最全热轧无缝钢管生产工艺
无缝管工艺流程

无缝管工艺流程无缝管是一种重要的管材产品,广泛应用于石油、化工、天然气、电力、航空、造船、煤炭等行业。
无缝管具有高强度、耐高温、耐腐蚀等优点,因此在工业生产中有着重要的地位。
无缝管的生产工艺流程十分复杂,需要经过多道工序才能完成。
下面我们将详细介绍无缝管的生产工艺流程。
1. 原料准备。
无缝管的原料主要是钢坯,钢坯是通过炼钢厂生产的,具有一定的化学成分和机械性能。
在生产无缝管之前,首先需要对钢坯进行质量检测,确保其符合生产要求。
同时需要对钢坯进行预加热处理,以提高后续加工的效率。
2. 穿孔。
穿孔是无缝管生产的第一道工序,也是最关键的工序之一。
穿孔是将加热后的钢坯放入穿孔机中,通过旋转钢管和钻头的相对运动,在钢管内壁形成一定的孔径和壁厚。
这一工序的质量直接影响到后续工序的进行,因此需要严格控制穿孔的参数和工艺。
3. 热轧。
经过穿孔后的钢管需要进行热轧加工,将其加热到一定温度后进行轧制。
热轧是将钢坯进行加热,然后通过轧机进行轧制,使其形成一定的外径和壁厚。
热轧是无缝管生产中的重要工序,需要控制好加热温度和轧制参数,以保证产品的质量。
4. 酸洗。
经过热轧后的钢管表面会形成一层氧化皮,需要进行酸洗处理。
酸洗是将钢管浸入酸液中,去除表面的氧化皮和锈蚀,以保证产品的表面质量。
酸洗还可以改善钢管的表面光洁度,为后续的加工工序提供良好的条件。
5. 冷拔。
经过酸洗处理后的钢管需要进行冷拔加工,将其拉制成无缝管的标准尺寸。
冷拔是通过拉拔机将钢管拉制成一定的外径和壁厚,同时提高其表面质量和机械性能。
冷拔是无缝管生产中的关键工序,需要控制好拉拔参数,以保证产品的尺寸精度和表面光洁度。
6. 热处理。
经过冷拔后的无缝管需要进行热处理,以提高其机械性能和耐腐蚀性能。
热处理是将钢管加热到一定温度,然后进行保温和冷却,使其组织结构发生相应的改变。
热处理可以提高无缝管的强度和硬度,同时改善其组织结构,提高其耐腐蚀性能。
7. 检测。
经过热处理后的无缝管需要进行质量检测,包括化学成分分析、机械性能测试、尺寸检测等。
热轧无缝钢管工艺流程

热轧无缝钢管工艺流程热轧无缝钢管是一种常用的钢铁制品,广泛应用于石油、天然气、化工、电力、航空等领域。
本文将详细描述热轧无缝钢管的工艺流程,包括原材料准备、加热和轧制、冷却和修边等步骤。
1. 原材料准备热轧无缝钢管的原材料通常为圆坯(也称为毛坯)。
圆坯是通过连铸或锻造制成的,其直径和长度根据不同规格的钢管需求而定。
在生产之前,需要对圆坯进行外观检查和化学成分分析,确保其质量符合要求。
2. 加热和轧制2.1 加热圆坯需要经过加热处理,以提高其塑性和可变形性。
加热通常采用感应加热或火焰加热的方式进行。
在感应加热中,圆坯通过感应线圈中的电流产生涡流,并且由于涡流效应而发生加热。
火焰加热则是利用火焰的高温将圆坯加热至适当的温度。
2.2 轧制加热后的圆坯被送入轧机,经过一系列的轧制工序进行塑性变形。
首先,圆坯通过粗轧机进行初步轧制,将其直径减小到一定程度。
然后,通过中间轧机和精轧机进行进一步的轧制,使钢管直径逐渐减小,并且壁厚逐渐增加。
在这个过程中,可以根据需要使用多辊轧制机、斜辊轧制机等不同类型的设备。
3. 冷却和修边3.1 冷却经过轧制后的钢管需要进行冷却处理,以恢复其力学性能和尺寸稳定性。
通常采用水冷或气冷的方式进行。
水冷可以快速降低钢管温度,并且具有良好的冷却效果;气冷则相对较慢,但可以避免钢管表面出现水迹等问题。
3.2 修边经过冷却处理后的钢管可能存在一些缺陷或不规则形状,需要进行修边操作。
修边主要是通过切割或磨削等方式将钢管两端的不规则部分去除,使其具有一定的平整度和尺寸精度。
4. 检测和包装4.1 检测热轧无缝钢管在生产过程中需要进行多种检测,以确保其质量符合要求。
常见的检测方法包括尺寸检测、外观检查、化学成分分析、力学性能测试等。
通过这些检测手段,可以对钢管的尺寸、表面质量、化学成分和力学性能等进行全面评估。
4.2 包装经过检测合格的热轧无缝钢管需要进行包装,以便运输和储存。
常见的包装方式包括捆扎包装、打包包装等。
无缝钢管的热轧工艺

无缝钢管1。
