基于差影和模板匹配的微小轴承表面缺陷检测
基于机器视觉的滑动轴承缺陷检测系统设计

基于机器视觉的滑动轴承缺陷检测系统设计摘要:目前,滑动轴承加工制作成品后,针对部分滑动轴承内部出现压坑与划伤缺陷通过人工目测方法来判处不达标产品,不但极易发生漏检或者误检现象,且整体工作效率低下,欠缺规范性检测流程。
与此同时,检测结果精准性与检测人员自身技能与知识储备有着紧密联系,从而会表现出稳定性较差。
故接下来文章重点通过实践需求,从而抛出了滑动轴承内表面缺陷检测视觉检测方法。
然而,机器视觉技术在轴承检测中重点以轴承尺寸与表面质量为核心,详尽解析通过计算机收集的轴承图像,尤其针对轴承内表面压坑、毛刺。
划痕等问题展开辨别,同时取得了良好效果。
关键词:机器视觉;滑动轴承;缺陷;检测系统设计当前,传统滑动轴承加工制作中,基于滑动轴承内侧检测表现出速率慢、智能化水平低下、精准度较差等一系列问题。
随后依据机器视觉技术来顺利完成轴承体内表面的自动检测功能,且通过实验检测设计平台截取了轴承内侧图像,随后依据形状模板来分配计算方法,从而更好的匹配预处理后的图像,结果较快完成目标物体与缺陷范围位置精准锁定。
而要想获取滑动轴承缺陷,并抛出了区域灰度值图像分割方法与形态学处理特征方法。
最终通过大量实践表明,全新检测系统与传统检测方法比较,其优势更加突出,并为滑动轴承内表面检测未来发展指明了方向。
一、滑动轴承缺陷自动检测系统组成分析(一)自动检测系统硬件系统组成分解1.1相机与镜头如何满足检测精准度与高品质图像采集需求,针对不同硬件主要参数的筛选至关重要。
首先,工业相机为收集图像的主要仪器,且为机器视觉系统设计中主要构成组件。
因此,需严格按照相应检测标准以及现场实际情况,从而更好的明确缺陷最小值是0.1mm,工件内部直径25mm,以及外部直径27mm,且工位合理区间要小于150mm,而相机类型挑选要重点关注下述几个方面:第一,面阵或线阵相机,其中1XN方式排列为线阵相机芯片,而MXN方式排列则为面阵相机芯片,随即形成了MXN个像素点矩形图像。
基于计算机视觉的微小轴承表面缺陷检测_陈向伟

像中灰度有阶跃或尖顶状变化的那些像素的集合, 边 缘广泛存在于物体与物体、物体与背景之间。是图像
分割、纹理特征提取和形状特征提取等图像分析所依
赖的重要基础 [ 1- 3] 。
系统边缘检测采用阈值法, 该方法是对灰度图像 用一阈值进行二值化处理, 大于阈值的点为黑, 小于 阈值的点为白, 获得二值图像后, 边缘便一目了然。
CH EN X iangw e,i ZHANG Xue jun, GUAN Shan ( College o f Pow er and M echan ical Eng ineering of N ortheast D ian liUn iversity, Jilin 132012, China)
Abstrac t: In o rder to perform non-con tact inspection on surface defec t o f bear ing, a new inspection m ethod based on Charge Coupled D ev ice ( CCD ) im ag e, wh ich use the A102 fCCD dig ita l cam era as im ag e sensor and utilizes im ag e-processing technology, w as proposed to inspect the surface de fect of bearing. In the inspection sy stem, the m a in approaches include collec ting image, filtering im age and reduc ing no ise w ith the edge retention filter, creating a b inary im age w ith thresho ld m ethod, detec ting edge o f the image, using the subtracting betw een two im ag es to inspect surface defect. T he expe rim en t indicates that the above system has the advantag es of conven ience, correct location, the capab ility of no ise resistance, high speed pro cessing and tem pora l correctness.
