论文:济钢洁净钢生产工艺论文
洁净钢生产工艺技术

洁净钢生产工艺技术1. 简介洁净钢是一种具有高纯度、低气体含量和低不纯物含量的钢材。
洁净钢的生产工艺技术在钢铁行业中起着重要的作用。
本文将介绍洁净钢的生产工艺技术、工艺流程和相关设备。
2. 洁净钢生产工艺技术的意义洁净钢的生产工艺技术可以有效降低钢材中的气体含量和不纯物含量,提高钢材的纯度和质量。
洁净钢广泛应用于汽车制造、航空航天、电子设备等高端领域,对提高产品的品质和性能具有重要意义。
3. 洁净钢生产工艺技术的主要方法洁净钢的生产工艺技术主要包括如下几种方法:3.1 精炼精炼是洁净钢生产的关键步骤之一。
通过在高温条件下对炼钢液进行溶解和脱气处理,可以将钢液中的气体含量和不纯物含量大大降低,提高钢材的纯度。
3.2 熔盐浸渍熔盐浸渍是一种将钢材浸入熔盐中,通过离子交换和溶解作用去除钢材表面的氧化物和其他杂质的方法。
这种方法可以显著降低钢材中的含氧量和含杂质量,提高钢材的纯度。
3.3 真空处理真空处理是将钢材放入真空设备中进行处理的方法。
利用真空环境可以有效去除钢材中的气体,减少钢材中的含气量和含杂质量,提高钢材的纯度。
3.4 气体透平气体透平是通过气体的透平作用去除钢材中的气体的方法。
通过将高速气体喷射到钢材中,可以将钢材中的气体冲出,降低钢材中的气体含量。
3.5 再结晶控制再结晶控制是通过控制钢材的热处理过程中的再结晶过程,来提高钢材的晶粒度和纯度的方法。
通过精确控制再结晶过程中的温度和时间,可以得到具有更好性能和纯度的洁净钢材。
4. 洁净钢生产工艺技术的工艺流程洁净钢的生产工艺技术一般包括以下几个主要步骤:1.原料准备:将适量的生铁、废钢和合金等原料按照一定比例混合。
2.熔炼:通过高炉冶炼或电炉冶炼,将原料熔化成钢水。
3.精炼:在精炼炉中对钢水进行溶解和脱气,去除其中的气体和不纯物。
4.过滤:通过过滤器将钢水中残余的杂质和固体颗粒去除。
5.熔盐浸渍:将钢材浸入熔盐中,去除表面氧化物和其他杂质。
济钢洁净钢生产工艺实践
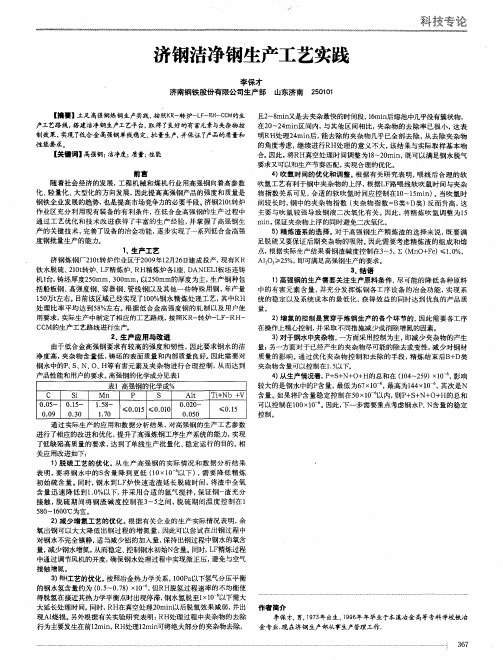
CC M的生产工艺路线 进行对于高 强钢生 产精 炼渣 的选择 来说 , 既要 满 足脱硫 又要 保证 后期夹杂 物 的吸附 。 因此需 要考虑 精炼 渣的组 成和 熔 点, 根据 实际生 产结果看 钢渣碱度 控制在3 ~ 5 , ∑( Mn O + F e ) ≤1 . 0 %,
l
表1高强钢的化学成%
C I S i l Mn I P 1 S l Al t l Ti +Nb + V
f I 1 ’ i l ≤ ㈣ s l ≤ 0 埘 o 1
l ≤ s
较大的是 钢水 中的P 含量 , 最低为 6 7 × 1 0 一, 最 高为1 4 4 × 1 0 _ 。 。 , 其次是 N 含量 。 如 果将P 含 量稳 定控制 在5 0 × 1 0 以 内, NP + S + N+ 0 + H的总和 可以控制 在1 0 0 x 1 0 ~。 因此 , 下一步需 要重 点考虑钢水P 、 N含量 的稳定
在操 作上精心控制 , 并采取 不同措施减少或 消除增氮的 因素 。 2 , 生 产应 用与 改进 3 ) 对于钢水 中夹杂物 。 一方面采用控 制为主 , 即减 少夹杂 物的产生 由于低 合金高强 钢要求 有较 高的强度 和韧 性 , 因此要求 钢水 的洁 量 ; 另一方面对于 已经产生 的夹杂 物尽可能的 除去或变性 , 减少对 钢材 净度 高, 夹杂 物含 量低 , 铸 坯的表 面质量和 内部质量 良好 因此需 要对 质量 的影响 。 通过优 化夹杂 物 控制和 去除 的手 段, 精 炼 结束后 B + D 类 钢水 中的P 、 S 、 N、 O、 H等有 害元 素及夹 杂物 进行合 理控制 , 从而 达到 夹杂物含量可 以控 制在1 . 5 以] - a 产品性能和用户的要求。 高强钢 的化学成分见表 1 4 ) 从生产情况看 , P + s + N+ 0+ H的总和在 ( 1 0 4 - 2 5 9 ) × 1 0 ~, 影响
洁净钢的生产实践

洁净钢的生产实践
洁净钢是一种高质量、低含杂质的钢,它的生产实践主要有以下几个方面。
一、原料准备
使用洁净钢前,必须对原料进行良好的准备,包括对原料的分析、检测和加工。
首先,应检查原料的成分,如少量元素的含量、碳含量和其它元素的含量,以确保原料的质量。
其次,通过进行化学分析,确保原料不含有杂质,以及原料中应该有的元素含量。
最后,应将原料进行冶炼或热处理,以达到所需的物理性能。
二、清洗
为了确保洁净钢的质量,必须在生产过程中进行清洗。
清洗的目的是去除原料上的污垢和油污,以便更好地精炼钢,使其达到洁净钢的要求。
