双循环流化床半干法烟气悬浮脱硫工艺
(仅供参考)半干法烟气脱硫技术

0.45 0.4
0.35 0.3
0.25 0.2
123 4 5
1——f=1.0 2——f=0.8 3——f=0.6 4——f=0.4
5——f=0.2
0.15
B
0.1
0.05
A
0 0 20 40 60 80 100 120 140 160 180 200
q℃
半干法烟气脱硫工艺基本概念
) ppm及mg/Nm3 1ppm=2.86 mg/Nm3
– 式中:A:脱硫装置统计期间可运行小时数。
–
B:脱硫装置统计期间强迫停运小时数。
–
C:脱硫装置统计期间强迫降低出力等效停运小时数。
) 脱硫效率 脱硫效率 = C1 − C2 ×100% C1
– 式中,C1:脱硫前烟气中SO2在同一含氧量下的折算浓度;
–
C2:脱硫后烟气中SO2在同一含氧量下的折算浓度。
) BLI (Boiler Limestone Injection Activation) 锅炉石灰石喷射活化工艺
SDA(Spray Drying Absorption) 旋转喷雾干燥脱硫技术
• 旋转喷雾干燥法烟气脱硫技术是80年代迅速发展起来的一种新兴脱硫工艺。
• 目前世界上装有这种脱硫装置的发电机组总容量超过15000MW,已投入正常 运行的超过6000MW,单机容量超过500 MW,这些装置主要用于燃用中低硫煤 的电厂烟气脱硫。
半干法烟气脱硫工艺常用术语
) 脱硫岛 – 指脱硫装置及为脱硫服务的建(构)筑物 .
) 吸收剂
– 指脱硫工艺中用于吸收硫氧化物等有害物质的反应剂,本工艺的吸收剂是氢 氧化钙和氧化钙(Ca(OH)2和CaO)
) 一级除尘器(或预除尘器) – 布置在吸收塔进口,用以除去锅炉出口烟气中飞灰的除尘器 .
半干法烟气脱硫技术介绍

一.总流程描述清华同方环境有限责任公司的循环流化床半干法烟气脱硫工艺是在清华大学热态实验研究的基础上,开发的具有自主知识产权的循环流化床半干式烟气脱硫技术。
清华同方循环流化床半干法烟气脱硫工艺总流程描述如下:锅炉空气预热器出口烟气首先经过预除尘器,除去绝大部分粉煤灰,一般除尘效率设定为85%,预除尘器的作用主要是使大部分粉煤灰得以回收和进行后续的再利用;从预除尘器出来的烟气从循环流化床脱硫塔的底部经文丘里喷管进入脱硫塔中,消石灰粉料通过气力输送形式喷入脱硫塔,流态化的物料和烟气中的二氧化硫等酸性气体在脱硫塔中发生化学反应,脱除掉大部分的二氧化硫等酸性气体;雾化水通过水喷嘴均匀的喷射进入脱硫塔使烟气均匀降温,使脱硫反应达到最佳反应状态;然后烟气经过脱硫塔的顶部排出,经袋式除尘器除去绝大部分细灰;袋式除尘器除下的灰部分经过空气斜槽进入脱硫塔循环利用,以提高脱硫剂的利用率,布袋除尘器的另部分灰由仓泵打入脱硫灰库;处理后的干净烟气经过引风机排入烟囱。
流程图见附图1。
图1 流程图二.分系统描述循环流化床半干法烟气脱硫系统主要包括:流化床脱硫塔系统、消石灰制备及供给系统、循环灰返料系统、除尘系统、工业水供给系统等几部分组成(1)流化床脱硫塔系统循环流化床半干法烟气脱硫技术是在锅炉尾部利用循环流化床技术进行烟气脱硫,脱除烟气中的大部分二氧化硫、达到排放要求。
该技术具有如下特点:①主要以消石灰、飞灰等作循环物料,脱硫塔内固体颗粒浓度均匀,固体内循环强烈,气固混合、接触良好,气固间传热、传质十分理想。
②在脱硫塔直接喷水增湿,达到最佳的反应温度。
固体颗粒之间的强烈接触摩擦,造成脱硫塔中气、固、液三相之间极大的反应活性和反应表面积,对于塔内二氧化硫的去除,达到非常理想的效果。
③固体物料经布袋除尘器收集,再经空气斜槽回送至脱硫塔,使脱除剂反复循环,在反应器内的停留时间延长,从而提高吸收剂的利用率,降低运行成本。
④在脱硫塔体适当部位增设喷水点,调节脱硫塔内脱硫反应的温度始终保持在烟气酸露点温度10 ℃以上,同时取得较佳的脱硫反应温度,保证脱硫效率,无结垢,无腐蚀。
火力发电循环流化床半干法脱硫技术简介
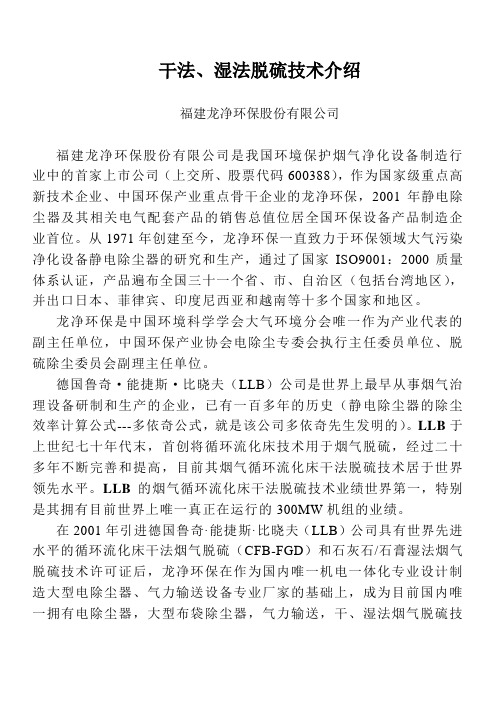
干法、湿法脱硫技术介绍福建龙净环保股份有限公司福建龙净环保股份有限公司是我国环境保护烟气净化设备制造行业中的首家上市公司(上交所、股票代码600388),作为国家级重点高新技术企业、中国环保产业重点骨干企业的龙净环保,2001年静电除尘器及其相关电气配套产品的销售总值位居全国环保设备产品制造企业首位。
从1971年创建至今,龙净环保一直致力于环保领域大气污染净化设备静电除尘器的研究和生产,通过了国家ISO9001:2000质量体系认证,产品遍布全国三十一个省、市、自治区(包括台湾地区),并出口日本、菲律宾、印度尼西亚和越南等十多个国家和地区。
龙净环保是中国环境科学学会大气环境分会唯一作为产业代表的副主任单位,中国环保产业协会电除尘专委会执行主任委员单位、脱硫除尘委员会副理主任单位。
德国鲁奇·能捷斯·比晓夫(LLB)公司是世界上最早从事烟气治理设备研制和生产的企业,已有一百多年的历史(静电除尘器的除尘效率计算公式---多依奇公式,就是该公司多依奇先生发明的)。
LLB于上世纪七十年代末,首创将循环流化床技术用于烟气脱硫,经过二十多年不断完善和提高,目前其烟气循环流化床干法脱硫技术居于世界领先水平。
LLB的烟气循环流化床干法脱硫技术业绩世界第一,特别是其拥有目前世界上唯一真正在运行的300MW机组的业绩。
