甲醇裂解工段
甲醇裂解制氢装置VPSA脱碳部分的操作规程

甲醇裂解制氢装置VPSA脱碳部分的操作规程一、VPSA部分介绍1.装置规模公称产氢能力:10000Nm3/h;装置操作弹性:60〜110%;年生产时数:8000小时2.装置组成本单元由10台脱碳吸附塔和3台真空泵等设备组成。
3.工艺流程来自甲醇裂解部分的甲醇裂解气自塔底进入脱碳吸附塔。
其中绝大部分CO2 及一些杂质气体被吸附下来,脱碳后的氢气等气体进入提氢单元。
吸附塔吸附的CO2等气体通过真空泵抽真空被解吸后高点排放。
4.原料气规格本装置的设计允许原料气组分和压力在较宽的范围内变化,但在不同的原料气条件下吸附参数应作相应的调整以保证产品的质量,同时产品氢收率也将随原料而变化。
当原料气条件变化时,物料平衡也将发生相应的变化。
在原料气条件不变的情况下,所有的调节均可由计算机自动完成。
本单元设计的原料气为:甲醇裂解气其详细规格如下:5.产品规格本单元的主要产品为脱碳气,副产品为脱碳解吸气。
在实际生产中,脱碳气的纯度可通过改变PSA单元的操作条件进行调节,而解吸气的组成也会随原料气和产品气的不同而略有不同。
以下为设计的产品气规格:脱碳气脱碳气纯度:CO2 <3.98 v%脱碳气产量:13650Nm3/h脱碳气温度:40℃脱碳气压力:2.5MpaG脱碳解吸气脱碳解吸气温度:40℃脱碳解吸气压力:0.02MpaG二、工艺过程说明1.基本原理吸附是指:当两种相态不同的物质接触时,其中密度较低物质的分子在密度较高的物质表面被富集的现象和过程。
具有吸附作用的物质(一般为密度相对较大的多孔固体)被称为吸附剂,被吸附的物质(一般为密度相对较小的气体或液体)称为吸附质。
吸附按其性质的不同可分为四大类,即:化学吸着、活性吸附、毛细管凝缩、物理吸附。
其中物理吸附是指依靠吸附剂与吸附质分子间的分子力(即范德华力)进行的吸附。
其特点是:吸附过程中没有化学反应,吸附过程进行得极快,参与吸附的各相物质间的平衡在瞬间即可完成,并且这种吸附是完全可逆的。
甲醇裂解变压吸附制氢装置操作手册
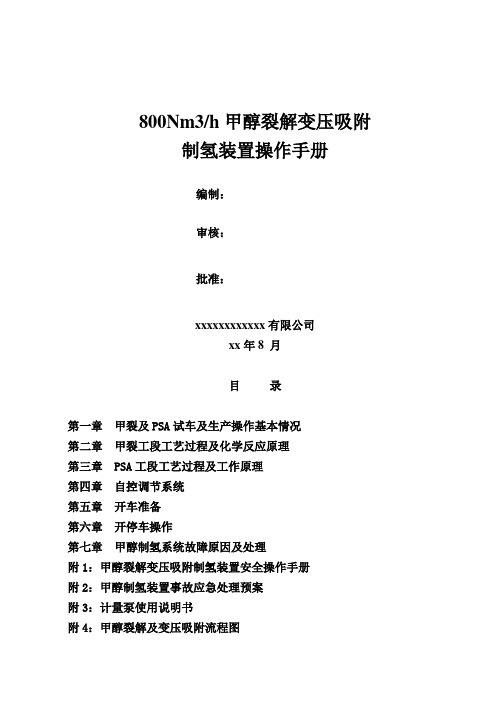
800Nm3/h甲醇裂解变压吸附制氢装置操作手册编制:审核:批准:xxxxxxxxxxxx有限公司xx年8 月目录第一章甲裂及PSA试车及生产操作基本情况第二章甲裂工段工艺过程及化学反应原理第三章 PSA工段工艺过程及工作原理第四章自控调节系统第五章开车准备第六章开停车操作第七章甲醇制氢系统故障原因及处理附1:甲醇裂解变压吸附制氢装置安全操作手册附2:甲醇制氢装置事故应急处理预案附3:计量泵使用说明书附4:甲醇裂解及变压吸附流程图第一章甲裂及PSA试车及生间操作基本情况一、试车及生产操作人员小组人员配置试车组长或生产主管:(业主配置)技术指导:(业主配置)工艺操作工:2人/班分析操作工:1人/班仪表值班:1人/班电气值班:1人/班机械值班:1人/班公用工程协调(调度):1人/班应急对外协作:1人/班安全员:1人/班二、试车时间及地点时间:2019年10月。
地点:甲醇裂解制氢生产区三、工艺指标1.甲醇:符合GB338—2004标准优等品要求。
2.脱盐水:Cl -≤ 1ppmSO42-≤ 1ppm90℃以下稳定,对碳钢、不锈钢无腐蚀电导率≤10μs/cm。
3.温度汽化塔进料温度 140~160℃汽化塔底部温度 160~180℃汽化塔顶部温度~180℃进转化器温度 220~250℃出转化器温度 230~250℃导热油温度 250~280℃出换热器转化气温度 120~140℃出冷凝器转化气温度≤40℃4.压力导热油进口压力0.4~0.6MPa进工段冷却水压力≥0.3 MPa进工段仪表空气压力≥0.4~0.6 MPa 5.浓度甲醇~50%(Wt)水~50%(Wt)转化气组成如下:H273~74.5%23~24.5%CO2CO 0~1%≤ 200ppmCH46.产品气H2≥99.99%(v/v)7.分析内容第二章甲裂工段工艺过程及化学反应原理第一节工艺过程甲醇催化裂解、转化工艺过程包括:原料汽化过程、催化裂解转化反应、转化气冷却冷凝、气液分离等。
天然气制甲醇工艺流程及其控制研究分析

天然气制甲醇工艺流程及其控制研究分析摘要:经济的发展,社会的进步推动了我国综合国力的提升,也带动了科学技术的不断完善和创新,近年来,天然气装置长期处于低负荷运行状态,工艺参数发生变化。
在不断增长世界天然气产量的同时,为天然气化工提供了充足的原料。
天然气已经成为社会发展的主体性产业,为积极响应我国所提出的可持续发展理念,全面落实环保工作,需要对天然气化工的发展现状进行明确的分析,确保天然气得到有效的应用,积极推动我国与其他国家之间的交流和合作,不断加强新技术的学习,以发挥天然气化工技术的重要作用,积极推动我国社会经济稳定性的提高。
基于此,本文主要对天然气制甲醇工艺流程及其控制进行研究分析,详情如下。
关键词:天然气;制甲醇;工艺流程;控制引言甲醇是常见的化工生产原料的一种,当前在多领域有着广泛的应用,医药、农药、燃料等化工生产体系中,甲醇均有着广泛的生产应用,当前随着全球范围内出现严重的能源危机问题,天然气甲醇的生产制造成为学科领域研究的重点问题。
天然气中的游离水或水蒸气,在一定的温度和压力下形成液态水,液态水脱出后与天然气中分子量较小的气体组分结合后,就形成了天然气水合物。
1天然气制甲醇分析天然气主要的成分为甲烷,用天然气制造甲醇,则需要将其进行裂解处理,裂解制取甲醇需要蒸汽转化、催化氧化以及非催化氧化等环节,其中蒸汽氧化是首先需要完成的内容。
在进行工艺处理的过程中,甲烷通过氧化锌床,将硫物质降低到目标水平后,通入一定量的水蒸气,经过加热转化处理后,向装有镍钼催化剂的绝热反应器放置,完成反应后,向转化炉中放置来完成后续反应。
甲烷的水蒸气裂解为一种吸热的反应程序,为了确保转化能够持续进行,需要在炉管间提供一定的热量,以确保燃料能够稳定燃烧,此为转化反应的关键环节。
因为甲烷的裂解为富氢反应,应该严格按照最佳氢碳比例进行配比,以获得更高的甲醇转化率。
