洁净钢的生产及品种钢开发2009-9-17,顾克井
洁净钢与纯净钢
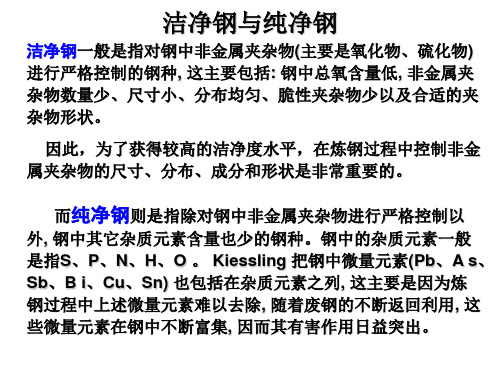
洁净关钢于一纯般净是钢指(对pu钢ri中ty非st金ee属l)夹或杂洁物净(钢主(要c是lea氧n化st物ee、l) 硫的化概物念), 进目行前严国格内控外制尚的无钢统种一, 这的主定要义包。括: 钢中总氧含量低, 非金属夹 杂物数量少、尺寸小、分布均匀、脆性夹杂物少以及合适的夹 杂物形状。
纯净钢除了要考虑[S]+[P]+[N]+[O]+[H]五大元素外,随废钢
量的增加,还要关注Cu、Zr、Sn、Bi、Pb等伴生元素。
研究发现,即Байду номын сангаас将钢中总氧降到10ppm以下,钢液中仍 然存在15微米尺度的夹杂物,因此洁净钢的研究目前沿 着两种发展方向进行: 一种是控制钢中总氧量来降低夹杂物含量; 另一种是控制夹杂物成分以减小其对钢性能的影响。
洁净钢是一个相对概念
当1.2某钢0世中一纪的杂杂6质0质年含元代量素:降或[S]非低+[金P到]属+什[N夹么]杂+[水O物]平直+[H接决]或<定9间0于0接p钢p影m种响;和产产品的品生用产途; 性金么不程能属这同度或夹种的决使杂钢年定用物就78代 于性的可00年年, 装能数以代代对 备时量认::,、为洁 和[[SS该尺是净工]]++钢寸洁[[钢艺PP就或净]]++有现不分钢[[NN不代是布。]]++同化洁对可[[OO净产见的水]]++钢品,[[平要HH;的“]]。求<<而性洁8600;如能净00pp有果都钢ppmm害杂没”;;质有不元元影同素素响于降或,“低非那纯 净念地<22钢不生.0高p”是产p附的为出m加概了可;9值念一以0年夹,味稳产代杂“追定品:物洁求地对[S净纯满数]洁+钢净足量[P净”用,]而要+度并户[是N少不加的]为+;指工[要了O夹越和]能求+纯使杂[够H是越用物]高<:好要1效尺0。求0T率寸p[所的p、O要m以优]低;要小质,成洁低商<本净5品0、钢μ钢成的m材批概;。 这夹2样杂1世的物纪“形洁态净要钢合”概适[S念。]+不[P仅]+具[N有]+质[O量]+含[H义]<,5而0p且pm具。有经济含义。
品种钢与洁净钢冶炼考试范围
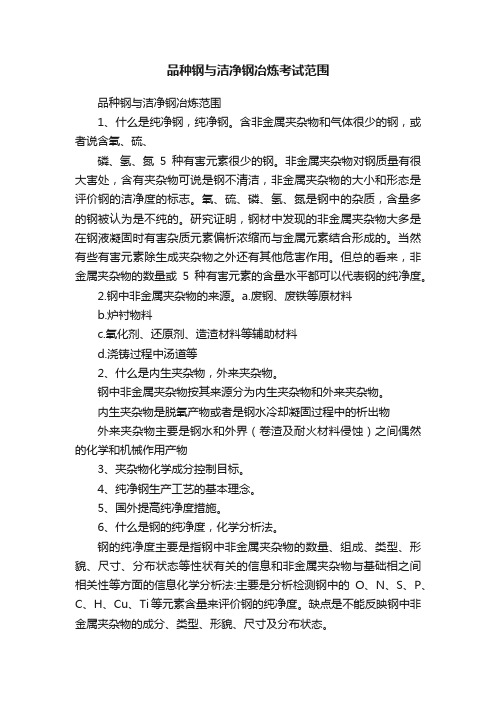
品种钢与洁净钢冶炼考试范围品种钢与洁净钢冶炼范围1、什么是纯净钢,纯净钢。
含非金属夹杂物和气体很少的钢,或者说含氧、硫、磷、氢、氮5种有害元素很少的钢。
非金属夹杂物对钢质量有很大害处,含有夹杂物可说是钢不清洁,非金属夹杂物的大小和形态是评价钢的洁净度的标志。
氧、硫、磷、氢、氮是钢中的杂质,含量多的钢被认为是不纯的。
研究证明,钢材中发现的非金属夹杂物大多是在钢液凝固时有害杂质元素偏析浓缩而与金属元素结合形成的。
当然有些有害元素除生成夹杂物之外还有其他危害作用。
但总的看来,非金属夹杂物的数量或5种有害元素的含量水平都可以代表钢的纯净度。
2.钢中非金属夹杂物的来源。
a.废钢、废铁等原材料b.炉衬物料c.氧化剂、还原剂、造渣材料等辅助材料d.浇铸过程中汤道等2、什么是内生夹杂物,外来夹杂物。
钢中非金属夹杂物按其来源分为内生夹杂物和外来夹杂物。
内生夹杂物是脱氧产物或者是钢水冷却凝固过程中的析出物外来夹杂物主要是钢水和外界(卷渣及耐火材料侵蚀)之间偶然的化学和机械作用产物3、夹杂物化学成分控制目标。
4、纯净钢生产工艺的基本理念。
5、国外提高纯净度措施。
6、什么是钢的纯净度,化学分析法。
钢的纯净度主要是指钢中非金属夹杂物的数量、组成、类型、形貌、尺寸、分布状态等性状有关的信息和非金属夹杂物与基础相之间相关性等方面的信息化学分析法:主要是分析检测钢中的O、N、S、P、C、H、Cu、Ti等元素含量来评价钢的纯净度。
缺点是不能反映钢中非金属夹杂物的成分、类型、形貌、尺寸及分布状态。
7、硫对钢材性能的影响。
硫(S):硫在通常情况下也是有害元素。
使钢产生热脆性,降低钢的延展性和韧性,在锻造和轧制时造成裂纹。
硫对焊接性能也不利,降低耐腐蚀性。
所以通常要求硫含量小于0.055%,优质钢要求小于0.040%。
在钢中加入0.08-0.20%的硫,可以改善切削加工性,通常称易切削钢。
7.脱氮困难的原因,生产低【N】钢系用措施。
8、对真空精炼优点及缺点。
品种钢与洁净钢冶炼

1 纯净钢生产工艺的基础理念
