关于工业机器人的事故分析及其对策
起重机事故原因分析及对策
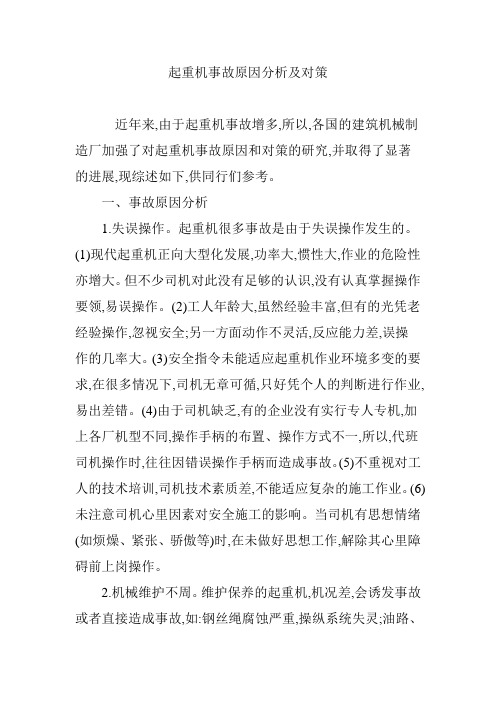
起重机事故原因分析及对策近年来,由于起重机事故增多,所以,各国的建筑机械制造厂加强了对起重机事故原因和对策的研究,并取得了显著的进展,现综述如下,供同行们参考。
一、事故原因分析1.失误操作。
起重机很多事故是由于失误操作发生的。
(1)现代起重机正向大型化发展,功率大,惯性大,作业的危险性亦增大。
但不少司机对此没有足够的认识,没有认真掌握操作要领,易误操作。
(2)工人年龄大,虽然经验丰富,但有的光凭老经验操作,忽视安全;另一方面动作不灵活,反应能力差,误操作的几率大。
(3)安全指令未能适应起重机作业环境多变的要求,在很多情况下,司机无章可循,只好凭个人的判断进行作业,易出差错。
(4)由于司机缺乏,有的企业没有实行专人专机,加上各厂机型不同,操作手柄的布置、操作方式不一,所以,代班司机操作时,往往因错误操作手柄而造成事故。
(5)不重视对工人的技术培训,司机技术素质差,不能适应复杂的施工作业。
(6)未注意司机心里因素对安全施工的影响。
当司机有思想情绪(如烦燥、紧张、骄傲等)时,在未做好思想工作,解除其心里障碍前上岗操作。
2.机械维护不周。
维护保养的起重机,机况差,会诱发事故或者直接造成事故,如:钢丝绳腐蚀严重,操纵系统失灵;油路、汽路不畅通或泄漏;电路接触不良或短路、断路、滑轮、轴承缺油(脂)、转动不灵或卡住不转动等。
3.缺乏安全装置。
有的起重机,没有安装防超载防碰撞等安全装置,当出现事故预兆时,不能报警或停机,从而酿成了事故。
4.环境因素。
在下列环境中作业,起重机易发生事故:在回填土方或泥泞场地吊装;在坡地吊装;有几台吊车在狭窄地段内同时作业,与土建施工交叉作业,在雨后路滑的地段吊装;在输电线路禁区附近吊装。
5.部件质量差。
起重机吊杆、支腿等部件质量差,如材质不合格,有裂纹等,会成为导致起重机发生事故的重要原因。
6.综合原因。
由上述两种或两种以上因素综合作用,更易发生事故。
二、防止事故发生的对策1.改进设计和制造工艺。
机械伤害事故原因分析及其对策

机械伤害事故原因分析及其对策机械加工设备由于运转速度快,在运转过程中,操作人员如不熟练操作或违反操作规程,很容易造成严重伤害和死亡事故,为预防机械设备伤害和死亡事故发生,经过调查分析,现就其造成事故的原因进行剖析,同时提出相应的预防措施及对策。
一、机械伤害事故的直接原因分析(一)物的不安全状态机械设备的质量、技术、性能上的缺陷以及在制造、维护、保养、使用、管理等诸多环节上存在的不足,是导致机械伤害事故的直接原因之一。
具体表现为:一是机械设备在设计制造上就存在缺陷,有的设备机械传动部位没有防护罩、保险、限位、信号等装置;二是设备设施、工具、附件有缺陷,加之有的企业擅自改装、拼装和使用自制非标设备,设备安全性能难以保证;三是设备日常维护、保养不到位、机械设备带病运转、运行,对设备的使用、维护、保养、安全性能的检测缺少强有力的监管;四是从业人员个人防护用品、工具缺少或缺陷,导致工人在操作中将身体置身于机械运转的危险之中;五是生产作业环境缺陷,有的企业设备安装布局不合理,机械设备之间的安全间距不足,工人操作空间不符合要求,更有少数单位现场管理混乱,产成品乱堆乱放、无定置、无通道。
(二)人的不安全行为人的不安全行为是造成机械伤害事故的又一直接原因,集中表现为:一是操作失误,忽视安全,忽视警告。
操作者缺乏应有的安全意识和自我防护意识,思想麻痹,有的违章指挥,违章作业,违反操作规程;二是操作人员野蛮操作,导致机器设备安全装置失效或失灵,造成设备本身处于不安全状态;三是手工代替工具操作或冒险进入危险场所、区域,有的工人为图省事,走捷径,擅自跨越机械传动部位;四是机械运转时加油、维修、清扫,或者操作者进入危险区域进行检查、安装、调试,虽然关停了设备,但未能开启限位或保险装置,又无他人在场监护,将身体置身于他人可以启动设备的危险之中;五是操作者忽视使用或佩戴劳保用品。
二、机械伤害事故的间接原因分析一是安全机构不健全,有的企业没有专职安全员或安全员配备不足,有的安全员一人多职,职责不明,人浮于事;二是安全宣传、安全培训不到位,有的企业新工人未经培训就直接上岗作业,特别是特种作业人员未经相关部门培训,缺乏安全操作技术知识,存在边学边干的现象;三是安全生产制度、操作规程不健全,即使有制度也流于形式,执行不到位,监管不到位;四是对事故隐患整改不力,有的企业虽然定期进行安全检查,但对发现的问题和隐患,往往一查了之,不能跟踪督查整改到位。
工业机器人安全分析报告
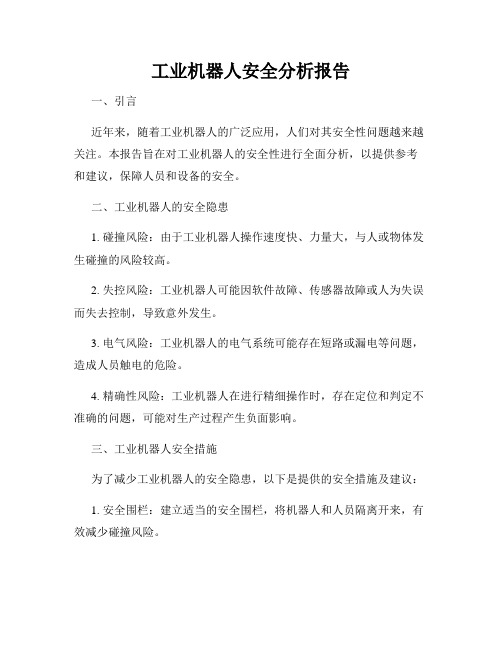
工业机器人安全分析报告一、引言近年来,随着工业机器人的广泛应用,人们对其安全性问题越来越关注。
本报告旨在对工业机器人的安全性进行全面分析,以提供参考和建议,保障人员和设备的安全。
二、工业机器人的安全隐患1. 碰撞风险:由于工业机器人操作速度快、力量大,与人或物体发生碰撞的风险较高。
2. 失控风险:工业机器人可能因软件故障、传感器故障或人为失误而失去控制,导致意外发生。
3. 电气风险:工业机器人的电气系统可能存在短路或漏电等问题,造成人员触电的危险。
4. 精确性风险:工业机器人在进行精细操作时,存在定位和判定不准确的问题,可能对生产过程产生负面影响。
三、工业机器人安全措施为了减少工业机器人的安全隐患,以下是提供的安全措施及建议:1. 安全围栏:建立适当的安全围栏,将机器人和人员隔离开来,有效减少碰撞风险。
2. 紧急停止开关:在工作区域设置易于访问的紧急停止开关,以便在紧急情况下立即停止机器人运行。
3. 安全传感器:安装安全传感器,通过检测人员或物体的接近来及时停止机器人的运动,避免碰撞事故。
4. 定位系统:引入先进的定位系统,提高机器人的位置精确性,减少操作中的误差。
5. 定期维护:定期检查和维护机器人的电气系统,确保正常运行,避免电气故障导致的风险。
