50T转炉炉体设计书
50t新概念电弧炉大纲(新)
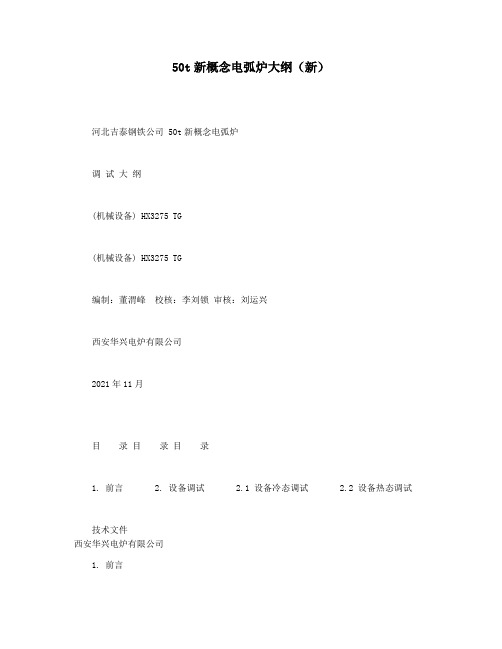
50t新概念电弧炉大纲(新)河北吉泰钢铁公司 50t新概念电弧炉调试大纲(机械设备) HX3275 TG(机械设备) HX3275 TG编制:董渭峰校核:李刘锁审核:刘运兴西安华兴电炉有限公司2021年11月目录目录目录1. 前言2. 设备调试 2.1 设备冷态调试 2.2 设备热态调试技术文件西安华兴电炉有限公司1. 前言该设备是为河北吉泰钢铁公司电炉厂新建50t新概念电弧炉而设计和制造。
用于该厂钢水的熔炼,其具体功能及主要技术参数见HX3275 SM(50t新概念使用说明书)。
该文件与HX3275 SM(机械设备)为配套文件,故该设备的布�Z形式及结构简介参见HX3275 SM相应部分。
2. 设备调试设备调试分设备冷态调试和热态调试。
2.1 设备冷态调试2.1.1 设备调试前的准备工作a. 设备调试应在设备安装初步验收合格的基础上进行,初步��验收的主要内容含:①设备完整性验收;②设备安装主要尺寸验收;③设备安装精度验收;④设备公用设施供给验收;⑤设备安装主要技术要求验收;⑥设备修复件的主要尺寸及技术要求验收。
b. 设备操作人员培训①设备操作人员应熟悉该设备工作原理,设备组成及设备主要结构。
②设备操作人员应具备炉前操作的基本训练和培训。
③设备操作人员应接受安技教育并确认合格。
c. 设备操作的必要工具。
d. 设备检修的常用工具。
2.1.2 设备冷态调试a. 水冷炉盖及其提升机构、旋转机构。
(旋转支撑、水平锁定应到位)炉盖反复提升、旋转3次,检查炉盖行程,保证工作行程450mm;炉盖下沿1技术文件西安华兴电炉有限公司圈应下降到下限位�Z时(即盖在炉体上时)旋转锁定插销应可靠地插入倾动平台相应的孔之中,炉盖提升至上限位�Z时,旋转锁定连杆插销,应可靠地提出倾动平台保证旋转动作,炉盖旋开角度≥70°;炉盖通水试验(水压1.0MPa)应无渗漏等异常现象;炉盖提升与下降、旋转时,炉盖进出水管(金属软管)应无扭折现象。
50t转炉氧枪设计说明书

河北工业职业技术学院毕业论文论文题目:50t转炉氧枪设计说明书系别材料工程系专业年级09冶金技术一班学生姓名马志龙李建刚李雷学号28 25 48指导教师黄伟青职称讲师日期 2012年3月23日河北工业职业技术学院毕业设计(论文)成绩评定表毕业设计(论文)任务书课题名称50t转炉氧枪设计说明书专业冶金技术班级09级冶金一班姓名马志龙李建刚李雷学号28 25 48一、毕业论文(设计)目的:1、学生应在指导教师指导下,独立完成冶金生产总结及调查研究工作,并整理分析所搜集的资料,最后撰写出毕业论文。
2、在毕业论文中能综合运用所学的知识。
3、通过毕业论文的撰写使学生学会围绕课题进行调研,收集整理资料,并锻炼分析问题、解决问题的能力,掌握冶金生产工作的一般程序、内容和方法。
4、培养实事求是、扎扎实实的工作作风和严肃认真的科学态度。
5、论文格式、字数符合河北工院毕业论文撰写规范。
二、毕业论文(设计)时间进度安排:论文(设计)按五周计算:第一周:熟悉毕业论文任务书,在指导教师的帮助下对该论题进行初步调研分析,查阅相关文献资料。
第二周:完成论文框架的构建,并提交论文写作大纲。
第三~四周:完成论文初稿写作。
第五周:经指导教师的审阅完成论文的定稿及写作,准备参加论文答辩。
三、计划答辩时间:2012 年6月9日~6月11日指导教师(签字):毕业实践领导小组组长(签字):年月日年月日50t转炉氧枪设计说明书一概述氧枪是转炉吹氧设备中的关键部分,它对顶吹氧气转炉冶炼起关键的作用,它是由喷头,枪身和枪尾组成。
在吹炼过程中转炉内的温度高达2000~2600℃,所以氧枪受到炉气和炉衬的严重的辐射。
熔池内的化学反应对氧枪严重冲刷。
所以说氧枪必须要有良好的水冷系统和牢固的金属结构,并且便于加工制造。
枪身由三层同心钢管组成,内管同氧气,内层和中层管之间是冷却水的进水通道,中层管和外层管之间是冷却水的出水通道。
喷头处于转炉内的最高温度区,因此,其必须拥有良好的导热性并且工作效率要高,保证吹炼的进行,提高工作效率。
50th燃烧高焦炉混合煤气环形加热炉设计设计说明书

50t/h燃烧高焦炉混合煤气环形加热炉设计摘要:环形加热炉是借炉底的旋转,使放置在炉底上的坯料由装料口移到出料口的一种炉型。
炉子用侧进料侧出料的方式,并且用侧烧嘴加热。
本设计主要针对中径15米环形加热炉尺寸、燃料和排烟系统进行设计,具体包括燃料燃烧计算、钢坯加热时间计算、炉子基本尺寸的确定、热平衡计算及燃料消耗量的确定,排烟系统计算。
炉子分为三段式,预热段为一段,加热段为一段,均热段为一段。
本设计采用高焦炉混合煤气作为环形加热炉的主要燃料。
本设计中环形加热炉的排烟方式采用机械排烟。
由于炉子排烟系统阻力较大,故采用排烟机直接排烟的形式进行排烟。
在排烟系统设计中,主要进行了烟道阻力的计算、烟囱的计算、炉膛内阻力的计算、掺冷风机的选取以及排烟机的选取等工作。
本组设计是在6个人共同合作下完成的。
关键词:环形加热炉、热平衡、排烟系统。
AbstractThe design of the main diameter of 15 meters rotary hearth furnace,fuel and exhaust system design, including fuel combustion,the billet heating time,the furnace to determine the basic size,the heat balance calculation and the determination of fuel consumption,smoke extraction system calculation. Stove is divided into three parts, and warm for a period of heating period, for a long, hot for a period of time.Rotary hearth furnace using natural coke oven gas as main fuel。
50吨转炉岗位作业指导书(DOC 7页)
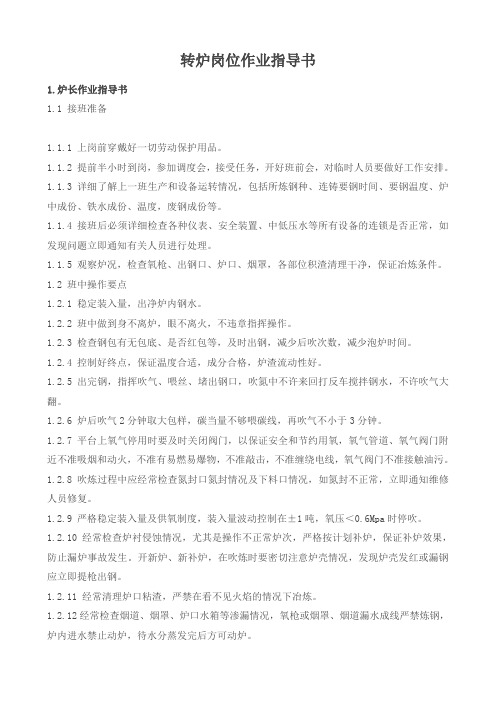
