精益生产推行改善方案
精益管理改善方案(优秀3篇)
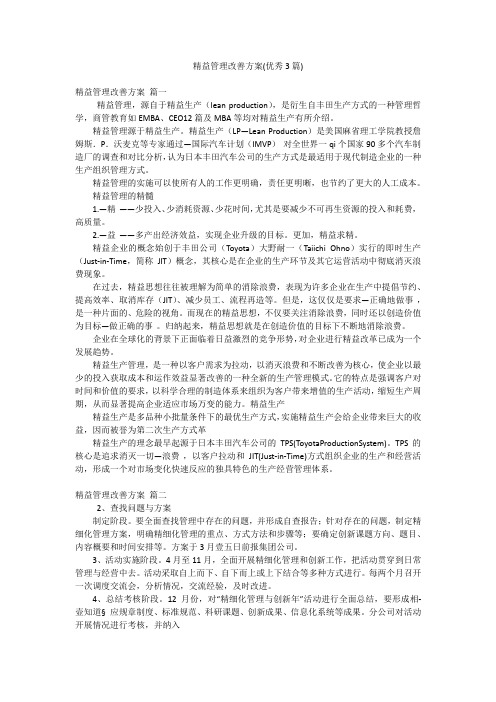
精益管理改善方案(优秀3篇)精益管理改善方案篇一精益管理,源自于精益生产(lean production),是衍生自丰田生产方式的一种管理哲学,商管教育如EMBA、CEO12篇及MBA等均对精益生产有所介绍。
精益管理源于精益生产。
精益生产(LP—Lean Production)是美国麻省理工学院教授詹姆斯.P.沃麦克等专家通过―国际汽车计划(IMVP)‖对全世界一qi个国家90多个汽车制造厂的调查和对比分析,认为日本丰田汽车公司的生产方式是最适用于现代制造企业的一种生产组织管理方式。
精益管理的实施可以使所有人的工作更明确,责任更明晰,也节约了更大的人工成本。
精益管理的精髓1.―精‖——少投入、少消耗资源、少花时间,尤其是要减少不可再生资源的投入和耗费,高质量。
2.―益‖——多产出经济效益,实现企业升级的目标。
更加,精益求精。
精益企业的概念始创于丰田公司(Toyota)大野耐一(Taiichi Ohno)实行的即时生产(Just-in-Time,简称JIT)概念,其核心是在企业的生产环节及其它运营活动中彻底消灭浪费现象。
在过去,精益思想往往被理解为简单的消除浪费,表现为许多企业在生产中提倡节约、提高效率、取消库存(JIT)、减少员工、流程再造等。
但是,这仅仅是要求―正确地做事‖,是一种片面的、危险的视角。
而现在的精益思想,不仅要关注消除浪费,同时还以创造价值为目标―做正确的事‖。
归纳起来,精益思想就是在创造价值的目标下不断地消除浪费。
企业在全球化的背景下正面临着日益激烈的竞争形势,对企业进行精益改革已成为一个发展趋势。
精益生产管理,是一种以客户需求为拉动,以消灭浪费和不断改善为核心,使企业以最少的投入获取成本和运作效益显著改善的一种全新的生产管理模式。
它的特点是强调客户对时间和价值的要求,以科学合理的制造体系来组织为客户带来增值的生产活动,缩短生产周期,从而显著提高企业适应市场万变的能力。
精益生产精益生产是多品种小批量条件下的最优生产方式,实施精益生产会给企业带来巨大的收益,因而被誉为第二次生产方式革精益生产的理念最早起源于日本丰田汽车公司的TPS(ToyotaProductionSystem)。
精益生产改善方法有哪些?详解:精益生产之持续改善
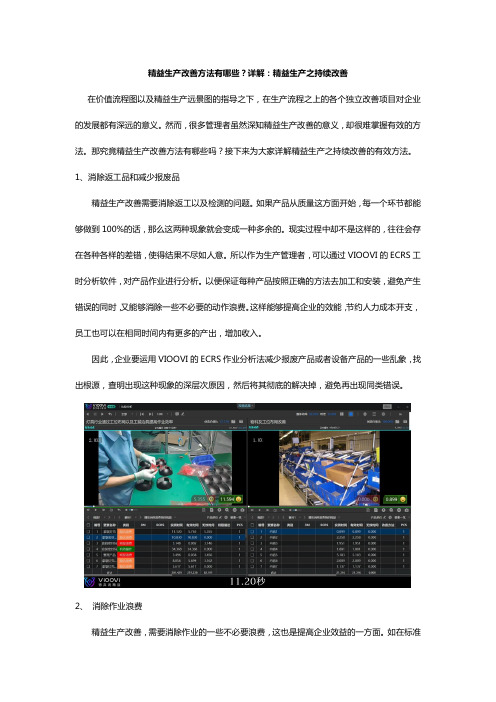
精益生产改善方法有哪些?详解:精益生产之持续改善在价值流程图以及精益生产远景图的指导之下,在生产流程之上的各个独立改善项目对企业的发展都有深远的意义。
然而,很多管理者虽然深知精益生产改善的意义,却很难掌握有效的方法。
那究竟精益生产改善方法有哪些吗?接下来为大家详解精益生产之持续改善的有效方法。
1、消除返工品和减少报废品精益生产改善需要消除返工以及检测的问题。
如果产品从质量这方面开始,每一个环节都能够做到100%的话,那么这两种现象就会变成一种多余的。
现实过程中却不是这样的,往往会存在各种各样的差错,使得结果不尽如人意。
所以作为生产管理者,可以通过VIOOVI的ECRS工时分析软件,对产品作业进行分析。
以便保证每种产品按照正确的方法去加工和安装,避免产生错误的同时,又能够消除一些不必要的动作浪费。
这样能够提高企业的效能,节约人力成本开支,员工也可以在相同时间内有更多的产出,增加收入。
因此,企业要运用VIOOVI的ECRS作业分析法减少报废产品或者设备产品的一些乱象,找出根源,查明出现这种现象的深层次原因,然后将其彻底的解决掉,避免再出现同类错误。
2、消除作业浪费精益生产改善,需要消除作业的一些不必要浪费,这也是提高企业效益的一方面。
如在标准化的车间里面,零件是要来回搬来搬去的,这样的生产线路更长,生产周期也比较长,成本也会增加,这是企业不愿意看到的。
如在一些超市的分拣区域,也会发生这样的现象。
(如图VIOOVI ECRS的分拣作业分析)在这样的情况之下布局就是相当不合理的,还有很大的提升空间,完全可以想办法去改善,所以建议各位可以把加工顺序安排完毕,这样能够让生产过程更加顺利的完成,尽可能的不要去移动,这样路线就会缩短,也不会对物品产生一定的影响,就可以节省一定的成本,这样才叫做精益生产改善的彻底方法深度改善一下,这对于提升企业的基础效能来说是至关重要的。
3、合理安排生产计划在精益生产企业当中,精益生产改善是必须具备的,这代表着企业能够非常精准的量入而出。
精益生产效率改善方案
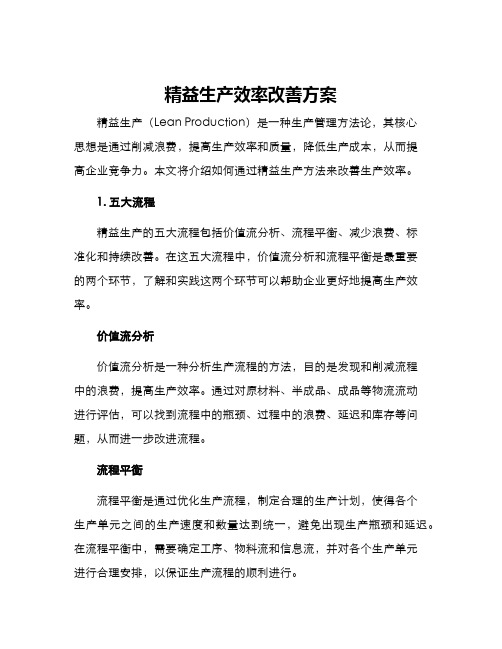
精益生产效率改善方案精益生产(Lean Production)是一种生产管理方法论,其核心思想是通过削减浪费,提高生产效率和质量,降低生产成本,从而提高企业竞争力。
本文将介绍如何通过精益生产方法来改善生产效率。
1. 五大流程精益生产的五大流程包括价值流分析、流程平衡、减少浪费、标准化和持续改善。
在这五大流程中,价值流分析和流程平衡是最重要的两个环节,了解和实践这两个环节可以帮助企业更好地提高生产效率。
价值流分析价值流分析是一种分析生产流程的方法,目的是发现和削减流程中的浪费,提高生产效率。
通过对原材料、半成品、成品等物流流动进行评估,可以找到流程中的瓶颈、过程中的浪费、延迟和库存等问题,从而进一步改进流程。