清洗的方法有化学法和物理法。
常用的物理法清洗方法有振动清洗、气动清洗、风力清洗、旋流清洗、喷射清洗等。
三、精炼
精炼是洁净钢生产实践中最重要的环节,因为它是洁净钢质量的决定因素。
精炼的目的是去除杂质,使钢中的各种元素达到所需的含量。
精炼的方法有电弧炉精炼法、渣浆精炼法和熔渣精炼法。
四、冷却
冷却是洁净钢生产实践的重要一步,它主要是为了确保洁净钢的结构稳定,同时也是为了改善洁净钢的耐腐蚀性和焊接性能。
冷却的方法有水冷却、空气冷却等。
五、检测
检测是洁净钢生产实践的最后一步,目的是确定洁净钢的质量。
检测主要有机械性能检测、表面质量检测、化学成分检测、热处理检测等。
以上是洁净钢生产实践中的主要步骤,其中每一步都必须精确控制,才能保证洁净钢的质量。
只有通过严格的检测,才能保证洁净钢的质量,从而满足客户的要求。
济钢无钢事例

济钢无钢事例
近年来,随着环保意识的提升和产业结构的调整,济钢集团在无钢事例方面做出了积极的努力,为推动绿色发展作出了突出贡献。
一、创新科技,提升能源效率
济钢集团充分认识到能源消耗对环境造成的影响,积极推进技术创新,提升能源效率。
通过引进先进的高效冶炼技术,济钢集团成功降低了钢铁生产过程中的能源消耗。
同时,还利用余热发电技术,将冶炼过程中产生的废热转化为电能,实现了资源的最大化利用。
这一系列措施不仅降低了碳排放,还大幅减少了环境污染,为绿色发展树立了榜样。
二、优化产业结构,推动绿色转型
济钢集团积极响应国家政策,加大了对绿色产业的投入。
通过优化产业结构,逐步转向高附加值和绿色环保型产业,济钢集团实现了从传统钢铁企业到现代化绿色企业的转型升级。
同时,济钢集团还加强了与环保科研机构的合作,共同开展环境保护技术研究,为绿色转型提供了科技支撑。
三、加强环境监管,履行企业社会责任
济钢集团始终将环境保护作为企业的核心责任,加强了环境监管工作。
通过建立健全的环境保护管理体系,济钢集团确保了钢铁生产过程中的污染物排放符合国家标准。
同时,济钢集团积极参与环境
保护公益活动,关注社会问题,履行企业社会责任。
他们通过捐款、志愿服务等方式,积极参与社会公益事业,为推动绿色发展贡献力量。
济钢集团无钢事例的成功经验,为其他钢铁企业提供了宝贵的借鉴。
通过创新科技、优化产业结构和加强环境监管,钢铁行业的绿色发展已经成为可能。
未来,我们有理由相信,济钢集团将继续在无钢事例方面取得更大的成就,为推动绿色发展贡献更多力量。
让我们共同努力,为建设美丽中国贡献自己的一份力量。
洁净钢生产技术及应用
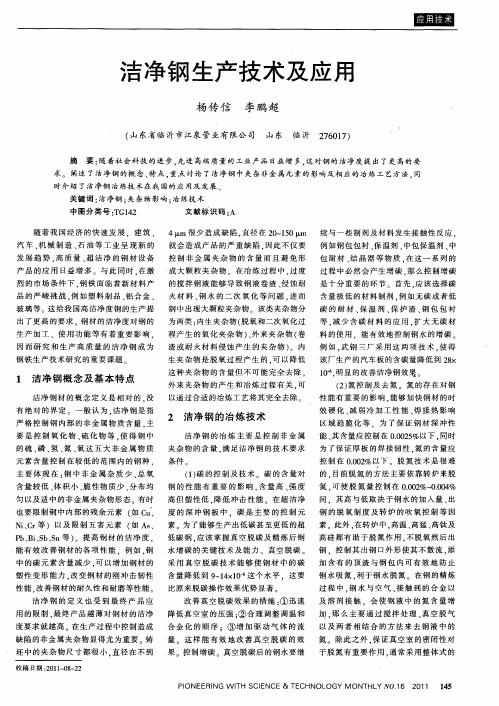
含量 较 低 、 积 小 、 性 物 质 少 、 布 均 钢 的性 能 有 重 要 的影 响 。 量 高 、 度 氮 . 使脱 氮 量 控 制 在 00 2 004 体 脆 分 可 . %~ . % 0 0 含 强 出 匀 以及适 中的非 金属 夹杂 物形 态 有 时 高但 塑性 低 . 降低 冲 击性 能 。在 超 洁 净 间 .其 高与 低取 决 于钢 水 的加 入量 、 也要 限 制钢 中 内部 的残余 元 素 ( C 、 度 的深 冲钢 板 中 .碳 是 主 要 的控 制 元 钢 的 脱 氧 制 度 及转 炉 的 吹氧 控 制 等 因 如 u
求。 阐述 了洁净 钢 的概 念 、 点 , 点讨 论 了洁净钢 中夹 杂非金 属 元 素的 影 响及相 应 的 冶炼 工艺 方法 , 特 重 同 时介 绍 了洁净 钢 冶炼技 术在 我 国的应 用及 发展 。 关键 词 : 洁净钢 : 夹杂物影 响 : 冶炼技 术
中图分类号 :G 4 T 12
效 硬 化 、 弱 冷 加 工 性 能 、 接 热影 响 减 焊 区域 趋 脆 化 等 .为 了保 证 钢 材 深 冲性 能 、 含量应 控制 在 00 2 %以下 。 时 其 .0 5 同
为 了保 证厚 板 的焊 接 韧性 . 的含量 应 氮
要 是 控 制 氧 化 物 、 化 物 等 . 得 钢 中 硫 使
品 的严 峻挑 战 , 例如 塑 料 制 品 、 合 金 、 铝
出了更 高 的要 求 钢材 的洁净度 对 钢 的
火 材 料 、 水 的二 次 氧 化 等 问题 , 而 钢 进
为两类 : 内生夹 杂物 ( 氧和二 次氧化 过 脱 渣 或 耐火 材 料 侵蚀 产 生 的夹 杂 物 ) 内 。 生 夹 杂物 是 脱 氧过 程 产 生 的 . 以降 低 可
RH/TCOB精炼工艺的实践与优化
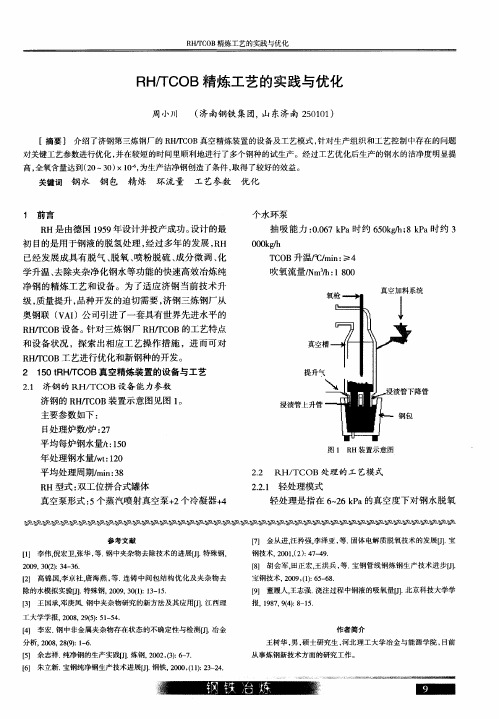
真空泵形式 : 个蒸汽 喷射真 空泵 + 个冷凝 器+ 5 2 4
