克劳斯硫回收操作规
克劳斯硫回收工艺总结含流程图
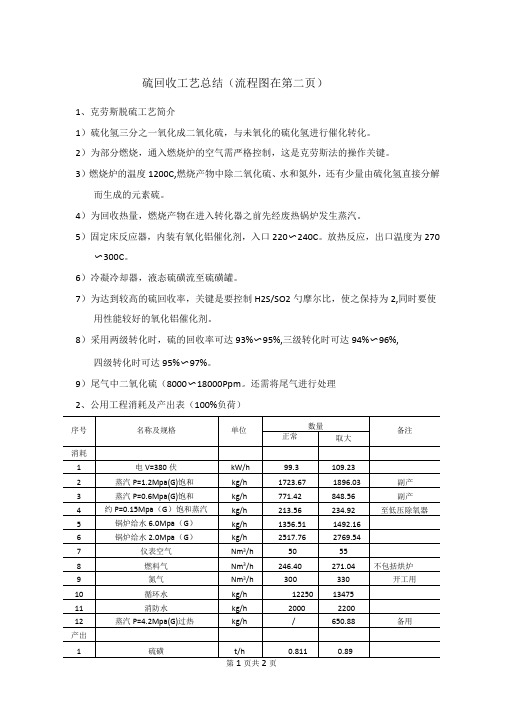
硫回收工艺总结(流程图在第二页)1、克劳斯脱硫工艺简介1)硫化氢三分之一氧化成二氧化硫,与未氧化的硫化氢进行催化转化。
2)为部分燃烧,通入燃烧炉的空气需严格控制,这是克劳斯法的操作关键。
3)燃烧炉的温度1200C,燃烧产物中除二氧化硫、水和氮外,还有少量由硫化氢直接分解而生成的元素硫。
4)为回收热量,燃烧产物在进入转化器之前先经废热锅炉发生蒸汽。
5)固定床反应器,内装有氧化铝催化剂,入口220〜240C。
放热反应,出口温度为270〜300C。
6)冷凝冷却器,液态硫磺流至硫磺罐。
7)为达到较高的硫回收率,关键是要控制H2S/SO2勺摩尔比,使之保持为2,同时要使用性能较好的氧化铝催化剂。
8)采用两级转化时,硫的回收率可达93%〜95%,三级转化时可达94%〜96%,四级转化时可达95%〜97%。
9)尾气中二氧化硫(8000〜18000Ppm。
还需将尾气进行处理2、公用工程消耗及产出表(100%负荷)第页共页空气燃料气变换汽提气酸性气闪蒸酸性气F=1200Nm3气靖解F=1700Nm3,H2S33%,CO260%*-w主烧嘴主燃烧室3000Nm3,900C中压蒸汽一级废锅、।F=90Nm3H2S+3/2O2-SO2+H2OH2S+I/2SO2TH2O+3/4S气分离F=1650Nm3,H2S35% CO260%(克劳斯脱硫总■阿I 320c中压蒸汽3.8MPa230 C,0.044MPa2H2s+SO2f3/xSx+2H2OCOS+H2O-H2s+CO2CS2+2H2O-2H2s+CO2T=280C,P=0.04MPa,H2s=2%入口气量:1700Nm3 出去火炬:4000Nm3 硫磺外售:800kg/h2H2s+SO2T3/xSx+2H2H t中压蒸汽3.8MPa170℃F=2700Nm3100m32800Nm3,220C,0.035MPaCOS+H2。
7H2s+CO—二级再热器T=230C,P=0.03MPa,H2s=0.3%2H2S+O2T2/xSx+2H2O副产中压蒸汽100kg/h催化氧化支应器F=1200Nm3,P=30KPa第2页共2页。
硫磺回收系统的操作要求和工艺指标

一、制硫工艺原理硫磺回收系统的操作要求和工艺指标Claus制硫总的反应可以表示为:2H2S+02/X S x+2H20在反应炉内,上述反应是部分燃烧法的主要反应,反应比率随炉温变化而变化,炉温越高平衡转化率越高;除上述反应外,还进行以下主反应:2H2S+3O2=2SO2+2H2O在转化器中发生以下主反应:2H2S+SO23/XS x+2H2O由于复杂的酸性气组成,反应炉内可能发生以下副反应:2S+2CO2COS+CO+SO22CO2+3S=2COS+SO2CO+S=COS在转化器中,在300摄氏度以上还发生CS2和COS的水解反应:COS+H2O=H2S+CO2二、流程描述来自上游的酸性气进入制硫燃烧炉的火嘴;根据制硫反应需氧量,通过比值调节严格控制进炉空气量,经燃烧,在制硫燃烧炉内约65%(v)的H2S进行高温克劳斯反应转化为硫,余下的H2S中有1/3转化为SO2燃烧时所需空气由制硫炉鼓风机供给。
制硫燃烧炉的配风量是关键,并根据分析数据调节供风管道上的调节阀,使过程气中的H2S/SO2比率始终趋近2:1,从而获得最高的Claus转化率。
自制硫炉排出的高温过程气,小部分通过高温掺合阀调节一、二级转化器的入口温度,其余部分进入一级冷凝冷却器冷至160℃,在一级冷凝冷却器管程出口,冷凝下来的液体硫磺与过程气分离,自底部流出进入硫封罐。
一级冷凝冷却器管程出口160℃的过程气,通过高温掺合阀与高温过程气混合后,温度达到261℃进入一级转化器,在催化剂的作用下,过程气中的H2S和SO2转化为元素硫。
反应后的气体温度为323℃,进入二级冷凝冷却器;过程气冷却至160℃,二级冷凝冷却器冷凝下来的液体硫磺,在管程出口与过程气分离,自底部流出进入硫封罐。
分离后的过程气通过高温掺合阀与高温过程气混合后温度达到225℃进入二级转化器。
在催化剂作用下,过程气中剩余的H2S和SO2进一步转化为元素硫。
反应后的过程气进入三级冷凝冷却器,温度从246℃被冷却至1.60~C。
克劳斯硫回收操作规程
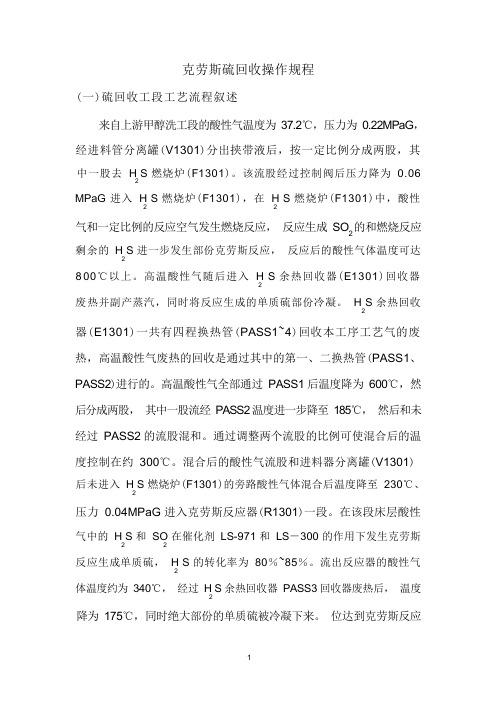
克劳斯硫回收操作规程(一)硫回收工段工艺流程叙述来自上游甲醇洗工段的酸性气温度为37.2℃,压力为0.22MPaG,经进料管分离罐(V1301)分出挟带液后,按一定比例分成两股,其中一股去H S 燃烧炉(F1301)。
该流股经过控制阀后压力降为0.06 2MPaG 进入H S 燃烧炉(F1301),在H S 燃烧炉(F1301)中,酸性2 2气和一定比例的反应空气发生燃烧反应,反应生成SO的和燃烧反应2剩余的H S 进一步发生部份克劳斯反应,反应后的酸性气体温度可达2800℃以上。
高温酸性气随后进入H S 余热回收器(E1301)回收器2废热并副产蒸汽,同时将反应生成的单质硫部份冷凝。
H S 余热回收2器(E1301)一共有四程换热管(PASS1~4)回收本工序工艺气的废热,高温酸性气废热的回收是通过其中的第一、二换热管(PASS1、PASS2)进行的。
高温酸性气全部通过PASS1 后温度降为600℃,然后分成两股,其中一股流经PASS2 温度进一步降至185℃,然后和未经过PASS2 的流股混和。
通过调整两个流股的比例可使混合后的温度控制在约300℃。
混合后的酸性气流股和进料器分离罐(V1301)后未进入H S 燃烧炉(F1301)的旁路酸性气体混合后温度降至230℃、2压力0.04MPaG 进入克劳斯反应器(R1301)一段。
在该段床层酸性气中的H S 和SO 在催化剂LS-971 和LS-300 的作用下发生克劳斯2 2反应生成单质硫,H S 的转化率为80%~85%。
