煤气回收量计算
钢铁企业大气污染物排放量核算方法
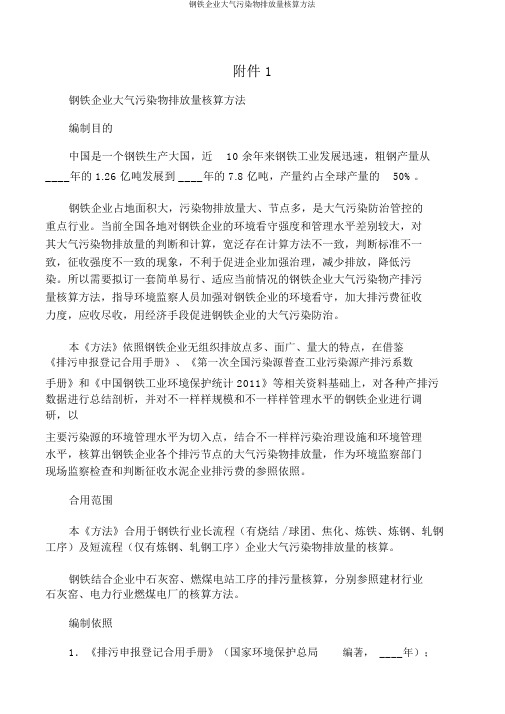
附件 1钢铁企业大气污染物排放量核算方法编制目的中国是一个钢铁生产大国,近10 余年来钢铁工业发展迅速,粗钢产量从____年的 1.26 亿吨发展到 ____年的 7.8 亿吨,产量约占全球产量的50%。
钢铁企业占地面积大,污染物排放量大、节点多,是大气污染防治管控的重点行业。
当前全国各地对钢铁企业的环境看守强度和管理水平差别较大,对其大气污染物排放量的判断和计算,宽泛存在计算方法不一致,判断标准不一致,征收强度不一致的现象,不利于促进企业加强治理,减少排放,降低污染。
所以需要拟订一套简单易行、适应当前情况的钢铁企业大气污染物产排污量核算方法,指导环境监察人员加强对钢铁企业的环境看守,加大排污费征收力度,应收尽收,用经济手段促进钢铁企业的大气污染防治。
本《方法》依照钢铁企业无组织排放点多、面广、量大的特点,在借鉴《排污申报登记合用手册》、《第一次全国污染源普查工业污染源产排污系数手册》和《中国钢铁工业环境保护统计 2011》等相关资料基础上,对各种产排污数据进行总结剖析,并对不一样样规模和不一样样管理水平的钢铁企业进行调研,以主要污染源的环境管理水平为切入点,结合不一样样污染治理设施和环境管理水平,核算出钢铁企业各个排污节点的大气污染物排放量,作为环境监察部门现场监察检查和判断征收水泥企业排污费的参照依照。
合用范围本《方法》合用于钢铁行业长流程(有烧结 / 球团、焦化、炼铁、炼钢、轧钢工序)及短流程(仅有炼钢、轧钢工序)企业大气污染物排放量的核算。
钢铁结合企业中石灰窑、燃煤电站工序的排污量核算,分别参照建材行业石灰窑、电力行业燃煤电厂的核算方法。
编制依照1 / 212.《第一次全国污染源普查工业污染源产排污系数手册》(第八分册黑色金属冶炼及压延加工业);3.《干净生产标准钢铁行业(烧结)》(HJ/T426-2008);4.《干净生产标准炼焦行业》(HJ/T126-2003);5.《干净生产标准钢铁行业(高炉炼铁)》(HJ/T427-2008);6.《干净生产标准钢铁行业(炼钢)》(HJ/T428-2008);7.《中国钢铁工业环境保护统计 2011》(中国钢铁工业协会信息统计部);8.《钢铁烧结、球团工业大气污染物排放标准》(GB 28662-2012);9.《炼焦化学工业污染物排放标准》(GB16171-2012);0.《炼铁工业大气污染物排放标准》(GB 28663-2012);1.《炼钢工业大气污染物排放标准》(GB 28664-2012);2.《产业结构调整指导目录(____年本)(修正)》。
转炉煤气全回收实验
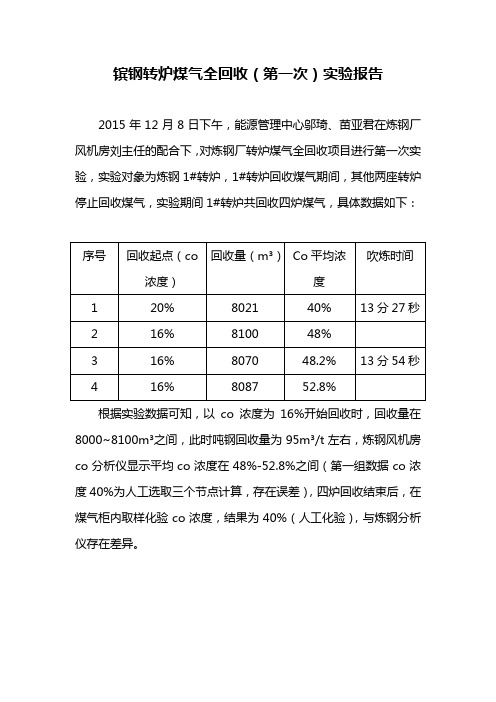
2015年12月8日下午,能源管理中心邬琦、苗亚君在炼钢厂风机房刘主任的配合下,对炼钢厂转炉煤气全回收项目进行第一次实验,实验对象为炼钢1#转炉,1#转炉回收煤气期间,其他两座转炉停止回收煤气,实验期间1#转炉共回收四炉煤气,具体数据如下:序号回收起点(co回收量(m³)Co平均浓度吹炼时间浓度)1 20%802140%13分27秒2 16%810048%3 16%807048.2%13分54秒4 16%808752.8%根据实验数据可知,以co浓度为16%开始回收时,回收量在8000~8100m³之间,此时吨钢回收量为95m³/t左右,炼钢风机房co分析仪显示平均co浓度在48%-52.8%之间(第一组数据co浓度40%为人工选取三个节点计算,存在误差),四炉回收结束后,在煤气柜内取样化验co浓度,结果为40%(人工化验),与炼钢分析仪存在差异。
炼钢厂通过对第一次实验报告数据进行统计分析后,认为在吹炼过程中实时调节二文喉口开度可提高转炉煤气回收量,具体改进方案如下:将吹炼过程分为四个阶段,每个阶段喉口开度通过自动化程序设定一个固定值,如下表。
吹炼时间(min)喉口开度(mm)0-4 2004-12 26012-停吹260停吹后190通过以上改进措施,炼钢厂风机房工作人员和能管中心相关人员于2015年12月13日下午对炼钢1#转炉进行第二次回收实验,具体数据如下:回收量(m³)Co平均浓度吹炼时间序号回收起点(co浓度)1 16%7801 47% 12分22秒2 16%7723 46.3% 12分58秒3 16%8145 48.3% 12分31秒备注:煤气柜人工化验co浓度为43%通过对比两次实验数据可知,在回收起点相同的前提下,回收煤气量与co平均浓度与第一次实验数据差异不大,但是第二次实验吹炼时间与第一次实验相比,缩短一分钟,所以可推导出结论:若在同时保证回收起点和吹炼时间相等的条件下,第二次实验每炉可多回收煤气1000-1100m³(回收瞬时流量为65000-68000m³/h),此时吨钢回收转炉煤气量约为107-110m³/t,所以,通过对喉口开度的改进,使吨钢回收量提高约12m³/t(co平均浓度由50%下降到47%)。
炉顶料罐均压煤气回收方案

按每天料批150批,作业天数350天计
算,年煤气发电产生效益:
18.1×150×2×350=1900500元(190.05万 元)
四、设计、生产中的相关技术方案
工艺流程:将炉顶料罐均压煤气在均放管道上,引出一 路煤气沿煤气下降管引到干法除尘箱体,除尘后由箱体 引入调压阀组后净煤气管道。达到均压煤气净化、回收 的目的。
三、效益分析
以唐钢南区3200高炉为例,效益测算: 回收放散的煤气量 :
P1V1/T1=P2V2/T2 P1:顶压 335kPa P2:表态压力 100kPa V1:料罐容积 72M3 V2:相应净煤气体积 M3 按煤气温度 T1=T2=70℃ V2=241.2M3
回收70℃煤气量:V=241.2-72=169.2 M3,折 合成表态体积为:V标=144.5M3
