克劳斯法硫回收装置液硫系统的优化设计
超优克劳斯硫回收工艺装置的设备布置及管道设计

和压降, 要求设备相对集中布置, 采用多层构架立 体布置 , 充分利用空 间。超优克劳斯硫 回收装置
与传统 克 劳斯硫 回收 的设 备 布 置基 本 相 同 , 除硫
规 定指 标 , 同 时 降低 了装 置 投 资 费 用 。硫 回 收装 置 的操 作介 质 特殊 , 液硫凝 固点较 高 , 易造成 管道 及 设备 的堵 塞 。设计 时 , 要 求设 备 布置 紧凑 , 管道
酸气预 热器
血
阀放置 在第 2或 第 3层 平 台 上 , 保 证 安全 阀 出 口 管线 “ 步步 低 ” 流 向管廊 上 的火 炬 总管 。另外 , 酸 性 气具 有一 定 的腐蚀 性 , 且为 高度 危害 介质 , 管道 材 质具 有 一定 的 特殊 性 , 不 宜与 燃 料 气 放 空管 线
一 .
有 u形 。 ( 2 ) 可燃气体 的安全阀出口管线一旦低于火 炬总管 , 会 造成 管线 积液 , 由于硫 回收装 置可 燃气
体 的积 液含 有毒 有 害物质 , 不 可 随意排 放 , 在 布置 时应综 合考 虑 主管 廊 上 火 炬 总 管 的标 高 , 将 安 全
占
. .. . . . .. . . . j I .. .
一 — _. 一 一 ●一
◆; 一
一
一 —十
一一
一 ●一
一一
硫黄造粒 包装厂房
・ 出 1 _ - — —
图 1 地 面 上 的设 备布 置
小氮肥
第4 3卷
第1 O期
2 0 1 5年 1 0月
1 9
1 . 2 第 2层平 台设 备布 置
克劳斯硫黄回收装置优化改造总结
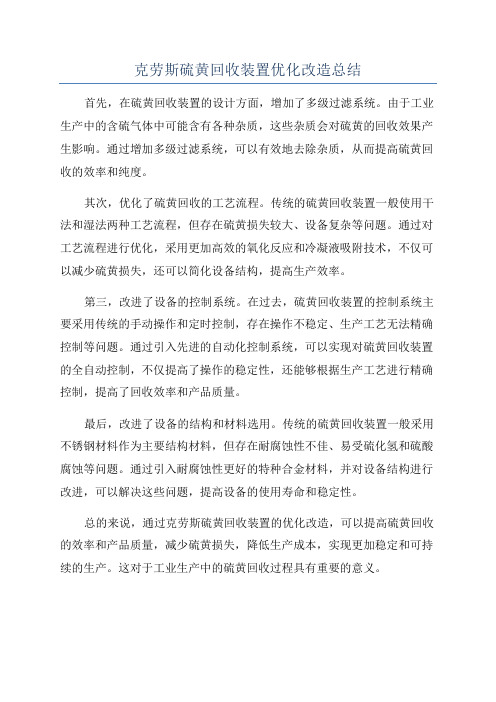
克劳斯硫黄回收装置优化改造总结
首先,在硫黄回收装置的设计方面,增加了多级过滤系统。
由于工业生产中的含硫气体中可能含有各种杂质,这些杂质会对硫黄的回收效果产生影响。
通过增加多级过滤系统,可以有效地去除杂质,从而提高硫黄回收的效率和纯度。
其次,优化了硫黄回收的工艺流程。
传统的硫黄回收装置一般使用干法和湿法两种工艺流程,但存在硫黄损失较大、设备复杂等问题。
通过对工艺流程进行优化,采用更加高效的氧化反应和冷凝液吸附技术,不仅可以减少硫黄损失,还可以简化设备结构,提高生产效率。
第三,改进了设备的控制系统。
在过去,硫黄回收装置的控制系统主要采用传统的手动操作和定时控制,存在操作不稳定、生产工艺无法精确控制等问题。
通过引入先进的自动化控制系统,可以实现对硫黄回收装置的全自动控制,不仅提高了操作的稳定性,还能够根据生产工艺进行精确控制,提高了回收效率和产品质量。
最后,改进了设备的结构和材料选用。
传统的硫黄回收装置一般采用不锈钢材料作为主要结构材料,但存在耐腐蚀性不佳、易受硫化氢和硫酸腐蚀等问题。
通过引入耐腐蚀性更好的特种合金材料,并对设备结构进行改进,可以解决这些问题,提高设备的使用寿命和稳定性。
总的来说,通过克劳斯硫黄回收装置的优化改造,可以提高硫黄回收的效率和产品质量,减少硫黄损失,降低生产成本,实现更加稳定和可持续的生产。
这对于工业生产中的硫黄回收过程具有重要的意义。
克劳斯硫磺回收装置优化改造总结
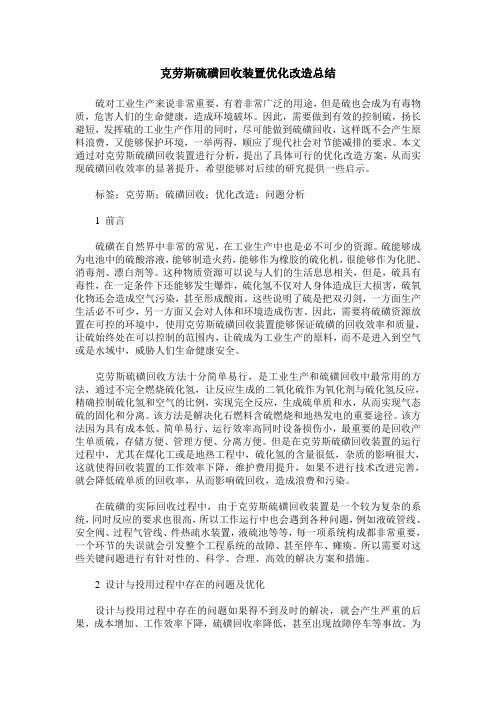
克劳斯硫磺回收装置优化改造总结硫对工业生产来说非常重要,有着非常广泛的用途,但是硫也会成为有毒物质,危害人们的生命健康,造成环境破坏。
因此,需要做到有效的控制硫,扬长避短,发挥硫的工业生产作用的同时,尽可能做到硫磺回收,这样既不会产生原料浪费,又能够保护环境,一举两得,顺应了现代社会对节能减排的要求。
本文通过对克劳斯硫磺回收装置进行分析,提出了具体可行的优化改造方案,从而实现硫磺回收效率的显著提升,希望能够对后续的研究提供一些启示。
标签:克劳斯;硫磺回收;优化改造;问题分析1 前言硫磺在自然界中非常的常见,在工业生产中也是必不可少的资源。
硫能够成为电池中的硫酸溶液,能够制造火药,能够作为橡胶的硫化机,很能够作为化肥、消毒剂、漂白剂等。
这种物质资源可以说与人们的生活息息相关,但是,硫具有毒性,在一定条件下还能够发生爆炸,硫化氢不仅对人身体造成巨大损害,硫氧化物还会造成空气污染,甚至形成酸雨。
这些说明了硫是把双刃剑,一方面生产生活必不可少,另一方面又会对人体和环境造成伤害。
因此,需要将硫磺资源放置在可控的环境中,使用克劳斯硫磺回收装置能够保证硫磺的回收效率和质量,让硫始终处在可以控制的范围内,让硫成为工业生产的原料,而不是进入到空气或是水域中,威胁人们生命健康安全。
克劳斯硫磺回收方法十分简单易行,是工业生产和硫磺回收中最常用的方法,通过不完全燃烧硫化氢,让反应生成的二氧化硫作为氧化剂与硫化氢反应,精确控制硫化氢和空气的比例,实现完全反应,生成硫单质和水,从而实现气态硫的固化和分离。
该方法是解决化石燃料含硫燃烧和地热发电的重要途径。
该方法因为具有成本低、简单易行、运行效率高同时设备损伤小,最重要的是回收产生单质硫,存储方便、管理方便、分离方便。
但是在克劳斯硫磺回收装置的运行过程中,尤其在煤化工或是地热工程中,硫化氢的含量很低,杂质的影响很大,这就使得回收装置的工作效率下降,维护费用提升,如果不进行技术改进完善,就会降低硫单质的回收率,从而影响硫回收,造成浪费和污染。
超级克劳斯硫璜回收装置在设计、运行中存在的问题及优化方案

