全尾砂高浓度充填技术规程
金属矿山全尾砂胶结充填胶凝材料技术要求

金属矿山全尾砂胶结充填胶凝材料技术要求1 范围本标准规定了金属矿山全尾砂胶结充填胶凝材料的分类和标记、组分与材料、强度等级、技术要求、试验方法、检验规则和包装、标志、运输与贮存要求。
本标准适用于金属矿山全尾砂充填胶结材料。
2 规范性引用文件下列文件对于本文件的应用是必不可少的。
凡是注日期的引用文件,仅所注日期的版本适用于本文件。
凡是不注日期的引用文件,其最新版本(包括所有的修改单)适用于本文件。
GB50771 有色金属采矿设计规范GB175 通用硅酸盐水泥GB/T1596 用于水泥和混凝土中的粉煤灰GB/T18046 用于水泥和混凝土中的粒化高炉矿渣粉GB/T20491 用于水泥和混凝土中的钢渣粉GB/T1345 水泥细度检验方法(筛析法)GB/T1346 水泥标准稠度用水量、凝结时间、安定性检验方法(GB/T 1346-2001,eqv ISO 9597:1989)GB/T2419 水泥胶砂流动度测定方法GB/T17671 水泥胶砂强度检测方法(ISO法)(GB/T17671-1999,idt ISO679:1989)GB/T2847 用于水泥中的火山灰质混合材料3 术语和定义下列术语和定义适用于本标准。
3.1全尾矿full tailing选矿分选作业的产物,有用目标组分含量较低而无法用于生产,且未经粒径分级的部分称为全尾矿。
33.2胶结充填backfill将选矿分选产生的尾矿砂浆,掺入适量的胶凝材料,搅拌制成胶结充填料桨,将料浆回填到采空区,胶结形成一定强度的、整体的充填体,此工艺过程称为胶结充填。
3.3胶凝材料cementing material以具有潜在水硬特性的物料、激活物料、其它功能性辅料混合制成的具有水硬性的、用于矿山胶结充填的混合材料称为胶凝材料。
3.4收缩率shrinkage ratio刚制备好的浆体体积与浆体固化脱模后的体积差与原体积的比。
3.5坍落度slump坍落度是指充填浆体的和易性,具体来说就是充填浆体的保水性、流动性和粘聚性的综合表现形式。
全尾砂胶结充填实验方案

1 实验目的本次试验通过采用尾砂和水泥等作为充填骨料,测试充填试块的固结特性、强度指标等,以检测充填体是否满足回采强度和相关工艺要求,以此确定金鑫金矿实验采空区回采残矿要求的充填材料及其控制参数等。
2 取样本次试验根据实验目的,主要采用的试验材料为尾砂、水泥以及水等。
为了符合实际,本次试验所用尾砂从金鑫金矿现场获取,托运至实验室进行试验,可确保所得数据与矿山实际相符。
具体材料包括以下几种:(1)骨料原料:主要为选矿全尾砂。
(2)胶结材料:普通32.5水泥。
(3)水:采用自来水。
4、主要试验内容根据试验目的,确定本次试验主要内容为:1)尾砂物理力学性质及化学成分测定(1)测定金鑫金矿尾砂原料的物理力学性能,主要包括比重、容重、含水率、孔隙率、自然安息角和渗透系数等;(2)测定并分析尾砂的化学成分;(3)测定尾砂的粒级组成;(4)测定尾砂的压缩系数和压缩模量。
2)充填料配比试验(1)尾砂添加水泥后的固结特性研究,选取至少2个不同浓度和3个不同灰砂比的组方进行试验(2)根据试验结果推荐尾砂充所需的充填材料配比参数。
4、技术指标和参数试验得到以下指标和参数:(1)尾砂原料的基本物理力学参数,主要包括比重、含水率、密度、孔隙率、休止角和渗透系数等;(2)尾砂的粒级组成;(3)各组方充填料的比重、含水率等;(4)不同养护龄期(7d、28d、60d)下的各组方的充填体单轴抗压强度、弹性模量等;(5)充填体不同养护龄期(7d、28d、60d)劈裂强度,计算其内摩擦角和粘结力,并绘制莫尔应力圆。
5 试验方法和方案本实验主要是在对尾砂进行物理力学性能测定和化学成分分析的基础上,选择不同充填配比进行室内充填体试块制作,测定其养护期为7d、28d、60d充填体单轴抗压强度和典型试块的7d、28d、60d劈裂强度,绘制摩尔圆,并求解内摩擦角及粘结力。
在得到以上物理化学性质分析结果和强度试验等结果后,对其进行技术经济分析,推荐尾砂材料充填所需的充填材料配比参数。
尾砂充填工安全技术操作规程
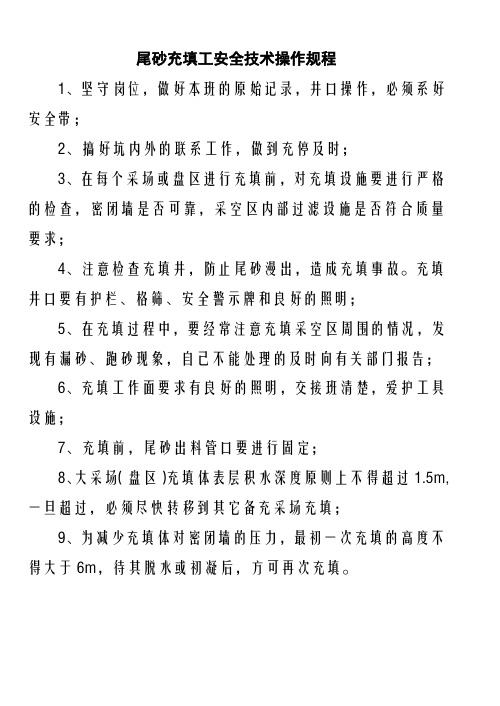
尾砂充填工安全技术操作规程
1、坚守岗位,做好本班的原始记录,井口操作,必须系好安全带;
2、搞好坑内外的联系工作,做到充停及时;
3、在每个采场或盘区进行充填前,对充填设施要进行严格的检查,密闭墙是否可靠,采空区内部过滤设施是否符合质量要求;
4、注意检查充填井,防止尾砂漫出,造成充填事故。
充填井口要有护栏、格筛、安全警示牌和良好的照明;
5、在充填过程中,要经常注意充填采空区周围的情况,发现有漏砂、跑砂现象,自己不能处理的及时向有关部门报告;
6、充填工作面要求有良好的照明,交接班清楚,爱护工具设施;
7、充填前,尾砂出料管口要进行固定;
8、大采场(盘区)充填体表层积水深度原则上不得超过1.5m,一旦超过,必须尽快转移到其它备充采场充填;
9、为减少充填体对密闭墙的压力,最初一次充填的高度不得大于6m,待其脱水或初凝后,方可再次充填。
巡墙工作业程序
1、保持通讯线路畅通完好。
进入工作面后,首先用电话向制备站联系后,方可正常充填。
2、充填盘区及相邻盘区密闭工作面,要备有足够的堵漏工具(木楔、麻布、棕等)。
3、巡视过程中,发现岩隙、滤水设施漏砂要及时处理,并根据需要,向制备站联系停止放砂或向工区报告漏砂的情况。