流出反应器的酸性气2体温度约为340℃,经过H S 余热回收器PASS3 回收器废热后,温度2降为175℃,同时绝大部份的单质硫被冷凝下来。
位达到克劳斯反应器二段所需的温度,流程中设置了第一再加热器 (E1302),酸性气进入该加热器预热到约238℃后进入克劳斯反应器二段继续进行克劳斯反应以回收剩余的硫。
在二段反应床中,H S 的转化率约为75%,反2应后的酸性气温度约为255℃。
克劳斯硫回收接气步骤

硫回收岗位引酸气操作步骤:一、开工前准备于确认:1、D45002TI0509温度控制在900℃--_1000℃,R45001温度TI0515达到240℃±5℃,R45002温度TI1135A达到200℃±5℃,D45006温度TI2101达到850℃—900℃,TI2105控制在220—-260℃,TI0509温度可通过FV0108调节燃料气量进行,TI0515温度通过混合阀TV0515控制,TI1135A通过调节LV0525控制,TI2101温度可通过TV2101调解;各废热锅炉、冷凝器液位在50%——75%,当发现液位调节阀全开液位仍下降时要及时开旁路阀补水,如果液位仍然下降采取降低FI2103流量控制2、低温甲醇洗B框架PV0647阀门开100%,D45001入口手阀开100%,D45001导淋关闭及D45001顶部压力表根部阀打开,关酸气引入炉前PV0127阀,投用D45001液位计,对45001泵进行盘车、检查油位、油脂、是否送电3液位计、压力表、流量计、DCS、ESD等各仪表处于完好可控条件。
4、准备好各种防护用品:包括空气呼吸器、便携式防毒面具、四合一分析仪等报警系统好用备好扳手、对讲机等5、在岗员工做好开工准备,主操坚守岗位且能熟练操作,外操现场开工协助,要做到熟悉流程,能有效处置突发事件发生6、做好开工各种记录。
7、与化验分析取得联系,随时做好分析的准备。
取样点好用。
8、与调度联系,做好准备工作。
二、开工顺序燃料气和酸气混合燃烧在燃料气仍燃烧的情况下引入酸气,按下“启动酸气”按钮450HS0103,空气控制器从450FY0103设定一个自动设定点,酸气控制器设定为手动状态。
启动时,主空气控制器将按大致比率给酸气提供必要的燃烧空气。
将450FS0103设定到450FY0104B位置,并且将调整空气控制器设定为自动状态。
如果达到以下条件,可开始燃烧混合气:1、引燃烧嘴正在燃烧;2、主燃料气烧嘴正在燃烧(燃料气正在燃烧);3、燃烧炉的温度超过900℃;4、R-45002温度达到200℃左右。
681_岗位操作规程.

1 适用范围及职责范围1.1 适用范围本操作规程仅适用于克劳斯硫回收工号1.2 岗位任务681#硫回收装置的主要任务是接受51#、52#、53#送来的富H2S气体,通过该装置回收,制成片状硫磺,同时本装置采用烟囱组合型简易湿式脱硫装置,用稀氨水溶液喷淋吸收尾气中的SO2,使排放废气达到国家排放标准。
1.3 职责范围1.3.1 负责本工号所有设备、管线、仪表、电气等设施的操作、维护保养,主要设备有F68102酸性气分离器、C68101、C68102克劳斯反应器,D68101酸气燃烧炉、D68102尾气燃烧炉,W68101、W68105酸气(尾气)废锅及汽包、W68102、W68103、W68104换热器,W68107锅炉给水预热器、W68108锅炉给水冷却器、W68109过热气加热器,F68101A/B液硫捕焦器及K68101吸收塔B68110热水槽等设备。
1.3.2 在值班期间,坚守岗位,认真操作,并按时填写操作记录,遵守并严格执行各项工艺纪律和安全技术规定,做好巡检。
1.3.3 在值班期间,接受值班长的领导,对生产中出现的问题及时向值班长或有关领导汇报。
1.3.4 负责保管好本岗位的工器具及防护器材,做到文明生产。
1.3.5 认真做好交接班工作。
2 工艺指标及质量要求2.1 设计数据进工号酸性气总流量1405m3/h温度20℃压力0.18Mpa(A)出工号废气流量483.35m3/h温度150℃压力0.08Mpa(A)燃料气(用于开停车流量)100m3/h温度0℃压力0.75Mpa(A)2.2 正常操作指标C68101入口温度240℃C68102入口温度240℃D68101燃烧室温度1300℃D68102燃烧室温度1140℃入D68101空气压力0.06MPa(G)入D68102空气压力0.035MPa(G)入K68101空气压力0.06MPa(G)2.3 产品产量及规格硫横:543kg/h 其中含S≥99.8%副产低压蒸汽:7.45t/h 0.6MPa(A)158℃2.4 公用工程物料消耗用量低压锅炉给水0.8Mpa(G)105℃52500kg/h循环冷却水0.4Mpa(G)32℃42000kg/h低压蒸汽0.6Mpa(G)158℃1500kg/h(开车时间)低压氮气0.6Mpa(G)200Nm2/h(开停车用)高压蒸汽 3.8Mpa(G)420℃195kg/h2.5 催化剂2.5.1 硫磺回收催化剂物理性质:白色球状,直径4~6m m,比表面积≥300m2/g,抗压强度≥150N/颗,磨耗率<0.3%,孔容≥0.4m l/g,堆密度≥0.65k g/L,A l2O3>92%,一次装填量12m3。
硫回收岗位操作规程

硫回收岗位操作规程硫回收岗位操作规程一、岗位职责硫回收岗位是在炼油厂中负责对硫化氢进行回收以确保工厂生产安全和环境保护,具体职责如下:1. 对硫化氢进行回收,确保生产、操作过程中的安全性;2. 按照工艺流程,对回收硫化氢所得的硫进行处置;3. 其他与硫回收相关的负责职责。
二、操作规程1. 安全防护硫回收岗位操作是有一定风险的,因此,首先要建立负责人带领操作人员进行系统的安全培训。
在实际操作中需要进行个人防护,如戴胶手套、戴护目镜等,同时工作场所要保持干燥、防火、通风等条件。
2. 设备检查硫回收设备在每个工班开始作业前必须仔细检查设备,包括连接管道、热管、加热器、控制仪器等,确保设备处于正常工作状态。
