精益生产改善简介共73页
精益生产现场管理和改善课件

精益生产现场管理和改善课件一、引言精益生产是一种以减少浪费为核心的管理方法,旨在通过流程改进和效率提升,提高生产效率和质量,降低成本,以满足客户需求。
精益生产现场管理和改善是精益生产理论在实际生产现场中的应用和实施过程。
本课件将介绍精益生产现场管理和改善的基本概念和方法。
二、精益生产的基本原则精益生产的基本原则包括以下几个方面:1.价值观念: 以客户价值为导向,理解客户需求,追求超越客户期望的产品和服务。
2.价值流分析: 通过对生产过程的分析和改进,消除非价值增加的活动,实现流程的优化和效率的提升。
3.拉动生产: 基于客户需求,实施按需生产,避免过度生产和库存积压。
4.精益生产现场管理: 设立标准化工作,实施5S管理,建立可视化管理系统,确保生产现场的秩序和纪律。
5.持续改善: 不断寻求改进机会,推动精益思维的落地,实现持续的进步和竞争力的提升。
三、精益生产现场管理的基本概念1.标准化工作: 标准化工作是指在生产过程中,通过制定操作规程、工艺流程和工作标准,确保每个操作人员按照相同的方法和标准执行工作,达到产品质量的稳定性和一致性。
2.5S管理: 5S管理是指清理整理 (Sort)、整顿 (Set in order)、清洁(Shine)、标准化 (Standardize)和维护 (Sustain)的五个基本步骤。
通过5S管理,将生产现场保持整洁有序,提高工作效率和质量。
3.可视化管理系统: 通过使用标识、标牌、流程图等可视化工具,使生产现场的状态、流程和问题一目了然,便于管理人员和操作人员进行沟通和决策。
4.问题解决: 问题解决是精益生产现场管理的重要环节。
通过团队和个人的参与,寻找生产过程中的问题,分析问题的根本原因,制定解决方案,并持续追踪改进效果。
5.员工培训和参与: 精益生产现场管理需要员工全员参与和培训,使员工具备改善工作和解决问题的能力,从而推动持续改进的实施。
四、精益生产现场管理的实施步骤1.确定改善目标: 确定改善的关键指标和目标,例如提高生产效率、降低生产成本、提高质量等。
精益生产改善

项目实施与管理
副总经理
各部门指定精益专员组 成精益改善小组
品管部
精益专员
技术部
精益专员
生产部 精益专员
精益主任
胡晓东
曾志胜
刁云夫、杨国兴 饶剑、郑强
精益改善小组
张华
林尉谦
成立精益改善小组,建议每个部门经理主管拆分开组合,并确立改善项目 第一精益小组:刁云夫、林尉谦、郑强、胡晓东 第二精益小组:曾志胜、杨国兴、饶剑、张华 以上为建议分组,只供参考采纳。
快速换线(SMED)运行方式
快速换线(SMED)
SMED六大步骤
6、颁布新的 SOP 5、减少内部活动时间 4、将内外部活动流畅化 3、识别并执行同步作业 2、将内部活动转为外部活动 1、描述当前换线流程及活动
车床快速换线
将现有换线方式: 操作员手动编程,调机 改为调机与生产分离
三、初步推行计划
搬运的浪费
不良品的浪费
12
我们的浪费
