火力发电厂烟气脱硫技术(FGD)
烟气脱硫FGD设备及工艺原理讲义
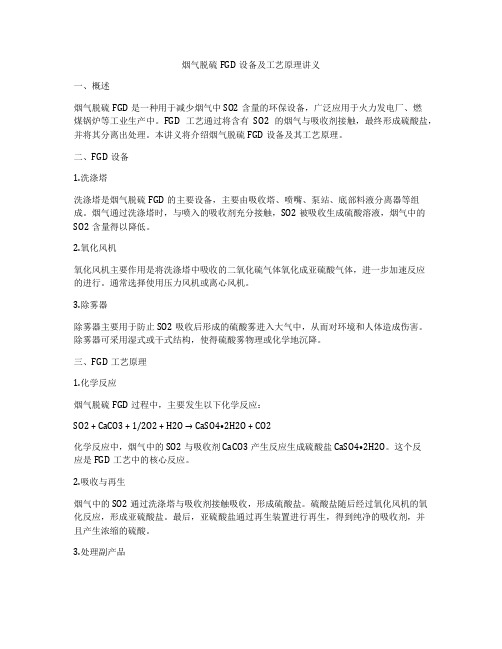
烟气脱硫FGD设备及工艺原理讲义一、概述烟气脱硫FGD是一种用于减少烟气中SO2含量的环保设备,广泛应用于火力发电厂、燃煤锅炉等工业生产中。
FGD工艺通过将含有SO2的烟气与吸收剂接触,最终形成硫酸盐,并将其分离出处理。
本讲义将介绍烟气脱硫FGD设备及其工艺原理。
二、FGD设备1.洗涤塔洗涤塔是烟气脱硫FGD的主要设备,主要由吸收塔、喷嘴、泵站、底部料液分离器等组成。
烟气通过洗涤塔时,与喷入的吸收剂充分接触,SO2被吸收生成硫酸溶液,烟气中的SO2含量得以降低。
2.氧化风机氧化风机主要作用是将洗涤塔中吸收的二氧化硫气体氧化成亚硫酸气体,进一步加速反应的进行。
通常选择使用压力风机或离心风机。
3.除雾器除雾器主要用于防止SO2吸收后形成的硫酸雾进入大气中,从而对环境和人体造成伤害。
除雾器可采用湿式或干式结构,使得硫酸雾物理或化学地沉降。
三、FGD工艺原理1.化学反应烟气脱硫FGD过程中,主要发生以下化学反应:SO2 + CaCO3 + 1/2O2 + H2O → CaSO4•2H2O + CO2化学反应中,烟气中的SO2与吸收剂CaCO3产生反应生成硫酸盐CaSO4•2H2O。
这个反应是FGD工艺中的核心反应。
2.吸收与再生烟气中的SO2通过洗涤塔与吸收剂接触吸收,形成硫酸盐。
硫酸盐随后经过氧化风机的氧化反应,形成亚硫酸盐。
最后,亚硫酸盐通过再生装置进行再生,得到纯净的吸收剂,并且产生浓缩的硫酸。
3.处理副产品FGD工艺除了可以减少烟气中SO2的含量外,还能产生有价值的副产品硫酸。
硫酸可作为化肥原料或者工业原料使用,具有较高的经济价值。
以上就是对烟气脱硫FGD设备及工艺原理的简要介绍,FGD工艺在环保和资源利用方面具有重要意义,对减少大气污染和促进资源回收利用具有重要作用。
烟气脱硫FGD设备及工艺原理四、FGD工艺的应用1.环保效果烟气脱硫FGD工艺可以有效降低燃煤电厂和工业锅炉等设施排放的二氧化硫,减少大气中的酸雨、酸性沉积物等问题,保护生态环境,改善空气质量。
电厂环保——烟气脱硫脱硝

主要性能: (1)脱硫效率高,≥95%;
至只有欧洲现行标准的一半 ) 烟尘 30mg/m3
排放总量控制————产生史上最严厉标准
中国燃煤SO2污染现状
中国的大气污染属典型的煤烟型污染,以粉尘和酸雨危害最大,酸雨问题实质 就是SO2污染问题。
中国SO2污染经济损失(2005) (单位:109元人民币)
SO2控制区 控酸雨制区 “两控区” 两控区之外
以上是煤燃烧生成烟气中的SO2,现在对烟气脱硫,以脱 硫90%计算,则最后排放SO2: 160吨*10%=16吨
二、烟气排放标准
GB 13223-2011最新《火电厂大气污染物排放标准》, 见附件一
史上最严厉的排放标准: 2012年1月1日之前的锅炉,在2014年7月1日起
SO2 200mg/m3(2012年1月1日锅炉:100mg/m3) NO2 100mg/m3(比美国现行标准低35mg/m3,甚
要求听讲者对锅炉的工作过程与主要设备有基本了解。
一、燃煤产生的污染
燃煤产生的烟气污染物:SO2、NOx、CO2、Hg等
燃煤烟气中SO2的量:
以燃烧10000吨煤为例计算,产生的SO2: 10000吨*1%(煤含硫量)*2(SO2是S重量的2倍) *80%(煤中S转化为SO2的百分率)=160吨
E1 德国比晓夫公司
鲁奇·能捷斯·比晓夫公司和鲁奇能源环保公司于2002年12月 合并为鲁奇能源环保股份有限公司(LLB)。
国外燃煤电厂烟气脱硫技术综述

国外燃煤电厂烟气脱硫技术综述【摘要】国外燃煤电厂烟气脱硫技术取得了较大的发展。
湿法脱硫技术使用较广,约占85%左右,其它如喷雾干燥式脱硫技术等也有较好的业绩。
美国、德国、日本等工业发达国家的燃煤电厂普遍采用了脱硫措施,并制定了严格的环境保护法律、法规;对燃煤电厂规定了烟气的SO2排放标准,减轻了对周围环境的污染。
【关键词】燃煤电厂环境保护脱硫技术烟气SO21.国外常用的脱硫技术近年来,世界各发达国家在烟气脱硫(Flue Gas Desulfurization,FGD)方面均取得了很大的进展,美国、德国、日本等发达工业国家计划在2000年前完成200610MW的FGD处理容量。