流程平衡流程平衡是通过优化生产流程,制定合理的生产计划,使得各个生产单元之间的生产速度和数量达到统一,避免出现生产瓶颈和延迟。
在流程平衡中,需要确定工序、物料流和信息流,并对各个生产单元进行合理安排,以保证生产流程的顺利进行。
减少浪费减少浪费是体现精益生产的核心思想,目的是尽可能地减少不必要的生产环节和资源消耗,提高生产效率。
在精益生产中,浪费分为七大类:过产、等待、运输、处理、库存、运动和设计,通过分析每一种浪费的情况,制定相应的改进措施,可以有效地降低生产成本。
标准化标准化是指通过规范化和标准化生产流程,确保生产过程中的质量稳定性和效率。
标准化包括对生产设备、生产工艺和生产流程的统一规范和管理,通过制定标准化的生产流程和工艺,可以避免或减少人为错误和浪费的出现。
持续改善精益生产强调持续改善,通过不断地进行价值流分析、流程平衡、减少浪费和标准化,逐步提高生产效率和质量。
持续改善需要设立具体的改善目标,制定可行的改善方案,并建立相应的改善措施和评估指标,从而持续推进企业的生产效率和竞争力。
2. 精益生产的实践案例下面介绍一个精益生产的实践案例,以帮助读者更好地理解如何将精益生产方法应用于生产中。
精益生产改善提案管理办法

精益生产改善提案管理办法XXX精益生产改善提案实施办法批准:审核:编制:生效日期:年月日1.目的挖掘员工潜能,激发员工的活力和创造力,以主人翁的态度,推进企业技术进步,推动全员参与改善工作,实现经济效益最大化,为促进企业的快速发展做贡献。
2.适用范围本办法适用于XXX群众性改善提案的管理与组织工作。
参与对象为XXX所有员工,重点对象是各生产班组一线员工。
3.引用文件《员工提案管理制度》、《精益生产理念》4.术语4.1班组本办法中,除特殊注明的,所称班组指生产一线班组。
4.2改善提案4.2.1改善提案的定义针对现状,提出的更好的方法、措施或设想。
主要包括针对质量、成本、交货期、安全、环境方面的问题及对策,基本要素包括:针对的问题、准备采取的措施、以及预计达到的效果。
4.2.2按提案提出对象来分:小我提案:指员工小我提出来的一些比较简朴易行的改善提案或建议。
团队提案:指员工或团体提出针对公司业务流程(包括物料、品质、成本,机器等)等方面的一些大的改善项目。
4.2.3本办法所称改善提案,均须符合公司有效建议的请求。
4.2.4.精益生产改善提案的一般范围。
4.2.4.1现场类主要包括:工具、设备、仪器、装配的创新、改进;生产工艺、操作方法、制造技术的进步;安全隐患排除;安全生产、劳动保护、环境保护的方法和手段的创新、改进;物资储藏、运输技术的创新、改进;节约能源;更有效地利用原料、材料、设备及自然条件的技术措施;4.2.4.2经营管理和服务类主要包括:在现场管理、管理技术上有创新,对进步谋划管理、进步谋划效益或本钱效益有指导作用;在工作构造、制度划定等方面提出的办法或改进方案,对进步工作效率、员工满意度或服务质量有显著结果4.2.4.3提案如果属于下列各项范围,视为不适当提案不予受理:攻击团体或个人的投诉、抱怨等;小我看法、诉苦或请求改善待遇、福利等;与曾经提出大概曾经采用过的提案内容相同大概相近者;属于本身工作职责范围内的提案。
精益生产推行之物流改善方法

汇报人:
• 成果与效益:通过精益管理的实施,该企业成功地提高了物流效率,降低了成本,并提升了客户满意度。 具体来说,他们实现了以下成果:订单处理时间缩短了30%,运输成本降低了20%,客户投诉率减少了 15%。
• 经验教训与启示:该企业的精益管理实践表明,精益管理是一种有效的提升物流效率的方法。但实施过 程中需要注意以下几点:首先,要有明确的目标和计划;其次,要持续改进和优化流程;最后,要培养 员工的精益意识,使其成为企业文化的一部分。 以上内容仅供参考,您可以根据自身需求进行调整优 化。
持续改进:不断寻求改进机会,通过数据分析和经验总结,不断优化生产流程,提高生 产效率和质量。
跨部门协作:加强跨部门之间的协作和沟通,确保各个部门都能够为精益生产物流的实 施提供支持和帮助。
案例背景:某制造企业面临物流效率低下、成本高昂的问题,决定实施精益生产物 流改善方法。
改善措施:通过减少库存、优化运输方式、提高物流信息化水平等手段,实现物流加标题
添加标题
提高物流效率
添加标题
添加标题
提升客户满意度
定义和类型:识别 并消除生产过程中 的浪费
价值流分析:确定 价值创造和非价值 创造活动
消除七大浪费:运 输、等待、库存、 过度加工、缺陷、 动作和过度使用资 源
持续改进:通过不 断改进消除浪费, 提高生产效率和质 量
实施过程:详细描述精益生产物流改善方法的实施过程,包括计划制定、团队组建、 培训宣传、实施执行等环节。
成果展示:展示该制造企业实施精益生产物流改善方法后的成果,包括物流效率的 提升、成本的降低、客户满意度的提高等。
总结与启示:总结该案例的成功经验,并探讨精益生产物流改善方法在其他制造企 业中的应用前景和推广价值。
(优质)精益改善项目计划

精益改善项目计划
1、标杆考察,发现差距:推行精益生产,意味着在企业里展开一场工作方式、思维习惯的变革,需要高层领导的决心、中层管理者理念意识的统一和基层员工不折不扣的执行。
2、意识引导,培训先行:精益生产方式把生产中一切不能增加价值的活动都视为浪费,强调人的作用,充分发挥人的潜力,以持续改善来消除浪费。
