丰田公司经营模式分析
详解丰田精益生产管理模式

供应链管理:需要与供应商建立紧密的合作关系,确保原材料的供应和质量
单击此处输入你的正文,请阐述观点
面临的挑战与应对策略
挑战:市场竞争激烈,需要不断提高产品质量和降低成本
应对策略:采用精益生产管理模式,通过消除浪费、提高生产效率和产品质量来降低成本
挑战:员工素质参差不齐,需要提高员工的技能和素质
持续改进:不断改进生产过程,提高产品质量和生产效率
拉动原则:通过客户需求拉动生产,实现准时化生产
消除浪费:通过消除生产过程中的浪费,提高生产效率和降低成本
减少浪费
减少动作浪费:通过改进工作流程和操作方法,减少不必要的动作和浪费时间
减少等待浪费:通过合理安排生产计划和流程,减少等待时间和空闲时间
减少不良浪费:通过提高产品质量和减少缺陷,降低不良率,减少浪费
04
价值流分析
识别产品或服务流程中的浪费
确定价值流中的关键过程和活动
制定改进计划并实施
持续改进并优化价值流
制定生产计划与目标
确定生产计划:根据市场需求和产能规划,制定合理的生产计划
设定生产目标:明确生产目标,包括产量、质量、成本等方面的要求
制定生产计划表:将生产计划细化为具体的生产计划表,包括生产时间、生产数量、生产批次等方面的信息
丰田生产方式(TPS)的诞生
精益生产管理模式的形成与发展
发展历程
起源:二战后日本汽车工业的崛起
1950年代:丰田生产方式的初步形成
1960年代:精益生产概念的提出
1970年代至今:精益生产管理模式的不断完善与创新
精益生产管理模式的核心理念
消除浪费:通过消除生产过程中的浪费,提高生产效率和产品质量
《丰田模式—精益制造的14项管理原则》
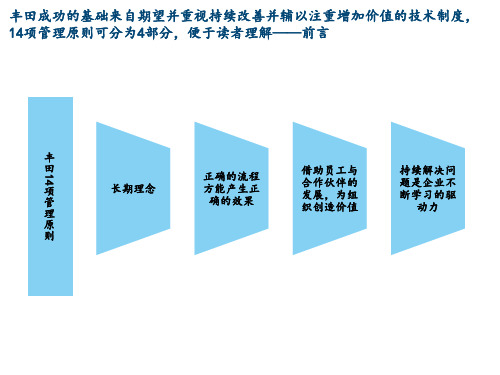
流程 (消除浪费)
理念 (长远的思维方式)
原则一:管理决策以长期理念为基础即便因此牺牲短期财务目标也在 所不惜
比赚钱更重 要的使命
做有益于顾 客的事情
别让事业决 策伤害到信 任与相互尊
重
以仰赖自我 与责任感来 决定自己的
命运
丰田的使命 与指导原则
拟定坚定的 目标,留名
青史
丰田模式的14项原则的第二类
卓越的作业流程是丰田作为世界一流企业让各国企业管理者学习的基础
大多数“精益” 型公司所处阶段
解决问题 (持续的改进与学习
) 员工/合作伙伴 (尊重他们挑战他们 使他们成长)
流程 (消除浪费)
理念 (长远的思维方式)
丰田经营之道:“4P模式”
改善作业流程的方法
杜绝时间与资源的浪费 在工作场所的体制中内建
质检 寻找低成本但可靠的方法
以代替昂贵的新技术 力求作业流程的尽善尽美 建立追求持续改善的学习
文化
丰田家族代代展现一致的领导者逐步形成了让世界企业争相学习的丰田模式
丰田佐吉是优秀的工程师,被称为日本的“发明大王”热衷于持续改
丰田佐吉
善的工作理念与方法
他以父亲的管理理念和方法为基础,融入了自己的创新。丰田的理念
原则三:使用拉动式生产方式以避免生产过剩
原则:由顾 客拉动进行
补货
看板:日常 生活中的拉
动补货
公司的存货越多……就越不可能达成期 望目标。
——大野耐一
看板:在必 要之处实施
拉动
预定进度表 的推动式生
产方式
原则四:使工作负荷平均(生产均衡化)
均衡化:使生产与流 程均衡化 均衡化是使生产量和 产出组合都能平均化 并不是根据顾客订单 的实际流量来制造产 品,顾客订单流量可 能会出理明显波动, 均衡化拿一段期间内 的总订单量来平均化 ,使每天的产量与产 出组合相同
丰田管理模式全集
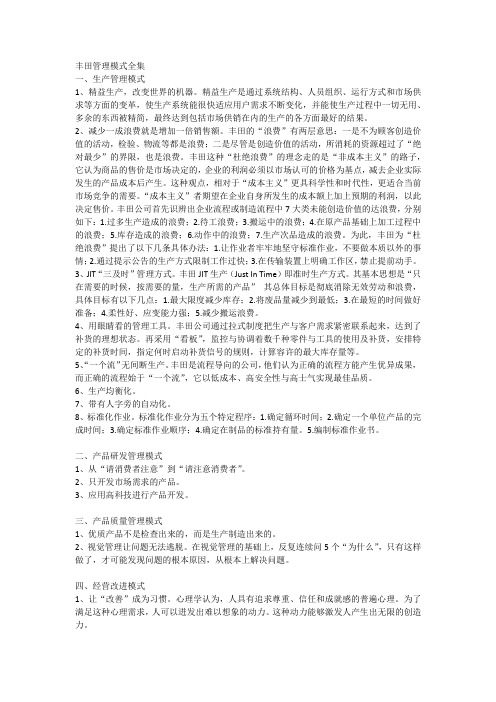
丰田管理模式全集一、生产管理模式1、精益生产,改变世界的机器。
精益生产是通过系统结构、人员组织、运行方式和市场供求等方面的变革,使生产系统能很快适应用户需求不断变化,并能使生产过程中一切无用、多余的东西被精简,最终达到包括市场供销在内的生产的各方面最好的结果。
2、减少一成浪费就是增加一倍销售额。
丰田的“浪费”有两层意思:一是不为顾客创造价值的活动,检验、物流等都是浪费;二是尽管是创造价值的活动,所消耗的资源超过了“绝对最少”的界限,也是浪费。
丰田这种“杜绝浪费”的理念走的是“非成本主义”的路子,它认为商品的售价是市场决定的,企业的利润必须以市场认可的价格为基点,减去企业实际发生的产品成本后产生。
这种观点,相对于“成本主义”更具科学性和时代性,更适合当前市场竞争的需要。
“成本主义”者期望在企业自身所发生的成本额上加上预期的利润,以此决定售价。
丰田公司首先识辨出企业流程或制造流程中7大类未能创造价值的达浪费,分别如下:1.过多生产造成的浪费;2.待工浪费;3.搬运中的浪费;4.在原产品基础上加工过程中的浪费;5.库存造成的浪费;6.动作中的浪费;7.生产次品造成的浪费。
为此,丰田为“杜绝浪费”提出了以下几条具体办法:1.让作业者牢牢地坚守标准作业,不要做本质以外的事情;2.通过提示公告的生产方式限制工作过快;3.在传输装置上明确工作区,禁止提前动手。