四、安全培训和教育除了以上安全措施,工业机器人使用者和操作者需要进行安全培训和教育,掌握以下知识:1. 机器人操作规程:了解机器人的正确操作方法和流程,避免人为失误导致事故。
2. 安全操作技巧:掌握安全操作技巧,包括正确的姿势、距离和操作步骤等,减少操作中的风险。
3. 紧急情况应对:学习在紧急情况下如何正确使用紧急停止开关或其他紧急设备,及时避免事故。
4. 事故处理和报告:了解事故处理和报告的程序,及时采取措施并向相关部门做好报告。
五、机器人安全标准和监管要求为了规范工业机器人的使用和安全管理,相关机构制定了一系列安全标准和监管要求,使用者和制造商应当遵守:1. ISO 10218标准:该标准规定了机器人系统的整体安全要求和技术规范。
工业机器人安全事故统计表
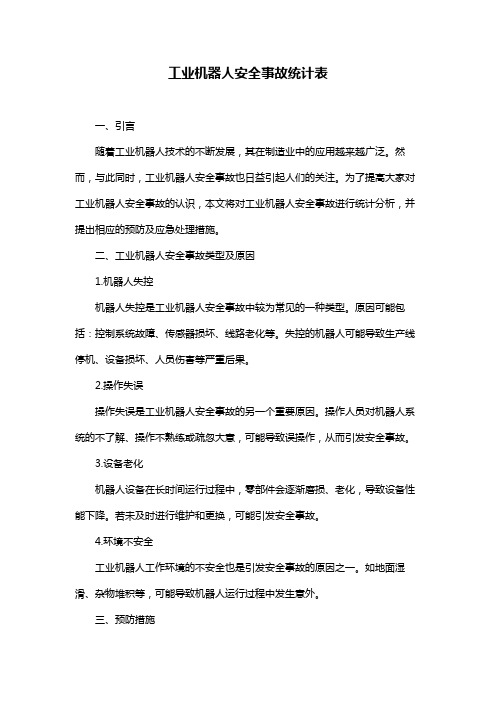
工业机器人安全事故统计表一、引言随着工业机器人技术的不断发展,其在制造业中的应用越来越广泛。
然而,与此同时,工业机器人安全事故也日益引起人们的关注。
为了提高大家对工业机器人安全事故的认识,本文将对工业机器人安全事故进行统计分析,并提出相应的预防及应急处理措施。
二、工业机器人安全事故类型及原因1.机器人失控机器人失控是工业机器人安全事故中较为常见的一种类型。
原因可能包括:控制系统故障、传感器损坏、线路老化等。
失控的机器人可能导致生产线停机、设备损坏、人员伤害等严重后果。
2.操作失误操作失误是工业机器人安全事故的另一个重要原因。
操作人员对机器人系统的不了解、操作不熟练或疏忽大意,可能导致误操作,从而引发安全事故。
3.设备老化机器人设备在长时间运行过程中,零部件会逐渐磨损、老化,导致设备性能下降。
若未及时进行维护和更换,可能引发安全事故。
4.环境不安全工业机器人工作环境的不安全也是引发安全事故的原因之一。
如地面湿滑、杂物堆积等,可能导致机器人运行过程中发生意外。
三、预防措施1.机器人系统安全设计在设计阶段,应充分考虑机器人的安全性。
如增加安全防护装置、设置合理的安全距离、采用可靠的控制系统等。
2.加强操作人员培训操作人员是工业机器人安全运行的关键。
企业应加强对操作人员的培训,提高他们的安全意识,确保他们能熟练、安全地操作机器人。
3.定期设备检查与维护定期对机器人设备进行检查和维护,及时发现并排除安全隐患,是预防安全事故的重要手段。
4.改善工作环境企业应加强工作环境的管理,确保地面干燥、整洁,无杂物堆积,降低安全事故发生的概率。
四、应急处理措施1.紧急停止按钮在机器人工作区域内设置紧急停止按钮,当发生安全事故时,操作人员可迅速按下按钮,切断机器人电源,避免事故扩大。
2.物理隔离在机器人工作区域设置物理隔离,确保在发生安全事故时,其他人员不会受到波及。
3.应急预案企业应制定针对工业机器人安全事故的应急预案,明确事故发生后各人员的职责和应对措施,确保事故得到及时、有效的处理。
工业机器人安全事故统计表

工业机器人安全事故统计表【原创实用版】目录1.工业机器人概述2.工业机器人的安全事故统计3.工业机器人安全事故的原因分析4.工业机器人安全防护措施5.工业机器人的安全标准和规范6.工业机器人的安全管理建议正文一、工业机器人概述工业机器人是一种能够自动化执行工业任务的机器人。
它们通常被用于制造业和其他工业领域,以完成各种重复性、高精度或高风险的任务。
工业机器人通常由多个关节组成,可以在三维空间内自由移动和操作,并且可以根据程序和传感器的指令执行特定的任务。
工业机器人可以进行各种操作,例如焊接、喷涂、装配、搬运、包装、质检等。
它们可以大大提高生产效率和质量,减少人力成本和人员受伤的风险,因此在现代工业中得到广泛应用。
二、工业机器人的安全事故统计据不完全统计,每年全球范围内发生的工业机器人安全事故数量呈上升趋势。
这些安全事故主要包括机械伤害、电气伤害、火灾和爆炸等,可能导致人员伤亡、设备损坏和生产中断等问题。
三、工业机器人安全事故的原因分析工业机器人安全事故的原因多种多样,主要包括以下几个方面:1.设计缺陷:工业机器人在设计过程中可能存在缺陷,导致在实际操作过程中出现安全隐患。
2.制造和安装质量:工业机器人的制造和安装质量直接关系到其安全性能。
如果制造和安装过程中存在问题,可能导致机器人运行不稳定,增加安全事故的风险。
3.维修和保养不到位:工业机器人在长期运行过程中,需要定期进行维修和保养。
如果维修和保养不到位,可能导致机器人性能下降,增加安全事故的风险。
4.操作人员培训不足:操作工业机器人的人员需要经过专门的培训,掌握相关的安全知识和操作技能。
如果操作人员培训不足,可能导致安全事故的发生。
5.安全管理不善:企业如果没有建立完善的安全管理体系,可能导致工业机器人的安全事故风险得不到有效控制。
四、工业机器人安全防护措施为了降低工业机器人安全事故的风险,企业应采取以下措施:1.机器人本体设计优化:在设计阶段充分考虑机器人的安全性能,采用合适的材料和结构,提高机器人的抗冲击和抗磨损能力。
工业机器人安全分析报告评估工业机器人的安全控制系统

工业机器人安全分析报告评估工业机器人的安全控制系统工业机器人安全分析报告工业机器人在现代工业生产中发挥着重要的作用,但其安全性成为人们关注的焦点。
为了评估工业机器人的安全控制系统,本报告将从机器人的安全设计、紧急停止系统以及人机交互等方面进行分析,并提出相关的评估方法和建议。
一、机器人的安全设计在工业机器人的设计阶段,应将安全性作为重要考虑因素之一。
以下是一些关键设计要点:1. 编程控制:机器人的编程应考虑到安全保障,从而确保机器人能够在工作过程中遵循规定的路径和速度,避免对人员造成危险。
2. 周围感应:机器人应配备适当的传感器和监控系统,以便能够感知周围环境和目标物体。
这样机器人可以在接近人员或其他物体时自动减速或停止运动,以避免碰撞。
3. 安全外壳:机器人应设计合理的外壳结构,以保护内部的运动部件和电子设备。