为降低钢中[O]D,在LF精炼采用白渣操作+氩气搅拌,钢渣精炼扩散
脱氧,既能把钢水中[O]D 降到20ppm以下 ,也能有效地脱硫
([S]<0.01%)。图1表示硅镇静钢,LF精炼后钢水中[O]D 与水口堵塞 和针孔的关系。表明: [O]D<10ppm, —— 水口堵塞增加; [O]D>20ppm, —— 铸坯针孔增加; [O]D=10~20ppm,—— 最佳范围。 Mn/Si低时形成SiO2夹杂,增加了水口堵塞的可能性; Mn/Si高时形成典型的MnO· 2(54.1%:45.9%),夹杂物容易 SiO 上浮; 铁合金中铝:带入的铝使钢水中[Al]S>0.003%形成固态Al2O3; 控制LF白渣精炼时间,减少MgO· 2O3生成。 Al
脱氧产物合适的组成
夹 杂 物 的 排 除 方 法
合适的顶渣成分
熔池的搅拌能力
1 纯净钢生产工艺的基础理念
冶炼过程控制非金属夹杂物
(1)初炼 在炼钢初期,尽量降低钢液和渣的氧化状态,以降低 脱氧强度。因此,在转炉中,应用过程控制系统例如均衡 装料、副枪测量、熔池搅拌、终点控制模型和动态控制方 法,例如噪声和气体分析确保出钢时低氧化性。在吹炼和 后吹过程通过向钢液中吹入惰性气体(氮气或氩气)来搅 拌钢液,使出钢时钢渣接近化学平衡,这有利于降低钢液 和渣的氧化性,促进磷从钢液向渣中扩散,从而降低钢液 磷含量,并降低出钢时钢液的氮含量。
1 纯净钢生产工艺的基础理念
② 真空脱气
真空脱气最初于20世纪50年代用来降低模铸钢中的氢含量, 根据不同的铸坯断面和硫含量,氢一般能从0.0005%(5ppm)左 右脱除到0.0002%(2ppm)以下。如此低的氢含量避免了裂纹的 生成。 最常用的是RH或真空再循环脱气装置。 在这个装置中,两个浸渍管浸入到钢包钢液中。真空泵对 真空室抽真空后,通过向上升管中吹入氩气,使钢液从上升管 中流人真空室,再从下降管中流出,从而持续地将钢液暴露于 真空室中。由于低气压降低了氢气在钢液中的溶解度,氢从钢 液中扩散进入真空室。钢液在真空度为100 Pa下保持15min 能 将钢液中的氢含量降低一半,从3.5ppm降低到1.5ppm。
高效低成本洁净钢生产课件

总结词:介绍了高效低成本洁净钢生产所需的设备和材料,包括熔炼炉、精炼装置、连铸机、轧机等设备和耐火材料、保护气体等辅助材料。
高效低成本洁净钢生产实践与案例分析
03
高效低成本洁净钢生产设备
介绍关键的生产设备及其工作原理,如真空脱气装置、连铸机、轧机等。
01
高效低成本洁净钢生产技术
介绍当前主流的高效低成本洁净钢生产技术,如连铸连轧技术、纯净钢冶炼技术等。
高效低成本洁净钢生产课件
目录
引言洁净钢生产技术高效低成本洁净钢生产工艺高效低成本洁净钢生产实践与案例分析结论与展望
引言
洁净钢是指钢中氧、氮、氢、硫、磷等杂质元素含量较低,且夹杂物细小弥散分布的钢种。
洁净钢的生产过程需经过冶炼、连铸和轧制等工序,通过控制各工序的工艺参数和操作条件,达到降低杂质元素含量和去除夹杂物的目的。
国内外典型案例对比
结论与展望
高效低成本洁净钢生产技术已取得显著成果,为钢铁行业的发展提供了有力支持。
高效低成本洁净钢生产技术涉及多个领域,包括冶金、材料科学、化学等,需要跨学科合作。
高效低成本洁净钢生产技术还需要在生产实践中不断优化和完善,以提高生产效率和降低成本。
钢铁行业将继续推进高效低成本洁净钢生产技术的研发和应用,以提高产品质量和降低生产成本。
02
高效低成本洁净钢生产工艺流程
详细阐述从原料选择、冶炼、连铸、轧制到产品精整的整个生产工艺流程。
分析该企业在高效低成本洁净钢生产方面的成功经验,包括技术应用、工艺优化、设备改造等方面的具体措施。
某钢铁企业高效低成本洁净钢生产实践
对比分析国内外在高效低成本洁净钢生产方面的典型案例,总结各自的优势和不足。
未来钢铁行业将更加注重环保和可持续发展,高效低成本洁净钢生产技术将发挥更加重要的作用。
洁净钢生产实践概述

洁净钢生产实践概述【摘要】本文简要介绍了青钢第二炼钢厂的装备及工艺技术水平,叙述了青钢近年来为实现洁净钢生产在铁水预处理(脱硫)、转炉冶炼(脱磷)、炉后扒渣(防止回磷)、钢水精炼(脱硫、脱氧及夹杂物控制)、连续浇注(罐外开浇、保护浇注、中间包流场)等方面所做的工作以及在胎圈钢丝等典型钢种上的应用,实现了[o]t≤25ppm、[p]+[s]≤0.015%、夹杂物级别≤1.5级洁净钢的生产。
