精益生产推行方案20140219
精益生产方案

精益生产方案精益生产(Lean Production)是一种以最小化浪费为目标的生产管理方法,旨在提高生产效率、降低成本并提升产品质量。
以下是一个针对精益生产方案的详细介绍:一、方案背景精益生产得到了广泛的应用,它的目标是通过消除浪费,优化生产流程并最大程度地满足顾客需求。
为了更好地实施精益生产,公司决定制定一套个性化的精益生产方案,以期达到持续改进和卓越绩效。
二、方案目标1. 提升生产效率:通过流程优化、减少等待时间和缩短生产周期等措施,实现生产效率的提升。
2. 降低生产成本:通过消除浪费、减少库存和减少不必要的环节,以降低生产成本。
3. 提高产品质量:通过改进现有工艺、加强质量控制和培训员工等手段,提高产品质量。
4. 增强员工参与:倡导员工的积极参与和思考,培养团队合作精神。
三、方案实施步骤1. 现状分析:对现有生产流程进行全面的分析,找出存在的问题和潜在的改进点。
2. 流程优化:根据现状分析的结果,对生产流程进行优化设计,避免不必要的等待和环节。
3. 绩效评估:制定评估指标,对优化后的生产流程进行绩效评估,以确保方案的有效性。
4. 培训与协作:提供员工培训,加强他们在精益生产中的理解和参与,并促进部门之间的合作。
5. 持续改进:推行持续改进的理念,定期开展评估和改进活动,确保方案能够不断适应市场和客户需求的变化。
四、方案预期效果1. 生产效率提升:生产周期缩短、交货时间得到保证,客户满意度提高。
2. 生产成本降低:减少浪费、降低库存成本,实现生产成本的有效控制。
3. 产品质量提高:加强质量控制手段,提升产品的一致性和可靠性。
4. 员工参与度提升:员工积极参与,主动改进工艺和流程,增强团队凝聚力和合作精神。
五、总结与展望精益生产方案是一种以最小化浪费为目标的生产管理方法,可以有效提高生产效率、降低成本并提升产品质量。
通过实施这一方案,公司将能够实现持续改进和卓越绩效,从而在激烈的市场竞争中保持竞争优势。
精益生产推行方案
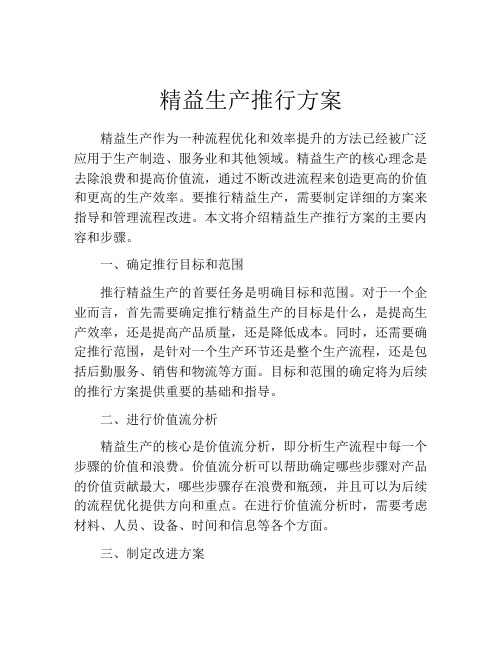
精益生产推行方案精益生产作为一种流程优化和效率提升的方法已经被广泛应用于生产制造、服务业和其他领域。
精益生产的核心理念是去除浪费和提高价值流,通过不断改进流程来创造更高的价值和更高的生产效率。
要推行精益生产,需要制定详细的方案来指导和管理流程改进。
本文将介绍精益生产推行方案的主要内容和步骤。
一、确定推行目标和范围推行精益生产的首要任务是明确目标和范围。
对于一个企业而言,首先需要确定推行精益生产的目标是什么,是提高生产效率,还是提高产品质量,还是降低成本。
同时,还需要确定推行范围,是针对一个生产环节还是整个生产流程,还是包括后勤服务、销售和物流等方面。
目标和范围的确定将为后续的推行方案提供重要的基础和指导。
二、进行价值流分析精益生产的核心是价值流分析,即分析生产流程中每一个步骤的价值和浪费。
价值流分析可以帮助确定哪些步骤对产品的价值贡献最大,哪些步骤存在浪费和瓶颈,并且可以为后续的流程优化提供方向和重点。
在进行价值流分析时,需要考虑材料、人员、设备、时间和信息等各个方面。
三、制定改进方案在明确了推行目标和进行了价值流分析后,需要制定具体的改进方案。
改进方案应该根据价值流分析的结果,选取重要的改进方向和目标,确定改进的具体步骤和计划,并且制定详细的改进方案文档和流程图。
改进计划应该涵盖人员、设备、流程、培训和评估等方面。
四、实施改进制定的改进方案需要在实施阶段得到贯彻和落实。
实施改进需要考虑流程优化、文化建设、培训和质量评估等方面。
在推行过程中,还需要注意和人员和团队的沟通和协调,确保每个人都能理解和认同改进方案的目标和效果。
五、持续改进和监控精益生产是一个不断改进的过程。
一旦实施了改进方案,就需要不断地监控和评估改进效果,并且寻找更多的优化机会。
监控和评估可以通过流程指标、质量评估和客户反馈等方式进行。
持续改进的目标是不断提高生产效率和产品质量,不断满足客户需求,并且为企业带来更多的价值。
综上所述,精益生产推行方案是一项关键的管理活动。
精益生产推行方案

为实现目标,制定详细的实施计划,包括实施时间、资源投入、 关键里程碑等。
考虑风险
预测实施过程中可能出现的风险和障碍,制定应对措施。
价值流分析
识别价值流
01
分析产品或服务的整个价值流,包括原材料采购、生
产制造、物流配送等环节。
找出瓶颈
02 识别价值流中的瓶颈和问题,如生产效率低下、物料
短缺等。
制定优化方案
03
针对瓶颈制定优化方案,如改进工艺流程、调整生产
线布局等。
流程优化与重组
流程梳理
梳理现有流程,发现流程中的问题和浪费。
流程优化
针对问题,提出优化方案,如简化流程、合 并重复环节等。
流程重组
对整个流程进行重新设计,实现流程的简化 和高效化。
消除浪费与持续改进
1 2
识别浪费
分析生产过程中的浪费,如等待时间、过量生产 、不良品等。
2. 持续改进创新
鼓励员工提出创新性改进方案 ,不断优化生产流程和技术。
未来发展方向与展望
3. 深化供应链协同
与供应商和合作伙伴建立更紧密的合作关系, 实现更高效的供应链协同。
4. 引入先进技术
引进先进的生产技术和设备,提高生产效率和 产品质量。
展望
通过不断努力和完善,预计在未来的3-5年内,企业将实现以下目标
持续改进文化的建立
树立持续改进的意识
