延迟焦化流程图及相关数据总结
延迟焦化装置吸收稳定系统工艺与操作要点ppt
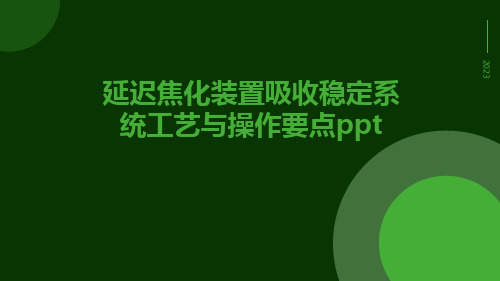
1 2
原料切割
将重油切割成小段,降低加热炉内的结焦倾向 。
加热和脱水
将原料加热到一定温度,并去除其中的水分和 轻质组分。
脱盐和脱硫
3
去除原料中的盐类和硫化物,防止腐蚀设备。
延迟焦化反应过程
加热炉加热
将原料加热到焦化反应所需温度。
焦化反应
原料在加热炉中发生裂解反应,生成气体、汽油 、柴油和重焦炭等产品。
对原料油的API、残碳、硫含量等性质进行严格把控,保 证进料质量。
原料加热
将原料加热到适当的温度,以便在焦化反应中达到最佳 效果。
进料方式选择
可选择连续进料或间歇进料方式,根据实际情况进行选 择。
反应条件优化
反应温度
01
通过控制加热炉出口温度,保证焦化反应在适宜的温度范围内
进行。
反应压力
02
通过控制分馏塔顶部压力,保证焦化反应在适宜的压力范围内
应用案例二:延迟焦化装置优化操作
优化背景
延迟焦化装置操作复杂,影响因素多,需要进行优化以提高装置的经济效益和环保性能。
优化内容
采用先进的在线监测和分析技术,对加热炉出口温度、压力,进料速度等关键参数进行实 时监测和调控。
优化效果
优化后装置运行更加稳定,产品质量和收率得到提高,同时降低了能耗和污染物排放。
2023
延迟焦化装置吸收稳定系 统工艺与操作要点ppt
目录
• 引言 • 延迟焦化装置工艺流程 • 操作要点 • 安全与环保 • 应用案例与效果展示
01
引言
目的和背景
介绍延迟焦化装置 吸收稳定系统的工 艺与操作要点
帮助企业优化生产 过程和提高经济效 益
为相关领域技术人 员提供操作指南
延迟焦化技术总结

代表技术
特点
应用情况
中国
石油化工科学研究院(RIPP)的技术
RIPP相继开发了多产轻质油品延迟焦化技术、针状焦生产技术、劣质渣油延迟焦化加工技术及含酸原油延迟焦化加工技术等多项新技术
中国石化、中国石油、中海油及部分地方炼油企业的绝大多数延迟焦化装置的基础设计数据都是由RIPP提供
2010年以来,我国逐步加大对外合作。在2011年中国石油、中国石化、中国海油三家分别与委内瑞拉和加拿大就能源方面展开了一系列合作。2011年初,中石油又与沙特阿美海外公司、俄罗斯石油公司、荷兰皇家壳牌公司、卡塔尔公司合作在中国各地相继建设炼油厂。2011年6月,中石化与科威特石油公司计划在广东建厂。由于进口原油大多是超重油,属于高密度、高黏度、高硫、高残炭、高金属、高沥青质的劣质原油,给炼油厂的加工提高了难度。因此,我国炼油工业面临着大量加工重质原油和含硫原油的严峻挑战。
采用低压、低循环比操作。
目前, Kellogg典型的焦炭塔操作压力为0.10~0.14MPa,装置的循环比可按0.05设计。
Lummus公司的延迟焦化技术
最大灵活性的设计;适应进料的变化;适应加工能力的变化;工艺设备设计的灵活性
目前,已有60余套装置采用了Lummus的延迟焦化技术。
由于原油价格的增长、焦炭和馏分油价格差距的增大,提高馏分油收率降低焦炭产率对提高炼油厂的经济效益十分有利。国外的延迟焦化装置以追求液体收率最大化为操作目标,国内通常以平稳运行和降低能耗为目的,操作条件相对缓和。国内外延迟焦化过程的主要操作条件对比见表1[19-20]。
石油作为最重要的能源和资源之一。随着世界经济的不断发展,常规石油资源日益减少,重质油资源逐渐成为大家关注的热点。近年来,发生在华尔街的金融危机和北非、中东地区的政局动荡对原油供给安全和全球能源价格产生了深远影响。随着我国经济快速发展,我国石油消费量从1980年的87.6Mt增长2011年490Mt,自1993年成原油净进口国以来,进口量逐年增大,2011年进口量达到251Mt,对外优存度达到56.5%,预计2020年进口量将达到600Mt,对外依存度接近70%。已成为世界第二大石油进出口国[5]。
延迟焦化工艺流程

延迟焦化工艺流程延迟焦化1. 延迟焦化工艺流程:本装置的原料为温度90℃的减压渣油,由罐区泵送入装置原料油缓冲罐,然后由原料泵输送至柴油原料油换热器,加热到135℃左右进入蜡油原料油换热器,加热至160℃左右进入焦化炉对流段,加热至305℃进入焦化分馏塔脱过热段,在此与来自焦炭塔顶的热油气接触换热。
原料油与来自焦炭塔油气中被凝的循环油一起流入塔底,在380~390℃温度下,用辐射泵抽出打入焦化炉辐射段,快速升温至495~500℃,经四通阀进入焦碳塔底部。
