几个主要工艺参数的计算
工艺参数的计算

采用未抛光的硅片进行加工,直径520.3m μ±,电阻率60~70cm Ω,厚度4208m μ±,晶向(111)面偏(110)方向3D 。
扩散源分为两种。
第一种:8:100g ml 23B O :乙醇=,超声8小时后,净置2~3天,配成饱和溶液,取1ml 的饱和溶液,加入10ml 乙醇,即可配置成110的扩散硼源,依例可配1100或1300的扩散源;第二种:Al(N 10:100g ml =33O ):乙醇,超声8小时后,净置2~3天,配成饱和溶液,涂源时可以直接使用。
扩散温度:1200C D ,扩散时间:44小时。
下面给出扩散时间的计算:22j x k Dt = (1)1200T C =D ,1228.310/D cm s −=×,60j x m μ=(2)17121131102(ln ) 5.51510k ×==× (3) 或131112175102(1)2(12(0.9995) 4.92110D S N k erf erf erf N −−−×=−=−× (4) 求平均 5.2k = (5)2422212(6010)16040544.65.28.310j x t s hr k D −−×==≈≈×× (6) 考虑到扩散后还需要慢降温,因此,我们取扩散时间为44hr 。
扩散22hr 后抽测结深,测试结果44.4j x m μ=。
扩散及慢降温结束后,测得结深62j x m μ=。
单项实验:一、预淀积硼,45/R =Ω,,(1个),30/R <Ω,,(2个)。
注意:温度不变,时间延长。
二、1140T C =D ,干2N 推进6′,硅片立放。
三、漂净BSG (1:10),去净,测量R ,四、推进,1140,3T C t hr ==D ,三片同时立放。
五、看硅片是否变形,光刻涂胶台能否吸住。
测量结深。
高炉炼铁技术主要工艺参数计算公式
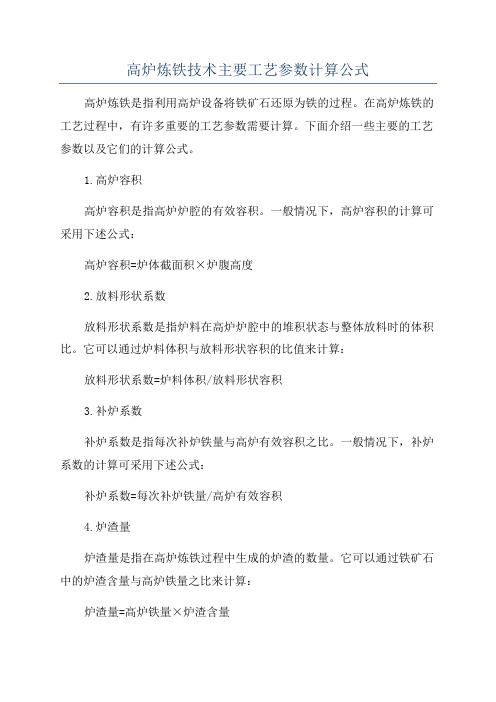
高炉炼铁技术主要工艺参数计算公式高炉炼铁是指利用高炉设备将铁矿石还原为铁的过程。
在高炉炼铁的工艺过程中,有许多重要的工艺参数需要计算。
下面介绍一些主要的工艺参数以及它们的计算公式。
1.高炉容积高炉容积是指高炉炉腔的有效容积。
一般情况下,高炉容积的计算可采用下述公式:高炉容积=炉体截面积×炉腹高度2.放料形状系数放料形状系数是指炉料在高炉炉腔中的堆积状态与整体放料时的体积比。
它可以通过炉料体积与放料形状容积的比值来计算:放料形状系数=炉料体积/放料形状容积3.补炉系数补炉系数是指每次补炉铁量与高炉有效容积之比。
一般情况下,补炉系数的计算可采用下述公式:补炉系数=每次补炉铁量/高炉有效容积4.炉渣量炉渣量是指在高炉炼铁过程中生成的炉渣的数量。
它可以通过铁矿石中的炉渣含量与高炉铁量之比来计算:炉渣量=高炉铁量×炉渣含量5.进料系数进料系数是指进入高炉的原料中铁矿石与高炉铁量之比。
一般情况下,进料系数的计算可采用下述公式:进料系数=铁矿石量/高炉铁量6.还原度还原度是指高炉还原反应的程度,也可以理解为高炉炼铁过程中铁矿石中铁元素的转化率。
还原度可以通过炉内原料的化学成分以及进气温度等因素进行估算。
7.炉渣碱度炉渣碱度是指炉渣中碱金属氧化物与二氧化硅之比。
一般情况下,炉渣碱度的计算可采用下述公式:炉渣碱度=(Na2O+K2O)/SiO2以上是一些高炉炼铁过程中常用的工艺参数及其计算公式。
当然,实际计算过程可能会更加复杂,因为高炉炼铁是一个多参数、多反应的复杂过程。
因此,在实际操作中需要根据具体情况综合考虑各个因素,并进行相应的修正计算。
几个重要工艺参数的计算
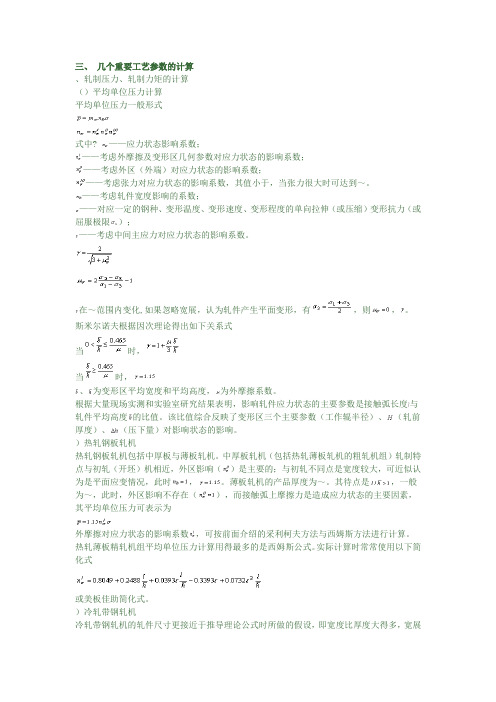
三、几个重要工艺参数的计算、轧制压力、轧制力矩的计算()平均单位压力计算平均单位压力一般形式式中? ——应力状态影响系数;——考虑外摩擦及变形区几何参数对应力状态的影响系数;——考虑外区(外端)对应力状态的影响系数;——考虑张力对应力状态的影响系数,其值小于,当张力很大时可达到~。
——考虑轧件宽度影响的系数;——对应一定的钢种、变形温度、变形速度、变形程度的单向拉伸(或压缩)变形抗力(或屈服极限);——考虑中间主应力对应力状态的影响系数。
在~范围内变化,如果忽略宽展,认为轧件产生平面变形,有,则,。
斯米尔诺夫根据因次理论得出如下关系式当时,当时,、为变形区平均宽度和平均高度,为外摩擦系数。
根据大量现场实测和实验室研究结果表明,影响轧件应力状态的主要参数是接触弧长度与轧件平均高度的比值。
该比值综合反映了变形区三个主要参数(工作辊半径)、(轧前厚度)、(压下量)对影响状态的影响。
)热轧钢板轧机热轧钢板轧机包括中厚板与薄板轧机。
中厚板轧机(包括热轧薄板轧机的粗轧机组)轧制特点与初轧(开坯)机相近,外区影响()是主要的;与初轧不同点是宽度较大,可近似认为是平面应变情况,此时,。
薄板轧机的产品厚度为~。
其待点是,一般为~,此时,外区影响不存在(),而接触弧上摩擦力是造成应力状态的主要因素,其平均单位压力可表示为外摩擦对应力状态的影响系数,可按前面介绍的采利柯夫方法与西姆斯方法进行计算。
热轧薄板精轧机组平均单位压力计算用得最多的是西姆斯公式。
实际计算时常常使用以下简化式或美板佳助简化式。