2 . 轻处 理模式 .1 2
轻处理是 指在 6 2 P 的真空度下对 钢水脱氧 ~ 6k a
参 考 文 献
【 金从 进, 7 】 汪矜强, 李泽亚 , 固体电解质脱氧技术的发展[ _ 等. J 宝 】 钢技术. 0 1 2 : 7 4 . 20 , )4—9 (
式 中:
环流量 d i; m n 浸渍管 内径 m;
G_ _ 环流气流量 N a i; m/ n m
一
量。 也可提高钢水 的洁净度。通过这种方法大量处理 多炉低碳铝镇静钢 , 该法节约铝约 l 钢 , 有明显 k 具
的经济效益 。 22 本处理模式 .. 2
P, o P分别是大气压和槽 内压力 k a P; 济钢 10 H设备 的 D 0 5i,大气压 P= O 5t R =. 5 n ol0
R /C B精炼工艺 的实践与优化 HT O
R /C H _ OB精炼 工 艺 的 实践 与优 化 r
周小川 ( 南钢铁 集 团, 济 山东济 南 200 ) 5 11
[摘要 ] 介绍 了济钢第三炼钢厂的 R /C B真空精炼装 置的设 备及 工艺模式 , Hr O 针对生产组织 和工 艺控 制中存在的问题 对关键工艺参数进行优化 , 并在较短 的时间里顺利地进行 了多个钢种 的试生产 。经过工艺优化后生产 的钢水 的洁净度 明显提 高, 全氧含量达到(0—3 ) 0 为生产洁净钢创造 了条件 , 2 0 ×1 , 取得 了较好的效益 。
[] 胡会军, 8 田正宏 , 王洪兵 , . 等 宝钢管线 钢炼钢生产技术进 步『. J 1 宝钢技术, 0 9 ()6 — 8 2 0 ,1: 5 6 .
环保型钢材生产技术研究

环保型钢材生产技术研究一、前言钢材是现代工业生产的重要原材料,而环境污染已经成为了全球范围内的问题。
如何在钢材生产过程中实现环保,是当前钢铁行业需要解决的一项重要问题。
本文将着重探讨环保型钢材生产技术的研究,包括原材料清洁化技术、生产工艺优化技术以及污染物治理技术等方面。
二、环保型钢材生产技术1. 原材料清洁化技术传统的钢材生产过程中,炼钢用的焦炭和铁矿石都会产生大量的二氧化碳和硫化氢等有害气体,对环境造成污染。
因此,在环保型钢材生产中,清洁化原材料是很重要的一步。
首先,清洁能源的利用。
环保型钢材生产中,应采用清洁能源,减少对环境的影响。
如采用BFG(高炉煤气)代替石油等传统燃料,既可以降低环境污染,还可以减少燃料消耗。
其次,对原材料进行预处理。
在采用焦炉煤气等清洁能源的情况下,仍然会产生有毒有害物质,如一氧化碳和氰化物等。
为了降低对环境的影响,应采用煤气清洁化技术,去除有毒有害物质。
2. 生产工艺优化技术环保型钢材生产中,钢材生产工艺的优化也极为重要。
采用环保型钢材生产工艺,可在生产过程中降低对环境的污染,提高钢材的质量。
其中,主要工艺优化如下:(1)清洁炼钢技术:传统的炼钢过程中,产生的烟尘和废气会对环境造成污染,采用清洁炼钢技术,可降低对环境的影响。
目前,生产中采用的清洁炼钢技术有—炼钢氧吹技术和电弧炉直接还原法等。
(2)节能技术:生产过程中钢材炉温至关重要,可以通过节能技术来减少炉温。
例如,在热轧钢板生产中,采用先小后大的卷取工艺,可以减少热量损耗,降低对环境的污染。
(3)循环利用技术:钢材生产中,废钢和废渣的处理方法直接影响钢铁产品的绿色化程度。
采用循环利用技术,将钢材生产过程中的废渣、废渣回收再利用,减少浪费和对环境的影响。
3. 污染物治理技术钢铁生产过程中产生的烟尘、废水、废气等污染物,都会对环境造成污染。
因此,针对这些污染物的治理技术也至关重要。
(1)烟尘治理技术:在钢铁生产过程中,通过采用粉尘收集器、静电除尘器等烟尘治理技术,降低钢铁生产过程中产生的粉尘对环境的影响。
31.75mm厚规格X65M管线钢的开发
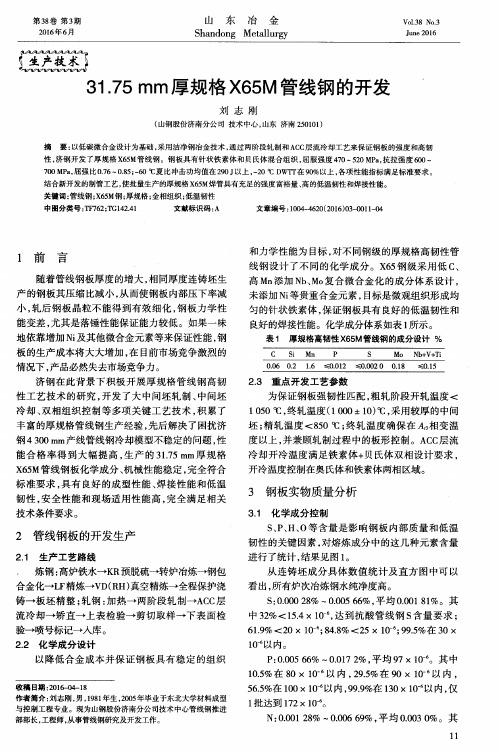
C Si Mn P
S
Mo Nb+V+Ti
0.06 0.2 1 6 ≤0012 ≤00020 0 1R :≤:0 1 5
2.3 重点 开发工 艺参数 为保 证 钢板 强韧 性 匹配 ,粗轧 阶段 开 轧温 度 <
1 050℃ ,终轧 温度 (1 000-4-10)oC,采 用较 厚 的 中间 坯 ;精 轧 温度 <850℃ ;终 轧 温 度确 保 在 相变 温 度 以上 ,并 兼顾 轧制 过程 中的板形 控 制 。ACC层 流 冷却开冷温度满足铁素体+贝氏体双相设计要求 , 开冷 温度控制 在奥 氏体和铁 素体两相 区域 。
中图分类号 :TF762;TG142.41
文献标识码 :A
文章 编号 :1004—4620(2016)03—0011-04
1 前 言
