刀具角度的选择
十几把刀的刀锋角度有哪些选择?

十几把刀的刀锋角度有哪些选择?一、刀锋角度的重要性刀锋角度是影响刀具性能的关键因素之一。
不同的刀锋角度适用于不同的刀具和工作材料,正确选择刀锋角度有助于提高切削效率和刀具寿命。
二、常见的刀锋角度选择1. 锋角小的刀锋角度刀锋角度小于30度的刀具适用于切削硬度较高的工作材料,如金属和硬塑料。
小锋角能够集中切削力,减少切削阻力,提高切削效率。
同时,由于刀具的切削压力集中在小的刀锋区域,刀具磨损也相对较小,延长了刀具的使用寿命。
2. 锋角大的刀锋角度刀锋角度大于30度的刀具适用于切削软性材料,如木材和软塑料。
大锋角能够扩散切削力,减少切削压力,避免材料的过度压缩和变形。
此外,大锋角还能够提供更好的切削质量,减少切削表面的毛刺和破损。
3. 锋角中等的刀锋角度对于一些切削难度适中的工作材料,如一些常见的金属合金和工程塑料,中等大小的刀锋角度是较为合适的选择。
这种刀锋角度可以在保证切削力集中的同时,减少切削阻力和切削热量,并提高切削质量和刀具寿命。
4. 不同材料常用的刀锋角度除了刀具设计和加工要求外,不同工作材料的特性也会影响刀锋角度的选择。
例如,钻削金属时,常用的刀锋角度大约为118度;而钻削木材时,则常用的刀锋角度为90度,这是因为木材的纤维结构不同于金属。
5. 刀锋角度与切削力和切削质量的关系正确选择刀锋角度不仅能够降低切削力,提高切削效率,还能够改善切削质量。
合适的刀锋角度可以减少切削表面的毛刺和破损,提高切削精度和表面质量,适用于精密加工和高精度要求的工作。
总结:刀锋角度的选择是影响刀具性能的关键因素之一。
根据不同的刀具和工作材料,我们可以选择不同锋角大小的刀锋角度。
锋角小的刀锋角度适用于切削硬度较高的工作材料,锋角大的刀锋角度适用于切削软性材料,而中等大小的刀锋角度适用于一些切削难度适中的工作材料。
在选择刀锋角度时,我们也要考虑材料的特性以及刀具的设计和加工要求。
正确选择刀锋角度不仅能够提高切削效率和刀具寿命,还能够改善切削质量,满足精密加工和高精度要求的工作。
金属切削刀具常用的5个切削角度

金属切削刀具是制造业中常用的工具,正确的切削角度对切削质量有着重要的影响。
在金属加工过程中,常用的五个切削角度包括:刀尖倒角角度、主偏角、副偏角、前角和后角。
一、刀尖倒角角度刀尖倒角角度是指刀具前端倒角的角度,它的大小会影响切削的刀尖强度和耐磨性。
一般来说,刀尖倒角角度越小,刀尖强度越高,耐磨性也越好。
常见的刀尖倒角角度为15度至45度不等,选用合适的刀尖倒角角度能够减小切屑厚度、改进切削刚度和提高刀具寿命。
二、主偏角主偏角又称前角,是指切削刃与工件表面的夹角。
主偏角的大小直接影响着刀具的切削力和切屑的形态。
通常情况下,主偏角越小,切削力越小,切削刚度越大。
然而,主偏角过小也容易导致刀具容易断裂和刀尖易磨损。
在实际加工中需要根据不同的工件材料和加工条件来选择合适的主偏角。
三、副偏角副偏角又称侧倾角,是指刀具刃部与切削面的夹角。
副偏角的大小影响着切屑的流动和刀具的耐磨性。
一般情况下,副偏角越小,切屑流动越顺畅,切屑的形态也更好。
但过小的副偏角容易导致刀具刃部的磨损加剧。
在选择副偏角时需要兼顾切屑形态和刀具的耐磨性。
四、前角前角是刀具刃部与工件表面接触时形成的角度,它的大小直接影响着切削时的切削力和切屑的形态。
一般情况下,前角越大,切削力越小,切屑流动也更加顺畅。
然而,过大的前角容易导致刀具刃部的磨损加快。
在实际加工中需要根据工件材料和加工条件来选择合适的前角。
五、后角后角是刀具刃部背面与工件表面形成的角度,它的大小影响着刀具刃部的强度和切削力。
一般情况下,后角越大,刀具刃部强度越高,切削力也相对较小。
然而,过大的后角会导致刃部切削过程中的摩擦增大,从而影响切削质量。
在选择后角时需要根据实际情况进行合理的选择。
总结:金属切削刀具的切削角度对切削质量和刀具寿命有着重要的影响。
正确选择刀尖倒角角度、主偏角、副偏角、前角和后角,可以有效地改善切削过程中的刀具性能,提高加工质量,降低成本,增加经济效益。
在实际加工中,需要根据具体的工件材料和加工条件来合理选择切削角度,以达到最佳的加工效果。
简要说明刀具的主要角度及其选用原则

简要说明刀具的主要角度及其选用原则刀具,这个东西,看似简单,实则里面的学问可大着呢!要说到刀具的主要角度,首先得从“切”这个动作说起。
你想,刀具不就是为了帮助我们切得又快又好嘛?不过别以为这事儿很简单,刀具角度可讲究了,不同的角度对应不同的切削效果,不是随便调一调就行的。
话说回来,刀具的角度主要有几个重要的,比如主切削角、前角、后角、侧角等。
这些角度的选用和调整,直接关系到切削的效率和刀具的使用寿命,关系到你切得快不快、刀刃磨得快不快,甚至刀具能不能“吃得住”硬材料。
所以说呀,选刀具角度可得当心,别瞎选,否则刀具很可能“生病”,不但切不好东西,磨得还特别快,浪费可就大了!首先说说主切削角吧,这个角度就像是刀具的“个性”,它决定了刀具切入材料时的态势。
主切削角越小,刀具的切入角度越大,越容易切进去,工作时感觉特别轻松,不会太费劲。
但是呢,主切削角也不能小得过头,不然刀具容易变钝,切削时材料不容易被带走,刀具负担加重,热量产生也会增多,刀具的寿命可就大打折扣了。
你知道的,刀具这种东西,不能嫌它重也不能嫌它轻,最讲究的就是一个“合适”字。