4、巡墙工作要两人同时进行,所经过的路线要注意浮石,车辆来往、溜井。
到相邻盘区要注意电扒运行、爆破作业,并注意检查平台、梯子是否牢固,杜绝工伤事故的发生。
全尾砂胶结充填井下作业安全操作规程

全尾砂胶结充填井下作业安全操作规程1. 背景全尾砂胶结充填是一种常见的井下作业方式,主要用于井下空洞和裂缝的加固,以及减少地面上下沉和沉降等问题。
在进行全尾砂胶结充填作业时,必须遵守安全操作规程,以确保安全高效完成作业任务。
2. 前期准备2.1 安全培训在进行全尾砂胶结充填井下作业之前,所有参与作业的人员都必须接受安全培训,了解井下作业的安全操作规程,并掌握必要的安全技能和知识。
安全培训内容包括:•作业流程和方法•作业安全要求和操作规程•紧急情况的处理方法和应急预案2.2 风险评估进行全尾砂胶结充填井下作业之前,必须进行风险评估,分析可能产生的危险和风险,并制定相应的措施进行防范和控制。
风险评估内容包括:•作业环境的评估和分析•作业过程中可能产生的危险和风险•防范和控制措施的制定和实施计划2.3 作业准备在进行全尾砂胶结充填井下作业之前,必须进行充分的作业准备,包括:•检查工具和设备的完好性和可靠性•确认作业场地的安全状态•制定作业方案和时间表•分配作业人员和工作任务3. 作业操作规程3.1 作业流程全尾砂胶结充填井下作业的基本流程包括:•准备工作,包括设备和工具的准备、场地检查和工作人员的安排•确认作业空间的安全状态,包括空气质量、地质条件、天气等•将铁骨架和模板部件运输至作业车厢,进行组装和调整•混合胶结剂和尾砂,并将其输送至作业车厢•将胶结剂和尾砂从作业车厢输送至井下作业点,并进行注入和压实•检查作业效果和安全状态,撤离作业现场3.2 安全决策在进行全尾砂胶结充填井下作业时,必须进行安全决策,包括:•作业前必须检查作业现场的安全情况和空气质量•定期监测作业现场的安全状况和空气质量•遇到异常情况时,必须立即中止作业,并采取相应的安全措施•在作业过程中,必须经常进行沟通和协调,确保作业人员的安全和作业效率3.3 作业选择在进行全尾砂胶结充填井下作业时,必须选取合适的工具和设备,并确保其完好可靠:•选择适合井下作业的铁骨架和模具等辅助工具和设备•选择合适的胶结剂和尾砂,并进行混合和调配•选择合适的运输方式和输送设备,确保胶结剂和尾砂输送的准确性和安全性3.4 安全保障在进行全尾砂胶结充填井下作业时,必须采取必要的安全保障措施,包括:•提供足够的通风装备、照明设备、应急装备和安全设备•保障作业人员的安全,制定作业时长和休息时间规范•采取遏制断电、救援措施和应急预案等措施4. 作业结束4.1 工作检查在全尾砂胶结充填井下作业结束后,必须进行工作检查,包括:•检查作业现场的安全状态和空气质量•检查模具、铁骨架等装备的完好性和可靠性•检查胶结剂和尾砂的使用情况和剩余量•检查作业效果和安全情况4.2 设备清理和维护全尾砂胶结充填井下作业结束后,必须进行设备清理和维护,包括:•清理作业车厢和设备,包括模具、铁骨架的清洁和消毒•检查设备的可靠性和安全性•给予设备保养和维护,保证下次作业顺利进行4.3 文档记录全尾砂胶结充填井下作业结束后,必须对作业过程和结果进行记录和整理,包括:•作业性质和用途•作业人员名单和工作表现•安全情况、事故及其处理情况•作业合理化提出档案5.全尾砂胶结充填井下作业是一项安全生产关键作业,必须遵循一定的安全操作规程和要求。
高浓度全尾砂自流胶结充填
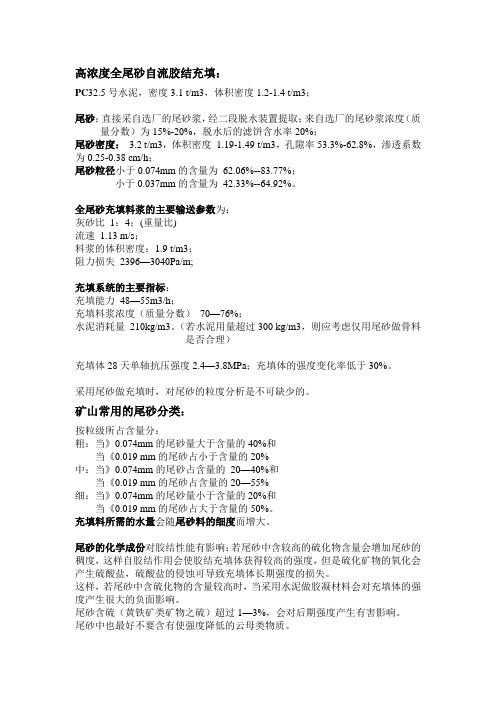
高浓度全尾砂自流胶结充填:PC32.5号水泥,密度3.1 t/m3,体积密度1.2-1.4 t/m3;尾砂:直接采自选厂的尾砂浆,经二段脱水装置提取;来自选厂的尾砂浆浓度(质量分数)为15%-20%,脱水后的滤饼含水率20%;尾砂密度:3.2 t/m3,体积密度 1.19-1.49 t/m3,孔隙率53.3%-62.8%,渗透系数为0.25-0.38 cm/h;尾砂粒径小于0.074mm的含量为62.06%--83.77%;小于0.037mm的含量为42.33%--64.92%。
全尾砂充填料浆的主要输送参数为:灰砂比1:4;(重量比)流速1.13 m/s;料浆的体积密度:1.9 t/m3;阻力损失2396—3040Pa/m;充填系统的主要指标:充填能力48—55m3/h;充填料浆浓度(质量分数)70—76%;水泥消耗量210kg/m3。
(若水泥用量超过300 kg/m3,则应考虑仅用尾砂做骨料是否合理)充填体28天单轴抗压强度2.4—3.8MPa;充填体的强度变化率低于30%。
采用尾砂做充填时,对尾砂的粒度分析是不可缺少的。
矿山常用的尾砂分类:按粒级所占含量分:粗:当》0.074mm的尾砂量大于含量的40%和当《0.019 mm的尾砂占小于含量的20%中:当》0.074mm的尾砂占含量的20—40%和当《0.019 mm的尾砂占含量的20—55%细:当》0.074mm的尾砂量小于含量的20%和当《0.019 mm的尾砂占大于含量的50%。
充填料所需的水量会随尾砂料的细度而增大。
尾砂的化学成份对胶结性能有影响:若尾砂中含较高的硫化物含量会增加尾砂的稠度,这样自胶结作用会使胶结充填体获得较高的强度,但是硫化矿物的氧化会产生硫酸盐,硫酸盐的侵蚀可导致充填体长期强度的损失。
这样,若尾砂中含硫化物的含量较高时,当采用水泥做胶凝材料会对充填体的强度产生很大的负面影响。
尾砂含硫(黄铁矿类矿物之硫)超过1—3%,会对后期强度产生有害影响。
全尾砂膏体充填技术试验研究与设计.