随着 管线 钢板 厚度 的增 大 ,相 同厚 度连 铸坯 生 产 的钢板 其 压缩 比减 小 ,从 而 使钢 板 内部压 下率 减 小 ,轧 后 钢 板 晶粒 不 能得 到有 效 细化 ,钢板 力 学 性 能变差 ,尤其是落锤性能保证能力较低。如果一味 地依靠增加 Ni及其他微合金元素等来保证性能 ,钢 板 的生产 成本 将 大大增 加 ,在 目前市 场竞 争激 烈 的 情况下 ,产品必然失去市场竞争力 。
3 钢板实 物质量分 析
3.1 化学成 分控制 s、P、H、0等 含 量 是 影 响钢 板 内部 质量 和低 温
韧性 的关 键 因素 ,对熔 炼 成分 中的这几 种元 素含 量 进行 了统计 ,结果见 图 1。
从 连 铸 坯 成 分 具体 数 值 统 计 及 直方 图 中可 以 看 出 ,所有炉 次冶炼钢 水纯净 度高 。
洁净钢高效生产工艺集成技术探讨

性、 抗 裂 和抗 腐 蚀性 等 要 求 不 断提 高 , 从而 对 钢 材 的 洁净度 提 出 了越 来 越高 的要 求 , 洁净 钢 的市场 需 求量 也越 来越 大 。进 一步减 少 钢 中杂质 含量 , 提 高 钢种 洁净 度 , 成 为 钢 铁 冶金 发 展 的 主要 方 向 , 也 是 钢铁企业 提高产 品竞争 力 的主要 途径之 一 [ 2 _ 3 J 。 本研 究探讨 的高效洁净钢生产工 艺 中的“ 高
效” 包含有高效率和高效益两层含义 , 即在最大 限 度 提高 生产 效率 的前 提下 生 产 出高 质量 、 低 成本 的
洁净钢 产 品。
2 洁净 钢冶炼 的主要 工艺手段
若 在 同一 容器 中完成 多项 冶炼 任务 , 其 中必 然 会存 在许 多复杂 的矛盾 , 如: 脱 c与脱 P的矛盾 、 脱P
温、 脱 0合 金化 、 控 制 夹杂 物 、 成分微 调 等过 程各 自
在最 佳 的热 力学 、 动 力学 条件 下进 行 。虽然 这样 会
收稿 日期 : 2 0 1 3 — 0 5 — 1 6 作者简介 : 成小龙 , 男, 1 9 7 7 年生 , 2 0 0 2 年毕业 于包头钢铁学院钢铁
第3 5 卷 第4 期
2 0 1 3 年8 月
・ ,。 ’ , ’ , 。 ~ , 、 、 “ . 、 、 ’ ?
山 东 冶 金
t a l l u r g y S h a n d o n g Me
V0 I J 3 5 No . 4 Au g u s t 2 0 1 3
个工序的衔接 , 上世纪9 0 年代中后期 , 新E t 铁、 住友 金属 、 神 户 制钢 、 N K K等纷 纷 开 展利 用 氧气 转 炉进
洁净钢的工艺流程

洁净钢的工艺流程洁净钢啊,简单来说就是杂质特别少的钢。
那它的工艺流程是有好多环节的哦。
一、原料的选择。
在制作洁净钢的时候,原料的选择那可太重要啦。
就像我们做菜一样,食材不好,做出来的菜味道就不行。
制作洁净钢要选优质的铁矿石和其他一些添加的原料。
比如说铁矿石要是含铁量高的,杂质少的那种。
要是含铁量低,里面有好多乱七八糟的东西,像硫啊磷啊这种杂质太多,那后面要费好大劲儿去除呢。
而且其他的添加原料也要纯净,不然就会把杂质带进钢里面去。
二、炼铁环节。
这炼铁就像是一场魔法表演的开始。
把选好的铁矿石、焦炭等原料放进高炉里。
高炉可是个大家伙,在高炉里会发生好多神奇的反应。
高温下,焦炭会和氧气反应产生热量,这个热量能让铁矿石中的铁氧化物被还原成铁水。
但是呢,这时候铁水里还是有一些杂质的,像硅啊、锰啊之类的,不过没关系,后面还有步骤来处理它们呢。
三、炼钢环节。
炼钢环节那就是让铁水大变身的时候啦。
这时候会把铁水倒进转炉或者电炉里。
在转炉里,会往里面吹入氧气,这个氧气可厉害啦,它能把铁水里多余的碳烧掉,让碳的含量达到我们想要的水平。
而且啊,那些在炼铁环节残留的杂质,像硅、锰还有一些硫磷等,也会在这个过程中被去除一部分。
在电炉里呢,是通过电能来加热铁水,也能达到类似的去除杂质的效果。
在这个过程中,炼钢工人就像超级英雄一样,时刻盯着各种参数,确保炼钢的过程顺利进行。
四、精炼环节。
精炼环节就像是给钢做一个深度清洁和调理。
这个环节有好多不同的方法呢。
比如说有真空精炼,把钢水放到真空环境里,那些在常压下很难去除的气体杂质,像氢气,在真空环境下就很容易跑出来啦。
还有炉外精炼,会往钢水里加入一些特殊的材料,这些材料就像小清洁工一样,把钢水里剩余的微小杂质吸附起来。
这就好比我们给脸做深度清洁,把毛孔里的脏东西都弄出来,让钢变得更加纯净。
五、连铸环节。
经过前面的重重工序,钢水已经很纯净啦。
这时候就到了连铸环节。
钢水会被倒入连铸机里,连铸机就像一个神奇的模具制造机。
洁净钢制备技术的研究现状及发展