同时在操作过程中,每隔一定时间对操作设备进行一次检查,发现故障及时处理。
3. 操作流程硫回收岗位的操作流程分为三步:a) 将含硫氢气体输送进硫回收塔。
b) 进行高温热解,将HS分解成H2和S。
在此步骤中,温度需要掌握好,过高容易引起其他问题,过低则会影响硫的产出。
c) 硫的进一步处理。
在结束时,应及时调整操作参数,防止设备超载。
4. 日常维护硫回收岗位为保持设备的稳定运行,要定期,定点进行设备维护,如清洗、检修、换热补等。
5. 紧急处置在意外情况下遇到问题,应立即切断气的供应管道,同时通知厂区相关人员参与紧急处理,并尽快撤离现场。
三、工艺要求1. 操作人员需经过严格的培训和考试,获得符合国家有关工艺操作标准的操作证书。
2. 严格按照标准操作,不得随意更改操作过程,确保设备处于正常运行状态。
3. 操作期间,加强对操作设备的监督和维护,确保设备的良好状态。
4. 对于工艺过程中出现异常情况,在保证安全的前提下,及时调整和控制。
5. 对于全天候的硫回收设备,需备有多组后备设置,以确保生产不因设备问题而中断。
四、检查及记录1. 在硫回收操作过程中,要对设备、工艺流程、安全防护等进行全面检查。
如发现问题和隐患,要立即停止操作,直至问题得到解决。
超级克劳斯硫磺回收工艺
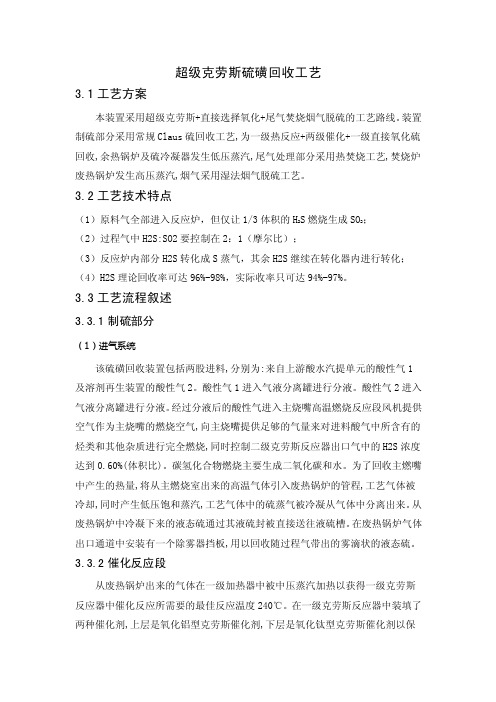
超级克劳斯硫磺回收工艺3.1工艺方案本装置采用超级克劳斯+直接选择氧化+尾气焚烧烟气脱硫的工艺路线。
装置制硫部分采用常规Claus硫回收工艺,为一级热反应+两级催化+一级直接氧化硫回收,余热锅炉及硫冷凝器发生低压蒸汽,尾气处理部分采用热焚烧工艺,焚烧炉废热锅炉发生高压蒸汽,烟气采用湿法烟气脱硫工艺。
3.2工艺技术特点(1)原料气全部进入反应炉,但仅让1/3体积的H2S燃烧生成SO2;(2)过程气中H2S:SO2要控制在2:1(摩尔比);(3)反应炉内部分H2S转化成S蒸气,其余H2S继续在转化器内进行转化;(4)H2S理论回收率可达96%-98%,实际收率只可达94%-97%。
3.3工艺流程叙述3.3.1制硫部分(1)进气系统该硫磺回收装置包括两股进料,分别为:来自上游酸水汽提单元的酸性气1及溶剂再生装置的酸性气2。
酸性气1进入气液分离罐进行分液。
酸性气2进入气液分离罐进行分液。
经过分液后的酸性气进入主烧嘴高温燃烧反应段风机提供空气作为主烧嘴的燃烧空气,向主烧嘴提供足够的气量来对进料酸气中所含有的烃类和其他杂质进行完全燃烧,同时控制二级克劳斯反应器出口气中的H2S浓度达到0.60%(体积比)。
碳氢化合物燃烧主要生成二氧化碳和水。
为了回收主燃嘴中产生的热量,将从主燃烧室出来的高温气体引入废热锅炉的管程,工艺气体被冷却,同时产生低压饱和蒸汽,工艺气体中的硫蒸气被冷凝从气体中分离出来。
从废热锅炉中冷凝下来的液态硫通过其液硫封被直接送往液硫槽。
在废热锅炉气体出口通道中安装有一个除雾器挡板,用以回收随过程气带出的雾滴状的液态硫。
3.3.2催化反应段从废热锅炉出来的气体在一级加热器中被中压蒸汽加热以获得一级克劳斯反应器中催化反应所需要的最佳反应温度240℃。
在一级克劳斯反应器中装填了两种催化剂,上层是氧化铝型克劳斯催化剂,下层是氧化钛型克劳斯催化剂以保证COS和CS2在催化床层下部进行水解反应。
一级克劳斯反应器入口温度通过进入一级加热器的中压蒸汽流量来进行调节控制。
硫回收操作规程
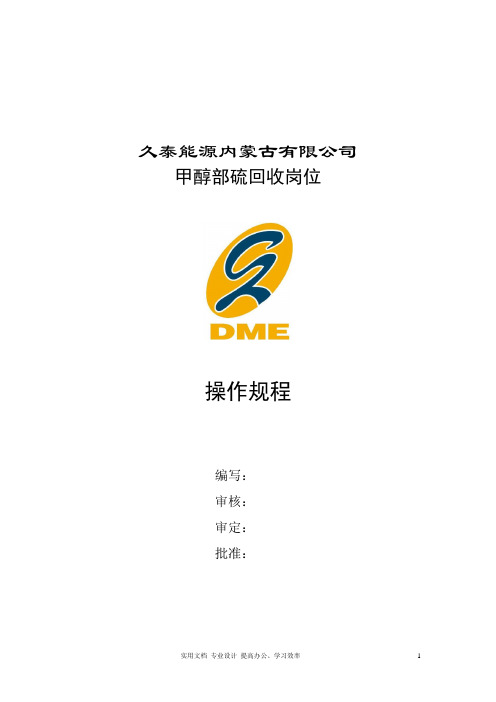
久泰能源内蒙古有限公司甲醇部硫回收岗位操作规程编写:审核:审定:批准:目录1.本工段任务‥‥‥‥‥‥‥‥‥‥‥‥‥‥‥‥‥‥‥‥‥‥22.生产方法、流程特点‥‥‥‥‥‥‥‥‥‥‥‥‥‥‥‥‥‥23.基本原理‥‥‥‥‥‥‥‥‥‥‥‥‥‥‥‥‥‥‥‥‥‥‥24.生产流程简述‥‥‥‥‥‥‥‥‥‥‥‥‥‥‥‥‥‥‥‥‥3 4.1热反应阶段‥‥‥‥‥‥‥‥‥‥‥‥‥‥‥‥‥‥‥‥‥3 4.2克劳斯反应阶段‥‥‥‥‥‥‥‥‥‥‥‥‥‥‥‥‥‥‥4 4.3尾气加氢处理阶段‥‥‥‥‥‥‥‥‥‥‥‥‥‥‥‥‥‥44.4热焚烧反应阶段‥‥‥‥‥‥‥‥‥‥‥‥‥‥‥‥‥‥‥55.主要控制指标‥‥‥‥‥‥‥‥‥‥‥‥‥‥‥‥‥‥‥‥‥56.主要设备介绍‥‥‥‥‥‥‥‥‥‥‥‥‥‥‥‥‥‥‥‥‥77.岗位生产操作法‥‥‥‥‥‥‥‥‥‥‥‥‥‥‥‥‥‥‥147.1开工前的准备‥‥‥‥‥‥‥‥‥‥‥‥‥‥‥‥‥‥‥147.2克劳斯硫回收部分‥‥‥‥‥‥‥‥‥‥‥‥‥‥‥‥‥157.3尾气加氢部分‥‥‥‥‥‥‥‥‥‥‥‥‥‥‥‥‥‥‥197.4紧急事故处理原则‥‥‥‥‥‥‥‥‥‥‥‥‥‥‥‥‥228.附件:‥‥‥‥‥‥‥‥‥‥‥‥‥‥‥‥‥‥‥‥‥24安全阀数据一览表‥‥‥‥‥‥‥‥‥‥‥‥‥‥‥‥‥24 硫回收工段试压方案‥‥‥‥‥‥‥‥‥‥‥‥‥‥‥‥‥24 克劳斯、加氢催化剂的装填方案‥‥‥‥‥‥‥‥‥‥‥‥‥26 点火烘炉方案‥‥‥‥‥‥‥‥‥‥‥‥‥‥‥‥‥‥‥‥27 点炉升温‥‥‥‥‥‥‥‥‥‥‥‥‥‥‥‥‥‥‥‥‥‥28 加氢加热炉的点火烘炉‥‥‥‥‥‥‥‥‥‥‥‥‥‥‥‥30 系统升温及系统保温‥‥‥‥‥‥‥‥‥‥‥‥‥‥‥‥‥30 引酸性气入系统‥‥‥‥‥‥‥‥‥‥‥‥‥‥‥‥‥‥‥32 装置停工‥‥‥‥‥‥‥‥‥‥‥‥‥‥‥‥‥‥‥‥‥‥391.本工段任务硫回收装置处理净化装置送来的富含硫化氢酸性气体将硫化氢转化成单质硫加以回收,生产出高品质硫磺,从而减少污染物排放,达到环保要求。
硫回收岗位操作规程

硫回收岗位操作规程硫回收岗位操作规程一、岗位任务、职责及范围1、岗位任务本岗位负责将系统来的酸气通过克劳斯炉还原为元素硫磺,并将尾气进行冷却处理后,并入吸煤气系统。
2、职责及范围2.1 在值班长或主操的领导下,负责本岗位的生产操作、设备维护、保养、清洁文明、环保、定置管理等工作。
2.2 认真执行各项规章制度,杜绝违章作业,保证安全生产,执行中控室指令,及时调控好工艺指标。
2.3 做好设备检修前的工艺处理和检修后的验收工作。