长了均放时间的弊端,提出的氮气填充法直接采用氮气均压,下料同时 对料罐进行补压,下料结束后关闭下料阀和供氮气阀门,对料罐内氮气 进行排放,实现放散气体洁净,煤气无外排。 (3)煤气引射法:通过采用高压煤气引射低压煤气的方法,将炉顶料罐排 放到布袋除尘器的低压煤气引入净煤气管网。实现料罐煤气的全部回收。 引射效率可达1:10以上,即一立方米高压煤气可将10立方米的低压煤气 引入净煤气管网。
2、炉顶料罐煤气回收工艺流程
3、炉顶料罐煤气回收工艺说明
从高炉料罐均压放散的荒煤气经均压放散管道进入旋风除尘器初步除尘后, 进入与之串联的布袋除尘器形成净煤气, 布袋除尘器后串联引射器,净煤气 在引射器的作用下,被快速引射进入净煤气管网中,实现称量料罐均压放散 煤气的快速放散和回收。引射器的引射动力源是高炉煤气布袋除尘器后的高 压净煤气。通过引射器的引射作用将布袋除尘器内抽成一定程度真空,当料 罐放散煤气时,瞬时将料罐压力降到大气压力。压力达到或稍低于大气压力 时关闭旋风除尘器后通往布袋除尘器的均放阀。引射器可继续引射布袋除尘 器内的净煤气,达到一定真空度要求后停止引射器工作,或在料罐煤气放散 前启动喷射器,使布袋除尘器内达到一定真空度。
转炉煤气理论计算
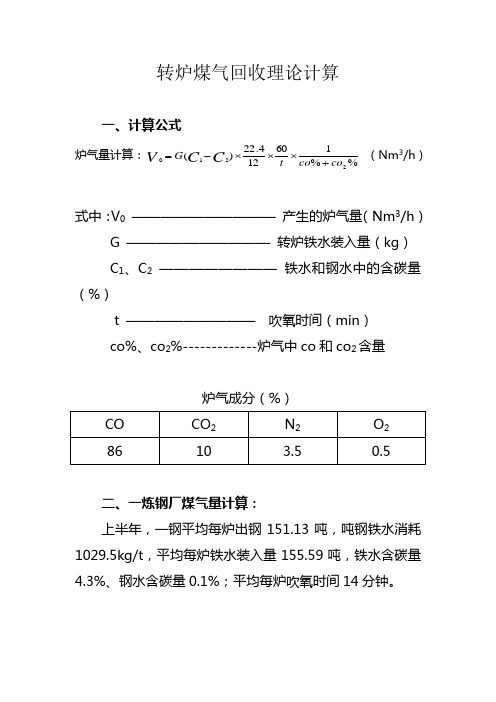
转炉煤气回收理论计算一、计算公式炉气量计算: %%160124.22)(2210co co tG C C V+⨯⨯⨯-= (Nm 3/h )式中:V 0 —————————— 产生的炉气量(Nm 3/h )G —————————— 转炉铁水装入量(kg ) C 1、C 2 ———————— 铁水和钢水中的含碳量(%) t ————————— 吹氧时间(min ) co%、co 2%-------------炉气中co 和co 2含量炉气成分(%)二、一炼钢厂煤气量计算:上半年,一钢平均每炉出钢151.13吨,吨钢铁水消耗1029.5kg/t ,平均每炉铁水装入量155.59吨,铁水含碳量4.3%、钢水含碳量0.1%;平均每炉吹氧时间14分钟。
炉气量10.086.011460124.22)001.0043.0(1555900+⨯⨯⨯-⨯=V= 54457(Nm 3/h )由于铁水成分不稳定,喷溅时炉口粘渣,另外炼钢工需要观察炉口火焰进行炼钢操作,造成烟罩降不到位,高温炉气中的CO 部分在炉口处遇空气燃烧,按炉气中20%的CO 燃烧(即燃烧系数α=0.2)计算生成的烟气量:V = (1+1.88α×CO%)V 0= (1+1.88×0.2×0.86)×54475 = 72090 (Nm 3/h )烟气中CO 计算:CO% =(1-α)×86% VV 0⨯=(1-0.2)×867209054475⨯ =52%(1570kcal/m 3)一钢回收的煤气在风机入口为53℃左右的湿煤气,需将烟气量换算成煤气量: )273273)(804.01t d V V++=(煤气式中:d ----------------------煤气含水量(kg/m 3) t ---------------------煤气温度(℃))273273)(804.01t d V V ++=(煤气=)27353273)(804.015.0172090++⨯(=102137 (m 3/h ) 煤气中CO 含量为:%100804.0804.0%%⨯+⨯=dCO CO 煤气=%10015.0804.0804.052.0⨯+⨯=44%假如在冶炼过程中煤气全部回收,回收量为102137×14/60÷151.13=157.7m 3/t ,按每炉回收11分钟,吨钢回收量124m 3/t 。
提高120t转炉煤气回收量的生产实践
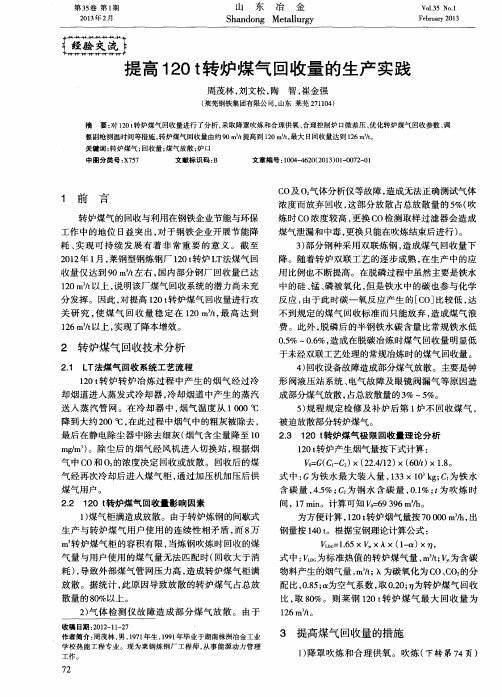
提高 1 2 0 t 转炉煤气 回收量 的生产 实践
周茂林 , 刘文松 , 陶 智, 崔金强
( 莱芜钢铁集 团有限公 司, 山东 莱芜 2 7 1 1 0 4 ) 摘 要: 对1 2 0t 转炉煤气 回收量进行 了分析 , 采取 降罩 吹炼和合理供氧、 合理控制炉 口微差压 、 优化转炉煤气 回收参数 、 调
1 2 0 t 转炉产 生烟气量按 下式计算 :
V o = G ( c 一 C : ) ×( 2 2 . 4 / 1 2 ) ×( 6 0 / t ) ×1 . 8 。
气 中C O和 O 气柜 , 通 过加 压机 加压 后供
生产 与转 炉 煤气 用 户使 用 的连 续 性相 矛 盾 , 而8 万
r n 3 转 炉煤 气 柜 的容 积 有 限 , 当炼钢 吹炼 时 回收 的煤
气量与用户使用的煤气量无法匹配时( 回收大于消 耗) , 导致 外部 煤气 管 网压 力高 , 造 成转 炉煤 气柜 满
中的硅 、 锰、 磷被氧化 , 但是铁水 中的碳也参与化学 反应 , 由于 此 时碳一 氧 反 应产 生 的 [ C O ] 比较低 , 达 不 到 规定 的煤 气 回收标 准而 只 能放弃 , 造 成煤 气 浪
费 。此外 , 脱 磷后 的半 钢铁 水碳 含量 比常规 铁水 低 0 . 5 % 0 . 6 %, 造 成在脱 碳 冶炼 时煤 气 回收量 明显 低
第3 5 卷 第1 期
2 0 1 3 年2 月
L. ‘ L 址 L L
山 东 冶 金
S h a n d o n g Me t a l l u r g y
V0 1 . 3 5 No . 1
生活垃圾燃烧烟气量计算公式
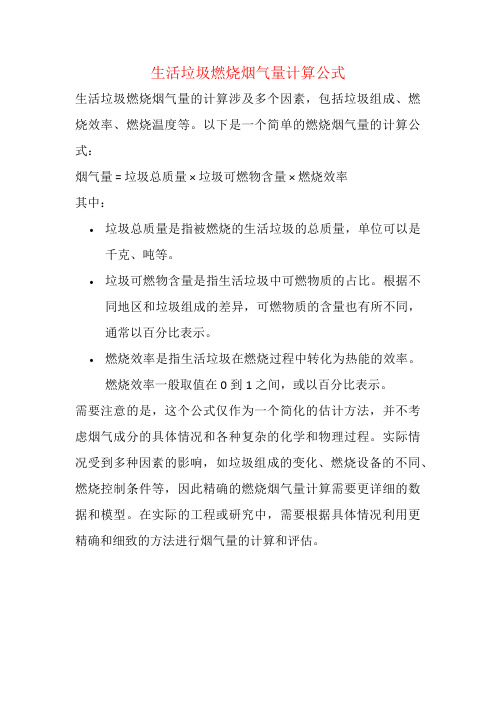
生活垃圾燃烧烟气量计算公式
生活垃圾燃烧烟气量的计算涉及多个因素,包括垃圾组成、燃烧效率、燃烧温度等。
以下是一个简单的燃烧烟气量的计算公式:
烟气量 = 垃圾总质量 × 垃圾可燃物含量 × 燃烧效率
其中:
•垃圾总质量是指被燃烧的生活垃圾的总质量,单位可以是千克、吨等。
•垃圾可燃物含量是指生活垃圾中可燃物质的占比。
根据不同地区和垃圾组成的差异,可燃物质的含量也有所不同,
通常以百分比表示。
•燃烧效率是指生活垃圾在燃烧过程中转化为热能的效率。
