受到剪切力后的不同表现,这对于工程应用具有重要意义。
因此,在工程设计中,我们应该根据材料的剪切性能选择合适的材料,以确保结构的稳定性和安全性。
同时,我们也需要进一步研究和探索材料的剪切性能,以满足不同工程领域的需求。
剪切试验原理

剪切试验原理
剪切试验是一种常用的力学试验方法,用于测定材料在剪切力作用下的变形和破坏性能。
其原理基于剪切力引起的材料内部层间滑动和相对位移。
在剪切试验中,一块材料样品被固定在剪切试验机上,两个剪切载荷平行的力悬挂在样品两侧。
施加的剪切载荷随时间逐渐增加,直到样品发生破坏或达到一定的变形。
通过测量施加在样品上的剪切力和样品的变形,可以得到剪切应力和剪切应变的关系。
剪切试验的基本原理是,当施加的剪切力足够小时,材料内部的分子间力支持着剪切应力和剪切应变的线性关系。
这被称为线性弹性区域。
当剪切力增加到一定程度时,材料开始发生塑性变形,此时剪切应力和剪切应变的关系变得非线性。
最终,当剪切力达到一定大小时,材料会破坏,形成断裂面。
通过剪切试验可以获取一些重要的材料力学参数,例如剪切强度、剪切模量、屈服强度和断裂韧性等。
这些参数对于材料的设计和评估具有重要意义。
需要注意的是,剪切试验的结果受到多种因素的影响,如样品的几何形状、载荷速率和温度等。
因此,在进行剪切试验时,需要根据具体情况选择合适的试验条件,并进行数据分析和处理,以得到准确可靠的试验结果。
铝合金剪切试验方法
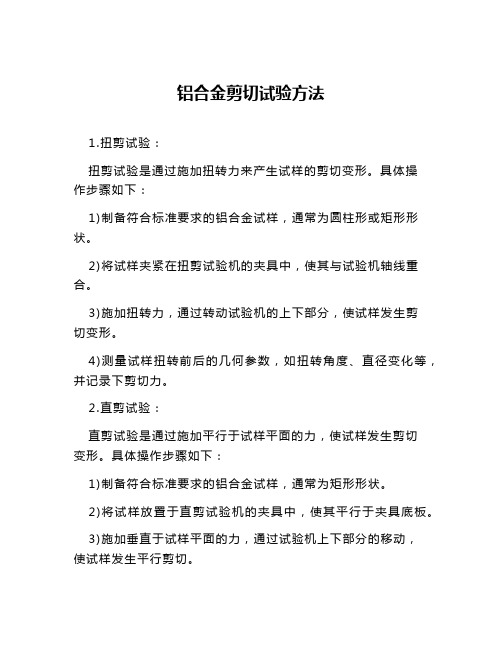
铝合金剪切试验方法
1.扭剪试验:
扭剪试验是通过施加扭转力来产生试样的剪切变形。
具体操
作步骤如下:
1)制备符合标准要求的铝合金试样,通常为圆柱形或矩形形状。
2)将试样夹紧在扭剪试验机的夹具中,使其与试验机轴线重合。
3)施加扭转力,通过转动试验机的上下部分,使试样发生剪
切变形。
4)测量试样扭转前后的几何参数,如扭转角度、直径变化等,并记录下剪切力。
2.直剪试验:
直剪试验是通过施加平行于试样平面的力,使试样发生剪切
变形。
具体操作步骤如下:
1)制备符合标准要求的铝合金试样,通常为矩形形状。
2)将试样放置于直剪试验机的夹具中,使其平行于夹具底板。
3)施加垂直于试样平面的力,通过试验机上下部分的移动,
使试样发生平行剪切。
4)测量试样剪切前后的几何参数,如试样长度、试样宽度等,并记录下剪切力。
在进行铝合金剪切试验时,需要注意以下几点:
1)试样的准备应符合相应的标准要求,以保证试验结果的准
确性和可比性。
2)在进行试验前,应校准试验仪器,确保测量结果的准确性。
3)试样在夹具中的位置和位置应保持一致,以排除位置对试
验结果的影响。
4)试验过程中应控制施加力的速度和大小,以保证试验的稳
定性和可重复性。
5)根据试验要求,可在试验前或试验过程中对试样进行预处理,如热处理、冷处理等,以研究不同处理条件下的铝合金剪
切性能。
以上是铝合金剪切试验的常用方法和注意事项。