外壳应尽可能避免锋利的边缘和突出物,防止操作人员被划伤或受伤。
4. 急停按钮:机器人应配置紧急停止按钮,以方便操作人员在紧急情况下立即停止机器人运动。
5. 防护栏材料:安全栏材料应能够防止工作人员误入机器人的工作区域,必要时还应具备防护性能,如耐高温、耐腐蚀等。
二、紧急停止系统紧急停止系统是保障机器人安全的重要手段之一。
以下是几种常见的紧急停止系统:1. 急停按钮:操作人员可以通过按下紧急停止按钮来迅速停止机器人运动。
急停按钮应易于操作,安装位置应在工作区域内方便人员触达。
2. 传感器检测:配置必要的传感器来监测紧急情况,如火灾、气体泄露等。
一旦发现危险情况,机器人系统应立即触发紧急停止程序。
3. 机器人控制系统:机器人控制系统应具备自动停止功能,通过监测关键参数,如温度、电流等,判断是否存在故障或运行异常,并立即停止机器人运动。
三、人机交互人机交互是工业机器人安全控制的重要环节。
以下是几点关键要点:1. 操作界面:机器人的操作界面应简洁、直观,易于理解和操作。
必要时可以提供相关的提示和警告信息,帮助操作人员正确地使用和控制机器人。
关于工业机器人的事故分析及其对策

关于工业机器人的事故分析及其对策摘要:工业机器人是高科技机电产品,在工业领域广泛应用,可以代替人们从事繁重的、危险性的工作,但由于工业机器人故障所造成的人身伤害事故也时有发生。
从工业机器人的可靠性、工业机器人事故案例、能量类型分类等多角度对工业机器人事故进行了分析,从故障树分析法、基本安全性原则、工业安全技术等几方面提出了相应的对策。
关键词:工业机器人事故安全分析对策1 引言工业机器人被广泛地应用于制造业等诸多部门,它可以代替人们在具有危险性的场所从事繁重的工作。
工业机器人在将人们从繁重的危险性劳动中解放出来的同时,也存在产生危险的因素,由于工业机器人故障所造成的人身伤害事故时有发生。
工业机器人是由一个复杂的机电系统组成的,这个系统包括传感器、控制器、工作制造部件、输送部件等。
人要对工业机器人进行安装、编程、维修,还有可能靠近机器人进行操作,因此,人也将参与到机器人的工作系统中去,当人靠近工业机器人时就可能出现安全问题[1]。
机器人的自由度比其他普通机械大得多,它的工作制造部件可以在较大空间内运行,具有高速运动的大功率手臂和复杂自主的动作,若机器人发生故障可能造成更为严重的危害。
所以,有必要对工业机器人的有关事故情况进行分析,并研究相应对策。
2 工业机器人安全性概况2.1 工业机器人的可靠性分析鉴于工业安全问题的重要性,世界上有许多国家(如日本、美国、英国、德国、瑞典等)从上世纪80年代开始就注意对工业机器人的事故进行记录,并进行统计和分析,为工业机器人的安全性、可靠性研究奠定了基础。
日本某公司对工业机器人发生事故的类别进行了调查统计,其中控制装置的故障占66.9%,机器人装置上的工作部件,如焊枪等工具的故障占18.5%,工作场所噪声信号的干扰引起的机器人失控占11.1%,其他原因的故障占3.5%。
表1 为机器人的平均无故障时间(MTBF)的统计。
可以看出,在机器人工作不到100h的时间内,其平均无故障率只有28.70%,工作100h 以上,其平均无故障率明显下降。
工业机器人的故障诊断技术分析

基于数学模型的故障诊断技术
简介
基于数学模型的故障诊断技术 是一种通过建立系统数学模型 ,并利用输入输出数据来识别
系统故障的方法。
优点
能够精确地描述系统动态行为, 对于复杂系统具有较强的适用性 。
缺点
建立数学模型需要较高的技术要求 ,并且对于某些复杂系统难以建立 有效的数学模型。
基于信号处理的故障诊断技术
存储和分析历史数据,提供数据支持。
故障诊断系统的故障检测与识别
1 2
故障检测模块
实时监测工业机器人的运行状态,发现异常情 况。
故障识别模块
通过对数据的分析,识别出具体的故障类型和 位置。
故障定位模块
3
进一步确定故障的具体位置和影响范围。
故障诊断系统的决策与控制
决策模块
根据故障类型和位置,制定相应的维修策略。
03
模型优化和更新
通过对模型的持续优化和更新,可以提高模型的自适应能力和诊断性
能,实现更高效和准确的故障诊断。
基于物联网的远程故障诊断技术
远程故障诊断
利用物联网技术,可以实现工业机器人的远程故障诊断 ,及时发现并解决故障问题,提高生产效率和降低维修 成本。
在线监测与预警
通过实时监测工业机器人的运行状态和各项参数,可以 实现故障预警和预防性维护,降低故障发生率和提高机 器人的使用寿命。
加工与装配
工业机器人可以用于加工 和装配,如铣削、钻孔、 拧螺丝等,提高生产效率 和精度。
工业机器人技术的发展历程
第一代工业机器人
基于示教再现技术的工业 机器人,通过示教盒对机 器人进行在线编程,实现 机器人的重复运动。
第二代工业机器人
具有感知能力的工业机器 人,通过传感器感知环境 信息,实现机器人的自适 应控制。
工业机器人行业存在问题及对策分析
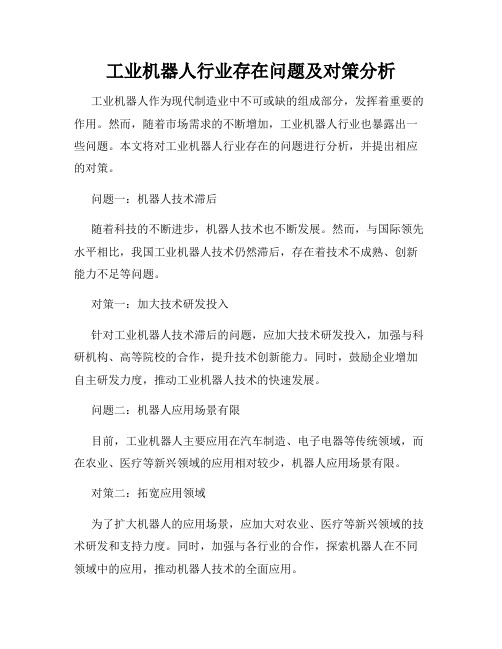
工业机器人行业存在问题及对策分析工业机器人作为现代制造业中不可或缺的组成部分,发挥着重要的作用。
然而,随着市场需求的不断增加,工业机器人行业也暴露出一些问题。
本文将对工业机器人行业存在的问题进行分析,并提出相应的对策。
问题一:机器人技术滞后随着科技的不断进步,机器人技术也不断发展。
然而,与国际领先水平相比,我国工业机器人技术仍然滞后,存在着技术不成熟、创新能力不足等问题。
对策一:加大技术研发投入针对工业机器人技术滞后的问题,应加大技术研发投入,加强与科研机构、高等院校的合作,提升技术创新能力。
同时,鼓励企业增加自主研发力度,推动工业机器人技术的快速发展。
问题二:机器人应用场景有限目前,工业机器人主要应用在汽车制造、电子电器等传统领域,而在农业、医疗等新兴领域的应用相对较少,机器人应用场景有限。
对策二:拓宽应用领域为了扩大机器人的应用场景,应加大对农业、医疗等新兴领域的技术研发和支持力度。
同时,加强与各行业的合作,探索机器人在不同领域中的应用,推动机器人技术的全面应用。