3、JIT“三及时”管理方式。
丰田JIT生产(Just In Time)即准时生产方式。
其基本思想是“只在需要的时候,按需要的量,生产所需的产品”其总体目标是彻底消除无效劳动和浪费,具体目标有以下几点:1.最大限度减少库存;2.将废品量减少到最低;3.在最短的时间做好准备;4.柔性好、应变能力强;5.减少搬运浪费。
4、用眼睛看的管理工具。
丰田公司通过拉式制度把生产与客户需求紧密联系起来,达到了补货的理想状态。
再采用“看板”,监控与协调着数千种零件与工具的使用及补货,安排特定的补货时间,指定何时启动补货信号的规则,计算容许的最大库存量等。
企业丰田生产管理模式
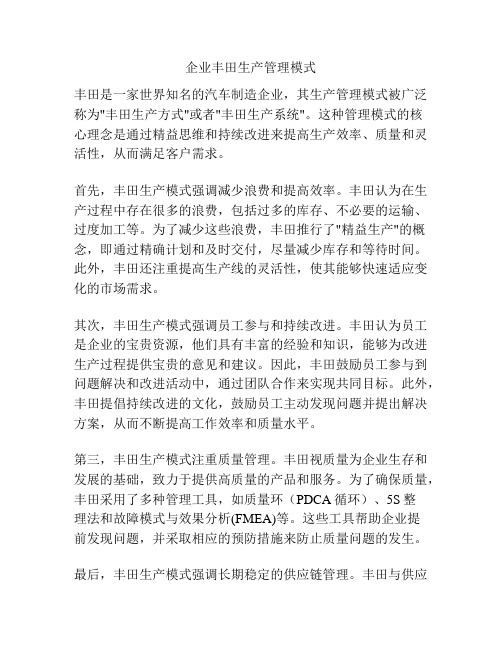
企业丰田生产管理模式丰田是一家世界知名的汽车制造企业,其生产管理模式被广泛称为"丰田生产方式"或者"丰田生产系统"。
这种管理模式的核心理念是通过精益思维和持续改进来提高生产效率、质量和灵活性,从而满足客户需求。
首先,丰田生产模式强调减少浪费和提高效率。
丰田认为在生产过程中存在很多的浪费,包括过多的库存、不必要的运输、过度加工等。
为了减少这些浪费,丰田推行了"精益生产"的概念,即通过精确计划和及时交付,尽量减少库存和等待时间。
此外,丰田还注重提高生产线的灵活性,使其能够快速适应变化的市场需求。
其次,丰田生产模式强调员工参与和持续改进。
丰田认为员工是企业的宝贵资源,他们具有丰富的经验和知识,能够为改进生产过程提供宝贵的意见和建议。
因此,丰田鼓励员工参与到问题解决和改进活动中,通过团队合作来实现共同目标。
此外,丰田提倡持续改进的文化,鼓励员工主动发现问题并提出解决方案,从而不断提高工作效率和质量水平。
第三,丰田生产模式注重质量管理。
丰田视质量为企业生存和发展的基础,致力于提供高质量的产品和服务。
为了确保质量,丰田采用了多种管理工具,如质量环(PDCA循环)、5S整理法和故障模式与效果分析(FMEA)等。
这些工具帮助企业提前发现问题,并采取相应的预防措施来防止质量问题的发生。
最后,丰田生产模式强调长期稳定的供应链管理。
丰田与供应商建立了长期合作关系,共同努力提高供应链的效率和质量。
丰田通过合理的资源配置、及时的信息共享和有效的沟通来实现供应链的协同运作,从而保证产品能够按时交付给客户。
总之,丰田生产管理模式在全球范围内被广泛应用和赞誉,其创新的理念和方法对其他企业也具有很大的借鉴意义。
通过减少浪费、员工参与和持续改进、质量管理以及稳定的供应链管理,丰田取得了令人瞩目的成功,并赢得了全球客户的信赖和认可。
丰田生产管理模式是丰田汽车公司的核心管理模式,也是丰田成功的关键之一。
丰田的管理模式jit
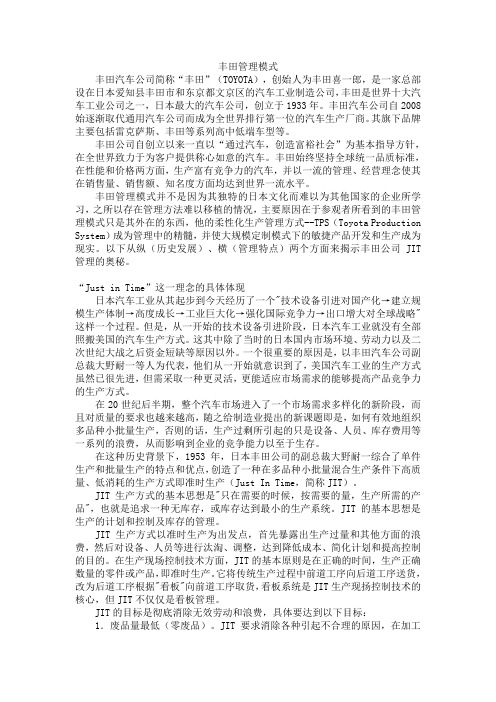
丰田管理模式丰田汽车公司简称“丰田”(TOYOTA),创始人为丰田喜一郎,是一家总部设在日本爱知县丰田市和东京都文京区的汽车工业制造公司,丰田是世界十大汽车工业公司之一,日本最大的汽车公司,创立于1933年。
丰田汽车公司自2008始逐渐取代通用汽车公司而成为全世界排行第一位的汽车生产厂商。
其旗下品牌主要包括雷克萨斯、丰田等系列高中低端车型等。
丰田公司自创立以来一直以“通过汽车,创造富裕社会”为基本指导方针,在全世界致力于为客户提供称心如意的汽车。
丰田始终坚持全球统一品质标准,在性能和价格两方面,生产富有竞争力的汽车,并以一流的管理、经营理念使其在销售量、销售额、知名度方面均达到世界一流水平。
丰田管理模式并不是因为其独特的日本文化而难以为其他国家的企业所学习,之所以存在管理方法难以移植的情况,主要原因在于参观者所看到的丰田管理模式只是其外在的东西,他的柔性化生产管理方式--TPS(Toyota Production System)成为管理中的精髓,并使大规模定制模式下的敏捷产品开发和生产成为现实。
以下从纵(历史发展)、横(管理特点)两个方面来揭示丰田公司JIT 管理的奥秘。
“Just in Time”这一理念的具体体现日本汽车工业从其起步到今天经历了一个"技术设备引进对国产化→建立规模生产体制→高度成长→工业巨大化→强化国际竞争力→出口增大对全球战略"这样一个过程。
但是,从一开始的技术设备引进阶段,日本汽车工业就没有全部照搬美国的汽车生产方式。
这其中除了当时的日本国内市场环境、劳动力以及二次世纪大战之后资金短缺等原因以外。
一个很重要的原因是,以丰田汽车公司副总裁大野耐一等人为代表,他们从一开始就意识到了,美国汽车工业的生产方式虽然已很先进,但需采取一种更灵活,更能适应市场需求的能够提高产品竞争力的生产方式。
在20世纪后半期,整个汽车市场进入了一个市场需求多样化的新阶段,而且对质量的要求也越来越高,随之给制造业提出的新课题即是,如何有效地组织多品种小批量生产,否则的话,生产过剩所引起的只是设备、人员、库存费用等一系列的浪费,从而影响到企业的竞争能力以至于生存。
丰田模式的14项原则