2天然气制甲醇工艺流程及其控制2.1天然气制合成气天然气制甲醇工艺流程及其控制之一是天然气制合成气。
一种在敞开环境下的甲醇裂解燃烧的方法与流程

一种在敞开环境下的甲醇裂解燃烧的方法与流程一种在敞开环境下的甲醇裂解燃烧的方法与流程在工业生产和日常生活中,我们经常会接触到甲醇这种化学物质。
甲醇能够被用作溶剂、燃料和化工原料,其应用十分广泛。
然而,由于甲醇易燃、挥发性大,一旦发生泄漏或不慎使用不当,就有可能引发火灾和爆炸,对人身和环境造成危害。
研究一种在敞开环境下的甲醇裂解燃烧的方法与流程,具有重要的意义。
本文将从简到繁、由浅入深地探讨这一主题,以便读者更深入地理解这一领域的相关知识。
一、传统的甲醇裂解燃烧方法在传统的工业生产中,甲醇裂解燃烧常采用加热器和燃烧室相结合的方式。
将甲醇通过加热器进行加热,使其蒸气化;然后将蒸气化后的甲醇送入燃烧室进行燃烧反应。
这种方法简单易行,但存在能量损耗大、燃烧不完全等问题,且对环境的影响较大。
二、新型的敞开环境下甲醇裂解燃烧方法针对传统方法存在的问题,近年来科学家们已经提出了一种新型的敞开环境下甲醇裂解燃烧方法。
该方法利用先进的催化剂和反应器,在较低温度下就能实现甲醇的裂解和燃烧反应,减少了能量损耗和燃烧不完全的情况。
该方法还能有效降低燃烧产物中有害物质的排放量,对环境友好。
三、流程介绍新型的敞开环境下甲醇裂解燃烧方法的具体流程如下:1. 催化剂反应器预热:将催化剂反应器进行预热,保证反应器内部温度稳定在适宜的范围,以提高反应效率。
2. 甲醇裂解:将甲醇送入催化剂反应器中,经过催化剂的作用,甲醇分子发生裂解反应,产生一些碳氢化合物和一氧化碳等燃烧物质。
3. 燃烧反应:裂解后的燃料混合气体被引入燃烧器,进一步与氧气进行燃烧反应,释放出大量热能和二氧化碳等燃烧产物。
4. 产物处理:经过燃烧反应后,产生的燃烧产物需要经过处理,以净化有害物质和回收资源。
四、个人观点与理解从简单的甲醇燃烧到深入研究敞开环境下的甲醇裂解燃烧方法,我对这一领域有了更深入的了解。
新型的敞开环境下甲醇裂解燃烧方法不仅可以提高能量利用率,减少排放对环境的影响,更重要的是为我们提供了一种更加安全和高效的甲醇利用方式。
甲醇精馏工段操作法

甲醇精馏工段操作法主要内容和适用范围本项目甲醇精馏工序采用三塔工艺,精馏用汽为低压蒸汽。
各塔再沸器蒸汽冷凝液用作粗甲醇预热器热源,以节约能量。
为减少精馏不凝气中甲醇损失,本工序设有洗涤系统,洗涤后的不凝气去气柜。
排放槽用水采用甲醇回收塔塔底废水,以减少除盐水用量。
为了提高甲醇回收率和产品甲醇质量,本项目在常压塔后设回收塔,虽然增加一个塔,但由于降低了常压塔负荷,因而投资和蒸汽消耗基本上不增加。
不仅甲醇回收率增加,而且可以在粗甲醇杂质含量较高时从回收塔取出的甲醇用作燃料,避免杂质在系统累积而影响产品甲醇质量。
本项目采用板式塔。
生产原理粗甲醇中杂质种类较多,为了制备合格精甲醇产品,必须将杂质除去。
在工业生产中,主要是利用各组份的沸点不同,用精馏的方法将甲醇与其它组份分开,也就是同时并且多次地运用部分汽化和部分冷凝的方法,以达到完全分离混合液中各组分的连续操作过程。
为完成此过程,本装置采用3+1塔精馏流程,在预蒸馏塔中除去溶解性气体及低沸点杂质。
在加压塔及常压塔中除去水及高沸点杂质,从而制得合格的精甲醇产品。
此外,在回收塔中回收常压塔底排出的废水中的少量甲醇和其他杂醇。
工艺流程简述来自甲醇合成工序的粗甲醇经粗甲醇预热器(E15501)加热至70℃,然后进入预蒸馏塔(C15501)精馏。
塔顶出来的蒸汽温度为74.2℃,对应的压力为0.13MPa(A),先经过预塔冷凝器A(E15506)在65℃左右将其中的大部分甲醇冷凝下来,冷凝下来的甲醇进预塔回流槽(T15501),未冷凝的气体则进入预塔冷凝器B(E15515)冷却至40℃后部分冷凝,冷凝液流入萃取槽(T15508),萃取后也进入预塔回流槽(T15501),预塔回流槽的液体由预塔回流泵(P15503A/B)加压后作预蒸馏塔回流液,由预塔冷凝器B(E15515)出来的气体去排放槽(T15506),不凝气洗涤后经不凝气预热器(E15505)加热至150℃后去气柜。
甲醇精馏工段操作规程

精馏工段操作规程(10万吨/年)1.工艺原理概述在合成甲醇的同时伴随有许多副反应,从而生成许多副产物。
由于这些副产物的存在,使甲醇纯度下降,影响其质量。
另外CO2与H2合成甲醇时也有水生成,需要将水分离掉,得到符合质量要求的精甲醇。
现将粗甲醇中有代表性组分的分子量与沸点列于下由表可知,粗甲醇中的杂质可以分为两大类:一类包括二甲醚、甲酸甲酯等,它们的沸点低于甲醇;另一类包括乙醇、丙醇、水、丁醇等,它们的沸点高于甲醇沸点。
本工序正是利用这两类物质沸点的差异,采用三塔精馏工艺,在第一塔中除去沸点低于甲醇沸点的物质,在第二塔和第三塔中采出符合国家标准的精甲醇。
把液体混合物经过多次部分气化和部分冷凝,使液体分离成相当纯的组分的操作称为精馏。
连续精馏塔可以想象是由一个个简单蒸馏釜串联起来,由于原料液中组分的挥发度不同,每经过一个蒸馏釜蒸馏一次,蒸汽中轻组分的含量就提高一次,即yn+1>yn>X(y代表气相组成,X代表液相组分),增加蒸馏釜的个数就可得到足够纯的轻组分,而塔中残液中所含轻组分的量会越来越少,接近于零。
将这些蒸馏釜叠加起来,在结构上加以简化即成为精馏塔。
随着精馏操作压力的提高,液体混合物的沸点相应提高,加压精馏塔顶甲醇的冷凝温度相应提高,利用加压精馏塔顶较高温度成品甲醇的冷凝热来作为常压精馏塔再沸器的热源,这样可以降低甲醇精馏的蒸汽消耗。
本工序就是利用预蒸馏塔、加压精馏塔、常压精馏塔分离出粗甲醇中的轻组分物质和重组分物质而得到产品精甲醇。
三塔均用组合式导向浮阀塔,它比传统的浮阀塔板有更好的传质、传热性能。