超级克劳斯硫璜回收装置在设计、运行中存在的问题及优化方案超级克劳斯硫璜回收装置在设计、运行中存在的问题及优化方案摘要:超优克劳斯工艺基础是富氧燃烧,通过控制富氧空气与酸性气的比例来控制进入超级克劳斯反应器中硫化氢的浓度。
过量的氧进入下游反应器,也会造成反应器床层温度剧烈波动,严重时会发生燃烧反应,损坏设备。
关键词:废锅液流捕集器过程气工艺管线催化剂床层化学当量燃烧过氧国电赤峰化工有限公司硫回收装置采用的是荷兰荷丰超优/超级克劳斯专利技术,由赛鼎工程有限公司详细设计,日产硫磺25.4吨。
2012年12月17日开车投产,2013年3月20日-3月27日超级克劳斯硫酸盐化结束,超级克斯反应器投用,并成功引入氧气,采用富氧操作模式,至今运行比较稳定,排放达标。
针对超优克劳斯反应特点,就开车中存在的重大安全隐患问题做简单介绍并给出解决方案,以供同行借鉴和参考。
一、硫回收装置在设计中存在的问题我公司硫磺回收装置采用的超优/超级克劳斯工艺,其基础是以比值控制富氧空气流量实现硫化氢部分燃烧。
紧急停车后再开车的燃烧过程中,会造成废锅出口过程气过氧,引起克劳斯反应器催化剂床层温度剧烈波动,从而使催化剂活性降低、烧结、粉碎,减少催化剂使用寿命。
另外过程气工艺管线管道壁会残存硫化亚铁,当过程气中氧含量高时,会引发硫化亚铁与氧气燃烧反应,从而损坏管道、设备。
基于上述安全隐患,必须对原有工艺管线进行改造。
原工艺流程简图如下:改造后的工艺简图:燃料气二、改造方案综合考虑,本着投资少、见效快、大大降低安全隐患的原则,在主体设备不动的情况下,对设备管线进行了如下改造。
1.从废锅出口过程气工艺管线PG61501-400上引一条副线PG61519-300到液流捕集器出口阀后与尾气管线相连接;2.废锅出口过程气工艺管线PG61501-400上增加总阀DN400,并且为夹套蝶阀,使用0.5MPa低压蒸汽伴热;3.废锅出口过程气副线PG61519上两端各增加DN300夹套蝶阀做为隔离使用,并使用使用0.5MPa低压蒸汽伴热;4.废锅出口过程气副线PG61519一定要有倾斜度,保证液体自流;管线使用三根0.5MPa低压蒸汽伴热,防止由于阀门内漏造成硫磺堵塞。
克劳斯硫黄回收装置优化改造总结

污 导淋 , 用 于判 断堵 塞 情 况 和 事 故 状 态 下 的 紧急
处 理
本 文 作 者 的联 系 方 式 : w u s h i k a i 1 6 8 @1 6 3 . e o m
为便 于施 工及 流 量 计 的 维护 , 设 计 方 将 二级 反 应
Abs t r a c t T he e x i s t i n g p r o b l e ms o f Cl a u s s u l f u r r e c o v e r y u ni t i n d e s i g n a n d o p e r a t i o n a r e a n a l y z e d a n d r e l e v a n t me a s u r e s a n d o p t i mi z a t i o n s c h e me a r e c a r r i e d o u t . Af te r t h e r e v a mp, t h e
ZHANG Yo ng.W U S h i k a i
( H e n a n L o n g y u C o a l C h e m i c a l C o . , L t d . , Y o n g c h e n g 4 7 6 6 0 0 ,C h i n a )
措施
1 . 1 液 硫 管线 的设计 优化
都设 置 了进 口隔 断 阀并 增 设 铅 封 。在 试 车 过 程 中, 因管 线 吹扫不 彻 底 而 导致 异 物 进 入 密封 面 以 及仪 表失 准 、 安全 阀质量 不过 关 、 操 作事 故等 因素 而 导致安 全 阀 内漏 或 起 跳后 出现 内漏 时 , 可 通 过 根 部 阀的隔 断 以有 效 避 免泄 漏 、 降 负 荷 和停 车 等 事 故 的发 生 。
常规克劳斯硫回收装置优化改进总结

櫋櫋櫋櫋櫋櫋櫋櫋櫋櫋櫋櫋櫋櫋櫋櫋櫋櫋櫋櫋櫋櫋櫋櫋櫋櫋殹殹殹殹甲醇及下游产品[收稿日期]2020 05 19[作者简介]张培培(1987—),女,河南禹州人,助理工程师櫅櫅櫅櫅櫅櫅櫅櫅櫅櫅櫅櫅櫅櫅櫅櫅櫅櫅櫅櫅櫅櫅櫅櫅櫅櫅櫅櫅櫅櫅櫅櫅櫅櫅櫅櫅櫅櫅櫅櫅櫅櫅櫅櫅。
(4)尿素硝酸铵液体肥盛装用塑料吨桶,每个塑料吨桶成本价700元。
上述各项合计,吨尿素硝酸铵液体肥的总生产成本为939 08+83 3+700=1722 4元;尿素硝酸铵液体肥售价以2200元/t计,其利润在500元/t左右;按年生产尿素硝酸铵液体肥4000t计,全年利润为4000×500÷10000=200万元。
未来甘肃刘化还可建立与现代农业大用户的联储联销机制,回收利用产品包装物(塑料吨桶),可进一步降低尿素硝酸铵液体肥的生产成本,如此一来本项目的经济效益将更为可观。
6 结束语针对合成氨高温变换催化剂制备废液直接引入现有污水处理系统难以消化、废水不能达标排放的难题,甘肃刘化通过技术合作将此废液提浓后用于生产尿素硝酸铵液体肥,不仅解决了催化剂生产过程中高总氮含量废液的排放问题,减轻了污水处理系统的压力、降低了污水处理的成本,而且回收了废液中的硝酸铵用于生产质量完全符合NY2670—2015要求的尿素硝酸铵液体肥,在解决环保问题的同时还创造了一定的经济效益。
本合成氨高温变换催化剂制备废液生产尿素硝酸铵液体肥的新工艺,值得在业内推广。
[参考文献][1]耿莉莉,杨凯旭,张诺伟,等.Ru和Cu协同催化湿式氧化处理氨氮废水[J].化工学报,2018,69(9):3869-3878,4137.[2]陈 昕.含氨氮催化剂生产废水的处理[J].化工环保,2014,34(2):128-132.[3]陈 怡,李 强,詹爱霞.催化剂含氨氮污水治理技术的探讨[J].石油化工环境保护,2004,27(3):26-29.常规克劳斯硫回收装置优化改进总结张培培,李俊杰(新乡中新化工有限责任公司,河南获嘉 453800)[摘 要]新乡中新化工有限责任公司300kt/a煤基甲醇装置及200kt/a乙二醇装置配套的酸性气硫回收装置采用“单级常规克劳斯+H2S直接氧化”组合式工艺,主要包括酸性气部分燃烧转化、单级常规克劳斯催化反应、H2S直接氧化催化反应和尾气洗涤等四个单元。
硫回收优化运行改造总结