)冷轧带钢轧机冷轧带钢轧机的轧件尺寸更接近于推导理论公式时所做的假设,即宽度比厚度大得多,宽展很小,可认为是平面变形问题。
轧件厚度小,轧件内部不均匀变形可忽略,因而平面断面假设和滑动摩擦理论与冷轧带钢(薄板)的情况较符合。
此外,冷轧时均采用张力轧制,因而计算冷轧平均单位压力时,必须考虑张力影响。
其平均单位压力可表示为计算冷轧带钢轧机平均单位压力常采用斯通方法,亦可采用考虑张力影响后的采利柯夫方法或其柯洛辽夫简化公式。
A O法工艺计算 带公式
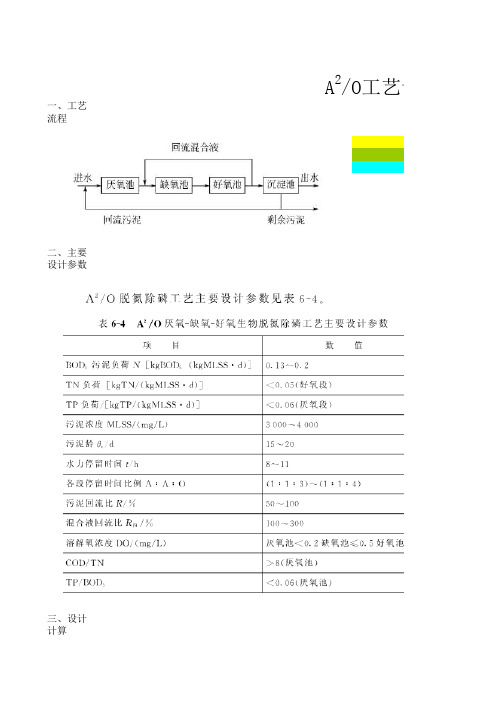
去除每1kgBOD5的需
氧量=AOR/[Q(S0-
(kgO2/kgBO
S)]= 1.5456727 D5)
2、标准需 氧量 采用鼓风 曝气,微 孔曝气器 。曝气器 敷设于池 底,距池 底0.2m, 淹没深度 将实际需 氧量AOR换 算成标准 状态下的 需氧量SOR 。
查表得水 中溶解氧 饱和度: 空气扩散 气出口处 绝对压 为: 空气离开 好氧反应 池时氧的 百分比:
设回流污 泥泵房1 座,内设3 台潜污泵 (2用1 备);
水泵扬程
单泵流量QR单 =0.5QR=
13、混合 液回流设 备 (1)混合 液回流泵
300 m3 1500 w
300 m3 1500 w
100 %
RQ=
4000 m3/d
= 166.66667 (m3/h)
83.33333333 (m3/h)
4、出水堰 及出水井 按矩形堰 流量公式 计算:
单组反应池回流污 泥管设计流量Qk=
0.046 (m3/s)
管道流速V=
0.8 m/s;
管道过水断面积A= 0.0575 (m2)
管径d= 0.2706444 (m)
取进水管管径DN 900 mm
进水孔过流量Q2= 0.0462963 (m3/s)
孔口流速V=
力出水总
管设计流
量Q7=Q6=
0.0462963 m/s
设计流速采用v=
1.2 m/s
管道过水断面积A= Q7/v= 0.0385802 m2
管径d= 0.2216908 (m)
取泵房压力出水管
管径DN
700 mm
O工艺计算
取值填入部分 计算结果部分 输入数据部分
(整理)几个重要工艺参数的计算.
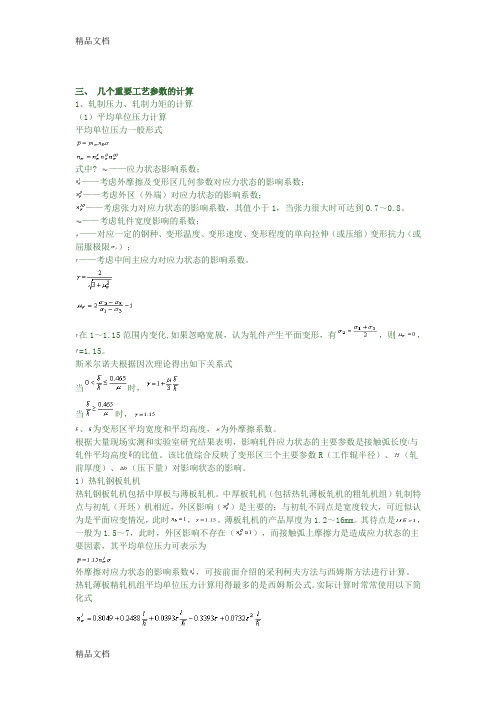
三、几个重要工艺参数的计算1、轧制压力、轧制力矩的计算(1)平均单位压力计算平均单位压力一般形式式中? ——应力状态影响系数;——考虑外摩擦及变形区几何参数对应力状态的影响系数;——考虑外区(外端)对应力状态的影响系数;——考虑张力对应力状态的影响系数,其值小于1,当张力很大时可达到0.7~0.8。
——考虑轧件宽度影响的系数;——对应一定的钢种、变形温度、变形速度、变形程度的单向拉伸(或压缩)变形抗力(或屈服极限);——考虑中间主应力对应力状态的影响系数。
在1~1.15范围内变化,如果忽略宽展,认为轧件产生平面变形,有,则,=1.15。
斯米尔诺夫根据因次理论得出如下关系式当时,当时,、为变形区平均宽度和平均高度,为外摩擦系数。
根据大量现场实测和实验室研究结果表明,影响轧件应力状态的主要参数是接触弧长度与轧件平均高度的比值。
该比值综合反映了变形区三个主要参数R(工作辊半径)、(轧前厚度)、(压下量)对影响状态的影响。
1)热轧钢板轧机热轧钢板轧机包括中厚板与薄板轧机。
中厚板轧机(包括热轧薄板轧机的粗轧机组)轧制特点与初轧(开坯)机相近,外区影响()是主要的;与初轧不同点是宽度较大,可近似认为是平面应变情况,此时,。
薄板轧机的产品厚度为1.2~16mm。
其待点是,一般为1.5~7,此时,外区影响不存在(),而接触弧上摩擦力是造成应力状态的主要因素,其平均单位压力可表示为外摩擦对应力状态的影响系数,可按前面介绍的采利柯夫方法与西姆斯方法进行计算。
热轧薄板精轧机组平均单位压力计算用得最多的是西姆斯公式。
实际计算时常常使用以下简化式或美板佳助简化式。
2)冷轧带钢轧机冷轧带钢轧机的轧件尺寸更接近于推导理论公式时所做的假设,即宽度比厚度大得多,宽展很小,可认为是平面变形问题。
轧件厚度小,轧件内部不均匀变形可忽略,因而平面断面假设和滑动摩擦理论与冷轧带钢(薄板)的情况较符合。
此外,冷轧时均采用张力轧制,因而计算冷轧平均单位压力时,必须考虑张力影响。
高炉炼铁技术主要工艺参数计算公式
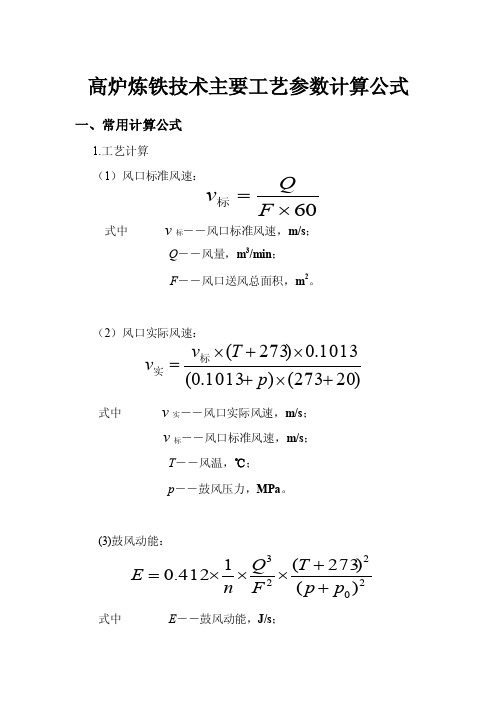
高炉炼铁技术主要工艺参数计算公式一、常用计算公式1.工艺计算(1)风口标准风速:式中v 标--风口标准风速,m/s ;Q ――风量,m 3/min ; F ――风口送风总面积,m 2。
(2)风口实际风速:式中 v 实--风口实际风速,m/s ;v 标--风口标准风速,m/s ;T --风温,℃; p --鼓风压力,MPa 。
(3)鼓风动能:式中 E --鼓风动能,J/s ;60⨯=F Q v 标)20273()1013.0(1013.0)273(+⨯+⨯+⨯=p T v v 标实20223)()273(1412.0p p T F Q n E ++⨯⨯⨯=Q --风量,m 3/min ;n --风口数目,个;F --风口总截面积,m 3; T --热风温度,℃;P --热风压力,Pa ;P 0--标准大气压,等于101325Pa 。