转炉岗位作业指导书1.炉长作业指导书1.1 接班准备1.1.1 上岗前穿戴好一切劳动保护用品。
1.1.2 提前半小时到岗,参加调度会,接受任务,开好班前会,对临时人员要做好工作安排。
1.1.3 详细了解上一班生产和设备运转情况,包括所炼钢种、连铸要钢时间、要钢温度、炉中成份、铁水成份、温度,废钢成份等。
1.1.4 接班后必须详细检查各种仪表、安全装置、中低压水等所有设备的连锁是否正常,如发现问题立即通知有关人员进行处理。
1.1.5 观察炉况,检查氧枪、出钢口、炉口、烟罩,各部位积渣清理干净,保证冶炼条件。
1.2 班中操作要点1.2.1 稳定装入量,出净炉内钢水。
1.2.2 班中做到身不离炉,眼不离火,不违章指挥操作。
1.2.3 检查钢包有无包底、是否红包等,及时出钢,减少后吹次数,减少泡炉时间。
1.2.4 控制好终点,保证温度合适,成分合格,炉渣流动性好。
1.2.5 出完钢,指挥吹气、喂丝、堵出钢口,吹氮中不许来回打反车搅拌钢水,不许吹气大翻。
1.2.6 炉后吹气2分钟取大包样,碳当量不够喂碳线,再吹气不小于3分钟。
1.2.7 平台上氧气停用时要及时关闭阀门,以保证安全和节约用氧,氧气管道、氧气阀门附近不准吸烟和动火,不准有易燃易爆物,不准敲击,不准缠绕电线,氧气阀门不准接触油污。
1.2.8吹炼过程中应经常检查氮封口氮封情况及下料口情况,如氮封不正常,立即通知维修人员修复。
1.2.9 严格稳定装入量及供氧制度,装入量波动控制在±1吨,氧压<0.6Mpa时停吹。
1.2.10 经常检查炉衬侵蚀情况,尤其是操作不正常炉次,严格按计划补炉,保证补炉效果,防止漏炉事故发生。
开新炉、新补炉,在吹炼时要密切注意炉壳情况,发现炉壳发红或漏钢应立即提枪出钢。
1.2.11 经常清理炉口粘渣,严禁在看不见火焰的情况下冶炼。
1.2.12经常检查烟道、烟罩、炉口水箱等渗漏情况,氧枪或烟罩、烟道漏水成线严禁炼钢,炉内进水禁止动炉,待水分蒸发完后方可动炉。
包钢炼钢厂50吨转炉设计

包钢炼钢厂50吨转炉设计摘要:一、包钢炼钢厂50 吨转炉设计的背景和意义二、50 吨转炉的设计原理和关键技术三、50 吨转炉的设计流程和实施步骤四、50 吨转炉设计的优势和预期效果五、总结正文:一、包钢炼钢厂50 吨转炉设计的背景和意义包钢炼钢厂是我国重要的钢铁生产基地之一,一直以来都在为国家的经济发展和社会进步做出重要贡献。
为了提高生产效率,降低生产成本,提升产品质量,包钢炼钢厂决定设计一款50 吨转炉。
这款转炉的设计,不仅可以满足市场需求,还能推动钢铁行业的技术进步,具有重要的现实意义和深远的历史意义。
二、50 吨转炉的设计原理和关键技术50 吨转炉的设计原理主要是利用高温下的氧化还原反应,将铁矿石还原成纯铁。
在这个过程中,需要对炉内温度、压力、氧气浓度等进行精确控制,以保证钢铁的质量和产量。
关键技术包括高温熔融技术、氧气控制技术、炉内压力控制技术等。
三、50 吨转炉的设计流程和实施步骤设计50 吨转炉的过程可以分为两个阶段,第一阶段是设计阶段,主要包括确定转炉的规模、结构、材料等;第二阶段是实施阶段,主要包括转炉的制造、安装、调试等。
在设计阶段,需要进行详细的设计计算,以确定转炉的各项参数。
在实施阶段,需要严格按照设计要求进行,以保证转炉的正常运行。
四、50 吨转炉设计的优势和预期效果50 吨转炉的设计,可以大幅提高炼钢的效率和质量,降低生产成本。
预期效果主要包括提高钢铁产量、降低生产成本、提高产品质量等。
此外,50 吨转炉的设计,还能推动我国钢铁行业的技术进步,提升我国钢铁行业的国际竞争力。
五、总结包钢炼钢厂50 吨转炉的设计,是一项重要的技术创新,对于提高我国钢铁行业的技术水平,推动我国钢铁行业的发展具有重要的作用。
包钢炼钢厂50吨转炉设计
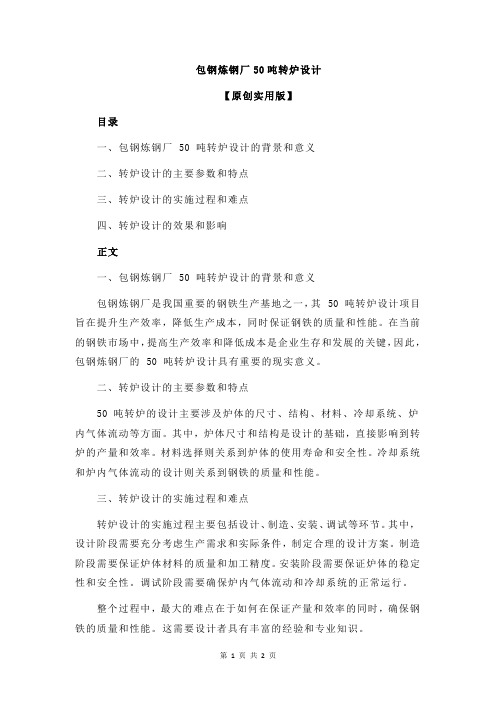
包钢炼钢厂50吨转炉设计
【原创实用版】
目录
一、包钢炼钢厂 50 吨转炉设计的背景和意义
二、转炉设计的主要参数和特点
三、转炉设计的实施过程和难点
四、转炉设计的效果和影响
正文
一、包钢炼钢厂 50 吨转炉设计的背景和意义
包钢炼钢厂是我国重要的钢铁生产基地之一,其 50 吨转炉设计项目旨在提升生产效率,降低生产成本,同时保证钢铁的质量和性能。
在当前的钢铁市场中,提高生产效率和降低成本是企业生存和发展的关键,因此,包钢炼钢厂的 50 吨转炉设计具有重要的现实意义。
二、转炉设计的主要参数和特点
50 吨转炉的设计主要涉及炉体的尺寸、结构、材料、冷却系统、炉内气体流动等方面。
其中,炉体尺寸和结构是设计的基础,直接影响到转炉的产量和效率。
材料选择则关系到炉体的使用寿命和安全性。
冷却系统和炉内气体流动的设计则关系到钢铁的质量和性能。
三、转炉设计的实施过程和难点
转炉设计的实施过程主要包括设计、制造、安装、调试等环节。
其中,设计阶段需要充分考虑生产需求和实际条件,制定合理的设计方案。
制造阶段需要保证炉体材料的质量和加工精度。
安装阶段需要保证炉体的稳定性和安全性。
调试阶段需要确保炉内气体流动和冷却系统的正常运行。
整个过程中,最大的难点在于如何在保证产量和效率的同时,确保钢铁的质量和性能。
这需要设计者具有丰富的经验和专业知识。
四、转炉设计的效果和影响
50 吨转炉的设计成功实施后,包钢炼钢厂的生产效率得到了显著提升,生产成本得到了有效控制,同时钢铁的质量和性能也得到了保证。
年产50万t钢转炉炼钢厂工艺设计本科设计

年产50万t钢转炉炼钢厂工艺设计本科设计(2013届)本科毕业设计(论文)资料题目名称:年产 510万t钢转炉炼钢厂工艺设计学院(部):冶金工程学院专业:冶金工程学生姓名:王盼班级:冶金工程092 学号: 09495200127指导教师姓名:高泽平职称:教授最终评定成绩:湖南工业大学教务处2013届本科毕业设计资料第一部分毕业设计说明书(2013届)本科毕业设计(论文)题目名称:年产510万t钢转炉炼钢厂工艺设计学院(部):冶金工程学院专业:冶金工程学生姓名:王盼班级:冶金工程092 学号: 09495200127指导教师姓名:高泽平职称:教授最终评定成绩:2013年6月湖南工业大学本科毕业设计诚信声明本人郑重声明:所呈交的毕业设计,题目《年产510万t钢转炉炼钢厂工艺设计》是本人在指导教师的指导下,进行研究工作所取得的成果。