浪费类别 类别细分 两手空闲 单手空闲 作业动作停止 动作太大 动作的浪费 左右手交换 步行多 转身角度大 移动中变化状态 额外的加工工序 加工精度超过了工 艺或客户的要求 没完没了的修饰 频繁的分类、测试 、检验 实际体现 在操作作业中,出现两只手均无事可做的时间段的浪费 在操作作业中,出现一只手无事可做的时间段的浪费 因操作顺序不合理等原因导致动作出现停顿的浪费 动作幅度超出“经济动作”范围,导致浪费 因零件/工具等放置位置不合适,导致拿取过程中必须进行左右手 交换的动作浪费 空手等无价值的步行的浪费 超出“经济动作”范围,导致浪费 因零件/工具等放置位置不合适,导致拿取/使用过程中必须进行 方向等交换动作浪费 产品加工中存在多余的加工工序 超出客户要求的工艺标准 无限度的返工 反复分类、测试、检验 严重程度 综合评分 (轻<1>中<2>重<3>) 2 3 2 2 2 3 2 2 2 2 2 1 7 18
2-2.193 精益知识——精益生产改善内容有哪些

75、精益知识——精益生产改善内容有哪些精益生产改善内容有哪些?暴露问题是精益生产改善的起点,为了提高员工的改善能力,往往需要企业开展精益生产改善活动,从而帮助杜绝浪费,持续改进,可以帮助企业提高管理水平。
精益生产咨询专家介绍企业精益生产改善的主要内容如下:一、精益生产计划管理改善以顾客需求为导向,根据客户订单、市场预测及库存状况,进行合理的、有计划的生产,做到在需要的时间,仅按所需要的数量生产。
生产与销售是同步的,也就是按销售的需求来进行生产,这样就可以保持物流的平衡,任何过早或过晚的生产都会造成浪费。
二、精益生产流程管理改善规范生产各环节流程,就要建立无间断流程以追求快速反应,将流程中不增值的无效时间尽可能压缩,以缩短整个流程的时间,逐步将规范的流程标准化。
标准化并不是一种限制和束缚,而是将企业中最优秀的做法固定下来,使不同的人来做都可以做得最好,发挥最大成效和效率。
而且,标准化也不是僵化、一成不变的,标准需要不断地创新和改进,今天最好的方法到了明天不一定是最好的,在现有标准的基础上不断改善,就可以推动组织持续地进步。
三、精益产品品质管理改善以“零缺陷”为工作目标,打破传统规律中“不良品是不能避免的、允许一定的不良品率存在”的观念。
精益生产通过持续不断地改进来预防问题发生,不断改善质量,消除质量浪费,从而实现质量成本的降低。
质量是制造出来的,而不是检验出来的,检验只是一种事后补救。
因此,应将品质建于设计、流程和制造当中去,建立一个不会出错的品质保证系统,一次做对。
四、精益人力资源管理改善以人为本是精益生产的特点之一,其具体做法如下:一要尊重员工的建议和意见,鼓励职工参与决策,为员工发挥才能创造机会;二要加强人与人之间、部门和部门之间的相互交流和合作,解决跨部门、跨层次的问题,减少扯皮现象,消除彼此的指责和抱怨,在相互理解的前提下共同完成公司目标;三要优化人力资源配置,解决结构性冗员和结构性缺员的矛盾,消除不创造价值的人员配置。
《精益改善周简介》课件

PAR改进
随着企业竞争加剧,精益改善周 将更加注重持续改进,不断优化
流程、提高效率和降低成本。
数字化转型
随着数字化技术的广泛应用,精益 改善周将更加注重数字化转型,利 用大数据、人工智能等技术提高生 产效率和产品质量。
绿色环保
随着社会对环保问题的关注度提高 ,精益改善周将更加注重绿色环保 ,通过减少浪费和排放,降低对环 境的影响。
详细描述
在精益改善周的结束阶段,需要对改善成果进行总结 和评估。这包括对实施过程中的数据进行分析,以及 对最终效果进行评估。通过总结成果,可以明确改善 措施对企业运营的贡献,并为后续的持续改进提供参 考和借鉴。同时,应将总结成果与团队成员共享,以 提高团队士气和凝聚力。在总结成果的基础上,应不 断反思和改进,以实现持续改进的目标。
PART 04
精益改善周的案例分析
案例一:某制造企业的精益改善实践
总结词
通过精益改善,提高生产效率,降低成本