2.工艺流程说明从合成工段送来的浓度为93%左右的粗甲醇到粗甲醇贮槽,经粗甲醇泵打到粗甲醇预热器,由蒸汽冷凝水提温至65℃左右进入预蒸馏塔,预蒸馏塔下部的预塔再沸器采用0.5MPa,170℃过热蒸汽间接加热液体粗甲醇,保持温度在75-80℃左右,塔顶温度用回流液控制在70℃左右,为了防止低沸点组分在塔顶冷凝,同时尽量减少甲醇损失,塔顶采用两级冷凝,一级冷凝器温度控制在65℃,二级冷凝器温度控制40℃。
甲醇制氢

汽化过热 转化反应 变压吸附 (PSA-H2)-
产品氢气
脱盐水
循环液 冷却、吸收
解吸气
系统操作参数
• 氢气气量: 500--1000NM3/H(温度:常温, 纯度:99.99%,杂质CO≤10PPm、 CO2≤10PPm) • 操作压力:1.0 MPa • 操作温度:230~300℃
0.2%)系统保压0.4MPa。
紧急停车
• 当装置突然停电、停水、停气或装置突然 出现故障时,则需要紧急停车,步骤如下: 1、关闭产品出口阀,关闭裂解气至PSA切断 阀。PSA停止运行。 2、迅速将转化器切至副线,(只关闭转化器 入口阀以免转化器憋压)。 3、导热油开始降温。此时降温的幅度可加大 至20-30℃/h
催化剂保护
1、在任何情况下,催化剂层温度禁止超过300℃。
2、还原后的催化剂绝对禁止与氧气或空气接触。 3、催化剂使用中应尽量避免中途停车。每停一 次车,尽管采取了钝化或氮气保护操作,还是会影
响催化剂使用寿命。
催化剂保护
• 4、 催化剂的升温和降温都必须缓 慢进行,禁止急速升温和降温。 • 5、 在满足生产能力、产率的前提 下,催化剂应在低温下操作,有利 于延长催化剂使用寿命。
换热器
• 利用废热将原料加热。
• 使裂解气降温。
汽化过热器
• 汽化过热器用于将经过换热后的原料液汽 化并过热至接近于反应温度。 • 加热介质是导热油。
冷凝器
• 用循环冷却水将裂解气进一步降温。
• 冷却后的重整气温度小于40℃。
原料罐和脱盐水罐
• 用于储存原料,其材料选用1Cr18Ni9Ti。 (304不锈钢)。
4、停混合液原料泵。
5、联系各部门查明原因及恢复时间,若短时 间能够恢复不做处理,待正常后系统恢复生 产。若长时间不能恢复,则按系统停车处理。
合成车间甲醇工段操作规程定稿(DOC)
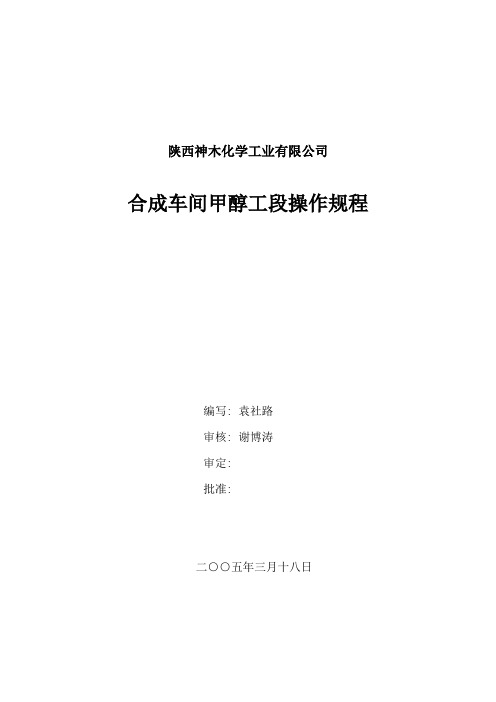
陕西神木化学工业有限公司合成车间甲醇工段操作规程编写: 袁社路审核: 谢博涛审定:批准:二○○五年三月十八日目录一、甲醇合成岗位操作规程--------------------------2二、氢回收岗位操作规程----------------------------23三、精馏岗位操作规程------------------------------30四、成品罐区操作规程------------------------------61五、灌装站操作规程--------------------------------66六、岗位制度--------------------------------------68七、安全环保责任制--------------------------------71一、甲醇合成岗位操作规程1.岗位任务:本岗位的任务是将净化工段来的新鲜合成气经合成气压缩机(C2001)加压后进入合成塔,在一定的压力、温度及触媒作用下生成甲醇,反应后的气体经冷却、冷凝分离出产品甲醇,未反应的气体进入 C2001 循环段补充压力后返回合成塔,甲醇生产的反应热用于副产 2.5Mpa(G)的饱和蒸汽。
2.工艺描述及设备2.1工艺流程说明(附工艺流程图)来自净化的甲醇合成气(P=2.9Mpa(G),T=40℃)与氢回收来的渗透气(P=3.0Mpa(G),T=40℃)混合,进入合成气压缩机一段,压缩至 5.5Mpa(G)后与循环气混合,再经循环段压缩至 P=6.0Mpa,T=56℃后进入中间换热器 (E2001) 的壳程,混合气被预热至 204 ℃后由顶部进入甲醇合成塔(R2001)。
甲醇合成塔的上部有一段高约 600mm 的催化剂绝热层,入塔气出绝热段的温度约为 206 ℃。
在甲醇合成塔中,CO、CO2 和 H2在铜基触媒作用下进行如下反应:CO+2H2 = CH3OH + QCO2+3H2= CH3OH + H2O + Q反应生成甲醇和水及少量有机杂质,并放出大量的热。
甲醇裂解制纯氢及CO技术

甲醇裂解制纯氢及CO技术3甲醇转化制取400Nm/h 纯氢及CO合成气装臵时间:项目名称:甲醇转化制取400Nm3/h 纯氢及CO合成气装臵业主:建设地点:一产品规格及规模纯度(V/V) ?99.9% 氢压力 MPa(G) 1.0气温度 ? ?40.0产量 Nm3/h 210纯度(V/V) ?50% 不含氧、HO 2CO压力 MPa(G) ?0.02 合成温度 ? ?40.0 气产量 Nm3/h 190 二装臵能力 1 公称能力 Nm3/h 400 2 年生产时数小时 ?8200 3 装臵运行方式连续运行 4 操作弹性 40--110% 三装臵消耗 1 甲醇 kg/h ~243.43 符合GB338-92,工业一级氯离子?0.1mg/l,电导2 脱盐水 Kg/h ~2.46 率?10μS/cm 3 循环水 m3/h ~50.0 循环量包括机泵、真空泵用电及4 电 KWh/h ~40.0 车间照明 5 仪表空气 Nm3/h ~30.0 四三废排放量1 废水 t/h 无本装臵基本无废水排放本装臵解析气即为产品2 废气 Nm3/h 无 CO合成气催化剂 490.8 年平均更新的催化剂、吸3 废渣 kg/年吸附剂 744.2 附剂(可回收) 4 废液 t/年未反应甲醇及副产物回烧处理2五装臵占地面积 m ~200 根据现场情况具体确定六装臵定员人 8 按四班三运转考虑组分合计名称单位一氧化二氧化甲醇脱盐水氢气甲烷二甲醚碳碳mol% 99.00% 1.00% 100.00% 1 原料Kg/h 243.43 2.46 245.88V% 4.75% 0.43% 61.64% 27.50% 2.37% 0.57% 2.75% 100.00% 裂解2 Nm3/h 20.45 1.84 265.31 118.37 10.20 2.45 