无缝钢管的制造加工方法:(1)热轧(挤压无缝钢管):圆管坯→加热→穿孔→三辊斜轧、连轧或挤压→脱管→定径(或减径)→冷却→矫直→水压试验(或探伤)→标记→入库(2)冷拔(轧)无缝钢管:圆管坯→加热→穿孔→打头→退火→酸洗→涂油(镀铜)→多道次冷拔(冷轧)→坯管→热处理→矫直→水压试验(探伤)→标记→入库2。
热轧(1)热轧的概念:热轧(hot rolling)是相对于冷轧而言的,冷轧是在再结晶温度以下进行的轧制,而热轧就是在再结晶温度以上进行的轧制.(2)热轧的优缺点优点:a.热轧能显著降低能耗,降低成本。
热轧时金属塑性高,变形抗力低,大大减少了金属变形的能量消耗.b.热轧能改善金属及合金的加工工艺性能,即将铸造状态的粗大晶粒破碎,显著裂纹愈合,减少或消除铸造缺陷,将铸态组织转变为变形组织,提高合金的加工性能。
c.热轧通常采用大铸锭,大压下量轧制,不仅提高了生产效率,而且为提高轧制速度、实现轧制过程的连续化和自动化创造了条件。
缺点:a。
经过热轧之后,钢材内部的非金属夹杂物(主要是硫化物和氧化物,还有硅酸盐)被压成薄片,出现分层(夹层)现象。
分层使钢材沿厚度方向受拉的性能大大恶化,并且有可能在焊缝收缩时出现层间撕裂.焊缝收缩诱发的局部应变时常达到屈服点应变的数倍,比荷载引起的应变大得多。
b.不均匀冷却造成的残余应力.残余应力是在没有外力作用下内部自相平衡的应力,各种截面的热轧型钢都有这类残余应力,一般型钢截面尺寸越大,残余应力也越大。
残余应力虽然是自相平衡的,但对钢构件在外力作用下的性能还是有一定影响。
如对变形、稳定性、抗疲劳等方面都可能产生不利的作用。
c。
热轧不能非常精确地控制产品所需的力学性能,热轧制品的组织和性能不能够均匀。
其强度指标低于冷作硬化制品,而高于完全退火制品;塑性指标高于冷作硬化制品,而低于完全退火制品。
d。
热轧产品厚度尺寸较难控制,控制精度相对较差;热轧制品的表面较冷轧制品粗糙Ra值一般在0。
无缝钢管生产工艺流程

无缝钢管生产工艺流程
无缝钢管是一种没有焊接接头的钢管,它具有较高的强度和抗压能力,广泛应用于石油、化工、天然气、航空航天等领域。
下面将介绍一下无缝钢管的生产工艺流程。
无缝钢管的生产工艺主要包括三个部分:钢坯的制备、热轧和冷加工。
首先,钢坯的制备是生产无缝钢管的关键步骤之一。
钢坯(一般为圆坯)可以通过两种方法制备:一是采用连铸技术,通过液态钢的连续铸造获得钢坯;二是采用轧制方法,通过将坯料轧制成所需直径的钢坯。
其次,热轧是无缝钢管的主要生产工艺。
将钢坯加热到适当的温度,然后经过一连串的轧制和拉拔过程,最终成形为外径、壁厚与长度符合要求的无缝钢管。
热轧过程中,首先采用粗轧将钢坯进行初轧成形,然后通过中轧和精轧过程进行进一步的轧制。
轧制过程中,会采用不同直径的轧辊进行多道次的轧制,使钢的外径和壁厚逐渐减小,达到所需尺寸。
最后,使用拉拔机将热轧后的钢管进行拉拔,使其尺寸更加精确。
最后,冷加工是对热轧钢管的进一步加工和改善。
冷加工是通过轧制和拉拔等工艺对热轧钢管进行调整和改善。
首先,使用冷轧机将钢管进行冷轧,使其尺寸更加精确,并提高表面光洁度。
然后,通过冷拉机对冷轧钢管进行拉拔,改善内外径的精度和表面质量。
总之,无缝钢管的生产工艺流程包括钢坯的制备、热轧和冷加工三个步骤。
每个步骤都是必不可少的,它们相互配合,共同完成对钢坯的加工和成形,最终得到优质的无缝钢管。
这一工艺流程是现代工业生产中不可缺少的一环,为各行各业的发展提供了坚实的支撑。
无缝钢管制作方法

无缝钢管制作方法无缝钢管是一种不具有焊接接缝的钢管,其制作方法独特而精细。
本文将介绍无缝钢管的制作方法以及相关工艺和设备。
无缝钢管的制作方法主要包括:热轧法、冷轧法、冷拔法和挤压法。
下面将分别介绍这几种制作方法。
热轧法是最常用的制作无缝钢管的方法之一。
这种方法首先将钢坯加热到一定温度,然后通过连续轧制的方式将钢坯轧制成管状。
热轧法制作的无缝钢管具有良好的韧性和塑性,适用于各种应用场合。
冷轧法是在室温下制作无缝钢管的方法。
这种方法需要将钢坯加热到较高温度后进行轧制,然后通过冷却和拉伸的工艺来制作无缝钢管。
冷轧法制作的无缝钢管表面光滑,尺寸精确,适用于对外观和尺寸要求较高的场合。
冷拔法是将热轧或冷轧的钢管继续进行加工的方法。
这种方法需要将钢管加热到一定温度后进行拉拔,通过不断减小模具的孔径来制作无缝钢管。
冷拔法制作的无缝钢管表面光滑,尺寸精确,适用于对尺寸要求较高的场合,如汽车、机械等领域。
挤压法是将金属坯料置于模具中,通过施加压力使其从模具的孔口挤出,形成无缝钢管的方法。