一种基于图像展开与拼接的精密轴承表面缺陷光学检测方法

一种基于图像展开与拼接的精密轴承表面缺陷光学检测方法杨加东;谢明【期刊名称】《机床与液压》【年(卷),期】2017(45)4【摘要】建立一种基于机器视觉的精密轴承表面缺陷光学检测系统.利用图像展开和拼接技术获得轴承侧面完整而又没有重复的二维图像,在此基础上对微小轴承表面缺陷进行检测、缺陷提取和分类.实验结果表明:采用该方法能够快速、高效地检测出微小精密轴承表面大于10 μm的缺陷形貌;能够准确地对凹坑、裂纹和划痕缺陷进行分类.%A kind of precision bearing surface defects optical test system was established based on machine vision.Image expanding and splicing technology was used to acquire the two dimensional (2-DOF) image of bearing with whole profile and no repeat,on this basis,the bearing surface tiny defects detection,defects extraction and classification were carried out.Experimental results show that using this method can quickly and efficiently detect the precision bearing surface tiny defects which are greater than 10 μm;and can accurately classify pi ts,cracks and scratches of defects.【总页数】4页(P160-163)【作者】杨加东;谢明【作者单位】南京工业大学电气工程与控制科学学院,江苏南京 211816;南京工业大学电气工程与控制科学学院,江苏南京 211816【正文语种】中文【中图分类】TP391.4【相关文献】1.基于图像拼接的惯性约束聚变终端光学元件在线检测 [J], 冯博;陈凤东;张建隆;孙和义;彭志涛;刘国栋2.基于图像融合分割的实木地板表面缺陷检测方法 [J], 张怡卓;许雷;丁亮;曹军3.基于图像的缸体零件表面缺陷检测方法 [J], 谭亚雄;刘伟;张海洋4.一种基于图像的光学系统测角精度检测方法 [J], 王凤娇;景文博;刘学;王晓曼;韩学辉5.基于图像修复的无监督表面缺陷检测方法 [J], 胡广华;王宁;何文亮;唐辉雄因版权原因,仅展示原文概要,查看原文内容请购买。
基于计算机视觉的微小轴承表面缺陷检测

基于计算机视觉的微小轴承表面缺陷检测
陈向伟;张学军;关山
【期刊名称】《机床与液压》
【年(卷),期】2009(037)009
【摘要】提出了一种基于计算机视觉的轴承表面缺陷检测的新方法,采用
A102fCCD数字摄像头作为图像传感器,利用数字图像处理技术对轴承表面缺陷进
行检测,其主要步骤包括:图像的采集;采用边缘保持滤波器进行滤波、降噪;采用阈值法将图像二值化,并进行边缘检测;采用差影方法对有缺陷表面进行识别.试验证明,用该方法进行轴承表面缺陷检测是可行的,并具有方法简单、定位准确、抗噪能力强、计算速度快、实时性好等优点.
【总页数】3页(P130-132)
【作者】陈向伟;张学军;关山
【作者单位】东北电力大学能源与机械学院,吉林吉林,132012;东北电力大学能源
与机械学院,吉林吉林,132012;东北电力大学能源与机械学院,吉林吉林,132012【正文语种】中文
【中图分类】TP391
【相关文献】
1.微小轴承表面缺陷检测中的自动分拣系统设计 [J], 张振祥;袁云龙;陈廉清
2.基于差影和模板匹配的微小轴承表面缺陷检测 [J], 陈廉清;崔治;王龙山
3.基于计算机视觉的微小轴承表面缺陷在线识别 [J], 陈廉清;崔治;王龙山
4.基于计算机视觉的墙地砖表面缺陷检测 [J], 熊建平
5.基于计算机视觉的轴承表面缺陷检测 [J], 陈国君;陈鹏;张学军
因版权原因,仅展示原文概要,查看原文内容请购买。
一种基于支持向量机的轴承表面缺陷检测方法

一 种 基 于 支 持向 量 机 的 轴 承 表 面 缺 陷 检 测 方 法
涂宏斌, 周新建
(华东交通大学 C A D / CA 研究室, 江西 南昌 330 0 1 3)
摘要: 提出了一种基于支持支持向量机和主成分分析的轴承表面缺陷检测算 法, 该算 法把轴承 中的非缺陷 区域和缺陷 区域分 别看作两种不同的纹理模式, 先利用主成分分析法 ( CA ) 对图像进 行降维处 理, 然 后用支 持向量 机方法 对降维 后的样 本采样 学习, 然后进行分类判断 . 实验结果表明, 该算法能够较好地实现轴承缺陷的检测分类, 有一定的实用价值 . 关 键 词: 表面缺陷; 主成分分析; 支持向量机 文献标识码: A 中图分类号:H 1 63
行分类判断, 最后得到实验结果 .