问题三:专业人才短缺工业机器人行业的发展需要大量的高素质专业人才,然而,目前我国工业机器人领域的专业人才相对短缺,严重制约了行业的发展。
对策三:培养专业人才针对工业机器人专业人才短缺的问题,应加大对相关专业的培养力度。
同时,推动高校与企业的合作,加强实践教学,培养出符合市场需求的高素质专业人才。
另外,鼓励企业提供更多的岗位培训和转岗机会,提高员工的专业素质。
问题四:安全风险隐患随着工业机器人的广泛应用,安全问题也日益凸显。
工业机器人在操作中存在安全隐患,如机器人与人员发生碰撞、机器人系统失效等。
对策四:加强安全管理为了解决工业机器人的安全隐患,应加强对工业机器人的安全管理和监管。
制定并执行严格的安全标准和规范,确保机器人的产品质量和系统安全性。
同时,加强对从业人员的安全培训,提高员工的安全意识和应急处置能力。
问题五:产业链配套不完善工业机器人行业的快速发展需要完善的产业链支撑,然而目前我国工业机器人产业链还不够完善,存在配套设备供应不足、技术服务不完善等问题。
关于工业机器人的事故分析及其对策
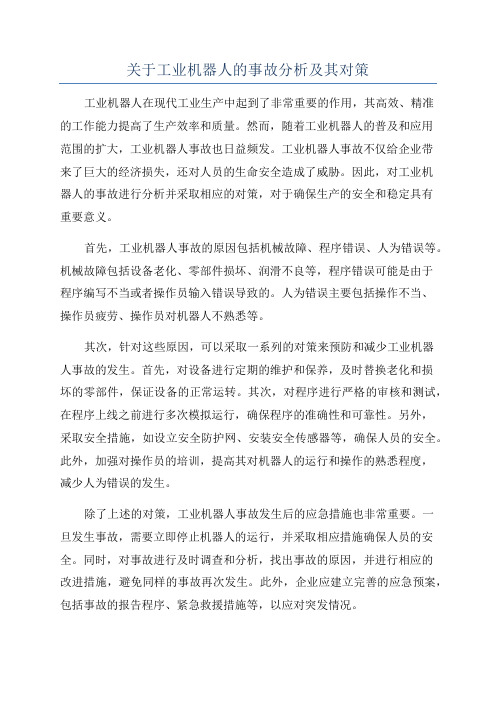
关于工业机器人的事故分析及其对策工业机器人在现代工业生产中起到了非常重要的作用,其高效、精准的工作能力提高了生产效率和质量。
然而,随着工业机器人的普及和应用范围的扩大,工业机器人事故也日益频发。
工业机器人事故不仅给企业带来了巨大的经济损失,还对人员的生命安全造成了威胁。
因此,对工业机器人的事故进行分析并采取相应的对策,对于确保生产的安全和稳定具有重要意义。
首先,工业机器人事故的原因包括机械故障、程序错误、人为错误等。
机械故障包括设备老化、零部件损坏、润滑不良等,程序错误可能是由于程序编写不当或者操作员输入错误导致的。
人为错误主要包括操作不当、操作员疲劳、操作员对机器人不熟悉等。
其次,针对这些原因,可以采取一系列的对策来预防和减少工业机器人事故的发生。
首先,对设备进行定期的维护和保养,及时替换老化和损坏的零部件,保证设备的正常运转。
其次,对程序进行严格的审核和测试,在程序上线之前进行多次模拟运行,确保程序的准确性和可靠性。
另外,采取安全措施,如设立安全防护网、安装安全传感器等,确保人员的安全。
此外,加强对操作员的培训,提高其对机器人的运行和操作的熟悉程度,减少人为错误的发生。
除了上述的对策,工业机器人事故发生后的应急措施也非常重要。
一旦发生事故,需要立即停止机器人的运行,并采取相应措施确保人员的安全。
同时,对事故进行及时调查和分析,找出事故的原因,并进行相应的改进措施,避免同样的事故再次发生。
此外,企业应建立完善的应急预案,包括事故的报告程序、紧急救援措施等,以应对突发情况。
在工业机器人事故分析和对策的过程中,还需要加强政府、行业协会等相关机构的监管和指导。
政府应加强对工业机器人生产和应用的监管,制定相关的规范和标准,引导企业加强对机器人的管理和安全措施。
行业协会可以开展相关培训和知识普及活动,提高企业和操作员对工业机器人事故的认识和应对能力。
综上所述,工业机器人事故的分析和对策具有重要的意义和作用,可以预防和减少事故的发生,保护人员的生命安全和财产安全。
工程机械事故应急处置方案

工程机械事故应急处置方案一、工程机械事故的类型工程机械事故是指在施工过程中,由于机械设备、施工工艺或其他因素引起的设备破损、损毁或人员伤亡事件。
工程机械事故的类型较多,主要包括但不限于以下几种:1. 机械设备故障:包括机械部件损坏、电路故障、液压系统故障等。
2. 使用误操作:人员在操作工程机械设备时,由于疏忽大意、技术不熟练或工作状态不佳,对机械设备造成破坏或危险情况。
3. 施工作业失误:机械设备在施工过程中受到错误操作或材料质量不合格等原因导致事故。
4. 外部环境因素:包括恶劣天气、地形地貌、环境污染等对机械设备的影响。
5. 人为因素:如设备维护不当、未经授权的改装或维修等引起的事故。
二、应急处置方案的制定1. 事前准备在施工前,应对工程机械设备进行全面检查,包括机械部件、电气线路、液压系统等,确保设备完好无损。
此外,还应对施工现场周边环境进行评估,对可能影响设备安全的因素进行排查和处理。
同时,制定完整的施工计划和安全预案,确定应急处置方案和责任分工。
2. 事故预防教育培训在施工现场,必须对操作人员和相关人员进行事故预防教育培训,包括对机械设备的正确操作方法、安全使用规范、事故预防知识等方面的培训,以提高员工的安全意识和操作技能。
3. 应急处置准备建立应急处置队伍和预案,明确各工种岗位的职责分工和处置程序,确保在发生事故时可以快速、有效地进行处置。
建立健全的通讯系统和联络机制,及时上报事故信息和请求救援。
4. 应急处置设备准备配备应急处置装备,包括灭火器、急救箱、安全带、救生索等,预先储备一些常用的维修零部件和工具,以便在发生事故时迅速进行维修和救援。
5. 安全检查定期对施工现场和工程机械设备进行安全检查,及时发现和处理存在的安全隐患,保证施工安全。
三、工程机械事故应急处置流程1. 发现事故一旦发现工程机械设备出现异常情况,应立即停止操作,切断设备电源,并及时向领导和相关人员报告情况。
2. 事故控制在事故发生后,首先要对现场人员进行安全疏散,确保施工区域内没有人员受伤。
员工失误撞坏喷涂机器人事故分析与整改报告
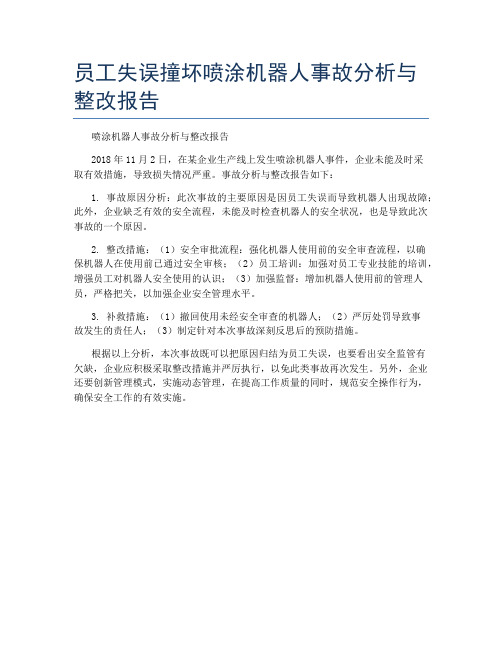
员工失误撞坏喷涂机器人事故分析与整改报告
喷涂机器人事故分析与整改报告
2018年11月2日,在某企业生产线上发生喷涂机器人事件,企业未能及时采
取有效措施,导致损失情况严重。
事故分析与整改报告如下:
1. 事故原因分析:此次事故的主要原因是因员工失误而导致机器人出现故障;此外,企业缺乏有效的安全流程,未能及时检查机器人的安全状况,也是导致此次事故的一个原因。
2. 整改措施:(1)安全审批流程:强化机器人使用前的安全审查流程,以确
