各种硅片不良的解决方案
硅片解决方案

硅片解决方案一、背景介绍硅片是一种用于制造集成电路的重要材料,其质量和性能直接影响到电子产品的稳定性和可靠性。
因此,提供一种高效、可靠的硅片解决方案对于电子行业来说至关重要。
二、问题描述目前存在以下几个问题需要解决:1. 硅片制造过程中的缺陷率较高,导致产品的质量不稳定。
2. 硅片的生产效率相对较低,无法满足市场需求。
3. 硅片的成本较高,影响了产品的竞争力。
三、解决方案为了解决以上问题,我们提出了以下硅片解决方案:1. 提高制造过程中的质量控制通过引入先进的质量控制技术,如光学检测和自动化控制系统,可以实时监测硅片制造过程中的缺陷,并及时采取纠正措施。
同时,建立完善的质量管理体系,对每一道工序进行严格监控,确保产品质量的稳定性。
2. 优化生产工艺,提高生产效率通过改进硅片的生产工艺,如优化材料配比、提高设备的自动化程度等,可以提高生产效率,缩短生产周期。
此外,合理安排生产计划,提前预测市场需求,避免产能闲置或供应不足的情况发生。
3. 降低成本,提高竞争力通过节约能源、优化原材料采购、提高设备利用率等方式,可以降低硅片的生产成本。
此外,与供应商进行合作,争取更有竞争力的价格和优惠条件,进一步降低成本。
降低硅片的成本可以提高产品的竞争力,使其更具吸引力。
四、预期效果通过以上硅片解决方案的实施,我们预期可以达到以下效果:1. 硅片的质量得到显著提升,缺陷率降低,产品质量更加稳定可靠。
2. 生产效率提高,生产周期缩短,能够更好地满足市场需求。
3. 硅片的成本降低,产品竞争力提升,市场份额增加。
五、实施计划为了有效实施硅片解决方案,我们制定了以下实施计划:1. 设立专门的项目组,负责方案的实施和监督。
2. 对硅片制造过程进行全面的分析和评估,确定存在的问题和改进的方向。
3. 寻找合适的供应商和合作伙伴,与其共同推动方案的实施。
4. 制定详细的实施计划和时间表,明确各项任务的责任人和完成时间。
5. 进行必要的培训和技术支持,确保方案的顺利实施和运行。
硅片水波纹缺陷
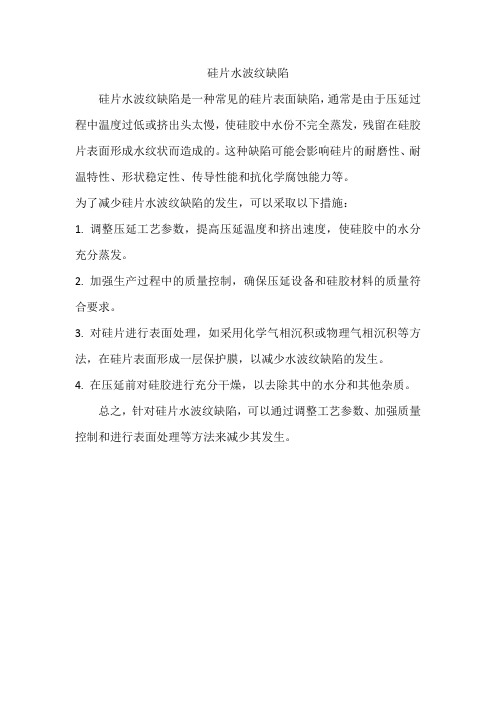
硅片水波纹缺陷
硅片水波纹缺陷是一种常见的硅片表面缺陷,通常是由于压延过程中温度过低或挤出头太慢,使硅胶中水份不完全蒸发,残留在硅胶片表面形成水纹状而造成的。
这种缺陷可能会影响硅片的耐磨性、耐温特性、形状稳定性、传导性能和抗化学腐蚀能力等。
为了减少硅片水波纹缺陷的发生,可以采取以下措施:
1. 调整压延工艺参数,提高压延温度和挤出速度,使硅胶中的水分充分蒸发。
2. 加强生产过程中的质量控制,确保压延设备和硅胶材料的质量符合要求。
3. 对硅片进行表面处理,如采用化学气相沉积或物理气相沉积等方法,在硅片表面形成一层保护膜,以减少水波纹缺陷的发生。
4. 在压延前对硅胶进行充分干燥,以去除其中的水分和其他杂质。
总之,针对硅片水波纹缺陷,可以通过调整工艺参数、加强质量控制和进行表面处理等方法来减少其发生。
硅片解决方案

硅片解决方案一、引言硅片是半导体行业中的关键材料,广泛应用于集成电路、光伏发电和电子器件等领域。
本文旨在提供一种针对硅片的解决方案,以解决目前在生产、质量控制和应用方面存在的问题。
二、生产方面的解决方案1. 材料选择:通过对硅片材料的研究和分析,选择高纯度、低杂质的硅材料作为原料,以确保硅片的质量和性能。
2. 制备工艺:采用先进的制备工艺,如Czochralski法和浮区法,以获得高质量的硅片。
同时,优化工艺参数,控制温度、压力和时间等因素,以提高硅片的晶体结构和表面平整度。
3. 检测设备:引入先进的硅片检测设备,如光学显微镜、扫描电子显微镜和X 射线衍射仪等,对硅片进行全面的检测和分析,以确保其质量符合标准要求。
三、质量控制方面的解决方案1. 检测方法:建立一套完整的硅片质量检测方法体系,包括外观检查、尺寸测量、电性能测试和物理性能测试等。
通过对硅片的多个方面进行综合检测,确保其质量和性能的稳定性。
2. 统计分析:采用统计学方法对硅片的质量数据进行分析,建立质量控制图和过程能力指数,及时发现和解决硅片生产过程中的异常情况,确保产品质量的稳定性和一致性。
3. 质量管理体系:建立完善的质量管理体系,包括质量手册、程序文件和工作指导书等,明确质量目标和责任,规范硅片的生产和质量控制流程,确保产品符合相关标准和客户要求。
四、应用方面的解决方案1. 封装技术:针对硅片在集成电路中的应用,研发先进的封装技术,如芯片封装、封装材料和封装工艺等,以提高芯片的可靠性和性能。
2. 光伏应用:针对硅片在光伏发电中的应用,研发高效的光伏电池技术,如多晶硅电池和单晶硅电池等,以提高光伏发电的效率和可持续性。
3. 电子器件应用:针对硅片在电子器件中的应用,研发新型的电子器件结构和工艺,如功率器件和传感器等,以满足不同领域对硅片的需求。
五、总结本文提供了一种针对硅片的解决方案,从生产、质量控制和应用三个方面进行了详细的阐述。
硅片存在的问题及解决方法

硅片厚薄不均原因分析
环境
地面共振
车间温湿度变化大 导向条质量
辅料
槽距不均匀 小滑轮槽 距不均匀 无 切片机张力 不稳定
人员
树脂导向条错位,未放过滤袋/过滤网
工件和托板/工件夹紧螺丝未拧紧
线径不均匀
使用搅拌时间不到的砂浆
厚薄不 均
砂浆配置比例 主辊/导轮质量问题
工艺设计不科学
二次切割程序
工艺入门
切片工艺是设备(包括设备状态和设备准备),切割材料和基于耗材的切 割条件的综合。为确保好的切割和保持尽可能高的收率,就必须认真对待 下面每一步。
设备准备 砂浆 操作人
收率
硅块
钢线
Page 1
不同工艺参数的影响
回收砂浆
悬浮液 硅片厚度 温度 砂子粒径 TTV
线痕
砂浆流量
进给速率 设备稳定性
钢线磨损度
Page 3
花污片原因分析
环境