(4)富氧率:1)氧气兑入口在冷风管道孔板前面,即富氧量流经流量孔板,考虑鼓风湿度时富氧率公式为:不考虑鼓风湿度时富氧率公式为:2)氧气兑入口在冷风管道孔板后面,即富氧量未流经流量孔板,考虑鼓风湿度时富氧率公式为:不考虑鼓风湿度时富氧率公式为:()()%10021.029.021.0⨯⎥⎦⎤⎢⎣⎡-++⨯-=风氧氧风Q b Q f Q Q B ()%10021.0⨯-=风氧Q Q b B ()%10021.029.021.0⨯⎥⎥⎦⎤⎢⎢⎣⎡-+++⨯=氧风氧风Q Q b Q f Q B ()%10021.0⨯+⨯-=氧风氧Q Q Q b B式中 B --富氧率,%;Q 风--风量(冷风流量孔板显示值),m 3/min ;Q 氧--富氧量,m 3/min ;0.21--鼓风中含氧率;b --氧气中含氧率,%; f --鼓风湿度,%。
(5)冶炼周期: 式中t --冶炼周期,h ;V ′--由料线到风口中心线的容积,m 3; n --每天料批数,批;V --每批料体积,m 3/批;c --炉料在高炉内压缩率,一般为12~15%。
压铸工艺参数及计算公式

1、低速流量Q1=V1*AV1=冲头面积 3.14/4*D*D (D为锤头直径)A1=0.2M/S (低速速度为30CM每秒 为预估值)2、低速时间T1=V2/Q1V2流道系统体积由CAD内计算Q1低速流量公式1计算3、高速流量QH=V3进料口截面积*A2进料口速度进料口速度估计值与产品平均壁厚有关进料口速度估计为40M/S 转成4000CM/S进料口面积由CAD内计算4、高速时间TH=V4(产品+渣包的体积)/QH高速流量V4产品+渣包的体积由CAD内计算5、四段设定341 22点到3点加上0.005S时间4点时间为(3点时间+4点时间)的2-3倍计算公式 (单位:Q1低速流量T1低速时间V1锤头面积V2流道系统体积A1低速速度QH高速流量A2进料口速度V4产品+渣包的体积V3进料口截面积A3高速锤头速度TH高速时间单位:cm)Q1V1A1(CM/S)锤头直径MM圆周率3078.76153.9420140 3.14159T1V2Q10.3962636612203078.76QH进料口面积V3进料口速度A299600.0024.94000TH体积V4QH0.017317771724.8599600.001234时间00.39630.0223流量3078.763078.7699600.0099600.00低速冲头速度高速冲头速度0.2 6.47M/SQ1V1A1(CM/S)锤头直径MM圆周率3078.76153.9420140 3.14159 T1V2Q10.3962636612203078.76QH进料口面积V3进料口速度A2104580.0024.94200TH体积V4QH0.00192675201.5104580.001234时间00.39630.0069流量3078.763078.76104580.00#########低速冲头速度高速冲头速度0.21631.98M/S。
高炉主要工艺参数计算公式_第三次讨论(10.13)

高炉主要工艺参数计算公式1、风口标准风速:V标=Q/(F*60)式中V标--风口标准风速,m/sQ――风量,m3/minF――风口送风总面积,m22、风口实际风速:V实= V标*(T+273)*0.1013/ (0.1013+P)*(273+20)式中V实--风口实际风速,m/sV标--风口标准风速,m/sT--风温,℃P--鼓风压力,MPa3、鼓风动能:E=0.412 * 1/n * O3/F2 * (T+273)2/(P+P0)2式中E--鼓风动能,j/sQ--风量,m3/minn--风口数目,个F--风口总截面积,m3T--热风温度,℃P--热风压力,MPaP0--标准大气压,等于101325PaV――炉缸煤气量,m3宝信疑问:O3是否就是Q3?Q:风量,m3/min;(是的)(动能公式按确认文件中宝信理解计算)V――炉缸煤气量,m3,公式中未使用;(不用)6、焦炭负荷:P=Q矿/Q焦式中P--焦炭负荷Q矿--矿石批重,kgQ焦--焦炭(干基)批重,kg7、综合负荷:P=Q矿/Q焦式中P--综合负荷Q矿--矿石批重,,kgQ综焦--综合干焦量批重(干焦量十其它各种燃料量×折合干焦系数批重,)kg宝信疑问:报表上的负荷采取焦炭负荷还是综合负荷;其中干基是否就是干焦(是的);(参照新发给你的报表)8、休风率: u=t/T×100%式中 u――休风率,%t ——高炉休风停产时间,minT——规定日历作业时间(日历时间减去计划达中休时间),min9、生铁合格率生铁合格率是指检验合格生铁占全部检验生铁的百分比。
其计算公式为:生铁合格率(%)= 生铁检验合格量(吨)×100%生铁检验总量(吨)生铁检验合格量是否同下面焦比中合格生铁产量一个概念(不是,生铁检验合格量不进行折算,而焦比中合格生铁产量要进行折算)或者说它们的关系如何计算说明:(1)高炉开工后,不论任何原因造成的出格生铁,均应参加生铁合格率指标的计算。
包覆纱机工艺计算方法

包覆纱机工艺计算方法
包覆纱机是一种用于生产各种包覆线的设备。
它通过将一根或多根芯线缠绕在外层纤维上来制成包覆线。
在包覆纱机中,有几个关键的工艺参数需要考虑,包括包覆比、绕线速度和张力等。
接下来将分别介绍这些参数以及计算方法。