对本文的研究作出重要贡献的个人和集体,均已在文章以明确方式注明。
除此之外,本设计不包含任何其他个人或集体已经发表或撰写过的作品成果。
本人完全意识到本声明应承担的责任。
作者签名:日期:年月日摘要本设计简要叙述了转炉炼钢技术的发展趋势。
根据设计说明书要求,结合本专业所学理论知识设计一座年产510万t合格铸坯的转炉炼钢车间。
选取了两座250t顶底复吹转炉。
采用了先进且具有较大发展余地的工艺流程:铁水预处理→转炉→精炼→连铸。
为提高钢材质量并符合高效连铸的要求,车间配备LF、VD和RH精炼设备。
本设计整个生产过程由计算机自动进行动态和静态控制。
主要设计内容包括:物料平衡与热平衡计算;转炉炉型及氧枪设计;主要技术经济指标的确定;厂房布置。
为了更加详细说明转炉车间设计中的一些工艺及设备结构,本设计穿插了图形,为能够明确、直观的介绍了转炉炼钢车间的工艺布置。
设计方案以技术新,效益高为原则,并充分体现了其可持续发展性。
关键词:转炉炼钢;物料平衡;热平衡;工艺流程ABSTRACTThe design briefly described the development trends of converter steelmaking technology. According to the demand of the design explanation combined the knowledge of metallurgy subject learned before to design an annual output of 5.1million tons of converter steel mill slab qualified. Two BOF blowing converters with the capacity of 250t have been selected.It choosed the process flow which is advanced and possess greater space for development: Molten iron pretreatment→Converter→Refining→Continuous casting. In order to improve the quality of steel and keep with the needs of high-efficiency continuous casting, workshops are provided with LF, VD and RH refining device. Computer being operated automatically control the technological process of whole plant dynamically and satirically. The design includes: the balance of material and quantity of heat; the design of furnace shape and oxygen lance; the settlement of major technological and economic quota; layout of the workshopFor more detailed description of some of the converter workshop design technology and equipment structure, the design with graphics, which can clear,intuitive introduces converter steelmaking plant process arrangement.Design program is based on new technique and high profit, it presents sustainable development either.Keywords: Converter steel making; Material balance; Heat balance; Process flow湖南工业大学本科毕业设计(论文)目录第1章绪论 (1)1.1 选题背景 (1)1.2 我国钢铁工业现状 (1)1.3 国外钢铁工业现状 (1)1.4 现代转炉炼钢工工艺流程与新技术 (1)1.4.1 铁水预处理 (1)1.4.2 转炉炼钢 (1)1.4.3 炉外精炼 (2)1.4.4 连续铸钢 (2)1.5 节能环保技术 (2)1.6 转炉炼钢技术发展趋势 (2)第2章设计概述 (3)2.1 厂址选择论证 (3)2.2 产品方案 (3)2.3 金属平衡 (4)2.4 转炉车间作业指标 (5)2.4.1 转炉作业率 (5)2.4.2 铸坯收得率 (5)2.5 转炉容量和座数的确定 (5)第3章物料平衡与热平衡计算 (6)3.1 原始数据的选取 (6)3.1.1 原材料成分 (6)3.1.2 假设条件 (7)3.2 物料平衡计算 (7)3.2.1 渣料及其成分计算 (7)3.2.2 冶炼中吹损计算 (11)3.2.3 氧气消耗量计算 (11)3.2.4 炉气量及成分计算 (12)3.2.5 物料平衡表 (12)3.3 热平衡计算 (13)3.3.1 热收入 (13)3.3.2 热支出 (14)3.3.3 热平衡表 (15)3.4 吨钢物料平衡 (15)第4章转炉炉型设计 (17)4.1 转炉炉型的选择 (17)4.2 转炉炉容比比高宽比 (17)4.2.1 炉容比 (17)4.2.2 高宽比 (17)4.3 转炉主要尺寸确定 (17)4.3.1 熔池尺寸 (17)4.3.2 炉帽尺寸 (17)4.3.3 炉身尺寸 (18)4.3.4 出钢口尺寸 (18)4.3.5 炉衬 (18)4.3.6 炉壳 (19)4.3.7 高径比确定 (19)4.4 炉壳设计 (20)4.5 炉衬各层填充材料的选择 (20)第5章氧枪及底部供气构件设计 (21)5.1 氧枪设计 (21)5.1.1 氧气流量 (21)5.1.2 工况氧压和喉口直径 (21)5.1.3 喷孔出口直径 (21)5.1.4 喷孔其他几何尺寸 (22)5.1.5 枪身各层钢管 (22)5.1.6 