硫回收优化运行改造总结针对克劳斯硫回收尾气中含硫量大、克劳斯反应器转化率低、后系统带硫严重等问题,制定了专门的改造方案并实施了改造,對改造时间节点和改造内容进行了详细地阐述。
通过改造前后的一些相关数据对比,确定此次改造达到了预期的目的。
标签:硫回收;克劳斯;捕集器;预热器;改造;出口总硫1 前言兖矿鲁南化工有限公司有两套硫回收装置,东西厂区各一套,均为克劳斯法硫回收装置。
由于克劳斯装置本身的转化率有限,加之普通捕集器及分离器捕集或分离效果不好,很容易导致液硫带入后系统,增加后系统负荷的同时,也造成了硫磺的浪费。
2 改造前的状况改造前硫回收后系统带硫严重,正常生产时,一、二、三级冷凝器西侧捕集器捕集效果不好,导致液硫带入后系统,造成克劳斯转化率降低、烟囱内部堆积硫磺、烟囱尾气中二氧化硫含量较高等问题。
另外,二级克劳斯反应器入口温度控制是酸性气炉分流部分高温高硫气体控制温度,该高温气体中硫含量高,影响克劳斯反应器的转化率,增大了烟囱尾气中二氧化硫含量。
3 改造时间2016年7月召开硫回收优化运行相关会议,7月8日完成硫回收优化运行改造方案的编制并通过签字审批。
8月份:硫回收优化改造项目所需的设备已完成招标,材料已进行采购,钢材、法兰、弯头等部分材料已到货。
9月份:硫回收优化改造项目中,除所需的设备厂家正在制造,其余所需的材料均已到货。
10月底,硫回收优化改造项目中所需的三个捕集器、高效分离器以及预热器已制造完成并运至硫回收现场,10月31日,施工单位开始在硫回收界区外进行管道预制和预热器浇注料的铺设。
11月4日9:10硫回收切气开始热态运行,11月7日9:00系统开始加盲板进行改造施工。
11月11日15:00改造项目完成施工,开始抽盲板。
11月12日12:00硫回收点炉升温。
11月14日16:10硫回收系统接气,改造项目投入使用。
4 改造内容为增强液流捕集效果,一、二、三级冷凝器捕集器有卧式改为立式。
克劳斯法硫磺回收控制系统的设计与实现

克劳斯法硫磺回收控制系统的设计与实现摘要:随着经济的发展,人们生活水平的提高,人们逐渐意识到可持续发展的重要。
近年来,环境污染问题日益严重,而石化企业在对资源加工处理过程中,不可避免地会产出硫化氢等污染物质。
采用克劳斯法硫磺回收工艺,不仅可以最大限度地降低废气对环境的污染问题,而且能够高效地回收硫磺产品,从而提高了能源的利用效率与价值。
目前我国克劳斯法工艺流程的应用现状还存在诸多不足,因此只有不断对工艺进行改进、创新和升级,才能实现硫磺回收和尾气处理的高效协同发展。
本文就克劳斯法硫磺回收控制系统的设计与实现展开探讨。
关键词:克劳斯法;硫磺回收;工艺引言克劳斯法硫磺回收虽然并非属于气体净化工艺,但由醇胺法脱硫、克劳斯法硫磺回收、配套尾气处理技术组成工艺技术路线,经70余年的技术开发,现已成为从含硫天然气和炼厂气中回收硫磺最重要的技术路线。
1克劳斯法硫磺回收工艺的优势首先,克劳斯法硫磺回收工艺具有操作灵活方便和弹性范围大的优点,而且热稳定性、化学稳定性和机械强度也很高,同时维修方便,装置运行平稳可靠,并能减少有害物质的排放,催化剂的使用寿命能多达10年左右;其次,克劳斯法对于硫磺的转化效率和回收效率十分可观,可以实现加工处理过程的连续周期运转,同时副反应的现象能够有效控制,最为关键的是可以满足环保排放的标准要求;再次,克劳斯法对于酸性气浓度不同范围的适应能力较强,不仅可以满足新建装置设备,而且对于传统装置改造升级的情况也较为适合。
同时三废问题可以得到最大限度的降低和抑制。
基于克劳斯法装置适应性强的特点,因此广泛应用于石化企业硫磺回收与尾气处理环节;最后,相对来讲克劳斯法的系统操作并不复杂,因此投资费用低,而且工艺流程也容易操控和管理。
此外硫磺作为生产硫酸产品的重要工业原料,其经济价值更为凸显。
2工艺流程选择从1883年英国化学家克劳斯(Claus)提出原始的克劳斯法制硫工艺至今已有100多年历史。
1938年德国法本公司对原始克劳斯法工艺作了重大改革,其要点是把H2S的氧化分为两个阶段完成。
硫磺回收装置液硫池脱气系统优化

硫磺回收装置液硫池脱气系统优化摘要:液硫池中储存的液硫含有少量的硫化氢,通过液硫鼓泡脱气技术,将液硫中溶解的硫化氢解析出来,并通过抽射器将解析出的硫化氢引至焚烧炉燃烧。
通过对液硫脱气系统的优化,降低了液硫池气相空间的硫化氢含量,保证液硫池的安全运行。
关键词:液硫池;脱气系统;硫化氢米桑油田硫磺回收装置采用克劳斯工艺回收硫磺,各级硫冷器产生的液硫自流至液硫池。
液硫池分为I区和II区,I区主要用于接收硫冷器产生的液硫,一般情况从硫冷器进入液硫池的液硫,硫化氢浓度约300ppm左右。
通过空气鼓泡脱气后输送至II区;II区主要用于储存液硫,并将脱气完成的液硫转输至硫磺成型厂房进行后续加工。
1液硫池工艺简介1.1液硫池工艺液硫池长15m,宽5m,深3.1m。
分为I区和II区,其中I区长3m, II区长5m。
I设计有新鲜空气吸入口以及蒸汽抽射器,通过蒸汽抽射器将液硫中脱除的废气输送至尾气焚烧炉灼烧后排放至大气,新鲜空气持续从空气吸入口被吸入I区,保证了I区气相空间硫化氢等可燃气体浓度持续保持在爆炸极限以下。
液硫池设计条件为:设计压力(-10kpa),设计温度210℃,操作温度138℃。
1.2原设计液硫池脱气流程图2新鲜空气吸入口位置选择液硫中溶解携带的硫化氢经鼓泡脱气后会聚集在液硫池上部的气相空间,如不及时清除,将可能聚集到爆炸极限浓度,I区空间狭小,原设计中新鲜空气入口位于I区起不到很好的脱气效果。
如将液硫池原I区新鲜空气吸入口位置迁移至II区远离抽射器吸入口的位置,改造完成后可以确保整个液硫池气相空间形成有效循环。
这样做的好处主要有以下几个方面:(1)在生产运行过程中,保证了液硫池I区和II区的气相空间中的硫化氢等可燃爆炸性气体浓度可以持续保证在较低的浓度,确保操作安全。
(2)在生产运行过程中,液硫池气相空间硫化氢分压持续较低,有利于液硫中硫化氢的析出,保证液硫中硫化氢浓度降低,确保液硫品质合格。
3液硫脱气系统优化3.1空气鼓风量的选择通过工艺模拟可知液硫中H2S含量在某一固定值时,鼓风量越大越有利于H2S析出,但根据现场经验鼓风量过大,空气口处会有气体冒出,不利于安全。
含硫瓦斯气及克劳斯尾气脱硫装置溶剂系统优化改造