目前国际上已实现工业应用的燃煤电厂烟气脱硫技术主要有:(1)湿法脱硫技术,占85%左右,其中石灰-石膏法约占36.7%,其它湿法脱硫技术约占48.3%;(2)喷雾干燥脱硫技术,约占8.4%;(3)吸收剂再生脱硫法,约占3.4%;(4)炉内喷射吸收剂/增温活化脱硫法,约占1.9%;(5)海水脱硫技术;(6)电子束脱硫技术;(7)脉冲等离子体脱硫技术;(8)烟气循环流化床脱硫技术等。
以湿法脱硫为主的国家有:日本(约占98%)、美国(约占92%)和德国(约占90%)等。
1.1 湿法石灰石/石灰烟气脱硫工艺技术这种技术在70年代因其投资大、运行费用高和腐蚀、结垢、堵塞等问题而影响了其在火电厂中的应用,经过多年的实践和改进,工作性能和可靠性大为提高,投资与运行费用显著减少。
突出的优点是:(1)脱硫效率高(有的装置Ca/S=1时,脱硫效率大于90%);(2)吸收剂利用率高,可大于90%;(3)设备运转率高(可达90%以上)。
目前从设计上综合考虑加强反应控制,强制氧化和加入氧化剂,从而减少吸收塔和附属设备体积、降低电耗,减小基建投资和运行费用;选用耐腐蚀材料,提高吸收塔及出口烟道、挡板、除雾装置等处的使用寿命,提高气液传质效率,建造大尺寸的吸收塔等因素,对此项技术作了进一步改进和提高。
火电厂烟气脱硝技术介绍

火电厂烟气脱硝技术介绍据统计,我国大气污染物中NOx 60 %来自于煤的燃烧, 其中, 火电厂发电用煤又占了全国燃煤的70%。
2000 年我国火电厂氮氧化物排放量控制在500万t 左右,按照目前的排放控制水平,到2020 年,氮氧化物排放量将达到1 000 万t 以上。
面对严峻的环保形势,我国于1991 年制定了第一部《火电厂污染物排放标准》,在此后的12 年间,历经两次修订(1996 版和2003 版) ,排放标准日益严格。
2004 年,国家允许的氮氧化物最高排放浓度(标准状态,下文称为标) 为450 mg/ m3 (V daf > 20 %) 。
此排放限值已接近于目前炉内低氮燃烧技术所能达到的最高水平,若要进一步降低NOx 的排放浓度,只有安装烟气脱硝系统。
1 脱硝技术概况1.1 NOx 的形成机理NOx 是NO 和NO2 的统称,燃煤电厂烟气中的NOx 主要是煤燃烧产生的。
通常,燃烧生成的NOx 由超过90 %的NO 和小于10 %的NO2 组成。
依据氮氧化物生成机理,可分为热力型、燃料型和快速型NOx 3类,其中快速型NOx 生成量很少,可以忽略不计。
热力型NOx 是指当炉膛温度在1 350 ℃以上时,空气中的氮气在高温下被氧化生成NOx ,当温度足够高时,热力型NOx 可达20 %。
燃料型NOx 指的是燃料中的有机氮化物在燃烧过程中生成的NOx ,其生成量主要取决于空气燃料的混合比。
燃料型NOx 约占NOx 总生成量的75%~90%。
1.2 低NOx 燃烧技术对应NOx 的两种主要生成机理,炉内脱硝技术主要从两方面入手降低NOx 生成:(1) 降低炉内燃烧温度以减少热力型NOx 生成; (2) 营造煤粉着火区域的还原性气氛以减少燃料型NOx 生成。
在具体的应用上,往往是两种技术的综合,既降低燃烧温度,又降低着火区域的氧气浓度。
低NOx 燃烧技术主要包括低氧燃烧、分级燃烧、烟气再循环、采用低NOx 燃烧器等。
烟气脱硫(FGD)设备及工艺原理

2.按脱硫剂分类
目前开发的多种烟气脱硫技术,尽管设备构造和工艺流程各不 相同,但基本原理都是以碱性物质作SO2的吸收剂。
以石灰石、生石灰为基础的钙法 按 脱 硫 剂 分 类 以氧化镁为基础的镁法
以合成氨为基础的氨法
以有机碱为基础的碱法 以亚硫酸钠、氢氧化钠为基础的钠法
2.国家对SO2的治理要求
法律的要求: 1995年修订的《中华人民共和国大气污染防治法》提出:在“两 区”内的火电厂新建或已建项目不能采用低硫煤的,必须建设配套脱 硫、除尘装置。 国家污染物排放标准的要求: 《火电厂大气污染物排放标准》(GB13223-1996),对1997年1月1日 起新、扩、改建火电厂,在实行全厂排放总量控制的基础上,增加了 烟囱二氧化硫排放浓度限制。 国务院对“两控区”内火电厂二氧化硫控制的要求:
以湿法脱硫为主的国家有:日本(约占98%)、美 国(约占92%)和德国(约占90%)等。
炉内
活化
CaCO3 → CaO + CO2 CaO + SO2 + 1/2 O2→ CaSO4 CaO+SO3 → CaSO4
CaO + H2O → Ca(OH)2 Ca(OH)2 +SO2 → CaSO3 + H2O CaSO3 + 1/2 O2 → CaS。
3、常用的脱硫技术