在2001年引进德国鲁奇·能捷斯·比晓夫(LLB)公司具有世界先进水平的循环流化床干法烟气脱硫(CFB-FGD)和石灰石/石膏湿法烟气脱硫技术许可证后,龙净环保在作为国内唯一机电一体化专业设计制造大型电除尘器、气力输送设备专业厂家的基础上,成为目前国内唯一拥有电除尘器,大型布袋除尘器,气力输送,干、湿法烟气脱硫技术研发、设计、制造、安装综合服务能力的高水平的专业环保企业。
一.烟气循环流化床(CFB-FGD)干法脱硫工艺1.工艺描述1.1工艺流程从工艺流程图表明(见图1):一个典型的CFB-FGD系统由吸收塔、除尘器、吸收剂制备系统、物料输送系统、喷水系统、脱硫灰输送及存储系统、电气控制系统等构成。
循环流化床半干法烟气脱硫超净排放技术分析
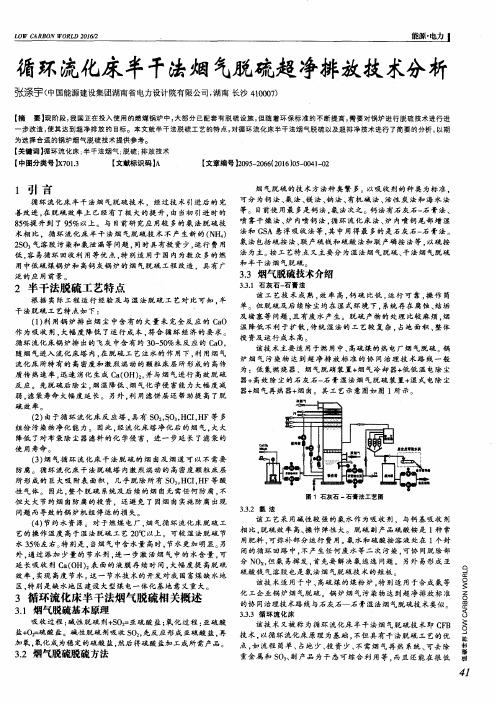
图 1石灰石 一石膏法工艺图
问题 而导 致 的 锅 炉 机 组 停 运 的损 失 。
3_3.2 氨 法
(4)节 约 水 资 源 。 对 于 燃 煤 电 厂 ,烟 气循 环 流 化床 脱 硫 工
器+烟 气再 热 器+烟 囱。 其 工 艺 示 意 图如 图 1所 示 。 弱 .滤 袋寿 命 大幅 度 延 长 。 另 外 ,利 用 滤 饼 层 还 帮助 提 高 了脱
硫 效 率 。 (2)由 于循 环 流 化床 反 应 塔 ,具 有 SO2,so3,HCI,HF等 多
西
t:=墓
—_。‘
Байду номын сангаас
温 降 低 不 利 于 扩散 ,传 统 湿 法 的 工 艺较 复 杂 ,占地 面积 、整 体 投 资及 运 行 成 本 高 。
该 技 术 主 要 适 用 于 燃 用 中 、高 硫 煤 的 热 电厂 烟 气脱硫 。锅
炉 烟 气 污 染 物 达 到 超 净 排 放 标 准 的 协 同 治 理 技 术 路 线 一 般 流 化 床 所 特 有 的 高 密 度 和 激 烈 湍 动 的 颗 粒 床 层 所 形 成 的 高 传
巡 -l Ⅲ● 一0皿 1. 露.
所 形 成 的 巨大 吸 附 表 面积 , 几 乎 脱 除 所 有 SO3,HCI,HF等 酸
性 气体 。 因此 ,整 个 脱硫 系统 及后 续 的 烟 囱无 需 任 何 防腐 ,不 但 大 大节 约 烟 囱防 腐 的 投 资 .还 避 免 了 因 烟 囱实施 防 腐 出现
组 份 污染 物 净 化 能 力 。 因此 。经 流 化床 塔 净 化 后 的 烟 气 .大 大 降低 了对 布 袋 除 尘 器 滤 料 的 化 学侵 害 .进 一 步 延 长 了滤 袋 的 使 用 寿 命
半干法脱硫技术方案(1)

3×75t锅炉烟气脱硫除尘工程总承包技术方案业主方:总包方:山东先进能源科技有限公司二○一八年三月目录1、技术规范 (2)1.1工程范围 (2)1.1.1设计范围: (2)1.1.2设计内容 (2)1.1.3设备制造及供货 (4)1.1.4设备及系统安装 (25)1.2设计基础资料 (26)1.2.1锅炉主要特性 (26)1.2.6厂址气象和地理条件 (28)1.2.7土建设计基础资料 (29)1.3工程方案 (30)1.3.1工艺设计 (30)1.3.2主要设计原则 (30)1.3.3方案设计 (31)1.4性能保证值 (34)1.5总包方提供的基本参数 (35)1.6设备清册(设备厂家供参考、设备选型以初设选型为准) (41)2业主人员培训 (48)2.1培训内容 (48)2.2培训方式 (48)2.3设计联络会 (49)3 监造、检验和性能验收试验 (51)2.1概述 (51)2.2工厂检验 (51)2.3设备监造 (52)1、技术规范1.1工程范围山东临沂电厂位于位于临沂市以南,距市区约3公里,在大菜园村以南,许家冲村以西地区,北距临沂火车站3公里,东距沂河5公里,位于临沂市规划区范围以内。
为改善电厂周围及临沂地区的大气环境,根据临沂发电厂二氧化硫治理规划和环保要求,临沂电厂将继续对剩余锅炉进行脱硫技改工作,本期工程将先行对5#、6#锅炉加装脱硫装置。
综合各方面情况考虑,临沂电厂机组设计含硫量为2.0%。
本工程为改造工程,采用循环流化床(干法)脱硫工艺,其装置在60%-100%BMCR工况下进行全烟气脱硫,脱硫效率不低于90%。
本工程包括脱硫除尘岛内系统正常运行、紧急情况处理及检修等所必需具备的工艺系统设计、设备选择、采购、运输及储存、制造及安装、土建建(构)筑物的设计、施工、调试、试验及检查、试运行、考核验收、消缺、培训和最终交付投产等方面的内容。
总包应对脱硫除尘岛的性能负全部责任。
循环悬浮式烟气半干法脱硫技术的实验相关解析

一、循坏悬浮式烟气半干法脱硫技术原理在对锅炉中的烟气处理过程中,静电除尘器是其进入的第一个环节。
在这个环节之中,主要是收集烟气中的干灰,能收集的干灰达85%。
在完成静电除尘后,即开始进入下一个环境中:脱硫净化塔。
在净化塔内反应主要应用悬浮方式,基于喷雾增湿活化以及循环硫化床理论,保证烟气中的干飞灰与石灰粉之间的循环、悬浮,充分接触二氧化硫,并进行相应的反应,实现脱硫工作。
随后实现脱硫工作后的烟气进入下一个环境中:布袋除尘器,对烟气开展除尘工作后,符合达标要求后,即可排出。
受到一些因素的影响,石灰粉并未与二氧化硫充分反映,因此还会有大量的石灰粉存在于布袋除尘器的粉尘中,为了对脱硫系统中的硫、钙的比例有效降低,对脱硫的成本降低,可以将上述布袋除尘器收集到的粉尘进入脱硫净化塔中,进行循环应用工作,从而有效降低粉尘中的石灰粉含量,在此同时在净化塔中添加石灰粉,开展下一轮的脱硫工作。