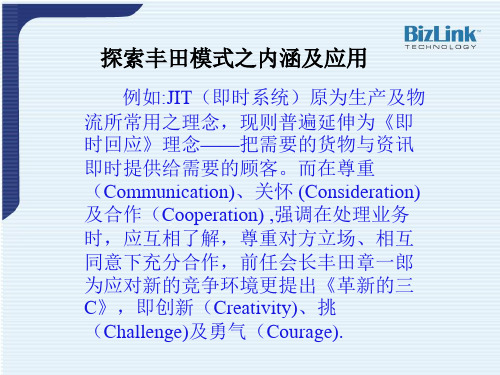
• •
丰田模式的14项原则
《第二类》正确的流程方能产生正确结果 原则6. 职务工作的标准化是持续改善与授权员工的基楚。 • • 在工作场所中的任何地方都使用稳定、可重复的方法,以 维持流程的可预测性、规律的时间,及规律的产出,这是 单件流程作业与后拉制度的基础。 到一定时间时,应该吸取对流程的累积学习心得,把现今 的最佳实务标准化,让个别员工表达他们对于改善标准的 创意见解,把这些见解纳入新标准中,如此来,当员工异 动时,便可以把学习心得移转给接替职务工作的员工。
•
丰田模式的14项原则
《第二类》正确的流程方能产生正确结果 原则3. 使用后拉式制度以避免生产过剩。 • •
•
在你的生产流程下游顾客需求的时候供应他们正确数量的 正确东西,材料的补充应该由消费量决定,这是即时生产 的基本原则。 使在制品及仓库存货减至最少,每项产品只维持少量存货, 根据顾客实际领取的数量,经常补充存货。 因应顾客需求的每天变化,而不是仰赖电脑时程表与系统 来追踪浪费的存货。
借由去除流程中每个步骤的浪费以缩短前置期,可以促成最佳 品质、降低成本,以及改善安全性与员工士气.
展现富创造力的精神接受挑战
我们以富创造力的精神接受挑战,鼓励实现我们的梦想而不失 去动力或精神;本者乐观真诚相信我们的贡献的价值,对我们的工 作展现旺盛精神.我们努力于决定自己的命运,仰赖自我,相信自己 的能力;我们对自己的行为及维持与改善创造价值的技能等负责.
•生产产品的前置期缩短93%(从12天缩短至6.5小时)。 •在制品存货期(work-in-process inventory)缩短83%(从9小时 缩短至1.5小时)。 •最终成品存货量减少91%(从30,500单位减少至2,890单 位)。 •加班时间减少50%(从平均每人每周10小时减少为5小时)。 •生产力提高87.5%(从平均每员工每小时生产2.4件增加到4.5 件。
丰田公司的企业文化 丰田公司管理经营模式
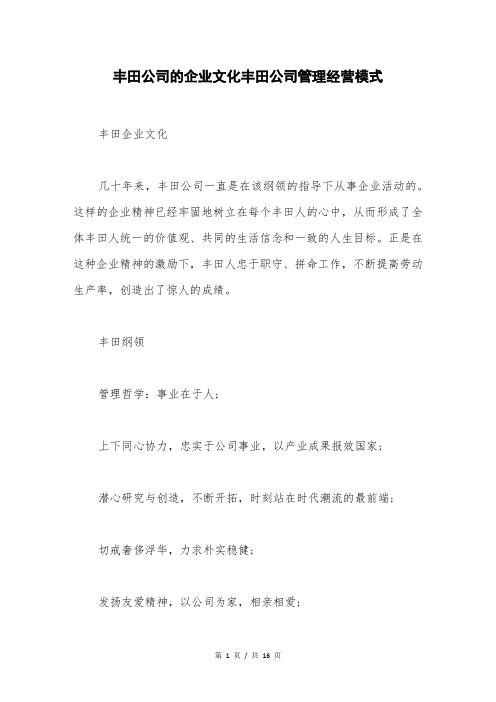
丰田公司的企业文化丰田公司管理经营模式丰田企业文化
几十年来,丰田公司一直是在该纲领的指导下从事企业活动的。
这样的企业精神已经牢固地树立在每个丰田人的心中,从而形成了全体丰田人统一的价值观、共同的生活信念和一致的人生目标。
正是在这种企业精神的激励下,丰田人忠于职守、拼命工作,不断提高劳动生产率,创造出了惊人的成绩。
丰田纲领
管理哲学:事业在于人;
上下同心协力,忠实于公司事业,以产业成果报效国家;
潜心研究与创造,不断开拓,时刻站在时代潮流的最前端;
切戒奢侈浮华,力求朴实稳健;
发扬友爱精神,以公司为家,相亲相爱;
第 1 页/ 共16 页。
丰田模式的解读

理念—方法/工具—技术
走入精益之路
• 13个诀窍: • 从技术性制度入手,紧接着进行文化变革。 • 先要“干中学”,再施以训练 • 以流程价值先导计划为起点,把精益当成一种制度来展示,提供 一个观摩的典范 • 使用价值流程图以建立未来情况愿景,并帮助员工学习如何观察 • 使用改善研习营来教导,并促成快速变革 • 根据价值流程来架构管理工作 • 把精益行动变成命令
• 13个诀窍:(续) • 一次危机可能促使公司采取精益行动,但未必会促成公司的真正 转型 • 随时留意可以产生重大财务影响的机会 • 检讨所使用的评量指标使其能强调价值流程的改善 • 在你公司的根基上建立自己的发展模式---借鉴而非否定自我价值 • 聘请或自行栽培精益领导者,并建立接班人制度 • 善用专家以教导员工,并快速获得成效。
丰田生产方式是卓越的创造价值流 程,是建立在顾客为导向(顾客拉 动)、以人为中心(尊重员工、释 放员工潜能)、坚持挑战(不满现 状、追求卓越)、持续改善和创新 的可持续发展理念的基础上。 丰田模式的本质是通过释放人的潜 能,追求卓越。
推进精益制造体系的障碍是企业的 长期思维,共赢分享及以人为本等 根本的理念与原则。
• 未被使用的员工创造力:员工未参与或未被倾听造成员工的时 间、构想、技能,使员工失去改善与学习机会。
丰田的理念是达成共识,共同解决问题这是结合理性与务实, 再加正直与卓越的手法,虽然有政治力量的介入,但丰田并不 想击败任何一方,整个处理过程中并没有任何敌对的行动---水 源地开发中各方参与协商的实例
邓德海--日本制造业管理研究
中心高级研究员,华制精益咨询 集团总裁
方宜勇—卓越制造长城奖执
委会主席,制慧网CEO
丰田模式是一套卓越的管理企业操 作软件,涉及企业如何选择使命和 价值观,如何调动企业全体员工积 极主动参与识别、理解、管理和持 续改进价值创造过程以实现企业目 标。不同的生产方式,要求不同的 劳动组织形式,管理支持架构、思 维方式及经营原则。
丰田模式

团队应该有4到5个人和无数的管理要求组成。成功取决于整个团队而不是个人。
[编辑] 原则11
* 尊重你的合作伙伴和供应商,挑战他们的能力,并帮助他们进步。