氧枪长度的确定 (23)5.2 转炉底部供气构件设计 (23)5.2.1 底气种类 (23)5.2.2 底气用量 (23)5.2.3 供气构件 (23)5.2.4 底吹元件布置 (23)第6章生产工艺设计 (24)6.1 装料制度 (24)6.2 供养制度 (24)6.3 造渣制度 (25)6.3.1 炉渣碱度的控制与石灰加入量的确定 (25)6.3.2 炉渣黏度的控制 (25)6.3.3 炉渣氧化性的控制 (25)6.3.4 泡沫渣及其控制 (26)6.3.5 放渣及留渣操作 (26)6.4 温度制度 (26)6.5 终点控制和出钢 (26)6.6 脱氧制度及合金化 (27)第7章车间主要设备的设计 (28)7.1 原料跨主体设备 (28)7.1.1 混铁车的设计 (28)7.1.2 废钢料斗的计算 (28)7.2 转炉跨主体设备 (29)7.2.1 钢包的计算 (29)7.2.2 渣罐数量的确定 (29)7.3 精炼跨主体设备 (30)7.3.1 钢包吹氩设备布置 (30)7.3.2 LF炉设备与工艺布置 (30)7.3.3 RH真空循环脱气装置工艺布置 (31)7.4 连铸机参数的确定 (31)7.5 车间起重机的选择 (33)第8章主厂房工艺布置 (34)8.1 原料跨间布置 (34)8.2 转炉跨间布置 (35)8.2.1 横向布置 (36)8.2.2 转炉跨各层平台的确定 (37)8.3 转炉跨起重机轨面标高 (39)8.4 连铸机设备的布置 (40)第9章转炉车间烟气净化与回收 (43)9.1 转炉烟气与烟尘 (43)9.1.1 转炉烟气 (43)9.1.2 烟尘的特征 (43)9.2 烟气净化方案的选择 (43)9.2.1 炉口附近烟气处理方法 (44)9.2.2 转炉烟气净化方法 (44)9.3 烟气净化系统 (44)9.4 烟气净化回收系统主备 (44)9.4.1 烟罩 (44)9.4.2 静电除尘器 (45)9.4.3 煤气柜 (45)结论 (46)参考文献 (47)致谢 (48)第1章绪论1.1 选题背景本设计题目根据目前国内外转炉炼钢生产车间的生产状况,意在将学生四年的学习的基础和专业知识加以综合运用,并结合现有先进技术,对钢铁企业炼钢生产车间和连铸车间的工艺布置及主体设备进行设计和计算,从而对钢铁生产过程具有更加深刻的理解。
50T转炉技术协议

1、总则;1.1 新建一座50T氧气顶吹炼钢转炉1.2 项目设计范围;转炉本体、转炉倾动、氧抢升降、氧抢横移、活动烟罩、汽化冷却、烟气净化、上料系统、一次除尘风机、二次除尘风机、煤气回收、中心水泵控制、软水系统控制、蒸汽能源利用、高低压供电系统。
辅助设备;散装料下料、钢包车、渣车、吹氧、吹氮、水冷却、电气自动化及仪表系统、工业图像监控等。
2、系统设计要求转炉本体部分转炉本体部分的设备控制系统主要有倾动控制系统、氧抢控制系统、氧气氮气控制系统、活动烟罩、炉前档火门、钢包车、渣盘车、散装料下料控制、汽化冷却系统的控制及操作。
2.1 转炉主控操作按工艺要求分为手动、自动、检修选择。
手动操作主要作为单体设备启动、停止操作但各个设备之间有安全连锁。
自动操作主要做为某些工艺操流程顺序自动动作,并与工艺安全连锁。
检修只是对某一单体设备操作,各个设备间没有连锁。
机旁操作箱用于单体设备的调试及检修,各设备间无任何联锁。
2.2 转炉倾动系统转炉倾动由4台45KW电机驱动,4台爱默生交流变频器由PLC 程序控制实现位置矢量闭环控制电机驱动倾动设备,画面可用校正角度位置。
转炉兑铁、出钢、倒渣、加废钢和测温取样时采用低速控制操作,其余操作为快速动作,按工艺要求可以调整速度。
倾动转动方向为正反两个旋转360度,两地进行操作;主控室、炉后操作台。
主控室选择操作权限,主控室控制兑铁水、加废钢、出渣、测温,炉后控制操作出钢,炉后操作完毕后把控制操作权限交换给主控室,完成工艺流程操作。
倾动角度为主令控制器及编码器反馈双向控制。
转炉倾动控制必须有安全连锁条件;活动烟罩在下限位转炉倾动不能倾动;氧抢处在待吹为以下转炉不能倾动;倾动液压站油泵没有启动,油压没有达到允许条件不能倾动,有故障时允许解除连锁;倾动在零位、出渣位、出钢位自动停止,主令回零位复位后可用继续操作。
倾动保护装置;保证转炉倾动设备平衡启动停止,必须在驱动电机回路先建立起一定力矩后才能松开抱闸启动电机。
转炉设计书0

第一章转炉炉型选型设计及相关参数计算1转炉炉型设计1.1.1 炉型选择氧气顶底复吹转炉是20世纪70年代中、后期,开始研究的一项新炼钢工艺。
其优越性在于炉子的高宽比略小于顶吹转炉却又大于底吹转炉,略呈矮胖型;炉底一般为平底,以便设置底部喷口。
综合以上特点选用转炉炉型为锥球型(适用于中小型转炉见图1-1)。
图1-1 常见转炉炉型(a)筒球型;(b)锥球型;(c)截锥型1.1.2 主要参数的确定本设计选用氧气顶吹转炉(公称容量50t)。
(1) 炉容比炉容比系指转炉有效容积与公称容量之比值。
转炉炉容比主要与供氧强度有关,与炉容量关系不大。
从目前实际情况来看,转炉炉容比一般取0.9~1.05m3/t。
本设计取炉容比为1.05m3/t。
(2) 高径比转炉高径比,通常取1.35~1.65。
小炉子取上限,大炉子取下限。
本设计取高径比:1.40。
(3) 熔池直径D可按以下经验公式确定:tG KD = (1-1)式中 D ——熔池直径,m ;G ——新炉金属装入量,t ,可取公称容量; K ——系数,参见表1-1;t ——平均每炉钢纯吹氧时间,min ,参见表1-2。
表1-1 系数K 的推荐值表1-2 平均每炉钢冶炼时间推荐值注:括号内数系吹氧时间参考值。
设计中转炉的公称容量为50t ,取K 为1.85,t 取15min 。
可得:38.3155085.1==D m(4) 熔池深度h锥球型熔池倒锥度一般为12°~30°,当球缺体半径R=1.1D 时,球缺体高h1=0.09D 的设计较多。
熔池体积和熔池直径D 及熔池深度h 有如下的关系:23665.0033.0DD V h +=池 (1-2)由池V G 1ρ=可得:09.705.7501===ρGV 池(m 3)将池V 代入式(7-2)得:98.038.3665.038.3033.009.7665.0033.02323=⨯⨯+=+=DD V h 池(m)(5) 炉身高度身H转炉炉帽以下,熔池面以上的圆柱体部分称为炉身。