�
引言 � 支持向量机
线性情况 支持向量机是从线性可分 情况下的最优 分类
铁路货车 轴承是关系到铁路运输 安全的关键 部件, 如果对照铁道部指定的图谱, 用目测或手感 来判断轴承内外圈及 滚子是否存在表面缺陷及其
�. �
类型和损伤程度, 则工人工作量大, 检测 结果随机 面发展而来的, 基本思想可用图 1的两维情况说明 性大, 因此 人工检测方法已经很难满足实 际要求 . � 图中, 实心点和空心点代表两类样本, 为分类线,
1
(5 ) (6)
可行的 . 2)一般主成分分析算法实施 有数据矩阵:
若 � 为最优解, 则有 ��
… � 即最优分 类面的权系数向量是训 � 练样本向量 � 11 12 1 的线性组合 . … � � � 21 22 2 ……………………………
[1 ] 使用机器对轴承进行缺陷检测就显得十分必要 . 1
,
2
基于机器视觉的轴承防尘盖表面缺陷检测

基于机器视觉的轴承防尘盖表面缺陷检测陈文达;白瑞林;吉峰;温振市【摘要】To realize the automatic detection of bearing shield surface, this paper proposes a method based on machine vision. It uses the blue coaxial light to overcome the metal reflection;it uses the least squares method to fit the bearing outer circle. According to the bearing type, it segments the bearing. Using Otsu’s method and Roberts edge extraction it processes the shield image. It calculates the points when value is 1 per 2°. Compared with the template data, it obtains the phase angle, then separates the character region and no-character region;there is no interference when the two parts defect is detected. Experiments show that:the captured image is unambiguous and the correct rate of detection algorithm is more than 96%. It can realize the automatic detection of bearing shield surface.%为实现工业现场中轴承防尘盖表面缺陷的自动检测,提出一种基于机器视觉技术的检测方法。
对基于支持向量机的轴承表面缺陷检测研究

83中国设备工程Engineer ing hina C P l ant中国设备工程 2019.01 (下)采用以往传统的轴承检测方式,不但工作量较大,且检测结果具有较强的随机性,如若有漏检的轴承,且其中刚好存在缺陷,将对使用安全生产构成较大威胁。
对此,为了尽可能的降低检测中的成本投入、减少漏检、误检率,应积极利用机器对轴承进行检测。
在本文的研究过程中,在支持向量机的基础上,对轴承表面缺陷的检测方式进行分析,并将轴承的表面区域划分为缺陷区域与非缺陷区域两个方面,借助主成分分析法对图像进行降维处理,然后采用支持向量机的方式,分别对两种不同类型的样本特征进行提取与学习,同时对其进行分类判断。