通过这些试
验方法,可以评估铝合金的剪切性能和剪切强度,为相关工程
和应用提供参考和依据。
直接剪切试验

直接剪切试验(快剪试验)1试验设备(1)应变控制式直剪仪:由剪切盒、垂直加压设备、剪切传动装置、量力环等组成。
(2)环刀:内径61.8mm,高度20mm。
(3)量力环:率定系数C=6 N/0.01mm。
2 试验步骤(1)对准剪切容器上下盒,插入固定销,在下盒内放硬塑料薄膜,将带有试样的环刀刃口向上,对准剪切盒口,在试样上放硬塑料薄膜,将试样小心地推入剪切盒内。
(2)移动传动装置,使上盒前端钢珠刚好与量力环接触,依次放上传压板、加压框架,将量力环百分表调至零位。
(3)施加各级垂直压力(100,200,400kPa,对应砝码质量2.55,5.1,10.2kg),拔去固定销,以0.8mm/min的剪切速度(4 r/min)进行剪切至试验结束,使试样在3-5min内剪损。
试样每产生剪切位移0.4mm,测记测力计读数,直至测力计读数出现峰值,继续剪切至剪切位移为4mm时停机,记下破坏值;当剪切过程中测力计读数无峰值时,剪切至剪切位移为6mm时停机。
(4)剪切结束,退去剪切力和垂直压力,移动加压框架,取出试样。
3 数据处理(1)直剪试验记录(2)剪应力按下式计算:τ—试样所受的剪应力(kPa);C—量力环率定系数(N/0.01mm);R—测力计量表读数(0.01mm);A0—试样面积(cm2)。
(2)以剪应力为纵坐标,剪切位移为横坐标,绘制剪应力(τ)与剪切位移(Δl)关系曲线,取曲线上剪应力的峰值为抗剪强度,无峰值时,取剪切位移4 mm所对应的剪应力为抗剪强度。
(3) 以抗剪强度为纵坐标,垂直压力为横坐标,绘制抗剪强度与垂直压力关系曲线,直线的倾角为摩擦角,直线在纵坐标上的截距为粘聚力。
剪切试验实验报告
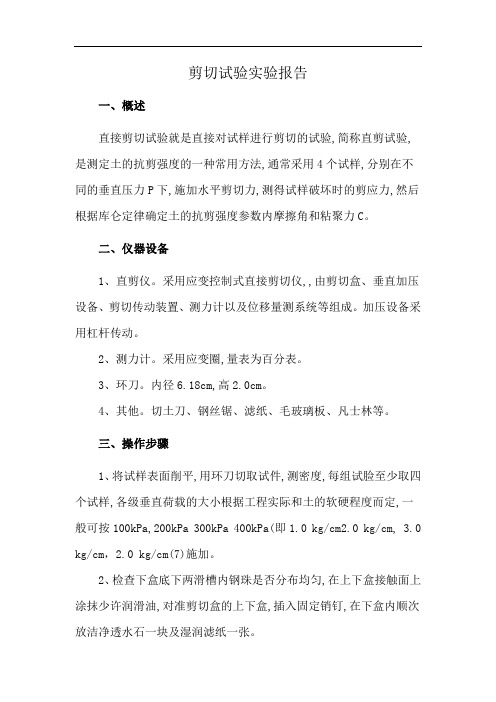
剪切试验实验报告
一、概述
直接剪切试验就是直接对试样进行剪切的试验,简称直剪试验,
是测定土的抗剪强度的一种常用方法,通常采用4个试样,分别在不
同的垂直压力P下,施加水平剪切力,测得试样破坏时的剪应力,然后根据库仑定律确定土的抗剪强度参数内摩擦角和粘聚力C。
二、仪器设备
1、直剪仪。
采用应变控制式直接剪切仪,,由剪切盒、垂直加压设备、剪切传动装置、测力计以及位移量测系统等组成。
加压设备采用杠杆传动。
2、测力计。
采用应变圈,量表为百分表。
3、环刀。
内径6.18cm,高2.0cm。
4、其他。
切土刀、钢丝锯、滤纸、毛玻璃板、凡士林等。
三、操作步骤
1、将试样表面削平,用环刀切取试件,测密度,每组试脸至少取四个试样,各级垂直荷载的大小根据工程实际和土的软硬程度而定,一
般可按100kPa,200kPa 300kPa 400kPa(即1.0 kg/cm2.0 kg/cm, 3.0 kg/cm,2.0 kg/cm(7)施加。