要让员工认识到持续改进的重要性,培养员工主动发现问题、提 出改进措施的意识。
建立奖励机制
对于提出有效改进措施的员工,应当给予适当的奖励和激励,以鼓 励更多的员工参与到持续改进中来。
营造学习氛围
企业需要营造一个积极的学习氛围,鼓励员工不断学习和掌握新技 能,为企业的持续改进提供源源不断的动力。
精益生产推行步骤

推行精益生产的顺序与步骤步骤一:意识引导,培训先行精益生产方式把生产中一切不能增加价值的活动都视为浪费。
强调人的作用,充分发挥人的潜力,以持续改善来消除浪费。
因此,在实施的第一步,应进行多全员的意识培训,培训对象应上至总经理、副总经理,下至作业员、搬运员,培训内容应包括"竞争情况"、。
浪费的观念〃、拉动生产〃、〃5S〃、〃团队改善〃、〃全员设备管理"、全面质量管理"。
只有建立在全员对精益生产的了解和基本认同的基础上推动才能顺利进行。
步骤二:成立项目领导和推行小组很多企业在实施精益生产的时候,都会建立一个精益生产组织,有的叫"精益生产委员会",有的叫"改善组织"。
一般来说,总经理应是精益组织的负责人,有些企业也把工厂负责的副总经理列为负责人,组织应包括生产管理部门、制造部门、生产技术郎门、品质部门的等相关部门的主管,要确立负责人的改善职责。
实施精益生产应做好计划,包括系统的实施计划、年度计划和月度计划。
计划应该包括项目、分析、责任人、完成时间等,并按照PDCA的方式进行记录。
步骤三:示范线改善,体现成果,建立改善样板区域任何改善都是建立在对美好的期望基础上的,要让员工真正的接受变革,必须让员工看到实际的成果,并且很多精益的工具也需要在实际的实施过程才能诠释它的优点。
精益生产的实施开始3到6个月,当5s取得初步成果的时候,可以选择一条生产线进行示范改善。
有的企业把示范线改善,叫做"对象线改善"或"小范围改善",改善的内容要尽可能的运用精益的工具,选择示范线进行改善的时候,应该选择流水作业的线,要认真确认好改善前的状态,包括:成品及使用零件清单、现状平面布置Layout图、现状物与情报流程图、现行各工程C/T时间调查、线边库存状况调查、送货频率及数量等。
改善应该循序渐进,并落实每个事情的责任人,还应注意多运用头脑风暴的方法、集思广益。
精益生产推行计划

精益生产推行计划1.目的:精远制定精益生产推行计划主要目的是更好的将精益生产的思想灌输到每一个员工的内心当中,并指导每位员工所想的就是如何在自己的工作中找出浪费、消除浪费、解决实际问题,通过不断地消除浪费、解决问题实现以最小的资源投入为仓门模块创造最大的价值,在尽可能短的时间内满足领导要求。
并最终使精益成为持续改善的文化,成为一种精益求精的思想和理念。
2.适用范围:适用于公司内部各部门3.精益生产怎样推行步骤(三阶段,六步骤):精远将精益生产模块推行分为三个阶段,分六步完成一:三个阶段1、准备阶段2、实施评估阶段3、巩固阶段二:六个步骤1、成立推行组织2、策划3、宣传造势、员工培训4、局部试行5、全面导入6、巩固,纳入日常管理活动精益生产推行具体内容是什么?(一)成立推行组织1、制定活动导入程序图2、成立精益生产推行小组成立益生产推行小组,结合模块组织力量,以形成体系的保障(1)小组职位设置:组长、组员、精益专员(2)小组总人数应控制在15人内。
3、确定组织职责(1)推行小组:负责精益生产活动的计划和工作的开展;(2)组长:负责精益生产小组的运作,指挥和监督所属组员和精益生产专员(3)精益生产专员A 制订、修订精益生产活动计划,确实执行组长之命;B 拟定各种活动办法;C 负责进行本部门的宣传教育、推动精益生产活动;D 搜集模块员工改善提议,并整理形成A3提案;E 负责精益生产活动的定期审核;F 定期检讨、改善;G 进行活动指导及争议的处理;H 处理其它有关精益生产活动事务。
(4)组员:A 参与制订、修订精益生产活动计划,确实执行组长之命;B 参与拟定各种活动办法;C 参与本部门的宣传教育、推动精益生产活动;D 参与活动指导及争议的处理;E 处理其它有关精益生产活动事务。
(二)策划1、拟定推行口号及目标(1)推行口号(参考)彻底推行,全员参与改善从今天开始(2)推行目标精益生产活动期望的目标:2、收集资料收集精益生产相关的资料,如推行手册、标语、培训资料、其他厂的案例等,为后面的工作做准备。
精益生产推行方案

精益生产推行方案1. 引言精益生产是一种高效率、低浪费的生产管理方法,旨在通过优化生产过程,减少资源浪费,提高产品质量和生产效益。
本文档旨在介绍精益生产的推行方案,以帮助企业提升生产效率和竞争力。
2. 目标与原则2.1 目标推行精益生产的目标是实现以下几点: - 减少生产中的浪费,提高资源利用效率; - 提高产品质量,降低不良品率; - 缩短生产周期,提高客户满意度; - 提高员工参与度和工作满意度。
2.2 原则在推行精益生产时,需要遵循以下原则: - 根据客户需求进行价值流分析; - 持续改进,追求卓越; - 实施团队合作与员工参与; - 减少浪费,提高效率; - 优化生产流程,降低生产周期; - 精确管理,高效执行。
3. 推行步骤3.1 价值流分析首先,需要进行价值流分析,分析生产过程中的价值流和非价值流,找出存在的浪费和瓶颈,为后续的改进工作提供依据。
通过价值流分析,可以明确产品的价值链,识别出可以优化和改进的环节。