保机器人在使用前已通过安全审核;(2)员工培训:加强对员工专业技能的培训,增强员工对机器人安全使用的认识;(3)加强监督:增加机器人使用前的管理人员,严格把关,以加强企业安全管理水平。
3. 补救措施:(1)撤回使用未经安全审查的机器人;(2)严厉处罚导致事
故发生的责任人;(3)制定针对本次事故深刻反思后的预防措施。
根据以上分析,本次事故既可以把原因归结为员工失误,也要看出安全监管有
欠缺,企业应积极采取整改措施并严厉执行,以免此类事故再次发生。
另外,企业还要创新管理模式,实施动态管理,在提高工作质量的同时,规范安全操作行为,确保安全工作的有效实施。
机器人常见故障及解决方案doc资料

机器人常见故障及解决方案内容来源网络,由“深圳机械展(11万㎡,1100多家展商,超10万观众)”收集整理!更多cnc加工中心、车铣磨钻床、线切割、数控刀具工具、工业机器人、非标自动化、数字化无人工厂、精密测量、3D打印、激光切割、钣金冲压折弯、精密零件加工等展示,就在深圳机械展.当机器人在工作过程中发生故障不要慌张,如果故障不是由于控制器引起的,那么故障的原因肯定是机器部件发生损坏。
为了尽快以最简便的方法处理故障、应当对故障进行分析。
并且需要找出是哪个零件引起了故障。
自从20世纪60年代初,人类创造了第一台工业机器人以后,工业机器人就显示出它极大的生命力,在短短40多年的时间中,工业机器人技术得到了迅速的发展,工业机器人已在工业发达国家的生产中得到了广泛的应用。
目前,工业机器人已广泛应用于汽车及汽车零部件制造业、机械加工行业、电子电气行业、橡胶及塑料工业、食品工业、木材与家具制造业等领域中。
在工业生产中,焊接机器人、装配机器人、喷涂机器人及搬运机器人等工业机器人都已被大量采用。
公司机器人越来越多,担心机器人出问题?怎样才能有备无患?怎样将解决方法化繁为简?下面交大家一些小诀窍以及常见的故障分析。
当机器人在工作过程中发生故障不要慌张,如果故障不是由于控制器引起的,那么故障的原因肯定是机器部件发生损坏。
为了尽快以最简便的方法处理故障、应当对故障进行分析。
并且需要找出是哪个零件引起了故障。
请按下面步骤进行简单检查和维护:第1步:那一个轴出现了问题?首先、检查是哪一个轴引起了故障。
如果很难检测出故障、核对是否有下列可能出现的机器异常。
①是否有零件发出噪音?②是否有零件过热?③是否有零件松动或有后坐力?第2步:哪个零件损坏了?如果检测出了不正常的轴、检查哪一部分引起了问题。
同一种现象会有很多种可能的原因。
注意:1) 过载——当负载超过额定电机负载时现象出现。
具体来说就是触发了线圈保护器的热继电器。
2) 操作时有噪音——现象是在操作过程中出现振动。
2023年机械行业生产安全事故分析

2023年机械行业生产安全事故分析机械行业是国民经济的支柱性产业,是工业经济大盘的“压舱石”,是拉动内需和推动内循环的重要引擎。
2023年,机械行业主要经济指标实现稳定增长,为拉动制造业乃至全国工业平稳发展发挥了重要作用。
一、2023年机械行业生产安全事故特点(一)事故总体情况。
2023年,机械行业共发生生产安全事故310起、死亡294人(不含火灾、特种设备、建设工程事故)。
其中较大事故1起、死亡3人。
(二)行业分布情况。
按照《国民经济行业分类》(GB/T4754-2017),2023年机械9个细分行业中,生产安全事故起数前五位的分别是:金属制品业、专用设备制造业、通用设备制造业、机械和设备修理业、汽车制造业,事故起数超过机械行业事故总量的80%。
(三)事故类型情况。
按照事故类型分析,2023年机械行业事故起数居前五位的分别是机械伤害、物体打击、高处坠落、触电、中毒和窒息,事故起数超过机械行业事故总量的90%。
(四)工艺分布情况。
主要生产工艺中事故起数居前三位的分别是铸造、压力加工、焊接。
铸造工艺事故主要是高温熔融金属泄漏、作业环境不良等原因导致灼烫、爆炸、机械伤害;压力加工工艺事故主要原因是设备安全防护装置缺失等;焊接工艺事故主要原因是电焊设备漏电、作业区缺氧窒息、作业人员违章作业等。
辅助生产工艺中事故起数居首位的是设备检维修作业,主要是由于设备检维修作业多为临时作业,作业场所、作业人员、施工工艺和方法不固定,没有预先制定作业安全方案,机械设备危险能量控制措施不足,作业前安全技术交底不充分,“三违”现象屡有发生。
二、安全风险提示总体来看,机械行业存在造成群死群伤的重大安全风险,较大以上事故时有发生,一般事故总量较大,存量风险和增量风险交织叠加,危险有害因素复杂。
结合行业存在的风险和事故教训,对机械行业典型安全风险梳理提示如下:(一)重大风险。
1.铝、镁等金属制品机加工打磨抛光工序,除尘系统防爆措施不到位,现场粉尘清理不及时,遇点火源可能导致粉尘爆炸。
机械伤害事故原因分析及其对策

第二,严格科学设置机械加工设备的安全。机械加工设备包括所有的金属切削设备,各种类型的锻压压力设备、木工机械、热加工设备、砂轮机以及机械传动装置等。那么企业对所有机械加工设备的布局、设备与设备之间的间距、设备本身的安全操作空间必须符合《工厂安全卫生规程》,做到统一布局、科学安装。同时对所有机械加工设备的危险部位都必须安装防护装置,保护机床区域内的操作者和其他人不受机械设备工作点、卷入挤压点、回转零件、飞出的碎屑和火花造成伤害,对防护网、防护罩、栏杆、防护档板等,必要时应增加安全连锁装置,这些装置必须与机械加工设备同时设计、同时施工、同时投入使用。另外根据机械加工设备的维护保养的要求和规定进行日常的维护保养、定期维护保养及定期的检修,以便及时发现和排除设备安全隐患,将事故隐患遏制在萌芽状态。
二、机械伤害事故的间接原因分析
一是安全机构不健全,有的企业没有专职安全员或安全员配备不足,有的安全员一人多职,职责不明,人浮于事;二是安全宣传、安全培训不到位,有的企业新工人未经培训就直接上岗作业,特别是特种作业人员未经相关部门培训,缺乏安全操作技术知识,存在边学边干的现象;三是安全生产制度、操作规程不健全,即使有制度也流于形式,执行不到位,监管不到位;四是对事故隐患整改不力,有的企业虽然定期进行安全检查,但对发现的问题和隐患,往往一查了之,不能跟踪督查整改到位。