近年来,世界各发达国家在烟气脱硫(FGD)方面均取得了很大的进 展,美国、德国、日本等发达工业国家计划在2000年前完成200-- 610 MW的FGD处理容量。 目前国际上已实现工业应用的燃煤电厂烟气脱硫技术主要有:
(1)湿法脱硫技术,占85%左右,其中石灰-石膏法约占36.7%,其它 湿法脱硫技术约占48.3%; (2)喷雾干燥脱硫技术,约占8.4%; (3)吸收剂再生脱硫法,约占3.4%; (4)炉内喷射吸收剂/增温活化脱硫法,约占1.9%; (5)海水脱硫技术; (6)电子束脱硫技术; (7)脉冲等离子体脱硫技术; (8)烟气循环流化床脱硫技术等。
火电厂及燃煤电厂烟气脱硫脱硝技术简介

总计
农作物 森林 人体健康 合计
12.27 0.00 65.02 77.29
167.70 775.80 56.18 999.68
179.97 775.67 88.37
217.67 775.80 171.87 1165.3
三、烟气脱硫技术概况
脱硫反应塔
● 交错布置的喷淋层 3~5层喷嘴; 设3~5台循环泵。
喷嘴
● LLB除雾器 高效两级人字形除雾器; 设计成可更换的组件,便于维护; 除雾器布置在塔顶,节约场地。
除雾器结构
人字形除雾器
● 浆液池脉冲悬浮系统 LLB专利技术; 塔浆池采用扰动搅拌; 防止塔底浆液沉积; 能耗比机械搅拌低; 提高可用率和运行安全性; 提高石灰石浆液利用率; 便于维护。
(2)吸收剂耗量低,钙硫比≤1.03; (3)石膏品位高,含水率≤10%。
系统流程图
主要设备
●吸收塔
上部浆液PH值低,提高氧化效率; 加入氧化空气,增大石灰石溶解度; 石膏排出点合理; 特殊设计的吸收塔喷嘴,不易堵塞; 采用独特的吸收池分隔管件,将氧化区和新 鲜浆液区分开,有利于SO2的充分吸收并快 速生成石膏,而且生成石膏的晶粒大; 采用专利技术的脉冲悬浮搅拌系统; 净化的烟气可通过冷却塔或安装在吸收塔顶 部的烟囱排放。
PH值下运行,提供了很好的氧化条件,下部有新加入的吸收 剂,再由泵运到喷淋层,不会产生上下两层混合的问题; ➢ (4)LLB公司拥有专利技术的脉冲悬浮系统,冲洗吸收塔的 水平池底时,无论多大尺寸的吸收塔都不会发生阻塞和石膏的 沉降,吸收塔不需要搅拌器,长期关机后也可无障碍启动;
主要性能: (1)脱硫效率高,≥95%;
HSO42 HSO4
C a2SO 42K SP 2C aSO 42H 2O (s)
火力发电厂脱硫脱硝工艺知识讲解
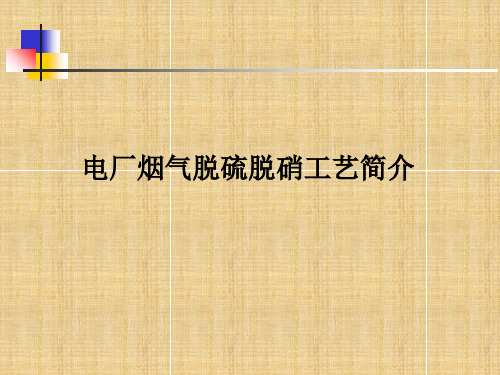
排放总量控制————产生史上最严厉标准
中国燃煤SO2污染现状
中国的大气污染属典型的煤烟型污染,以粉尘和酸雨危害最大,酸雨问题实质 就是SO2污染问题。
中国SO2污染经济损失(2005) (单位:109元人民币)
SO2控制区 控酸雨制区 “两控区” 两控区之外
巴威公司对某500MW机组的设计比较(入口SO2浓度1800ppm,脱硫率95%)
项目
Ca/S L/G(L/Nm3) 液气比
烟气压降 (Pa) 泵功率(KW) 风机功率(KW) 总功率(KW)
采用托盘 1.03 14.5
1240 2760 6860 9620
不采用托盘 1.03 20
870 3750 6580 10330
(2)吸收剂耗量低,钙硫比≤1.03; (3)石膏品位高,含水率≤10%。
系统流程图
主要设备
●吸收塔
上部浆液PH值低,提高氧化效率; 加入氧化空气,增大石灰石溶解度; 石膏排出点合理; 特殊设计的吸收塔喷嘴,不易堵塞; 采用独特的吸收池分隔管件,将氧化区和新 鲜浆液区分开,有利于SO2的充分吸收并快 速生成石膏,而且生成石膏的晶粒大; 采用专利技术的脉冲悬浮搅拌系统; 净化的烟气可通过冷却塔或安装在吸收塔顶 部的烟囱排放。
电厂烟气脱硫脱硝工艺简介
第一部分 烟气脱硫技术
一、燃煤产生的污染 二、烟气排放标准 三、烟气脱硫技术概况 湿法烟气脱硫技术(WFGD技术) 半干法烟气脱硫技术(SDFGD技术)
旋转喷雾干燥法 烟气循环流化床法脱硫 增湿灰循环脱硫(NID)
干法烟气脱硫技术(DFGD技术)
炉膛干粉喷射 高能电子活化氧化法(EBA) 荷电干粉喷射(CDSI)
电厂脱硫工艺

电厂脱硫工艺电厂脱硫工艺多为烟气脱硫(FlueGasDesulfurization,简称FGD)是目前燃煤电厂控制SO2气体排放最有效和应用最广的技术。
电厂烟气脱硫工艺电厂烟气脱硫工艺按脱硫剂及脱硫反应产物的状态可分为湿法、干法及半干法三大类。