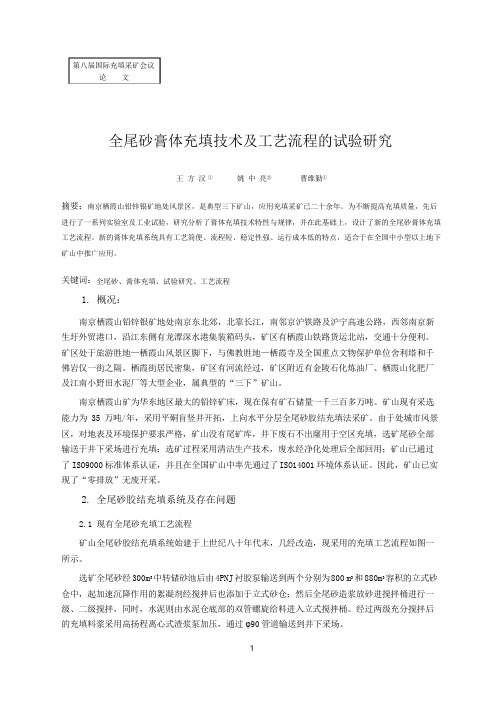
第八届国际充填采矿会议论文全尾砂膏体充填技术及工艺流程的试验研究王方汉①姚中亮②曹维勤①摘要:南京栖霞山铅锌银矿地处风景区,是典型三下矿山,应用充填采矿已二十余年。
为不断提高充填质量,先后进行了一系列实验室及工业试验,研究分析了膏体充填技术特性与规律,并在此基础上,设计了新的全尾砂膏体充填工艺流程。
新的膏体充填系统具有工艺简便、流程短、稳定性强、运行成本低的特点,适合于在全国中小型以上地下矿山中推广应用。
关键词:全尾砂、膏体充填、试验研究、工艺流程1.概况:南京栖霞山铅锌银矿地处南京东北郊,北靠长江,南邻京沪铁路及沪宁高速公路,西邻南京新生圩外贸港口,沿江东侧有龙潭深水港集装箱码头,矿区有栖霞山铁路货运北站,交通十分便利。
矿区处于旅游胜地—栖霞山风景区脚下,与佛教胜地—栖霞寺及全国重点文物保护单位舍利塔和千佛岩仅一街之隔。
栖霞街居民密集,矿区有河流经过,矿区附近有金陵石化炼油厂、栖霞山化肥厂及江南小野田水泥厂等大型企业,属典型的“三下”矿山。
南京栖霞山矿为华东地区最大的铅锌矿床,现在保有矿石储量一千三百多万吨。
矿山现有采选能力为35万吨/年,采用平硐盲竖井开拓,上向水平分层全尾砂胶结充填法采矿。
由于处城市风景区,对地表及环境保护要求严格,矿山没有尾矿库,井下废石不出窿用于空区充填,选矿尾砂全部输送于井下采场进行充填;选矿过程采用清洁生产技术,废水经净化处理后全部回用;矿山已通过了ISO9000标准体系认证,并且在全国矿山中率先通过了ISO14001环境体系认证。
因此,矿山已实现了“零排放”无废开采。
2.全尾砂胶结充填系统及存在问题2.1现有全尾砂充填工艺流程矿山全尾砂胶结充填系统始建于上世纪八十年代末,几经改造,现采用的充填工艺流程如图一所示。
选矿全尾砂经300m3中转储砂池后由4PNJ衬胶泵输送到两个分别为800m3和880m3容积的立式砂仓中,起加速沉降作用的絮凝剂经搅拌后也添加于立式砂仓;然后全尾砂造浆放砂进搅拌桶进行一级、二级搅拌,同时,水泥则由水泥仓底部的双管螺旋给料进入立式搅拌桶。
磷矿高浓度全尾砂充填技术研究
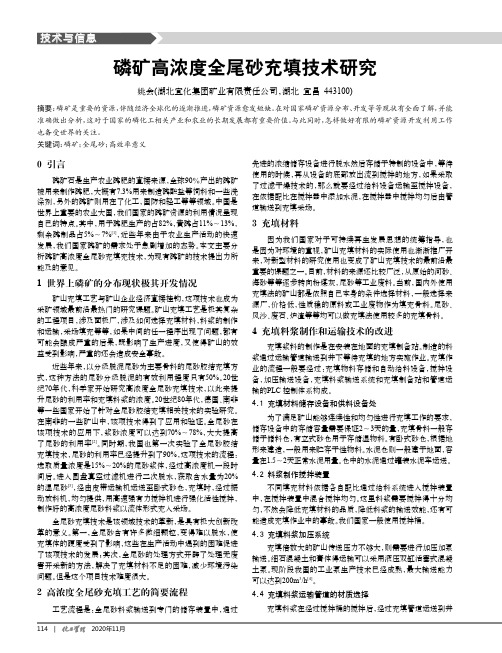
先进的浓缩储存设备进行脱水然后存储于特制的设备中,等待使用的时候,再从设备的底部放出流到搅拌的地方,如果采取了过滤干燥技术的,那么就要经过给料设备运输至搅拌设备,在依据配比在搅拌器中添加水泥,在搅拌器中搅拌均匀后由管道输送到充填采场。
3 充填材料因为我们国家对于可持续再生发展思想的统筹指导,也是因为对环境的重视,矿山充填材料的实际使用也渐渐推广开来,对新型材料的研究使用也变成了矿山充填技术的最前沿最重要的课题之一。
目前,材料的来源还比较广泛,从原始的河砂、海砂等等逐步转向粉煤灰,尾砂等工业废料。
当前,国内外使用充填法的矿山都是依照自己本身的条件选择材料,一般选择来源广,价格低,性质稳的原料或工业废物作为填充骨料。
尾砂、风沙、废石、炉渣等等均可以做充填法使用较多的充填骨料。
4 充填料浆制作和运输技术的改进充填浆料的制作是在安装在地面的充填制备站。
制造的料浆通过运输管道输送到井下等待充填的地方实施作业。
充填作业的流程一般要经过:充填物料存储和自动给料设备,搅拌设备,加压输送设备,充填料浆输送系统和充填制备站和管道运输的PLC 控制体系构成。
4.1 充填材料储存设备和供料设备处为了满足矿山能够连续性和均匀性进行充填工作的要求,储存设备中的存储容量需要保证2~3天的量,充填骨料一般存储于储料仓,有立式砂仓用于存储湿物料。
有卧式砂仓,根据地形来建造,一般用来贮存干性物料。
水泥仓则一般建于地面,容量在1.5~2天正常水泥用量。
仓中的水泥通过罐装水泥车运送。
4.2 料浆制作搅拌装置不同填充材料依据各自配比通过给料系统进入搅拌装置中,在搅拌装置中混合搅拌均匀。
这里料浆需要搅拌得十分均匀,不然会降低充填材料的品质,降低料浆的输送效能,还有可能造成充填作业中的事故。
我们国家一般使用搅拌桶。
4.3 充填料浆加压系统充填倍数大的矿山传送压力不够大,则需要进行加压加泵输送。
细石混凝土和膏体得运输可以采用液压双缸活塞式混凝土泵。
金属矿山高浓度及膏体细尾砂充填技术一、技术类型金属矿山高效

金属矿山高浓度及膏体细尾砂充填技术一、技术类型金属矿山高效采矿技术。
二、适用范围矿山开采,尾矿综合利用、回填与干堆等。
三、技术内容(一)基本原理将不同粒度和性质的尾砂分离开来,分别采取不同的脱水方式,选用不同的脱水设备,以提高整体的脱水效果和降低生产成本;深锥浓密机脱水工艺技术在传统的深锥浓密机基础上进行合理化改造,增加了底流浓度的稳定性和可靠性;充填料均匀搅拌设备及控制技术采用专用的高效和节能搅拌设备进行搅拌,通过软件模拟批量生产工艺过程进行控制,达到各种充填物料的高度均匀和连续制备的目的,减少了充填灰砂比。