燃烧效率一般取值在0到1之间,或以百分比表示。
需要注意的是,这个公式仅作为一个简化的估计方法,并不考虑烟气成分的具体情况和各种复杂的化学和物理过程。
实际情况受到多种因素的影响,如垃圾组成的变化、燃烧设备的不同、燃烧控制条件等,因此精确的燃烧烟气量计算需要更详细的数据和模型。
在实际的工程或研究中,需要根据具体情况利用更精确和细致的方法进行烟气量的计算和评估。
焦炉煤气发生量计算公式
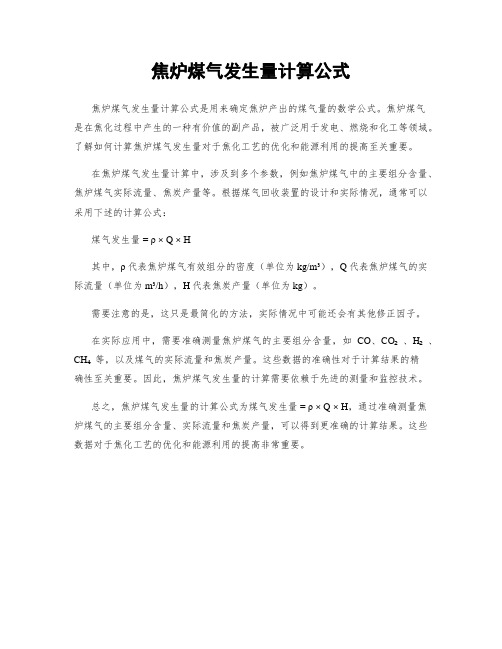
焦炉煤气发生量计算公式
焦炉煤气发生量计算公式是用来确定焦炉产出的煤气量的数学公式。
焦炉煤气
是在焦化过程中产生的一种有价值的副产品,被广泛用于发电、燃烧和化工等领域。
了解如何计算焦炉煤气发生量对于焦化工艺的优化和能源利用的提高至关重要。
在焦炉煤气发生量计算中,涉及到多个参数,例如焦炉煤气中的主要组分含量、焦炉煤气实际流量、焦炭产量等。
根据煤气回收装置的设计和实际情况,通常可以采用下述的计算公式:
煤气发生量= ρ × Q × H
其中,ρ代表焦炉煤气有效组分的密度(单位为kg/m³),Q代表焦炉煤气的实际流量(单位为m³/h),H代表焦炭产量(单位为kg)。
需要注意的是,这只是最简化的方法,实际情况中可能还会有其他修正因子。
在实际应用中,需要准确测量焦炉煤气的主要组分含量,如CO、CO₂、H₂、CH₄等,以及煤气的实际流量和焦炭产量。
这些数据的准确性对于计算结果的精
确性至关重要。
因此,焦炉煤气发生量的计算需要依赖于先进的测量和监控技术。
总之,焦炉煤气发生量的计算公式为煤气发生量= ρ × Q × H,通过准确测量焦炉煤气的主要组分含量、实际流量和焦炭产量,可以得到更准确的计算结果。
这些数据对于焦化工艺的优化和能源利用的提高非常重要。
浅析转炉煤气回收的影响因素及提高措施
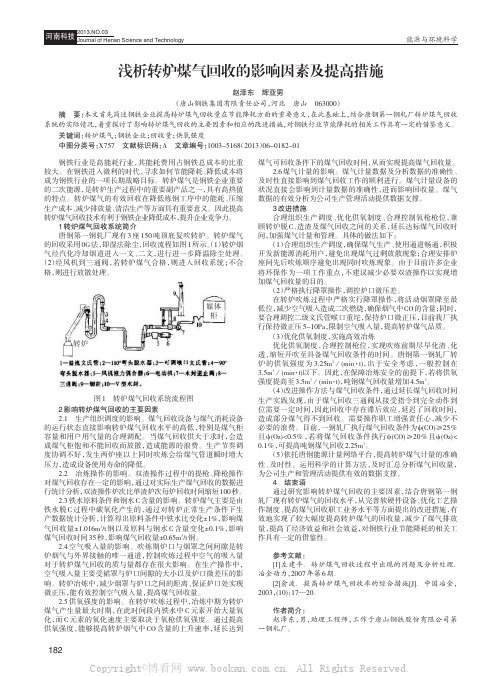
钢铁行业是高能耗行业,其能耗费用占钢铁总成本的比重较大。
在钢铁进入微利的时代,寻求如何节能降耗、降低成本将成为钢铁行业的一项长期战略目标。
转炉煤气是钢铁企业重要的二次能源,是转炉生产过程中的重要副产品之一,具有高热值的特点。
转炉煤气的有效回收在降低炼钢工序中的能耗、压缩生产成本、减少排放量、清洁生产等方面具有重要意义。
因此提高转炉煤气回收技术有利于钢铁企业降低成本,提升企业竞争力。
1转炉煤气回收系统简介唐钢第一钢轧厂现有3座150吨顶底复吹转炉。
转炉煤气的回收采用0G法,即湿法除尘,回收流程如图1所示。
(1)转炉烟气经汽化冷却烟道进入一文、二文,进行进一步降温除尘处理。
(2)经风机到三通阀,若转炉煤气合格,则进入回收系统;不合格,则进行放散处理。
2影响转炉煤气回收的主要因素2.1生产组织调度的影响。
煤气回收设备与煤气消耗设备的运行状态直接影响转炉煤气回收水平的高低,特别是煤气柜容量和用户用气量的合理调配。
当煤气回收供大于求时,会造成煤气柜饱和不能回收而放散,造成能源的浪费。
生产节奏调度协调不好,发生两炉座以上同时吹炼会给煤气管道瞬时增大压力,造成设备使用寿命的降低。
2.2冶炼操作的影响。
双渣操作过程中的提枪、降枪操作对煤气回收存在一定的影响,通过对实际生产煤气回收的数据进行统计分析,双渣操作炉次比单渣炉次每炉回收时间缩短100秒。
2.3铁水原料条件和钢水C含量的影响。
转炉煤气主要是由铁水脱C过程中碳氧化产生的,通过对转炉正常生产条件下生产数据统计分析,计算得出原料条件中铁水比变化±1%,影响煤气回收量±1.016m3/t钢以及原料与钢水C含量变化±0.1%,影响煤气回收时间35秒,影响煤气回收量±0.65m3/t钢。
2.4空气吸入量的影响。
吹炼期炉口与烟罩之间间隙是转炉烟气与外界接触的唯一通道,控制吹炼过程中空气的吸入量对于转炉煤气回收的质与量都存在很大影响。
gsc的物料平衡和热平衡计算

gsc的物料平衡和热平衡计算GSC(高炉煤气干燥除尘系统)是一种用于高炉喷吹系统的煤气清洁设备,它的物料平衡和热平衡计算是非常重要的。
1. 物料平衡计算GSC中的物料平衡计算主要是指干燥、粉碎、输送和回收等过程中各种物料的量的计算。
其计算方法如下:(1)4种物料的流量计算GSC中的4种物料分别是煤气、煤粉、水分和粉尘。
它们的流量应分别进行计算,其中煤气和煤粉的计算方法为:煤气和煤粉流量 =煤气和煤粉的质量控制 + 称量误差校正。
而水分和粉尘的计算方法为:水分和粉尘流量 = 流速测量器读数× 面积。
(2)各物料的贮存计算GSC中的各种物料都需要进行贮存,它们的贮存时间应进行计算。
计算公式为:贮存物料的总质量 = 流量× 时间。
(3)水分的蒸发计算GSC中的水分会随着煤气一起被带出去,需要进行计算。
计算公式为:水分的蒸发量 = 含水量× 煤气的质量。
2. 热平衡计算GSC中的热平衡计算主要是指煤气、煤粉和水分等热量的计算。
其方法如下:(1)煤气的热量计算煤气的热量可以通过其温度、压力和流量进行计算。
计算公式为:煤气的热量 = 煤气流量× 煤气的热值。
(2)煤粉的热量计算煤粉的热量可以通过其温度和质量进行计算。
计算公式为:煤粉的热量 = 煤粉的质量× 煤粉的比热× 煤粉的温度。
(3)水分的热量计算水分的热量可以通过其水份含量、温度和质量进行计算。
计算公式为:水分的热量 = 水分的质量× (水分的温度 - 煤气的温度)×水的比热。
综上所述,GSC的物料平衡和热平衡计算是其正常运行的基础和保障,这也说明物料和热量的平衡管理对于高炉的稳定和效率非常重要。
转炉干法一次除尘[整理]
![转炉干法一次除尘[整理]](https://img.taocdn.com/s3/m/c2b2b07226d3240c844769eae009581b6bd9bd8e.png)
转炉已一次干法除尘技术1 转炉干法除尘技术背景转炉煤气干法除尘是鲁奇(Lurgi)和蒂森(Thyssen)公司20世纪60年代末合作开发的。