含硫瓦斯气及克劳斯尾气脱硫装置溶剂系统优化改造何文建 胡滨平 金陵石化有限公司烷基苯厂 南京 210046摘要 某含硫瓦斯气及克劳斯尾气脱硫装置溶剂系统存在不合理现象:尾气吸收塔操作弹性小、溶剂使用量大、焚烧炉烟气二氧化硫排放浓度较高、装置能耗高。
对该溶剂系统进行改造,将溶剂系统重新分配,提高溶剂系统的合理性。
增加尾气吸收塔填料高度,提高尾气吸收塔操作弹性。
改造后降低了贫液使用量,减少了装置蒸汽消耗,降低了装置焚烧炉烟气二氧化硫排放值,达到节能减排的目的。
相关经验和做法可为同行借鉴。
关键词 脱硫装置 溶剂系统 尾气吸收塔 优化改造 节能减排何文建:高级工程师。
2002年7月毕业于四川大学化工工艺专业。
现在中国石化金陵石化公司烷基苯厂从事工艺技术管理工作。
联系电话:(025)58975612,E mail:hewenj jlsh@sinopec com;hwj9813321@163 com。
1 生产现状某含硫瓦斯气及克劳斯尾气脱硫装置利用醇胺法脱硫,将加氢精制来的含硫瓦斯气进行净化,分离出净化瓦斯和硫化氢。
硫化氢送至硫磺回收单 元,经克劳斯+RAR工艺进行制硫。
净化瓦斯至PSA单元分离出高纯氢和解析气。
装置尾气吸收塔C 902和瓦斯脱硫塔C 701塔底富溶剂汇合后送至溶液再生塔C 702解吸硫化氢,C 702塔底贫液循环回吸收塔使用,具体流程见图1。
图1 吸收解吸装置流程简图 装置运行时C 902操作弹性较小,装置酸性气波动时,易造成焚烧炉F902烟气二氧化硫超标。
在夏季高温天气,F 902烟气二氧化硫浓度约为80mg/m3,部分时间段二氧化硫排放浓度为90mg/m3,接近二氧化硫国家规定的排放上限(<100mg/m3),遇酸性气波动,二氧化硫瞬时值易超标。
为保证二氧化硫排放合格,需要多次将C 902塔顶过程气切进碱洗系统,不仅增加碱液消耗,同 时也增加了班组的操作强度。
2 现状分析2 1 贫液质量分析该装置使用的脱硫溶液为N-甲基二乙醇胺(MDEA),分子式为CH3-N(CH2CH2OH)2,其主要吸收反应如下:2R2R’N+H2S→(R2R’NH)2S(R2R’NH)2S+H2S→2R2R’NHHS贫液质量对硫化氢吸收效果起着至关重要作用[1],对贫液浓度和硫化氢含量进行跟踪,具体见表1。
硫回收工艺设计因素优化探究

硫回收工艺设计因素优化探究摘要:本文简述了炼厂克劳斯法硫回收工艺基本原理、影响硫回收的因素及设计优化措施,然后列举某炼厂硫回收工艺设计实例来说明如何通过设计因素优化提高硫回收率,通过硫回收装置运行期间出现的问题,探究了优化设计的有效措施,以供同行从事硫回收工艺设计参考。
关键词:硫回收影响因素设计优化措施1克劳斯法硫回收工艺简介1.1基本原理酸性气在反应器内部,通过低温催化反应以及在燃烧炉内部的高温热量,将H2S转变成SO2,在燃烧炉内部SO2和H2S进一步氧化成元素硫,反应方程式见式(1)和式(2)。
H2S+3/2O2=SO2+H2O (1)2H2S+SO2=3/2S2+2H2O (2)其中1/3H2S参与第一环节反应,2/3H2S参与第二环节反应,进一步转变成元素硫,在酸性气燃烧炉的高温下,硫元素大体上以S2的形态存在,酸性气中不但涵盖H2S,还包含了H2O、N2以及CO2;来自炼油厂的酸性气还包含了HCN以及氨等,于是在酸性气燃烧炉内的反应十分繁琐,其中核心的副反应涵盖消耗或生成H2与CO的副反应、消耗或生成CS2与COS副反应以及烃与氨的氧化反应等。
1.2工艺策略按照酸性气中H2S含量的区别,克劳斯法硫回收工艺分3种策略:直接氧化法、分流法以及部分燃烧法。
通常酸性气里面的H2S体积浓度超过50%时采取部分燃烧法;H2S体积浓度小于15%时采取直接氧化法;H2S浓度位于两者之间采取分流法。
因为炼厂酸性气里面的H2S体积浓度都超过了50%,特别是上游的胺处理装置采取选择性溶剂后,H2S体积浓度至少提升到70%,于是炼厂硫回收装置基本都采取部分燃烧法。
2影响响硫回收率主要因素及设计优化本文以某石化公司委托的2wt/a新建硫回收装置工艺设计为例,分析影响硫回收率的因素并对其提出优化措施。
2.1原料组成炼厂硫回收装置进料酸性气一般来自酸性水汽提装置以及脱硫装置,一般是不稳定的,特别是其中的氨以及烃的含量变化非常大。
超级克劳斯硫回收工艺优化运行及改造分析

超级克劳斯硫回收工艺优化运行及改造分析摘要:在合成氨工艺中,硫回收是该工艺的重要环节,这是因为硫回收关系到水煤气的净化能否维持正常运转,基于此,贵州开阳化工有限公司在合成氨硫回收工艺中,采取采用荷兰荷丰超级克劳斯硫回收技术,年副产硫磺2.1万吨,有效保障环保指标达标排放。
随着公司在提高产能,节能降耗方面的需求,优化改造硫回收工艺势在必行。
关键词:合成氨;硫回收;工艺运行;改造引言:将变换来含氨汽提气和甲醇洗来的H2S体积不大于40%酸性气经过焚烧、催化反应,转化为纯度为99.9%的硫磺,经造粒、包装后外销,尾气达标后(SO2≤960mg/Nm3)通过烟囱排放。
1.超级克劳斯硫回收工艺流程在来自低温甲醇洗工序酸性气经过水洗,脱除大部分甲醇,经过分离器脱除水分,经预热器加热后进入主烧嘴(M6003)内与空分来的氧气按一定比例混合燃烧,大部分酸性气体燃烧后进入酸性气废锅(E6001)与脱盐水换热,同时副产253℃、4.1MPa饱和蒸汽。
酸性气进入第一冷凝器(E6002)冷凝到195℃,出第一冷凝器的液硫经A#液硫封(X6001A)直接流入液硫槽。
未反应完的酸性气再进入第一再热器(E6009)加热到240℃,进入一级克劳斯反应器(R6001),在催化剂作用下进行反应后进入第二冷凝器(E6003),出第二冷凝器的液硫经B#液硫封(X6001B)直接流入液硫槽,出第二冷凝器的克劳斯气体温度约为195℃,在第二再热器(E6010)中再次加热到215 ℃,进入二级克劳斯反应器(R6002),同样在催化剂作用下进行反应后,进入第三冷凝器(E6004),产生液态硫经C#液硫封(X6001C)流入液硫槽。
克劳斯气体进入第三再热器(E6011)再次加热到200 ℃,进入三级克劳斯反应器(R6003)进行反应,出来的克劳斯气体进入第四冷凝器(E6005)被冷却,硫被分离出去,产生液态硫经D#液硫封(X6001D)流入液硫槽。
克劳斯法硫磺回收方法
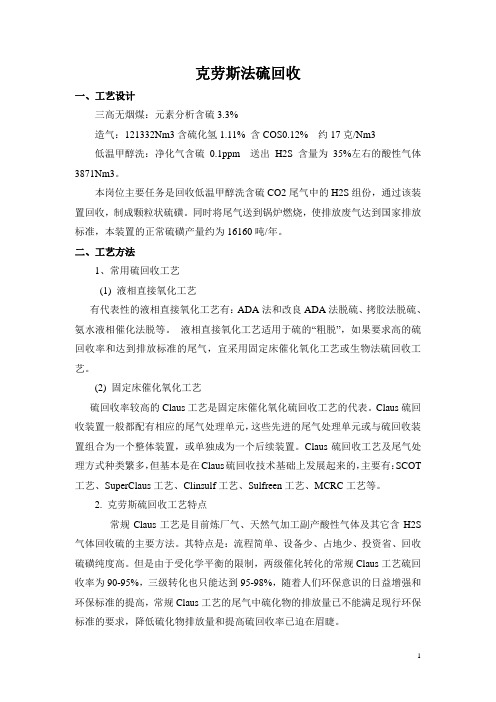
克劳斯法硫回收一、工艺设计三高无烟煤:元素分析含硫3.3%造气:121332Nm3含硫化氢1.11% 含COS0.12% 约17克/Nm3低温甲醇洗:净化气含硫0.1ppm 送出H2S含量为35%左右的酸性气体3871Nm3。
本岗位主要任务是回收低温甲醇洗含硫CO2尾气中的H2S组份,通过该装置回收,制成颗粒状硫磺。
同时将尾气送到锅炉燃烧,使排放废气达到国家排放标准,本装置的正常硫磺产量约为16160吨/年。
二、工艺方法1、常用硫回收工艺(1) 液相直接氧化工艺有代表性的液相直接氧化工艺有:ADA法和改良ADA法脱硫、拷胶法脱硫、氨水液相催化法脱等。
液相直接氧化工艺适用于硫的“粗脱”,如果要求高的硫回收率和达到排放标准的尾气,宜采用固定床催化氧化工艺或生物法硫回收工艺。
(2) 固定床催化氧化工艺硫回收率较高的Claus工艺是固定床催化氧化硫回收工艺的代表。
Claus硫回收装置一般都配有相应的尾气处理单元,这些先进的尾气处理单元或与硫回收装置组合为一个整体装置,或单独成为一个后续装置。
Claus硫回收工艺及尾气处理方式种类繁多,但基本是在Claus硫回收技术基础上发展起来的,主要有:SCOT 工艺、SuperClaus工艺、Clinsulf工艺、Sulfreen工艺、MCRC工艺等。
2. 克劳斯硫回收工艺特点常规Claus工艺是目前炼厂气、天然气加工副产酸性气体及其它含H2S 气体回收硫的主要方法。
其特点是:流程简单、设备少、占地少、投资省、回收硫磺纯度高。
但是由于受化学平衡的限制,两级催化转化的常规Claus工艺硫回收率为90-95%,三级转化也只能达到95-98%,随着人们环保意识的日益增强和环保标准的提高,常规Claus工艺的尾气中硫化物的排放量已不能满足现行环保标准的要求,降低硫化物排放量和提高硫回收率已迫在眉睫。
一般克劳斯尾气吸收要经过尾气焚烧炉,通过吸收塔,在吸收塔内用石灰乳溶液或稀氨水吸收,生成亚硫酸氢钙或亚硫酸氢铵,通过向溶液中通空气,转化为石膏或硫酸铵,达到无害处理,我公司硫回收尾气送至锅炉燃烧并脱硫后排放。
克劳斯硫回收装置存在的问题及改进措施