2、检查下盒底下两滑槽内钢珠是否分布均匀,在上下盒接触面上涂抹少许润滑油,对准剪切盒的上下盒,插入固定销钉,在下盒内顺次放洁净透水石一块及湿润滤纸一张。
6.5 剪切试验

层间剪切强度
在层间材料中沿层间单位面积上能承受的最大剪切 负荷
6
断纹剪切强度
沿垂直于板面的方向剪断的剪切强度。 沿垂直于板面的方向剪断的剪切强度。
屈服剪切强度
在剪切负荷—变形曲线上, 在剪切负荷 变形曲线上,负荷不随变形增加的 变形曲线上 第一个点的剪切应力。 第一个点的剪切应力。
剪切弹性模量
指材料在比例极限内剪应力与剪应变之比。 指材料在比例极限内剪应力与剪应变之比。
15
环境温度
随温度的升高,剪切强度明显下降,且热塑性材料较热 随温度的升高,剪切强度明显下降, 固性材料的影响更为明显
试样加工方法
试样加工方法不同对剪切强度也有影响, 试样加工方法不同对剪切强度也有影响,因此应按 规定的标准方法和条件准备试样
不同受力方式
单面压缩剪切和单面拉伸剪切,结果的极限误差较大 单面压缩剪切和单面拉伸剪切,结果的极限误差较大; 穿孔式纯双面剪切极限误差较小。 穿孔式纯双面剪切极限误差较小。
F F 试样
4
剪切力F作用于矩形试样的面积 , 剪切力 作用于矩形试样的面积A,产生位 作用于矩形试样的面积 移为△ , 移为△L,则剪切应力与应变的关系表示如 下
τ =FA
ε = ∆L d
5
概念
剪切应力
试验过程中任一时刻试样单位面积上所承受的的剪 切负荷。 切负荷。
剪切强度
试样在剪切力作用下破坏时单位面积上所能承受 的负荷值。 的负荷值。
20
橡胶的剪切试验
引用橡胶剪切性能试验标准GB/T1700—2001。 。 引用橡胶剪切性能试验标准
在橡胶中加入硫磺和其他配合剂, 在橡胶中加入硫磺和其他配合剂,经硫化制造成 的一种硬质材料, 的一种硬质材料,由于大量硫化剂的作用使它具 有较高的硬度称为硬质橡胶 硬质橡胶。 有较高的硬度称为硬质橡胶。
直剪切实验报告(3篇)

第1篇一、实验目的本次实验旨在通过直剪切试验,测定土体的抗剪强度指标,包括内摩擦角和粘聚力,为土压力、地基承载力和土坡稳定等工程计算提供基础数据。
二、实验原理土体在受到外力作用时,其内部会产生剪切应力,当剪切应力达到一定值时,土体将发生剪切破坏。
直剪切试验通过施加水平剪切力,使土体发生剪切变形,直至破坏,从而测定土体的抗剪强度。
三、实验仪器1. 直剪仪:用于施加剪切力,测量剪切位移。
2. 垂直加载设备:用于施加垂直压力。
3. 环刀:用于取样。
4. 天平:用于称量土样。
5. 量角器:用于测量内摩擦角。
四、实验步骤1. 样品制备:从原状土样中取出一定数量的土样,将其风干、筛分,并按要求的干密度进行制备。
2. 样品安装:将制备好的土样装入直剪仪的剪切盒中,并调整垂直压力。
3. 施加水平剪切力:启动直剪仪,逐渐施加水平剪切力,直至土样破坏。
4. 记录数据:记录剪切过程中施加的水平剪切力和对应的剪切位移。