转炉干法除尘的基本原理是对经汽化烟道后的高温煤气进行喷水冷却,将煤气温度由900℃~1000℃降低到200℃左右,采用电除尘器进行处理。
转炉干法除尘系统主要包括:蒸发冷却器、静电除尘器、煤气切换、煤气冷却器、放散烟囱、除灰系统等。
与湿法除尘(OG)法比较,干法除尘有以下优点:.除尘效率高。
净化后烟气含尘量为10mg/Nm3~20mg/Nm3,如有特殊要求可降至5mg/Nm3。
.系统阻力小,耗能低,风机运行费低,寿命长,维修工作少。
.在水、电消耗方面具有明显的优越性。
.不需要泥浆沉淀池及污泥处理设施。
.含铁干粉灰压块后可直接供转炉利用。
2 首钢京唐干法除尘设施的技术特点及实施情况首钢京唐炼钢厂采用2+3的“全三脱”两步法冶炼生产模式。
配置2座300t脱磷转炉和3座300t脱碳转炉。
脱磷转炉平均冶炼周期25min ,脱碳转炉平均冶炼周期28min。
正常情况下,实行2+3转炉全量脱磷、脱碳处理,转炉与板坯连铸机采用3对3的高效快节奏的生产模式。
在欧洲转炉干法除尘技术应用非常普遍,但是欧洲钢厂均没有采用“全三脱”转炉两步法冶炼技术。
在日本“三脱”转炉两步法冶炼技术应用很多,却没有采用转炉干法除尘的实例。
首钢京唐钢铁公司是世界上第一个在“全三脱”两步法冶炼的大型快节奏转炉上采用干法除尘技术的钢厂。
该工艺特点是:“三脱”处理后的铁水,已基本不含Si,C、Mn 含量也有较大的降低。
但是在工业化生产中仍需解决以下两个问题,对“三脱”处理后铁水进行吹炼,开吹后的炉气量和炉气中的CO含量是否会显著增加?如采用干法除尘是否会增加卸爆发生频率?为了实现在“全三脱”冶炼的转炉上应用煤气干法电除尘技术,技术团队对国外进行了考察调研和认真分析研究。
分析结论认为:与常规吹炼相比,“三脱”铁水吹炼前期炉气中CO比率不会增加,这对减少卸爆有利。
转炉煤气回收量的分析与实践

转炉煤气回收量的分析与实践摘要:本文通过物料平衡的方法,计算出转炉煤气回收的极限量,并结合实际生产操作,放宽转炉煤气回收条件,将转炉实际最大回收量与极限量进行对比,并从电能利用方面分析提高转炉煤气回收量的经济性。
关键词:转炉煤气极限回收经济性1 概述随着国家能源政策的进一步加强,钢铁市场竞争的越发剧烈,各钢铁企业在追求钢材品质的同时,更在力争如何降低吨钢能耗,而在整个冶炼工序中,唯一能实现负能冶炼的就是转炉炼钢环节。
转炉煤气回收占整个转炉工序能源回收的80%-90%,是降低炼钢能耗,实现负能炼钢的关键环节,因此,各企业都十分重视转炉煤气回收,尽可能的多回收转炉煤气。
目前,对如何提高转炉煤气回收的研究较多,但对于煤气回收量的潜力有多大的研究较少,从而导致一些企业对吨钢回收量预估不足,后续煤气柜和加压系统配置能力偏低,一旦想提高吨钢煤气回收量则困难重重,设备能力受限,造成能源的浪费;同时也有些企业为了追求吨钢回收量,过大的配置煤气柜容量,以及加压机风量的配置,提高了工程一次投资成本和运行成本,设备能力上也是大马拉小车,造成一定程度的浪费。
本文基于碳平衡原理,建立转炉煤气回收量计算模型,计算了转炉煤气回收量的极限值,同时放宽回收条件,从实际生产中最大限度的提高吨钢回收量,得到生产数据,进而根据实际回收量与极限回收量对比确定转炉煤气回收的潜力,为后续回收设施的选型提供可靠依据。
2 转炉煤气极限回收量计算模型根据冶金反应原理,转炉烟气主要是由原料中碳氧化产生的,含碳原料主要有铁水和炭质发热剂。
原料中的碳以一定的比例氧化成CO、CO,以炉气形式排2出,经炉口处吸入一定的空气形成烟气。
转炉烟气根据回收设备条件和回收技术水平,回收成可利用的能源介质即转炉煤气。
按物料平衡和热平衡建立转炉煤气回收量计算模型,如下:式中:折算为标准热值后的转炉煤气量,m3/t;3018——CO热值,Kcal/m32000——标准热值,Kcal/m3碳氧化生成的炉气量,m3/t;炭质发热剂生成的炉气量,m3/t;空气吸入系数,即实际空气吸入量与转炉气完全燃烧所需的理论空气量的比值;转炉煤气回收比,即煤气回收量与转炉煤气发生量的比值,%;的分配比。
转炉煤气回收规律及其影响因素研究
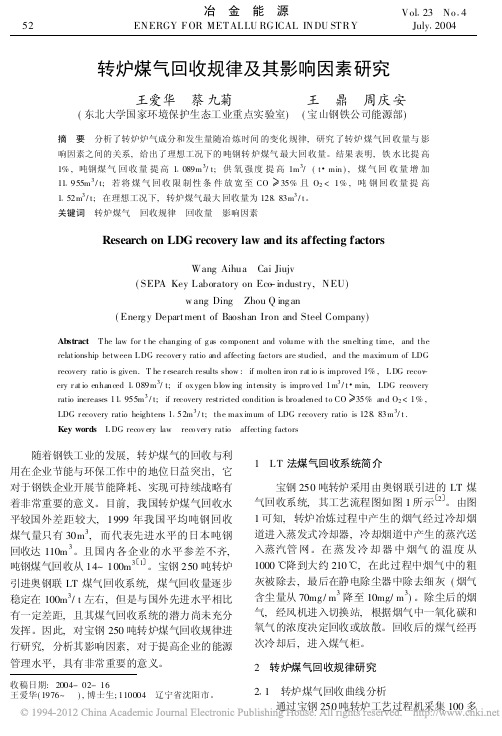
续时间, 均随原料条件、供氧强度和钢种等因素 而变化。
( 2) 回收平稳期是煤气回收过程中的重要阶 段, CO 浓度在此期间处 于最高值, CO 浓度越 高, 煤气热 值越高, 折算 成标准 热值 ( 2000 @ 4118kJ/ m3) 体积量越大。
(3) CO 和 O2 浓度散点始终围绕图中的一 条黑实线, 它是 CO 和 O2 浓度随冶炼时间变化 的均值线, 代表了宝钢 250 吨转炉煤气 回收中 CO 和 O2 浓 度的变化规律。因此重 点研究均值 线中 CO 和 O2 浓度随吹炼时间的变化规律, 以 及转炉煤气回收量与其影响因素之间的关系。 212 影响转炉煤气回收因素的一般分析
( 100- O2<)
N2-
V干
( 3Fe+
V
< O2
017 78FeO)
式中
CO、H2、O2、N2 ) ) ) 风机前干烟气成分
( %) O2< ) ) ) 氧枪供氧的氧气纯度 ( % ) L) ) ) 烟尘浓度 ( mg/ m3) Fe ) ) ) 烟尘中铁的含量 ( % )
FeO ) ) ) 烟尘中氧化亚铁的含量 ( % ) 经过计算可知, 目前 250 吨转炉冶炼中的空 气吸入系数 A平均在 0109~ 0116 之间。 A越小, 煤气热值越高。通过严格遵守降罩操作制度, 控 制炉口处于微正压 ( 约 0~ 60Pa) , 可以使空气
2 转炉煤气回收规律研究
211 转炉煤气回收曲线分析 通过宝钢 250 吨转炉工艺过程机采集 100 多
Vol123 No14
冶金能 源
Ju ly1 2004
ENERGY FOR M ET ALL URGICAL INDUST RY
60吨转炉设计
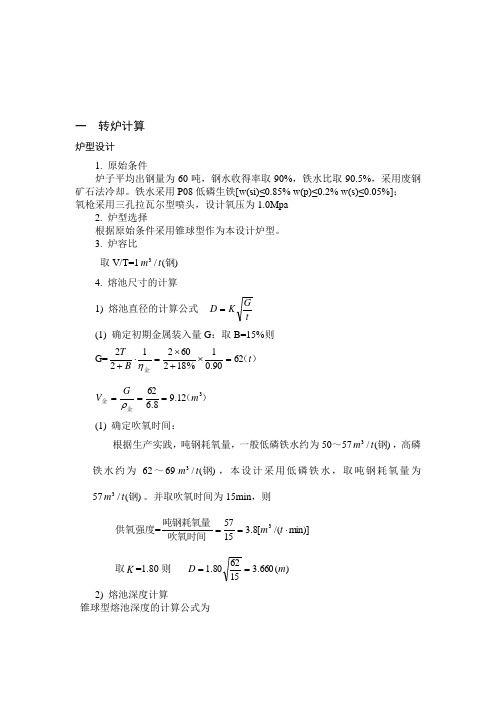