详细描述
该制造企业面临生产效率低下、成本高昂的问题,通过引入精益改善周,对生 产线进行全面梳理和优化,减少了浪费,提高了生产效率,有效降低了成本。
案例二:某服务企业的精益改善实践
总结词
优化服务流程,提高客户满意度
提高生产效率。
优化换模流程
对换模流程进行全面分析,找 出瓶颈和浪费环节,进行改进
和优化。
快速调整
在换模过程中,快速调整设备 和工具,缩短调整时间,提高
生产效率。
标准化换模
将换模过程标准化,制定详细 的操作规程和注意事项,确保
快速、准确地完成换模。
目视化管理
直观展示信息
通过看板、图表等形式 ,直观地展示生产数据
详细描述
精益生产与改善

精益生产与改善在当今竞争激烈的市场环境中,企业需不断寻求提升效率、降低成本的方法。
其中,精益生产和改善技术成为许多企业追求的目标。
本文将探讨精益生产的概念和原则,并介绍一些改善技术的应用,以帮助企业在竞争中保持领先地位。
一、精益生产的概念及原则1. 精益生产的概念精益生产是一种以“削减浪费、提高价值”为核心的生产管理理念。
它的目标是通过降低生产中的各种浪费,从而实现高效、高质的生产过程。
精益生产有着广泛的适用范围,可以应用于制造业、服务业以及公共部门等各个领域。
2. 精益生产的原则(1)价值流:从顾客角度定义价值,并通过精确地定义价值流,消除非价值流以提高效率。
(2)价值流映射:通过绘制价值流映射图,揭示出各个环节中的浪费,以便有针对性地进行改进。
(3)流程平衡:通过平衡各个工作站的产能,避免过度生产和仓库积压。
(4)拉动生产:以顾客需求为导向,减少生产的批量和间隔时间。
(5)持续改进:通过不断反思和改进过程,实现持续的效率提升。
二、改善技术的应用1. 5S管理5S管理是一种改善技术,通过整理、整顿、清扫、清洁、纪律的五个步骤,提高工作场所的效率和安全性。
它的目标是改善工作环境,减少浪费和错误,提高员工的工作效率。
2. KAIZEN改善活动KAIZEN是一种源于日本的改善活动方法。
它鼓励员工积极参与日常的改进工作,通过标准化工作、海报活动等形式,激发员工的创造力和团队合作精神。
KAIZEN的核心思想是小步快走,循序渐进地不断改善,以实现效率和质量的提升。
3. 价值流分析价值流分析是一种通过绘制价值流映射图的方法,发现并改进价值流中的浪费。
通过对物料和信息流的分析,可以明确每个环节的价值和非价值活动,为改进提供目标和方向。
这个方法可以帮助企业发现并优化生产过程中的瓶颈和浪费,提高整体的效率和生产能力。
4. 标准化工作标准化工作是一种通过制定明确的工作流程和标准,保证每个环节的一致性和效率。
通过标准化工作,可以降低人为因素造成的错误和误操作,提高产品质量并减少浪费。
精益生产简介及推进方法介绍

4
第一部分 精益生产简介
二、精益生产的特点
➢消除一切浪费 ➢追求精益求精和不断改善 ➢去掉一切不增值的岗位及流程
2、准时化生产—JIT生产系统
在顾客需要的时候,按顾客需要的量,提供需要的产品。由一系列 工具来使企业实现准时化生产,主要工具有:
¨ 平衡生产周期--单件产品生产时间Takt Time==Cycle Time ¨ 持续改进KAIZEN(Continuous Improvement) ¨ 一个流生产—One Piece Flow ¨ 单元生产Cell Production--U型布置 ¨ 价值流分析VA/VE ¨ 方法研究IE ¨ 拉动生产与看板PULL & KANBAN ¨ 可视化管理 ¨ 减少生产周期—LEADTIME减少 ¨ 全面生产维护(TPM) ¨ 快速换模(SMED)