11.84 430.45 气Kg/h 29.21 1.48 23.69 147.96 20.04 1.75 21.76 245.88V% 60.45% 2.34% 37.21% 净化3 分离 Kg/h 28.18 1.09 17.35 46.62V% 99.99% 0.01% 100.00% 产品4 Nm3/h 209.98 0.02 210.00 氢气Kg/h 18.75 0.01 18.76V% 0.38% 0.25% 29.13% 62.32% 5.37% 1.29% 1.26% 100.00% 解析5 Nm3/h 0.72 0.48 55.33 118.37 10.20 2.45 2.40 189.95 气Kg/h 1.03 0.39 4.94 147.96 20.04 1.75 4.41 180.521.1.1 工艺指标, 压力 ?1.0MPa(表压G), 温度 ?40?3, 流量210Nm/h, 纯度 ?99.9%(V/V) 1.1.2 生产规模3, 210Nm/h氢气,弹性范围40~110%。
【精品】甲醇裂解制氢资料

甲醇裂解制氢技术综述【关键词】甲醇裂解制氢【摘要】氢气在工业上有着广泛的用途。
近年来,由于精细化工、蒽醌法制双氧水、粉末冶金、油脂加氢、林业品和农业品加氢、生物工程、石油炼制加氢及氢燃料清洁汽车等的迅速发展,对纯氢需求量急速增加.甲醇蒸汽转化制氢和二氧化碳技术1前言氢气在工业上有着广泛的用途。
近年来,由于精细化工、蒽醌法制双氧水、粉末冶金、油脂加氢、林业品和农业品加氢、生物工程、石油炼制加氢及氢燃料清洁汽车等的迅速发展,对纯氢需求量急速增加。
对没有方便氢源的地区,如果采用传统的以石油类、天然气或煤为原料造气来分离制氢需庞大投资,“相当于半个合成氨”,只适用于大规模用户。
对中小用户电解水可方便制得氢气,但能耗很大,每立方米氢气耗电达~6度,且氢纯度不理想,杂质多,同时规模也受到限制,因此近年来许多原用电解水制氢的厂家纷纷进行技术改造,改用甲醇蒸汽转化制氢新的工艺路线。
西南化工研究设计院研究开发的甲醇蒸汽转化配变压吸附分离制氢技术为中小用户提供了一条经济实用的新工艺路线。
第一套600Nm3/h制氢装置于1993年7月在广州金珠江化学有限公司首先投产开车,在得到纯度99。
99%氢气同时还得到食品级二氧化碳,该技术属国内首创,取得良好的经济效益。
此项目于93年获得化工部优秀设计二等奖、94年获广东省科技进步二等奖。
2工艺原理及其特点本工艺以来源方便的甲醇和脱盐水为原料,在220~280℃下,专用催化剂上催化转化为组成为主要含氢和二氧化碳转化气,其原理如下:主反应:CH3OH=CO+2H2+90.7KJ/molCO+H2O=CO2+H2-41。
2KJ/mol总反应:CH3OH+H2O=CO2+3H2+49.5KJ/mol 副反应:2CH3OH=CH3OCH3+H2O-24。
9KJ/mol CO+3H2=CH4+H2O—+206.3KJ/mol上述反应生成的转化气经冷却、冷凝后其组成为H273~74%CO223~24。
年产量1000吨高压法甲醇分离工段工艺设计

年产量1000吨高压法甲醇分离工段工艺设计作者姓名xxx专业化学工程与工艺指导教师姓名xxx专业技术职务讲师目录目录 (Ⅰ)摘要 (4)ABSTRACT (5)第一章总论 (6)1.1概述 (6)1.2文件综述 (7)1.2.1甲醇简介 (7)1.2.2甲醇工艺发展 (9)1.2.3甲醇工艺简介 (9)1.2.4我国甲醇发展及市场需求 (13)1.2.5世界甲醇发展及市场需求 (15)1.2.6甲醇将来需求展望 (16)1.3设计任务旳项目起源 (16)1.4原料规格及起源 (16)1.5水、电、汽供给情况 (17)1.5.1给水、排水系统 (17)1.5.2电力供给 (17)1.5.3蒸汽供给 (17)1.6贮存和运送 (17)1.7节能 (17)第二章生产流程方案确实定 (19)2.1生产方案确实定 (19)2.2生产流程简述 (19)2.2.1生产工艺流程简图 (19)2.2.2流程简述 (19)第三章工艺计算 (19)3.1小时生产能力 (19)3.2物料衡算和能量衡算 (19)3.2.1计算条件 (19)3.2.2物料衡算 (19)3.2.3热量平衡计算 (22)第四章主要设备工艺计算和设备选型 (25)4.1主要工艺操作数据 (25)4.1.1化学控制 (25)4.1.2压力控制 (25)4.1.3温度控制 (25)4.2主要设备(主精馏塔)塔径旳工艺计算 (25)4.2.1理论塔板数计算 (25)4.2.2塔径工艺计算 (28)4.2.3水力学性能计算 (30)4.3塔体与裙座机械设计 (32)4.3.1设计条件 (32)4.3.2按计算压力计算塔体与封头厚度 (33)4.3.3设备载荷计算 (33)4.3.4风载荷与风弯矩计算 (36)4.3.5地震弯矩计算 (37)4.3.6地震偏心弯矩计算 (39)4.3.7塔体水压试验和应力校核 (39)4.3.8基础环设计 (40)4.3.9地脚螺栓计算 (40)第五章原材料、动力消耗定额及消耗量 (33)5.1原料消耗 (42)5.2动力消耗 (42)第六章经济分析与投资概算 (42)6.1经济分析 (42)6.2车间经费 (43)第七章环境保护 (44)7.1环境保护 (44)7.2主要卫生、安全、环境保护等阐明……………………………………44第八章设计心得与体会 (44)参照文件 (46)附录 (47)致谢 (48)摘要甲醇是主要旳化工原料, 广泛用于有机合成、燃料、医药、涂料和国防等工业, 在国民经济中有主要作用。
甲醇裂解工段

H2 CO2 CO CH3OH
~1100 Nm3/h ~1.2MPa 73~74.5 % 23~24.5 % ≤1 % ≤ 200ppm
≥0.4 MPa ~ 0.6 MP
其他 1.进工段冷料规格
甲醇:符合GB3382004标准一等品要求。严禁含乙醇、氯离子、硫离子、烃类。
区间(℃)
80~110 110 110~150 150~200* 200 200 200