t顶底复吹转炉炉型设计说明书DOC

目录前言 (1)一、转炉炉型及其选择 (1)二、炉容比的确定 (3)三、熔池尺寸的确定 (3)四、炉帽尺寸的确定 (5)五、炉身尺寸的确定 (6)六、出钢口尺寸的确定 (6)七、炉底喷嘴数量及布置 (7)丿八、咼径比 (9)九、炉衬材质选择 (9)十、炉衬组成及厚度确定 (9)十一、砖型选择 (12)十二、炉壳钢板材质与厚度的确定 (14)十三、校核 (15)参考文献 (16)专业班级________ 学号____________ 姓名 _____________ 成绩 ____________前言:转炉是转炉炼钢车间的核心设备。
转炉炉型及其主要参数对转炉炼钢的生产率、金属收的率、炉龄等经济指标都有直接的影响,其设计是否合理也关系到冶炼工艺能否顺利进行,车间主厂房高度和与转炉配套的其他相关设备的选型。
所以,设计一座炉型结构合理,满足工艺要求的转炉是保证车间正常生产的前提,而炉型设计又是整个转炉车间设计的关键。
设计内容:100吨顶底复吹转炉炉型的选择与计算;耐火材料的选择;相关参数的选择与计算。
、转炉炉型及其选择转炉有炉帽、炉身、炉底三部分组成。
转炉炉型是指由上述三部分组成的炉衬内部空间的几何形状。
由于炉帽和炉身的形状没有变化,所以通常按熔池形状将转炉炉型分为筒球形、锥球型和截锥形等三种。
炉型的选择往往与转炉的容量有关。
炉帽•炉身炉底简球型H吒转炉常用炉量图(1)筒球形。
熔池由球缺体和圆柱体两部分组成。
炉型形状简单,砌砖方便,炉壳容易制造,被国内外大、中型转炉普遍采用。
(2)锥球型。
熔池由球缺体和倒截锥体两部分组成。
与相同容量的筒球型比较,锥球型熔池较深,有利于保护炉底。
在同样熔池深度的情况下,熔池直径可以比筒球型大,增加了熔池反应面积,有利于去磷、硫。
我国中小型转炉普遍采用这种炉型,也用于大型炉。
(3)截锥形。
熔池为一个倒截锥体。
炉型构造较为简单,平的熔池底较球型底容易砌筑。
在装入量和熔池直径相同的情况下,其熔池最深,因此一般不适用于大容量炉,我国30t以下的转炉采用较多。
炼钢工艺流程图

炼钢厂工艺流程与设备规格性能一、炼钢厂工艺流程图二、炼钢厂示意图1、转炉示意图及工艺参数工艺参数转炉炉体1.1炉体总高(包括炉壳支撑板):7050mm1.2炉壳高度:6820mm1.3炉壳外径:Φ4370mm1.4高宽比: H/D=1.561.5炉壳内径:Φ4290mm1.6公称容量:50t1.7有效容积:39.5m31.8熔池直径: Φ3160mm1.9炉口内径:Φ1400mm1.10出钢口直径:140mm1.11出钢口倾角(与水平):20°1.12炉膛内径:Φ3160mm1.13炉容比:0.79m3 /t.s1.14熔池深度:1133mm1.15炉衬厚度:熔池:500mm 炉身:500mm 炉底:465mm 炉帽:550mm 1.16炉壳总重:77.6t1.17炉衬重量:120t1.18炉口结构:水冷炉口1.19炉帽结构:水冷炉帽1.20挡渣板结构:双层钢板焊接式1.21托圈结构:箱式结构(水冷耳轴)倾动装置型式:四点啮合全悬挂扭力杆式(交流变频器调速)最大工作倾动力矩:100t*m最大事故倾动力矩:300t*m倾动角度:±360°倾动速度:0.2~1r/min二、方坯连铸示意图大包中包方坯弧形连铸机铸机基本参数:机型:全弧形铸机弧型半径:R6000/12000mm;机~流:5~5流间距:1250mm弯曲:连续弯曲矫直:连续矫直铸坯规格:120mm × 120mm;150mm × 150mm;100mm × 173mm;130mm × 173mm;拉速:120mm × 120mm 3.2~3.76 m/min;150mm × 150mm 2.0~3.0 m/min;100mm × 173mm; 2.8~3.4 m/min;130mm × 173mm; 2.0~3.0 m/min;冶金长度: 14.69 m(全凝固矫直);17.27 m(带液芯矫直)铸机长度:16.16m(铸机外弧基准线至固定挡板)定尺长度:3~6m铸机有效作业率:85%钢水收得率:96.8%设计年产量:80万吨/年三、板坯连铸大包中包结晶器板坯连铸机示意图铸机基本参数:机型:立弯式连铸机铸机弧型半径:6000mm;机~流:2~2流间距:4700mm弯曲:8点弯曲,R65000mm、R30600mm、R19300mm、R14000mm、R11000mm、R9000mm、R7200mm、R6000mm矫直:6点矫直,R6000mm、R7200mm、R9000mm、R11700mm、R16700mm、R31600mm 铸坯规格:150mm × 350~680mm;180mm × 350~680mm;200mm × 350~680mm;拉速:150mm × 350~680mm; V max:1.6 m/min; 180mm × 350~680mm; V max:1.5 m/min;200mm × 350~680mm; V max:1.2 m/min;冶金长度:17.43 m铸机长度:17.43 m定尺长度:6500m铸机有效作业率:82%钢水收得率:97%设计年产量:60万吨/年。
50t新概念超高功率电弧炉技术协议书
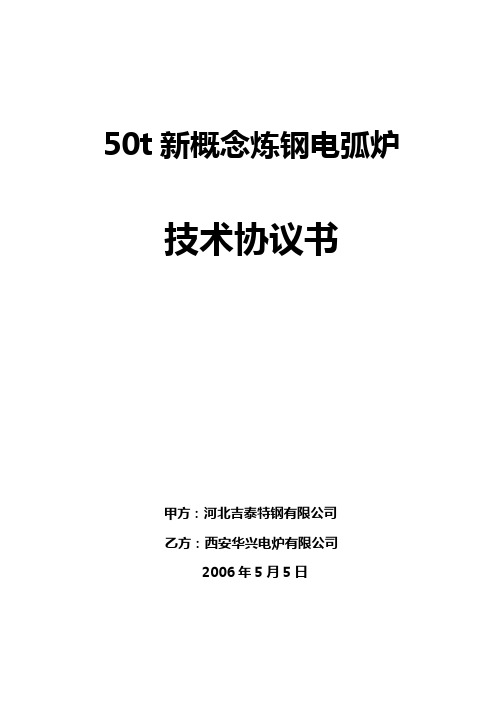
50t新概念炼钢电弧炉技术协议书甲方:河北吉泰特钢有限公司乙方:西安华兴电炉有限公司2006年5月5日目录一、前言二、50t新概念电弧炉主要技术参数三、机械设备说明四、电气设备说明五、供货范围明细六、设计范围和双方资料提供七、性能保证值八、设备的安装、检验及标准九、卖方主要设备分包方及制造厂家十、人员培训一、前言传统的炼钢电弧炉,废钢分二至三次从炉顶装入,依靠电极与废钢之间产生的电弧来熔化废钢。
因此,传统的电弧炉只能间断的向炉内送电,也就是间隔一段时间即停电,旋开炉盖装料。
这样便极大地降低了炉子的生产率,增加了炉子的热损失和能源消耗。
同时,大量烟尘,在装料时排放到厂房内,增加了除尘、环保的难度。
间断式的在电极与废钢间产生明弧,增大了对电网的冲击和噪音的危害等等。
针对以上问题,上世纪末,世界上相继出现了数种新型炼钢电弧炉。
炉子向着大型化、快节奏、连续式、低能耗、环保型的方向发展。
本炉型紧跟世界电炉炼钢发展趋势,消化、吸收各种炼钢新技术、新工艺,并为我所用。
结合我国国情,开发研制了新概念炼钢电弧炉。