❖认识浪费的种类 ❖指标衡量体系如
何识别这些浪费 ❖衡量指标如何促
使基层单位消除浪费
6
第一部分 精益生产简介
1、消除一切浪费
多余动作 生产过剩 多余的流程
需要時才 搬运过去
搬运 纠错
七大浪费
等待 库存
7
第一部分 精益生产简介
1、消除一切浪费
多余动作
需要時才搬运
搬运
过去
与顾客需求和满意度无关的、不必要的或多余的作
四、实施主要内容及要求
4. 发挥劳动力的主观能动性强调“发挥团队的主观能动性是精益企 业的基本运行方式。”要鼓励团队精神,推倒企业各部门之间的墙壁 。
精益生产现场管理和改善

精益生产现场管理和改善精益生产现场管理和改善一、引言随着全球经济的不断发展和竞争压力的不断加强,企业在面临生产和管理方面的挑战越来越多。
传统的生产方式已经无法满足企业的需求,必须采用更加高效、灵活的生产方式。
精益生产是当前企业中较为流行的生产方式之一。
它强调精益、高效的生产方式,以减少浪费和提高生产效率为主要目标。
精益生产是通过对生产现场进行管理和改善,来实现生产效率的提高和管理水平的提升的。
本文主要介绍精益生产现场管理和改善相关的概念、原则和方法,旨在帮助企业更好地了解和应用精益生产,提升生产效率和效益。
二、精益生产现场管理和改善概述精益生产是源于日本的一种生产模式,它的核心理念是精细化、高效率、低成本生产。
其中,现场管理和改善是精益生产的核心内容。
现场管理是指在生产现场通过现场视察、数据观测、分析评估等手段,及时掌握生产现场的运作情况和问题,并进行管理和控制。
现场改善是指在现场管理的基础上,通过对生产流程、产品质量、人员安全等方面的改进,提高生产效率和产品质量水平。
精益生产现场管理和改善的基本原则是“流、拉、平、精、安、绿”。
其中,“流”强调实现生产流程的连续化;“拉”强调生产需求的精准控制;“平”强调无浪费、无停顿的生产;“精”强调高品质、精密化的制品;“安”强调人员安全和生产环境的安全;“绿”强调环保和可持续发展。
根据这些原则,企业可以在精益生产现场管理和改善中,通过各种手段和方法,实现生产的高效、优质和可持续。
三、精益生产现场管理和改善方法1. 5S管理5S管理是现场管理和改善的基本手段之一,它包括整理、整顿、清扫、清洁和素养。
通过5S管理,企业可以实现生产现场的整洁、有序、清洁,并保证生产现场的良好环境和人员素质。
具体措施可以包括:对生产现场进行整理和清理,定期对设备和机器进行定期维护和清洗,对废物和污水实行分类储存和处理等。
2. 价值流分析价值流分析是一种通过分析产品生产的实际流程,找出在生产过程中出现的浪费,进而减少生产成本的方法。
《精益改善周简介》课件
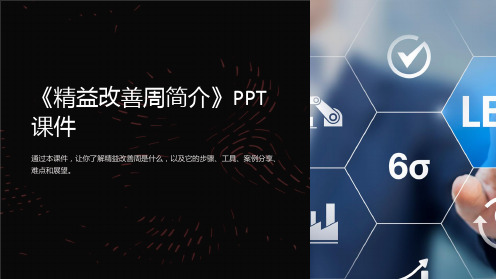
收集和分析数据
2
并设定可量化的目标。
通过数据分析来识别问题和潜在的
改善机会。
3
制定改善计划
基于数据分析结果,制定具体的改
实施改善计划
4
善计划和方法。
将改善计划转化为实际行动,并监
督改善过程。
5
监测和评估改善成果
通过持续监测和评估来确保改善成 果的可持续性。
精益改善周的工具和技术
价值流图
通过绘制流程图来识别和消除价值流中的 浪费。
《精益改善周简介》PPT 课件
通过本课件,让你了解精益改善周是什么,以及它的步骤、工具、案例分享、 难点和展望。
精益改善周是什么?