3.2 浪费识别在价值流分析的基础上,对生产线进行浪费识别,主要包括以下几个方面: - 过多的库存造成的浪费; - 不必要的运输和等待时间造成的浪费; - 产品质量问题造成的浪费; - 人员不合理利用造成的浪费。
3.3 浪费消除通过识别浪费,制定对策并实施,以消除浪费,提高生产效率。
常用的浪费消除方法包括: - 库存管理优化,实现“按需生产”; - 设备维护保养,避免因设备故障导致的生产停滞; - 实施自动化生产,提高生产线的灵活性和效率; - 员工培训和激励,提高工作质量和效率。
3.4 持续改进推行精益生产需要持续改进,通过不断地优化生产流程和管理方法,实现生产效率的持续提升。
为实现持续改进,可以采取以下措施: - 建立良好的绩效评估体系,以评估生产过程中的问题和潜在改进点; - 建立团队合作机制,鼓励员工提出改进建议,并进行实施; - 定期召开改进会议,总结经验,分享最佳实践。
精益生产推进计划

精益生产推进计划一、背景随着市场竞争的日益激烈,企业面临着提高生产效率、降低成本、提升产品质量等诸多挑战。
精益生产作为一种有效的生产管理方式,能够帮助企业消除浪费、优化流程、提高生产灵活性,从而增强企业的竞争力。
为了在本企业成功推行精益生产,特制定以下推进计划。
二、目标1、在接下来的具体时间段内,将生产周期缩短X%。
2、减少库存X%,降低库存成本。
3、提高产品质量,将次品率降低至X%以下。
4、提升员工的工作效率X%。
三、推进步骤1、培训与教育组织全体员工参加精益生产的培训课程,包括理论知识和实际案例分析。
邀请外部专家进行讲座,分享精益生产的成功经验。
内部成立精益生产学习小组,定期进行交流和研讨。
2、现状评估对现有生产流程进行详细的价值流分析,找出其中的浪费环节和瓶颈。
收集生产过程中的各项数据,如生产周期、库存水平、次品率、员工工时等。
与同行业的先进企业进行对标,找出差距和改进方向。
3、制定改进方案根据现状评估的结果,制定具体的改进方案,明确责任人和时间节点。
优先解决对生产影响较大的问题,如过长的生产周期、高库存等。
鼓励员工提出改进建议,对有价值的建议给予奖励。
4、实施改进方案按照制定的改进方案,逐步推进实施。
建立有效的监控机制,定期检查改进措施的执行情况和效果。
及时调整改进方案,确保达到预期目标。
5、持续改进将精益生产的理念和方法融入企业文化,形成持续改进的氛围。
定期对生产流程进行评估和优化,不断寻找新的改进机会。
建立精益生产的绩效考核体系,激励员工积极参与。
四、资源需求1、人力资源成立精益生产推进小组,包括生产、质量、工程等部门的人员。
培训内部的精益生产专家,负责指导和推进工作。
2、资金投入预算具体金额用于培训、咨询、设备改造等方面。
设立专项奖励基金,激励员工的创新和改进行为。
3、时间安排为每个推进步骤制定详细的时间计划,确保按时完成任务。
五、风险与应对措施1、员工抵触加强沟通和培训,让员工了解精益生产的好处和对个人的影响。
《推行精益生产》管理办法范本
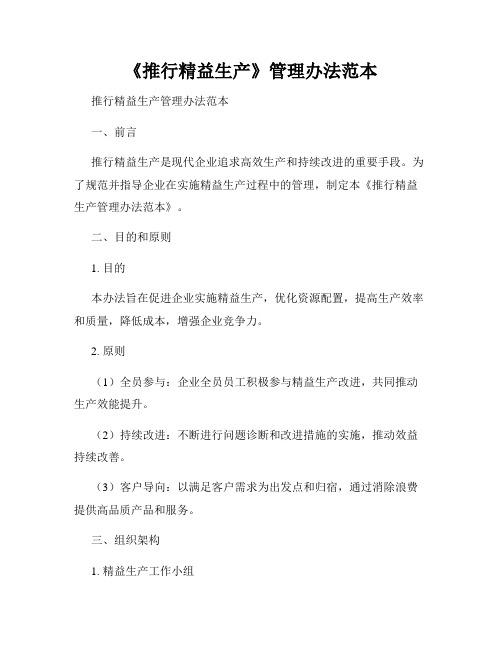
《推行精益生产》管理办法范本推行精益生产管理办法范本一、前言推行精益生产是现代企业追求高效生产和持续改进的重要手段。
为了规范并指导企业在实施精益生产过程中的管理,制定本《推行精益生产管理办法范本》。
二、目的和原则1. 目的本办法旨在促进企业实施精益生产,优化资源配置,提高生产效率和质量,降低成本,增强企业竞争力。
2. 原则(1)全员参与:企业全员员工积极参与精益生产改进,共同推动生产效能提升。
(2)持续改进:不断进行问题诊断和改进措施的实施,推动效益持续改善。
(3)客户导向:以满足客户需求为出发点和归宿,通过消除浪费提供高品质产品和服务。
三、组织架构1. 精益生产工作小组(1)设立一个由高级管理人员领导的精益生产工作小组,负责全面推行精益生产管理。
(2)精益生产工作小组成员包括各部门负责人、生产线负责人、工程师等。
2. 生产现场改善团队(1)每个生产现场设立一个改善团队,由相关岗位员工组成。
(2)改善团队负责收集问题和改进意见,协助制定和执行改进计划。
四、精益生产改进流程1. 问题诊断与目标设定(1)通过调研和数据分析,确定关键问题和改进重点。
(2)制定具体的改进目标,并与生产现场改善团队沟通和确认。
2. 参与员工培训(1)组织相关员工参加精益生产培训课程,提高员工对于精益生产理念和工具的了解和运用能力。
(2)培训课程包括精益生产原理、价值流分析、5S整理、标准化工作、持续改进等内容。
3. 现场改善活动(1)展开现场改善活动,通过使用精益工具和方法,发现并解决生产中存在的问题。
(2)改善活动包括价值流分析、5S整理、设备保养管理、设备故障分析等。
4. 改进计划制定与执行(1)针对问题和目标,制定具体的改进计划。
(2)实施改进计划,并跟踪改进效果。
5. 效果评估与总结(1)评估改进计划的效果,分析改进结果。
(2)总结经验教训,形成改进案例,为今后的改进活动提供借鉴。
五、精益生产改进工具1. 价值流图价值流图是用来描述产品和信息在生产过程中的流动情况的一种工具,通过分析价值流图,找出流程中的浪费点并提出改进措施。
实施精益生产的方案
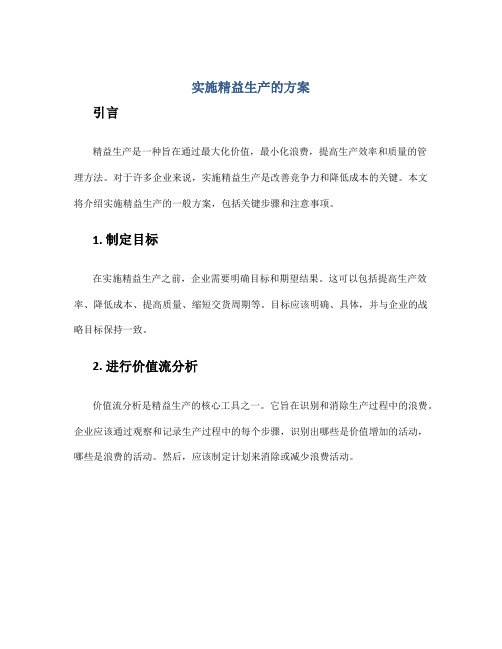
实施精益生产的方案引言精益生产是一种旨在通过最大化价值,最小化浪费,提高生产效率和质量的管理方法。
对于许多企业来说,实施精益生产是改善竞争力和降低成本的关键。