超纯水
辅料
柠檬酸 草 酸 乳酸 责任心差
人员
不遵守时间
违规脱胶 违规清洗
回收液质量
清洗剂质量
酸的更换量
花污片
超声波衰减
清洗剂更换量 温控不准确 预冲洗喷淋管 堵塞
自来水压力泵 时间控制器
清洗剂PLC控制系统
工艺
仪器
机器
Page 4
花污片预防和返工措施
1. 切割液掺有次氯酸,特别是回收液,对硅片腐蚀特别严重。(请品管 部门分析切割 液的成分) 2. 预冲洗的水压(2.5MPa),水质(中水),流量(5000l/h),角度(10),冲洗时 间(30-40min)等,总之预冲洗要硅片表面无明显脏污,才能进入脱胶 3. 脱胶时尽量全泡,水温50-60℃,加3%的草酸或柠檬酸或乳酸,自然倒伏。 4. 脱胶插片完毕,25-30℃纯水中超声10分钟,超声功率在2000w左右,水要循环。 (插片槽改成具有超声功能) 5. 清洗剂(不同厂家)大部分都是重量比为5%的比例,温度设为60℃,超声3-5分钟。 6. 关键是员工有没有执行和我们提供的设备工具能否满足需要. 7. 如果是个老厂,突然出现花污片了一般要在辅料上找问题(切割液 清洗液 回收液等). 8. 更换时一定要用标准容器,更换量视故硅片规格和数量而定.一般6和6.5寸8000pcs全换 一次,4000pcs时更换一半. 9. 污片返工关键技术:直接经过两槽清洗剂槽,时间3分钟,两槽纯水槽5分钟;花片返工关键 技术:0.2%的氢氟酸100l纯水,浸泡1分钟,先过纯水,再过清洗剂槽。合格率极低。 另外也可采用快速极冷法物理剥离赃物和硅片。
硅片解决方案

硅片解决方案硅片解决方案是指针对硅片生产和应用中的问题提出的解决方案。
硅片是半导体制造过程中的关键材料,广泛应用于电子、光电子、太阳能等领域。
为了提高硅片的质量和生产效率,各种解决方案被提出和应用。
一、硅片生产解决方案1. 原材料选择:在硅片生产过程中,原材料的选择对最终产品的质量有重要影响。
优质的硅原料应具有高纯度、低杂质含量和均匀的晶体结构。
通过严格的原材料筛选和检测,确保生产过程中的杂质控制和晶体生长的均匀性。
2. 晶体生长技术:硅片的生长过程决定了其晶体结构和性能。
采用先进的晶体生长技术,如Czochralski法、浮区法等,可以获得高质量的硅片。
控制晶体生长的温度、压力和速度等参数,优化晶体生长过程,提高硅片的晶体质量和均匀性。
3. 切割和研磨技术:硅片在生产过程中需要进行切割和研磨,以获得所需的尺寸和表面质量。
采用高精度的切割和研磨设备,控制切割和研磨参数,可以实现硅片的精确尺寸和光滑表面。
4. 表面处理技术:硅片的表面处理对其后续工艺步骤和性能有重要影响。
采用化学腐蚀、氧化、涂覆等表面处理技术,可以改善硅片的表面质量、降低表面缺陷和提高其耐腐蚀性能。
二、硅片应用解决方案1. 半导体器件制造:硅片作为半导体器件的基底材料,广泛应用于集成电路、光电子器件、传感器等领域。
针对不同的半导体器件制造需求,提供定制化的硅片解决方案,包括不同尺寸、材质和表面特性的硅片供应。
2. 光伏发电系统:硅片是太阳能电池的核心材料,影响着太阳能电池的转换效率和稳定性。
通过优化硅片的结构和制造工艺,提高太阳能电池的光电转换效率,降低成本,推动光伏发电系统的应用和发展。
3. 光学器件制造:硅片在光学器件制造中具有重要作用,如光纤通信、激光器、光学传感器等。
通过精确的硅片加工和光学薄膜涂覆技术,提供高精度、高性能的光学器件解决方案,满足不同领域的应用需求。
4. 生物医学领域:硅片在生物医学领域的应用日益增多,如基因芯片、生物传感器等。
硅片解决方案

硅片解决方案一、引言硅片是集成电路制造中的关键材料之一,其质量和性能直接影响到芯片的可靠性和性能。
本文将介绍一种可行的硅片解决方案,以满足集成电路制造过程中对高质量硅片的需求。
二、背景在集成电路制造过程中,硅片是用于制造芯片的基础材料。
高质量的硅片能够提供更好的电性能和可靠性。
然而,目前市场上存在一些硅片质量不稳定、价格高昂的问题。
因此,寻找一种解决方案以提供高质量且成本效益高的硅片变得尤为重要。
三、解决方案基于市场需求和技术发展,我们提出以下硅片解决方案:1. 材料选择选择高纯度多晶硅作为硅片材料,其具有较低的杂质含量和较高的晶格完整性。
材料的高纯度可以提供更好的电学性能和可靠性,而晶格完整性则有助于减少晶体缺陷,提高硅片的质量。
2. 制备工艺采用先进的硅片制备工艺,如Czochralski法和区域熔融法。
这些工艺能够在保证硅片质量的同时提高生产效率。
制备过程中,需要严格控制温度、压力和杂质含量等参数,以确保硅片的均匀性和一致性。
3. 检测和筛选引入严格的硅片检测和筛选流程,以确保只有符合质量标准的硅片被用于芯片制造。
检测项目包括电学性能、晶体缺陷、杂质含量等。
通过使用高精度的测试设备和仪器,可以及时发现并淘汰不合格的硅片,提高生产效率和质量。
4. 质量控制建立完善的质量控制体系,包括从原材料采购到成品交付的全过程质量控制。
通过制定标准操作规程、设立质量检测点、实施质量记录和追溯,可以确保硅片的质量稳定性和可追溯性。
四、效益采用上述硅片解决方案可以带来以下效益:1. 提高芯片质量:高纯度硅片和严格的质量控制可以提供更好的电学性能和可靠性,从而提高芯片的质量和可靠性。
2. 降低成本:通过优化制备工艺和引入自动化设备,可以提高生产效率,降低生产成本。
3. 提高产能:高效的制备工艺和质量控制体系可以提高生产效率,增加硅片的产能。
4. 增强竞争力:提供高质量且成本效益高的硅片,可以帮助客户提升产品竞争力,拓展市场份额。
单晶硅片的整改措施
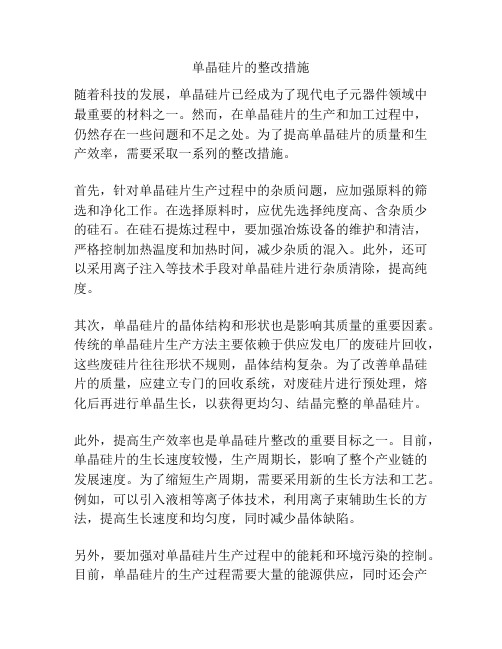
单晶硅片的整改措施随着科技的发展,单晶硅片已经成为了现代电子元器件领域中最重要的材料之一。