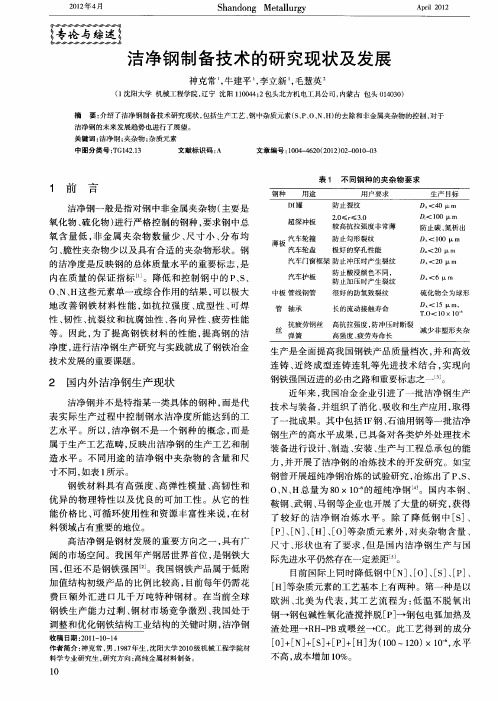
高 洁净 钢是 钢材 发 展 的重要 方 向之一 , 具有 广
阔 的市场 空 间 。我 国年 产钢 居世 界首 位 , 是钢铁 大 国 , 还不 是钢 铁 强 国 。我 国钢铁 产 品属 于低 附 但
尺寸 、 形状 也 有 了要 求 , 是 国 内洁净 钢 生产 与 国 但 际先进 水平仍然存 在一定 差距b。 目前 国 际上 同时 降低 钢 中 [ 、0] [] [ ] N] [ 、S 、P 、 [ 等杂质 元素 的工艺 基本上 有两 种 。第一种 是 以 H] 欧洲 、 北美 为 代 表 , 工 艺 流 程 为 : 温 不 脱 氧 出 其 低 钢一 钢包 碱性 氧化 渣搅 拌脱 [ 卜+ 包 电弧加 热及 P 钢
鞍钢 、 钢 、 武 马钢等 企业 也开 展 了大量 的研究 , 得 获
了较 好 的 洁 净 钢 冶 炼 水 平 。 除 了降 低 钢 中 [ ] S、 [ ] [ 、H] [ ] 杂质 元 素外 , P 、N] [ 、 0 等 对夹 杂 物 含 量 、
能价 格 比 、 循 环 使用 性 和 资源 丰 富性 来 说 , 材 可 在
出
D <10 m 0
氧 含 量 低 , 金 属 夹 杂 物 数 量 少 、 寸 小 、 布均 非 尺 分 匀、 脆性 夹 杂物 少 以及 具 有合适 的夹杂 物形状 。钢 的洁净 度是 反 映钢 的总体 质量 水平 的重 要标 志 , 是 内在 质 量 的保 证 指 标 n。降低 和 控 制 钢 中 的 P S 、、 O、 H这 些元 素单一 或综 合作用 的结果 , N、 可以极 大 地 改 善 钢 铁 材 料 性 能 , 抗 拉 强 度 、 型 性 、 焊 如 成 可 性、 韧性 、 裂 纹 和抗 腐 蚀 性 、 向异 性 、 劳 性 能 抗 各 疲 等 。 因此 , 了 提高 钢 铁材 料 的性 能 , 高钢 的 洁 为 提 净度 , 进行 洁净 钢生 产研 究与 实践 就成 了钢 铁冶金
洁净钢生产工艺及技术

洁净钢生产工艺及技术1. 引言洁净钢是一种具有高纯净度和低杂质含量的钢材,它在现代工业中具有广泛的应用。
洁净钢的生产工艺和技术对于提高钢材的质量和性能具有重要意义。
本文将介绍洁净钢的生产工艺及技术,包括材料准备、熔炼工艺、净化工艺和热处理工艺等方面。
2. 材料准备洁净钢的生产首先需要准备高质量的原材料。
一般而言,使用优质的铁矿石和石墨粉为原材料。
在材料准备过程中,需要对铁矿石进行破碎、筛分和磁选等处理,以去除其中的杂质。
同时,还需要对石墨粉进行筛分和干燥处理,以确保其纯净度和质量。
3. 熔炼工艺洁净钢的熔炼工艺是保证钢材质量的关键步骤。
在熔炼过程中,采用电弧炉作为主要设备,并在炉内加入适量的石墨粉,以促进石墨的溶解和扩散。
此外,还需要在熔炼过程中控制熔炼温度、保持炉内气氛的稳定,并通过合理调整熔炼时间和翻炉工艺等措施,以确保熔炼的钢液质量达到洁净钢的要求。
4. 净化工艺净化工艺是提高钢材纯净度的重要措施。
常用的净化工艺包括真空脱气、氧化脱硫和氢脱氮等。
在真空脱气过程中,通过将熔炼好的钢液置于真空环境下,利用钢液中的氢、氮等气体的挥发性,将其去除。
氧化脱硫是指在钢液中加入氧化剂,使之与硫反应生成气体,从而将硫从钢液中去除。
氢脱氮是指通过在钢液中通入氢气,使之与钢液中的氮气反应生成气体,从而将氮从钢液中去除。
5. 热处理工艺热处理工艺是洁净钢生产的最后一道工序,它能够通过改变钢材的组织结构,进一步提高钢材的性能。
常见的热处理工艺包括淬火、回火和正火等。
淬火是指将热处理后的钢材迅速冷却,以使其获得较高的硬度和强度。
回火是指将淬火后的钢材加热到适当的温度,然后冷却,以使其获得合适的韧性和延展性。
正火是指将热处理后的钢材加热到适当的温度,保温一段时间后,进行缓慢冷却,以改变钢材的组织结构。
6. 结论洁净钢的生产工艺及技术对于提高钢材的质量和性能具有重要意义。
在生产过程中,需要注意材料准备、熔炼工艺、净化工艺和热处理工艺等方面的要求,以确保生产出符合洁净钢标准的优质钢材。
洁净钢生产新流程的研究与开发(刘浏原件)【范本模板】

洁净钢生产新流程的研究与开发刘浏钢铁研究总院1.前言建设高效低成本洁净钢平台是市场和时代发展的要求,是洁净钢生产领域的重大技术革命。
其目标是实现转炉直接冶炼洁净钢,并使转炉生产效率提高1倍,洁净钢生产成本低于传统转炉普通钢。
本文系统介绍了钢铁研究总院与首钢合作研究开发的洁净钢生产新工艺流程在京唐钢铁公司的开发与应用情况,阐述了高效低成本洁净钢平台建设的三项核心技术:洁净钢稳定化生产工艺、洁净钢高效化生产工艺、洁净钢低成本制造工艺.2.传统洁净钢生产流程与主要问题图1给出传统洁净钢生产流程示意图。