丰田对待供应商和对待自己的员工差不多,对他们提出更高的目标,并帮助他们实现。丰田提供跨职能团队帮助供应商发现问题解决问题,这样他们可以做的更好。
目录
[隐藏]
* 1 14原则
o 1.1 第一部分-长远的理念
+ 1.1.1 原则1
o 1.2 第二部分-正确的步骤会产生正确的结果
+ 1.2.1 原则2
+ 1.2.2 原则3
+ 1.3.1 原则9
+ 1.3.2 原则10
+ 1.3.3 原则11
o 1.4 第四部分-不断解决根本问题会促进整体学习
+ 1.4.1 原则12
2. 弄清问题
3. 确定问题发生范围或原因
4. 调查根本原因(5个为什么)
5. 对策
6. 评估
7. 标准化
3. 考虑一系列解决问题的办法
4. 成立解决问题的委员会
5. 使用有效的交流工具
[编辑] 原则14
* 通过不停的反省和持续的改进形成学一个学习的整体。
形成持续学习的整体的过程包括批评一个人做的每一个方面。通常确认根源并解决问题的技术包括:
1. 最初发现问题
[编辑] 第四部分-不断解决根本问题会促进整体学习
[编辑] 原则12
* 亲自到现场查看问题以充分了解整个情况。
丰田的管理者都要求到现场查看情况。不亲自体验现场管理者对怎么改进没有任何概念。并且管理者还必须奉行Tadashi Yamashima(丰田技术中心总裁)的十条管理原则:
第十三讲 丰田模式
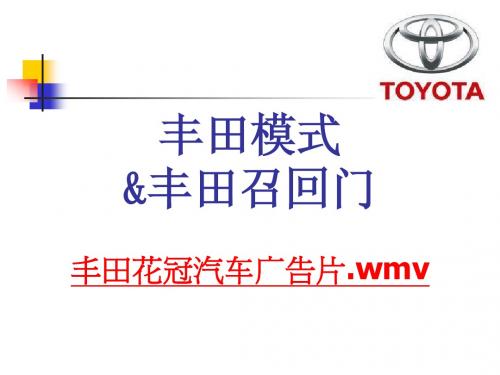
丰田模式的事业原则
第一类原则 长期理念(原则1) 第二类原则 正确的流程方能产生正确结 果(原则2~原则8) 第三类原则 发展员工与事业伙伴为组织 创造价值(原则9~原则11) 第四类原则 持续解决根本问题,组织型 学习的驱动力(原则12~原则14)
解决问题 (持续改善 与学习)
员工与事业伙伴
原则1:管理决策必须以长期理 念为基础,即使必须因此牺牲短 期财务目标也在所不惜。
【第二类】正确的流程方能产 生正确结果(process)
原则2:建立无间断的作业流程以使问题 浮 现。 原则3:使用「后拉式制度」以避免生产过剩。 原则4:使工作负荷平均(平准化),工作应该像 龟兔赛跑中的乌龟一样。 原则5:建立立即暂停以解决问题、一开始就 重 视 品 管 的 文 化 。
丰田模式的14项事业原则
8. 使用可靠且已经充分测试的技术以支持人员及流程 。 9. 栽培彻底了解且拥抱公司理念的员工成为领导者并使她 们能教导其他员工。 10. 栽培与发展信奉公司理念的杰出人才与团队。 11. 重视事业伙伴与供货商网络,挑战它们且帮助它们改善。 12. 亲临现场查看以彻底了解情况。(现地现物) 13. 决策不急躁,以共识为基础,彻底考虑所有可能选择, 快速执行决策。 14. 透过不断省思与持续改善,以变成一个学习型`组织。
于1927年完成了“即时到位”的生产思 想和方法,即彻底完备各种专用工作机器 和加工组装工具,并统一它们的规格。 与此同时, 对零部件进行提前喷漆和辅助安装,然 后供给组装工厂的流水作业形式。
丰田喜一郎
1933年,在“丰田自动织布机制造所” 设立了汽车部。丰田喜一郎的同学隈部 一雄从德国给他买回一辆德国DKW牌前轮 子驱动汽车,经过两年的拆装研究,终 于1935年8月造出了一辆GI牌汽车。
丰田汽车跨国经营模式研究
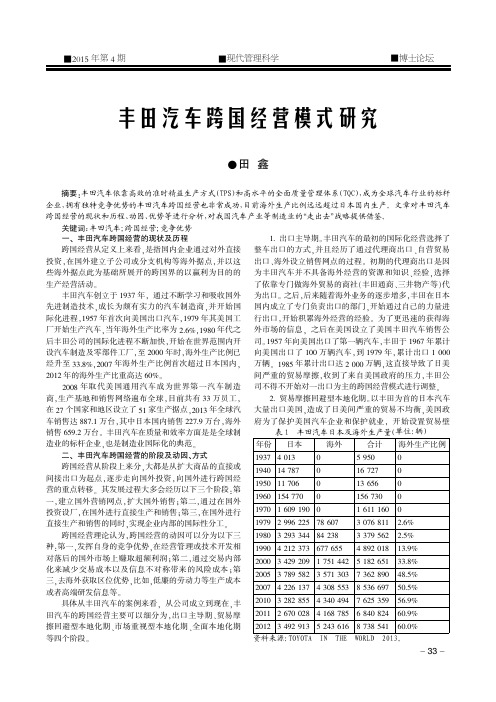
年份日本海外合计海外生产比例193740130595001940147870167270195011706013656019601547700156730019701609190016111600197929962257860730768112.6%198032933448423833795622.5%19904212373677655489201813.9%200034292091751442518265133.8%200537895823571303736289048.5%200742261374308553853669750.5%201032828554340494762535956.9%201126700284168785684082460.9%201234929135243616873854160.0%表1丰田汽车日本及海外生产量(单位:辆)资料来源:TOYOTA IN THE WORLD 2013。
一、丰田汽车跨国经营的现状及历程跨国经营从定义上来看,是指国内企业通过对外直接投资,在国外建立子公司或分支机构等海外据点,并以这些海外据点此为基础所展开的跨国界的以赢利为目的的生产经营活动。
丰田汽车创立于1937年,通过不断学习和吸收国外先进制造技术,成长为颇有实力的汽车制造商,并开始国际化进程,1957年首次向美国出口汽车,1979年其美国工厂开始生产汽车,当年海外生产比率为2.6%,1980年代之后丰田公司的国际化进程不断加快,开始在世界范围内开设汽车制造及零部件工厂,至2000年时,海外生产比例已经升至33.8%,2007年海外生产比例首次超过日本国内,2012年的海外生产比重高达60%。