精益改善周是一种持续改善方法,旨在提高组织的效率和质量。它通过减少 浪费、提高流程和培养创新能力来实现变革。
精益改善周的步骤和流程
1
定义项目范围和目标
明确要改善的目标范围和关键指标,
创新解决方案
通过应用精益改善方法,解 决了一个多年存在的难题, 为公司节省了数百万资金。
团队协作
通过精益改善周,团队合作 解决了一个复杂的问题,增 强了团队凝聚力和创新意识。
精益改善周的难点和挑战
1 改变组织文化
改善周需组织文化的转变,这是一个长期而复杂的过程。
2 投资时间和资源
实施精益改善周需要投入大量的时间、人力和财力。
3 持续改进
精益改善周并不是一次性的,需要持续改进和不断优化。
精益改善周的总结和展望
总结
精益改善周是一种强大的 改善方式,可以提高组织 的效率、质量和创新能力。
展望
未来,精益改善周将在更 多组织中得到应用,并发 展出更多创新的工具和方 法。
建议和启示
精益生产(改善)简介

(Kaizen)
精益生产 (改善)简介
The Toyota Production System丰田生产体系
A solution to the particular problems Toyota faced, developed through trial and error on the shopfloor, to address:
• Lack of training 缺少培训
• Lack of adherence 纪律松懈
• Unbalanced Workload 工作负荷不平衡
• Quality problems 质量问题
• Unreliable equipment 设备不可靠
• No Standardized work 工作无规范
• Organize by Type of Process 按工艺类型安排部局
• Bottleneck operation 平颈口
• No Back-up/Cross Training 无备份或交叉培训
• Machines in value stream at different cycle times 机器循环时间不一
Staging 制消
Inspection
储存
检验
Assembly 组装
Shipping 发运
Raw Material 毛料
Time
时间
Finished Parts 成品
= Value Added Time 增值时间
= Non-Value Added Time (WASTE) 非增值时间 (浪费)
Value Added Time is only a very small percentage of the Leadtime.
精益生产现场管理和改善(打印稿)
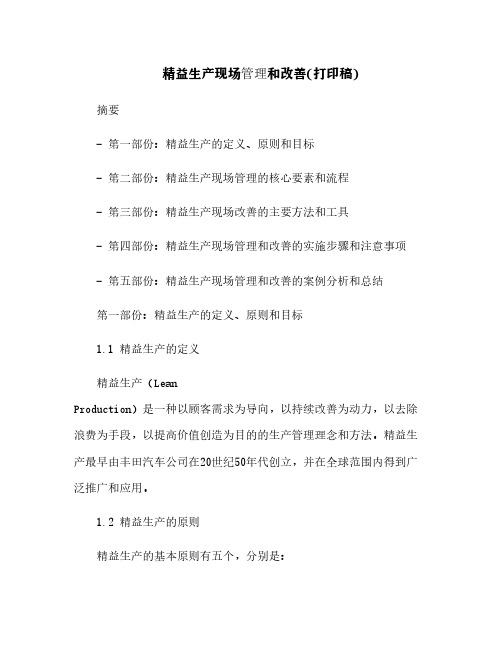
精益生产现场管理和改善(打印稿)摘要- 第一部份:精益生产的定义、原则和目标- 第二部份:精益生产现场管理的核心要素和流程- 第三部份:精益生产现场改善的主要方法和工具- 第四部份:精益生产现场管理和改善的实施步骤和注意事项- 第五部份:精益生产现场管理和改善的案例分析和总结第一部份:精益生产的定义、原则和目标1.1 精益生产的定义精益生产(LeanProduction)是一种以顾客需求为导向,以持续改善为动力,以去除浪费为手段,以提高价值创造为目的的生产管理理念和方法。
精益生产最早由丰田汽车公司在20世纪50年代创立,并在全球范围内得到广泛推广和应用。
1.2 精益生产的原则精益生产的基本原则有五个,分别是:以价值为中心:从顾客的角度识别并提供有价值的产品或者服务,满足或者超越顾客的期望。
-以流程为基础:将整个生产过程划分为一系列有序的步骤,确保每一步都能有效地完成,并消除不必要的等待、挪移、存储等活动。
-以拉动为驱动:根据顾客的实际需求来安排生产计划和调度,避免过度生产或者库存积压,实现及时交付。
-以完美为追求:不断地检查、评估和改进生产过程中的各个环节,消除缺陷、错误、变异等问题,提高质量水平和一次性通过率。