然而,在单晶硅片的生产和加工过程中,仍然存在一些问题和不足之处。
为了提高单晶硅片的质量和生产效率,需要采取一系列的整改措施。
首先,针对单晶硅片生产过程中的杂质问题,应加强原料的筛选和净化工作。
在选择原料时,应优先选择纯度高、含杂质少的硅石。
在硅石提炼过程中,要加强冶炼设备的维护和清洁,严格控制加热温度和加热时间,减少杂质的混入。
此外,还可以采用离子注入等技术手段对单晶硅片进行杂质清除,提高纯度。
其次,单晶硅片的晶体结构和形状也是影响其质量的重要因素。
传统的单晶硅片生产方法主要依赖于供应发电厂的废硅片回收,这些废硅片往往形状不规则,晶体结构复杂。
为了改善单晶硅片的质量,应建立专门的回收系统,对废硅片进行预处理,熔化后再进行单晶生长,以获得更均匀、结晶完整的单晶硅片。
此外,提高生产效率也是单晶硅片整改的重要目标之一。
目前,单晶硅片的生长速度较慢,生产周期长,影响了整个产业链的发展速度。
为了缩短生产周期,需要采用新的生长方法和工艺。
例如,可以引入液相等离子体技术,利用离子束辅助生长的方法,提高生长速度和均匀度,同时减少晶体缺陷。
另外,要加强对单晶硅片生产过程中的能耗和环境污染的控制。
目前,单晶硅片的生产过程需要大量的能源供应,同时还会产生大量的废气、废水和废弃物。
为了减少能源消耗和环境负荷,可以采用新能源和高效节能设备,同时加强废气、废水和废弃物的处理和利用。
最后,要提高单晶硅片的品质管理和质量控制水平。
建立完善的质量管理体系,从源头抓起,严格控制每一个生产环节的质量要求,避免次品和不合格品的产生。
加强对单晶硅片的检测和测试,采用先进的检测设备和技术手段,确保产品的质量符合标准要求。
总之,提高单晶硅片的质量和生产效率需要从多个方面进行整改和改进。
通过加强原料选材、改进生产工艺、增强质量管理和控制,以及减少能耗和环境污染等措施的综合应用,可以有效改善单晶硅片的质量,提高产能和降低成本,为电子元器件产业的发展做出贡献。
硅片解决方案

硅片解决方案一、背景介绍硅片是半导体行业中的关键材料,广泛应用于电子设备创造、太阳能光伏发电、光学器件等领域。
为了满足市场需求,提高生产效率和产品质量,需要制定一套完善的硅片解决方案。
二、市场分析1. 硅片市场规模:根据行业研究报告,全球硅片市场规模估计在2025年将达到3000亿美元。
2. 硅片应用领域:硅片广泛应用于集成电路、光伏发电、光学器件等领域,其中集成电路市场占领主导地位。
3. 市场竞争格局:目前硅片市场竞争激烈,主要厂商有美光科技、英特尔、三星电子等。
三、问题分析1. 生产效率低下:传统的硅片创造过程中存在生产效率低下的问题,无法满足市场需求。
2. 能源消耗大:硅片创造过程中需要大量的能源,对环境造成不可忽视的影响。
3. 产品质量不稳定:传统创造工艺容易导致硅片产品质量不稳定,影响产品的可靠性和寿命。
四、解决方案1. 创造工艺优化:通过优化硅片创造工艺,提高生产效率,减少生产成本。
例如,引入先进的自动化设备和智能控制系统,提高生产线的自动化水平,减少人工操作,提高生产效率。
2. 节能减排:引入节能环保的创造工艺,减少能源消耗和废弃物排放。
例如,采用先进的能源回收技术,将废热转化为电能,降低能源消耗;同时,加强废水处理和废气处理,减少对环境的污染。
3. 质量控制提升:引入先进的质量控制技术,提高硅片产品质量的稳定性和一致性。
例如,建立完善的质量管理体系,加强原材料的筛选和检测,优化生产过程中的质量控制点,确保每一片硅片的质量符合标准要求。
4. 创新研发:加大对硅片创造技术的研发投入,提升核心竞争力。
例如,开展新材料的研究,探索新的硅片创造工艺,提高硅片的性能和可靠性。
5. 合作共赢:与供应商、客户和研究机构建立密切的合作关系,共同推动硅片解决方案的研发和应用。
通过共享资源和技术,实现互利共赢。
五、实施计划1. 确定目标:明确硅片解决方案的目标和关键指标,如提高生产效率10%,降低能源消耗20%,提高产品质量合格率到99%等。
硅片解决方案
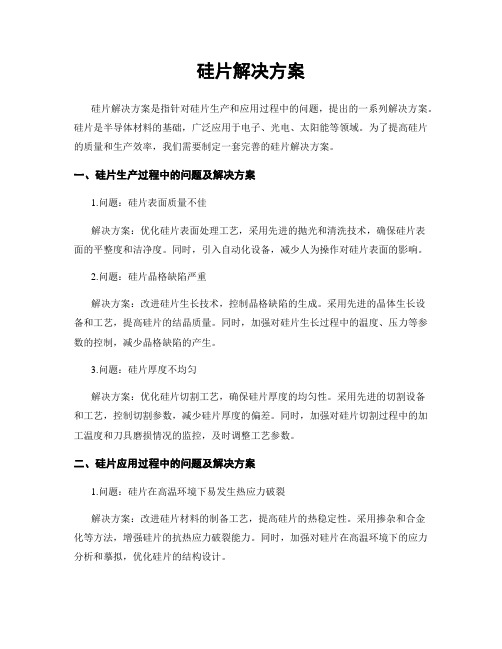
硅片解决方案硅片解决方案是指针对硅片生产和应用过程中的问题,提出的一系列解决方案。
硅片是半导体材料的基础,广泛应用于电子、光电、太阳能等领域。
为了提高硅片的质量和生产效率,我们需要制定一套完善的硅片解决方案。
一、硅片生产过程中的问题及解决方案1.问题:硅片表面质量不佳解决方案:优化硅片表面处理工艺,采用先进的抛光和清洗技术,确保硅片表面的平整度和洁净度。
同时,引入自动化设备,减少人为操作对硅片表面的影响。
2.问题:硅片晶格缺陷严重解决方案:改进硅片生长技术,控制晶格缺陷的生成。
采用先进的晶体生长设备和工艺,提高硅片的结晶质量。
同时,加强对硅片生长过程中的温度、压力等参数的控制,减少晶格缺陷的产生。
3.问题:硅片厚度不均匀解决方案:优化硅片切割工艺,确保硅片厚度的均匀性。
采用先进的切割设备和工艺,控制切割参数,减少硅片厚度的偏差。
同时,加强对硅片切割过程中的加工温度和刀具磨损情况的监控,及时调整工艺参数。
二、硅片应用过程中的问题及解决方案1.问题:硅片在高温环境下易发生热应力破裂解决方案:改进硅片材料的制备工艺,提高硅片的热稳定性。
采用掺杂和合金化等方法,增强硅片的抗热应力破裂能力。
同时,加强对硅片在高温环境下的应力分析和摹拟,优化硅片的结构设计。
2.问题:硅片在光电器件中易发生光衰减解决方案:改进硅片的光学特性,提高硅片的光传输效率。
采用表面纳米结构化和光学涂层等技术,增强硅片的光吸收和光耦合能力。
同时,加强对硅片光学性能的测试和评估,确保硅片在光电器件中的稳定性和可靠性。
3.问题:硅片在太阳能电池中的转化效率低解决方案:改进硅片的太阳能转化效率,提高太阳能电池的发电能力。
采用多晶硅和单晶硅等高效硅片材料,优化硅片的能带结构和电子传输性能。