再说了,主切削角也不是越小越好,越大反而越容易磨损,刀具就容易变得“不听话”了。
所以这角度要选得恰到好处,得看你切的是啥材料,硬度如何,得结合实际情况。
再来看看前角。
这个角度直接影响刀具的锋利程度,前角大,刀具就会锋利,切得也快,顺畅无比。
要是前角太小,切削时材料就不容易被带走,刀具就像是被困住了,切得慢,费力还不省事儿。
前角一般都得大一些,尤其是当我们切的是一些软材料时,前角越大,切削更容易,省力省时。
不过也得小心,如果前角过大,刀具的强度就会降低,容易崩刃,后果可不堪设想。
所以,前角和主切削角一样,得精挑细选,不是随便选一个大的角度就好。
再来说说后角,听起来很简单,其实影响也不小。
后角决定了切削的稳定性,影响着刀具的摩擦情况。
后角大,刀具和工件的接触面小,摩擦就小,切削过程顺畅,刀具也不会那么快磨损。
刀具几何角度的作用及选择原则

刀具几何角度的作用及选择原则刀具的几何角度对加工质量、切削力和切削温度等有很大的影响,正确的选择刀具几何角度可以提高切削效率和工件表面质量。
本文将从切削角、主偏角、切削刃前角和切削刃后角四个方面来探讨刀具几何角度的作用及选择原则。
一、切削角切削角是刀具主切削面与工件切削表面的夹角,一般分为正的和负的两种情况。
1.正切削角:也称为刀具顶角,是指刀具主切削面与工件切削表面夹角大于90°的情况。
正切削角有利于降低切削力和切削温度,减少刀具磨损。
因此,在切削硬材料或脆性材料时,一般选择正切削角。
但是正切削角也会增大刀具与工件接触面积,增加切削力,从而需要更大的功率投入。
2.负切削角:也称为刀具反角,是指刀具主切削面与工件切削表面夹角小于90°的情况。
负切削角能降低切削力和切削温度,提高切削稳定性和切削质量。
因此,在切削软材料或难切削材料时,一般选择负切削角。
然而,负切削角的刀具易产生振动,增加切削噪声,且不易控制切削深度。
在实际应用中,切削角的选择应根据材料的性质、切削目标和加工条件综合考虑,一般需要通过试切试验来确定最佳切削角。
二、主偏角主偏角是刀具俯仰角,是指刀具主切削面与铣削切削方向之间的夹角。
主偏角的大小会直接影响刀具的切削力和切削质量。
1.大主偏角:大主偏角可以降低刀具的切削力和切削温度,提高切削稳定性和切削质量。
大主偏角适用于切削精度要求高、切削深度相对较小、切削速度相对较低的情况。
2.小主偏角:小主偏角可以提高刀具的切削效率和切削速度,适用于切削深度相对较大、切削速度相对较高的情况。
然而,小主偏角容易导致切屑的卡刀现象,增加刀具磨损和加工表面粗糙度。
主偏角的选择应结合切削效率和切削质量的要求,同时考虑刀具的刚度和加工条件等因素。
三、切削刃前角切削刃前角是刀具切削刃前的锥度角,主要影响刀具的切削稳定性和切削质量。
1.大切削刃前角:大切削刃前角可以增加切削深度和切削范围,提高切削效率和切削速度。
切割刀的磨刀角度

切割刀的磨刀角度磨刀角度的选择选择合适的磨刀角度可以提高切割刀的效果。
以下是一些常见的磨刀角度选择:1. 倾角(bevel angle):倾角是指刀刃的斜面与刀背之间的夹角。
一般来说,较小的倾角可以提供更尖锐的切割,但刀刃会更薄,容易损坏。
较大的倾角则可以提供更坚固的刀刃,但切割效果可能会打折扣。
选择适当的倾角要考虑材料的硬度和切割需求。
2. 冲刃(relief angle):冲刃是指刀刃斜面与工件接触的角度。
较大的冲刃角度可以降低刀刃与工件的摩擦,减少切割时的热量和切割力,从而减轻刀具磨损。
然而,过大的冲刃角度可能导致切割质量下降。
冲刃角度的选择要综合考虑工件材料和切割表面质量的要求。
3. 前角(rake angle):前角是指切削刃面与工件表面接触的角度。
较小的前角可以提高切削性能和切削质量,但也会增加刀具磨损和加工力。
较大的前角则可以减少磨损,但可能会降低切割效果。
选择合适的前角要综合考虑切削材料和切削力的平衡。
4. 周角(side angle):周角是指刀刃侧面与工件切削方向之间的夹角。
周角的选择会影响刀具的清除能力和刀刃的强度。
较小的周角可以增加清除能力,减轻切屑堆积,但会使刀刃变薄,降低强度和刚度。
较大的周角则可以提高刀刃强度,但可能会减弱清除能力。
周角的选择要综合考虑清除要求和刀具强度的平衡。
磨刀角度的调整调整切割刀的磨刀角度可以实现更好的切割效果。
以下是一些常见的角度调整方法:1. 砂轮磨削:使用合适的砂轮对切割刀进行磨削,调整倾角、冲刃角、前角和周角。
确保砂轮选用合适的粒度和颗粒强度,以获得需要的刀刃形状和质量。
2. 使用磨刀机:磨刀机可以提供更精确和一致的角度磨削。
根据切割需求和材料特性,在磨刀机上调整磨刀角度,确保刀具的切割效果和寿命。
3. 定期检查和校准:定期检查切割刀的磨刀角度,以确保其处于良好状态。
根据需要进行调整和校准,以维持切割质量和刀具寿命。
总之,选择合适的磨刀角度和进行角度调整对于切割刀的切割效果和寿命至关重要。
第五章 切削用量及刀具几何角度的选择(机械制造技术A)

Thank you for your listening!
测试1:
1、积屑瘤在粗、精加工中各起什么作用?当其有害 时怎样抑制它?
2、影响积屑瘤大小的因素?精加工外圆时怎样抑制它? 为什么?
3、试推导变形系数ξ与剪切角Φ之间的关系。
4、单位切削力的定义?