循环油和减压渣油中蜡油以上馏分在焦碳塔内由于高温和长时间停留而发生裂解、缩合等一系列的焦化反应,反应的高温油气自塔顶流出进入分馏塔下部与原料油直接换热后,冷凝出循环油馏份;其余大量油气上升经五层分馏洗涤板,在控制蜡油集油箱下蒸发段温度的条件下,上升进入集油箱以上分馏段,进行分馏。
从下往上分馏出蜡油、柴油、石脑油(顶油)和富气。
分馏塔蜡油集油箱的蜡油在343℃温度下,自流至蜡油汽提塔,经过热蒸汽汽提后蜡油自蜡油泵抽出,去吸收稳定为稳定塔重沸器提供热源后降温至258℃左右,再为解吸塔重沸器提供热源后降温至242℃左右,进入蜡油原料油换热器与原料油换热,蜡油温度降至210℃,后分成三部分:一部分分两路作为蜡油回流返回分馏塔,一路作为下回流控制分馏塔蒸发段温度和循环比,一路作为上回流取中段热;一部分回焦化炉对流段入口以平衡大循环比条件下的对流段热负荷及对流出口温度;另一部分进水箱式蜡油冷却器降温至90℃,一路作为急冷油控制焦炭塔油气线温度,少量蜡油作为产品出装置。
柴油自分馏塔由柴油泵抽出,仅柴油原料油换热器、柴油富吸收油换热器后一部分返回分馏塔作柴油回流,另一部分去柴油空冷器冷却至55℃后,再去柴油水冷器冷却至40℃后分两路:一路出装置;另一路去吸收稳定单元的再吸收塔作吸收剂。
由吸收稳定单元返回的富吸收油经柴油富吸收油换热器换热后也返回分馏塔。
分馏塔顶油气经分馏塔顶空冷器,分馏塔顶水冷器冷却到40℃,流入分馏塔顶气液分离罐,焦化石脑油由石脑油泵抽出送往吸收稳定单元。
延迟焦化工艺图

延迟焦化延迟焦化是应用最为广泛的一种焦炭化工业应用形式,是炼油厂提高氢转移收率的重要手段之一,在我国炼油工业中发挥着重要的作用。
(1) 延迟焦化的原料延迟焦化可以处理多种原料,如原油、常压重油、减压渣油、沥青等,以及硫含量较高、残炭值高达50%的残渣原料,甚至是芳香烃含量很高难以裂化的催化裂化澄清油和热裂解渣油等。
(2) 延迟焦化的产品特性延迟焦化的产品包括气体、汽油、柴油、蜡油和石油焦,其产率及性质在很大程度上取决于原料性质。
①气体。
焦化气体含有较多的甲烷、乙烷和少量烯烃。
②汽油。
焦化汽油含有较多的不饱和烃,并且含有较多的硫、氮等非烃化合物,其安定性较差。
③柴油。
焦化柴油的安定性差,残炭值高,以石蜡基原油的减压渣油为原料时所得焦化柴油的十六烷值较高。
④蜡油。
焦化蜡油的烃类组成和直馏蜡油基本相同,重金属含量较低,硫、氮含量较高,可用作催化裂化和加氢裂化的原料。
⑤石油焦。
石油焦是焦炭化过程的特有产品。
我国延迟焦化生产的石油焦属于低硫石油焦,一般硫含量小于2%。
从焦炭塔出来的生焦含有8~12%的挥发分,经1300℃煅烧可变成熟焦,挥发分降至0.5%以下,可用于冶炼工业和化学工业。
(3) 延迟焦化工艺流程延迟焦化的工艺流程如下图所示。
原料油换热后进入分馏塔下部,与来自焦炭塔的高温油气(430~440℃)换热,一方面加热原料油,将原料油中的轻质油蒸发出来,同时又将过热的焦化油气降至可进行分馏的温度。
原料油和循环油一起从分馏塔的塔底抽出,送至加热炉加热到500℃左右,然后经过四通阀进入焦炭塔底部。
热的原料油在焦炭塔内进行裂解、缩合等反应,最后生成焦炭。
焦炭聚集在焦炭塔内,反应油气自焦炭塔顶部逸出,进入分馏塔,得到焦化气、汽油、柴油、蜡油和循环油。
延迟焦化工艺流程示意图。
延迟焦化工艺流程

延迟焦化工艺流程延迟焦化工艺流程是一种能够将重质石油馏分转化为具有高热值和高炭素含量的焦炭的技术。
它是对传统的焦化工艺进行改进和优化,以减少生产焦炭过程中的环境污染和能源浪费。
延迟焦化工艺流程具有高效节能、环保低污染和资源综合利用的特点,在石油化工行业被广泛应用。
1.原料准备:在延迟焦化工艺中,主要原料为重质石油馏分,通常是从石油精炼过程中得到的渣油。
这些渣油首先被送入预处理装置,经过脱硫、脱水和脱盐等处理,以提高其炭含量和降低硫、氮等杂质的含量。
2.煤炭炭化:预处理后的渣油与煤炭混合后,进入煤气化炉进行炭化反应。
煤炭炭化过程中,渣油中的碳分子与煤炭中的碳分子发生化学反应,生成焦炭和煤气。
同时,煤炭中的含硫化合物也得到部分转化或吸附,以减小煤气中硫化物的含量。
3.煤气净化:产生的煤气含有一定的杂质,如硫化物、苯、酚等。
煤气进入净化装置,经过除硫、除苯等处理,使煤气中的有害物质达到排放标准,同时,其中的一部分能源也得到回收利用,用于工艺过程中的煤气加热等。
4.焦炭冷却:经过煤气净化后,煤气中的焦油被分离出来,作为石油化工原料的补充。
随后,焦炭经过冷却装置,使其温度降低至环境空气温度,以保证焦炭的质量和可收回的热能。