为保证净化塔内足够的湿润度,净化塔内会有两级增湿活化器,为其内部的环境增湿。
为了对脱硫的效率提升,可以应用活化器,其中的介质为压缩空气,将工业水雾转为十分细小的水滴。
为了保证脱硫系统有最好的脱硫效率,且为干脱硫灰,需要严格把握水滴的直径以及喷水量。
借助上述操作,能够对水露点温度与增加湿度后烟气温度之间的差别值有效控制,避免烟气中水分过大影响后续脱硫工作。
此外,净化塔中的烟气干灰主要的状态是悬浮循环,基于该条件,可以保证固体颗粒与烟气之间滞留时间的充足性,保证充分的化学反应。
该脱硫技术涉及的主要流程如表1:表1 半干法脱硫技术涉及的主要流程二、循环悬浮式烟气半干法脱硫技术应用效果本节主要对循环悬浮式烟气半干法脱硫技术应用效果进行分析。
应用循环悬浮式烟气半干法脱硫技术有很好的优势,如表2:表2 应用循环悬浮式烟气半干法脱硫技术优势其一,有较小的占地面积。
借助该技术,能够对气体、液体以及固体之间的传质强化,对烟气处理设备所占的面积有效降低,从而进一步降低了运行的费用以及投资成本。
火力发电厂烟气循环流化床半干法脱硫系统设计规程

火力发电厂烟气循环流化床半干法脱硫系统设计规程一、前言火力发电厂作为能源的重要供应者,在发展过程中也面临着环保要求的不断提高。
烟气脱硫是保护大气环境、减少硫氧化物对人体健康的影响的重要手段。
烟气循环流化床半干法脱硫技术因其具有高脱硫效率、低能耗、操作稳定等优点,逐渐受到火力发电厂的青睐。
二、烟气循环流化床半干法脱硫系统工艺概述烟气循环流化床半干法脱硫系统是采用石灰石浆液作为脱硫剂,通过在反应塔内与烟气进行接触反应,将烟气中的二氧化硫进行吸收,形成石膏。
脱硫反应后的烟气通过旋风除尘器,净化后排放到大气中。
而石膏通过脱硫废水处理系统进行处理,使其达到国家排放标准。
系统操作中,石灰石浆液通过气力输送管道输送到反应器塔中,通过旋风分离器将石膏和石灰石分离,石膏送到石膏浆液处理系统,石灰石返回到循环槽进行循环利用。
三、烟气循环流化床半干法脱硫系统主要设备及其特点1.反应器塔反应器塔是烟气循环流化床半干法脱硫系统的核心设备,主要由进气口、出口、填料层、雾化喷淋层等组成。
其主要特点包括:填料层的选择要注意填料的比表面积,容积比和对流湿度等参数;雾化喷淋层的设计要根据烟气流速、反应器的容积和石灰石浆液的流量进行合理设计。
2.旋风除尘器旋风除尘器是用于对脱硫反应后烟气中的粉尘进行除尘,其主要特点包括:结构紧凑、除尘效率高、易于维护、运行稳定等。
3.气力输送系统气力输送系统是用于输送石灰石浆液到反应器塔中,其主要特点包括:输送过程中石灰石浆液无泄漏、设备运行稳定、输送距离远等。
4.脱硫废水处理系统脱硫废水处理系统是用于对反应后产生的废水进行处理,使其达到国家排放标准,其主要特点包括:处理效率高、占地面积小、废水排放达标、运行成本低等。
四、设计规程1.设计依据根据国家《烟气污染物排放标准》等相关标准,结合火力发电厂的实际情况,确定系统的设计参数和工艺流程。
2.脱硫效率系统设计应保证脱硫效率达到国家标准要求,并对脱硫效率进行动态监测,确保系统运行稳定、可靠。
循环流化床半干法脱硫原理

循环流化床半干法脱硫原理烟气循环流化床(CFB)干法脱硫工艺是在80年代中期开发的适用于燃煤电厂的一种干法脱硫工艺。
循环流化床烟气脱硫系统主要由以下系统组成:1) 吸收剂存储、干式消化和输送;2) 烟气雾化增湿调温;3) 脱硫剂与含湿烟气雾化颗粒充分接触混合;4) 二氧化硫吸收;5) 增湿活化;6) 灰循环;7) 废渣排除。
它以循环流化床为原理,通过物料在床内的内循环和高倍率的外循环,使得吸收剂与SO2间的传热传质交换强烈,吸收剂内的传质过程强烈,固体物料在床内的停留时间长达30—60分钟,且运行温度可降至露点附近,从而大大提高了吸收剂的利用率和脱硫率。
在较低的Ca/S比(Ca/S=1.1~1.3)情况下,脱硫率可与石灰石湿法工艺相媲美,即大于90%。
具体的循环流化床半干法脱硫原理(以毅腾环保为例)如下:从锅炉尾部排出的含硫烟气被引入循环流化床反应器喉部,在这里与水、脱硫剂和还具有反应活性的循环干燥副产物相混合,石灰以较大的表面积散布,并且在烟气的作用下贯穿整个反应器。
然后进入上部筒体,烟气中的飞灰和脱硫剂不断进行翻滚、掺混,一部分生石灰则在烟气的夹带下进入旋风分离器,分离捕捉下来的颗粒则通过返料器又被送回循环流化床内,生石灰通过输送装置进入反应塔中。
由于接触面积非常大,石灰和烟气中的SO2能够充分接触,在反应器中的干燥过程中,SO2被吸收中和。
在反应器内,消除二氧化硫的化学反应如下:SO2 + Ca(OH)2 + H2O = CaSO3+ 2H2O。
含有废物颗粒、残留石灰和飞灰的固体物在随后的旋风分离器内分离并循环至反应器,由于固体物的循环部分还能部分反应,即循环石灰的未反应部分还能与烟气中的SO2反应,通过循环使石灰的利用率提高到最大。
循环流化床半干法脱硫技术的应用

循环流化床半干法脱硫技术的应用摘要:本文结合承钢180m2烧结机烟气脱硫工程的应用实例,介绍了循环流化床半干法脱硫系统的工艺、设备选型、运行情况及技术经济指标。
关键词:循环流化床;半干法;脱硫;工艺;循环流化床半干法脱硫技术在我国许多大型钢铁企业得到了广泛应用,接下来,笔者将以大连绿诺集团有限公司总承包的承钢180m2烧结机烟气脱硫工程为例,介绍循环流化床半干法脱硫技术的具体应用。