本文将介绍实施精益生产的一般方案,包括关键步骤和注意事项。
1. 制定目标在实施精益生产之前,企业需要明确目标和期望结果。
这可以包括提高生产效率、降低成本、提高质量、缩短交货周期等。
目标应该明确、具体,并与企业的战略目标保持一致。
2. 进行价值流分析价值流分析是精益生产的核心工具之一。
它旨在识别和消除生产过程中的浪费。
企业应该通过观察和记录生产过程中的每个步骤,识别出哪些是价值增加的活动,哪些是浪费的活动。
然后,应该制定计划来消除或减少浪费活动。
3. 提升员工技能实施精益生产需要员工具备一定的技能和知识。
企业应该提供培训和教育机会,以提高员工的技能水平。
这包括培训员工使用精益工具和技术,如价值流映射、5S、持续改进等。
4. 实施持续改进机制持续改进是精益生产的核心原则之一。
企业应该建立一个持续改进的机制,以不断寻找和消除浪费,优化生产过程。
这可以包括定期召开改进会议,收集员工的改进建议,实施改进措施并持续监控改进效果。
5. 设置关键绩效指标为了跟踪实施精益生产的效果,企业应该设置关键绩效指标(KPIs)。
这些指标可以包括生产效率、质量指标、交货周期、库存水平等。
通过监控这些指标,企业可以及时了解改进措施的效果,并制定新的改进计划。
6. 建立改进文化实施精益生产需要企业建立一种改进文化,鼓励员工主动参与持续改进活动。
这可以通过提供奖励制度、与员工分享改进成果、建立改进小组等方式实现。
建立改进文化可以激励员工积极参与改进活动,推动精益生产的实施。
7. 管理变革实施精益生产可能需要对现有的生产方式和流程进行改变。
这对于企业来说可能是一项挑战,需要管理层提供足够的支持和资源,并积极解决员工的抵触情绪。
透明的沟通和开放的反馈机制可以帮助管理层和员工共同应对变革。
精益生产管理推行方案

精益生产管理推行方案一、引言精益生产管理是一种以消除浪费为核心,追求最大效率的生产管理方式。
它起源于日本的丰田汽车公司,现在已经被全球许多企业广泛采用。
本方案旨在通过实施精益生产管理,提高生产效率,降低生产成本,提升产品质量和客户满意度。
二、目标1. 提高生产效率:通过消除生产过程中的各种浪费,提高生产效率。
2. 降低生产成本:通过优化生产流程,减少不必要的投入,降低生产成本。
3. 提升产品质量:通过持续改进,提升产品质量,满足客户需求。
4. 提升客户满意度:通过提供高质量的产品和服务,提升客户满意度。
三、实施步骤1. 培训和教育:对全体员工进行精益生产管理的培训和教育,使员工了解精益生产管理的理念和方法。
2. 价值流分析:通过对生产流程的分析,识别出浪费的环节,为后续的改进提供依据。
3. 流程优化:根据价值流分析的结果,优化生产流程,消除浪费。
4. 持续改进:建立持续改进的机制,定期对生产流程进行检查和改进。
四、实施策略1. 领导层的支持:精益生产管理的实施需要领导层的支持和推动。
2. 全员参与:精益生产管理的实施需要全员的参与,每个人都要成为改进的一部分。
3. 持续改进:精益生产管理的实施是一个持续改进的过程,需要不断地学习和改进。
五、预期效果1. 生产效率的提高:通过消除浪费,提高生产效率。
2. 生产成本的降低:通过优化生产流程,减少不必要的投入,降低生产成本。
3. 产品质量的提升:通过持续改进,提升产品质量。
4. 客户满意度的提升:通过提供高质量的产品和服务,提升客户满意度。
六、总结精益生产管理是一种有效的生产管理方式,它可以帮助企业提高生产效率,降低生产成本,提升产品质量和客户满意度。
但是,精益生产管理的实施需要全员的参与和持续的努力,只有这样,才能真正实现精益生产管理的目标。
某公司精益生产推进方案
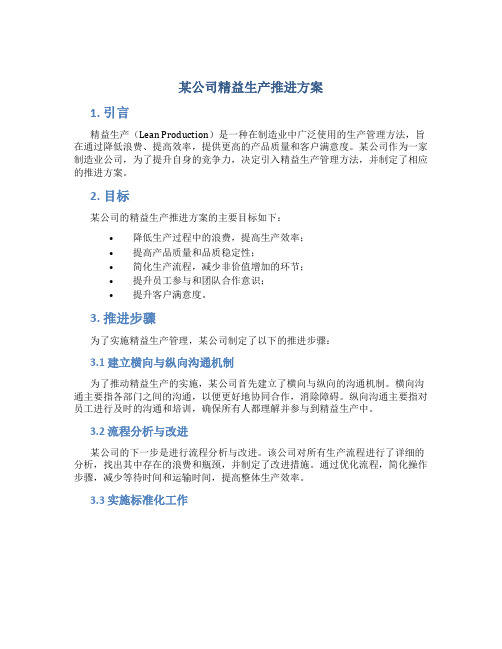
某公司精益生产推进方案
1. 引言
精益生产(Lean Production)是一种在制造业中广泛使用的生产管理方法,旨在通过降低浪费、提高效率,提供更高的产品质量和客户满意度。
某公司作为一家制造业公司,为了提升自身的竞争力,决定引入精益生产管理方法,并制定了相应的推进方案。
2. 目标
某公司的精益生产推进方案的主要目标如下:
•降低生产过程中的浪费,提高生产效率;
•提高产品质量和品质稳定性;
•简化生产流程,减少非价值增加的环节;
•提升员工参与和团队合作意识;
•提升客户满意度。
3. 推进步骤
为了实施精益生产管理,某公司制定了以下的推进步骤:
3.1 建立横向与纵向沟通机制
为了推动精益生产的实施,某公司首先建立了横向与纵向的沟通机制。
横向沟通主要指各部门之间的沟通,以便更好地协同合作,消除障碍。
纵向沟通主要指对员工进行及时的沟通和培训,确保所有人都理解并参与到精益生产中。
3.2 流程分析与改进
某公司的下一步是进行流程分析与改进。
该公司对所有生产流程进行了详细的分析,找出其中存在的浪费和瓶颈,并制定了改进措施。
通过优化流程,简化操作步骤,减少等待时间和运输时间,提高整体生产效率。
3.3 实施标准化工作。
精益生产推行预案
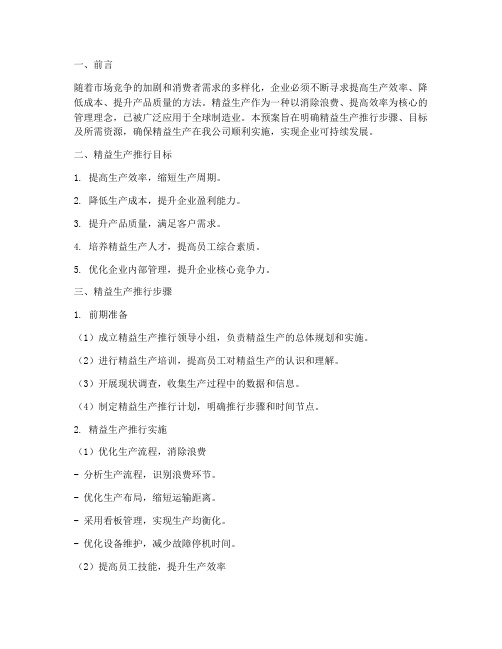
一、前言随着市场竞争的加剧和消费者需求的多样化,企业必须不断寻求提高生产效率、降低成本、提升产品质量的方法。
精益生产作为一种以消除浪费、提高效率为核心的管理理念,已被广泛应用于全球制造业。
本预案旨在明确精益生产推行步骤、目标及所需资源,确保精益生产在我公司顺利实施,实现企业可持续发展。