1.高效节能:延迟焦化工艺能够充分利用原料中的热能和化学能,使其转化为焦炭和煤气,减少能源浪费。
同时,延迟焦化过程中产生的煤气也能够回收利用,用于工艺过程中的能源供应。
2.环保低污染:延迟焦化工艺通过净化装置等设备对煤气中的有害物质进行处理,使得煤气排放达到环境保护要求。
此外,延迟焦化过程中采用的高效脱硫等技术能够显著降低硫化氢等有害气体的排放。
3.资源综合利用:延迟焦化工艺能够将废弃的重质石油馏分转化为焦炭和煤气,提高了资源的综合利用率。
同时,工艺中产生的焦油和焦炭也能够作为石油化工原料的补充,实现循环利用。
总之,延迟焦化工艺流程是一种高效、环保、资源综合利用的工艺,在石油化工行业有着广泛的应用和发展前景。
延迟焦化装置工艺及操作2006 精品

延迟焦化装置工艺及操作培训目标(一)精通延迟焦化生产操作,能组织、指挥装置生产;(二)解决装置的生产技术难题;(三)能对装置生产工况进行指导优化。
1、概述1.1焦化生产工艺简介一九三0年,第一套工业化生产的延迟焦化装置投产以来,焦化技术发展很快。
特别是一九三八年水力除焦技术在延迟焦化装置上应用后。
焦化方法有釜式焦化、平炉焦化、延迟焦化(Delayed Coking)、接触焦化和流化焦化(Fluid Coking)等五种。
其中延迟焦化,由于它的工艺技术简单、操作方便,装置的灵活性大,开工率高及开工周期长等优点,发展较快。
世界上85%以上的焦化处理能力都属于延迟焦化类型,只有少数国家(如美国)的部分炼油厂采用流化焦化。
1.2延迟焦化生产概况延迟焦化装置生产过程主要由焦化分馏部分、加热炉部分、焦炭塔部分、吸收稳定部分、干气及液化气脱硫部分、冷切焦水部分、吹汽放空部分组成。
1.3荆门分公司延迟焦化装置简介荆门分公司延迟焦化装置始建于一九七0年。
由北京设计院设计,当年建成、当年投产。
原设计处理能力40万吨/年,“一炉两塔”工艺;一九九六年由北京设计院和荆门石化总厂设计院对原装置进行扩能改造,处理能力提高到60万吨/年,“两炉四塔”工艺;一九九九年,由荆门石化总厂设计院设计了吸收脱硫系统,处理能力为4.8万吨/年,采用柴油单吸收流程;二00四年,仍由北京设计院和荆门石化总厂设计院共同对原装置进行改造,处理能力提高到100万吨/年,“三炉六塔”工艺,装置改造后增加了吸收稳定系统、液化气脱硫系统。
装置原料采用减压渣油掺兑20%比例的丙烷半沥青,还有部分催化装置油浆等。
吸收稳定、脱硫部分设计处理能力11万吨/年。
荆门分公司延迟焦化装置包括三炉六塔3个系列,焦化设计处理能力为100万吨/年,包括焦化、分馏、吸收稳定和干气液化气脱硫系统。
荆门分公司延迟焦化装置于1970年投产,几经改造于2004年11月扩能到100万吨/年。
延迟焦化焦炭塔系统
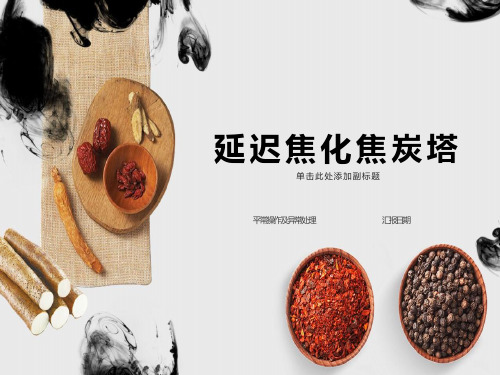
原因 预热油气量太小 油气循环线结焦或堵塞 温度测量或指示故障
塔底油甩不出去
新塔预热时顶温上不去
原因: 塔底进料线被焦堵塞 甩油泵不上量 甩油线流程有误
01
D106底过滤器堵塞
02
新塔预热时底温上不去
原因: 换塔是吹汽不及时或汽量太小,造成粘油堵塞焦炭孔道 给水阀门坏
给水泵出口压力表坏
冷焦水给不进去或进水量很小
焦炭塔塔壁变形示意图
胜利炼油厂3号焦炭塔塔壁变形的 间直径大,中下部变化大,顶部较小;中下部东西直径大,南北直径小,成为椭圆形状
01
塔体下封头筒体环焊缝以上第二至第四道圈板之间变形最大。
02
塔体环焊缝处变形较小,多年来基本无变化。
03
塔体变形量达一定数值后,渐趋缓慢。
延迟焦化焦炭塔
平常操作及异常处理
汇报日期
单击此处添加副标题
生焦操作
除焦操作
除焦操作
除焦操作
、焦炭塔的塔体变形、开裂及可能产生的腐蚀
焦炭塔塔体变形 焦炭塔塔体由于长期处于冷、热交变的操作下,受热应力影响,易发生塔体鼓胀变形,经对国内八家炼厂的焦炭塔进行调查(88年秋)有5家有明显变形,变形部位多在塔体下部,塔壁径向鼓凸,呈糖葫芦状。塔壁的鼓凸变形过程如下图。
冲塔
原因: 炉出口温度偏低,泡沫层升高 处理量大,生焦超过安全高度 系统压力波动波动太大 新塔预热温度不够 换塔时,新塔油没有甩净 原料性质变化 注汽量太大
四通阀切换不过去或油线蹩压
原因: 方向搞错 四通阀没给汽封或汽封过小,阀内结焦 切换方向错误或配合不当 管线堵塞或隔断阀未开
炉出口温度变化太大
04
塔体变形的规律
底盖泄露或着火
简述延迟焦化工艺流程

简述延迟焦化工艺流程延迟焦化工艺流程,那可真是个挺有趣的东西呢。
一、原料准备。
咱先说这原料啊,一般就是减压渣油之类的。
