认识浪费与效率PPT(共 34张)
合集下载
精益生产的效率与七大浪费(ppt 17页)
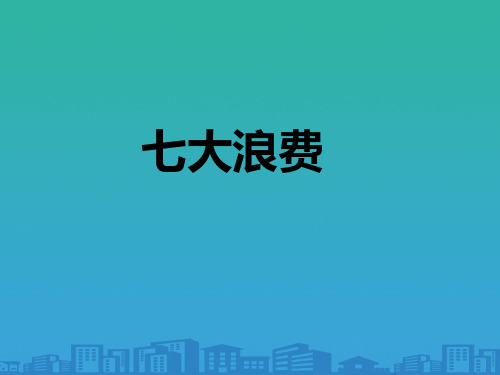
七大浪费
目录
1. 精益生产的效率 2. 浪费的定义 3. 七大浪费 4. 动作研究
精益生产的效率
传统的效率 • 简单化 • 高速大量生产
精益生产的效率: • 消除浪费
-- 库存/等待 -- 搬运 -- 摆放
生产过剩是 最大的浪费
浪费
• 浪费是指那些导致成本增加的因素 • 虽然增加价值,但耗用资源过高
2. 过量生产浪费
1. 超出下一操作的需求量 2. 提前生产下一操作的需求 3. 设备速度过快
3. 过分加工浪费
1. 超出/低于产品特定需求的精度 2. 多余的作业项目
质量成本概念
4. 搬运浪费
• 也就是说“每个工位都从手工操作开始”.
-- 找到、拿起、移动,用手放,然后
-- 从手推车移到货板
-- 从货仓到工厂
-- 从工厂到生产线 -- 从生产线到机械化车间
讨论: 自动化搬运的误区
-- 从机械化车间到操作工位
5. 库存浪費
• 存货过多 -- 过多的原材料 • 交货周期过长? • 错误的订货量? -- 过多的成品 • 是因为生产过剩? • 是因为生产排期错误?
6. 移動浪費
1. 动作太大 2. 单手空闲 3. 转身动作过大 4. 操作动作不流畅 5. 重复/不必要的动作 6. 不必要的弯腰动作
2.关于操作场所布置:
(9)工具物料应放于固定处。 (10)工具物料及装置应布置于工作者之前面近处。 (11)零件物料之供给,应利用其重量堕至工作者手边。 (12)[堕送]方法应尽可能利用之。 (13)工具物料应依照最佳之工作顺序排列。 (14)应有适当之照明设备,使视觉满意舒适。 (15)工作台及椅之高度,应使工作者坐立适宜。 (16)工作椅式样及高度,应可使工作者保持良好的姿势。
目录
1. 精益生产的效率 2. 浪费的定义 3. 七大浪费 4. 动作研究
精益生产的效率
传统的效率 • 简单化 • 高速大量生产
精益生产的效率: • 消除浪费
-- 库存/等待 -- 搬运 -- 摆放
生产过剩是 最大的浪费
浪费
• 浪费是指那些导致成本增加的因素 • 虽然增加价值,但耗用资源过高
2. 过量生产浪费
1. 超出下一操作的需求量 2. 提前生产下一操作的需求 3. 设备速度过快
3. 过分加工浪费
1. 超出/低于产品特定需求的精度 2. 多余的作业项目
质量成本概念
4. 搬运浪费
• 也就是说“每个工位都从手工操作开始”.
-- 找到、拿起、移动,用手放,然后
-- 从手推车移到货板
-- 从货仓到工厂
-- 从工厂到生产线 -- 从生产线到机械化车间
讨论: 自动化搬运的误区
-- 从机械化车间到操作工位
5. 库存浪費
• 存货过多 -- 过多的原材料 • 交货周期过长? • 错误的订货量? -- 过多的成品 • 是因为生产过剩? • 是因为生产排期错误?