【关键词】洁净钢;脱硫;脱磷;胎圈钢丝0 前言洁净钢指钢中有害元素含量低和非金属夹杂物数量、尺寸或分布对产品性能无有害影响的钢,不同用途的钢对洁净度的要求不同。
洁净钢是衡量钢铁工业发展水平和产品结构的一个重要标志,因此,提升洁净钢生产水平,调整产品结构,一直是钢铁工业发展中各方关注的重点,也是近几年结构调整中的发展重点。
美国、日本、德国等钢铁生产先进国家生产能力早已过剩,洁净钢产品生产能力也很高,但仍然要淘汰相对落后的工艺,目的就是进一步提高产品洁净度,增强产品市场竞争力。
洁净钢的生产贯穿于整个炼钢生产过程,包括铁水预处理、转炉吹炼过程控制、转炉终点控制、脱氧合金化、炉外精炼、保护浇注等。
为满足洁净钢生产需求,各企业做了大量的技术工作,采用了铁水预脱硫、双渣法吹炼、夹杂物去除及形态控制等技术,这些技术的应用使得生产[o]t≤25ppm、[p]+[s]≤0.015%、夹杂物级别≤1.5级洁净钢成为可能[1],由此确保钢材在加工性能、使用性能或其它方面的要求。
近年来青钢通过装备水平的提升和工艺技术的开发应用,逐渐形成了提高钢的洁净度和控制钢中非金属夹杂物数量和形态的洁净钢生产工艺技术,实现了以胎圈钢丝为代表的洁净钢的生产。
1 青钢炼钢生产流程及主要工艺装备青钢第二炼钢厂生产工艺流程为:混铁炉→铁水预脱硫→转炉→lf→连铸。
主要设备参数为:2 青钢洁净钢生产技术表1 炼钢系统主要设备及功能2.1 钢中硫的控制除易切削钢外,硫是有害元素,对产品使用性能将产生不良影响,因此洁净钢对钢中硫含量有较为严格的要求,一般要求[s]≤0.015%,某些情况下要求[s]≤0.007%,青钢通过喷吹颗粒镁脱硫、转炉控制回硫、lf脱硫等技术,有效降低了钢中的硫含量。
洁净钢生产实践概述

Science &Technology Vision科技视界0前言洁净钢指钢中有害元素含量低和非金属夹杂物数量、尺寸或分布对产品性能无有害影响的钢,不同用途的钢对洁净度的要求不同。
洁净钢是衡量钢铁工业发展水平和产品结构的一个重要标志,因此,提升洁净钢生产水平,调整产品结构,一直是钢铁工业发展中各方关注的重点,也是近几年结构调整中的发展重点。
美国、日本、德国等钢铁生产先进国家生产能力早已过剩,洁净钢产品生产能力也很高,但仍然要淘汰相对落后的工艺,目的就是进一步提高产品洁净度,增强产品市场竞争力。
洁净钢的生产贯穿于整个炼钢生产过程,包括铁水预处理、转炉吹炼过程控制、转炉终点控制、脱氧合金化、炉外精炼、保护浇注等。
为满足洁净钢生产需求,各企业做了大量的技术工作,采用了铁水预脱硫、双渣法吹炼、夹杂物去除及形态控制等技术,这些技术的应用使得生产[O]T ≤25PPm、[P]+[S]≤0.015%、夹杂物级别≤1.5级洁净钢成为可能[1],由此确保钢材在加工性能、使用性能或其它方面的要求。
近年来青钢通过装备水平的提升和工艺技术的开发应用,逐渐形成了提高钢的洁净度和控制钢中非金属夹杂物数量和形态的洁净钢生产工艺技术,实现了以胎圈钢丝为代表的洁净钢的生产。
1青钢炼钢生产流程及主要工艺装备青钢第二炼钢厂生产工艺流程为:混铁炉→铁水预脱硫→转炉→LF→连铸。
主要设备参数为:2青钢洁净钢生产技术表1炼钢系统主要设备及功能2.1钢中硫的控制除易切削钢外,硫是有害元素,对产品使用性能将产生不良影响,因此洁净钢对钢中硫含量有较为严格的要求,一般要求[S]≤0.015%,某些情况下要求[S]≤0.007%,青钢通过喷吹颗粒镁脱硫、转炉控制回硫、LF 脱硫等技术,有效降低了钢中的硫含量。
2.1.1铁水预处理脱硫铁水预处理脱硫是生产低硫钢的重要环节,因铁水碳含量高、氧低,硫的活度系数大,是钢铁生产流程中脱硫效果最好、最经济的环节。
纯净钢简介及使用PPT课件

夹杂物“临界尺寸”为5~8μm。当夹杂物小于5μm时,钢材在负荷条件下,
不再发生裂纹扩展,可将此界定为超洁净钢标准之一。
•
近年来,加拿大Mitchell教授和新日铁Fukumoto博士提出“零氧化物夹杂
钢”的概念。
.
7
2 夹杂物的控制
• 加拿大Mitchell教授和新日铁Fukumoto提出了“零夹杂”钢的概念。
•
因此,可能存在的亚微米夹杂物来自两部分,一部分是由原始合金或初炼炉带来的含Al2O3、
SiO2、CaO的夹杂物,另一部分是钢液凝固过程中析出的氧化物、硫化物和氮化物夹杂。
.
8
3 纯净钢的生产
钢液中析出硫化物和氮化物的溶积 度远比析出氧化物的溶积度高,在一 般情况下液相中不可能析出硫化物 和氮化物。
.