传统洁净钢生产流程的基本特征是:钢水提纯主要依靠炉外精炼,精炼工艺流程长,生产波动大。
也是造成钢水质量不稳定,生产能耗高、成本高和CO2排放量高的主要技术原因。
高炉LF转炉冶炼铁水脱硫RH CC图1 传统洁净钢生产流程示意图传统流程的主要工艺特点是:●采用全量铁水脱硫预处理工艺;●采用传统转炉炼钢工艺脱磷、脱碳;●采用LF炉还原精炼工艺进行深脱硫和脱氧,控制T.O含量;●采用RH真空精炼工艺,降低钢中气体含量;●采用全连铸工艺深入分析传统流程中进行的脱磷、脱硫、脱碳、脱硅等反应过程可以看出,传统流程中存在以下基本矛盾:(1)炼钢回硫,脱硫后的超低硫铁水(通常控制[S]≤0.005%)在转炉冶炼过程中大量回硫,通常不能满足连铸钢水对硫含量的基本要求,需通过LF炉进行二次脱硫。
(2)低碳脱磷,由于转炉中碳、磷反应平衡限制了转炉实现高碳脱磷的反应能力,钢水脱磷大多在[C]≤0.3%以下才能有效进行。
因此,稳定生产[P]≤0.015%的低磷钢水常常需要把钢水[C]降低到0。
08%以下,造成炉渣和钢水的严重过氧化,出钢a O≥800 10-6。
(3)钢水过氧化,增大脱氧剂消耗使钢中脱氧产物形成的夹杂物大量增加,为夹杂物去除带来很大困难.(4)脱氧产生的大量夹杂物,很难上浮去除,往往需要大幅度延长“软吹”时间。
延长“软吹”时间又由于炉渣和耐火材料的侵蚀以及完成脱硫任务等过程产生大量新的细小夹杂物,很难去除.(5)渣量大,炉渣利用率低,难以实现炉渣循环利用。
洁净钢的生产实践
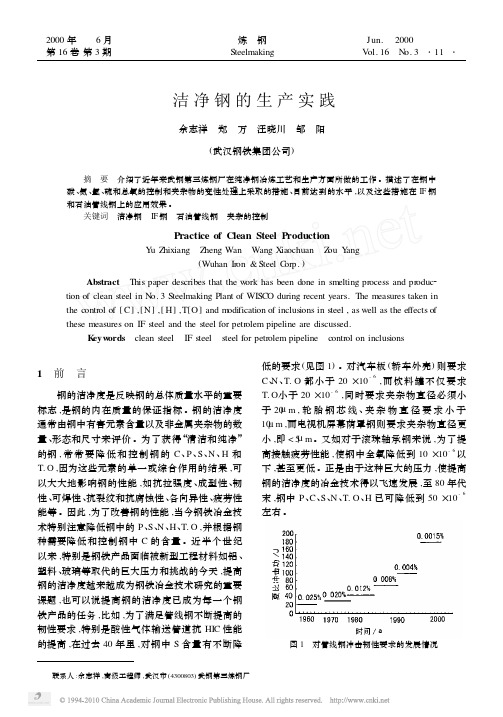
图 5 转炉复吹和无复吹时的碳氧平衡
目前可达到 FeO + MnO < 1 % ; (5) 充分利用二次精炼手段净化钢水 ; (6) 连铸保护浇注技术 ,降低二次氧化程度 ; (7) 钢包下渣监测技术 ; (8) 大容量中包的使用 ,使夹杂物与钢水分
离 ,钢液深度 ≥1m 时钢水在中包内平均滞留时间 ≥10min ;
(9) 碱性中包内衬和保温剂的使用 ; (10) 减少中包吹氩量 ; (11) 结晶器液面自动控制技术 ,确保精度为 ≤±3mm 。 通过采取上述各项措施 ,使钢水的全氧大大 降低 ,尤其是 IF 钢 ,目前铸坯的全氧已下降到 25 ×10 - 6 左右 。 由于我厂能较好地控制钢中 C、N 和全氧含 量 ,因此已能成功地生产出 IF 汽车用钢 。目前 IF 钢达到的水平如下 。 (1) 已实现了批量生产 ,1998 年 1 月~1999 年 7 月份共生产 IF 钢 222 炉 ,约 5. 8 万 t ,炼成率 为 96 %。表 1 列出 IF 钢的主要技术指标 。 (2) 通过对 IF 钢的碳 、硅 、氮和洁净度的控 制 , 有效地提高了 IF 钢的机械性能 。目前 , 按此
2 洁净钢生产技术的发展与产品质量现 状
2. 1 三炼钢简介
武钢三炼钢是利用西班牙贷款进行建设的国 家重点工程项目 ,德国的 DEMAG 公司对工程的 技术问题负责 。一期工程包括两座公称容量为 250t 的转炉 (以二吹一方式生产) 和两台双流弧形 板坯连铸机 ,并配有铁水脱硫 (国内设计与供货) 和钢包吹氩 、钢包炉 、RH 真空脱气装置 ,形成年 产 250~300 万 t 的设计生产能力 。
2. 2 脱碳技术与碳的控制
碳作为钢中的间隙原子 ,在超深冲薄板 ,尤其 是汽车板 IF 钢中成为主要控制对象 ,要求尽可能 低 。为了获得碳含量小于 30 ×10 - 6 甚至更低的超 低碳钢 ,关键是真空脱碳的水平及精炼后控制钢 水增碳的能力 。
钢铁企业的生产过程和对环境的影响以及如何清洁生产【论文】

钢铁企业的生产过程和对环境的影响以及如何清洁生产钢铁企业的生产过程和对环境的影响以及如何清洁生产-职教文章清洁生产论文如何以及企业生产过程环境影响钢铁摘要:钢铁企业的生产过程的简介和生产过程对环境产生的影响和危害;针对生产过程中产生的环境问题,企业当以科学发展观为指导,促进企业自主创新能力,在生产中实行清洁生产。
钢铁企业生产过程简介:炼钢法原料--可以是铁矿石也可以是废铁,这取决于工艺过程--首先熔化成钢水。
以矿砂为原料的炼钢须使用高炉,而以废铁为原料的工艺使用的是电弧熔炉。
然后,钢水被倒入连铸机中凝固,这样就生产出了我们所知道的半成品。
这些半成品可以是具有矩形横截面的扁钢锭,也可以是具有个正方形截面的块钢或者钢坯。
它们都是一些坯料,用于制造最后的成品。
最后,这些半成品被变形或轧制成为最终成品。
其中的一些须经过热处理,就是所谓的“热轧”。
随后,一半以上的经过热轧的薄钢板在环境温度下再次轧制(即所谓的“冷轧”)。