二、精益生产推行目标1. 提高生产效率,缩短生产周期。
2. 降低生产成本,提升企业盈利能力。
3. 提升产品质量,满足客户需求。
4. 培养精益生产人才,提高员工综合素质。
5. 优化企业内部管理,提升企业核心竞争力。
三、精益生产推行步骤1. 前期准备(1)成立精益生产推行领导小组,负责精益生产的总体规划和实施。
(2)进行精益生产培训,提高员工对精益生产的认识和理解。
(3)开展现状调查,收集生产过程中的数据和信息。
(4)制定精益生产推行计划,明确推行步骤和时间节点。
2. 精益生产推行实施(1)优化生产流程,消除浪费- 分析生产流程,识别浪费环节。
- 优化生产布局,缩短运输距离。
- 采用看板管理,实现生产均衡化。
- 优化设备维护,减少故障停机时间。
(2)提高员工技能,提升生产效率- 开展技能培训,提高员工操作技能。
- 实施岗位责任制,明确员工职责。
- 建立绩效考核制度,激发员工积极性。
(3)加强质量管理,提升产品质量- 严格执行质量标准,确保产品质量。
- 建立质量追溯体系,实现产品质量可追溯。
- 加强供应商管理,确保原材料质量。
(4)优化供应链管理,降低生产成本- 建立供应商评估体系,选择优质供应商。
- 优化库存管理,降低库存成本。
- 实施准时制生产,减少库存积压。
3. 精益生产推行评估(1)定期评估精益生产推行效果,分析存在的问题。
(2)根据评估结果,调整精益生产推行计划。
(3)总结成功经验,形成标准化作业流程。
四、所需资源1. 人力资源:成立精益生产推行领导小组,选拔具备相关经验和技能的员工参与推行。
2. 物力资源:提供必要的学习资料、培训设备和改善工具。
精益生产推进计划
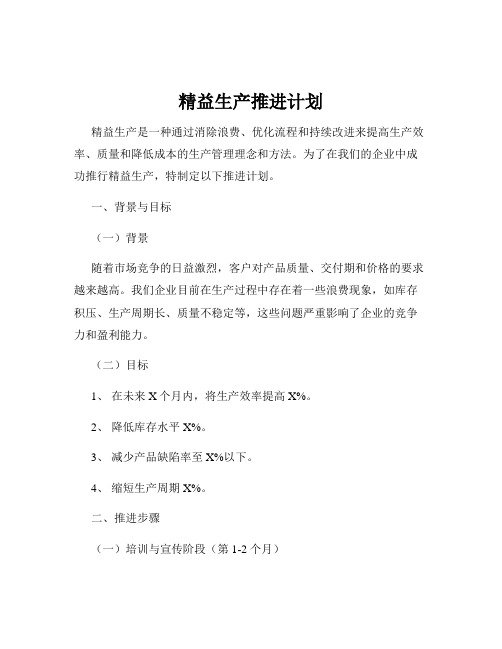
精益生产推进计划精益生产是一种通过消除浪费、优化流程和持续改进来提高生产效率、质量和降低成本的生产管理理念和方法。
为了在我们的企业中成功推行精益生产,特制定以下推进计划。
一、背景与目标(一)背景随着市场竞争的日益激烈,客户对产品质量、交付期和价格的要求越来越高。
我们企业目前在生产过程中存在着一些浪费现象,如库存积压、生产周期长、质量不稳定等,这些问题严重影响了企业的竞争力和盈利能力。
(二)目标1、在未来X个月内,将生产效率提高X%。
2、降低库存水平X%。
3、减少产品缺陷率至X%以下。
4、缩短生产周期X%。
二、推进步骤(一)培训与宣传阶段(第 1-2 个月)1、组织全体员工参加精益生产理念和方法的培训课程,邀请专业的精益生产顾问进行授课,让员工了解精益生产的核心概念和工具,如价值流分析、5S 管理、准时制生产等。
2、在企业内部张贴精益生产的宣传海报,发放宣传手册,营造精益生产的氛围。
3、成立精益生产推进小组,小组成员包括各部门的负责人和骨干员工,负责推进计划的制定和实施。
(二)现状评估阶段(第 3 个月)1、运用价值流分析工具,对企业的主要产品进行价值流图绘制,找出生产过程中的非增值环节和浪费点。
2、对生产现场进行 5S 检查,评估现场管理水平。
3、收集质量数据,分析产品缺陷的类型和原因。
4、与供应商和客户进行沟通,了解上下游环节的需求和问题。
(三)方案制定阶段(第 4 个月)1、根据现状评估的结果,制定具体的改进方案,明确改进的目标、措施、责任人、时间节点等。
2、针对库存管理问题,制定库存优化方案,如采用拉动式生产、设置安全库存等。
3、针对质量问题,制定质量改进计划,如加强过程控制、引入质量管理工具等。
4、针对生产流程优化,制定流程再造方案,消除不必要的工序和等待时间。
(四)实施改进阶段(第 5-8 个月)1、按照改进方案逐步实施改进措施,定期进行检查和评估,确保改进工作按计划进行。
2、推行 5S 管理,保持生产现场的整洁、有序,提高工作效率。
精益生产推行方案

:50%↓
Out-Put Image
现场 活动Manual
•3. 2023~2023年度精益生产
活动方向
8月: 精益生产开启 9月初: 5S 竞赛
8~9月: 部门报告
奖励
日程计划 实施内容
8
9
10
11
12
1
2· 3
4
5
6
7
精益Team增援
7月: 第二年计划
制定项目有关实施细则 及人员安排
•2023年1月5:月:评价委员会 精益年度总结及预想
3 精益生产旳工作方向
•3- 1 •3- 2 •3- 3 •3- 4 •3- 5 •3- 6
18~23年度精益 Vers 18~23年度精益项目别 18~23年度年间活动计 精益评价Check Shee 精益生产项目别定义及 精益生产项目别等级基
Prologue
序言: 一种对精益没有执行经验旳企业需要导入精益系统,其真正旳开端并不是开启精益
精益 Team +评价委员
精益 Team +评价委员
• - 实施措施,Skill增援
•3. 2023~2023年度精益生产 活动方向
目旳
经过基本遵守及发明优质旳现场环境构成迅速执行旳基础
4) 5S竞赛准备
时间
•23年9月
•※ 各注塑生产机台及有关生产区域
对象
车间管理现场/办公区域
评价委员
5S 担当及精益Team
3.人旳培养;---精益(IE)除本身专业知识外,本身就是措施论,结合各各岗位旳专业知识加以应用 才干发挥作用(基础IE+统计学、系统工程、运筹学)
Prologue
个别员工执行力差是能力问题,企业整体执行力差是就是管理问题!