(二)关键技术低成本细尾砂脱水及控压助流技术;尾砂分级脱水技术;深锥浓密机脱水工艺技术;充填料均匀搅拌设备及控制技术;充填料满管输送技术;充填采场工艺技术。
(三)工艺流程根据控压助流的技术原理,通过采用中国恩菲的专利脱水装置或采用分级脱水技术、深锥浓密机脱水工艺技术,将细粒级尾砂(-20μm全尾砂可占40%以上)直接低成本地制备成高浓度(74%以上)料浆或膏体从脱水装置底部排出,可以再适当添加水泥、粉煤灰、炉渣等搅拌混合均匀后,通过管道自流或泵送设备输送至井下采矿区或地表尾矿堆场,以达到提高采矿回收率和资源综合利用的目的。
尾砂分级脱水示意图四、主要技术指标对于极细粒级的全尾砂(-20μm全尾砂约占40%以上)直接制备成高浓度(74%以上)砂浆,解决了传统立式砂仓充填工艺存在的上述缺点。
底流尾砂浓度为74%-80%;流量可达到50-200m3/h。
采用此工艺技术用于充填可使采矿回收率达到90%-97%左右。
五、典型实例及成效崇礼紫金矿业有限责任公司,采矿能力2500t/d,充填站及输送系统总投资约2943.08万元,建设周期1年,投资回收期1年,使以前不能回采的残矿得以回收,矿山服务年限得以有效延长,采矿回收率提高约15%以上;减少地表尾矿排放量约60%,年增加经济效益超过2000万元。
冬瓜山铜矿充填系统,建设规模10000t/d, 占地面积1600m2,总投资11600万元,运行费用约3800万元/年,综合利用效益4363万元/年,投资回收年限为4年,开采回采率提高8%以上。
全尾砂高浓度充填技术规程

全尾砂高浓度连续充填技术规程目录全尾砂 (1)高浓度连续充填技术规程 (1)一、充填前期准备 (3)1. 地表系统 (3)2. 井下充填设施 (3)3. 其他准备 (3)二、全尾砂充填料浆制备工序技术规程 (3)1. 范围 (3)2. 术语 (4)3. 技术规程 (4)4. 尾砂进料 (5)5. 放砂及充填料浆制备 (5)6. 停车顺序 (8)一、充填前期准备1.地表系统1.1.尾砂输送泵房设备、仪表、管线、阀门、事故放空池等检查与维护;1.2.尾砂输送管线巡查,检查管线是否正常;1.3.絮凝剂制备设备、仪表、流量泵、管线、阀门检查与维护;1.4.充填搅拌站内设备、仪表、管线、阀门、控制系统检查与维护;1.5.尾砂进料管线、放砂管、溢流管及药剂(絮凝剂等)管线检查;1.6.水泥添加系统检查;1.7.地表通讯设施检查与维护;1.8.搅拌机械、电器设备、进出口阀门检查与维护;1.9.高压水源、常压水源供给情况检查;1.10.压气设备检查与维护。
2.井下充填设施2.1.井下通讯设施检查与维护;2.2.采场底部结构、充填挡墙检查及渗漏治理;2.3.充填主管路管线检查、安全检查及隐患处理。
3.其他准备3.1水泥30t,絮凝剂~200kg;3.2对讲机4个,手电筒2个,浓度壶2个(不锈钢),电子秤1台(精度1g),取样勺一个(手柄长~1.5m),简易手持砂面料位计(用20m皮尺绑重块制作)。
二、全尾砂充填料浆制备工序技术规程1.范围本规程规定了全尾砂高浓度充填料制备工序的基本准则,具体细节可根据实际情况酌情调整。
本规程适用于尾矿胶结充填站充填料浆制备工序。
2.术语下列术语和定义适用于本规程:2.1.高浓度尾砂胶结充填:指将选矿厂产出的尾砂浆体浓缩至一定浓度(如68%~72%)以上,与一定比例的胶结材料混合搅拌制备均匀后通过管路回填至井下采空区的过程和作业;2.2.灰砂比:指尾砂胶充填作业中胶结材料与尾砂干量的质量比(如1:6);2.3.活化:指为了使得砂仓浓密(压缩)后的高浓度顺利排出,通过高压风、水,使砂仓内的尾矿流态化的过程;2.4.破拱:指当尾砂在立式砂仓内经过长期压缩产生死角和板结,为加速尾砂实现流态化,在不动用砂仓内的高压风水造浆喷嘴系统的条件下,采用独立的高压水,从而实现砂仓内的高浓度尾砂浆迅速排出。
全尾砂膏体充填技术规范制定研究
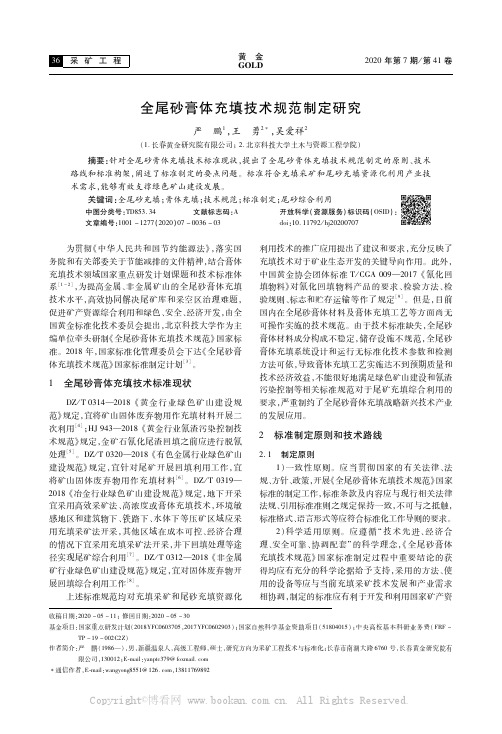
黄 金 GOLD
2020年第 7期 /第 41卷
全尾砂膏体充填技术规范制定研究
严 鹏1,王 勇2 ,吴爱祥2
(1.长春黄金研究院有限公司;2.北京科技大学土木与资源工程学院)
Байду номын сангаас
摘要:针对全尾砂膏体充填技术标准现状,提出了全尾砂膏体充填技术规范制定的原则、技术
路线和标准构架,阐述了标准制定的要点问题。标准符合充填采矿和尾砂充填资源化利用产业技
限公司,130012;Email:yanptc379@foxmail.com 通信作者,Email:wangyong8551@126.com,13811769892
Copyright©博看网 . All Rights Reserved.