这些原料被送到装置里,就像是一群小士兵,要开始它们的奇妙之旅啦。
这些原料的性质可重要了呢,如果原料太稠或者杂质太多,那后面的工序可能就会有点小麻烦。
就好比你做饭,食材要是不新鲜或者没处理好,做出来的菜可能就不太美味啦。
二、加热炉加热。
然后啊,这些原料就被送到加热炉里去加热。
加热炉可就像一个大火炉,给原料们加足了热量。
这个时候,原料的温度会变得特别高,就像是被火烤得热烘烘的小土豆。
在加热的过程中,原料会发生一系列的反应,像是分子结构开始有了变化。
这就好比是一个人在经历了一场火热的历练之后,内心和外在都有了改变一样。
三、焦炭塔反应。
从加热炉出来后,原料就进入了焦炭塔。
在焦炭塔里,那可就是大变化的地方喽。
原料在这里会发生热裂解和缩合反应。
热裂解就像是把一个大的团体打散成一个个小的个体,而缩合反应呢,就像是这些小个体又重新组合起来,不过组合的方式可不一样啦。
慢慢地,在焦炭塔里就会形成焦炭和油气。
焦炭就像是沉淀在塔底的小硬块,而油气就像是轻盈的小仙子,它们要继续往别处去呢。
四、分馏过程。
接着,从焦炭塔出来的油气就进入了分馏塔。
分馏塔就像是一个大的分拣器,把油气按照不同的沸点分成不同的产品。
就像你把一堆不同颜色的小珠子按照颜色分类一样。
比如说,轻汽油、柴油、蜡油这些产品就被分出来了。
这个过程可不能马虎,要是分馏得不好,那产品的质量可就没法保证啦。
就像你把东西分类分错了,后面用的时候肯定会出问题。
五、焦炭处理。
再说说焦炭塔底部的焦炭吧。
这些焦炭可是不能一直留在塔里的,得把它们弄出来。
这就像是清理家里的垃圾一样,要及时处理。
有的时候是通过水力除焦的方式,就像用水枪把焦炭冲出来,这个过程看着还挺带劲的呢。
把焦炭处理好了,焦炭塔才能继续迎接下一轮的原料反应。
六、产品精制。
最后呢,那些分馏出来的产品也不是就直接能用啦,还得经过精制。
延迟焦化工艺过程

3.2.1 延迟焦化工艺过程延迟焦化工艺是焦炭化过程(简称焦化)主要的工业化形式,由于延迟焦化工艺技术简单,投资及操作费用较低,经济效益较好,因此,世界上85%以上的焦化处理装置都采用延迟焦化工艺。
延迟焦化工艺基本原理就是以渣油为原料,经加热炉加热到高温(500℃左右),迅速转移到焦炭塔中进行深度热裂化反应,即把焦化反应延迟到焦炭塔中进行,减轻炉管结焦程度,延长装置运行周期。
焦化过程产生的油气从焦炭塔顶部到分馏塔中进行分馏,可获得焦化干气、汽油、柴油、蜡油、重蜡油产品;留在焦炭塔中的焦炭经除焦系统处理,可获得焦炭产品(也称石油焦)。
减压渣油经焦化过程可以得到70%左右的馏分油。
焦化汽油和焦化柴油中不饱和烃含量高,而且含硫、含氮等非烃类化合物的含量也高。
因此,它们的安定性很差,必须经过加氢精制等精制过程加工后才能作为发动机燃料。
焦化蜡油主要是作为加氢裂化或催化裂化的原料,有时也用于调和燃料油。
焦炭(也称石油焦)除了可用作燃料外,还可用作高炉炼铁之用,如果焦化原料及生产方法选择适当,石油焦经煅烧及石墨化后,可用于制造炼铝、炼钢的电极等。
焦化气体含有较多的甲烷、乙烷以及少量的丙烯、丁烯等,它可用作燃料或用作制氢原料等石油化工原料。
从焦化过程的原料和产品可以看到焦化过程是一种渣油轻质化过程。
作为轻质化过程,焦化过程的主要优点是它可以加工残炭值及重金属含量很高的各种劣质渣油,而且过程比较简单、投资和操作费用较低。
它的主要缺点是焦炭产率高及液体产物的质量差。
焦炭产率一般为原料残炭值的1.4~2倍,数量较大。
但焦炭在多数情况下只能作为普通固体燃料出售,售价还很低。
尽管焦化过程尚不是一个很理想3的渣油轻质化过程,但在现代炼油工业中,通过合理地配置石油资源和优化装置结构,它仍然是一个十分重要的提高轻质油收率的有效途径。
近年来,对用于制造冶金用电极,特别是超高功率电极的优质石油焦的需求不断增长,对某些炼油厂,生产优质石油焦已成为焦化过程的重要目的之一。
延迟焦化介绍

化物含量一般可以控制在800ppm左右。再生碱液质量高、 碱液循环使用周期长,碱渣率大幅度降低。环保效益明显。 常温氧化再生工艺不需要蒸汽加热和循环水冷却,节能降 耗。
焦化液化气液膜脱硫介绍
原料:胺洗后焦化液化气(脱除H2S后)、硫醇硫,以S 计正常值3500-5000ppm,最大值8000ppm、流量15t/h。
切焦水处理采用高速离心分离、过滤、罐式贮存等技术, 减少占地和环境污染。
吸收稳定采用典型的四塔流程
茂名焦化工艺流程
原料部分 分馏系统 加热炉系统 焦碳塔系统 压缩机系统 吸收稳定系统 冷切焦水系统 放空、吹汽系统 除焦系统