5、切削用量三要素对切削力的影响与对刀具耐用度 的影响有什么不同?请利用指数公式对该问题进行 分析,并提出降低切削力和提高刀具耐用度的措施。
5.4 过渡刃与修光刃参数的选择
一、过渡刃及其参数选择 ⑴外圆车刀过渡刃参数:
过渡刃偏角
rs
1 2
r
过渡刃长度
bs=0.5~2mm
⑵切断刀过渡刃参数 过渡刃偏角 κrs=45° 过渡刃长度 bs=(0.20~0.25)ap
Κ'r
Κr
3)圆弧过渡刃
⑴高速钢车刀 r 0.5 ~ 5mm ⑵硬质合金车刀 r 0.5 ~ 2mm
3.负前角单面型 优点:刃口强度高。 缺点:刃口钝,对切削层的挤压严重。
使用场合: ⑴主要用于硬质合金车刀和铣刀; ⑵切削高强度、高硬度材料和切削淬火钢; ⑶当磨损主要发生在后刀面时。
4.正前角正倒棱 使用场合:适用于高速钢刀具 正倒棱尺寸参数:
br1 (0.5 ~ 1) f ; 01 0 ~ 5
在刀具前刀面上,切屑流出的方向与切削刃法线 间的夹角Ψλ称为流屑角。
主切削刃法线 主切削刃
(1)用测定切屑宽度bc的方法求流屑角:
cos
bc b
cos s
⑵实际切削角 ①流屑剖面:包含切屑流出方向和切削速度的剖面Pλ。 ②实际切削角:在流屑剖面内测量的角度 实际切削前角
sin oe cos sin n cos s sin sin s sin oe sin2 s cos2 s sin n
刀具角度选择

1、前角的选择
1)按加工性质选: 粗车时前角小 精车时前角大
2)按工件材料选: 塑性材料前角大 脆性材料前角小
3)按刀具材料选: 硬质合金前角小 高速钢前角大
2、后角的选择
1)按加工性质选: 粗车时后角小 精车时后角大
2)按工件材料选: 塑性材料后角大 脆性材料后角小
3)选负值(可避免刀尖受冲击,保护刀尖); 精车:选正值(使切屑向待加工表面流出)。
3、主偏角的选择
1)按工件形状选: 有直角台阶时主偏角大于等于90度;
2)按工件材料选: 材料硬(软)时选较小(大)主偏角;
3)按工件刚性选: 刚性好(差)时选较小(大)主偏角。
4、副偏角的选择 1)一般选60~80; 2)按工件表面粗糙度要求选: 要求高时选较小副偏角,但不 能太小,太小会加大与已加工 表面的摩擦,反而降低表面粗 糙度。
刀具几何参数与刀具材料的合理选择-yxj资料

种类
碳素 工具 钢 合金 工具 钢
常用牌号
T8A、T10A T12A
9siCr 、 CiWMn
高速 钢
W9Mo3Cr 4V 、 W6Mo5Cr V2
硬度HRC (HRA)
60~64 ( 81 ~ 83) 60~65 ( 81 ~ 84)
63~69 ( 82 ~ 87)
抗弯强 度
( GP 2.4a5) ~ 2.75
2.刃倾角的选择
选择刃倾角时,应按照刀具的具体工作条件进行具体分析,一般情 况可按加工性质选取。精车λs =0o~5o;粗车λs =0o~-5o; 断续车削λs=-30o~-45o;大刃倾角精刨刀λs=75o~80o。
(1)控制切屑的流向 如图5-5所示,当λS =0o 时,切屑垂
直于切削刃流出;λS为负值时,切屑流向已加工表面; λS为正值时,切屑流向待加工表面。
用于机动复 杂的中速刀 具,如钻头、 铣刀、齿轮 刀具等
硬质 合金
陶瓷
( YG 类 ) 69~81 K 类 ( YT ( 89 ~ 类 ) P 类 93) ( YW 类 ) M类
SG4 、 ( 93 ~
AT6
94)
1500~
2100HV
1.08 ~ 2.16
0.4 ~ 1.115
800 ~ 1100
2.前角的选择原则 (1)主要根据工件材料的性质选择 (2)兼顾根据刀具材料的性质和加工性质 表5-1是硬质 合金车刀合理前角的 参考值。
3.前刀面型式(图5-3 前刀面型式)
(1)正前角平面型 如图5-3a所示,正前角平面型式的特点为:制造简单
能获得较锋利的刃口,但强度低,传热能力差。一般用于精加工刀 具、成形刀具、铣刀和加工脆性材料的刀具。
刀具角度选择
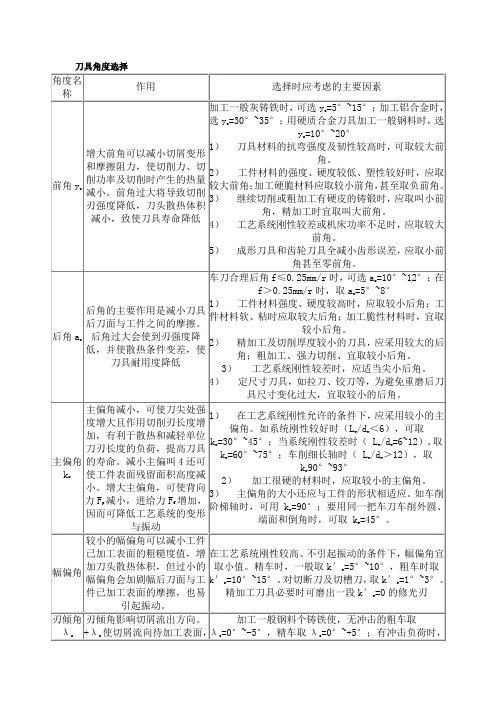
后角的主要作用是减小刀具后刀面与工件之间的摩擦。后角过大会使到刃强度降低,并使散热条件变差,使刀具耐用度降低
车刀合理后角f≤0.25mm/r时,可选ao=10°~12°;在f>0.25mm/r时,取ao=5°~8°
1) 工件材料强度、硬度较高时,应取较小后角;工件材料软、粘时应取较大后角;加工脆性材料时,宜取较小后角。
1)前刀面Ay—切下的切屑沿其流出的表面。