1 工艺介绍烧结机主抽风机出来的烟气经入口挡板门进入脱硫塔的底部,烟气流经脱硫塔底部文丘里装置时被加速,并与喷入的水和浆液接触,烟气降至70~90℃左右。
烟气中的SO2与脱硫剂反应,生成亚硫酸钙、硫酸钙等。
烟气带走大量的固体颗粒,进入布袋除尘器除尘,除尘后的净烟气经增压风机排入新建烟囱。
布袋除尘器收集到的脱硫灰一部分经过返料装置进入脱硫塔,另一部分至灰库外排。
循环流化床半干法脱硫工艺流程框图如图1所示。
2设备选型及技术参数承钢180m2烧结机烟气参数:入口烟气量105万m3/h(工况),入口烟气温度150℃,入口SO2浓度≤1500mg/Nm3,入口粉尘浓度≤200mg/Nm3;要求出口粉尘浓度≤30 mg/Nm3,出口SO2浓度≤100mg/Nm3。
根据上述参数,对主要设备选型:1)脱硫塔根据烟气量,选择脱硫塔直径8.2m,高度42m。
2)布袋除尘器选择长袋低压脉冲布袋除尘器,过滤面积20588m2,压力损失<1.5kPa,耐负压5kPa。
3)脱硫风机脱硫系统配置一台可以满足烧结机满负荷生产的离心式风机,采用变频器控制,用于克服FGD装置造成的烟气压降。
脱硫风机的处理烟气量为105万m3/h,全压4kPa。
3 运行情况承钢180m2烧结机烟气脱硫项目(如图2所示)已通过河北省环境保护厅工程治理验收。
整体设备运行稳定,出口烟气SO2浓度≤100mg/Nm3,符合《大气污染物综合排放标准》GB16297-1996 的要求。
烟气半干法脱硫技术方案

烟气半干法脱硫技术方案1. 吸收塔1.1工艺流程图1-1 循环流化床半干法工艺流程示意图原烟气由循环流化床半干法净化装置底部进入循环悬浮流化床脱硫塔。
Ca(OH)2原料经过螺旋输送机送入脱硫塔,流态化的物料和烟气中的二氧化硫在脱硫塔中发生化学反应,脱除掉大部分的二氧化硫。
烟气通过脱硫塔底部的文丘里管的加速,进入循环流化床体,物料在循环流化床里,气固两相由于气流的作用,产生激烈的湍动与混合,充分接触,在上升的过程中,不断形成絮状物向下返回,而絮状物在激烈湍动中又不断解体重新被气流提升,使得气固间的滑落速度高达单颗粒滑落速度的数十倍;脱硫塔顶部结构进一步强化了絮状物的返回,进一步提高了塔内颗粒的床层密度,使得床内的Ca/S 比高达50以上。
这样循环流化床内气固两相流机制,极大地强化了气固间的传质与传热,为实现污染物高脱除率提供了根本的保证。
喷嘴的安装位置设置在文丘里扩散段,喷入的雾化水以降低脱硫塔内的烟温,从而使得SO2与Ca(OH)2的反应转化为可以瞬间完成的离子型反应。
吸收剂、循环脱硫灰在文丘里段以上的塔内进行第二步的充分反应,生成副产物CaSO3·1/2H2O,还与SO3等反应生成相应的副产物CaSO4·1/2H2O等。
烟气在上升过程中,颗粒一部分随烟气被带出脱硫塔,一部分因自重重新回流到循环流化床内,进一步增加了流化床的床层颗粒浓度和延长吸收剂的反应时间。
烟气在文丘里以上的塔内流速为3.5~5.5m/s,烟气在塔内的气固接触时间大约为6~8秒左右,从而有效地保证了脱硫效率。
从化学反应工程的角度看,SO2与氢氧化钙的颗粒在循环流化床中的反应过程是一个外扩散控制的反应过程;SO2与氢氧化钙反应的速度主要取决于SO2在氢氧化钙颗粒表面的扩散阻力,或说是氢氧化钙表面气膜厚度。
当滑落速度或颗粒的雷诺数增加时,氢氧化钙颗粒表面的气膜厚度减小,SO2进入氢氧化钙的传质阻力减小,传质速率加快,从而加快SO2与氢氧化钙颗粒的反应。
烟气双循环流化床半干法悬浮脱硫净化技术
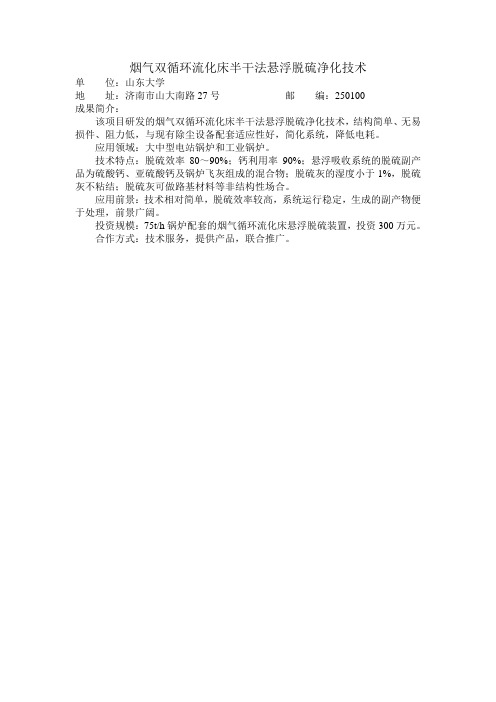
烟气双循环流化床半干法悬浮脱硫净化技术
单位:山东大学
地址:济南市山大南路27号邮编:250100
成果简介:
该项目研发的烟气双循环流化床半干法悬浮脱硫净化技术,结构简单、无易损件、阻力低,与现有除尘设备配套适应性好,简化系统,降低电耗。
应用领域:大中型电站锅炉和工业锅炉。
技术特点:脱硫效率80~90%;钙利用率90%;悬浮吸收系统的脱硫副产品为硫酸钙、亚硫酸钙及锅炉飞灰组成的混合物;脱硫灰的湿度小于1%,脱硫灰不粘结;脱硫灰可做路基材料等非结构性场合。
应用前景:技术相对简单,脱硫效率较高,系统运行稳定,生成的副产物便于处理,前景广阔。
投资规模:75t/h锅炉配套的烟气循环流化床悬浮脱硫装置,投资300万元。
合作方式:技术服务,提供产品,联合推广。
半干法烟气脱硫技术工艺及技术参数
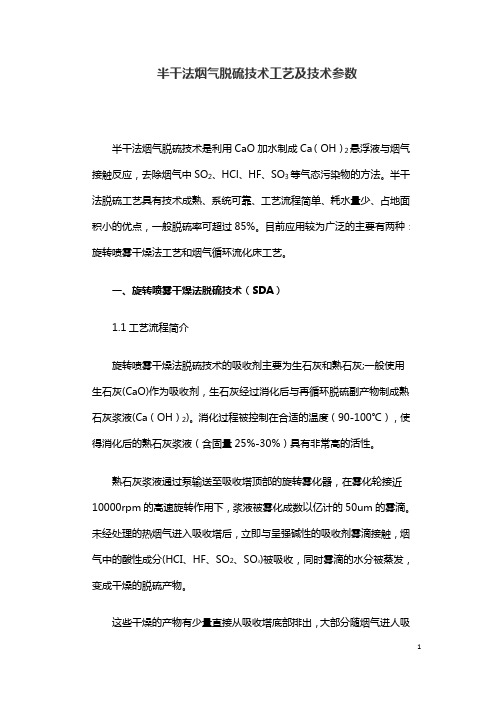
半干法烟气脱硫技术工艺及技术参数半干法烟气脱硫技术是利用CaO加水制成Ca(OH)2悬浮液与烟气接触反应,去除烟气中SO2、HCl、HF、SO3等气态污染物的方法。
半干法脱硫工艺具有技术成熟、系统可靠、工艺流程简单、耗水量少、占地面积小的优点,一般脱硫率可超过85%。
目前应用较为广泛的主要有两种:旋转喷雾干燥法工艺和烟气循环流化床工艺。
一、旋转喷雾干燥法脱硫技术(SDA)1.1工艺流程简介旋转喷雾干燥法脱硫技术的吸收剂主要为生石灰和熟石灰;一般使用生石灰(CaO)作为吸收剂,生石灰经过消化后与再循环脱硫副产物制成熟石灰浆液(Ca(OH)2)。
消化过程被控制在合适的温度(90-100℃),使得消化后的熟石灰浆液(含固量25%-30%)具有非常高的活性。