6. 移動浪費
1. 动作太大 2. 单手空闲 3. 转身动作过大 4. 操作动作不流畅 5. 重复/不必要的动作 6. 不必要的弯腰动作
2.关于操作场所布置:
(9)工具物料应放于固定处。 (10)工具物料及装置应布置于工作者之前面近处。 (11)零件物料之供给,应利用其重量堕至工作者手边。 (12)[堕送]方法应尽可能利用之。 (13)工具物料应依照最佳之工作顺序排列。 (14)应有适当之照明设备,使视觉满意舒适。 (15)工作台及椅之高度,应使工作者坐立适宜。 (16)工作椅式样及高度,应可使工作者保持良好的姿势。
2019【培训课件】认识浪费与效率
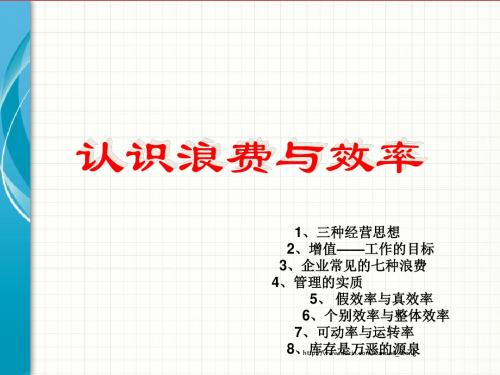
CWMC 国慧顾问
等 待 浪费
等待不创造价值
常见的等待现象: ☆ 物料供应或前工序能力不足造成待料 ☆ 监视设备作业造成员工作业停顿 ☆ 设备故障造成生产停滞 ☆ 质量问题造成停工 ☆ 型号切换造成生产停顿 造成等待的常见原因: ☆ 线能力不平衡 ☆ 计划不合理 ☆ 设备维护不到位 ☆ 物料供应不及时
cost
成本C:通过有效管理, 把顾客的负担降到最低程度
通过高成本力减小顾客负担;通过 提高技术含量和服务质量来提高对顾客 的附加价值。
/sundae_meng
CWMC 国慧顾问
delivery
交货期D:抓住时机, 即时满足顾客需要 足够短的生产周期;按时交货,瞬 时响应市场。
/sundae_meng
CWMC 国慧顾问
3、企业常见的八种浪费
国内企业之大现状: ☆ 现场混乱,插不进脚 ☆ 员工仪容不整,两眼无光 ☆ 物料混放,标识不清 ☆ 设备故障不段,苟延残喘 ☆ 人海战术,加班加点但还是要待工待料
/sundae_meng
/sundae_meng
CWMC 国慧顾问
4、管理的实质
创造性的管理活动 提高产品和服务的附加价值
+1 0
-1
增加价值 消除浪费
最大限度地减少不增值劳动 封闭性的管理活动
/sundae_meng
CWMC 国慧顾问
关于“
/sundae_meng
CWMC 国慧顾问
6、个别效率与整体效率
例
能力需求:100件/H
项 能
目 力
工序1 100件/H 100% 标准产量奖金 个别效率合格
工序2 125件/H 125% 125%奖金 个别效率高
工序3 80件/H 80% 0 个别效率低
认识浪费与效率(PPT 34页)
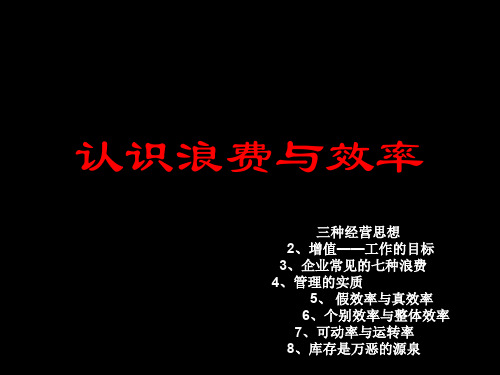
工序3 80件/H
80% 0
个别效率低
工序4 100件/H
80% 0
个别效率低
≠ 个别效率
整体效率
专业化作业有利于提高个别效率,不少企 业因此实行计件工资。
但是,效率追求的重点应该是关注【整体 效率】,这对企业才有创造利润的实际意义。
所以,有必要将奖励个别效率的企业行为 转变为奖励整体效率,如:计件工资以完成品 (而非半成品)为标准,实行团队计件。
2、增值——工作的目标
利润 实现
企业的使命实践
市场 需求
企业 管理
产品 实现
顾客 满意
$
增值
工作的根本目的是给产品和服务 增加价值。
一切不增加对顾客和企业价值的 活动都是浪费。
3、企业常见的八种浪费
国内企业之大现状: ☆ 现场混乱,插不进脚
☆ 员工仪容不整,两眼无光 ☆ 物料混放,标识不清
☆ 设备故障不段,苟延残喘 ☆ 人海战术,加班加点但还是要待工待料