1 支持向量机概述在支持向量机的应用中,主要是从线性可分情况下发展而来,其基本思想主要体现在两个方面,分别用空心点与实心点表示两类样本,通过H 线将其分割开来,H 1与H 2属于与H 线距离较近样本的直线,与H 线相平行,二者之间的距离被看作为分类间隔。
所谓的最优分类线主要是指该线的存在除了能够将两类正确区分以外,保障分类之间的间隔处于最大状态,可以对其进行归一化,构建成线性可分的样本集(x i ,y i ),i 的取值范围为1到n,并且满足以下公式:这时的分类间隔为w /2,保障最大间隔与2w 最小值相同。
在满足上述公式的基础上,使2w/2中最小的分类面看作为最优分类面,这时在H 1与H 2上的训练样本点便可以被看作为支持向量。
要想对所选样本的类型进行正确的划分,便可以符合上述公式。
从上述分析中可以看出,对于最优超平面的研究问题可以转化成约束优化的问题,也就是在满足上述公式的前提下,对函数2/)(2w w =Φ中的最小数值进行分析,并且由此得出函数:∑=−=ni Tia wa b w L 12/)(),,(式中,a i 的数值大等于0,w 与b 均为函数中的极小值,分别对二者求取偏微分,并且令其为0则能够将问题转变为求对偶的问题,这时的最优分类面权系数向量便可以看作为训练样本向量中的线性组合。
基于机器视觉的轴承表面缺陷检测系统研究

基于机器视觉的轴承表面缺陷检测系统研究摘要:轴承是大型机械设备的重要组成部分,其性能的优劣直接关系到设备的工作稳定。
近几年,随着我国工业的迅速发展,各种工业对轴承的需求与日俱增,对轴承的外观品质提出了更高的要求,特别是在进出口贸易中,更是如此。
虽然国内的机械制造技术已有相当程度的提高,但是在大批量生产中不可避免地残次品的出现。
目前,我国的企业对轴承的分拣仍然是以人眼检测、手工分拣为主;这种方式工作量大、效率极低,受作业人员分拣标准的差异、视觉疲劳等原因影响,造成分拣过程中出现的漏检率和错检率高。
关键词:轴承;机器视觉;图像处理;缺陷检测引言:制造业是国家经济的主体,是国家的国防、军队的核心,是国家发展的根本。
《中国制造2025》为我国从制造大国向制造强国转变指明了发展方向和路径,大力推动自主研发关键技术、打破对外国科技的依赖性、增强国内制造业的竞争能力,逐步建立和健全现代产业制造系统。
但是,目前国内的基本生产技术和基本材料工业都落后于世界先进水平,很多产品的可靠性不能完全适应大功率的要求。
为了改变目前的发展状况,国家建议重点发展高速、精密、重载轴承等机械基本零件,并逐渐增加对轴承的研究与开发,以改善轴承的可靠性和寿命。
本文根据轴承工业的实际需要,从轴承的概念、检测系统分析规划、硬件设计等方面进行了深入的探讨。
本系统对推动计算机图象处理技术的发展和发展具有重要的理论意义;同时也能很好地解决当前许多轴承厂家手工目视分类所带来的速度、精度等问题,从而达到提高生产效率、减少人工成本、促进轴承工业自动化改造的目的。
一、轴承简介轴承是一种在机械驱动中具有稳定和减少负载摩擦力的零件,它主要用于导向轴系零件的转动和承载轴向车体上的负载。
在此基础上,从图1可以看出,目前的轴承按其构造和运动的摩阻性能可划分为两种类型:滚动和滑动两种。
滚动支座按承载的方向可分成两类:向心型和止推型,而按其润滑形式可划分成动压型和静态压型两类。
基于图像处理技术的调心球轴承表面缺陷检测

基于图像处理技术的调心球轴承表面缺陷检测引言:调心球轴承是广泛应用于各种机械设备中的重要零部件之一。
其高负荷承载能力和自动调心特性使其在工业生产中扮演着重要的角色。
然而,由于使用频繁和工作环境的恶劣性,调心球轴承的表面可能会产生一些缺陷,例如裂纹、磨损和划痕等。
及早发现和修复这些表面缺陷,对于确保轴承的可靠性和延长轴承的使用寿命至关重要。
因此,基于图像处理技术的调心球轴承表面缺陷检测方法成为了一个备受关注的研究领域。
1. 调心球轴承表面缺陷的特征分析调心球轴承表面缺陷通常包括裂纹、磨损和划痕等。
这些缺陷具有一定的几何和颜色特征。