延迟焦化生焦周期
典型焦碳塔生焦周期采用24小时生焦,国内惠州炼油420万吨/年采用18 小时生焦。国外普遍采用18、16小时生焦。茂名两套焦化采用20小时。 203:40 AM小时与24小时对比处理能力增加20%。
采用高效的梯型浮阀塔板,提高分馏的操作弹性,更适 合优化分馏塔的操作工况。设柴油、中段油、蜡油和原 料渣油的换热器,尽可能的利用分馏塔的过剩热来加热 原料,提高热利用率。同时由于原料和中段油、蜡油、 柴油均有换热,便于分馏塔取热比例的调整和换热后渣 油温度的控制。在工艺流程设计中,采用分馏塔内直接 换热和馏分油外循环的技术调节循环比。
低温热利用没有,影响能耗降低。
操作影响因素
延迟焦化主要影响因素有三个,影响到 焦化产品分布和质量,也就是加热炉出 口温度、焦化塔顶压力、循环比。
温度
在一定的温度和循环比下,石油焦的收 率随反应温度升高而降低。 部分较重烃 类分子在低温下会留在焦化塔内转化为 石油焦,当温度升高时会变为油气由塔 顶逸出。 事实上,温度可调范围很小。 延迟焦化是一个绝热反应,炉出口温度 是焦化反应温度的控制点。
延迟焦化装置工艺过程简述及工艺流程简图

延迟焦化装置工艺过程简述及工艺流程简图2.1 工艺流程简述原料渣油(包括催化油浆及常Ⅲ洗涤油等)从装置外来,进入原料缓冲罐(V1101),经原料油泵(P1101/1、2)抽出升压后,先与柴油换热至181℃(E1101/1、2),接着与中段油换热至227℃(E1102/1、2),最后与蜡油换热至289℃ (E1103/1~4)后分两路进入分馏塔,一路进入分馏塔(T1102) 下段换热区与来自焦炭塔(T1101/1、2)的高温油气接触换热,高温油气中的循环油馏分被冷凝,原料油与冷凝的循环油一起进入分馏塔底,另一路直接进入分馏塔底部。
分馏塔底油经辐射进料泵入口过滤器FI1102/1、2过滤后由辐射进料泵(P1102/1~2)升压后进入加热炉(炉1101),经对流室和辐射室加热至490~505℃出加热炉,经过四通阀进入焦炭塔(T1101/1、2)底部。
在焦炭塔内经过高温和长时间停留,原料油和循环油在焦炭塔内发生一系列复杂的裂解、缩合等反应,最后生成焦炭和油气。
生成的高温油气自焦炭塔顶逸出去分馏塔下段换热区,焦炭在塔内沉积生焦并储存在塔内。
当焦炭塔生焦到一定高度后停止进料,切换到另一个焦炭塔内进行生焦。
切换后,老塔用蒸汽进行小吹汽,将塔内残留油气吹至分馏塔回收,小吹汽结束后改大吹汽、给水进行冷焦,焦炭塔大吹汽、给水冷焦时产生的大量高温蒸汽及少量油气进入接触冷却塔(T1103),接触冷却塔底的污油由接触冷却塔底泵(P1112/1、2)抽出,经水箱冷却器(WC1105)冷却后,部分作为T1103顶回流,部分送入本装置污油罐经脱水后做急冷油回炼。
塔顶蒸汽及轻质油气经塔顶空冷器、水冷器后入接触冷却塔顶油气分离器(V1106)分离,分离出的污油送入本装置污油罐,污水经接触冷却塔顶污水泵(P1113/1、2)升压后送入冷焦水热水灌(V1401),不凝气进入低压瓦斯管网。
进入分馏塔(T1102)下段换热区的高温油气与原料油直接接触换热后,冷凝下来的循环油进入分馏塔底,大量油气经过5块洗涤板后进入蜡油集油箱以上进行分馏,从下往上分别切割出蜡油、柴油、汽油和富气等馏分。
延迟焦化工艺流程(总4页)

延迟焦化工艺流程(总4页)-CAL-FENGHAI.-(YICAI)-Company One1-CAL-本页仅作为文档封面,使用请直接删除炼油厂的炼油工艺流程介绍上传时间:2009-07-31 12:03 点击:110正文:延迟焦化、加氢精制、制氢工艺流程工艺流程简述前言:根据济南炼油厂、海化集团等公司的延迟焦化装置、加氢装置、制氢装置的工艺流程整理而成。
并参考洛阳设计院、北京设计院、华西所提供材料。
一、100万吨/年延迟焦化装置本装置原料为减压渣油,温度为150℃,由常减压装置直接送入焦化装置内与柴油换热,换热后温度为170℃,进入原料油缓冲罐(D-101)。
原料油缓冲罐内的减压渣油由原料油泵抽出,与热蜡油经过两次换热再进加热炉对流段(Ⅱ)加热后分两股入焦化分馏塔(C-102)下段的五层人字挡板的上部和下部,在此与焦炭塔(C-101/1,2)顶来的油气接触,进行传热和传质。
原料油中蜡油以上馏分与来自焦炭塔顶油气中被冷凝的馏分(称循环油)一起流入塔底,在384℃温度下,用加热炉幅射进料泵抽出打入加热炉幅射段,在这里快速升温至500℃,然后通过四通阀入焦炭塔底。