1. 包覆比
包覆比是指包覆线中外层纤维的重量与总重量之比。
包覆比的大小对织物的品质和性能起着至关重要的作用。
包覆比的计算方法如下:
包覆比= (外层纤维重量/ 总重量) ×100%
其中,外层纤维重量是指包覆线中外层纤维所占的重量,总重量是指包覆线的总重量。
2. 绕线速度
绕线速度是指芯线在包覆纱机上的运动速度。
绕线速度的大小对包覆线的品质和生产效率有着重要的影响。
绕线速度的计算方法如下:
绕线速度= π×直径×转速
其中,π是圆周率,直径是指芯线或外层纤维的直径,转速是指包覆轮的转速。
3. 张力
张力是指芯线或外层纤维在包覆过程中所受的拉力。
张力的大小对于包覆线的品质和成品的物理性能有着重要的影响。
张力的计算方法如下:
张力= 力/ 面积
其中,力是指所施加的拉力,面积是指所受力的截面积。
总之,包覆纱机工艺的计算方法主要涉及包覆比、绕线速度和张力等关键参数的计算,这些参数的大小对于包覆线的品质和生产效率有着重要的影响。
在生产过程中需要根据具体的情况进行适当的调整,以确保生产出高品质的包覆线。
简述工艺计算包括的内容。
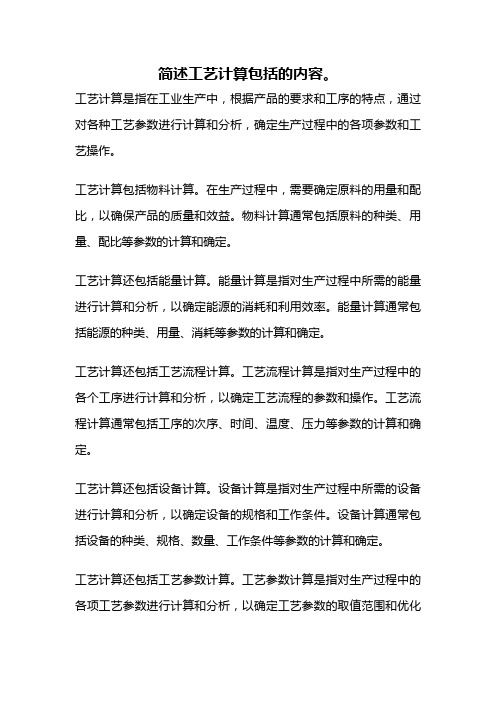
简述工艺计算包括的内容。
工艺计算是指在工业生产中,根据产品的要求和工序的特点,通过对各种工艺参数进行计算和分析,确定生产过程中的各项参数和工艺操作。
工艺计算包括物料计算。
在生产过程中,需要确定原料的用量和配比,以确保产品的质量和效益。
物料计算通常包括原料的种类、用量、配比等参数的计算和确定。
工艺计算还包括能量计算。
能量计算是指对生产过程中所需的能量进行计算和分析,以确定能源的消耗和利用效率。
能量计算通常包括能源的种类、用量、消耗等参数的计算和确定。
工艺计算还包括工艺流程计算。
工艺流程计算是指对生产过程中的各个工序进行计算和分析,以确定工艺流程的参数和操作。
工艺流程计算通常包括工序的次序、时间、温度、压力等参数的计算和确定。
工艺计算还包括设备计算。
设备计算是指对生产过程中所需的设备进行计算和分析,以确定设备的规格和工作条件。
设备计算通常包括设备的种类、规格、数量、工作条件等参数的计算和确定。
工艺计算还包括工艺参数计算。
工艺参数计算是指对生产过程中的各项工艺参数进行计算和分析,以确定工艺参数的取值范围和优化方案。
工艺参数计算通常包括工艺参数的种类、取值范围、优化方案等参数的计算和确定。
工艺计算还包括生产成本计算。
生产成本计算是指对生产过程中的各项费用进行计算和分析,以确定生产成本的构成和控制方案。
生产成本计算通常包括原材料成本、能源成本、设备成本、人工成本等费用的计算和确定。
工艺计算是工业生产中的重要环节,通过对物料、能量、工艺流程、设备、工艺参数和生产成本等方面的计算和分析,确定生产过程中的各项参数和工艺操作,以提高生产效率和产品质量,降低生产成本,实现工业生产的可持续发展。
纬编工艺参数计算

纬编工艺参数计算1. 引言纬编工艺是纺织工业中一种常用的加工工艺,通过纬编织机将纱线按照指定的编织规则交叉织成织物。
纬编工艺参数的合理调整对织物的质量和性能有着重要影响。
本文将介绍纬编工艺参数的计算方法。
2. 纬编工艺参数纬编工艺参数包括针数、纱线密度、编织规则等。
下面将对其中几个重要参数的计算方法进行介绍。
2.1 针数针数是指纬编织机每英寸上的针的数量。
针数的选择一般与织物的用途、纱线的粗细以及预期的织物品质等因素有关。
针数的计算公式如下:针数 = 每英寸针数 * 25.42.2 纱线密度纱线密度是指在单位长度内纱线的质量。
纱线密度的计算公式如下:纱线密度 = 纱线质量 / 单位长度2.3 编织规则编织规则是指纱线的交织方式,常见的编织规则有平编、斜编、提花编等。
编织规则的选择通常根据织物的图案和纺织品的需求来确定。
3. 纬编工艺参数计算实例下面以一个实例来演示纬编工艺参数的计算过程。
假设我们需要编织一块宽度为100厘米的织物,要求针数为30针/英寸,纱线密度为150克/米。
根据上述计算公式,我们可以计算出针数和纱线密度的具体数值。
针数的计算:针数 = 30 * 25.4 = 762 针/米纱线密度的计算:纱线密度 = 150克/米4. 结论纬编工艺参数的合理计算对织物的品质和性能有着重要的影响。
通过对针数、纱线密度和编织规则等参数的计算,可以得到适合纬编工艺的具体数值,从而保证织物的质量和性能。
希望本文对纬编工艺参数计算提供了一定的帮助。
以上是关于纬编工艺参数计算的介绍,希望对您有所帮助。
参考文献:[1] 纺织加工技术.王明全,高彦慧编著.中国纺织出版社.2008. [2] 纺织工艺学.张志远著.东华大学出版社.2010.。
1工艺参数的计算
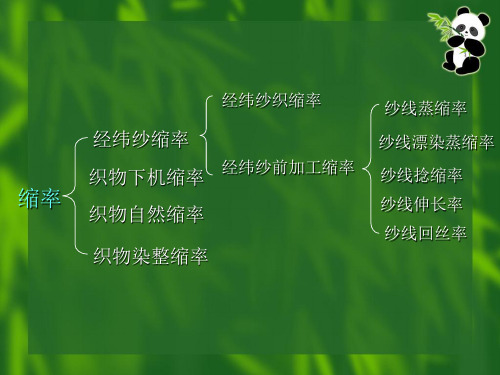
❖ 2、纬织缩率
❖ 定义:由于纱线在形成织物后,纬纱在织物中交错 屈曲,因此织造时所使用之纱线长度大于所形成 织物的长度,因而将其差值与纱线原长之比值称 做纬织缩率aw
❖ 采用“先假设,后求正”的做法 ❖ 纬织缩率=(经纱穿筘幅宽-实测成包前布幅)÷
❖ 染整长缩率=(坯布长度-成品长度)÷坯布长度 ×100%
❖ 染整幅缩率=(坯布幅宽-成品幅宽)÷坯布幅宽 ×100%
❖ 成品幅宽与坯布幅宽之比称染整幅宽加工系数.