11.卸模时,卸模板手滑脱,反弹伤脸或牙齿
12.射出的喷块料(PP,PE,POM,PA)未冷,用手拿,料粘到手上,烫伤手
13.唧嘴堵塞,用金属棒捅,手触到喷嘴或料嘴烫伤手
14.全自动机械手操作的机台,人站在机械手作业区域,被机械手插伤
15产品吃静模或动模时,用钳子拨,力道过猛,手撞在动模或静模,使手受伤
1.着装整齐,扣子拉链拉好
工业机器人系统故障引发的安全生产事故应急预案
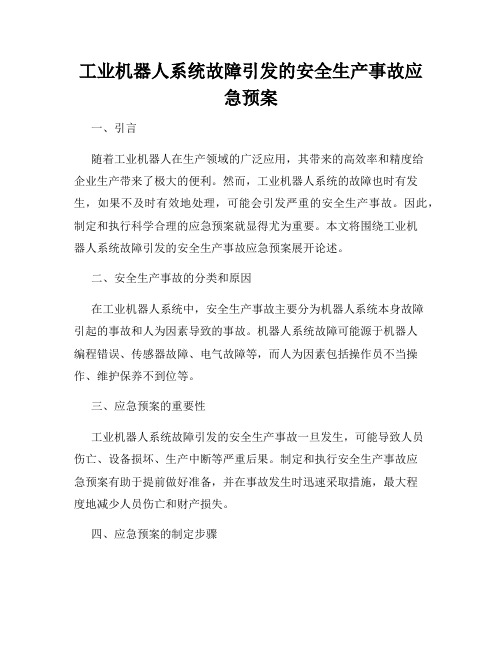
工业机器人系统故障引发的安全生产事故应急预案一、引言随着工业机器人在生产领域的广泛应用,其带来的高效率和精度给企业生产带来了极大的便利。
然而,工业机器人系统的故障也时有发生,如果不及时有效地处理,可能会引发严重的安全生产事故。
因此,制定和执行科学合理的应急预案就显得尤为重要。
本文将围绕工业机器人系统故障引发的安全生产事故应急预案展开论述。
二、安全生产事故的分类和原因在工业机器人系统中,安全生产事故主要分为机器人系统本身故障引起的事故和人为因素导致的事故。
机器人系统故障可能源于机器人编程错误、传感器故障、电气故障等,而人为因素包括操作员不当操作、维护保养不到位等。
三、应急预案的重要性工业机器人系统故障引发的安全生产事故一旦发生,可能导致人员伤亡、设备损坏、生产中断等严重后果。
制定和执行安全生产事故应急预案有助于提前做好准备,并在事故发生时迅速采取措施,最大程度地减少人员伤亡和财产损失。
四、应急预案的制定步骤1. 事故风险评估:对工业机器人系统故障引发的安全生产事故进行风险评估,确定可能发生的事故类型和风险程度。
2. 预案目标和原则:明确应急预案的目标和制定原则,确保预案的科学性和可执行性。
3. 预警与监测:建立预警机制,及时监测工业机器人系统的运行状态,发现潜在故障风险。
4. 应急组织与指挥:明确责任分工,建立应急组织机构和指挥体系,确保在事故发生时能够快速、有效地响应。
5. 应急资源准备:储备必要的应急救援资源,包括人员、装备、工具等,以迅速应对事故。
6. 应急演练与培训:定期组织应急演练与培训,提高员工的应急响应和处置能力。
7. 事故调查与总结:对每起事故进行调查,总结教训,完善应急预案。
五、应急预案的具体措施1. 应急联络:建立应急联系人名单,保证与相关部门的紧密联系和信息交流。
2. 事故报告与处置:明确事故报告流程和处理措施,及时通知相关人员,采取紧急措施控制事态发展。
3. 人员疏散与救援:制定人员疏散方案,确保安全迅速疏散,并做好伤员救治工作。
焊接机器人危险性分析及安全防护对策
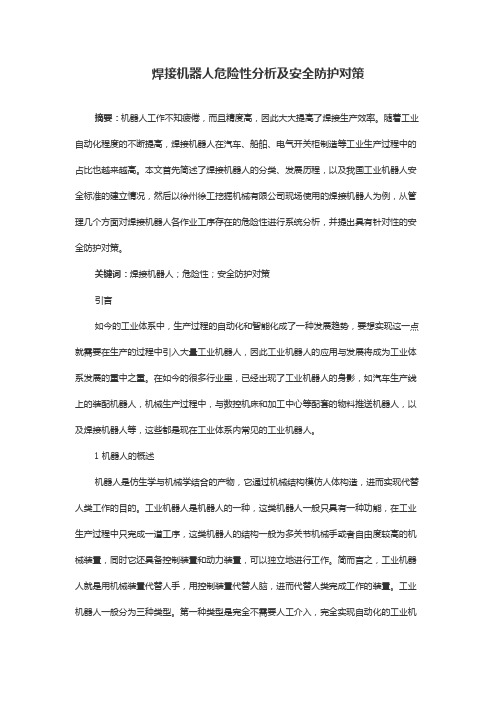
焊接机器人危险性分析及安全防护对策摘要:机器人工作不知疲倦,而且精度高,因此大大提高了焊接生产效率。
随着工业自动化程度的不断提高,焊接机器人在汽车、船舶、电气开关柜制造等工业生产过程中的占比也越来越高。
本文首先简述了焊接机器人的分类、发展历程,以及我国工业机器人安全标准的建立情况,然后以徐州徐工挖掘机械有限公司现场使用的焊接机器人为例,从管理几个方面对焊接机器人各作业工序存在的危险性进行系统分析,并提出具有针对性的安全防护对策。
关键词:焊接机器人;危险性;安全防护对策引言如今的工业体系中,生产过程的自动化和智能化成了一种发展趋势,要想实现这一点就需要在生产的过程中引入大量工业机器人,因此工业机器人的应用与发展将成为工业体系发展的重中之重。
在如今的很多行业里,已经出现了工业机器人的身影,如汽车生产线上的装配机器人,机械生产过程中,与数控机床和加工中心等配套的物料推送机器人,以及焊接机器人等,这些都是现在工业体系内常见的工业机器人。
1机器人的概述机器人是仿生学与机械学结合的产物,它通过机械结构模仿人体构造,进而实现代替人类工作的目的。
工业机器人是机器人的一种,这类机器人一般只具有一种功能,在工业生产过程中只完成一道工序,这类机器人的结构一般为多关节机械手或者自由度较高的机械装置,同时它还具备控制装置和动力装置,可以独立地进行工作。
简而言之,工业机器人就是用机械装置代替人手,用控制装置代替人脑,进而代替人类完成工作的装置。
工业机器人一般分为三种类型。
第一种类型是完全不需要人工介入,完全实现自动化的工业机器人,它是一种完全独立的工业机器人,可以单独的完成一项工作,还可以通过改变其内部程序实现不同的工作需要。
第二种类型是需要人工进行操作的工业机器人,它最早出现于核物理领域,和军事领域,这类工业机器人也被称作操作机,主要用于代替人类完成一些危险的工作,最开始是通过有线连接实现对操作机的控制,后来经过发展改为了通过无线连接进行对操作机的控制,目前这类机器人的发展前沿是外星球探测车。
如何应对工业机器人对劳动者安全的威胁

如何应对工业机器人对劳动者安全的威胁随着科技的迅猛发展,工业机器人在现代制造业中扮演着越来越重要的角色。
传统的劳动模式被自动化取代的趋势不可逆转,然而,工业机器人也给劳动者带来了一定的安全威胁。
本文将探讨如何应对工业机器人对劳动者安全的威胁,并提出相应的解决方案。
一、加强工业机器人的安全设计和制造工业机器人的安全设计和制造是解决劳动者安全问题的关键。
制造商应当遵循相关标准和规范,确保机器人具备可靠的安全功能。
例如,机器人应该具备感知能力,能够及时识别人体存在,并停止运动以避免碰撞事故的发生。
此外,机器人的操作界面应当简明易懂,设置紧急停止按钮等安全设备,方便操作人员在紧急情况下迅速停止机器人的运动。
二、完善工业机器人的安全监控系统除了安全设计和制造,安全监控系统也是确保劳动者安全的重要手段。
监控系统可以通过监测工业机器人的状态和运行情况,及时发现潜在的安全隐患,减少事故的发生。
监控系统可以通过声音、光线、图像等多种传感器来实现,实时监控机器人的运动轨迹和工作状态。