循环油和原料油中蜡油以上馏分在焦炭塔内由于高温和长停留时间,产生裂解和缩合等一系列复杂反应,最后生成油气(包括富气、汽油、柴油和蜡油),由焦炭塔进入分馏塔,而焦炭则结聚在焦炭塔内。
从焦炭塔顶逸出的油气和水蒸气混合物进入分馏塔,在塔内与加热炉对流段来的原料换热,冷凝出循环油馏分,其余大量油气从换热段上升进入蜡油集油箱以上的分馏段,在此进行传热和传质过程,分馏出富气、汽油、柴油和蜡油。
焦化分馏塔油集油箱的蜡油经换热至90℃出装置进蜡油罐;另外引出两分路90℃冷蜡油作焦炭塔顶急冷油和装置封油用。
中段回流经中段回流蒸汽发生器发生蒸汽。
分馏塔顶回流从分馏塔抽出,经冷却后返回。
柴油从分馏塔进入汽提塔,经蒸汽汽提,柴油由汽油塔下部抽出,经换热冷却至70℃后分成两路,一路至加氢装置;另一路冷却至40℃进入柴油吸收塔作吸收剂来自压缩富气分液罐的富气进入柴油吸收塔下部,经吸收后,塔顶干气出装置进入全厂燃料气管网;塔底吸收油利用塔的压力(表)自压入分馏塔作回流。
延迟焦化流程图及相关数据总结

1.延迟焦化工艺在炼油厂重油深加工中作用世界重油加工能力构成2.延迟焦化工艺特点--通过调节温度、压力和循环比等参数增加操作弹性不同循环比减渣焦化产品收二.延迟焦化工艺流程若呼给水一■n#屐的中瓦斯油不印箱典型的延迟焦化工艺流程-可调循环比焦化工艺流程典型的延迟焦化工艺流程--CONOCO焦化零自然循环原则流程放空系统流程延迟焦化装置放空系统流程图放空系统流程-美国ABB Lunnns 公司延迟焦化装置放空流程 滤器空冷器 分离罐d放宁塔甩油罐来去火炬或—.污油系统Y 去切焦水/冷焦水素建 * ---- -去污油系统 竺雪 ------- 1去分储塔蒸汽一 焦炭处理系统流程--直接装3.操作压力延迟焦化装置操作压力对产品收率的影响焦化原料焦化产品原油:威尔明顿原油焦化汽油,%(质) 12.0 12.4 实沸点(TBP )切割温度,℃: 552相对密度d 15.6L 05360.79360.7923相对密度,d i5.6 : 1.0536 硫含量,%(质) 1.4 1.3 康氏残炭值,%(质):20.6 焦化瓦斯油,%(质) 37 3 33 3 硫,%(质):2.4 相对密度醯A15.60.9402 0.9352 焦炭塔操作压力,MPa 0.10550.2461 硫含量,%(质) 1.8 1.8 产品收率焦炭,%34.6 37.8 干气和LPG,%(质)16.1 16.5 焦炭硫含量,%(质)2.42.4补充水去放空系统焦炭塔压力对焦化馏出油产率的影响联合循环比(TPR)对焦化液体产品收率的影响联合循环比对大庆减压渣油焦化产品收率的影响焦化工艺参数优化延迟焦化产品收率及焦化重瓦斯油的质量比较焦化工艺参数优化生产加氢裂化原料的延迟焦化装置产品收率。
延迟焦化工艺流程.pptx

延迟焦化工艺流程
想一想,练一练
1、延迟焦化工艺组成由有几种部分?
焦化部分
分馏部分
水力除焦部分
焦化气体回收和 脱硫
焦炭焙烧部分
2、延迟焦化过程主要设备有哪些?
加热炉
焦炭塔
分馏塔
谢谢观看
课程:石油炼制运行与操控 知识点:延迟焦化工艺流程
江苏省高校品牌专业——石油化工技术
所谓延迟是指将焦化油(原料油和循环油)经过加热炉加热迅速升温至焦化反应温度,在反应 炉管内不生焦,而进入焦炭塔再进行焦化反应,故有延迟作用,称为延迟焦化技术。
延迟焦化工艺流程
一、延迟焦化概述
原料:延迟焦化原料可以是重油、渣油、甚至是沥青。延迟焦化产物分为气体、汽油、 柴油、蜡油和焦炭。
优缺点:延迟焦化可处理残碳和金属含量很高的劣质原料,提高轻质油的收率和脱碳效 率;有操作连续化、处理量大、灵活性强、脱碳效率高、投资和操作费用低的优点。 缺点是低价值产品焦炭产率高,液体产品性质差。
延迟焦化原理流程图 1-加热炉;2-焦炭塔;3-分馏塔
延迟焦化工艺流程
二、延迟焦化工艺
焦化分馏塔的特点: ①塔的底部是换热段, 新鲜原料与高温反应 油气换热,同时把反 应油气中携带的焦炭 粉末淋洗下来; ②塔底油循环避免塔 底结焦和堵塞。
延迟焦化工艺流程
340 - 350℃
裂解和缩合
快速升温
三、主要焦化流程
脱水和储运系 统
蒸汽发生部 分
吹气放空系 统
焦炭焙烧部 分
延迟焦化工艺流程
二、延迟焦化工艺
在加热炉管中温度很高, 为了防止原料油在炉管中 结焦,必须向炉管中注水 提高原料油在炉管中的线 速度,减少原料油在炉管 中的停留时间(一般仅为 几秒钟),从而避免炉管 结焦,而将结焦过程延迟 在焦炭塔中进行。
第3章延迟焦化
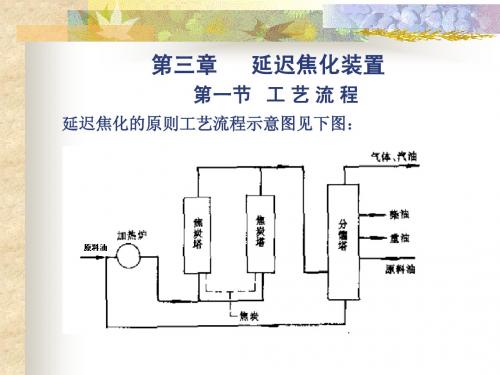
3.蠕变