一 转炉计算炉型设计1. 原始条件炉子平均出钢量为60吨,钢水收得率取90%,铁水比取90.5%,采用废钢矿石法冷却。
铁水采用P08低磷生铁[w(si)≤0.85% w(p)≤0.2% w(s)≤0.05%]; 氧枪采用三孔拉瓦尔型喷头,设计氧压为1.0Mpa2. 炉型选择根据原始条件采用锥球型作为本设计炉型。
3. 炉容比取V/T=1)(/3钢t m 4. 熔池尺寸的计算1) 熔池直径的计算公式 tG KD = (1) 确定初期金属装入量G :取B=15%则 G=)(金t B T 6290.01%182602122=⨯+⨯=⋅+η )(金金312.98.662m G V ===ρ (1) 确定吹氧时间:根据生产实践,吨钢耗氧量,一般低磷铁水约为50~57)(/3钢t m ,高磷铁水约为62~69)(/3钢t m ,本设计采用低磷铁水,取吨钢耗氧量为57)(/3钢t m 。
并取吹氧时间为15min ,则 供氧强度=m in)]/([8.315573⋅==t m 吹氧时间吨钢耗氧量取K =1.80则 )(660.3156280.1m D == 2) 熔池深度计算锥球型熔池深度的计算公式为)(162.166.37.066.30363.01.970.00363.02323m D D V h =⨯⨯+=+=金 确定D =3.66m, h =1.162m3) 熔池其他尺寸确定 (1) 球冠的弓形高度:)(3294.066.309.009.01m D h =⨯==(2) 炉底球冠曲率半径:)(026.466.31.11.1m D R =⨯==(3) m D h 3294.09.01== 5. 炉帽尺寸的确定 1) 炉口直径 0d :()m D d 90.166.352.052.00=⨯==2) 炉帽倾角θ:取067=θ3) 炉帽高度帽H)(07.267tan )9.166.3(21tan 2100m d D H =-=-=θ)(锥取mm H 380=口,则整个炉帽高度为:)(口锥帽m H H H 45.238.007.2=+=+=在炉口处设置水箱式水冷炉口炉帽部分容积为:口锥帽)(H d d Dd D H V 202002412ππ+++=)06.1438.09.14)9.19.166.366.3(07.2123222m =⨯⨯++⨯+⨯⨯=ππ6. 炉身尺寸确定1) 炉膛直径D D =膛=3.66m (无加厚段) 2) 根据选定的炉容比为1,可求出炉子总容积为)(容360601m V =⨯= )(帽池总身382.3606.1412.960m V V V V =--=--=3) 炉身高度)(50.366.3482.36422m D V H =⨯=⨯=ππ身身4) 炉型内高)(身帽内m H H h H 112.750.345.2162.1=++=++=由97.166.3112.7H ==膛内H 知符合2.2—1.85范围 7. 出钢口尺寸的确定1) 出钢口直径)(13.0)(136075.16375.163m cm T d T =≈⨯+=+= 2) 出钢口衬砖外径)(78.013.066m d d T ST =⨯== 3) 出钢口长度)(91.013.077m d L T T =⨯== 4) 出钢口倾角β:取015=β8. 炉衬厚度确定炉身工作层选600mm,永久层115mm,填充层90mm,总厚度为600+115+90=805(mm )炉壳内径为27.52805.066.3=⨯+=壳内D炉帽工作层500mm ,炉底工作层选550mm,炉帽永久层为150mm,炉底永久层用标准镁砖立砌一层230mm 粘土砖,平砌三层65×3=195(mm ),则炉底衬砖总厚度为550+230+195=975(mm ),故炉壳内形高度为)087.8975.112.7m H (壳内=+=,工作层材质全部采用镁碳砖。
转炉炼钢煤气回收
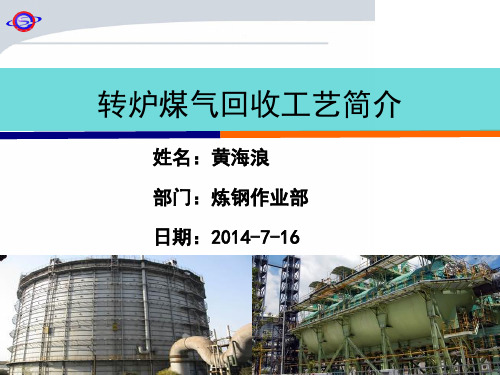
而使烟气中的尘粒与气体分离,净化了气体,而荷电尘粒沉积于极板表
面,当极板上的粉尘越积越厚会使极板间距变小,这时启动振打装置将 极板表面上的灰尘振落,再由刮板链条输送到细灰储灰仓。 从电除尘器的工作原理可以看出电除尘器的工作过程为:气体电离 →尘粒荷电→荷电粒子在电场力的作用下向异极方向移动→荷电粒子沉 积于极板、极线→振打简介
另外,在干式电除尘器进风口和出风口上方分别设
计3个φ1200mm的泄爆阀,当电除尘器内部发生煤气爆
炸使压力达到5000Pa时泄爆阀自动打开卸压,减少过 压对壳体及内部构件造成的破坏。 电场的工作原理
转炉煤气回收工艺简介
阴极丝和阳极板
阴阳极振打
泄爆阀
对3*120t转炉使用了干法除尘,而投产后10天就达到设计能力,
并持续稳定地生产。至今三套“LT”系统均已通过了考核验收。
转炉煤气回收工艺简介
2) 缺点: (1)系统复杂,从而要求设备、仪表仪器质量高,以满足生 产要求;对施工质量要求也高; (2)要求管理和操作水平高,必须对管理和操作人员进行较 完善的培训,并在实际生产中达到熟练操作和维护;并且要 与炼钢工艺操作紧密配合和协调,杜绝野蛮操作; (3)一次投资高。 从以上特点分析,氧气转炉煤气干法净化回收技术具有 独特的优越性,所以被越来越多的国家所采用以取代湿法。 采用干法净化回收技术,不但经济效益明显,且环境效益也 好。
转炉煤气回收工艺简介
煤气冷却器:
当切换站将烟气切换至回收侧时,净化后的煤气温度约 在170℃左右,进入煤气冷却器后,通过冷却水的直接喷淋 冷却,温度可降至70℃以下。对净化煤气进行冷却降温处理 ,其目的是为了使煤气在煤气柜的容积尽可能小,同时还可 以进一步降低烟尘含量,在10mg/Nm³以下。 煤气冷却器为一竖直的圆筒形结构,主要作用是使净化 后的转炉煤气降温。净化后的转炉煤气从煤气冷却器筒体下 部进入,上部流出,冷却器排出的冷却水经降温后循环使用 。冷却后煤气通过管网送入煤气柜。
转炉煤气理论计算