一旦发现异常,系统应该能够自动停机或者发出警报,并及时通知相关人员进行处理。
三、加强劳动者的安全培训和教育劳动者的安全意识和操作技能对于预防机器人事故同样至关重要。
企业应该加强对员工的安全培训和教育,使他们熟悉工业机器人的工作原理和操作规程,并掌握正确的应对措施。
此外,企业还应定期组织演练和模拟实验,帮助员工熟悉各类应急情况下的处理方式,提高应对危机的能力。
四、建立完善的法律法规和制度完善的法律法规和制度也能够有效应对工业机器人对劳动者安全的威胁。
政府应制定相关法律和标准,明确工业机器人的设计、制造、使用和监管要求。
同时,加强对企业的监督检查,对违反安全规定的企业进行处罚,促使企业重视劳动者安全问题。
此外,建立工业机器人安全事故报告和调查机制,及时总结经验教训,为工业机器人安全提供参考和借鉴。
五、积极推动人机协作模式的发展针对工业机器人对劳动者安全的威胁,推动人机协作模式的发展是一种有益的解决方案。
- 1、下载文档前请自行甄别文档内容的完整性,平台不提供额外的编辑、内容补充、找答案等附加服务。
- 2、"仅部分预览"的文档,不可在线预览部分如存在完整性等问题,可反馈申请退款(可完整预览的文档不适用该条件!)。
- 3、如文档侵犯您的权益,请联系客服反馈,我们会尽快为您处理(人工客服工作时间:9:00-18:30)。
编号:SM-ZD-12083关于工业机器人的事故分析及其对策Organize enterprise safety management planning, guidance, inspection and decision-making, ensure the safety status, and unify the overall plan objectives编制:____________________审核:____________________时间:____________________本文档下载后可任意修改关于工业机器人的事故分析及其对策简介:该安全管理资料适用于安全管理工作中组织实施企业安全管理规划、指导、检查和决策等事项,保证生产中的人、物、环境因素处于最佳安全状态,从而使整体计划目标统一,行动协调,过程有条不紊。
文档可直接下载或修改,使用时请详细阅读内容。
摘要:工业机器人是高科技机电产品,在工业领域广泛应用,可以代替人们从事繁重的、危险性的工作,但由于工业机器人故障所造成的人身伤害事故也时有发生。
从工业机器人的可靠性、工业机器人事故案例、能量类型分类等多角度对工业机器人事故进行了分析,从故障树分析法、基本安全性原则、工业安全技术等几方面提出了相应的对策。
关键词:工业机器人事故安全分析对策1 引言工业机器人被广泛地应用于制造业等诸多部门,它可以代替人们在具有危险性的场所从事繁重的工作。
工业机器人在将人们从繁重的危险性劳动中解放出来的同时,也存在产生危险的因素,由于工业机器人故障所造成的人身伤害事故时有发生。
工业机器人是由一个复杂的机电系统组成的,这个系统包括传感器、控制器、工作制造部件、输送部件等。
人要对工业机器人进行安装、编程、维修,还有可能靠近机器人进行操作,因此,人也将参与到机器人的工作系统中去,当人靠近工业机器人时就可能出现安全问题[1]。
机器人的自由度比其他普通机械大得多,它的工作制造部件可以在较大空间内运行,具有高速运动的大功率手臂和复杂自主的动作,若机器人发生故障可能造成更为严重的危害。
所以,有必要对工业机器人的有关事故情况进行分析,并研究相应对策。
2 工业机器人安全性概况2.1 工业机器人的可靠性分析鉴于工业安全问题的重要性,世界上有许多国家(如日本、美国、英国、德国、瑞典等)从上世纪80年代开始就注意对工业机器人的事故进行记录,并进行统计和分析,为工业机器人的安全性、可靠性研究奠定了基础。
日本某公司对工业机器人发生事故的类别进行了调查统计,其中控制装置的故障占66.9%,机器人装置上的工作部件,如焊枪等工具的故障占18.5%,工作场所噪声信号的干扰引起的机器人失控占11.1%,其他原因的故障占3.5%。
表1 为机器人的平均无故障时间(MTBF)的统计。
可以看出,在机器人工作不到100h的时间内,其平均无故障率只有28.70%,工作100h以上,其平均无故障率明显下降。
假如生产流水线上,机器人平均每天工作按20h 计算,则在一周左右的时间内,机器人极有可能发生故障。
从上述统计分析可知,机器人的控制装置、工作部件以及工作场所噪声信号的干扰等易使机器人发生故障,而且机器人故障的发生也很频繁。
因此,机器人的可靠性还是很有限的,应当引起人们足够的重视,充分考虑各项安全措施。
2.2 工业机器人的事故分析以下是日本机器人协会(1234)提供的0 个典型的工业机器人事故案例[2]:(1)1 名工人的手指被正在做正常上下运动的机器人夹在工件与切割夹具之间;(2)机器人在进行正常操作时,当它把薄钢板传递到工人手中时割破了工人的手指;(3)在进行正常操作的机器人的手臂撞在工人身上,将工人撞伤;(4)在进行人工操作时机器人手臂不符合指令要求,正当操作人员要进行调整时,头部被机器人划破。
表2 为机器人事故原因的调查统计分析。
表2 机器人事故原因统计分析由上述事故案例和事故原因的调查统计分析,可以得出以下结论:(1)在人工操作机器人时,机器人造成危险的可能性很大;(2)在机器人造成的危险中,归因于设备自身误动作的有一半之多;(3)由机器人自身错误所引起的和由人为失误所引起的事故发生率几乎相等;(4)机器人作为自动化设备在其正常操作条件下,发生事故次数占总事故次数的比重很大,可达22.4%-66.4%;(5)机器人的设计和生产不能保证使用机器人时绝对安全或绝对不发生故障,安全使用机器人还取决于使用者的技术水平和保养及维修等诸多因素。
3 工业机器人的安全对策分析3.1 故障树分析法(FTA)故障树分析法(FTA)是被广泛使用的演绎分析工具,可以用清晰的结构层次展现故障的发生原因、情形。