3、成立项目领导和推行小组:在实施精益生产的时候,建立一个精益生产组织,"精益生产委员会","改善组织",以便后续工作。
4、示范线改善,体现成果,建立改善样板区域:任何改善都是建立在对美好的期望基础上的,要让员工真正的接受变革,必须让员工看到实际的成果,并且很多精益的工具也需要在实际的实施过程才能诠释优点。
5、现场改善:改善现场环境的5个步骤,具体为:整理、整顿、清扫、清洁、素养,让现场走向有序化,减少一些比较显现的浪费现象;另一方面,通过领导的参与,让员工明白管理层对改善的决心,提高全员的改善意识。
6、选择要改进的关键流程,画出价值流程图:精益生产方式不是一蹴而就的,强调持续的改进,首先应该先选择关键的流程,力争把它建立成一条样板线。
7、开展改进研讨会:精益远景图必须付诸实施,否则规划得再巧妙的图表也只是废纸一张,实施计划中包括什么,什么时候和谁来负责,并且在实施过程中设立评审节点,全体员工都参与到全员生产性维护系统中。
8、推广到整个公司:精益生产利用各种工业工程技术来消除浪费,着眼于整个生产流程,而不只是个别或几个工序,样板线的成功要推广到整个公司,使操作工序缩短,推动式生产系统被以顾客为导向的拉动式生产系统所替代。
精益生产持续改善建议

精益生产持续改善建议
1. 设置持续改善目标:明确确定持续改善的目标和愿景,使整个组织都能朝着这个目标努力。
2. 建立改善团队:组建专门的团队来负责推动持续改善工作,团队成员应包括各部门的代表以及一些具有改进经验和知识的人员。
3. 进行价值流分析:对生产过程进行详细的价值流分析,找出其中的浪费和瓶颈,为改善工作提供基础和方向。
4. 使用工具和方法:运用精益生产的工具和方法,如5S、Kaizen、Kanban等,来提高生产效率和质量。
5. 建立反馈机制:建立一个有效的反馈机制,收集员工和客户的意见和建议,及时发现问题并解决。
6. 进行员工培训:培训员工关于持续改善的知识和技能,提高员工在改进工作中的参与度和贡献度。
7. 固化改善成果:将持续改善的成果固化下来,通过标准化和文档化等方式,确保改善工作的持续性。
8. 建立奖励和激励机制:为积极参与持续改善工作的员工提供奖励和激励,增强员工的主动性和积极性。
9. 持续监测和评估:对持续改善工作进行监测和评估,及时调
整和改进改善的策略和方法。
10. 建立合作伙伴关系:与供应商和客户建立紧密的合作伙伴关系,共同推动持续改善工作的进行。
精益生产效率改善方案

精益生产效率改善方案什么是精益生产?精益生产是一种以最小化浪费和提高效率为目标的生产管理方法。
它的核心思想是通过对生产过程的优化,达到产品质量提高、生产周期缩短和成本降低的目的。
为什么需要精益生产?在如今激烈的市场竞争中,生产效率的提升已经成为企业持续发展的关键。
精益生产可以通过最小限度地消除浪费,使得生产过程更加高效、灵活和可持续,提高生产效率,降低成本,提高质量,进而使企业在市场竞争中处于优势位置。
精益生产效率改善方案在实施精益生产过程中,需要采用一系列的工具和技术,以下是一些常用的精益生产效率改善方案。
价值流分析价值流分析是一种用于分析生产过程中价值创造的流程的工具。
它可以帮助生产企业找到并消除不必要的步骤、动作和停顿,从而减少浪费,优化生产流程。
PDCA循环PDCA是“计划-执行-检查-行动”四个词的缩写,是一种改进方法的循环过程,通过不断循环实施计划和持续改善,实现生产过程的优化。
PDCA循环的每个阶段都有其具体的任务,如计划阶段需要确定目标、分析问题和确定解决方案;执行阶段需要实施改进方案并收集数据;检查阶段需要对数据进行分析和验证;行动阶段需要采取措施来解决问题,并进行改进。
5S工作法5S工作法是一种用于整理、整顿、清扫、清洁和整容的工作法。
它可以帮助企业清理不必要的物品、标准化生产线、整理工具、提高工作效率和改善工作环境。
运用合理化建议制度合理化建议制度可以激励员工提出改进意见,并将这些意见纳入到生产过程中。
可以采用奖励制度来鼓励员工的积极性并提高员工的工作满意度,进而提高生产效率。
生产线平衡生产线平衡是以最小化动作为目标的生产流程改善方法。
它可以通过消除不必要的操作来提高生产效率和质量,并减少生产周期。
总结只有实现高效的生产过程,才能实现生产效率的提升,从而在市场竞争中保持竞争力。
采用以上的精益生产效率改善方案,可以将业务的复杂度降低到最低限度,提高生产效率,降低成本,并提高产品质量。
精益生产改善总结报告
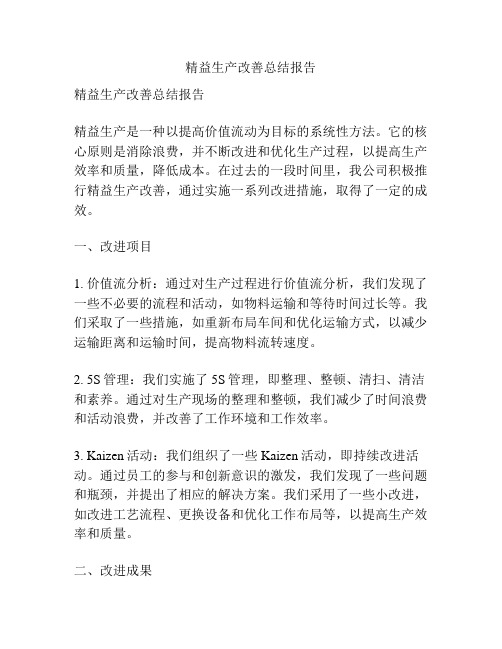
精益生产改善总结报告精益生产改善总结报告精益生产是一种以提高价值流动为目标的系统性方法。
它的核心原则是消除浪费,并不断改进和优化生产过程,以提高生产效率和质量,降低成本。
在过去的一段时间里,我公司积极推行精益生产改善,通过实施一系列改进措施,取得了一定的成效。
一、改进项目1. 价值流分析:通过对生产过程进行价值流分析,我们发现了一些不必要的流程和活动,如物料运输和等待时间过长等。
我们采取了一些措施,如重新布局车间和优化运输方式,以减少运输距离和运输时间,提高物料流转速度。
2. 5S管理:我们实施了5S管理,即整理、整顿、清扫、清洁和素养。
通过对生产现场的整理和整顿,我们减少了时间浪费和活动浪费,并改善了工作环境和工作效率。
3. Kaizen活动:我们组织了一些Kaizen活动,即持续改进活动。
通过员工的参与和创新意识的激发,我们发现了一些问题和瓶颈,并提出了相应的解决方案。