可动率与设备的保养状态息息相关。设备 故障、设备调整、机型切换等都将降低设备可 动率。
例
出勤时间
8×2=16H
一天故障
2H
设备调整
1H
设备可动时间
13H
——————————————
设备可动率 13÷16=81.25%
★ 有必要减少设备故障和调整时间, 以提高设备可动率
运转率并非越高越好
设备1
设备2
省人化的两种形式: ☆ 正式工 + 季节工 / 临时工(变动用工) ☆ 固定人员 + 公用人员(弹性作业人员)
6、个别效率与整体效率
例 能力需求:100件/H
项目 能力 达成率 奖金 效率
浪费的识别与消除ppt课件

纠正的浪费
原因:
. 过程能力不足 . 过大的变差 . 供应商能力不足 . 操作工控制失误 . 管理层的决策 . 缺乏培训 . 不适当的工装/设备 . 车间布置差/不必要的搬运 . 高的存货水平
资金是运动的价值,资金的价值是随 时间变 化而变 化的, 是时间 的函数 ,随时 间的推 移而增 值,其 增值的 这部分 资金就 是原有 资金的 时间价 值
资金是运动的价值,资金的价值是随 时间变 化而变 化的, 是时间 的函数 ,随时 间的推 移而增 值,其 增值的 这部分 资金就 是原有 资金的 时间价 值
过程能力演示
资金是运动的价值,资金的价值是随 时间变 化而变 化的, 是时间 的函数 ,随时 间的推 移而增 值,其 增值的 这部分 资金就 是原有 资金的 时间价 值
是指两个相互依赖的变量不 完全同步所造成的空闲时间
资金是运动的价值,资金的价值是随 时间变 化而变 化的, 是时间 的函数 ,随时 间的推 移而增 值,其 增值的 这部分 资金就 是原有 资金的 时间价 值
等待造成的浪费
特点:
– People Waiting for Machine人等机器 – Machine Waiting for People机器等人 – People Waiting for People人等人 – Unbalanced Operations (Work)不平衡的操作 – Lack of Concern for Equipment Breakdowns 对设备故障漠不关心 – Unplanned Equipment Downtime 计划外的停机
存货的浪费
特点:
– Stagnated Material Flow 停滞的物料流 – FISH instead of FIFO“先进后出” 取代“先 进先出”
《JIT》系列课程之二认识浪费与效率
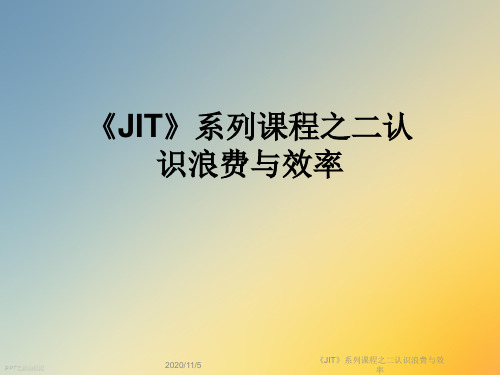
PPT文档演模板
《JIT》系列课程之二认识浪费与效 率
•CWMC 国慧顾问
•提要
• 1960年代开始,以丰田为代表的日本汽车制 造业通过实施JIT生产模式,以低成本、高质量的突 出优势迅速占领美国汽车市场,引发了美日之间长 达十年的汽车贸易战。JIT——因其经营效率极限化 被美国学者赞誉为“精益生产”,并对人类的生产 革命产生了长远影响。
•擅长业务:◎企业运营系统改善
•
· 现场管理
•
· 质量管理
•
· 生产管理
•
· 价值工程
•
◎企业中层干部培养
•工作外语:日语
《JIT》系列课程之二认识浪费与效 率
•CWMC 国慧顾问
•【讲师简介】
•
陈祖林