❖ 五.织物规格中有关参数的计算与设计
❖ (一)织物紧度与密度的确定 ❖ 1.紧度与织物身骨.手感有很大关系,是织物设计
经纱穿筘幅宽×100%
❖ 练习题: 1、已知某织物匹长为30m,其经向织造缩 率为7.41%,试计算浆纱墨印长度
2、已知某织物下机幅宽为160cm,上机筘幅为
168.6cm,试计算该织物纬向织造缩率
❖ (二)纱线前处理缩率:
❖ 1、蒸缩率: ❖ 为了避免扭结及纬纱疵点,棉混纺或化纤纯纺纱线
一般都通过热湿定型蒸纱工艺, 蒸缩率表示纱线 经过蒸纱后收缩的程度.T/C ,T/L纱蒸缩率一般为 1.5%
❖ 棉布成包后1-2个月内缩变较大,随时间延长逐渐 稳定.一般:高特纱织物和卡其织物约为1%-2%(全 线卡其3%);平布约0.5%-1.5%;色织物:0.55%0.85%
❖ 3.染整缩率
❖ 染色布、色织布要经过染色和后整理加工,在加 工过程中产生的缩率称为染整缩率,也称缩水率. 其中沿经纱方向产生的缩率称染整长缩率,沿纬 纱方向产生的缩率称染整幅缩率.
❖ 设计中所采用的回丝率一般根据统计分析而定. 经纱回丝率约为0.3~1%,纬纱回丝率约为0.6~1%. 工艺计算中常用上、了机回丝,浆回丝,白回丝.
简述工艺计算包括的内容。

简述工艺计算包括的内容。
工艺计算是指在工程和制造过程中,通过运用数学和物理等科学原理,对工艺参数进行计算和分析,以确定最佳的工艺方案和操作参数。
它是工程技术领域中的一项重要工作,能够提高生产效率、降低成本、改善产品质量。
工艺计算包括以下几个方面的内容:1. 工艺流程计算:工艺流程是指物料在生产中的处理过程,包括物料的输入、加工和输出等环节。
在工艺流程计算中,需要确定物料的流量、温度、压力等参数,以及各个环节中的能耗和产量等指标。
通过对工艺流程进行计算和分析,可以确定最佳的生产工艺,提高生产效率和产品质量。
2. 材料配方计算:材料配方是指在生产中使用的原材料的比例和配比关系。
在材料配方计算中,需要根据产品的要求和性能指标,确定各个原材料的比例和配比。
通过对材料配方进行计算和分析,可以确定最佳的原材料组合,提高产品的性能和质量。
3. 设备选型计算:设备选型是指在生产中选择适合的设备和工具。
在设备选型计算中,需要考虑生产的工艺要求、生产能力和设备的性能指标等因素。
通过对设备选型进行计算和分析,可以确定最佳的设备和工具,提高生产效率和产品质量。
4. 工艺参数优化计算:工艺参数优化是指在生产过程中,通过调整工艺参数,使产品的性能和质量达到最佳状态。
在工艺参数优化计算中,需要分析生产过程中各个环节的参数和指标,确定最佳的工艺参数。
通过对工艺参数进行优化计算,可以提高产品的性能和质量,降低生产成本。
5. 能耗计算:能耗是指生产过程中消耗的能量。
在能耗计算中,需要对生产过程中的各个环节进行能耗分析,确定能耗的来源和消耗情况。
通过对能耗进行计算和分析,可以找出能耗的问题和瓶颈,采取相应的措施减少能耗,提高能源利用效率。
6. 生产成本计算:生产成本是指生产过程中所需的各种资源和费用。
在生产成本计算中,需要对生产过程中的各个环节进行成本分析,确定各项费用的来源和消耗情况。
通过对生产成本进行计算和分析,可以找出成本的问题和瓶颈,采取相应的措施降低成本,提高生产效益。
高炉主要实用工艺全参数计算公式_第三次讨论(10.13)
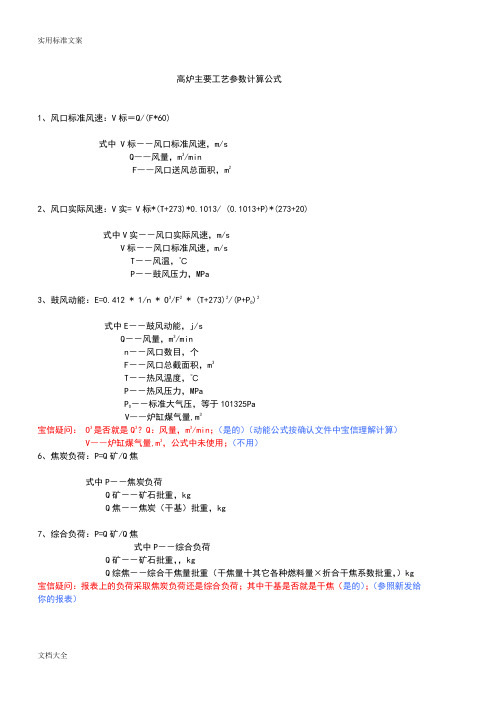
高炉主要工艺参数计算公式1、风口标准风速:V标=Q/(F*60)式中 V标--风口标准风速,m/sQ――风量,m3/minF――风口送风总面积,m22、风口实际风速:V实= V标*(T+273)*0.1013/ (0.1013+P)*(273+20)式中V实--风口实际风速,m/sV标--风口标准风速,m/sT--风温,℃P--鼓风压力,MPa3、鼓风动能:E=0.412 * 1/n * O3/F2 * (T+273)2/(P+P0)2式中E--鼓风动能,j/sQ--风量,m3/minn--风口数目,个F--风口总截面积,m3T--热风温度,℃P--热风压力,MPaP0--标准大气压,等于101325PaV――炉缸煤气量,m3宝信疑问: O3是否就是Q3?Q:风量,m3/min;(是的)(动能公式按确认文件中宝信理解计算)V――炉缸煤气量,m3,公式中未使用;(不用)6、焦炭负荷:P=Q矿/Q焦式中P--焦炭负荷Q矿--矿石批重,kgQ焦--焦炭(干基)批重,kg7、综合负荷:P=Q矿/Q焦式中P--综合负荷Q矿--矿石批重,,kgQ综焦--综合干焦量批重(干焦量十其它各种燃料量×折合干焦系数批重,)kg 宝信疑问:报表上的负荷采取焦炭负荷还是综合负荷;其中干基是否就是干焦(是的);(参照新发给你的报表)8、休风率: u=t/T×100%式中 u――休风率,%t ——高炉休风停产时间,minT——规定日历作业时间(日历时间减去计划达中休时间),min9、生铁合格率生铁合格率是指检验合格生铁占全部检验生铁的百分比。
其计算公式为:生铁合格率(%) = 生铁检验合格量(吨)×100%生铁检验总量(吨)生铁检验合格量是否同下面焦比中合格生铁产量一个概念???(不是,生铁检验合格量不进行折算,而焦比中合格生铁产量要进行折算)或者说它们的关系如何???计算说明:(1)高炉开工后,不论任何原因造成的出格生铁,均应参加生铁合格率指标的计算。
机械工艺技术计算

机械工艺技术计算机械工艺技术是机械制造业的核心技术之一,它对于机械制造过程中的各种工艺参数的计算至关重要。