我们采用了一些小改进,如改进工艺流程、更换设备和优化工作布局等,以提高生产效率和质量。
二、改进成果经过一段时间的改进工作,我们取得了以下一些成果:1. 生产效率提高:通过消除浪费和优化流程,我们的生产效率提高了20%。
生产时间缩短,生产速度提升,产量增加。
这使我们能够更好地满足客户需求,并提高竞争力。
2. 质量改善:通过改进工艺和优化设备,我们的产品质量得到了提高。
产品合格率提高了10%,不良品率降低了20%。
这不仅降低了生产成本,还增强了顾客对我们产品的信任和满意度。
3. 成本降低:通过消除浪费和减少不必要的活动,我们的生产成本得到了一定的降低。
这使我们能够更好地控制成本,并提高利润空间。
4. 员工参与度提高:通过推行精益生产改善活动,我们激发了员工的参与意愿和创新意识。
员工参与度提高了,他们对工作更加积极主动,提出了很多有价值的改进意见和建议。
三、改进方向虽然我们在精益生产改善方面取得了一些成果,但仍然存在一些问题和挑战。
精益生产现场管理和改善方案

精益生产现场管理和改善方案精益生产现场管理和改善方案1如何用精益生产方式来改善现场?与批量生产相比,企业精益生产注重时间效率,注重识别整体价值流,创建增值流程,在短时间内创建增值行为,并寻找价值创造的源泉。
减少企业浪费,在稳定的需求环境下,以小的成本和时间提供高品质的产品。
精益生产是以及时生产为核心,寻找适合于企业的产品开发、生产和销售的精益方法。
那么如何用精益生产方式来改善现场呢?1:提高企业全体员工的意识。
上至企业领导,下至车间员工,都应加强精益生产管理意识的教育和培训。
训练内容包括:竞争状况,浪费观念,激励生产,5S,团队改善,全套设备管理,精益生产品质管理等,以促进企业全体员工观念的转变,增强落实精益生产方法的意识和主动性。
设立领导和执行机构,负责实施精益生产方法,并让相关业务人员参与,各岗位人员责任分工明确,拟定精益生产的工作计划。
2:建立项目领导者和项目执行团队。
这一步就是建立精益生产组织,在许多企业中,这也是一个必要的步骤。
精益生产其组织形式包括:生产管理、制造、生产技术、质量部等相关部门。
监督人员应该建立改善负责人的职责。
3:精益生产建立一个示范生产线。
选一条生产线作为示范,以便后续持续更进改善。
尽可能使用精益工具,并且明确改进之前的状况。
改善工作要遵守循序渐进的原则,派专人坚持记录并完善。
4:改善生产环境。
要实施精益生产,首先要清理生产场所不必要的物品,减少空间的占用。
保持工作场所清洁、物品分门别类归纳、及时维护设备。
让员工将养成良好的现场作业环境习惯,从而提高公司的生产效率和产品质量。
5:改善研讨企业的不足。
必须把精益生产化为行动,否则一切皆为空谈。
每一个流程中的每一个自立的改进项目,都需定期研讨改善。
6:消除生产浪费。
精益生产平衡各生产工艺的生产能力,减少生产过剩,消除生产过剩的浪费。
减少批量生产,缩短生产等候时间,消除等待浪费。
记住精益生产现场管理和改善的根本是人的管理人的质量问题。
工厂精益整改措施方案

工厂精益整改措施方案1. 引言在当今竞争激烈的市场环境中,工厂的生产效率和质量保证是提高竞争力的关键因素之一。
精益生产(Lean Production)作为一种优化生产流程,减少浪费的方法,被广泛应用于各个行业。
本文将提出一套工厂精益整改的具体措施方案,以优化工厂的生产流程,提高生产效率和质量。
2. 现状分析在进行整改之前,首先需要对现状进行分析。
主要分析以下几个方面:2.1 生产流程详细了解工厂的生产流程,包括原材料采购、生产加工、成品制造、质量检验和包装装运等环节。
通过流程分析,找出存在的问题和不合理之处。
2.2 工作流程分析工作流程,了解各个岗位的工作职责和工作内容。
同时,与员工进行深入交流,了解员工对工作流程的评价和意见,找出改进的空间。
2.3 设备和设施调研现有的设备和设施状况,包括设备的技术性能、使用年限和维护保养情况。
根据调研结果,判断设备是否需要更换或升级,以提高生产效率和质量。
3. 精益整改措施了解现状后,接下来提出一套具体的精益整改措施方案。
3.1 价值流分析(Value Stream Mapping)通过价值流分析方法,绘制出工厂的价值流图。
通过对价值流图的分析,识别出浪费的环节和非增值的活动。
然后,优化这些环节,减少不必要的运动、等待和库存。
3.2 快速换模(Quick Changeover)对于需要频繁进行换模的设备和工序,采取快速换模的措施。
通过简化换模步骤、标准化工具和改善操作方法,缩短换模时间,提高生产效率。
3.3 周期时间降低(Lead Time Reduction)精益生产的目标之一是缩短产品从订单到交付的周期时间。
通过优化生产计划和流程,减少不必要的等待和调度时间,降低周期时间,提高客户满意度。
3.4 5S整理法采用5S整理法,即整理、整顿、清扫、清洁和素养的步骤,来改善工作环境和工作效率。
通过整理物品、标准化工作区域、定期清洁和培养良好的工作习惯,提高工作效率和质量水平。
精益生产改善方案

精益生产改善方案
以下是 7 条关于精益生产改善方案:
1. 人员效率最大化,这可不是开玩笑!你想想,就像一场比赛,每个队员都要全力以赴,咱这生产线上的每个工人不也得充分发挥嘛!比如说,咱可以搞个技能大比拼,看谁做得又快又好,激发大家的斗志,这样不就能让效率蹭蹭往上涨啦!