转炉煤气回收吨钢量理论计算前言:1、转炉煤气回收吨钢量的标准定义:一吨铁水在冶炼成合格钢水所产生的CO 量;即煤气柜回收存储的等压状况下的煤气量;现大多钢厂都有误区用加压机以后的流量计算是不准确的。
一、计算公式炉气量计算: %%160124.22)(2210co co t G C C V +⨯⨯⨯-= (Nm 3/h )式中:V 0 —————————— 产生的炉气量(Nm 3/h )G —————————— 转炉铁水装入量(kg ) C 1、C 2 ———————— 铁水和钢水中的含碳量(%)t ————————— 吹氧时间(min )co%、co 2%-------------炉气中co 和co 2含量炉气成分(%)二、一炼钢厂煤气量计算:上半年,一钢平均每炉出钢151.13吨,吨钢铁水消耗1029.5kg/t ,平均每炉铁水装入量155.59吨,铁水含碳量4.3%、钢水含碳量0.1%;平均每炉吹氧时间14分钟。
炉气量10.086.011460124.22)001.0043.0(1555900+⨯⨯⨯-⨯=V = 54457(Nm 3/h )由于铁水成分不稳定,喷溅时炉口粘渣,另外炼钢工需要观察炉口火焰进行炼钢操作,造成烟罩降不到位,高温炉气中的CO 部分在炉口处遇空气燃烧,按炉气中20%的CO 燃烧(即燃烧系数α=0.2)计算生成的烟气量:V = (1+1.88α×CO%)V 0= (1+1.88×0.2×0.86)×54475= 72090 (Nm 3/h )烟气中CO 计算:CO% =(1-α)×86% VV 0⨯ =(1-0.2)×867209054475⨯ =52%(1570kcal/m 3)一钢回收的煤气在风机入口为53℃左右的湿煤气,需将烟气量换算成煤气量: )273273)(804.01t d V V ++=(煤气式中:d ----------------------煤气含水量(kg/m 3)t ---------------------煤气温度(℃))273273)(804.01t d V V ++=(煤气=)27353273)(804.015.0172090++⨯( =102137 (m 3/h )煤气中CO 含量为:%100804.0804.0%%⨯+⨯=dCO CO 煤气=%10015.0804.0804.052.0⨯+⨯=44% 假如在冶炼过程中煤气全部回收,回收量为102137×14/60÷151.13=157.7m 3/t ,按每炉回收11分钟,吨钢回收量124m 3/t 。
煤气柜施工方案

一、方案设计1.总论1.1工程概况由于煤气回收煤气的特殊工况,稀油密封气柜不适合(活塞升降速度慢、满足不了瞬时流量大的要求;对煤气含尘量要求较高)对煤气的回收,国内也没有运用先例,并且容量也偏小,现决定新建的3万立方米气柜选用橡胶膜干式煤气柜。
全部工程包括一座30000m3橡胶膜干式煤气柜及气柜基础、1座煤气加压站和相应的配套设施、煤气回收和输出(用户)管道设施建设以及混合站系统。
1.2设计依据(1)新冶特钢3万m3煤气储配站工程现场条件和业主要求;(2)国家现行的规程、规范及有关标准。
1.3设计原则(1)严格遵守国家现行的规程、规范及有关标准;(2)充分利用现有设施和场地,尽量节省投资;(3)设计采用先进、适用、安全、可靠的技术,有利于集中管理、减少定员和提高经济效益;(4)重视安全、消防和能源计量,提高节能效益,注意环境保护。
1.4工程内容和工程范围1.4.1工程内容新冶特钢3万m3煤气储配站工程包括以下内容及相应的设计:(1)新建1座30,000m3橡胶膜密封型煤气柜及其基础;(2)新建一座煤气加压站(暂定2台煤气加压机,1用、1备);(3)新建站区内的配套公辅设施:•站区内的自动化仪表;•站区内的供配电、照明及防雷接地;•站区内的给、排水及消防设施;•站区工艺管线;•一座综合操作值班室;•站区内电讯和火灾报警;•站区围墙、大门及消防通道;(4)站区外进出管道设施;(5)煤气与高炉煤气混合系统。
1.4.2工程范围本设计方案范围自出口部分的放散烟囱外,至煤气各用户点。
含站区管道(煤气、氮气、蒸汽、上、下水)、低压供电电缆及电讯电缆。
2.煤气柜站区的燃气工艺设施设计根据新冶特钢炼钢3万m3煤气储配站工程现场条件和业主要求,新建转气储配站包括:新建1座30000m3煤气柜及气柜基础1座煤气加压站和相应的配套设施。
现对上述项目中的燃气工艺设施分述如下:30000m3干式煤气柜的总图布置(业主提供原始平面图后规划布置)2.130000m3煤气柜设计2.1.1煤气柜型式的确定干式气柜是国内在八十年代消化吸收国外技术而引进的,分为稀油密封干式气柜和橡胶膜密封干式气柜,现在已广泛运用于冶金、市政、石化等行业,在冶金行业,高炉和焦炉煤气的回收均采用稀油密封干式气柜,而对于煤气含尘量大、瞬时流量变化大的煤气则均采用橡胶膜密封干式气柜。
转炉煤气的回收及利用

黄卫超
工程 师
16 生 94年
18 94年毕业 于 上海 市机 电工业 学校 26 8 9 6465
转炉 煤气 主要 是 由原料 中 的碳 氧化 产生 的 , 因此 原料 条件对 煤气 发生 量 的影 响很 大 。通过对
现 从 事 能 源调 度 工 作 电话
E. i ma i @ b o t e . O mal ln a se 1 C B
煤气 的引入 , 存 在一些 问题需 要探 讨 和优化 。 也
1 转 炉 煤气 回收潜 力
对 于煤气 回收环节 的潜力 有多 大 的研 究 尚不 多见 , 钢在此 方 面作 了一些定 量化 研究 ¨ 。 宝 J
1 1 原 料 因素 .
气加 压 机 一 管 网一 ( 气 混 合 站 ) 用 户 。 炉 煤 一 转
关键 词 : 转炉煤 气 ; 回收 ; O E C R X煤 气
中图分 类 号 : 7 7 文 献标 志码 : 文章 编号 :0 8— 7 6 2 0 ) 3— 0 7— 4 X5 B 10 0 1 ( 0 9 0 0 1 0