本文将探讨机械工艺技术的计算方法以及其在机械制造过程中的应用。
首先,机械工艺技术的计算方法主要包括几何尺寸计算、工艺参数计算和加工工艺数值模拟等。
几何尺寸计算是指根据物体的形状、尺寸和公差要求,进行几何参数的计算。
例如,在零件的设计过程中,需要计算出其长度、宽度、高度等几何尺寸。
工艺参数计算包括工作量的计算、工时的计算、生产能力的计算等。
例如,在机械制造过程中,需要计算出每个工序的加工时间,以及整个工艺流程的总加工时间。
加工工艺数值模拟是通过利用计算机软件进行数值模拟,对机械加工过程进行仿真和优化。
通过模拟计算,可以验证机械加工过程的可行性,并且找到最优化的工艺参数。
其次,机械工艺技术的计算方法在机械制造中有着广泛的应用。
首先,它可以对机械零件的几何尺寸进行计算,从而保证零件的尺寸精度和公差要求。
例如,在机械加工过程中,需要根据设计图纸上的几何要求,计算出机械零件的精确尺寸,以便于进行下一步的加工操作。
其次,它可以对机械制造过程中的工艺参数进行计算,以保证加工效率和质量。
例如,在数控加工中,需要计算出每个工序的加工时间,并根据不同的工艺参数进行优化,以提高加工效率和质量。
此外,机械工艺技术的计算方法还可以在机械制造过程中进行加工工艺的数值模拟,以预测加工过程中的变形、剧变等问题,从而优化工艺参数并提高加工质量。
最后,在进行机械工艺技术计算时,需要注意一些关键问题。
首先,需要使用合适的计算方法和工具,例如使用数学计算软件、计算机辅助设计软件等。
其次,需要根据实际情况进行准确的数据输入,以保证计算结果的准确性。
此外,需要不断学习和掌握新的工艺技术和计算方法,以适应快速发展的机械制造业。
总之,机械工艺技术的计算是机械制造过程中必不可少的一环。
通过准确计算几何尺寸、工艺参数和进行加工工艺数值模拟,可以保证机械零部件的质量和加工效率,并提高机械制造的水平。
压铸工艺参数及计算公式
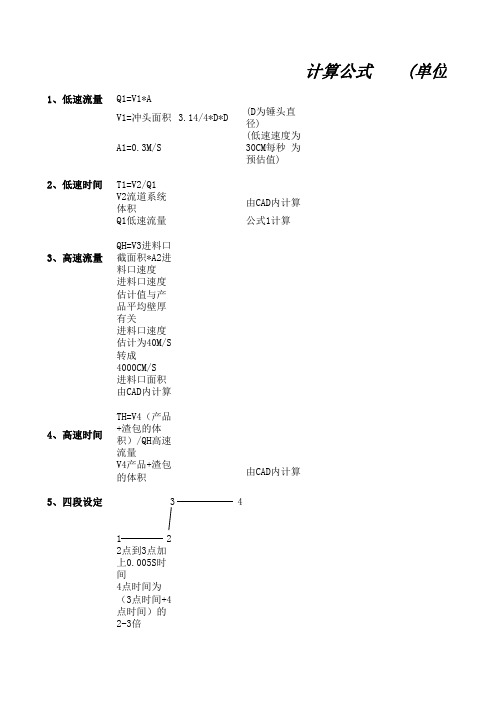
1、低速流量Q1=V1*AV1=冲头面积 3.14/4*D*D (D为锤头直径)A1=0.3M/S (低速速度为30CM每秒 为预估值)2、低速时间T1=V2/Q1V2流道系统体积由CAD内计算Q1低速流量公式1计算3、高速流量QH=V3进料口截面积*A2进料口速度进料口速度估计值与产品平均壁厚有关进料口速度估计为40M/S 转成4000CM/S进料口面积由CAD内计算4、高速时间TH=V4(产品+渣包的体积)/QH高速流量V4产品+渣包的体积由CAD内计算5、四段设定341 22点到3点加上0.005S时间4点时间为(3点时间+4点时间)的2-3倍计算公式 (单位:Q1低速流量T1低速时间V1锤头面积V2流道系统体积A1低速速度QH高速流量A2进料口速度V4产品+渣包的体积V3进料口截面积A3高速锤头速度TH高速时间单位:cm)Q1V1A1(CM/S)锤头直径MM圆周率0.000.00 3.14159T1V2Q1#DIV/0!0.00QH进料口面积V3进料口速度A20.00TH体积V4QH#DIV/0!0.001234时间0#DIV/0!#DIV/0!流量0.000.000.000.00低速冲头速度高速冲头速度0#DIV/0!M/SQ1V1A1(CM/S)锤头直径MM圆周率0.000.00 3.14159T1V2Q1#DIV/0!0.00QH进料口面积V3进料口速度A20.00TH体积V4QH#DIV/0!201.50.001234时间0#DIV/0!#DIV/0!流量0.000.000.000.00低速冲头速度高速冲头速度0#DIV/0!M/S。
第七章1工艺参数的计算
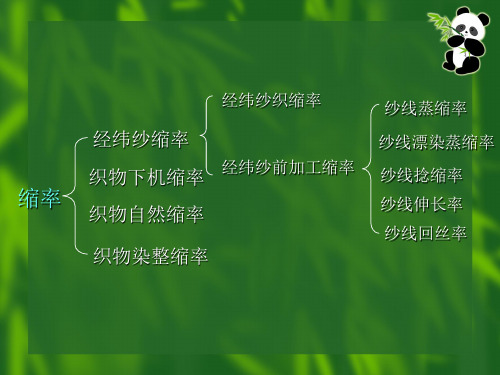
(三)筘号的确定和计算 筘号是根据经纱特数、密度、织物组织及每筘穿入数等来确定。筘号选用正确与否会影响经纱断头率、织物幅宽、经密和织物风格等。 筘号分公制筘号Nk和英制筘号Ne。(Ne=0.508Nk) 1.筘号计算公式
一般情况下: 斜纹布,哔叽,色织府绸,平布等为2%左右 卡其,府绸,色织格布为3% 劳动布,鞋用帆布大于3% 毛织品:2%~3%
2.自然缩率 指织物在折叠成件打包存放后所产生的缩率 自然缩率=(成包前织物长度-成包后织物长度) ÷成包前织物长度×100% 棉布成包后1-2个月内缩变较大,随时间延长逐渐稳定.一般:高特纱织物和卡其织物约为1%-2%(全线卡其3%);平布约0.5%-1.5%;色织物:0.55%-0.85%
2. 织物密度 可分为成品密度,坯布密度,公制单位为:根/10cm, 小数后不足0.5舍去;在0.5-1之间计0.5; 英制单位为:根/英寸,一般取整数 坯布密度又分为机上和机下密度 本白坯织物规格中所给的经纬密度一般指下机坯布的经纬密度,其与成品密度的关系如下: (下机)坯布经密(根/10cm)=成品经密×成品幅宽/坯布幅宽 (下机)坯布纬密(根/10cm)=成品纬密×(1-染整长缩率)
(1)经纱百米用纱量(kg/百米) = (2)纬纱百米用纱量(kg/百米) =
例题:某一中平布,其规格如下:254*248(根/10cm),25*28tex,91.5cm,1/1, 其中边纱共24根,地入筘数为2,边入筘数为4, 求: 1、总经根数 2、经织缩率 3、百米经、纬纱用纱量 (附:(25+28)tex分档织缩系数为:0.0208; 25 tex用纱量系数:0.002509;28 tex用纱量系数:0.002855)