这种方法适用于制作大口径和壁厚较薄的无缝钢管,具有生产效率高、产品质量好等优点。
除了上述的制作方法,制作无缝钢管还需要使用一些特殊的设备和工艺。
例如,热轧法需要使用轧机和加热炉,冷轧法需要使用冷轧机和冷却设备,冷拔法需要使用拉拔机和模具,挤压法需要使用挤压机和模具等。
在无缝钢管的制作过程中,还需要注意一些关键的工艺控制。
例如,控制钢坯的加热温度和轧制温度,以及控制轧制力和轧制速度等。
这些工艺参数的控制对于保证无缝钢管的质量和性能至关重要。
无缝钢管的制作方法多种多样,每种方法都有其适用的场合和优劣势。
在实际应用中,需要根据具体的要求来选择合适的制作方法和工艺,以确保无缝钢管的质量和性能。
通过不断改进和创新,无缝钢管的制作技术将会得到进一步的提升和发展。
轧管工艺技术(1)——《热轧无缝钢管实用技术》

78技术讲座轧管工艺技术(I)-《热轧无缝钢管实用技术》轧管工序的主要任务是将芯棒穿入毛管内孔,在外部工具(轧辐或银模)的作用下,压缩毛管的外径和壁厚,从而获得尺寸和质量符合要求的荒管。
按轧管机的结构和金属变形方式的不同,可将轧管机分为纵轧管机和斜轧管机。
纵轧管机主要有连轧管机、顶管机(CPE)、自动轧管机、周期轧管机、挤压管机和径向锻管机等;斜轧管机主要有阿塞尔(Assel)轧管机、狄塞尔(Diescher)轧管机、精密(Accu Roll)轧管机、斜轧扩管机和行星轧管机等。
轧管机按机架数量的多少,可分为单机架轧管机和多机架轧管机。
单机架轧管机有自动轧管机、阿塞尔轧管机、狄塞尔轧管机、精密轧管机、周期轧管机、挤压管机、径向锻管机和行星轧管机等。
多机架轧管机有连轧管机和顶管机等。
目前,使用最为广泛的是限动芯棒连轧管机和精密轧管机,其次是周期轧管机、阿塞尔轧管机、挤压管机和顶管机。
行星轧管机还处在推广应用阶段。
1连轧管工艺技术1.1连轧管机概况连轧管法是将经过润滑后的长芯棒穿入毛管内孔,芯棒和毛管一同连续通过多个呈串列布置的轧车昆孔型,将毛管轧制成符合尺寸和质量要求的荒管的一种轧管方法。
早在1843年,就有人开始研究连轧管法,历经几代人对连轧管工艺、芯棒操作方式、机架数、机架形式和传动方式等方面的研究和生产实践,连轧管技术日臻成熟,连轧管机已成为当今业界首选的无缝钢管轧机。
连轧管机的最大延伸系数可达3.5-6.0,荒管最大出口速度可达5~7m/so其主要特点是生产能力大,生产效率高;所轧制的荒管长度长,产品质量好,规格范围广等。
连轧管机按机架型式不同,可分为二辘式连轧管机和三银式连轧管机;按芯棒操作方式的不同,可分为全浮动芯棒连轧管机、限动芯棒连轧管机和半浮动(也称半限动)芯棒连轧管机。
限动芯棒连轧管机的芯棒循环可分为芯棒在线回退和线外循环两种。
二辐式连轧管机由两个轧槽组成孔型,相邻机架的轧银呈90。
无缝不锈钢管制作工艺

无缝不锈钢管制作工艺无缝不锈钢管的制造工艺可以大致分为两类:热轧(挤压)无缝钢管和冷拔(轧制)无缝钢管。
这两类工艺在细节上有所不同,但都是为了获得高质量的无缝钢管。
一、热轧(挤压)无缝钢管的制作工艺如下:1、圆管坯:这是无缝钢管的原材料,一般由钢锭或者钢坯经过热轧或挤压成一定尺寸的圆形截面。
这是无缝钢管制造的第一步,坯料的质量直接影响到后续工艺的效果。
2、加热:将管坯加热到一定温度,使其软化,以便进行后续的穿孔和轧制。
加热过程需要严格控制温度,以确保坯料的软化效果。
3、穿孔:将加热后的管坯穿孔,形成空心钢管。
这是无缝钢管制造的关键步骤之一,穿孔的效果直接影响到钢管的内部质量。
4、三辊交叉轧制、连续轧制或挤压:根据工艺要求,使用三辊轧机、连续轧机或挤压机对钢管进行轧制或挤压,以得到所需的外径和壁厚。
这一步骤需要精确控制轧制力度和速度,以保证钢管的尺寸精度。
5、管道剥离:将钢管从穿孔中拔出。
这一步骤需要保证钢管的表面光滑,无划痕等缺陷。
6、上浆(或减量):在钢管表面涂抹润滑剂或其他材料,以减小轧制过程中的摩擦力。
这有助于提高轧制效率,降低能耗。
7、冷却:将钢管冷却至一定温度,使其保持所需的形状和性能。
冷却速度和温度控制是关键,过快的冷却可能导致钢管变形。
8、矫直:对钢管进行矫直,以消除轧制过程中产生的弯曲和扭曲。
矫直质量直接影响到钢管的直线度和平整度。
9、水压试验(或探伤):对钢管进行水压试验或无损探伤,以确保其密封性能和无缺陷。