2.4 按时巡检,按时做好各项原始记录,书写仿宋化。
2.5 负责本岗位的正常开、停车及事故处理。
2.6 负责本岗位环境因素和危险源的控制,确保本岗位安全生产、环保、消防、卫生等各项工作符合规定要求。
2.7 贯彻执行岗位《操作技术规程》《工艺技术规程》《安全规程》有关规章制度。
2.8 搞好巡检工作,及时发现、处理和汇报安全隐患,保证各设备、换热器、反应器、管道、阀门畅通。
2.9 控制好本岗位“三废”排放,搞好环保工作。
二、巡回检查路线及检查内容1、巡回检查路线操作室→空气风机→克劳斯炉→废热锅炉→锅炉供水处理槽→硫反应器→硫分离器→硫封→硫池→煤气增压机→硫磺结片机→操作室2、检查内容巡检时间定为整点前十五分钟开始,整点结束;检查锅炉汽包液位、各温度、压力点变化情况,各润滑部位油位,润滑情况,各泵、增压机、空鼓有无异常声音,是否处于正常运行状态,进出口压力是否在指标范围内,有无漏点;硫封出硫是否正常,有无堵塞现象,夹套蒸汽是否畅通,有无漏点。
看地沟盖板是否完好,是否畅通,有无杂物淤积。
三、工艺流程、生产原理简述及主要设备工作原理1、工艺流程从再生塔顶来的约66—72℃含H2S约20﹪的酸汽酸汽(含有H2S、HCN和少量的NH3及CO2)送入一个带特殊燃烧器的克劳斯炉,在克劳斯炉燃烧室内加入主空气,使约1/3的H2S燃烧生成SO2,SO2再与2/3的H2S反应生成元素硫,反应热可使过程气维持在1100℃左右,当酸汽中H2S含量较低时,尚需补充少量煤气。
克劳斯法硫磺回收方法
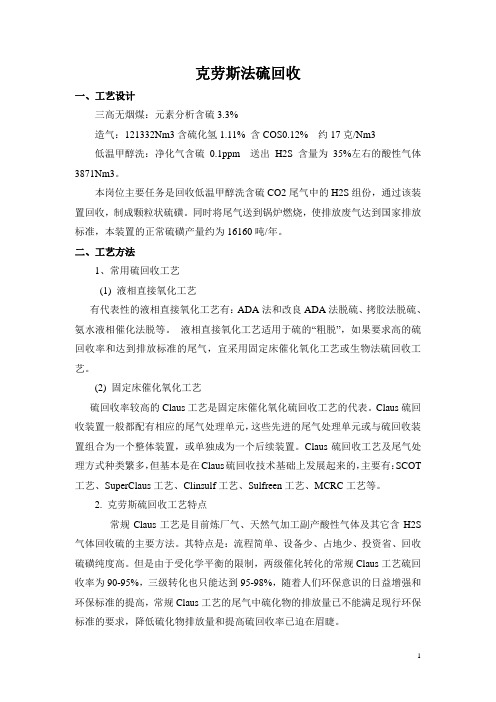
克劳斯法硫回收一、工艺设计三高无烟煤:元素分析含硫3.3%造气:121332Nm3含硫化氢1.11% 含COS0.12% 约17克/Nm3低温甲醇洗:净化气含硫0.1ppm 送出H2S含量为35%左右的酸性气体3871Nm3。
本岗位主要任务是回收低温甲醇洗含硫CO2尾气中的H2S组份,通过该装置回收,制成颗粒状硫磺。
同时将尾气送到锅炉燃烧,使排放废气达到国家排放标准,本装置的正常硫磺产量约为16160吨/年。
二、工艺方法1、常用硫回收工艺(1) 液相直接氧化工艺有代表性的液相直接氧化工艺有:ADA法和改良ADA法脱硫、拷胶法脱硫、氨水液相催化法脱等。
液相直接氧化工艺适用于硫的“粗脱”,如果要求高的硫回收率和达到排放标准的尾气,宜采用固定床催化氧化工艺或生物法硫回收工艺。
(2) 固定床催化氧化工艺硫回收率较高的Claus工艺是固定床催化氧化硫回收工艺的代表。
Claus硫回收装置一般都配有相应的尾气处理单元,这些先进的尾气处理单元或与硫回收装置组合为一个整体装置,或单独成为一个后续装置。
Claus硫回收工艺及尾气处理方式种类繁多,但基本是在Claus硫回收技术基础上发展起来的,主要有:SCOT 工艺、SuperClaus工艺、Clinsulf工艺、Sulfreen工艺、MCRC工艺等。
2. 克劳斯硫回收工艺特点常规Claus工艺是目前炼厂气、天然气加工副产酸性气体及其它含H2S 气体回收硫的主要方法。
其特点是:流程简单、设备少、占地少、投资省、回收硫磺纯度高。
但是由于受化学平衡的限制,两级催化转化的常规Claus工艺硫回收率为90-95%,三级转化也只能达到95-98%,随着人们环保意识的日益增强和环保标准的提高,常规Claus工艺的尾气中硫化物的排放量已不能满足现行环保标准的要求,降低硫化物排放量和提高硫回收率已迫在眉睫。
一般克劳斯尾气吸收要经过尾气焚烧炉,通过吸收塔,在吸收塔内用石灰乳溶液或稀氨水吸收,生成亚硫酸氢钙或亚硫酸氢铵,通过向溶液中通空气,转化为石膏或硫酸铵,达到无害处理,我公司硫回收尾气送至锅炉燃烧并脱硫后排放。
克劳斯硫回收操作规

克劳斯硫回收操作规程1. 岗位任务及意义我厂所采用的原料煤硫含量较高, 如果不加以回收,就会污染空气。
本岗位接受低温甲醇洗岗位送来的硫化氢尾气, 通过克劳斯回收装置回收,并制成固体硫磺。
本装置H2S的总转化率90-95 %; COS不发生克劳斯反应,通过尾气烟囱直接放空。
年产硫磺1 万吨,回收硫磺不仅经济效益可观还可以消除污染。
2. 工艺原理及流程叙述2.1工艺原理克劳斯法回收硫的基本反应如下:H2S+ 1/2Q—S+ H2O (1)H2S+ 3/ 2Q2—SQ+ H2Q (2)2H2S + SQ—3S+ 2H2Q (3)反应(1)(2)在燃烧室中进行,在温度1150C— 1300C,压力0.06MPa 和严格控制气量的条件下,将硫化氢燃烧成二氧化硫,为催化反应提供(H2S+ CS)/SQ为2/1的混合气体。
此气体通过ALQ基触媒,按反应(3)生成单质硫。
2.2流程叙述来自上游甲醇洗工序的酸性气温度为37.2 C,压力为0.22MPaG经进料管分离罐(V1301)分出挟带液后,按一定比例分成两股,其中一股去HtS 燃烧炉(F1301)。
该流股经过控制阀后压力降为0.06 MPaG 进入HS燃烧炉(F1301),在H2S燃烧炉(F1301 )中,酸性气和一定比例的反应空气发生燃烧反应,反应生成SO2 的和燃烧反应剩余的H2S进一步发生部分克劳斯反应,反应后的酸性气体温度可达800C以上。
高温酸性气随后进入H2S余热回收器(E1301)回收器废热并副产蒸汽,同时将反应生成的单质硫部分冷凝。
HS余热回收器(E1301)—共有四程换热管(PASS什4)回收本工序工艺气的废热,高温酸性气废热的回收是通过其中的第一、二换热管(PASS、PASS2进行的。
高温酸性气全部通过PASS1后温度降为600C,然后分成两股,其中一股流经PASS2温度进一步降至185C,然后和未经过PASS2勺流股混和。
通过调整两个流股的比例可使混合后的温度控制在约300 C o混合后的酸性气流股和进料器分离罐(V1301 )后未进入H2S燃烧炉(F1301)的旁路酸性气体混合后温度降至230C、压力0.04MPaG进入克劳斯反应器(R1301)—段。
硫回收操作规程..