- 1、下载文档前请自行甄别文档内容的完整性,平台不提供额外的编辑、内容补充、找答案等附加服务。
- 2、"仅部分预览"的文档,不可在线预览部分如存在完整性等问题,可反馈申请退款(可完整预览的文档不适用该条件!)。
- 3、如文档侵犯您的权益,请联系客服反馈,我们会尽快为您处理(人工客服工作时间:9:00-18:30)。
三、几个重要工艺参数的计算1、轧制压力、轧制力矩的计算(1)平均单位压力计算平均单位压力一般形式式中? ——应力状态影响系数;——考虑外摩擦及变形区几何参数对应力状态的影响系数;——考虑外区(外端)对应力状态的影响系数;——考虑张力对应力状态的影响系数,其值小于1,当张力很大时可达到0.7~0.8。
——考虑轧件宽度影响的系数;——对应一定的钢种、变形温度、变形速度、变形程度的单向拉伸(或压缩)变形抗力(或屈服极限);——考虑中间主应力对应力状态的影响系数。
在1~1.15范围内变化,如果忽略宽展,认为轧件产生平面变形,有,则,=1.15。
斯米尔诺夫根据因次理论得出如下关系式当时,当时,、为变形区平均宽度和平均高度,为外摩擦系数。
根据大量现场实测和实验室研究结果表明,影响轧件应力状态的主要参数是接触弧长度与轧件平均高度的比值。
该比值综合反映了变形区三个主要参数R(工作辊半径)、(轧前厚度)、(压下量)对影响状态的影响。
1)热轧钢板轧机热轧钢板轧机包括中厚板与薄板轧机。
中厚板轧机(包括热轧薄板轧机的粗轧机组)轧制特点与初轧(开坯)机相近,外区影响()是主要的;与初轧不同点是宽度较大,可近似认为是平面应变情况,此时,。
薄板轧机的产品厚度为1.2~16mm。
其待点是,一般为1.5~7,此时,外区影响不存在(),而接触弧上摩擦力是造成应力状态的主要因素,其平均单位压力可表示为外摩擦对应力状态的影响系数,可按前面介绍的采利柯夫方法与西姆斯方法进行计算。
热轧薄板精轧机组平均单位压力计算用得最多的是西姆斯公式。
实际计算时常常使用以下简化式或美板佳助简化式。
2)冷轧带钢轧机冷轧带钢轧机的轧件尺寸更接近于推导理论公式时所做的假设,即宽度比厚度大得多,宽展很小,可认为是平面变形问题。
轧件厚度小,轧件内部不均匀变形可忽略,因而平面断面假设和滑动摩擦理论与冷轧带钢(薄板)的情况较符合。
此外,冷轧时均采用张力轧制,因而计算冷轧平均单位压力时,必须考虑张力影响。
其平均单位压力可表示为计算冷轧带钢轧机平均单位压力常采用斯通方法,亦可采用考虑张力影响后的采利柯夫方法或其柯洛辽夫简化公式。
柯洛辽夫简化公式为,式中? ——变形程度(压下率);、——变形区入口和出口处轧件受到的张应力。
由于冷轧带钢较薄较硬,因此接触弧上的单位压力较大,使轧辊在接触处产生压扁现象,加长了接触弧的实际长度。
由于接触弧长度的加大,势必增强轧辊与轧件接触面上摩擦力的影响,从而使单位压力加大。
因此,在计算冷轧薄板平均单位压力时,必须考虑轧辊弹性压扁现象。
冷轧时由于存在加工硬化现象,在计算冷轧薄板平均单位压力时,轧件材料变形抗力(对冷轧亦可称为屈服极限)需按考虑加工硬化后的选用。
由于存在加工硬化影响,各道次的变形抗力不仅与本道次变形程度有关,而且还与前面各道次的总变形程度有关。
对本道次来说,沿接触弧的也是变化的,出口处比入口处要大,计算时一般把变形区作为圆弧(或抛物线)变化来计算平均总变形程度,按此平均总变形程度来计算或选取平均变形抗力。
平均总变形程度用下式计算式中? ——本道次入口处的总变形程度(从退火状态开始各道次变形程度的累计),——本道出口处的总变形程度,——退火状态坯料原始厚度;、——本道次轧件轧前轧后厚度。
a——系数,一般取;b——系数,一般取。
通常取,;在选取a、b数值时,a与b的和必须等于1。
(2)轧制压力的计算轧件对轧辊的总压力P为轧制平均单位压力与轧件和轧辊接触面积F之乘积,即接触面积F的一般形式为式中?? 、b——轧制前、后轧件的宽度;——接触弧长度的水平投影。
轧制中厚板(包括热轧薄板粗轧机组)可以不考虑轧辊弹性压扁,此时接触弧长度的水平投影(变形区长度)为式中? R——轧辊半径;——压下量。
在热轧薄板及冷轧薄板时由于单位压力较高,因此轧辊产生局部弹性压缩变形(即压扁),它将使得接触弧长度有较显著的增加。
考虑轧辊弹性压扁时的变形区长度、工作辊半径计算式中包含平均单位压力。
式中 C——系数,对于钢辊弹性模数;波松比,则。
——压扁系数。
在热轧薄板时,可简化为在冷轧薄板时可简化为式中? ——咬入角,。
压扁影响也可用轧辊当量半径的形式来计算。
、与公式联解,一般可采用迭代法,其具体步骤如下:1)选择不考虑弹性压扁计算公式算出;2)将计算的代入计算式(),并求出;3)再将代入先前的计算式,再求得;4)又将代入先前的计算式(),求出。
这样反复数次(一般3~5次就能达到计算精度的要求),使计算所得的(计算精度要求,一般为5%)或。
最后根据、计算轧件与轧辊的接触面积F和总轧制力P。
(3)轧制力矩的计算确定轧制力矩的方法有三种:1)按金属作用在轧辊上的总压力P计算轧制力矩。
在实际计算中如何根据具体轧制条件,确定合力作用角β的数值。
2)按金属作用在轧辊上的切向摩擦力计算轧制力矩。
轧制力矩等于前滑区、后滑区的切向摩擦力与轧辊半径之乘积的代数和。
在轧辊不产生弹性压缩时上式是正确的。
由于不能精确地确定摩擦力的分布及中性角γ,这种方法不便于实际应用。
3)按轧制时的能量消耗确定轧制力矩。