然后,它可以被涂上一层抗腐蚀的防护材料。
1、烧结在烧结车间中,制备铁矿石。
铁矿石被压碎碾成标准化的颗粒,被烧结或粘合在一起。
烧结的铁矿石随后被压碎,并按一层焦炭、一层矿石的交替方式,被加入高炉中。
焦炭是是从富炭煤蒸馏出的固体残渣,极易燃烧。
2、高炉在高炉中,从铁矿石中提取铁。
固态的矿石和焦炭由顶部加入高炉,而高炉底部送来的一股热气(1200℃)致使几乎是100%含炭量的焦炭开始燃烧。
这便产生了碳的氧化物,它通过除氧过程来减少了氧化铁,从而分离出铁。
由燃烧产生的热量将铁和脉石(矿石中矿物的集合)熔化成液体。
脉石,由于比较轻,会漂浮至铁水表面,就是所谓的“生铁”。
纯净钢的开发与生产

纯净钢的开发与生产
张爱民;袁松涛
【期刊名称】《安徽工业大学学报(自然科学版)》
【年(卷),期】2003(020)0z1
【摘要】对纯净钢的生产工艺和技术进行了简述,结合济钢三炼钢和中厚板的生产实际,提出了改进连铸坯内部质量的措施,为进一步开发生产高附加值、高难度和高技术含量的纯净钢提供了依据.
【总页数】3页(P166-167,174)
【作者】张爱民;袁松涛
【作者单位】济南钢铁股份有限公司,济南,250101;济南钢铁股份有限公司,济南,250101
【正文语种】中文
【中图分类】TF703.5.4
【相关文献】
1.纯净钢及纯净铸坯的生产技术 [J], 朱立光;唐国章;
2.转炉高纯净度GCrl5轴承钢的试制开发 [J], 李金浩
3.开发纯净钢冶炼技术生产高强度钢丝绳用钢 [J], 王秉喜;郭大勇
4.超高纯净钢生产技术的开发 [J], 竹之内朋;文凡
5.为生产纯净钢开发的白渣高效脱硫工艺 [J],
因版权原因,仅展示原文概要,查看原文内容请购买。
济钢从靠钢吃饭到无钢发展的主要经验申论
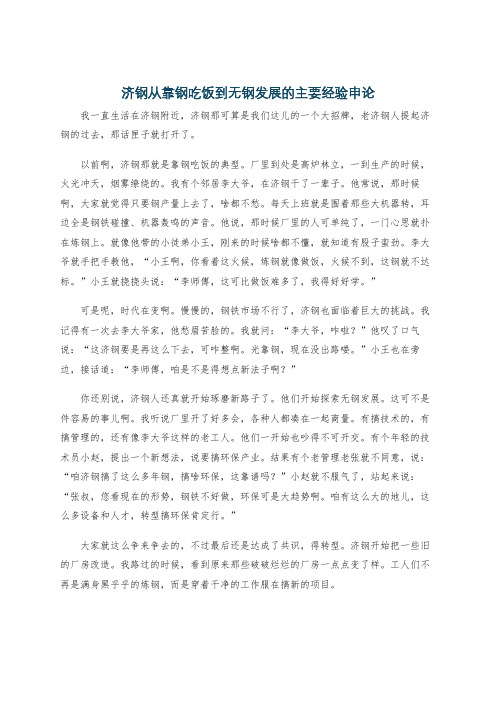
济钢从靠钢吃饭到无钢发展的主要经验申论我一直生活在济钢附近,济钢那可算是我们这儿的一个大招牌,老济钢人提起济钢的过去,那话匣子就打开了。
以前啊,济钢那就是靠钢吃饭的典型。
厂里到处是高炉林立,一到生产的时候,火光冲天,烟雾缭绕的。
我有个邻居李大爷,在济钢干了一辈子。
他常说,那时候啊,大家就觉得只要钢产量上去了,啥都不愁。
每天上班就是围着那些大机器转,耳边全是钢铁碰撞、机器轰鸣的声音。
他说,那时候厂里的人可单纯了,一门心思就扑在炼钢上。
就像他带的小徒弟小王,刚来的时候啥都不懂,就知道有股子蛮劲。
李大爷就手把手教他,“小王啊,你看着这火候,炼钢就像做饭,火候不到,这钢就不达标。
”小王就挠挠头说:“李师傅,这可比做饭难多了,我得好好学。
”可是呢,时代在变啊。
慢慢的,钢铁市场不行了,济钢也面临着巨大的挑战。
我记得有一次去李大爷家,他愁眉苦脸的。
我就问:“李大爷,咋啦?”他叹了口气说:“这济钢要是再这么下去,可咋整啊。
光靠钢,现在没出路喽。
”小王也在旁边,接话道:“李师傅,咱是不是得想点新法子啊?”你还别说,济钢人还真就开始琢磨新路子了。
他们开始探索无钢发展。
这可不是件容易的事儿啊。
我听说厂里开了好多会,各种人都凑在一起商量。
有搞技术的,有搞管理的,还有像李大爷这样的老工人。
他们一开始也吵得不可开交。
有个年轻的技术员小赵,提出一个新想法,说要搞环保产业。
结果有个老管理老张就不同意,说:“咱济钢搞了这么多年钢,搞啥环保,这靠谱吗?”小赵就不服气了,站起来说:“张叔,您看现在的形势,钢铁不好做,环保可是大趋势啊。
咱有这么大的地儿,这么多设备和人才,转型搞环保肯定行。
”大家就这么争来争去的,不过最后还是达成了共识,得转型。
济钢开始把一些旧的厂房改造。
我路过的时候,看到原来那些破破烂烂的厂房一点点变了样。
工人们不再是满身黑乎乎的炼钢,而是穿着干净的工作服在搞新的项目。
李大爷虽然一开始也有点不适应,但是看到厂里有了新变化,也很高兴。
- 1、下载文档前请自行甄别文档内容的完整性,平台不提供额外的编辑、内容补充、找答案等附加服务。
- 2、"仅部分预览"的文档,不可在线预览部分如存在完整性等问题,可反馈申请退款(可完整预览的文档不适用该条件!)。
- 3、如文档侵犯您的权益,请联系客服反馈,我们会尽快为您处理(人工客服工作时间:9:00-18:30)。
济钢洁净钢生产工艺实践
前言
随着社会经济的发展,工程机械和煤机行业用高强钢向着高参数化、轻量化、大型化的方向发展,因此提高高强钢产品的强度和质量是钢铁企业发展的趋势,也是提高市场竞争力的必要手段。
济钢210t转炉作业区充分利用现有装备的有利条件,在低合金高强钢的生产过程中通过工艺优化和技术改进获得了丰富的生产经验,并掌握了高强钢生产的关键技术,完善了设备的冶金功能,逐步实现了一系列低合金高强度钢批量生产的能力。