通过对缺陷的特征分析,可以更好地理解和区分不同类型的表面缺陷。
裂纹通常呈线状,具有一定的长度和宽度。
磨损主要表现为表面的光洁度下降和表面凹痕的出现。
划痕则表现为一条窄而深的凹槽。
2. 图像处理技术在调心球轴承表面缺陷检测中的应用基于图像处理技术的调心球轴承表面缺陷检测方法可以分为以下几个步骤:图像获取、图像预处理、特征提取和缺陷分类。
2.1 图像获取调心球轴承的表面图像可以通过摄像机、扫描仪或显微镜等设备获取。
关键是保证图像的清晰度和分辨率,以便后续处理。
2.2 图像预处理图像预处理是为了提高图像质量、增强缺陷的对比度和减少噪声等。
这一步骤包括图像去噪、图像锐化和图像增强等操作。
常用的算法有中值滤波、均值滤波和高斯滤波等。
2.3 特征提取特征提取是为了从图像中获取表面缺陷的关键特征信息。
常用的特征包括像素值、纹理、形状和颜色等。
基于人工智能算法的特征提取方法如卷积神经网络(CNN)、支持向量机(SVM)和主成分分析(PCA)等被广泛应用于调心球轴承缺陷检测中。
2.4 缺陷分类在特征提取阶段得到的特征向量会被输入到分类器中进行缺陷的分类。
常用的分类算法有决策树、逻辑回归和随机森林等。
这些算法采用监督学习的方式,通过训练样本和标签来构建模型并进行缺陷分类。
3. 基于图像处理技术的调心球轴承表面缺陷检测的优势和挑战基于图像处理技术的调心球轴承表面缺陷检测方法具有以下优势:3.1 非接触式检测基于图像处理技术的缺陷检测方法无需对轴承进行接触,可以减少因接触而引入的额外损坏。
基于深度学习的轴承外圈表面缺陷分类关键技术研究
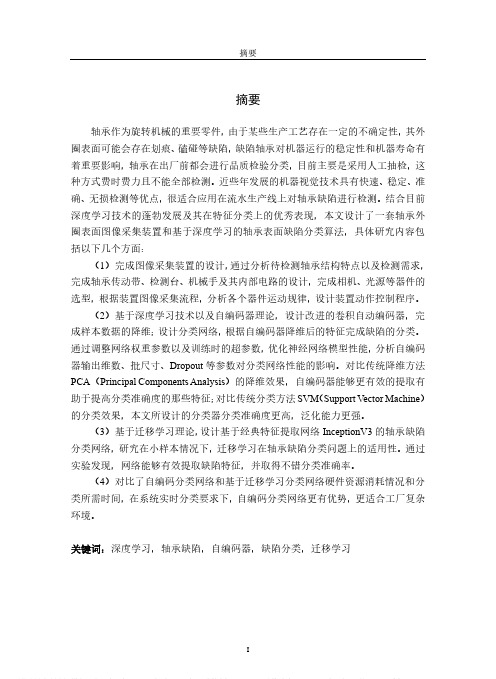
摘要摘要轴承作为旋转机械的重要零件,由于某些生产工艺存在一定的不确定性,其外圈表面可能会存在划痕、磕碰等缺陷,缺陷轴承对机器运行的稳定性和机器寿命有着重要影响,轴承在出厂前都会进行品质检验分类,目前主要是采用人工抽检,这种方式费时费力且不能全部检测。
近些年发展的机器视觉技术具有快速、稳定、准确、无损检测等优点,很适合应用在流水生产线上对轴承缺陷进行检测。
结合目前深度学习技术的蓬勃发展及其在特征分类上的优秀表现,本文设计了一套轴承外圈表面图像采集装置和基于深度学习的轴承表面缺陷分类算法,具体研究内容包括以下几个方面:(1)完成图像采集装置的设计,通过分析待检测轴承结构特点以及检测需求,完成轴承传动带、检测台、机械手及其内部电路的设计,完成相机、光源等器件的选型,根据装置图像采集流程,分析各个器件运动规律,设计装置动作控制程序。
(2)基于深度学习技术以及自编码器理论,设计改进的卷积自动编码器,完成样本数据的降维;设计分类网络,根据自编码器降维后的特征完成缺陷的分类。
通过调整网络权重参数以及训练时的超参数,优化神经网络模型性能,分析自编码器输出维数、批尺寸、Dropout等参数对分类网络性能的影响。
对比传统降维方法PCA(Principal Components Analysis)的降维效果,自编码器能够更有效的提取有助于提高分类准确度的那些特征;对比传统分类方法SVM(Support Vector Machine)的分类效果,本文所设计的分类器分类准确度更高,泛化能力更强。
(3)基于迁移学习理论,设计基于经典特征提取网络InceptionV3的轴承缺陷分类网络,研究在小样本情况下,迁移学习在轴承缺陷分类问题上的适用性。
通过实验发现,网络能够有效提取缺陷特征,并取得不错分类准确率。
(4)对比了自编码分类网络和基于迁移学习分类网络硬件资源消耗情况和分类所需时间,在系统实时分类要求下,自编码分类网络更有优势,更适合工厂复杂环境。
基于差影和模板匹配的微小轴承表面缺陷检测

基于差影和模板匹配的微小轴承表面缺陷检测
陈廉清;崔治;王龙山
【期刊名称】《中国机械工程》
【年(卷),期】2006(017)010