2020年第 7期 /第 41卷
为贯彻 《中 华 人 民 共 和 国 节 约 能 源 法 》,落 实 国 务院和有关部委关于节能减排的文件精神,结合膏体 充填技术领域国家重点研发计划课题和技术标准体 系 [1-2],为提高金属、非 金 属 矿 山 的 全 尾 砂 膏 体 充 填 技术水平,高效协同解决尾矿库和采空区治理难题, 促进矿产资源综合利用和绿色、安全、经济开发,由全 国黄金标准化技术委员会提出,北京科技大学作为主 编单位牵头研制《全尾砂膏体充填技术规范》国家标 准。2018年,国家标准化管理委员会下达《全尾砂膏 体充填技术规范》国家标准制定计划[3]。
2 标准制定原则和技术路线
2.1 制定原则 1)一致 性 原 则。 应 当 贯 彻 国 家 的 有 关 法 律、法
规、方针、政策,开展《全尾砂膏体充填技术规范》国家 标准的制定工作,标准条款及内容应与现行相关法律 法规、引用标准准则之规定保持一致,不可与之抵触, 标准格式、语言形式等应符合标准化工作导则的要求。
高浓度结构流全尾砂胶结充填实验研究与应用

一
2 0m以上 矿段 。初 步 设 计 生 产能 力 为 9 0 9万 ta / ,根 据 矿
1 概 述
吴 集 铁 矿 ( 段 ) 位 于 霍 邱 矿 区南 部 ,霍 邱 铁 矿 区 分 北 布 南 北 长 约 4 m, 东 西 宽 3 8k 0k ~ m的 范 围 内 , 截 止 2 0 02 年 全 区铁 矿 石 探 明储 量 累计 1 . 亿 t 72 ,远 景储 量 为 3 O亿 t 。
摘要 :针对吴集铁 矿矿 床被 约1 0m厚第 四系岩石覆 盖 ,采矿过 程 中地表不允许 塌落 ,合 理选择 了阶 4 段空 场嗣后充填法 采矿 ,开展了低品位铁矿高浓度全尾砂结 构流胶结 充填实验研 究并成功应 用 ,取 得 良好
的 经 济 和 社会 效 益 。 关 键 词 :结 构 流 全 尾 砂 胶 结 充 填 ;充 填 体 ;强 度 ;效 益 中圈 分 类 号 :T 2 . D837 文 献标 识 码 :B 文 章 编 号 :1 7 — 8 5 (0 1 6 00 3 6 1 5 0 2 1 )0 —0 2 —0
终 工 业 产 品为 单 一 优 质 铁 精 粉 ,铁 精 矿 含 铁 6 . 。选 矿 65 工 艺 为 三 段 一 闭 路 流 程 ,综 合 选 比 3 7 . 。若 选 矿 能 力 按 处 理 10万 ta 模 计 算 ,则 干 抛 尾 矿 比率 为 1 , 干 抛 尾 0 /规 5 矿量 约 1 5万 t ,人 磨 矿 石 量 8 5万 t ,精 矿 年 产 量 2 8万 t ,
同时 全 尾 砂 粒 级 较 粗 ,一 5 一 1 z 及 0/ m所 占 比例 分 别 为
当超 过 7 时 ,其 坍 落度 ( 2 m ,料 浆 流 动 性 明 显 降低 , 4 2c
全尾砂胶结充填井下作业安全操作规程

全尾砂胶结充填井下作业安全操作规程一、充填管道的运输1、管道运输时不应受到猛烈撞击、抛摔。
贮存时应放在不超过40℃的库房内,并远离热源。
2、运输充填管道要求人工抬运,不得用电机车拖拉,防止管道损坏。
3、管道下井时,应具有绞车等吊装工具,用铁管横挡井口,管道末端上好管箍,绳索绑扎在卡箍上,而后慢慢下放。
绳索抗拉强度要求是被放管道重量的5倍以上,绳索长度要超过管道下放区间高度的20米以上,并且每次作业最多只答应下放一根管道。
4、更换井间废旧管道时,下放废旧管道上端绑扎要牢,下放要慢,井底不得站人,待废旧管道下至井底后,再来人将管道慢慢拉离井底。
此作业过程,上、下井口要联系好才可进行。
二、管道的铺设与安装1、在充填管道安装前,应检查管路的完好情况。
如充填管路显现深槽、大面积磨损等情况时,应先将破损部分截掉,否则禁止运用。
2、正确辨认管路联接件的用途。
在安装前管道切口要求打磨平滑,切口垂直管壁,以利安装。
管路联结要求安全、牢靠,严禁显现脱落、跑浆等现象。
3、巷道中管路铺设要求尽量平直、整齐,上下井口马头门处及过桥的弯曲必需平缓自然、绑扎牢靠,使其不得有摇摆的自由度。
4、井筒中管道除正常的接头联接外,应视详细情况增加管路与井架等的固定点,以防止管道坠井及振动现象的发生。
三、充填准备工作1、检查充填管路及联接是否完好、坚固。
2、按时更换磨损严峻的管道、管件,使整个充填管路保持正常待工作状态。
3、接到充填作业通知后,确认其充填地点、形式、时间,做好充填管路拨头、联结工作。
4、做好与充填搅拌站的联系工作。
5、做好充填采场的顶板安全检查、照明、通讯、管路、筑坝、滤水等工作。
6、充填前要做好钢模架设工作,每分层充填最上部钢模的上口应增加30~40cm高的滤水圈。
四、充填作业1、在做好充填作业准备工作后,通知选厂搅拌站开头充填作业。
在确认选厂冲洗管路作业开头5分钟或冲洗水变清后,可通知选厂进行正常充填。
在此过程中,勿使冲洗水进入待充区。
尾矿回填-全尾砂胶结充填工艺

尾矿回填-全尾砂胶结充填工艺矿山机械选矿厂家尾矿库已到服务年限,如果不对尾矿做科学的综合治理方案,势必超期服役。
并且,随着尾矿量不断增加,建立新的尾矿库已势在必行,新的尾矿库的建立需要占用大量的农林用地。
一个年产20万吨铅锌矿的选矿厂,建一座尾矿库需占地800~1000亩(1亩=667㎡),能够维持10~15年生产之用。
由于土地资源越来越紧张,征地费用越来越高,导致尾矿库的基建投资占整个采选企业费用的比例越来越大,且尾矿库的维护也需消耗大量的资金。
每年的营运费用高达100万元之多,因此,实施尾矿综合开发治理,减少尾矿库投入成本,是企业降低经济负担,提高经济效益的需要。
目前在我国应用的充填工艺主要有全尾砂胶结充填、分级尾砂充填、废石胶结充填、膏体泵送胶结充填、磨砂胶结充填、赤泥胶结充填、少量的天然砂胶结充填和干式充填。
全尾砂胶结充填是充分利用尾矿资源,实现矿山无废开采,同时也是将尾砂视为一种远景资源储存于井下,待将来技术经济成熟再对其进行二次开发利用来满足国民经济发展的需要,是现代采矿工业中一项有利于矿业可持续发展的新技术。
一、全尾砂胶结充填工艺:全尾砂胶结充填工艺是以物理化学和胶体化学的理论为基础,直接采用选厂尾砂浆,经浓密机和砂仓沉降脱水,将全尾砂与一定比例的水泥和水通过双轴叶片式搅拌机和高速活化搅拌机合成均质的胶结充填料,利用管道将充填料充入采场。
尾砂流量,水泥流量,加水量以及合成充填体料浆的浓度等参数由自动控制系统进行控制。
二、全尾砂胶结充填系统:全尾砂胶结充填系统主要由脱水系统、搅拌系统、管路输送系统和自动检测及调节系统等四部分组成的。
1、脱水系统在生产过程中一般采用浓密、沉缩两段脱水工艺,选厂全尾砂料浆经高效浓密机第一段脱水后,泵入立式砂仓进行第二次沉缩脱水,从砂仓放出料浆直接进入搅拌。
2、搅拌系统通过脱水系统排除的矿砂与一定比例的胶结材料和水通过高浓度矿浆搅拌桶,受上、下螺旋方向相反的叶轮作用,形成两股相对流动的矿流,互相冲击、搅拌而使浆料混合均匀。
超细全尾砂赤泥浓缩脱水高浓度造浆充填方案