1.3 精益生产的目标精益生产的主要目标有四个,分别是:-提高效率:通过优化生产流程、减少浪费、增加速度、节省时间等方式,提高单位时间内完成的产品或者服务数量。
提高质量:通过预防缺陷、控制变异、保证标准、实施改善等方式,提高产品或者服务符合规格或者顾客需求的概率。
-提高客户满意度:通过满足或者超越顾客对产品或者服务的功能、性能、可靠性、安全性、外观等方面的期望,提高顾客对产品或者服务的认可和信赖。
-降低成本:通过减少物料、人力、设备、能源等资源的消耗,降低单位产品或者服务的生产成本。
第二部份:精益生产现场管理的核心要素和流程2.1 精益生产现场管理的核心要素精益生产现场管理(Lean Production SiteManagement)是指在生产现场实施精益生产原则和方法,以实现高效、高质、低成本的生产目标的管理活动。
精益生产改善简介

精益生产改善简介精益生产改善是一种针对生产过程进行优化的方法,旨在消除浪费、提高效率和质量。
它源自于日本的丰田生产方式(Toyota Production System),采用了许多概念和工具,可以适用于各种规模和类型的生产环境。
精益生产改善的核心理念是消除各种形式的浪费:包括过度生产、库存过量、等待时间、物料运送、过度处理、不合格品等。
通过深入分析生产过程,精益生产改善可以帮助企业找到并消除这些浪费,从而提高生产效率和质量。
在实施精益生产改善的过程中,企业需要采用一系列工具和方法来评估当前的生产状况,并确定改善的重点。
其中包括价值流图(Value Stream Mapping),它可以帮助企业绘制生产流程的全貌,并找到改进的机会点;5S整理法,用于整理和优化生产环境;流程改进工具,如Kaizen活动和快速换模(SMED)等,用于找到并消除瓶颈和瓶颈;以及质量管理工具,如可靠性工程(RE)和统计过程控制(SPC),用于保证产品质量。
通过实施精益生产改善,企业可以获得许多益处。
首先,生产效率得以提高,周期时间和交付周期被大大缩短。
其次,质量得到提升,不合格品的数量和成本大大降低。
此外,通过消除浪费和优化流程,企业可以节约成本并提高利润。
最重要的是,精益生产改善可以帮助企业建立一个持续改进的文化,使员工积极参与到改进活动中,并不断推动企业向更高水平发展。
精益生产改善是一个持续改进的过程,而不是一次性的项目。
企业应该不断关注并改进生产过程,以确保持续的效率和质量的提高。
同时,培养员工的意识和技能,使他们成为改进的推动者,是成功实施精益生产改善的关键因素之一。
总之,精益生产改善是一种基于消除浪费、优化流程和提高质量的方法,可以帮助企业提高效率、降低成本并建立持续改进的文化。
通过实施精益生产改善,企业能够在竞争激烈的市场中取得优势,并实现可持续发展。
精益生产改善(Lean Production Improvement)是一种重要的管理方法,它通过消除浪费、提高效率和质量来优化生产过程。
精益生产工作方法改善讲义共54页文档

36、“不可能”这个字(法语是一个字 ),只 在愚人 的字典 中找得 到。--拿 破仑。 37、不要生气要争气,不要看破要突 破,不 要嫉妒 要欣赏 ,不要 托延要 积极, 不要心 动要行 动。 38、勤奋,机会,乐观是成功的三要 素。(注 意:传 统观念 认为勤 奋和机 会是成 功的要 素,但 是经过 统计学 和成功 人士的 分析得 出,乐 观是成 功的第 三要素 。
▪
27、只有把抱怨环境的心情,化为上进的力量,才是成功的保证。——罗曼·罗兰
▪
28、知之者不如好之者,好之者不如乐之者。——孔子
▪
29、勇猛、大胆和坚定的决心能够抵得上武器的精良。——达·芬奇
▪
30、意志是一!
54
39、没有不老的誓言,没有不变的承 诺,踏 上旅途 ,义无 反顾。 40、对时间的价值没有没有深切认识 的人, 决不会 坚韧勤 勉。
▪
26、要使整个人生都过得舒适、愉快,这是不可能的,因为人类必须具备一种能应付逆境的态度。——卢梭