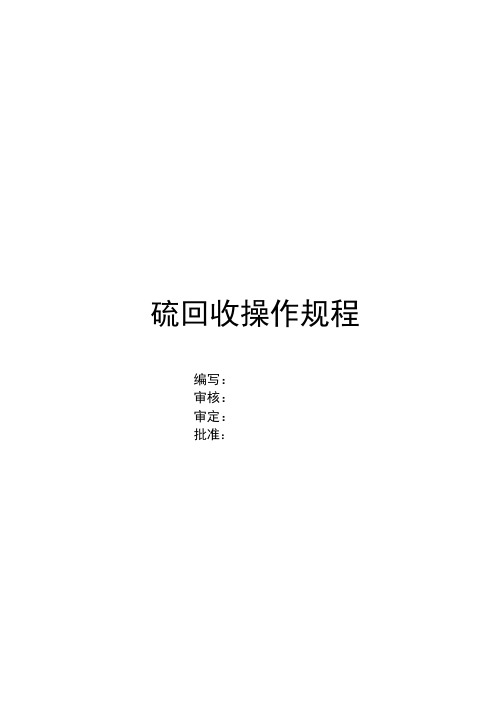
硫回收操作规程编写:审核:审定:批准:目录第一章: 工艺说明 (1)1.岗位任务 (1)2.管辖范围 (1)3.工艺原理 (1)4.工艺流程 (3)5.工艺联锁说明 (7)第二章:岗位操作法 (20)一.开车 (20)二.停车 (55)三.正常操作要点及注意事项 (61)四.硫磺回收装置故障分析 (66)五.紧急情况处理 (68)第三章:转动设备开停车及关键设备维护 (72)1.转动设备的开车 (72)2.转动设备停车 (74)3.关键设备维护 (75)第四章:安全技术要点及保安措施 (79)1.有毒有害气体性质 (79)2.保安措施 (80)第五章:工艺管理制度 (81)1.岗位责任制 (81)2.交接班制度 (82)3.设备维护保养制度 (83)4.巡回检查制度 (83)5.质量检查制度 (84)附表 (86)附表1:1223单元安全阀一览表 (86)附表2:1223单元工艺操作参数一览表(温度) (87)附表3:1223单元工艺操作参数一览表(压力) (90)附表4:1223单元工艺操作参数一览表(液位) (93)附表5:1223单元工艺操作参数一览表(流量) (95)附表6:取样分析一览表 (98)附表7:调节阀一览表 (99)附表8控制按钮、控制器 (101)附表9:1223单元设备一览表 (103)第一章: 工艺说明1.岗位任务本岗位的任务是将低温甲醇洗工序送来的酸性气体,通过燃烧氧化,部分H2S转化成SO2,然后H2S 与SO2经两级常规克劳斯催化反应和一级超优克劳斯催化反应、一级超级克劳斯催化反应,转化成单质硫。
通过硫磺造粒机生产纯度为99.9%(wt)的硫磺颗粒,包装出售;克劳斯尾气再经焚烧炉燃烧,H2S 完全燃烧转化成SO2,焚烧后的尾气经烟囱高空排放,保证排放到大气中的气体指标合格,符合环保要求。
2.管辖范围(1).塔C-2301,共1台(2).废热锅炉、换热器E-2301,E-2308、E-2302/03~E-2307,E-2309~E-2314共12台(3). 槽罐类V-2301~V-2307,共12台(4). 机泵类P-2301A/B~P-2303,K-2301A/B,共7台(5). 炉子F-2301(烧嘴),F-2302(烧嘴),F-2303,F-2304,共4台(6). 反应器R-2301/02/03/04,共1台(7). 其他:J-2301,X-2301,X-2302A/B,X-2303 共5台上述设备及设备的附属管线、阀门及仪表等。
硫回收岗位操作规程
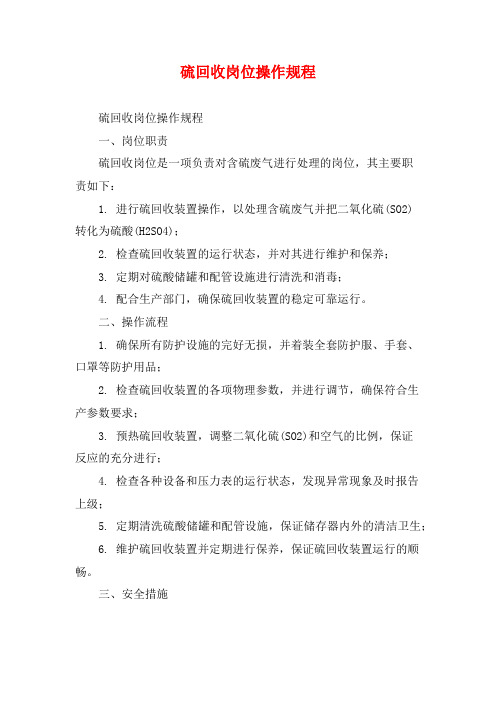
硫回收岗位操作规程硫回收岗位操作规程一、岗位职责硫回收岗位是一项负责对含硫废气进行处理的岗位,其主要职责如下:1. 进行硫回收装置操作,以处理含硫废气并把二氧化硫(SO2)转化为硫酸(H2SO4);2. 检查硫回收装置的运行状态,并对其进行维护和保养;3. 定期对硫酸储罐和配管设施进行清洗和消毒;4. 配合生产部门,确保硫回收装置的稳定可靠运行。
二、操作流程1. 确保所有防护设施的完好无损,并着装全套防护服、手套、口罩等防护用品;2. 检查硫回收装置的各项物理参数,并进行调节,确保符合生产参数要求;3. 预热硫回收装置,调整二氧化硫(SO2)和空气的比例,保证反应的充分进行;4. 检查各种设备和压力表的运行状态,发现异常现象及时报告上级;5. 定期清洗硫酸储罐和配管设施,保证储存器内外的清洁卫生;6. 维护硫回收装置并定期进行保养,保证硫回收装置运行的顺畅。
三、安全措施1. 确保各项设施的完好无损,设施的维护和操作周期要根据使用情况及时进行调整;2. 操作时要仔细阅读技术说明和安全规程,严格遵守操作规程和作业流程;3. 操作前需要对各项设施进行检查和维修,确保设备的正常运行;4. 在加入反应液时要缓慢且稳定,避免溅出和爆炸;5. 操作中应保持警觉,如有异常现象要及时报告上级;6. 操作后对相关设施进行清洗和消毒,保证器具的整洁卫生。
四、紧急处理1. 发生任何紧急情况要立即停止操作,并采取相应的安全措施;2. 如发生泄漏,要立即关闭泄漏口,并使用适当材料和手段进行清除和处理;3. 如发生工人意外事故,应立即拨打急救电话,做好相关抢救措施,及时报告上级。
五、操作注意事项1. 操作前必须穿戴全套防护服及其他防护设施,工作中需注意安全,切莫慌张或大意;2. 操作过程中如遇到其他工作人员前来观察或询问,要在确认安全情况下允许其观察;3. 操作人员应当时注意保养和检查所需装备的工作情况,及时报告工作质量问题,认真对待与工作有关的一切事宜。
硫磺回收装置工艺操作规程
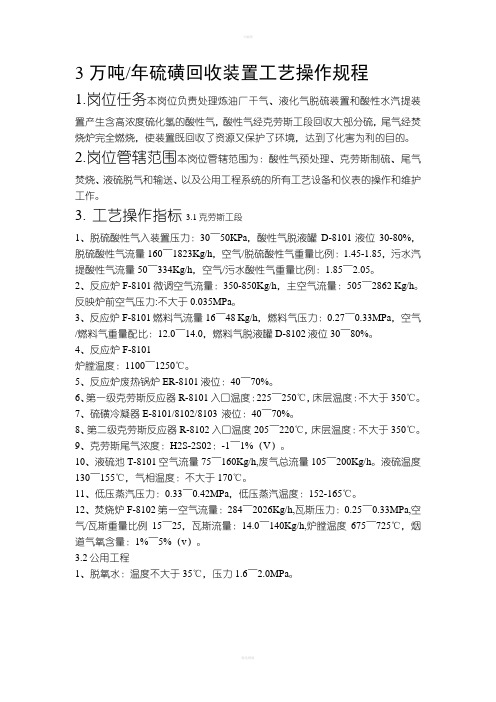
3万吨/年硫磺回收装置工艺操作规程1.岗位任务本岗位负责处理炼油厂干气、液化气脱硫装置和酸性水汽提装置产生含高浓度硫化氢的酸性气,酸性气经克劳斯工段回收大部分硫,尾气经焚烧炉完全燃烧,使装置既回收了资源又保护了环境,达到了化害为利的目的。
2.岗位管辖范围本岗位管辖范围为:酸性气预处理、克劳斯制硫、尾气焚烧、液硫脱气和输送、以及公用工程系统的所有工艺设备和仪表的操作和维护工作。
3. 工艺操作指标3.1克劳斯工段1、脱硫酸性气入装置压力:30~50KPa,酸性气脱液罐D-8101液位30-80%,脱硫酸性气流量160~1823Kg/h,空气/脱硫酸性气重量比例:1.45-1.85,污水汽提酸性气流量50~334Kg/h,空气/污水酸性气重量比例:1.85~2.05。
2、反应炉F-8101微调空气流量:350-850Kg/h,主空气流量:505~2862 Kg/h。
反映炉前空气压力:不大于0.035MPa。
3、反应炉F-8101燃料气流量16~48 Kg/h,燃料气压力:0.27~0.33MPa,空气/燃料气重量配比:12.0~14.0,燃料气脱液罐D-8102液位30~80%。
4、反应炉F-8101炉膛温度:1100~1250℃。
5、反应炉废热锅炉ER-8101液位:40~70%。
6、第一级克劳斯反应器R-8101入口温度:225~250℃,床层温度:不大于350℃。
7、硫磺冷凝器E-8101/8102/8103 液位:40~70%。
8、第二级克劳斯反应器R-8102入口温度205~220℃,床层温度:不大于350℃。
9、克劳斯尾气浓度:H2S-2S02:-1~1%(V)。
10、液硫池T-8101空气流量75~160Kg/h,废气总流量105~200Kg/h。
液硫温度130~155℃,气相温度:不大于170℃。
11、低压蒸汽压力:0.33~0.42MPa,低压蒸汽温度:152-165℃。
12、焚烧炉F-8102第一空气流量:284~2026Kg/h,瓦斯压力:0.25~0.33MPa,空气/瓦斯重量比例15~25,瓦斯流量:14.0~140Kg/h,炉膛温度675~725℃,烟道气氧含量:1%~5%(v)。