下面介绍按轧制压力确定轧制力矩。
在实际中,通常借助于力臂系数确定轧制力矩。
在简单轧制时:在轧制矩形断面轧件时,轧制力矩可表示为下面分热轧和冷轧考虑轧制力矩计算方法。
A、冷轧时的轧制力矩计算斯通轧制力矩计算方法是基于与推导轧制压力公式相同的假设条件得到的。
轧制力矩公式为式中,为考虑轧辊弹性压扁的接触弧长度;可由下式确定其中系数C为由上两式可得到由斯通轧制压力公式可得到简单的轧制力矩公式B、热轧时的轧制力矩计算西姆斯轧制力矩计算方法? 西姆斯推荐采用下式来计算单位宽度b=1时作用在两轧辊上的力矩式中R——轧辊的理论半径;——考虑弹性压扁的轧辊半径;——与及有关的函数(见图3-1)。
库克一马克洛姆(Cook Mccrum)轧制力矩计算公式库克一马克洛姆(Cook Mccrum)轧制力矩计算公式为为几何系数,与及压下量有关,由图3-2确定;为平均条件屈服应力。
为平面应变压缩屈服应力。
邓顿一卡兰(Denton-Crane)轧制力矩公式:轧制力矩为式中? ——变形区平均长宽比;—一平面应变压缩屈服应力。
力臂长度也可由下式确定西姆斯一怀特(Sims-Wright)轧制力矩公式? 西姆斯和怀特根据开坯机、板坯及带材轧机得到的精确轧制数据,计算了力臂系数值。
根据对于条件下的分析,得到轧制软钢时的力臂系数为根据实验数据得到范围更宽的力臂系数计算式,即对于,力臂系数为图3-1 与、的关系图3-2? 轧制力矩计算时的几何系数2、钢的变形抗力的计算方法(1)热轧变形抗力的计算方法利用高速形变凸轮试验机对几十种钢进行了高温、高速变形阻力试验(变形温度为1123~1523K,变形速度为5~100s-1),为适应计算机对变形阻力模型的要求,把各种钢(合金)的数据按下列公式结构进行非线性回归,得到各项系数。
——变形温度℃;——基准变形阻力(MPa),即T=1273K,e=0.4和u=10s-1时的变形阻力;u——变形速度(s-1);e——变形程度(真正变形程度);及——回归系数。
对于变形区平均真实变形程度的计算,由于,,故有,。
主要钢种的、及等系数如表3-2、3-3。
表3-2? 普通碳钢变形阻力数学模型回归系数回归系数牌号AD1143.6-3.130 3.9840.4103-0.41050.4847 1.575AD2146.9-2.655 3.3790.1456-0.07540.4673 1.579 Q215(A2)150.0-2.793 3.5560.2784-0.24600.4232 1.468 Q235(A3)150.0-2.878 3.6650.1861-0.12160.3795 1.402 Q235(A3F)140.3-2.923 3.7210.3102-0.26590.4554 1.520 Q215(B2F)138.4-2.716 3.4580.2099-0.13460.4552 1.595 Q235(B3F)139.8-2.861 3.6420.2540-0.19930.4349 1.510Q235(B3F(2))143.9-2.703 3.4410.2572-0.20160.4408 1.552 Q235(B3Cu)147.3-2.977 3.7890.3104-0.26610.4534 1.697表3-3? 优质碳素结构钢变形阻力数学模型回归系数回归系数牌号08F 136.1-3.387 4.3120.5130-0.53200.5887 1.87908Al136.8-2.999 3.8180.3552-0.31860.4996 1.74210151.4-2.771 3.5280.1147-0.03530.4537 1.59320152.7-2.609 3.3210.2098-0.13320.3898 1.45445158.8-2.780 3.5390.2262-0.15690.3417 1.379(2)冷轧变形抗力的计算冷轧变形阻力(常温)可用下面公式计算式中? 、——与含碳量有关的系数;见表3-4。
表3-4? 碳钢的加工硬化系数0.140.200.230.310.450.610.97 1.16含碳量/%n0.290.290.260.260.280.270.280.27a(MPa)9008108508901580182021402240某大学对08AlCu等钢种变形抗力实验数据求得的回归方程式如下:08AlCu08AlQ215(B2F)Q235(B3F)Q235(B3Cu)??式中? K——平面变形抗力,。
3、摩擦系数的计算(1)热轧咬入时的摩擦系数咬入时的摩擦系数是通过用实验方法测定极限咬入角来确定的。
取艾克隆德推荐用下式来确定摩擦系数与温度(不低于700℃)的关系:式中,对于冷硬光滑表面铸铁辊;对于钢轧辊,,t为轧件温度(℃)。
斯米尔诺夫提出了考虑轧件温度、轧辊表面粗糙度、轧件化学成分以及轧辊速度与摩擦系数的关系式:式中?——轧辊的算术平均表面粗糙度,μm;——钢中碳含量质量分数。
系数取决于轧辊速度,见表3-5。
表3-13?系数与轧辊圆周速度的关系表3-6?热轧时最大咬入角和咬入摩擦系数表3-7?冷轧碳钢咬入时的摩擦系数乌萨托斯基给出了各种轧辊表面状态时的最大咬入角和咬入时的摩擦系数,实验结果见表3-6。
最大咬入角和咬入摩擦系数随轧辊表面粗糙度的增加而增加。
(2)冷轧咬入时的摩擦系数冷轧时轧件材质、润滑条件及轧制速度对咬入时摩擦系数的影响:1)轧件材质的影响?表3-7是冷轧时由碳素钢轧件、轧辊表面粗糙度RMS(均方根值)0.2~0.4μm,得到的摩擦系数。