5. 计算内摩擦角和粘聚力:根据实验数据,利用相关公式计算内摩擦角和粘聚力。
五、实验结果与分析1. 内摩擦角:本次实验测得土体的内摩擦角为26.9°,表明该土体具有一定的抗剪强度。
2. 粘聚力:本次实验测得土体的粘聚力为42.9 kPa,表明该土体具有一定的内聚力。
3. 结果分析:本次实验结果与理论计算值基本吻合,说明直剪切试验能够有效地测定土体的抗剪强度指标。
六、实验总结1. 直剪切试验是一种常用的土体抗剪强度测试方法,能够有效地测定土体的内摩擦角和粘聚力。
2. 实验过程中应注意以下几点:- 确保土样制备质量,避免因土样制备不当而影响实验结果。
- 正确操作实验仪器,确保实验数据的准确性。
- 仔细记录实验数据,为后续分析提供依据。
七、实验建议1. 增加实验次数,以提高实验结果的可靠性。
2. 研究不同土体的抗剪强度特性,为工程实践提供更全面的数据支持。
3. 探索直剪切试验在其他领域的应用,如岩土工程、地质勘探等。
剪切实验报告
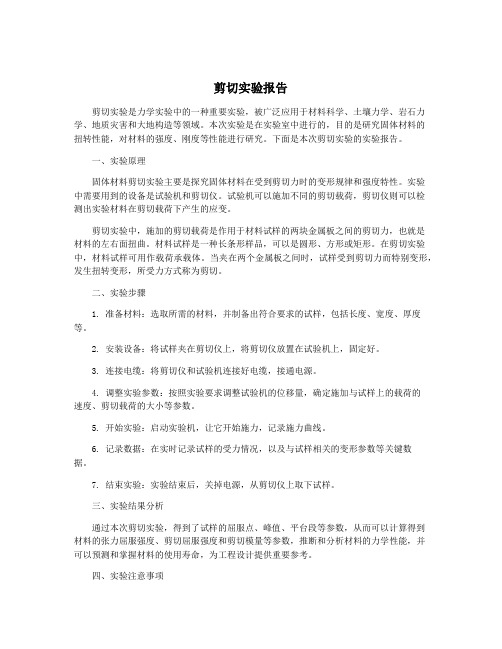
剪切实验报告剪切实验是力学实验中的一种重要实验,被广泛应用于材料科学、土壤力学、岩石力学、地质灾害和大地构造等领域。
本次实验是在实验室中进行的,目的是研究固体材料的扭转性能,对材料的强度、刚度等性能进行研究。
下面是本次剪切实验的实验报告。
一、实验原理固体材料剪切实验主要是探究固体材料在受到剪切力时的变形规律和强度特性。
实验中需要用到的设备是试验机和剪切仪。
试验机可以施加不同的剪切载荷,剪切仪则可以检测出实验材料在剪切载荷下产生的应变。
剪切实验中,施加的剪切载荷是作用于材料试样的两块金属板之间的剪切力,也就是材料的左右面扭曲。
材料试样是一种长条形样品,可以是圆形、方形或矩形。
在剪切实验中,材料试样可用作载荷承载体。
当夹在两个金属板之间时,试样受到剪切力而特别变形,发生扭转变形,所受力方式称为剪切。
二、实验步骤1. 准备材料:选取所需的材料,并制备出符合要求的试样,包括长度、宽度、厚度等。
2. 安装设备:将试样夹在剪切仪上,将剪切仪放置在试验机上,固定好。
3. 连接电缆:将剪切仪和试验机连接好电缆,接通电源。
4. 调整实验参数:按照实验要求调整试验机的位移量,确定施加与试样上的载荷的速度、剪切载荷的大小等参数。
5. 开始实验:启动实验机,让它开始施力,记录施力曲线。
6. 记录数据:在实时记录试样的受力情况,以及与试样相关的变形参数等关键数据。
7. 结束实验:实验结束后,关掉电源,从剪切仪上取下试样。
三、实验结果分析通过本次剪切实验,得到了试样的屈服点、峰值、平台段等参数,从而可以计算得到材料的张力屈服强度、剪切屈服强度和剪切模量等参数,推断和分析材料的力学性能,并可以预测和掌握材料的使用寿命,为工程设计提供重要参考。
四、实验注意事项1. 操作试验机设备时应注意安全,遵守实验室的规定。
2. 在试验准备期间,必须要了解试样的材料性质以及实验条件,使用必要的仪器进行试验,并记录下来。