2008年取代美国通用汽车成为世界第一汽车制造商,生产基地和销售网络遍布全球,目前共有33万员工,在27个国家和地区设立了51家生产据点,2013年全球汽车销售达887.1万台,其中日本国内销售227.9万台,海外销售659.2万台。
丰田模式
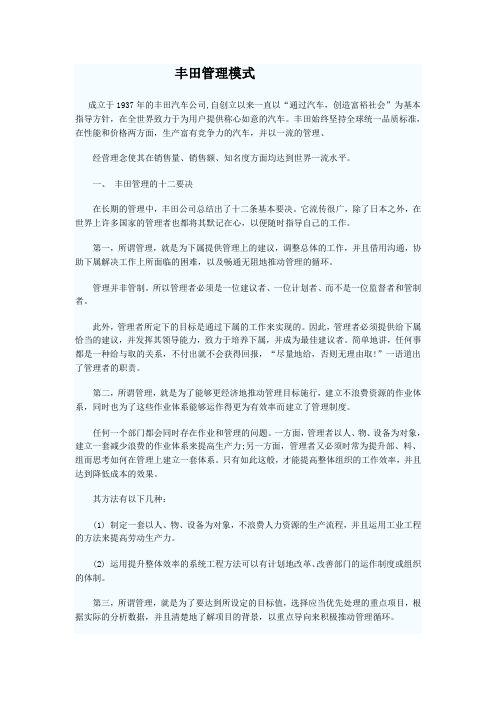
丰田管理模式成立于1937年的丰田汽车公司,自创立以来一直以“通过汽车,创造富裕社会”为基本指导方针,在全世界致力于为用户提供称心如意的汽车。
丰田始终坚持全球统一品质标准,在性能和价格两方面,生产富有竞争力的汽车,并以一流的管理、经营理念使其在销售量、销售额、知名度方面均达到世界一流水平。
一、丰田管理的十二要决在长期的管理中,丰田公司总结出了十二条基本要决。
它流传很广,除了日本之外,在世界上许多国家的管理者也都将其默记在心,以便随时指导自己的工作。
第一,所谓管理,就是为下属提供管理上的建议,调整总体的工作,并且借用沟通,协助下属解决工作上所面临的困难,以及畅通无阻地推动管理的循环。
管理并非管制。
所以管理者必须是一位建议者、一位计划者、而不是一位监督者和管制者。
此外,管理者所定下的目标是通过下属的工作来实现的。
因此,管理者必须提供给下属恰当的建议,并发挥其领导能力,致力于培养下属,并成为最佳建议者。
简单地讲,任何事都是一种给与取的关系,不付出就不会获得回报,“尽量地给,否则无理由取!”一语道出了管理者的职责。
第二,所谓管理,就是为了能够更经济地推动管理目标施行,建立不浪费资源的作业体系,同时也为了这些作业体系能够运作得更为有效率而建立了管理制度。
任何一个部门都会同时存在作业和管理的问题。
一方面,管理者以人、物、设备为对象,建立一套减少浪费的作业体系来提高生产力;另一方面,管理者又必须时常为提升部、料、组而思考如何在管理上建立一套体系。
只有如此这般,才能提高整体组织的工作效率,并且达到降低成本的效果。
其方法有以下几种:(1) 制定一套以人、物、设备为对象,不浪费人力资源的生产流程,并且运用工业工程的方法来提高劳动生产力。
(2) 运用提升整体效率的系统工程方法可以有计划地改革、改善部门的运作制度或组织的体制。
第三,所谓管理,就是为了要达到所设定的目标值,选择应当优先处理的重点项目,根据实际的分析数据,并且清楚地了解项目的背景,以重点导向来积极推动管理循环。
丰田模式

4、精益生产实施过程全貌
易 缺 难 足
☆ 零切换浪费 ☆ 零库存 ☆ 零浪费 ☆ 零不良 ☆ 零故障 ☆ 零停滞 ☆ 零事故
零目标
零 切换 浪费
目的
现
状
思考原则与方法
· 经济批量 · 物流方式JIT · 生产计划标准化 · 作业管理 · 标准化作业 · 探求必要库存的原因 · 库存规模的合理使用 · 均衡化生产 · 设备流水化 · 整体能力协调 · 拉式生产彻底暴露问题 · 流程路线图
五.改善建议
一.丰田管理模式的理论知识总结 丰田式生产管理(Toyota Management),或称丰田 生产体系(Toyota Production System,TPS)由日本 丰田汽车公司的副社长大野耐一创建,是丰田公司的 一种独具特色的现代化生产方式。它顺应时代的发展 和市场的变化,经历了20多年的探索和完善,逐渐形 成和发展成为今天这样的包括经营理念、生产组织、 物流控制、质量管理、成本控制、库存管理、现场管 理和现场改善等在内的较为完整的生产管理技术与方 法体系。
多品种 切换时间长, 对应 切换后不稳定
零 库存
发现 真正 问题Βιβλιοθήκη 降低 成本大量库存造成成 本高、周转困难 ,且看不到真正 的问题在哪里 “地下工厂”浪 费严重,似乎无 法发现、无法消 除
零 浪费
零目标 零 不良
目的 质量 保证
现
状
思考原则与方法 · 三不主义 · 零缺陷运动 · 工作质量 · 全员质量改善活动 · 自主研究活动 · 质量改善工具运用 · 效率管理 · TPM全面设备维护 · 故障分析与故障源对策 · 初期清扫与自主维护 · 同步化、均衡化 · 生产布局改善 · 设备小型化、专用化
丰田公司经营模式分析

丰田公司经营模式分析丰田公司是世界著名的汽车制造商,其经营模式值得深入分析。
以下是对丰田公司经营模式的分析。
1.质量第一:丰田公司一直以来以质量第一为原则。
丰田汽车以其出色的质量赢得了全球消费者的信任。
为了确保产品质量,丰田公司实施了严格的质量控制制度,包括从供应链开始到加工制造和交付给顾客的所有环节都经过了严格的质量检测。
因此,丰田汽车以其高品质而闻名于世。
2.丰田生产系统(TPS):丰田生产系统是丰田公司的核心竞争力之一,也被广泛称为“精益生产”。
该系统旨在提供高效的生产流程,消除浪费,并确保每个工作步骤都能增加价值。
丰田生产系统注重员工参与和持续改进。
每个员工都被鼓励提出改善建议来提高生产效率和质量。
3.客户导向:丰田公司一直致力于满足客户需求。