2019年05月设备运维克劳斯硫回收装置存在的问题及改进措施许升旗(煤气化公司义马气化厂,河南三门峡472300)摘要:随着国民经济的快速增长,我国的煤化工领域和石化工业也得到了迅速发展,同时造成的废气污染也十分的严重。
为了使尾气污染排放达到国家大气污染综合排放标准,克劳斯硫磺回收工艺技术也在不断的优化和完善,进而向高效化、品质化、环保化和经济化趋势逐步衍变。
文章简单介绍了义马气化厂681#克劳斯硫回收装置的工艺以及在运行中出现的问题和技改措施,希望能为同行业提供一些建议。
关键词:硫磺回收;克劳斯;技改1克劳斯装置的发展现状随着国民经济的快速增长,我国的煤化工领域和石化工业也得到了迅速发展,同时造成的废气污染也十分的严重。
为了使尾气污染排放达到国家大气污染综合排放标准,克劳斯硫磺回收工艺技术也在不断的优化和完善,进而向高效化,品质化,环保化和经济化趋势逐步衍变。
克劳斯法工艺十分成熟,已具有近百年的历史,在脱硫过程中产生的含H2S 气体中回收硫,进而实现硫磺产品以及其他行业化工原料的回收,同时获得良好的经济效益,又解决工业废气对大气的污染问题并实现环保和效益之间的同步协调发展,是一种较为成熟的酸性气体硫回收工艺,在国内焦化厂,发电厂,炼油厂,煤气化厂,甲醇厂和化肥厂等石化企业得到广泛的应用。
克劳斯工艺特点是流程简单、设备少,占地少,操作灵活、回收硫纯度高、投资费用低、环境及规模效益显著,克劳斯工艺回收硫磺的纯度可达到99.8%,可作为生产硫酸的一种硫资源,也可作其他部门的化工原料。
2克劳斯硫回收工艺2.1硫回收的工艺原理我厂的硫磺回收装置采用两级劳斯硫回收技术,将原料酸性气中的硫化氢转化成硫磺加以回收,尾气经过锅炉装置的洗涤塔脱硫后达标排放。
在主燃烧室其主要反应式为:H 2S+3/2O 2→SO 2+H 2O H 2S+1/2SO 2→H 2O+3/4S 2在一级反应器内主要的化学反应是:2H 2S +SO 2→3/xS x +2H 2O COS +H 2O →H 2S +CO 2CS 2+2H 2O →2H 2S +CO 2在二级反应器中主要的化学反应是:2H 2S +SO 2→3/xS x +2H 2O 2.2硫回收工艺的流程原料酸性气经过酸性气分离器进行气液分离(F681A01)后进入酸性气预热器(W681A01)预热至220℃。
液硫脱气废气入克劳斯炉在硫磺回收装置的应用

技改,工艺简图如图1所示。
新增1台空气加热器,将燃烧空气加热至135~140℃,防止含硫废气堵塞克劳斯空气管线;新增2台中压蒸汽抽射器取代低压蒸汽抽射器,新建1条液硫池废气入克劳斯炉炉头空气管线的夹套管线,利用中压蒸汽将液硫池废气送至克劳斯炉,其余管线利旧。
图1 液硫脱气废气入克劳斯炉改造安全仪表系统涉及中压蒸汽切断阀、废气至尾炉切断阀和废气至克劳斯炉切断阀。
具体动作如下:当液硫池着火和尾炉停车时,联锁关闭中压蒸汽和废气入克劳斯炉切断阀;克劳斯炉联锁跳车,关闭废气入克劳斯炉切断阀,打开去尾炉切断阀。
2 测试结果测试之前预先投用空气加热器,11月2日液硫池废气由去尾炉流程转至克劳斯炉流程。
新工艺投用前后克劳斯炉酸性气负荷稳定在31000~32300Nm 3/h ,同时为了探索新工艺对烟气SO 2排放影响,尾气吸收塔的贫胺液和再生塔所消耗的低压蒸汽流量分别固定为240t/h 和48t/h 。
0 引言某硫磺回收装置以上游胺液再生塔的酸性气为原料设计生产硫磺20万t/a ,该装置的工艺路线由常规两级克劳斯和配套SCOT 尾气处理组合而成,总硫回收率达99.8%。
各级硫冷凝器的液硫一般含有100×10-6~300×10-6 H 2S ,为了保证下游硫磺成型单元的安全,液硫必须进行处理使H 2S 含量降低至10×10-6。
该装置采用的是最为常见的Shell 空气鼓泡工艺[1],空气自克劳斯风机引至液硫池脱气区。
为保证液硫池微负压操作,液硫池产生的含硫废气采用蒸汽抽射器送至尾气焚烧炉的工艺(简称“常规工艺”,下同)进行焚烧,使烟气中的SO 2排放量增加100~200mg/Nm 3[2]。
为了控制SO 2的排放量,国家对污染物排放提出了更高的要求,发布GB 31570—2015《石油炼制工业污染物排放标准》,其中酸性气回收装置要求烟气中SO 2浓度小于400mg/m 3,环境敏感地区排放限值为100mg/m 3。
克劳斯硫回收系统常见问题及优化改进措施