这是质量控制的重要环节。
10、标记:在钢管上打上标记,包括规格、生产日期等。
这有助于区分不同型号和生产批次的钢管。
11、仓储:将钢管储存起来,以备后续的处理或使用。
合理的仓储条件可以保证钢管的质量稳定。
二、冷拔(轧制)无缝钢管的制作工艺如下:1、圆管坯:与热轧(挤压)无缝钢管的坯料相同。
2、加热:将管坯加热到一定温度,使其软化。
3、穿孔:将加热后的管坯穿孔,形成空心钢管。
4、退火:使钢管软化,以减小轧制过程中的变形阻力。
无缝钢管生产工艺流程
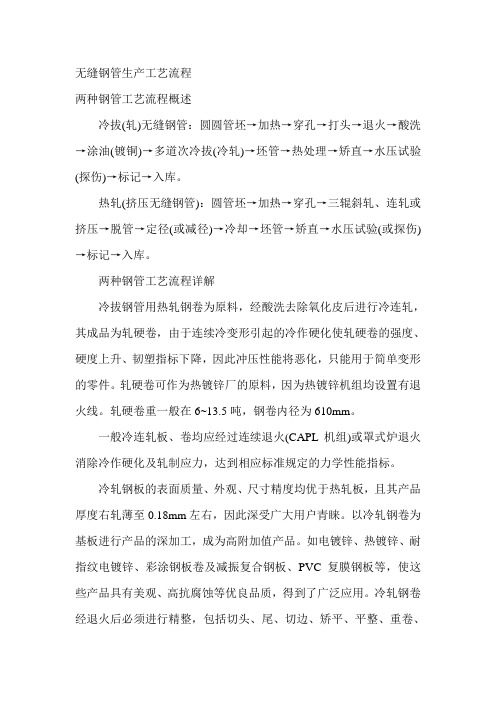
无缝钢管生产工艺流程两种钢管工艺流程概述冷拔(轧)无缝钢管:圆圆管坯→加热→穿孔→打头→退火→酸洗→涂油(镀铜)→多道次冷拔(冷轧)→坯管→热处理→矫直→水压试验(探伤)→标记→入库。
热轧(挤压无缝钢管):圆管坯→加热→穿孔→三辊斜轧、连轧或挤压→脱管→定径(或减径)→冷却→坯管→矫直→水压试验(或探伤)→标记→入库。
两种钢管工艺流程详解冷拔钢管用热轧钢卷为原料,经酸洗去除氧化皮后进行冷连轧,其成品为轧硬卷,由于连续冷变形引起的冷作硬化使轧硬卷的强度、硬度上升、韧塑指标下降,因此冲压性能将恶化,只能用于简单变形的零件。
轧硬卷可作为热镀锌厂的原料,因为热镀锌机组均设置有退火线。
轧硬卷重一般在6~13.5吨,钢卷内径为610mm。
一般冷连轧板、卷均应经过连续退火(CAPL机组)或罩式炉退火消除冷作硬化及轧制应力,达到相应标准规定的力学性能指标。
冷轧钢板的表面质量、外观、尺寸精度均优于热轧板,且其产品厚度右轧薄至0.18mm左右,因此深受广大用户青睐。
以冷轧钢卷为基板进行产品的深加工,成为高附加值产品。
如电镀锌、热镀锌、耐指纹电镀锌、彩涂钢板卷及减振复合钢板、PVC 复膜钢板等,使这些产品具有美观、高抗腐蚀等优良品质,得到了广泛应用。
冷轧钢卷经退火后必须进行精整,包括切头、尾、切边、矫平、平整、重卷、或纵剪切板等。
冷轧产品广泛应用于汽车制造、家电产品、仪表开关、建筑、办公家具等行业。
钢板捆包后的每包重量为3~5吨。
平整分卷重一般为3~10吨/卷。
钢卷内径610mm。
热轧钢管用连铸板坯或初轧板坯作原料,经步进式加热炉加热,高压水除鳞后进入粗轧机,粗轧料经切头、尾、再进入精轧机,实施计算机控制轧制,终轧后即经过层流冷却和卷取机卷取、成为直发卷。
直发卷的头、尾往往呈舌状及鱼尾状,厚度、宽度精度较差,边部常存在浪形、折边、塔形等缺陷。
其卷重较重、钢卷内径为760mm。
(一般制管行业喜欢使用。
)将直发卷经切头、切尾、切边及多道次的矫直、平整等精整线处理后,再切板或重卷,即成为:热轧钢板、平整热轧钢卷、纵切带等产品。
热轧无缝钢管生产工艺流程

热轧无缝钢管生产工艺流程热轧无缝钢管是一种常见的钢管产品,广泛应用于石油、天然气、化工、电力、航空、航天、环保等领域。
它具有高强度、耐腐蚀、耐高温等优点,因此在各个行业中都有着重要的地位。
下面将介绍热轧无缝钢管的生产工艺流程。
热轧无缝钢管的原材料是钢坯。
钢坯是经过炼钢厂熔炼后得到的一种半成品,通常为方坯或圆坯。
钢坯的质量对于钢管的生产具有重要的影响,因此要对钢坯进行严格的质量控制。
第二步是加热。
将钢坯加热到适当的温度,一般为1150℃左右。
加热的目的是使钢坯变得柔软,方便后续的轧制和成形。
在加热过程中,需要控制加热温度和加热时间,以确保钢坯达到预定的加热要求。
第三步是轧制。
将加热后的钢坯送入轧机进行轧制。
轧制一般分为粗轧和精轧两个阶段。
粗轧是将钢坯通过辊道进行初步的压制,使其形成一定的形状和尺寸。
精轧是在粗轧后对钢坯进行进一步的压制,使其达到预定的尺寸和表面质量要求。
第四步是定径。
将轧制后的钢坯通过定径机进行定径。
定径机是一种专门用于调整钢管外径的设备。
通过定径机的作用,可以使钢管的外径达到预定的尺寸要求。
第五步是坯管退火。
将定径后的钢管进行退火处理。
退火是将钢管加热到一定温度,然后缓慢冷却的过程。
退火的目的是消除钢管内部的应力,改善钢管的机械性能和物理性能。
第六步是酸洗。
将退火后的钢管进行酸洗处理。
酸洗是将钢管浸泡在酸液中,去除钢管表面的氧化物和锈蚀物,以提高钢管的表面质量。
第七步是冷拉。
将酸洗后的钢管通过冷拉机进行冷拉。
冷拉是将钢管通过模具进行拉伸,使其达到预定的尺寸和表面质量要求。