•服务过的部分客户: • 松下电器、IBM、东莞山一(日) • 富士工具(日)、富士电机(日) • 浦金钢板(韩)、生益电子(港) • 美的空调、新飞电器、华凌空调 • 万宝集团、顺威电器、新宝电器 • 恒达实业、深圳曼妮芬、德赛集团 • 惠州邮电工程、美涂士集团……
•5、拒绝干扰(非紧急情况下,
•
请勿接受干扰)。
•6、禁止在课室内吸烟。
•小憩及用餐后请准时回到课室 •切勿流连忘返
《JIT》系列课程之二认识浪费与效 率
•CWMC 国慧顾问
1 •第 日
PPT文档演模板
9:00~ 9:20 9:20~10:50 10:50~11:30 11:30~12:00 12:00~14:00 14:00~14:40 14:40~15:40 15:40~17:10
•练习5 空中耐力 •练习6 空中蜕变 •练习7 钎焊的烦恼
《JIT》系列课程之二认识浪费与效 率
认识浪费与消除浪费PPT课件

为什幺安排在这些部门做?)
在何时做?(这些工作在流程上处于第几道工序?
何时开始?何时结束?为什幺在这个时间做?)
由谁做?(这些工作分别是由谁来完成的?为什幺
安排这些人来做?)
怎幺做?(这些工作分别是用什幺方法,采用了何
种工具和设备完成的?为什幺要用这样的方法做?)
运用“5W1H”提问技术可以发现哪些问题?
70 第一季度 第二季度 第三季度 第四季度
通过实际值与目标值的差异发现问题点
140000
120000
100000 98000 90000
80000
100000
110000 90000
120000 80000
60000 40000 20000
实际销量 目标销量
0 第一季度
第二季度
第三季度
第四季度
通过本企业与主要竞争对手的比较发现问题点
一、认识浪费
精益管理的核心
彻底消除无效劳动与浪费
实施精益管理,必须从消除一切无效劳动与浪费开始。
(一)什么是无效劳动与浪费?
无效劳动与浪费:消耗了资源,增加了成本,但是没有 创造价值(或使附加值增加)的一切活动;也包括虽然创造 了价值,但耗费资源过高的工作。
浪费的表现
(二)无效劳动与浪费的表现
日本丰田汽车公司归纳为以下7种:
★ 与目标比较(计划进度、目标成本、预算、其他各种
目标值)
★ 与标杆比较(标杆企业、竞争对手)
★ 与历史比较(历史同期、历史最好)
★ 所得与耗费比较(耗费的人力、资金、设备、能源、
材料、时间等)
通过实际值与目标值的差异发现问题点
105
100
95
90
在何时做?(这些工作在流程上处于第几道工序?
何时开始?何时结束?为什幺在这个时间做?)
由谁做?(这些工作分别是由谁来完成的?为什幺
安排这些人来做?)
怎幺做?(这些工作分别是用什幺方法,采用了何
种工具和设备完成的?为什幺要用这样的方法做?)
运用“5W1H”提问技术可以发现哪些问题?
70 第一季度 第二季度 第三季度 第四季度
通过实际值与目标值的差异发现问题点
140000
120000
100000 98000 90000
80000
100000
110000 90000
120000 80000
60000 40000 20000
实际销量 目标销量
0 第一季度
第二季度
第三季度
第四季度
通过本企业与主要竞争对手的比较发现问题点
一、认识浪费
精益管理的核心
彻底消除无效劳动与浪费
实施精益管理,必须从消除一切无效劳动与浪费开始。
(一)什么是无效劳动与浪费?