克劳斯硫回收原始开车方案

原始开车1烘炉1.1 烘炉目的:大修后或新开工的炉子,需脱除耐火衬里的水份和结晶水,使耐火材料达到一定强度,并让炉体各部位在热状态下的设备情况能满足工艺生产要求。
1.2 烘炉步骤:1.2.1 本燃烧炉烘炉曲线规定如下;a)升温到120□,升温速度15□∕h,需用时间8h;b) 120□上保温32h;c) 120口升温至U300口,升温速度10□∕h,需用时间18h;d) 300□上保温32h;e) 300□升温至∣J5OO□,升温速度10口∕h,需用时间20h;f) 500□上保温20h;g) 500□升温至∣J8OO□,升温速度25口∕h,需用时间12h;h)在800□上保温8ho全部烘炉过程累计时间150h,烘炉完成后,应自然冷却。
1.2.2 做好点火准备,按点火规程进行点火。
1.2.3 火点着后,利用燃料气和空气量来调节升温速度;1.2.4 绘制实际升温曲线;3.4.2点火操作燃烧炉系统包括:主风机、燃烧炉、废热锅炉及汽包,点火前必须系统试压、试漏、吹扫、清洗合格后才能点火运行。
3.3.4.2.1 点火前的准备:a)各设备及仪表正常且处于备用状态。
b)开工烟囱畅通,E2301出口阀已关闭。
c)关闭FV2321,将N2引至炉前备用。
d)启动风机,打开FV2315并关闭E2311出口阀将空气炉前放空备用;e)关闭FV2322将燃料气引至炉前(经分析氧含量小于0.5%方合格),并将压力保持在0.2〜0.3MPa;f)对废热锅炉先用低压蒸汽预热,待点火正常约15分钟左右,加水建立废热锅炉液位。
然后打开V2305放空阀,关闭PV2326;g)打开FV2321,用N2置换炉内至CO+H2<0.5%; h)打开系统伴热蒸汽,并排放冷凝水;D打开点火所需电磁阀。
3.3.4.2.2 点火燃烧炉点火操作通常在就地点火控制柜(见YKGR-K01)上进行:3.3.4.2.2.1 开点火控制柜电源按钮(36),电源指示灯(37)亮;3.3.4.2.2.2 燃烧炉在其各个参数检测正常后,检测风门控制挡板位置,处于关闭位置时,可启动风机;3.3.4.223 启动后,柜上启动联锁灯(35)亮;3.3.422.4 操作点火开关(38)到扫风位置,吹扫中灯(23)亮;3.3.422.5 五分钟后,吹扫完成,吹扫中灯(23)灭;3.3.422.6 燃烧炉点火灯(25)亮;3.3.422.7 操作点火开关(38)1切到点火位置;3.3.422.8 点火燃料气切断阀开灯(26)亮;3.3.422.9 火焰正常灯,(31)亮;3.3.422.10 燃料气调节阀最小位置灯(32)亮;3.3.422.11 11燃料气切断阀开灯(29)亮;3.3.422.12 操作点火开关(38)切到运行位置,点火燃料气切断阀关灯(27)亮。
硫回收操作规程 最终版

净化专业硫回收操作规程编制:审核:审定:批准:一、引言3二、工艺描述:3三、操作及控制描述9四、试车18五、首次开车29六、停车36七、安全42八、故障排除47九、维护55十、正常操作指标:58十一:联锁报警值:62十二:联锁逻辑图:67一、引言硫磺回收装置的设计旨在对上游装置产生的酸气中的硫进行回收。
其工艺设计基于超优克劳斯和超级克劳斯工艺,从含H2S的气流中回收元素硫。
此工艺是传统克劳斯工艺与JNL工艺的结合,通过选择性地氧化硫化氢来得到硫(即通常所说的超级克劳斯工艺),及减少SO2生成 H2S及硫蒸汽的产生(即通常所说的超优克劳斯工艺)。
硫磺回收装置由一个热反应段组成。
在此过程中,部分H2S在空气中燃烧;接下来是两个克劳斯催化阶段以及一个超优克劳斯催化阶段和一个超级克劳斯催化阶段。
最后阶段的尾气被输送到焚烧炉。
液硫池可存储3天的硫磺产品。
二、工艺描述:1、化学过程:1.1热反应段本手册采用的硫磺回收工艺,即通常所说的EUROCLAUS®工艺,是基于硫化氢(H2S)与受控比率的99.6%纯氧气流进行的部分燃烧。
氧气流自动维持,以实现酸性原料气中所有碳氢化合物的完全氧化。
同时,在EUROCLAUS®催化阶段的出口获得0.5 % vol. 的H2S。
在传统Claus工艺中,氧气(空气)与酸气的比率应能保证催化废气中的H2S与SO2的比率刚好为2/1。
这个H2S与SO2的比率是Claus反应的最佳比率。
而EUROCLAUS®工艺的操作则是基于不同的原理。
在此工艺中,氧气与酸气的比率将调整,以便在SUPERCLAUS®催化阶段的入口处获得H2S浓度。
为适应此要求,前端燃烧步骤要在非Claus比率(H2S与SO2的比率高于2/1)下进行。
换言之,前端燃烧步骤的操作是基于对H2S反馈的控制,而非传统的对H2S/SO2反馈比率的控制。
过程气分析器将测量EUROCLAUS®阶段所产生的废气流中的H2S浓度。
克劳斯硫磺回收主要设备及操作条件

编号:AQ-JS-06458( 安全技术)单位:_____________________审批:_____________________日期:_____________________WORD文档/ A4打印/ 可编辑克劳斯硫磺回收主要设备及操作条件Main equipment and operating conditions of Claus sulfur recovery克劳斯硫磺回收主要设备及操作条件使用备注:技术安全主要是通过对技术和安全本质性的再认识以提高对技术和安全的理解,进而形成更加科学的技术安全观,并在新技术安全观指引下改进安全技术和安全措施,最终达到提高安全性的目的。
现以直流法为例,这类硫磺回收装置的主要设备有反应炉、余热锅炉、转化器、硫冷凝器和再热器等,其作用和特点如下。
1.反应炉反应炉又称燃烧炉,是克劳斯装置中最重要的设备。
反应炉的主要作用是:①使原料气中1/3体积的H2S氧化为SO2;②使原料气中烃类、硫醇氧化为CO2等惰性组分。
燃烧在还原状态下进行,压力为20~100kPa,其值主要取决于催化转化器级数和是否在下游需要尾气处理装置。
反应炉既可是外置式(与余热锅炉分开设置),也可是内置式(与余热锅炉组合为一体)。
在正常炉温(980~1370℃)时,外置式需用耐火材料衬里来保护金属表面,而内置式则因钢质火管外围有低温介质不需耐火材料。
对于规模超过30t/d硫磺回收装置,外置式反应炉更为经济。
无论从热力学和动力学角度来讲,较高的温度有利于提高转化率,但受反应炉内耐火材料的限制。
当原料气组成一定及确定了合适的风气比后,炉膛温度应是一个定值,并无多少调节余地。
反应炉内温度和原料气中H2S含量密切有关,当H2S含量小于30%时就需采用分流法、硫循环法和直接氧化法等才能保持火焰稳定。
但是,由于这些方法的酸气有部分或全部烃类不经燃烧而直接进入一级转化器,将导致重烃裂解生成炭沉积物,使催化剂失活和堵塞设备。
硫回收操作法.