2)主后刀面Aa—与工件上过渡表面相对的表面。
3)副后刀面A'a—与工件上已加工表面相对的的表面。
4)主切削刀S—前刀面与主后刀面的交线,它承担主要切削工作。
5)副切削刃S'—前刀面与副后刀面的交线,它协同主切削刃完成切削工作,并最终形成已加工表面。
6)刀尖—主切削刃与副切削刃连接处的那部分切削刃。
刀具角度选择
角度名称
作用
选择时应考虑的主要因素
前角yo
增大前角可以减小切屑变形和摩擦阻力,使切削力、切削功率及切削时产生的热量减小。前角过大将导致切削刃强度降低,刀头散热体积减小,致使刀具寿命降低
加工一般灰铸铁时,可选yo=5°~15°;加工铝合金时,选yo=30°~35°;用硬质合金刀具加工一般钢料时,选yo=10°~20°
2) 精加工及切削厚度较小的刀具,应采用较大的后角;粗加工、强力切削、宜取较小后角。
3) 工艺系统刚性较差时,应适当尖小后角。
4) 定尺寸刀具,如拉刀、铰刀等,为避免重磨后刀具尺寸变化过大,宜取较小的后角。
主偏角kr
主偏角减小,可使刀尖处强度增大且作用切削刃长度增加,有利于散热和减轻单位刀刃长度的负荷,提高刀具的寿命。减小主偏叫4还可使工件表面残留面积高度减小。增大主偏角,可使背向力Fp减小,进给力Ff增加,因而可降低工艺系统的变形与振动
刀具角度的功用与选择精选文档
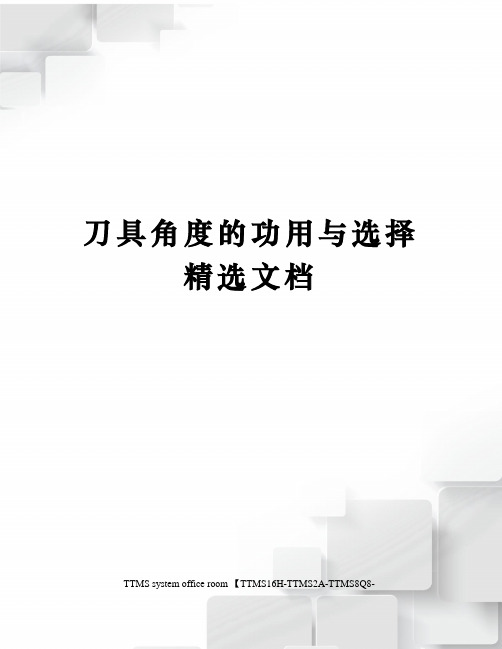
副偏角的大小主要根据表面粗糙度的要求选取,一般为5°~15°,粗加工时取大值,精加工时取小值。切断刀、锯片刀为保证刀头强度,只能取很小的副偏角,一般为1°~2°。
(1)根据工件材料选择前角。加工塑性材料时,特别是硬化严重的材料(如不锈钢等),为了减小切削变形和刀具磨损,应选用较大的前角;加工脆性材料时,由于产生的切屑为崩碎切屑,切削变形小,因此增大前角的意义不大,而这时刀屑间的作用力集中在切削刃附近,为保证切削刃具具有足够的强度,应采用较小的前角。
工件强度和硬度低时,切削力不大,为使切削刃锋利,可选用较大的甚至很大的前角。工件材料强度高时,应选用较小的前角;加工特别硬的工件材料(如淬火钢)时,应选用很小的前角,甚至选用负前角。因为工件的强度、硬度愈高,产生的切削力愈大,切削热愈多,为了使刃具有足够的强度和散热,防止崩刃和磨损,应选用较小的前角。
(1)根据切削厚度选择后角。合理后角大小主要取决于切削厚度(或进给量),切削厚度hD愈大,则后角应愈小;反之亦然。如进给量较大的外圆车刀后角=6°~8°,而每齿进刀量不超过mm的圆盘铣刀后角=?30°。这是因为切削厚度较大时,切削力较大,切削温度也较高,为了保证刃口强度和改善散热条件,所以应取较小的后角。切削厚度愈小,切削层上被切削刃的钝圆半径挤压而留在已加工表面上并与主后刀面挤压摩擦的这一薄层金属占切削厚度的比例就越大。若增大后角,就可减小刃口钝圆半径,使刃口锋利,便于切下薄切屑,可提高刀具耐用度和加工表面质量。
数控机床、自动机床和自动线用刀具,为保证刀具工作的稳定性,使其不易发生崩刃和破损,一般选用较小的前角。
(完整版)刀具角度选择
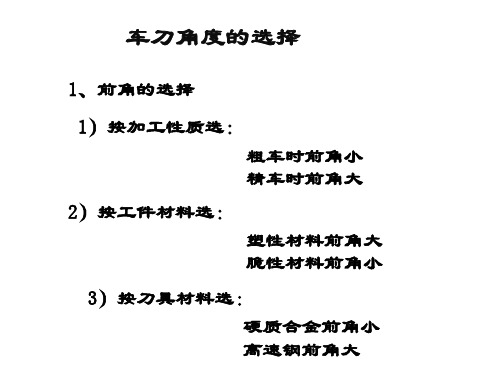
3、主偏角的选择
1)按工件形状选: 有直角台阶时主偏角大于等于90度;
2)按工件材料选: 材料硬(软)时选较小(大)主偏角;
3)按工件刚性选: 刚性好(差)时选较小(大)主偏角。
4、副偏角的选择 1)一般选60~80; 2)按工件表面粗糙度要求选: 要求高时选较小副偏角,但不 能太小,太小会加大与已加工 表面的摩擦,反而降低表面粗 糙度。
5、刃倾角的选择 粗车:选负值(可避免刀尖受冲击,保护刀尖); 精车:选正值(使切屑向待加工表面流出)。
车刀角度的选择
1、前角的选择
1)按加工性质选: 粗车时前角小 精车时前角大
2)按工件材料选: 塑性材料前角大 脆性材料前角小
3)按刀具材料选: 硬质合金前角小 高速钢前角大
2、后角的选择
1)按加工性质选: 粗车时后角小 精车时后角大
2)按工件材料选: 塑性材料后角大 脆性材角大。
车刀的几何角度及选择原则

车刀的几何角度及选择原则newmaker为了决定车刀刃口的锋利程度及其在空间的位置,必须建立一个坐标系,该坐标系由三个基准平面构成。
下面以外圆车刀为例,介绍车刀的几何角度。
如图所示。
基面:过主切削刃选定点的平面,此平面在主切削刃为水平时包含主刀刃并与车刀安装底面即水平面平行,此平面主要作为度量前刀面在空间位置的基准平面。
切削平面:过主切削刃选定点与主切削刃相切,并与基面相垂直的平面。