无效劳动与浪费:消耗了资源,增加了成本,但是没有 创造价值(或使附加值增加)的一切活动;也包括虽然创造 了价值,但耗费资源过高的工作。
浪费的表现
(二)无效劳动与浪费的表现
日本丰田汽车公司归纳为以下7种:
★ 与目标比较(计划进度、目标成本、预算、其他各种
目标值)
★ 与标杆比较(标杆企业、竞争对手)
★ 与历史比较(历史同期、历史最好)
★ 所得与耗费比较(耗费的人力、资金、设备、能源、
材料、时间等)
通过实际值与目标值的差异发现问题点
105
100
95
90
相关主题
- 1、下载文档前请自行甄别文档内容的完整性,平台不提供额外的编辑、内容补充、找答案等附加服务。
- 2、"仅部分预览"的文档,不可在线预览部分如存在完整性等问题,可反馈申请退款(可完整预览的文档不适用该条件!)。
- 3、如文档侵犯您的权益,请联系客服反馈,我们会尽快为您处理(人工客服工作时间:9:00-18:30)。
☆ 监视设备作业造成员工作业停顿 ☆ 设备故障造成生产停滞 ☆ 质量问题造成停工 ☆ 型号切换造成生产停顿
造成等待的常见原因: ☆ 线能力不平衡
☆ 计划不合理 ☆ 设备维护不到位 ☆ 物料供应不及时
搬运浪 费
移动费时费力
空间、时间、人力和工具浪费 搬运过程中的放置、堆积、移
动、整理等都造成浪费。
浪费
2、增值——工作的目标
利润 实现
企业的使命实践
市场 需求
企业 管理
产品 实现
顾客 满意
$
增值
工作的根本目的是给产品和服务 增加价值。
一切不增加对顾客和企业价值的 活动都是浪费。
3、企业常见的八种浪费
国内企业之大现状: ☆ 现场混乱,插不进脚
☆ 员工仪容不整,两眼无光 ☆ 物料混放,标识不清
☆ 设备故障不段,苟延残喘 ☆ 人海战术,加班加点但还是要待工待料
缺货 损失
缺货造成机会损失
由于各种浪费消耗了企业资源, 降低了经营效率,反过来制约企业 的订单履行,造成缺货损失:
☆ 紧急订单造成额外成本 ☆ 延迟订单造成额外成本 ☆ 订单取消造成利润损失 ☆ 客户流失造成市场机会损失
4、管理的实质
创造性的管理活动 提高产品和服务的附加价值
+1 增加价值
0
-1
消除浪费
最大限度地减少不增值劳动 封闭性的管理活动
重要
关于“
”的两个问题
☆ 对提高顾客满意度 有帮助吗? 有损害吗?
☆ 对提高企业效益 有帮助吗? 有损害吗?