3. 在试验过程中需要小心施力,不得过度施力。
土的剪切试验和强度指标

土的剪切试验和强度指标土的剪切试验是研究土体剪切特性和强度的重要方法之一、它通过对土体进行剪切加载,测量土体在不同剪切应力和剪切变形条件下的剪切变形、荷载变化等参数来评判土的剪切性能和强度参数,为土力学研究提供了重要的实验数据。
土的剪切试验及其强度指标对土的工程性质评价、土工设计和土力学研究等领域都具有重要意义。
土体剪切试验包括直剪试验、剪切扭转试验、三轴剪切试验等多种试验方法,根据试验装置、加载方式和试验目的等不同,选择不同的试验方法。
以下是直剪试验的介绍。
直剪试验是一种简单直观的试验方法,用于测定孤立土体剪切强度和土壤的内摩擦角等参数。
试验时,将土样制备成典型的长方形梯形形状,上下两部分以给定的剪切速率进行相对位移,通过测量上下两部分的位移和所加荷载,计算剪切变形、剪切应力、剪切荷载等参数。
同时,利用不同剪切刚度的试样进行实验,可绘制出剪切刚度剪切应力的曲线,以分析土体的变形刚度及其与荷载的关系。
直剪试验是土力学实验中最为基础的剪切试验,具有操作简便、试验容易、结果清晰等优点,被广泛应用于土力学实验。
直剪试验的强度指标主要包括抗剪强度(剪切极限、抗剪强度极限等)和内摩擦角两个参数。
抗剪强度是土体剪切破坏所能承受的最大抗剪力,通常用剪切极限强度表示。
剪切极限强度是当剪切应力逐渐增大时,土体达到承载能力极限的水平,并发生剪切破坏的场景。
它是土体抗剪切变形的极限。
内摩擦角则是反映土体颗粒间摩擦力的大小和土体内摩擦特性的参数。
内摩擦角是土体剪切破坏过程中剪切面上剪切应力与法向应力之比的角度。
这两个参数是评价土体抗剪特性和变形刚度的重要指标,它们的值直接影响到土工工程设计和土力学分析的结果。
土体的抗剪强度决定了土体的稳定性和承载能力,内摩擦角则决定了土体的变形性质和剪切刚度。
因此,对土体的剪切试验及其强度指标的研究能够为土力学领域的工程实践提供重要的理论依据和实验数据。
值得注意的是,土壤的剪切性状和强度指标受到多种因素的影响,包括土体类型、土粒特性、水分含量、固结状况、载荷方式、判别依据等。
直接剪切试验报告
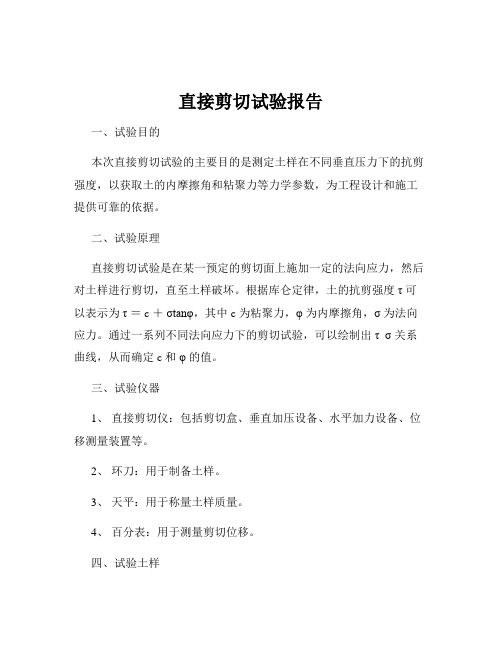
直接剪切试验报告一、试验目的本次直接剪切试验的主要目的是测定土样在不同垂直压力下的抗剪强度,以获取土的内摩擦角和粘聚力等力学参数,为工程设计和施工提供可靠的依据。
二、试验原理直接剪切试验是在某一预定的剪切面上施加一定的法向应力,然后对土样进行剪切,直至土样破坏。
根据库仑定律,土的抗剪强度τ 可以表示为τ = c +σtanφ,其中 c 为粘聚力,φ 为内摩擦角,σ 为法向应力。
通过一系列不同法向应力下的剪切试验,可以绘制出τ σ 关系曲线,从而确定 c 和φ 的值。
三、试验仪器1、直接剪切仪:包括剪切盒、垂直加压设备、水平加力设备、位移测量装置等。