1、湿法脱硫工艺世界各国的湿法烟气脱硫工艺流程、形式和机理大同小异,主要是以碱性溶液为脱硫剂吸收烟气中的SO2。
湿法脱硫工艺主要有:石灰石/石灰-石膏法、海水法、双碱法、亚钠循环法、氧化镁法等。
2、干法脱硫工艺工艺用于电厂烟气脱硫始于20世纪80年代初。
干法脱硫工艺主要有:荷电干法吸收剂喷射脱硫法、电子束照射法、吸附法等。
3、半干法脱硫工艺工艺融合了湿法、干法脱硫工艺的优点,具有广阔的应用前景。
半干法脱硫工艺主要有:喷雾干燥法、循环流化床法、增湿灰循环法、烟道喷射法等。
目前烟气脱硫技术以湿法脱硫工艺占主导,同时干法、半干法脱硫工艺也在发展中。
四大电厂烟气脱硫工艺石灰石/石灰-石膏法是技术最成熟、应用最多、运行状况最稳定的方法,其脱硫效率在95%以上。
石灰石/石灰-石膏湿法是300MW及以上机组中最广泛采用的脱硫方式。
世界各国(如德国、日本等)在大型火电厂中,90%以上采用湿式石灰石/石灰-石膏法烟气脱硫工艺。
目前,石灰石/石灰法是世界上应用最多的一种FGD工艺,对高硫煤,脱硫率可在90%以上,对低硫煤,脱硫率可在95%以上。
喷雾干燥法烟气脱硫最先由美国JOY公司和丹麦NiroAtomier公司共同开发的脱硫工艺,20世纪70年代中期得到发展,第1台电站喷雾干燥脱硫装置于1980年在美国北方电网河滨电站投入运行,并在电力工业迅速推广应用。
该工艺目前已基本成熟,在欧洲应用较多,法国、奥地利、丹麦、瑞典、芬兰等国家均建有这种设备。
器,用以脱除烟气中的SO2。
炉内喷钙脱硫技术早在20世纪50年代中期就已开始研究,但由于脱硫效率不高(只有15%~40%),钙利用率低(15%)而被搁置。
FGD 脱硫技术

二
NH3
烟气SO2
化肥
NADS 氨-肥法 ?
新的FGD技术 具有我国自主知识产权
发明专利号:99113403.6 01113415.1 02136906.2 02266994.9
11
氨-肥法之反应原理
氨吸收SO2
碳铵NH4HCO3
吸收
亚硫铵
SO2+xNH3+H2O
(NH4)xH2-xSO3
(钙法:SO2+CaCO3+2H2O=CaSO3.2H2O+CO2) 亚硫酸钙
我国的SO2问题
• SO2排放和酸雨大国 SO2排放量: >2000万吨/年 酸雨损失: • 硫酸和化肥大国 SO2需求: • 硫资源缺乏大国 进口S=300 >1000亿元/年 >2000万吨/年
SO2=600万吨/年
回收烟气SO2 变废为宝、化害为利! 目标:可资源化的FGD技术!
4
烟气脱硫方法
16
氨-肥法特点(2):原料灵活
三种氨源可灵活选择,对北方地区,其比较为:
液氨 分子式 NH3 含量,% N 含量 原料单价,元/吨 单位 N 价格,元/N 运输及储运 NH3 99.5 82 1800 22.6 氨水 NH3 和 H2O 混合物 20-25 16.5-20.5(18) 350 19.8 碳铵 NH4HCO3 21.5 17.0-17.7(17.5) 400 22.8 普通汽(火)车运输 仓库储存
副产品量, 2.6-2.7 吨/吨 SO2 产品-原料差价, -185 元/吨 SO2
(NH4)2SO4, 化肥 可作化肥添加剂, 可 作 玻 璃 生 产 原 高效农用化肥, 但基本抛弃 料,但因质量差, 市场良好, 二次渣或水污染 基本抛弃 600 元/吨 无废渣和水污染 3.8-3.9 2.22 2.1 -280 -1992 +260
烟气脱硫脱硝技术

(2)石灰
• 石灰旳主要成份是CaO,自然界没有天然旳石灰资源。 • 气脱硫使用旳石灰都是将石灰石煅烧后而成旳。
• 石灰旳优劣完全取决于燃烧过程中旳质量控制,不然会 混有大量旳欠烧或过烧旳杂质,影响脱硫效率和运营费用
• 因为煅烧过程是一吸热反应,所以,要消耗一定量燃料, 同则会产生SO2等有害气体。
• 石灰有很强旳吸湿性,遇水后会发生剧烈旳水合反应, 对人体皮肤、眼睛有强烈旳烧灼和刺激作用,应采用措施 预防在石灰旳处理过程中产生旳危害和对环境旳不良影响。
• 石灰作为吸收剂,比石灰心具有更高旳活性,其分子虽比石 灰石几乎小50%,所以、单价质量酌脱硫效率比石灰石高约 一倍,是一种高效旳吸收SO2,同步也能吸收SO3旳脱硫剂。
– 用作脱硫剂旳钠基化合物涉及Na2SO3,Na2CO3、 NaHCO3等
– 应用于湿法洗涤烟气脱硫工艺和用于炉内喷射与管 道喷射等工艺旳脱硫吸收剂,脱硫效果好,而且兼 有一定旳脱氮作用。
– 钠基脱硫剂能够再生,以循环利用。
– 使用钠基脱硫剂旳主要问题是脱硫剂旳起源困难, 价格相对较高;另外,脱硫产物中钠盐易溶于水, 造成灰场水体旳污染。