同时,加强对硅片太阳能电池的工艺流程和参数的优化,提高硅片的光电转换效率。
以上是关于硅片解决方案的一些内容,通过优化硅片生产工艺和改进硅片材料性能,可以提高硅片的质量和应用效果。
光伏电池片外观不良解决方案
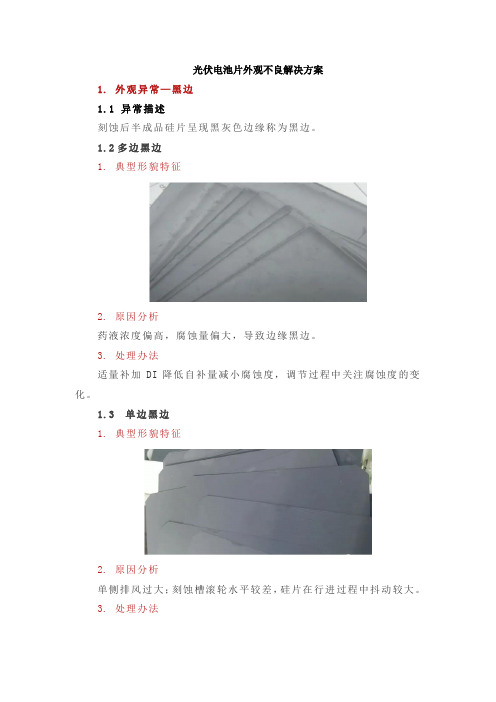
光伏电池片外观不良解决方案1. 外观异常—黑边1.1 异常描述刻蚀后半成品硅片呈现黑灰色边缘称为黑边。
1.2多边黑边1. 典型形貌特征2. 原因分析药液浓度偏高,腐蚀量偏大,导致边缘黑边。
3. 处理办法适量补加DI降低自补量减小腐蚀度,调节过程中关注腐蚀度的变化。
1.3 单边黑边1. 典型形貌特征2. 原因分析单侧排风过大;刻蚀槽滚轮水平较差,硅片在行进过程中抖动较大。
3. 处理办法适当降低黑边背侧排风;观察找出偏高或偏低的滚轮,调节滚轮水平。
1.4 边角黑边1. 典型形貌特征2. 原因分析单根滚轮不平,一边高一边低会导致偏低的一侧边角出现黑边;侧面排风过大;3. 处理办法观察找出不平的滚轮,调节滚轮水平;根据黑边出现的方位,调节侧排。
1.5 黑边原因分析总结1. 药液浓度偏高,腐蚀量偏大,导致边缘黑边;2. 刻蚀槽滚轮水平较差,硅片在行进过程中抖动较大;3. 侧面排风过大。
1.6 黑边处理办法总结1. 适量补加DI降低自补量减小腐蚀度,调节过程中关注腐蚀度的变化。
2. 观察找出偏高或偏低的滚轮,调节滚轮水平;3. 根据黑边出现的方位,调节侧排。
2. 外观异常—滚轮印2.1 异常描述刻蚀后或在EL图中出现与刻蚀滚轮位置一致的印记称为滚轮印。
2.2 典型形貌特征:2.3 原因分析1. 刻蚀槽流量偏低,背面部分N型硅未被刻蚀掉;2. 进槽滚轮偏高,硅片接触药液时间偏短;3.上下滚轮脏污,脏污粘在硅片表面。
2.4 处理办法1. 如果滚轮印出现在非扩散面,可以适当增加刻蚀槽流量来解决;2. 调节进槽滚轮高度;3. 如果脏污情况较轻,可以通过跑假片的方法来去除;如果脏污情况较严重,可以将所有槽药液打至Tank槽,用酒精擦拭除刻蚀槽外所有滚轮,再用DI水擦拭,最后跑假片复机即可。
3. 外观异常—皮带印3.1 异常描述在EL图中出现皮带印位置与刻蚀皮带印宽度一致称为皮带印。
3.2 典型形貌特征:3.3 原因分析1. 电池片正面与下料机下料皮带进行摩擦接触,在EL缺陷分选检测出与刻蚀下料皮带对应的皮带印;2. 电池片在皮带传送过程中因摩擦力较小容易与皮带产生打滑,导致电池片与皮带接触打滑区域受损导致电池片与皮带接触位置EL不良。
硅片解决方案

硅片解决方案一、背景介绍硅片是半导体创造中的重要组成部份,它被广泛应用于电子产品、太阳能电池等领域。
为了提高硅片的创造效率和质量,需要针对硅片的加工、测试、封装等环节提供解决方案。
二、硅片加工解决方案1. 切割技术硅片的切割是创造过程中的关键步骤,常用的切割技术包括线切割和激光切割。
线切割是一种传统的切割方法,适合于硅片的大规模生产。
激光切割则具有高精度和高效率的优势,适合于对硅片进行精细加工。
2. 表面处理技术硅片的表面处理对于提高其质量和性能至关重要。
常见的表面处理技术包括化学机械抛光(CMP)、氧化、薄膜沉积等。
CMP技术可以去除硅片表面的不平整和污染物,使其表面更加光滑。
氧化技术可以形成硅片表面的氧化层,提高硅片的电学性能。
薄膜沉积技术则可以在硅片表面形成各种功能性薄膜,满足不同应用的需求。
3. 掺杂技术硅片的掺杂是为了改变其导电性能和光学性能。
常用的掺杂技术包括扩散法、离子注入法等。
扩散法是通过将掺杂物加热到高温,使其在硅片中扩散,改变硅片的导电性能。
离子注入法则是通过将掺杂物注入到硅片中,形成掺杂层,改变硅片的光学性能。
三、硅片测试解决方案1. 电学测试电学测试是对硅片导电性能的检测,常用的测试方法包括电阻测试、电容测试等。
电阻测试可以测量硅片的电阻值,判断其导电性能是否正常。
电容测试则可以测量硅片的电容值,判断其绝缘性能是否正常。
2. 光学测试光学测试是对硅片光学性能的检测,常用的测试方法包括透光率测试、反射率测试等。
透光率测试可以测量硅片对光的透过程度,判断其透光性能是否正常。
反射率测试则可以测量硅片对光的反射程度,判断其反射性能是否正常。
四、硅片封装解决方案1. 封装材料硅片的封装需要使用材料来保护硅片并提供电气连接。
常用的封装材料包括塑料、陶瓷、金属等。
塑料封装具有成本低、分量轻等优势,适合于大规模生产。
陶瓷封装具有高温耐受性和抗腐蚀性,适合于高性能应用。
金属封装具有良好的散热性能,适合于高功率应用。
各种不良硅片的表现形式及改善方法
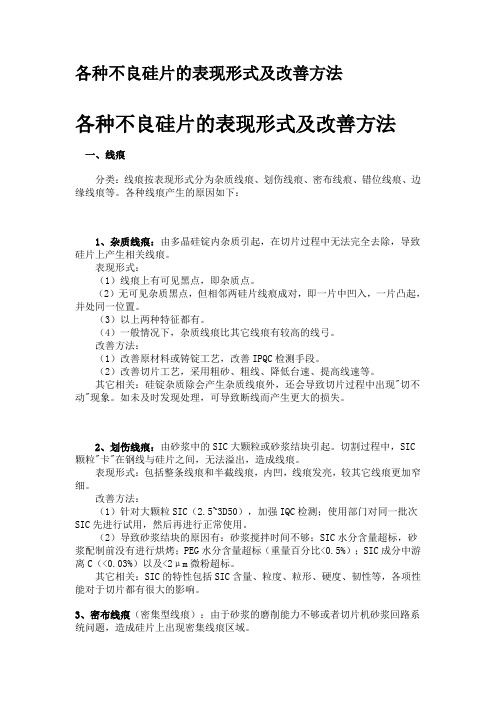
各种不良硅片的表现形式及改善方法各种不良硅片的表现形式及改善方法一、线痕分类:线痕按表现形式分为杂质线痕、划伤线痕、密布线痕、错位线痕、边缘线痕等。
各种线痕产生的原因如下:1、杂质线痕:由多晶硅锭内杂质引起,在切片过程中无法完全去除,导致硅片上产生相关线痕。
表现形式:(1)线痕上有可见黑点,即杂质点。
(2)无可见杂质黑点,但相邻两硅片线痕成对,即一片中凹入,一片凸起,并处同一位置。
(3)以上两种特征都有。
(4)一般情况下,杂质线痕比其它线痕有较高的线弓。
改善方法:(1)改善原材料或铸锭工艺,改善IPQC检测手段。
(2)改善切片工艺,采用粗砂、粗线、降低台速、提高线速等。
其它相关:硅锭杂质除会产生杂质线痕外,还会导致切片过程中出现"切不动"现象。
如未及时发现处理,可导致断线而产生更大的损失。
2、划伤线痕:由砂浆中的SIC大颗粒或砂浆结块引起。
切割过程中,SIC 颗粒"卡"在钢线与硅片之间,无法溢出,造成线痕。
表现形式:包括整条线痕和半截线痕,内凹,线痕发亮,较其它线痕更加窄细。