此平面主要作为度量主后刀面在空间位置的基准面。
主剖面:过主切削刃选定点并同时垂直于基面和主切削平面的平面。
(1)、前角γ0 前刀面与基面的夹角,在主剖面中测量。
前角的大小影响切削刃锋利程度及强度。
增大前角可使刃口锋利,切削力减小,切削温度降低,但过大的前角,会使刃口强度降低,容易造成刃口损坏。
取值范围为:-8°到+15°。
选择前角的一般原则是:前角数值的大小与刀具切削部分材料、被加工材料、工作条件等都有关系。
刀具切削部分材料性脆、强度低时,前角应取小值。
工件材料强度和硬度低时,可选取较大前角。
在重切削和有冲击的工作条件时,前角只能取较小值,有时甚至取负值。
一般是在保证刀具刃口强度的条件下,尽量选用大前角。
如硬质合金车刀加工钢材料时前角值可选5°-15°。
(2)、主后角α0 主后刀面与切削平面间的夹角,在主剖面中测量。
其作用为减小后刀面与工件之间的摩擦。
它也和前角一样影响刃口的强度和锋利程度。
选择原则与前角相似,一般为0到8°。
(3)、主偏角κ r 主切削刃与进给方向间的夹角,在基面中测量。
其作用体现在影响切削刃工作长度、吃刀抗力、刀尖强度和散热条件。
主偏角越小,吃刀抗力越大,切削刃工作长度越长,散热条件越好。
选择原则是:工件粗大刚性好时,可取小值;车细长轴时为了减少径向切削抗力,以免工件弯曲,宜选取较大的值。
常用在15°到90°之间。
(4)、副偏角κ 'r 副切削刃与进给反方向间的夹角,在基面中测量。
刀具角度的功用与选择
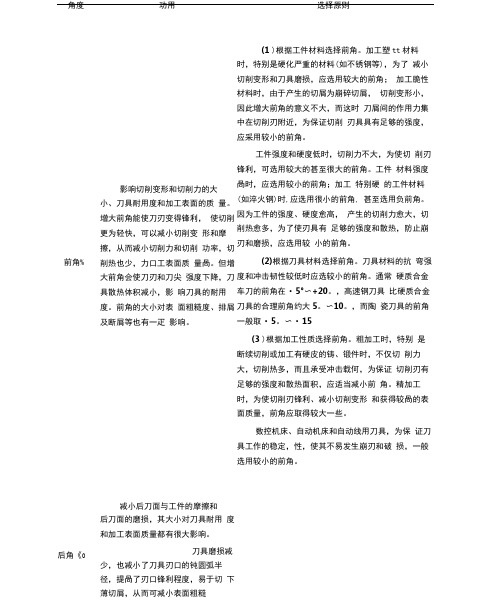
(1 )根据工件材料选择前角。
加工塑tt 材料 时,特别是硬化严重的材料(如不锈钢等),为了 减小切削变形和刀具磨损,应选用较大的前角; 加工脆性材料时,由于产生的切屑为崩碎切屑, 切削变形小,因此增大前角的意义不大,而这时 刀屑间的作用力集中在切削刃附近,为保证切削 刃具具有足够的强度,应采用较小的前角。
工件强度和硬度低时,切削力不大,为使切 削刃锋利,可选用较大的甚至很大的前角。
工件 材料强度咼时,应选用较小的前角;加工 特别硬 的工件材料(如淬火钢)时,应选用很小的前角, 甚至选用负前角。
因为工件的强度、硬度愈高, 产生的切削力愈大,切削热愈多,为了使刃具有 足够的强度和散热,防止崩刃和磨损,应选用较 小的前角。
(2)根据刀具材料选择前角。
刀具材料的抗 弯强度和冲击韧性较低时应选较小的前角。
通常 硬质合金车刀的前角在・5°〜+20。
,高速钢刀具 比硬质合金刀具的合理前角约大5。
〜10。
,而陶 瓷刀具的前角一般取・5。
〜・15 (3 )根据加工性质选择前角。
粗加工时,特别 是断续切削或加工有硬皮的铸、锻件时,不仅切 削力大,切削热多,而且承受冲击载何,为保证 切削刃有足够的强度和散热面积,应适当减小前 角。
精加工时,为使切削刃锋利、减小切削变形 和获得较咼的表面质量,前角应取得较大一些。
数控机床、自动机床和自动线用刀具,为保 证刀具工作的稳定,性,使其不易发生崩刃和破 损,一般选用较小的前角。
角度功用 选择原则 减小后刀面与工件的摩擦和 后刀面的磨损,其大小对刀具耐用 度和加工表面质量都有很大影响。
后角《0刀具磨损减 少,也减小了刀具刃口的钝圆弧半 径,提咼了刃口锋利程度,易于切 下薄切屑,从而可减小表面粗糙 前角%影响切削变形和切削力的大 小、刀具耐用度和加工表面的质 量。
增大前角能使刀刃变得锋利, 使切削更为轻快,可以减小切削变 形和摩擦,从而减小切削力和切削 功率,切削热也少,力口工表面质 量咼。
车刀种类和刀刃角度选取原则

正交平面参考系
1.正交平面参考系时各参考面 :(右图)
——过切削刃选定点平行或垂直刀具安装面(或轴线)的平面。
——过切削刃选定点与 切削刃相切并垂直于基面的平面。
切削平面ps
正交平面po
基面pr
2. 刀具的标注角度
前角γo ——在主切削刃选定点的正交平面po内,前刀面与基面之间的夹角。 后角αo ——在正交平面po内,主后刀面与切削平面之间的夹角。
3.在一定切削条件下的基本选择方法 :
1)前角和前刀面形状的选择
5)刃倾角的选择
3)主偏角、副偏角的选择
2)后角及形状的选择
4)刀尖形状的选择
1.前角和前刀面形状的选择 (1) 前角的选择: 在选择刀具前角时首先应保证刀刃锋利,同时也要兼顾刀刃的强度与耐用度。 刀具前角的合理选择,主要由刀具材料和工件材料的种类与性质决定。
三分手艺、七分刀
徒弟的手、师傅的刀
重要性
1.磨刀步骤(图a~d)