化法、烟气循环流化床脱硫法
• 脱硫产物处理方式
–回收法
–脱硫剂旳再生使用。 –流程较复杂,运营难度较大,投资和运营费用均较高。
–抛弃法
–设备简朴,操作轻易,投资及运营费用较低。 –废渣需要占用场地堆放,轻易造成二次污染。 –当烟气中SO2浓度较低、脱硫产物无回收价值或投资有限,
且大气污染物排放控制严格时,多采用抛弃法。
• 干法在脱硫效率为70%时.钙硫摩尔比可达2~2.5。
• 湿法脱硫上艺旳脱硫剂利用率最高,达90%以上,干 法脱硫工艺最低,为30%左右。
烟气脱硫技术简述

烟气脱硫技术简述1.1烟气脱硫技术的分类烟气脱硫(Flue Gas Desulfurization,FGD)是世界上唯一大规模商业化应用的脱硫方法,是控制酸雨和二氧化硫污染的最为有效的和主要的技术手段。
目前,世界上各国对烟气脱硫都非常重视,已开发了数十种行之有效的脱硫技术,但是,其基本原理都是以一种碱性物质作为SO2的吸收剂,即脱硫剂。
按脱硫剂的种类划分,烟气脱硫技术可分为如下几种方法。
(1)以CaCO3(石灰石)为基础的钙法;(2)以MgO为基础的镁法;(3)以Na2SO3为基础的钙法;(4)以NH3为基础的氨法;(5)以有机碱为基础的有机碱法。
世界上普遍使用的商业化技术是钙法,所占比例在90%以上。
烟气脱硫装置相对占有率最大的国家是日本。
日本的燃煤和燃油锅炉基本上都装有烟气脱硫装置。
众所周知,日本的煤资源和石油资源都很缺乏,也没有石膏资源,而其石灰石资源却极为丰富。
因此FGD的石膏产品在日本得到广泛的应用。
这便是钙法在日本得到广泛应用的原因。
因此,其他发达国家的火电厂锅炉烟气脱硫装置多数是由日本技术商提供的。
在美国,镁法和钠法得到了较深入的研究,但实践证明,它们都不如钙法。
在我国,氨法具有很好的发展土壤。
我国是一个粮食大国,也是化肥大国。
氮肥以合成氨计,我国的需求量目前达到33Mt/a,其中近45%是由小型氮肥厂生产的,而且这些小氮肥厂的分布很广,每个县基本上都有氮肥厂。
因此,每个电厂周围100km内,都能找到可以提供合成氨的氮肥厂,SO2吸收剂的供应很丰富。
更有意义的是,氨法的产品本身就是化肥,就有很好的应用价值。
在电力界,尤其是脱硫界,还有两种分类方法,一种方法将脱硫技术根据脱硫过程是否有水参与及脱硫产物的干湿状态分为湿法、干法和半干(半湿)法。
另一种分类方法是以脱硫产物的用途为根据,分为抛弃法和回收法。
在我国,抛弃法多指钙法,回收法多指氨法。
下面我们将依据脱硫界的分类,先介绍湿式和干式两种脱硫方法。
火电厂湿法烟气脱硫系统技术(FGD)应用的初步研究

第3 2卷第 l 2期 20 0 7年 l 2月
环境科学与管理
ENVI RONM ENTAL SCI ENCE AND ^ d AGEM匝 NT
V0| 2 l l 3 N 2
De .2 o c o 7
文 章编号 :6 3—1 1 (0 7)2— 1 2— 4 17 22 20 1 0 0 0
为湿法 、 干法 、 半 干法 三大 类 , 主要有 湿式 石 灰石/ 石 膏法 等多种 。
l 湿 式 石 灰 石/ 膏 法 石
目前 , 石灰/ 石灰 石法 是世 界上 应用最 多 的一 种 F D工艺 , 高硫 煤 , 硫率 可 在 9 % 以上 , G 对 脱 0 对低 硫 煤, 脱硫 率可在 9 % 以上 。 在现 有 的电厂 烟 气脱 硫 5 工艺 中 , 式 石 灰 石 ( 灰 ) 涤 工 艺 技 术 最 为 成 湿 石 洗
Th r e e ti we tto u o s Me h d Ha e e mo l c rc Po r S a in Aq e u t o z
D slh r ainytm T cn lg F D)A piainP ei n r td eup ui t ss eh ooy( G z 0 e p l t rl aySu y c o mi
时期 内,G F D将是控制 S 2 O 排放 的主要方 法。文章对烟气脱硫技术进行 了较为全 面的 阐述 , 并对烟气脱硫 装置
在 国 内的应用情况进行 了详 细的介 绍 , 需要装设脱硫 装置的燃煤火力发 电厂可 以起到一定 的指导作 用。 对
关 键 词 : 气脱 硫 ;G 湿 法 ; 烟 FD 石灰 石 一石 膏 中 图分 类 号 : 74 x 8 文 献标 识码 : A
烟气循环流化床脱硫CFB-FGD技术简介