改善方法:(1)针对大颗粒SIC(2.5~3D50),加强IQC检测;使用部门对同一批次SIC先进行试用,然后再进行正常使用。
(2)导致砂浆结块的原因有:砂浆搅拌时间不够;SIC水分含量超标,砂浆配制前没有进行烘烤;PEG水分含量超标(重量百分比<0.5%);SIC成分中游离C(<0.03%)以及<2μm微粉超标。
其它相关:SIC的特性包括SIC含量、粒度、粒形、硬度、韧性等,各项性能对于切片都有很大的影响。
3、密布线痕(密集型线痕):由于砂浆的磨削能力不够或者切片机砂浆回路系统问题,造成硅片上出现密集线痕区域。
表现形式:(1)硅片整面密集线痕。
(2)硅片出线口端半片面积密集线痕。
(3)硅片部分区域贯穿硅片密集线痕。
(4)部分不规则区域密集线痕。
(5)硅块头部区域密布线痕。
硅片解决方案

硅片解决方案一、背景介绍硅片是半导体行业中非常重要的材料之一,广泛应用于电子设备、太阳能电池、光电器件等领域。
然而,硅片制造过程中存在一些技术难题,如晶圆质量控制、晶圆表面处理等,需要找到解决方案来提高生产效率和产品质量。
二、解决方案一:晶圆质量控制晶圆质量是影响半导体器件性能和可靠性的重要因素。
为了解决晶圆质量控制的问题,可采取以下措施:1. 引入先进的晶圆检测设备:利用高分辨率显微镜、电子显微镜等设备对晶圆进行全面检测,以确保晶圆表面没有缺陷、杂质等问题。
2. 优化晶圆生产工艺:通过改进晶圆生产工艺,减少晶圆制造过程中的缺陷产生,提高晶圆的质量稳定性。
3. 引入智能化质量控制系统:利用人工智能和大数据技术,建立晶圆质量控制系统,实时监测晶圆制造过程中的关键参数,及时发现和修正问题,提高晶圆质量。
三、解决方案二:晶圆表面处理晶圆表面处理是硅片制造过程中的关键环节,直接影响晶圆的电性能和可靠性。
为了解决晶圆表面处理的问题,可采取以下措施:1. 清洗工艺优化:通过改进清洗工艺,提高清洗效率和清洗质量,确保晶圆表面没有杂质和污染物。
2. 引入新型表面处理技术:如等离子体增强化学气相沉积(PECVD)、离子注入等技术,提高晶圆表面的平整度和纯净度。
3. 引入自动化表面处理设备:利用自动化设备,实现晶圆表面处理的自动化和高效化,提高生产效率和一致性。
四、解决方案三:晶圆回收利用在硅片制造过程中,会产生一定数量的废弃晶圆,为了减少资源浪费,可采取晶圆回收利用的解决方案:1. 晶圆切割和拼接技术:通过切割废弃晶圆并将其拼接成新的晶圆,实现晶圆的再利用。
2. 晶圆材料回收技术:利用化学方法、物理方法等技术,将废弃晶圆中的硅材料回收再利用。
3. 环保意识培养:加强对员工的环保意识培养,提高废弃晶圆的回收利用率。
五、解决方案四:晶圆生产过程优化为了提高硅片制造过程的效率和质量,可采取以下解决方案:1. 自动化生产线:引入自动化设备和机器人技术,实现晶圆生产过程的自动化和高效化。
硅片解决方案

硅片解决方案一、背景介绍硅片是半导体材料中最重要的基础材料之一,广泛应用于电子、光电子、太阳能等领域。
然而,硅片的制备过程中存在着一些技术难题,例如晶体生长、切割、抛光等环节,需要寻找解决方案以提高生产效率和产品质量。
二、晶体生长解决方案1. 材料选择:选择高纯度的硅原料,确保晶体生长过程中的杂质含量低,提高晶体质量。
2. 晶体生长技术:采用Czochralski法(CZ法)或区熔法(FZ法)进行硅晶体生长。
CZ法适用于大尺寸晶体生长,而FZ法适用于高纯度硅晶体的生长。
3. 控制晶体生长条件:通过控制温度、气氛、溶液成分等参数,优化晶体生长过程,降低晶体缺陷密度。
三、硅片切割解决方案1. 切割工艺选择:常用的硅片切割工艺包括线锯切割、内切割和磨割切割。
根据不同的应用需求选择合适的切割工艺。
2. 切割工艺优化:通过改变切割参数(如切割速度、切割深度等),优化切割过程,提高切割效率和切割质量。
3. 切割工具选择:选择高质量的切割工具,如金刚石线锯片、切割盘等,确保切割过程中的切割质量和硅片表面质量。
四、硅片抛光解决方案1. 抛光工艺选择:常用的硅片抛光工艺包括机械抛光和化学机械抛光(CMP)。
根据不同的应用需求选择合适的抛光工艺。
2. 抛光液配方优化:通过调整抛光液的成分和浓度,优化抛光过程中的材料去除效果和表面平整度。
3. 抛光设备选择:选择高精度的抛光设备,如双面抛光机、CMP机等,确保抛光过程中的抛光质量和硅片表面质量。
五、硅片质量检测解决方案1. 表面缺陷检测:利用光学显微镜、扫描电子显微镜等设备对硅片表面进行检测,判断是否存在缺陷,如划痕、裂纹等。
2. 晶体缺陷检测:利用X射线衍射、拉曼光谱等技术对硅片晶体结构进行分析,检测晶体缺陷,如晶界、位错等。
3. 电学性能检测:利用电子测试仪器对硅片的电学性能进行测试,如电阻、电容等参数。
六、总结通过以上的硅片解决方案,可以有效提高硅片的生产效率和产品质量,满足不同领域对硅片的需求。
硅片解决方案

硅片解决方案硅片解决方案是指针对硅片生产过程中的各种问题提供的解决方案。
硅片是半导体材料中最为重要的基础材料之一,广泛应用于集成电路、光伏发电、光电器件等领域。
在硅片生产过程中,可能会遇到晶圆质量不稳定、晶圆表面缺陷、晶圆切割不均匀等问题,这些问题会严重影响硅片的质量和性能,因此需要针对这些问题提供解决方案。
一、晶圆质量不稳定的解决方案晶圆质量不稳定是指在硅片生产过程中,晶圆的厚度、杂质浓度、晶格缺陷等参数存在较大波动,导致硅片的性能不稳定。
为了解决这个问题,可以采取以下措施:1. 优化晶圆生长工艺:通过调整生长温度、生长速率、气氛控制等参数,优化晶圆的生长过程,提高晶圆的质量稳定性。
2. 引入晶圆质量监测系统:在生产线上引入晶圆质量监测系统,实时监测晶圆的厚度、杂质浓度等参数,及时发现并修正异常情况,确保晶圆质量的稳定性。