2. 库存管理也很重要哇!那堆积如山的库存不就像一块大石头压在心里嘛!咱得精确计算需要多少货,不多不少刚刚好。
就好比做饭,盐放多了咸,放少了没味,得恰到好处!咱精确管理库存,资金不就流动起来更顺畅啦!
3. 生产流程优化,这就像给机器上润滑油啊!顺畅得很!比如说原来那些繁琐的步骤,咱简化一下,不就快起来啦!就像走迷宫,找到最优路径,那速度,绝对杠杠的!
4. 品质管理可不能马虎,这可是咱的招牌啊!就像爱护宝贝一样对待产品品质,有一点点瑕疵都不行!一旦出了问题,那多丢面子啊!所以每一道工序都严格把关,让客户拿到手的都是精品,那口碑不就来了嘛!
5. 设备维护得跟上呀!设备要是出毛病了,那不就抓瞎啦!就像战士的武器,得时刻保养好。
定期检查、保养,该修的修,该换的换,让设备一直处于最佳状态,生产才能稳稳当当呀!
6. 团队沟通和协作,这就是成功的关键呐!大家心往一处想,劲往一处使,那力量多大呀!就好比划船,大家动作一致,船才能飞速前进。
有了问题一起商量,办法总比困难多,是不是呀!
7. 持续改进不能停!这世界变化快呀,咱得跟上脚步。
今天觉得好的,明天可能就不够啦!所以得不断找问题,想办法,让咱的精益生产一直升级。
这就像爬山,一步一步往上爬,风景越来越好!
我觉得精益生产改善方案就是要全面考虑,每个方面都做好,才能让企业发展得越来越好!。
精益改善方案

精益改善方案第1篇精益改善方案一、背景随着市场竞争的加剧,企业追求效率与成本的双重优化成为提升核心竞争力的重要途径。
精益思想作为一种全面的管理策略,旨在消除浪费,优化流程,提升企业整体运营效率。
结合我国企业实际情况,特制定本改善方案,以期实现企业可持续发展。
二、目标1. 提高生产效率,降低生产成本;2. 优化业务流程,缩短交付周期;3. 提升产品质量,减少不良品率;4. 增强员工素质,提高企业整体竞争力。
三、实施方案1. 精益生产(1)推行5S管理:整理、整顿、清扫、清洁、素养,营造整洁、有序、安全的工作环境。
(2)标准化作业:制定作业标准,规范操作流程,提高生产效率。
(3)看板管理:实施可视化生产,实时掌握生产进度,提高生产调度效率。
(4)拉动式生产:以客户需求为导向,减少库存,降低生产成本。
2. 流程优化(1)价值流程分析:分析现有流程,识别价值流,消除非价值增值环节。
(2)流程再造:对核心业务流程进行优化,简化流程环节,提高工作效率。
(3)信息化建设:整合企业资源,提高信息共享,降低沟通成本。
(4)协同办公:推行跨部门协同,提高工作协同效率。
3. 质量管理(1)全面质量管理:全员参与质量管理,提高产品质量。
(2)质量改进:运用PDCA循环,持续改进产品质量。
(3)供应商管理:严格筛选供应商,提升供应链质量。
(4)客户满意度调查:关注客户需求,提高客户满意度。
4. 员工培训与激励(1)培训体系建设:完善培训体系,提高员工技能水平。
(2)内部讲师制度:选拔内部讲师,共享知识经验。
(3)激励机制:设立绩效奖金,激发员工积极性。
(4)员工关怀:关注员工身心健康,提升员工幸福感。
四、实施步骤1. 项目启动:成立项目组,明确项目目标、范围、时间表等;2. 现状分析:收集数据,分析现有问题,确定改进方向;3. 方案设计:根据现状分析,制定具体的改进措施;4. 方案实施:分阶段、分步骤推进方案实施;5. 效果评估:定期评估改进效果,调整改进措施;6. 成果巩固:总结经验,固化成果,形成长效机制。
改善专 案实施方案(精益生产必看).ppt

现 状 调 研
问 题 分 析
目 标 值 设 定
对 策 制 定
对 策 实 施
效 果 确 认
标 准 化
形 成 报 告 书
(
与台塑专案改善理念相同
降本增效、专案改善与方针管理三者关系
降本增效 – 选择降本 增效点 专案改善 – 立项 方针管理 方针确定
P
– 设定月和 年度目标 – 制定改善 方案
– 设定目标值
C A
STEP1 发掘问题(脑力激荡法 、查检表 ......) STEP2 选定题目(柏拉图、特性要因图 ......)