熟石灰浆液通过泵输送至吸收塔顶部的旋转雾化器,在雾化轮接近10000rpm的高速旋转作用下,浆液被雾化成数以亿计的50um的雾滴。
未经处理的热烟气进入吸收塔后,立即与呈强碱性的吸收剂雾滴接触,烟气中的酸性成分(HCI、HF、SO2、SO3)被吸收,同时雾滴的水分被蒸发,变成干燥的脱硫产物。
这些干燥的产物有少量直接从吸收塔底部排出,大部分随烟气进人吸收塔后的除尘器内被收集,再通过机械或气力方式输送,处理后的洁净烟气通过烟囱排放。
根据实际情况,SDA系统还可以采用部分脱硫产物再循环制浆以提高吸收剂的利用率。
烟气在喷雾干燥吸收塔中的停留时间一般为10-12S,吸收塔内飞灰和脱硫灰大部分通过除尘器收集,只有5%-10%的干燥固体物从吸收塔底部排出。
1.2影响脱硫效率的主要因素1.2.1雾滴粒径雾滴粒径越小,传质面积也越大,但粒径过细,干燥速度也越快,气液反应就变成了气固反应,脱硫效率反而会降低。
有关研究表明,雾化粒径在50um时脱硫率较高。
1.2.2接触时间在旋转喷雾干燥法脱硫技术中,以烟气在脱硫塔中的停留时间来衡量烟气与脱硫剂的接触时间,停留时间主要取决于液滴的蒸发干燥时间,一般为10-12S,降低脱硫塔的空塔流速,延长停留时间,有利于提供脱硫率。
循环流化床CFB半干法脱硫工艺计算程序

循环流化床干法脱硫业主:Circulating Fluidized Bed DryScrubber项目:工艺计算technical calculation输入参数gas volume 烟气量300,000Nm^3/h工况烟气量烟气量放量10.0%烟气含 SO2 量烟气温度140℃要求出口含 SO2 量温度放量10℃要求脱硫效率CDS入口粉尘浓度 0.25g/Nm^3CaO的利用率为要求粉尘排放浓度15mg/Nm^3脱硫需要的Ca/S比为一年运行小时数7000小时取CaO的纯度为烟气喷水冷却后温度70℃消石灰含水标况烟气量计算结果计算温度150℃计算烟气量后除尘器入口含尘浓度#REF!g/Nm^3工况烟气量除尘效率#REF!则SO2排放浓度为飞灰生成量#REF!Kg/h check每小时需脱去的SO2量为石灰消化用水量 130Kg/h烟气喷水冷却水量 14,447Kg/h一年运行天数喷嘴进水管水量 21,670Kg/h脱硫需要的CaO为系统耗水量 14,577Kg/h脱硫需要的Ca(OH)2为一天消化石灰用水为 3.1t/day一天所需CaO为一年消化石灰用水为 913t/year一年所需CaO为一天需要的脱硫用水为 347t/day一天需要的Ca(OH)2为一年需要的脱硫用水为 101,128t/year一年需要的Ca(OH)2为设计:校对:日期:日期:业主:项目:主要设备选型计算脱硫塔台数1台文丘里喉口速度漏风系数 2.0%文丘里个数出口法兰标高 3.5m塔内气速底部灰斗角度60 °脱硫塔进口烟气流速出灰口宽(方形)300mm出口烟道进口烟气量141.45am^3/s出口烟气量CDS塔几何尺寸单塔截面积31.5m^2文丘里段塔截面CDS塔直径 A 6.40m文丘里段塔直径 E 出口法兰高 B2 5.6m单塔喉口总面积计算出口法兰宽 B1 5.7m喉口直径 I天圆地方高 C 3.3m文丘里喉高 J3CDS塔直段高 D16.7m文丘里之间边距入口法兰宽 F 3.7m一级缩管直径 H1入口法兰高 G 2.7m二级缩管直径 H2底部灰斗高 2.94m一级缩管高 J1文丘里出口变径 L 3.7m二级缩管高 J2塔反应段高度29.3m文丘里出口喇叭高 J4反应时间 6.51s文丘里总高 K CDS塔总高38.40mCDS塔离地高41.9m单塔重#REF!t设计:校对:日期:日期:业主:项目:消石灰仓 Ca(OH)2数量1台数量储期1天储量消石灰容重0.6t/m^3脱硫灰容重直径3m直径取锥角63度取锥角出口法兰宽400mm出口法兰宽容积利用率90.0%容积利用率所需容积20.4m^3所需容积锥体积7.7m^3锥体积直段高度 2.9m直段高度整个仓高 5.4m整个仓高仓重#REF!t仓重中间石灰仓数量0台数量储期0.5h储量消石灰容重0.5t/m^3直径直径1m所需容积所需容积0.6m^3高度高度0.7m水箱重仓重#REF!t生石灰仓数量1台系统数量储期3天数量生石灰容重 1.2t/m^3储量直径3m脱硫灰容重所需容积24.1m^3直径直段高度 3.4m取锥角仓重#REF!t出口法兰宽容积利用率所需容积锥体积直段高度整个仓高仓重中转灰仓数量0台系统数量储量0.15h数量脱硫灰容重0.6t/m^3储量循环灰量#REF!t/h脱硫灰容重直径2m直径取锥角60度取锥角出口法兰宽400mm出口法兰宽容积利用率90.0%容积利用率所需容积#REF!m^3所需容积锥体积 2.1m^3锥体积直段高度#REF!m直段高度整个仓高#REF!m整个仓高仓重t仓重日期:2022/2/24锅炉:130Tam^3/h标况烟气 -Nm^3/h800mg/Nm^3石灰石细度:90%小于44μm(325目)30.0mg/Nm^3湿法中SO3以气溶胶的形式存在,跟随性较好,将绕过喷淋层液滴直接进入烟囱,排放到大气中,在半法脱硫中中,SO3表面不会以气溶脱的形式存在,SO3可以很好的与脱硫剂反应,生成96.3%65.0%Ca(OH)2+ SO2=CaS O3.1/2H2 O+1/2H2 O1.48CaSO3.1/ 2H2O+3/2 H2O+1/2 O2=CaSO 4.2H2O80.0%量要求:石灰粉细度宜在2mm以下;加适量水后4min内温度可升高到60度(或是3min温升45度),纯度:CaO含量>=85%.1.0%300000Nm^3/h499,231am^3/h138.68am^3/s循环倍率3630.0mg/Nm^3循环灰量#REF!Kg/hOK 沉降室效率0%248Kg/h 沉降室灰量#REF!Kg/h 沉降室灰量#REF!T/h291.7天脱硫灰容重0.6T/m^3402Kg/h 沉降室灰量#REF!m^3/h511Kg/h中转灰仓灰量#REF!T/h9.6t/day循环灰量#REF!T/h 2,813t/year排出量#REF!T/h12.3t/day3,576t/year布袋效率100%布袋收灰量#REF!T/h灰斗个数#REF!