3. 加强工艺控制:建立完善的工艺控制体系,对生产过程中的各个环节进行严格控制,确保每一批晶圆的质量稳定。
二、晶圆表面缺陷的解决方案晶圆表面缺陷是指晶圆表面存在的各种缺陷,如划痕、氧化、污染等,这些缺陷会降低硅片的质量和性能。
为了解决这个问题,可以采取以下措施:1. 引入表面处理技术:采用化学机械抛光、离子注入、溅射等表面处理技术,去除晶圆表面的缺陷层,提高晶圆表面的平整度和光洁度。
2. 引入清洁工艺:建立完善的晶圆清洁工艺,对晶圆进行彻底的清洁,去除表面的污染物,减少晶圆表面缺陷的产生。
3. 引入自动化检测系统:在生产线上引入自动化检测系统,对晶圆表面进行快速、准确的检测,及时发现并修复表面缺陷,提高硅片的质量。
三、晶圆切割不均匀的解决方案晶圆切割不均匀是指在硅片生产过程中,晶圆的切割厚度存在较大偏差,导致硅片的尺寸不一致,影响产品的可靠性和一致性。
为了解决这个问题,可以采取以下措施:1. 优化切割工艺:通过调整切割速度、切割深度、刀具材料等参数,优化切割工艺,提高硅片切割的精度和一致性。
硅片解决方案
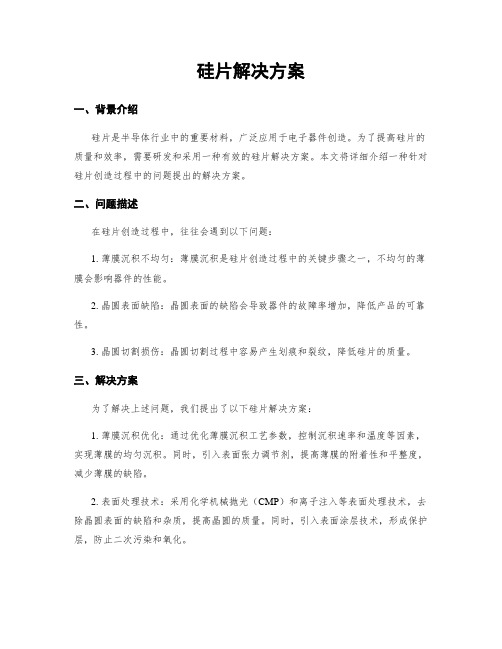
硅片解决方案一、背景介绍硅片是半导体行业中的重要材料,广泛应用于电子器件创造。
为了提高硅片的质量和效率,需要研发和采用一种有效的硅片解决方案。
本文将详细介绍一种针对硅片创造过程中的问题提出的解决方案。
二、问题描述在硅片创造过程中,往往会遇到以下问题:1. 薄膜沉积不均匀:薄膜沉积是硅片创造过程中的关键步骤之一,不均匀的薄膜会影响器件的性能。
2. 晶圆表面缺陷:晶圆表面的缺陷会导致器件的故障率增加,降低产品的可靠性。
3. 晶圆切割损伤:晶圆切割过程中容易产生划痕和裂纹,降低硅片的质量。
三、解决方案为了解决上述问题,我们提出了以下硅片解决方案:1. 薄膜沉积优化:通过优化薄膜沉积工艺参数,控制沉积速率和温度等因素,实现薄膜的均匀沉积。
同时,引入表面张力调节剂,提高薄膜的附着性和平整度,减少薄膜的缺陷。
2. 表面处理技术:采用化学机械抛光(CMP)和离子注入等表面处理技术,去除晶圆表面的缺陷和杂质,提高晶圆的质量。
同时,引入表面涂层技术,形成保护层,防止二次污染和氧化。
3. 切割工艺优化:通过优化晶圆切割工艺参数,如切割速度、切割角度等,减少切割过程中的损伤。
同时,引入切割液和切割刀具的优化,提高切割的精度和平整度。
四、方案优势我们的硅片解决方案具有以下优势:1. 提高硅片质量:通过优化工艺参数和引入新技术,可以有效地提高硅片的质量,降低缺陷率,提高产品可靠性。
2. 提高生产效率:优化工艺参数和引入新技术可以提高生产效率,减少生产成本,提高市场竞争力。
3. 环保节能:我们的解决方案采用环保材料和工艺,减少对环境的污染,降低能源消耗。
五、应用案例我们的硅片解决方案已成功应用于多个硅片创造企业,并取得了显著的效果。
例如,某硅片创造企业在采用我们的解决方案后,硅片的缺陷率从10%降低到了2%,产品的可靠性得到了大幅提升。
六、总结通过我们提出的硅片解决方案,可以有效地解决硅片创造过程中的问题,提高硅片的质量和效率。
硅片解决方案

硅片解决方案概述:硅片是半导体行业中的重要组成部分,广泛应用于电子产品制造和太阳能发电等领域。
硅片解决方案是指针对硅片制造过程中的技术和工艺进行优化和改进,以提高硅片的质量和生产效率,降低成本,并满足客户的需求。
一、硅片制造工艺硅片制造过程主要包括单晶硅生长、切割、抛光和清洗等步骤。
在单晶硅生长阶段,通过化学气相沉积或单晶生长炉等设备,将硅原料转化为单晶硅棒。
然后,通过切割机将单晶硅棒切割成薄片,形成硅片。
接下来,对硅片进行抛光处理,以去除表面缺陷和杂质。
最后,对硅片进行清洗,以确保表面的纯净度。
二、硅片解决方案的关键技术和工艺1. 单晶硅生长技术:采用先进的化学气相沉积技术,控制气氛组成、温度和压力等参数,以实现高纯度、低缺陷的单晶硅生长。
同时,优化晶体生长速度和晶体结构,提高硅片的晶体质量和均匀性。
2. 切割技术:采用先进的切割机设备,结合高精度切割刀具,实现硅片的高效切割。
同时,优化切割参数,减少切割损失和切割缺陷,提高硅片的利用率和质量。
3. 抛光技术:采用高精度的抛光机设备,结合优化的抛光液体配方,实现硅片表面的高效抛光。
同时,控制抛光时间和压力等参数,减少表面缺陷和杂质,提高硅片的光洁度和平整度。
4. 清洗技术:采用先进的清洗设备,结合优化的清洗液体配方,实现硅片表面的高效清洗。
同时,控制清洗时间和温度等参数,去除硅片表面的有机和无机杂质,提高硅片的纯净度和可靠性。
三、硅片解决方案的优势和应用1. 提高硅片质量:通过优化硅片制造工艺和技术,减少表面缺陷和杂质,提高硅片的晶体质量和光洁度。
从而,提高半导体器件的性能和可靠性。
2. 提高生产效率:通过优化硅片制造工艺和设备,提高生产线的自动化程度和生产效率。
从而,降低生产成本,提高生产能力和产能利用率。
3. 降低成本:通过优化硅片制造工艺和材料选择,降低硅片的制造成本。
从而,提高企业的竞争力和盈利能力。
4. 广泛应用:硅片解决方案广泛应用于半导体行业、太阳能行业、光电子行业等领域。
硅片等级和硅片出现问题解决方案

硅片等级和硅片出现问题解决方案硅片等级分类及标准一、优等品1:硅片表面光滑洁净。
2:TV:220±20μm。
3:几何尺寸:边长125±0.5mm;对角150±0.5mm、148±0.5mm、165±0.5mm;边长103±0.5mm、对角135±0.5mm;边长150±0.5mm 、156±0.5mm、对角203±0.5mm、200±0.5mm。
同心度:任意两个弧的弦长之差≤1mm。
垂直度:任意两边的夹角:90°±0.3。
二、合格品一级品:1:表面有少许污渍、轻微线痕。
2:220±20μm ≤TV≤220±30μm。