(a) (b) (c) (d) 图a~d 刃磨外圆车刀的一般步骤 a)磨前刀面 b)磨主后刀面 c)磨副后刀面 d)磨刀尖圆弧
C、负前角平面型 (右图) 特点:切削刃强度较好, 但刀刃较钝,切削变形大。 主要用于硬脆刀具材料。加工高强度高硬度材料,如淬火钢。 图示类型负前角后部加有正前角,有利于切屑流出。
刀具几何参数的合理选择

主偏角选择的具体原则 如下:
1.根据加工工艺系统刚性选择 粗加工、半精加工和工艺系统刚性不足时,为减小背 向力,减小振动,提高刀具耐用度,应选用较大主偏角, 一般主偏角为60 o~75 o。 2.根据加工材料选择 在加工高强度、高硬度材料时,为减轻单位长度切削 刃上的负荷,改善刀尖的散热条件,提高刀具强度和寿命, 应选取较小主偏角。 3.根据加工表面形状要求选择 在车阶梯轴时,选择主偏角=90o~92o;需要用一把刀 车外圆、车端面和倒角时,应选择主偏角=45o的车刀。
金属切削加工
刀具几何参数的合理选择
刀具的几何参数主要包括:刀具角度、前面与后面型式、 切削刃与刃口形状等。
刀具合理几何参数——是指在保证加工质量的前提下, 能够获得最高的刀具寿命,从而达到提高生产效率、降低生 产成本的刀具几何参数。
1.1前角和前面型式的选择
1.前角的选择 增大前角,切削刃锋利,切削变形减小、切削力减小、 切削温度降低、刀具磨损减小、加工表面质量提高。但若前 角过大,刀具刚度和强度降低,散热条件变差,切削温度高, 刀具易磨损或破损,刀具寿命低。总结正、反两方面的影响, 前角应有一个最佳值。 选择前角的原则:“固中求锐”。 (1)按工件材料选—— 切塑性材料时,应选较大前角; 切脆性材料,宜选较小前角。材料强度和硬度越高,前角越 小,有时甚至取负值。 (2)按刀具材料选——高速钢刀具材料的抗弯强度、抗 冲击韧性高,可选取较大的前角;硬质合金材料的抗弯强度 较低、脆性大,故前角应小些;陶瓷刀具材料的强度和韧性 更低、脆性更大,故前角应更小些。
2.前面型式的选择
(1)正前角平面型(图4.19a)——特点是结构简单、 制造容易、刀刃锋利,但刀尖强度较低、散热能力较差。
(2)正前角带倒棱型(图4.19b)——提高刀具刃口强 度、改善散热条件、增强刀具耐用度。
第十章 刀具合理几何参数的选择

第一节 前角及前刀面形状的选择
三、带卷屑槽的前刀面形状及其参数的选择
2、直线形卷屑槽 直线形卷屑槽的槽底角,对切屑的卷曲变形由直接 的影响。 一般取槽底角等于 110°~130° 3、全圆弧形卷屑槽 可获得较大的前角,而不至于使切削刃部分强度影 响很大。 4、卷屑槽长度Wn对切屑变形影响很大影响: Wn小,易断屑,太小,切屑飞溅; Wn大, 不易断屑。 一般取Wn=(7~10)f
后刀面
刀面
第二节 后角的选择
减小后角、设臵消振棱,可提高工艺系统刚性、提 高加工表面粗糙度的主要原因: a :增加了后刀面与已加工表面之间的接触面积, 可以产生同振动位移方向相反的摩擦阻力; b:对已加工表面起一定的烫压作用。
(3)对尺寸精度要求较高的刀具,宜采用较小的 后角。原因:NB一定时,较小的后角可使刀具 耐用度提高(如前图10-8所示),切削尺寸稳定。 车削钢和铸铁时,后角一般取4°~ 6°;切断刀副后 角一般取1°~ 2°。见图10-10所示。
第二节 后角的选择
后角数值合理与否直接影响已加工表面 的质量、刀具使用寿命和生产率。 后角的功用 ①影响后刀面与加工表面之间的摩擦
② 影响加工工件的精度 ③影响刀具耐用度和刃口的强度
第二节 后角的选择
一、增大后角,可提高刀具耐用度的原因
1、增大后角,可减小弹性恢复层与后到面的接触 长度,因而减小后刀面的摩擦与磨损; 2、后角增大,楔角减小,刀刃钝圆半径减小,可 减小工件表面的弹性恢复; 3、在磨损标准VB一定的情况下,后角的增大,可 使刀具磨去较大体积的刀具材料,因而增加了刀 具寿命。 后角太大时,由于楔角的减小,将消弱切削刃 的强度。 如下图所示
下,能够获得最高刀具耐用度,达到提高效率或
降低生产成本的几何参数。
收藏!刀具5个角度选择基础
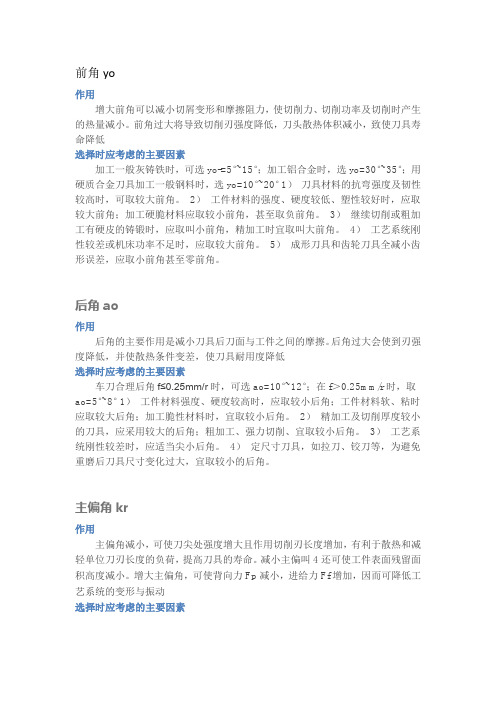
前角yo作用增大前角可以减小切屑变形和摩擦阻力,使切削力、切削功率及切削时产生的热量减小。
前角过大将导致切削刃强度降低,刀头散热体积减小,致使刀具寿命降低选择时应考虑的主要因素加工一般灰铸铁时,可选yo-=5°~15°;加工铝合金时,选yo=30°~35°;用硬质合金刀具加工一般钢料时,选yo=10°~20° 1)刀具材料的抗弯强度及韧性较高时,可取较大前角。