新概念电弧炉从根本上改变了旋开炉盖向炉内加废钢的传统,克服了上述传统电弧炉的诸多弊端。
改变了人们对电弧炉的传统概念。
其加入废钢的方式是采用专用设备将废钢从上部加到密闭的竖井内,通过竖井内的手指,将经过预热的废钢加到竖井下部的料槽中,该料槽由振动式小车带动,采用专用的四轴激震式传动机构将料槽内的废钢连续地从炉体侧面加入炉内。
这样便将间断式地向竖井内加料变为连续地向炉内加料。
实现电弧炉全熔池操作。
高温烟气从炉体侧面进料口经烟道进入竖井,和废钢逆向而行,预热了废钢后,烟气从竖井上部排入烟道,经沉降室后进入除尘系统。
新概念电弧炉消化吸收了近年来炼钢生产中的新技术、新工艺,是结合我国国情,自主开发、设计的新炉型,经过科学技术项目查新,新概念电弧炉的设计思想和结构特点与查新的专利技术内容不同,是一种先进、新颖的新炉型,我公司具有自主知识产权。
转炉基础设计方案

转炉基础设计方案转炉是一种用于炼钢的重要设备,其基础设计方案的合理性和可靠性直接关系到整个冶金过程的正常进行和生产效益的提高。
下面给出一份转炉基础设计方案的700字示例:一、设计目标:该转炉设计旨在提高钢水质量和生产效率,并减少能源消耗和环境污染。
主要目标包括提高炉后合格品质率、降低转炉喷吹时间、增加钢水温度的恒定性和提高炉后脱氧效果。
二、转炉型号选择:根据生产工艺和产能需求,选用50吨中倾转炉作为目标型号。
该型号具有适中的产能和灵活的操作性能,能够满足生产需求。
三、结构设计:转炉底本身使用整体浇铸,底部设计防爆口,以应对突发情况。
炉身采用钢筋混凝土结构,增加了稳定性和耐磨性。
炉盖采用活动式结构,方便装卸料和维护。
四、吹氧系统设计:吹氧系统采用双面吹氧,以提高氧气利用率和搅拌效果。
吹风系统要求高压、大流量、稳定性好,并配备过滤装置,防止炉衬堵塞。
同时,安装可调节喷嘴,以便根据不同炼钢工艺的需要进行调整。
五、钢渣处理系统设计:为了提高钢渣处理效率,设计采用双辊倾转混渣机,以提高钢渣的处理速度和均匀度。
同时增加钢渣铺垫泥石圈,以提高钢渣的液流性和隔热性,减少热损失。
六、自动化控制系统设计:为了提高生产效率和产品质量,设计采用现代化的自动化控制系统。
通过温度传感器、压力传感器和氧气含量传感器等监控设备,及时获取各个指标的数据,并通过计算机控制中心进行集中处理,实现转炉的自动化操作。
七、安全防护措施设计:为了保障生产人员的安全,设计要求安装爆炸防护装置,实时监测转炉内部的温度和压力,并在超过设定值时及时报警。
此外,还要配备火焰探测器和自动灭火系统,以应对火灾和爆炸等紧急情况。
这是一份转炉基础设计方案的示例,能够满足提高钢水质量和生产效率的要求,并符合安全防护标准。
当然,实际设计还需根据具体情况进行细化和优化。
50t转炉课程设计

50t转炉课程设计一、课程目标知识目标:1. 学生能够理解并掌握50t转炉的基本结构及其在钢铁冶炼过程中的作用。
2. 学生能够描述50t转炉冶炼过程中的主要化学反应及物理变化。
3. 学生能够了解并解释50t转炉冶炼过程中的能量转换原理。
技能目标:1. 学生能够通过观察和实际操作,掌握50t转炉操作的基本步骤和安全规范。
2. 学生能够运用所学知识,分析并解决50t转炉冶炼过程中出现的问题。
3. 学生能够运用数据计算,评估50t转炉冶炼过程中的能源消耗和效率。
情感态度价值观目标:1. 培养学生对钢铁行业的热爱,激发他们投身于祖国钢铁事业的热情。
2. 培养学生的团队合作精神,使他们能够在实际操作中相互协作、共同进步。
3. 培养学生的环保意识,让他们认识到在钢铁冶炼过程中节能减排的重要性。
分析课程性质、学生特点和教学要求,本课程将目标分解为以下具体学习成果:1. 学生能够正确绘制50t转炉的结构示意图,并解释各部分功能。
2. 学生能够通过实验操作,演示50t转炉冶炼过程,并分析实验数据。
3. 学生能够编写50t转炉冶炼过程的操作规程,并提出安全防护措施。
4. 学生能够撰写关于50t转炉冶炼过程中的能量转换及环保措施的研究报告。
二、教学内容根据课程目标,本章节教学内容主要包括以下几部分:1. 50t转炉的结构与原理- 介绍50t转炉的构造、各部分功能及工作原理。
- 分析50t转炉在钢铁冶炼过程中的应用及优势。
2. 50t转炉冶炼过程及操作- 阐述冶炼过程中的化学反应、物理变化及能量转换。
- 解析冶炼过程中的关键操作步骤、安全规程及注意事项。
3. 50t转炉冶炼过程中的环保与节能- 探讨冶炼过程中的节能减排技术及措施。
- 分析我国钢铁行业在环保方面的政策及发展趋势。
教学大纲安排如下:第一课时:50t转炉的结构与原理- 引导学生认识50t转炉的构造,理解其工作原理。
- 教学内容关联教材第三章第一节。
第二课时:50t转炉冶炼过程及操作- 指导学生掌握冶炼过程的关键操作,了解安全规程。
某炼钢厂50吨转炉底吹系统技术方案及设备选型.doc

某炼钢厂50吨转炉底吹系统技术方案及设备选型-顶底复吹转炉改造1前言2炼钢厂改造前工艺及设备现状2.1工艺状况2.2设备状况转炉选用的是活炉底,耳轴只有3个通气孔,配套的旋转接头只3个通气孔,没有底吹阀门系统,转炉的控制系统为西门子控制系统,吹炼PLC为西门子S7400系列,操作画面是Wincc。
3改造方案确认3.1概述氮气、氩气送至底吹阀站,一个阀站对应一座转炉,阀站内有一条控制主管路,三条控制支管路,每条管线单独控制一块透气砖,管线设备有旁通阀。
从阀站出来的管线经转炉旋转接头送至底的透气砖上。
阀前氮气压力≥1.0~1.3Mpa,流量40~400Nm3/h。
3.2转炉底吹气工艺参数复吹型式:弱搅拌型复吹方式底吹气体种类:氮气(N2)底吹气体介质要求:氮气要求无油,气体杂质(特别是H2O,O2)含量小于百万分之一。
透气砖型式和块数(每座转炉):针管式透气砖3块3.3气路设计50吨转炉炉底透气砖设计为3块,现有转炉短耳轴旋转接头有5个通道,其中2个通道为炉帽冷却水通道,一进一出,另3通道进气管。
转炉底吹系统原则上设计成一个通道对应一块透气砖,能够实现一对一控制,如果一块砖堵塞,也不会影响另外砖的流量、压力控制。
3.4工艺设备旋转接头:安装在转炉耳轴上氮气供气通道,要求旋转接头通水与通气分开,通气通道内不会进水,配套选型旋转接头能满足工艺要求。
3.5控制仪表设备压力测量仪表:测量氮气总管和各支管的压力,信号送至PLC中,现场配有减振压力表。