4
1 纯净钢的概念
减少钢中的杂质含量,可以显著地改善钢材的延展性、韧性、加工、焊接、抗腐 蚀等性能。 对于钢性能要求不同,纯净度所要求的控制因素也不同。
如:
用于高层建筑、重载桥梁、海洋设施等重要用途钢板目前硫控制在80ppm以下, 将来会降到50ppm以下
对于新一代汽车用超深冲IF钢冷轧钢板,氮要求低于25ppm 轴承钢中总氧量每低1ppm,其寿命可提高10倍,目前轴承钢中总氧量最好水平
• 材料的纯净度是指材料中的夹杂物含量。目前国内外轴承钢生产企业都严格 控制钢中的含氧量,因为钢中的氧基本上是以夹杂物的形式存在的。瑞典SKF 公司和日本山阳特殊钢公司在轴承钢氧含量与疲劳寿命关系方面的大量试验 研究明确表明:当氧含量从非精炼钢的40ppm降到精炼钢的10ppm时,轴承的 疲劳寿命可延长10倍,降到5ppm时可延长30倍,与真空自耗和电渣重熔钢的 疲劳寿命相当。轴承钢的均匀性是指材料的化学成分、内部组织等的均匀程 度。
洁净钢生产工艺及技术概述
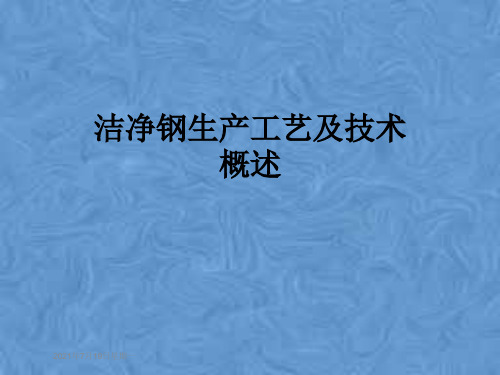
37
水口堵塞
• 改良耐材
– 配合紧密,防止二次氧化
– 无碳耐材内衬,减少第一层反应的厚 度
• 降低来自耐材内部的氧化性气体 • 增加绝热性能 • 降低表面粗糙度
– 通过钢液与耐材之间的反应对夹杂物
进行变性
图25.内衬为低碳质耐火材料 的设计方案
38
水口堵塞
• 合理选用与改良水口
化铝型夹杂。 – 钙处理强度过大,钢液表面翻腾产生二次氧化。 – 对不同硫含量的钢种,易发生夹杂物种类的转变
36
水口堵塞
• 吹氩密封
– 增加水口内的压力,防止二次氧化,减少夹杂物聚集 。
– 降低氧化性气体分压,减缓钢液与耐材之间的反应。 – 在水口壁上形成氩气薄膜,降低接触时间,机械清理
,降低吸附力。 – 氩气泡吸附夹杂物,将其从水口内壁分离。
拌→20min左右静置。
图7.CAS(-OB)装置
13
钢包操作
• 钢液成分 • 出钢条件 • 耐火材料 • 脱氧剂和合金的加入 • 钢包衬与钢包残留物 • 钢包渣 • 夹杂物变性 • 精炼时间
14
炉渣乳化
• 乳化渣产生机制
– 出钢铸流冲击渣层 – 渣钢界面气泡引起的搅动 – 钢流速度和方向变化引起渣钢界面之间的漩涡和
– SEN出口布流不均匀引起
– 在较高钢通量的情况下,钢水和保护渣之间聚集的 泡沫。
16
炉渣乳化
• 影响卷渣的参数
– Kelvin-Helmholtz不稳定性标准(不同层流之间相对运动波动
– Taylor-Saffman不稳定性Δv标约为准4(2c不m同/s,黏度适与于密高度拉)速
• 产生剪切应力,同时由于表面张力的作用产生颈缩。
洁净钢技术与工艺概况简介

洁净钢技术与工艺概况简介发表日期:2007年10月30日在经历了10年的深入研究并取得重大的进步后,洁净度仍然是当今世界钢铁界研究和工业生产的主题。
对钢材要求的日益严格和钢铁技术专家的聪明才智是提高钢材品质的两大驱动力,从而导致了对洁净度要求不断提高并得以实现。
自2001年以来,国际钢铁协会技术委员会针对洁净钢的工业生产和研发情况进行了广泛的调研和比较。
从本期开始,本报将分期介绍世界洁净钢技术和工艺的发展概况。
目标与目的钢洁净度在钢铁应用的发展中是最重要的。
钢的性能决定了它的用途与竞争能力,而化学成分和最终的显微组织确定了钢的性能。
因此,不会有一个完整的洁净钢定义,它仅仅是与应用有关的一个术语。
氧化物在改变钢的显微组织上扮演了重要角色,因此,成为本次研究的焦点。
它们要么以钢水二次氧化的形式存在,要么以耐材或保护渣吸卷的方式进入钢中。
因此,炼钢,尤其是二次冶金处理和连铸工序是实现所要求的洁净度的关键。
为判定最佳操作和建立科学的概念,收集了关于设备、工艺和控制方面的数据。
这些数据来自22个国家的64套设备上,各个数据表包含了800条不同的信息,总共获得了5万余条可用信息。
选择了低碳钢、超低碳钢、管线钢、高碳长材和弹簧钢进行研究,应用领域涵盖了汽车裸露件、管线和滚珠轴承等。
比较工业实践仅仅是该项目的一个部分,此外,还进行了深入的文献调查,以确定今后的发展与进步。
氧化洁净度是优质钢最重要的一个指标。
全世界在改进二次炼钢和连铸工艺技术方面付出了巨大努力。
主要目的是要将钢水中夹杂物含量减少到最低程度,促进颗粒分离,避免被大气、炉渣和耐火材料二次氧化等。
有害夹杂物一个主要成因是非常小的夹杂物在紊流区凝结,这出现在从大包到中间包、中间包再到结晶器传输钢水的过程。
相反,外来非金属夹杂物源于炉渣夹带,因此,保护渣绝不能乳化进入钢水。
这是对钢铁工业在这个艰难冶金领域里继续发展提出的挑战。
洁净钢这次的研究不是要建立洁净钢的通用定义,因为洁净度是钢材使用的直接结果,对洁净度的要求各不相同。
纯净钢的生产技术和应用新日铁讲解PPT课件

(After M. Tani M, Proceedings of 4th第E2u2r页op/共ea4n8C页ontinuous Casting Conference, 2002)
电磁连铸( EMC )原理图
(After M. Tani M, Proceedings of 4th European Continuous Casting Conference, 2002)
20
第20页/共48页
表面净化(气孔)
Vc=1.2m/min.
Vc=2.0m/min.