2)工件材料的强度、硬度较低、塑性较好时,应取较大前角;加工硬脆材料应取较小前角,甚至取负前角。
3)继续切削或粗加工有硬皮的铸锻时,应取叫小前角,精加工时宜取叫大前角。
4)工艺系统刚性较差或机床功率不足时,应取较大前角。
5)成形刀具和齿轮刀具全减小齿形误差,应取小前角甚至零前角。
后角ao作用后角的主要作用是减小刀具后刀面与工件之间的摩擦。
后角过大会使到刃强度降低,并使散热条件变差,使刀具耐用度降低选择时应考虑的主要因素车刀合理后角f≤0.25mm/r时,可选ao=10°~12°;在f>0.25mm/r时,取ao=5°~8° 1)工件材料强度、硬度较高时,应取较小后角;工件材料软、粘时应取较大后角;加工脆性材料时,宜取较小后角。
2)精加工及切削厚度较小的刀具,应采用较大的后角;粗加工、强力切削、宜取较小后角。
3)工艺系统刚性较差时,应适当尖小后角。
4)定尺寸刀具,如拉刀、铰刀等,为避免重磨后刀具尺寸变化过大,宜取较小的后角。
主偏角kr作用主偏角减小,可使刀尖处强度增大且作用切削刃长度增加,有利于散热和减轻单位刀刃长度的负荷,提高刀具的寿命。
减小主偏叫4还可使工件表面残留面积高度减小。
增大主偏角,可使背向力Fp减小,进给力Ff增加,因而可降低工艺系统的变形与振动选择时应考虑的主要因素1)在工艺系统刚性允许的条件下,应采用较小的主偏角。
如系统刚性较好时(Lw/dw<6),可取kr=30°~45°;当系统刚性较差时(Lw/dw=6~12),取kr=60°~75°;车削细长轴时(Lw/dw>12),取kr90°~93°2)加工很硬的材料时,应取较小的主偏角。
车刀切削部分的四个基本角度
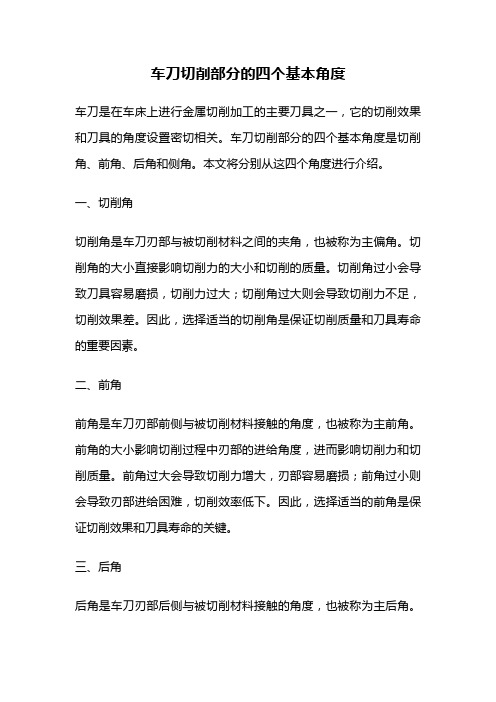
车刀切削部分的四个基本角度车刀是在车床上进行金属切削加工的主要刀具之一,它的切削效果和刀具的角度设置密切相关。
车刀切削部分的四个基本角度是切削角、前角、后角和侧角。
本文将分别从这四个角度进行介绍。
一、切削角切削角是车刀刃部与被切削材料之间的夹角,也被称为主偏角。
切削角的大小直接影响切削力的大小和切削的质量。
切削角过小会导致刀具容易磨损,切削力过大;切削角过大则会导致切削力不足,切削效果差。
因此,选择适当的切削角是保证切削质量和刀具寿命的重要因素。
二、前角前角是车刀刃部前侧与被切削材料接触的角度,也被称为主前角。
前角的大小影响切削过程中刃部的进给角度,进而影响切削力和切削质量。
前角过大会导致切削力增大,刃部容易磨损;前角过小则会导致刃部进给困难,切削效率低下。
因此,选择适当的前角是保证切削效果和刀具寿命的关键。
三、后角后角是车刀刃部后侧与被切削材料接触的角度,也被称为主后角。
后角的大小影响切削过程中刃部的切削深度,进而影响切削力和切削质量。
后角过大会导致切削力增大,刃部容易磨损;后角过小则会导致刃部切削深度不足,切削效果差。
因此,选择适当的后角是保证切削效果和刀具寿命的关键。
四、侧角侧角是车刀刃部侧面与被切削材料接触的角度,也被称为主侧角。
侧角的大小影响切削过程中的切削力和切削质量。
侧角过大会导致切削力增大,刀具容易破碎;侧角过小则会导致切削力不足,切削效率低下。
因此,选择适当的侧角是保证切削质量和刀具寿命的关键。
总结车刀切削部分的四个基本角度,即切削角、前角、后角和侧角,是影响车刀切削效果和刀具寿命的重要因素。
选择适当的角度可以保证切削质量和刀具寿命,同时减少切削力和提高切削效率。
因此,在进行车刀切削加工时,需要根据被切削材料的性质和切削要求来合理设置这四个角度,以获得最佳的切削效果。
刀具切削角度及其选择

刀具切削角度及其选择
刀具的切削角度及其作用(如图) 刃倾角
向旋转
1-
主偏角副偏角。
副前角。
副后角。
后角前角
切削表面已加工表面
车刀
前角r 前面经过主切削刃与基面的夹角,在主截面内测出。
它影响
切屑变形和切屑与前面的摩擦及刀具强度
副前角r 。
前面经过副切削刃与基面的夹角,在副截面内测出
后角 a 主后面与切削平面的夹角,在主截面内测出。
用来减少主后面与工件的摩擦
副后角a 。
副后面与能通过副切削刃垂直于基面的平面之间的夹角,
在副截面内测出。
用来减少副后面与已加工表面的摩擦
主偏角 k 主切削刃与被加工表面(走刀方向)之间的夹角
当吃刀深度和走刀力量一定时,改变主偏角可以使切屑
变薄或变厚,影响散热 情况和切削力的变化
副偏角 k 。
副切削刃与已加工表面(走刀方向)之间的夹角。
它可