克劳斯硫回收系统常见问题及优化改进措施摘要:近年来,随着环保形势日益严峻,煤化工与石油化工企业多采用克劳斯工艺进行对硫化氢酸性气进行处理。
克劳斯硫回收不仅回收了硫单质,创造了经济效益,而且降低了烟气脱硫成本。
但在其运行过程中存在不稳定因素,影响到生产效率的提高,现就常见问题进行原因分析,并提出了优化改进措施。
关键词:克劳斯硫回收;环保设施;经济效益晋煤集团天溪煤制油分公司年产30万t甲醇装置,变换气经低温甲醇洗脱除H2S后,经过再生浓缩生成25%~35%的H2S高浓度酸性气,送往年产0。
8万t克劳斯硫回收装置。
本装置采用分流法三级克劳斯工艺,硫回收率达到98%左右,运行相对稳定。
1克劳斯硫回收工艺介绍按照酸性气中H2S含量的区别,克劳斯法硫回收工艺分三种:直接氧化法、部分燃烧法以及分流法。
通常酸性气里面的H2S体积浓度小于15%时采取直接氧化法;H2S体积浓度超过50%时采取部分燃烧法;H2S浓度位于两者之间采取分流法。
我公司采用分流法:将三分之一的酸性气体通入燃烧炉,加入空气使其燃烧生成SO2,而其余三分之二酸性气走旁路,绕过燃烧室,与燃烧后的气体汇合进入催化剂床层进行反应。
克劳斯硫回收装置工艺流程主要有传统克劳斯工艺、超级克劳斯工艺和带有SCOT尾气处理的克劳斯工艺等。
其中传统克劳斯工艺三级转换,要求H2S、SO2摩尔比值为2的条件下进行;超级克劳斯工艺是在两级普通克劳斯转化之后,第三级改用选择性氧化催化剂,将H2S直接氧化成元素硫,硫回收率可以从98%提升至99。
5%;而带有SCOT尾气处理的克劳斯工艺,通过第三级加氢还原将过程气中的SO2和单质硫转化为H2S,同时将COS和CS2水解为H2S,采用MDEA吸收尾气中的H2S,胺溶液经加热再生循环使用,再生塔顶的酸性气送制硫燃烧炉,吸收塔顶尾气送尾气焚烧炉燃烧后达标排放。
我公司采用传统三级克劳斯工艺,尾气送至锅炉进行焚烧,炉内进行干法脱硫后,通过镁法脱硫,实现环保排放合格。
克劳斯硫回收系统优化改进总结

克劳斯硫回收系统生产的硫磺主要以液硫形 式出售,液硫合格品执行标准 《工业硫磺 第 2 部分:液体产品》(GB/T24492—2015);另外, 据市场需求也可将部分液硫送往硫磺造粒系统生 产固体硫磺,固体硫磺合格品执行标准 《工业 硫磺 第 1部 分: 固 体 产 品 》(GB/T24491— 2014)。
进作一总结。
2 运行中存在的问题及优化改进
21 酸性气燃烧炉点火改用燃料气 211 酸性气燃烧炉原点火方式存在的问题
克劳斯硫回收系统酸性气燃烧炉点火原设计 采用液化气点火,点火成功并燃烧稳定后再逐渐 改用 工 厂 燃 料 气 (甲 醇 装 置 燃 料 气 管 网 燃 料 气)。点火时,先 将 液 化 气 引 至 界 区 自 调 阀 前, 接着控制室点击主燃烧炉点火按钮,酸性气燃烧 炉氮气置换程序即自启动,置换 5min后,点火 枪插入,进主烧嘴的空气切断阀打开供给助燃空 气,然后液化气进主烧嘴切断阀打开,点火枪打 火;一般 5s内应点火成功,否则燃烧器脱扣跳 闸,需重新进行点火。但实际生产中发现,液化 气点火效果不太理想,需多次点火才能稳定燃 烧,切换为工厂燃料气的过程中易出现熄灭现 象,不得不重新点火;此外,液化气价格高,液 化气站安全管理要求高,每年的维护费用很高。 212 优化改进措施
[关键词]克劳斯硫回收系统;酸性气燃烧炉点火方式;酸性气燃烧炉炉温;副产中压蒸汽外送;保温 蒸汽余热利用;催化剂床层 “飞温”;系统压力;优化改进
克劳斯硫磺回收控制系统研究与设计

克劳斯硫磺回收控制系统研究与设计克劳斯硫磺回收控制系统研究与设计引言:硫磺是一种重要的化工原料,广泛应用于化肥、农药、医药、橡胶等行业中。
正因为其广泛应用,硫磺污染在工业生产中成为一个不可忽视的环境问题。
严重的硫磺污染不仅会危害环境,还会对工人的健康造成威胁。
因此,开发高效的硫磺回收控制系统至关重要。
一、硫磺污染的主要问题:1. 大气污染:硫磺燃烧会释放大量的二氧化硫,形成酸雨,对大气环境造成严重污染。
2. 水体污染:硫磺在水中溶解后会形成亚硫酸、硫酸等物质,对水体的生态平衡产生不利影响。
3. 土壤污染:硫磺流入土壤后会导致土壤酸化,降低土壤肥力。
4. 对人体健康的影响:硫磺燃烧产生的二氧化硫和硫酸等有害物质,对呼吸系统和消化系统造成损害。
二、克劳斯硫磺回收控制系统的设计思路:1. 增加燃烧效率:通过改进燃烧设备,提高硫磺燃烧效率,减少二氧化硫的排放。
2. 废气净化技术:采用干式或湿式烟气净化技术,去除燃烧后的硫酸和硫化氢等有害气体,达到排放标准。
3. 液体处理技术:针对水体中的硫酸盐和亚硫酸盐,采用沉淀、过滤等工艺,将其中的硫磺回收利用。
4. 土壤修复技术:通过添加中性化合剂,改善酸性土壤,恢复土壤肥力。
5. 生物处理技术:采用生物反应器、微生物降解等方法,将硫酸盐和亚硫酸盐转化为无害的物质。
三、克劳斯硫磺回收控制系统的关键技术:1. 燃烧器的优化设计:通过改变燃料喷射、燃烧区结构等参数,提高燃烧效率和燃烧稳定性。
2. 气液分离技术:采用静电旋风分离器、湿式电除尘器等装置,有效去除烟尘颗粒和硫酸雾滴。
3. 硫酸盐和亚硫酸盐回收技术:通过逆渗透膜、离子交换树脂等方法,将硫酸盐和亚硫酸盐从水中分离和浓缩,以便后续的资源化利用。
4. 微生物降解技术:通过选择和培养适宜的微生物,使其能够将硫酸盐和亚硫酸盐转化为无害的气体或物质。
四、系统的成本效益分析:克劳斯硫磺回收控制系统的成本主要包括设备投资、设备运行维护成本以及后续的废水和废气的处理费用。
克劳斯硫磺回收工艺装置设计
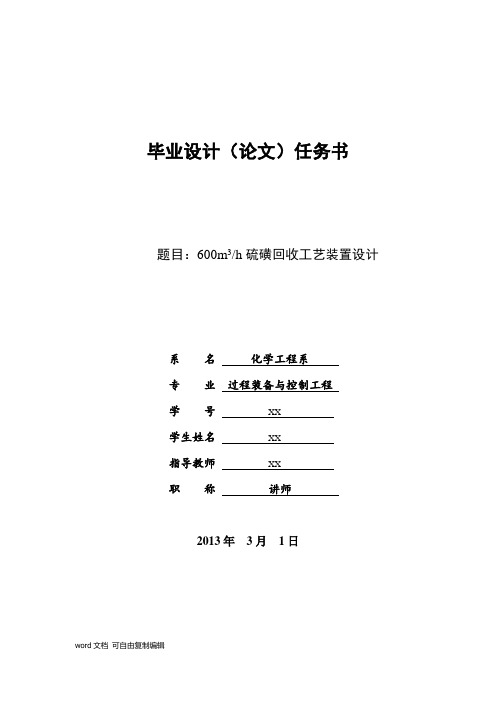
毕业设计(论文)任务书题目:600m3/h硫磺回收工艺装置设计系名化学工程系专业过程装备与控制工程学号XX学生姓名XX指导教师XX职称讲师2013年3月1日一、原始依据1.设计规模:装置正常处理能力:酸性气量600m3/h最大生产能力:10%设计余量年操作日:330天2.气体组成:(1)酸性气的组分:组成氢气一氧化碳二氧化碳硫化氢硫氧化碳H2O Σ湿基备注V% 0.41 0.95 1.00 92.42 0.03 5.19 100.0温度:40 ℃,压力:0.145MPa(a)(2)放空气体的组成要求H2S V% ≤ 0.01%温度:≤54℃,压力:0.115MPa(a)克劳斯反应的基本原理:1883年英国化学家Claus开发了H2S氧化制硫的方法,即:3H2S+3/2O2 =cat/570~600K= 3/xSx+3H2O+615KJ/mol上式称为克劳斯反应,这一经典的反应由于强的放热而很艰难维持合适的温度,只能借助于限制处理量来获得80%~90%的转化率。
20世纪30年代,德国法本公司将克劳斯工艺发展为改良克劳斯工艺,H2S的部分氧化分两阶段完成,同时忽略了烃类和其他可燃性气体的反应。
第一阶段是1/3的H2S氧化为SO2的自由火焰氧化反应(高温放热反应或燃烧反应),第二阶段是余下的2/3的H2S在催化剂上与反应炉中生成的SO2反应(中等放热的催化反应),由于酸气中含有烃、CO2、水等杂质,他们在反应炉达到的高温下将发生复杂的副反应,导致生成COS、CS2、CO和H2,反应平衡是复杂的。
二、参考文献[1] [美]气体加工和供应者协会.气体加工工程数据手册[M].北京:石油工业出版社,1992.[2] 南京化学工业公司设计院.硫酸工艺设计手册[M].南京:化工部硫酸工业科技情报中心站,1990.[3] 刘光启,马连湘,刘杰.化学化工物性数据手册[M].北京:化学工业出版社,2002.[4] 禹晓伟,王百森,黄福泉.化学化工物性数据手册[M].北京:中国石化出版社,2010.[5] 刘天齐.三废处理工程技术手册(废气卷)[M].北京:化学工业出版社,1999.[6] GA VIN MCINTYRE,LILI L YDDON.Claus Sulphur Recovery Options [J].Bryan Researchand Engineering,1997:57-61.三、设计(研究)内容和要求产品规格:硫磺纯度≥99.5 其余为有机杂质采样时间纯(S), % 硫磺度,% 灰份,% 有机物,% 砷含量,% 铁含量,% 水份,% 执行指标≥99.5 ≤0.005 ≤0.10 ≤0.30 ≤0.01 ≤0.005 ≤2.0设计内容:(1)600m3/h硫磺回收工艺装置设计(2)物料衡算、热量衡算(3)主要生产设备设计计算与选型(4)编写设计说明书(5)绘制设计图纸厂址选择:天津静海开发区指导教师(签字)年月日审题小组组长(签字)年月日XX大学XX学院本科生毕业设计(论文)开题报告毕业设计(论文)说明书题目:600m3/h硫磺回收工艺装置设计系名化学工程系专业过程装备与控制工程学号XX学生姓名XX指导教师XX2013年5月29日摘要随着工业产生的含硫尾气日益增多,硫磺回收工艺迅速发展。
克劳斯硫回收控制系统研究与设计