【摘要】针对轴承表面缺陷的位置、面积、深度等随机变化导致图像采集具有不确定性的特点,设计了一套采用光电耦合器图像识别技术进行缺陷自动检测的系统.该系统光源恒定、处理速度快、图像精度高,能长时间稳定工作,显著提高了图像采集质量.经过深入研究图像分割、图像差影、模板匹配等模式识别理论与技术及微小轴承图像特征发现,要检测轴承的表面缺陷,需将轴承表面分割成两部分进行识别,轴承表面的均匀分布区域直接采用差影法,文字刻印区域采用模板匹配法,结果表明该方法识别正确率达98%.
【总页数】4页(P1019-1022)
【作者】陈廉清;崔治;王龙山
【作者单位】宁波工程学院,宁波,315016;吉林大学,长春,130025;吉林大学,长春,130025
【正文语种】中文
【中图分类】TP391.4;TH133.3
【相关文献】
1.微小轴承表面缺陷检测中的自动分拣系统设计 [J], 张振祥;袁云龙;陈廉清
2.基于计算机视觉的微小轴承表面缺陷检测 [J], 陈向伟;张学军;关山
3.基于差影法粗分割与多模板匹配的人脸检测 [J], 周彩霞;匡纲要;宋海娜;易江义
4.基于模板匹配和差影处理的票据图象检测 [J], 陈强;杨静宇;娄震;张重阳
5.用差影法与多模板匹配快速实现人脸检测 [J], 周彩霞;匡纲要;宋海娜;易江义因版权原因,仅展示原文概要,查看原文内容请购买。
- 1、下载文档前请自行甄别文档内容的完整性,平台不提供额外的编辑、内容补充、找答案等附加服务。
- 2、"仅部分预览"的文档,不可在线预览部分如存在完整性等问题,可反馈申请退款(可完整预览的文档不适用该条件!)。
- 3、如文档侵犯您的权益,请联系客服反馈,我们会尽快为您处理(人工客服工作时间:9:00-18:30)。
缺陷 , 其底部放置均匀可
调背 光 源以 消除 工 件阴
影, 加装偏振器滤去数字
摄像 机的杂光 , 采用暗箱
隔绝外界环境光 。这种设
计既能满足图像采集的需 1. 检测系统 2. CCD 摄像头
要, 又有利于保持光源的 恒定 , 保证系统能够长时 间稳定工作[ 1] 。 该系统的
3. 偏振器 4. 锥形光源 5. 检测轴承 6. 背光源 图 1 图像采集系统
图 4 所示为为方便计算机视觉系统的质量检 测而对轴承图像进行的理论区域分割 。 将内外圈 端面(图 4 中的阴影线部分以及图 5a)作为一个 整体进行图像处理及差影 , 将刻印文字所在的密 封盖端面(图 4 中的网格线部分以及图 5b)作为 一个单独表面进行图像处理完成表面质量检测 。
由于轴承的形状为圆形 , 只需求出圆心坐标 和半径就可以完全确定其位置 。圆心的定位可由 H ough 变换方法得到[ 3] 。在进行 H ough 变换前要 进行 XY 双向扫描 , 根据灰度变化检测出图像中 的有效图像坐标极值 , 并以此大致确定轴承所在 的一个方形区域 , 同时也就确定了圆心可能存在 的范围 , 从而显著减小了 H ough 变换的运算量 。 然后采用标准 H ough 变换对图像边缘进行圆度 拟合 , 实现圆心的精确定位 。
轴承表面上的凹坑缺陷位置 、缺陷的深度与 斜面倾斜角均为随机值 , 使得表面对于平行光的 反射出现不确定性 , 导致所采集的缺陷图像也具 有不确定性 。 在检测系统中 , 图像灰度及其分布 是一个很重要的参数 , 光源与照明方案的设计应 尽可能突出被检测工件的灰度特征量 。 在增加对 比度的同时 , 还应保证被检测区域有足够的整体
是指对两幅输入图像进行点对点的减法而得到输
出图像的运算 , 其数学表达式如下 :
C( x , y) = A(x , y) - B(x , y)
(1)
式 中 , A(x , y) 和 B( x , y) 为 输 入 图 像 ;C(x , y) 为 输 出图像 。
图像相减可用于去除一幅图像中不需要的加
性图案 , 加性图案可能是缓慢变化的背景阴影 、周