烟气循环流化床脱硫CFB-FGD技术简介1. 概况烟气循环流化床(CFB)脱硫技术在最近几年中已有所发展,不但用户增多,而且系统的烟气处理能力也比过去增大了,达到950,000Nm3/h,用于300MW机组的烟气脱硫系统。
目前,已达到工业化应用的主要有三种流程, 它们是:1.由德国Lurgi公司开发的烟气CFB脱硫技术;2.由德国Wulff公司在Lurgi技术基础上进行改进后的RCFB脱硫技术;3.由丹麦F.L.Smith公司开发的GSA烟气脱硫技术。
早在七十年代初,擅长于冶金工业工程建设的德国Lurgi公司就采用了烟气循环流化技术对炼铝设备的尾气进行处理。
八十年代中期,由于开始对环境质量的严格控制以及政府的有关法规的强行规定,德国的动力工业对烟气脱硫设备有了巨大的需求。
Lurgi公司在原来用于炼铝尾气处理的技术的基础上开发了一种新的适用于锅炉和其它燃烧设备的干法烟气脱硫工艺,即烟气循环流化床脱硫工艺。
这种工艺以循环流化床原理为基础,通过吸收剂的多次再循环,使吸收剂与烟气接触时间增加,一般可达30分钟以上,从而大大提高了吸收剂的利用效率。
这种工艺不但具有干法工艺的许多优点,如流程简单、占地少、投资低以及脱硫副产品呈干态,因而易于处理或综合利用,而且能在很低的钙硫比的情况下(Ca/S=1.1-1.2)达到与湿法工艺相近的脱硫效率(95%)。
德国Wulff公司是一个成立较晚的设计和建造烟气CFB脱硫工程的小型企业。
它的创始人R. Graf原是Lurgi公司在烟气CFB脱硫技术开发方面的主要负责人。
脱离Lurgi公司后自建了Wulff公司,专门从事烟气CFB脱硫技术的开发工作,在Lurgi技术的基础上开发研制了一种叫做回流式烟气循环流化床的烟气CFB脱硫技术,对烟气CFB脱硫技术作了较大的改进,使之更加适用于动力工业(详见后)。
F.L.Smith公司是丹麦最大的工业企业,在水泥工业及散装物料输送机械制造方面享有很高的声誉。
火电厂脱硫的几种方法

火电厂脱硫的几种方法(1)通过对国内外脱硫技术以及国内电力行业引进脱硫工艺试点厂情况的分析研究,目前脱硫方法一般可划分为燃烧前脱硫、燃烧中脱硫和燃烧后脱硫等3类。
其中燃烧后脱硫,又称烟气脱硫(Flue gas desulfurization,简称FGD),在FGD技术中,按脱硫剂的种类划分,可分为以下五种方法:1、以CaCO3(石灰石)为根底的钙法,2、以MgO为根底的镁法,3、以Na2SO3为根底的钠法,4、以NH3为根底的氨法,5、以有机碱为根底的有机碱法。
世界上普遍使用的商业化技术是钙法,所占比例在90%以上。
按吸收剂及脱硫产物在脱硫过程中的干湿状态又可将脱硫技术分为湿法、干法和半干(半湿)法。
A、湿法FGD技术是用含有吸收剂的溶液或浆液在湿状态下脱硫和处理脱硫产物,该法具有脱硫反响速度快、设备简单、脱硫效率高等优点,但普遍存在腐蚀严重、运行维护费用高及易造成二次污染等问题。
B、干法FGD技术的脱硫吸收和产物处理均在干状态下进展,该法具有无污水废酸排出、设备腐蚀程度较轻,烟气在净化过程中无明显降温、净化后烟温高、利于烟囱排气扩散、二次污染少等优点,但存在脱硫效率低,反响速度较慢、设备庞大等问题。
C、半干法FGD技术是指脱硫剂在枯燥状态下脱硫、在湿状态下再生(如水洗活性炭再生流程),或者在湿状态下脱硫、在干状态下处理脱硫产物(如喷雾枯燥法)的烟气脱硫技术。
特别是在湿状态下脱硫、在干状态下处理脱硫产物的半干法,以其既有湿法脱硫反响速度快、脱硫效率高的优点,又有干法无污水废酸排出、脱硫后产物易于处理的优势而受到人们广泛的关注。
按脱硫产物的用处,可分为抛弃法和回收法两种。
1脱硫的几种工艺(1)石灰石——石膏法烟气脱硫工艺石灰石——石膏法脱硫工艺是世界上应用最广泛的一种脱硫技术,日本、德国、美国的火力发电厂采用的烟气脱硫装置约90%采用此工艺。
它的工作原理是:将石灰石粉加水制成浆液作为吸收剂泵入吸收塔与烟气充分接触混合,烟气中的二氧化硫与浆液中的碳酸钙以及从塔下部鼓入的空气进展氧化反响生成硫酸钙,硫酸钙到达一定饱和度后,结晶形成二水石膏。
FGD工程实施的过程
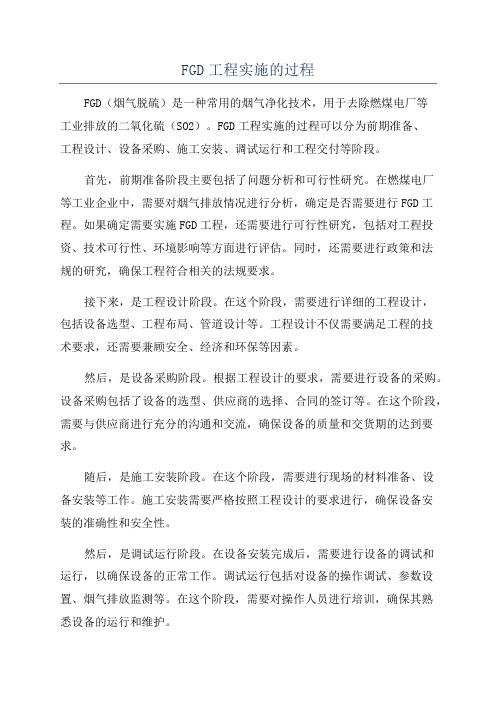
FGD工程实施的过程FGD(烟气脱硫)是一种常用的烟气净化技术,用于去除燃煤电厂等工业排放的二氧化硫(SO2)。
FGD工程实施的过程可以分为前期准备、工程设计、设备采购、施工安装、调试运行和工程交付等阶段。
首先,前期准备阶段主要包括了问题分析和可行性研究。
在燃煤电厂等工业企业中,需要对烟气排放情况进行分析,确定是否需要进行FGD工程。