硫回收操作法试行目录1.0简介2.0工艺描述2.1 工艺流程描述2.2 公用工程系统3.0操作与控制说明3.1 催化剂处理3.1.1 克劳斯催化剂活化3.1.2 超优克劳斯催化剂3.1.3 超级克劳斯催化剂3.2 正常操作3.2.1 操作变量与控制3.2.2 硫锁斗的堵塞3.2.3 考虑要点3.3 工艺控制,报警和安全保障系统3.4 温度失控3.4.1 克劳斯反应器内部着火3.4.2 超级克劳斯反应器内温度失控3.4.3 液硫槽中着火4.0试车4.1 简介4.2 废热锅炉和冷凝器的清扫4.2.1 废热锅炉/克劳斯冷凝器4.2.2 超级克劳斯冷凝器4.3 公用工程与仪表系统的试车4.4 燃料气引入与干燥4.4.1 引入4.4.2 简化轮廓图4.4.3 详细轮廓4.5 装填催化剂5.0原始开车5.1 装填催化剂后的升温5.2 引入原料气以前的准备工作5.3 引入原料气5.4 超级克劳斯投入使用5.5 液硫槽开车6.0停车6.1 概述6.2 短期停车步骤 (热备用)6.3 长期停车步骤(全面停车))6.4 液硫槽停止运行6.5 自动停车(跳车)6.6 自动停车 (跳车) 后的再次启动6.6.1 装置已经过升温而且硫磺在设备中时的再次启动6.6.2 装置为冷态而且硫碘在设备中时的再次启动6.6.3 硫磺不在设备中时的再次启动7.0安全S 监测设备7.1 环境 H27.2 特殊安全措施和工业卫生7.3 急救措施7.4 毒性数据S的生理影响7.4.1 H2的生理影响7.4.2 SO2S 的性质与毒性影响7.4.3 H2性质与毒性影响7.4.4 SO27.4.5 硫粉尘7.5 着火与爆炸数据8.0故障排除8.1 简介8.2 工艺问题8.2.1 概述8.2.2 烧嘴 & 燃烧室8.2.3 反应段8.2.4 焚烧炉8.2.5 液硫槽8.2.6 低硫回收8.2.7 压力降8.2.8 堵塞8.2.9 温度失控8.3 机械问题8.3.1 运行问题8.3.2 点火器8.3.3 锅炉或冷凝器泄漏8.3.4 耐火材料8.3.5 波动与携带的碳氢化合物8.3.6 腐蚀8.4 硫回收装置运行时的关键区域9.0维护9.1 设备9.1.1 洗涤器/气液分离罐9.1.2 预热器&再热器9.1.3 烧嘴9.1.4 燃烧室9.1.5 废热锅炉9.1.6 硫冷凝器9.1.7 反应器9.1.8 硫聚结器9.1.9 焚烧炉9.1.10 硫锁斗9.1.11 液硫槽9.1.12 液硫槽中的蒸汽盘管9.1.13 运行设备9.1.14 管道与阀门9.1.15 分析仪10.0附录:安全数据表1. 简介硫回收装置的设计目的是为了处理来自煤基化工装置的酸性废气。
克劳斯硫磺回收主要设备及操作条件
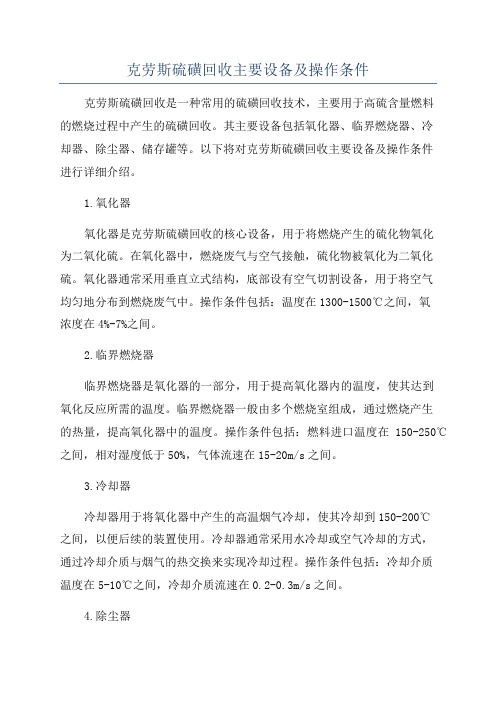
克劳斯硫磺回收主要设备及操作条件克劳斯硫磺回收是一种常用的硫磺回收技术,主要用于高硫含量燃料的燃烧过程中产生的硫磺回收。
其主要设备包括氧化器、临界燃烧器、冷却器、除尘器、储存罐等。
以下将对克劳斯硫磺回收主要设备及操作条件进行详细介绍。
1.氧化器氧化器是克劳斯硫磺回收的核心设备,用于将燃烧产生的硫化物氧化为二氧化硫。
在氧化器中,燃烧废气与空气接触,硫化物被氧化为二氧化硫。
氧化器通常采用垂直立式结构,底部设有空气切割设备,用于将空气均匀地分布到燃烧废气中。
操作条件包括:温度在1300-1500℃之间,氧浓度在4%-7%之间。
2.临界燃烧器临界燃烧器是氧化器的一部分,用于提高氧化器内的温度,使其达到氧化反应所需的温度。
临界燃烧器一般由多个燃烧室组成,通过燃烧产生的热量,提高氧化器中的温度。
操作条件包括:燃料进口温度在150-250℃之间,相对湿度低于50%,气体流速在15-20m/s之间。
3.冷却器冷却器用于将氧化器中产生的高温烟气冷却,使其冷却到150-200℃之间,以便后续的装置使用。
冷却器通常采用水冷却或空气冷却的方式,通过冷却介质与烟气的热交换来实现冷却过程。
操作条件包括:冷却介质温度在5-10℃之间,冷却介质流速在0.2-0.3m/s之间。
4.除尘器除尘器用于去除冷却后烟气中的固体颗粒物,保证排放的烟气符合环保要求。
除尘器通常采用电除尘、湿式除尘或布袋除尘等方式,通过不同的除尘原理将烟气中的固体颗粒物分离出来。
操作条件包括:电除尘的电压在50-70kV之间,湿式除尘的水压在2.5-3.5kPa之间,布袋除尘的气流速度在1-1.5m/s之间。
5.储存罐储存罐用于存储从冷却器中收集到的液态硫磺。
储存罐通常采用立式或卧式结构,具备密封性能,以防止硫磺挥发和泄漏。
储存罐的操作条件包括:温度在110-130℃之间,压力在0.2-0.3MPa之间,储存罐内部应保持干燥,以防止硫磺结块和质量变化。
总的来说,克劳斯硫磺回收主要设备包括氧化器、临界燃烧器、冷却器、除尘器和储存罐等。
- 1、下载文档前请自行甄别文档内容的完整性,平台不提供额外的编辑、内容补充、找答案等附加服务。
- 2、"仅部分预览"的文档,不可在线预览部分如存在完整性等问题,可反馈申请退款(可完整预览的文档不适用该条件!)。
- 3、如文档侵犯您的权益,请联系客服反馈,我们会尽快为您处理(人工客服工作时间:9:00-18:30)。
克劳斯硫回收操作规程1.岗位任务及意义我厂所采用的原料煤硫含量较高,如果不加以回收,就会污染空气。
本岗位接受低温甲醇洗岗位送来的硫化氢尾气,通过克劳斯回收装置回收,并制成固体硫磺。
本装置H2S的总转化率90-95%;COS不发生克劳斯反应,通过尾气烟囱直接放空。
年产硫磺1万吨,回收硫磺不仅经济效益可观还可以消除污染。
2.工艺原理及流程叙述2.1工艺原理克劳斯法回收硫的基本反应如下:H2S+1/2O2→S+H2O (1)H2S+3/2O2→SO2+H2O (2)2H2S+SO2→3S+2H2O (3)反应(1)(2)在燃烧室中进行,在温度1150℃-1300℃,压力0.06MPa 和严格控制气量的条件下,将硫化氢燃烧成二氧化硫,为催化反应提供(H2S+CS2)/SO2为2/1的混合气体。
此气体通过AL2O3基触媒,按反应(3)生成单质硫。
2.2流程叙述来自上游甲醇洗工序的酸性气温度为37.2℃,压力为0.22MPaG,经进料管分离罐(V1301)分出挟带液后,按一定比例分成两股,其中一股去H2S燃烧炉(F1301)。
该流股经过控制阀后压力降为0.06 MPaG 进入H2S燃烧炉(F1301),在H2S燃烧炉(F1301)中,酸性气和一定比例的反应空气发生燃烧反应,反应生成SO2的和燃烧反应剩余的H2S 进一步发生部分克劳斯反应,反应后的酸性气体温度可达800℃以上。
高温酸性气随后进入H2S余热回收器(E1301)回收器废热并副产蒸汽,同时将反应生成的单质硫部分冷凝。
H2S余热回收器(E1301)一共有四程换热管(PASS1~4)回收本工序工艺气的废热,高温酸性气废热的回收是通过其中的第一、二换热管(PASS1、PASS2)进行的。
高温酸性气全部通过PASS1后温度降为600℃,然后分成两股,其中一股流经PASS2温度进一步降至185℃,然后和未经过PASS2的流股混和。
通过调整两个流股的比例可使混合后的温度控制在约300℃。
混合后的酸性气流股和进料器分离罐(V1301)后未进入H2S燃烧炉(F1301)的旁路酸性气体混合后温度降至230℃、压力0.04MPaG进入克劳斯反应器(R1301)一段。
在该段床层酸性气中的H2S和SO2在催化剂LS-971和LS-300的作用下发生克劳斯反应生成单质硫,H2S的转化率为80%~85%。
流出反应器的酸性气体温度约为340℃,经过H2S余热回收器PASS3回收器废热后,温度降为175℃,同时绝大部分的单质硫被冷凝下来。
为达到克劳斯反应器二段所需的温度,流程中设置了第一再加热器(E1302),酸性气进入该加热器预热到约238℃后进入克劳斯反应器二段继续进行克劳斯反应以回收剩余的硫。