克劳斯硫回收控制系统研究与设计发表时间:2019-05-24T11:15:37.327Z 来源:《电力设备》2018年第32期作者:李明泽[导读] 摘要:随着我国经济高速发展和工业化步伐的加快,能源消耗急剧增加,导致环境日益恶化,如何在工业生产各环节实现能源的高效利用及减少污染排放量是实现工业可持续发展的首要任务。
(内蒙古大唐国际克什克腾煤制天然气有限责任公司内蒙古赤峰 025350)摘要:随着我国经济高速发展和工业化步伐的加快,能源消耗急剧增加,导致环境日益恶化,如何在工业生产各环节实现能源的高效利用及减少污染排放量是实现工业可持续发展的首要任务。
目前,随着全球天然气资源的大量开发,硫磺回收工段成为工业生产中重要的环保工艺,且克劳斯硫磺回收工艺是工业硫回收的主流工艺。
优化克劳斯硫磺回收自动控制系统,提升系统自动化水平和稳定性,保证系统安全运行,提高硫磺回收率,减少污染气体的排放,不仅具有一定的经济意义,而且具有重要的社会意义和环保意义。
关键词:克劳斯硫;回收控制系统;研究;设计自20世纪30年代以来,以酸性气体(主要是硫化氢)为原料的改进硫磺回收和环保装置已在世界范围内逐步工业化,并在科学研究和实际应用中迅速发展。
基于克劳斯(Claus)工艺的硫磺回收装置中硫的回收率仅为96%~97%,而4%的元素硫以SO2的形式直接排放到大气中,造成严重的环境污染问题。
与此同时,世界各国工业化的快速发展加速了污染源的扩大和污染物的扩散。
环境保护越来越受到重视,一些国家已经颁布了相应法规。
虽然不同国家实施的环境标准在国内外并不相同,但各国都在改善我们的共同生活环境,从不同角度不断研究和提高硫磺回收工艺,共同提高硫磺回收效率。
硫化氢尾气在焚烧前被焚烧,没有任何其他处理环节。
此外,焚烧系统使聚集在一起的硫化氢在无法控制的恶劣天气如雨,雪,大风等条件下不燃烧排出,对当地环境有一定的影响。
由于硫化氢的平均分子量大于空气的平均分子量,因此在从高空排出后会集中在排放点附近,导致牲畜和人的中毒。
- 1、下载文档前请自行甄别文档内容的完整性,平台不提供额外的编辑、内容补充、找答案等附加服务。
- 2、"仅部分预览"的文档,不可在线预览部分如存在完整性等问题,可反馈申请退款(可完整预览的文档不适用该条件!)。
- 3、如文档侵犯您的权益,请联系客服反馈,我们会尽快为您处理(人工客服工作时间:9:00-18:30)。
克劳斯法硫回收装置液硫系统的优化设计
黄占修
(洛阳宏兴新能化工有限公司,河南省洛阳市471112)
摘要:克劳斯(Claus)法制硫是从酸性气中回收单质硫的重要技术之一。
在克劳斯硫回收装置的液硫回收系统设计中,常规做法是设置四级硫封罐,从四级硫封罐出来的液硫汇集成到一根总管后进入硫池中,存在液硫管线布置复杂、占地面积大等缺点。
优化设计方案提出,通过改变冷凝器出来的液硫流向,在液硫线上增设U型弯,克服硫冷凝器、反应器之间的压力降,在过程气间形成有效液封,起到原设计中硫封罐的作用,相比常规做法可减少3个硫封罐的设置。
同时对液硫总线进硫池的方式、硫池内蒸汽伴热盘管等内构件的材质选择等方面存在的问题提出了相应优化措施。
关键词:Claus硫磺回收硫封罐硫池优化设计
1概述
随着含硫原油和含硫天然气的开发利用,用克劳斯(Claus)法从酸性气中回收单质硫元素的工艺已成为加工含硫天然气或炼厂气的一种重要形式。
Claus法回收单质硫元素主要分两个阶段⑴,一个是高温热反应阶段,主要在酸性气燃烧炉内完成,控制炉膛温度一般不低于980¾[2],炉内H?S的转化率为65%-70%;另一个是催化反应阶段,控制酸性气燃烧炉出口过程气中H?S和SO2的摩尔比为2:1,在反应器内Claus催化剂参与下,和SO?完成氧化还原反应,生成单质硫,该阶段单质硫元素收率约25%~30%。
一般认为,在合适的操作条件下,Claus制硫部分总硫转化率约95%⑶。
为提高催化反应阶段单质硫元素的转化率,利用硫冷凝器冷却去除过程气中的单质硫蒸汽,降低生成物分压,促进比S和SO2的反应向正方向进行。
硫蒸汽冷凝成液硫后,由液硫回收系统统一回收到硫池,进一步脱气、成型处理。
图1为Claus工艺原则流程。
图1克劳斯制硫工艺原则流程
液硫回收系统由硫封罐、液硫管线、地下硫池组成。
若硫封罐或硫池设置不合理,容易岀现液硫管线布置不集中、占地面积大、液硫凝固堵塞,甚至会出现液硫池中液硫倒窜、硫池着火等安全事故,影响装置长周期运行。
2硫封罐优化设计
2.1硫封罐的原理及作用
Claus制硫工艺中生成的液硫,在酸性气燃烧炉废热锅炉或硫磺冷凝器中完成气液分离,液硫自流进入硫封罐中。
硫封罐设置有一定高度,靠液硫自
重产生的静压形成液封,避免过程气随液硫经硫池窜入大气中,实现过程气和液硫的气液分离以及反应系统和液硫储存系统的隔离⑷。
典型硫封罐结构见图2。
图2硫封罐典型结构
硫封罐整体采用0.4MPa蒸汽夹套伴热,防止液硫凝固,蒸汽冷凝液自硫封罐底部排出。
液硫进入硫封罐后经内管靠重力自流至硫封罐底部,再从外管溢流进入硫池,内管液位和溢流口之间的高度差H就是实际的硫封有效高度,H形成的液柱静压P即是装置所允许的最高系统压力,系统压力大于P时,硫封被突破,过程气串入液硫池引发安全事故。
部分装置硫封液柱静压值P通常设为1.25-1.30⑴倍风机出口最高压力,即使风机故障导致Claus制硫装置系统压力达到设计最高值,也不会出现过程气突破硫封罐有效液封现象。
2.2硫封罐设置优化
2.2.1硫封罐常规布置
常规二级Claus制硫工艺中,一般在酸性气燃烧炉废热锅炉,一、二、三级硫冷凝器后各设一个硫封罐,液硫捕集器与三级硫冷凝器共用一个硫鞋罐(图1)。
部分装置在冷凝器后分设4个水泥井,四级硫封罐各自安装在井内,水泥井口与硫封罐用法兰连接固定;部分装置专设一个硫封坑,把4个硫封 罐集中布置在硫封坑内,硫封坑用钢板覆盖(图3);还有的装置把硫冷凝器布置在二层平台,一、二