20g在400℃以上即可产生蠕变, ℃的蠕变极限为 的蠕变极限为56MPa. 20g在400℃以上即可产生蠕变,450 ℃的蠕变极限为56MPa. 以上即可产生蠕变
(五)焦炭塔顶部腐蚀原因 五 焦炭塔顶部腐蚀原因 1、顶部塔壁腐蚀较重的部位,其塔外壁均有焊接件, 顶部塔壁腐蚀较重的部位,其塔外壁均有焊接件, 因塔壁外焊接件处保温效果不好,传热较快, 因塔壁外焊接件处保温效果不好,传热较快,达不到结焦 温度,内壁无结焦层附着于塔壁,致使塔壁裸露而被腐蚀。 温度,内壁无结焦层附着于塔壁,致使塔壁裸露而被腐蚀。 2、塔的泡沫段内壁腐蚀较重是因为由于介质波动造 成冲刷,使得塔壁上附着的焦层被冲刷掉, 成冲刷,使得塔壁上附着的焦层被冲刷掉,从而造成较重 的腐蚀。 的腐蚀。
二、腐蚀原因
(一) 一 高温硫腐蚀的原因
1、高温硫腐蚀范围 高温硫对设备的腐蚀从240 ℃开始,随着温度升高而迅 开始, 高温硫对设备的腐蚀从 速加剧, 左右达到最高点,以后又逐渐减弱。因此, 速加剧,到480 ℃左右达到最高点,以后又逐渐减弱。因此 腐蚀发生的温度范围为240—500℃。 腐蚀发生的温度范围为 ℃ 2.高温硫腐蚀的过程 . 详见第一章常减压装置
2.2 1.6 1.3 3.2
第五节
防
护
措
施
一、焦炭塔的防护措施 各炼油厂焦炭塔存在的缺陷表现为:塔体局部变形,焊 各炼油厂焦炭塔存在的缺陷表现为:塔体局部变形, 缝开裂及顶部腐蚀、防护措施主要为: 缝开裂及顶部腐蚀、防护措施主要为: (—)防止塔体变形和焊缝开裂措施 防止塔体变形和焊缝开裂措施
第六节
设备选材
轻微腐蚀:原料油总含硫量小于1.2%,酸值小于0.5mgKOH/g 轻微腐蚀:原料油总含硫量小于1.2%,酸值小于0.5mgKOH/g 1.2% 严重腐蚀:原料油总含硫量大于等于1.2%,酸值大于等于0.5mgKOH/g 严重腐蚀:原料油总含硫量大于等于1.2%,酸值大于等于0.5mgKOH/g 1.2%
延迟焦化工艺和参数
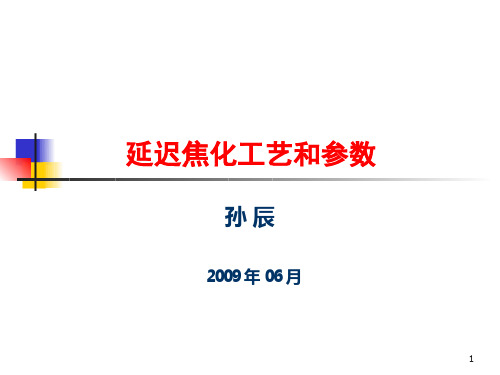
15
二 . 延迟焦化工艺流程
• 典型的延迟焦化工艺流程 • 放空系统流程 • 焦炭处理系统流程
16
二 . 延迟焦化工艺流程
1. 典型的延迟焦化工艺流程
• 延迟焦化是一种主要的重油加工工艺,通过热裂化和缩合反应使
重质烃类轻质化
• 常规延迟焦化装置由焦化、分馏(有的包括气体回收)、焦炭处
理、放空系统和冷、切焦水处理等几个部分所组成
2. 放空系统流程 - 美国 ABB Lunnns 公司延迟焦化装置放空流程 塔顶冷凝水可去切焦水和/或 冷焦水系统回用
回收的污油可去分馏塔回用 轻烃气体可密闭利用作燃料 气
25
二 . 延迟焦化工艺流程
2. 放空系统流程
•
国内现已设计的全密闭放空系统在放空塔底增设塔釜温度控制的 塔底油循环加热器,以保证塔釜油脱水和除焦粉。这种工艺流程 具有如下特点:
32
三 . 延迟焦化基本参数
1. 原料性质 作为轻质化加工手段
• 高酸值高稠原油,可考虑用延迟焦化匹配原油予处理的联合工艺, • 普通高稠原油可按照“稀释→换热→深度电脱盐脱水→加热→闪馏
→或初馏→焦化”流程进行加工
• 塔河油常渣、辽河稠油渣油、沙轻减渣、伊朗油和科威特油减渣等
高沥青质含量、高残炭、低热稳定性的焦化料,建议不要采用超低 循环比操作条件,避免在加热炉管及主分馏塔底结焦;选用具有在 线清焦技术的双面辐射炉型;在工艺设计中考虑选择性瓦斯油外循 环流程,以增加产品方案灵活性和延长焦化炉运行周期,并且可以 避免弹丸焦的生成
3. 焦炭处理系统流程 -- 焦池装车
焦池装车系统流程图
28
二 . 延迟焦化工艺流程
3. 焦炭处理系统流程 -- 储焦坑装车
延迟焦化工艺流程

2.循环比
▪ 循环比=循环油/新鲜原料油
▪ 联合循环比=(新鲜原料油量+循环油量)/新鲜原料油量=1+循环比
循环比增大,可使焦化汽油、柴油收率增加,焦化蜡油收率减少,焦 炭和焦化气体的收率增加。
降低循环比也是延迟焦化工艺发展趋向之一,其目的是通过增产焦化 蜡油来扩大催化裂化和加氢裂化的原料油量,再通过加大裂化装置处理 量来提高成品汽、柴油的产量。另外,在加热炉能力确定的情况下,低 循环比还可以增加装置的处理能力。降低循环比的办法是减少分馏塔下 部重瓦斯油回流量,提高蒸发段和塔底温度。
36
本章小结:
1. 减粘裂化
目的:是为了减小高黏度燃料油的黏度和倾点,改善其输送和燃烧性能
原料:常压重油、减压渣油和脱沥青油
产品:低黏度的燃料油;少量的轻质馏分油和气体产品
工艺流程:主要分无反应塔的减粘工艺和有反应塔的减粘工艺