Re o e y a i z to fCo e t r G a c v r nd Utl a i n o nv r e s i
c se u s d.Th u h ri r v me t n r c ci g c n e e a r r p s d wh n t e efc fi to u— e f r e mp o e n si e y ln o v r rg sa e p o o e e h fe to nr d t t cn ig COREX a n t e b l n e o h o v re a y t m sf ly c n i e e . g s o h aa c ft e c n e trg ss se i u l o sd r d K e r : o v re a ;r c v r y wo ds c n e rg s e o e y;COREX a t gs
※焦炉荒煤气显热深度回收热力计算分析

第36卷,总第208期2018年3月,第2期《节能技术》ENERGY CONSERVATION TECHNOLOGYVol.36,Sum.No.208Mar.2018,No.2 焦炉荒煤气显热深度回收热力计算分析丁红光1,张忠孝1,曹先常2,潘金荣2,陈时选1(1.上海理工大学能源与动力工程学院,上海 200093;2.上海宝钢节能环保技术有限公司,上海 200093)摘 要:针对焦炉荒煤气显热回收中受热面布置空间小及受热表面结焦致使热回收难以持续等问题,提出下降管多层膜式壁换热结构,且在热回收低温段采取镍涂层、喷氨等除焦措施,对荒煤气显热进行深度回收。
热力计算结果表明:入口流量400Nm3/h、温度750℃的荒煤气在经过上升管换热器回收部分显热后,再通过下降管热回收装置最终出口平均温度可达301.3℃,突破了由于焦油凝析结焦带来的荒煤气出口温度的限制,下降管换热器可产生1.9MPa饱和蒸汽174kg/h,系统总热回收效率高达65%,可实现显热深度回收利用。
关键词:荒煤气;显热回收;下降管;多层膜式壁;热力计算中图分类号:TK115 文献标识码:A 文章编号:1002-6339(2018)02-0156-05 Thermodynamic Calculation Analysis of Full Recoveryof Sensible Heat of Coke-oven Raw GasDING Hong-guang1,ZHANG zhong-xiao1,CAO Xian-chang2,PAN Jin-rong2,CHEN Shi-xuan1 (1.School of Energy and Power Engineering,University of Shanghai for Science and Technology, Shanghai200093,China;2Shanghai Baosteel Energy Tech Co.,Ltd.,Shanghai200093,China)Abstract:In order to solve the problems that there are small space for heating surface and the unsustain⁃able heat recovery because of heating surface coking,existing in the process of coke-oven raw gas of sensible heat recovery,the paper proposes a multi-layer membrane wall heat exchanging structure in downcomer,and it takes some decoking measure in low temperature heat recovery section as well,such as spraying ammonia,nickel coating.The result obtained by thermodynamic calculation shows:the raw gas with inlet flow rate400Nm3/h and the temperature750℃,flowing through the heat exchanger in ris⁃er,are recovered partial sensible heat and then passes through the heat recovery device in downcomer,its average temperature at the downcomer outlet reaches301.3℃,breaking through the limit of the tempera⁃ture brought by the coal tar of condensation and coking,during the running process,the heat exchanger in downcomer can produce174kg/h of1.9MPa saturated vapor,the overall efficiency of heat recovery system reaches up to65%,which can realize the full recovery and utilization for the sensible heat of coke-oven raw gas.Key words:coke-oven raw gas;sensible heat recovery;downcomer;multi-layer membrane wall;ther⁃modynamic calculation收稿日期 2017-06-08 修订稿日期 2017-07-21基金项目:国家重点研发计划课题资助项目(2016YFB0601402)作者简介:丁红光(1991~),男,硕士研究生,主要从事余热回收和节能技术方面研究。