在人机器人工作环境中,所有潜在的危险都是由于不安全条件和不安全行为所致,可用故障树分析(FTA)方法对危险的原因结果逻辑关系作演绎分析。
由于机器人的使用方式和操作对象不同,完成的工作以及使用的工具都不尽相同,涉及的能量形式也不同,因此,在进行故障分析时应全面考虑,对上述各种不同点都要有对应的安全措施。
以下是对机器人误动作造成的人身伤害事故的原因进行归纳整理,做出的故障树(见图1)。
通过FTA对人机器人环境中潜在事故危险的分析研究发现,可采取以下几点措施来有效地减少危险:(1)减少异常能量的转换。
如图中的X1、X2、X3、X9等。
要提高机器人硬件的可靠性,例如改进控制板的设计,采取标准化措施,有完全可靠的紧急停车方法,避免机器人失控。
同时还应尽量避免操作人员在机器人的危险区内工作。
(2)使异常能量最小化。
如图中的X2、X3、X8等。
用降低机器人运动速度的办法来减少,例如编程操作人员必须接近机器人的危险时,应密切注意负载情况。
一旦发现负载的重量、尺寸和形状超过极限,就要立即停车检查;还要研究负载的运动,以减少错误操作和机器人的误动作。
(3)优化防护措施。
如图中的X4、X5、X8等。
在使用机器人时应该采取各种预防事故的措施,如安装防护栏、安全闸,用传感器监控,用检测器检测等。
在有机器人的全自动装配线等大型自动化系统中,还应更多地从工艺过程角度出发,制订更全面、合理的安全措施。
图1 机器人误动作故障树[2](4)完善机器人控制措施。
如图中的X6、X7、X9、X10等。
工业自动化与安全措施是相辅相成、共同发展的。
因此,要使工人充分认识到机器人存在的危险性,并远离机器人危险区,要对操作员、程序员、维修工程师进行全面的安全技术教育与培训。
3.2 工业机器人系统的危险性评价与安全性评价(1)危险性评价:在技术上采取安全对策时,必须在适当的指标的基础上进行。
假设因机器人产生了某种事故,其事故带来的危险性可由下式表示:危险性=失败的频度(类型1)×危险侧迁移率(类型2)×伤害强度(类型3)[2]。
式中所指的失败(类型1)可分为:①不经修理就不可恢复正常状态的硬件故障;②消除外部原因(如电磁噪音干扰)就能恢复正常状态;③由于操作错误或因不安全行为所产生的人为故障等。
为了减少失败,必须对机器人系统进行高可靠性设计。
所谓危险侧迁移率(类型3)是指出现了故障(失败)以后所产生的危险,对人而言,人就成了危险的一侧,危险一侧所占的危险比例,就是危险侧迁移率。
即不管出现什么故障(失败)都要确保人身的安全,只能侧重这一方面。
因此就必须在机器人的基本结构设计方面多想方法,例如联锁装置和故障自动排除装置等均很有效。
所谓伤害强度(类型’),是指随着机器人往大型、高速方面发展的过程中给予人的伤害危险的潜在能量越来越大,这就是伤害强度。
这里,重要的是要减少在使用机器人时对人构成的危险性,也就是说要极力降低类型1和类型2的发生概率,使危险侧迁移率变小。
在系统设计阶段,要尽量抑制对人产生威胁的机器人所产生的力或运动,这样才有可能从根本上保证人身安全。
(2)安全性评价:它阐明造成人体实质损害危险发生的机理,评估安全性对策的效果和系统中的剩余风险。
需要指出的是,对于只有较小数据的较新型的系统,是通过系统化预测或演绎来进行评价的,包含以下3个基本步骤:①识别系统中可能产生的危险;②及时分析危险发生的机理并研究安全性对策;#评价剩余风险[3]。
3.3 基本原则性的安全对策针对工业机器人的特殊性,以下一些安全对策是不可缺少的:(1)尽量减少危险部位。
采用机器人组成自动化系统时,由于机器人的动作范围大,与其他机械设备衔接的地方很多,因而对人构成威胁的危险部位比一般的机械设备要多,所以在考虑系统布局时,应尽量减少这些危险部位。
例如,在机器人有伸缩、摆动、俯仰、夹紧与放开等动作的部位放置挡块等制动器,或适当降低机器人的输出功率和运动速度,以减少对人的危险。
(2)将人与机器人的危险部位进行隔防。
在机器人自动运行时,原则上应用栏杆围障或罩子把人与机器人隔离,人只能在栏杆等屏障外操纵机器人。
这些方法符合人机工程学的一般原则,结构也简单。
但若需对机器人进行示教或维修又必须进入隔离区时,则需另外采取相应的防护与监视措施。
(3)附加安全装置。
附加安全装置应具有自我诊断的功能,而且这些装置对故障或异常现象的信号处理都与机器人的运动无关,是一些保护人身安全的有用装置。
(4)故障自动保护。
一是必须具有通过伺服系统对机器人的误动作进行监视的功能,如有异常动作应自动切断电源;二是必须具有当人误入危险区时,能立即测知并自动停机的故障自动检测系统。
具体措施有:安装警示灯,监视器,防越程装置,紧急停止装置等。
这些基本原则性的安全对策应逐步具体化、规范化乃至立法化,世界上许多工业发达国家已经开始实施,如美国国家标准工业机器人系统安全标准ANSI/RIA R15.06-1986和日本的工业机器人安全规则(JISB8433-1986)等[3]。
4 结语工业机器人的广泛应用促进了它的设计水平和制造水平的提高。
智能机器人的研制在现阶段飞速发展,它能完成的技术操作是人工无法相比的。
因此,随着机器人的普及和复杂化,人机器人工作环境中的安全问题就显得尤为突出。
机器人系统在现阶段可靠性不高,事故时有发生。
为此,不仅要解决在设计阶段的技术难点,也要研究从使用现场,事故分析中反馈回来的信息,以便及时提出相应的对策。
只有发展到机器人本身能够检测到人的接近,并能自动、准确地采取适当措施时,才能确保人---机器人工作环境的安全[3]。
参考文献1 张建民等,机电一体化系统设计,北京:北京理工大学出版社,49962 日本机器人学会,机器人技术手册,北京:科学出版社,1996,3 廖炯生,机器人的可靠性、维修性、安全性* 科学出版社,19944 蔡自兴,机器人原理及应用* 中南工业大学出版社5 余达太,马香峰等* 工业机器人的应用工程。
北京:冶金工业出版,1999这里填写您的企业名字Name of an enterprise。