阶段
升温、纯N2气 升温、纯N2气 升温、加0.5%H2 升温、加0.5%H2 恒温、加0.5%H2 恒温、加1%H2 恒温、加1.5%H2
升温速度(℃/hr)
15 0 10 5 0 0 0
时间(hr)
2 2 4 10 5 8 2
组成 含量%(重 量) CuO >60 ZnO 5~15 Al2O3 5~15 Na2O <0.1 烧失重 ≤10
2.催化剂的包装、贮存和装卸
1.催化剂用塑料袋包装后装入铁桶内。贮存在室内,严防受潮、受震和毒物污染。搬运过程 中不要在地上滚动。 不能从高于0.5米的地方落下,或撞击。 2.在正常情况下,催化剂可以贮存一年以上,对催化剂的活性和物理性能不会影响。 3.催化剂装入反应其前,应用3mm筛子过筛,除渠少量粉末。并检查反应器有无堵塞物或遗 留工具等。 4.催化剂装入反应器时,采用专用布袋或胶管。将催化剂装入布袋再导入反应管中填装,直 至管板表面为止。装填时应防止催化剂架桥。要求每根反应管所装催化剂数量相同,高度相 同。 5.操作人员在装填催化剂时,严禁直接在催化剂上行走、踩踏。应在催化剂上垫木板,站在 木板上操作。防止催化剂破碎。 6.催化剂装填完毕后,用空气或氮气将管内和管板上的催化剂粉末清除干净。 7.催化剂使用前要进行还原活化。如需卸出活化后的催化剂,应对催化剂进行钝化。
甲醇裂解制氢PSA工段讲解
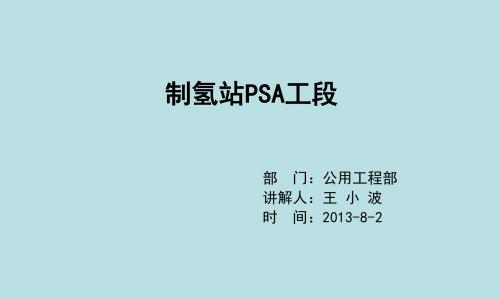
一均降(E1D) 开启阀KV0205a;
A塔停止吸附后,与结束二均升步骤的C塔以出口端相连,即通过阀KV0205a、KV0205c
与C塔进行第一级压力平衡,A塔压力降低,均压后A、C塔压力基本相等。
关闭阀KV0205a。
二均降(E2D) 开启阀KV0204a;
A塔完成一均降步骤后,与刚结束三均升步骤的D塔以出口端相连,即通过阀KV0204a、
• 沸石分子筛:简写为MS,是硅酸钠和铝酸钠等与NaOH水溶 液反应制得的胶体经干燥后而成,有均匀的孔径,具有分子 筛的作用。PSA工业中主要用于制氢、提纯CO、空分制富 氧、提纯甲烷、精度脱水和CO2等。
第四部分 变压吸附工艺
1.工 艺 描 述
PSA提纯氢气装置是由五台吸附塔(C0201A~E,下简称A、B、C、 D、E塔)、一台气液分离缓冲罐(F0201)、 一台产品氢气缓冲罐 (F0202) 、两台氢气缓冲罐(F0203A、B)和一系列程控阀组成。压力~ 1.2Mpa的甲醇裂解转化气(原料气)进入吸附塔(C0201A、B、C、D、E) 进行吸附,得到的产品气经过产品氢气缓冲罐(F0202)和氢气缓冲罐 (F0203A、B)的缓冲之后,再经过计量和调节到用户去。杂质气体即废 气放空。
3、表面的含义
• 表面--有内表面和外表面之分,吸附主要发生在内表面,外表面与内表面相 比相当小,而内表面积大是固体作为吸附剂的先决条件。以下为几种常用吸附
剂的表面积的大小:
• 硅胶 SG
500~600 m2/g
• 活性炭 Ac
700~1100 m2/g
• 分子筛 MS
700~1000 m2/g(其外表面积仅 为2.67×10-4 m2/g
冲洗压力
冲洗步骤应当在过程的最低压力下进行,此压力越低,对吸附剂解吸杂质越有利。为此,在
甲醇裂解制氢气的相关技术

甲醇裂解制氢气的相关技术摘要:在节能减排的大背景之下,氢能作为高效洁净的环保能源成为本世纪最理想的替代能源。
而液体燃料甲醇作为储氢载体,能量密度高、安全可靠、存储运输成本低、制氢转化条件相对温和、不含硫、低毒、制氢过程相对容易实现等特点成为这些富氢燃料中的首选。
关键词:甲醇;裂解制氢;技术前言在节能减排的背景下,新能源汽车发展速度加快,而氢燃料电池车由于其节能环保高效成为最近研究的热点,并且国家出台各项法规和政策支持其发展。
目前车载氢燃料电池中的氢气以高压气态形式储存,能量密度低,成本高,且存在一定的安全隐患。
而甲醇作为储氢载体,能量密度高、安全可靠、存储运输成本低、制氢转化条件相对温和、反应温度一般在250~300℃、不含硫、低毒、制氢工艺相对容易实现等特点成为这些富氢燃料的首选。
甲醇可以从化石能源制取,也可从新能源中制取,如生物质能,目前我国主要以煤为主要原料。
随着CO2合成甲醇技术的突破,甲醇制氢可进一步发展为甲醇储氢,实现二氧化碳零排放,具有广阔的应用前景。
甲醇燃料电池车是以甲醇为原料,甲醇水溶液经过重整器后产生氢气,氢气和氧气经过电化学反应产生电能的一种发电设备,产生的电力除了应用于交通领域外,还可以作为移动电源、备用电源、分布式发电、便携式电源、军民融合发电等。
1甲醇裂解制氢甲醇裂解制氢工艺简单,是甲醇和水在催化剂的催化下裂解转化成氢气和二氧化碳,同时会产生少量一氧化碳和甲烷气体,经变压吸附提纯可以制得不同纯度的氢气。
甲醇裂解制氢相较于煤制氢和天然气制氢技术具有技术投资成本低,耗能少。
但是,甲醇原料的成本较高,造成制氢单位成本较高。
因此解决甲醇的来源问题,降低原料成本,提高甲醇的催化裂解效率是甲醇制氢取得长足发展的关键。
1.1工艺原理甲醇和水受热气化之后会进入到甲醇裂解反应器中,在铜系催化剂的作用下发生反应,制得氢气,具体的反应如下:CH3OH=CO+2H2CO+H2O=CO2+H21.2制氢工艺甲醇裂解制氢工艺路线是加压汽化后的甲醇气与水蒸气混合后,在铜系催化剂的作用下,于250~300℃发生甲醇裂解转化反应,生成转化气,重整气经多级热回收冷却后送入变压吸附,以提高氢气纯度。
甲醇裂解制氢装置操作规程

甲醇裂解装置操作规程目录1.原料及转化的规格 (1)2. 工艺 (1)2.1.反应原理 (1)2.2.工艺过程及化学反应原理 (1)2.3化学反应原理 (2)2.4.工艺流程叙述 (2)3.主要控制指标 (2)3.1.原料汽化过热 (2)3.2.转化反应 (2)3.3.转化气指标 (3)4.操作程序 (3)4.1 开车前的准备工作 (3)4.2 汽化过热器开车 (3)4.3 .转化器开车的条件: (3)5.开车 (4)5.1初次开车前的准备工作 (4)6.停车和停车后再启动 (5)6.1正常停车 (5)6.2紧急停车 (5)6.3临时停车 (5)6.4长期停车 (5)6.5停车后再启动 (6)7.安全技术 (6)7.1.氢气的性质 (6)7.2.装置的安全设施 (6)7.3.氢气系统运行安全要点 (7)7.4.消防 (7)7.5生产基本注意事项 (7)正文1.原料及转化的规格1.1原料规格甲醇:符合GB338—2004标准一等品要求。