影响因素:原料的组成和性质;裂化温度;裂化压力及反应时间等 37
返回 本章
33
3.操作温度 1.它的变化直接影响到炉
管内和焦炭塔内的反应深 度,从而影响到焦化产物 的产率和性质。
2.提高焦炭塔温度将使气体和 石脑油收率增加,瓦斯油收 率降低。焦炭产率将下降, 并将使焦炭中挥发分下降。
3.焦炭塔温度过高,容易造成泡沫 夹带并使焦炭硬度增大,造成除焦 困难。温度过高还会使加热炉炉管 和转油线的结焦倾向增大,影响操 作周期。
34
4.焦炭塔温度过低,则焦 化反应不完全将生成软焦 或沥青。
它的变化直接影响到炉管 内和焦炭塔内的反应深度, 从而影响到焦化产物的产 率和性质。
提高焦炭塔温度将使气体和 石脑油收率增加,瓦斯油收 率降低。焦炭产率将下降, 并将使焦炭中挥发分下降。
延迟焦化工艺参数优化及操作控制

0.05MPa,液体收率平均增加1.3%,焦炭产率下降1%。国内 典型操作压力为0.15-0.2MPa,目前新设计的装置设计压力为 0.1MPa。 如果生产针状焦,应采用高压:1.03MPa以上。
操作压力对产品收率的影响
焦化原料 原油:威尔明顿原油 实沸点切割温度:552℃ 汽油收率/% 12.0 12.4 1.3 1.3
4.原料在焦炭塔内反应生成焦炭,聚积在焦炭塔 内,油气从焦炭塔顶出来进入分馏塔,不原料油
换热后,经过分馏得到气体、汽油、柴油和蜡油。
塔底循环油和原料一起再进行焦化反应。
焦化生成的焦炭留在焦炭塔内,通过水力除焦从
塔内排出。
延迟焦化装置所产气体、汽油,分别用气体压缩
机和泵送入吸收稳定部分进行分离得到干气及液
与塔底泵抽空。
④由于受换热流程中热流体温位限制,加热炉进料温度最高为330℃, 降低了加热炉进料泵苛刻度。
⑤焦化新鲜原料渣油不进入分馏塔内与高温油气接触,对稳定、提高蜡
油产品质量有利。 ⑥提高了调节循环比的灵活性,可实现零循环比操作。
2 降低焦化操作压力
延迟焦化发展趋是降低操作压力:当焦炭塔压力为
③低循环比使焦化炉进料油性质变差,残炭及沥青质含量增加, 炉管内结焦可能性及结焦速率增加。 ④ 当 循 环 比 < 0.15 时 , 主 分 馏 塔 下 部 换 热 段 温 度 可 能 升 高 到
390℃以上,将有裂化、综合反应发生,导致分馏塔下部结焦, 影响操作。
三、焦化工艺参数优化
1. 焦化循环比优化 国外常规焦化装置循环比小于0.15,低循环比焦化装置小于0.05, 此外还有单程焦化(零循环比)。 国内焦化装置循环比一般高于0.15,甚至高达0.4。如果要改造 为低循环比焦化,需要对分馏塔下部结构、蒸发段上部各回注取 热负荷的分配与焦化加热炉进行改造。对缺乏二次加工蜡油加氢 精制装置的炼厂,改造困难。 循环比增加,蜡油干点下降,中沸点馏分增加,质量得到改善。
- 1、下载文档前请自行甄别文档内容的完整性,平台不提供额外的编辑、内容补充、找答案等附加服务。
- 2、"仅部分预览"的文档,不可在线预览部分如存在完整性等问题,可反馈申请退款(可完整预览的文档不适用该条件!)。
- 3、如文档侵犯您的权益,请联系客服反馈,我们会尽快为您处理(人工客服工作时间:9:00-18:30)。
1. 延迟焦化工艺在炼油厂重油深加工中作用
世界重油加工能力构成
2. 延迟焦化工艺特点--产品的灵活性焦炭塔压力及不同渣油焦化产品收率
2. 延迟焦化工艺特点--通过调节温度、压力和循环比等参数增加操作弹性
二. 延迟焦化工艺流程
典型的延迟焦化工艺流程-可调循环比焦化工艺流程
典型的延迟焦化工艺流程--CONOCO焦化零自然循环原则流程
放空系统流程
延迟焦化装置放空系统流程图
放空系统流程-美国ABB Lunnns公司延迟焦化装置放空流程
焦炭处理系统流程--直接装车
延迟焦化装置操作压力对产品收率的影响
焦化产品
12.0 12.4
0.7936 0.7923
1.4 1.3
焦炭塔压力对焦化馏出油产率的影响
联合循环比(TPR)对焦化液体产品收率的影响
联合循环比对大庆减压渣油焦化产品收率的影响
焦化工艺参数优化
延迟焦化产品收率及焦化重瓦斯油的质量比较
焦化工艺参数优化
生产加氢裂化原料的延迟焦化装置产品收率
项目
氮含量,ppm 庚烷不溶物,ppm 康氏残炭值,%(质) 特性因数,(K) 分馏试验,℃
10%(体)
50%(体)
干点
项目
焦化产品收率
干气,%(体)
液化气,%(体)
石脑油,%(体)
焦化轻瓦斯油,%(体) 焦化重瓦斯油,%(体) 焦炭,%(质)
焦化重瓦斯油性质
相对密度
镍+钒,ppm
康氏残炭值,%(质)。