3:几何尺寸:边长125±0.5mm;对角150±0.5mm、148±0.5mm、165±0.5mm;边长103±0.5mm、对角135±0.5mm;边长150±0.5mm 、156±0.5mm、对角203±0.5mm、200±0.5mm。
同心度:任意两个弧的弦长之差≤1.2mm。
垂直度:任意两边的夹角:90°±0.5。
二级品:1:表面有少许污渍、线痕、凹痕,轻微崩边。
2:220±30μm ≤TV≤220±40μm。
3:凹痕:硅片表面凹痕之和≤30μm。
4:崩边范围:崩边口不是三角形状,崩边口长度≤1mm,深度≤0.5mm 5:几何尺寸:边长125±0.52mm;对角150±0.52mm、148±0.52mm、165±0.52mm;边长103±0.52mm、对角135±0.52mm;边长150±0.52mm 、156±0.52mm、对角203±0.52mm、200±0.52mm。
- 1、下载文档前请自行甄别文档内容的完整性,平台不提供额外的编辑、内容补充、找答案等附加服务。
- 2、"仅部分预览"的文档,不可在线预览部分如存在完整性等问题,可反馈申请退款(可完整预览的文档不适用该条件!)。
- 3、如文档侵犯您的权益,请联系客服反馈,我们会尽快为您处理(人工客服工作时间:9:00-18:30)。
断线善后处理首先做好断线记录(断线时间、机台号、部位、切深)留好线头一.查明断线原因及断线情况.二.急时上报,未经同意,不得私自处理。
三.处理流程:1.在出线端断线,宽度不超过10毫米的直接拉线切割.2.切深≦60mm中部或进线端断线,以30mm/min直接升起,迅速布线,8000流量砂浆冲洗,冲片时在线网上铺上无尘纸,冲开粘在一起的片子后,迅速把晶棒降到距线网2mm处,然后以10mm/min的进给认真仔细的“认刀”。
3.中部或进线端断线,切深在50mm---80mm之间的,以10mm/min的速度升料到距进刀处30--40毫米,,停止。
线速调到2m/s,以2%走线1cm,以调平线网,停止。
打开砂浆8000流量均匀冲片子。
把晶棒两侧的线网小心的剪掉(剪时要用手捏着),留出3-4厘米的线头,另一端不剪.(进线端有线网的一定要保留该部分线网,以便重新布线.剪两侧线网时一定要用手或其他夹紧物,夹紧预留的线网头.)布线网,重新切割。
4进线端或中部断线切深超过80mm的视情况能认刀的就认刀否则就反切或直接拉线正向切割。
4.进线端断线,第一次断线,切深在80mm.1换掉放线轮,用一个空的收线轮来代替。
以低于原2N(左19和右21)的张力,切割线方向改为:右,其他参数不变,手动2m/s的线速走1m,不要开砂浆。
2把晶棒提升至30---40mm处,重新对接焊线,焊线时要焊接均匀,焊接点的点径要和线径相同。
经15N的线速走线300——400米,改张力为自动切割的张力,每秒1米,不开沙浆,走到出线端5米时,把张力改为15N,待线头在收线轮上绕2——3圈,改回原来的张力。
把晶棒压到断线位置误差在0.05mm,打开砂浆。
以1m/s 速度的20%,走上1m,经班长确认无误后进行切割。
5.经上环节中必须处理好线网(其中包括,碎片、胶条、沙浆颗粒)在升晶棒前,把胶条去掉,上升速度为每分钟10mm,上升过程中如夹线,不可用手去摸,只能用手动轻微探摁一下,把线网走平。
6.认线前5m/s的速度走线100m,在不松开张力的情况下,停止走线,然后以10mm/min认刀,要一次性认进。
7.反向切割设置修改:进给降低1个百分点,线速降低1M/S,流量增加300KG/H。
8.线头编号方法:年+月+日+机台号+第几次断线数.例如:080501-20-019.请工序稽查人员按照此标准做巡检崩边问题问题点:粘胶面崩边异常现象:脱胶后,在方棒两头的硅片粘胶面呈现边沿发亮,硅层呈线式脱落崩边, 及距粘胶面0.1mm处线式崩边。
脱胶和清洗时观察不到崩边,检验时能发现崩边。
原因分析:一.开方进给不稳,外圆刀锯转速不稳,刀锯金刚砂层质量不好,造成刀痕过重,方棒表面刀纹不平,凹凸起伏,隐型损伤(指的是锯开方)线开方损伤可忽略二.方棒温度低,胶在凝固时的高温反应热,破坏了粘胶面的硅层结构三.硅片预冲洗水温低于XX度,脱胶水温低于XX度,胶层未完全软化时员工就用手把硅片用力作倒。
四.由于采用的是小槽距大线径,不可避免会在出刀时造成硅片向阻力小的一方的倾斜,方棒两头的硅片受到的阻力最小,造成两个棒子四个头部近32毫米长度内的硅片出现崩边。
五.粘接剂太硬(不便说出硬度系数),在钢线出硅棒粘胶面的瞬间,破坏了硅层。
预防措施:一.脱胶,经过控制脱胶的规范操作,即使前道工序已经对方棒表面产生不良影响,经过优化粘胶方式和手法,也要把损失降低到最低点。
在目前的设备配置前提下,严格要求脱胶工“45~50 度温水,浸泡25分钟”联系设备部,做硅片隔条,降低硅片倒伏时的倾度。
二.严格控制方棒超声池的水温在40度,超声到粘胶的时间间隔控制在2小时内,粘胶房的温度控制在25度,湿度不超过50%。
三.对开方机进行一次进给和转速校正,开方后的方棒经打磨后再滚圆。
并请设备部做出设备三级维护计划书。
做定期维护保养四.“分线网”硅片切割:方棒两头各留出2mm不切割,减少切割过程中硅片向两侧“分叉”另外一种办法:做一个可调试挡板系统,挡住方棒两头,防止硅片“分叉”崩边。
五,采用线开方和磨面机,有条件的最好腐蚀一下。
更换粘接力强但硬度适中的粘接剂善后处理:磨砂玻璃和1700#碳化硅按一定的水分比例选择某种手势,力度,角度磨掉在边长要求范围内的崩边(标准作业指导书)硅片厚薄不均预防措施一.T V偏大或偏小:根据客户要求片厚,计算出最佳成本/质量的槽距,钢线,碳化硅,砂浆密度。
二.TTV》15um的硅片占比超过0.62%,属于异常。