2、环刀:用于制备土样。
3、天平:用于称量土样质量。
4、百分表:用于测量剪切位移。
四、试验土样本次试验所采用的土样为取自_____工程场地的粉质黏土。
土样的基本物理性质指标如下:1、天然含水量:_____%2、天然密度:_____g/cm³3、液限:_____%4、塑限:_____%五、试验步骤1、切取土样用环刀在原状土样上切取若干个试样,每个试样的高度和直径分别为_____mm 和_____mm。
对切取的试样进行编号,并测量其质量和高度。
2、安装试样将下剪切盒放入仪器底座中,并在盒内放入透水石和滤纸。
将土样放入下剪切盒中,然后放上上剪切盒,使上下剪切盒对齐,并在盒内放入透水石和滤纸。
3、施加垂直压力启动垂直加压设备,按照预定的垂直压力等级(如 100kPa、200kPa、300kPa、400kPa 等)依次对土样施加垂直压力。
每级垂直压力施加后,等待试样变形稳定(一般为 5 分钟)。
4、进行剪切试验启动水平加力设备,以缓慢均匀的速度对土样施加水平剪切力,直至土样破坏。
剪切过程中,记录剪切力和剪切位移的变化。
5、重复试验更换土样,重复上述步骤,进行至少 4 组试验。
六、试验结果及数据处理1、试验数据记录记录每级垂直压力下土样破坏时的剪切力和剪切位移,如下表所示:|垂直压力(kPa)|剪切力(kN)|剪切位移(mm)||||||100|_____|_____||200|_____|_____||300|_____|_____||400|_____|_____|2、绘制τ σ 关系曲线以垂直压力σ 为横坐标,剪切力τ 为纵坐标,绘制τ σ 关系曲线。
复合材料剪切试验
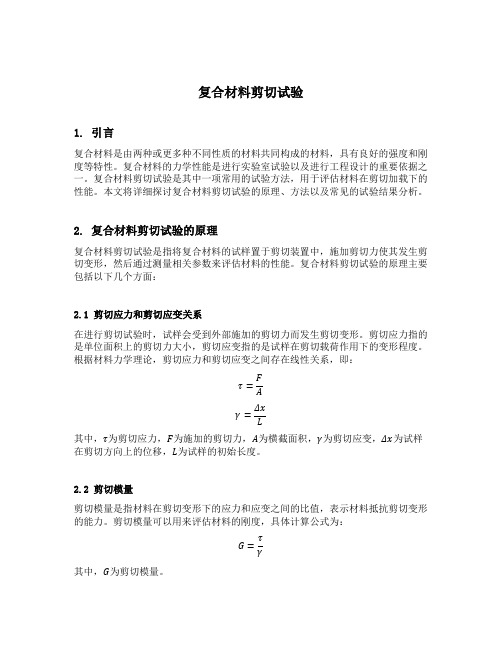
复合材料剪切试验1. 引言复合材料是由两种或更多种不同性质的材料共同构成的材料,具有良好的强度和刚度等特性。
复合材料的力学性能是进行实验室试验以及进行工程设计的重要依据之一。
复合材料剪切试验是其中一项常用的试验方法,用于评估材料在剪切加载下的性能。
本文将详细探讨复合材料剪切试验的原理、方法以及常见的试验结果分析。
2. 复合材料剪切试验的原理复合材料剪切试验是指将复合材料的试样置于剪切装置中,施加剪切力使其发生剪切变形,然后通过测量相关参数来评估材料的性能。
复合材料剪切试验的原理主要包括以下几个方面:2.1 剪切应力和剪切应变关系在进行剪切试验时,试样会受到外部施加的剪切力而发生剪切变形。
剪切应力指的是单位面积上的剪切力大小,剪切应变指的是试样在剪切载荷作用下的变形程度。
根据材料力学理论,剪切应力和剪切应变之间存在线性关系,即:τ=F Aγ=Δx L其中,τ为剪切应力,F为施加的剪切力,A为横截面积,γ为剪切应变,Δx为试样在剪切方向上的位移,L为试样的初始长度。
2.2 剪切模量剪切模量是指材料在剪切变形下的应力和应变之间的比值,表示材料抵抗剪切变形的能力。