气孔指数 气孔指数
(Data of Kimitsu Works)
21
第21页/共48页
电磁感应的原理
电流
线圈中的交流电 时间
电感线圈
感应线圈
如果是液态金属
感应电流
感应磁场
洛伦兹力
流动
洛伦兹力
产生了电磁力驱动的流场
(After K. Wunnenberg, Revue de Metallurgie, 2005)
32
第32页/共48页
有害夹杂物的尺寸范围
(After K. Wunnenberg, Revue de Metallurgie, 2005)
33
第33页/共48页
有害夹杂物的来源
(After K. Wunnenberg, Revue de Metallurgie, 2005)
4
第4页/共48页
内容
1.引言 纯净钢概述
2.纯净钢生产工艺的基础理念 3.纯净钢生产的主要技术和应用这些技术后纯净钢的物
化特性
3.1 降低氧化物夹杂总量 3.2 减少大颗粒夹杂 3.3 降低板坯表面及皮下夹杂物 3.4 控制夹杂物化学成分
纯洁钢-多媒体

薄板
管材 棒材 丝 注:DA
11
高附加值产品洁净度:
高附加值产品对洁净度要求是: • T[O]要低<20ppm; • 夹杂物数量要少; • 夹杂物尺寸要小<50μ m; • 夹杂物形态要合适。
12
由上述讨论,可得出以下认识:
•
纯净钢或洁净钢是一个相对概念;
• 某一夹杂含量降低到什么水平决定于钢种和产品用途; • 有害元素的降低程度决定于装备和工艺现代化水平; • 不管生产什么用途得钢,总是要求钢中夹杂物数量尺寸、 形态得到控制。
用 Si、 Mn 脱氧平衡[O]溶 含量较高。仅用 Si 、 Mn 脱氧钢中[O]溶 为 4060ppm。在结晶器内凝固时铸坯易产生皮下气孔。
15
钢中夹杂物评价:
人们预测2000年后生产超洁净钢,钢中[O]要达到5ppm水平,
T[O]= [O]溶+ [O]夹
解决途径: • • 生产“零夹杂物”钢; [O]夹 → 0,即钢中夹杂物完全去除; 进一步降低[O]溶 对于Al—K钢,炉外精炼改变Al—O 热力学平衡,Al2O3溶于 渣中可使熔渣中Al2O3活度达到0.001,与 [Al]S相平衡得[O]溶小小 于1ppm。 对于Si—K钢,炉外精炼控制炉渣组成,使SiO2溶于铝酸钙渣 中,降低aSiO2,可使钢中[O]溶降到与Al—K钢水平。
就脱氧而言,分三种情况:
1)用Si+Mn脱氧 形成的脱氧产物有:
• • •
纯SiO2(固体): MnO • SiO2(液体); MnO • FeO(固溶体)。 控制合适的Mn/Si比,得到液相MnO •SiO2 容易上浮 排除。但往往由于脱氧不良,铸坯会产生皮下气孔。
18
钢中夹杂物控制原理
纯净钢的生产技术
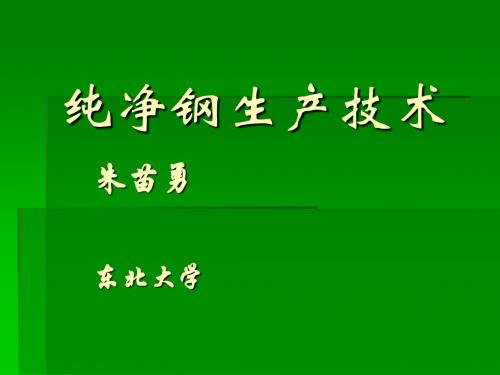
为了用较少的熔剂进行有效脱硫,在CaO中混入Mg
或CaC2,可以将硫降到50ppm以下。
脱硫预处理后的低硫铁水,在转炉炼钢过程,通常
不仅不能进一步脱硫,废钢、铁水渣、石灰中的硫
反而会进入钢水中,回硫量可达20-50ppm以上。
炼钢过程中回硫是生产超低硫钢的重大障碍。生产 超低硫钢时应采用较高铁水装入比,并尽量减少铁 水的带渣量。
硫还会明显降低钢的焊接性能,引起高温龟裂,并 在焊缝中产生气孔和疏松,从而降低焊缝的强度。 硫含量超过0.06%时,会显著恶化钢的耐蚀性。硫 还是连铸坯中偏析最为严重的元素。
硫除对钢材的热加工性能、焊接性能、抗腐蚀性能
有大的影响外,对力学性能影响主要表现在:
与钢材轧制方向相比,非轧制方向强度、延展性、
竞争加剧:要求生产成本低,增加生产率;
技术投资增加,同时研究经费投入加大;
需要基本标准和改进生产、提高效益措施; 贸易壁垒和贸易保护主义愈加严重;
全球经济发展,但部分地区出现经济危机;
除欧洲,钢铁工业合并延缓。
1.2 钢铁工业的挑战
能力过程,并将继续蔓延;
较差的经济效益;
当钢中的硫含量超过0.020%时,钢水在凝固过程中由于 偏析,低熔点Fe-FeS共晶体分布于晶界处,在1150-1200℃ 的热加工过程中,晶界处的共晶体熔化,钢受压时造成晶界 破裂,即发生“热脆”现象。
如果钢中的氧含量较高,FeS与FeO形成的共晶体熔 点更低(940℃),更加剧了钢的“热脆”现象的 发生。 锰可在钢凝固范围内生成MnS和少量的FeS,纯MnS 的熔点为1610℃,共晶体FeS-MnS(占93.5%)的熔 点为1164℃,它们能有效的防止钢热加工过程的 “热脆”。
宝钢炼钢纯净钢生产技术进展共15页文档

宝钢炼钢纯净钢生产技术进展郑贻裕蒋晓放(宝山钢铁股份有限公司炼钢厂,上海,200941)摘要:本文简要介绍了宝钢炼钢厂主要装备,重点介绍了炼钢厂生产纯净钢在磷、硫、氧、氮、碳等元素的控制水平和采取的措施,以及目前厚板钢种残余元素的控制水平。
关键词:洁净钢,炼钢,残余元素此文是本刊特约的文章Progress of Production Technology for Clean Steel atBaosteelZheng Yiyu Jiang Xiaofang (Steelmaking Plant, Baoshan Iron & Steel Co., Ltd.,Shanghai, 200941)ABSTRACT The main equipments of steelmaking plant of Baosteel are briefly introduced in this paper. The progress in control technology of phosphorus, sulphur, total oxygen, nitrogen, carbon in steel is discussed at Baosteel. The control level of residual elements in heavy plate is introduced too.KEYWORDS clean steel, steelmaking, residual elements 文中红色字体是审稿时建议作者补充的(红色字体的分节和小节标题除外)1 前言所谓纯净钢一般指钢中杂质元素磷、硫、氧、氮、氢(有时包括碳)和非金属夹杂物含量很低的钢。