每灰斗灰量#REF!T/h日期:2022/2/24锅炉:60m/s 7个4.5m/s 14.00m/s 正方形m出口烟道正方形119.82am^3/s长方形m10.20m^2进CDS烟道截面3.23700mm 2.36m^2650mm975.0mm文丘里之间边距60.0mm75.0mm 文丘里与壁之间边距52.5mm1158mm 827.0mm 165.5mm 331.0mm 1441.0mm 2913.0mm文丘里计算日期:2022/2/24锅炉:1台9h0.6t/m^32m61度400mm80.0%#REF!m^32.2m^3#REF!m#REF!m#REF!t1台4h4.6m86.7m^35.2m#REF!t1套#5,#6炉共设两座直径为10m 的灰库,每座灰库有效贮灰容积为1860m^3,可供两炉存灰48h 。
循环流化床半干法脱硫工艺流化床的建立及稳床措施

循环流化床半干法脱硫工艺流化床的建立及稳床措施浙江洁达环保工程有限公司吴国勋、余绍华、傅伟根、杨锋【摘要】循环流化床半干法脱硫工艺技术要求高,建立和稳定流化床是两个关键点,只有做好恰当的流化床设计和配置合理的输送设备,才可保证脱硫系统的稳定高效运行。
【关键词】循环流化床半干法脱硫床体1、简介循环流化床脱硫工艺技术是较为先进的运用广泛的烟气脱硫技术。
该法以循环流化床原理为基础,主要采用干态的消石灰粉作为吸收剂,通过吸收剂的多次再循环,延长吸收剂与烟气的接触时间,以达到高效脱硫的目的,其脱硫效率可根据业主要求从60%到95%。
该法主要应用于电站锅炉烟气脱硫,已运行的单塔处理烟气量可适用于6MW~300MW机组锅炉,是目前干法、半干法等类脱硫技术中单塔处理能力最大、在相对较低的Ca/S摩尔比下达到脱硫效率最高、脱硫综合效益最优越的一种方法。
该工艺已经在世界上10多个国家的20多个工程成功运用;最大业绩项目烟气量达到了1000000Nm3/h,最高脱硫率98%以上,烟尘排放浓度30mg/Nm3以下,并有两炉一塔、三炉一塔等多台锅炉合用一套脱硫设备的业绩经验,有30余套布袋除尘器的业绩经验,特别是在奥地利Thesis热电厂300MW机组的应用,是迄今为止世界上干法处理烟气量最大的典范之作;在中国先后被用于210MW,300MW,50MW 燃煤机组的烟气脱硫。
但是很多循环流化床半干法脱硫项目由于未能建立稳定的床体,导致项目的失败,不能按原有计划完成节能减排的要求。
因此很有必要在此讨论一下关于“循环流化床半干法工艺流化床的建立及稳定措施”的相关问题。
2、循环流化床脱硫物理学理论循环流化床脱硫塔内建立的流化床使脱硫灰颗粒之间发生激烈碰撞,使颗粒表面生成物的固形物外壳被破坏,里面未反应的新鲜颗粒暴露出来继续参加反应,从而客观上起到了加快反应速度、干燥速度以及大幅度提高吸收剂利用率的作用。
另外由于高浓度密相循环的形成,塔内传热、传质过程被强化,反应效率、反应速度都被大幅度提高,而且脱硫灰中含有大量未反应吸收剂,所以塔内实际钙硫比远远大于表观钙硫比。
湿法与半干法烟气脱硫工艺技术比较
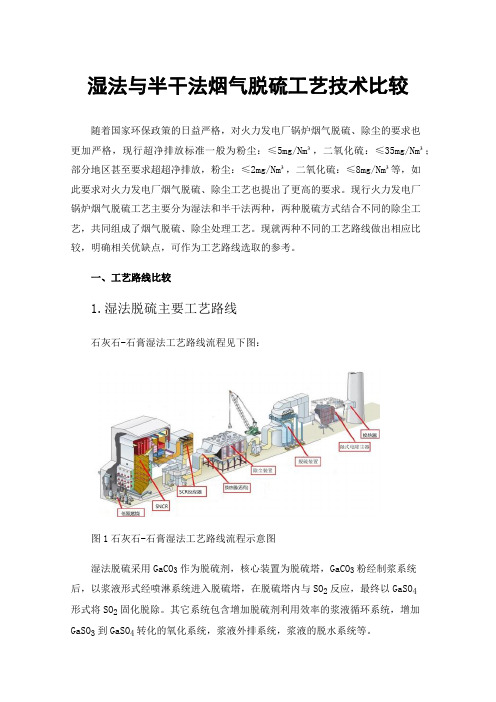
湿法与半干法烟气脱硫工艺技术比较随着国家环保政策的日益严格,对火力发电厂锅炉烟气脱硫、除尘的要求也更加严格,现行超净排放标准一般为粉尘:≤5mg/Nm³,二氧化硫:≤35mg/Nm³;部分地区甚至要求超超净排放,粉尘:≤2mg/Nm³,二氧化硫:≤8mg/Nm³等,如此要求对火力发电厂烟气脱硫、除尘工艺也提出了更高的要求。
现行火力发电厂锅炉烟气脱硫工艺主要分为湿法和半干法两种,两种脱硫方式结合不同的除尘工艺,共同组成了烟气脱硫、除尘处理工艺。
现就两种不同的工艺路线做出相应比较,明确相关优缺点,可作为工艺路线选取的参考。
一、工艺路线比较1.湿法脱硫主要工艺路线石灰石-石膏湿法工艺路线流程见下图:图1石灰石-石膏湿法工艺路线流程示意图湿法脱硫采用GaCO3作为脱硫剂,核心装置为脱硫塔,GaCO3粉经制浆系统后,以浆液形式经喷淋系统进入脱硫塔,在脱硫塔内与SO2反应,最终以GaSO4形式将SO2固化脱除。
其它系统包含增加脱硫剂利用效率的浆液循环系统,增加GaSO3到GaSO4转化的氧化系统,浆液外排系统,浆液的脱水系统等。
为降低大量粉尘进入脱硫塔,对脱硫循环浆液造成不利影响,一般在烟气进入脱硫塔前,须进行脱尘处理。
而又由于湿法脱硫塔顶部仅设有除雾器,对液滴脱除效率不高,要达到粉尘超净排放,一般需在脱硫塔后配套湿式电除尘器来实现。
故整体处理工艺一般如下:锅炉烟气经SCR脱硝处理后,一级配套高效除尘器(电袋、布袋除尘器、电除尘器)进行脱硫前除尘,保证脱硫入口烟气粉尘浓度满足要求。