推行精益生产方式的实施方案.doc

推行精益生产方式的实施方案7 推行精益生产方式的实施方案(一)改变文化,转变观念。
培养新的价值观作为一种先进的制造系统,精益生产方式是企业内人、技术和经营思想的高度集成和统一。
精益生产方式与企业理念之问有着广泛的内在联系。
精益生产方式本身就是“逆向思维”的结果。
它将是企业战略观念的根本性变革,这一变革将困难重重。
实施精益生产方式所必需的企业精神和人文环境的培育就必须通过精益企业理念的构建和贯彻来促进和强化。
精益生产是一个系统的工程,涉及企业生产活动的各个环节,需要全体员工的高度重视与共同参与。
要通过教育、培训,使全体员工树立这样一种理念:即浪费是最大的“敌人”。
要通过教育、培训,使各层级的员工掌握精益生产的基本理论与方法。
(二)强化规范,树立遵章守纪、以“人”为中心、渐进式的企业文化第一,学习和推行精益生产方式只有理念和意识是远远不够的。
还必须有一些强制机制。
在精益生产方式中,为了实现准时化生产,同时保证无限向零库存逼近,生产系统本身应该是具有对产品和零部件质量的强制性约束机制,即强迫生产过程中的每一道下序必须产出质量合格的制品。
“一次把事情做对”。
这一切都要求管理者、操作者严格遵照规矩办事,在遵章守纪的基础上进行创新。
也只有尽量排除了人员的随意性,才能发现企业运营系统与市场需求之间的差距,推动企业不断改善。
第二,精益生产方式要求高层管理者充分信任员工,训练员工。
提高他们的素质,加大他们决策权力,建守起以“人”为中心的人本文化。
生产过程中大量浪费是无形的,微小的,与员工的工作密切相关。
要杜绝这些现象,首先要依靠员工,高度信任员工。
因为这些浪费,需要员工思想观念的逐步转换,工作习惯的不断改变才能实现。
其次,要不断提高员工素质。
管理者应成为教练员、协调员、支持者和服务者,负责训练和培养员工,提高员工的整体素质,让员工有能力发现生产中的各种浪费现象并能自己分析解决。
再次要充分授权给员工,加大他们的决策范围。
{精益生产管理}精益生产推行方案
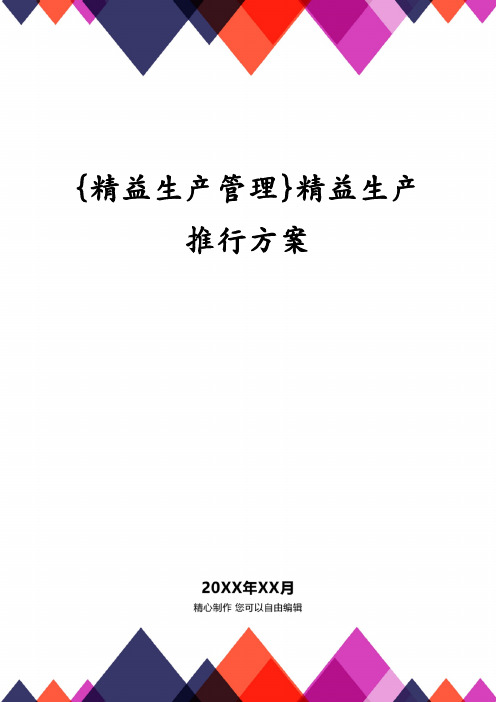
{精益生产管理}精益生产推行方案摘要近年来,随着市场竞争的增强,企业的经营面临着较为严峻的挑战。
在公司中实施精益生产,是目前企业生产管理中的当务之急。
下面我们将跟随公司灯具的生产现状,运用价值流图析技术,识别出当前流程活动中的浪费现象;使用作业测定方法,测定生产线作业时间并计算其标准工时和生产节拍,发现生产线的平衡性差、员工工时利用率低下;使用工序分析方法,发现了在制品停滞、搬运时间过长等问题。
我们利用工业工程和精益生产工具,制定并实施了一套精益生产方案。
首先,对工序流程进行改善,利用ECRS(取消、合并、重排、简化)原则和5W2H方法,减少流程当中半成品的停滞时间,清除不必要的搬运活动。
其次,通过作业改善和优化,平衡生产线,使员工平均利用率得以提高。
接着,为了充分实现工序流程改善效果,公司还可辅以生产布局的改善,对生产线进行消除合并、重排优化、作业设计改进,提高了生产线利用率;同时,我们通过生产看板系统和准时化供货,保证可视化管理和生产准时化。
总结改善结果,绘制改善后的价值流程图。
最后,通过调整组织机构和实施5S、TPM等措施,保证精益生产的持续进行。
关键词:精益生产方案设计生产线平衡价值流图第一章绪论随着市场趋向全球化,摆在所有制造业面前的将是更为激烈和变幻莫测的市场竞争,竞争的核心是以知识为基础的新产品竞争。
为提高竞争力,制造企业必须以最快的上市速度、最好的质量、最低的成本、最优的服务及最清洁的环境来满足不同顾客对新产品的需求和社会可持续发展的要求。
企业为了获得自身的可持续发展,它必须将精益生产理念作为经营战略中的一个首要因素来对待。
支撑创新力经济的生产方式“精益生产(LeanProduction-LP)”是获取与提升各类组织自主创新力的四大技术群之一。
正如詹姆斯·沃麦克等人指出的那样,精益生产的理念“可以适用于任何国家与地区的不同制造业和不同的工厂和不同的企业文化”。
因为“没有一个国家可以在低廉的工资基础上在全球竞争中建立长时间的绝对优势”,“但可以通过精益生产和精益理念来维持优势”。
精益生产管理实施方案

精益生产管理实施方案一、总体指导思想1.精益生产作为当今最为先进的制造管理方法,具有很强的实践性。
改善实施必须始终围绕精益生产管理体系的核心即消除浪费来开展各项工作,时时以精益生产思想作为工作指导的有力武器。
2.任何一项管理理论都不是一成不变的适用每一个企业。
在应用精益生产理论进行改善时,必须时刻结合企业所处的行业环境和企业本身的特殊性进行灵活应用,因地制宜。
只有这样,才一不至于在改善中生搬硬套,走错方向。
例如由于手机行业存在市场机会成本,战略要求不能完全做到“零库存”管理。
3一个拥有卓越企业文化和管理的企业,需要经过多年的实践积淀才能实现。
丰田公司自成立初期就开始不断探讨生产模式,历经四十年时间才一逐步形成了初步成型的丰田方式。
时至今日,丰田方式仍在不断改善进步中。
因此,没有那个企业的实现是一瞰而就的,需要一点一滴的积累。
卓越企业管理需要系统性的全面进行改善,但需要结合实际状况分步骤分门别类的逐步改善进而达成阶段目标并最终实现总目标。
4.改善不能脱离现场。
所有数据必须现场测量,所有问题必须现场观察,充分与一线员工交流并亲身实践才能得出结论。
脱离现场,脱离实际,脱离基层员工,任何改善都只是纸上谈兵。
5.改善成果必须实现标准化,没有标准化的改善不是完美的改善。
6.精益生产的改善需要以人为本,全员参与。
只有全员参与,充分发挥人的主动性和能动性,改善才能处处开花。
7.改善是一个持续创新不断发现问题不断进步的过程。