冷拉还可以提高钢管的机械性能,使其更加坚固和耐久。
最后一步是检验和包装。
对生产出来的热轧无缝钢管进行检验,包括外观质量、尺寸偏差、物理性能等方面的检测。
合格的钢管经过检验后,进行包装和标识,以便运输和使用。
以上就是热轧无缝钢管的生产工艺流程。
每个环节都非常重要,对于钢管的质量和性能有着直接的影响。
通过严格的生产工艺流程控制和质量管理,可以生产出高质量的热轧无缝钢管,满足各种工程和应用的需求。
热轧钢管生产工艺课件

安全教育培训情况
检查员工是否接受安全教育培训,是否掌握 安全知识和技能,培训效果是否达标。
应急预案制定和演练活动安排
应急预案制定
针对可能发生的生产安全事故, 制定相应的应急预案,明确应急 组织、通讯联络、现场处置等方
面要求。
应急演练计划
制定应急演练计划,包括演练时 间、地点、参与人员等,确保演
练活动有序进行。
分类
根据钢管的截面形状和用途,热轧钢 管可分为无缝钢管和焊接钢管两大类 。其中,无缝钢管又可分为热轧无缝 钢管和冷拔无缝钢管两种。
生产工艺流程及特点
生产工艺流程
热轧钢管的生产工艺流程包括原料准备、加热、穿 孔、轧制、定径、冷却、矫直、切割、检验等环节 。其中,加热温度和轧制速度是影响钢管质量的关 键因素。
发展趋势
未来,随着科技的不断进步和环保政策的加强,热轧钢管行业将面临转型升级的压力。一方面,企业需要加大技 术创新力度,研发高强度、耐腐蚀、轻量化的新型钢管产品;另一方面,企业需要推进绿色生产,降低能耗和排 放,实现可持续发展。
02
原料准备与加热制度
Chapter
原料选择与检验标准
原料选择
选用符合标准要求的钢坯作为原 料,确保化学成分、尺寸和表面 质量等指标合格。
热轧钢管质量控制
讲述钢管尺寸精度、表面质量、力学性能等方面的质量要求,以及 质量检查与评估的方法。
行业发展趋势分析
1 2 3
绿色环保生产
随着环保政策的日益严格,热轧钢管生产行业将 更加注重清洁生产和节能减排,推广绿色制造技 术和循环经济模式。
智能化与自动化
智能化制造和自动化技术将在热轧钢管生产中发 挥越来越重要的作用,提高生产效率和产品质量 稳定性。
无缝钢管生产工艺流程

无缝钢管生产工艺流程无缝钢管是一种通过热轧、冷轧或冷拔等加工工艺制成的钢管,具有优良的机械性能和高度的可靠性。
无缝钢管广泛应用于石油、天然气、化工、电力、航空航天等领域。
本文将详细介绍无缝钢管的生产工艺流程,包括原材料准备、加热处理、穿孔、轧制和尺寸修整等步骤。
1. 原材料准备•钢坯选择:选用合适的碳素钢或合金钢作为原材料,根据不同的应用需求选择不同牌号的钢坯。
•检查质量:对每批钢坯进行外观检查和化学成分分析,确保质量符合要求。
•切割:将钢坯按照所需长度切割成适当尺寸。
2. 加热处理•加热炉预热:将切割好的钢坯放入加热炉中进行预热处理。
预热温度根据不同牌号和规格的钢坯而定,一般在1000℃以上。
•坯料调质:将预热好的钢坯放入调质炉中进行调质处理,以提高其可塑性和韧性。
3. 穿孔•穿孔机加工:将调质后的钢坯放入穿孔机中进行穿孔加工。
穿孔机通过旋转刀具对钢坯进行连续穿孔,形成初始管型。
•冷却:冷却穿孔后的管坯,以降低温度并增加管材硬度。
4. 轧制•热轧:将冷却后的管坯放入热轧机中进行热轧处理。
热轧机通过多道次的辊道轧制,使管坯逐渐变长、变薄,并最终形成无缝钢管。
•冷拔:将热轧得到的管坯放入冷拔机中进行冷拔处理。
冷拔机通过拉拽和拉伸的力量,使管坯进一步变细、变长,并提高表面光洁度和尺寸精度。
5. 尺寸修整•切割:根据客户需求,将冷拔后的无缝钢管切割成所需长度。
•调直:将切割好的无缝钢管放入调直机中进行调直处理,以消除管材的弯曲和扭曲。
•酸洗:将调直后的无缝钢管放入酸洗槽中进行酸洗处理,去除表面氧化层和锈蚀物。
•水冷:用水对酸洗后的无缝钢管进行冷却,恢复环境温度。
6. 检测与包装•检测:对生产好的无缝钢管进行外观检查、尺寸检测、力学性能测试等多项检测,确保质量符合标准要求。
•包装:将合格的无缝钢管按照规格和长度分类包装,并附上标签和证书。
以上是无缝钢管生产工艺流程的主要步骤。
每个步骤都需要精细操作和严格控制,以确保最终产品质量符合要求。
无缝钢管生产工艺流程
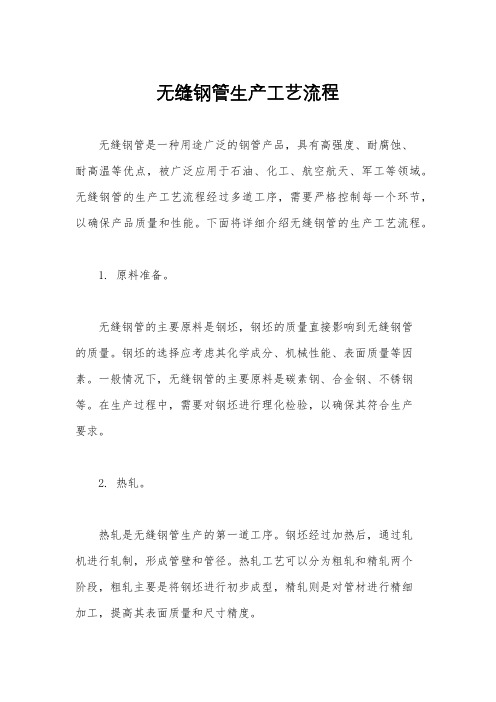