经一级除尘后烟气进入湿法喷淋塔进行脱除SO2反应。
由于湿法脱硫反应环境无法脱除烟气中以细微硫酸雾滴存在的SO3,在湿法喷淋塔之后必须进一步配套湿式电除尘器来实现脱除。
配套的二级湿式电除尘器同时肩负粉尘减排提效作用。
由于湿法路线后级脱硫及除尘均在湿式环境下进行,为了提高排烟温度,系统通常还同时配套换热器。
半干法脱硫技术

一、工艺概述循环悬浮式半干法烟气脱硫技术兼有干法与湿法的一些特点,其既具有湿法脱硫反应速度快、脱硫效率高的优点,又具有干法无污水排放、脱硫后产物易于处理的好处而受到人们广泛的关注。
循环悬浮式半干法烟气脱硫技术是近几年国际上新兴起的比较先进的烟气脱硫技术,它具有投资相对较低,脱硫效率相对较高,设备可靠性高,运行费用较低的优点,因此它的适用性很广,在许多国家普遍使用。
循环悬浮式半干法烟气脱硫技术主要是根据循环流化床理论,采用悬浮方式,使吸收剂在吸收塔内悬浮、反复循环,与烟气中的S02充分接触反应来实现脱硫的一种方法。
利用循环悬浮式半干法最大特点和优势是:可以通过喷水(而非喷浆)将吸收塔内温度控制在最佳反应温度下,达到最好的气固紊流混合并不断暴露出未反应的消熟石灰的新表面;同时通过固体物料的多次循环使脱硫剂具有很长的停留时间,从而大大提高了脱硫剂的利用率和脱硫效率。
与湿法烟气脱硫相比,具有系统简单、造价较低,而且运行可靠,所产生的最终固态产物易于处理等特点。
二、技术特点循环悬浮式半干法烟气脱硫技术是在集成浙大和国外环保公司半干法烟气脱硫技术基础上,结合中国的煤质和石灰品质及国家最新环保要求,经优化、完善后开发的第三代半干法技术。
它是在锅炉尾部利用循环流化床技术进行烟气净化,脱除烟气中的大部分酸性气体,使烟气中的有害成分达到排放要求。
与第一、第二代半干法相比,第三代循环悬浮式半干法烟气脱硫技术具有以下特点:八、、・1、在吸收塔喉口增设了独特的文丘里管,使塔内的流场更均匀。
2、在吸收塔内设置上下两级双流喷嘴,雾化颗粒可达到50µm 以下,精确的灰水比保证了良好的增湿活化效果,受控的塔内温度使脱硫反应在最佳温度下进行,从而取得较高的脱硫效率,较长的滤料使用寿命。
3、采用比第二代更完善的控制系统,操作更简捷。
4、采用成熟的国产原材料和设备,降低成本,节约投资.5、占地少,投资省,运行费用低,无二次污染。
循环硫化床烟气脱硫技术及工艺设计
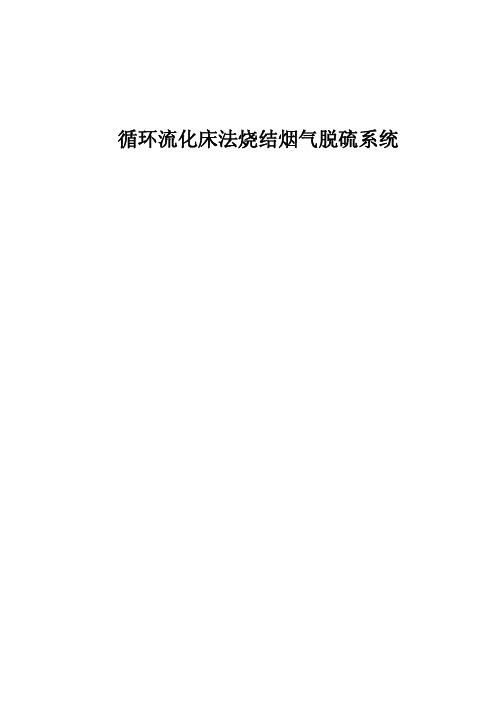
空气污染控制。 2.1.2 国内烧结厂烟气脱硫现状
烧结机是钢铁生产过程的重要设备。烧结工艺将各种粉矿混合伴匀, 布料于烧结带上燃烧,粉矿熔融粘结成烧结矿。混料中加有粉焦或煤粉作 为燃料。燃料燃烧时,穿过料层吸入空气助燃,燃烧产生的废气中含有 SO2 等污染物,SO2 浓度与燃料含硫量有关。从烟气脱硫角度来看,烧结 烟气具有以下特征:1)废气量大;2)烟气温度高;3)SO2 浓度低,总 量大。
一般来说,在人为中排放的 SO2 总量中,火电厂约占一半,工业企 业占 1/3,其余属于交通运输工具移动源和广泛分散的商用民用炉灶。
近 10 几年来,由于国家推行清洁生产,加大环保投入,强化环境管 理的结果,SO2 污染势头有所遏制,但尚未发生根本变化。未来 10 年将 是我国经济持续高速发展时期,如不采取有效措施,SO2 污染可能制约发 展的速度。
半干法的工艺特点是:反应在气、固、液三相中进行,利用烟气显热
-6-
蒸发吸收液中的水份,使最终产物为于粉状,脱硫废渣一般抛弃处置。该 方法既能结合湿法和干法脱硫的优点,实现脱硫效率高、吸收率高,同时 投资少、设备简单。
根据钢铁企业烧结烟气气量较大、SO2 浓度较低等特点,比较以上脱硫 工艺,我们推荐采用半干法的循环流化床工艺进行烧结烟气脱硫。
-2-
二、烧结烟气脱硫状况、技术和工艺推荐
2.1 国内外烧结烟气脱硫现状
2.1.1 国外烟气脱硫现状
国外烧结烟气脱硫的总体状况和技术水平,以日本、美国和德国为代 表。由于日本环保法规严厉,烧结废气含硫较高的各类生产厂几乎都设有 废气脱硫装置,因此其烧结烟气脱硫工艺的应用程度高于美国和德国。
日本烧结厂比较重视环境保护,针对生产过程中产生和散发的灰尘、
在世界上属于一流,在废气脱硫方面,日本在 20 世纪 70 年代就已开发了
- 1、下载文档前请自行甄别文档内容的完整性,平台不提供额外的编辑、内容补充、找答案等附加服务。
- 2、"仅部分预览"的文档,不可在线预览部分如存在完整性等问题,可反馈申请退款(可完整预览的文档不适用该条件!)。
- 3、如文档侵犯您的权益,请联系客服反馈,我们会尽快为您处理(人工客服工作时间:9:00-18:30)。
当烟气接近绝热饱和温度时,脱硫效率及钙利用率提高。常规的喷雾干燥法不能在烟气过饱和温度(反应器出口烟温与烟气的绝热饱和温度之差)小于11℃的条件下运行,否则会使颗粒团粘。在悬浮反应塔内,传质与传热得到加强,使喷入的石灰浆得到彻底的干燥,从而可在烟气过饱和温度较低的条件下安全运行。ﻫ (3)石灰耗量
钙硫比定义为系统入口的SO2摩尔数与进入系统钙的摩尔数之比。因为烟气可在较低的温度下运行,脱硫效率高、钙利用率高,因而钙硫比低,石灰耗量少。钙硫比1.2∽1.3。
(4)脱硫副产品
悬浮吸收系统的脱硫副产品为硫酸钙、亚硫酸钙及锅炉飞灰组成的混合物。脱硫灰的湿度小于1%,脱硫灰不粘结。对脱硫副产品的处理可以采用与锅炉飞灰相同的方式进行处置。ﻫ 2.3 控制系统