没有最好,只有更好,持续改善,不断进步,这是丰田方式的精髓。
只有深深理解这一精髓,并将其作为企业文化融入到员工心中,才能够在精益生产的实践应用中取得长久发展。
二、实施方案指导框架结合企业自身实际状况,借鉴国内外的精益生产理论指导和实践案例研究,研究将精益生产的各钟软硬件技术进行分类,提出了新的改善模型,作为公司推行精益生产管理的指导框架。
改善模型称为新“TPS”模型,T代表技术(Technology ),P代表人员(Person ),S代表系统(System,如图4-1所示。
- 1、下载文档前请自行甄别文档内容的完整性,平台不提供额外的编辑、内容补充、找答案等附加服务。
- 2、"仅部分预览"的文档,不可在线预览部分如存在完整性等问题,可反馈申请退款(可完整预览的文档不适用该条件!)。
- 3、如文档侵犯您的权益,请联系客服反馈,我们会尽快为您处理(人工客服工作时间:9:00-18:30)。
精益之道一、精益核心:精益求精,持续改善;二、精益之道:依靠忠诚实干的员工,通过暴露问题,解决根因,消除浪费,持续改善,建立稳定连续的增值流程。
三、推行精益生产的几个基本问题:一、一个企业发展良好的原因在哪里?二、一个企业发展不好的原因在哪里?三、公司的核心理念是什么?企业存在的使命和目标是什么?四、公司推行精益生产的目的是什么?追求利润还是员工的福利?共同繁荣。
五、如何对待流程?依靠忠实的员工,暴露问题,持续改善,稳定持续增值的流程。
六、如何对待问题?如何对待员工的错误?暴露问题,持续改善。
七、如何看待员工和机器的关系?人使用机器;不能人成为机器的奴隶。
八、如何对待员工?平等、尊重、信任、理解、关怀、激励、鼓励。
九、当员工利益与公司利益冲突时,怎么来解决?改善&管理;共生共赢;十、领导者和员工之间是什么关系?利益?交换?雇佣?剥削?矛盾对立?建国君民,教学为先;师者,传道授业解惑也。
十一、公司如何看待员工的学习?员工为什么而工作?十二、若何落实企业的使命、价值、信念、宣言及目标?制度、文化及理念,如何支持实现精益?十三、企业需要精英还是耕耘者?十四、企业如何尊重员工?以问题教导员工思考,并让员工负责持续改善。
四、精益前提:如何才能成功实施精益生产?(一)高层的支持:决策、决心、危机。
愿力!!!竞争激烈、订单丢失、成本攀升、利润下降;(二)顾问的专业:战略、方向、计划。
智力!!!精益之道、现实调查、整套方案、推动有方;(三) 中层的配合:信心、行动、支持。
压力!!!高层的压力、顾问的推动、实践的成效、专业培训及理念教育;样板试行。
(四)基层的落实:兴趣、意愿、合作。
动力!!!学习长进、承担责任、积极动力、成效助兴;和合互助,集体力量。
信仰、价值观、责任感、主人翁精神。
(五) 核心人员的稳定:专业顾问、中层执行、基层行动。
(六) 专业培训及理念教育:IE&Lean、工具的应用、现场改善及培训;标杆参观。
(七) 扎实的基础:人才、文化、理念、意识、态度、责任、立场、方略;改善环境和氛围;士气和干劲。
(八) 企业的精益愿景及共同繁荣;(九) 领导的决心&理念;领导的德行管理及智慧教导;(十) 中层的积极执行及热情带动;(十一) 员工的改善才能及责任态度;(十二) 责任/立场/态度/理念/意识/文化→基础/环境/文化/资源→积极主动,思考问题,持续改善→指标达成。
五、鸟瞰精益:(一) 客户的要求:零缺陷的产品、准时顺序的交货、较低的价格、优质的服务;(二) 公司的目标:质量零缺陷(6Sigma/PPM/FPY)、低材料损耗率、短生产周期(L/T)、减少批量及库存(库存周转率)、提高效率(OEE/PCUR/)及增大产能(CPH)、降低成本(MPM、库存、WIP、单位产品综合成本)、提高交货达成率及交货准时率、财务指标(资金积占、净利率)、安全;士气;员工增值。
(三) 达成的途径:通过设立Supermarket运用Pull System,降低库存及保证供货顺序,Value Stream Mapping, 稳定的流程(流程、工艺、物流、质量、效率、产能),一个流(SMED减少批量,连续/流动/顺畅/平衡/均衡/稳定),标准化的生产(5S/WI/控制图),异常问题的显现(红箱子/VM/5S/Andon/Jidongka/Poke-Yoke),现场持续改善(QCC/Kaizen),人员的稳定及成长,意识理念态度责任的提高。
(四) 达成的方法:依靠忠实的员工持续逐步改善不间断的增值流程;改善,持续改善;改善即是管理;成员的共同努力精诚合作;精益工具的应用、IE手法的应用;质量控制手法的应用;六西格玛工具的应用;等。
六、基本认识:(一) 共同繁荣需要利润支持;利润来之于竞争优势(客户需要的产品:质量、成本、交货);竞争优势在于忠实员工的持续改善;员工的积极贡献来自于企业文化;企业文化在于老板的心量。
(二) 企业是员工和老板共同所有的;老板和员工不是对立关系,而是共赢。
企业是大家共同实现价值的修行道场。
企业经营是共同成长的过程。
员工不是被剥削的对象。
(三) 企业追求长期持续的发展,生产出好产品,必然需要稳定员工,需要提高员工的待遇、增长员工的能力,需要员工积极主动改善公司的问题。
吃饭问题,过道问题,---,无处不体现老板对员工的态度。
(四) 靠持续改善和卓越管理才能让企业取得盈利、让员工提高待遇。
(五) 如何对待问题?显现问题,暂停生产,迫使思考,分析根因,寻找方法,解决根本;不能拖延掩盖问题;不能被动消极地完成任务;不能得过且过。
(六) 减少浪费由人来实施,而不是对人来实施。
(七) 完成工作+深入思考解决问题增值流程。
(八) 塑优秀员工,造优质产品;制造产品之前,先培养人才;优秀员工制造优质产品。
(九) 只有人才能改善提高,才能促成企业长期发展。