无缝钢管生产工艺流程无缝钢管是一种用途广泛的钢管产品,具有高强度、耐腐蚀、耐高温等优点,被广泛应用于石油、化工、航空航天、军工等领域。
无缝钢管的生产工艺流程经过多道工序,需要严格控制每一个环节,以确保产品质量和性能。
下面将详细介绍无缝钢管的生产工艺流程。
1. 原料准备。
无缝钢管的主要原料是钢坯,钢坯的质量直接影响到无缝钢管的质量。
钢坯的选择应考虑其化学成分、机械性能、表面质量等因素。
一般情况下,无缝钢管的主要原料是碳素钢、合金钢、不锈钢等。
在生产过程中,需要对钢坯进行理化检验,以确保其符合生产要求。
2. 热轧。
热轧是无缝钢管生产的第一道工序。
钢坯经过加热后,通过轧机进行轧制,形成管壁和管径。
热轧工艺可以分为粗轧和精轧两个阶段,粗轧主要是将钢坯进行初步成型,精轧则是对管材进行精细加工,提高其表面质量和尺寸精度。
3. 穿孔。
经过热轧后的钢坯需要进行穿孔,形成无缝钢管的管壁。
穿孔工艺是将加热后的钢坯放入穿孔机中,通过旋转锥形工具对钢坯进行穿孔,形成管状结构。
4. 酸洗。
酸洗是为了去除无缝钢管表面的氧化铁皮和锈蚀物,提高管材的表面质量。
酸洗工艺一般采用盐酸或硫酸进行酸洗,去除表面氧化物,然后经过清洗和中和处理,最终得到清洁的钢管表面。
5. 冷拔。
冷拔是为了提高无缝钢管的尺寸精度和表面质量。
经过酸洗的钢管通过冷拔机进行拉拔,使得管材的尺寸精度更高,表面质量更好。
6. 热处理。
热处理是为了改善无缝钢管的组织结构和性能。
经过冷拔后的钢管需要进行退火或正火处理,以消除加工硬化和应力,提高钢管的塑性和韧性。
7. 直径校直。
直径校直是为了保证无缝钢管的尺寸精度和表面质量。
经过热处理的钢管通过校直机进行校直,使得管材的直径误差和偏心率达到生产要求。
8. 检测。
无缝钢管生产的最后一个环节是对产品进行检测。
检测项目包括外观质量、尺寸精度、化学成分、机械性能等多个方面。
合格的产品才能够出厂销售。
通过以上工艺流程,钢坯经过一系列的加工和处理,最终形成优质的无缝钢管产品。
无缝钢管工艺
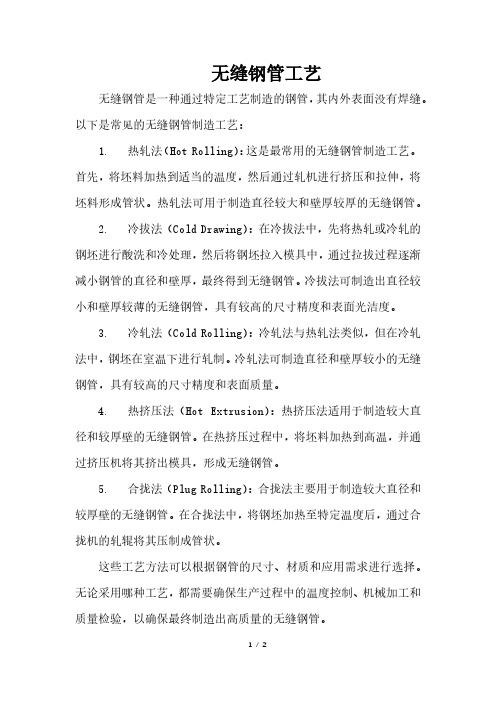
无缝钢管工艺
无缝钢管是一种通过特定工艺制造的钢管,其内外表面没有焊缝。
以下是常见的无缝钢管制造工艺:
1. 热轧法(Hot Rolling):这是最常用的无缝钢管制造工艺。
首先,将坯料加热到适当的温度,然后通过轧机进行挤压和拉伸,将坯料形成管状。
热轧法可用于制造直径较大和壁厚较厚的无缝钢管。
2. 冷拔法(Cold Drawing):在冷拔法中,先将热轧或冷轧的钢坯进行酸洗和冷处理,然后将钢坯拉入模具中,通过拉拔过程逐渐减小钢管的直径和壁厚,最终得到无缝钢管。
冷拔法可制造出直径较小和壁厚较薄的无缝钢管,具有较高的尺寸精度和表面光洁度。
3. 冷轧法(Cold Rolling):冷轧法与热轧法类似,但在冷轧法中,钢坯在室温下进行轧制。
冷轧法可制造直径和壁厚较小的无缝钢管,具有较高的尺寸精度和表面质量。
4. 热挤压法(Hot Extrusion):热挤压法适用于制造较大直径和较厚壁的无缝钢管。
在热挤压过程中,将坯料加热到高温,并通过挤压机将其挤出模具,形成无缝钢管。
5. 合拢法(Plug Rolling):合拢法主要用于制造较大直径和较厚壁的无缝钢管。
在合拢法中,将钢坯加热至特定温度后,通过合拢机的轧辊将其压制成管状。
这些工艺方法可以根据钢管的尺寸、材质和应用需求进行选择。
无论采用哪种工艺,都需要确保生产过程中的温度控制、机械加工和质量检验,以确保最终制造出高质量的无缝钢管。
热轧无缝钢管工艺流程
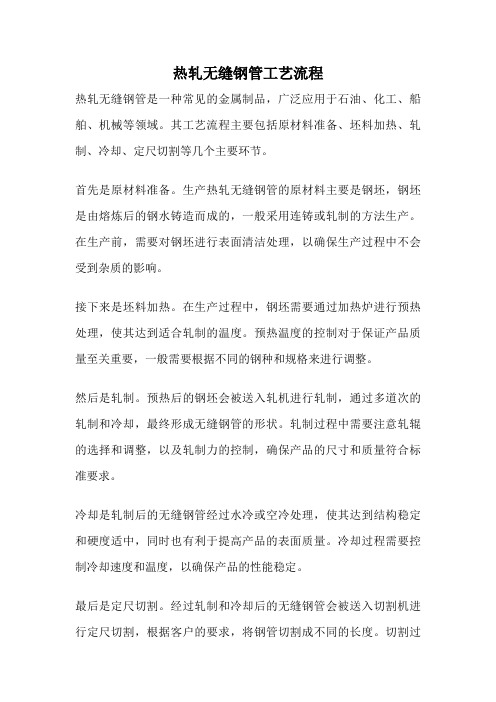
热轧无缝钢管工艺流程
热轧无缝钢管是一种常见的金属制品,广泛应用于石油、化工、船舶、机械等领域。
其工艺流程主要包括原材料准备、坯料加热、轧制、冷却、定尺切割等几个主要环节。
首先是原材料准备。
生产热轧无缝钢管的原材料主要是钢坯,钢坯是由熔炼后的钢水铸造而成的,一般采用连铸或轧制的方法生产。
在生产前,需要对钢坯进行表面清洁处理,以确保生产过程中不会受到杂质的影响。
接下来是坯料加热。
在生产过程中,钢坯需要通过加热炉进行预热处理,使其达到适合轧制的温度。
预热温度的控制对于保证产品质量至关重要,一般需要根据不同的钢种和规格来进行调整。
然后是轧制。
预热后的钢坯会被送入轧机进行轧制,通过多道次的轧制和冷却,最终形成无缝钢管的形状。