如果确定需要实施FGD工程,还需要进行可行性研究,包括对工程投资、技术可行性、环境影响等方面进行评估。
同时,还需要进行政策和法规的研究,确保工程符合相关的法规要求。
接下来,是工程设计阶段。
在这个阶段,需要进行详细的工程设计,包括设备选型、工程布局、管道设计等。
工程设计不仅需要满足工程的技术要求,还需要兼顾安全、经济和环保等因素。
然后,是设备采购阶段。
根据工程设计的要求,需要进行设备的采购。
设备采购包括了设备的选型、供应商的选择、合同的签订等。
在这个阶段,需要与供应商进行充分的沟通和交流,确保设备的质量和交货期的达到要求。
随后,是施工安装阶段。
在这个阶段,需要进行现场的材料准备、设备安装等工作。
施工安装需要严格按照工程设计的要求进行,确保设备安装的准确性和安全性。
然后,是调试运行阶段。
在设备安装完成后,需要进行设备的调试和运行,以确保设备的正常工作。
调试运行包括对设备的操作调试、参数设置、烟气排放监测等。
在这个阶段,需要对操作人员进行培训,确保其熟悉设备的运行和维护。
最后,是工程交付阶段。
在设备调试运行正常后,可以进行工程的交付。
工程交付包括了工程验收、资料整理等工作。
同时,还需要进行相关的申报手续,以确保工程符合相关法规的要求。
总结起来,FGD工程实施的过程包括前期准备、工程设计、设备采购、施工安装、调试运行和工程交付等阶段。
每个阶段都需要严格按照相应的流程进行,以确保工程的顺利进行和质量的达到要求。
实施FGD工程可以有效地降低工业排放的二氧化硫含量,保护环境和人类健康。
- 1、下载文档前请自行甄别文档内容的完整性,平台不提供额外的编辑、内容补充、找答案等附加服务。
- 2、"仅部分预览"的文档,不可在线预览部分如存在完整性等问题,可反馈申请退款(可完整预览的文档不适用该条件!)。
- 3、如文档侵犯您的权益,请联系客服反馈,我们会尽快为您处理(人工客服工作时间:9:00-18:30)。
关键词: 电力节能环保 火力发电 烟气脱硫
火力发电厂烟气脱硫技术(FGD)的发展
0概述
大气中SO2主要是含硫燃料,如煤、燃料油、石油焦碳等燃烧的产物,而以燃烧化石燃料为基础的火力发电厂,是世界上最大的SO2排放源之一。据1994年的统计:火力发电厂燃烧设备的SO2排放已超过全球SO2排放总量的70%。如果不采取合理的控制SO2排放措施,其污染必将对人类的健康及社会生存环境造成严重的危害。如对人的呼吸系统影响、引起或恶化人的心血管疾病;造成湖泊、河流的酸化、农作物的生长及损坏建筑物等。因此,控制火力发电厂设备的SO2排放以保护环境,必将在世界范围内的电力生产发展中得到进一步的重视。
3结束语
以上分析表明:湿法脱硫技术,特别是传统的石灰/石灰石——石膏湿法脱硫工艺是一种成熟的、目前国内外脱硫市场上仍占据主导地位的烟气脱硫技术。但随着技术的不断进步,其他新型的、更适合市场需求的脱硫工艺必将得到进一步的发展(如FGD-CFB等)。同时,尽管烟气脱硫技术已历经30余年的发展历史,但国内大型火力发电厂的烟气脱硫市场还处于起步阶段。因此,进一步调查研究国外烟气脱硫技术发展的历史和应用的成熟经验,对于开发适合国情的大型燃煤电站烟气脱硫技术,将具有重要指导意义。
(1)基于提高其工作参数的常规煤粉电站+烟气脱硫处理(PC+FGD);
(2)循环流化床锅炉(CFB);
(3)增压流化床燃烧联合循环发电技术(PF-BC-CC);
(4)整体煤气化联合循环发电技术(IGCC)。
但是,就我国目前火力发电厂生产的实际情况看,在近一段时期内,电厂锅炉燃烧排放控制工作的重点将集中在前者的第一种情况。特别是,自1998年我国政府关于酸雨控制区和二氧化硫污染控制区(简称两控区)的文件颁布以来,随着国家环保政策的进一步落实,电力环保烟气脱硫技术(FGD)必将得到进一步的发展。本文在回顾国外烟气脱硫技术的发展的基础上,分析了我国电力环保烟气脱硫技术的应用状况,并对我国今后烟气脱硫技术的发展和应用前景进行了展望。
此外,随着技术的进步,其他脱硫技术工艺(半干法、干法)也必将得到进一步发展。特别是80年代发展起来的烟气循环硫化床脱硫技术(FGD-CFB),以其具有高效、适用含硫燃料范围广、更低建设和运行成本、小占地面积等特点,将会得到进一步的重视和发展。目前,该工艺在国外已成功用于200MW机组的烟气脱硫,国内已同丹麦FLS公司合作,并用于云南小龙潭电厂100MW机组脱硫工程示范。
研究的主要内容一般包括:
(1)建立具备先进测量手段的湿法脱硫模型实验台。同时,以流体力学现代测量技术理论为基础,配备可靠、先进的测量和控制系统。