收稿日期 :2005 — 12 — 05 基金项目 :宁波市工业科研攻关项目(2005B100014)
1 数字图像采集系统设计
在基于 CCD 技术的微小轴承表面缺陷检测 系统中 , 光源的设计 、图像的采集与处理是整个系 统成功与否的关键 。 为了采集到高质量的图像信 息 , 便于后续图像特征量的提取和分析 , 本系统采 用德国 Basler 公司的 A102f 型 CCD 面阵数字摄 像头为图像传感器 , 利用数字图像处理技术对微 小轴承的表面质量特征进行识别检测 , 该系统可 供调节的参数有曝光时间 、灰度值 、采集范围以及 采样频率 。通过图像采集卡转化为数字化图像输 入计算机 , 由系统进行在线识别 。
图 3 差影图像
10 20
1. 刻印文字 2. 密封端盖 3. 压槽 4. 轴承内圈 5. 轴承外圈
图 4 理 论轴承图区域分割
对于同一型号的轴承 , 图 5 中所标出的各图 像边缘半径 R1 ~ R6 都是确定不变的 , 对于尺寸 标定已经完成的图像 , 在内外圈及密封盖的圆心 定位后可以直接按照 r ∈ (R1 , R 2) ∪ (R5 , R6)及 r ∈ (R3 , R4 )将图形分割为 S1 (内外圈端面) 和 S2 (密封盖端面)。
Key words:change couple device(CCD);micro bearing ;surface defect ;subst raction ;template matching
0 引言
微小轴承在 生产 、装 配过程中 , 由于 加工技 术 、微小异物等因素 , 在轴承的外圆表面 、密封盖 端面等处会产生各种压痕 、吭伤 、划痕等缺陷 , 这 些缺陷将会对微小轴承的使用性能和外观产生一 定影响 。 对微小轴承 进行表面检测 是保证其正 常 、安全 、可靠运行的重要技术手段 。 目前 , 国内 轴承生产厂家对轴承表面的检测主要利用人工目 测完成 , 由于受检查人员技术 、经验 、工作环境以 及视力疲劳等影响 , 很容易出现误检和漏检 , 这种 方法不仅效率低 、缺乏准确性和规范化 , 并且不能 将检测数据实时送入计算机进行质量管理 , 对企业 造成不必要的损失 。 本文提出一种将光电耦合器 (change couple device , CCD)技术应用于微小轴承 表面缺陷检测的方法 , 并开发出一套利用计算机控 制且具有实时图像处理和分类功能的检测系统 。
1. Ningbo Unive rsity o f T echnolog y , Ning bo , Z hejiang , 315016 2. Ji li n Univ ersity , Changchun , 130025
Abstract :Focusing o n t he charact eri sti cs t hat t he col lected image w as uncer tain because of the bearing surface defect’ s posi tion and area as well as dept h chang ing random ly , an auto matic def ect inspection sy stem by t he image identifi catio n t echno logy w as desig ned. T he system had adv ant ag es of the i nvariableness of lig ht source and lo ng stable w o rking time , w hich i mproved the image collecting precision great ly . By studyi ng the digit al image feat