严禁含乙醇、氯离子、硫离子、烃类。
脱盐水:C1﹣≤3ppm,电导率≤20u s/cm,90℃以下稳定,对碳钢、不锈钢无腐蚀。
1.2转化气规格组成:H2 73~74.5%CO2 23~24.5%CO ≤1.0%CH3OH ≤200ppmH2O 饱和压力: 1.4~1.6Mpa-G温度:≤40℃2. 工艺2.1.反应原理甲醇和水按一定配比经加压、汽化过热,其混合蒸汽在催化剂作用下发生催化裂解和转化反应。
CH3OH -----------CO+2H2-90.7 kJ/mo1 CO+H2O----------CO2+H2+41.2 KJ/molCH3OH+H2O=CO2+3H2-49.5KJ/mol2.2.工艺过程及化学反应原理2.2.1工艺过程甲醇催化转化制气工艺过程包括:原料汽化、催化转化反应、转化气冷却冷凝以及洗涤净化等。
2.2.2原料汽化原料汽化是指,将甲醇和脱盐水按规定比例混合,用泵加送入系统进行预热、汽化过热至转化温度的过程。
甲醇裂解法制氢气规程、教材(8)

甲醇裂解—变压吸附制氢培训教材............................................................................................. ①第一章概论............................................................................................................................... ②甲醇裂解法制氢气. (12)甲醇裂解制氢含甲醇蒸汽转化和变压吸附制氢两部分 (13)甲醇裂解—变压吸附制氢培训教材目录:第一章概论第二章化石燃料制氢第一节天然气或裂解石油气制氢第三章甲醇制氢第四章变压吸附法提纯氢气第五章甲醇制氢装置介绍第一章概论氢是自然界里最轻的元素,其分子量为2.016。
在一个大气压和20℃下的密度为83.764g/m3,其液化温度大约为-253℃。
由于这种特性,如按它的能量密度算,氢是难于以适当的形式来贮存的,而且有时还要消耗很多的能量。
自然界中的氢决大多数是不以游离状态存在的,而是以化合物的形态存在,其中最为常见的是水和化石类化合物。
在工业中利用水制取氢气需要消耗大量的电能,而利用化石燃料制取氢气又会加剧自然环境的恶化。
能源与环境是人类社会可持续发展涉及的最主要问题。
地球上的化石燃料储量有限,并且其使用会造成自然环境急剧恶化,从化石燃料逐步转而利用可持续发展、无污染的非化石能源是关键所在。
氢能是理想的清洁能源之一,已引起极大重视并广泛使用。
如将氢气直接用于内燃机的燃料,可获得比一般碳氢化合物燃料更高的效率,而且还具有零污染排放的优异性能;将氢气用于氢氧燃料电池则可得到高达45%~60%的化学能-电能转化效率,而一般的内燃机的热机效率仅为15%。
由于质子交换膜燃料电池技术的突破,高效燃料电池动力车样车已陆续出现。
甲级防火区安全规定(5篇)

甲级防火区安全规定1.我公司甲级防火区域为主车间加氢岗位中的加氢釜;甲醇罐、燃油罐区及泵区;甲醇裂解变压吸附工段;氢压机房;氢气贮罐区等部位。
甲级防火区涉及易燃、易爆、高温、高压等范畴。
2.在该岗位工作的操作人员必须持两证上岗,即压力容器操作证和Ⅲ级以上锅炉操作证。
严禁无证人员上岗或顶岗。
3.甲级防火区属非参观区域,无关人员严禁进入甲级防火区域。
4.严禁携带引火种、发火等危险品进入甲级防火区域。
5.通常情况禁止一切车辆进入甲级防火区。
特殊情况(如卸甲醇和燃油)经生产技术安全部批准,并在车辆排气管加戴防火罩(阻火器),按指定路线行驶方可进入。
停车后立即熄灭发动机,不准在卸料作业过程中启动发动机。
车辆出现故障时,严禁在区域内检修车辆或强行启动车辆,必须将故障车辆牵引出或推出甲级防火区外方可进行检查。
6.进入甲级防火区作业及巡查工作人员,要关闭BP机、手机和小灵通等通讯工具,严禁使用手机及BP机、小灵通。
7.严禁在防火区内堆放除燃油和甲醇以外的任何易燃物品,如油污、油布、纸张、木材等杂物。
管沟、电缆沟保持畅通,不得积存油污、垃圾等。
下水系统不得存油和渗油,要定期进行冲洗。
8.甲级防火区要定时、定人进行巡回检查,有异常情况要立即向车间领导和生产技术安全部及公司分管领导报告,并采取有效应急措施。
9.甲级防火区内的灭火设施如烟雾气溶胶和自动报警系统、消防水源要完善;要布置合理、有足够的消防器械,并使其始终处于完好状态,要定时检查与更换。
消防道路要保持畅通无阻,不得堵塞。
10.避雷装置和防静电接地装置每年要进行一次全面检测,发现问题及时整改。
11.应定期检查管道密闭性能是否良好,呼吸阀、安全阀、阻火器等安全附件是否正常完好。
12.甲醇罐车和燃油罐车在卸料入贮罐时,应先把槽车罐体进行可靠接地放电后,方可接入卸料泵打入贮罐。
13.对甲醇罐及燃油罐要用冷却水冷却罐顶及罐壁。
14.加强对氢气系统的设备管理,对高压氢部位设备和管道的氢腐蚀、氢脆等情况,定期进行技术分析和系统检漏,发现问题,立即处理,并请有关技监部门进行监检,确保安全。
甲醇化工段工艺操作规程
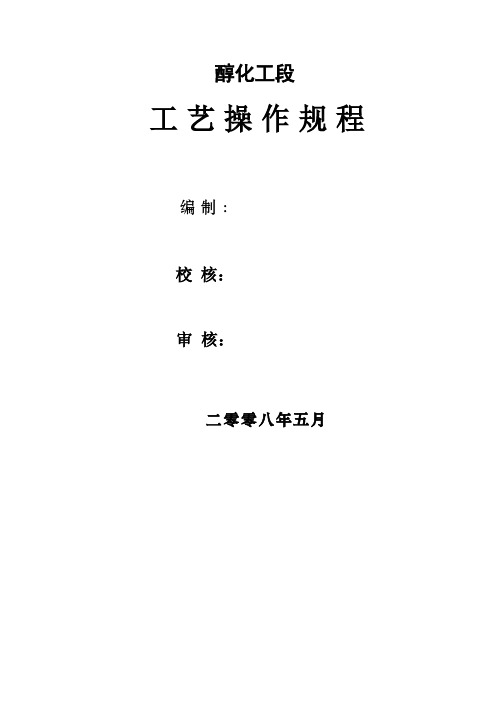
醇化工段工艺操作规程编制:校核:审核:二零零八年五月醇化工艺操作规程目录第一节主要任务与管辖范围第二节工作原理与工艺流程第三节主要设备第四节主要工艺指标第五节开、停车程序第六节正常生产中的操作要点第七节不正常现象判断及处理第八节巡回检查程序第九节交接班事项第十节安全生产规程第一节主要任务与管辖范围醇化工段主要任务是:将压缩送来的原料气中CO+CO2指标降到0.5%以下,净化为主,并副产粗甲醇。