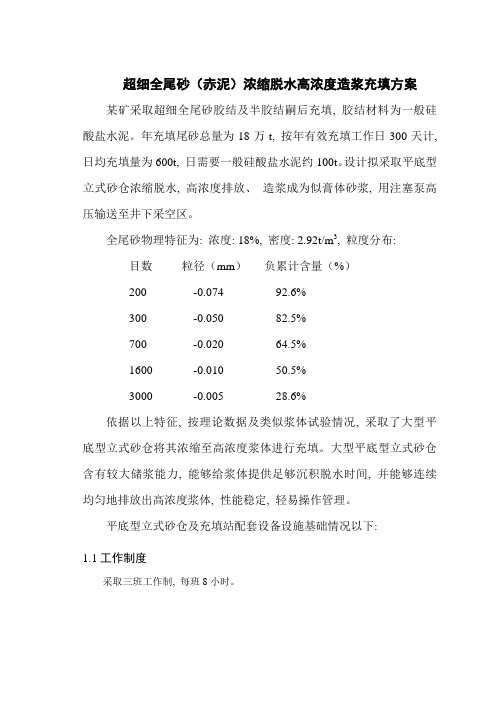
超细全尾砂(赤泥)浓缩脱水高浓度造浆充填方案某矿采取超细全尾砂胶结及半胶结嗣后充填, 胶结材料为一般硅酸盐水泥。
年充填尾砂总量为18万t, 按年有效充填工作日300天计, 日均充填量为600t, 日需要一般硅酸盐水泥约100t。
设计拟采取平底型立式砂仓浓缩脱水, 高浓度排放、造浆成为似膏体砂浆, 用注塞泵高压输送至井下采空区。
全尾砂物理特征为: 浓度: 18%, 密度: 2.92t/m3, 粒度分布: 目数粒径(mm)负累计含量(%)
200 -0.074 92.6%
300 -0.050 82.5%
700 -0.020 64.5%
1600 -0.010 50.5%
3000 -0.005 28.6%
依据以上特征, 按理论数据及类似浆体试验情况, 采取了大型平底型立式砂仓将其浓缩至高浓度浆体进行充填。
大型平底型立式砂仓含有较大储浆能力, 能够给浆体提供足够沉积脱水时间, 并能够连续均匀地排放出高浓度浆体, 性能稳定, 轻易操作管理。
平底型立式砂仓及充填站配套设备设施基础情况以下:
1.1工作制度
采取三班工作制, 每班8小时。
1.2劳动定员
表1 充填工程劳动定员表
充填站定员10人。
1.3充填站总投资估算
表2充填设备单位工程概算表单位: 元
表4充填土建单位工程概算表单位: 元
表5 电气土建单位工程概算表单位: 元
表7充填站总投资估算表
1.4充填单位成本。
全尾砂胶结充填技术应用和改造实施膏体充填探讨

• 造成的原因主要有两方面:
• 一是尾砂给料不均匀。由于尾砂属于高细度有粘 性物料,压滤后呈块状,通过振动漏斗给料极不 均匀,造成皮带秤计量误差较大,影响灰砂比和 料浆浓度。
• 二是自流输送不能满足倍线增加的需要。随着采 矿区域向远处延伸,充填倍线不断增加,最远处 的充填倍线将达到15,在充填倍线达到3.5以上, 充填浓度55%已难以自流,为了实现自流,只能 降低充填浓度,降低充填体质量。
2.5灰砂比和料浆浓度
• 在料浆浓度为54~67%,张马屯铁矿的灰砂比1: 4,1:5,1:6, 60天龄期单轴抗压强度在0.85~ 2.38MPa,大部分在1.0~1.68Mpa。
• 张马屯铁矿的全尾砂胶结充填设计为高浓度充填 ,浓度在60-65%。但生产难以达到。通过斜井自 流输送浓度最高只能到62%,超过既发生堵管。 生产应用55-57%,由于尾砂给料不均匀,再高极 易堵管。试验表明在灰砂比不变时,随浓度的增 加,其强度的增加还是比较显著的。
• 建矿以来一直开采的张马屯铁矿床,属矽卡岩型 磁铁矿床,位于矿区中部济南辉长岩体东部接触
带,是济南铁矿区中规模较大的一个隐伏矿床, 由Ⅰ、Ⅱ号两个主要矿体和少量零星矿体组成。 矿体范围内为平原地形,地势平坦,标高在29~ 33m之间。地表为村庄农田,又紧邻胶济铁路和
公路,无河流通过,无汇水体,矿体埋藏深。累 计探明储量2883.8万吨,平均地质品位54%,属高 硫半自熔高炉富矿。
• 采用高速活化搅拌工艺,将浓密脱水后的选矿尾 砂按一定的灰砂比,与适量的水泥和水混合,先 经双轴搅拌机初步搅拌后,再经高速搅拌机进行 强力活化搅拌,制成浓度60%左右的全尾砂料浆 ,通过Φ125mm充填管自流输送充填采空区,形 成的充填体自立高度可达60m,具有良好的稳定 性。
全尾砂膏体充填技术标准

全尾砂膏体充填技术标准本技术标准适用于全尾砂膏体充填系统的设计和运行。
全尾砂膏体充填技术旨在通过使用膏体状尾砂进行充填,实现对矿山废料的有效处理和利用。
本标准详细介绍了全尾砂膏体充填技术的各个方面,包括充填材料、充填设备、充填工艺、质量检测与控制以及环境影响控制。
1. 充填材料全尾砂膏体充填材料应具备以下特性:1.1. 稳定性:膏体充填材料应具有良好的稳定性,以确保在运输和充填过程中不发生分离或沉淀。
1.2. 充填性能:膏体充填材料应具有良好的流动性,以便实现自流充填和泵送充填。
1.3. 固化性:膏体充填材料应能在一定时间内固化,以保持充填体的稳定性。
1.4. 抗侵蚀性:膏体充填材料应能抵抗地下水和外部环境的侵蚀,以确保充填体的长期稳定性。
1.5. 环保性:膏体充填材料应使用环保材料,减少对环境的影响。
2. 充填设备全尾砂膏体充填系统应配备以下设备:2.1. 搅拌设备:用于制备膏体状尾砂。
2.2. 输送设备:用于将膏体状尾砂输送到充填地点。
2.3. 充填设备:包括自流充填设备和泵送充填设备,根据实际情况选择使用。
2.4. 监测设备:用于监测充填过程和效果。
3. 充填工艺全尾砂膏体充填工艺应包括以下步骤:3.1. 搅拌:将尾砂和膏体粘合剂按一定比例混合,制备成膏体状尾砂。
3.2. 输送:将膏体状尾砂输送到充填地点。
3.3. 充填:根据设计要求,将膏体状尾砂充填到指定地点。
3.4. 监测:对充填过程和效果进行监测,确保达到设计要求。
4. 质量检测与控制全尾砂膏体充填系统的质量检测与控制应包括以下方面:4.1. 材料检测:对使用的尾砂和膏体粘合剂进行检测,确保符合设计要求。
4.2. 搅拌控制:控制搅拌设备的运行参数,确保制备出稳定的膏体状尾砂。
4.3. 输送监控:监控输送设备的运行情况,确保膏体状尾砂顺利输送到充填地点。
4.4. 充填效果检测:对充填后的区域进行检测,确保充填效果达到设计要求。
4.5. 数据分析与改进:对监测数据进行分析,发现存在的问题并采取改进措施。
尾砂充填系统工艺流程

尾砂充填系统工艺流程英文回答:Tailings filling system is a crucial process in mining operations, especially in underground mining. It involves the disposal of waste materials, known as tailings, into underground voids or mined-out areas. This process not only helps in waste management but also provides support to the surrounding rock mass, thus ensuring the stability and safety of the underground mine.The process of tailings filling system typically involves several steps. First, the tailings are dewatered to reduce their moisture content. This can be done using various methods such as thickening, filtration, or centrifugation. Dewatering is important as it helps in reducing the volume