ures and the theories and technolo gy of pat tern recognitio n such as segment ation of i mage , t he subt ract ing bet ween tw o im ag es and tem plat e m atching , the paper came to t he co nclusions t hat t he bearing surface image should be divided into tw o part s t o inspect the def ect effi cient ly , one wi th reg ular g ray - value and the ot he r wi th ir reg ular g ray - value because of m odel tex t. T he subt ract ion could be directly used i n t he f ormer situatio n and t he t emplate mat chi ng could be used in t he later. Finally t he expe riment resul t show s that accuracy of t he sy st em reached as hig h as 98 %.
中国机械工程第 17 卷第 10 期 2006 年 5 月下半月
存在相当大的干扰(图 3), 不利于后续对缺陷的 判别工作 。
通过对加工现场进行统计归类 , 约 80 %的轴 承表面缺陷出现在内外圈端面及密封盖端面上 , 为了简化检测模型及加快检测速度 , 可以对轴承 采集图像先进行区域分割 , 重点突出检测部位 , 以 便按照不同的表面条件进行分步检测 。
特点是处理速度快 、图像精度高 , 并可以保证检测
系统的实时性 。
2 微小轴承的图像特征分析
轴承表面主要由外圈工作面 、外压槽 、密封盖 端面 、内压槽及内圈工作面组成 , 其中在密封盖端 面上还刻印有轴承型号等文字 。在大量实验的基 础上 , 我们对轴承采集图像的特征进行了详细分 析 , 图 2 为标准轴承与缺陷轴承的对比图 。
图 2 标准轴承和缺陷轴承比 较
目前 , 利用计算机视觉进行工件在线检测的
方法一般为差影法 , 即将检测目标图像与事先采
集的标 准模 板图 像进行 差影计算来进行判断[ 2] 。
但进行 差影 的前 提条件
是两个 图像 不存 在较大
的位置误差和角度误差 ,
在图 2a 和图 2b 中 , 由于
Hale Waihona Puke 密封盖 端面 上刻 印文字 的影响 , 使两图差影结果
基于差影和模板匹配的微小轴承表面缺陷检测 ——— 陈廉清 崔 治 王龙山
基于差影和模板匹配的微小轴承表面缺陷检测
陈廉清1 崔 治2 王龙山2
1. 宁波工程学院 , 宁波 , 315016 2. 吉林大学 , 长春 , 130025
摘要 :针对轴承表面缺陷的位置 、面积 、深度等随机变化导致图像采集具有不确定性的特
点 , 设计了一套采用光电耦合器图像识别技术进行缺陷自动检测的系统 。 该系统光源恒定 、处
理速度快 、图像精度高 , 能长时间稳定工作 , 显著提高了图像采集质量 。 经过深入研究图像分 割 、图像差影 、模板匹配等模式识别理论与技术及微小轴承图像特征发现 , 要检测轴承的表面
缺陷 , 需将轴承表面分割成两部分进行识别 , 轴承表面的均匀分布区域直接采用差影法 , 文字
陷 , 有可能产生误检 。
由此需要在全局统计意义上对两差影图像进
行分析 , 将两差影图像差值均方误差 D 与预先设
定阈值进行比较 , 其中 D 的计算公式如下 :
期性的噪声或者是在图像上每一像素处均已知的