煤气回收量计算范文
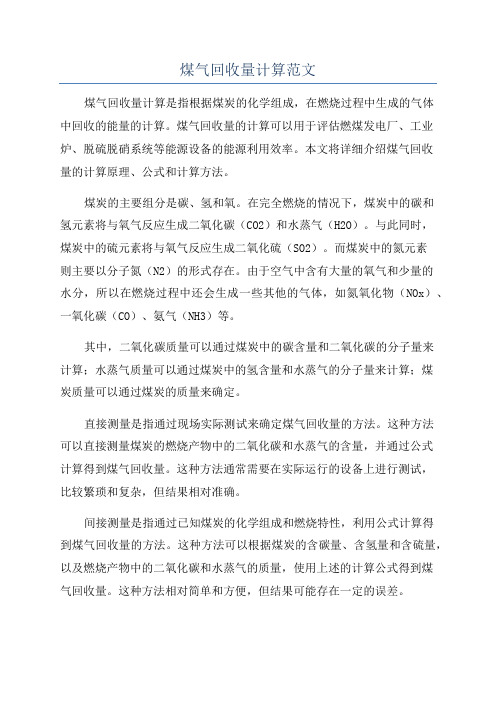
煤气回收量计算范文煤气回收量计算是指根据煤炭的化学组成,在燃烧过程中生成的气体中回收的能量的计算。
煤气回收量的计算可以用于评估燃煤发电厂、工业炉、脱硫脱硝系统等能源设备的能源利用效率。
本文将详细介绍煤气回收量的计算原理、公式和计算方法。
煤炭的主要组分是碳、氢和氧。
在完全燃烧的情况下,煤炭中的碳和氢元素将与氧气反应生成二氧化碳(CO2)和水蒸气(H2O)。
与此同时,煤炭中的硫元素将与氧气反应生成二氧化硫(SO2)。
而煤炭中的氮元素则主要以分子氮(N2)的形式存在。
由于空气中含有大量的氧气和少量的水分,所以在燃烧过程中还会生成一些其他的气体,如氮氧化物(NOx)、一氧化碳(CO)、氨气(NH3)等。
其中,二氧化碳质量可以通过煤炭中的碳含量和二氧化碳的分子量来计算;水蒸气质量可以通过煤炭中的氢含量和水蒸气的分子量来计算;煤炭质量可以通过煤炭的质量来确定。
直接测量是指通过现场实际测试来确定煤气回收量的方法。
这种方法可以直接测量煤炭的燃烧产物中的二氧化碳和水蒸气的含量,并通过公式计算得到煤气回收量。
这种方法通常需要在实际运行的设备上进行测试,比较繁琐和复杂,但结果相对准确。
间接测量是指通过已知煤炭的化学组成和燃烧特性,利用公式计算得到煤气回收量的方法。
这种方法可以根据煤炭的含碳量、含氢量和含硫量,以及燃烧产物中的二氧化碳和水蒸气的质量,使用上述的计算公式得到煤气回收量。
这种方法相对简单和方便,但结果可能存在一定的误差。
在实际应用中,为了准确计算煤气回收量,需要对煤炭的化学分析结果进行实验测定,并结合实际运行的工况参数进行综合计算。
此外,还需要考虑一些因素的修正,如燃烧的效率、燃料的含硫量、燃料的湿度等。
综上所述,煤气回收量的计算是一项基于煤炭的化学组成,通过测量或计算煤炭燃烧产物中的二氧化碳和水蒸气的含量,并结合实际运行的工况参数来评估能源设备的能源利用效率。
通过煤气回收量的计算,可以为能源管理和节能减排提供科学依据。
- 1、下载文档前请自行甄别文档内容的完整性,平台不提供额外的编辑、内容补充、找答案等附加服务。
- 2、"仅部分预览"的文档,不可在线预览部分如存在完整性等问题,可反馈申请退款(可完整预览的文档不适用该条件!)。
- 3、如文档侵犯您的权益,请联系客服反馈,我们会尽快为您处理(人工客服工作时间:9:00-18:30)。
转炉煤气回收量计算
一、转炉煤气回收吨钢
90m3;日产钢量3300t; 转炉煤气热值:1400大卡h/m3;
每天产煤气量
297000m3=12375m3/h×1400大卡h/m3=1732.5万大卡/h
转炉煤气每小时的热量折算标准煤:
1732.5万大卡/h÷7000大卡
=2475Kg/h=2.475t/h (注:标煤热值为7000大卡/Kg)1度电需0.333kg标煤
二、转炉煤气回收供发电效益计算:
理论计算值:1kg标煤发电3.0KW.h;(5m3转炉煤气=1kg标煤)
长沙利能计算:转炉煤气发电消耗标煤:42.04t标煤/天×1300元/t=54652元/天
年发电2800万Kwh
计算式:煤气量
8750m3/h×8000h=7000万m3/年(余出3625m3/h)
7000万×1400÷7000=14000000Kg标煤=14000t标煤/年=42.04t标煤/t天
注:理论上:煤气烧锅炉变为蒸汽属于二次转换,锅炉热效率80%,蒸汽消耗损失
5%;其他损失未计在内。
三、生产白灰费用计算分析:
白灰窑需用18000m3/h
高炉煤气(现在用12500m3/h);
白灰产量300t/天(设计值);外购白灰价格:240元/t;
每天需用标煤计算:
18000×650÷7000=1671.4Kg=1.6714t×24h=40.113t/天
生产1吨白灰需要0.1337t标煤。
1t白灰需要668m3转炉煤气1t
白灰需要标煤费用:0.1337t×1300元/t煤=173.81元/t白灰
每天需要标煤计算:0.1337t×300t/天=40.11t
40.11t×1300元/t标煤=52143元/天
生产白灰价值:300t×240元/t=72000元/天(另外白灰节省4000m3/h转炉煤气)
(注:白灰价格240元/t;石灰石43元/t是采购部提供的采购价;标煤价格1300元/t)因煤气是富余产品,都燃烧放散,煤气平衡调整好后能满足白灰窑使用,因此未增加燃料费用。
白灰窑用转炉煤气: 从5万煤气柜要架设DN1000专用管道620m。
(投资约60万元)
转炉煤气供白灰窑与发电对比:
1、白灰窑每天能耗:0.1337t×300t/天=40.11t×1300元/t标煤=52143元/天
煤气发电每天能耗:42.04t标煤/天×1300元/t=54652元/天
2、白灰窑每天能耗比煤气发电每天能耗节省:54652-52143=2509元/天
年节省能耗:
2509元×350天=87.815万元/年
四、带钢加热炉用转炉煤气计算:
高炉煤气3.8万m3/h(冷坯);3.0万m3/h(热送);高炉煤气热值:650大卡/m3
用转炉煤气折算成高炉煤气:
1400大卡/m3/650大卡/m3×12375=26653m3/h
煤气缺口:
38000-26653=11347m3/h(冷坯); 30000-26653=3347m3/h(热坯)
因此需要混合缺部分高炉煤气(如一座转炉检修缺口更多);要上煤气混合站。
高炉煤气是按每小时的体积算的,加热炉如果使用纯高炉煤气的话,加热到1250C°,须采用蓄热式燃烧技术,燃耗按380Kcal/kg计算,需要380*45000kal/h,高炉煤气热值按800Kcal/kg,需用高炉煤气380*45000/800Nm3的高炉煤气。