而所谓杂质又是随钢种而变的,某一元素在某钢种内是有害杂质,在另一种钢内其有害程度可能轻些甚至是有益的。
也就是说,对于钢性能要求的不同,纯净度所要求的控制因素也不同。
洁净钢生产新流程的研究与开发(刘浏原件)【范本模板】

洁净钢生产新流程的研究与开发刘浏钢铁研究总院1.前言建设高效低成本洁净钢平台是市场和时代发展的要求,是洁净钢生产领域的重大技术革命。
其目标是实现转炉直接冶炼洁净钢,并使转炉生产效率提高1倍,洁净钢生产成本低于传统转炉普通钢。
本文系统介绍了钢铁研究总院与首钢合作研究开发的洁净钢生产新工艺流程在京唐钢铁公司的开发与应用情况,阐述了高效低成本洁净钢平台建设的三项核心技术:洁净钢稳定化生产工艺、洁净钢高效化生产工艺、洁净钢低成本制造工艺.2.传统洁净钢生产流程与主要问题图1给出传统洁净钢生产流程示意图。
传统洁净钢生产流程的基本特征是:钢水提纯主要依靠炉外精炼,精炼工艺流程长,生产波动大。
也是造成钢水质量不稳定,生产能耗高、成本高和CO2排放量高的主要技术原因。
高炉LF转炉冶炼铁水脱硫RH CC图1 传统洁净钢生产流程示意图传统流程的主要工艺特点是:●采用全量铁水脱硫预处理工艺;●采用传统转炉炼钢工艺脱磷、脱碳;●采用LF炉还原精炼工艺进行深脱硫和脱氧,控制T.O含量;●采用RH真空精炼工艺,降低钢中气体含量;●采用全连铸工艺深入分析传统流程中进行的脱磷、脱硫、脱碳、脱硅等反应过程可以看出,传统流程中存在以下基本矛盾:(1)炼钢回硫,脱硫后的超低硫铁水(通常控制[S]≤0.005%)在转炉冶炼过程中大量回硫,通常不能满足连铸钢水对硫含量的基本要求,需通过LF炉进行二次脱硫。
(2)低碳脱磷,由于转炉中碳、磷反应平衡限制了转炉实现高碳脱磷的反应能力,钢水脱磷大多在[C]≤0.3%以下才能有效进行。
因此,稳定生产[P]≤0.015%的低磷钢水常常需要把钢水[C]降低到0。
08%以下,造成炉渣和钢水的严重过氧化,出钢a O≥800 10-6。
(3)钢水过氧化,增大脱氧剂消耗使钢中脱氧产物形成的夹杂物大量增加,为夹杂物去除带来很大困难.(4)脱氧产生的大量夹杂物,很难上浮去除,往往需要大幅度延长“软吹”时间。
延长“软吹”时间又由于炉渣和耐火材料的侵蚀以及完成脱硫任务等过程产生大量新的细小夹杂物,很难去除.(5)渣量大,炉渣利用率低,难以实现炉渣循环利用。
纯净钢
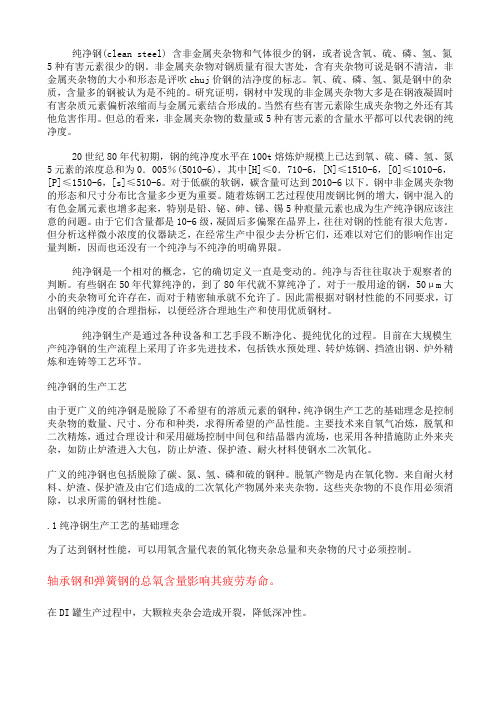
纯净钢(clean steel) 含非金属夹杂物和气体很少的钢,或者说含氧、硫、磷、氢、氮5种有害元素很少的钢。
非金属夹杂物对钢质量有很大害处,含有夹杂物可说是钢不清洁,非金属夹杂物的大小和形态是评吹chuj价钢的洁净度的标志。
氧、硫、磷、氢、氮是钢中的杂质,含量多的钢被认为是不纯的。
研究证明,钢材中发现的非金属夹杂物大多是在钢液凝固时有害杂质元素偏析浓缩而与金属元素结合形成的。
当然有些有害元素除生成夹杂物之外还有其他危害作用。
但总的看来,非金属夹杂物的数量或5种有害元素的含量水平都可以代表钢的纯净度。
20世纪80年代初期,钢的纯净度水平在100t熔炼炉规模上已达到氧、硫、磷、氢、氮5元素的浓度总和为0.005%(5010-6),其中[H]≤0.710-6,[N]≤1510-6,[O]≤1010-6,[P]≤1510-6,[s]≤510-6。
对于低碳的软钢,碳含量可达到2010-6以下。
钢中非金属夹杂物的形态和尺寸分布比含量多少更为重要。
随着炼钢工艺过程使用废钢比例的增大,钢中混入的有色金属元素也增多起来,特别是铅、铋、砷、锑、锡5种痕量元素也成为生产纯净钢应该注意的问题。
由于它们含量都是10-6级,凝固后多偏聚在晶界上,往往对钢的性能有很大危害。
但分析这样微小浓度的仪器缺乏,在经常生产中很少去分析它们,还难以对它们的影响作出定量判断,因而也还没有一个纯净与不纯净的明确界限。
纯净钢是一个相对的概念,它的确切定义一直是变动的。
纯净与否往往取决于观察者的判断。
有些钢在50年代算纯净的,到了80年代就不算纯净了。
对于一般用途的钢,50μm大小的夹杂物可允许存在,而对于精密轴承就不允许了。
因此需根据对钢材性能的不同要求,订出钢的纯净度的合理指标,以便经济合理地生产和使用优质钢材。
纯净钢生产是通过各种设备和工艺手段不断净化、提纯优化的过程。
目前在大规模生产纯净钢的生产流程上采用了许多先进技术,包括铁水预处理、转炉炼钢、挡渣出钢、炉外精炼和连铸等工艺环节。
纯净钢的开发与生产

纯净钢的开发与生产
张爱民;袁松涛
【期刊名称】《安徽工业大学学报(自然科学版)》
【年(卷),期】2003(020)0z1
【摘要】对纯净钢的生产工艺和技术进行了简述,结合济钢三炼钢和中厚板的生产实际,提出了改进连铸坯内部质量的措施,为进一步开发生产高附加值、高难度和高技术含量的纯净钢提供了依据.