其开发汽车的初衷是为了提供性能卓越、安全可靠且经济高效的产品,以满足顾客的期望。
为了更好地了解客户需求,丰田公司积极与顾客互动,并收集顾客反馈进行产品改进。
4.研发创新:丰田公司积极投资于研发创新,以保持在汽车行业的领导地位。
公司持续不断地开展研究和开发,推出新技术和新产品。
丰田还与其他企业、大学和研究机构合作,进行合作研究和知识共享,以提高创新能力。
5.全球化战略:丰田公司在全球范围内推行全球化战略,通过在不同地区建立生产和销售网络,以满足当地市场需求。
丰田在多个国家建立了工厂,并在当地聘用本土员工,以更好地了解当地市场和文化,并满足当地客户的需求。
6.环保可持续发展:丰田公司一直努力推动环保可持续发展。
公司积极探索低碳和零排放技术,目标是减少对环境的负面影响。
丰田还提倡可持续供应链,鼓励供应商与公司一道努力,实现环境友好型的供应链。
7.员工培养和发展:丰田公司致力于以人为本,重视员工培养和发展。
通过持续培训和教育,丰田帮助员工不断提升技能和知识,以适应不断变化的市场需求。
此外,丰田还通过建立员工参与和反馈机制,激励员工的创新和改进意识。
综上所述,丰田公司的成功主要归功于其以质量第一为原则的经营模式、精益生产系统、客户导向、研发创新、全球化战略、环保可持续发展以及员工培养和发展。
浅析丰田精益管理模式的本质

理体系束缚技术、设备和人力的能力发挥” 理体系束缚技术、设备和人力的能力发挥”
效率驱动效益 ·
包容提速增长
丰田生产模式(TBS):
丰田生产方式(TPS) 丰田生产方式(TPS)已经成为全世界公认的先进管理模
式。“只要杜绝浪费,生产效率就有可能提高10倍。”
“彻底杜绝浪费”是TPS的基本思想,而贯穿其中的 彻底杜绝浪费” 两大支柱是:准时化和自働化。
效率驱动效益 ·
包容提速增长
二、精益管理中的---“流”
容易被忽视的- 时间流 时间流” 过程管理) 容易被忽视的-“时间流”(过程管理)
过程周期时间-----组织(协调)力 节拍时间------现场力 客户需求节拍----管理力
效率驱动效益 ·
包容提速增长
二、精益管理中的---“流”
“时间流”管理的不同结果: 时间流”管理的不同结果: 时间流
四、访日归来的思考:
对日本的民族纠结影响了几代人。 对日本的民族纠结影响了几代人。
矛盾的日本人: 唯物意识形态----信奉天皇(精神第一) 既谦卑----又好胜 国内倡导和谐----国外争霸强权 对生活的无限眷恋----厌世、悲观 ------------
效率驱动效益 ·
包容提速增长
四、访日归来的思考:
围绕这两大支柱的是TPS总结出的一系列独特的改善技术, 如“看板拉动”、“标准作业”和“造物既造人”等, TPS要求工人在细节上实现这种技术,提出了“持续改善” 的基础理念,最大程度消灭看得见的浪费;最大程度消灭 看不见的浪费。
效率驱动效益 ·
包容提速增长
丰田生产模式(TBS):
1985年,美国麻省理工学院国际汽车项目组织了 世界上14个国家的专家、学者,耗资500万美金, 对日本等国汽车工业的生产管理方式进行调查研 究后总结出来的生产方式,在日本称之为“丰田 生产方式”(TBS)也叫精益生产方式。
企业经营管理优秀实践案例:丰田模式14项原则
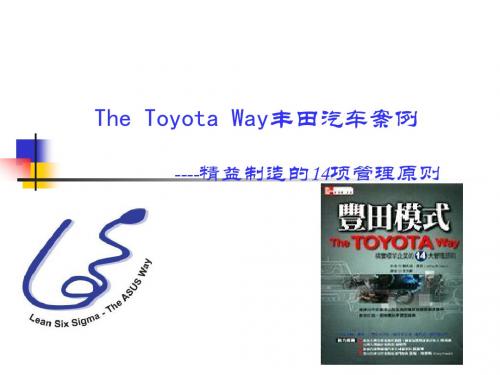
原则2:建立无间断的操作流程以使问题浮现
无间断的流程
所谓无间断的流程,是指当顾客下订单时,便会指示流程取得顾 客订单所需要的原材料,而且只是供应这笔订单所需要的原材 料数量,不多不少.接着,这些原材料将立即被输送至供货商工厂, 工人立刻加上零部件,然后输送至另一个工厂,由工人立即组装, 完成顾客订单所需要的产品,最后立即递给顾客. 整个流程只需花几个小时或数天,而不是几个星期或几个月.
第四类原则 持续解决根本问题是企业不断学习的驱动力
原则12: 亲临现场查看以彻底了解情况(现地现物) 原则13: 不急于作决策,以共识为基础,彻底考虑所有可能选择,并快速执 行决策 原则14: 通过不断省思与持续改进以变成一个学习型组织
第一类原则 长期理念
解决问题 (持续改进与学习) 员工与事业伙伴 (尊重他们、激励他们、 使他们成长) 流 程
原则6: 工作的标准化是持续改进与授权员工的基础
原则7: 运用视觉管理使问题无处隐藏 原则8: 使用可靠的、已经过充分测试的技术以协助员工及生产流程
目录
第三类原则 发展员工与事业伙伴,为组织创造价值
原则9: 把彻底了解且拥护公司理念的员工培养成为领导者,使他们能 教导其他员工 原则10: 培养与发展信奉公司理念的杰出人才与团队 原则11: 重视事业伙伴与供货商网络,激励并助其改进
原则1:管理决策以长期理念为基础 即使因此牺牲短期财务目标也在所不惜 丰田的使命陈述与指导原则
丰田真正的使命有3个部分
1. 对运营所在地国家(外部利害关系人)的经济成长作出贡献. 2. 对员工(内部利害关系人)的稳定与福祉作出贡献. 3. 对丰田公司的整体成长作出贡献.