轧制过程中需要注意轧辊的选择和调整,以及轧制力的控制,确保产品的尺寸和质量符合标准要求。
冷却是轧制后的无缝钢管经过水冷或空冷处理,使其达到结构稳定和硬度适中,同时也有利于提高产品的表面质量。
冷却过程需要控制冷却速度和温度,以确保产品的性能稳定。
最后是定尺切割。
经过轧制和冷却后的无缝钢管会被送入切割机进行定尺切割,根据客户的要求,将钢管切割成不同的长度。
切割过
程中需要注意切割速度和刀具的选择,以保证切割的精度和效率。
总的来说,热轧无缝钢管的生产工艺流程复杂,需要各个环节的紧密配合和严格控制,才能生产出符合标准要求的高质量产品。
通过不断优化工艺流程和技术装备,可以提高生产效率,降低生产成本,满足市场需求,促进行业的发展。
轧管工艺流程简介

热轧无缝钢管生产线工艺流程一、天津钢管公司热轧无缝钢管轧机类别简介天津钢管公司拥有三种热轧无缝钢管生产线,每一种生产线对应着一种轧机,分别为MPM轧机,阿塞尔轧机和PQF轧机。
其中一套轧管生产线为φ250mm口径MPM轧机,三套轧管生产线为219mm 口径阿塞尔轧机,其余生产线为168mm、258mm和460mm口径PQF 轧机。
限动芯棒连轧管机,英文缩写MPM(即Multi-Stand Pipe Mill),是无缝钢管生产中的重要设备。
中国第一套限动芯棒连轧管机组,引进自意大利,于1992年在天津钢管集团股份有限公司投产。
经技术改造,天津钢管集团的Φ250mm限动芯棒连轧管机组已经由设计年产能力50万吨,扩大到现在的年产能力100万吨。
(注:天津钢管公司轧管厂Φ250MPM机组,引进的是意大利皮昂蒂公司的技术和设备。
该项目竣工投产时,时任意大利伊利集团总裁的普罗迪先生亲自前来剪彩。
2006年,作为意大利总理的普罗迪再次来到钢管公司)。
阿塞尔轧机由一个名叫W .J.Assel 的人于1932年发明。
天津钢管集团股份有限公司2005年新建的现代Φ219mm阿塞尔轧管机组,引进了德国SMS Meer公司近年来最新开发的阿塞尔轧制工艺技术和ABB公司最新的ACS6000SD传动控制系统。
二套轧管的168mm口径PQF(Premium Quality Finishing)轧机是世界上第一套PQF轧机,由SMS MEER公司设计,2003年底热试成功。
由于是一个新开发出的轧制技术,作为第一个使用该技术的天津钢管公司冒了很大的风险。
钢管公司与西马克公司签订合同的时候,提到了五年之内世界上的其他钢管公司不得上PQF轧机生产线,以保证自己对于该项技术的领先。
在以后的几年里。
天津钢管公司又陆续筹建了258mm口径和460mm口径PQF轧管生产线。
二、阿塞尔轧机、MPM轧机和PQF轧机的简单对比1.阿塞尔轧机:三辊式,单机架;轧制时,钢管及芯棒一起作螺旋运2.MPM轧机:两辊式,多机架;轧制时,钢管及芯棒一起作直线运3.PQF轧机:三辊式,多机架;轧制时,钢管及芯棒一起作直线运动。
无缝钢管生产工艺流程(一)

无缝钢管生产工艺流程(一)无缝钢管生产工艺1. 前置处理工序1.材料选料:根据使用要求和环境条件,选择相应的材料。
2.加热处理:将钢坯加热到一定温度,以便后面的轧制和穿孔等操作。
3.轧制:将加热后的钢坯进行轧制,使其成为所需大小和形状的毛坯。
2. 穿孔工序1.冷穿孔:用轮胎式轧辊将毛坯推入圆锥形模具中,从而穿出成型管。
2.热穿孔:将毛坯在高温下进行穿孔成型,常用的方法为两辊挤压法和三辊挤压法。
3. 热轧加工工序1.热轧加工:将穿孔成型后的钢管进行热轧加工,使其成为所需的精确尺寸和形状。
2.热处理:将热轧加工后的钢管进行淬火或回火处理,以改善其力学性能。
4. 表面处理工序1.啮缝:用啮合器将钢管表面的氧化物和锈垢去除。
2.直条砂轮:用研磨机将钢管表面进行粗磨。
3.高速砂带:用高速砂带机将钢管表面进行精磨,使其达到表面光洁度要求。
5. 检测工序1.超声波检测:用超声波探头对钢管进行检测,以发现可能存在的裂纹等问题。
2.磁粉探伤:涂上磁粉的钢管在磁粉感应下进行检测,以发现表面和内部的裂纹等问题。
3.气密性检测:将气密性要求高的钢管进行检测,以发现可能存在的气泄漏等问题。
6. 包装工序1.包装:将检测合格的钢管进行包装,以保护其表面不受污染和磨损。
2.贮存:将已包装的钢管进行贮存,等待出售或运输。