of tailings and makes them easier to handle and transport.Once the tailings are dewatered, they are mixed withadditives such as cement, fly ash, or lime to improve their properties. These additives help in enhancing the strength and stability of the tailings, making them suitable for filling underground voids. The tailings and additives are thoroughly mixed using specialized equipment, such as agitators or mixers, to ensure a homogeneous mixture.After the mixing process, the tailings mixture is transported to the underground voids using pipelines or conveyor belts. The transportation system should be designed to minimize the segregation or settling oftailings during the transportation process. The tailings mixture is then discharged into the voids using controlled flow rates to ensure uniform filling.During the filling process, it is important to monitor and control the density and flow characteristics of the tailings mixture. This can be done by regularly sampling the mixture and conducting laboratory tests to ensure that it meets the required specifications. Adjustments can be made to the mixture composition or flow rates if needed to achieve the desired filling results.Once the filling is complete, the tailings undergo a curing process to allow them to gain strength and stability. This process typically takes several days or weeks, depending on the composition and properties of the tailings mixture. After the curing period, the filled voids can be further supported by installing support systems such asrock bolts or shotcrete.Overall, the tailings filling system is a complex process that requires careful planning, monitoring, and control to ensure its effectiveness and safety. It plays a crucial role in waste management and underground mine stability. Proper implementation of the system can help in minimizing environmental impacts and maximizing the utilization of mining resources.中文回答:尾砂充填系统是矿山作业中的一个关键工艺流程,尤其在地下矿山中。
- 1、下载文档前请自行甄别文档内容的完整性,平台不提供额外的编辑、内容补充、找答案等附加服务。
- 2、"仅部分预览"的文档,不可在线预览部分如存在完整性等问题,可反馈申请退款(可完整预览的文档不适用该条件!)。
- 3、如文档侵犯您的权益,请联系客服反馈,我们会尽快为您处理(人工客服工作时间:9:00-18:30)。
全尾砂高浓度连续充填技术规程目录全尾砂 (1)高浓度连续充填技术规程 (1)一、充填前期准备 (3)1. 地表系统 (3)2. 井下充填设施 (3)3. 其他准备 (3)二、全尾砂充填料浆制备工序技术规程 (3)1. 范围 (3)2. 术语 (4)3. 技术规程 (4)4. 尾砂进料 (5)5. 放砂及充填料浆制备 (5)6. 停车顺序 (8)一、充填前期准备1.地表系统1.1.尾砂输送泵房设备、仪表、管线、阀门、事故放空池等检查与维护;1.2.尾砂输送管线巡查,检查管线是否正常;1.3.絮凝剂制备设备、仪表、流量泵、管线、阀门检查与维护;1.4.充填搅拌站内设备、仪表、管线、阀门、控制系统检查与维护;1.5.尾砂进料管线、放砂管、溢流管及药剂(絮凝剂等)管线检查;1.6.水泥添加系统检查;1.7.地表通讯设施检查与维护;1.8.搅拌机械、电器设备、进出口阀门检查与维护;1.9.高压水源、常压水源供给情况检查;1.10.压气设备检查与维护。
2.井下充填设施2.1.井下通讯设施检查与维护;2.2.采场底部结构、充填挡墙检查及渗漏治理;2.3.充填主管路管线检查、安全检查及隐患处理。
3.其他准备3.1水泥30t,絮凝剂~200kg;3.2对讲机4个,手电筒2个,浓度壶2个(不锈钢),电子秤1台(精度1g),取样勺一个(手柄长~1.5m),简易手持砂面料位计(用20m皮尺绑重块制作)。
二、全尾砂充填料浆制备工序技术规程1.范围本规程规定了全尾砂高浓度充填料制备工序的基本准则,具体细节可根据实际情况酌情调整。
本规程适用于尾矿胶结充填站充填料浆制备工序。
2.术语下列术语和定义适用于本规程:2.1.高浓度尾砂胶结充填:指将选矿厂产出的尾砂浆体浓缩至一定浓度(如68%~72%)以上,与一定比例的胶结材料混合搅拌制备均匀后通过管路回填至井下采空区的过程和作业;2.2.灰砂比:指尾砂胶充填作业中胶结材料与尾砂干量的质量比(如1:6);2.3.活化:指为了使得砂仓浓密(压缩)后的高浓度顺利排出,通过高压风、水,使砂仓内的尾矿流态化的过程;2.4.破拱:指当尾砂在立式砂仓内经过长期压缩产生死角和板结,为加速尾砂实现流态化,在不动用砂仓内的高压风水造浆喷嘴系统的条件下,采用独立的高压水,从而实现砂仓内的高浓度尾砂浆迅速排出。