醇化工段管辖范围:醇化塔、醇化预热器、循环机、醇分离器、水冷器及所属设备、管道、阀门、仪表。
第二节工作原理与工艺流程一、醇化工序的工作原理:主反应:CO+2H2→CH3OH+QCO2+3H2→ CH3OH+H2O+Q副反应:2CO+4H2→(CH3)2O+H2O+QCO+3H2→CH4+H2O+Q4CO+8H2→C4H9OH+3H2O+QCO2+H2→CO+H2O-QnCO+2nH2→(CH2)n+nH2O+Q二、醇化工序的工艺流程:压缩送来的12.5MPa脱碳后的原料气(1~2%的CO、≤0.4%的CO2),经油分分离油污后,进醇化塔塔前预热器管间(上进上出),换热后进醇化塔;气体进醇化塔下部的换热器管内,与管间的出塔气体换热,温度升高后经中心管上升进入上绝热层反应;另一部分气经醇化塔内外筒环隙(下进),再经下降管进入冷管束,移走内冷层的触媒反应热。
两部分气在混合分布器Ⅱ混合后进入第二绝热层反应,接着进入冷管层反应,再进入分气筒径向流动,出径向段的气体走径向筐与内筒的环隙,进入换热器管间,与进塔的未反应气换热后出塔,约180℃的出塔气体进入醇化预热器管内,上进下出,温度降至80℃以下;水冷器进一步降低温度后,进入醇分离器,将粗甲醇分离下来(送入粗醇中间槽),醇后气体被送入下一工段;另一部分可进循环机系统打循环。
醇化系统以精制净化为主。
第三节主要设备第四节主要工艺指标醇化工段主要工艺指标:第五节开、停车程序一、醇化系统1、系统开车:1.1 系统原始开车:A、系统设备、管道安装、催化剂装填结束,所有电器、仪表完好;B、管道应另行制定分段吹除方案进行管道吹除;C、系统臵换和气密性试验另行制定方案进行;D、系统臵换、气密性试验合格后,按《催化剂升温还原方案》开车1.2 系统开车:A、系统检修完毕、臵换和气密性试验合格后,系统补入合格的原料气(各项指标在工艺指标范围内),充压至5.0MPa;B、阀门调整:关补入阀,关层冷激阀,关塔底冷副阀,关系统出口阀,关醇分放醇阀。
- 1、下载文档前请自行甄别文档内容的完整性,平台不提供额外的编辑、内容补充、找答案等附加服务。
- 2、"仅部分预览"的文档,不可在线预览部分如存在完整性等问题,可反馈申请退款(可完整预览的文档不适用该条件!)。
- 3、如文档侵犯您的权益,请联系客服反馈,我们会尽快为您处理(人工客服工作时间:9:00-18:30)。
H21.2MPa 73~74.5 % 23~24.5 % ≤1 % ≤ 200ppm
≥0.4 MPa ~ 0.6 MP
其他 1.进工段冷却水压力 2.进工段仪表空气压力
4.原料规格
甲醇:符合GB3382004标准一等品要求。严禁含乙醇、氯离子、硫离子、烃类。
产品氢气
解吸气
甲醇裂解工段
第一部分 工业制氢方法介绍
工业制氢方法
1.天然气蒸汽重整制氢
液氨
2.电解水制氢
3.甲醇蒸汽转化制氢 4. 烃类氧化重整制氢 5.其他含氢物质分解制氢。
其中,前三种方法使用较为普遍。
1.天然气制氢
• 天然气水蒸气重整制氢: 以天然气为原料,用水蒸气转化制取富氢混合气,应用的是合成氨生产领域成熟 的一段炉造气工艺。该工艺包含两个步骤:天然气脱硫和烃类的蒸汽转化。出 口混合气含氢量约为70%。
2.工艺流程叙述
来自甲醇高位槽(F0102)的甲醇经流量调节系统(FFC-0102)进入混合管, 与收集在原料液罐(F0101)中的净化塔(C0101)底部的循环液混合,配成规 定比例的醇、水混合物,由原料液计量泵(P0101A/B)加压计量后进入换热器 (E0102A/B)预热,再进入汽化过热器(E0101A/B),被导热油加热汽化并过 热至规定温度的醇、水混合蒸汽进入转化器(R0101A/B)内,在此,同时完成 催化裂解和转化反应,生成的高温转化气在换热器(E0102A/B)中被原料液冷 却,再经冷凝器(E0103A/B)冷却冷凝降温后入净化塔(C0101)进一步洗涤 除去液相甲醇及水,回收的甲醇、水至原料液罐(F0101)循环使用。净化塔 (C0101)洗涤用水,由脱盐水计量泵(P0102A/B)将来自原料液罐的脱盐水 加压供给。 从净化塔(C0101)出来的转化气进入变压吸附工段气液分离缓冲罐 (F0201)缓冲后进入吸附塔。 汽化、过热及转化反应所需热量由过热蒸汽加热导热油供给。
CH3 (OH) CO 2H2 90.8kJ mol
-1
-1
CO H2O CO2 H2 47.3kJ mol
工 业 制 氢 比 较
比较项目
天然气蒸汽转化 -变压吸附制氢
甲醇蒸汽转化 -变压吸附制氢 较成熟 低 <2.5
水电解制氢 -纯化 成熟 较高 5~6
技术成熟性 一次性投资 生产成本(元 •Nm-3)
电0.2 kW · 。 h
天然气中的甲烷含量按96.9 %(体积分数) 计。
2.水电解制氢
• 电解水制氢:直流电作用下,水分子分解为氢离子和氢氧根离子,在阳极氢氧 根离子失去电子产生氧气,在阴极氢离子得到电子产生氢气。 • 电解水制氢效率较高,且工艺成熟,设备简单无污染,但耗电大,一般氢气电 耗为4.5~5.5kW/m3,生产成本高,电费占整个生产费用的80%左右。 • 主要消耗定额:原料脱盐水0.82kg,电耗5.5kW· h
主装置占地
大
较小
第二部分 甲裂工段工艺介绍
1.工艺原理
• 本工艺以来源方便的甲醇和脱盐水为原料,在220~280℃下,专用催化剂 上催化转化为组成为主要含氢和二氧化碳转化气。 • 其原理如下: • 主反应: CH3OH=CO+2H2 +90.7 KJ/mol • CO+H2O=CO2+H2-41.2 KJ/mol
氢气纯度可达99.9 %、氧气纯度可达99.5 %。若进一步经纯化装置处理,氢 气的最高纯度可达99.9999 %。
4.甲醇裂解制氢