冷凝器后的3个硫封罐悬空安装。
这3种布置方案,采用硫封坑集中布置时,在硫封坑内形成一密闭空间,很容易导致H?S在坑底部沉积,存在较大安全隐患,也存在占地面积大,液硫管线及相应的蒸汽伴热管线不好布管,不建议使用此种方案。
其他两种布置方案,均存在液硫管线及蒸汽伴热管线不好布置,硫封罐检修作业不方便等问题。
2.2.2硫封罐优化设计
如前所述,液硫罐最大有效硫封高度H形成的液柱静压P=pgH是反应系统所允许的最大工作压力,此种流程液硫走向:冷凝器一硫封罐一硫池,冷凝器端是最大工作压力,硫池端是常压,4个硫封罐液封高度相同。
硫封罐布置中,可以把前三级硫封罐取消,液体流向:酸性气燃烧炉废热锅炉出口-一级冷凝器岀口T二级冷凝器出口T三级冷凝器出口T总硫封罐-硫池(图4)。
由于硫冷凝器、反应器之间存在压力降,在酸性气燃烧炉废热锅炉、一、二级硫冷凝器出来的液硫管线上,各设一个U型弯,U型弯高度H1产生的静压值只需克服相邻设备间的最大压力降,即可满足各级硫冷凝器之间的过程气不互串的要求,前3级硫冷凝器产生的液硫汇集到一起进入总硫封罐.液硫由总硫封罐流入到硫池中。
设置总硫封罐的有效液封高度H不变,避免系统压力升高时过程气突破硫封,起到气液隔离效果。
如:液硫自一级冷凝器出来至二级冷凝器出口之间,设有一级反应器加热器、一级反应器和二级硫冷凝器,每台设备的压力降按5kPa计,则总压力降为15kPa,液硫密度取1780kg/n/,由P=pgHl可计算出U型弯的理论高度Hl=0.86m,考虑到异常工况可能导致设备压力降升高,把总压力降放大1.5倍,则U型弯高度可取1.3m。
为避免U型弯底部由于固体杂质积存出现液硫管线堵塞⑹,可增设排污阀门。
3硫池的优化设计
液硫池为钢筋混凝土结构,内衬为特种耐酸砖。
硫池内部用墙隔离,分为脱气池和成品池两部分。
硫冷凝器过来的液硫中含&S(质量分数300~ 400^8),采用合适的脱气措施,使液硫中H?S在脱气池脱除,脱气后液硫由泵导入到成品池,实现下一步的成型或液体装车出厂。
3.1液硫进硫池方式存在的问题及改进
存在的问题:从硫封罐过来的总液硫管线进硫池的配管设计中,部分装置把总液硫管线置于地沟内,从硫池侧面进入,如图5中a线所示。
由于液硫管线采用蒸汽夹套伴热,管线存在温度变化,热胀冷缩导致进入硫池时的管线与硫池壁接触面密封不严,存在间隙,一旦硫池内液硫液位高过进口位置,会出现液硫倒窜进入地沟,形成安全隐患。
如某炼油企业40kt/a硫回收装置,四级硫封罐集中布置在硫封坑内,总液硫管线通过地沟从硫池侧面进池,出现液硫从地沟回窜到硫池坑的情况,从硫封坑内一次清理出废硫磺约10t,后来只能用细沙把地沟填实,但不能从根本上避免液硫从硫池倒窜。
图5液硫进硫池示意
优化措施:适当提高硫封罐液硫出口高度,在满足液硫管线自流倾角要求前提下,液硫管线从硫池的顶部进入,如图5中b红线所示,避免液硫总线走地沟从硫池的侧面进池。
3.2液硫伴热盘管材质选用
存在的问题:液硫池内部设有蒸汽伴热盘管,主要用于液硫的加热保温,使液硫温度保持在138-148T C蒸汽伴热盘管材质多采用20号钢,但这种材质极易与硫反应生成FeS。
目前多数装置液硫脱气采用非净化风鼓泡脱气方式,使硫池的气相空间中保持有一定浓度的氧气,即使采用其他液硫脱气方式,由于液硫池密封不严,液硫脱气产生的含硫废气通过蒸汽喷射器抽至尾气焚烧炉或酸性气炉处理,使液硫池处于微负压状态,仍会导致空气进入硫池内,这样极易出现FeS自燃,发生硫池着火事故。
优化措施:硫池蒸汽伴热盘管的进汽、出水管线、液硫泵泵体、液位计、热电偶套管、支撑角钢等所有暴露在硫池气相空间的管件,全部采用更耐硫腐蚀的不锈钢材质,如316L等,尽可能减少FeS生成;为节省投资费用,平铺在硫池底部的蒸汽盘管由于长期淹没在液硫以下,与气相中的氧气隔离,极少岀现FeS自燃,此部分蒸汽盘管可采用20号钢材质;但在装置检修,硫池中的液硫需排空作业时,需要加强蒸汽盘管FeS自燃监控;在正常生产时应注意避免硫池液位过低,防止底部蒸汽盘管暴露到含氧气相空间。
4结论
(l)
Claus制硫工艺中的液硫回收系统有四级
并联式硫封罐,优化设计后,改液硫并联为串联,并在液硫线上增加U型弯,克服设备间的压力降,避免过程气互串。
用U型弯代替原设计的硫封罐,可减少3个硫封罐的设置,节省设备费、施工费等各种费用约40余万元。
由于静设备减少,液硫管线更易配置,减少了占地面积,也节约了3个硫封罐的伴热蒸汽消耗。
(2)液硫管线进硫池应首选从上部进入,避免由于液硫管线从硫池的侧面进入时液硫管线与硫池壁密封不严,当硫池液位高时,液硫从密封点的环隙向外泄漏的风险。
(3)硫池内构件采用20号钢材质时,有生成FeS的可能性,与氧气反应会出现硫池着火事故。
暴露在气相空间的管件宜采用如316L等不锈钢材质,减少FeS生成;平铺在硫池底部的盘管,液硫与气相空间隔离,不与气相中的氧气接触,发生FeS自燃的几率较低,可以采用20号钢材质,但在装置停工检修硫池抽空时,需加强FeS自燃监控。
参考文献:
[1]陈庚良,肖学兰,杨仲熙,等.克劳斯法硫磺回收工艺技
术[M].北京:石油工业出版社,2007:4.
[2]黄婉露,文竟伟.Claus硫磺回收工艺影响因素探讨
[J].化学工程与装备,2012(6):60,
[3]陈處良.克劳斯法硫磺回收工艺技术发展评述[J].天
然气与石油,2013,31(4):24.
[4]单鹏华.液硫封罐的制造[J].石油和化工设备,2017,
20(3):17.
[5]张宪忠.硫磺回收装置硫封突破的原因分析及预防
[J].广东化工,2018,45(12):212.
[6]崔显德.硫磺装置常见堵塞部位及其预防[J].山东化
X,2011,40(7):85,。