快速切断阀:氮气总管和各支管配有快速切断控制并由PLC控制,能保证总管控制及各方管分开控制,总管总管压力调节阀:控制氮气总管压力,PLC控制,控制气源压力0.5~0.7MPa 电磁电源DC24V、输入信号ON/OF,公称通径DN50公称压力2.5MPa,输入信号4~20mA,调节后压力0~1.3MPa。
流量计:测量总管及各支管氮气体流量,信号送至PLC中,是控制底吹流量调节阀的关键。
马钢三钢厂50吨电弧炉自动控制系统设计—本科毕业设计

安徽工业大学毕业设计任务书学院、系:电气信息学院专业:自动化学生姓名:学号:设计题目:马钢三钢厂50吨电弧炉自动控制系统设计起迄日期: 2013年设计地点:安徽工业大学指导教师:系主任:发任务书日期:2013年02月25日毕业设计任务书毕业设计任务书摘要电弧炉是利用电弧的能量来熔炼金属的一种电炉。
电弧炉控制系统包括基础自动化和过程自动化。
它是一个多变量、非线性、强祸合、时变、工作环境恶劣及随机干扰性较强的系统,各种参数的多变使得系统电极位置、电弧长度、电弧电流/电压、系统功率及功率因数很难保持在最佳状态下运行,也一直阻碍着电弧炉过程控制技术的进一步发展。
电弧炉炼钢是靠电极和炉料间放电产生的电弧,使电能在弧光中转变为热能,并借助辐射和电弧的直接作用加热并熔化金属和炉渣,是冶炼某些特殊金属及合金必须使用的炼钢方法。
论文以马钢三钢厂50 吨电弧炉计算机控制系统为研究对象,在查阅了大量国内外相关文献的基础上,综述了电弧炉控制技术的发展历程、研究现状及今后的发展趋势。
根据电弧炉熔炼工艺对控制系统的控制要求,给出了控制系统总体设计方案,对电弧炉计算机控制系统的硬件系统配置作了详细的说明。
在电极调节器控制方案设计的基础上给出了实用的控制算法的实现方法,应用德国西门子公司S7-300 系列编程软件编写了整个控制系统控制软件,包括电极调节控制单元、液压站控制单元、真空开关合、分闸控制单元、变压器调压换档控制单元和其它逻辑控制单元。
电弧炉炼钢过程一般是以物料、热量和化学平衡为基础,采用理论与经验相结合的方法,建立的超高功率电弧炉冶炼工艺静态控制模型和动态控制模型,并对主要参数进行了计算。
静态模型的建立能确定主要操作参数的计算,并对钢质量影响较大的终点温度及碳的含量进行神经网络预报。
在电极调节器控制方案设计的基础上给出了实用的控制算法的实现方法,应用德国西门子公司S7-300 系列编程软件编写了整个控制系统控制软件,包括电极调节控制单元、液压站控制系统单元、真空开关合、分闸控制单元、变压器调压换档保护控制单元和水冷事故单元以及电弧炉炉体操作部分单元等其他控制单元。
- 1、下载文档前请自行甄别文档内容的完整性,平台不提供额外的编辑、内容补充、找答案等附加服务。
- 2、"仅部分预览"的文档,不可在线预览部分如存在完整性等问题,可反馈申请退款(可完整预览的文档不适用该条件!)。
- 3、如文档侵犯您的权益,请联系客服反馈,我们会尽快为您处理(人工客服工作时间:9:00-18:30)。
目录1.原始条件 42.炉型选择 43.炉容比的确定 44.熔池直径的计算 45.炉帽尺寸的确定 66.炉身尺寸的确定 67.出钢口尺寸的确定 68.炉衬厚度确定79.炉壳厚度的确定910.验算高宽比91序言现在钢铁联合企业包括炼铁,炼钢,轧钢三大主要生产厂。
炼钢厂则起着承上启下的作用,它既是高炉所生产铁水的用户,又是供给轧钢厂坯料的基地,炼钢车间的成产正常与否,对整个钢铁联合企业有着重大影响。
目前,氧气转炉炼钢设备的大型化,生产的连续化和高速化,达到了很高的生产率,这就需要足够的设备来共同完成,而这些设备的布置和车间内各种物料的运输流程必须合理,才能够使生产顺利进行。
转炉是炼钢车间的核心设备,设计一座炉型合理满足工艺需求的转炉是保证车间正常生产的前提,而炉型设计又是整个转炉设计的关键。
炉衬简介1 炉衬组成转炉炉衬由永久层,填充层和工作层组成。
永久层紧贴着炉壳钢板,通常是用一层镁砖或铝砖侧砌而成,其作用是保护炉壳。
修炉时一般不拆除炉壳永久层填充层介于永久层和工作层之间,一般用焦油镁砂或焦油白云石料捣打而成。
工作层直接与钢水,炉渣和炉气接触,不断受到物理的,机械的和化学的冲刷,撞击和侵蚀作用,另外还要受到工艺操作因素的影响,所以其质量直接诶关系到炉龄的高低。
国内外中小型转炉普遍采用焦油白云石或焦油镁砂质大砖砌筑炉衬。
为提高炉衬寿命,目前已广泛使用镁质白云石为原料的烧成油浸砖。
我国大中型转炉多采用镁碳砖。
2 炉衬砌筑(1) 砌筑顺序:转炉炉衬砌筑顺序是先测定炉底中心线,然后进行炉底砌筑,在进行炉身,炉帽和炉口的砌筑,最后进行出钢口炉内和炉外部分的砌筑。
(2) 砌筑要求①背紧,靠实,填满找平,尽量减少砖缝;2②工作层实行干砌,砖缝之间用不定型耐火材料填充,捣打结实;③要注意留有一定的膨胀缝.3 提高炉衬寿命的措施(1) 提高耐火材料的质量;(2) 采用均衡炉衬提高砌炉质量;(3) 改进操作工艺;(4) 转炉热态喷补;(5) 激光监测;(6) 采用溅渣护炉技术;3原始条件炉子平均出钢量为50t ; 铁水采用生铁水; 氧枪采用四孔喷头。
1. 炉型选择根据初始条件采用锥球型作为设计炉型。
转炉由炉帽、炉身、炉底三部分组成,转炉炉型是指由上述三部分组成的炉衬内部空间的几何形状。
有于炉帽和炉身的形状没有变化,所以通常按熔池形状将转炉炉型分为筒球型、锥球型和截锥型三种。
炉型的选择往往与转炉的容量有关。
所选50t 转炉属小型故用截锥型。
2. 炉容比的确定炉容比是指转炉有效容积V t 与公称容量G 的比值V t /G(m 3/t)。
V t 系炉帽、炉身和熔池三个内腔容积之和。
公称容量以转炉炉役期的平均出钢量来表示。
确定炉容比应综合考虑。
通常,铁水比增大,贴水中Si 、S 、P 行两高,用矿石作冷却剂以及供氧强度提高时,为了减少喷溅或溢渣损失,提高金属收得率和操作稳定性,炉容比要适当增大。
但过大的炉容比又会使基建和设备投资增加。
对于大型转炉,由于采用多孔喷枪和顶底复吹,操作比较稳定,因此在其他条件相同的情况下,炉容比有所减少。
转炉新砌炉衬的炉容比推荐值为0.90~0.95m 3/t ,大转炉取下限,小转炉取上限。
本题中,取炉容比取上限为0.95m ³/t.3. 熔池直径的计算① 熔池直径的计算 熔池直径的计算公式tGK D式中D--熔池直径,m ; G--新炉金属装入量,t ; t--吹氧时间,min ;K--比例系数,如表1所示。