STEP3 追查原因(层别法、5W1H、流程图......) STEP4 分析资料(抽样法、散布图、直方图 ......) STEP5 提出方案(脑力激荡法、方法研究......)
专案改善目的
从根源上解决问题—通过专案改善的形式对存在的问题进行系统分析并加以改善
专案改善作用
1
培养系统思考能力
系统思考:就是人们运用系统理论和系统方法对问题进行系统分 析,透过表面现象看到藏在问题背后的深层次原因所在, 使这些 问题明朗化的思维方式
不是就问题而解决问题,“头痛医头,脚痛医脚”的做法,培养主管及专业序列人员系统思 考能力。
方针管理
做专案、做标准
岗 位 序 列
专业序列
研究如何做
专案改善
执行标准
基层序列
基层序列
按照标准做
自主管理
提案制度
2、专案改善与日常工作的关系
1
专案改善是专业人员的本职工作; 专案改善是专业人员必须掌握的一种工作方法和技能。
2
各项管理活动间的关系
管理活动间的关系
问题提出 方 针 管 理 对 标 管 理
精益生产线的四种改善思路

精益生产线的四种改善思路精益生产线的四种改善思路:1、平衡生产线生产线平衡是对生产线上的全部工位进行平均化、调整作业负荷,以使各作业时间尽可能使用相近的技术手段与方法。
对整个作业内容进行重新组合,按照目标节拍进行调整,每一次作业内容的调整需与技术、生产等相关部门进行沟通协调,以增强改善活动的可操作性。
2、优化工序制件的运动不间断、不堆积、不超越、不落地;创造无中断、无绕道、无交叉、无回流、无等待、无废品的增值活动流,制定创造价值流的行动方案。
优化工序流程的目的是通过对现场的宏观分析,减少和消除不合理、不增值的工艺内容、方法和程序,设计出最优化、经济、合理的工艺程序,缩短制造周期。
3、动作分析动作分析是研究分析人在进行各种工作操作时的动作要素,删除无效动作,使操作简便有效、轻松经济、以提高工作效率。
发现操作人员的无效动作、浪费现象或不安全因素; 简化操作,减少工人疲劳,提高操作安全性,建议在此基础上制定出标准作业程序。
对生产流程的安排,应遵守流程路线经济原则:①路线越短越好②减少停滞和消除重诬③禁止逆行,消除交叉路线④禁止孤岛加工⑤减少动作的数量⑥双手同时进行动作,其生产过程中采集的数据要真实、要及时利用、分析、判断、对出现的问题要及时解决并跟踪反馈。
4、实行“三现”机制以现场为中心,处理事情以现场、现事、现物(三现)为主体,以车间主管为首的“三现”全员参与机制。
“三现”要求快速、有效地处理现场的异常状况,实现高效服务。
生产现场改善的5条黄金法则:①如果发生问题,首先去现场②检查问题发生的现场③立刻采取暂时性措施④查找问题发生的真正原因,拟定永久行动对策⑤验证永久行动对策的有效性,使其标准化,以避免类似问题的再次发生。
精益生产包装线改善方案
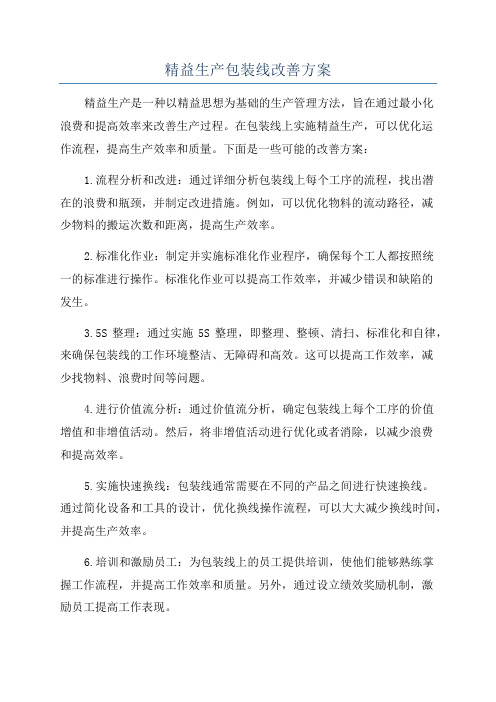
精益生产包装线改善方案精益生产是一种以精益思想为基础的生产管理方法,旨在通过最小化浪费和提高效率来改善生产过程。
在包装线上实施精益生产,可以优化运作流程,提高生产效率和质量。
下面是一些可能的改善方案:1.流程分析和改进:通过详细分析包装线上每个工序的流程,找出潜在的浪费和瓶颈,并制定改进措施。
例如,可以优化物料的流动路径,减少物料的搬运次数和距离,提高生产效率。
2.标准化作业:制定并实施标准化作业程序,确保每个工人都按照统一的标准进行操作。
标准化作业可以提高工作效率,并减少错误和缺陷的发生。
3.5S整理:通过实施5S整理,即整理、整顿、清扫、标准化和自律,来确保包装线的工作环境整洁、无障碍和高效。
这可以提高工作效率,减少找物料、浪费时间等问题。
4.进行价值流分析:通过价值流分析,确定包装线上每个工序的价值增值和非增值活动。
然后,将非增值活动进行优化或者消除,以减少浪费和提高效率。
5.实施快速换线:包装线通常需要在不同的产品之间进行快速换线。
通过简化设备和工具的设计,优化换线操作流程,可以大大减少换线时间,并提高生产效率。
6.培训和激励员工:为包装线上的员工提供培训,使他们能够熟练掌握工作流程,并提高工作效率和质量。
另外,通过设立绩效奖励机制,激励员工提高工作表现。
7.进行持续改进:精益生产是一个持续改进的过程。
定期对包装线进行评估,分析并改进其中的不足之处,以达到更高的生产效率和质量。
总结起来,精益生产包装线改善方案的核心是通过减少浪费、提高效率和质量来优化包装流程。
这需要对工序进行详细分析,制定标准化作业程序,并实施5S整理、价值流分析、快速换线等措施。
同时,培训员工并激励他们参与持续改进也是至关重要的。
通过这些改善方案的实施,可以使包装线更加高效、稳定和可持续。
精益生产改善方案活动的开展

制定改善计划 设定改善期限
分析现状和问题
识别浪费:识别生产过程中的浪费现象 确定改善目标:明确改善的目标和范围 制定改善计划:制定详细的改善计划和时间表 实施改善措施:按照计划实施改善措施,并记录实施过程和结果 评估改善效果:对改善效果进行评估和总结
制定改善措施
确定改善目 标:明确改 善方向和目 标,为后续 措施提供指 导
识别问题:通 过现场观察、 数据分析等方 式,识别出生 产过程中的问
题和浪费。
制定改善措施: 针对识别出的 问题,制定相 应的改善措施, 如优化流程、 改进设备等。
制定实施计划: 明确改善措施 的实施时间、 责任人、所需 资源等,确保 改善活动的顺
利进行。
实施改善活动
确定改善目标:明确改善活动的目标,确保活动方向正确
03
应用场景:适用于重复性、简单性、危险性或 高精度要求的生产任务。
优点:减少人工操作,降低人为因素对产品质 量的影响,提高生产效率和产品质量稳定性。
02
实施步骤:评估现有生产流程,确定自动化改 造的可行性;设计自动化生产线,进行设备选 型和采购;实施自动化改造,进行设备调试和 员工培训;优化自动化生产线,提高生产效率
注重环保和可持续发展
减少浪费和污染:精益 生产改善方案应注重减 少生产过程中的浪费和 污染,提高资源利用效 率。
绿色供应链管理:与供 应商合作,推动绿色供 应链管理,确保原材料 和零部件的环保性能。
能源消耗和排放控制: 优化生产工艺和设备, 降低能源消耗和排放, 符合国家和行业环保 标准。
循环经济和废弃物利用: 推动循环经济和废弃物 利用,将废弃物转化为 可再利用的资源,降低 对环境的影响。