3.技术规程3.1.尾砂输送泵房开车准备3.1.1.检查各阀门状态,检查各设备是否供电,设备就地和远程设置是否正确;3.1.2.开启尾砂输送泵电动机,如需调整电动机频率时要时刻注意观察输送流量和管路压力;当流量到达设计值左右时给定该频率,保持该流量运行;3.1.3.进砂作业完毕后,关闭尾砂给料阀门,用水持续冲洗管路~30min;关闭尾砂输送泵电动机。
3.2.絮凝剂制备准备3.2.1.操作人员正确穿戴好劳保用品,检查絮凝剂是否受潮,将粉状絮凝剂添加至絮凝剂制备料斗;3.2.2.打开制备罐放水阀,将水加至适当位置;3.2.3.按制备要求,检查电源情况,关启好相关闭路循环阀门。
3.3.絮凝剂制备设备开车顺序3.3.1.按絮凝剂站制备技术质量要求,开或闭好所有的阀门;3.3.2.打开螺杆泵,并按需要值调节流量调节阀门输送絮凝剂到砂仓内。
4.尾砂进料4.1.选矿厂产出的全尾砂输送至砂仓顶部,通过仓顶的电动球阀分配至使用的砂仓;4.2.进入砂仓的浓度尽可能保持在~20%;4.3.来自选矿的全尾砂料浆在来源处需经格筛装置,去除杂物;4.4.进入砂仓的流程是:选矿料浆——输送泵——管路系统——砂仓顶部——添加絮凝剂(如果需要使用絮凝剂)——仓内缓冲斗——进入砂仓沉降、存储;4.5.控制进砂干量,在只进砂不放砂时,砂面高度应不超过12m;进砂的同时放砂,则尽量让砂仓的砂面保持进出平衡,即砂面的高度变化不大,保持相对恒定;4.6.为避免仓内设施不被损坏,砂仓进料时必须将砂仓内充满清水;4.7.当砂位高于12m时或严重跑浑时,应观测砂位高度,分析原因,采取1)、添加絮凝剂;2)、减少进砂量,加大放砂量;3)如果浓密机的溢流水也无法澄清,应注意该水对生产水池的影响,如有必要则立即停止供料;4.8.为控制溢流浓度,每个砂仓进料不宜大于300m3/h(在砂面高度超过10m,或来料尾砂浓度超过30%时,应适当降低进料小时量)。
5.放砂及充填料浆制备5.1.放砂时,根据所需充填量,必须保证仓内料位和进料浓度相对恒定,流量大小根据砂位高度调节进料量;5.2.放砂应尽量使用新砂,实际操作一般可按下述2种方式管理,1)每个班均进砂和放砂,砂在仓中存储时间较短,每个班保持相对平衡;2)头班进的砂,交接班后,接班人员将砂仓的砂放至低位(2~4m),为下一个班的进砂腾出空间,进砂、放砂在3个班之间交替进行,砂面高度每天保持相对平衡;5.3.管路造浆系统的使用原则:一般使用高压水,部分时候使用压气,用气造浆后需继续使用高压水(压气一般不单独使用,高压水造浆可单独使用),造浆时间一般为5 min~30min,未达到效果时,可适当增加次数,造浆的压风和高压水压力均不小于0.6MPa(6kg 压力);5.4.一般在下述三种情况使用造浆系统:1)当浓度过高不利于放砂时,可适时开启造浆系统稀释放砂浓度稳定流量;2)放砂后,需清理砂仓的泥沙挂壁现象,尽量使砂面均匀下降;或尾砂只进料不放砂充填时,每班应开启造浆管路5~15min活化砂浆;3)砂仓不好放砂、砂仓长时间存砂或砂仓清空时,则应开启较多的管路进行全面的活化造浆,或开启风水联动造浆(先压风造浆后高压水造浆),造浆时间长短视间隔停车时间长短而定;5.5.每班充填作业完毕后,应清洗造浆管路的返砂,即关闭进仓的阀门,开启冲洗端口的阀门进行冲洗,时间5~10min;5.6.料浆制备的最佳流量为90 m3/h~110m3/h,流量波动时,一般会伴随浓度波动,要及时使用造浆系统,使放砂流量、浓度尽量保持稳定;5.7.当放砂流量波动较大时,应适时先后启动1、2#环管,直至流量稳定为止;如果持续流量较低或者不稳定,如放砂量持续10min 小于30m3/h时,应该同时启动多层环、列管进行全面造浆活化;5.8.制备高浓度料浆时,应按絮凝剂添加技术规程添加絮凝剂(使用絮凝剂前,需落实絮凝剂对选矿指标的影响),为防止尾砂跑浑;在最初添加絮凝剂时,絮凝剂添加量约20g/t;为节药絮凝剂用量,并保证充填料浆制备浓度,尽可能保证在较低砂位放砂;絮凝剂的制备浓度为0.03%~0.05%,溶解搅拌时间不低于30min,溶解的絮凝剂溶液均匀,无鱼眼状漂浮物,应根据尾矿特性、溢流浓度要求,确定是否添加絮凝剂和添加量的大小和时间;5.9.为降低砂仓顶部的溢流浓度,在放砂前在砂仓制备料浆时,同时进出砂时,可通过控制砂面的高度使溢流浓度保持在较低的水平;一般在满足充填浓度和能力的前提下,砂面高度一般控制在3~10m之间,建议不要超过12m;5.10.在制备胶结充填料浆时,应根据充填需要的灰砂比和充填倍线,制备料浆,料浆浓度一般在68%~72%范围内,其充填料浆制备原则是先放砂,后添加胶结材料,当砂位放至搅拌槽内1m 高度时,再开始添加水泥;5.11.在进行料浆输送时搅拌槽液位应控制在1.2m~1.5m,过低液位易造成灰砂混合不均匀及结块,过高易造成水泥将下料口堵塞;5.12.在进行充填时,每班应不少于2次对充填浓度进行浓度壶抽检,并记录;5.13.充填时,应对各类阀门和管线的巡视,发现问题及时停止给料,并对充填管线进行冲洗;5.14.当井下人员发现管线堵塞时,应立即启动停止料浆供给,输送清水高压冲洗管路;5.15.充填作业前需放引流水,充填作业完毕后需放冲洗水;引流水排放时间为3~5min,管道冲洗水时间为10~15min;输送引流水和冲洗水时,都应将搅拌槽水面保持约1.5m高度,再开启阀门冲洗;5.16.根据采空区充填区域的强度要求,并结合相关强度试验数据,确定充填灰砂比。
胶结充填时,严格按充填灰砂比添加水泥、水要求,制备胶结料浆,避免强度达不到要求,或堵管现象发生;5.17.制备人员根据充填作业的时间要求,应提前对仓内料浆进行试放,若流动性差,则应开启造浆管路活化、破拱,保证下料顺畅;5.18.连续充填的原则是以砂位定浓度和流量,为确保料浆制备质量在连续充填时,一般仓内料位在3m~10m范围内为宜;当砂面较高时,应每小时测试溢流浓度一次,并及时充填放砂,避免砂面长时间偏高;当砂面较低时,应监测放砂浓度,浓度较低时,可以停止放砂,待砂面升高到可放砂的浓度时继续放砂充填,平时应及时记录相关进砂、放砂数据,总结适合本矿进砂放砂的经验数据;5.19.充填输送时应尽可能保证料浆满管流;5.20.连续充填必须经常对仪表进行检查,发现异常时及时校正(如流量计、液位计、浓度计等);5.21.地表、井下充填系统要配备专巡视,及时沟通,发现情况要及时联络反馈。
必要时地表搅拌站停止进料,加水清洗;6.停车顺序(先开的后关,先关的后开)6.1.关闭水泥(胶结充填时)仓底闸板阀;6.2.关仓底放砂刀闸阀;6.3.打开冲洗水;与井下沟通,将搅拌槽和管线冲洗干净;6.4.关闭搅拌槽停电动机,关闭放砂管路的球闸阀和搅拌槽出口的锥形阀;6.5.根据仓内砂位情况确定是否停止该仓的尾砂进料;6.6.清理、冲洗现场;6.7.定期清理事故沟、事故池。