丰田汽车公司的指导原则
2023年企业经营知识管理实践案例丰田管理模式

共同决策决策
共同决策是丰田管理模式的核心之一。在共同决策中,公司的决策不仅仅由高层管理层来做出,而是由各个层级的员工共同参与和贡献。
1. 充分听取员工意见丰田重视每个员工的意见和建议,在制定重要决策时充分听取员工的意见。通过设立各种沟通渠道和机制,公司鼓励员工提出自己的想法和改进建议。这种开放式的决策模式使得员工感到被尊重和重视,并促进了更好地集思广益。
激发员工参与
开放沟通渠道
丰田管理模式
创新意识
培训和发展
员工参与
激励机制
1.丰田管理模式:培养员工创造力和自主性丰田管理模式注重培养员工创造力和自主性。丰田鼓励员工参与问题解决和改进流程的决策过程,通过全员参与的方式激发员工的创新能力。2.丰田:信任与资源驱动员工创新,推动持续改进与创新通过信任员工的创新想法和提供相应的资源支持,丰田有效地激发并发掘员工的潜力,从而推动公司持续改进和创新。
2. 提升员工的满意度和归属感:让员工参与决策意味着给予他们发言权和权力,从而满足他们的参与需求,增强员工的归属感和满意度,有利于员工的持续发展和稳定性。
优化组织决策过程:员工参与决策能够促进信息共享和沟通,减少汇报层级和决策过程中的不必要环节,提高决策效率和灵活性。
提倡员工参与决策的必要性
员工参与决策的实施效果
2023/8/7
Introduction to Toyota Management Mode
丰田管理模式简介
沉默之建
The Construction of Silence TEAM
Contents
Toyota participates in employee decision-making
丰田参与员工决策
丰田经营模式的思考概述

丰田经营模式的思考概述丰田是一家全球知名的汽车制造公司,以其独特的经营模式而闻名。
该模式被称为“丰田生产方式”(Toyota Production System),是丰田汽车成功的关键之一。
这种模式的核心思想是通过优化生产流程、减少浪费和提高效率来实现持续改进。
以下是对丰田经营模式的几点思考概述。
首先,丰田经营模式注重质量管理。
丰田始终以提供高质量的产品为目标,通过严格的质量控制和持续改进来实现这一目标。
丰田通过追求客户的满意度,持续改进产品和服务,为消费者提供可靠的汽车。
其次,丰田经营模式强调团队合作和员工参与。
团队合作是丰田成功的关键之一。
丰田鼓励员工积极参与决策制定和问题解决过程,在生产线上形成了高效的团队合作氛围。
每个员工都被激励去发现问题并提出改进的建议,从而不断为丰田的持续改进做出贡献。
此外,丰田经营模式注重流程优化和精益生产。
丰田致力于减少浪费,通过精确计划、流程标准化和自动化实现高效的生产。
丰田的生产线被设计成可以灵活适应变化,并及时发现和解决问题,以避免生产中断。
最后,丰田经营模式强调持续改进和学习。
丰田的经营理念是“挑战、改进、创新”。
丰田认为,持续改进是实现卓越的关键。
丰田鼓励员工从失败中学习,并找到改进的机会。
这种不断学习和改进的文化使得丰田能够不断适应市场变化和客户需求,并在汽车行业中保持竞争优势。
总之,丰田的经营模式以其独特的质量管理、团队合作、流程优化和持续改进的理念为基础,使其成为全球汽车行业的佼佼者。
丰田的成功证明了这种经营模式的有效性,并提供了灵感和启示给其他企业。
通过借鉴和应用丰田的经营模式,其他企业可以实现质量提升、效率提升和持续创新,从而在竞争激烈的市场中获得成功。
丰田经营模式是丰田汽车公司在多年的实践和经验中形成的,它不仅是丰田汽车制造过程的一个重要组成部分,也是丰田成功的关键之一。
这种经营模式也被广泛应用于其他行业,成为一个值得学习和借鉴的范例。
丰田经营模式的核心理念是消除浪费和不断改进。
- 1、下载文档前请自行甄别文档内容的完整性,平台不提供额外的编辑、内容补充、找答案等附加服务。
- 2、"仅部分预览"的文档,不可在线预览部分如存在完整性等问题,可反馈申请退款(可完整预览的文档不适用该条件!)。
- 3、如文档侵犯您的权益,请联系客服反馈,我们会尽快为您处理(人工客服工作时间:9:00-18:30)。
第一章以卓越的操作流程为战略性武器丰田汽车公司最早引起世界注目的是在20世纪80年代,当时情况明显显示,日本企业及其产品的品质和效率确有独到之处,日本制造的汽车比美国汽车耐用,需要的维修明显较少。
到了20世纪90年代,更明显的迹象显示,相较于其他日本汽车制造商,丰田汽车公司显然更特别、突出。
这并非指它的汽车设计或性能令人赞叹(尽管这是事实,丰田车开起来流畅顺手,其设计也多半非常精致),而是丰田汽车的工程与制造模式实现了令人难以置信的流程与产品的一致性。
丰田的汽车设计更快速,可靠性更高,同时,即使在日本汽车业劳动力工资水准相对较高的情况下,丰田仍然得以维修极具竞争力的汽车制造成本。
令人印象深刻的另一点是,每当丰田出现明显弱点、似乎将不敌竞争时,它总是能奇迹般地解决问题,并且以更强壮之势卷土重来。
今天,丰田已是全球第二大汽车制造商,仅次于通用汽车公司,在全球170个国家的年汽车销售量超过600万辆,但是,丰田比全世界任何汽车制造商都要赚钱。
汽车业分析师预估,若以现在的趋势持续下去,丰田汽车的全球销售量最终会超越通用汽车,而成为全世界最大的汽车制造商。
丰田的成功主要源自其卓著的品质声誉。
消费者知道他们可以信赖丰田汽车,不论新购或使用了一段期间,其性能都很可靠,不像大多数美国或欧洲制造的汽车,新购买期间的性能大概还不错,但是,大约开了1年左右,就开始出现大大小小的毛病,得进厂修理了。
以2003年为例,丰田汽车在美国市场的召回率比福特汽车少79%,比克莱斯勒汽车少92%。
汽车购买者最常阅读的杂志之一《消费者报告》于2003年进行过一项研究,从过去7年所有汽车制造商生产的车款中,评选出最值得信赖的38款车,其中,丰田/凌志就囊括了15款车,没有一家汽车制造商可与之匹敌,通用汽车、奔驰、宝台等,没有一款车跻身这38名之列。
在同一份研究调查中,丰田没有一款车被列入“应该避免购买”的名单中,福特汽车有不少车款被列入此黑名单,通用汽车公司出厂的车款中有将近10%入选,克莱斯勒车款被归属此类者更是超过3%。
成功的秘诀:丰田DNA的双螺旋到底丰田的成功秘诀是什么呢?丰田能够持续缔造如此辉煌的成就,是卓越的操作流程所创造的直接成果,丰田已经把操作流程的卓越性变成其战略性武器。
这种操作流程的卓越性,其部分基础在于丰田闻名制造业界的工具及品质改善方法,包括准时生产(just-time)、持续改进(kaizen)、“一个流”(one-piece flow)、自动化(jidoka)、生产均衡化(heijunka)等,这些生产技巧孕育了“精益制造”(lean manufacturing)革命。
但是,工具与技巧并不是使企业变革成功的秘密武器。
丰田之所以能持续成功地运用这些工具与技巧,必须归功于公司以了解与激励员工为基础的企业经营理念。
换句话说,丰田的成功根源在于,它能培养领导力、团队与文化,而且它能制定有效策略,建立坚实的供货商关系,以及打造并维持一个学习型企业。
把这14项原则区分成4大类,全都以P这个字母开头——理念(Philosophy)、流程(process)、员工/事业伙伴(people/partners)、解决问题(problem solving),。