• 甲醇裂解制氢:250oC,1.5MPa下,甲醇和水的混合液经过预热、气化后, 进人转化反应器,在催化剂(双功能催化剂)作用下,同时发生甲醇的催化裂解 反应和一氧化碳的变换反应,生成约75%的氢气和约25%的二氧化碳以及少 量杂质。
3.主要控制指标
原料汽化过热
1. 物料量 原料甲醇流量 原料液流量 2.温度 汽化过热器进料温度 汽化过热器底部温度 汽化过热器顶部温度 3.汽化过热器压力 4.原料液组成: 甲醇 水
200~ 330kg/h ~950kg/h 130~160℃ 150~160℃ 180~260℃ ~1.2MPa ~50% (Wt) ~50% (Wt)
3.催化剂的升温、还原、活化和钝化
CNZ—1型催化剂有铜、锌、铝的氧化物组成。使用前应进行还原。 1. 还原条件: 还原压力:常压 还原空速:1000时-1 还原气:含H2 0.5~10%的纯氮气(或脱硫天然气) 2.还原气质量:O2<0.1% H2O<0.2% S<0.1ppm 氧化物<0.1ppm 油雾极微 3.升温还原程序 还原前必须检查还原用N2。并使其处于最佳状态。还原过程中如有事故、 停电(或鼓风机坏了)等必须马上停止进入H2
组成 含量%(重 量) CuO >60 ZnO 5~15 Al2O3 5~15 Na2O <0.1 烧失重 ≤10
2.催化剂的包装、贮存和装卸
1.催化剂用塑料袋包装后装入铁桶内。贮存在室内,严防受潮、受震和毒物污染。搬运过程 中不要在地上滚动。 不能从高于0.5米的地方落下,或撞击。 2.在正常情况下,催化剂可以贮存一年以上,对催化剂的活性和物理性能不会影响。 3.催化剂装入反应其前,应用3mm筛子过筛,除渠少量粉末。并检查反应器有无堵塞物或遗 留工具等。 4.催化剂装入反应器时,采用专用布袋或胶管。将催化剂装入布袋再导入反应管中填装,直 至管板表面为止。装填时应防止催化剂架桥。要求每根反应管所装催化剂数量相同,高度相 同。 5.操作人员在装填催化剂时,严禁直接在催化剂上行走、踩踏。应在催化剂上垫木板,站在 木板上操作。防止催化剂破碎。 6.催化剂装填完毕后,用空气或氮气将管内和管板上的催化剂粉末清除干净。 7.催化剂使用前要进行还原活化。如需卸出活化后的催化剂,应对催化剂进行钝化。
建议用30Kt/y以上规模合成甲醇装置产品,运输过程无污染;严禁使用回收 脱盐水: 符合国家GB12145-89P要求,且氯离子含量小于或等于3ppm 电导率 ≤20μs/cm
第三部分 CNZ—甲醇制氢催化剂
Z—甲醇制氢催化剂
cNZ---1型催化剂是一种以铜为活性组分。由铜、锌、铝等的氧化物组成的 新型催化剂。其对甲醇蒸汽转化制氢和二氧化碳具有高活性和良好的选择性。 主要特性 型号:CNZ—1型 外观颜色、外观尺寸和形状:催化剂为黑色圆柱体。表面光滑,有光泽。 公称尺寸:φ5×5毫米 化学组成(重量%) 1. 堆密度:0.85~1.15公斤/升 2. 机械破碎强度:≥60牛[顿]/厘米
成熟 高 ~1.3
适用规模
(Nm3· -1) h 最高纯度/% 杂质种类 建设地点
>1000
20~2500
2~300(单槽)
99.999 CO2、CO、CH4 受限于天然气的供应
99.999 CO2、CO 较自由:要求在合理的 距离内有甲醇供应
99.9999 O2、H2O 自由:几乎不存在 建设地域限制 较大
反应器温度(℃)
钝化气 甲醇/N2 氧含量(%) 0 0 0.1 1 5
需要时间(小时)
≥100 100~150 ≤50 <60 <60
甲醇 N N N N
4 8 5
<60
O
100
5
4.催化剂保护
1、在任何情况下,催化剂层温度禁止超过300℃。
2、还原后的催化剂绝对禁止与氧气或空气接触。 3、催化剂使用中应尽量避免中途停车。每停一次车,尽管采取了钝化或氮气 保护操作, 还是会影响催化剂使用寿命。 4、催化剂的升温和降温都必须缓慢进行,禁止急速升温和降温。 5、在满足生产能力、产率的前提下,催化剂应在低温下操作,有利于延长催 化剂使用寿命。 6、绝对禁止含硫、磷、卤素元素等有毒物质混入系统,以免造成催化剂中毒。 7、对装置使用的原料甲醇、脱盐水、氮气、氢气等必须符合要求,严格规范 检测程序。 8、如发现有异常特别是反应系统异常,应立即停车分析检查,排除后再开车。
累计时间(hr)
2 4 8 18 23 31 33
200
200~230 230 230 230
恒温、加2%H2
升温、加2%H2 恒温、加2%H2 恒温、加5%H2 恒温、加10%H2
0
10 0 0 0
2
3 8 2 2
35
38 46 48 50
还原终点的判断:还原反应出口气中H2浓度接近进口气浓度。不再消耗H2,也 不产生更 水。便可认为以到还原终点了。至此还原完毕。 注*:150~200℃的升温阶段必须更加严格控制。操作时密切注视反应管—— 催化剂床的温度变化。如发现催化剂床温度急剧上升,有超温现象出现时。立 即停止加入氢气或关小加入氢气量,并停止升温。待超温现象消除后再按正常 操作进行。 注*:若加入10%H2含量有困难,可改为加入5%H2气量操作。但相应要延 长加H2时间,直至进出口氢含量相等为止。以保证催化剂充分还原。 4.还原结束后,停止加入氢气,关小氮气量至原氮气流量的80%。加 入新鲜水甲醇。起始甲醇含量为正常开车时水甲醇加入量的20%(加入水甲醇 前,水甲醇预热、汽化段必须先控制在正常开车时的温度值)待反应器温度指 示有明显下降时,再按上述要求再减少氮气量并再增加加入水甲醇量。如此操 作直至全部氮气替换水甲醇,便进入正常开车。
区间(℃)
80~110 110 110~150 150~200* 200 200 200
阶段
升温、纯N2气 升温、纯N2气 升温、加0.5%H2 升温、加0.5%H2 恒温、加0.5%H2 恒温、加1%H2 恒温、加1.5%H2
升温速度(℃/hr)
15 0 10 5 0 0 0
时间(hr)
2 2 4 10 5 8 2
甲醇裂解制氢
部 门:公用工程部 讲解人:王 小 波 时 间:2013-9-12
制 氢装置组成
生产装置由导热油加热工段
、甲醇裂解工段和变压吸附提氢(PSA)