以避免副切削刀与已加工表面摩擦,影响已加工表面粗。
- 1、下载文档前请自行甄别文档内容的完整性,平台不提供额外的编辑、内容补充、找答案等附加服务。
- 2、"仅部分预览"的文档,不可在线预览部分如存在完整性等问题,可反馈申请退款(可完整预览的文档不适用该条件!)。
- 3、如文档侵犯您的权益,请联系客服反馈,我们会尽快为您处理(人工客服工作时间:9:00-18:30)。
刀具角度的选择
摘要:刀具合理几何参数的选择是切削刀具理论与实践的重要课题。
中国有句谚语说:“工欲善其事,必先利其器”,刀具正是切削
加工的直接作用工具,它的完善程度对切削加工的现状和发展起着决
定性的作用。
由于刀具结构和几何参数的改进,刀具使用寿命每隔十
年几乎提高二倍。
刀具的合理几何参数包含以下四个方面基本内容:
1.刃形,
2.切削刃刃区的剖面型式及参数,
3.刀面型式及参数,
4.刀具角度。
所以在此我从刀具四个几何参数中选取刀具角度做专题报
告,探讨如何正确的选取刀具的角度。
正文:刀具切削部分有6个基本角度,它们是前角γO、后角αo、副后角αoˊ、主偏角κr、副偏角κr ˊ和刃倾角λs。
如图所示。
主偏角κr:主切削刃在基面上的投影与进给运动速度v f方向之间的夹角。
副偏角κr ˊ :副切削刃在基面上的投影与进给方向的夹角。
前角γO :主切削刃上任意一点的前角,是在主剖面内,该点的前刀面与基面之间的夹角。
后角αo : 主切削刃上任意一点的后角,是在主剖面内,该点后面与切削平面之间的夹角。
副后角αoˊ :在副剖面内,该点副后刀面与切削平面之间的夹角。
刃倾角λs : 主切削刃与基面之间的夹角。
一、前角、后角的选择
1、前角和后角的作用
车刀是否锋利主要取决于前角的大小,它直接影响切削能否顺利地切下来。
增大前角可以减小切削变形,并减少切屑与车刀前面的摩擦,从而使切削力减少,切削热降低,所以前角应尽可能选择大一些。
但前角不能过大,否则会降低道具的强固性。
后角的作用主要是减少刀具的后面与工件之间的摩擦,减少刀具后面的摩擦,提高刀的耐用度,但后角过大也会削弱刀具的强度。
2、前角、后角选择的原则
(1)加工硬度高、强度大以及脆性材料时,应选择较小的前角和后角,加工硬度低,强度小及较软的材料时,应选较大的前角和后角。
(2)粗加工时,一般工件表面不规则且工余量大,选取较小的前角、后角一便增加刀头的强度。
精加工时,选取较大的前角和后角,使刀具锋利并减少后刀面与工件的摩擦,以利于工件的精度和光洁度。
(3)刀具材料韧性差时(例如硬质合金刀具),为了防止崩刀,前角
应取小,刀具材料韧性好时(例如高速钢刀具)前角可取大一些。
(4)机床,夹具,刀具工件系统刚性较差时,前角取大些,以减小切削力,后角取小些,用来增大后刀面与工件间的接触面积,有利于减少震动。
二、主偏角κr,与副偏角κr ˊ的选择
1、主偏角的作用
(1)在相同的走刀量的切削深度加工下,减少主偏角可使切屑变薄,刀刃参加切削的长度增加,刀刃的散热面积增大,散热情况得
到改善。
而且刀尖角增大,相应的提高了刀具的强度,若以减
小主偏角对延长刀具寿命有利,
(2)主偏角影响切削力的分布配,当减小主偏角时,径向力增大,轴向力减小;当增大主偏角时,径向力减小,轴向力增大。
在实际生产中,通常采用主偏角45-75度,而当加工细长轴时,常用75度、90度或大于90度的主偏角,为了减小径向力,使工件不至于弯曲,切削平稳。
2、副偏角的作用
主要是减小车刀与已加工表面的摩擦,同时它的大小直接影响已加工表面的光洁度,一般用3-10度。
二、刃倾角λs的选择
刃倾角对刀刃的强度有直接的影响,而且能控制切削的流出方向,当刃倾角为正值时,刀头强度好,切削流向工作已加工表面,所以适合粗加工。
在精加工时,我们希望切削部划伤加工表面,所以刃倾角采用负值较为合适。
四、总结
最后我们以北京通用机械厂总结的选择角度的经验,做小结。
将加工材料可以分为脆性材料(灰口铸铁、可锻铸铁、黄铜等),塑性材料(普通钢材、合金钢、紫铜等)和特硬材料(淬火钢、高锰钢等),刀具主要角度变化规律如下:
为了适应粗、精加工的不同特点,刀具角度应作如下变化:
1、一般情况下,前角和后角的变化规律是粗加工前、后角都小,
而精加工前后角都大。
2、粗加工时,也可选用较大的前角,但应加负倒棱,并取正刃倾
角。
3、精加工时,可增大刀尖圆弧半径或增大修光刀。
参考文献:
【1】《金属切削技术加工问答》郑文虎编,机械工业出版社,2013年
【2】《金属切削技术》华中工学院编,湖北人民出版社,1975年6月。