【总页数】3页(P166-167,174)
【作者】张爱民;袁松涛
【作者单位】济南钢铁股份有限公司,济南,250101;济南钢铁股份有限公司,济南,250101
【正文语种】中文
【中图分类】TF703.5.4
【相关文献】
1.纯净钢及纯净铸坯的生产技术 [J], 朱立光;唐国章;
2.转炉高纯净度GCrl5轴承钢的试制开发 [J], 李金浩
3.开发纯净钢冶炼技术生产高强度钢丝绳用钢 [J], 王秉喜;郭大勇
4.超高纯净钢生产技术的开发 [J], 竹之内朋;文凡
5.为生产纯净钢开发的白渣高效脱硫工艺 [J],
因版权原因,仅展示原文概要,查看原文内容请购买。
- 1、下载文档前请自行甄别文档内容的完整性,平台不提供额外的编辑、内容补充、找答案等附加服务。
- 2、"仅部分预览"的文档,不可在线预览部分如存在完整性等问题,可反馈申请退款(可完整预览的文档不适用该条件!)。
- 3、如文档侵犯您的权益,请联系客服反馈,我们会尽快为您处理(人工客服工作时间:9:00-18:30)。
合金结 具有高强度和弹簧、锯条、传动链 65Mn 构钢 良好耐磨性。 条等。
4
一、主要热连轧产品分类及用途简介
产品类别 特 点 典型用途
代表 钢号
汽车用 良 好 的 力 学 性 能 和汽车大梁、车轮 510L 钢 优良的加工性能。 轮辋及轮辐等。 380CL 除具有与结构钢一 专 用 耐候钢 样 的 综 合 性 能 外 ,用于车辆车厢和 SPA-H 还 具 有 良 好 耐 大 气集装箱制造。 钢 腐蚀性能。 高 纯 净 度 , 具 有 高用于制造石油、 管线钢 强 度 、 低 温 冲 击 韧天然气输送管线 S415 J55 性和良好焊接性。 和石油套管。
注意:钢中的元素包括有益元素(有意加入钢中的
)和有害元素2种。钢中各元素含量的不同对应有不同的 预期使用性能,或者说,钢材使用要求和性能要求的不 同必须以多样化的钢的化学成分来保证。
1、碳(C ):
碳主要以碳化物形式(Fe3C),是决定钢强度的主 要元素。随钢中含碳量升高: ——硬度、强度提高 ——塑性、韧性和冲击韧性降低,焊接性能下降
出钢过程脱氧(Si,Mn ,Al ):
(1)硅脱氧 2[O] + [Si] =(SiO2)
19
三、炼钢生产流程与工艺 (二)、炼钢主要生产工序冶金原理
2. 转炉冶炼工序
转炉钢的冶炼工艺过程:
将铁水、冷料装入转炉,摇正炉体后降氧枪、同时 加造渣料开始吹炼,当氧气流与炉内铁水接触时,硅、 锰开始氧化(称为点火),熔池温度升高后进入脱碳氧 化,在吹炼末期,根据炉口火焰、供氧参数判断终点后 ,提枪倒炉测温取样,根据检验结果可确定出钢(必要 时可补吹处理后再出钢)。出钢过程中根据需要加入铁 合金进行脱氧合金化。出完钢溅渣后,将剩余钢渣倒入 渣罐,即可开始下一炉钢的冶炼。
23
三、炼钢生产流程与工艺
(二)、炼钢主要生产工序冶金原理 5. 连铸工序
工艺原理:
连续铸钢即把钢水连续注入特定形状的水冷结晶器,并经 二次喷水冷却凝固得到连铸坯的过程。
连续铸钢的工艺过程为:
待浇钢水到钢包回转台后,旋转至浇注位,打开滑动水口 向中间包浇注钢水,当中间包钢水液面达到一定高度时开启中 间包塞棒(水口)将钢水注入结晶器。当结晶器内钢液上升到 一定高度后,拉矫机起步,利用引锭装置将铸坯一同拉出,在 二冷区,铸坯喷水冷却逐渐凝固。引锭过拉矫机后切去坯头, 铸坯切割为要求的定尺后,经输坯辊道送入冷床。
12
二、钢中主要化学元素的作用
6、其它合金元素(Al,Nb,V,Ti):
铝:起脱氧和合金元素双重作用,可细化晶粒
、固定钢中氮,提高冲击韧性、降低冷脆和时效 倾向性。 注:个:常用微合金元素,可细化晶粒,
改善钢的综合性能(强度,塑性,焊接等等)。
13
二、钢中主要化学元素的作用
(一)、炼钢生产过程简述
炼钢的生产过程可简单地描述为:
铁水进厂脱硫处理后装入转炉,配加冷料后 吹氧冶炼至终点,倒炉出钢时添加铁合金,再进 行吹氩精炼(特殊质量要求的钢种需LF精炼甚至 RH真空处理),即可送连铸机浇注得到连铸坯。
17
三、炼钢生产流程与工艺 (二)、炼钢主要生产工序冶金原理
1. 铁水予处理工序
21
三、炼钢生产流程与工艺 (二)、炼钢主要生产工序冶金原理
3. LF精炼工序
依靠钢包内的白渣,在低氧的气氛下,钢包底 吹氩气搅拌并由石墨电极对钢水加热进行精炼。
冶金原理:
见前述脱氧反应(沉淀脱氧及扩散脱氧)。
LF精炼的工艺过程为:
钢水到站后取样测温,然后就升温位,降电极 加热埋弧精炼,升温完毕后调整成分出站。 精炼过程的四个特点是:炉内气氛、氩气搅拌 、埋弧加热和白渣精炼。
2. 转炉冶炼工序
炼钢就是用氧化的方法,通过直接或间接的氧化及冶金 造渣反应,将铁水中的杂质元素去处,再依据目标钢种的技 术要求加入适量种类的合金,即可生产出合格的钢水。
冶金原理如下:
(1)脱硅反应: 2(FeO)+ [Si] =(SiO2)+ 2[Fe] 2[O] + [Si] =(SiO2) (2)脱碳反应: [O] + [C] = {CO} (3)脱磷反应: 2[P] + 5(FeO)+ n(CaO)= (nCaO· 2O5)+ 5[Fe] P