在二段反应床中,H2S的转化率约为75%,反应后的酸性气温度约为255℃。
经过H2S余热回收器PASS4回收该股的废热后,流股的温度降至175℃,其中的单质硫也被大部分冷凝分离。
经过第二再加热器预热至230℃后该流股进入反应器三段发生克劳斯反应,此时H2S的转化率约为40%左右。
由于经过前面的一、二反应床后,剩余的H2S和SO2均已较少,因而反应热不多,故反应后的酸性气体与入口相比,温升不大。
该股酸性气体经过最终冷凝器(E1304)进一步冷凝分离其中的单质硫。
最终冷凝器(E1304)产生约300Kg/h的120℃低压蒸汽,低压蒸汽不便利用而直接排入大气。
克劳斯反应器各段反应生成的熔融硫分别通过第一密封腿(V1302)、第二密封腿(V1303)被统一收集到硫磺池(V1304)中。
熔融硫由硫磺泵(P1301A/B)输送至硫磺造粒机(Y1301)生产固体硫磺成品。
H2S余热回收器(E1301)副产的0.34MPaG低压蒸汽送至界区的低压蒸汽管网。
3.生产操作法3.1正常操作3.1.1酸性气组成和流量波动的处理方法如果由于上游装置的影响,酸性气的流量和H2S的组成有波动,F-1301的炉膛温度也会相应变化。
也就是说,其它条件不变的情况下,酸性气的流量和H2S的组成减少会导致炉膛温度降低。
在这种情况下,缓慢调节分流比例,调节到烧嘴的酸性气流量,和通过旁路的酸性气流量,使炉膛温度维持在1100-1300℃之间。
但是,至少需要40%的酸性气进入H2S燃烧炉。
如果炉膛温度低于1100℃,需要加入LP或FG助燃。
助燃步骤如下:a.计算配风比空气与LP之比为25.3Nm3/Nm3(完全燃烧)空气与FG之比为1.84Nm3/Nm3(完全燃烧)b. 点燃H2S点火烧嘴,慢慢打开FV-1304或FV-1305。
c. 逐渐打开燃料气管线上的切断阀, LP或FG燃烧。
然后增加空气流量。
d. 增加燃料气流量,直到FICA-1304或FICA-1305可投入自动控制。
e. 调节FICA-1304或FICA-1305,使炉膛温度控制在1100-1300℃。
f.确认克劳斯反应器中温度正常g.确认在线分析(AT-1302)分析E-1304出口尾气H2S与SO2 之比为2。
h.如果炉膛温度过高,通入氮气或蒸汽降温,或者增加进燃烧炉的酸性气流量。
3.1.2操作要点要特别注意以下参数:①进岗位的酸性气总量FIA1301、空气量FICA1303A/B、燃料气量FV1305。
②E1301炉膛温度TIA1304、TIA1305;R1301床层入口温度TICA1312、TICA1315、TICA1322。
③酸性气压力PIA1301、及蒸汽压力PIA1303。
④E1301 、E1304液位。
3.1.3转动设备的开停操作3.1.3.1熔融硫泵P1301A/B开停操作3.1.3.1.1 起动前的准备(1)电气人员检查电机绝缘合格后,送电。
(2)电机已试运转,旋转方向和电机壳体指示方向一致。
(3)确认泵体和出口管线及硫磺池(V1304)底部已伴热,疏水器工作正常。
(4)确认泵冷却循环水压力正常且投用。
(5)确认硫磺池液位正常。
(6)盘泵,确认泵转动灵活,无异常响声。
(7)开泵出口压力表根部阀泵出口回流阀。
(8)确认造粒机布料器已预热具备接受液态硫磺的条件。
3.1.3.1.2起动P1301泵(1)P1301泵送电后,按起动按钮,P1301泵起动。
然后开泵出口阀,同时缓慢关闭回流阀,注意泵出口压力在0.2~0.3MPa,熔融硫磺送硫磺造粒机。
(3)检查泵运行情况。
3.1.3.1.3 停P1301泵(1)开泵出口回流阀,关出口阀。
(2)按停车按钮停泵。
(3)检查备用状态。
(4)若泵要检修,要切断电源。
3.1.3.2转鼓结片机CF1.0-10.4-3开、停操作3.1.3.2.1起动前准备工作(1)检查钢带、钢带传动辊轮圆柱面是否落入杂物或粘附着异物,避免损坏钢带。
(2)首次开车前,应确认布料器上游管道无杂质、开车前断开进行二次吹扫;以后开前检查过滤器即可。
3.1.3.2.2系统预热(1)启动布料器,使布料器处于低速旋转状态,打开加热罩蒸汽对布料器进行预热(注意:第一次开车布料器空转时间5-10分钟),将布料器预热至120℃以上。
(2)待布料器预热到指定温度,将布料器的变频调速器设定至10HZ 左右。
(3)启动钢带,使其处于低速旋转状态。
3.1.3.2.3开车操作步骤(1)设备运转正常、各控制点达到设定值并且参数稳定后,打开冷却水进水阀并调节水量,使雾化水喷淋在钢带内表面。
(2)调节布料器转数与钢带线速度到操作控制点,然后打开进料阀,同时观察颗粒成型状态,调节物料流量到理想出料状态。
(3)若操作不当,开车过程中可能出现一些现象及处理方法:①若出现硫磺颗粒小尾巴或呈长圆形状,可采用下述方法:a.适当提高物料进料温度;b.适当提高布料器加热罩的设定温度;c.调低钢带速度,或适当提高布料器转数。
②若出现硫磺滴落钢带后,成型颗粒之间相互粘连,可采用如下方法:a.可减少进入布料器的物料的输送压力或流量,减小液滴量;b.提高钢带转速,拉开颗粒间距;c.提高布料器转速,缩短滴料时间、减小滴料量。
③布料器沿轴向(即宽度方向)布料不均,一端颗粒偏大、一端颗粒偏小,可采用如下方法:a.调整布料器水平度;b.升高或降低布料器及加热罩设定温度,若进料端流量偏大,则升高布料器温度,否则降低其温度;c.采用两端进料。
④落在钢带上的硫磺颗粒扁平、不饱满,可采用如下方法:a.适当降低物料以及布料器、加热罩沿管程加套的温度,以提高熔融物料的表面张力;b.调整布料器与钢带之间的距离,以减少重力对颗粒形状的影响。
3.1.3.2.4停车操作步骤(1)在物料用尽前10分钟停止对布料器的加热。
(2)待物料基本排净后,停止加热罩的加热,然后停止布料器的旋转操作。
(3)待钢带的物料用尽后,关闭钢带驱动电机,同时关闭冷却水进口阀门、清理现场;(4)若停机三天以内,一般不必清理布料器,在下次开车投料前,只需将管路、布料器及加热罩预热到工艺设定温度并稳定30分钟,即可按开车顺序进行投料生产。
3.1.3注意事项1、点火时要确保炉膛形成微负压。
2、为提高硫磺回收率要掌握好H2S和SO2反应比例。
3、系统为低压设备,在检修后气密,运行中系统压力不能高于0.1MPaG。
4、长期停车必须扫硫。
5、如果炉膛温度高,要注意使用N3和S3降温。
3.2开车3.2.1原始开车3.2.1.1开车前的准备工作①触媒升温还原已结束。
②确认主流程已打通,有足够的H2S气体且浓度满足要求。
③确认公用工程具备条件:蒸汽、锅炉给水、燃料气、循环水具备条件。
3.2.1.2开车前的检查、确认工作①阀位的确认:应开阀:a、E1301蒸汽放空管线FS-1304-3″-A6A-P上节流阀打开 b、E1304低压蒸汽管线上的压力控制阀PV1316的上下游截止阀打开c、液位计截止阀。
d、仪表根部阀。
应关阀:a、E1301、E1304熔硫管线上的球阀。
b、H2S点火嘴和H2S烧嘴上所有阀门。
c、所有界区阀。
d、所有导淋阀、排污阀、放空阀。
②确认所有的仪表调节阀动作正常。
③确认系统联锁动作正常无误。
④确认所有盲板限流孔板位置正确无误。
⑤确认转动设备备用。
⑥确认蒸汽盘管、夹套、伴热管线蒸汽已投用,各疏水器畅通、疏水正常。
⑦确认E1301、E1304液位已到正常值。
⑧1#、2#密封槽液位已充至溢出口。
⑨投用E1302、E1303蒸汽。
⑩测压点、检测点通保护氮。
⑾AI-1301、AI-1302、AI-1303正常投用。
3.2.2开车歩骤①启动风机a、确认冷却水已投用。
b、确认润滑油油位正常。
c、确认PCV1301、FV1302关闭;手动打开TV1312。
d、启动风机,同时打开放空阀PV1305放空30分钟,检查轴温和轴振动。
e、将PIC1305设定为0.075MPaG,投自动。
②H2S锅炉点火酸性气(SG)、LPG(LP)和燃料气(FG)可作为H2S燃烧炉的燃料。