7. 总结无缝钢管的制造工艺是一个复杂的过程,需要严格的控制质量和工艺参数,以保证钢管的力学性能和表面质量符合使用要求。
从前置处理工序到最终的包装贮存,每个环节都有严格的要求和标准。
检测工序的重要性也不可小觑,只有通过科学的检测才能保证无缝钢管的质量和可靠性。
钢管热处理工艺技术(Ⅱ)--《热轧无缝钢管实用技术》

80技术讲座钢管热处理工艺技术(n )—《热轧无缝钢管实用技术》3钢管在线常化和直接淬火工艺3.1在线常化钢管在线常化是指将轧制后的荒管直接放在常 化冷床上冷却到温度以下,使其发生共析转变 (由奥氏体全部转变为铁素体+珠光体组织)之后,再送进再加热炉中加热到温度以上,并保温一 段时间,直到钢管组织又全部转变成奥氏体后出 炉,经定(减)径机定(减)径,并按一定的冷却速度 冷却到室温,以获得较为细小、均勻的铁素体+珠 光体组织的一种热处理工艺。
在线常化工艺可节约能源,降低生产成本,简 化生产工序。
如果将在线常化与控制冷却相结合, 钢管就可以得到良好的金相组织,改善其综合性 能,尤其是能大幅度提高钢管的冲击韧性;但在线 常化工艺会影响生产节奏,降低轧机产量。
根据在线常化的工艺要求,必须注意以下3个 关键要点。
(1)荒管进再加热炉之前的温度控制。
荒管在进再加热炉之前,必须冷却到温度以下。
为减少冷却时间,提高生产效率可采用吹风或吹风+喷雾的方式加大钢管的冷却速度。
(2) 再加热炉加热温度和加热时间的控制。
荒 管再加热温度应控制在以上30~50 1,并保温 适当时间,使钢中奥氏体均匀化、晶粒细小。
为了 防止奥氏体晶粒粗化,除要严格控制加热温度和加 热时间外,还可在钢的成分设计上,适量添加微量 合金元素,如V 、Ti 、N b 等。
这些元素与钢中的C 、N 元素形成的M (C 、N )化合物质点,可以有效抑制晶粒长大。
(3) 钢管终轧温度和冷却速度的控制。
控制钢 管的终轧温度并采用控冷技术,以加快钢管定(减) 径后的冷却速度。
在线常化工艺已广泛应用于油井管、锅炉管、 结构管、流体输送管等钢管品种的生产。
3.2直接淬火直接淬火是指钢管经过定(减)径后,利用钢管 自身的余热进行淬火,以获得马氏体组织的一种热处理工艺。
东北大学研究的钢管定(减)径后特快速 冷却直接淬火工艺,已成功应用于工业生产,并取 得了很好的效果。
无缝钢管生产工艺流程及轧机轧辊的选用

无缝钢管生产工艺流程及轧机轧辊的选用无缝钢管生产流程及几种主要轧辊工具的材质、硬度选用介绍如下:1无缝钢管生产工艺流程无缝钢管生产主要经过以下几道工序;管坯——切断——加热——穿孔——轧管——定(减)径——矫直——切头尾——检验——包装——入库。
而根据轧管方式的不同可将无缝钢管轧机分为自动轧管机组、连轧管机组(MPM两辊连轧管机组、PQF三辊连轧管机组)、Assel轧辊机组、Accu轧管机组、周期轧管机组等,新上的轧机以MPM连轧管机组、PQF三辊连轧管机组居多,比如天津钢管公司的Φ460、Φ258PQF连轧管机组、衡阳钢管的Φ273MPM连轧管机组、攀钢成都无缝的Φ340MPM连轧管机组、Φ159PQM连轧管机组、鞍山Φ170PQF连轧管机组等。
2穿孔机管坯穿孔是热轧无缝钢管生产中最重要的变形工序,它的任务是将实心管坯穿轧成空心毛管。
根据穿孔机的结构和穿孔过程的变形特点,可将现有的穿孔方法分为:斜轧穿孔、推轧穿孔和压力穿孔,而以斜轧穿孔应用最为广泛,斜轧穿孔机轧辊的形状有辊式、菌式(锥形)和盘式三种,辊式穿孔机轧辊应用于小型轧机,而大型的机组穿孔机采用菌式轧辊。
盘式穿孔机应用较少。
不论轧辊形状如何,为了保证管坯咬入和穿孔过程的实现都有穿孔锥(轧辊入口锥)、碾轧锥(轧辊出口锥)和轧辊轧制带(入口锥与出口锥之间的过度部分)组成。
穿孔机轧辊大多采用辊轴和辊套的组合结构,两者采用直接过盈组合或加键过盈组合。
这样,当轧辊报废后,辊轴可继续复用,以减小工具成本。
小型穿孔机辊轴材质多选用45或40Cr,调质处理。
大型的穿孔机辊轴多用42CrMo,调质处理。
轧辊材质目前各厂家选用较杂,有的厂家选用锻造45、55等优质碳素结构钢。
有的厂家选用50Mn、65Mn、70Mn、70Mn2Mo、60CrMnMo等合金铸钢或锻钢;硬度范围要求也不一致,有的要求HB180-220,有的要求HB220-260。
为了增加咬入性,大型穿孔轧辊一般在入口锥上加工有深度为0.8~1.2mm的网状花纹。