对于一次切割的单位,应增加导向条(部位不提供),两次切割的单位最好把导轮(主辊)槽距改一下或第二次切割时砂浆流量增大500公斤/小时(5l/min)或多更换20公斤砂浆。
三.硅片的进刀处的进线端(角)偏薄或偏厚,应修改进刀时的砂浆流量四:同一个硅片的厚度呈大-小-大-小分布的,应调整切割工艺程序。
进给,线速,流量应均匀同步变化。
五,跳线引起的某刀硅片厚度异常,同一个片的厚度异常,不同片子的厚度偏差等,因通过加过滤网/过滤袋/振荡过滤器和切割前仔细过滤,没有跳线来消除。
线痕5m1e分析花污片分析:一.切割液掺有次氯酸,特别是回收液.对硅片腐蚀特别严重.(请品管部门分析切割液的成分)2.预冲洗的水压,水质,流量,角度,冲洗时间等,总之预冲洗要硅片表面无明显赃污,才能进入脱胶3.脱胶时尽量全泡,水温50-60℃,加3%的草酸或柠檬酸或乳酸,自然倒伏.4.脱胶完毕后,25~30℃纯水中超声10分钟,超声功率在2000w左右水要循环.5.清洗剂(不同厂家)大部们都是重量比为5%的比例,温度设为60℃,超声5分钟.6.关键是员工有没有执行和我们提供的设备工具能否满足需要.\7.如果是个老厂,突然出现花污片了一般要在辅料上找问题(切割液清洗剂回收砂等.)8.更换时一定要用标准容器,更换量视故硅片规格和数量而定我们这次碰到的结果发现花污提取物中含有超过3%Fe,由于在线切过程中大量带进Fe的只会是刚线本身的磨损,所以可以看出,硅片经过脱胶清洗之后,仍然残留Fe,就是残余砂浆在作祟。
Fe本身在切割液环境中是出于还原气氛,所以相对稳定,但是在脱胶的时候,接触的是60度左右的水,这是一个氧化的环境,金属氧化物非常容易与残余的碳氢键形成共价物粘附于硅表面,难以清洗。
一种是将整轴钢线进多次切割,每次为单向切割,这种工艺我们使用在NTC机型上;一种是一段线进行多次切割,这种工艺我们使用在MBDS264机型上。
钢线有两个参数,一个是椭圆度,一个是磨损量。
你可以从这两个方面考虑,钢线经过一次切割后会磨损变形,这是多次切割就会对硅片表面造成影响。
单向切割表面粗糙度一般在5微米内,双向切割表面粗糙度会增加3——5倍。
线网断线:我的定义:拉伸强度超出了钢线的极限拉伸强度,造成拉伸断裂。
分析问题的方法:人、机、料、法、环。
人、机、法、环:广度较大,我不做分析。
料:硅料、浆料硅料:分单晶和多晶。
切割过程中,我认为硅棒对钢线的作用主要是力的作用,径向的压力(工件平台始终向下运动),摩擦力(阻碍钢线横向移动);浆料:切割过程中,我认为浆料对钢线的伤害是很大的,也存在很多不确定因素。
主要表现为磨损,降低钢线的极限拉升强度。
综上,硅棒对钢线的作用力越大,浆料对钢线的磨损越严重(极限拉伸强度越小),钢线越易断线。
注:多晶比单晶易断线,因为多晶存在晶界,晶界的组成很复杂,由于硬度等关系,对钢线的作用力是变化,瞬间超出极限拉伸强度的可能性较大。
浆料中杂质较多,颗粒不均匀,钢线断线的几率也会提高断线主要分布在1、收放线部分。
1-1、滑轮磨损过大或被割穿,这个时候也许不会断线!但是钢线会缠在滑轮上!所以滑轮品质的稳定性非常重要。
1-2、钢丝的磨损过大也容易引起收线端断线。
1-3、象楼上的兄弟所定义:拉伸强度超出了钢线的极限拉伸强度,造成拉伸断裂。
所以滑轮的材质要选对,不能太硬。
利用软件系统记录每一次切片的详细数据,比如说:整个切片过程中机器的各种参数及其变化曲线、浆料信息、以及前段工艺中有关硅块结晶情况等等。
将这些数据与切片的结果关联起来,做成一个庞大的数据库。
这个数据库,就是宝贵的专家经验。
接着这样做:系统自动比对前段工艺中的硅块的品质信息,线切机最近的运行状态,钢线的使用次数、磨损量,装载的浆料的成分品质信息、回收次数等等。
然后找出以前的切片中与之最匹配、切片效果最佳的配方设定点,线速、线弓大小、力度等等。
钢线。
如果钢线的椭圆度差的话,也会出现线痕。
比如片子上整体比较干净,但是在某个高度时出现单道线痕,而且是所有片子在同一个高度出现。
在切割过程中,大家经常会遇到各种问题,谨就大家经常认为是碳化硅微粉造成的影响以及硅片表面线痕问题探讨如下:1. 硅片表面偶尔出现单一的一条阴刻线(凹槽)或一条阳刻线(凸出),并不是由于碳化硅微粉的大颗粒造成的,而是单晶硅、多晶硅在拉制或浇筑过程中出现的硬质点造成线网波动形成的;2. 硅片表面在同一位置带有线痕,很乱且不规则,我认为是导轮或机床震动过大或者是多晶硅铸锭的大块硬质点造成的;3. 重启机床后第一刀出现线痕——机床残留水分或液体,造成砂浆粘度低,钢线粘附碳化硅微粉量下降,切削能力降低。
4. 调整新工艺、更换新型耗材后出现线痕:①砂、液比例不合适,或液体粘度太大,造成砂浆粘度太大或太小,砂浆难以进入线缝或碳化硅含量较低。
②碳化硅切割能力差,无法与切割速度相适应。
③钢线圆度不好,进入锯缝砂浆量不稳定。
④钢线的张力太大或太小,造成钢线携带砂浆能力差或线弓太小砂浆无法正常进入锯缝。
⑤钢线速度过快或过慢,造成砂浆无法粘附或切割效率下降,影响切割效果。
⑥各参数适配性差。
5. 硅片切割到某一段出现偏薄或偏厚的废片,分界非常明显,一般是由于跳线引起的,跳线的原因:①导轮使用时间太长,严重磨损引起的跳线。
②砂浆的杂质进入线槽引起的跳线。
③导轮表面脏污。
④晶棒端面从切割开始到切割结束依次变长,造成钢线受侧向力而跳出槽外。
⑤晶棒存在硬质点,造成钢线偏移距离过大跳出槽外。
线痕业内在拣片工序大致可分以下几类:(由轻到重)1。
摩擦线痕:清洗后由片子相互摩擦产生,可能是由于清洗不净或表层脱离引起2。
亮线痕:钢线摩擦硅片产生的白色线痕,就是你说的线印3。
突起状线痕,也就是常说的线痕:应该是由于跳线或切削力不足或晶体硬质点引起的4。
轻微划伤,轻而短的未贯串的划伤:大颗粒或碎硅片引起的短划伤5。
划痕,贯串整个片子较深的划伤,易从划伤处产生裂片:单晶较少出现,多晶主要由硬质点、晶界或微晶引起。