5、 假效率与真效率
例:市场需求100件/天
10个人1天 生产
100件产品
10个人1天 生产
120件产品
假效率
8个人1天 生产
100件产品
工序3 80件/H
80% 0
个别效率低
工序4 100件/H
80% 0
个别效率低
≠ 个别效率
整体效率
专业化作业有利于提高个别效率,不少企 业因此实行计件工资。
但是,效率追求的重点应该是关注【整体 效率】,这对企业才有创造利润的实际意义。
所以,有必要将奖励个别效率的企业行为 转变为奖励整体效率,如:计件工资以完成品 (而非半成品)为标准,实行团队计件。
还应该以提高整体效率为目标,改善生产 线的布局,如:将水平布置和离岛式布置调整 为流线式布置,这样有利于团队协作。
库存的危害: ☆ 额外的搬运储存成本
☆ 造成空间浪费 ☆ 资金占用(利息及回报损失) ☆ 物料价值衰减 ☆ 造成呆料废料 ☆ 造成先进先出作业困难 ☆ 掩盖问题,造成假象
制造过多/过早
浪费
违背JIT原则
制造过多/过早造成浪费: ☆ 造成在库
☆ 计划外/提早消耗 ☆ 有变成滞留在库的风险 ☆ 降低应对变化的能力
不良造成额外成本
常见的等待现象: ☆ 材料损失
☆ 设备折旧 ☆ 人工损失 ☆ 能源损失 ☆ 价格损失
☆ 订单损失 ☆ 信誉损失
动作
浪费
多余动作 增加强度降低效率
常见的12种浪费动作:
① 两手空闲
⑦ 转身角度大
② 单手空闲
⑧ 移动中变换动作
③ 作业动作停止 ⑨ 未掌握作业技巧
④ 动作幅度过大 ⑩ 伸背动作
认识浪费与效率
1、三种经营思想 2、增值——工作的目标 3、企业常见的七种浪费 4、管理的实质
5、 假效率与真效率 6、个别效率与整体效率 7、可动率与运转率 8、库存是万恶的源泉
1、三种经营思想
成本中心思想 售价=成本+利润
售价中心思想 利润=售价-成本
利润中心思想 成本=售价-利润
根据成本和计划利润 决定售价
以顾客为起 点的经营
供应商
顾客
顾客满意五要素
顾客
Q
满意
F
C DS
Q
quality
质量Q:站在顾客立场, 制造令顾客称心满意的产品
以产品和服务为媒体完全实现 对顾客之承诺。
C
cost
成本C:通过有效管理, 把顾客的负担降到最低程度
通过高成本力减小顾客负担;通过 提高技术含量和服务质量来提高对顾客 的附加价值。
仅适用于卖方市场
利润根据售价变动 属于被动利润型
根据售价变化 主动降低成本
企业使命及其实践
为世界 作贡献
创造利润 达成经营目标
为顾客创造价值 使顾客满意
企业存在的最直接目 的就是生产金钱。为世界 作贡献是企业的共同理念!
生产、质量、 安全、成本等各项经营活动
现代市场竞争 已经由企业之间的竞争 转变为供应链之间的竞争
等待浪费
搬运浪费
工 8 不良浪费
厂 大 动作浪费
浪 常
见
加工浪费
的 费 库存浪费
地下工厂
企业每生产一件产品就在制 造一份浪费。伴随企业运营中各 业务环节不被察觉或不被重视的 浪费,日本企业管理界将之形象 地比喻为“地下工厂”。
制造过多(过早)浪费
缺货损失
等待 浪费
等待不创造价值
常见的等待现象: ☆ 物料供应或前工序能力不足造成待料
⑤ 左右手交换 ⑾ 弯腰动作
⑥ 步行多
⑿ 重复/不必要动作
加工 浪费
过剩的加工造成浪费
常见的加工浪费: ☆ 加ห้องสมุดไป่ตู้余量
☆ 过高的精度 ☆ 不必要的加工
过剩加工造成的浪费: ☆ 设备折旧 ☆ 人工损失
☆ 辅助材料损失 ☆ 能源消耗
库存 浪 费 库存造成额外成本
常见的库存: ☆ 原材料、零部件
☆ 半成品 ☆ 成品 ☆ 在制品 ☆ 辅助材料 ☆ 在途品
D
delivery
交货期D:抓住时机, 即时满足顾客需要