考核机制:建立科学的 考核机制,对员工在精 益生产改善活动中的表 现进行评估和考核,确 保活动的有效实施
精益生产中kaizen改善活动如何开展

精益生产中kaizen改善活动如何开展在当今竞争激烈的市场环境中,企业想要持续发展,提高生产效率和质量,降低成本,精益生产中的 kaizen 改善活动无疑是一个有力的手段。
那么,kaizen 改善活动究竟如何开展呢?首先,我们要明确 kaizen 改善活动的核心理念。
Kaizen 意味着持续改进,它不是一蹴而就的大规模变革,而是通过一系列小的、渐进的改进,逐步积累,最终实现显著的效果。
这种理念强调每个人都参与其中,从一线员工到管理层,都有责任和能力提出并实施改进措施。
开展 kaizen 改善活动的第一步是建立一个有效的团队。
这个团队应该包括来自不同部门和岗位的人员,他们能够从不同的角度看待问题,提出多元化的解决方案。
团队成员要有积极的态度和合作精神,愿意为了共同的目标而努力。
在团队组建完成后,接下来就是确定改善的目标。
目标要具体、可衡量、可实现、相关联且有时限(SMART 原则)。
例如,将某条生产线的生产周期缩短 20%,或者将产品的不良率降低 50%等。
目标的确定需要充分考虑企业的战略规划、当前的生产状况以及客户的需求。
明确了目标,就需要对现状进行深入的分析。
这包括收集数据、观察流程、与相关人员交流等。
例如,如果目标是缩短生产周期,那么就需要详细记录每个生产环节所花费的时间,找出其中的瓶颈环节。
在分析现状的基础上,团队成员要共同探讨可能的改善方案。
这个过程要鼓励创新思维,不怕提出看似“疯狂”的想法。
然后,对这些方案进行评估和筛选,选择那些具有可行性和预期效果较好的方案。
方案确定后,就是实施阶段。
在实施过程中,要密切关注进展情况,及时解决出现的问题。
同时,要做好记录,包括实施的步骤、遇到的困难以及解决的方法等。
实施完成后,要对改善的效果进行评估。
这同样需要依靠数据说话,将改善后的指标与设定的目标进行对比,看是否达到了预期的效果。
如果没有达到,要分析原因,进行进一步的改进。
在整个 kaizen 改善活动中,沟通是至关重要的。
精益生产八大浪费的改善方法

精益生产八大浪费的改善方法
精益生产是一种流程优化的方法,旨在消除浪费并提高效率。
其中最重要的概念就是八大浪费,即:
1. 过度生产:过度生产会导致库存增加,占用空间和资金,造成浪费。
改善方法是采用按需生产模式,即根据市场需求进行生产,减少库存。
2. 等待:等待是一种浪费时间和资源的行为,可以通过优化流程和减少瓶颈来缩短等待时间。
3. 运输:运输浪费时间和成本,可以通过在生产线上进行加工和装配,减少产品运输。
4. 过度加工:过度加工意味着增加了生产成本,但并不会为产品增加价值。
可以通过检查和优化工序,减少不必要的加工。
5. 库存:库存是一种资金和空间的浪费,可以通过压缩生产周期,减少库存。
6. 返工和修补:返工和修补是一种成本高昂的浪费,可以通过提高生产的质量和流程控制来减少。
7. 过度处理:过度处理也会增加成本,但并不会为产品增加价值。
可以通过优化工艺和流程来减少过度处理。
8. 无用的员工:如果员工没有得到充分利用,他们的劳动力就会浪费。
可以通过培训,激励和优化流程来提高员工的工作效率。
总之,通过精益生产的八大浪费改善方法,企业可以提高生产效率,减少成本,提高质量,增强市场竞争力。
- 1、下载文档前请自行甄别文档内容的完整性,平台不提供额外的编辑、内容补充、找答案等附加服务。
- 2、"仅部分预览"的文档,不可在线预览部分如存在完整性等问题,可反馈申请退款(可完整预览的文档不适用该条件!)。
- 3、如文档侵犯您的权益,请联系客服反馈,我们会尽快为您处理(人工客服工作时间:9:00-18:30)。
2. Plan计划
machine
流水线太长 占用空间太大
人员数量/人 流水线长/M
工作区域面积
Actrual Expectati TD on 22 21 28 20
213.3㎡ 152.4㎡
等待时间较长
各工位的时间的分配不均 导致有些工位存在等待装框后使用流水线 将组件转移到下一 工位占用空间太大 method environment
96-cell及72-cell装框 机摆放位置不合理
Target Sheet Progress目 标进度表
kaizen progress status owner huangwenm ing huangwenm ing huangwenm ing huangwenm ing huangwenm ing ww1 7.1 ww1 7.2 ww1 7.3 ww1 7.4 ww1 7.5 ww 17 .6 ww 18 .1
7
Process and Information Flow工艺和信息流程 改善前
8m
1.9m
17.1m
96-cell 72-cell
硅胶机
7.9m
72-cell流水线
72-cell 72-cell
合计28m
Process and Information Flow工艺和信息流程 改善后
4.1m
1.9m
Team Title团队名称 :
CTQs
层压与包装精益生产团队
Unit Of Measurement度 量单位 Start 开始 Target 目标
Date: Week 1 日 期: 1 周
Customer/Model客户/模型 : Line/Area/ Module 产线、区域、组件: 层
Date: Week 2日 期: 2周 Day 1 Day 2 Day 3 Day 4 Day 5
• Use suggested color code ( Blue, Green, Yellow & Red ) in target sheet to visualize the achievement. 在工作表上使用建议的颜色代码(蓝色,绿色,黄色和红色),更形象化进程 • Formula to calculate % Improved = (Start – Actual) / (Start – Target) 计算改善率的公式=(开 始 — 实际)(开始 — 目标)
戴学岗 陈 飞
李 剑
牛建红 陈 欢 林家辉
设备主管, 工程中心
主管,生产中心 IE主管, 工程中心 PE,工程中心
何
军
PE操作员,工程中心
QC主管,品质中心 PE,工程中心 PE操作员,工程中心
刘丽丽 王朋荔 肖菊平
龙
隆
改善组, 生产中心
5
目标及目的