,最终,我们也采纳了此文件中所提出的4项高级原则——现地现物(Genchi Genbutsu)、持续改进(kaizen)、尊重与团队合作、挑战,并把它们与我的4个分类相结合。
丰田模式和丰田生产方式(丰田的制造方法)是丰田公司DNA的双螺旋,它们共同定义了管理作风,以及该公司的特色。
我希望通过此书阐释说明,丰田的成功模式可以如何应用于其他企业,以改善从销售到产品发展、营销、物流作业与管理等的企业流程。
为帮助读者理解,我在书中列举了许多例子,说明丰田公司如何维持如此优异的成就,也探讨了其他产业与服务业的公司如何有效应用丰田模式的原则。
丰田生产方式与精益生产丰田生产方式是丰田公司独特的制造方法,它是精益生产行动的主要基础,而精益生产和六西格玛是过去十几年制造业流程的主流方法。
虽然精益生产的影响力极大,但我希望在此书中说明的是,大多数企业在应用此方法时的做法相当肤浅,因为它们过度着重工具(例如“5S”法和准时生产),不了解完整的精益生产方式必须渗透至企业文化中。
大多数实施精益生产的公司,其资深管理层并未参与日常的运营作业与持续改进行动,而这些都是精益生产方式中极重要的部分,丰田公司本身实施此方式的做法非常不同于一般企业。
精益的企业到底是怎样的面貌呢?我们或许可以说,精益的企业是把丰田生产方式应用于企业所有层面所获得的结果。
詹姆斯·沃麦克(James Womack)和丹尼尔·琼斯(Daniel Jones)在他们精辟的著作《精益思维》中把“精益制造”定义为包含5个步骤的流程:定义顾客的价值(customer value)、定义价值流程(value stream)、建立无间断的操作流程(flow)、拉式(Pulling)生产制度、努力追求卓越。
欲成为一个精益的制造业者,思维模式必须着重使用产品的生产变成无间断(亦即“一个流”)的有加值效应有流程;采取根据顾客需求而决定生产量的拉式生产制度——亦即前一个制造流程只生产补充下一个制造流程在短期内要邻取的材料或零部件;同时,打造一个人竭力追求持续改进的公司文化。
丰田生产方式发明者之一大野耐一的阐述更简洁:我们所做的,其实就是注意从接到顾客订单向顾客收账这期间的作业时间,由此剔除不能创造价值的浪费,以缩短作业时间。
在迈入21世纪后,丰田在全球市场的成功基础依然是着重无间断的操作流程。
还有不少公司,也以缩短前置期、提高存货周转率、快速收账等特色实现快速成长而闻名。
戴尔计算机就是一个例子,但是,就连戴尔计算机也还是刚踏上通往精益企业之路,而丰田却已经在这条路上学习与努力了几十年。
不幸的是,多数公司迄今仍然使用亨利·福特于1920年发明的大规模生产的方法。
在那个年代,灵活弹性与提供顾客更多选择并不重要,大规模生产注重的是个别流程的效率,此概念可追溯到20世纪弗雷德里克·泰勒(Frederick Taylor)及其科学管理。
和丰田生产方式的发明者一样,泰勒也试图去除生产流程中的浪费,他仔细观察工作者,设法除掉每一个缺乏效率的动作。
倡导大规模生产方法的思维者认为,机器的停转是另一种未能创造价值的明显浪费——机器因为维修而停工时,就不能生产零部件,从而也就无法赚钱。
可是,让我们来看看丰田生产方式对于未能创造价值之浪费有不同于一般直觉的下列看法:●许多情况下,最佳做法是让机器停工,不生产材料或零部件。
因为,这么做可避免生产过剩,在丰田生产方式中,这种情形是最根本的浪费。
●通常,最好建立最终成品的某一存货水准,以维持平稳的生产进度而不是根据实际顾客订单的需要波动来生产。
维持平衡的生产进度(生产均衡化)是无间断流程与拉式生产制度的基础,并有助于使供应链的存货降至最低水准(生产均衡化指维持平衡均匀的生产项目的数量与组合,使每天的生产不致有明显流动与变异)。
●通常,最好选择性地增加间接成本,并之取代直接劳动成本。
当你把创造价值的员工中之浪费情形除去时,你必须对工作者提供高品质的支持,就像在重大手术中为外科医生提供支持样。
●让人铁员工忙碌于尽可能快速地生产原材料或零部件,并不一定是最佳做法。
你应该根据顾客的需求量来生产材料或零部件,若只是为了用尽员工的生产力而快速生产,只会造成另一种形式的生产过剩,且会导致雇用过多的劳动力。
●最好能选择性地使用信息技术,而且在许多时候,纵使可以采取自动化,以降低劳动力人数与成本,最好还是使用人工流程。
人是最具弹性的资源,如果你未能了解人工流程并使之变得有效率,就无法知道流程的哪些部分需要自动化以作为支持。
换言之,丰田对某些问题的解决方法,往往看似增加浪费,而非杜绝,这些看似矛盾的解决方法得自大野耐一亲自观察工厂作业后,对于“未能创造价值的浪费”所获得的特殊发现:它和充分运用劳动力与机器设备没有太大关联,主要源于把原材料转化成可销售的商品的流程。
大野耐一亲自观察工厂作业的目的,是为了找出可以为原材料增加附加价值的活动,不能创造附加价值的活动则予以摒除。
通过此观察学习之旅,他学会了绘制价值流程图——从原材料转化成顾客愿意付钱购买的最终产品。
这是一个完全不同于大规模生产的方法,大规模生产的方法只是从现有的生产流程中找出、列举与排除浪费的时间与工作。
第二章全球最杰出的制造商:丰田家庭与丰田生产方式我打算尽可能地缩减工作流程,以及输送零件、材料流程中的松散时间,为实现计划,基本原则是采取准时生产制度,指导原则是不要太早或太晚输送货品。
——丰田汽车公司创办人丰田喜一郎,1938年在丰田公司追求卓越的路上,最引人注目的产物是其制造理念,一般称之为丰田生产方式。
此生产方式是继亨利·福特发明的大规模生产方式后,第二次改进企业流程效率的重大变革,它被详细记载、分析,并传递至全世界各产业公司。
在丰田公司以外,丰田生产方式经常被称为精益或精益生产,因为以下两本畅销书使用这两个名词而使其变得家喻户晓:《改变世界的企业经营体制:精僧生产的故事》、《精益思维》。
不过,这两本书的作者非常明确地强调,他们对于精益生产的研究,是以丰田生产方式及丰田公司对此方式的发展为基础。
尽管丰田公司现在全球各地总计有超过24万名员工,但就许多方面而言,它依旧是一个大型的家族企业,创办该公司的丰田家族仍然对该公司有相当大的影响力。
为了解丰田生产方式与丰田模式,以及该公司如何发展成为全世界最优秀的制造业者,我们首先应该了解创办该公司的家族成员的历史与个性,因为丰田家族对丰田公司文化留下了持久的影响。
最重要的不是某家族的掌控(福特汽车公司在这方面也是类似情况),而是丰田在其整部历史中实施了非常一致的领导与管理理念。
丰田模式中所有原则的根源皆可追溯至该公司创始之初,丰田的每一位领导者,不论是不是丰田家庭成员,都融入了丰田模式的DNA。
丰田家族:代代都展现一致的领导风格丰田家族的故事始于丰田佐吉(Sakichi Toyoda),他擅长修修补补,也是发明家,其出身背景和亨利·福特相仿,成长于19世纪末期日本名古屋郊外一个偏僻的农村。
在当时的日本,织布是主要产业,日本政府为了促进小型企业的发展,鼓励全日本各地创立家庭工业,于是雇用少数员工的小型工作坊与工厂随处可见,家庭主妇普遍到附近的作坊或在家里工作,以赚取微薄工资贴补家用。
丰田佐吉从小就跟着父亲学习木工,后来,他把这项技艺应用到设计与建造织布机上。
1894年,他开始制造更全家,但性能更佳的手动织布机。
丰田佐吉对他改良的织布机感到满意,但是,看到母亲、祖母和他们的朋友们仍然必须非常辛苦地转动织布机,令他感到难过。