足够短的生产周期;按时交货,瞬 时响应市场。
S
safety
安全S:健康、安全、环保
绝对的安全卫生保证,遵守环保和 技术法规。
F
flexibility
柔性F:敏锐感觉市场,敏捷适应变化 预见性地满足顾客需要
倾听顾客的声音(VOC)。 应变力。 管理与技术创新力(领变力)。
真效率
假效率
固定的人员
真效率
最少的人员
生产出仅需的产品
生产出更多的产品
能力提升是效率的基础。 但效率建立在有效需求的基础 上,以【是否创造利润】为标 准;如果不创造效益甚至造成 在库,则此种效率是假效率。
假效率 真效率
能力 提升
【效率建立在有效需求的基础上】 能力提升是效率提升的基础。但有时能力 提升会造成效率提升的假象。 管理者的责任就是在能力提升的基础上, 将假效率转化成真效率。 所以,“省人化”是效率的关键。
省人化的两种形式: ☆ 正式工 + 季节工 / 临时工(变动用工) ☆ 固定人员 + 公用人员(弹性作业人员)
6、个别效率与整体效率
例 能力需求:100件/H
项目 能力 达成率 奖金 效率
工序1 100件/H
100% 标准产量奖金 个别效率合格
工序2 125件/H
125% 125%奖金 个别效率高
造成等待的常见原因: ☆ 线能力不平衡
☆ 计划不合理 ☆ 设备维护不到位 ☆ 物料供应不及时
搬运浪 费
移动费时费力
空间、时间、人力和工具浪费 搬运过程中的放置、堆积、移
动、整理等都造成浪费。
浪费
2、增值——工作的目标
利润 实现
企业的使命实践
市场 需求
企业 管理
产品 实现
顾客 满意
$
增值
工作的根本目的是给产品和服务 增加价值。
一切不增加对顾客和企业价值的 活动都是浪费。
3、企业常见的八种浪费
国内企业之大现状: ☆ 现场混乱,插不进脚
☆ 员工仪容不整,两眼无光 ☆ 物料混放,标识不清
☆ 设备故障不段,苟延残喘 ☆ 人海战术,加班加点但还是要待工待料
缺货 损失
缺货造成机会损失
由于各种浪费消耗了企业资源, 降低了经营效率,反过来制约企业 的订单履行,造成缺货损失:
☆ 紧急订单造成额外成本 ☆ 延迟订单造成额外成本 ☆ 订单取消造成利润损失 ☆ 客户流失造成市场机会损失
4、管理的实质
创造性的管理活动 提高产品和服务的附加价值
+1 增加价值
0
-1
消除浪费
最大限度地减少不增值劳动 封闭性的管理活动
重要
关于“
”的两个问题
☆ 对提高顾客满意度 有帮助吗? 有损害吗?
☆ 对提高企业效益 有帮助吗? 有损害吗?
5、 假效率与真效率
例:市场需求100件/天
10个人1天 生产
100件产品
10个人1天 生产
120件产品
假效率
8个人1天 生产
100件产品
工序3 80件/H
80% 0
个别效率低
工序4 100件/H
80% 0
个别效率低
≠ 个别效率
整体效率
专业化作业有利于提高个别效率,不少企 业因此实行计件工资。
但是,效率追求的重点应该是关注【整体 效率】,这对企业才有创造利润的实际意义。
所以,有必要将奖励个别效率的企业行为 转变为奖励整体效率,如:计件工资以完成品 (而非半成品)为标准,实行团队计件。
还应该以提高整体效率为目标,改善生产 线的布局,如:将水平布置和离岛式布置调整 为流线式布置,这样有利于团队协作。
库存的危害: ☆ 额外的搬运储存成本
☆ 造成空间浪费 ☆ 资金占用(利息及回报损失) ☆ 物料价值衰减 ☆ 造成呆料废料 ☆ 造成先进先出作业困难 ☆ 掩盖问题,造成假象
制造过多/过早
浪费
违背JIT原则
制造过多/过早造成浪费: ☆ 造成在库
☆ 计划外/提早消耗 ☆ 有变成滞留在库的风险 ☆ 降低应对变化的能力
不良造成额外成本
常见的等待现象: ☆ 材料损失