剪切模量可以用来评估材料的刚度,具体计算公式为:G=τγ其中,G为剪切模量。
2.3 破坏模式复合材料剪切试验中,试样往往会发生不同的破坏模式。
常见的破坏模式包括剪切失效、层间剪切失效和纤维剪切失效等。
剪切失效是指试样发生断裂,层间剪切失效是指复合材料的层间界面发生剪切破坏,纤维剪切失效是指纤维束在剪切载荷下发生滑移和折断。
通过分析试验中的破坏模式,可以进一步了解复合材料的力学性能及其对不同加载的响应。
3. 复合材料剪切试验方法进行复合材料剪切试验时,需要准备试样及相应的试验设备。
以下是常见的复合材料剪切试验方法:3.1 试样制备根据试验要求和标准,将复合材料切割成相应的试样形状和尺寸。
常用的试样形状包括直角梁试样、轴向梁试样和剪切带试样等。
试样的制备过程需要注意保持试样的几何形状和尺寸的精确性,以及防止在制备过程中损伤试样。
焊接剪切试验
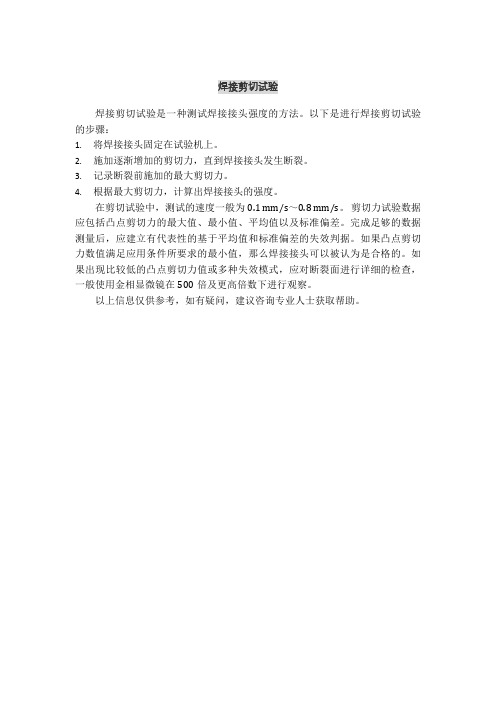
焊接剪切试验
焊接剪切试验是一种测试焊接接头强度的方法。
以下是进行焊接剪切试验的步骤:
1.将焊接接头固定在试验机上。
2.施加逐渐增加的剪切力,直到焊接接头发生断裂。
3.记录断裂前施加的最大剪切力。
4.根据最大剪切力,计算出焊接接头的强度。
在剪切试验中,测试的速度一般为0.1 mm/s~0.8 mm/s。
剪切力试验数据应包括凸点剪切力的最大值、最小值、平均值以及标准偏差。
完成足够的数据测量后,应建立有代表性的基于平均值和标准偏差的失效判据。
如果凸点剪切力数值满足应用条件所要求的最小值,那么焊接接头可以被认为是合格的。
如果出现比较低的凸点剪切力值或多种失效模式,应对断裂面进行详细的检查,一般使用金相显微镜在500倍及更高倍数下进行观察。
以上信息仅供参考,如有疑问,建议咨询专业人士获取帮助。
- 1、下载文档前请自行甄别文档内容的完整性,平台不提供额外的编辑、内容补充、找答案等附加服务。
- 2、"仅部分预览"的文档,不可在线预览部分如存在完整性等问题,可反馈申请退款(可完整预览的文档不适用该条件!)。
- 3、如文档侵犯您的权益,请联系客服反馈,我们会尽快为您处理(人工客服工作时间:9:00-18:30)。
切槽试样的拉伸-压缩试验方法
层间剪切试样
层间剪切环状试样
十字层梁试样
十字层梁的电阻应变片的粘贴位置
平面剪切:由 yx xy引起的剪切。
层间剪切;由 xz或 yz 引起的剪切。
纤维增强复合材料试验方法 ①平面剪切试验; ②层间剪切试验; ③剪断试验; 试样的形式 ①管状试样; ②棒状试样; ③板状试样; ④环状和弓形试样;
温度和湿度
加载方式
-随试样形状、尺寸和试验目的不同,采用不同加载方式。
对剪加载方式的夹具
平板剪切用的双剪夹具
弹性常数的算出: 测量标距对角线 P1 和应变 1 , 2 若平板为纯剪力状态,则: 切应力 xy 和剪应力 xy 可由几何关系算出 :
Gxy xy / xy
P xy 2ah 1 2 xy 1 1 2