1、生产工艺
济钢炼钢厂210t转炉作业区于2009年12月26日建成投产,现有KR铁水脱硫、210t转炉、LF精炼炉、RH精炼炉各1座、DANIELI 板坯连铸机1台,铸坯厚度250mm、300mm,以250mm的厚度为主,生产钢种包括船板钢、高强度钢、容器钢、管线钢以及其他一些特殊用钢,年产量150万t左右。
目前该区域已经实现了100%钢水精炼处理工艺,其中RH处理比率平均达到58%左右。
根据低合金高强度钢的轧制以及用户使用要求,实际生产中制定了相应的工艺路线,按照KR-转炉-LF-RH-CCM的生产工艺路线进行生产。
2、生产应用与改进
由于低合金高强钢要求有较高的强度和韧性,因此要求钢水的洁净度高,夹杂物含量低,铸坯的表面质量和内部质量良好。
因此需要对钢水中的P、S、N、O、H等有害元素及夹杂物进行合理控制,
从而达到产品性能和用户的要求。
高强钢的化学成分见表1
通过实际生产的应用和数据分析结果,对高强钢的生产工艺参数进行了相应的改进和优化,提升了高强炼钢工序生产系统的能力,实现了低缺陷高质量的要求,达到了单线生产批量化、稳定运行的目的。
相关应用改进如下:
1)脱硫工艺的优化。
从生产高强钢的实际情况和数据分析结果表明,要将钢水中的S含量降到更低(10×10-6以下),需要降低精炼初始硫含量。
同时,钢水到LF炉快速造渣延长脱硫时间,将渣中全氧含量迅速降低到1.0%以下,并采用合适的氩气搅拌,保证钢-渣充分接触,脱硫期间将钢渣碱度控制在3~5之间,脱硫期间温度控制在1 580~1600℃为宜。
2)减少增氮工艺的优化。
根据有关企业的生产实际情况表明,余氧出钢可以大大降低出钢过程的增氮量,因此可以尝试在出钢过程中对钢水不完全镇静,适当减少铝的加入量,保持出钢过程中钢水的氧含量,减少钢水增氮,从而稳定、控制钢水初始N含量。
同时,LF精炼过程中通过调节风机的开度,确保钢水处理过程中实现微正压,避免与空气接触增氮。
3)RH工艺的优化。
按照冶金热力学关系,100Pa以下氢气分压平衡的钢水氢含量约为(0.5~0.78)×10-6,但RH脱氢过程速率的不均衡使得脱氢在接近其热力学平衡点时出现停滞,钢水氢脱至1×10-6以下需大大延长处理时间。
同时,RH在真空处理20min以后脱氧效果减弱,并出现Al烧损。
另外根据有关实验研究表明:RH处
理过程中夹杂物的去除行为主要发生在前12min,RH处理12min可将绝大部分的夹杂物去除,且2~8min又是去夹杂最快的时间段,16min 后熔池中几乎没有簇状物,在20~24min区间内,与其他区间相比,夹杂物的去除率已很小,这表明RH处理24min后,能去除的夹杂物几乎已全部去除,从去除夹杂物的角度考虑,继续进行RH处理的意义不大,该结果与实际取样基本吻合。
因此,将RH真空处理时间调整为18~20min,既可以满足钢水脱气要求又可以和生产节奏匹配,实现合理的优化。
4)吹氩时间的优化和调整。
根据有关研究表明,喂线后合理的软吹氩工艺有利于钢中夹杂物的上浮,根据LF路喂线软吹氩时间与夹杂物指数关系可见,合适的软吹氩时间应控制在10~15min)。
当吹氩时间较长时,钢中的夹杂物指数(夹杂物指数=B类+D类)反而升高,这主要与吹氩较强导致钢液二次氧化有关。
因此,将精炼吹氩调整为15 min,保证夹杂物上浮的同时避免二次氧化。
5)精炼渣系的选择。
对于高强钢生产精炼渣的选择来说,既要满足脱硫又要保证后期夹杂物的吸附。
因此需要考虑精炼渣的组成和熔点,根据实际生产结果看钢渣碱度控制在3~5,∑(MnO+Fe)≤1.0%,Al2O3≥25%,即可满足高强钢生产的要求。
3、结语
1)高强钢的生产需要关注生产原料条件,尽可能的降低各种原料中的有害元素含量,并充分发挥炼钢各工序设备的冶金功能,实现系统的稳定以及系统成本的最低化,获得效益的同时达到优良的
产品质量。
2)增氮的控制是贯穿于炼钢生产的各个环节的,因此需要各工序在操作上精心控制,并采取不同措施减少或消除增氮的因素。
3)对于钢水中夹杂物,一方面采用控制为主,即减少夹杂物的产生量;另一方面对于已经产生的夹杂物尽可能的除去或变性,减少对钢材质量的影响。
通过优化夹杂物控制和去除的手段,精炼结束后B+D类夹杂物含量可以控制在1.5以下。
4)从生产情况看,P+S+N+O+H的总和在(104~259)×10-6,影响较大的是钢水中的P含量,最低为67×10-6,最高为144×10-6,其次是N含量。
如果将P含量稳定控制在50×10-6以内,则P+S+N+O+H 的总和可以控制在100×10-6。
因此,下一步需要重点考虑钢水P、N 含量的稳定控制。