工业上使用的脱硫剂有电石、石灰、苏打、金 属镁等。
冶金原理如下:
金属镁: Mg(g) + [S] = Mg S(s)
铁水脱硫的工艺过程为:
铁水包送至喷吹脱硫位,下降喷枪,以氮气 为载体把脱硫剂吹入铁水,脱硫后扒渣,由天车 将脱硫铁水装入转炉。
18
三、炼钢生产流程与工艺 (二)、炼钢主要生产工序冶金原理
3
一、主要热连轧产品分类及用途简介
代表 产品类别 特 点 典型用途 钢号 普通结 保证力学性能建筑、一般结构件, Q235 SS400 构用 和工艺性能。 电缆桥架等。 GDQ240
结 具有良好的综桥梁、工程机械、汽 构 焊接结 合力学性能和车等要求焊接性能优 Q345B 用 构用 焊接性能。 良结构件。 钢
5
一、主要热连轧产品分类及用途简介
产品类别 特 点 典型用途 代表 钢号
特 殊 用 途 钢
防滑要求船板 扁豆形花纹,具有 甲板、建筑楼 Q235H 花纹板 良好防滑性能。 梯等。 优良的冷轧延展性 马口铁 ,适用于较复杂冲冷轧镀锡基板 SPHC-M 压变形加工
热水器 高强度及良好的成热水器内胆制 GFR390 造 内胆用钢 型性
四、SPHC的炼钢工艺及洁净度控制
(三)高纯净钢主要指标的实际意义
(1)去除杂质元素:
超低[C]:如汽车板; 超低[S],低[H]:如输气管线; 超低[N]:如铁素体不锈钢废气管,冷锻线棒材; 超低[P]:如高压容器钢板。
(2)去除夹杂物(洁净度)
超低T[O]:如滚珠钢,汽车板; 夹杂物尺寸及形态控制:如拉拔钢丝,管线钢。
22
三、炼钢生产流程与工艺 (二)、炼钢主要生产工序冶金原理
4. RH精炼工序 冶金原理:
(1)脱氢: a[H]=KH(pH2)1/2 (2)脱碳脱氧: [O] + [C] = {CO}
RH精炼的工艺过程为:
钢水包就位,顶起,浸渍管插入抽真空,钢水 吹氩循环(必要时吹氧处理),破真空,钢水包复 位,出站。
20
三、炼钢生产流程与工艺
(二)、炼钢主要生产工序冶金原理
2. 转炉冶炼工序 转炉冶炼工艺的5大基本操作制度:
(1)装入制度:采用分期(按炉龄)定量装入制度。先装铁 水后装废钢。 (2)供氧制度:采用分期(按炉龄)恒压变枪位供氧制度。 (3)造渣制度:一般钢种采用单渣法,冶炼高碳钢或铁水磷 硫含量高时也采用双渣法。 (4)温度制度:根据冶炼钢种要求和铁水温度、成分、炉况 等确定废钢加入量,控制终点出钢温度。 (5)脱氧合金化制度:依终点钢水温度、成分及钢种要求确 定合金种类和加入量,按脱氧能力由弱至强的顺序依次加入 ,钢水出至3/4时加完。
技术讲座资料
洁净钢的生产及品种钢开发
唐山国丰钢铁有限公司
顾克井
1
主要内容
一、主要热连轧产品分类及用途简介
二、钢中主要化学元素的作用
三、炼钢生产流程与工艺 四、SPHC的炼钢工艺及洁净度控制 五、品种钢开发的技术策划及实施
2
一、主要热连轧产品分类及用途简介
产品类别 特 点 典型用途 代表 钢号
一般 有一定的延展性适用冷 轧 后 用 于 建 筑 ( Q195L(LF) Q195L-1(非LF ) 冷轧 于一般冷轧 涂镀)、油桶等
三、炼钢生产流程与工艺
15
三、炼钢生产流程与工艺
散状料(石灰、白云石、萤石、铁矿石、污泥球等)
高炉铁水 脱 硫 站 氧(氮、氩)气 金属冷料
顶底复吹转炉
回炉钢 铁合金 钢包
钢渣 煤气柜 除尘 方坯连铸机 吹 氩 站
LF精炼炉
板坯连铸机
造渣料、铁合金等
16
RH(2#生产线)
三、炼钢生产流程与工艺
注意:锰增加钢的淬透性、耐磨性(加工硬化特 点—红硬性)。
10
二、钢中主要化学元素的作用 4、磷(P):
磷使钢的塑性、韧性降低。 ——尤其在低温时明显降低韧性(冷脆) ——可降低铁损,提高电磁性能;提高抗腐蚀性 ;改善切削加工性能。
11
二、钢中主要化学元素的作用 5、硫(S):
硫含量升高产生“热脆”。 ——降低钢材横向(垂直于加工方向)强度 、延性,冲击韧性,降低钢的抗HIC能力。 ——改善钢的切削加工性能。
产品 汽车板 易拉罐 Shadow mask for CRT 防罩屏 轮胎钢芯线 滚珠 管线 钢轨 备注:D 指夹杂物直径
26
洁净度 T[O]<20ppm T[O]<20ppm D<50μm D<20μm
备注 防薄板表面线状缺陷 防飞边裂纹 防止图象浸蚀 防冷拔断裂 增加疲劳寿命 抗腐蚀 防断裂
D<5μm 冷拔 0.15-0.25mm D<10μm T[O]<10ppm D<15μm D<100μm 氧化物形态控制 T[O]<20ppm 单个 D<13μm 链状 D<200μm
(3)成分控制
窄化学成分控制范围,保证产品性能均一性。
27
四、SPHC的炼钢工艺及洁净度控制
钢洁净度控制的主要内容是:
T[O]要低<20ppm; 夹杂物数量要少; 夹杂物尺寸要小<50µ m; 夹杂物形态要合适。
28
四、SPHC的炼钢工艺及洁净度控制
由前述可见: 纯净钢或洁净钢是一个相对概念; 某一杂质含量降低到什么水平决定于钢种 和产品用途; 有害元素的降低的程度决定于装备和工艺 现代化水平; 不管生产什么用途的钢, 总是要求钢中夹杂 物数量的尺寸、形态得到控制。