x' y'
2
2
(1
1 yx Ex
)
和正应力 ,因此,以此种方式加载的正交平板已不 再是纯剪应力。 在标准的销钉铰接四杆框架中,接头的转轴同试样标距的 四角常是不重合,因而,造成纤维铺放方向同四连杆框 架的轴成450
夹具类型
改进后的四连杆夹具
③正方形平板的扭曲:使用广泛,主要由于测定弹性常数。 ④各向异性直条的拉伸:最简单、经济,但精度稍差。
薄壁管的扭转
-主要用于长丝或织物缠绕的薄壁管扭转试验。
若 h / R 足够小,剪切变形沿厚度 方向的变化可忽略,从而获得均 匀的切应力分布场。 薄壁管加工及试验时的要求 -层片数量应足以传递载荷;厚 度均匀,偏差小。电阻应变片要 使用+450/00/-450,用以检测应变 状态。 -为保证试件端头在加载时不破 裂及均匀加载,要对端头进行处 理。 R
强度的计算:
Pu Pu F 2ah
u xy
各向异性直条试样的拉伸
1 12 x sin 2 2 12 ( y x )sin 2 xy cos 2
x x Ex y xy x xy a16 x
-测量的最佳角 度450
复合材料剪切试验
抗剪性能的研究方法 -复合材料主要缺点-抗剪能力差(刚度、强度),特别是层 合结构,因此,对剪切性能研究十分重要。 剪切试验方法的难点:如何产生纯剪问题。 •随着复合材料各向异性和非均质性的增加
以及试件端头效应区的增大都使得纯剪问
题难度增大,均匀应力区愈加难以获得。 •试验方法取决于材料结构和载荷相对于对称 轴的方向。可分为平面剪切和层间剪切两种。
则为纯剪。 •对于不平衡的正交各向异 性的材料制成的平板,只 要材料的对称主轴平行于 连杆,应力状态与此相同。 •若不平衡的正交异性材料 的平板对称主轴同x和y轴 重合,有条件 得:
y
1 xy E y 1 yx Ex
即沿对角线的拉伸力不等于沿另一条对角线的压缩 力,此时, x y x 1 xy Ey 平板边缘有切应力:
测量值 结构限制
Gxy , xy
p,
Gxy , xy
Gxy
p,
p, w
00,900,00/900铺层 00, 900取向
在线性范围内,叠层对称
物理限制
正方形变为平行四边形,则 易算出:
1 2 xy 即 p1 p2 ( x y , xy 0)
Z
MT l G z . I p
M T 施加扭距 I p 极转动惯量 1 I p ( R04 Ri4 ) 2
平板剪切
-通常有三种加载方式。
-四连杆框架夹具最为常 用,装载试样的夹具连杆 应有足够的弯曲和拉-压 刚度。即 x y,且在加 载过程中形状不变。
测定性能
①扭转;②弯曲;③单向和双向的拉伸-压缩等加载方式。 平面剪切试验的方法 ①薄壁管的扭转 ②平板的剪切 ③正方形平板的扭曲;④各向异性 直条的拉伸; 各种剪切试验方法的特点 ①薄壁管的扭转:应力状态均匀,但耗材大。获得的数据不能由于 评价板状试样的性能,因制备方法不同。
②平板的剪切:可测定剪切模量和剪切强度,但耗材也较大。