改善是只有员工才能全面持续开展的。
员工是否有能力和有积极性进行持续改善?通过现场的实际问题,引导员工利用A3报告开展精益思考,让员工负责持续改善。
改善,学会改善,持续改善。
七、精益目的:(一) 企业:1. 谋求福祉;造福乡里;2. 创造价值;作出贡献;(二) 员工:1. 薪酬福利;发展机会;2. 实现自我;贡献价值;(三) 统一目标:共同繁荣;(四) 客户的核心价值;→企业的核心目的&核心流程;→VSM;→CI;→员工;→企业文化;(五) 为什么推行Lean?为谁而Lean?(六) 客户有什么需求/要求?客户需要的价值是什么?(七) 企业老板能为员工做些什么?(八) 员工能为企业做些什么?(九) 员工能为团队同事做些什么?八、如何落实全员参与?如何长期持续改善?(一) 4P:Philosophy、People、partner、Problem Solving;(二) 市场时势:竞争,残酷激烈;生存,岌岌可危;改善,势在必行;(三) 长期战略:公司愿景、存在价值、经营目标;(四) 稳定流程:依靠忠实的员工持续逐步改善不间断的增值流程、有机系统、VSM、SIPOC、KPI;(五) 扎实基础:人才团队、核心技术、竞争优势、盈利资金;(六) 企业文化:平等、尊重、信任、理解、关怀;珍惜;公平公正,正大光明;(七) 经营管理:人性管理;德行感召;上下一心;鼓励/激励/激发/调动;(八) 带动员工:共同工作、学习、改善、成长;学习型组织;(九) 理念教化:建国君民,教学为先;德行修养,以身作则;理念、意识、责任、态度、精神;境随心转:改善修行、传统文化、中医养生、人生启迪、觉悟知道;(十) 凝聚和合:成就感、成长感、欢喜感、认同感、归属感、责任感;(十一) 持续改善:压力、动力、责任、态度、精神;兴趣;实效;习惯&素养的养成;立场及行动的转变;持续学习&改善;(十二) 实施原则:整体效益、长期效果、根本改善;现场实际;产品、工艺、品种批量;(十三) 改善修行:正常/异常;善恶标准;直截了当,勇猛精进;精益求精,日正日新,日积月累,持之以恒;做有意义的事,做有价值的人,做有贡献的团队。
(十四) 精益文化:精进学习、积极改善、开心工作、幸福生活。
反思改过修行;学习型组织。
九、改善前后:(一) 超负荷(Mula)、不均衡/波动(Muda)、浪费/NVA(Muri);(二) 问题:断裂、搬运、批量、库存、排队、等待、失衡、过量;NVA、7Ws;(三) 目标:连续、流动、平衡、均衡、顺畅、稳定、拉动、一个流;依靠忠实的员工持续逐步改善不间断的增值流程;十、精益误区:(一)追求短期、局部、表面效果;急功近利、急于求成;全方面推进。
(二) 靠运动来推行,势必不能持久;忽视精益的根本的建立及基础的奠实;(三)设定推行目标,一味追求KPI;追求结果;像西医用指标了判定健康或生病,并不能从根本上治病;只是强制把指标符合;要像中医一样,从整体、精神气血、阴阳、经络、症证来诊治。
迫于上级压力,为达成KPI,完成任务,可以交差,被动消极。
将问题推给下游,拖延或掩藏问题的解决。
不是积极主动自觉自发的持续改善。
不是追求持续改善的不间断增值流程。
(四)靠权力驱使推行,而不是靠员工自动自发自觉进行持续改善;造成员工的抵触;(五)完全依靠专家的推动,人亡政息。
(六) 忽视员工的建议,打消员工的积极性,阻碍员工发挥主观能动性;(七) 为精益而精益,生搬硬套,削足适履;拿来主义;本本主义;形式主义。
(八) 为发挥工具而推行精益生产;不要像西医一样,拿药治病;要像中医一样先诊断后开方用药。
中医治人,西医用药。
六西格玛、逻辑规则、量化数据。
(九)追求技术及自动化设备,迷信系统(信息系统、财务系统、质量体系等);(十)忽视基础的坚实,期望一蹴而就;急于追求质变,要求立竿见影,不远耐心用心培植养育;(十一)追求利润;短期导向,快速回报;向外驰求;指望别人来帮助自己实现精益;十一、推行原则:(一)依靠忠实的员工持续逐步改善连续稳定的增值流程;(二)暂停流程,迫使问题显现并势必解决;(三)改革愿景;制定战略;明确方向;(四)建立支持;扎实基础;转变理念;(五)坚持原则;按部就班;有条不紊;(六)不裁员;不损害员工的利益;(七)长期、整体、根本;持续、恒久;(八)简单、便利;切實、合理、可行、有效;現場現地、实事求是;理论结合实际/實踐為本;在实干中学习和在现场中改善;PDCA;(九)带动员工共同参与:工作、学习、改善、提高;听取员工的意见;发挥员工的积极性及主观能动性;十二、领导者的工作:(一) 领导人的决心&态度&理念&意识;尽职尽责、尽心尽力、修炼德行、以身作则。
(二) 战略共识;(三) 稳定流程;(四) 成立精益生产部门,设立VSM Manager;(五) 使用A3报告推动精益价值流经理及一线员工,学会通过思考解决问题,持续改善,达成KPI目标;(六) 培养精益管理者:培训、教导;激励、鼓励;支持、带动;(七) 深入现场、注重过程、自我学习、持续改善;愿景导向、培育教导;十三、推进过程:(一)Launch:破产危机、订单丢失、成本压力、高层决策、领导明师、团队组建、计划进度、项目管理。
精益动员;标杆参观。
背景时势。
(二)Define: Product Family/Pareto Chart;VSM;VOC;CTQ;Key issues/Y,y1,y2,y3;NoneValue Add;7Ws;变异波动;主要问题。
(三)Measure: KPI,BSC,SIPOC,D、L/T、Q、C,Inventory、Product Capacity。
士气;现状分析。
目标设定。
(四)Analysis: QC7、SPC、鱼骨图、树状图,---,FMEA,2sample,DOE。