表1 不同吨位下的K 值转炉吨位/t<30 30~100 >100 备注K1.85~2.101.75~1.851.50~1.75达容量取下限,小容量取上限4A . 确定初期金属装入量G :则m314.7750===ρG V 液(钢液的密度取t m /0.73)B . 确定吹氧时间:表2 平均每炉钢冶炼时间推荐值转炉容量/t<3030~100>100备注 冶炼时间/min28~32 (12~16) 32~38 (14~18) 38~45 (16~20)结合供氧强度,铁水成分和所炼钢种等具体条件确定。
取吨钢耗氧量为60m 3/t 钢,并取吹氧时间为15min (参见表2)。
则min /m341560(min))/m32∙===t t q o 供氧时间吨钢耗氧量(供氧强度K 取1.8 则mm G K D 328615508.1t =*==取3.286m氧气射流穿透深度mm nq T H o 980)(36.0)(36.0256.04450256.02=⨯=∙=⨯穿 ② 熔池深度的计算筒球型熔池深度的计算公式为:m tD V 156.1)286.3(574.0/m314.7574.0c h 22=⨯==深 W 为防止炉底直接接受氧气射流冲击,氧气射流穿透深度应小于熔池深度,一般应使深穿h H 〈本题中:深穿h H 〈符合要求。
所以确定D=3.286m,h=1.156m5即D=3286mm, h=1156mm4. 炉帽尺寸的确定① 炉口直径d炉口直径取43%的熔池直径m D 413.1m 286.343.0%43d =⨯==取d 为1413mm ② 炉帽倾角θ选取原则:便于炉气逐渐收缩逸出,减少炉气对炉帽衬砖的冲刷侵蚀;使帽锥各层砖逐渐收缩,缩短砌砖的错台长度,增加砌砖的稳定性。
如果角度值过大,砌砖错台太长容易脱落。
取︒=63θ. ③ 炉帽高度H 帽;取H 口=300mm ,则整个炉帽高度为:m tg H tg d D H 102.2mm 30063)413.1286.3(2/1)(2/1=+︒-=+-=∏θ帽 取H=2102mm在炉口设置水冷管水冷炉口。
虽然制作难度比较大但为安全考虑防止烧穿。
炉帽容积为:口口帽帽)(H d D D H H V 222d 785.0)d -(262.0-++=带入数据 ))(帽22413.1413.1286.3286.3(3.0-m 102.2262.0m m m m m V +⨯+=-0.785口H 2d =8.232m ³。
5. 炉身尺寸的确定① 炉膛直径D 膛=D (无加厚段)② 根据选定的炉容比为0.95,可求出炉子总容积为5.475095.0=⨯=总V m ³3333128.3214.7232.8m 5.47--m m m V V V V =--==池帽有效身③ 炉身高度m 791.342==DVH π身身取整H=3791mm6. 出钢口尺寸的确定出钢口尺寸一般都设在炉帽与炉身的交界处,以使转炉出钢时其位置最低,便于钢水全部出净。
出钢口的主要尺寸是中心线的水平倾角和直径。
① 出钢口直径6出钢口直径决定出钢时间,随炉子容量不同而异。
出钢时间通常为2至8分钟。
时间缩短(即出钢口过大),难以控制下渣,且钢包内钢液静压力增长过快,脱氧产物不易上浮。
时间过长(即出钢口过小),钢液容易二次氧化和吸气,散热也达。
通常按下面的公式来确定:cm 27.125075.16375.163=⨯+=+=T d 出取d=122.7mm ② 出钢口衬砖外径mm d d ST 614m 7.12255=⨯=⨯=出取=ST d 614mm ③ 出钢口长度859mm m 7.1227d 7=⨯==出T L取=ST L 859mm ④ 出钢口倾角θ:为了缩短出钢口长度以利于维修和减少钢液二次氧化及热损失,大型转炉θ趋于减小。
取︒=63θ7. 炉衬厚度确定通常炉衬由永久层、填充层、工作层组成。
有些转炉则在永久层和炉壳钢板之间夹有一层石棉板绝热层。
永久层紧贴炉壳(无绝热层时),修炉时一般不予拆除。
其主要作用是保护炉壳。
该层用黏土砖砌筑。
填充层介于永久层和工作层之间,一般用焦油镁砂捣打而成。
其主要作用是减轻炉衬受热膨胀时对炉壳产生挤压和便于拆除工作层。
炉帽可用二步煅烧镁砖,也可根据具体条件选用其他材质。
转炉各部位的炉衬厚度设计参考值如表3所示。
7表3 转炉炉衬厚度设计参考值炉衬各部分名称转炉容量/t<100 100-200 >200炉帽永久层厚度/mm60-115 115-150 115-150 工作层厚度/mm400-600 500-600 550-650炉身(加料侧)永久层厚度/mm115-150 115-200 115-200 工作层厚度/mm550-700 700-800 750-850炉身(出钢侧)永久层厚度/mm115-150 115-200 115-200 工作层厚度/mm500-650 600-700 650-700炉底永久层厚度/mm300-450 350-450 350-450 工作层厚度/mm550-600 600-650 600-750:炉衬选择应遵循以下原则:①耐火度高;②高温下机械强度高,耐极冷极热性能好;③化学性质稳定;④资源广泛,价格便宜。
根据如上850t 氧气顶吹转炉炉衬厚度选取炉帽永久层厚度/mm 80 工作层厚度/mm 500 炉身(加料侧)永久层厚度/mm 120 工作层厚度/mm 600 炉身(出钢侧)永久层厚度/mm 120 工作层厚度/mm 600 炉底永久层厚度/mm 400 工作层厚度/mm580选填充层100mm 选用焦油镁砂填料。
8. 炉壳厚度确定炉壳都采用60mm16Mn 钢。
则249.812.008.1156.1791.3102.2h =++++=++++=钢板炉衬身帽总H h H H H m 046.512.082.082.0286.3h =+++=++=钢板炉衬总D D D9. 验算高宽比增大高宽比有利于减少喷溅和溢渣、提高金属收得率。
但是高宽比过大,在炉膛体积一定时,反应面积过小,氧气流股易冲刷炉壁,对炉衬寿命不利;而且导致厂房高,基建费用大;转炉倾动力矩大,耗电大。
转炉高宽比推荐值为1.35-1.65。
63.1046.5249.8==总总D H符合转炉高宽比推荐值(1.35~1.65),因此认为所设计的炉子尺寸基本上是合适的。
能够保证转炉的正常冶炼进行。
9。