目的: 1、缩短流水线长度,减少空间浪费 2、减少组件在流水线上停留时间 3、96-cell及72-cell流水线共用,节约资源 4.工序合并,精简人员
Standard Work Sheet (After) )标准作业工作表( 之后)
Takt / Cycle Time Graph (After)生产节拍/周期时间表(之后) 21 Spaghetti Chart (After) Spaghetti 图表(之后) 22 23
Kaizen News Paper 改善报
huangwenm ing huangwenm ing
4. Check检查
0-70%
71%-90%
91%-100%
Above 100%
3. Do实施
3
改善需求的独立研究
1、当前的状态及问题: (第一阶段改善) 1 、装框流水线较长,占用空间较大,实际生产中并不 需要太长流水线 2.清洁工位与贴接地标贴工序人员过剩 3.72cell与96cell组件流水线不可通用 (第二阶段改善) 1、切边工位切边后装箱及装框工位从周转箱中取板,为 无价值动作,且浪费了较多的时间 2 、切边后将组件存放在周转箱中时间较长,导致产品 在生产中存在较长等待时间
0-70% 71%-90% 91%-100%
Inventory Inventory (Raw)库 (Wip)库 存(原 存(在制 料) 品) # / DOS # / DOS
Sec
UPH
$ or Hrs
m
OEE
PM time PM时间 Mins
Sec
Above 100%
Mins
%
Quality 质量 Defects Defects (In # of (Raw process)不 Space空 touch接 material ) 良(制程 间 触的数量 不良(原 中) 料) pcs per hour # Sqm #
组建精益生产团队
done
商讨改善对策 现场模拟,评估改善的 可实施性 将72-cell装框后流水线 取消 将清洗工位与贴接地标 贴工位合并精简2名员工 用简单的操作台面使用 一台96-cell装框机装框 后的操作流程 开展会议讨论精益生产 进度
done
done
none
none
none on going
22
21
22
21
28
20
28
28
33
33
People人员 Material物料 Parts Inventory travel (FG)库存 distance零 (成品) 件移动距 离 # / DOS m Other其他
Walking Saftey 安全 Crew size人员数量 Cycle time周期 Productivity 产能 Over time超时 distance 不行距离 UoM度量单位 # # Machine 设备 Down time Change over兑换 (day)停机时 间(天) UoM度量单位
Slide(s)页码
18 19 20
PDCA (Plan – Do – Check – Adjust) PDCA(计划— 执行 — 检 查 — 调整) 3 Independent Study on Kaizen Needs改善需求的独立研究 4 Kaizen Team Members改善团队成员 5 Goals & Objectives目标&目的 6 Target Sheet目标工作表 7 Process & Information Flow工艺&信息流程 8 Value Stream Map 价值流程图 9-11 Standard Work Sheet (Before) 标准作业工作表(之前) 12 Standard Work Combination Sheet标准作业工组合作表 13 Takt / Cycle time Graph (Before) 生产节拍/周期时间表(之前) 14 Spaghetti Chart (Before) Spaghetti 图表(之前) 15 5 Why Analysis Why 分析 16 7 Ways 七种方法 17
目标:
目标
流水线长度 切边后组件流入下一流程 等待时间 精简1名员工 节省空间
量度单位
米(m) 秒(s) (个) 平方米 (㎡)
现状
28 / 22 213.3㎡源自目标20 / 21 152.4
改善效果(改 善率)
29% / 9% 29%
Target Sheet目标工作表
Date日期: 27-04-2011
Process Sketch 工序略图
切边 贴组件 标贴 装箱待 装框 装框 清洗 贴接地 标贴
Quality Requirements 质量要求
密封切口
接线盒打 硅胶
安装接 线盒
插引出线
堆放组件
Idea 1 第一个构想
层压与包装精益生产改善
Contents内容
• • • • • • • • • • • • •
Table of Contents目录
Slide(s)页码 Contents内容
Idea Evaluation Sheet 构想评估表 Before & After Kaizen 改善前&后
Head Count 总人数 Activity Cycle Time 活动 周期时间 Travel Distance 流动距 离 Peripherals 外围设备 Wip rack/N2在制品架子 Cassettes(tc,cc,qb) No. of cycle activities
HC s m pcs pcs qty
Kaizen Log (Homework Moving Forward)改善日记(进步的 任务) 24 Lesson & Tools Learned 学习的课程&工具 25
Kaizen Log (Proposal for Yokoten)改善日记(扩展的建议) 26 Attendance List 签到表 Financial Performance Dashboard财政状况Dashboard 28 VSM Icon & Symbols VSM 图标&标志 29 27
堆放组件
有价值动作
无价值动作
检查
工序
库存
10
Current Value Stream Mapping – Top Level (Overall)当前的价值流程图 — 最高水平(整体)
改善后
改善后可将清 洗与接地标题 工位合并
切边
贴组件 标贴
装箱待装框
装框
清洗
贴接地 标贴
密封切口
接线盒打 硅胶
安装接 线盒
Grasp The Situation ww ww ww