(2)进行以探索吸收塔内流场流动规律为目的的流体力学的研究。其主要内容包括:
·以实验台为物理模型基础,进行理论分析研究,建立吸收塔内有关数学模型,并进行相应数学分析或数值分析计算。
1.1.3燃烧后脱硫技术
燃烧后脱硫技术即烟气脱硫技术(FGD),按工艺特点可分为湿法、半干法和干法三大类;按副产物的处置方式又分回收和抛弃2种流程。以湿法烟气脱硫为代表的工艺有:石灰/石灰石——石膏法、双碱法、氨吸收法、海水法等;其特点是:技术工艺成熟、脱硫效率高(90%以上),且脱硫副产品大都可回收利用,但其投资和运行费用较高。半干法脱硫工艺为代表的有:旋转喷雾干燥法(SDA)、炉内喷钙尾部增湿活化(LIFAC)等;干法脱硫工艺为代表的有:荷电干式喷射脱硫法(CDSI)、等离子体法(电子束辐射/脉冲电晕)等。
1.1.2燃烧中脱硫技术
燃烧中脱硫技术是往煤中加入固硫剂,在煤的燃烧过程中,煤中的硫燃烧氧化,再与煤中的碱性物质或固硫剂反应生成硫酸盐而留在渣中,从而减少烟气中的S02浓度。这种方法主要在流化床/循环流化床锅炉(FB/CFB)中实现,目前脱硫效率可达80%~90%(Ca/S≥2)。另外,工业型煤炉前型煤固流成型技术也是解决燃烧中脱硫的有效措施之一。它不但可以解决型煤堆放占用场地和干燥等问题,而且还具有稳定燃烧,降低燃烧烟尘浓度等特点。我国从70年代开始进行型煤固硫的研究工作。目前,美国的型煤固硫率为87%,日本为70%~90%,我国约40%左右。
1.2烟气脱硫技术发展现状
湿法烟气脱硫技术的早期发展可追溯到20世纪的60年代中期,而干法烟气脱硫技术的早期发展则是20世纪70年代。然而,早期的烟气脱硫技术,不论是湿法,还是干法脱硫技术工艺,由于受到当时技术发展条件上的限制,整个脱硫系统建设投资和运行成本相对较高,而且脱硫效率低、系统复杂、运行可靠性能差,使得该技术在电力市场上的应用受到了一定的限制。经过了30多年的发展,到20世纪90年代,烟气脱硫技术有了长足的进展,特别是湿法烟气脱硫以其工艺的成熟性、运行的高可靠性,以及高的脱硫技术性能等特点,在世界电力市场上得到了广泛的应用。据英国(伦敦)国际能源机构的煤研究中心1998年的统计结果表明:在世界范围内,安装烟气脱硫装置的火电机组装机容量已达229484MW。同时,在已安装的烟气脱硫装置的所有火电机组中,采用湿法脱硫工艺脱硫的机组容量占整个安装烟气脱硫机组容量的86%以上,且其中采用传统的石灰/石灰石的湿法脱硫工艺占据了90%以上的份额。
在我国煤炭作为一次能源,约占我国能源结构的75%。其中,约84%的煤炭将直接用于燃烧。据2000年的统计,煤电在我国电力生产中占的比重约为78%。因此,在我国燃煤发电厂技术的发展除面临提高其发电效率外,还必将面临如何控制其燃烧发电排放水平的重大问题。自70年代开始,在世界范围内的能源专家们已开始着手研究开发高效、清洁的煤燃烧和发电技术,这主要表现在:
·研究并建立吸收塔内部主要流动参数间的相关关系,并最终形成具有自主知识版权的、具有最佳技术性能组合的湿法脱硫吸收塔系统的设计技术。
通过上述技术上的努力,现代的以石灰/石灰石湿法脱硫工艺的初投资建设和运行费用已大大降低,且单吸收塔的烟气处理能力也大幅度提高。如美国佛罗里达州坦帕市电力公司在2000年1月投入运行的湿法脱硫装置的脱硫效率大于95%,单塔容量为890MW,建设成本费用低于100美元/kW。
1脱硫技术及发展现状
1.1脱硫技主要包括燃烧前、燃烧中和燃烧后(烟气脱硫)。
1.1.1燃烧前脱硫技术
燃烧前脱硫技术主要是煤炭洗选技术。目前,国内煤炭入选率不到l7%,而美国为42%,英国为94.9%,法国为88.7%,日本为98.2%。我国曾对微波脱硫和高硫煤强磁分离脱硫进行过小型试验研究,总脱硫率达50%左右。但由于所需基建投资和运行费用都较高,脱硫后的煤是水煤浆,使用上受到一定限制。因此,这两项技术没有得到有效推广应用。发达国家正在进行摩擦电选技术脱硫降灰的研究,将煤粉通过摩擦电选机,分离出无机质(主要是黄铁矿硫);中国矿业大学也进行了该技术的中试研究。
·处理并分析整理有关实验数据,验证所建立的吸收塔内有关数值模型,以评价液滴粒子在吸收段的平均滞留时间,以及液滴雾化粒子的动力学特性和气、液两相的质量传递(扩散)规律等,并最终实现优化吸收塔结构的目的。
·研究除雾器效率及阻力特性的规律,以确定除雾器的选型和布置。
·研究雾化喷嘴的雾化性能、喷淋系统性能及阻力特性,以评价喷嘴的组合和布置。