☆ 设备折旧 ☆ 人工损失 ☆ 能源损失 ☆ 价格损失
☆ 订单损失 ☆ 信誉损失
动作
浪费
多余动作 增加强度降低效率
常见的12种浪费动作:
① 两手空闲
⑦ 转身角度大
② 单手空闲
⑧ 移动中变换动作
③ 作业动作停止 ⑨ 未掌握作业技巧
④ 动作幅度过大 ⑩ 伸背动作
认识浪费与效率
1、三种经营思想 2、增值——工作的目标 3、企业常见的七种浪费 4、管理的实质
5、 假效率与真效率 6、个别效率与整体效率 7、可动率与运转率 8、库存是万恶的源泉
1、三种经营思想
成本中心思想 售价=成本+利润
售价中心思想 利润=售价-成本
利润中心思想 成本=售价-利润
根据成本和计划利润 决定售价
以顾客为起 点的经营
供应商
顾客
顾客满意五要素
顾客
Q
满意
F
C DS
Q
quality
质量Q:站在顾客立场, 制造令顾客称心满意的产品
以产品和服务为媒体完全实现 对顾客之承诺。
C
cost
成本C:通过有效管理, 把顾客的负担降到最低程度
通过高成本力减小顾客负担;通过 提高技术含量和服务质量来提高对顾客 的附加价值。
仅适用于卖方市场
利润根据售价变动 属于被动利润型
根据售价变化 主动降低成本
企业使命及其实践
为世界 作贡献
创造利润 达成经营目标
为顾客创造价值 使顾客满意
企业存在的最直接目 的就是生产金钱。为世界 作贡献是企业的共同理念!
生产、质量、 安全、成本等各项经营活动
现代市场竞争 已经由企业之间的竞争 转变为供应链之间的竞争
等待浪费
搬运浪费
工 8 不良浪费
厂 大 动作浪费
浪 常
见
加工浪费
的 费 库存浪费
地下工厂
企业每生产一件产品就在制 造一份浪费。伴随企业运营中各 业务环节不被察觉或不被重视的 浪费,日本企业管理界将之形象 地比喻为“地下工厂”。
制造过多(过早)浪费
缺货损失
等待 浪费
等待不创造价值
常见的等待现象: ☆ 物料供应或前工序能力不足造成待料
⑤ 左右手交换 ⑾ 弯腰动作
⑥ 步行多
⑿ 重复/不必要动作
加工 浪费
过剩的加工造成浪费
常见的加工浪费: ☆ 加ห้องสมุดไป่ตู้余量
☆ 过高的精度 ☆ 不必要的加工
过剩加工造成的浪费: ☆ 设备折旧 ☆ 人工损失
☆ 辅助材料损失 ☆ 能源消耗
库存 浪 费 库存造成额外成本
常见的库存: ☆ 原材料、零部件
☆ 半成品 ☆ 成品 ☆ 在制品 ☆ 辅助材料 ☆ 在途品
D
delivery
交货期D:抓住时机, 即时满足顾客需要
足够短的生产周期;按时交货,瞬 时响应市场。
S
safety
安全S:健康、安全、环保
绝对的安全卫生保证,遵守环保和 技术法规。
F
flexibility
柔性F:敏锐感觉市场,敏捷适应变化 预见性地满足顾客需要
倾听顾客的声音(VOC)。 应变力。 管理与技术创新力(领变力)。
真效率
假效率
固定的人员
真效率
最少的人员
生产出仅需的产品
生产出更多的产品
能力提升是效率的基础。 但效率建立在有效需求的基础 上,以【是否创造利润】为标 准;如果不创造效益甚至造成 在库,则此种效率是假效率。
假效率 真效率
能力 提升
【效率建立在有效需求的基础上】 能力提升是效率提升的基础。但有时能力 提升会造成效率提升的假象。 管理者的责任就是在能力提升的基础上, 将假效率转化成真效率。 所以,“省人化”是效率的关键。
省人化的两种形式: ☆ 正式工 + 季节工 / 临时工(变动用工) ☆ 固定人员 + 公用人员(弹性作业人员)
6、个别效率与整体效率
例 能力需求:100件/H
项目 能力 达成率 奖金 效率
工序1 100件/H
100% 标准产量奖金 个别效率合格
工序2 125件/H
125% 125%奖金 个别效率高