(3) 保证脱硫塔内的气固比使脱硫灰达到一定浓度,才能有较高的脱硫效率。脱硫塔反应器内的气固比由循环灰量确定,气固比的变化反映出脱硫塔压差的变化。因此,可根据脱硫塔的压差,通过控制脱硫灰的回送量(或排走量)来调节脱硫塔内的脱硫灰量。
2.4脱硫剂ﻫ 采用石灰浆作为脱硫剂,其石灰消化工艺及其输送简单、方便,调节容易。ﻫ 2.5脱硫灰处理方式
电厂除灰方式有干除灰和湿除灰两种。
当为干Байду номын сангаас灰时,灰中掺和部分脱硫产物,可作为高钙灰利用。某些应用场合可提高灰的价值及可用性。
对于湿除灰系统,因灰中石灰的掺入,输灰系统的pH值提高,加剧了系统的结垢。因此,要考虑湿除灰系统的防垢措施。
2.6 装置及其布置ﻫ 脱硫塔采用双循环方式,初级分离设置在主塔内,二级分离为外置下排旋风式,易于布置和支撑。脱硫塔的烟气进出口设置方便。ﻫ 脱硫塔设置在锅炉与静电除尘器之间,可直接与静电除尘器连接,或设置旁路与静电除尘器连接。旁路具有一定的运行灵活性。设置旁路时相应设置切换烟道门。
烟气双循环流化床半干法悬浮脱硫装置是适应35t/h~670t/h锅炉,与静电除尘器良好配合的一种高效脱硫装置。
该装置已完成工业性优化试验及工业示范。表现出高的脱硫效率(90%)和与静电除尘器的良好配合特性。设计指标:脱硫效率∽90%,脱硫装置阻力∽1000Pa,钙硫比1.3∽1.2。ﻫ 根据国家环境保护总局、国家经济贸易委员会、科学技术部文件(环发[2002]26号)《关于发布〈燃煤二氧化硫排放污染防治技术政策〉的通知》中、及国家电力公司文件(国电科[2001]531号)《国家电力公司关于燃煤电厂建设脱硫除尘装置等有关情况的报告》中明确指出:电厂锅炉烟气脱硫的技术路线是:1)…。2)燃用中低硫煤(含硫<2%)的中小电厂锅炉(<200MW),或是剩余寿命低于10年的老机组建设烟气脱硫设施时,宜优先采用半干法、干法或其它费用较低的成熟技术,脱硫效率应保证在75%以上,…。
(1)脱硫及其效率
本工艺以石灰为脱硫吸收剂的(半)干法烟气脱硫系统。其主要反应为: ﻫ Ca(OH)2+SO2→CaSO3·1/2H2O+1/2H2O CaSO3+1/202→CaSO4
喷入吸收塔水分的作用是调质、降温,在烟气的干燥下,水分蒸发。本技术的脱硫效率可达到90%以上,与湿法相当。这决定于悬浮吸收塔内有良好的传热特性,塔内在接近烟气绝热温度的条件下运行,喷入的石灰浆反应后快速干燥,允许烟气的停留时间短,同时产生干态脱硫产物;脱硫灰循环倍率高,塔内颗粒浓,固体颗粒的表面积大,SO2的吸收在颗粒表面进行,传质得到强化。
烟气双循环流化床半干法悬浮脱硫工艺符合国家技术政策,是适应于135(125)MW机组的烟气脱硫方案。
2 烟气双循环流化床半干法悬浮脱硫工艺ﻫ 2.1 技术定义与工艺流程ﻫ 烟气双循环流化床半干法悬浮脱硫装置是一种两级惯性分离、内外双重循环的烟气循环流化床悬浮脱硫装置。其主要构成:流化装置及浓相悬浮脱硫反应塔、顶部惯性分离器、与除尘器配套的百叶窗惯性分离装置(或下排风式低阻旋风分离器)、脱硫灰回送及脱硫剂添加机构、控制系统。其工作原理是烟气经流化装置,把脱硫剂及脱硫灰流化并进入脱硫反应塔,进行脱硫半干式洗涤;在脱硫反应塔顶部的惯性分离器对高含灰烟气进行初步分离,分离出的脱硫灰靠重力直接进入脱硫反应塔,形成内循环方式。初步分离后的烟气进入二级分离器进行二级气固分离,然后烟气进入静电除尘器或布袋除尘器,除尘后由引风机排出。二级分离出的脱硫灰由灰料输送装置回送,形成脱硫灰的外循环方式。ﻫ 本技术构成了脱硫灰的内循环、外循环的双重循环特征;构成了两级惯性分离串联的气固分离特征。若初级分离效率为η1,二级分离效率为η2,则总分离效率η=η1+(1-η1)η2。若两级分离效率分别为90%,则总效率高达99%;若两级分离效率分别为80%,则总分离效率仍高达96%。分离器是构成循环的关键部件,对分离器的要求是阻力低,具有适当的分离效率。ﻫ 2.2工艺特点
双循环流化床半干法烟气悬浮脱硫工艺
———————————————————————————————— 作者:
———————————————————————————————— 日期:
ﻩ
双循环流化床半干法烟气悬浮脱硫工艺ﻫ
作 者:马春元 发文日期:(2002-09-08) 本文章被浏览:1493
ﻫ 摘 要 文中介绍了一种双循环流化床烟气半干法悬浮脱硫工艺及其工业中试情况。并就适应于135(125)MW机组锅炉烟气脱硫工艺进行了技术方案分析。
ﻫ 关键词 脱硫 双循环 流化床 125MW机组
1 概述ﻫ 烟气双循环流化床半干法悬浮脱硫装置利用流化床原理,将脱硫剂流态化,烟气与脱硫剂在悬浮状态下进行脱硫反应。脱硫剂及灰循环利用,提高了脱硫塔内的脱硫剂浓度,增加了脱硫反应几率,同时提高了脱硫效率及脱硫剂的利用率。ﻫ 与湿法脱硫工艺相比,烟气双循环流化半干法悬浮脱硫工艺具有优势:没有腐蚀、带水等难对付的问题,没有水的二次污染;因不用水处理、不用烟气加热而具有较低的投资。
为了保障正常运行,系统设置三个主要的自动控制回路:ﻫ (1) 根据烟气出口的SO2浓度及烟气量控制石灰浆(或石灰)给料量,保证达到脱硫效率必须的钙硫比。烟气进口的SO2浓度参数用来校正或微调脱硫剂的给料量。
(2) 根据烟气出口的烟气露点(温度)直接调节喷水量,使系统反应温度接近露点达到最佳反应状态。